SMC生产日期代码表
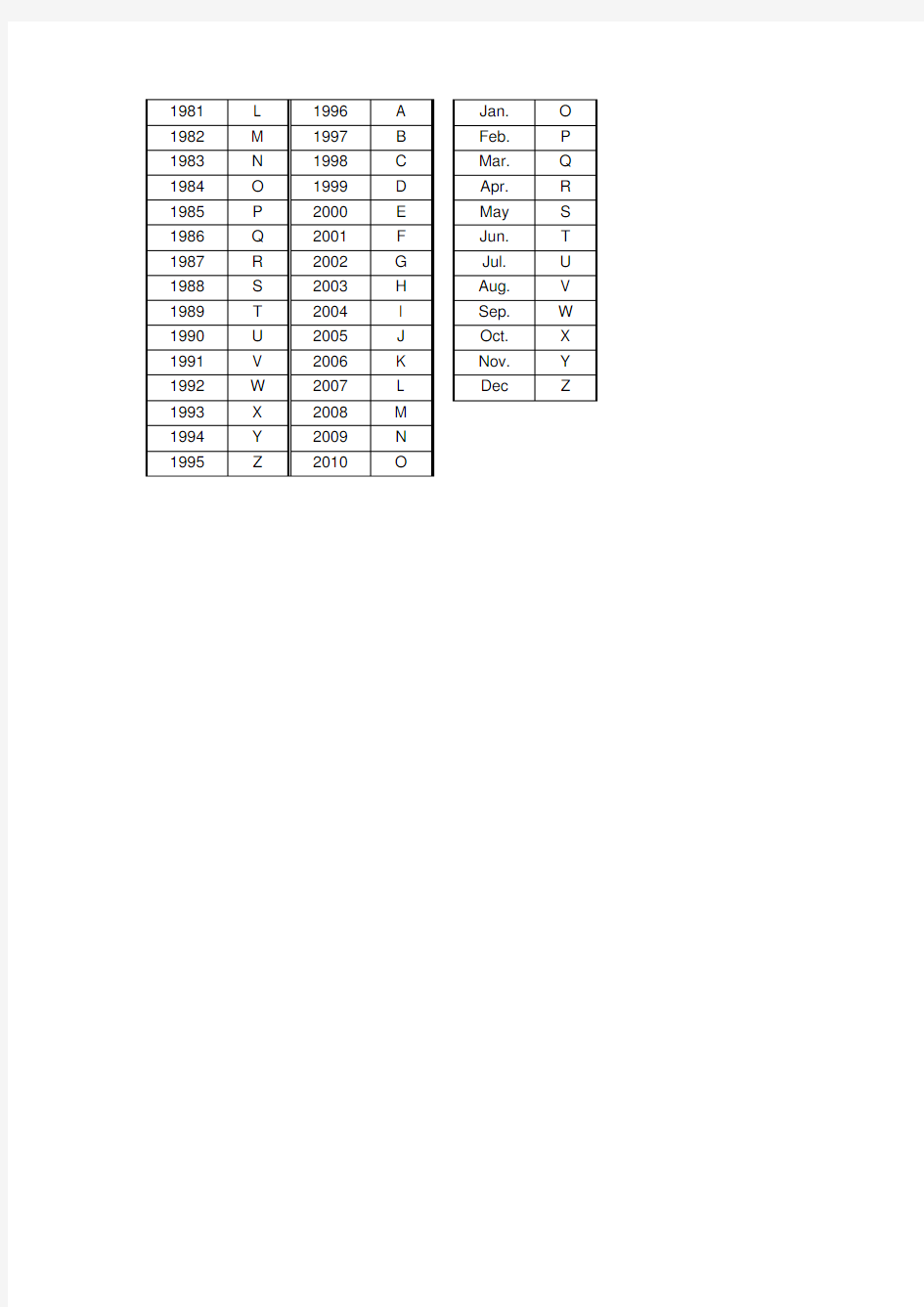
1981L1996A Jan.O 1982M1997B Feb.P 1983N1998C Mar.Q 1984O1999D Apr.R 1985P2000E May S 1986Q2001F Jun.T 1987R2002G Jul.U 1988S2003H Aug.V 1989T2004I Sep.W 1990U2005J Oct.X 1991V2006K Nov.Y 1992W2007L Dec Z 1993X2008M
1994Y2009N
1995Z2010O
气动工具维护与保养要点
气动工具的维护与保养 气动工具的保养及维护 要完成每项加工或装配任务,首先要装备合适、优秀的工具。五金工具不能只使用不维护保养,那样会减少五金工具的使用寿命,今天我们来说气动工具中的气动螺丝刀的使用以及维护。 气动工具主要应用于拧紧装配,汽车制造、电子、家电、汽车配件生产、设备维修、航空航天都是其应用的主要行业。精密性、可靠性、耐用性是气动工具的功能衡量标准。 旋转类气动工具的品质取决于六个方面: 1、内置的气动马达(旋转动力)的性能; 2、传动机构零部件所用金属材料及处理方式; 3、零部件的加工精度和工具的装配精度; 4、工具设计、生产的创新、优化、改良; 5、质量控制;
6、正确、合理的使用。 气动工具操作及其保养基本六大要点 1、正确之代供气系统: 进气压力于工具入口处(非空压机之出气压力)一般为90PSIG(6、2Kg/cm^2),过高、过低均有损工具之性能及寿命。进气必须含有充分润滑油,以便工具内气动马达得到充分润滑(可置一白纸于工具排气处检视是否有油渍,正常为有油渍现象)。 进气必须尽不含水份,若庄缩空气未经空气干燥机是不恰当的。 2、不可任意拆除工具的零件后而操作,除了会影响操作者的安全关会致使工具损坏。 3、若工具略有故障或经使用不能达到原有功能时,不可再继续使用,要立即检查。 4、定期(约每周一次)检查、保养工具,添加黄油(Grease)于轴承等转动部位,添加机油(Oil)于气动马达部位。 5、使用各式工具,务必遵照各种安全规定及使用说明操作。 6、要选用适当的工具工作,工具过大容易造成工作伤害,工具过小容易致使工具损害。气动技术发展趋向,随着生产自动化程度的不断提高,气动技术应用面迅速扩大、气动产品品种规格持续增多,性能、质量不断提高,市场
气动元件的正确使用和维护保养
气动元件的正确使用和维护保养 一套气动装置,如果不注意维护保养工作,就会过早损坏或频繁发生故障,使装置的使用寿命大大降低,在对气动装置进行维护保养时,应针对发现的事故苗头,及时采取措施,这样可减少和防止故障的发生,延长元件和系统的使用寿命。因此,企业应制定气动装置的维护保养管理规范,加强管理教育,严格管理。 维护保养工作的中心任务是保证供给气动系统清洁干燥的压缩空气,保证气动系统的气密性,保证油雾润滑元件得到必要的润滑,保证气动元件和系统得到规定的工作条件(如使用压力,电压等),以保证气动执行机构按预定的要求进行工作。 油雾器最好选用一周补油一次的规格,补油时,要注意油量减少情况。若耗油量太少,应重新调整滴油量,调整后滴油量仍减少或不滴油,应检查油雾器进出口是否装反,油道是否堵塞,所选油雾器的规格是否合适。 每月每季度的维护工作应比每日和每周的维护工作更仔细,但仍限于外部能够检查的范围。其主要内容是:仔细检查各处泄露情况,紧固松动的螺钉和管接头,端子台检查换向阀排出空气的质量,检查各调节部分的灵活性,检查指示仪表的正确性,检查电磁阀切换动作的可靠性,检查气缸活塞杆的质量以及一切从外部能够检查的内容。 维护工作可以分为经常性的维护工作和定期的维护工作。前者是指每天必须进行的维护工作,后者可以是每周,每月或每季度进行的维护工作。维护工作应有记录。维护工作应有记录,以利于今后的故障诊断和处理。 检查漏气时应采用在各个检查点涂肥皂液等办法,因其显示漏气的效果比听声音更灵敏。 https://www.360docs.net/doc/2e2141840.html,/ https://www.360docs.net/doc/2e2141840.html,/
气动绞车操作与维护保养规程审批稿
气动绞车操作与维护保 养规程 YKK standardization office【 YKK5AB- YKK08- YKK2C- YKK18】
气动绞车操作与维护保养规程 1 范围 本标准规定了气动绞车的操作及维护保养方法 本标准适用于钻井队XJFH系列气动绞车的操作及维护保养 2 主要技术参数 XJFH 系列气动绞车主要技术参数 型号XJFH-5/35 最大提升力50KN 最大绳速35m/min 额定功率16KW 额定进气压力 额定耗气量?/min 容绳量 140m(单刹)120m(双刹)钢丝绳直径 16mm(5/8in) 底座连接尺寸912mm*500(高底座) 重量550kg 3安装 1)绞车应安装在平整的平面上,固定牢固。 2)钢丝绳、吊钩及定滑轮选型应与绞车最大载荷匹配。
3)吊绳长度必须足够保证吊最远处重物时余绳不少于5圈,绳头固定必须符合要求。 4)吊绳无扭结、断股、断丝压扁等现象,符合要求,排列整齐,不跳滑轮槽。 5)气管线及元件不渗漏、压力足够。 4使用操作 使用前往气动马达壳体内加注两升空气压缩机油,齿轮传动部位和黄油嘴加注锂基润滑脂,拧下油雾器加油螺母,向内加入清洁润滑油升,调节针阀使其供油量在额定工况时10~15滴/分。 起升工况:操作分配阀手柄,往里拉,完成提升。 下降工况:操作分配阀手柄,往外推,完成下降,下降至离放置位置有一定高度时,应减速平稳下放。 刹车工况:操作分配阀处于中位,停止马达运转,同时操作刹车至刹死。 1) 初次使用时,先空负荷运转1~2分钟,然后再逐步增大提升负荷至额定拉力,检验刹车机构是否可靠。 2) 检查缸盖罩接合面处和壳体与分配阀接合面处是否有明显漏气。 3) 经常检查吊绳的损伤情况,凡损伤的吊绳严禁使用。 4) 使用中经常检查紧固件是否有松动现象,一旦松动立即紧固。 5) 使用中,如有异常响动,应立即停机检查,排除故障后才允许继续使用。 注意!不得载人。 吊重物前要估量重物是否超出绞车额定负荷。 吊重物应采取相应的稳定措施,不使重物乱摆乱晃。 5风险识别与控制措施
气动工具的构造及使用维修
气动工具的构造及使用维修 一、原理及简史: 以压缩气体为工作介质,靠气体的压力传递动力或信息的流体传动。传递动力的系统是将压缩气体经由管道和控制阀输送给气动执行元件,把压缩气体的压力能转换为机械能而作功﹔传递信息的系统是利用气动逻辑元件或射流元件以实现逻辑运算等功能,亦称气动控制系统。 简史:1829年出现了多级空气压缩机,为气压传动的发展创造了条件。 1871年风镐开始用于采矿。 1868年美国人G.威斯汀豪斯发明气动制动装置,并在1872年用于铁路车辆的制动。后 来,随着兵器﹑机械﹑化工等工业的发展,气动机具和控制系统得到广泛的应用。 1930年出现了低压气动调节器。50年代研制成功用于导弹尾翼控制的高压气动伺服机 构。 60年代发明射流和气动逻辑元件,遂使气压传动得到很大的发展。 二、气动工具与电动工具相比较的优点及其应用: 1、可以使用于爆炸性、腐蚀性、高温及潮湿的工作环境中; 2、可超负荷操作而不致使马达烧毁; 3、结构简单、坚固耐用、维护相对容易; 4、输出扭矩大、重量轻、效率高; 5、可实现无级调速,以及可产生旋转、往复及冲击运动; 6、工作压力低,一般为0.3~0.8兆帕,气体黏度小,管道阻力损失小,便于集中供气和中距离输送。 7、.耐水性强浸水虽然对工具有害,但不会像电动工具那样有致命的危害 等优点,而被广泛的应用于现代机械制造、船舶制造、汽车制造等许多领域,特别是在汽车制造业,广泛应用在整车生产过程中的打磨、抛光、喷涂、装配等工况,是现代汽车批量大规模生产不可缺少的重要工装设备之一,而由于在汽车制造业中,整车装配近90%的联接形式采用螺纹联接,因
超滤系统操作规程及维护保养
超滤系统操作规程及维护保养 1、超滤的手动操作 1.1产水操作 (1)气动阀门动作及状态 确认超滤装置上的产水、浓水排放、进水气动阀开启。气动阀门的开关通过超滤装置上的就地控制柜完成。保证超滤处于产水状态时,再启动原水进水阀的操作,从而保证超滤运行负荷不超标。 (2)混凝剂加药 确认药箱液位足够,开启加药泵进出口阀门,启动加药泵。停原水进水阀门后,再停加药泵。 2、反洗操作 2.1简反洗(包括上反洗和下反洗) 关闭一台超滤进水、产水和浓水排放气动阀,再启动两台反洗水泵对这台装置执行反洗操作,简反洗流量为310M3/H。 (1)上反洗 上反洗采用超滤产水作为反冲水,由组件产水口进入,浓水出口流出。此时入口水阀和产水阀关闭,反洗至排水清澈。 (2)下反洗 下反洗采用超滤产水作为反冲水,由组件产水口进入,进水口流出。此时浓水出口阀和产水阀关闭,反洗至排水清澈。 二台超滤的反洗时间应错开,即一台执行反洗程序时另一台应处在待机或运行状态。超滤反洗完成后,先关闭反洗水泵。 2.2完整反洗 (1)前正冲 由组件进水口至浓水出口,产水阀门关闭。 (2)上反洗 上反洗采用超滤产水作为反冲水,由组件产水口进入,浓水出口流出。此时入口水阀和产水阀关闭。执行此步骤时随反洗泵的投运启动次氯酸钠加药泵,投加浓度约为150PPM。 (3)下反洗 下反洗采用超滤产水作为反冲水,由组件产水口进入,进水口流出。此时浓水出口阀和产水阀关闭,执行此步骤时随反洗泵的投运启动次氯酸钠加药泵,投加浓度约为150PPM。 (4)后正冲 由组件进水口至浓水出口,产水阀门关闭。冲洗至出水清澈为止。 2.3化学加强反洗程序在反洗过程中向反洗水中假如化学药品。为了增加化学药品的反应 时间,在彻底反洗后可增加一定时间的浸泡时间。 3、性能检测 手动对膜组件进行完整性检测时,用气泡观察法。 3.1原理 检测完全浸泡过的膜组件时,当洁净的压缩气体从进水端进入膜组件时,气体会经过中空纤维的内腔的破裂处或大孔缺陷处,漏入纤维丝外侧,气泡经过中空纤维丝内腔上端或直接从产水端流入产水端透明管,即可观察到泄露的气泡,进而确定有问题的组件。 3.2检测步骤 (1)组件内充满水,开启压缩空气进气阀、产水端清洗回流阀,关闭其余阀门。
加工中心维护保养内容及要求
加工中心维护保养内容及 要求 Newly compiled on November 23, 2020
加工中心维护保养内容及要求 1 日常保养 定期时间:每班班前、班后。 作业时间:各15分钟内。 班前 对机床各重要部位进行检查(液压系统、导轨润滑系统、中央闭式循环系统、切削水系统是否足够)。 擦净机床外露导轨面及滑动面的尘土。 空车试运转。 . 班后 抹净操作屏上的油渍。 清扫、擦拭机床。 清扫铁屑。 各部归位。 2 一级保养 定期时间:每季度一次。 作业时间:4小时内。 外表 擦拭机床外表、罩盖及附件,达到内外清洁、无锈蚀、无黄袍。 检查补齐螺钉、螺母,油杯有无松动。 传动系统,工作台及导轨 检查主轴系统及各定位螺钉有无松动。
检查工作台及导轨面,去除毛刺。 检查各传动机构动作是否正常。 检查丝杆,螺母及调整间隙。 检查刀架、主轴头及刀库运动是否准确可靠。检查刀眼是否准确可靠。液压、润滑、冷却、气动 检查过滤器、冷却泵、冷却箱,要求管路、阀门畅通无泄漏。 检查油质、油量、油位是否符合要求。 检查液压、气动及润滑、冷却系统,调整工作压力。 电器 擦拭电动机及电器箱达到内外清洁。 检查线路是否漏电,各触点接触良好。 检查CNC的全部机能是否正常动作。 检查控制装置及伺服装置内外的外观情况是否良好。 检查限位装置与接地是否安全可靠。 3 二级保养 定期时间:每年一次。 作业时间:8小时内。 完成一级保养的各项内容(按一级保养要求)。 检查、调整各传动零部件,修复或更换磨损件。 刀架、工作台与导轨 检查导轨面,要求无油污、去毛刺、整修伤痕、调整间隙。 检查、调整刀架主轴及传动齿轮啮合间隙。 检查、调整各零部件,修复更换磨损件。
设备日常维护保养制度
离心风机的轴承总是坏,原因在哪儿?(已有结果) 有几台3级离心式风机,参数如下流量:250立方米每小时,转速:2970rpm,功率:280Kw,升压: 42.2KPa [b] 轴承[/b]使用的是SKF的,驱动端是一件1319,非驱动端是一件1319和一件7318,[b]更换[/b]了几台次的[b]轴承[/b],每次运行1-2个月时间,风机振动就会超标,严重时振动波动至0.3mm,检查[b]轴承[/b]的滚珠,1319[b]轴承[/b]的部分滚珠(有时一个,)出现浅层剥落现象, 求高手指点出现这种情况的原因及处理方法。 1、我们在设备选型时,一般注重选择叶轮采用ZL104精密优质铝合金,使叶轮具有较好的气动性能 和机械性能,并使叶轮重量及转动惯量降低,改善电机的启动性能,降低主轴负荷,使轴承寿命大大提高。并要求叶轮风道严格打磨,加工完后经静平衡校验,依次装在主轴上,再进行动平衡校验,平衡等级为G2.5级合格。 那么为何尽量少用钢板焊接叶轮呢?因钢板焊接叶轮重量大,其转动惯量也大,轴极易产生弯曲变形,也极易导致轴承损坏,造成轴承烧损塌架,使转子破损影响风机的正常使用。 2、轴承的选用 我们选用的SKF轴承一般选用开式、大游隙、普通级轴承,不知楼主选用的轴承游隙是否合理。 建议征求厂家意见。 3、用磁力表查找电机中心线与风机中心线的同轴度,用块规塞两联轴器端面的平行度是否符合要 求。 4、检查操作者的使用操作是否符合规定。 5、检查维护、保养、润滑情况,运行7-10天加油一次,润滑剂为锂基润滑脂2号(GB7324-87), 每个轴承加油量约为80克/次。 上述意见,不知是否有用? 谢谢各位的回复!大家分析的很全面。 遵照大家的建议,这个事情结果是这样子解决的: 首先排除了动平衡的问题,因为不可能风机动平衡一直都做不好,而别的风机都没问题(同一个单位做的动平衡),且也不应该是1~2个月后才出现振动超标。 所以问题就集中在了轴承质量和润滑上,于是兵分两路查找问题。 结果是:把库存的新轴承拿给SKF经销商公司,说是假的(我们采用合格供应商集中供货,不单独与各零件商联络);而润滑油温呢,一直控制在50°以下,应该没问题,一查牌号,是30号机械油,早已淘汰的产品! 奶奶的,两样都是伪劣产品! 设备的日常维护保养 2008-01-06 08:58 设备的日常维护保养 设备的日常维护保养包括每班维护保养和周末保养,由设备操作者进行。 一、设备的日常维护保养的工作内容主要是:对设备进行清扫、吹尘、擦拭,对各运动件和润滑点进行润滑,检查各种压力、温度、液体指示信号或传感器信号是否正常,安全装置是否正常,设备运行参数是否正常,电器电子控制柜是否正
空压系统操作及维护保养规程
空压系统操作及维护保养规程 1.目的:建立空压系统操作及维护保养的标准程序,规范操作人员的操作和维修人维护保养工 作。从而确保人员的安全及设备的正常运行。 2.范围:本标准适用于公司空压系统操作及维护保养。 3.职责: 3.1.操作人员:严格按照该SOP对空压系统进行操作和日常维护。 3.2.维修人员:严格按照该SOP对空压系统进行定期维护保养。 4.内容: 4.1.操作前准备 4.1.1.确认空压系统各机械零部件和管道连接可靠,如有松动现象及时处理。 4.1.2.确认空压机新风滤网无阻塞,如有阻塞及时清洁。 4.1.3.确认空压机在停机时油位高度,保证能机组正常运行。 4.1.4.确认空压机和干燥机(吸附式)电力供应正常。 4.1. 5.确认各个过滤器完好,在有效期内。 4.1.6.确认干燥机完好,平衡阀开度正确(调试时设置好一般不需要再动)。 4.1.7.确认储罐及管道上的流量计、压力表、安全阀等均已校验且在有效期内。 4.1.8.确认过滤器及储罐的排水阀工作正常,排水管道连接良好。 4.1.9.确认排风管道畅通且固定良好,防雨百叶完好。 4.1.10.确认机房补风口通畅,防虫纱网完好。 4.2.运行 4.2.1.打开空压机及干燥机电源,确认空压机急停按钮未按下。 4.2.2.按下空压机启动按钮,启动空压机即进入自动控制状态。 4.2.3.如需对空压机参数设置,则在控制屏上选择参数修改选项(根据不同的品牌,按说明书操作),输入密码后进行设置。一般只设置设备的卸载压力和加载压力。 4.2.4.空压运转平稳压力达到设置压力后,打开干燥机前进气总阀并按下干燥机启动按钮,启动干燥机进入自动控制状态。(确保干燥机气动控制阀的气源总阀打开) 4.2. 5.空压正常运转后,检查以下机组内各处有无漏油漏气现象,如漏气严重则立即停车处理。 4.2.6.检查系统管道确保旁通阀关闭(特殊情况除外),并确保依次从空压机-空压储罐-二级过滤器-空压干燥机-末端过滤器-空压储罐的主线路所有阀门打开。 4.2.7.待系统运转平稳后做好工作运行记录。比较各运行参数是否始终正常,如有反常情况应及时分析查找原因。 4.2.8.如需要停止运行机组,则只需按下停机按钮后,压缩机自动卸载后方可停机。 4.2.9.待空压机停机后关闭干燥机,并关闭空压机排气阀。如需连续使用的系统则无需对系统进行泄压,如需长期停机则,从空压储罐或系统末端进行泄压。如果为局部检修泄压则封闭需
设备设施定期维护保养管理制度
设备、设施定期维护保养管理制度编号:AQ-BZH-019-A 1 目的 为加强本公司设备、设施管理,防止和减少生产事故,保护员工和本公司财产安全,达到机械设备与员工的本质安全化,特制定本制度。 2 适用范围 适用于本公司所有设备、设施(消防设施及安全防护设施维护保养见消防安全管理制度)的管理。 3 引用文件(无) 4 职责 4.1行政部负责组织制定、修订设备、设施定期维护保养管理制度,并监督执行。 4.2生产部具体执行本制度。 4.2其它各部门负责本部门的办公设备、设施维护、保养。 5 程序内容 5.1 各部门在使用设备时必须依照该设备的操作说明及相应的操作规程操作。5.2本公司所有生产设备分为每日一级保养和定期﹑预防二级保养两种。 5.3一级保养:每日由生产部的各组长督导执行,按照《设备(设施)定期检查、维护、保养记录》中每日点检项目,各作业员对所使用的机器设备进行清洁﹑润滑﹑锁紧﹑功能检查等,并将实施检查结果填入《设备(设施)定期检查、维护、保养记录》上。一级保养可参考以下项目: ①运转和滑动部分是否异常。 ②运转和滑动部分润滑是否足够。 ③紧固部件是否松动。 ④有无震动﹑噪音现象。 ⑤控制开关﹑仪表是否正常。 ⑥防护装置是否可靠完好等。 5.4二级保养:由生产部主管督导执行,依照《设备保养及维护记录表》上的项目,对所有机械设备及夹具进行周期性检查﹑润滑﹑调整和修理,以保证机器正常运行。并将保养﹑检查情况记录于《设备(设施)定期检查、维护、保养记录》上。二级保养可参考以下项目: ①传动系统:皮带疲劳损坏。 ②油类系统:齿轮箱润滑油变质。 ③电器线路:仪表损坏,指示线路失控等。 ④气动系统:气动阀门损坏,空气过滤之异常等。 5.5作业员工在每日保养检查过程中发现机器设备异常现象,应及时通知部门负
废气处理系统维护保养制度
广东省航鑫科技股份公司 废气处理系统维护保养制度 一、系统完好标准 1.1零部件完整齐全,质量符合要求。 2.1.1风机零部件完整齐全,质量符合要求。 2.1.2电气、仪表气动执行机构、油位计、温度计、自动联锁装置等齐全、完整且灵敏准确。 2.1.3基础、机座稳固可靠,地脚螺栓和各部螺栓联接紧固、齐整,符合技术要求。 2.1.4管件、管线、阀门、支架等安装合理,牢固完整,标志分明,符合要求。 2.1.5防腐、保温、防冻设施完整有效,符合要求。 2.2设备运转正常,性能良好,达到铭牌出力或查定能力。 2.2.1设备生产能力达到设计能力的90%以上。 2.2.2设备运转平稳,无杂音。振动和噪音符合设计要求。 2.2.3设备外表无明显变形、过烧现象,不漏风、漏灰、漏烟、漏水。 2.2.4轴承温度、油质、油位及冷却水温、水压、运行电流等符合要求。设备润滑实行“五定”(定点、定人、定质、定时、定量)、“三级过滤” 2.3技术资料齐全、准确
2.3.1设备制造合格证、使用说明书、原始安装、试车及验收记录齐全。 2.3.2设备运行记录、检修及验收记录、历次技术改造记录、设备运转时间及累计运行时间记录齐全、完整。 2.3.3易损件图纸齐全。 2.3.4设备操作规程、维护检修规程齐全。 2.4设备整体布局合理、整齐。 2.4.1设备整体布局合理、整齐。 2.4.2设备油漆完整,外观清洁,动、静密封点泄漏率在规定范围内。 2.4.3设备周围环境清洁。 二、维护保养范围 1、锅妒本体,包括燃烧系统; 2、燃料输送和除尘设备; 3、水处理和给水设备; 4、鼓、引风等辅机设备; 5、安全附件和管道附件及仪表。 三、设备的维护 3.1日常维护 3.1.1操作人员对设备应做到“四懂”、“三会”。 3.1.2加强设备润滑管理,做到“五定”、“三过滤”。 3.1.3严格按照操作规程进行设备的启动、运行与停车;坚
气动马达-保养及日常维护
气动马达-保养及日常维护 一、结构说明: 空气调节阀(进气口) 二、使用条件说明: 使用流体:压缩空气 使用压力:5 kg/cm2 ( 70 psi ) 最高使用压力:6 kg/cm2 ( 85 psi ) 周围温度:-10°C ~+70°C(在不冻结的状态ba下才能使用)。 润滑油:IS0 VG32或相似品。(以油雾器给油是必要的,每分2~3滴),
可以连续使用但无负荷不可以连续运转 气马达缸体内部每年更换加注LUGREASELS-1EH黄油(适用于齿轮式和活塞式)。 三、使用时必须注意: 1.气动马达被驱动物的输出轴心连接不当时会形成不良动作或导致故障。2.发现故障时,应立即停止使用,须由专业维修人员进行检查、调整。 四、配管上必须注意: 1.气动马达和其它空气压力机器之故障主要原因,都是由于灰尘等异物的进入。配管前都必须先用压缩空气清扫管内,注意千万不能让切削粉、封缄带之断片、灰尘或锈等进入配管内。 2.不允许更改空气压力机器的管径大小。 五、运转时必须注意:
1.确认旋转方向是否正确或被驱动物与轴心之间有无不正常安装。 2.气动马达速度之控制和稳定性,必须从供应空气方进行调整,如此,排气边 就不会产生背压。 3.不可使马达在无负荷状态下连续旋转或高速旋转,如果连续无负荷空转时, 旋转速度将过度提高,气动马达将减少使用寿命或损坏。 4.带料试运转时,用空气调节阀,慢慢把旋转数提高到所需要的旋转数为止。 到达最大马力时,若再超过此旋转数的话,气动马达可能损坏,注意正确使用压力。 六、保养检查时必须注意: 空气过滤减压油雾器(三联件)要定期检查,油雾器内之润滑油若已减少时,就要补充。 压缩空气产生油雾主要由油雾器来完成。油雾器是以压缩空气为动力,将润滑油喷射成雾状,并混合于压缩空气中,使该压缩空气具有润滑气动元件的能力。目前,气动控制系统中的控制阀、气缸和气马达主要是靠带有油雾的压缩空气来实现润滑的,其优点是方便、干净、润滑质量高。 普通型油雾器也称为全量式油雾器,把雾化后的油雾全部随压缩空气输出,油雾粒径约为20μm。普通型油雾器又分为固定节流式和自动节流式两种,前者输出的油雾浓度随空气的流量变化而变化;后者输出的油雾浓度基本保持恒定,不随空气流量的变
气动马达-保养及日常维护
气动锚杆钻机设计 气动马达 -保养及日常维护 、 结构说明: 使用条件说明: 使用流体:压缩空气 使用压力: 5 kg/cm 2 ( 70 psi ) 最高使用压力: 6 kg/cm 2 ( 85 psi ) 周围温度: -10° C ~+70° C (在不冻结的状态 ba 下才能使用)。 润滑油: IS0 VG32或相似品。(以油雾器给油是必要的,每分 可以连续使用但无负荷不可以连续运转 空气调节阀 (进气口 ) 2~3滴),
气马达缸体内部每年更换加注LUGREASELS-1EH黄油(适用于齿轮式和活塞式)。 三、使用时必须注意: 1.气动马达被驱动物的输出轴心连接不当时会形成不良动作或导致故障。2.发现故障时,应立即停止使用,须由专业维修人员进行检查、调整。 四、配管上必须注意: 1.气动马达和其它空气压力机器之故障主要原因,都是由于灰尘等异物的进入。配管前都必须先用压缩空气清扫管内,注意千万不能让切削粉、封缄带之断片、灰尘或锈等进入配管内。 2.不允许更改空气压力机器的管径大小。 五、运转时必须注意: 1. 确认旋转方向是否正确或被驱动物与轴心之间有无不正常安装。 2. 气动马达速度之控制和稳定性,必须从供应空气方进行调整,如此,排气边就不会产生背压。
3.不可使马达在无负荷状态下连续旋转或高速旋转,如果连续无负荷空转时, 旋转速度将过度提高,气动马达将减少使用寿命或损坏。 4.带料试运转时,用空气调节阀,慢慢把旋转数提高到所需要的旋转数为止。 到达最大马力时,若再超过此旋转数的话,气动马达可能损坏,注意正确使用压力 六、保养检查时必须注意: 空气过滤减压油雾器(三联件)要定期检查,油雾器内之润滑油若已减少时,就要补充。 压缩空气产生油雾主要由油雾器来完成。油雾器是以压缩空气为动力,将润滑油喷射成雾状,并混合于压缩空气中,使该压缩空气具有润滑气动元件的能力。目前,气动控制系统中的控制阀、气缸和气马达主要是靠带有油雾的压缩空气来实现润滑的,其优点是方便、干净、润滑质量高。 普通型油雾器也称为全量式油雾器,把雾化后的油雾全部随压缩空气输出,油雾粒径约为20μm。普通型油雾器又分为固定节流式和自动节流式两种,前者输出的油雾浓度随空气的流量变化而变化;后者输出的油雾浓度基本保持恒定,不随空气流量的变
浅析气动控制系统维护保养
浅析气动控制系统维护保养 (重庆泰山电缆有限公司,) 气动控制系统的维护保养应及早进行,不应该拖延到问题已经在设备的某个部分产生, 并需要维修时才进行。为确保设备寿命,以及单个元件和整个控制系统的工作可靠性,首先 考虑的问题就是应对它们进行预防性维护保养。定期对系统维护保养不会带来任何不必要的 花费,相反它有利于减小因空气泄漏、修理和由于故障或损坏系统停止使用造成的对生产所 带来的损失。如果在工厂或车间安装一个大型气动系统,应指派在气动技术方面经过专门培 训的合格人员来维修保养。当维护保养工作量较小以及一个维护保养人员工作量不饱满时, 建议将维护保养工作交给车间人员管理。这样,他们只需用部分工作时间就可以完成设备的 维护保养。 系统维护保养通常根据维护保养检查表进行,预先计划的工作绝不能轻易忽视。在编制 维护保养检查表时,应参照设备和元件生产厂的产品说明书和有关维护保养技术资料。例如,对于压缩机装置和空气管道系统应编制联合检查表,而对于气动控制系统或气控机器应单独 编制检查表。作为操作指南,检查表中应含有维护保养过程和说明。在维护保养中,明确多 长时间检查一次(周、月等间隔时间)都应有详细记录供检修用。 在对主气管路和进气管路进行维护时,应注意管道系统、软管、控制阀和接头处的泄漏 以及冷凝水聚集。在空气管路系统中,通常应安装水分离器或冷凝水收集器,并应对其进行 定期排放(即将冷凝水放掉)。在这方面,自动排污器可以大大简化维护保养工作。为使系 统正常工作,排污器至少应每周检查一次,特别是要检查浮子阀。大颗粒灰尘沉积在浮子阀内,常对其开启或关闭动作产生不良影响。压缩空气泄漏就意味着投入加大,也就是说,损 失压缩空气,就要增加系统运行成本。因泄漏引起的压缩空气损失会造成很大经济损失。据 计算当管路压力为0.6MPa,面积仅为7mm2的小孔(孔径Φ3mm)的泄漏所带来的压缩空 气损失约为36m3/h,这样压缩机必须要消耗2Kw功率来弥补这个损失。因此,针对泄漏这 些情况,至少每月检查一次供气系统,任何存在泄漏的地方都应立即进行修补。 对于大型气动控制系统来说,编制相应的维护保养检查表,是保证气动控制系统正确维 护保养的有效措施。检查表中包括运动步骤图和回路图,这样有助于简化专用设备的维护保养,同样也有助于查找故障。气动设备和系统内也会产生泄漏损失。与供气系统一样,定期 检查也是及时发现泄漏的第一步,这样还可以避免造成更大浪费和损坏。这些浪费所构成的 总成本要比早期更换元件所需费用大得多。因此,对大型气动控制系统的检修要特别注意在 多灰尘工作的环境、防止灰尘进入气缸或控制阀内,以免造成气缸导向部分破坏,或使控制 阀产生误动作。 空气过滤器的使用过程实质就是大气中的灰尘颗粒在滤材上逐渐积累的过程。过滤器使 用时间长短,要由环境空气中的含尘量决定。空气中含尘量多,使用时间就短;空气中含尘 量少,使用时间就长。国内外对空气过滤器的使用,普遍采用以行程里程和工作小时数作为 更换依据。但是国内外地理环境不同,灰尘在空气中的含量随之不同,相差数倍至数十倍。 由于空气中的含尘量无法量化,因此空气过滤器的使用更换周期就无法简单规定了。例如用 户普遍对内燃机前期保养认识不够。在内燃机工作状态良好时,想不到必要的保养,当感觉 到内燃机工作有明显异常再做保养工作已经晚了。当空气过滤器被砂尘堵塞以至不能满足发 动机所需空气的体积流率时,发动机的工作状态会表现以下症状:轰鸣声发闷,加速反应迟缓、工作时表现无力,水温相对升高,加速时尾气烟度变浓。当这些症状出现时,就应该想 到可能是空气过滤器堵塞。因此,正确使用和维护保养空气过滤器是十分必要的。 为了在故障发生后,就能够以最小投入及时找出故障,并提出解决办法。绘制故障检修 流程图是健全有效的组织体系和检修故障的非常必要的措施之一。对于含有几个气动元件的 小型气动控制系统,为了查找故障,仔细检查整个系统还是可行的;但对于大型复杂气动控 制系统来说,再采用这种方法就像大海捞针一样,时间久、查找麻烦,影响工作。在这种情 况下,检修故障时,通常利用系统运动-步骤图和回路图。因此,虽然绘制运动-步骤图和回 路图是在系统完成之后才进行,但对每个气动控制系统,也包括车间设备,都应绘制相应的 运动-步骤图和回路图。 多种多样的气动系统在自动化和半自动化生产中发挥了重要作用。随着气动技术的不断
防排烟系统的维护保养
防排烟系统的维护保养 1、对排烟阀、排烟防火阀、送风阀的维护保养: (1)排烟口、送风口有无变形、损伤,周围有无影响使用的障碍物; (2)风管与排烟口连接部位的法兰有无损伤,螺栓是否松动; (3)阀件是否完整,易熔片是否脱落,动作是否正常; (4)旋转机构是否灵活,每年对机械传送机构加适量润滑剂; (5)制动机构、限位器是否符合要求; (6)进行手动、远程启闭操作,检查是否可完全打开. 2、对送风、排烟风机的维护保养: (1)风机房周围有无可燃物;安装螺栓是否松动、损伤; (2)传动机构是否变形、损伤;叶轮是否与外壳接触; (3)电动机的接线是否松动;电动机的外壳有无腐蚀现象; (4)电源供电是否正常(检查电压表或电源指示灯)。 (5)检查轴承部分润滑油状态是否异常(脏污、混入泥沙、尘等); (6)检查电动机的轴承部位润滑油液位是否正常; (7)检查传动皮带是否松动,联轴器是否牢固; (8)启动电动机,旋转时有无异常振动、杂音。 (9)操作手动或自动启动装置,进行每个防烟分区(或正压送风)的动作试验,检查下列事项: a、手动或自动能否正常启动; b、运转电流是否正常; c、运转中是否有不规则杂音及异常振动; d、动作设备的区域是否与原设计对应。 3、对风机电柜的维护保养: (1)控制柜是否设置在易于操作、检查、维修方便的位置。 (2)控制柜有无变形、损伤、腐蚀。 (3)线路图及操作说明是否齐全。 (4)电压、电流表的指针是否在规定的范围内。 (5)开关是否有变形、损伤、标志脱落、处于正常状态。 (6)操作开关,检查开关性能,检查指示灯显示状态是否正常。 (7)继电器是否脱落、松动,接点是否烧损,转换开关能否正常切换。 4、每年应对防排烟风机的风量进行测定。 5、正压送风阀:检查其送风阀是否完好,能否完成送风功能。
气动系统的基本原理和维修要点
第八讲气动系统及其使用维护简介 本讲介绍四个内容: z 气动技术概述 z 气动元件z 气动回路与系统z 气动系统的安装调试 与使用维护
8.1 气压传动概述 一、定义: 以压缩空气作为工作介质来传递动力和实现控制的技术称为气压传动。
二、气动系统的组成(五个部分) z能源元件:机械能→气压能:空压机(产生压缩空气)。 z执行元件:气压能→机械能:气缸和气马达。 z控制元件:控制气体压力、流量及流向:压力阀、流量阀及方向阀与气动逻辑元件。 z辅助元件:存储\净化压缩空气,为系统提供符合质量要求的工作介质:分水滤气器、干燥器、消声器、管道、接头等。 z工作介质:系统的工作媒介(干空气;可压缩性较液体大的多)。
三、气压传动特点及应用 &优点(5个): 工作介质经济易取,方便使用,不回收; 传输压损小,速度快,效率高,适用集中远距离 供气,动作速度快; 反应迅速,调节方便、维护简单,故障率低; 环境适应性好,污染少,防火防爆,安全性好; '缺点(3个):压力低(目前,气动系统常用的工作压力为0.1MPa~0.8MPa),故传力较小;噪 声较大;速度负载特性差,运动精度较低。 z应用广泛(几乎涵盖了液压技术涉足的各领域)
8.2 气动元件 一、空气压缩机 作用:将机械能转变成气压力能 分类(3种分类方式): z按结构分:活塞式、罗滋式;蜗杆式;离心式 z按输出压力:低压0.2~1MPa;中压1~10MPa; 高压10~100MPa;超高压≥100MPa z按流量分:微型<1m3/min ;小型1~10m3/min; 中型10 ~100m3/min;大型≥100m3/min