1控制入窑分解率的意义
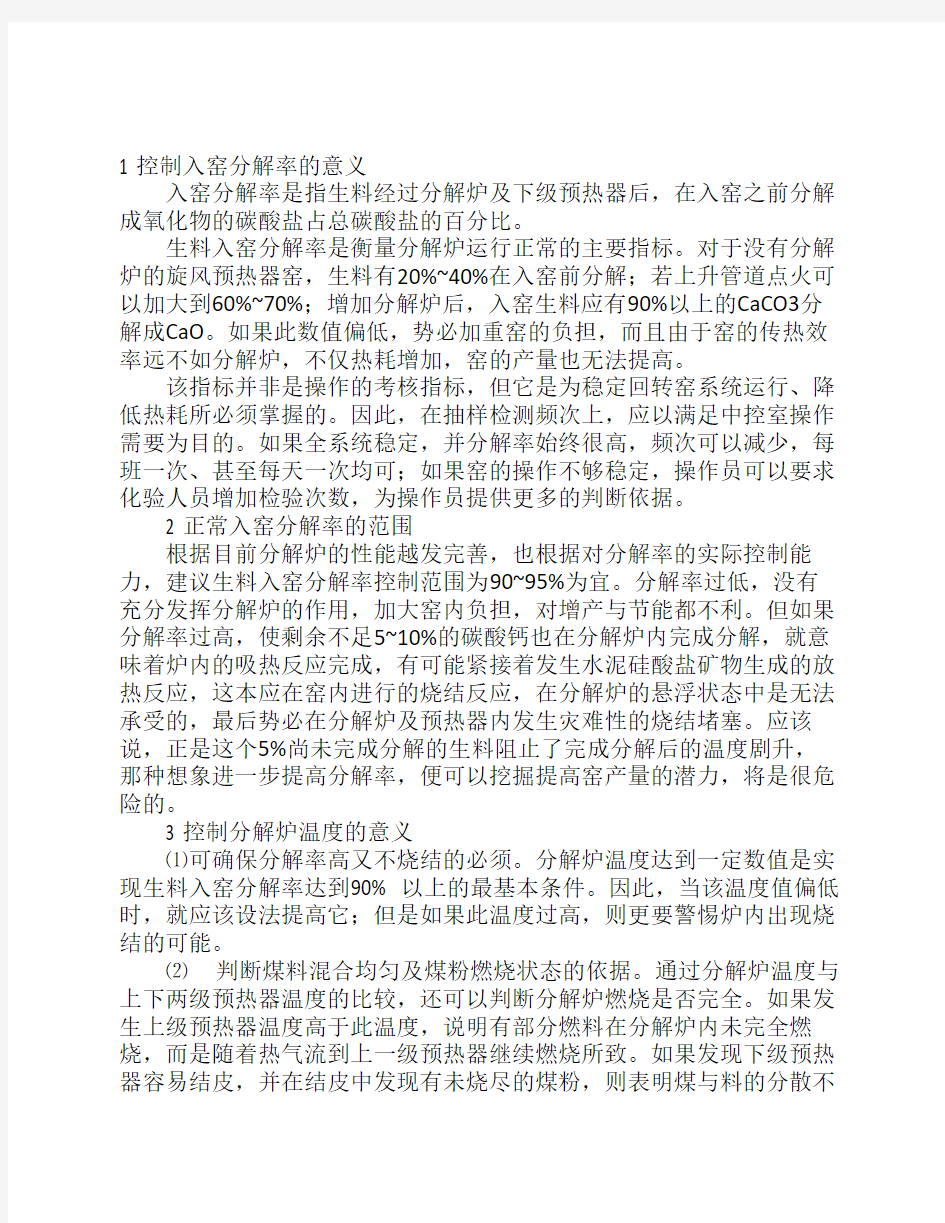
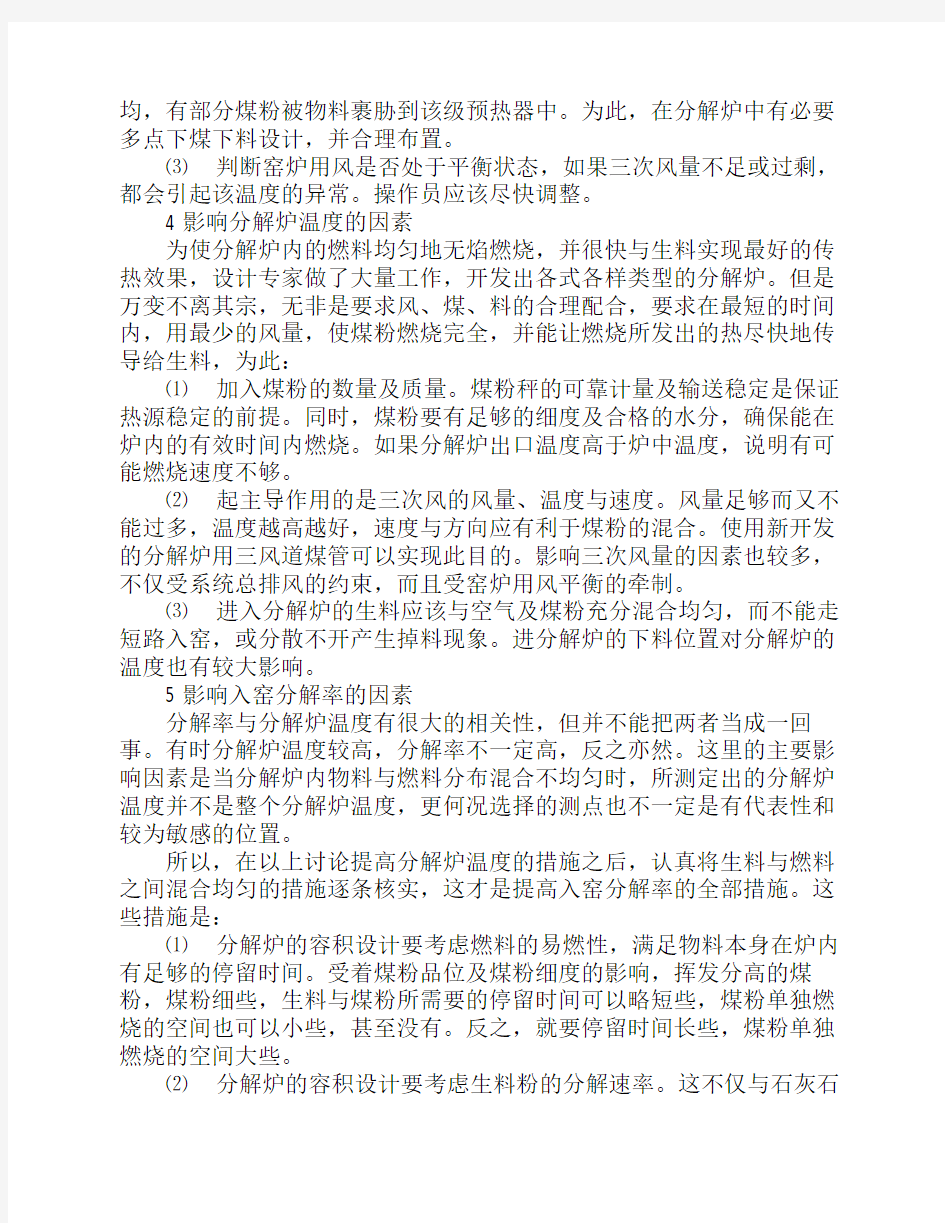
1 控制入窑分解率的意义
入窑分解率是指生料经过分解炉及下级预热器后,在入窑之前分解成氧化物的碳酸盐占总碳酸盐的百分比。
生料入窑分解率是衡量分解炉运行正常的主要指标。对于没有分解炉的旋风预热器窑,生料有20%~40%在入窑前分解;若上升管道点火可以加大到60%~70%;增加分解炉后,入窑生料应有90%以上的CaCO3分解成CaO。如果此数值偏低,势必加重窑的负担,而且由于窑的传热效率远不如分解炉,不仅热耗增加,窑的产量也无法提高。
该指标并非是操作的考核指标,但它是为稳定回转窑系统运行、降低热耗所必须掌握的。因此,在抽样检测频次上,应以满足中控室操作需要为目的。如果全系统稳定,并分解率始终很高,频次可以减少,每班一次、甚至每天一次均可;如果窑的操作不够稳定,操作员可以要求化验人员增加检验次数,为操作员提供更多的判断依据。
2 正常入窑分解率的范围
根据目前分解炉的性能越发完善,也根据对分解率的实际控制能力,建议生料入窑分解率控制范围为90~95%为宜。分解率过低,没有充分发挥分解炉的作用,加大窑内负担,对增产与节能都不利。但如果分解率过高,使剩余不足5~10%的碳酸钙也在分解炉内完成分解,就意味着炉内的吸热反应完成,有可能紧接着发生水泥硅酸盐矿物生成的放热反应,这本应在窑内进行的烧结反应,在分解炉的悬浮状态中是无法承受的,最后势必在分解炉及预热器内发生灾难性的烧结堵塞。应该说,正是这个5%尚未完成分解的生料阻止了完成分解后的温度剧升,那种想象进一步提高分解率,便可以挖掘提高窑产量的潜力,将是很危险的。
3 控制分解炉温度的意义
⑴可确保分解率高又不烧结的必须。分解炉温度达到一定数值是实现生料入窑分解率达到90% 以上的最基本条件。因此,当该温度值偏低时,就应该设法提高它;但是如果此温度过高,则更要警惕炉内出现烧结的可能。
⑵判断煤料混合均匀及煤粉燃烧状态的依据。通过分解炉温度与上下两级预热器温度的比较,还可以判断分解炉燃烧是否完全。如果发生上级预热器温度高于此温度,说明有部分燃料在分解炉内未完全燃烧,而是随着热气流到上一级预热器继续燃烧所致。如果发现下级预热器容易结皮,并在结皮中发现有未烧尽的煤粉,则表明煤与料的分散不
均,有部分煤粉被物料裹胁到该级预热器中。为此,在分解炉中有必要多点下煤下料设计,并合理布置。
⑶判断窑炉用风是否处于平衡状态,如果三次风量不足或过剩,都会引起该温度的异常。操作员应该尽快调整。
4 影响分解炉温度的因素
为使分解炉内的燃料均匀地无焰燃烧,并很快与生料实现最好的传热效果,设计专家做了大量工作,开发出各式各样类型的分解炉。但是万变不离其宗,无非是要求风、煤、料的合理配合,要求在最短的时间内,用最少的风量,使煤粉燃烧完全,并能让燃烧所发出的热尽快地传导给生料,为此:
⑴加入煤粉的数量及质量。煤粉秤的可靠计量及输送稳定是保证热源稳定的前提。同时,煤粉要有足够的细度及合格的水分,确保能在炉内的有效时间内燃烧。如果分解炉出口温度高于炉中温度,说明有可能燃烧速度不够。
⑵起主导作用的是三次风的风量、温度与速度。风量足够而又不能过多,温度越高越好,速度与方向应有利于煤粉的混合。使用新开发的分解炉用三风道煤管可以实现此目的。影响三次风量的因素也较多,不仅受系统总排风的约束,而且受窑炉用风平衡的牵制。
⑶进入分解炉的生料应该与空气及煤粉充分混合均匀,而不能走短路入窑,或分散不开产生掉料现象。进分解炉的下料位置对分解炉的温度也有较大影响。
5 影响入窑分解率的因素
分解率与分解炉温度有很大的相关性,但并不能把两者当成一回事。有时分解炉温度较高,分解率不一定高,反之亦然。这里的主要影响因素是当分解炉内物料与燃料分布混合不均匀时,所测定出的分解炉温度并不是整个分解炉温度,更何况选择的测点也不一定是有代表性和较为敏感的位置。
所以,在以上讨论提高分解炉温度的措施之后,认真将生料与燃料之间混合均匀的措施逐条核实,这才是提高入窑分解率的全部措施。这些措施是:
⑴分解炉的容积设计要考虑燃料的易燃性,满足物料本身在炉内有足够的停留时间。受着煤粉品位及煤粉细度的影响,挥发分高的煤粉,煤粉细些,生料与煤粉所需要的停留时间可以略短些,煤粉单独燃烧的空间也可以小些,甚至没有。反之,就要停留时间长些,煤粉单独燃烧的空间大些。
⑵分解炉的容积设计要考虑生料粉的分解速率。这不仅与石灰石
的特性有关,还与分解炉内的气氛有关。尤其是在线式分解炉窑的废气中CO2含量较高,不利于石灰石的分解速度。
⑶设置加料点、加煤点的位置及数量时要考虑生料在入炉前为燃料燃烧留有足够的空间,特别是对不易燃烧的无烟煤,还要考虑引入三次风的位置及方向等。不仅保证煤粉均匀充分燃烧,全炉中最高温度及最低温度两者相差不应超过20~30℃。通过改善生料与煤粉的混合均匀程度,达到改善传热均衡的目的。对于较大的分解炉,不应只设一个加料点与加煤点,更需要妥善布局。
6 分解炉用煤占总用煤的比例
根据生料预热与分解所消耗热量占熟料烧成总热量60%的原理,分解炉用煤的比例一般控制在60%左右,剩余40%用煤是窑内煅烧所需要,而且煅烧后的窑尾温度也达到1000℃以上,这些余热也为物料的预热及分解所用。这种比例已为大多数生产线所证实,随着具体矿物成分的变化,该比例会有所变动。
在操作中及设备装置的配备中,对二、三次风温度与风量的控制变化,一定会影响窑头与分解炉的用煤比例,比如,三次风利用篦冷机热风多时,就会降低分解炉的用煤量,反之,二次风温高就会节省窑前的用煤量。当操作中由于某种因素前后某点加煤受限时,为了满足熟料煅烧的热量需要,就只好向另一点多加煤,这种做法只能度过一时,难以应付长远,并会产生各种负面影响。
曾经发现某生产线由于使用无烟煤,窑头燃烧器加煤燃烧不利,于是使分解炉用煤达70%左右,企图让多余的10%用煤帮助提高窑内温度。这种操作虽然维持着窑的高产运行,但因为分解炉燃烧速度不够,剩余的煤量随着生料进入窑尾燃烧,造成后窑口结皮严重,窑尾温度偏高,严重时甚至直径4.8米的窑,尾部也结起厚圈,窑尾倒料,被迫停窑。当更换新燃烧器之后,窑前喷煤量增加,分解炉用煤量自然调整过来,窑尾结皮或结圈的症状就随之消失。
反之,如果分解炉供氧充足时,70%的用煤全部燃烧,则很难避免生料百分之百分解所带来的一系列恶果发生。
总之,不论何种情况,窑炉用煤比例不当,势必反映并导致系统不能正常运行。
7 分解炉的燃烧速度慢的症状
有时生产中会碰到这样的现象:分解率并不低,可以高达90%以上,但分解炉的出口温度要高于炉中温度40℃以上,尤其是在烧挥发分较低的无烟煤时。由于燃烧速度慢,导致仍有部分燃料不能在炉内燃烧,大量的热量未在炉内放出,即可使上一级预热器温度比分解炉温度
高,出现温度倒置现象,使一级出口温度升高,增加熟料热耗;也可直接影响到下一级预热器温度与窑尾温度的过分升高。造成如下后果:
⑴垂直上升烟道结皮严重,还会使窑尾部分的窑衬上结挂较厚的窑皮,甚至成圈、如果不及时改变这种非正常状态,后窑口向外倒料,就会迫使窑止料停窑处理;
⑵迫使窑头加不上煤,使分解炉的用煤量由60%提高到70%。从而束缚了窑系统产量的提高。
遇到这种现象,如果不认真分析,往往会归罪于窑头煤粉燃烧不好所致。
8 分解炉温度与下一级预热器温度的倒挂现象
造成分解炉出口温度高于下一级预热器温度的原因是分解炉内煤粉燃烧的速度,而这种速度又受着众多因素的影响:
⑴煤质本身的影响:挥发分含量较低的煤燃烧速度过慢,不利于分解炉温度的提高。尤其是未燃烧的无烟煤一直随生料到窑内才燃烧,则下一级预热器的温度会低于分解炉温度。
⑵风煤的配比影响燃料的燃烧速度,当二、三次风的分配不合理时,三次风量过大时,尤其是MFC炉更是如此;或总风量使用不足时,煤不能在分解炉充分燃烧,如果仍然到窑内燃烧,则下一级预热器温度会表现倒置。
⑶MFC炉更需要下料量的控制。在设计入炉生料量时如果可以调节,这种调节就显得尤为重要。如果入炉物料偏少,将会造成下一级预热器温度过低。
解决这类温度的倒挂现象,就要从上述产生的原因着手,确保分解炉的风、煤、料实现量与质的稳定,始终保持三者用量的合理比例;认真观察各相关参数的变化,如果发现异常,随时要考虑相关阀门及喷头等设施的可靠性,也要考虑结皮长落的动态变化。