虚拟样机技术及其在商用车操稳性能分析中的应用

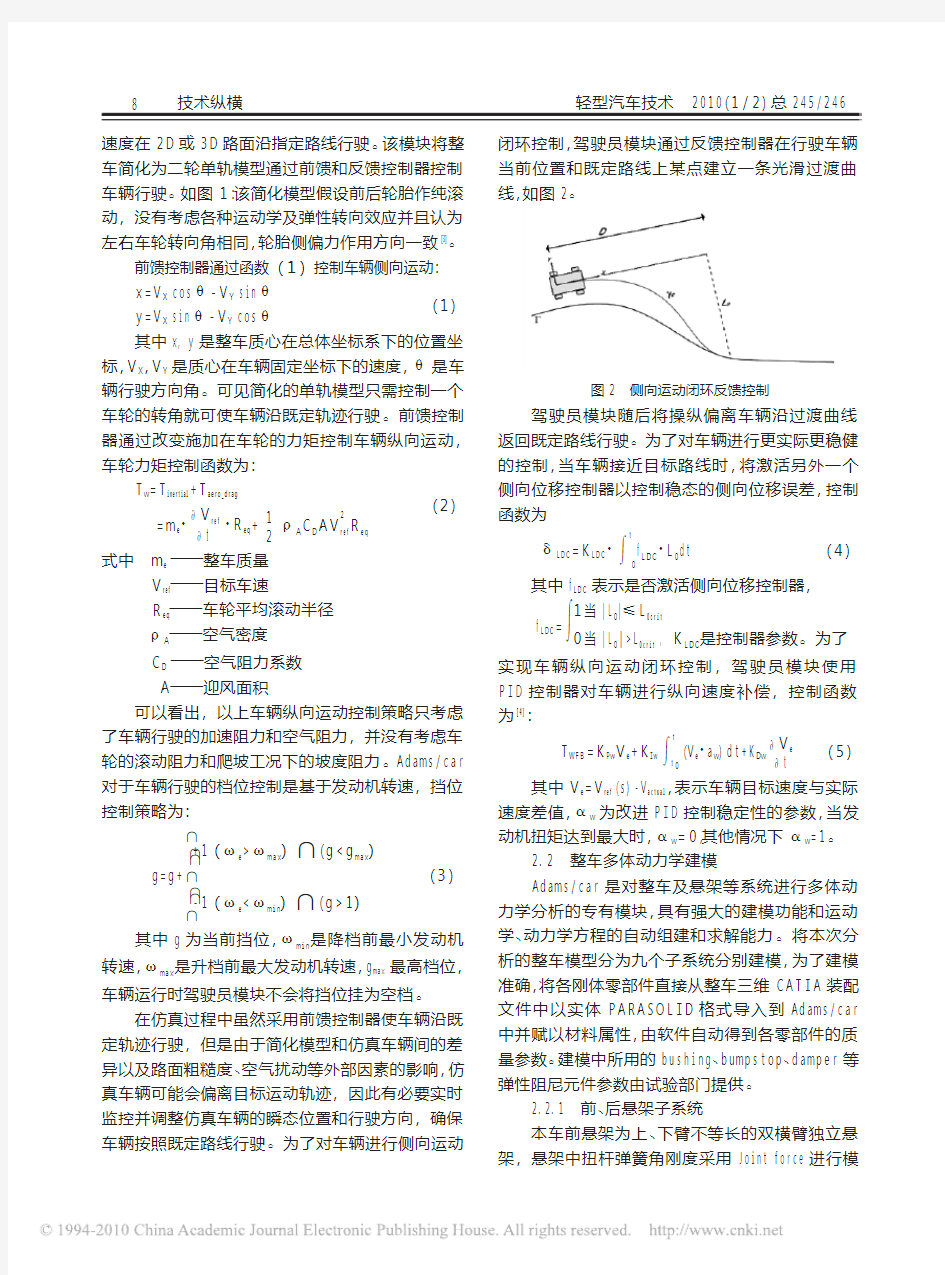
虚拟样机技术及其在商用车操稳性能分析中的应用
张守元
沈
磊
伏小龙郁
强
(上汽商用车技术中心车身开发部)
摘要随着市场竞争日益激烈,数字化虚拟样机技术在汽车产品研发中得到越来越广泛的应用。文章详细探讨了Adams/car软件整车仿真控制策略,
并针对公司内某款新开发商用车在Adamas/car中建立其刚弹耦合多体动力学整车模型,全面分析了该车开环及闭环控制下的操纵稳定性能并给出改进意见,为该车性能进一步提高提供指导。
关键词:虚拟样机
商用车操纵稳定性
虚拟样机VP(VirtualPrototype)技术是在CAD/CAM/CAE技术及多体系统MBS(Multi-bodySystem)动力学基础上发展起来的系统级的产品建模、仿真与分析技术。CAD/CAM/CAE技术的重点是针对零部件的优化设计,但零部件的最优并不代表产品性能的最优。虚拟样机技术则是对整个产品性能进行分析和优化设计,是基于系统的优化设计,能够通过虚拟试验精确、快速地预测产品整体性能[1]。随着中国汽车工业的迅猛发展和汽车的迅速普及,人们对汽车的要求也越来越高。汽车操纵稳定性不仅影响到汽车驾驶的操纵方便程度,更是影响汽车主动安全性的重要性能之一,是决定高速汽车安全行驶的一个重要性能。采用虚拟样机技术对开发初期的汽车产品进行整车操稳性能分析与改进,可以大幅度减少物理样机数量和试验次数,满足市场竞争情况下开发周期不断缩短的要求,可以在最短时间内设计制造出高质量的产品并且节约设计成本[2]。本文详细探讨了虚拟样机仿真软件Adams/car整车控制策略,针对公司内某款自主研发的商用车新车型,利用Adams/car建立其数字样机仿真模型,将难以模拟的钢板弹簧采用有限元方法处理成柔性体,最后建立整车刚弹耦合多体动力学模型,通过驾驶员控制模块对其进行整车操纵稳定性能仿真分
析,全面预测了该车的操稳性能并提出了改进意
见。
2.1Adams/car及其整车控制策略
Adams/car是MDI公司与Audi、BMW、Volvo等公司合作开发的整车多体动力学设计软件,与其它动力学分析软件如LMS/DADS、RecurDyn等相比,其包含的整车动力学模块可以方便的对建立的虚拟样机进行人-车-路闭环控制仿真,并输出标志操纵稳定性、制动性、乘坐舒适性和安全性的特征参数。
在整车仿真过程中,Adams/car通过内含的驾驶员控制模块模拟驾驶员的操作(如:转向、加速、换档等)对车辆进行控制,使车辆以指定的速度或加
1引言
2虚拟样机模型建立
图1
整车简化单轨控制模型
速度在2D或3D路面沿指定路线行驶。该模块将整车简化为二轮单轨模型通过前馈和反馈控制器控制
车辆行驶。
如图1:该简化模型假设前后轮胎作纯滚动,没有考虑各种运动学及弹性转向效应并且认为
左右车轮转向角相同,轮胎侧偏力作用方向一致[3]。
前馈控制器通过函数(1)控制车辆侧向运动:
x=VXcosθ-VYsinθy=VXsinθ-VYcosθ
其中x,y是整车质心在总体坐标系下的位置坐
标,VX,VY是质心在车辆固定坐标下的速度,θ是车辆行驶方向角。可见简化的单轨模型只需控制一个车轮的转角就可使车辆沿既定轨迹行驶。前馈控制器通过改变施加在车轮的力矩控制车辆纵向运动,车轮力矩控制函数为:
Tw=Tinertial+Taero_drag
=me
·鄣Vreft
·Req+12ρACDAV2refReq式中me———整车质量
Vref———目标车速
Req———车轮平均滚动半径ρA———空气密度CD———空气阻力系数A———迎风面积
可以看出,以上车辆纵向运动控制策略只考虑了车辆行驶的加速阻力和空气阻力,并没有考虑车
轮的滚动阻力和爬坡工况下的坡度阻力。Adams/car对于车辆行驶的档位控制是基于发动机转速,挡位控制策略为:
g=g++1(ωe>ωmax)疑(g<gmax)-1(ωe<ωmin)疑(g>1疑疑疑疑疑疑疑
)(3)
其中g为当前挡位,ωmin是降档前最小发动机转速,ωmax是升档前最大发动机转速,gmax最高档位,车辆运行时驾驶员模块不会将挡位挂为空档。
在仿真过程中虽然采用前馈控制器使车辆沿既定轨迹行驶,但是由于简化模型和仿真车辆间的差异以及路面粗糙度、空气扰动等外部因素的影响,仿真车辆可能会偏离目标运动轨迹,因此有必要实时监控并调整仿真车辆的瞬态位置和行驶方向,确保车辆按照既定路线行驶。为了对车辆进行侧向运动
闭环控制,驾驶员模块通过反馈控制器在行驶车辆当前位置和既定路线上某点建立一条光滑过渡曲线,如图2。
驾驶员模块随后将操纵偏离车辆沿过渡曲线返回既定路线行驶。为了对车辆进行更实际更稳健的控制,当车辆接近目标路线时,将激活另外一个侧向位移控制器以控制稳态的侧向位移误差,控制函数为
δLDC=KLDC·
t
乙0
f
LDC
·L0dt
(4)
其中fLDC表示是否激活侧向位移控制器,
fLDC=
1当|L0|≤L0crit
0当|L0|>L0crit,KLDC是控制器参数。为乙
了
实现车辆纵向运动闭环控制,驾驶员模块使用PID控制器对车辆进行纵向速度补偿,控制函数为[4]:
TWFB=KPwVe+KIw
t
t乙0(Ve
·aw
)dt+K
Dw
鄣Ve
t
(5)
其中Ve=Vref(s)-Vactual,表示车辆目标速度与实际速度差值,αw为改进PID控制稳定性的参数,当发
动机扭矩达到最大时,αw=0,其他情况下αw=1。
2.2整车多体动力学建模
Adams/car是对整车及悬架等系统进行多体动力学分析的专有模块,具有强大的建模功能和运动学、动力学方程的自动组建和求解能力。将本次分析的整车模型分为九个子系统分别建模,为了建模准确,将各刚体零部件直接从整车三维CATIA装配文件中以实体PARASOLID格式导入到Adams/car中并赋以材料属性,由软件自动得到各零部件的质量参数。建模中所用的bushing、bumpstop、damper等弹性阻尼元件参数由试验部门提供。
2.2.1前、后悬架子系统本车前悬架为上、下臂不等长的双横臂独立悬架,悬架中扭杆弹簧角刚度采用Jointforce
进行模
(1)
(2)图2侧向运动闭环反馈控制
拟,将横向稳定杆从中间分为两段,中间用旋转副联接并施加Jointforce模拟其角刚度,把转向横拉杆分
为两段,中间用滑移副联接,并分别施加Adjustableforce来调整车轮前束和车轮外倾角。扭杆弹簧后端通过垂直副与车身联接以消除模型中的冗余约束,转向系统采用齿轮齿条式转向器,齿轮与齿条通过耦合副连接,传动比为0.138,转向杆柱与转向中间杆间的锥齿轮啮合也通过耦合副模拟。前悬架总成模型由转向系统、稳定杆总成和前悬架三部分组成,如图3。该模型共有三个自由度,分别为左右车轮的上下跳动和方向盘的转动,无冗余约束[5]。
本车后悬架为钢板弹簧非独立悬架,钢板弹簧
为单片簧,在工作变形区域内,其刚度曲线近似为线性。采用单元长度为5mm的六面体对钢板弹簧进行网格划分,建立其有限元模型,使用MSC.Nastran对其进行刚度分析,并调整单元材料参数,使有限元模型刚度与试验测试刚度吻合如图4,钢板弹簧刚度294.5N/mm。钢板弹簧前端通过interfacepart和Revolute副与车架连接,后端通过吊耳支撑,吊耳与车架间用Revolute副连接。
2.2.2轮胎模型
轮胎的力学特性对汽车的操纵稳定性起着非常重要的作用,Adams/car中提供PAC89、FIALA、UA、
FTire等9种轮胎模型,由于操稳性分析主要是在水
平路面,本次仿真选择输入参数较少的FIALA轮胎模型,其特性文件需要10个参数,FIALA轮胎是FIALA在1954年由简化的轮胎理论模型推导出的无量纲解析式的一种轮胎模型,对于操稳性分析可以得到比较准确的结果。
2.2.3动力总成模型
动力总成模型包括发动机、离合器、变速箱和差速器等部件,结构复杂,为了在仿真过程中允许更大的积分时间步长,模型由一组微分方程组代替,其输出的功率和扭矩由发动机外特性曲线及节气门部分开启时的速度特性曲线决定。发动机悬置位置及其属性文件由设计部门提供。
2.2.4制动系模型采用简单的钳盘式结构建立制动系模型,通过在制动钳和制动盘间施加SFORCE对车轮施加制动力,单轮制动力矩由下式决定[6]:
T=2×A×P×μ×Re×STEP(6)其中A为制动缸活塞面积,P为制动压力,由制动踏板力和制动力分配系数决定,μ为制动效能,Re为有效制动半径,STEP函数通过监测车轮和转向节间的角速度防止车轮倒转。
2.2.5车身模型
拟分析车辆为非承载式车身,车身模型由车架和车身两个刚体组成,车架和车身间通过十个悬置联接,车身质量属性由设计部门提供。根据实车迎
图3前、
后悬架多体动力学模型
图4
钢板弹簧柔性体模型及其静态刚度曲线
风面积和风压中心位置等数据考虑整车行驶时空气阻力的影响。
最后通过建立communicator将各个子系统模型与驾驶员控制模型进行装配,得到的整车模型如图5。
3.1开路系统仿真分析在人-汽车开路系统中,假定驾驶者的任务只是机械地急速转动转向盘至某一转角并维持此角度不变,不允许驾驶者起任何反馈作用,汽车响应则完全取决于汽车的结构与参数,是汽车本身的固有特性。开路系统试验可以给出“汽车性能”与“汽车结构”之间的联系,从而可以得到改变汽车结构及结构参数以提高性能的具体途径。
3.1.1稳态转向特性试验
稳态转向试验用于评价汽车的稳态响应特性,国标中有两种试验方法,本次仿真采用固定转向盘转角,连续加速的试验方法。在水平路面,操纵汽车以最低稳定速度开始行驶,固定方向盘转角为196°使其沿半径为20米的圆周行驶,缓缓连续而均匀地加速(纵向加速度不超过0.25m/s2),直至汽车的侧向加速度达到6.5m/s2(或受发动机功率限制而所能达到的最大侧向加速度、或汽车出现不稳定状态)为止。编写驾驶员控制文件(.dcf)和驾驶员控制数据文件(.dcd),控制汽车按以上要求行驶。常采用以下参数来描述和评价汽车的稳态响应特性[7]:
1)前、后轮侧偏角绝对值之差(α1-α2)若把前轮转角δ作为输入,转向半径R作为输出,则有:
R=
Lδ-(α1-α2)
(7)
在一定的车轮转角δ下,若车速极低,侧偏角
可以忽略,转向半径R0=Lδ,
车速提高后,前、后轮存有侧偏角,若(α1-α2)为正值,则R>R0,由于(α1-α2)将随侧向加速度的提高而加大,转向半径R将逐渐加大,汽车即表现出不足转向特性;反
之,汽车转向效果逐渐加强,汽车表现出过多转向特性。本次仿真汽车运行轨迹如图6,可见该车具有不足转向特性。
(α1-α2)与汽车稳定性因数K的关系为:K=1αyL
(α1-α2)
(7)
其中αy为侧向加速度,L是轴距,当(α1-α2)>0时,K>0,为不足转向;当(α1-α2)=0时,K=0,为中性转向;当(α1-α2)<0时,K<0,为过多转向。
(α1-α2)与αy成线性关系,其斜率为LK,本次仿真的(α1-α2)与侧向加速度曲线如图7,可以看出,当侧向加速度小于0.3 ̄0.4g时,α1-α2与侧
向加速度成线性关系,斜率为1.19,侧向加速度大
图5
整车虚拟样机模型
3操纵稳定性仿真分析
图
8转向半径比随侧向加速度变化曲线
图6
稳态转向仿真汽车运行轨迹
图7
α1-α2随侧向加速度变化曲线
于0.3 ̄0.4g时,α1-α2与侧向加速度不再存在线性关系,曲线斜率迅速增大,这是因为轮胎侧偏特性已进入明显非线性区域,汽车在大侧向加速度下,稳态
响应特性发生显著变化。
2)转向半径的比R/R0
R/R0与稳定性因素K的关系为:RR0
1+Ku2(8)
其中u为车速。可见K>0时,R/R0>1,汽车为不
足转向,且由上式可知,转向半径将随车速增加而增大,反之,汽车有过多转向特性。R/R0与侧向加速度曲线如图8,同样可以看出,当侧向加速度大于0.3 ̄0.4g时,曲线不再成线性关系,不足转向有加强的趋势。
3.1.2转向盘角阶跃输入试验为评价汽车瞬态响应品质的好坏,通常给汽车前轮一个角阶跃输入,观察过渡过程中汽车的横摆角速度响应。首先使汽车以恒定速度在水平路面直线行驶,然后给方向盘以36°的角阶跃输入,持续时间为0.15秒,汽车分别以70、80、90、100km/h的速度行驶时,横摆角速度瞬态响应曲线如图9。
由上图可知,随着车速的提高,反应时间越来越
小,响应峰值却逐渐增大,稳态增益略有提高后又逐渐下降,当车速为80km/h时,横摆角速度稳态值达到最大8.18deg/s,由于该车具有不足转向特性,横摆角速度稳态增益达到最大时的车速即为该车特征车速。汽车以100km/h的速度行驶时,角阶跃转向输入后横摆角速度第一次达到稳定值的反应时间为1.08秒,达到稳态时的横摆角速度7.28deg/s,横摆角速度达到第一峰值的时间是0.66秒,最大横摆角速度8.89deg/s,超调量为123%,与市场上同类车型相比,该车瞬态响应特性尚存在一定差距。3.1.3转向盘角脉冲输入试验
在汽车操纵稳定性分析中,常以前轮转角或转向盘转角为输入,汽车横摆角速度为输出的汽车横
摆角速度频率响应来表征汽车的动态特性。通过直接给方向盘正弦角位移输入来测量汽车的频率特性较困难,实际中常用方向盘角脉冲位移输入试验来确定汽车的频响特性,方向盘角脉冲输入试验在平坦的场地上进行。试验车速为最高车速的70%,并且圆整为80、100或120km/h[8]。其最大转角应使汽车的侧向加速度达到0.2~0.3g。本次仿真中取车速为80和100km/h,给方向盘以45°的角脉冲输入,脉冲宽度取为0.35秒。仿真结果如图10:
从幅频相频特性曲线中可以看出车速提高时
共振频率处幅值增大,但相位角基本不变。该车共振峰频率0.39Hz,共振频率较低,0.1Hz时相位滞后
角3.78°,0.6Hz时的相位滞后角38.29°,与同类车型相比,该车动态响应特性较差。
3.2人-汽车闭路系统仿真分析操纵稳定性与驾驶者的操作特性紧密相关,因此,操纵稳定性的研究不能忽略驾驶者的反馈作用。汽车行驶中,驾驶者根据需要操纵转向盘使汽车做一定的转向运动,并实时修正对转向盘的操纵,使汽车沿一定的路线行驶,所以人-汽车系统是一个统一整体的闭路系统。
3.2.1转向轻便性仿真为了评价汽车低速行驶转向轻便性,操纵转向盘使汽车沿双纽线行驶,双纽线顶点处的曲率半径由汽车最小转弯半径决定。根据本次仿真车的最小转弯半径3532mm,得出此次仿真的双纽线轨迹的极坐标方程为:
图9
不同车速下横摆角速度瞬态响应曲线
图10不同车速下横摆角速度频响特性
幅频特性曲线
相频特性曲线
l =11655.6cos
(2φ)姨(单位:mm)(9)编写驾驶员控制文件(.dcf)和驾驶员控制数据文件(.dcd),操纵汽车沿双纽线中点"0"处的切线方向开始以10km/h的稳定车速沿双纽线路径行驶,同时记录汽车转向盘力矩、转向盘转角等数据。汽车行驶的轨迹如图11。
由仿真结果(图12-图13)中可以看出,汽车以10km/h的车速沿双纽线行驶时方向盘左转最大转角638.5°,右转最大转角663.1°,方向盘最大作用转矩9584.56N.mm,平均转矩3185.27N.mm。转向轻便性各项评价参数计算结果如表1。
转向盘平均操作力Fs的评价计分为:
NFs=60+40Fs60-Fs100
·(Fs60-Fs)=97.78(10)
式中
Fs60———转向盘平均作用力的上限值50NFs100———转向盘平均作用力的下限值15N
Fs———转向盘平均作用力的仿真值
转向盘最大操作力Fm的评价计分为:
NFm=60+
40Fm60-Fm100·(Fm60-Fm)=83.22(11)
式中
Fm60———转向盘最大作用力的上限值80N
Fm10———转向盘最大作用力的下限值30NFm———转向盘最大作用力的仿真值
转向轻便性试验的综合评价记分为:
NQ=NFs
+ηF·NFm
1+ηF=83.31(12)式中
ηF———0.6+0.08Ga
Ga———汽车最大总质量。
3.2.2ISO双移线试验仿真
双移线试验是综合测定人-车操纵性的闭环试验,它起源于本世纪60年代,在欧洲人们驱车追赶麋鹿时,麋鹿喜欢换道奔跑,而追赶的汽车常常在第二个转弯处发生侧翻,于是原联邦德国汽车委员会提出双移线试验用于评价汽车的抗侧倾能力及其追随性能。双移线道路设置(图14)按照ISO/3888标准[10]。
图13方向盘转矩-方向盘转角曲线
图11
转向轻便性仿真汽车行驶轨迹
图12方向盘转角随时间变化曲线
(转向盘直径376mm)
表1
转向轻便性仿真结果
转向盘最大作用力转向盘平均
作用力转向盘
所做功转向盘平均摩擦力矩
转向盘平均摩擦力50.98N
16.94N
273.42J
6017.9N.mm
6017.9N
图14
双移线道路设置
图15双移线仿真汽车行驶轨迹
图16侧倾角随时间变化曲线
操纵以汽车初始速度为100km/h,五档行驶,汽车沿前进方向行驶250米后停止仿真,仿真时间由
汽车初始速度决定,仿真过程及结果如图15-图17:
通过仿真结果可以得出,该车以100km/h的速度可以平顺的通过双移线通道,通过双移线通道的时间为9秒,汽车最大响应均发生在第二个转弯处,通过时最大侧倾角1.55°,最大横摆角速度14.27deg/s,最大侧向加速度0.6g,可以看出仿真汽车能以较高的稳定车速很好的按照设计轨迹行驶,该车具有满意的追随性能和抗侧翻能力。
虚拟样机技术的不断发展,使汽车计算机仿真模型能够更加精确地描述实际汽车,其性能仿真结
果也越来越接近试验测试结果,建立“虚拟汽车”和“虚拟试验场”是汽车CAE工程的必然趋势[11]。利用数字化样机技术通过将设计—试验—改进设计—再试验的设计理念转变为设计—仿真—试验,使设计中的主要问题在设计初期得以解决[12],尤其在今后考虑ESP、VSC等动力学与控制集成问题时可与Matlab联合仿真,数字化样机技术必将发挥更大作用。本文利用Adamas/car对公司内某一款新开发车型进行多体动力学建模,对后悬架板簧采用有限元方法建立其柔性体模型,组成刚弹耦合整车动力学模型,通过Adamas/car中整车分析与驾驶员控制模块相结合,对建立的虚拟样机模型进行开路系统与人-汽车闭路系统操纵稳定性仿真,预测新研制车辆的动力学性能,得出以下结论:
1
该车具有不足转向稳态响应特性,特征车速
80km/h,并随着车速的提高,不足转向有加强趋势。
2瞬态响应分析时,与同类车型相比,该车反应时间较长,横摆角速度峰值响应偏大,瞬态响应特性有待改进。横摆角速度频响分析中,共振峰频率偏低,动态响应特性较差。
3
该车低速行驶时,平均操舵力不大,但在方
向盘大转角工况下,操舵力迅速上升,该车转向盘
力特性有待改进。
4该车具有良好的抗侧翻和追随性能。
由于多体动力学模型在建立过程中进行了必要的假设和简化,各刚体部件之间采用理想副联接并且大量使用橡胶衬套元件,仿真分析结果与实际会有一定误差,但完全可以满足工程需要。本次仿真输入参数由设计部门提供,分析结果对汽车操纵稳定性设计具有指导意义。随着世界经济的一体
化,市场竞争日趋激烈,国内汽车企业应加快虚拟样机仿真和相关试验数据库积累,提高仿真分析在新产品研发中的作用,虚拟样机仿真取代试验将会极大地缩短开发周期,降低产品研发成本,为企业生存争得一席之地。
参考文献
1陈立平,张云清等.机械系统动力学分析及ADAMAS应用教程[M].清华大学出版社,2006:9 ̄11.
2胡景煌,汪文龙,周梅.车辆操稳性的虚拟样机技术研究[J].合肥工业大学学报,2007(7):817 ̄820.
3MDI公司.Adams/carFullSimulationTrainingGuide.Version12,56 ̄61.
4Schiehlen,W.OMultibodysystemdynam-ics-Rootsandperspective[J],MultibodySystemDy-namics.1997(1):67 ̄82.
5张守元,沈磊.基于Adams的某商务车前悬架K&C性能分析与优化设计[J].轻型汽车技术.2009(5/6):4 ̄9.
6MDI公司.Adams/carUserManual.1997(3):76 ̄83.
7余志生.汽车理论[M].机械工业出版社,2007:147 ̄151.
8汪文龙.车辆操纵稳定性的虚拟仿真技术研究[D].合肥工业大学,2006(5):43 ̄45.
9李白娜.汽车操纵稳定性的仿真分析研究[D].华中科技大学,2006(5):35 ̄40.
10PassengerCars-testforaseverelanechangemanoeuvre-Part1:Doublelanechange.ISO-2-2002.
11岑少起,潘筱,秦东晨.ADAMS在汽车操纵稳定性仿真中的应用研究[J].郑州大学学报,2006(9):55 ̄58.
12李显生,高延龄,王云鹏.提高商用车操纵稳定性的研究[J].汽车工程,2000(3):197 ̄200.
4结论
图17
横摆角速度随时间变化曲线
虚拟制造技术内容简介
虚拟制造技术内容简介 课程编号:B0200006C课程名称:虚拟制造技术 英文译名:Fundamentals of Virtual Manufacturing 适用学科:机械制造及其自动化、机械电子工程、机械设计及理论 先修课程:CAD/CAM技术基础、机械制造技术基础、计算机组成技术、 C语言程序设计 开课院(系):机电工程学院机械制造及自动化系 任课教师:姚英学、李建广 内容简介: 在介绍虚拟制造技术的发展历程与现状、虚拟制造的定义与分类、虚拟制造技术的应用等内容的基础上,主要讲解虚拟制造系统的工作原理、分类与组成、虚拟现实的原理及其在制造工程中的应用、虚拟产品建模与描述、虚拟制造中的典型数学算法、数字化样机技术、数字化加工技术、数字化装配技术、数字化生产车间、虚拟产品开发与管理、虚拟制造系统开发,最后简要介绍虚拟企业的概念、关键技术和应用。 主要教材: 1.姚英学,李建广编.《虚拟制造技术及其应用》.哈尔滨工业大学出版社(待出版) 2.朱名拴,张树生等编著.《虚拟制造系统与实现》.西北工业大学出版社2001.10 参考文献: 1.姚英学等编.《CAD/CAM技术基础》.高等教育出版社200 2.1 2.周祖德编.《数字化制造》.科学出版社2006.6 3.肖田元等著.《虚拟制造》.清华大学出版社200 4.8 4.汪成为,高文,王行仁。《灵境(虚拟现实) 技术的理论、实现及应用》,北京:清 华大学出版社,1996. 5.Andrew Kusiak. Intelligent Manufacturing Systems. Englewood Cliffs, N.J. : Prentice Hall, 1990
《虚拟样机技术》课程教学大纲
《虚拟样机技术》课程教学大纲 课程代码:020232030 课程英文名称:Virtual Prototyping Technology 课程总学时:32 讲课:32 实验:0 上机:0 适用专业:车辆工程能源与动力工程 大纲编写(修订)时间:2017.5 一、大纲使用说明 (一)课程的地位及教学目标 本课程为车辆工程、能源与动力工程专业学生的一门专业基础选修课,ADAMS作为机械系统动力学分析软件,在汽车等领域有着广泛的应用,它改变了传统产品设计开发过程,可以大大缩短产品开发周期,降低开发费用和成本,提高产品性能,获得最优化和创新的设计产品。通过本课程的学习,使学生掌握ADAMS软件中虚拟样机的仿真建模工具及汽车模块的应用,培养学生应用大型工程软件解决问题的能力,为毕业设计进行知识储备并奠定基础,使学生毕业后能够适应社会的发展。 本课程将系统地介绍机械系统动态仿真技术,从设计和创新设计的角度出发,结合大量的实例,介绍ADAMS入门的基础知识、虚拟样机的基本概念及ADAMS软件的主要功能和操作技巧。通过学习这门课程,培养学生解决实际问题的能力,使学生能够较全面地了解掌握ADAMS软件的使用方法,了解在ADAMS软件环境下进行产品虚拟样机的开发过程。 (二)知识、能力及技能方面的基本要求 通过学习和练习使学生了解ADAMS虚拟样机技术的基本知识;掌握ADAMS软件的基本操作,熟悉软件的特性和使用方法;掌握基本的实际工作流程和处理方法。培养学生分析和处理实际问题的能力,能够独立面对问题、分析问题、解决问题。具体要求: 1、掌握ADAMS软件的使用。 2、能使用ADAMS软件,使学生具备在ADAMS软件环境下开发产品虚拟样机的能力,能完成一些简单机械系统的动力学分析。 (三)实施说明 教师在授课过程中可以根据实际情况酌情安排各部分的学时,课时分配表仅供参考。根据各专业特点,教师应结合本专业的实际问题,在教学过程中注意理论与实际结合,突出实际应用。 课程的教学目标通过教师演示讲授,学生课堂练习相结合来实现。采用现场教学模式,即在教师讲授演示的同时,学生同步在计算机上操作演练,强化教师与学生的互动。教师要注重对基本概念、基本方法和解题思路的讲解,以便学生在实际应用中能举一反三,灵活运用。 (四)对先修课的要求 要求学生先修:《机械制图》、《三维建模技术》、《汽车构造》等课程,并达到这些课程的基本要求,同时要求对三维CAD技术有一定的掌握。 (五)对习题课、实验环节的要求 根据课程的要求,结合专业特点安排一定的实例,如汽车悬模型及整车模型等,通过课堂练、讲相结合完成。 本门课程是上机操作的课程,实践性很强。为了增强学生的动手能力,要求多媒体教学,并做到学生每人一台计算机并配备相应软件。
虚拟制造技术发展及应用.doc
虚拟制造技术发展及应用- 摘要:虚拟制造技术是近年来出现的先进技术之一,受到世界各个国家的高度重视。本文介绍了虚拟制造的定义、种类、关键技术及应用,展望其未来发展前景。 关键词:虚拟制造;仿真模拟;发展;应用 1.前言 随着市场的全球化,各种新兴技术在相关领域的综合使用,企业之间的竞争方式发生了巨变。制造行业遭遇了巨大的挑战,为了制造业能够更好的生存与发展,必须要满足市场所提出的多项要求:缩短产品开发周期、提高产品质量、降低制造成本以及用更好的技术支撑和售后服务来赢得客户的信赖。企业为了赢得市场,必须对市场形势做出准确评估和及时的调整,应对多变的市场需求。计算机软硬件技术及网络技术的迅速发展为实现这一目标提供了强有力的支持[1]。各种技术的发展及应用使得虚拟制造技术应运而生,作为一种全新的生产模式,必将给制造业指明新的前进方向。 2.虚拟制造技术 2.1 虚拟制造技术定义及特点 虚拟制造技术是对产品实际生产活动中的真实环境进行虚拟模拟,在计算机上得到数字化模型进而对生产活动进行分析、评估。产品研制过程中,通过仿真模拟建模技术模拟出产品在后续制造过程中的虚拟环境,分析各个环节甚至整个产品生命周期可能出现的活动对产品性能各方面的影响。通过虚拟环境下的情景展示及分析结果,尽早的发现生产活动中可能存在的隐患与问题,及时的信息反馈改进设计,合理的调整生产活动。降低研制
成本和产品开发周期,减少实际生产活动中带来的损失,更加合理的控制生产活动,提高企业生产效率,最终提高企业在市场中的综合竞争力。 2.2 虚拟制造的种类 广义的制造过程不仅包括了产品的模型研发、样机制造、性能测试、实体生产。同时还有企业对自身生产活动的市场调查、经营策划和实际生产活动中的调整控制。按这个思想考虑,虚拟制造可以被分为三大类:以设计为中心的虚拟制造、以生产为中心的虚拟制造和以控制为中心的虚拟制造[2]。 以设计为中心的虚拟制造强调根据产品的制造信息仿真建模得到统一的数字化模型,分析模型中的各类问题对产品各方面性能和产品的可装配性进行分析。以生产为中心的虚拟制造强调根据不同企业所拥有的设备资源等约束条件,仿真模拟各个加工过程结合企业的制造资源及环境进行加工过程的合理组合,使得生产计划更加合理优化。以控制为中心的虚拟制造强调将在企业管理控制中引入仿真模拟技术,对实际生产活动的环境进行虚拟模拟,提供虚拟环境模型使得企业对生产活动的控制更优化。 2.3 虚拟制造的关键技术 3.虚拟制造技术应用 3.1 虚拟制造技术在国外的应用 国外关于虚拟制造技术的应用已经有一定的规模,积极投入到各行各业的应用当中,完成相应的生成计划和目标,将市场需求的产品及时的投入到市场并收到良好的效果。在美国,波音公司生产的波音777客机是虚拟制造技术应用的经典产品。该机的设计研制包括众多的零部件,虚拟制造技术使得所有零部件的设计和改进全部是在由计算机组成的虚拟环境中完成,使得设计
虚拟制造技术
1、前言 随着国民经济的高速发展,人民生活水平的大幅提高,人们对汽车的需求量越来越大,汽车模具的市场竞争也越来越激烈。“质量好”、“精度高”、“价格低”、“交货期短”等是人们对现代汽车模具的基本要求。但是,汽车模具是一种大型模具,它体积庞大、结构复杂、尺寸精度和表面粗糙度要求较高,制造相当困难。而且,为了减轻模具的重量采用的底座掏空的薄壁式结构和为了维修容易中间型面采用的镶拼结构,给设计和制造带来了更大的困难。通常来说,一个汽车覆盖件零件需要3道或3道以上的工序才能完成,也就是说,生产一个汽车覆盖件零件至少需要3副或3副以上的模具。如果汽车覆盖件零件在设计的时候没有考虑到实际制造情况,那么设计出来的模具在制造的时候可能根本就无法进行加工,或者是制造出来的模具无法生产出预期的产品,从而导致模具的报废,延长产品的开发周期,这种经济损失是无法想象的。但是,模具在设计阶段是无法预料在制造过程中将出现的困难的。虚拟制造技术是一种软件技术,是CAD/CAE/CAM/CAPP和仿真技术的更高阶段,它能在计算机上实现模具从设计到制造到检验的全过程,根据虚拟模型的仿真过程,可以在计算机上根据“实际”的加工情况来修改模具的设计,避免了在模具制造过程中可能出现的问题,从而达到缩短模具的开发周期、降低开发成本、提高生产效率的目的,因而是汽车模具开发最有潜力最实用最有效的技术之一。 2、虚拟制造(VM) 虚拟制造(VirtualM anufacturing)又叫拟实制造,是80年代后期美国首先提出来的一种新思想,它是利用信息技术、仿真技术、计算机技术等对现实制造活动中的人、物、信息及制造过程进行全面的仿真,以发现制造中可能出现的问题,在产品实际生产前就采取预防措施,使得产品一次性制造成功,以达到降低成本、缩短产品开发周期,增强企业竞争力的目的。在虚拟制造中,产品从初始外形设计、生产过程的建模、仿真加工、模型装配到检验整个的生产周期都是在计算机上进行模拟和仿真的,不需要实际生产出产品来检验模具设计的合理性,因而可以减少前期设计给后期加工制造带来的麻烦,更可以避免模具报废的情况出现,从而达到提高产品开发的一次成品率,缩短产品开发周期,降低企业的制造成本的目的。 虚拟制造自从产生以来人们就力图给它一个统一的定义,但虚拟制造涉及的知识范围十分广泛,不同的研究人员,出发点和侧重点也不同,因而理解也大不相同,导致虚拟制造至今为止仍没有一个确切的定义。在不同的定义中,我们可以把虚拟制造理解为产品的虚拟设计技术、产品的虚拟制造技术和虚拟制造系统3方面关键技术的一个技术综合。 2.1 产品的虚拟设计技术(VDT) 产品的虚拟设计技术(VirtualD esignT echnology)是面向数字化产品模型的原理、结构和性能在计算机上对产品进行设计,仿真多种制造方案,分析产品的结构性能和可装配性,以获得产品的设计评估和性能预测结果,从而优化产品设计和工艺设计,减少制造过程中可能出现的问题,以到达降低成本、缩短生产周期的目的。 2.2 产品的虚拟制造技术(VMT) 产品的虚拟制造技术(VirtualM anufacturingTechnology)是利用计算机仿真技术,根据企业现有的资源、环境、生产能力等对零件的加工方法、工序顺序、工装及工艺参数进行选用,在计算机上建立虚拟模型,进行加工工艺性、装配工艺性、配合件之间的配合性、连
浅谈虚拟样机技术
虚拟样机技术及应用 (课程考试) 题目: 浅谈虚拟样机和虚拟样机技术学生: 陈川 班级: 机制1001班 学号: 2010200626 指导教师: 王春光
浅谈虚拟样机和虚拟样机技术 一虚拟样机产生的背景 进入21 世纪, 科学技术突飞猛进, 社会发展日新月异。人们对个性化产品的需求越来越迫切, 对产品性能的要求也越来越高, 全球化经济已明显地呈现出买方市场的特点。由于这一变化, 导致市场竞争日趋激烈, 而竞争的核心则主要体现在产品创新上, 体现在对客户的响应速度和响应品质上。传统的物理样机在产品的创新开发中, 在开发周期、开发成本、产品品质等方面已越来越不能满足市场需求, 虚拟样机技术正是在这一市场需求的驱动下产生的。 传统的产品设计模式通常采取的是一种设计→制造→试验→改进→设计的串行设计模式,尽管在结构设计方面采用CAD、CAE等软件,但由于不同学科软件相对独立性,产品的性能指标往往是通过大量的试验来确定特征参数。而且降低了产品的总体性能,使产品研发周期长、效率低。 如在传统的印刷机械设计工作过程中,都是由工程师先根据机器功能改进的需要,进行理论选型,然后计算结果,画出机械零件图、部件图和装配图,再交给车间进行试制。待样品出来以后,对样品进行运转测试,把测试到的实际结果与设计前的理论构想进行比对,寻找差异产生的原因,再重新进行设计上的修改,直到样品满足改进的需要。这种设计过程,需要的周期长,样品试制费用高,往往不能满足市场对新机器换代及时性的要求,带来了人力物力的巨大浪费。为了改变这些现象,提高产品的性能,缩短生产周期,降低生产成本,各行各业都在不断地创新,开发新的技术。这样通过不断地创新、改进,近年来终于找到了解决这些缺点的方法,并提出了虚拟样机技术。 二什么是虚拟样机 虚拟样机是建立在计算机上的原型系统或子系统模型,它在一定程度上具有与物理样机相当的功能真实度。 虚拟样机是一种计算机模型,它能够反映实际产品的特性,包括外观、空间关系以及运动学和动力学特性。利用这项技术,设计师可以在计算机上建立机械系统模型,然后以三维可视化处理,模拟在真实环境下系统的运动和动力特性并根据仿真结果精简和优化系统。 虚拟样机被美国国防部建模和仿真办公室(DMSO)定义为对一个与物理原型具有功能相似性的系统或者子系统模型进行的基于计算机的仿真;而虚拟样机则是使用虚拟样机来代替物理样机,对候选设计方案的某一方面的特性进行仿真测试和评估的过程。 虚拟样机的概念与集成化产品和加工过程开发 (Integrated Product and Process Development,简称IPPD)是分不开的。IPPD是一个管理过程,这个过程将产品概念开发到生产支持的所有活动集成在一起,对产品及其制造和支持过程
虚拟制造技术的内涵及应用
虚拟制造技术的内涵及应用 摘要:虚拟制造技术是一门新兴的先进制造技术。虚拟制造技术的应用应结合我国制造业自身的特点,在吸收国外成熟经验的基础上大胆创新,形成特色发展。本文分析了虚拟制造技术的内涵及特点,并提出了发展虚拟制造技术的应用。 关键词:虚拟制造内涵制造产品 虚拟制造作为信息时代制造技术的重要标志,它是不断吸收信息技术和管理科学的成果而发展起来的,这里的“制造”是一种广义的概念,即一切与产品相关的活动和过程,亦称之为“大制造”,这是相对于传统的狭义制造而言的。“虚拟”的含义则是这种制造虽然不是真实的、物化的,但却是本质上的,也就是在计算机上实现制造的本质内容。虚拟制造的实质是在产品制造过程的上游——设计阶段就对产品制造的全过程虚拟集成,将可能出现的问题解决在这一阶段,通过设计的最优化达到产品的一次性制造成功。 1.虚拟制造技术的内涵及其特点 1.1虚拟制造技术的内涵 虚拟制造是实际制造过程在计算机的本质实现,即采用计算机仿真与虚拟现实技术,在计算机上实现产品开发、制造以及管理与控制等制造的本质过程,以增强制造过程各级的决策与控制能力。 虚拟制造不是一成不变的技术,而是一个不断吸收各种高新技术而不断丰富其内涵的动态技术系统,它通过计算机虚拟环境和模型来模拟生产场景和预估产品功能、性能及可加工性等方面可能存在的问题,从而提高人们的预测和决策水平,它为工程师提供了从产品概念的形成、设计到制造全过程的三维可视及交互环境,使得制造技术走出主要依赖于经验的狭小天地,发展到了全方位预报的新阶段,它不是原有单项制造仿真技术的简单组合,而是在相关理论和已积累知识的基础上对制造知识进行系统化组织。 1.2 虚拟制造技术的特点 虚拟制造与实际制造相比,有如下特点: (1)虚拟经营和管理。作为虚拟制造的一个主要贡献——虚拟企业,使制造业在世界范围内的重组与集成成为可能,应用虚拟经营和虚拟管理,充分借助于企业外部力量,运用自身最强的优势和有限资源最大限度地提高企业的竞争力。 (2)高度集成。产品与制造环境均利用仿真技术在计算机上形成虚拟模型,在设计过程中,可用计算机对其进行产品设计、制造、测试,设计人员和用户甚
美国虚拟现实技术
美国虚拟现实技术发展现状、政策及对我国的启示 王健美,张旭,王勇,赵蕴华 (中国科学技术信息研究所,北京100038) 摘要:美国在虚拟现实技术领域拥有着无可争议的优势。不仅美国政府各部门积极资助虚拟现实技术的研发, 而且企业、高校及科研院所竞相掀起虚拟现实技术研究和应用热潮,同时它们还有一套适时有效的科技政策。 对美国虚拟现实技术的发展现状和相关政策法案的阐释,为我国相关技术领域的发展提供有益的借鉴。 关键词:虚拟现实;研发现状;科技政策;启示 中图分类号:G353.11∶TP391.9文献标识码:A Development Status and Policy of the Virtual Reality Technology of United States and their Enlightenment to China WANG Jianmei,ZHANG Xu,WANG Yong,ZHAO Yunhua (Institute of Scientific and Technical Information of China,Beijing 100038) Abstract:There is no doubt that the United States has superiority in the field of virtual reality technology.Several gov- ernment departments have been funding on the research and development of this technology,a surge of research and ap- plication into the technology has been found among large enterprises,universities and scientific research institutes.In ad- dition,they are carrying out a set of proper and effective science and technology policy.This article intends to provide some references for the development of relevant technology in China with a focus on the development status of the virtual reality technology and an good explanation on the policy and act of the technology concerned in US. Key words:virtual reality;current situation of research and development;scientific and technical policy;enlightenment 1引言 虚拟现实(Virtual Reality,简称VR)技术与多 媒体、网络技术并称为三大前景最好的计算机技术, 是一种综合计算机图形技术、多媒体技术、传感器 技术、人机交互技术、网络技术、立体显示技术以 及仿真技术等多种技术而发展起来的综合性技术 [1] 。 根据IEEE(电气和电子工程师协会)的定义,虚拟 现实是指在视、听、触、嗅、味觉等方面高度逼真 的计算机模拟环境 [2] 。用户可与此环境进行互动, 产生身临其境的体验。 VR技术起源于1965年Ivan Sutherland在IFIP
虚拟制造
1。虚拟制造的定义:虚拟制造是实际制造过程在计算机上的本质实现,即采用计算机建模与仿真技术,虚拟现实或可视化技术,在计算机网络环境下群组协同工作,模拟产品的整个制造过程,对产品设计,工艺规划,加工制造,性能分析,生产调度和管理,销售及售后服务等做出综合评价,以增强制造过程各个层次或环节的正确决策和控制能力2.映射的特性:(1)映射的定义域是实际制造过程,值域是虚拟制造过程,直接结果是全数字化产品,映射的介质是网络计算机环境。(2)该映射是非线性迭代过程,需要多次循环直到满足要求为止。(3)虚拟制造的结果千差万别,难以预测,因而可能是一个混沌的过程。(4)由于人是整个系统的主体,将人的智能以控制参数的形式复合进去,该映射在一定程度上也是可控的。由于不同的人其技术水平和经验不同,因而控制参数具有模糊特性。3 虚拟制造的优势:1缩短了产品的研发周期2 降低了产品的研发成本3 提供了一个先进的制造系统仿真平台4 虚拟制造系统是通过对实际制造系统进行抽象,分析,综合,得到实际生产的全部数字化模型 5 虚拟制造的相关技术包括:输入,输出设备及计算机硬件技术、集成这些硬件系统的电子技术和软件技术。6 虚拟制造技术的核心与关键技术:计算机仿真优化设计、三维建模技术和网络技术。7其他的先进技术有哪些: 1 计算机集成制造系统与虚拟制造系统2 敏捷制造与虚拟制造技术3 并行工程与虚拟制造技术4 精益生产与虚拟制造技术5 绿色制造与虚拟制造技术6智能制造与虚拟制造技术1 虚拟现实(VR、Virtual Reality)又称虚拟环境(VE):虚拟现实是由计算机生成的,通过视听触觉、嗅觉等多通道作用于用户,使之生产身临其境感的交互式计算机仿真,是一种可以创造和体验虚拟世界的计算机系统。2,虚拟现实的特征(1)多感知性(2)沉浸感(3)自治性(4)交互性3,虚拟现实的系统组成(1)检测输入装置(2)图像生成和显示系统(3)音频系统(4)力、触觉系统(5)高性能计算机系统(6)建模系统4虚拟对象的模型主要包括:几何模型、物理模型、运动模型、声音模型等5对象的几何模型:就是用来描述对象固有形状和外表的抽象模型,通常首先用三角形或多边形构造对象的几何外形,然后对几何模型进行纹理,颜色,光照等处理,后者称之为形象建模6 几何模型的生成方法:1测试法 2 CAD法 3二维视图变换法7 纹理的定义:是指物体表面细微的凹凸不平的条纹,可以用随机扰动法生成,即在表面各点法线方向附加微小的随机扰动量,从而产生表面微观不平度。1 虚拟制造系统的定义:是现实制造系统在虚拟环境下的映射,是现实制造系统的模型化,形式化以及计算机化的抽象描述和表示2 虚拟制造系统的功能需求:1工厂和产品生命周期中的全部活动的集成2 各种硬件软件人员及各种标准的集成虚拟世界与真实世界的集成3 虚拟制造系统的仿真需求:(1)虚拟制造系统的仿真是虚拟环境下的全方位仿真,是产品从设计生产销售到消费的全生命周期仿真(2)仿真器具有多种输入方式3)真实感输入4 虚拟制造系统的机构需求: 1 功能等价性(1)语义一致性(2)数值精确度(3)响应时间2 结构相似性3 开放性和柔性4 系统应满足分布式协同工作和动态运行操作5虚拟制造模式(前三种)1以设计为中心的虚拟制造为产品设计,产品评价和异地协同设计提供模拟环境。该环境集成了计算机分析,网络通信,可视化仿真技术等开发工具,以支持面向设计与管理的全球化合作2 以生产为中心的虚拟制造以生产为中心的虚拟制造主要研究内容包括车间设备的配置及分布,生产调度,生产环境的布局设计,设备集成,生产组织调度等。其输出是资源需求规划,生产规划,供货计划及精确的成本信息等3 以控制为中心的虚拟制造是将仿真加到控制模型和信息处理中,以实现基于仿真的最优化控制4 以加工为中心的虚拟制造以加工为中心的虚拟制造目标是研究产品的可加工性,6虚拟制造的结构体系结构有: Mediator体系、Iwata体系、分布式体系、虚拟开发平台体系等7 Mediator体系是通过一个开放式的信息和知识库体系,以提供一套支持复制制造环境的柔性管理技术。着重处理和解决了这种情况下的知识支持及通信技术。8 Mediator 体系是一个侧重于知识信息的管理体系,它考虑了多软件,多地域的集成9 Iwata体系的基本组成:虚拟信息系统VIS、虚拟物理系统VPS 、定时控制器和数据游览器组成10 系统建模是虚拟制造系统的核心,是构成虚拟制造的基础。在虚拟制造系统中,需要采用综合的、各阶段都连贯一致的模型表示方法,使后续操作可以利用前阶段的模型数据11 虚拟制造系统模型:实质上是真实制造系统要素的数字化表达,主要包括产品模型过程模型和生产系统模型,又称3P模型12 过程模型:过程模型有多种形式,如基于理论的物理模型和数字模型,基于经验的统计模型,基于计算机的过程仿真模型,以及列举方法表达的图表和规划等过程模型的有效表示是非常重要的,他提供了同虚拟制造环境的通信机制13 基础模型制造层用以建立描述制造过程及对象的基础模型14面向对象方法的基本特征:(1)抽象性(abstraction)(2)分类性(classification)(3)关联性(association)(4)组装(composition)(5)继承性(Inheretance)15结构式对象模型方法:结构式对象建模方法是基于面向对象方法的封装,继承与关联特性,利用派生图,对象图,事件转移图和状态转移图四种模型描述系统的组成及关系16 构成一个Petri网的基本要素有库所、变迁和令牌。17 问题求解是建立模拟系统的最终目的,归纳推理,演绎推理和推断推理是问题求解的基本方法18 从本质上说,多Agent系统是一种协同求解方法,全局目标的实现是各个Agent相互协作的结果19产品模型是用来表示制造过程中被制造对象的模型,它包括目标产品,零部件,毛坯及中间产品20 产品建模方法的发展过程:1 面向过程的产品模型2 面向几何的产品模型3 面向特征的产品模型4 面向知识的产品模型5 集成产品模型21 现代制造系统中的设备、仪器及工具主要包括物料处理设备和运输系统。22设备模型应当实现(1)物理设备几何特征的真实表达。可真实地复现物理设备的三维实体模型,体素特征和材料纹理特征。(2)物理设备系统操作的精确表达,以动画形式表达设备行为运动学,动力学信息。(3)系统性能,可靠性,灵敏性的精确估计。23 基本模型由基本模型—特征—体素三个层次组成,基本模型和特征为上层数据,而体素为底层数据。24 约束有一元约束和二元约束,尺寸约束属于一元约束,它包含一个几何参数和一个实值参数。1 STEP的定义:就是国际化标准组织(ISO)正在制定的一个产品数据表达与交换标准。STEP的目标:提供一种不依赖于具体系统的中性机制,能够描述产品整个生命周期中的相关数据STEP的标准体系结构: 1描述方法 2集成资源 3应用协议 4一致性测试方法论 5框架、实现方法 6抽象测试集虚拟样机的概念:在虚拟现实环境下模拟产品的设计、制造仿真、装配仿真等过程。4 虚拟样机与数字样机的区别:在CAD环境下的虚拟样机则采用数字样机的概念。5 数字样机按照承担的功能可分为:几何样机、性能样机、功能样机。6 数字样机关键技术包括:三维几何建模技术、产品数字化定义方法、数字化装配技术分析与仿真技术。7 三维几何建模方法:三维几何建模技术是数字样机的核心制程技术,它为数字样机的形状表达提供基本的建模工具和方法。四种方法:线框模型、表面模型、实体模型、特征模型。8 一个合理的产品结构不应当一颗装配书鼓励的表示,而应当使产品的结构具有产品定制功能、产品结构的整体控制功能。产品定制功能是通过产品结构树,根据用户的个性化需求,快速制定出一个产品的结构。10(论述题)数字化预装配数字化预装配是数字样机和虚拟设计的一个重要组成部分。其内容包括产品的装配建模、装配零件之间的约束、装配的间隙分析、可装配性分析与评价。(1)装配建模:包括产品结构设计和信息建模。在产品设计过程中,装配设计是在概念设计之后进行的,它可以将概念设计中的模糊、不确定的构思,通过产品结构和逐步求精细化,设计产品的整体装配结构,为详细设计提供一个基本框架。装配建模可以利用装配建模工具建立装配树。在装配建模中,信息量的大小是影响产品操作、浏览的一个重要因素,解决信息量大的方法有:(1)1)减少每次装配的零件数目。2)减少几何信息3)减少其他模型信息量(2).装配零件之间的约束数字化装配并不是简单的零件堆积,而是对装配零件进行几何或参数约束,模拟实际的装配条件。常见的约束类型有:面贴合、面对齐、角度约束、平行约束和垂直约束、对称约束、距离约束、相切约束(3).装配的间隙分析数字样机通过奸细分析判断装配的可行性。目前的装配间隙分析主要是从静态的干涉角度进行检查。主要有5钟干涉检查结果:无干涉、软干涉、接触干涉、硬干涉、包容(4).可装配性分析与评价可装配性指产品及其装配件易装配的能力和特性,是衡量装配结构优劣的重要指标11 并行设计:是以并行工程的思想贯穿于产品设计过程的一种集成化设计方法。12 DFM方法强调制造对设计的约束,在产品的设计阶段,分析制造因素对设计的影响。13 产品可制造性评价指标:技术指标、经济指标。1 虚拟装配系统包括:虚拟装配环境、虚拟零件设计、装配工艺规划、工作面布置、装配操作模拟2虚拟现实的三个特点:沉浸感、交互性、想象力3 装配工艺规划是连接装配设计和装配实施的桥梁。4 所谓装配序列的几何可行性是指:从几何约束角度来讲,两个装配单元之间的装配操作或分解操作不存在几何干涉现象。5 装配序列生成时所需要的装配信息主要包括零件的几何信息、非几何信息以及零件之间配合约束关系信息。6装配序列规划分类:1按装配的单调性分(1)单调装配规划(2)非单调装配规划2 按装配的序列性分(1)序列装配规划(2)非序列装配规划3 阿布装配的线性或非线性分(1)线性装配规划(2)非线性装配规划7 装配路径规划的内容主要包括:装配体及其相关的数据结构模型的前置处理、分离方向的确定、分离平移量的确定、拆分方向的确定和干涉检查。8 数字化装配路径规划方法主要有两种:可视图法和平移边界法。9 装配序列的选择方法:基于最短时间的装配序列、基于最低成本的装配序列、基于装配设备利用率最高的装配序列。1加工过程仿真包括:NC切削过程仿真、焊接过程仿真、冲压过程仿真、浇注过程仿真。2 切削过程仿真研究内容:1是刀具路径仿真2是评估加工工艺中规定的工艺参数是否合适。3 (论述)虚拟加工环境及系统应该具有以下功能1全面逼真的反应现实加工过程,在仿真中,人们可以直接“观察”全部的加工过程包括工件的装夹定位、机床调整、切削、检测等。2 可以真实的描述加工过程的物理效应,例如工件的切削温度与应力的分布,工件的变形等 3 能对加工过程中出现的碰撞、干涉进行检测,并提供报警。4 可以对工夹具的实用性进行评估,对产品的可加工性和工艺规程的合理性进行评估 5 对加工精度、表面粗糙度、加工时间等进行精准的估计,为宏观仿真提供数据。4 虚拟加工过程定义:在NC指令的驱动下,由机床刀具模型的运动过程和工件模型的变形过程构成5 虚拟加工过程4个仿真:1刀具运动轨迹的仿真 2夹具安装使用过程仿真 3机床运动过程仿真。4材料去除仿真。6在虚拟环境中,加工过程表现为包括时间在内的四维过程,建模时,需要将表达加工环境的实体几何模型、运动模型和表达加工过程的物理模型结合起来。7 数控机床零件几何模型之间的装配约束关系主要包括三类:几何约束、运动约束和排斥约束。8 数控机床定义:通过数控系统控制机床个运动轴的运动来实现工件与刀具之间的相对运动,从而完成切削加工的空间机构。9数控加工过程几何仿真技术包括定性图形显示和定量检验二个方面。根据建模方法特点,将数控加工过程几何仿真技术分为四类:直接实体建模、光线表示法、离散矢量法和空间分割法。10碰撞与干涉:主要包括检验刀具和主轴相对于非加工部位如夹具、工件非加工部位的干涉现象。碰撞与干涉检测方法:包容盒检测法、分层检测法。11 刀具轨迹生成目标:使所生成的刀具轨迹满足无干涉、无碰撞、轨迹平滑、切削负荷定性好、编程效率高、代码量小的要求。12刀具轨迹生成方法:1参数线法 2CC路径截面法 3CL路径截面法 4导动面法 5等距面法 6刀具接触点法13 NC加工过程物理建模与仿真包括:1切削力的建模与仿真 2切削温度的建模与仿真3加工震动模型 4加工误差模型与评估 5加工表面粗糙度预测与仿真。14表面粗糙度是最重要的表面质量特征参数之一。
虚拟样机技术概述
虚拟样机技术概述 1.1.行业背景 多年来,制造业完全依赖于物理样机来解决和交流设计过程中的问题,这就使得制造成本增加和产品设计时间的延长(见表1)。然而,近年来,制造业者已经认识到物理样机在快速抢占市场上已严重阻碍了其发展,成为发展过程中的一个重要障碍。 为了突破这个障碍,很多制造业者(如Boeing ,GM, Caterpillar ,Ford等)开始研究使用虚拟样机,而减少对物理样机的依赖。他们并不完全排除物理样机,只是减少物理样机的数量,用虚拟样机的灵活性去完成物理样机不能完成的功能。例如,90年代Boeing公司用虚拟样机技术用在波音777上取得了极大的成功,他们仅用一个较小的物理机头模型就在四年内把这种飞机推向市场(Boswell, 1998)。Caterpillar公司也同样利用这个技术应用于他们的履带机设计,他们发现这种技术在解决设计评审阶段节省了9个月时间(Ellis, 1996)。 表1 物理样机成本 虚拟样机的成功有两项关键技术,第一,实时的3D图形特性和位图质量要达到一定的标准,要求硬件产生的高质量位图包括150,000到250,000个三角形的数据。另外,这些位图刷新速度要达到交互速度的要求。第二,投影和其它显示技术的发展使得高清晰度的立体图像能被建立。结合这两项技术,虚拟样机赢得了一些评论家的关注。现在,这种技术也面临着有激烈地争议,但虚拟样机的高成长性和广泛应用已成为事实。 物理样机被用于解决贯穿整个生产过程的问题。通常情况下,一些独特的模型对解决某些关键的问题是必须的。表2列出一些通过样机解决的问题和关心
的主要问题。 下面给出虚拟样机技术在工业中的三个具体应用层面: 1.建立可信的图像 2.产品设计与制造过程的集成(DFM) 3.虚拟样机和现有测量工具的结合 表2 原型问题 1.2.虚拟样机的关键技术 1.2.1.建立可信赖的1:1产品虚拟原型 建立可信的图像是一个核心要求。目前,绘图师和设计师都用不同的射线跟踪包(沿物理样机)去形成高真实的图像或动画电影。这些工具对于交流是非常有用的,他们也能描述必需的经验上的碰撞。当你在墙上看到这些图像时,你就会想象你正经历着这个产品,或正在看它漂亮的图片。这种预先渲染的技术限制了通常物理样机所提供的探测和交互的种类。例如,你不能进入图像的内部和感受到聚集在你周围的场景。这种情况下,具有现实性的图像并没有充分的理由代替物理样机。既然这样,使用这种技术生成的虚拟样机的应用的可信度就会大打折扣,因为它们限制了探测场景的比例和现场的沉浸感。 当计算机可视化的价值得到工业界的普遍认可时,具有“沉浸感”的虚拟样机还是被许多专家持怀疑和观望态度。但当它呈现出高可信度的图像和虚拟样机时,这种怀疑的态度就会消失。虚拟样机的展示,的确给观察者一种与物理样机同处一室的感觉,这时,观察者就会认为他看到的虚拟样机是真实的。
虚拟制造技术及其应用外文文献翻译、中英文翻译、外文翻译
附录1 外文译文 虚拟制造技术及其应用 摘要:阐述了虚拟制造的基本概念,虚拟制造的核心技术,以及虚拟制造技术应用。 关键词:制造业虚拟制造虚拟现实 0 引言 当今的制造业基本技术日臻成熟,其市场处于以消费者为导向的市场环境下,产品品种、上市时间和用户满意度成为企业取得竞争优势的主要因素。制造业这种全球化的激烈竞争不断催生了各种先进制造技术和新的制造哲理,虚拟制造技术将会在本世纪涌向潮头,其朴素的思想和高新的技术手段都为研究领域和业界所推崇。 虚拟制造就是根据企业市场竞争的需求,在强调柔性和快速的前提下,美国80年代提出的,随着计算机技术和信息网络技术的发展,在90年代得到人们的重视,并获得迅速的发展。 1 虚拟制造 虚拟制造的基本思想是在产品制造过程的上游——设计阶段就进行对产品制造全过程的虚拟集成,将全阶段可能出现的问题解决在这一阶段,通过设计的最优化达到产品的一次性制造成功。 虚拟现实技术是使用感官组织仿真设备的真实或虚幻环境的动态模型生成或创造出人能够感知的环境或现实,使人能够凭借直觉作用于计算机产生的三维仿真模型的虚拟环境。基于虚拟现实技术的虚拟制造技术在一个统一模型之下对设计和制造等过程集成,它将与产品制造相关的各种过程与技术集成在三维的、动态的仿真真实过程的实体数字模型之上。其目的是在产品设计阶段,借助建模与仿真技术及时地、并行地、模拟出产品未来制造过程乃至产品全生命周期的各种活动对产品设计的影响,预测、检测、评价产品性能和产品的可制造性等等。从而更加有效的、经济的、柔性的组织生产,增强决策与控制水平,有力地降低由于前期设计给后期制造带来的回溯更改,达到产品的开发周期和成本最小化、产品设计质量的最优化、生产效率的最大化。 虚拟制造系统是各制造功能的虚拟集成,它的可视化集成范围包括与设计相关的各项子系统的功能,如用户支持、工程分析、材料选用、工艺计划、工装分析、快速原型,甚至包括制造企业全部功能(如计划、操作、控制)的集成。 虚拟制造系统拥有产品和相关制造过程的全部信息,包括虚拟设计、制造和控制产生的数据、知识和模型信息。虚拟控制制造系统按照功能归集为三种不同类型的子环境,共同构成中心三元耦合的系统模式: (1)虚拟制造设计中心:给设计者提供各种工具以便虚拟设计、虚拟制造,设计出符合设计准则(如DFX)的产品模型; (2)虚拟制造加工中心:研究开发产品制造过程模型和环境模型及其分析各种可行的生产计划和工艺规划; (3)虚拟制造控制中心:评价产品设计、产品原型、生产计划、制造模拟和控制策略等等。 2 虚拟制造技术支持 虚拟制造技术是多学科综合的系统技术,需要研究开发相应的硬件集成系统与软件,就软件技术而言,相关的研究支持如下: 可视化:真实、直观地再现主观产品与客观制造过程;
虚拟制造的发展及应用
虚拟制造的发展及应用 摘要:虚拟制造技术作为近几年出现的先进制造技术,本文在描述了虚拟制造技术的概念,我国虚拟制造技术发展现状,发展展望及应用。 关键词:虚拟制造技术;计算机仿真;虚拟现实;发展;应用 虚拟制造技术是在CAD/CAM/CAE技术基础上发展起来的。一方面,CAD/CAM/CAE技术为虚拟制造的实现提供了较为成熟的技术基础,如建模技术、分析优化技术、制造过程仿真技术、分析评价技术、设计分析评价技术和产品信息集成、转换、共享技术等。特别是特征建模技术在虚拟制造技术中占有极为重要的地位。另一方面,虚拟制造技术超越了CAD /CAM/CAE技术,CAD/CAM/CAE技术主要考虑产品本身信息的集成与建模,而虚拟制造技术还要考虑加工过程的建模等问题。 虚拟制造技术的基本概念 虚拟制造技术VMT是20世纪80年代后期提出并得到迅速发展的一个新思想。它是以虚拟现实和仿真技术为基础,对产品的设计、生产过程统一建模,在计算机上对产品从设计、加工和装配、检验、使用等整个生命周期进行模拟和仿真。采用虚拟制造技术,可以在产品的设计阶段就模拟出产品及其性能和制造过程,以此来优化产品的设计质量和制造过程,优化生产管理和资源规划,使产品的开发周期和成本最小化。 虚拟制造技术的发展现状 虚拟制造在工业发达国家:如美国、德国、日本等已得到了不同程度的研究和应用。美国处于国际研究的前沿。1 983年美国国家标准局提出了“虚拟制造单元”的报告,1 993年爱荷华大学的报告“制造技术的虚拟环境”中提出了建立支持虚拟制造的环境:1 99 5年美国标准与技术研究所的报告“国家先进制造实验台的概念设计计划”,强调了分散的、多节点的分散虚拟制造IDVM(即虚拟企业的概念)。美国已经从虚拟制造的环境和虚拟现实技术、信息系统、仿真和控制、虚拟企业等方面进行了系统的研究和开发。多数单元技术已经进入实验和完善的阶段。 我国在虚拟制造技术方面的研究只是刚刚起步。其研究也多数是在原先的CAD/CAE/CAM和仿真技术等基础上进行的。目前主要集中在虚拟制造技术的理论研究和实施技术准备阶段,系统的研究尚处于国外虚拟制造技术的消化和与国内环境的结合上。当前我国虚拟制造应用的重点研究方向是基于我国国情的产品三维虚拟设计,加工过程仿真和产品装配仿真。
虚拟制造技术
虚拟制造技术 制造业的发展对产品性能、规格、品种不断提出新的要求,产品的生命周期越来越短,新产品的开发时间是决定性因素。虚拟制造(virtual Manufacturing , VM )技术可以模拟由产品设计、制造到装配的全过程,对设计与制造过程中可能出现的问题进行分析与预测,提出改进措施,实现产品从开发到制造整个过程的优化,达到降低产品生命周期、减小开发风险、提高经济效益的目的。而机械加工过程仿真在虚拟制造中占有重要地位,它通过对机床一工件一刀具构成的工艺系统中的各种加工信息的有效预测与优化,为实际加工过程智能化的实现创造了有利条件,同时它也是研究加工过程的重要手段。 1 .虚拟制造的提出 从虚拟制造形成发展的过程来看,虚拟制造概念的最初提出与虚拟现实的出现有关。但是随着虚拟制造被广大学者接受的同时,虚拟制造的外沿也逐渐扩大。可以认为,虚拟制造技术就是利用计算机仿真、多媒体、传感器等技术将现实的产品设计制造过程虚拟化,其本质是以计算机仿真技术为前提,对设计、制造等生产过程进行统一建模,在产品设计阶段或产品制造之前,就能实时地并行地模拟产品的制造全过程及其对产品设计的影响,预测产品的性能、成本和可制造性,从而有助于更有效、更经济灵活地组织生产制造,使工厂和车间的资源得到合理配置,使生产布局更合理、更有效,以达到产品的开发周期和成本的最优化、生产效率的最高化等目的。 为了论证VM 技术在英国制造工业实现的可行性和其在制造中的技术潜力,英国Nottingham 大学的SueV · G · Cobb 等构造了一个虚拟示范工厂,包括虚拟设计一制造一检测几个环节,以便对虚拟制造技术的可行性进行演示和验证。其演示的内容包括: l )对一个“虚拟雕塑”进行建模,即尺寸的形成、修改、调整和着色; 2 )通过设计、制造和测试交互,形成快速原型; 3 )在工厂车间中进行漫步; 4 )视点的快速变换― 外部视点、内部视点和自主视点; 5 )对设备操作控制进行训练; 6 )制造过程中几个阶段的可视化; 7 )对制造质量进行工程学的评估。 虚拟示范工厂的开发者们在英国工业范围内选出了23 个有代表性的企业,如机械工业、汽车发动机制造业、建筑业、信息工业、零售业等,组织相关人员参观、控制和操作虚拟系统,并自行决定如何与虚拟系统进行交互。然后进行讨论并填写一些表格,回答对演示特征的印象、对工业领域的实用性和能否激励工程师和设计者使用VM 技术等问题。可行性研究的综合结果表明,几乎所有的被调查对象都深刻地认识到VM 技术在他们公司的应用前景是光明的,并且希望在下一个5 年内能用上它.
浅谈虚拟制造技术的研究及应用
浅谈虚拟制造技术的研究及应用
摘要:虚拟制造技术是在激烈的市场环境下所产生的应对措施之一,同时也是信息技术与制造科学相结合的产物。本文主要介绍了虚拟技术的定义、分类和支撑技术,归纳总结虚拟制造技术目前的研究和应用现状,并对虚拟制造的应用前景及发展方向进行展望。 关键字:虚拟制造;支撑技术;研究;应用 1 引言 随着科学技术的飞速发展和顾客需求的日益多样化,现代制造业面临全球范围的激烈竞争。虚拟制造作为新出现的技术,它能够在产品设计开发的各个阶段把握产品制造过程的实况,找出各个阶段可能出现的问题,有效地协调设计与制造环节的关系,以寻求企业的最有效益。从而能够降低了研发周期和研发资本,能够快速响应市场,适应现代制造业对产品T(time)、Q(quality)、C(cost)、S(service)、E(environment)的要求,极大地促进了敏捷制造的发展,推动了制造业的数字化、网络化、智能化。 2 虚拟制造技术的定义 虚拟制造技术(virtual manufacturing, VM)是使用计算机模型和制造过程的仿真,以辅助被制造产品的设计与生产。包括从生产开始就实时地、并行地对产品结构、工作性能、工艺流程、装配调试、作业计划、物流管理、资源调配及成本核算等一切生产活动进行仿真,检查产品的可加工性和设计的合理性,预测其制造周期和使用性能,以便及时修改设计,更有效地灵活组织生产。虚拟制造可以缩短产品的研制周期、获得最佳的产品质量、最低的成本和最短的开发周期。
虚拟制造,顾名思义,是一种不同于现实制造的制造技术。它不生产真实产品,基本不消耗材料和能量,而是利用制造对象、制造资源和制造工程的模型来展现“制造”的本质过程。虚拟制造技术是多种计算机辅助技术面向产品全生命周期的集成化综合应用。它不是对已有各单项技术的简单组合,而是对制造知识进行系统化组织,对产品对象、制造资源和制造活动进行全面建模。由于计算机软硬件技术和网络技术的广泛应用,虚拟制造具有以下几个特点: ⑴无须制造实物样机就可以预测产品性能,节约制造成本,缩短产品开发周期。 ⑵产品开发中可与及早发现问题,现实及时的反馈和更正; ⑶以软件模拟形式进行产品开发; ⑷企业管理模式基于 Intranet 或 Internet,整个制造活动具有高度的并行性。 3 虚拟制造的种类 按照与生产各个阶段的关系,虚拟制造可分为成为三类。即以设计为核心的虚拟制造,以生产为核心的虚拟制造和以控制为核心的虚拟制造。 “以设计为核心的虚拟制造”是将制造信息加入到产品设计与工艺设计过程中,在计算机中生成制造过程原型,对多种制造方案进行仿真,对数字化产品模型的性能、可制造性、可装配性、成本等进行分析,优化产品设计和工艺设计,以期尽早发现产品设计及工艺过程存在的问题。