风电设备状况

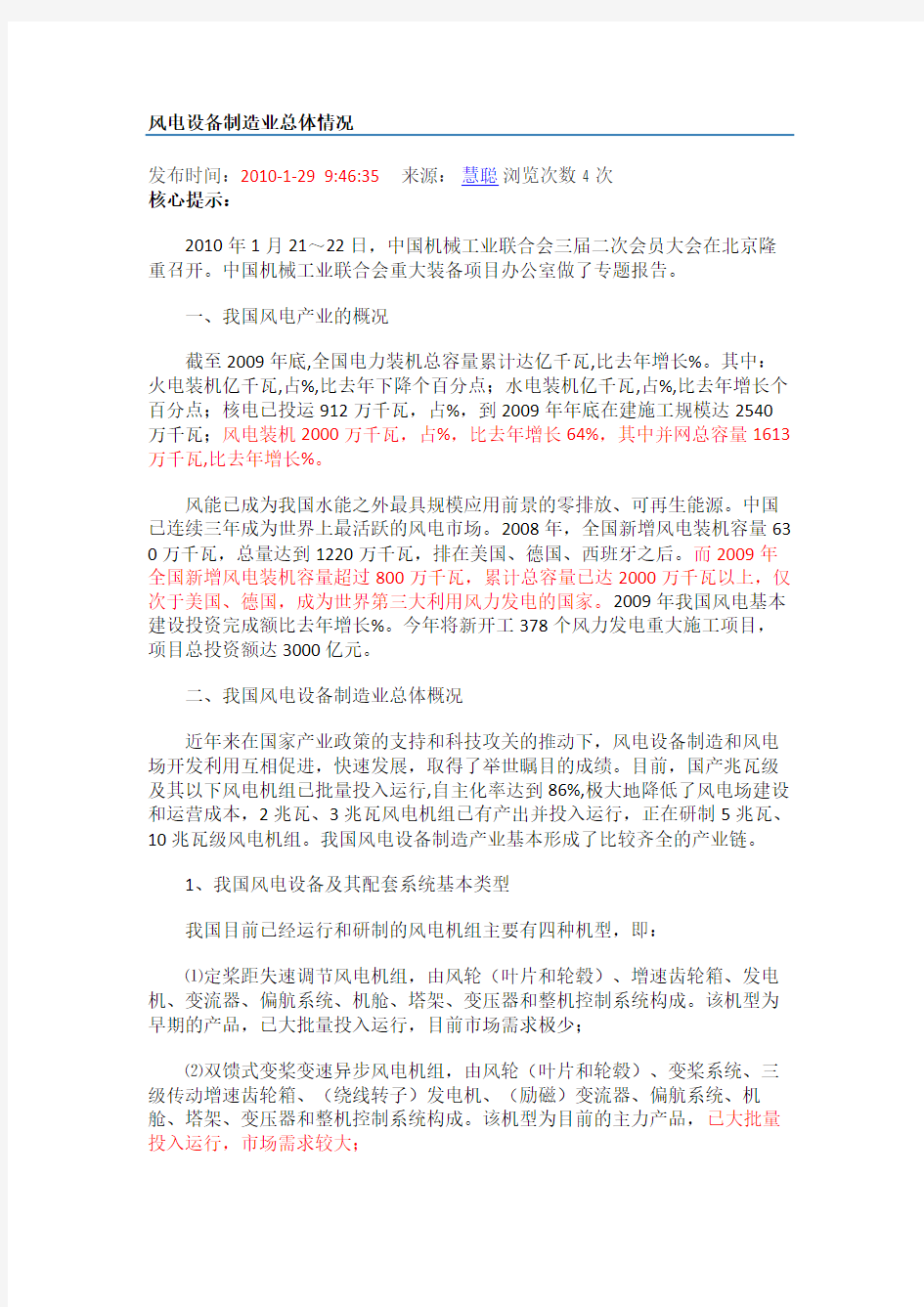
风电设备状况-CAL-FENGHAI-(2020YEAR-YICAI)_JINGBIAN
风电设备制造业总体情况
发布时间:2010-1-29 9:46:35来源:慧聪浏览次数 4 次
核心提示:
2010年1月21~22日,中国机械工业联合会三届二次会员大会在北京隆重召开。中国机械工业联合会重大装备项目办公室做了专题报告。
一、我国风电产业的概况
截至2009年底,全国电力装机总容量累计达亿千瓦,比去年增长%。其中:火电装机亿千瓦,占%,比去年下降个百分点;水电装机亿千瓦,占%,比去年增长个百分点;核电已投运912万千瓦,占%,到2009年年底在建施工规模达2540万千瓦;风电装机2000万千瓦,占%,比去年增长64%,其中并网总容量1613万千瓦,比去年增长%。
风能已成为我国水能之外最具规模应用前景的零排放、可再生能源。中国已连续三年成为世界上最活跃的风电市场。2008年,全国新增风电装机容量63 0万千瓦,总量达到1220万千瓦,排在美国、德国、西班牙之后。而2009年全国新增风电装机容量超过800万千瓦,累计总容量已达2000万千瓦以上,仅次于美国、德国,成为世界第三大利用风力发电的国家。2009年我国风电基本建设投资完成额比去年增长%。今年将新开工378个风力发电重大施工项目,项目总投资额达3000亿元。
二、我国风电设备制造业总体概况
近年来在国家产业政策的支持和科技攻关的推动下,风电设备制造和风电场开发利用互相促进,快速发展,取得了举世瞩目的成绩。目前,国产兆瓦级及其以下风电机组已批量投入运行,自主化率达到86%,极大地降低了风电场建设和运营成本,2兆瓦、3兆瓦风电机组已有产出并投入运行,正在研制5兆瓦、10兆瓦级风电机组。我国风电设备制造产业基本形成了比较齐全的产业链。
1、我国风电设备及其配套系统基本类型
我国目前已经运行和研制的风电机组主要有四种机型,即:
⑴定桨距失速调节风电机组,由风轮(叶片和轮毂)、增速齿轮箱、发电机、变流器、偏航系统、机舱、塔架、变压器和整机控制系统构成。该机型为早期的产品,已大批量投入运行,目前市场需求极少;
⑵双馈式变桨变速异步风电机组,由风轮(叶片和轮毂)、变桨系统、三级传动增速齿轮箱、(绕线转子)发电机、(励磁)变流器、偏航系统、机舱、塔架、变压器和整机控制系统构成。该机型为目前的主力产品,已大批量投入运行,市场需求较大;
⑶永磁直驱式变桨变速风电机组,由风轮(叶片和轮毂)、变桨系统、低速永磁同步发电机、全功率变流器、偏航系统、机舱、塔架、变压器和整机控制系统构成。该机型为目前的新产品,已批量投入运行,市场前景看好;
2、我国风电机组整机制造业的发展情况
到2009年底,全国已有83家企业进入并网风力发电机组整机制造行业。其中国有或国有控股公司39家,民营公司25家,合资公司9家,外商独资公司10家。上述公司按照风电机组生产能力与资产性质,大致可分为以下五种类型:
第一类:已具备大批量制造风电机组生产能力的企业。目前有3家,他们是:东方汽轮机有限公司、华锐风电科技有限公司、新疆金风科技股份有限公司。这三家企业已经年产数千台兆瓦级风电机组。
第二类:已具备一定批量制造风电机组生产能力的企业。目前有10家,他们是:广东明阳风电技术有限公司、湖南湘电风能有限公司、浙江运达风力发电工程有限公司、上海电气风电设备有限公司、江苏新誉风力发电设备有限公司、北重汽轮电机、江阴远景能源科技有限公司、国电联合动力技术有限公司、沈阳华创风能有限公司、南通航天万源安讯能风电设备制造有限公司。这些企业已经年产数百台兆瓦级风电机组。
第三类:已具备小批量制造风电机组生产能力的企业。目前有8家,他们是:重庆海装科技发展有限公司、浙江华仪风电有限公司、株洲南车风电公司、瑞能北方风电设备有限公司、汉维风力发电成套设备(大庆)有限公司、宁夏银星能源股份有限公司、保定惠德风电工程有限公司、保定天威风电科技有限公司等。这些企业已经年产数十台兆瓦级风电机组。
第四类:正在进行样机试制或试验,产业化工作有待进一步落实的风电机组制造企业。目前有59家,包括上海万德风力发电股份有限公司、无锡宝南机器制造有限公司、江西麦德风电公司、潍坊瑞奇能风电公司等。这些企业尚未向市场小批量供应兆瓦级风电机组。
第五类:具有成熟的设计制造技术,已具备在中国大批量制造风电机组生产能力的国外独资企业。目前有5家,他们是:丹麦维斯塔斯风力发电设备(中国)有限公司、西班牙歌美飒风电(天津)有限公司、美国通用电气能源(沈阳)有限公司、Nordex(天津)、印度苏司兰能源(天津)有限公司。
3、我国风电机组配套设备的发展情况
随着国内风电市场需求的扩大,风电机组关键部件配套生产企业有了较快的发展,风电设备制造和配套部件专业化产业链正逐步形成。其中:
⑴叶片:国内已有80多家制造企业,其中已经大批量生产的企业有:中航(保定)惠腾风电设备有限公司、连云港中复连众复合材料集团、天津LM公
司、中能风电设备有限公司、上海玻璃钢研究院、北京玻璃钢研究院等企业。目前,国产风电机组叶片从制造能力上已经完全能够满足甚至超出了国内风电产业发展的需要。但在研发设计技术上,基本上要依托国外有关公司。
⑵发电机:国内已有近10家制造企业,主要有:永济电机厂有限公司、兰州电机有限责任公司、上海电机厂有限公司、株洲南车电机股份有限公司、湘潭电机有限公司、大连天元电机公司、四川东风电机等,已基本能够满足国内风电产业发展的需要。
⑶齿轮箱:主要制造企业有:南京高精齿轮股份有限公司、重庆齿轮箱有限责任公司、杭州前进风电齿轮箱有限公司、大连重工起重集团、中国第二重型机械集团公司等,目前基本能满足国内风电产业发展的需要。但由于齿轮箱的配套轴承质量要求较高,目前国内尚无法提供合格的产品,齿轮箱产能受国外轴承供应的影响较大。
⑷轴承:风电机组配套有主轴轴承、齿轮箱轴承、发电机轴承、变桨轴承和偏航轴承,我国目前生产的主要是交流发电机轴承、变桨轴承和偏航轴承。制造企业有:洛阳轴承集团技术中心有限公司、瓦房店轴承集团有限责任公司、浙江天马轴承厂和徐州罗特艾德回转支承有限公司等。这些公司也在试生产主轴轴承、齿轮箱轴承,产品正处于运行考核阶段。目前,中国大部分风电机组制造公司还不得不从国外进口上述轴承,但靠进口供货周期较长且价格高,目前是制约中国风电机组产能发展的瓶颈之一。
⑸变流器和整机控制系统:目前主要的制造企业有:北京科诺伟业能源科技有限公司、合肥阳光电源有限公司、金风科技公司、北京清能华福风电技术有限公司等10多家企业。定桨距失速调节风电机组所需的变流器和整机控制系统已经全部国产化。双馈式变桨变速风电机组和永磁直驱风电机组的国产变流器和整机控制系统目前处于试应用或示范考核阶段,尚不能完全满足国内风电产业发展的需要,国内市场上需求的大部分变流器和整机控制系统仍需进口。
⑹塔筒、轮毂、机舱、机舱罩等部件的制造企业较多,已经完全能够满足国内风电产业发展的需要。
三、我国风电设备制造业存在的主要问题与制约因素
1、我国风电机组成套设计及风机设计技术尚未实现自主化
目前,我国风电设备制造企业通过引进技术、消化吸收,已基本掌握了风电设备的制造技术,已经成为世界上的风电设备制造大国,但风电机组整体设计及风机设计技术至今仍然是企业的薄弱环节,国内企业的设计技术来源主要有以下六种方式:
⑴购买国外公司风电机组生产许可证,经过对引进技术的消化吸收进行生产;
⑵与国外公司合资,按国外公司提供的技术进行生产;
⑶与国外设计咨询公司联合开发设计;
⑷请国外设计咨询公司对国内自行设计的风力发电机组进行评审和修改;
⑸参照国外产品和技术,国内自主研究开发的风力发电机组;
⑹在引进技术、消化吸收的基础上,跟踪国际上技术发展的趋势,进行再创新,自主研究开发的风力发电机组。
目前这是较快较好的一种方式,可以在短时间内实现企业较高水平的技术跨越,提高研究和开发的能力。
风电机组是一种技术密集型产品,它涉及到气象学、环境科学、空气动力学、结构动力学、材料科学、计算机与自动化控制技术、机电工程、电力电子等多种学科。目前,我国已商业化生产的风电机组,基本上都是在引进技术、消化吸收的基础上、通过部分自制加外部采购关键零部件,进行整机组装而实现批量化生产。自主创新还局限在国产材料的选用、局部工艺的改进等方面。在发展的模式上,新机型开发基本采用与国外公司联合的方式,合作开发过程中仍然以国外设计机构为主,尚未完全形成我们自己的设计理念和方法。我国的风电设备制造企业与研发机构中,严重缺乏系统掌握风电理论并具有风电机组设计实践经验的复合型人才。总之,兆瓦级以上风电机组的整体设计能力还很薄弱,很大程度上仍依赖于技术跟踪,未能形成具有国际先进水平的自主研发能力和自主知识产权,基本上只是扮演着国际成熟机型制造商的角色。因此,从总体上来看,我国风电设备制造业尚处于从“引进技术、消化吸收”阶段,转向“自主创新”阶段的过渡过程中。
2、我国风电设备关键部件设计制造技术的现状及问题
我国风电机组的技术落后于国际先进水平,不仅是机组的成套设计,也包括部分关键零部件。国外风电设备企业经过多年发展已经形成完整的产业链,风电设备零部件配套选择多且水平较高,但是国内的大规模风电设备制造起步时间不长,主要的零配件的技术水平和产品质量还存在一定差距。特别要指出的是:主轴轴承、齿轮箱轴承、是风电机组的关键零件。风机、变流器和整机控制系统是风电机组中技术含量最高的关键部件。对于这些产品的设计制造技术,我国还没有完全掌握,尚处在研制、小批量试用阶段。
四、加强技术创新、提高质量水平、为我国风电产业发展做贡献
尽管我国风电产业发展所取得的成绩很大,但必须要看到,目前我们的风电设备行业依然存在着技术上自主创新能力不强、产品的技术水平和质量水平不高、标准检测认证体系不健全等问题。同时,出现了投资过热、重复引进和低水平重复建设的现象。
经过改革开放30多年的经验表明,关键的核心技术是引进不来的,起步的阶段依靠引进技术是可以的,深层次的发展一定要建立在自主研发、自主创新的基础上。
从风电场建设和管理部门反映,国产风电机组质量欠佳的问题越来越成为突出问题。有的厂家积极消化吸收引进技术,注重产品质量,讲究企业信誉。但也有的厂家拿来技术未经消化,囫囵吞枣,就进行大批量生产。有的引进技术本身就不成熟,粗制滥造,流入市场,造成了许多麻烦和事故隐患,企业信誉和经济也蒙受损失。投入运行的国产机组多次出现大的质量和技术故障,如叶片断裂、轮毂裂纹、主轴问题、轴承问题、齿轮箱故障、电机故障等等。由于设备质量欠佳,造成风电场可利用率不高。采用国产机组的风电场,其机组可利用率明显低于采用国际先进品牌的机组,粗略估算整体上要低7%左右。有的机组运行不稳定,维护又不及时,还要远远低于这个数值。用户为此要承受很大损失。还应该看到的是,真正的质量问题可能现在还没有完全表现出来。因为多数国产机组运行时间还不长,还不到设备质量故障的高发期,更大的麻烦可能还在后面,必须要引起高度的重视。
风力发电具有随机性、间歇性和反调峰等特点,而且我国风电场一般位于电网末端,电网运行电压调整十分困难。尤其是大规模风电场并网后,在电网故障或受到冲击出现电压闪变时,不具备低电压穿越功能的风电机组,在风电场没有采取保护措施的情况下,为保护机组会采取切机逃逸的方式退出运行,从而使电网要承受第二次冲击,可导致事故扩大,甚至引发电网崩溃,这已经成为影响风电机组并网最关键的技术瓶颈。另外,在内蒙古、甘肃、东北地区,由于风电装机容量大,就地消化能力弱,电力送出的瓶颈已比较明显。可以预计,相应的风电设备的市场瓶颈也即将显现,希望能引起相关企业的关注。
五、正确引导风电设备制造业的投资行为
目前,国家有关部委正在贯彻落实国务院【2009】38号和116号文的有关精神,抓紧制修定相关行业的产业结构调整指导目录、规划、产业政策、准入条件等,其中风电设备制造业已被明确列入“产能过剩,重复建设”的行业之一。目前,从风电设备整个产业链的市场销售情况来看,“过剩”与“短缺”并存。其中,整机组装和叶片生产“产能过剩、重复建设”的问题已经比较严重,整机组装的问题尤其突出。按照我国风电发展规划,未来十年平均每年新增装机约1000万千瓦,而现在风电设备制造企业的前3家企业,产能就达到了900万千瓦,如果加上其他几十家企业,机组的产能已大大超过了未来十年的实际需求。但对于风电设备的部分关键零部件如:主轴轴承、齿轮箱轴承、变流器和整机控制系统等,国内产品从技术、质量方面尚不能满足风电机组的要求,大批量从国外进口。急需相关企业加大研发和投资力度,能为风电设备行业提供高水平、高可靠性的配套产品。
至于风电机组及其关键零部件的研究实验、设计开发、质量评定和关键性技术的攻关等,则更是关系到我国风电设备制造业可持续发展的重要环节,明