连铸连轧法生产铜杆技术
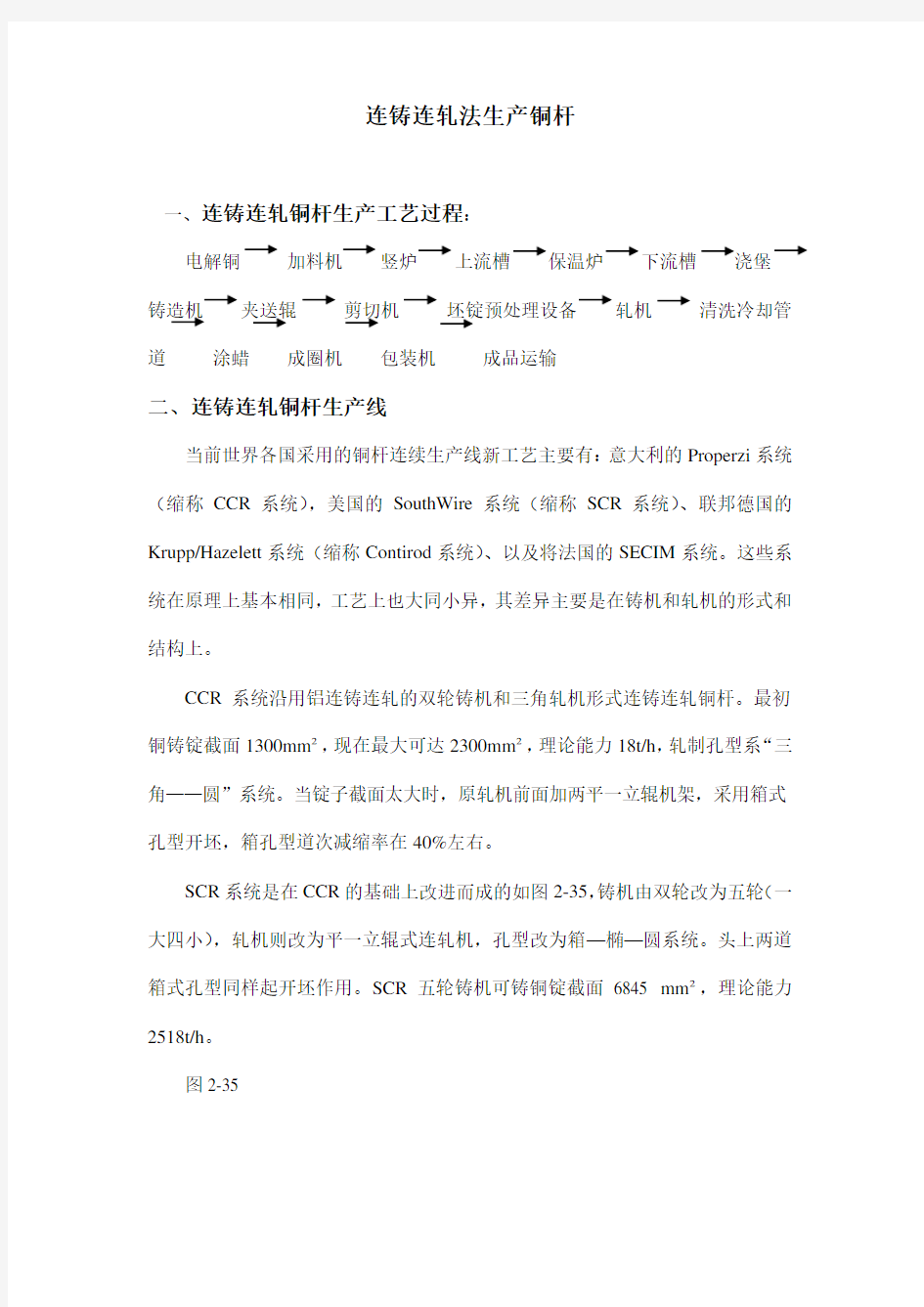
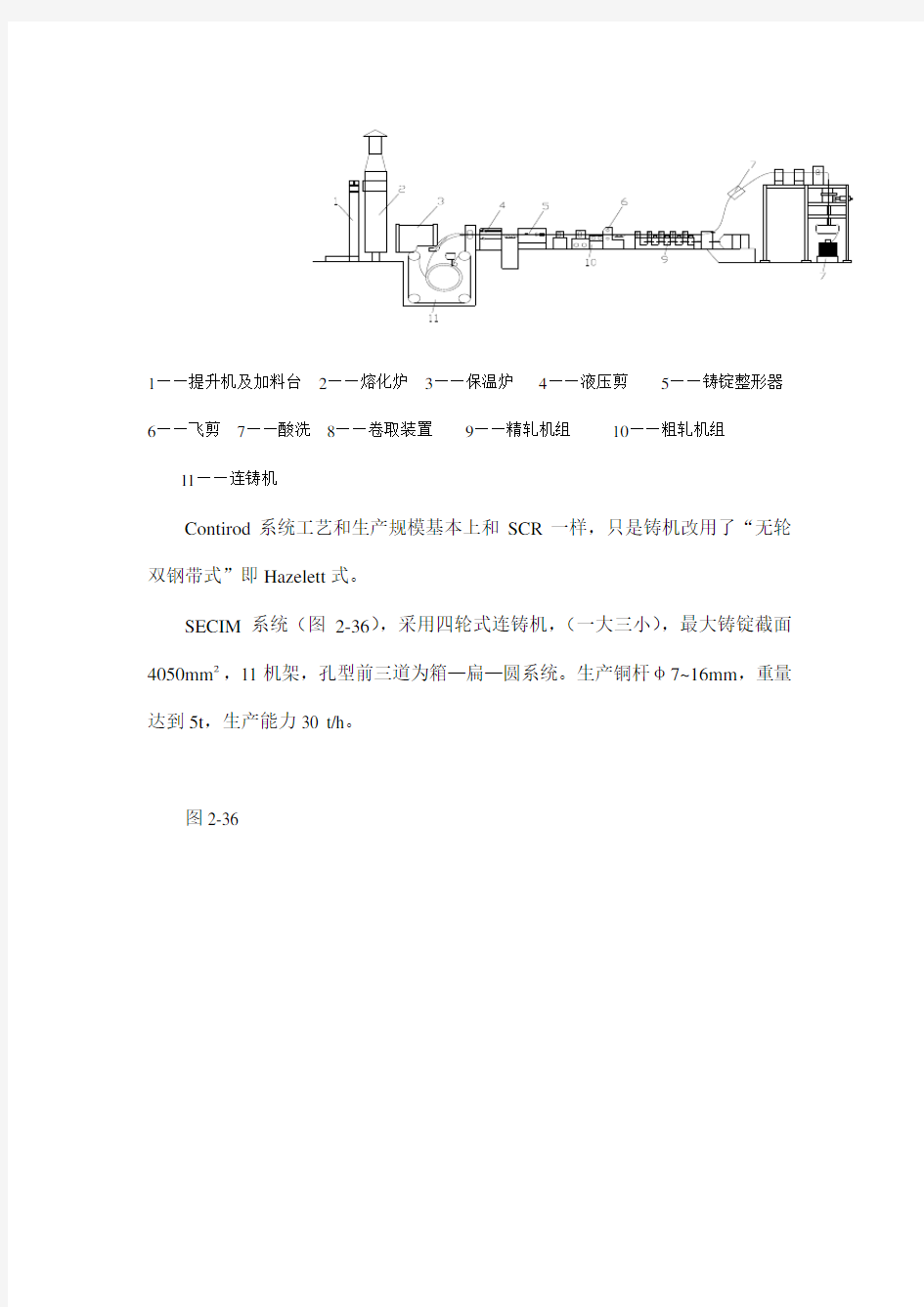
连铸连轧法生产铜杆
一、连铸连轧铜杆生产工艺过程:
电解铜加料机竖炉上流槽保温炉下流槽浇堡
铸造机夹送辊剪切机坯锭预处理设备轧机清洗冷却管道涂蜡成圈机包装机成品运输
二、连铸连轧铜杆生产线
当前世界各国采用的铜杆连续生产线新工艺主要有:意大利的Properzi系统(缩称CCR系统),美国的SouthWire系统(缩称SCR系统)、联邦德国的Krupp/Hazelett系统(缩称Contirod系统)、以及将法国的SECIM系统。这些系统在原理上基本相同,工艺上也大同小异,其差异主要是在铸机和轧机的形式和结构上。
CCR系统沿用铝连铸连轧的双轮铸机和三角轧机形式连铸连轧铜杆。最初铜铸锭截面1300mm2,现在最大可达2300mm2,理论能力18t/h,轧制孔型系“三角——圆”系统。当锭子截面太大时,原轧机前面加两平一立辊机架,采用箱式孔型开坯,箱孔型道次减缩率在40%左右。
SCR系统是在CCR的基础上改进而成的如图2-35,铸机由双轮改为五轮(一大四小),轧机则改为平一立辊式连轧机,孔型改为箱—椭—圆系统。头上两道箱式孔型同样起开坯作用。SCR五轮铸机可铸铜锭截面6845 mm2,理论能力2518t/h。
图2-35
1——提升机及加料台2——熔化炉3——保温炉4——液压剪5——铸锭整形器6——飞剪7——酸洗8——卷取装置9——精轧机组10——粗轧机组11——连铸机
Contirod系统工艺和生产规模基本上和SCR一样,只是铸机改用了“无轮双钢带式”即Hazelett式。
SECIM系统(图2-36),采用四轮式连铸机,(一大三小),最大铸锭截面4050mm2,11机架,孔型前三道为箱—扁—圆系统。生产铜杆φ7~16mm,重量达到5t,生产能力30 t/h。
图2-36
1——熔化炉2——保温炉3——四轮式连铸机4——去切边角装置5——予处理装置6——粗轧机7——中间剪刀8——精轧机9——清洗管道10——自动绕杆机
三、主要工艺设备
1.竖炉
竖炉熔铜炉是由美国熔炼公司研究设计的,它是用来连续熔化电解铜,也可以加入一些清洁的废铜屑,这种竖炉简称ASARCO,它具有生产效率高,控制方便不需要吹氧去硫和插木还原,就能获得合格的铜液。在技术,经济上的优越性是反射熔铜或电炉熔铜不能相比的,其主要特点归纳如下:
(1)生产工艺简单,不需要“吹氧去硫”及“插木还原”
(2)生产质量高,由于炉内保持微还原性气氛,铜液含氧量可以控制在很低的范围内;
(3)生产效率高
(4)占地面积小
(5)控制方便,容易开、停炉;
(6)劳动条件好、无公害、金属回收率高。
(7)炉子热效能高,燃料消耗少,还可节约大量木材。
采用小车式提升加料机或叉车加料。要求燃料无硫或含流量很低,目前使用的燃料有天然气,甲烷,丙烷,丁烷,石油,液化气和石脑油等。
近年来许多工厂,对ASARCO竖炉又作了某些改进和完善,如电解铜或铜屑的输送和装入炉的自动控制,含氧量的连续测定,空气与燃气的预混合系统,测氢系统的连续监测比例自动调正,包括用真空导管取样至控制进行快速气体分析等。图2-37为这种熔铜炉的剖面图。
图2-37
薄板坯连铸连轧(3)—邯钢CSP
薄板坯连铸连轧(3)—邯钢CSP https://www.360docs.net/doc/0919336331.html, 2006-12-19 邯钢薄板坯连铸连轧生产线于1997年11月18日开工建设,1999年12月10日生产出第一卷热轧卷板,建设工期历时两年零一个月。该生产线引进德国西马克90年代世界先进技术,总生产能力为250万t。 生产线的特点 1 主要工艺特点 邯钢薄板坯连铸连轧生产线主要包括薄板坯连铸机、1号辊底式加热炉、粗轧机(R1)、2号辊底式加热炉、精轧机组(F1~F5)、带钢层流冷却系统和卷取机 。产品规格为1.2~20mm厚、900~1680mm宽的热轧带钢钢卷。钢卷内径为762mm,外径为1100~2025mm,最大卷重为33.6t,最大单重为20kg/mm。工艺流程为:100t氧气顶底复吹转炉钢水—LF钢水预处理—钢包—中间包—结晶器—二冷段— 弯曲/拉矫—剪切—1号加热炉—除鳞—粗轧(R1)—2号加热炉—除鳞—精轧[F1~ F5(F6)]—冷却—卷取—出卷—取样—打捆—喷号—入库。 图邯钢CSP工艺流程示意图 2 主要技术参数
1)薄板坯连铸机 该连铸机为立弯式结构。中间包容量36t,结晶器出口厚度70mm,结晶器长度1100mm,铸坯厚度60~80mm,铸坯宽度900~1680mm,坯流导向长度9325~9705mm,铸速(坯厚70mm)低碳保证值最大4.8m/min、高碳保证值最大4.5m/min、最小2.8m/min,弯曲半径3250mm。 2)加热炉 该生产线包括两座辊底式加热炉,位于粗轧机前后。1号加热炉炉长178.8m,由加热段、输送段、摆动段、保温段组成,炉子同时具有加热、均热、储存(缓冲)的功能,可容纳4块38m长的板坯,单机生产的缓冲时间20~30min,最高炉温1200℃,铸坯入炉温度870~1030℃,出炉温度1100~1150℃。2号加热炉炉长66.8m,由一段构成,主要起均热、保温作用,最高炉温1150℃,铸坯最高入炉温度1120℃,最高出炉温度1130℃。加热炉燃料为混合煤气,烧嘴型式为热风烧嘴。 3)粗轧机 粗轧机为单机架四辊不可逆式轧机,其作用是将铸坯一道轧成所需坯厚。最大轧制力42000kN,工作辊尺寸 880/790mm×1900mm,支撑辊尺寸 1500/1350×1900mm,主电机功率8300kW,轧出坯厚33.0~52.5mm。 4)精轧机组 精轧机组有五架四辊不可逆式轧机(F1~F5),剪机为液压曲柄连杆式,除鳞为高压水除鳞,最大轧制力为4200kN,主电机功率均为8300kW,机架间距5500mm,F5最大出口速度12.6m/s,板带厚1.2~20mm,板带宽900~1680mm,终轧温度900~950℃。 5)冷却区 冷却方式为层流冷却,在一定时间内将带钢由终轧温度900~950℃冷却到550~650℃。冷却区长度为43200mm,另有一个4800mm的空冷段。最大水量约为5240m3/h,水压为0.07MPa(喷淋区水压为1MPa)。
连铸连轧法生产铜杆---图
连铸连轧法生产铜杆 一、连铸连轧铜杆生产工艺过程: 电解铜加料机竖炉上流槽保温炉下流槽浇堡 铸造机夹送辊剪切机坯锭预处理设备轧机清洗冷却管道涂蜡成圈机包装机成品运输 二、连铸连轧铜杆生产线 当前世界各国采用的铜杆连续生产线新工艺主要有:意大利的Properzi系统(缩称CCR系统),美国的SouthWire系统(缩称SCR系统)、联邦德国的Krupp/Hazelett系统(缩称Contirod系统)、以及将法国的SECIM系统。这些系统在原理上基本相同,工艺上也大同小异,其差异主要是在铸机和轧机的形式和结构上。 CCR系统沿用铝连铸连轧的双轮铸机和三角轧机形式连铸连轧铜杆。最初铜铸锭截面1300mm2,现在最大可达2300mm2,理论能力18t/h,轧制孔型系“三角——圆”系统。当锭子截面太大时,原轧机前面加两平一立辊机架,采用箱式孔型开坯,箱孔型道次减缩率在40%左右。 SCR系统是在CCR的基础上改进而成的如图2-35,铸机由双轮改为五轮(一大四小),轧机则改为平一立辊式连轧机,孔型改为箱—椭—圆系统。头上两道箱式孔型同样起开坯作用。SCR五轮铸机可铸铜锭截面6845 mm2,理论能力2518t/h。 图2-35 1——提升机及加料台2——熔化炉3——保温炉4——液压剪5——铸锭整形器6——飞剪7——酸洗8——卷取装置9——精轧机组10——粗轧机组11——连铸机 Contirod系统工艺和生产规模基本上和SCR一样,只是铸机改用了“无轮双钢带式”即Hazelett式。 SECIM系统(图2-36),采用四轮式连铸机,(一大三小),最大铸锭截面4050mm2,11机架,孔型前三道为箱—扁—圆系统。生产铜杆φ7~16mm,重量达到5t,生产能力30 t/h。
铸铜工艺流程
铸铜工艺流程 铸铜等铸造类雕塑首先是泥塑的塑造,然后翻制阴模,翻制阴模后再翻制成阳模,实际上是一个材料转换的过程,即从可塑性泥制品转换到石膏和玻璃钢进行定型、最后送到专业铸造厂进行最后的铸造过程。每件铸铜艺术品都是需要经过最少11道复杂严谨的工序制作而成,这些工序中既有传统手工艺的痕迹,也有精密铸造的现代技术精彩所在。。。。 工艺流程之一:泥塑(每件产品的前身都需要一个泥塑原型,泥塑都是经过雕塑师在原创设计稿的基础上反复揣摩、推敲之后进行的再创作,泥塑的造型好坏、神韵的体现与否、意图的表达呈现直接影响今后的产品好坏,所以优秀的泥塑离不开优秀的雕塑师) 第一步天然特殊胶泥备料筛选,喷水醒泥48小时以上,圆雕焊接雕塑钢筋造型骨架,在骨架上缠绕十字型木条托泥装置,雕塑骨架上大间隙铺设金属网,可减少用泥量减少总重量保证雕塑不垮塌。如是浮雕需木工板铺设底板在板上每隔15公分钉钉子,钉子钉入一半另外一半露出方便挂泥,另在钉子上纵横缠绕细铁丝同样方便挂泥料。 第二步上大泥覆盖雕塑造型。上泥完毕一边用木槌砸实一边补平泥间空袭。全部上泥后对大造型进行不断的调整。造型不准需要返工对骨架进行休整直到满意,以上必须由专业雕塑师来完成。从此阶段开始雕塑必须经常喷水保持不开裂,半途公休要覆盖塑料薄膜进行保湿直到雕塑模完成后。 第三部塑形,专业雕塑师来完成,塑形过程雕塑师中随时喷水随时塑造,具体细节其它工序简略。 第四步雕塑大型完成,通知甲方对大造型进行审核和提出意见或修改。继续不断的推敲调整和细节塑造达到完美,全部完成造型后进行整体推光泥塑,使用刮片进行推光。 第五步进入翻制阶段,在泥塑上用切片进行区块模具分割设计,然后喷洒肥皂水作为隔离防护。专业翻制技师配比石膏浆上于雕塑覆盖,具体石膏浆外层内层不同的水配比量由专业人员掌握和来完成。待石膏硬化干燥后开始脱模,脱模前要在区块上固定抓手,抓手用石膏麻木桩来制作。 第六步脱模后去掉分块模具上的残留泥,完毕后对石膏模进行细致修模,补磨。然后用金属铜网进行打磨。 第七部上玻璃钢,调配好树脂加入催化剂固化剂和填料与显色剂等。头层树脂上浆,二层配合玻璃丝布树脂一同上浆,一般需要三到五层上浆过程。形成厚度根据雕塑选择。 第八步拼合玻璃钢分体模块进行组合。拼合后进行缝隙的补平和加固,内部要建立永久性钢筋支持体系骨架。最后进行打磨,配合不同砂纸型号进行粗磨细磨水磨,大部分必须手工完成机器打磨无法圆润自然也难以完全无痕迹,所以必须手工砂带纸打磨。 工艺流程之二:矽xi胶开模(矽胶,英文名Silicon,此原料通常用作制作模具,精致度高,哪怕发丝粗细都可体现出来)
生产工艺流程及控制
第五章. 生产工艺流程及控制 本设计中的各个参数及控制参考特雷卡电缆有限公司技术部有关技术文件,相关标准和生产实践总结. 一.拉制 此电缆所用圆铜杆有两种规格PE线芯用TR2.58mm和主线芯及N线芯用TR2.25mm,均在十三模大拉机LHD3/13上生产. a: TR2.58mm 原材料用的为TR8.0mm的软铜杆,其拉制配模为: 8.0, 7.00, 6.04, 5.26, 4.62, 4.08, 3.63, 3.22, 2.86, 2.60 偏差为±0.03 mm.之所以最后一道模具的标称值比实际生产值大0.02mm,是因为在拉制退火过程中由于张力的存在会引起一定的缩径,只要控制好收线张力就行了.生产中的各个主要参数可设定如下: 退火电压: 44V 收线速度: 8m/s 收线张力: 0.25MPa 退火蒸汽保护: 0.1~0.6MPa 收线装置: 收线盘: PN500 收线框: Φ800×Φ500×1250 建议使用PN500的收线盘,为了以后的绞丝生产. b: TR2.25mm 进线直径为Φ8.0软铜杆,配模值为: 8.0, 6.70, 5.71, 4.88, 4.21, 3.66, 3.21, 2.81, 2.57, 2.27
其它参数和控制如下: 退火电压: 45V 收线速度: 8m/s 收线张力: 0.25MPa 退火蒸汽保护: 0.1~0.6MPa 同上建议使用PN500的收线盘,为了后道工序. 在断线或铜杆首尾焊接时要保证接头处焊接牢固,以免生产中断线给生产带来不便,降低生产率(两铜杆要融化均匀,无杂质,然后加热重新结晶后表面处理平整方可生产). 生产中常见的质量问题的原因及处理方法如下:
无氧铜杆连铸连轧生产线
无氧铜杆连铸连轧生产线 1.机组用途及组成 本机组是采用连铸连轧的工艺方法生产φ8mm低氧光亮铜杆,原材料为电解铜。本生产线由一台16吨/小时熔铜竖炉、一台12吨回转式保温炉、五轮式连铸机、牵引机、滚剪、校直刨角机、打毛机、连轧机、收杆装置、电控系统等组成。 2.简单工艺流程 电解铜──→竖炉────→回转式保温炉→流槽(熔体保护)→浇煲→连铸 机(铸坯)→铸坯处理装置(滚剪→校直→去角→除屑)→进轧装置(主动送料)→连轧机(轧杆)→铜杆冷却装置(表面还原)→连续绕杆装置(预成型)→梅花式收线装置(铜杆成卷) 3. 生产线主要技术参数 1). 生产铜杆直径:φ8 mm 2). 生产能力:14-16 t/h 3). 成圈重量: 3.0-5.0 t 4). 主要设备总尺寸: 40×7.8×6.1 m (不包括熔铜炉及循环冷却过滤系 统) 5). 主要设备总重量: 85 吨(不包括熔铜炉) 6). 主要设备总功率: 600 kW(不包括熔铜 炉) 4 .设备技术规范及组成 4.1熔铜炉一套 4.1.1熔化炉型:竖式冲天炉 4.1.2熔化炉最大铜熔化能力:16吨/小时 4.1.3熔铜炉上料机构最大装载量:5吨 4.1.4熔铜炉进料方式:提升式 4.1.5烧嘴单体最大燃烧能力:60万大卡/小时
4.1.6熔铜炉烧嘴数量:15只 4.1.7烧嘴冷却方式:水冷 4.1.8烧嘴点火方式:自动 4.1.9使用燃料:天然气、液化气、城市煤气 4.1.10保温炉炉型:液压回转式 4.1.11保温炉有效容量:12吨 4.1.12保温炉最高倾力角度:>70o 4.1.13烧嘴单体最大燃烧能力:60万大卡/小时 4.1.14保温炉烧嘴数量:1只 4.1.15燃烧控制方式:比例燃烧,具有保护装置 4.1.16燃气阀检漏方式:手动/自动 熔铜炉包括冲天式铜熔化炉、回转式保温炉、上下流槽、燃烧控制系统等四大部分。具有熔化速度快、铜水含氧量低、流量连续可调、铜水温度独立可控、单位铜水燃气消耗量低等特点。 ①冲天式铜熔化炉(竖炉) 熔化炉简称竖炉,由炉底、炉身、碰撞保护块、加料口、上料机构、烟囱、炉衬和冷却风机等部分组成。 炉底、炉身由优质钢板和型钢制作,炉底采用25mm钢板,中间用槽钢加固,使整个炉底可以承受100吨电解铜板的重量而不变形;炉身用16mm钢板圈成桶体,炉体内贴一层硅酸铝纤维毯,可大大降低炉壁温度,中间砌筑高铝耐火砖,最内层炉衬是直接触火焰和铜水的,采用SiC砖砌筑,荷重软化温度可达1700度,保证了炉衬的使用寿命。SiC砖采用纯度大于80%的SiC混合特殊的高温粘接剂,经压机预先压制成弧形砖,通过高温焙烧,使SiC砖形成半烧结状态,一方面增加了SiC砖的强度,便于运输、搬运、砌筑,同时在砌筑完成后,通过第二次烘烧,使竖炉内衬形成一个坚固的整体,使整个炉衬的强度大为提高。 炉体上部是防撞保护块,防止在加料时铜板撞在炉衬上,引起炉衬脱落破损甚至内衬倒塌。防撞保护块由耐热钢整体浇注而成,整体强度高,具有耐高温、耐冲击、不易脱落等优点,使用寿命长,可有效保护加料时铜板对炉身的冲击。 加料口设计在竖炉的上方,这种加料方式可以使铜板从炉底一直堆放到炉体加料口,延长了烧嘴
无氧铜生产工艺流程.
第四章工艺技术方案 4.1工艺技术方案 本项目采用的原材料为含铜量99%的电解铜,选用目前国内先进的蓄热式熔化炉和中频炉,用上引法连铸工艺方法生产氧的含量不大于0.02%,杂质总含量不大于0.05%,含铜量99.5%以上无氧铜杆。 4.2工艺流程简述 1、生产准备 本项目使用的电解铜在江西省内购买。
图4-1 项目生产工艺流程图 2、上引法连铸工艺流程 本项目采用上引法连铸工艺生产无氧铜杆。上引法连铸铜杆
的基本特点是“无氧”,即氧含量在10ppm以下。 上引法与连铸连轧和浸涂法相比,其特点是: 1)由于拉扎工艺和铸造工艺不是连续的,拉扎是在常温下进行的,不需要气体保护,钢材也不会被氧化。因此设备投资小,厂房布置也灵活。 2)单机产量变化范围大,年产量可以从几百吨到几万吨,可供不同规模的厂家选用不同型号的上引机组。此外,由于连铸机是多头的,可以很容易的通过改变铸造规格(铸杆直径),来改变单位时间的产量,因此其产量可视原材料的供应情况和产品的需求情况来确定,便于组织生产、节约能源。 3)只需更换结晶器和改变石墨模的形状,即可生产铜管、铜排等异型铜材,并可在同一机器上上产不同规格、品种的铜材,灵活机动,这是上引法的中最大特点。 上引法连铸工艺流程:原料通过加料机加入融化炉进行熔化、氧化、扒渣处理后,熔融的铜液经过一段时间的静置还原脱氧并达到一定的温度后,通过有CO气体保护的流槽经过渡腔(铜液在此进一步还原脱氧、清除渣质),进而平稳的流入中频炉保温静置,铜液的温度由热电偶测量,温度值由仪表显示,温度控制在1150℃±10℃。连铸机固定于中频保温炉的上方,连铸机铜液在结晶器中快速结晶连续不断地生产出铜杆,最后经双头挠杆机等辅助设备装盘成产品。 ⑴加料:原料一般用加料机加入,炉头多加、炉尾少加。加
电解铜箔电解液制造工艺流程
1.电解铜箔生产工艺 电解铜箔自20 世纪30 年末开始生产后,被用于电子工业,随着电子工业的发展,电解铜箔的品质在不断提高,其制造技术也在快速发展,各铜箔生产企业及相关研究单位对电解铜箔制造技术的研究也取得了相当大的进步,形成多家多种电解铜箔制造技术,各企业生产电解铜箔的关键技术千差万别,但无论关键技术及其具体工艺区别有多大,作为电解铜箔制造的工艺过程都大致包括电解液制备、原箔制造、表面处理、分切加工以及相关的检测控制、附属配备等工序。基本工艺流程如图5-1-1 。 5.11工艺流程 2.电解液的制备 电解液制备是电解铜箔生产的第一道工序,主要就是将铜料溶解成硫酸溶液,并经一系列过滤净化,制备出成分合格、纯净度很高的电解液。电解液质量的好坏,直接影响着铜箔产品品质的好坏,不但影响铜箔的内在质量,还影响铜箔外观质量。因此,必须严格控制溶铜造液过程所用的原料辅料,还要严格控制电解液制备的生产设备和操作过程。 作为制备电解液过程,所用的原料有电解铜、裸铜线、铜元杆、铜米等。要求原料含铜纯度必须达到99.95% 以上,铜料中各种杂质如Pb 、Fe、Ni 、As 、Sb 、AI 、S 及有机杂质等必须符合GB 4667-1997《电解阴极铜》国家标准中一号铜要求。硫酸作为一种重要的材料,生产过程中必不可少,其质量也要达到国家标准化学纯级技术要求。 (1).几种常见的电解液制备工艺流程 第一种流程
第二种流程 第三种流程
第四种流程 3. 电解液制备过程 上面仅列举了4 种有代表性的电解液制备工艺流程,除此之外,由于各铜箔生产企业技术水平、设备条件、配套能力等区别,以及生产铜箔档次要求的不同,在电解液制备循环方式上都有一定的区别。虽然电解液循环方式不同,但其机理都是一样的,都包含有铜料溶解、有机物去除、固体颗粒过滤、温度调整、电解液成分调整等作用和目的。 首先将经过清洗的铜料及硫酸、去离子水加入到具有溶解能力的溶铜罐中,向罐内鼓人压缩空气,在加热(一般为50-90 t) 条件下,使铜发生氧化,生成的氧化铜与硫酸发生反应,生成硫酸铜水溶液,当溶解到一定cu2 + 浓度(一般为120 -150 gIL) 时,进入原液罐(或经过滤后再到原液罐),与制筒机回流的贫铜电解液(一般为70 -100 gIL) 混合,以使电解液成分符合工艺要求,然后再经过一系列活性炭过滤、机械过滤、温度调整等设备及过程后,把符合工艺要求的电解液送人制筒机(或称电解机组)进行原箱生产制造。在实际生产过程中,电解液都是循环使用的,不断的从制循机中生产原筒,消耗电解液中的铜,而由溶铜罐不断溶铜,再经一系列过滤、温度调整、成分调整后,不断送人制筒机。这其中,利用活性炭吸附掉电解液中的有机物(包括有机添加剂) ,机械过滤滤掉(截留) 电解液中的固体颗粒物。 电解制备过程不但要保证电解液连续不断地循环,还要及时调整并控制好电解液成分(含铜、含硫酸浓度)、电解液温度、循环量匹配等技术指标。 4. 电解液制备主要工艺参数 电解液工艺指标是一个非常重要的参数,在很大程度上决定着电解铜锚质量,决定着溶铜造液的能力和电解液制备所用的设备规格和数量,电解液各工艺
[VIP专享]年产4万吨低氧铜杆废铜连铸连轧生产线(拉法格倾动炉)
年产4万吨低氧铜杆废铜连铸连轧生产线(选用拉法格倾动炉) 初步可行性研究分析 上海浦东力生电工机械有限公司 2013年6月25日
目录 一一总论 一一厂址 一一建设方案 一一环境保护、职业安全与卫生 一一节能与能耗 一一消防 一一人员培训 一一原料供应 一一投资估算 一一经济评估及投资回收期 十一. 初步可行性研究分析的结论和建议
1.总论 1.1 项目名称 年产4万吨低氧铜杆废铜连铸连轧生产线项目。(选用拉法格倾动炉)1.2 低氧铜杆的基本情况 按照我国现行标准GB/T3952-2008规定,用于导体的铜杆分为两大类:低氧铜杆和无氧铜杆(合金铜杆除外)。用电解铜生产的无氧铜杆牌号为TU1、TU2,低氧铜杆牌号为T1、T2;用废铜生产的无氧铜杆和低氧铜杆 的牌号统称为T3。 所有牌号的铜杆的电性能、机械性能、化学成份等各项指标均可在 标准中查得。 1.3 立项背景 (1)我国改革开放三十多年来,国民经济高速发展,随着城乡人民生活水平的不断提高,促使我国电力工业的飞速发展。我国已成为世界第 一用铜大国,2007年国内导体用铜从2000年的172万吨增至378万吨,2008年达到了412万吨。这几年都在快速增长,预计到2015年将达到705万吨。 (2)我国的铜资源非常贫乏,每年用铜量的大部分靠国外进口,世界的铜资源也很有限,所以每年大量进口废铜。同时我国正成为世界最大的 废铜产生国,拆拣废铜、再生利用,符合循环经济可持续发展的规律,是科学发展观的体现。 (3)长期以来,我国没有先进的装备和工艺用于废铜作为原料生产低氧 铜杆,只是利用反射炉进行冶炼。反射炉炼铜污染不易治理、能耗高、产品质量差,所以早在1997年3月国家发出通知,淘汰反射炉炼铜。 去年,由上海电缆研究所黄院士牵头,申报用西班牙拉法格炉子炼铜连 铸连轧生产低氧铜杆的项目获得国家有关部门批准,研发工作正在进行中。 (4)西班牙拉法格的FRHC废杂铜精炼技术,使低氧铜杆的品质大为提高,含铜量大于99.93%,导电率大于100.4%IACS,最高可到100.9%IACS。目前
铜矿生产工艺标准汇总
第一章铜业发展历程 1.1铜及铜精矿简介 铜精矿是低品位的含铜原矿石经过选矿工艺处理达到一定质量指标的精矿, 可直接供冶炼厂炼铜。 第二章铜矿石 2.1铜矿石分类 铜矿石种 类 主要成分图片产地 自然铜自 然 铜 Cu (Fe、Ag、 Au、) 世界:美国密执安州的苏必利尔湖南岸(1857年这 里发现重达420吨的自然铜块)、俄罗斯的图林斯克 和意大利的蒙特卡蒂尼等地。 中国:湖北、云南、甘肃、长江中下游等地铜矿床 氧化带中。 硫化矿黄 铜 矿 CuFeS2 (Ag、Au、Tl、 Se、Te) 中国:长江中下游地区、川滇地区、山西南部中条 山地区、甘肃的河西走廊以及西藏高原等。其中以 江西德兴、西藏玉龙等铜矿最著名。 世界:西班牙的里奥廷托,美国亚利桑那州的克拉 马祖、犹他州的宾厄姆、蒙大那州的比尤特,墨西 哥的卡纳内阿,智利的丘基卡马塔等。 斑 铜 矿 Cu5FeS4 (Pt 、Pd) 中国:云南东川等铜矿床。 世界:美国蒙大那州的比尤特,墨西哥卡纳内阿和 智利丘基卡马塔等。
提出在铜精矿中分别测定辉铜矿、斑铜矿、砷黝铜矿和黄铜矿的方法:称取三份试样,用含4%硫脲的0.15%硫酸浸取辉铜矿,用含15%硫脲的2N 盐酸浸取辉铜矿和斑铜矿。 第三章 铜矿的选矿、冶炼及成本 3.1铜矿的选矿工艺 铜矿的选矿工艺主要是破碎--球磨--分级--浮选--精选等,对含镍钴钼金等稀贵多金属矿,可将粗选铜精矿再分别浮选镍精矿、钴精矿、钼精矿、金精矿。 3.2浸染状铜矿石的浮选 一般采用比较简单的流程,经一段磨矿,细度-200网目约占50%~70%,1 次粗选,2~3次精选,1~2次扫选。如铜矿物浸染粒度比较细,可考虑采用阶段 辉铜矿 Cu 2S 中国:云南东川铜矿 世界:美国布里斯托、康涅狄格州、比尤特、蒙大拿、亚利桑那州、宾厄姆峡谷、犹他州、鸭城、田纳西州、英国康瓦耳、纳米比亚楚梅布、意大利托斯卡纳和西班牙的力拓矿区、美国的内华达州的Ely 矿区、Arizone 州的Morenci 、Miami 和Clifton 矿区以及蒙大拿州的比尤特矿区等地。 氧 化 矿 蓝铜矿 Cu 3(OH)2(CO3)2 中国:广东阳春、湖北大冶和赣西北。 世界:赞比亚、澳大利亚、纳米比亚、俄罗斯、扎伊尔、美国等地区。 赤铜矿 Cu 2O 世界:法国、智利、玻利维亚、南澳大利亚、美国等地有世界主要矿区。 中国:云南东川铜矿和江西、甘肃等地铜矿区。 孔雀石 Cu 2(OH)2CO 3 世界:赞比亚、澳大利亚、纳米比亚、俄罗斯、扎伊尔、美国等地区。 中国:广东阳春、湖北大冶和赣西北
铸铜工艺流程
铸铜工艺流程——失蜡铸造法 大铜世界的每件铸铜艺术品都是需要颠末11道复杂严谨的工序制作而成,这些工序中既有传统手工艺的痕迹,也有精密铸造的现代技术精彩所在。。。。 我们在这里向大家介绍的是今朝铸造行业至多用到的铸造手法,“失蜡铸造法”亦叫“脱蜡铸铜”。通常的失蜡铸造法工艺简略的概括为如下流程,仅供热爱铸造艺术的朋友们参考。 工艺流程之一:泥塑(每件产品的前身都需要1个目结土的雕塑原形,雕塑都是颠末雕塑师在原创设计稿的基础上反复揣摩、推敲之后行的再创编,泥塑的造型好坏、神韵的体现与否、意图的表达呈现直接影响此后的产品好坏,所以,我们的雕塑师都是业界中出类拔萃的高手) 工艺流程之二:矽胶开模(矽胶,英文名矽利康Silicon,此化学原料通经常使用作制作模具,精致度高,姑且有发丝粗细都可体现出来) 工艺流程之三:制作树脂原形(聚乙烯,又称波丽Polyethylene。矽胶模具制作完成之后,就可以灌制出雕塑原形的树脂胚体)工艺流程之四:修整树脂胚体(对胚体表面进行最后的打磨及肌理效果的处理及调整) 工艺流程之五:再制作矽胶模具(将修整好的树脂胚体再次制作成矽胶模具) 工艺流程之六:制作石蜡原形(再次制作出来的矽胶模具已很完
备及完好了,加热熔化的石蜡被加压射入矽胶模具来制造出1个腊胚,此腊胚乃为将生产产品的真实外形复制品) 工艺流程之七:石蜡原形修整(从矽胶模具中灌制并剥离出来的石蜡原形,表面遗留模具的模线及少许的损坏,所以石蜡原形需要再对照流程三的树脂原形胚体作修整,这是很重要的一环,是以环节会直接影响到产品最后的造型及表面效果) 工艺流程之八:砂模(陶壳)制作(把腊胚数个组成树串,连续多次重复浸入泥浆(或称石浆),外层包埋并除湿干燥,将陶壳制成9mm(5-7层)厚,再将此树串放入高热140-160℃烘箱或高压蒸气锅内溶解腊胚直到成中空陶壳) 工艺流程之九:铸造(上一道儿工序的中空陶壳被放入烧结炉依不同合金材料以1000℃-1150℃烧结,将铜液立刻铸入陶壳,冷却后将外层陶壳震破,剥离出来的就是铜质的产品粗胚体) 工艺流程之十:产品铸件修整及处理(对铸造出来的铜产品作喷砂及清洁,并作切割,研磨、热处理、整形、机加工、抛光等最后处理) 工艺流程之十一:表面效果处理及保护(在产品表面处理需要的效果,通常有冷作色以及热作色之分,具体的作色区分及特点,我们会在此后的文章中逐一介绍给各位朋友,最后再做打蜡保护及抛光) 如上概括出的工艺流程,还有众多细节可加以更多纤悉的描述。
铜杆的热加工.
铜杆的热加工 1 传统铜杆加工工艺 传统制造电线电缆用铜杆是由品位在99.95%及以上的电解铜铸成韧点铜(ETP铜)线锭,再经热轧而成。 1.1传统韧点铜线锭生产工艺 工艺过程:反射炉熔化-氧化扒渣-插木还原-铸锭。 ①熔化 在反射炉中进行。 炉料除电解铜外可掺入少量废线。 装炉容量10~300t。 燃料为:煤气、天然气或燃油。 熔炼及浇注周期:如50t炉,约17h。 ②氧化扒渣 炉料熔化后,将压缩空气吹入铜液进行氧化。通过吹气氧化,铜液中的硫及微量的砷和锑等杂质成为挥发性氧化气体,被炉气带走;其它杂质的氧化物和一定量的氧化亚铜(CuO)成为渣,浮在铜液表面而被扒出炉外。在整个氧化过程中,渣被陆续扒出去,直至铜液面不再浮起稠渣而形成一层CuO液层为止。此时可认为氧化完毕。 氧化完毕,取铜样观察不再有由析出二氧化硫而生成的小气泡,铜样呈脆性,击断断面呈砖红色,结晶粗松无光泽。此时,熔解在铜液中的氧化铜(Cu2O)达6~10%。 在氧化过程中,铜液熔解Cu2O的数量与温度有关,温度越高则熔解越多,故氧化时温度不宜过高,一般控制在1070~1090℃。 ③插木还原 把铜液池中的残渣扒净,用干木炭覆盖铜液面,在铜液中插入新鲜的青木杆,进行插木还原。 青木杆在铜液池的高温下干馏,放出H2O、CO2、H2及其它碳水化合物等气体,强烈搅动铜液。这种还有性气体逐步将氧化铜(Cu2O)还原成金属铜。另外,插木还原还能将铜液中的氧去除,使韧点铜(ETP)变成无氧铜(HCOF)。
在还原进行中,不断取样观察,当还原足够时,铜样很难击断,断口呈玫瑰红色,结晶细密,发射状晶体面上有丝质光泽。铜在此时达到韧点,故称韧点铜。 韧点铜含氧量约为300~500ppm。 在插木还原时,要保持适当的低温,以缩短还原时间。插木还原过头时,由于铜液中熔解了过量的还原性气体H2及CO,在凝固时大量析出,致使浇注出的铜线锭除导电率下降、性质变脆外,还含大量气孔,甚至线锭表面会变成“开花馒头”一样,难以使用。 ④铸锭 在铸韧点铜线锭生产中,铜锭表面会形成10~12mm厚的富氧层和气泡层,这层脆弱疏松的富氧-气泡层在线锭扎杆时,会被轧薄包在铜杆表面,小部分会夹入铜杆内。用这种杆拉出的线表面不光、容易起皮、脆断,很难拉出细线。这就是用传统工艺生产铜杆的局限性。 富氧-气泡层的厚度与浇注温度有关,浇注温度越高,气泡层越厚。在实际生产中,浇堡口铜液的温度最好控制在1100~1120℃范围。 此外,在αCu/ Cu2O共晶体界面上有较大的Cu2O共晶体颗粒存在(约100μm),这对拉细线极为不利,这种颗粒通过铜锭刨面、铜杆剥皮等措施也难以去除。 1.2 传统铜杆轧制工艺 在轧制提供前,铜线锭先经再热炉加热到约900℃,而后喂入回线式轧机,经粗、中、精三段热轧和14个孔型轧成Ф7.2mm黑铜杆。 再经酸洗后冷拉成线。 由于韧点铜线锭的缺陷,使回线式轧制杆难免有边翅、卷包及氧化皮夹入等。 1.3传统高导电无氧铜锭生产工艺 含氧量300~500ppm,含铜量99.95%以上的铜液,经过“去氧器”(一个由耐火材料填衬的,装满高质木炭的特殊闭合容器)脱氧,也可以制成高导电无氧铜,其为: 把铜液在1150℃时,通过木炭覆盖的流槽,连续流过“去氧器”脱氧,铜水注入“去氧器”内的木炭表面,除去所含残余氧分: C +Cu2O 2 Cu +CO
阴极铜产业链发展研究报告.
阴极铜产业链发展研究报告 学号:1231050531 班级:12大宗2 姓名:沈佳培 摘要 研究报告介绍阴极铜的基本定义和种类,同时报告中还提到了相关的成产加工环节,以及行业的基本概况和阴极铜国内外近几年的发展水平。报告中列举出了具体阴极铜进出口、产量、消费等相关数据。数据来源于国家统计局、上海有色金属网、有色金属协会、渤海交易所、中华人民共和国海关总署等网站以及百度文库等。
第一章电解铜行业概况 第一节电解铜定义 阴极铜又称电解铜。将粗铜(含铜99%)预先制成厚板作为阳极,纯铜制成薄片作阴极,以硫酸(H2SO4)和硫酸铜(CuSO4)的混和液作为电解液。通电后,铜从阳极溶解成铜离子(Cu)向阴极移动,到达阴极后获得电子而在阴极析出纯铜(亦称电解铜)。粗铜中杂质如比铜活泼的铁和锌等会随铜一起溶解为离子(Zn和Fe)。由于这些离子与铜离子相比不易析出,所以电解时只要适当调节电位差即可避免这些离子在阳极上析出。比铜不活泼的杂质如金和银等沉积在电解槽的底部。这样生产出来的铜板,称为“电解铜”,质量极高,可以用来制作电气产品。沉淀在电解槽底部的称为“阳极泥”,里面富含金银,是十分贵重的,取出再加工有极高的经济价值。 第二节电解铜标准
第三节阴极铜的加工方法
量仍满足不了工业用铜的要求,必须精炼后得到的精铜要求含铜99.95%以上。在硫化铜精矿冶炼的过程中同时还可以回收硫、金、银、锑、铋、镍、硒等有价元素在中国,从铜精矿中提取金属铜,主要采用火法冶金的方法,比较先进的就是闪速熔炼,其产量占全国产铜量的30%以上。由于能耗低,规模大,能有效控制环境污染等优点。这一冶炼技术正在炼铜工业上得到日益发展。闪速熔炼根据不同炉型的工作原理可分为两种类型:Outokumpu闪速熔炼、InCo闪速熔炼。以下介绍Outokumpu熔炼的工艺流程。 ⑵湿法冶金 Outokumpu熔炼的工艺流程 湿法冶金在许多情况下与火法相配合的。其过程的主要化学反应是在水溶液中进行的。铜(锌)矿物预先通过氧化或硫酸焙烧,转变可溶状态,然后再进行浸出、净化电积、以提取电解铜。通常有RLE法、常压氨浸出法(阿比特法)、高压氨浸出法、细菌浸出法等。从焙烧→浸出→净化→电积,简称RLE法。其生产流程,湿法冶金主要适用从低品位氧化矿、废矿堆及浮选尾矿中提取金属铜。 第四节铜产业链的结构
SCR法和Contirod法铜杆生产线的比较
美国SCR法和德国Contirod法 铜杆连铸连轧生产线的比较 美国南方线材公司的SCR法 美国南方线材公司的SCR法是由美国南方线材公司、摩根公司和西屋电气公司共同研制开发的。主要的工艺设备为:熔化采用美国精炼公司的竖炉,铸造采用五轮钢带式连铸机连铸,轧制配备了摩根二辊悬臂式连轧机组连轧。连铸机铸出铸坯截面为梯形,铸坯从连铸机引出后只须弯曲一定角度后即可直接进入连轧机组。美国SCR连铸连轧铜杆生产线型号规格见表 SCR法主要工艺设备连接图
德国西马克·梅尔公司的Contirod法 德国西马克·梅尔公司的Contirod法又叫康特洛德法。主要的工艺设备为:熔化同样采用美国精炼公司的竖炉,铸造采用美国哈兹列特公司的双带式连铸机,轧制配备了德国克虏伯公司的二辊连轧机组。双带式连铸机上下钢带之间的距离与左右側壁之间的距离均可根据工艺的要求进行调整,铸坯截面为矩形,因此也能用来轧制扁铜带。Contirod连铸连轧铜杆生线型号规格见表 德国Contirod连铸连轧铜杆生线主要工艺设备连接图
美国SCR法和德国Contirod法铜杆连铸连轧生产线简述 1.美国SCR法和德国Contirod法铜杆连铸连轧生产线工艺流程表观相似:首先都是将电解铜和返回料由地面叉车运止加料机,经加料口加入竖炉内。但是风机送来的空气与燃气美国SCR法和德国Contirod法的混合方式不同,SCR法是分组混合后送烧嘴,Contirod法是在烧嘴前单独混合后进入炉膛,整个熔化过程通过对燃气中CO的自动控制,使熔化过程处于微还原气氛中。炉内熔化铜液的温度控制在1115℃左右,正常生产时出竖炉铜液中氧含量一般小于100ppm。 熔化了的铜液经过上流槽流入可转动的保温炉。保温炉根据连铸机的浇铸速度的快慢,控制通过下流槽进入浇铸包或中间包的铜液。为防止流动铜液被氧化,上、下流槽都加盖板封闭,用燃气加热保温。连铸机的浇铸温度控制在1120℃左右。 2.美国SCR法和德国Contirod法在连铸设备和连铸过程中铜液液位控制上有较大的不同。 美国SCR法使用的是五轮钢带式连铸机,采用自动或手动控制铸轮的铜液液位,称为AMPS自动浇铸系统。浇包用一个测力传感器将信号传给保温炉控制系统,控制保温炉的铜液流量,使浇包液位稳定。铸轮的液位用闭路电视进行监测,由浇包上的塞棒控制流入铸轮的铜液。五轮钢带式连铸机由结晶轮、两个压轮、张紧轮、惰轮和钢带组成,结晶轮上的凹槽和压紧的钢带形成铜液的浇铸腔,铸轮和钢带配有冷却系统、吹扫系统、喷碳系统、并配有浇包预热装置。出铸机温度一般为900℃左右。 德国Contirod法的连铸机液位控制采用了EMLI控制系统,自动监测
阴极铜的生产工艺流程
铜精矿、冰铜、阴极铜的生产流程及主要工艺 铜冶金技术的发展是个漫长的过程,欧洲在公元前二十世纪中期已采用硫化铜矿炼铜,到公元初期的罗马帝国即已普及。16世纪阿里科拉(G.Arricola)在《冶金论》一书中叙述了铜的熔炼和精炼工艺。17世纪末,美国人赖特(D.Wright)用反射炉炼铜,产出锍(冰铜)。1880年开始用转炉吹炼锍,这是炼铜技术的重大进步。铜电解精炼技术也在此阶段发明。 目前冶炼方法主要有火法冶炼与湿法冶炼,前者多用于硫化矿的冶炼,后者一般用于氧化矿的冶炼。冶炼的纯铜可拉成很细的铜丝,制成很薄的铜箔。能与锌、锡、铅、锰、钴、镍、铝、铁等金属形成合金,形成的合金主要分成三类:黄铜是铜锌合金,青铜是铜锡合金,白铜是铜钴镍合金。 一、火法冶炼主要分采矿、选矿、熔炼、电解等步骤。 ⒈阴极铜火法冶炼过程 采矿就是将矿石与废石分离的过程。分离后的矿石运往选矿厂进行选矿。 选矿就是将采矿得到的矿石进行破碎、筛选获得品位较高的铜精矿的过程,包括破碎、浮选、分离、浓缩、脱水等步骤。矿石经过旋回破碎机、中细碎圆锥破碎机进行三级破碎后变成细颗粒状,再经球磨机碾磨成粉状进入浮选池。浮选池内加入药剂,经浮选机不断搅拌,金属吸附在搅拌后形成的泡沫上,泡沫悬浮在池的表面,金属随泡沫流入浮选池边上的槽内得到分离。分离后的矿浆经浓缩和过滤相结合的脱水手段,最后形成铜精矿。通过此过程,含铜量可由原矿的0.5%提高到30%(在干燥状态下)。 熔炼就是将铜精矿冶炼成合格的阳极铜,包括预干燥、闪速熔炼、转炉吹炼、阳极炉精炼及阳极浇铸等工序。
经过预干燥,矿的水分降至13%以下;干燥后,矿的水分降至3%以下。经闪速炉熔炼后的产物称“冰铜”,液体状,铜含量50%--75%,与硫混合。“冰铜”经转炉吹炼后的产物是“粗铜”,铜含量98.5%左右。粗铜再经阳极炉精炼并经过圆盘浇铸机浇铸,即形成阳极铜。阳极铜外型与阴极铜相似,但表面缺少光泽,厚度一般为阴极铜的2―3倍,是下一道工序电解中的阳极。 电解就是利用氧化-还原反应原理,阳极的铜电解进入电解液成为Cu离子,Cu离子带正电,流向阴极,在阴极富集,还原为金属铜,吸附在阴极上,阴极铜的纯度高于阳极。一般经过12天(阴极的反应周期)的电解反应,阴极上的铜就是所谓的“阴极铜”。阳极的反应周期24天。刚出炉的阴极铜呈砖红色,表面平整而光亮,铜的含量达99.95%以上。而阳极铜含多种其他元素,经电解后,这些元素在阳极沉淀下来,成为“阳极泥”。阳极泥再经处理可以得到金、银、粗硒和精碲等副产品。 电解的阴极,又称“始极片”,由专门的加工厂生产。始极片有三种:①由阴极铜制成,这种始极片电解后成为阴极铜的一部分;②钛板; ③不锈钢板。后两种可以重复使用,又称“永久阴极”。 ⒉ 火法冶炼的主要工艺 20 世纪70年代以前,火法冶炼普遍采用的炼铜设备是鼓风炉、反射炉和电炉。这几种工艺的共同缺点是能耗高、硫利用率低和污染环境。由于全球性的能源和环境问题突出,促使铜冶金技术从80年代起获得飞速发展。传统的冶炼方法逐渐被淘汰,随之兴起的是以闪速熔炼和熔池熔炼为代表的强化冶炼技术,其中最重要的突破是氧气的广泛应用。 ⑴ 闪速熔炼 包括国际镍公司闪速炉、奥托昆普闪速炉和旋涡顶吹熔炼3种。 奥托昆普闪速炉自1949年在芬兰Harjavalta冶炼厂投产以来,至今已投产42座。用此法生产的粗铜约占世界粗铜产量的45%左右,居
铜板带是什么(铜板带的生产工艺流程)
铜板带是什么 铜板带是什么?铜板带其实就是对铜板和铜带的统称。铜板是指铜经过轧制的板材,轧制包括了热轧和冷轧。铜带是指厚度在0.06~1.5mm之间的铜轧制加工品。铜板带可以根据不同的牌号分类,大致分为黄铜板带、紫铜板带、青铜类板带、白铜类板带。下面还可以细分。那么铜板带生产的工艺会有哪些呢?铜板带再生产中会有哪些工艺缺陷,我们又该如何解决呢? 铜板带的工艺流程 知道了铜板带是什么,我们接着来了解下铜板带的生产工艺: 1、铸锭热轧生产工艺:熔炼→铸造(立式半连铸或立式连铸)→(锯切)→加热→热轧→铣面→冷轧→热处理→精整→包装入库。 铸锭热轧法生产工艺是现阶段应用最广泛的的主流生产工艺。 2、水平连铸生产工艺:熔炼→水平连铸带坯→(退火)→铣面→冷轧→热处理→精整→包装入库
水平连铸生产工艺用于生产热轧困难的的合金品种(如锡磷青铜、铅黄铜)等。 其工序短,生产成本低,设备占地面小。 现阶段生产合金的比较单一,结晶器损耗大,铸坯上下表面组织均一性难以控制。 3、上引连续铸造法生产工艺:熔炼→上引带坯→(铣面)→冷轧→热处理→精整→包装入库 上引连续铸造法生产工艺是国内新开发的的短流生产工艺,用于生产紫铜。 其生产流程短,耗能低。 4、立弯连续铸造生产工艺:熔炼→立弯铸造→(热轧)→(铣面)→冷轧→热处理→精整→包装入库 其生产效率高,生产流程短,能耗低。 5、辊轮式/双带连续铸造法生产工艺:熔炼→辊轮/双带连续铸造→(热轧)→冷轧→热处理→精整→包装入库 辊轮式/双带连续铸造法生产工艺是在研发的的短流生产工艺。 其生产流程短,耗能低。 6、连续挤压法生产工艺:熔炼→上引铜杆→连续挤压→冷轧→热处理→精整→包装入库。 连续挤压法生产工艺主要生产铜排和铜扁线。 其带坯宽度及生产产品品种受到限制。 对铜板带是什么有所了解后,我们再来了解下铜板带的熔炼设备: 1、熔炼炉:主要分为感应电炉和燃气竖炉。 熔炼炉的特点: (1)电炉体积小,重量轻、效率高、耗电少; (2)炉子周围温度低、烟尘少、作业环境好; (3)操作工艺简单、熔炼运行可靠; (4)加热温度均匀、烧损少、金属成分均匀; (5)铸件质量好、熔化升温快、炉温易控制、生产效高; (6)炉子利用率高、更换品种方便。 (7)根据其在工业中的特点可称为工业炉,电炉,高频电炉,小型电炉,节能炉。 2、铸造机: (1)立式半连续铸造机:具有设备简单,生产灵活等特点,适宜铸造各种铜及铜合金扁锭。 (2)立式半全续铸造机:具有产量大,成品率高等特点,适宜大规模连续生产品种和规格单一的铸锭。立式半全续铸造机主要用于生产无氧铜。
各种连铸连轧生产线的比较
各种连铸连轧生产线的比较 一、基本概述 裸电线是电线电缆不可缺少的部分,除了光缆以外,几乎所有的电线电缆都需要导体、需要裸线,而且相当数量的一部分产品就以裸电线的形式出现,例如钢芯铝绞线。粗略概算,包括导体部分在内的裸电线的总产值,约占电线电缆总产值的三分之一,它有着举足轻重的作用。 裸电线、电线电缆导体,其材料主要是铜、铜合金、铝、铝合金,以及其它有色和稀有金属材料。 在工农业总的用铜量中,电线电缆行业用铜量占有很高的比重。九十年代初期,全国电线电缆行业的用铜量约近30万吨,而今年估计用铜量为80余万吨,约增加近二倍的用铜量,价格却从最高每吨3万元至现在每吨1.5万元,下跌约50%,因此一些在缺铜时采用铝作代用品的电线电缆产品又恢复采用铜,如布电线、电车线等,使铜的用量日增。铜作为电线电缆最主要的导电材料,又逐步向不同的用途延伸,如用作电车线的高强度、高耐磨的铜合金线应运而生;使用高纯度、高精度的铜线为通信电缆等提供优质导电材料;特细铜线、超细铜线更为新型的电子仪器设备、通信设备、办公自动化设备等提供更为优良的产品,用铜量的增加便是理所当然的。 每年几十万吨铜需要加工,从电解铜板、加工成杆、线或异型材,需要约万台套以上的杆材、线材和异型材的生产设备,这是十分庞大的设备群体。 铜杆生产中最主要四种方法的设备,我国都应有尽有。拥有2台套浸涂法设备和至少700余台套的上引法机组用于生产无氧铜杆,保守估计,设备年生产能力在180万吨至200万吨;从德国、美国、意大利引进的铜铸轧机组超过10
台套,加上国产的连铸连轧机组,光亮铜杆的生产能力至少为50万吨至60万吨;至于原有常用的横列式轧机轧制黑铜杆,加上用水平连铸法制作型材的坯料,其年生产能力不低于30万吨至50万吨。也就是说,我国拥有的生产设备中,无氧、低氧铜杆的年生产能力在220万吨至250万吨左右。加上黑铜杆生产能力,将超过300万吨。由于乡镇企业的大量出现,一些简易的生产铜杆的方法,也就无法在此估计之中。80万吨的需要量和250万吨无氧、低氧铜装机能力之间,存在着很大的距离,因此相当大的部分设备就不得不处于减产或停产状态,以700 余台套上引法机组为例,估计约1/3至1/4的机组由于各种原因而处于停产状态,而1/2的机组的产量尚未达到原设计的生产能力,但即使如此,由上引法机组生产的铜材,仍占有我国铜杆用量的半璧江山,起着重要的作用。 我国铜线拉线机约在万台左右,至少有一半是由电工机械厂制造的,少量由国外引进,这二部分设备的性能都较优,特别至九十年代中后期,国产大、中、小拉采用连续退火的水平,已与国外设备逐步靠近,差距大大缩小了。然而在乡镇企业中仍有土拉线机,这些机器能耗高、劳动强度高、效率低、粗糙,难以加工质优的产品,这部分设备数量估计约为总数的一半,需要给予彻底改造或弃之不用。 裸电线中大量采用铝,例如:铝绞线及钢芯铝绞线。九十年代初期,用铝量每年尚不超过20万吨,以后随着经济的增长逐年增加,由于以前国家在电力系统的政策上是重发电轻送电,使送电的增长赶不上发电的增长速度。近年来开始的城市电网和农村电网改造,使送电的增长速度急剧加快,兼之九十年代开始建设的大型电站,像二滩电站、黄河小浪底电站和长江三峡电站,将相继逐步建成,送电便成为电站建设以后的重中之重,送电工程建设步入本世纪以来最辉煌、
SGSCC单晶铜的生产工艺流程
SGSCC单晶铜的生产工艺流程——高纯铜—熔化—真空精练—过滤—区域熔炼—SGSCC单晶连铸—电磁约束成型—超低温介质冷却—牵引盘曲—表面处理—检测—包装—成品单晶铜杆通过SGSCC单晶连铸技 术制成。SGSCC单晶连铸技术是河南纳士科技股份有限公司与兰州理工大学在水平连铸技术的基础上共同研究开发的、具有自主知识产权的一种新型材料成型技术。其与传统连续铸造的根本区别是在于采用区域熔炼、电磁搅拌、电磁过滤与物理场过滤、电磁约束成型等新工艺、新技术,实现了金属液的无铸模成型,而非传统连铸的水冷铸模或结晶器成型。区域熔炼、电磁搅拌、电磁与物理场过滤等先进工艺技术的应用使得金属液内杂质得到有效去除,金属液更加纯净,同时无模的电磁约束成型使得金属晶核无法在模壁上结晶,并通过端部的超低温介质冷却形成金属液单方向凝固的高温度梯度,使金属液在脱离电磁约束成型作用的出口处瞬间凝固成型,从而得到表面光亮如镜、性能优异的单晶铸杆。单晶铜指整根铜杆仅由一个晶粒组成,内部无晶界存在,主要用于Hi-Fi音视频线材,亿被越来越多的Hi-Fi业界人士称为音响发烧线材的最理想导体。用单晶铜制作的高保真音响线材及插接件,其音质背景安静、细腻甜润,高中低频段层次分明,透明度、空气感、堂音及空间感皆属优秀,属世界极品线材的水平,深受Hi-Fi爱好者欢迎. 目前我国电缆行业一般采用连铸连轧法、浸涂成型法和上引法来生产低氧铜和无氧铜杆,所产出的铜杆内部组织不均匀,细线拉制非常困难。而国外已开始大量采用定向凝固技术生产单晶铜杆,单晶铜线材不但具有极好的信号传输和抗失真能力,还具有优异的塑性加工性能,因此可以加工成超细的线和超薄的箔,作为生产集成电路以及电子仪器、音响设备等所需信号线的原材料,其各项性能指标均高于目前常用的无氧铜I2』。热型连铸法(OCC 法)是一种生产单晶线材的新方法,与传统连铸法不同之处在于它采用加热结晶器,并在铸型外对棒坯进行直接喷水冷却,从而使得热量沿棒坯由铸型区向冷却区单向传递,以达到连续定向凝固的目的。对连铸过程中微观晶粒形态及演化过程进行研究,通过调整工艺参数来控制铸棒凝固过程中微观晶粒的生长状态,以获得高质量的单晶铜杆,这也是热型连铸的研究热点及难点H J