cooling technologies for the power cycle of a thermal power plant
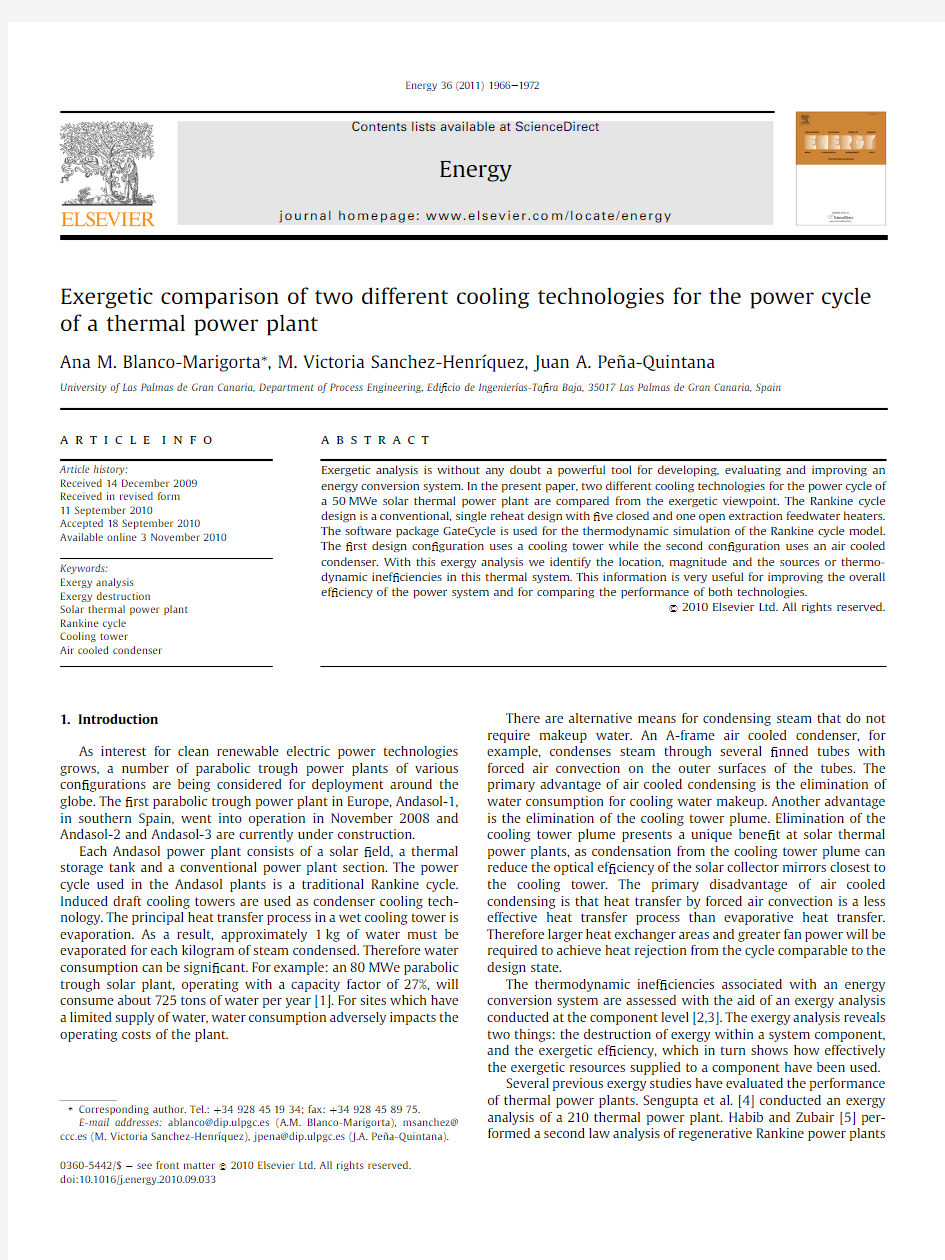

Exergetic comparison of two different cooling technologies for the power cycle of a thermal power plant
Ana M.Blanco-Marigorta *,M.Victoria Sanchez-Henríquez,Juan A.Pe?a-Quintana
University of Las Palmas de Gran Canaria,Department of Process Engineering,Edi ?cio de Ingenierías-Ta ?ra Baja,35017Las Palmas de Gran Canaria,Spain
a r t i c l e i n f o
Article history:
Received 14December 2009Received in revised form 11September 2010
Accepted 18September 2010
Available online 3November 2010Keywords:
Exergy analysis Exergy destruction
Solar thermal power plant Rankine cycle Cooling tower
Air cooled condenser
a b s t r a c t
Exergetic analysis is without any doubt a powerful tool for developing,evaluating and improving an energy conversion system.In the present paper,two different cooling technologies for the power cycle of a 50MWe solar thermal power plant are compared from the exergetic viewpoint.The Rankine cycle design is a conventional,single reheat design with ?ve closed and one open extraction feedwater heaters.The software package GateCycle is used for the thermodynamic simulation of the Rankine cycle model.The ?rst design con ?guration uses a cooling tower while the second con ?guration uses an air cooled condenser.With this exergy analysis we identify the location,magnitude and the sources or thermo-dynamic inef ?ciencies in this thermal system.This information is very useful for improving the overall ef ?ciency of the power system and for comparing the performance of both technologies.
ó2010Elsevier Ltd.All rights reserved.
1.Introduction
As interest for clean renewable electric power technologies grows,a number of parabolic trough power plants of various con ?gurations are being considered for deployment around the globe.The ?rst parabolic trough power plant in Europe,Andasol-1,in southern Spain,went into operation in November 2008and Andasol-2and Andasol-3are currently under construction.
Each Andasol power plant consists of a solar ?eld,a thermal storage tank and a conventional power plant section.The power cycle used in the Andasol plants is a traditional Rankine cycle.Induced draft cooling towers are used as condenser cooling tech-nology.The principal heat transfer process in a wet cooling tower is evaporation.As a result,approximately 1kg of water must be evaporated for each kilogram of steam condensed.Therefore water consumption can be signi ?cant.For example:an 80MWe parabolic trough solar plant,operating with a capacity factor of 27%,will consume about 725tons of water per year [1].For sites which have a limited supply of water,water consumption adversely impacts the operating costs of the plant.
There are alternative means for condensing steam that do not require makeup water.An A-frame air cooled condenser,for example,condenses steam through several ?nned tubes with forced air convection on the outer surfaces of the tubes.The primary advantage of air cooled condensing is the elimination of water consumption for cooling water makeup.Another advantage is the elimination of the cooling tower plume.Elimination of the cooling tower plume presents a unique bene ?t at solar thermal power plants,as condensation from the cooling tower plume can reduce the optical ef ?ciency of the solar collector mirrors closest to the cooling tower.The primary disadvantage of air cooled condensing is that heat transfer by forced air convection is a less effective heat transfer process than evaporative heat transfer.Therefore larger heat exchanger areas and greater fan power will be required to achieve heat rejection from the cycle comparable to the design state.
The thermodynamic inef ?ciencies associated with an energy conversion system are assessed with the aid of an exergy analysis conducted at the component level [2,3].The exergy analysis reveals two things:the destruction of exergy within a system component,and the exergetic ef ?ciency,which in turn shows how effectively the exergetic resources supplied to a component have been used.Several previous exergy studies have evaluated the performance of thermal power plants.Sengupta et al.[4]conducted an exergy analysis of a 210thermal power plant.Habib and Zubair [5]per-formed a second law analysis of regenerative Rankine power plants
*Corresponding author.Tel.:t34928451934;fax:t34928458975.
E-mail addresses:ablanco@dip.ulpgc.es (A.M.Blanco-Marigorta),msanchez@ccc.es (M.Victoria Sanchez-Henríquez),jpena@dip.ulpgc.es (J.A.
Pe?a-Quintana).Contents lists available at ScienceDirect
Energy
journal ho me page:www.elsevier.co m/lo
cate/energy
0360-5442/$e see front matter ó2010Elsevier Ltd.All rights reserved.doi:10.1016/j.energy.2010.09.033
Energy 36(2011)1966e 1972
with reheating.Dincer and Muslim[6]conducted a thermodynamic analysis of reheat cycle power plants.Tsatsaronis and Winhold[7] presented a formulation on exergoeconomic analysis and evalua-tion of energy conversion plants applied to a Coal-Fired Steam Power Plant.In Ref.[8]exergetic and thermoeconomic analyses for a500-MW combined cycle plant were performed.More recently,Aljundi [9]presented an energy and exergy analysis of a steam power plant in Jordan.Related to solar thermal power plants,Singh et al[10] presented a second law analysis based on an exergy concept for a solar thermal power system.Singh et al evaluated the respective losses as well as exergetic ef?ciency for typical solar thermal power systems under given operating conditions.They found that the main energy loss takes place in the condenser of the heat engine,and their exergy analysis shows that the collector e receiver assembly is the part where the losses are maximum.Gupta and Kaushik[11]carried out the energy and exergy analysis for the different components of a proposed conceptual direct steam generation solar thermal power plant.In Ref.[12],a35MW solar thermal power plant was analyzed with the aid of exergoeconomics.
This paper deals with the comparison of wet and dry cooling technologies for the power cycle of Andasol-1by means of exergy analysis.The solar?eld is not considered in the study.Through an exergy analysis,the real thermodynamic inef?ciencies(exergy destruction and exergy loss)of the power cycle are identi?ed.This information,which cannot be provided by other means(e.g.an energy analysis),is very useful for improving the overall ef?ciency of the power system or for comparing the performance of both cooling technologies.The results obtained here are expected to provide information that will assist in decision-making regarding alternative cooling technologies.
2.Description of the plant
The power plant has a net power capacity of50MWe.The cycle is a conventional,single reheat design with?ve closed and one open extraction feedwater heaters.The GateCycle?ow diagram is shown in Fig.1.
In direct operation mode,a heat transfer?uid(HTF,Therminol-VP1)is circulated through the solar?eld to the steam generation system,where steam is produced at a temperature of373 C and at a pressure of100bar.The HTF?uid acts as the heat transfer medium between the solar?eld and the power block;it is heated up in the solar collectors and cooled down while producing steam in the steam generator.The steam generation system consists of two parallel heat exchanger trains(preheater(ECON1)/steam generator(EVAP1)/superheater(SPHT1))and two reheaters (SPHT2),again connected in parallel.The superheated steam travels ?rst through the high pressure turbine(ST1),where it expands and propels the turbine blades.One extraction is taken from the high pressure turbine to preheat feedwater in one closed feedwater heater(FWH5).On exiting the high pressure turbine,the steam is directed through a reheater,where it is superheated to approxi-mately the same temperature reached at the outlet of the super-heater(373 C)and at a pressure of about16.5bar.The superheated stream then passes through the low pressure steam(ST2e3),where again the steam expands and propels the turbine blades.Five steam extractions are taken from the low pressure turbine:one is directed to the deaerator(DA1)and the remaining four are fed to feedwater heaters(FWH1e4).The steam leaving the low pressure turbine,at 0.063bar,is condensed in a surface condenser by heat exchange with circulating water.The condenser water is cooled using an induced draft cooling tower.The condensed steam(feedwater)is pumped to a suf?ciently high pressure(8.38bar)to allow it to pass through the three low pressure feedwater heaters and into the deaerator.The feedwater is pumped again at the outlet of the deaerator to a pressure slightly higher than the boiling pressure in the steam generator(103bar).Feedwater passes through the two high pressure feedwater heaters before returning to the preheater to complete the cycle.
3.Thermodynamic evaluation
3.1.Simulation and modelling
The software package GateCycle 5.61[13]was used for the thermodynamic simulation of the Rankine Cycle.Table1gives an overview on the main parameters and assumptions used in the thermodynamic simulation.Main plant operation data(detailed in Section2)were fed to the software as input variables.The results of the simulation were compared and validated using simultaneously plant operation data and EES Thermodynamic software[14].
The thermodynamic properties were calculated based on: IAPWS IF97Steam Tables[15]for water,JANAF Tables[16]for ambient air and NIST Tables[17]for Therminol-VP1streams.
The power cycle is modelled assuming that all components are adiabatic,except the steam generator system,and operating
at A.M.Blanco-Marigorta et al./Energy36(2011)1966e19721967
steady state.Heat loss in the steam generator is calculated from plant operation data.Changes in potential and kinetic energy of ?uid streams are assumed negligible.Gland steam production,as well as steam losses through line leaks,is neglected.Pressure losses in the steam lines to the feedwater heaters were set to zero.Also,negligible changes in ?uid state between the outlet of one component and the inlet of the next are assumed.In addition,the following assumptions are made:feedwater exits the preheater as saturated liquid (x ?0);steam exits the steam generator as satu-rated vapour (x ?1);condensed steam exits the heater as saturated liquid (x ?0);feedwater exits the deaerator saturated liquid (x ?0);feedwater exits the condenser as saturated liquid (x ?0).3.2.Evaluation of the condensing operation pressure
For the overall power process,the energetic ef ?ciency is de ?ned by:
h ?
_W
net m 60eh 63àh 60Ttm 64eh 65àh 64T
(1)
where _W
net includes the auxiliary elements of the cooling system studied in each case (refrigeration pump tcooling tower or air cooled condenser).
The ef ?ciency of a Rankine cycle is de ?ned,in large part,by the pressure and the temperature of the steam both entering and leaving the turbine.The steam conditions at the turbine outlet are de ?ned by the temperature at which the steam is condensed and the latent heat of vaporization can be transferred to the environ-ment.The lowest ambient temperature available is the wet bulb temperature;thus,most power plants use an evaporation process to provide the cooling water source for the condenser.For sites which have a limited supply of water,heat can be rejected to the environment by condensing turbine exhaust steam at the dry bulb,rather than the wet bulb,temperature.However,heat transfer by forced air convention is less effective than evaporative heat trans-fer;therefore,larger heat exchanger areas and greater fan power will be required to achieve the same heat rejection.
For the Andasol-1design turbine exit pressure (0.063bar),energetic ef ?ciency decreases from 34.2%to 32%when an air cooled condenser instead of a cooling tower is used.A con ?gu-ration with an air cooled condenser,even if it were possible to condense steam in the air cooled condenser at the ambient air temperature,would be inef ?cient.The increase in gross power output from the cycle would be outweighed by the increase in parasitic fan power required to reach this temperature.In this paper,a comparison between dry and wet cooling technologies from an exergetic viewpoint is carried out with the consideration that both technologies,operating with similar parameters,not only reject the same amount of heat but also have the same net cycle power.It is necessary,therefore,to determine the turbine exit pressure with which both con ?gurations produce an as close as possible net cycle power.Fig.2shows the tendency of net cycle power with the increase of condensing pressure using both technologies.As condensing pressure increases,net cycle power of both technologies get closer.A condensing pressure of 0.2bar and,consequently,a net cycle power of 45MWe was chosen to perform the comparison.Higher condensing pressures only cause unnec-essary decrease in energetic ef ?ciency.The condensing pressure of 0.2bar is neither a real operation pressure nor an optimum operation pressure proposal;it is only used for simulation and comparison purposes.
This study does not include optimization of the design and con ?guration of the air cooled condensing unit.The performance characteristics of an existing A-frame air cooled condensing unit [13]were used as reference.The thermodynamic properties of
the
Fig.1.GateCycle ?ow diagram 50MWe Rankine cycle with wet heat rejection.
Table 1
Main parameters and assumptions used in the thermodynamic simulation.Isoentropic ef ?ciency of the high pressure steam turbine 0.852Isoentropic ef ?ciency of the low pressure steam turbine 0.85Isoentropic ef ?ciency of the pumps 0.75First extraction line inlet pressure (bar)33.5Second extraction line inlet pressure (bar)14Third extraction line inlet pressure (bar) 6.18Fourth extraction line inlet pressure (bar) 3.04Fifth extraction line inlet pressure (bar) 1.17Sixth extraction line inlet pressure (bar)
0.37Terminal temperature difference in feedwater heaters ( C)4Drain cooler approach in feedwater heaters ( C)
5Temperature of the thermodynamic environment ( C)25Pressure of the thermodynamic environment (bar)1Dry bulb temperature of ambient air ( C)20Relative humidity of ambient air (%)60Cooling tower approach ( C) 6.8Cooling tower range
9.7
A.M.Blanco-Marigorta et al./Energy 36(2011)1966e 1972
1968
working ?uid used in the frame air cooled condensing unit were
obtained on the basis of data provided by the GateCycle software.4.Exergy analysis
In an exergy analysis,an exergy balance is formulated for the k th component at steady state conditions:
_E F ;k ?_E P ;k t_E D ;k t_E L ;k
(2)
Here it is assumed that the system boundaries used for all exergy
balances are at temperature T 0of the reference environment and thus there are no exergy losses associated with one component [18].Therefore the exergy destruction in the k th component is calculated only through the fuel and the product for the compo-nent.Exergy losses appear only at the level of the overall system,for which the exergy balance becomes:
_E
F ;tot ?_E P ;tot tX
k
_E D ;k t_E L ;tot
(3)
The exergetic ef ?ciency of the k th component is:
3?_E P ;k _E F ;k ?1à_E
D ;k
_E F ;k
(4)
In addition to the exergy destruction rate,_E D ;k
,and the exergetic ef ?ciency,the thermodynamic evaluation of a system component is based on the exergy destruction ratio,y D,k ,which compares the
exergy destruction in the k th component with the fuel exergy
supplied to the overall system,_E
F ;tot :y D ;k
?_E D ;k
_E F ;tot
(5)
This ratio expresses the percentage of the decrease in the overall
system ef ?ciency due to the exergy destruction in the k th system component:
3tot
?_E P ;tot _E F ;tot ?1àX k
y D ;k à_E L ;tot _E
F ;k
(6)
Alternatively,the component exergy destruction rate can be compared with the total exergy destruction rate within the system,_E
D ;tot ,giving the ratio:y *D ;k ?
_E D ;k
_E
D ;tot (7)
_E D ;k is an absolute measure of the inef ?ciencies in the k th
component whereas 3k ,y D,k and y *D ;k
are relative measures of the same inef ?ciencies.In 3k the exergy destruction within a compo-nent is related to the fuel for the same component whereas in y D,k the exergy destruction within a component is related to the fuel for
the overall system.In y *
D ;k
the exergy destruction within a compo-nent is related to the exergy destruction in the overall system.
The characterization of fuel and product for a component is arbitrary but of capital importance in order to give an appropriate de ?nition of the exergetic ef ?ciency.The product is determined by considering the desired result produced by the component and fuel by the resources expended to generate the result.In this study,fuel and product were calculated considering physical and chemical exergies of the material stream separately based on the de ?nitions given in [18].
In the formulation of fuel and product for the cooling tower (Fig.3),it was necessary to split the physical and the chemical exergy of the stream of wet air in the respective parameters of the components:dry air (N 2,O 2,CO 2and Ar)and H 2O:
_E F ;CT ?_W FAN tà_E 33à_E 39átà_E 37à_E 38
á
t_E 35à_E 34t _E PH
air ;50à_E PH air ;51 t _E CH H 2O ;50à_E CH
H 2O ;51 (8)
_E P ;CT ?
_E CH air ;51à_E CH air ;50 t _E PH H 2O ;51à_E PH H 2O ;50
(9)
Herein,the exergies of the ?ow streams (Tables 2and 3)were calculated according to the de ?nitions given in [19].For the speci ?c physical exergy:
e PH ?eh àh 0TàT 0es às 0T(10)
where subscript 0represents environmental conditions.The physical exergy was obtained based on the thermodynamic prop-erties calculated by GateCycle [13].The values of the standard chemical exergy of chemical compounds were taken from [20].
The results of the thermodynamic analysis are shown in Tables 2and 3.
5.Results and discussion
Tables 4and 5show the exergy destruction,exergetic ef ?ciency and exergy destruction ratios for each main plant component.
The results are presented in descending order of the parameter y *D ;k ,which compares the exergy destruction in the k th component
444648505254560,06
0,08
0,10
0,12
0,14
0,16
0,18
0,20
0,22
Pressure [bar]
W[MW]
Fig.2.Gross cycle power (),net cycle power with cooling tower ()and net
cycle power with air cooled condenser (
),versus condensing pressure (45MW).
Fig.3.GateCycle schematic of a cooling tower.
A.M.Blanco-Marigorta et al./Energy 36(2011)1966e 19721969
with the exergy destruction in the overall process,_E
D ;tot .As result,this parameter provides an insight into the exergetic meaning of each of the components of the overall system.
Exergy destruction ratio in condenser working at 0.063bar and using a cooling tower represents only 6.8%of total exergy destruction whereas with an air cooled condenser it represents 25.5%of total exergy destruction.This result is mainly due to the huge amount of parasitic fan power required by the air cooled condenser to work under this pressure condition.Working at 0.2bar,both components (wet and dry condenser)present a comparable and high value of exergy destruction:32.73%the wet condenser and 31.11%the dry condenser.These values represent almost a third of the total exergy destroyed in the global system.
Taking into account all the components that integrate the wet cooling technology (condenser,cooling tower and pump)it is necessary to sum the exergy destroyed in all the components.In this case,the exergy destructed ratio amounts to almost 12%operating at 0.063bar and 37.2%operating at 0.2bar.As a result we can say that,from an exergetic point of view,the use of an air cooled condenser is not an ef ?cient solution working at low exit turbine pressures but it becomes more competitive at higher pressures.
Exergy destructed in remaining components is not especially in ?uenced by the use of different cooling technologies,apart from the condenser working pressure.The sequence followed by
different components regarding the value of y *D ;k
is similar in both operation alternatives.
Exergetic ef ?ciency of each component assesses the fuel exergy wasted in the component as exergy destruction.Related to this concept,Tables 4and 5show the following:
-The exergetic ef ?ciency of the cycle is similar using both Technologies and working with the two pressure operation alternatives in the condenser:approximately 70percent.
-Each component presents also a similar value of the exergetic ef ?ciency with both technologies and working under both condenser pressure conditions:0.063e 0.2bar.The most important difference is presented in condenser:working at 0.063bar the exergetic ef ?ciency of the wet condenser is 63.3%whereas the air cooled condenser presents an exergetic ef ?-ciency of 25.8%.Thermodynamic inef ?ciencies associated with heat transfer are caused by mismatched heat capacity rates of the two streams and by a ?nite minimum temperature
Table 2
Thermodynamic and exergetic data of streams for 0.063bar of condensing pressure.
_m
(kg/s)T (C)p (bar)_E j
(kW)_E j
(kW)_E j
(kW)1
60.08373.00100.0072,21012072,3302 6.25241.4633.486123126135353.83208.4818.5046,91310847,021453.83373.4016.5057,81110857,9195 2.70352.1213.992778527846 2.71254.59 6.182248522537 2.69186.44 3.0418******** 2.80108.24 1.171433614389 1.9673.990.37651.446551040.9637.050.0635518236331148.4237.050.0644.59971411248.4237.158.3885.74971821348.4262.698.28484975811448.4297.518.1815859716821548.42128.848.0830519731471660.08159.99 6.18607312061931760.08161.71103.00675912068791860.08189.68102.50921312093331960.08234.85102.0013,94112014,0622060.08309.00101.2024,34212024,4622160.08313.00101.0063,73712063,85722 6.25194.6833.38969.812982238.95166.7113.8999418101224 2.69102.51 2.9498.26510425 5.5067.69 1.0764.711176267.4642.150.2714.5215
29
60533.40393.0015.80149,96819,854,63320,004,60161533.40381.0014.20140,70619,854,63319,995,33962533.40320.0012.6098,38319,854,63319,953,01763533.40301.0011.8086,68719,854,63319,941,3206468.50393.0015.8019,2562,549,7612,569,01665
68.50225.0013.5060502,549,7612,555,811Cooling tower 332869.2236.23 1.88279057348524340.0636.250.950.050610.1150.1653532.8632.850.052002662068362836.1928.830.95293.4566859613765.7327.00 1.00 2.0241311333831.8128.790.95 3.226467392869.2028.790.95290.557346024402869.2028.80 1.88560.257346294501791.1728.050.952912,38412,41351
1824.04
32.850.95418412,28116,465Air cooled condenser 5013,98928.050.9522496,73096,9535113,989
34.58
0.95
2176
96,730
98,906
A.M.Blanco-Marigorta et al./Energy 36(2011)1966e 1972
1970
difference of D T min .In an air cooled condenser,the mismatch between the heat capacity rates of the two streams is high and these inef ?ciencies are dif ?cult to avoid.Working at 0.2bar,the exergetic ef ?ciency of the air condenser improves,even while remaining a low value:40%,and the exergetic ef ?ciency of the wet condenser becomes considerably worse (27.5%)due to the increase in the temperature difference between inlet and outlet streams and to the increase in refrigeration water mass ?ow rate.
Apart from the condenser,it is interesting to add further comments about the results provided by the exergetic analysis of the rest of the components of the plant:
-Exergetic ef ?ciency of the steam turbines is similar operating under both pressure conditions (89e 90%).Pump s exergetic ef ?ciency is within the range of 74%for condensate pump,and 87%for feedwater pump where p COND ?0.063bar for both.Exergy destruction here is caused basically by friction.There-fore only an increase in the isentropic ef ?ciency can increase its exergetic ef ?ciency.
-Heat exchangers in the heat recovery steam generator present high exergetic ef ?ciency values under both condenser pressure conditions:between 82%,for the economizer,and 94%,for the superheater.Herewith,irreversibilities are mainly caused by heat transfer between material streams entering and exiting the heat exchanger.A small percentage is produced by pressure loss and heat loss with the surroundings.The high exergetic ef ?ciency values presented in Tables 4and 5are logical according to the similar heat capacity rates and the small value of the minimum temperature difference.
-The feedwater heaters and the deaerator present consistent values of exergetic ef ?ciency:the lower the minimum temperature difference,the lower the exergy destruction and the higher the exergetic ef ?ciency.
The exergy destruction ratio,y D ,gives a useful reference in comparison of components of different systems with similar fuel exergy.Regarding to this value,through Tables 4and 5it is possible to indicate:In the process operating with a condenser pressure of 0.063bar,the exergy destructed in the wet condenser represents only 1.7%of the fuel of the overall system while the destruction using an air cooled condenser is higher than 7%.Operating at
Table 3
Thermodynamic and exergetic data of streams for 0.2bar of condensing pressure.
_m
(kg/s)T (C)p (bar)_E j
(kW)_E j
(kW)_E j
(kW)1
60.08373.00100.0072,21012072,3302 6.25241.4633.486123126135353.83208.4818.5046,86210846,970453.83373.4016.5057,81110857,9195 2.70352.1213.992778527846 2.71254.59 6.182248522537 2.70185.81 3.0418******** 2.81106.83 1.1714326143890.2073.990.3766.80.467.21042.7160.060.2010,2828510,3681148.4260.060.20387974831248.4260.178.38429975251348.4262.698.28484975811448.4297.518.1815859716821548.42128.848.0830519731471660.08159.99 6.18607312061931760.08161.71103.00675912068791860.08189.68102.50921312093331960.08234.85102.0013,94112014,0622060.08309.00101.2024,34212024,4622160.08313.00101.0063,73712063,85722 6.25194.6833.3897012982238.95166.7113.8999418101224 2.70102.51 2.9498510425 5.5067.69 1.0765117626 5.7065.170.2759
11
71
60533.40393.0015.80149,96819,854,63320,004,60161533.40381.0014.20140,70619,854,63319,995,33962533.40320.0012.6098,38319,854,63319,953,01763533.40301.0011.8086,68719,854,63319,941,3206468.50393.0015.8019,2562,549,7612,569,01665
68.50
225.0013.5060502,549,7612,555,811Cooling tower 332254.5038.78 1.88317145057676340.0538.800.950.070.100.173534.0235.580.062786682854362220.4128.830.95230443746673765.7327.00 1.0021311333833.9828.780.9536871392254.5428.780.9522745054732402254.5028.78 1.8843845054943501407.4728.050.952397329754511441.49
35.58
0.954987964814,635Air cooled condenser 504075.9928.050.956528,18428,249514075.9951.02
0.95
4518
28,184
32,701
Table 4
Exergy destruction,exergetic ef ?ciency,and exergy destruction ratios for each main plant component;p COND ?0.063bar.
_E
F (kW)_E P (kW)_E D (kW)3
y D (%)y *D ;k ;tower (%)y *D ;k ;air (%)LP steam turbine e ST2e 3
45,31140,02352880.883 6.9128.0623.97Air cooled condenser e ACC17583195956240.2587.3525.50Evaporator e EVAP142,32339,39629270.931 3.8315.5313.27Reheater e SPHT2
13,20610,89823080.825 3.0212.2510.46HP steam turbine e ST119,17417,35518190.905 2.389.658.25Economizerr e ECON111,69710,40012970.889 1.70 6.88 5.88
Wet condenser e CND13521223012910.633 1.69 6.85Cooling tower e CT113,16912,09510740.918 1.40 4.49Superheater e SPHT1
926284727900.915 1.03 4.19 3.58Feedwater heater 5e FWH5515347284250.9180.56 2.26 1.93Feedwater heater 2e FWH2146611013650.7510.48 1.94 1.65Feedwater heater 1e FWH17023983030.5680.40 1.61 1.37Feedwater heater 4e FWH4275424543000.8910.39 1.59 1.36Feedwater heater 3e FWH3174114652760.8410.36 1.46 1.25Deaerator e DA1
206318442190.8940.29 1.160.99Feedwater pump e PUMP178********.8700.130.550.47Refrigeration pump e PUMP3316270460.8540.060.24Condensate pump e PUMP256
41
14
0.7410.02
0.08
0.07
Total with cooling tower
76,48655,72518,8460.754Total with air cooled condenser
76,486
52,471
22,058
0.712
A.M.Blanco-Marigorta et al./Energy 36(2011)1966e 1972
1971
pressure condenser of 0.2bar,terms are reversed:wet condenser is more inef ?cient:it destroys 9.44%of the fuel exergy whereas in the air cooled condenser the exergy destruction ratio is only one point higher as previously.The rest of the components show no note-worthy tendencies.
6.Conclusions and future work
The paper presents the exergetic comparison of dry and wet cooling technologies for the Rankine cycle of a solar thermal power plant.
Exergy analysis is a useful tool to locate and evaluate the ther-modynamic inef ?ciencies of the analyzed process.The third part of the inef ?ciencies is located in the heat rejection process.Other part is located in the steam generation process and another in the expansion process.The condenser is the component where more exergy of the total fuel exergy is wasted as exergy destruction.Related with the total fuel exergy,at the condensing pressure of 0.063bar,the air cooled condenser destroys four times the exergy destroyed in the condenser with cooling tower.At 0.2bar both con ?gurations destroy a similar amount of exergy.From an exer-getic point of view,the use of an air cooled condenser is not an ef ?cient solution to working at low exit turbine pressures.It becomes,however,more competitive at higher pressures.
This paper is a part of a series of works that analyzed dry and wet cooling technologies for the Rankine cycle of a solar thermal power plant.An advanced exergetic analysis will also be conducted to evaluate the avoidable and unavoidable part of the exergy destruction as well as the mutual in ?uence of the components of the process.An exergoeconomic analysis will also be performed to evaluate the cost of the inef ?ciencies and the real potential for reducing them.Acknowledgments
The authors want to thank Cobra Instalaciones y Servicios S.A.e Sener Ingeniería y Sistemas S.A.e C.T.Andasol-1UTE Ley 18-1982for the technical information provided to perform this study.
References
[1]Kelly B.Nexant parabolic trough solar power plant system analysis,Subcon-tract report NREL/SR-550-40163.S.Francisco,California:National Renewable Energy Laboratory.Available from:https://www.360docs.net/doc/0810350282.html,/csp/troughnet/pubs_power_plant.html#cooling;July 2006.
[2]Szargut J,Morris DR,Steward FR.Exergy analysis of thermal,chemical and
metallurgical processes.New York:Hemisphere Publishing Corporation;1988.[3]Tsatsaronis G,Cziesla F.Exergy and thermodynamic analysis.Six articles
published in topic “Energy ”in Encyclopedia of Life Support Systems (EOLSS),developed under the auspices of UNESCOAvailable from:.Oxford,UK:Eolss Publishers
[4]Sengupta S,Datta A,Duttagupta S.Exergy analysis of a coal-based 210MW
thermal power plant.International Journal of Energy Research 2007;31:14e 28.[5]Habib MA,Zubair SM.Second-law-based thermodynamic analysis of regen-erative-reheat Rankine-cycle power plants.Energy 1992;17:295e 301.
[6]Dincer I,Muslim H.Thermodynamic analysis of reheat cycle steam power
plants.International Journal of Energy Research 2001;25:727e 39.
[7]Tsatsaronis G,Winhold M.Exergoeconomic Analysis and evaluation of energy
conversion plants.Part II e analysis of a coal-?red steam power plant.Energy e The International Journal 1985;10:81e 94.
[8]Kwak H-Y,Kim D-J,Jeon J-S.Exergetic and thermoeconomic analyses of power
plants.Energy 2003;28:343e 60.
[9]Aljundi IH.Energy and exergy analysis of a steam power plant in Jordan.
Applied Thermal Engineering 2009;29:324e 8.
[10]Singh N,Kaushik SC,Misra RD.Exergetic analysis of a solar thermal power
system.Renewable Energy 2000;19:135e 43.
[11]Gupta MK,Kaushik SC.Exergy analysis and investigation for various feed
water heaters of direct steam generation solar e thermal power plant.Renewable Energy 2010;35:1228e 35.
[12]Kaushik SC,Abhyankar YP,Bose S,Mohan S.Exergoeconomic evaluation of
a solar thermal power plant.International Journal of Sustainable Energy 2001;21:293e 314.
[13]GateCycle ?version 5.61.0.r.The General Electric Company;2005.
[14]Engineering equation solver for Microsoft Window Operating Systems.
Academic version.S.A.Klein:F Chart Software;1992e 2008.
[15]Wagner W,Cooper JR,Dittmann A,Kijima J,Kretzschmar HJ,Kruse A,et al.The
IAPWS industrial formulation 1997for the thermodynamic properties of water and steam.Journal of Engine Gas,Turbines and Power 2000;122:150e 70.
[16]Chase MW,Davies CA,Downney Jr JR,Frurip DJ,Mc Donald RA,Syverud AN.
JANAF thermochemical tables.Journal of Physical and Chemical Reference Data 1985;14(1).3rd ed.
[17]NIST chemistry webbook e National Institute of Standards and Technology.
https://www.360docs.net/doc/0810350282.html,ernment.Available from:
calculating ef ?ciencies and costs in thermal systems.Energy 2006;31:1257e 89.
[19]Tsatsaronis G,Cziesla F.Thermoeconomics.In:Encyclopedia of physical
science and technology.3rd ed.,vol.16.Academic Press;2002.p.659e 80.[20]Diedrichsen C.Referenzumgebungen zur berechnung der chemischen Exergie.
Düsseldorf:VDI Verlag;1991.Number 50in Fortschr.-Ber.VDI,Rhi 19.
Table 5
Exergy destruction.exergetic ef ?ciency and exergy destruction ratios for each main plant component;p COND ?0.2bar.
_E
F (kW)_E P (kW)_E D (kW)3
y D (%)y *D ;k ;tower (%)y *D ;k ;air (%)Wet condenser e CND1
9955273372220.2759.4432.73Air cooled condenser e ACC111,140445566850.4008.7431.11LP steam turbine e ST2e 339,16434,94642180.892 5.5119.1219.63Evaporator e EVAP142,32339,39629270.931 3.8313.2613.62Reheater e SPHT2
13,20610,94922570.829 2.9510.2310.50HP steam turbine e ST119,22417,35518690.903 2.448.478.70Economizer e ECON111,69710,40012970.889 1.70 5.88 6.03Cooling tower e CT113,74312,7639800.929 1.28 4.25Superheater e SPHT1
926287425200.9440.68 2.36 2.42Feedwater heater 5e FWH5515347284250.9180.56 1.93 1.98Feedwater heater 2e FWH2146611013650.7510.48 1.65 1.70Feedwater heater 4e FWH4275424543000.8910.39 1.36 1.40Feedwater heater 3e FWH3174114652760.8410.36 1.25 1.28Desgasi ?cador e DA1
206318442190.8940.290.99 1.02Feedwater pump e PUMP178********.8700.130.470.48Refrigeration pump e PUMP3248211380.8490.050.17Feedwater heater e FWH17255170.7650.020.080.08Condensate pump e PUMP255
42
14
0.7550.02
0.06
0.06
Total with wet condenser
76,48650,81423,0460.699Total with air cooled condenser
76,486
50,271
21,491
0.719
A.M.Blanco-Marigorta et al./Energy 36(2011)1966e 1972
1972