贴金工艺流程简介
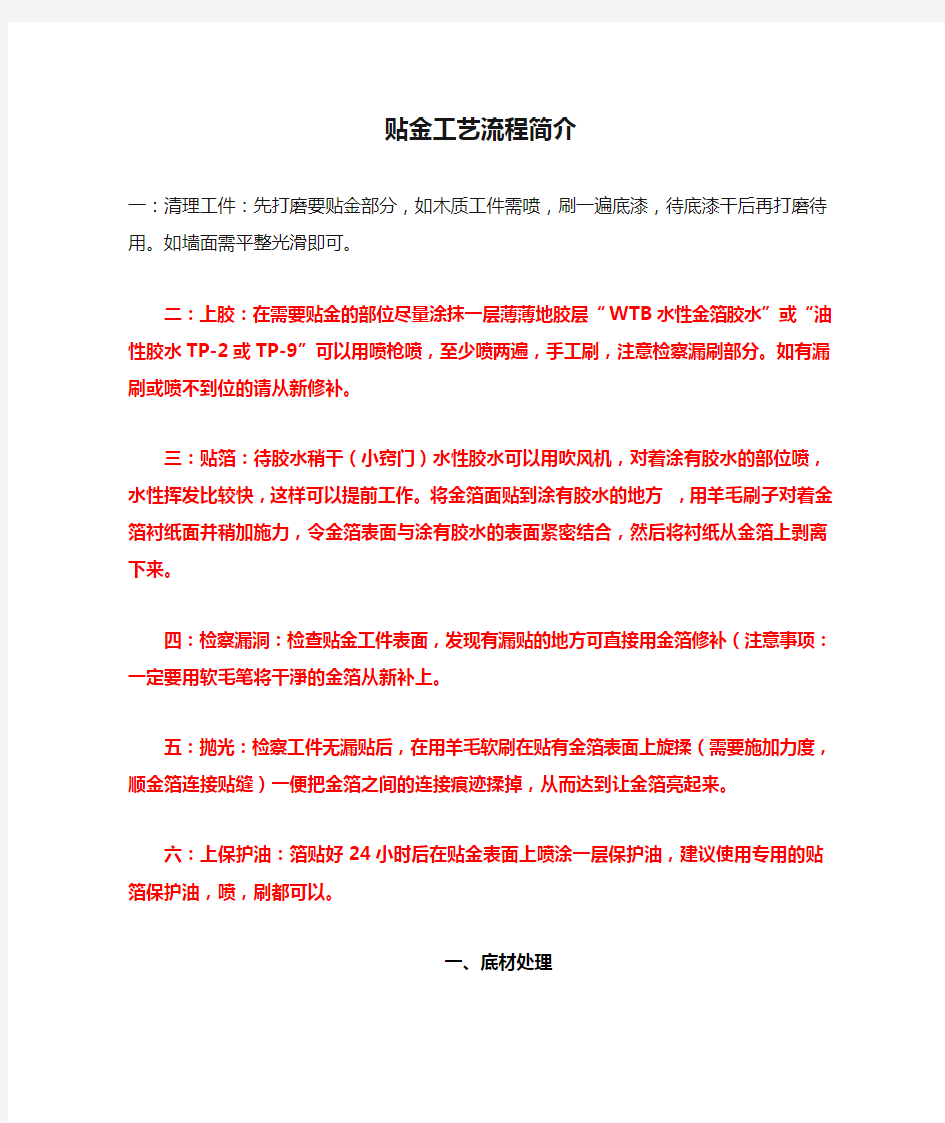
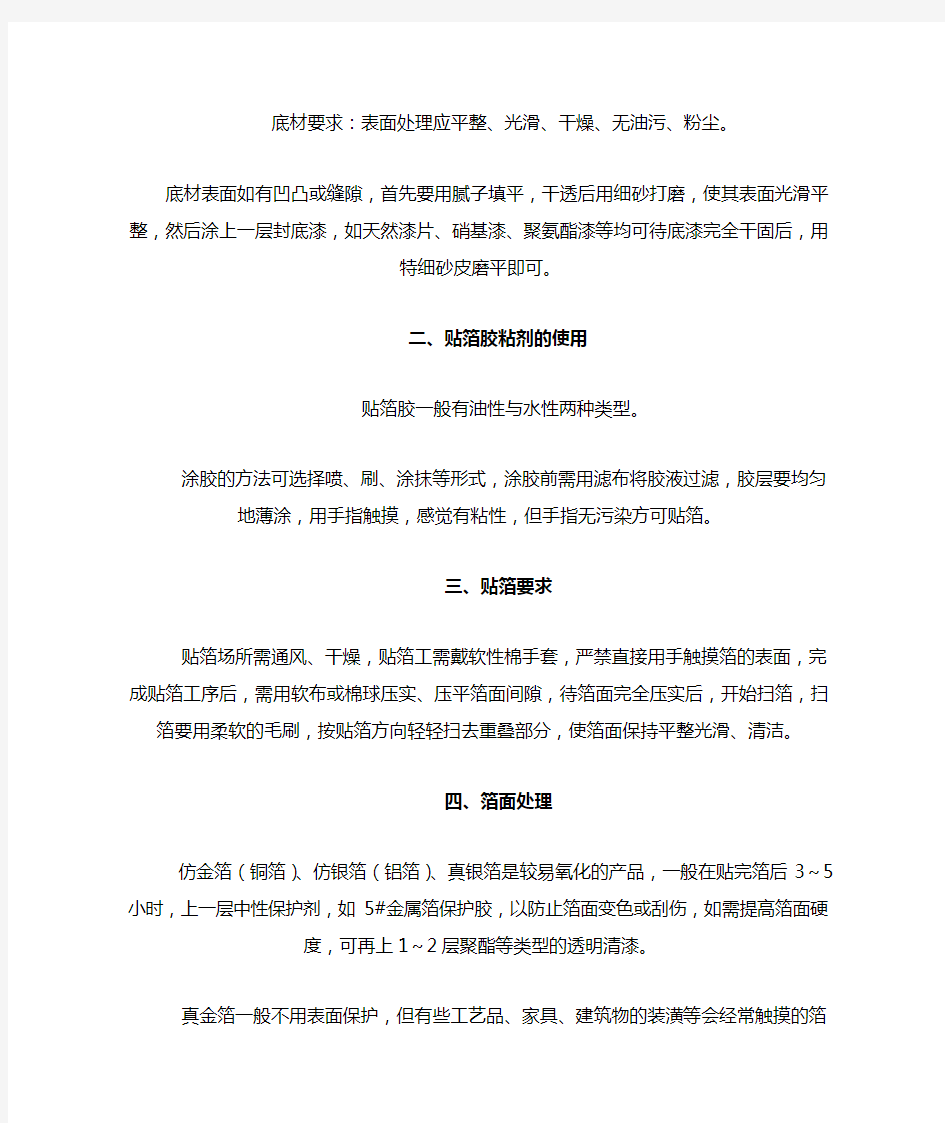
贴金工艺流程简介
一:清理工件:先打磨要贴金部分,如木质工件需喷,刷一遍底漆,待底漆干后再打磨待用。如墙面需平整光滑即可。
二:上胶:在需要贴金的部位尽量涂抹一层薄薄地胶层“WTB水性金箔胶水”或“油性胶水TP-2或TP-9”可以用喷枪喷,至少喷两遍,手工刷,注意检察漏刷部分。如有漏刷或喷不到位的请从新修补。
三:贴箔:待胶水稍干(小窍门)水性胶水可以用吹风机,对着涂有胶水的部位喷,水性挥发比较快,这样可以提前工作。将金箔面贴到涂有胶水的地方,用羊毛刷子对着金箔衬纸面并稍加施力,令金箔表面与涂有胶水的表面紧密结合,然后将衬纸从金箔上剥离下来。
四:检察漏洞:检查贴金工件表面,发现有漏贴的地方可直接用金箔修补(注意事项:一定要用软毛笔将干淨的金箔从新补上。
五:抛光:检察工件无漏贴后,在用羊毛软刷在贴有金箔表面上旋揉(需要施加力度,顺金箔连接贴缝)一便把金箔之间的连接痕迹揉掉,从而达到让金箔亮起来。
六:上保护油:箔贴好24小时后在贴金表面上喷涂一层保护油,建议使用专用的贴箔保护油,喷,刷都可以。
一、底材处理
底材要求:表面处理应平整、光滑、干燥、无油污、粉尘。底材表面如有凹凸或缝隙,首先要用腻子填平,干透后用细砂打磨,使其表面光滑平整,然后涂上一层封底漆,如天然漆片、硝基漆、聚氨酯漆等均可待底漆完全干固后,用特细砂皮磨平即可。
二、贴箔胶粘剂的使用
贴箔胶一般有油性与水性两种类型。
涂胶的方法可选择喷、刷、涂抹等形式,涂胶前需用滤布将胶液过滤,胶层要均匀地薄涂,用手指触摸,感觉有粘性,但手指无污
染方可贴箔。
三、贴箔要求
贴箔场所需通风、干燥,贴箔工需戴软性棉手套,严禁直接用手触摸箔的表面,完成贴箔工序后,需用软布或棉球压实、压平箔面间隙,待箔面完全压实后,开始扫箔,扫箔要用柔软的毛刷,按贴箔方向轻轻扫去重叠部分,使箔面保持平整光滑、清洁。
四、箔面处理
仿金箔(铜箔)、仿银箔(铝箔)、真银箔是较易氧化的产品,一般在贴完箔后3~5小时,上一层中性保护剂,如5#金属箔保护胶,以防止箔面变色或刮伤,如需提高箔面硬度,可再上1~2层聚酯等
类型的透明清漆。
真金箔一般不用表面保护,但有些工艺品、家具、建筑物的装潢等会经常触摸的箔面,可选用一种自干型的水性面漆,如WB型金箔保护剂可以提高表面的抗划伤性。
精密铸造产品流程翻译
从射蜡到沾浆制壳阶段工艺流程的英文翻译 (其他部分待完成) 低温蜡射蜡工艺规范Low temperature wax wax injection process specification 1、蜡料的配制石蜡和硬脂酸按1∶1(质量分数)进行配制,蜡料不允许混入水及其它脏物 1, 1:1 preparation of paraffin wax and stearic acid (concentration) ,formulated wax does not allow mixed with water and other dirt 2、蜡膏的配制取保温缸中的蜡水与蜡屑按1∶2(质量分数)在蜡糊搅拌机上进行充分的搅拌; 蜡糊搅拌机的温度设定在60~65℃之间,要求配制的蜡膏具有一定的流动性,手感均匀、细腻、无碎块2, Preparation of insulating cylinder of wax and wax chips by 1:2 (concentration) in fully on wax paste mixer mixing; which temperature setting are between 60~65℃, wax paste needs to has a certain degree of mobility, fine and smooth, no fragments 3、蜡样收缩率的控制压注ф100蜡样的收缩率控制在0.9~0.11%之间,要求每工作日检测一次 3, controlling shrinkage of wax: :wax injection Diameter 100millimetre ,shrinkage of wax needs to be control I between 0.9~0.11%, C heck once a day 4、蜡料温度的控制蜡料溶化缸温度设定在90±5℃,不允许超过95℃;保温缸温度控制在80±5℃;射蜡保温缸温度控制在48~50℃,射蜡嘴温度控制在54~60℃范围内。 4, material temperature control of wax,Wax melting cylinder temperature set at 90 ± 5 ° c, not exceeding 95 ° c; insulation cylinder temperature set at 80 ± 5 ℃; wax injection insulation cylinder temperature is 48~50℃,.Wax injection nozzle temperature control within the scope of 54~60℃ 6、射蜡工艺参数射蜡压力0.2~0.4Mpa,保压时间1~3分钟,根据蜡件的尺寸大小及壁厚、结构状况进行选定 6 wax injection process parameters Injection pressure 0.2~0.4Mpa, 1-3 minutes holding time, process parameters selected according to size and wall thickness and the structural condition of the wax, 7、对于具有盲孔的蜡件,为便于抽芯,允许在平厚处扎穿1~2个直径3~5mm的空洞,然后用红蜡修补上。 7, for the wax with a blind hole, for ease of extracting core, allow tie to wear 1~2 at the thick diameter 3~5mm hollow, then with red wax on the patch. 8、应经常清洁模具上各接合面,以保证蜡件的尺寸精度 8, clean the mould on the joint surface regularly, to ensure that the wax pieces size precision 9、蜡件冷却水温度控制在20~25℃之间 Wax cooling water temperature control between 20~25℃ 蜡件的检验及修补Inspection and repair of wax 1 蜡件必须逐个进行清理,修除批缝、毛刺及污物。 Wax must clear them one by one, in addition to sewing, burrs and dirt. 2、蜡件允许用红蜡进行修补,但必须保证表面的光洁度 2 Patch wax allows the use of red wax, but must ensure that the surface finish 、蜡件的几何尺寸在每班生产过程中进行抽检,但对重要尺寸要求的蜡件需100%检验。
硅溶胶精密铸造的工艺
硅溶胶精密铸造的工艺 一、蜡模制作 蜡料处理工艺操作守则 蜡料处理流程: (静置桶I中)静置脱水→(除水桶中)搅拌蒸发脱水→(静置桶II中)静置去污 1 工艺参数 静置桶I 静置温度85-90℃ 静置时间6-8h 除水桶搅拌温度110-120℃搅拌时间10-12h 静置桶II 静置温度80-85℃静置时间>12h 保温箱保温温度54±2℃保温时间>24h 2 操作程序 2.1 检查设备、温控仪表是否处于正常工作状态。 2.2 将脱蜡釜回收的旧蜡液倒入过滤槽中过滤;再送到静置桶I中,在低于90℃下静置6-8h。 2.3 静置完毕把沉淀水放掉后,将蜡液倒入除水桶中。 2.4 除水桶中的蜡液,在110-120℃保温并搅拌,使残留水分蒸发,到目视蜡液表面无泡沫为止。 2.5 将除完水的蜡液,经过<60目筛网过滤再放入<90℃的静置桶II中,保温静置12h 以上。 2.6 各除水桶、静置桶应定期性的放掉其底部的残留水和脏杂物。 2.7 把静置桶II中处理好的回收蜡液送到模头压蜡机保温桶中,用于主产模头(浇道)。 2.8 根据旧腊料性能和腊料消耗情况,不定期的在静置桶II中适量加新蜡,一般在3%-5%左右。 2.9 将合格的蜡液灌入保温箱内的蜡缸中,为减少蜡缸内蜡液中的气体,先保持一段高温时期80℃/2h后降至54℃。在54±2℃下保温24h后,方可用于压制蜡模。 3 注意事项 3.1除水桶,静置桶均应及时排水、排污。
3.2经常检查各设备温控仪表的工作状况,防止失控,尤其应防止温度过高造成蜡料老化。 3.3每月检查一次蜡处理设备各导热油的液面位置,油面应距设备顶面200㎜左右,防止油溢出。并注意检查设备有无渗油现象。 3.4经常检查环境状态,避免灰尘及外来物混入蜡料中。 压制蜡模工艺操作守则 1 工艺要求 室温24±3℃ 蜡缸温度54±2℃(大件应根据工艺要求设定) 射蜡嘴温度57-64℃ 压射压力 4.2Mpa(42kgf/cm2) 保压时间5-15s 冷却水温度<10℃ 2 操作规程 2.1 检查压蜡机油压、保温温度、操作按钮等是否正常。按照技术规定调整压蜡机压射压力、射蜡嘴温度、保压时间、冷却时间等。 2.2从保温箱中取出蜡缸,装在压蜡机上,放出上部混有空气的蜡料。 2.3 将模具放在压蜡机工作台面上,调整射蜡嘴使之与模具注蜡口高度一致,检查模具所有芯子活块位置是否正确,模具开合是否顺利。 2.4打开模具,喷上微薄一层分型剂。合型,对准射蜡嘴。 2.5双手按动工作按钮,压制蜡模。 2.6抽出芯子,打开模具,小心取出蜡模。按要求放入冷却水中或放入存放盘中冷却。并检查有下列缺陷的蜡模应报废: (1)有严重气泡的蜡模;(2)棱角不清晰的蜡模; (3)变形不能修复的蜡模;(4)尺寸不符号规定的蜡模。 2.7清除模具上残留的蜡料,注意只能用压缩空气吹净模具分型面、芯子上的蜡屑、脱模剂,不准用金属刀具去铲刮型腔、抽芯。慎防损害模具型腔部位。 2.8按以上各条进行下一次压制蜡模,以后往复循环生产。 2.9及时将蜡模从冷却水中轻轻取出,用压缩空气吹净蜡屑及水珠,并进行自检,将合格蜡模正确放入存放盘中。 2.10每班下班或模具当班生产完毕后,应用软布等清理模具。如发现模具有损伤应立即报告领班,由领班处理。并清扫压蜡机、工具及现场,做到清洁、整齐。 3 注意事项 3.1压制蜡模时,首先必须进行首件检查,确认合格后,方可进行操作。压制过程中不能轻易变动压制参数。 3.2使用新的模具时,务必弄清模具组装、拆卸顺序,蜡模取出方法。 3.3蜡模存放时,应注意搁置方向,防止变形。需要时可采取卡具等措施,以避免蜡模变形。
炼钢生产流程详细讲解
钢铁生产工艺主要包括:炼铁、炼钢、轧钢等流程。 (1)炼铁:就是把烧结矿和块矿中的铁还原出来的过程。焦炭、烧结矿、块矿连同少量的石灰石、一起送入高炉中冶炼成液态生铁(铁水),然后送往炼钢厂作为炼钢的原料。 (2)炼钢:是把原料(铁水和废钢等)里过多的碳及硫、磷等杂质去掉并加入适量的合金成分。 (3)连铸:将钢水经中间罐连续注入用水冷却的结晶器里,凝成坯壳后,从结晶器以稳定的速度拉出,再经喷水冷却,待全部凝固后,切成指定长度的连铸坯。 (4)轧钢:连铸出来的钢锭和连铸坯以热轧方式在不同的轧钢机轧制成各类钢材,形成产品。 炼钢工艺总流程图
炼焦生产流程:炼业是将焦煤经混合,破碎后加入炼焦炉经干馏后产生热焦碳及粗焦炉气之制程。
烧结生产流程:烧结作业系将粉铁矿,各类助熔剂及细焦炭经由混拌、造粒后,经由布料系统加入烧结机,由点火炉点燃细焦炭,经由抽气风车抽风完成烧结反应,高热之烧结矿经破碎冷却、筛选后,送往高炉作为冶炼铁水之主要原料。 高炉生产流程:高炉作业是将铁矿石、焦炭及助熔剂由高炉顶部加入炉,再由炉下部鼓风嘴鼓入高温热风,产生还原气体,还原铁矿石,产生熔融铁水与熔渣之炼铁制程。
转炉生产流程:炼钢厂先将熔铣送前处理站作脱硫脱磷处理,经转炉吹炼后,再依订单钢种特性及品质需求,送二次精炼处理站(RH真空脱气处理站、Ladle Injection盛桶吹射处理站、VOD真空吹氧脱碳处理站、STN搅拌站等)进行各种处理,调整钢液成份,最后送大钢胚及扁钢胚连续铸造机,浇铸成红热钢胚半成品,经检验、研磨或烧除表面缺陷,或直接送下游轧制成条钢、线材、钢板、钢卷及钢片等成品。 连铸生产流程:连续铸造作业乃是将钢液转变成钢胚之过程。上游处理完成之钢液,以盛钢桶运送到转台,经由钢液分配器分成数股,分别注入特定形状之铸模,开始冷却凝固成形,生成外为凝固壳、为钢液之铸胚,接着铸胚被引拔到弧状铸道中,经二次冷却继续凝固到完全凝固。经矫直后再依订单长度切割成块,方块形即为大钢胚,板状形即为扁钢胚。此半成品视需要经钢胚表面处理后,再送轧钢厂轧延.
铸造工艺标准经过流程介绍
铸造生产的工艺流程 铸造生产是一个复杂的多工序组合的工艺过程,它包括以下主要工序: 1)生产工艺准备,根据要生产的零件图、生产批量和交货期限,制定生产工艺方案和工艺文件,绘制铸造工艺图; 2)生产准备,包括准备熔化用材料、造型制芯用材料和模样、芯盒、砂箱等工艺装备; 3)造型与制芯; 4)熔化与浇注; 5)落砂清理与铸件检验等主要工序。 成形原理 铸造生产是将金属加热熔化,使其具有流动性,然后浇入到具有一定形状的铸型型腔中,在重力或外力(压力、离心力、电磁力等)的作用下充满型腔,冷却并凝固成铸件(或零件)的一种金属成形方法。 图1 铸造成形过程
铸件一般作为毛坯经切削加工成为零件。但也有许多铸件无需切削加工就能满足零件的设计精度和表面粗糙度要求,直接作为零件使用。 型砂的性能及组成 1、型砂的性能型砂(含芯砂)的主要性能要求有强度、透气性、耐火度、退让性、流动性、紧实率和溃散性等。 2、型砂的组成型砂由原砂、粘接剂和附加物组成。铸造用原砂要求含泥量少、颗粒均匀、形状为圆形和多角形的海砂、河砂或山砂等。铸造用粘接剂有粘土(普通粘土和膨润土)、水玻璃砂、树脂、合脂油和植物油等,分别称为粘土砂,水玻璃砂、树脂砂、合脂油砂和植物油砂等。为了进一步提高型(芯)砂的某些性能,往往要在型(芯)砂中加入一些附加物,如煤份、锯末、纸浆等。型砂结构,如图 2 所示 图2 型砂结构示意图 工艺特点 铸造是生产零件毛坯的主要方法之一,尤其对于有些脆性金属或合金材料(如各种铸铁件、有色合金铸件等)的零件毛坯,铸造几乎是唯一的加工方法。与其它加工方法相比,铸造工艺具有以下特点: 1)铸件可以不受金属材料、尺寸大小和重量的限制。铸件材料可以是各种铸铁、铸钢、铝合金、铜合金、镁合金、钛合金、锌合金和各种特殊合金材料;铸件可以小至几克,大到数百吨;铸件壁厚可以从0.5 毫米到1 米左右;铸件长度可以从几毫米到十几米。 2)铸造可以生产各种形状复杂的毛坯,特别适用于生产具有复杂内腔的零件毛坯,如各种箱体、缸体、叶片、叶轮等。 3)铸件的形状和大小可以与零件很接近,既节约金属材料,又省切削加工工时。 4)铸件一般使用的原材料来源广、铸件成本低。 5)铸造工艺灵活,生产率高,既可以手工生产,也可以机械化生产。 铸件的手工造型手工造型的主要方法砂型铸造分为手工造型(制芯)和机器造型(制芯)。手工造型是指造型和制芯的主要工作均由手工完成;机器造型是指主要的造型工作,包括填砂、紧实、起模、合箱等由造型机完成。泊头铸造工量具友介绍手工造型的主要方法:手工造型因其操作灵活、适应性强,工艺装备简单,无需造型设备等特点,被广泛应用于单件小批量生产。但手工造型生产率低,劳动强度较大。手工造型的方法很多,常用的有以下几种: 1.整模造型 对于形状简单,端部为平面且又是最大截面的铸件应采用整模造型。整模造型操作简便,造型时整个模样全部置于一个砂箱内,不会出现错箱缺陷。整模造型适用于形状简单、最大截面在端部的铸件,
熔模铸造工艺流程-图文.
熔模铸造工艺流程 模具制造 制溶模及浇注系 统 模料处理 模组焊接 模组清洗 上涂料及撒砂 涂料制备 重
复 型壳干燥(硬化 多 次 脱蜡 型壳焙烧 浇注 熔炼 切 割 浇 口 抛 光 或 机
工 钝化 修整焊补 热处理 最后清砂 喷丸或喷砂 磨内
口 震 动 脱 壳 模料 制熔模用模料为日本牌号:K512模料 模料主要性能: 灰分≤0.025% 铁含量灰分的10% ≤0.0025% 熔点 83℃-88℃(环球法)60℃±1℃ 针入度 100GM(25℃)3.5-5.0DMM 450GM(25℃)14.0-18.0DMM 收缩率 0.9%-1.1% 比重 0.94-0.99g/cm3 颜色新蜡——兰色、深黄色 旧蜡——绿色、棕色
蜡(模)料处理 工艺参数: 除水桶搅拌时温度 110-120℃ 搅拌时间 8-12小时 静置时温度 100-110℃ 静置时间 6-8小时 静置桶静置温度 70-85℃ 静置时间 8-12小时 保温箱温度 48-52℃ 时间 8-24小时 二、操作程序 1、从脱蜡釜泄出的旧蜡用泵或手工送到除水桶中,先在105-110℃下置6-8小时沉淀,将水分泄掉。 2、蜡料在110-120℃下搅拌8-12小时,去除水份。 3、将脱完水的蜡料送到70-85℃的静置桶中保温静置桶中保温静置8-12小时。 4、也可将少量新蜡加入静置桶中,静置后清洁的蜡料用手工灌到保温箱蜡缸中,保温温度48-52℃,保温时间8-24小时后用于制蜡模。
5、或把静置桶中的回收蜡料输入到气动蜡模压注机的蜡桶中,保温后压制浇道。 三、操用要点 1、严格按回收工艺进行蜡料处理。 2、除水桶、静置桶均应及时排水、排污。 3、往蜡缸灌蜡时,蜡应慢没缸壁流入,防止蜡液中进入空气的灰尘。 4、蜡缸灌满后应及时盖住,避免灰尘等杂物落入。 5、经常检查每一个桶温,防止温度过高现象发生。 6、作业场地要保持清洁。 7、防止蜡液飞溅。 8、严禁焰火,慎防火灾。 压制蜡(熔)模 一、工艺参数 室温20-24℃压射蜡温50-55℃ 压射压力0.2-0.5Mpa 保压时间10-20S 冷却水温度15±3℃ 二、操作程序
纺织生产工艺流程
我国纺织工业发展简介 “衣、食、住、行”是人类永久的需求。“衣”不单纯指衣服,它几乎可以涵盖所有纺织产品。“衣”人类永久的需要,具有广阔的市场。 从世界范围来看,纺织服装业销售额仅次于旅游业和信息产业,名列第三。它在世界经济中承担着极为重要的作用。它不仅满足人们生活的基本需要,而且是社会文化的时尚代言者和经济兴衰的晴雨表,它既是最传统的也是最时尚的产业,受到各国政府的重视。 纺织工业是我国国民经济的传统支柱产业和重要的民生产业,也是国际竞争优势明显的产业,对扩大就业、积累资金、出口创汇、带动相关产业和促进区域经济发展发挥了重要作用,所以纺织工业健康平稳发展,事关国计民生和社会稳定大局。 我国是世界上最大的纺织品生产及出口国。纺织工业曾经提出建设纺织大国的奋斗目标,如今我国的纺织业正在全面实现产业升级,逐步开始向纺织强国转变。 我国纺织品服装出口额: 2000年--- 520.8亿美元 2004年--- 931.0亿美元 2009年--- 1713.32亿美元 2010年---2065.30亿美元 织物的形成 织物的分类 织物(Fabric) ——由纺织纤维和纱线制成的柔软而具有一定力学性质和厚度的制品。 包括:机织物、针织物、非织造布、编织物等 一、织物的分类: 1.机织物:由相互垂直排列的二个系统的纱线,在织机上按一定规律交织成的制品。 2.针织物:是由纱线串套而成,线圈则是针织物的最小基本单元。 3.非织造织物:是一种由纤维层构成的纺织品。经机械或化学加工而成的制品。 4.编织物:由纱线通过用结节互相连接或钩连而成的制品,如网、花边等。 二、机织物的分类 1、按原料分类: (1)纯纺织物:经纬纱为同一种纤维的纱织布。 (2)混纺织物:二种或二种以上纤维混纺纱织布。 (3)交织织物:经纱与纬纱为不同类型纱线。 2、按织物用途分类 (1)服装用织物:外衣、内衣 (2)卫生用织物:毛巾、浴巾、枕巾…… (3)装饰用织物:窗帘、床罩、沙发罩…… (4)工业用织物:帆布、水龙带、帘子布…… 3、按织物组织分类: (1)基本组织织物:三原组织 (2)复杂组织织物:毛巾、灯芯绒、水龙带等 (3)小花纹组织织物:在基本组织基础上变化 (4)大花纹组织织物:装饰类家用纺织品
炼钢连铸工艺流程介绍
连铸工艺流程介绍 将高温钢水浇注到一个个的钢锭模内,而是将高温钢水连续不断地浇到一个或几个用强制水冷带有“活底”(叫引锭头)的铜模内(叫结晶器),钢水很快与“活底”凝结在一起,待钢水凝固成一定厚度的坯壳后,就从铜模的下端拉出“活底”,这样已凝固成一定厚度的铸坯就会连续地从水冷结晶器内被拉出来,在二次冷却区继续喷水冷却。带有液芯的铸坯,一边走一边凝固,直到完全凝固。待铸坯完全凝固后,用氧气切割机或剪切机把铸坯切成一定尺寸的钢坯。这种把高温钢水直接浇注成钢坯的新工艺,就叫连续铸钢。
【导读】:转炉生产出来的钢水经过精炼炉精炼以后,需要将钢水铸造成不同类型、不同规格的钢坯。连铸工段就是将精炼后的钢水连续铸造成钢坯的生产工序,主要设备包括回转台、中间包,结晶器、拉矫机等。本专题将详细介绍转炉(以及电炉)炼钢生产的工艺流程,主要工艺设备的工作原理以及控制要求等信息。由于时间的仓促和编辑水平有限,专题中难免出现遗漏或错误的地方,欢迎大家补充指正。? 连铸的目的: 将钢水铸造成钢坯。?将装有精炼好钢水的钢包运至回转台,回转台转动到浇注位置后,将钢水注入中间包,中间包再由水口将钢水分配到各个结晶器中去。结晶器是连铸机的核心设备之一,它使铸件成形并迅速凝固结晶。拉矫机与结晶振动装置共同作用,将结晶器内的铸件拉出,经冷却、电磁搅拌后,切割成一定长度的板坯。?连铸钢水的准备 一、连铸钢水的温度要求: 钢水温度过高的危害:①出结晶器坯壳薄,容易漏钢;②耐火材料侵蚀加快,易导致铸流失控,降低浇铸安全性;③增加非金属夹杂,影响板坯内在质量;④铸坯柱状晶发达;⑤中心偏析加重,易产生中心线裂纹。 钢水温度过低的危害:①容易发生水口堵塞,浇铸中断;②连铸表面容易产生结疱、夹渣、裂纹等缺陷; ③非金属夹杂不易上浮,影响铸坯内在质量。 二、钢水在钢包中的温度控制: 根据冶炼钢种严格控制出钢温度,使其在较窄的范围内变化;其次,要最大限度地减少从出钢、钢包中、钢包运送途中及进入中间包的整个过程中的温降。 实际生产中需采取在钢包内调整钢水温度的措施: 1)钢包吹氩调温 2)加废钢调温 3)在钢包中加热钢水技术 4)钢水包的保温 中间包钢水温度的控制
炼铁炼钢工艺流程
1.3 企业基本情况 新绛县祥益工贸有限公司根据山西省发展和改革委员会(晋发改备案【2007】146号)批文,建设450m3高炉,并配套建设90m3带式烧结机等。 新绛县祥益工贸有限公司位于运城市新绛县煤化工业园区,厂址距新绛县城10km,距离同蒲铁路侯马北货站10km,距大运高速公路出口2.5km,距晋韩高速公路出口3km,交通运输十分便利,地理位置非常优越。 新绛县祥益工贸有限公司占地面积约28万m2,目前拥有职工600余人,其中中层管理人员20人,各类专业技术人员40余人(其中高级技术人员3人,中级技术人员20人),职工队伍稳定,职工素质普遍提高。公司紧紧依托当地丰富的矿产资源优势,艰苦创业,我稳步发展。 新绛县祥益工贸有限公司始终坚持质量第一、信誉为本的宗旨,依靠全体员工团结拼搏、积极开拓、艰苦创业、自强不息的努力,企业迅速发展壮大,为新绛县经济发展做出贡献。 1.4 高炉生产工艺简述 高炉冶炼用的焦炭、含铁原料、溶剂在原料厂和烧结厂加工处理合格后,用皮带机运至料仓贮存使用。 各种炉料在仓下经二次筛分、计量后,按程序由仓下皮带机送到高炉料坑,由料车将炉料至炉顶加入炉内进行冶炼。 高炉冶炼的热源主要来源于焦炭和煤粉的燃烧。各种原料在炉内进行复杂的理化反应,炉内承受着高温高压作用。为此,高炉内要砌耐火材料,并在高温区和重要部位设冷却壁,确保高炉安全生产。 高炉冶炼用风由鼓风机站供给,冷风以热风炉加热后送入高炉。 高炉冶炼主要产品是生铁,副产品为煤气、炉渣、炉尘等。 高炉的铁水用铁水罐拉至铸铁机进行铸铁,或用汽车将铁水罐直接送至铸铁机进行铸铁,或用汽车将铁水罐直接送至炼钢厂进行炼钢。 高炉煤气经除尘、净化后一部分供热风炉烧炉,余下部分供烧结机、喷煤和6000kw发电机组。 高炉炉渣在炉前进行水冲渣,水渣送至建材厂制砖,或送至水泥厂作为制作水泥的原料。 高炉产生的各种原料、重力除尘拉到烧结厂进行配料烧结,煤气除尘的布袋拉到建材厂进行综合利用。 高炉生产工艺流程见图二。 1.6烧结生产工艺简述 90m3烧结机主要包括烧结机及相应配套的原料系统、配料系统、混料系统、破碎、筛分系统、鼓风冷却系统、成品贮存系统以及供风、供水、供电等辅助设施。 该工程主要由生产设施、辅助设施和生活设施三大部分组成,其中生活设施由建设单位同意考虑,故本设计只考虑生产设施和辅助设施。 生产设施包括原料及配料系统,主烧结室、带冷几室、风机房、烟卤,一混合室、二混合室、成品中间仓等。 辅助设施包括原料及配料系统除尘及配套风机,机头除尘室及配套风机、烟卤,机尾布袋出尘室及配套风机、变配电室、水泵房等。 生产设施的总图布置为带冷机室在、主烧结室东西方向布置,除尘室的南侧。原料上料及配料系统布置在主烧机室的东侧,一混合室、二混合室布置在主烧机室的南侧。成品中间仓布置在带冷机室的南侧,距高炉储矿槽100余米,由成品皮带将成品烧结矿送至高炉储矿槽上。 烧结生产工艺流程见图三。 1.8 高炉喷煤生产工艺简述 高炉喷煤配套工程,是节约焦炭、降低高炉炼铁生产成本的重要措施。自从六十年代我国鞍钢、首钢高炉喷煤会的成功以来很快在国内普遍推广应用,并且高炉喷煤在工艺及其相关技术得到了迅速发展。尤其是近几年发展的富氧大喷煤技术(宝钢喷煤煤比打达到≥200kg/Tfe水平)给高炉生产注入县的生机。国内炼铁生产规模不断扩大与高炉生产效率的提高,对焦炭需求量业日趋增加,由于国内
水玻璃法精密铸造工艺规程
水玻璃氯化铵法精密铸造工艺规程 1.目的为了便于操作者熟悉和掌握水玻璃法精密铸造的工艺特点、技术特 性,更好的在生产中加以应用,生产出优质的产品,特制定本规程。 2.适用范围本工艺规程适用于从蜡模配制到模壳浇注的全过程。 3.职责 3.1 技术部是本规程的制定和归口部门。 3.2 各工序工作人员均应按此规程进行操作。 4.工艺规程 4.1 制作蜡模 4.1.1 压制蜡模的模具应符合产品的图纸要求,经检验合格后使用。 4.1.2 蜡料应按石蜡:硬脂酸1:1进行配料,融化后加蜡屑机械搅拌成 糊状,加入压蜡机内往模具中注蜡。 4.1.3 蜡型要在模具中保压冷却才可取模,并及时对变形蜡模进行校 正,放入冷水冷却,待完全冷却后方可进行取出毛刺、修整等工 作。 4.1.4 修整好的蜡模经检验合格后,清洗表面油脂,方可与浇冒口组焊。 4.1.5 组焊好的模组,需将内外面的蜡屑清除干净后送涂挂制壳。 4.2 制壳 4.2.1 选料面层料浆用320目锆英粉,加固层料浆用200目以上的 高铝粉或焦宝石粉和石英粉,粘结剂用模数3.1~3.4,密度为 1.30~1.40的40#水玻璃。 4.2.2 选砂面层用80~100目的棕刚玉,二层用40~70目的石英砂, 三层用20~40目的石英砂,四层以后选用10~20目的石英砂。 4.2.3 料浆的配制面层与二层:将水玻璃加水稀释到密度为 1.28~1.30,然后加锆英粉,其比例为1:1.1~1.2(要注意根据 气温变化调节比例),进行机械搅拌,再加入清洗剂0.05%,消 泡剂0.05%,继续搅拌,时间不少于6小时,静置4小时熟化, 再搅拌均匀方可使用。三层过渡层用密度为1.30~1.32的水玻 璃加高铝粉和石英粉,比例为1:0.5:0.5。加固层同三层,比例略 为调厚一点。 4.2.4 料浆的粘度测定用100Ml的流量杯来测定,面层、二层及三层 为28~35秒,加固层为45~50秒。 4.2.5 挂浆将检验合格后的模组浸入搅拌均匀的料浆中,上下移动两 次,然后提出,用毛刷将字和死角处的气泡刺破并刷浆,把多余
炼钢工艺流程图
炼钢工艺流程 1炼钢厂简介 炼钢厂主要将铁水冶炼成钢水,再经连铸机浇铸成合格铸坯。现有5座转炉,5台连铸机,年设计生产能力为500万吨,现年生产钢坯400万吨。其中炼钢一分厂年生产能力达到240万吨;炼钢二厂年生产能力为160万吨。 2炼钢的基本任务 钢是以Fe为基体并由C、Si、Mn、P、S等元素以及微量非金属夹杂物共同组成的合金。 炼钢的基本任务包括:脱碳、脱磷、脱硫、脱氧去除有害气体和夹杂,提高温度,调整成分,炼钢过程通过供氧造渣,加合金,搅拌升温等手段完成炼钢基本任务,“四脱两去两调整”。 3氧气转炉吹炼过程 氧气顶吹转炉的吹氧时间仅仅是十分钟,在这短短的时间内要完成造渣,脱碳、脱磷、脱硫、去气,去除非金属夹杂物及升温等基本任务。 由于使用的铁水成分和所炼钢种的不同,吹炼工艺也有所区别。氧气顶吹转炉炼钢的吹炼过程,根据一炉钢吹炼过程中金属成分,炉渣成分,熔池温度的变化规律,吹炼过程大致可以分为以下3个阶段: (1)吹炼前期。(2)吹炼中期。(3)终点控制。 炼好钢必须抓住各阶段的关键,精心操作,才能达到优质、高产、低耗、长寿的目标。 装入制度 装入制度是保证转炉具有一定的金属熔池深度,确定合理的装入数量,合适的铁水废钢比例。
3.1.1装入量的确定 装入量是指转炉冶炼中每炉次装入的金属料总重量,它主要包括铁水和废钢量。目前国内外装入制度大体上有三种方式: (1)定深装入;(2)分阶段定量装入;(3)定量装入 3.2.2装入次序 目前永钢的操作顺序为,钢水倒完后进行溅渣护炉溅渣完后装入废钢,然后兑入铁水。 为了维护炉衬,减少废钢对炉衬的冲击,装料次序也可以先兑铁水,后装废钢。若采用炉渣预热废钢,则先加废钢,再倒渣,然后兑铁水。如果采用炉内留渣操作,则先加部分石灰,再装废钢,最后兑铁水。 供氧制度 制订供氧制度时应考虑喷头结构,供氧压力,供氧强度和氧枪高度控制等因素。 3.2.1氧枪喷头 转炉供氧的射流特征是通过氧枪喷头来实现的,因此,喷头结构的合理选择是转炉供氧的关键。氧枪有单孔,多孔和双流道等多种结构。永钢使用的是4孔拉瓦尔喷头形式喷枪。 3.2.2氧气压力控制 氧气压力控制受炉内介质和流股马赫数的影响。经测定,炉内介质压力一般为—,流股马赫数在—之间。因此目前在转炉上使用的工作压力为—,视各种扎容量而定。一般说来,转炉容量大,使用压力越高。 3.2.3氧气流量和供氧强度 (1)氧气流量:
纺纱工艺流程设备介绍
纺纱工艺流程设备介绍 一、纺织的定义 纺织原意是取自纺纱与织布的总称,但是随着纺织知识体系和学科体系的不断发展和完善,特别是非织造纺织材料和三维复合编织等技术产生后,纺织不仅是传统的纺纱和织布,也包括无纺布技术,三维编织技术,静电纳米成网技术等,所以,现代纺织是指一种纤维或纤维集合体的多尺度结构加工技术。 二、工艺流程及设备 纺纱按天然纤维分为棉纺、麻纺、绢纺、和毛纺,工艺流程和设备不尽相同。下面我们主要说说棉纺工艺流程及用到的设备。 纺织机把许多植物纤维捻在一起纺成线或纱,这些线或纱可用来织成布。 所有的纺纱机都只做两件事:首先把大量的短纤维聚合成松散的棉线,然后把棉线一点点的抽出来,捻搓成细密的棉线,棉线经过搓捻就变长了。 1、清棉工序: 开棉机:将紧压原棉松解成小的棉块或棉束,以方便混合、除杂。 清棉机:清除原棉中的大部分杂质、疵点及不宜纺纱的短纤维。
清棉机(亦称清弹机、开棉机、开清棉机等)是由分梳器和刺辊高速运转所产生的机械离心力来排除锦花中的杂质并将皮棉疏松,滚压成片,便于使用。 混棉机:将不同成分的原棉进行充分而均匀地混合。 成卷机:支撑一定重量、长度、厚薄均匀、外形良好的棉卷。 2、梳棉工序: 梳棉机(图1):对清棉工序下机的棉卷经过刺辊、锡林盖板、道夫等工序进行分梳、除杂、混合成棉条入筒。 (图1) 3、精梳工序: 精梳机: (1)除杂:清除纤维中的棉结、杂质和纤维疵点。 (2)梳理:进一步分离纤维,排除一定长度以下的短纤维。 (3)牵伸:将棉条拉细到一定粗细,并提高纤维平行伸直度。 4、并条工序: 并条机: (1)并合:用6~8根棉条进行并合,改善棉条长片段不匀。 (2)牵伸:把棉条拉长抽细到规定重量,并进一步提高纤维伸直平行程度。(3)混合:利用并合与牵伸,根据工艺在并条机上进行棉条混合。 (4)成条:将圈条做成成型良好的熟条,有规则地盘放在棉条筒里。 5、粗纱工序:
精密铸造工艺规程
精密铸造工艺规程 编制: 审核: 批准: 日期: 1 / 23
文件目录 序号文件编号文件名称页码 1 JZQ-ZZ-GY01-2013 蜡型工艺规程 3 2 JZQ-ZZ-GY02-201 3 浇口棒蜡模工艺规程 5 3 JZQ-ZZ-GY03-2013 蜡模组焊工艺规程 6 4 JZQ-ZZ-GY04-2013 制壳工艺规程7 5 JZQ-ZZ-GY05-2013 脱蜡工艺规程9 6 JZQ-ZZ-GY06-2013 蜡处理工艺规程10 7 JZQ-ZZ-GY07-2013 焙烧工艺规程11 8 JZQ-ZZ-GY08-2013 熔炼工艺规程12 9 JZQ-ZZ-GY09-2013 浇注工艺规程14 10 JZQ-ZZ-GY10-2013 后处理工艺规程15 11 JZQ-ZZ-GY11-2013 热处理工艺规程16 12 JZQ-ZZ-GY12-2013 焊补工艺规程19 13 JZQ-ZZ-GY13-2013 试棒管理规程22 14 15 16 2 / 23
3 / 23 蜡型工艺规程 一、工艺参数 1.蜡料的配臵(﹪) 季 节 冬 季 夏 季 四 季 备注 编号 材料 (1) (2) (3) (4) (5) 5-10月按夏季 11-4月按冬季 回收蜡 95-97 85-87 92 82 硬脂蜡 3-5 8-10 8 13 50 石蜡 5 5 50 2.蜡料使用的温度 序号 名称 温度℃ 序号 名称 温度℃ 1 熔点 56—58 2 搅成糊状温度 47-49 3 熔化温度 90-95 4 蜡料压蜡温度 42-50 5 压蜡保温水温度 48-53 3.压缩空气工作压力0.25—0.4 MPa 4.搅料用碎蜡块加入量占蜡液的30%(碎蜡块30% 蜡液70%) 5.新蜡与硬脂酸的比例1∶1 6.作业环境温度0-30℃ 南京金正奇交通设备有限责任公司 铸造事业部 文件编号 JZQ-ZZ-GY01-2013 版 本 A 编制日期 2013-3-27
炼钢工艺流程
【导读】:转炉炼钢是把氧气鼓入熔融的生铁里,使杂质硅、锰等氧化。在氧化的过程中放出大量的热量(含1%的硅可使生铁的温度升高200摄氏度),可使炉内达到足够高的温度。因此转炉炼钢不需要另外使用燃料。炼钢的基本任务是脱碳、脱磷、脱硫、脱氧,去除有害气体和非金属夹杂物,提高温度和调整成分。归纳为:“四脱”(碳、氧、磷和硫),“二去”(去气和去夹杂),“二调整”(成分和温度)。采用的主要技术手段为:供氧,造渣,升温,加脱氧剂和合金化操作。本专题将详细介绍转炉炼钢生产的工艺流程,主要工艺设备的工作原理以及控制要求等信息。由于时间的仓促和编辑水平有限,专题中难免出现遗漏或错误的地方,欢迎大家补充指正。 转炉冶炼目的:将生铁里的碳及其它杂质(如:硅、锰)等氧化,产出比铁的物理、化学性能与力学性能更好的钢。 【相关信息】钢与生铁的区别:首先是碳的含量,理论上一般把碳含量小于2.11%称之钢,它的熔点在1450-1500℃,而生铁的熔点在1100-1200℃。在钢中碳元素和铁元素形成Fe3C固熔体,随着碳含量的增加,其强度、硬度增加,而塑性和冲击韧性降低。钢具有很好的物理、化学性能与力学性能,可进行拉、压、轧、冲、拔等深加工,其用途十分广泛。 转炉冶炼原理简介: 转炉炼钢是在转炉里进行。转炉的外形就像个梨,内壁有耐火砖,炉侧有许多小孔(风口),压缩空气从这些小孔里吹炉内,又叫做侧吹转炉。开始时,转炉处于水平,向内注入1300摄氏度的液态生铁,并加入一定量的生石灰,然后鼓入空气并转动转炉使它直立起来。这时液态生铁表面剧烈的反应,使铁、硅、锰氧化 (FeO,SiO2 , MnO,) 生成炉渣,利用熔化的钢铁和炉渣的对流作用,使反应遍及整个炉内。几分钟后,当钢液中只剩下少量的硅与锰时,碳开始氧化,生成一氧化碳(放热)使钢液剧烈沸腾。炉口由于溢出的一氧化炭的燃烧而出现巨大的火焰。最后,磷也发生氧化并进一步生成磷酸亚铁。磷酸亚铁再跟生石灰反应生成稳定的磷酸钙和硫化钙,一起成为炉渣。当磷与硫逐渐减少,火焰退落,炉口出现四氧化三铁的褐色蒸汽时,表明钢已炼成。这时应立即停止鼓风,并把转炉转到水平位置,把钢水倾至钢水包里,再加脱氧剂进行脱氧。整个过程只需15分钟左右。如果氧气是从炉底吹入,那就是底吹转炉;氧气从顶部吹入,就是顶吹转炉。 转炉冶炼工艺流程简介:
铸造工艺设计步骤
铸造工艺设计: 就是根据铸造零件的结构特点,技术要求,生产批量和生产条件等,确定铸造方案和工艺参数,绘制铸造工艺图,编制工艺卡等技术文件的过程.设计依据: 在进行铸造工艺设计前,设计者应掌握生产任务和要求,熟悉工厂和车间的生产条件,这些是铸造工艺设计的基本依据.设计内容: 铸造工艺设计内容的繁简程度,主要决定于批量的大小,生产要求和生产条件.一般包括下列内容: 铸造工艺图,铸件(毛坯)图,铸型装配图(合箱图),工艺卡及操作工艺规程.设计程序: 1零件的技术条件和结构工艺性分析;2选择铸造及造型方法;3确定浇注位置和分型面;4选用工艺参数;5设计浇冒口,冷铁和铸肋;6砂芯设计;7在完成铸造工艺图的基础上,画出铸件图;8通常在完成砂箱设计后画出;9综合整个设计内容.铸造工艺方案的内容: 造型,造芯方法和铸型种类的选择,浇注位置及分型面的确定等.铸件的浇注位置是指浇注时铸件在型内所处的状态和位置.分型面是指两半铸型相互接触的表面.确定砂芯形状及分盒面选择的基本原则,总的原则是: 使造芯到下芯的整个过程方便,铸件内腔尺寸精确,不至造成气孔等缺陷,使芯盒结构简单.1保证铸件内腔尺寸精度;2保证操作方便;3保证铸件壁厚均匀;4应尽量减少砂芯数目;5填砂面应宽敞,烘干支撑面是平面;6砂芯形状适应造型,制型方法.铸造工艺参数通常是指铸型工艺设计时需要确定的某些数据.1铸件尺寸公差: 是指铸件各部分尺寸允许的极限偏差,它取决于铸造工艺方法等多种因素.2主见重量公差定义为以占铸件公称质量的百分率为单位的铸件质量变动的允许值.3机械加工余量: 铸件为保证其加工面尺寸和零件精度,应有加工余量,即在铸件工艺设计时预先增加的,而后在机械加工时又被切去的金属层厚度,称为机械加工余量,简称加工余量.代号用MA,由精到粗分为ABCDEFGH和J9个等级。
碱性电弧炉炼钢工艺流程
碱性电弧炉炼钢工艺流程 碱性电弧炉氧化法炼钢工艺过程主要包括原材料准备、补炉、配料及装料、熔化期、氧化期、还原期及出钢等7个阶段。 一、原材料准备 废钢是电弧炉炼钢的主要材料,废钢质量的好坏直接影响钢冶的质量、成本和生产率,因此,对废钢质量有如下几点要求。 1)废钢表面应清洁少锈,因废钢中沾有的泥沙等杂物会降低炉料的导电性能,延长熔化时间,还会影响氧化期去鳞效果及侵蚀炉衬。废钢锈蚀严重或沾有油污时还会降低钢和合金元素的收得率,并增加钢中的含氢量。 2)废钢中不得混有铅、锡、砷、锌和铜等有色金属。铅的密度大,熔点低,不溶于钢液,易沉积在炉底缝隙中造成漏钢事故;锡、砷和铜易引起钢的热脆。 3)废钢中不得混有密封容器,以及易燃、易爆物和有毒物,以保证安全生产。 4)废钢化学成分应明确,且需按成分分类存放,硫、磷含量不宜过高。 5)废钢外形尺寸不能过大(截面积不宜超过300mm×300mm,最大长度不宜超过350mm)。 二、补炉 一般情况下,每炼完一炉钢后,在装料前要进行补炉,其目的是修补炉底和被侵蚀的渣线及被破坏的部位,以维持正常的炉体形状,从而保证冶炼的正常进行和安全生产,补炉的要点如下:
1)出钢后立即检查炉衬,需填补炉底时,应先将炉底残渣全部扒出,然后进行填补。补炉的原则是高温、快补、薄补,维护炉膛原状。 2)补炉料要提前半个小时混合均匀,补炉后放下电极烘烤30min,若补镁砂量较大,应酌情延长烘烤时间。 三、配料及装料 配料是电炉炼钢工艺中不可缺少的组成部分,配料是否合理关系到炼钢工能否按照工艺要求正常地进行冶炼操作。合理的配料能缩短冶炼时间。配料时应注意以下几点:一是必须正确地进行配料计算和准确地称量炉料装入量;二是炉料的大小要按比例搭配,以达到好装、快速熔化的目的;三是各类炉料应根据钢液的质量要求和冶炼方法搭配使用;四是配料成分必须符合工艺要求。 装料前应先在炉底铺上一层石灰,其重量约为炉料重量的2%,以便提前造好熔化渣,有利于早期去磷,减少钢液吸气和加速升温。 装料时应将小料的一半放入底部,小料的上部、炉子中心区放入全部大料、低碳废钢和难熔炉料,大料之间放入小料,中型料装在大料的上面及四周,大料的最上面放入小料。凡在配料中使用的电极块应砸成50~lOOmm,装在炉料下层,且要紧实,装好的炉料为半球形,二次加料不使用大块料及湿料。 四、熔化期 在电弧炉炼钢工艺中,从通电开始到炉料全部熔清为止称为熔化期。熔化期的任务是将固体炉料迅速熔化成钢液,并进行脱磷,减少钢液吸收气体和金属的挥发。熔化期的操作工艺如下: 1)启弧阶段。通电启弧时炉膛内充满炉料,电弧与炉顶距离很近,如果输入功率过大、电压过高,炉顶容易被烧坏,因此一般选用中级电压和输入变压器额定功率的2/3左右。
消失模铸造工艺流程介绍
消失模铸造工艺流程及车间环境状况分析消失模铸造简称EPC,又称气化模铸造或实型铸造。它是采用泡沫塑料模样代替普通模样紧实造型,造好铸型后不取出模样、直接浇入金属液,在高温金属液的作用下,泡沫塑料模样受热气化、燃烧而消失,金属液取代原来泡沫塑料模样占据的空间位置,冷却凝固后即获得所需的铸件。 消失模铸造工艺简图: 消失模铸造生产线的工艺流程分为白区与黑区两大部分。 一、白区工艺流程: 首先根据铸件的材质以及壁厚选择适合它的原始珠粒。将原始珠粒按定量加入间歇式予发机中进行预发泡,使其达到工艺要求的密
度,通过予发机硫化床干燥后发送到熟化仓内进行熟化。熟化后的珠粒运送到成型间,将珠粒注入到成型机上的模具中,通蒸汽将其膨胀融解成型,形成铸件模样,通冷水进行冷却降温,使白模具有一样的强度,这时成型机起模人工取出白模放到白模烘干车上,运输至热风隧道通过式烘干室进行烘干。白模烘干车在烘干室轨道上行走,每推进室内一车,在另一端顶出一车,以此循环。烘干室采用热风强制循环系统,烘干室内的温度及湿度通过PLC自动控制达到工艺要求,大大提高了生产效率,并节约能源。白模烘干后运输到组模间组装、粘结浇冒口。组装好的白模运输至一次涂料间浸刷涂料,不同材质的铸件选择不同的涂料配方,将原材料放入涂料搅拌机中进行搅拌,达到工艺要求时间后测试涂料密度,经测试合格后再放入涂料槽中供工人使用。将浸刷好的白模放到烘干车上运输至黄模一次烘干室进行烘干,烘干后的黄模运输到二次涂料间进行二次浸刷涂料,达到工艺要求的涂层厚度,再运输至黄模二次烘干室进行烘干、修补。经过二次烘干后的黄模用烘干车运输到黑区造型工部进行填箱、造型,烘干车空车返回成型间。至此白区工艺流程全部结束。 二、黑区工艺流程: 1、造型工部: 造型工部由两条造型线和一条回箱线组成,砂箱的循环运行是由砂箱轨道、手动变轨车来完成,每一条生产线由工艺要求的砂箱数量组成。每一条造型线由一台2吨单维振实台,两台4吨变频三维振实台组成。造好型的砂箱依次进入两条浇注冷却线,浇注冷却线由真空对接机组成。浇注冷却线进入一定数量砂箱后真空对接机自动对接、人工浇注。浇注完成后进行保压冷却,保压后真空对接机复位,撤真空,保压结束后进入冷却段进行冷却。在这两条浇注线浇注的同时,造型线造好型的砂箱依次进入令外两条浇注线等待浇注,并重复前两条浇注线的动作,以此循环。 本造型工部采用BSZ-04k变频三维振实台,其结构及工作原理:
精密铸造各工序操作规程及注意事项
精密铸造各工序操作规程及注意事项 文件管理序列号:[K8UY-K9IO69-O6M243-OL889-F88688]
精密铸造各工序操作规程及注意事项 压蜡工序工艺操作规程及注意事项 一.工艺要求: 室温:24±2℃,蜡缸温度:54±2℃射蜡嘴温 度: 54±2℃压射压力:3.5-4.0mpa 保压时间:视蜡模大小,壁厚而定(一般为6-8秒) 冷却水温度:≤20℃ 二.操作程序: 1.检查压蜡机油压,保温温度,操作按钮是否正常,按照技术规定调整压 蜡机压射压力,射蜡嘴温度,保压时间,冷却时间等。 2.从保温箱中取出蜡缸,装在压蜡机上,挤出上部混有空气的蜡料。 3.将模具放在压蜡机工作台面上,调整射蜡嘴使之与模具注蜡口高度一 致,检查模具所有芯子,活块位置是否正确,模具开合是否顺利。 4.打开模具,喷薄薄一层分型剂,合型,对准射蜡嘴。 5.双手按动工作按钮,压制蜡模。 6.抽出芯子,打开模具,小心取出蜡模,放在工作台一侧,合上模具开始 压下一件,同时对该件粗略检查无缺陷后按要求放入冷却水中或放入存放盘中冷却,冷却时间为4小时,注意有以下缺陷的蜡模应报废: (1)因模料中卷入空气,蜡模局部有鼓起的; (2)蜡模任何部位有缺陷的; (3)蜡模有变形不能简单修复的; (4)尺寸不符合规定的。 7.清除模具上残留的模料,注意只能用竹刀,不可用金属刀片清除残留模料,防止模具型腔及分型面受损,用压缩空气气嘴吹净模具分型面。芯子上的蜡屑等,视模具结构及使用情况每2-10件喷一次分型剂。 8.及时将蜡模从冷却水中轻轻取出,用压缩空气吹净蜡屑及水珠,并进行 自检,将合。放入存放盘中。 9.每班下班或模具使用完毕后,应用软布或棉棒清理模具,如发现模具有 损伤或不正常,应立即报告领班,由领班处理。并清扫压蜡机,工具及现场,做到清洁、整齐。 三.注意事项: 1.压制蜡模时,首先必须进行检查,确认合格后,方可进行操作,压蜡模过程中不能轻易变动压制参数。 2.模具型腔不要喷过多的分型剂,并要均匀,必要时可用压缩空气气嘴辅助将分型剂吹均匀。 3.使用新模具时,务必弄清模具组装,拆卸顺序,蜡模取出方法。 4.蜡模放在存放盘中,彼此间应隔离以免碰损,应注意搁置方向,防止变形,有需要时可采用卡具等,避免蜡模变形。