铸造支架
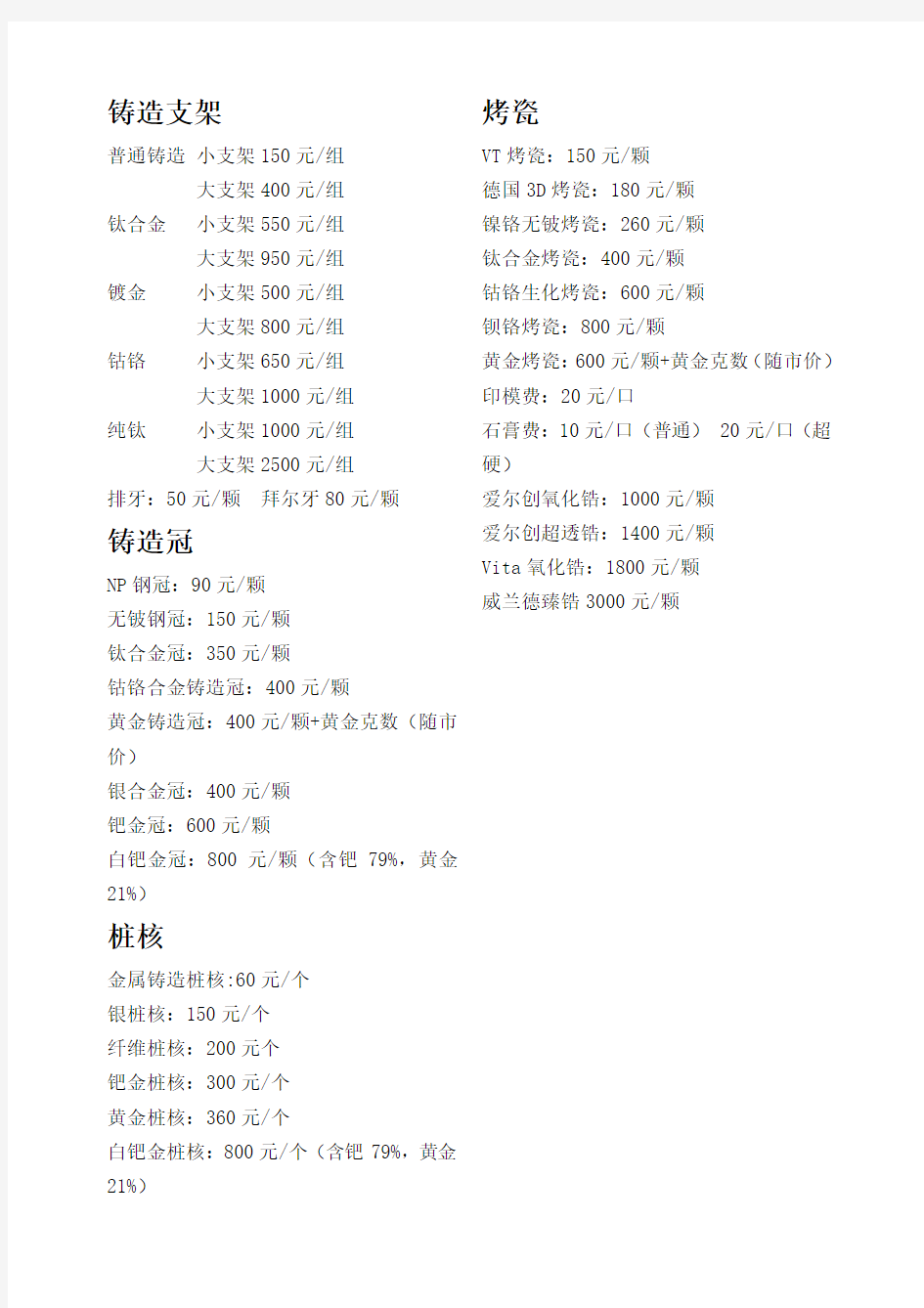
铸造支架
普通铸造小支架150元/组
大支架400元/组
钛合金小支架550元/组
大支架950元/组
镀金小支架500元/组
大支架800元/组
钴铬小支架650元/组
大支架1000元/组
纯钛小支架1000元/组
大支架2500元/组
排牙:50元/颗拜尔牙80元/颗
铸造冠
NP钢冠:90元/颗
无铍钢冠:150元/颗
钛合金冠:350元/颗
钴铬合金铸造冠:400元/颗
黄金铸造冠:400元/颗+黄金克数(随市价)
银合金冠:400元/颗
钯金冠:600元/颗
白钯金冠:800元/颗(含钯79%,黄金21%)
桩核
金属铸造桩核:60元/个
银桩核:150元/个
纤维桩核:200元个
钯金桩核:300元/个
黄金桩核:360元/个
白钯金桩核:800元/个(含钯79%,黄金21%)烤瓷
VT烤瓷:150元/颗
德国3D烤瓷:180元/颗
镍铬无铍烤瓷:260元/颗
钛合金烤瓷:400元/颗
钴铬生化烤瓷:600元/颗
钡铬烤瓷:800元/颗
黄金烤瓷:600元/颗+黄金克数(随市价)印模费:20元/口
石膏费:10元/口(普通) 20元/口(超硬)
爱尔创氧化锆:1000元/颗
爱尔创超透锆:1400元/颗
Vita氧化锆:1800元/颗
威兰德臻锆3000元/颗
支架零件铸造工艺设计说明书
支架零件铸造工艺设计 一、零件的生产条件、结构及技术要求 1、生产性质:大批量生产 2、材料:HT200 3、零件加工方法: 零件上有多个孔,除中间的大孔需要铸造以外,其他孔在考虑加工余量后不宜铸造成型,采用机械方法加工,均不铸出。 造型方法:机器造型;造芯方法:机器制芯 4、主要技术要求: 满足HT200的机械性能要求,去毛刺及锐边,铸件表面不允取有缺陷。 二、零件图及立体图结构分析 1、零件图如下: 零件主视图零件俯视图 2、立体图如下:
三、工艺设计过程 1、铸造工艺设计方法及分析 (1)铸件壁厚 为了避免浇不到、冷隔等缺陷,铸件不应太薄。铸件的最小允许壁厚与铸造的流动性密切相关。在普通砂型铸造的条件下,铸件最小允许壁厚见表1。 表1. 铸件最小允许壁厚 材料 铸件轮廓尺寸/mm 200x200以下200x200~500x500 500x500以上 铸钢6~8 10~12 18~25 铸铁5~6 6~10 15~20 球墨铸 铁 6 12 查得灰铁铸件在100~200mm的轮廓尺寸下,最小允许壁厚为5~6mm。由零 件图可知,零件中不存在壁厚小于设计要求的结构,在设计过程中,也没有出现 壁厚小于最小壁厚要求的情况。 (2)造型、制芯方法 造型方法:该零件需批量生产,为中小型铸件,因此,采用湿型粘土砂机 器造型,模样采用金属模,采用技术先进的机器造型。 制芯方法:在造芯用料及方法选择中,如用粘土砂制作砂芯原料成本较低, 但是烘干后容易产生裂纹,容易变形。在大批量生产的条件下,由于需要提高造 芯效率,且常要求砂芯具有高的尺寸精度,此工艺所需的砂芯采用热芯盒法生产 砂芯,以增加其强度及保证铸件质量。选择使用射芯工艺生产砂芯。采用热芯盒 制芯工艺热芯盒法制芯,是用液态固性树脂粘结剂和催化剂制成的一种芯砂,填 入加热到一定的芯盒内,贴近芯盒表面的砂芯受热,其粘结剂在很短的时间内硬化。而且只要砂芯表层有数毫米的硬壳即可自芯取出,中心部分的砂芯利用余热 可自行硬化。 (3)砂箱中铸件数目的确定及排布 初步确定一箱中放几个铸件,作为进行浇冒口设计的依据。一箱中的铸件 数目,应该是在保证铸件质量的前提下越多越好。 本铸件在一砂箱中高约130mm,长约200mm,宽约110mm,体积约99.7 cm^3,密度7.2g/cm^3,重约0.8Kg。结合沙箱内框尺寸:上箱为960*610*250mm 下箱为960*610*250mm,初选为一箱四件,铸件在砂箱中排列均匀对称,这样金
钛合金表面处理
钛合金表面处理 引言 钛在高温下易于与空气中的O、H、N等元素及包埋料中的Si、Al、Mg等元素发生反应,在铸件表面形成表面污染层,使其优良的理化性能变差,硬度增加、塑性、弹性降低,脆性增加。 钛的密度小,故钛液流动时惯性小,熔钛流动性差致使铸流率低。铸造温度与铸型温差(300℃)较大,冷却快,铸造在保护性气氛中进行,钛铸件表面和内部难免有气孔等缺陷出现,对铸件的质量影响很大。 因此,钛铸件的表面处理与其它牙用合金相比显得更为重要,由于钛的独特的理化性能,如导热系数小、表面硬度、及弹性模量低,粘性大,电导率低、易氧化等,这对钛的表面处理带来了很大的难度,采用常规的表面处理方法很难达到理想的效果。必须采用特殊的加工方法和操作手段。 铸件的后期表面处理不仅是为了得到平滑光亮的表面,减少食物及菌斑等的积聚和粘附,维持患者的正常的口腔微生态的平衡,同时也增加了义齿的美感;更重要的是通过这些表面处理和改性过程,改善铸件的表面性状和适合性,提高义齿的耐磨、耐蚀和抗应力疲劳等理化特性。 一、表面反应层的去除 表面反应层是影响钛铸件理化性能的主要因素,在钛铸件研磨抛光前,必须达到完全去除表面污染层,才能达到满意的抛光效果。通过喷砂后酸洗的方法可完全去除钛的表面反应层。 1. 喷砂:钛铸件的喷砂处理一般选用白刚玉粗喷较好,喷砂的压力要比非贵金属者较小,一般控制在0.45Mpa以下。因为,喷射压力过大时, 砂粒冲击钛表面产生激烈火花,温度升高可与钛表面发生反应,形成二次污染,影响表面质量。时间为15~30秒,仅去除铸件表面的粘砂、表面烧结层和部分和氧化层即可。其余的表面反应层结构宜采用化学酸洗的方法快速去除。 2. 酸洗:酸洗能够快速完全去除表面反应层,而表面不会产生其他元素的污染。HF—HCl系和HF—HNO3系酸洗液都可用于钛的酸洗,但 HF—HCl系酸洗液吸氢量较大,而HF—HNO3系酸洗液吸氢量小,可控制HNO3的浓度减少吸氢,并可对表面进行光亮处理,一般HF的浓度在3%~5 %左右,HNO3的浓度在15%~30%左右为宜。 二、铸造缺陷的处理 内部气孔和缩孔内部缺陷:可等热静压技术(hot isostatic pressing)去
材料成型与控制技术毕业论文支架铸造工艺设计
毕业设计论文设计(论文)题目:支架铸造工艺设计 下达日期:2012 年12 月3日 开始日期:2012年12 月 3 日 完成日期:2012 年 1 月8 日 指导教师:李明 学生专业:材料成型与控制技术 班级:材料1003 班 学生姓名: 教研室主任:杨兵兵 材料工程学院
前言 铸造是指熔炼金属,制造铸型,并将熔融金属浇入铸型,凝固后获得具有一定形状、尺寸和性能金属零件毛坯的成形方法。在金属加工领域中,铸造是世界历史上最悠久的工业之一。青铜冶炼技术的发明,使人类进入了青铜器时代。伴随着青铜冶炼技术的同时,出现了铸造技术。我国的铸造技术已有近6000年悠久的历史,是世界上较早掌握铸造技术的文明古国之一。2500多年以前(公元513年)就铸出270kg的铸铁邢鼎。我国是最早应用铸铁的国家之一,自周朝末年开始就有了铸铁,铁制农具发展很快,秦、汉以后,我国农田耕作使用了铁制农具,如耕地的犁、锄、镰、锹等,表明我过当时已具备有相当先进的铸造生产水平,到宋朝我国已使用铸铁炮和铸造地雷。 从商朝起,我国就已创造了灿烂的青铜文化,所谓“钟鸣鼎食”,成了当时贵族权势和地位的标志。 我国最大的钟是明朝永乐大钟,现存于北京大钟寺内,铸于明朝永乐年间(公元1418-1422年),全高6.75m,钟口外径3.3m,钟唇厚0.185m,重46.5t。据考证钟体铸型为泥范,芯分七段。先铸成钟钮,然后再使钟钮与钟体铸接成一体。钟体的内外铸满经文,约227000余字。大钟至今完好,声音优雅悦耳,声闻数十里,是世界上罕见的古钟之一。我国古代的钟、鼎等文物,有不少是用熔模远铸造的,其工艺复杂。铸工精湛、铸件精美,不难看出我国古代熔模铸造工艺已达到相当高的水平。 1953年在河北省兴隆县古燕国铸冶作坊遗址的挖掘中,发现距今2200-2350
钛及钛合金铸件生产过程
钛及钛合金铸件生产 本规程适用于采用机加石磨铸型,真空凝亮炉熔铸的钛及钛合金铸件。 1工艺流程 2.1根据用户提供的零件蓝图及技术要求绘制铸造模型工艺图,并编写铸造工艺卡。 2.2机加石磨型生产钛铸件加工余量按GB/T11350 CT 9-MA F级。 3铸型制备 3.1对石墨电极的要求 3.1.1制作铸型的石墨电极应符合GB 3072。电极表面裂纹宽度不大于0.5mm。 3.2模型应严格按照工艺图、蓝图、工艺卡片制作,如有改动,需征得技术人员的许可。 3.3制作完毕后的铸型,模型工要先组装自检,然后检察员按工艺图和零件蓝图检查尺寸和结构,合格者方可使用。 4铸型焙烧
4.1铸型真空脱气前,电阻炉内培烧。 5铸型真空脱气 5.1焙烧后的模型取出后应立即装入脱气炉脱气。 5.2往炉内装型时,必须将厚、重、大的铸型装在下部,薄、轻、小易碰坏的铸型装在上部,注意轻拿轻放。 5.6经过脱气处理的铸型要放在干燥处,防止污染,吸潮。放置三天以上不用时,必须重新脱气。 6,。装炉 7.浇注 8出炉清理 8.1拆型时先拆一次性破坏部分,再拆其余部份,可重复使用的铸型放在指定的位置,并作上标记。 8.2反复使用的铸型表面允许有深度不大于3㎜,其面积不大于20mm2的孔洞,超过此规定者应修补并经检查合格后在使用。 8.3气割浇冒口时,应注意不要割伤铸件,所留余量10~20㎜之间。 8.4铸件清砂时要求将石墨清理干净,并清理干净,同时不损伤铸件。 8.5出炉后立即将坩埚和炉膛清理干净,并清除表面密封下法兰处的飞溅物. 9铸件精整 9.1外观 9.1.1清砂后的铸件飞边毛刺应打理干净,并打磨清除表面轻微留痕、冷隔等缺陷,与基体圆滑过度。 9.2焊接修补 9.2.1铸件上裸露的气孔、缩孔、疏松、裂纹、夹杂和打磨后的尺寸缺陷,应进行补焊。补焊前队缺陷部位应彻底清除干净直至露出光亮金属表面。补焊后按图纸整形。 9.2.2加工过程中暴露的缺陷,或X射线检查发现的缺陷,根据需要可进行焊接修补,同时内部缺陷焊补并整形后要在通过X射线,以确认满足需要。 9.2.3补焊应在氩弧保护下进行,焊缝不的有严重氧化现象。 10.表面质量 10.1.1铸件表面用目测检查没有铸型材料、附着的异物、氧化皮、冷隔、凹凸、飞边毛刺等及铸件内外表面光滑。 10.1.2合同中有要求时,铸件表面可参照GB9443进行无损检验或双方协商确定。 10.2内部质量 合同中有要求时,铸件可进行X射线检验或双方协商确定。 10.3化学成份 11.5几何尺寸 11.5.1铸件几何形状性和尺寸应符合铸件图样或订货协议的规定。 11.5.2铸件尺寸公差符合GB/T 6414的规定,一般不应低于CT 11级。 11.6检验合格产品由检查做出合格标示并出具产品质量证明书。 11.7检查不合格的产品应作出不合格标识,填写不合格品报告/处理申请单,按最终处置意见办理。
转轴支架铸件设计
转轴支架铸件设计 转轴支架是大型纺织机械上的一个零件,该零件虽然受力不大,但要求可靠性好,使用寿命高。该零件材质为HT200,采用铸造成型,而铸造生产,需要铸造模具。铸造模具的结构、尺寸直接影响铸件的内在质量、外观质量和生产成本。本课题研究转轴支架铸件的工装模具设计,主要设计模样、模板等工装模具,要求达到保证产品质量且结构合理。 1.引言 在科技发展日新月异的今天,传统的产品研发模式已经在发生根本性的变革。过去,企业产品开发人员分为负责图纸设计和CAD 建模的设计工程师、专职产品性能分析的仿真工程师和决定产品最优化设计方案的优化工程师等。而现在,随着企业更加注重研发成本的控制以及计算机辅助工程(CAE)软件的快速发展,传统的分工界限已被打破。既懂设计、仿真,又掌握优化方法的技术人员已成为企业的新宠儿。 近年来,在计算机技术和数值分析方法支持下发展起来的有限元方法为解决这些问题提供了有效的途径[1-2]。AWE 集成开发平台是在有限元技术的基础上,为用户提供的一个便捷友好的平台。借助于这个平台,可以方便地对所设计的产品进行强度、刚度、动力学等方面的分析评价,代替企业对概念样品进行的试验、修改、再试验、再修改的反复过程,节省成本,缩短设计周期。支架是用以支承转轴以实现动力传递。支架结构设计的好坏,直接关系到转轴传动性能。本文以AWE 为平台,研究支架的构造,对其进行静力学及屈曲分析,用以指导支架的优化设计。 2.AWE 协同优化设计环境 CAE 技术发展到今天,它更多的应用于研发领域,为企业的研发搭建一个新的平台。AWE 的出现,使企业综合应用各种CAD、CAE 软件共同为企业产品研发服务成为可能。这种环境为CAD 系统提供了全新的平台,保证了最好CAE 结果[3]。AWE 提供一个集成统一的仿真环境帮助工程人员完成产品CAE 开发的全过程。本文利用三维建模软件Pro/E 建立支架的三维几何模型。利用Pro/E 和AWE 的接口程序,直接导入到AWE 中进行有限元分析。 3.支架有限元模型的建立 对实体结构进行三维建模时,常采用以下方法: 1)在AWE 中直接建模,适用于结构比较简单的模型。 2)在三维CAD 软件中建立三维模型,通过与分析软件的接口将模型导入,适用于较复杂的模型,但导入后模型容易出错,给下一步网格的划分带来困难,且修复模型需要浪费很多时间和精力。
支座铸造工艺设计.
热加工工艺课程设计支座铸造工艺设计 院系:工学院机械系 专业:机械设计制造及其自动化 班级:机电n班 姓名:欢迎学弟学妹咨询 学号:qq37730385 指导老师:刘万福 时间:2012年6月2日
黄河科技学院课程设计任务书 工学院机械系机械设计制造及其自动化专业2011级班 学号姓名指导教师刘万福 设计题目: 支座铸造工艺设计 课程名称:热加工工艺课程设计 课程设计时间:5 月26 日至6 月 2 日共 2 周 课程设计工作内容与基本要求(已知技术参数、设计要求、设计任务、工作计划、所需相关资料)(纸张不够可加页) 1、已知技术参数: 图1 支座零件图 2、设计任务与要求: (1)设计任务 1 选择零件的铸型种类,并选择零件的材料牌号。 2 分析零件的结构,找出几种分型方案,并分别用符号标出。 3 从保证质量和简化工艺两方面进行分析比较,选出最佳分型方案,标出浇注位 置和造型方法。 4 画出零件的铸造工艺图(图上标出最佳浇注位置与分型面位置、画出机加工余 量、起模斜度、铸造圆角、型芯及型芯头,图下注明收缩量) 5 绘制出铸件图。
(2)设计要求 1设计图样一律按工程制图要求,采用手绘或机绘完成,并用三号图纸出图。 2 按所设计内容及相应顺序要求,认真编写说明书(不少于3000字)。 3、工作计划 熟悉设计题目,查阅资料,做准备工作1天 确定铸造工艺方案1天 工艺设计和工艺计算2天 绘制铸件铸造工艺图1天 确定铸件铸造工艺步骤2天 编写设计说明书3天 答辩 1天 4.主要参考资料 《热加工工艺基础》、《金属成形工艺设计》、《机械设计手册》 系主任审批意见: 审批人签名: 时间:2012年月日
支架铸造工艺设计
毕业设计论文
设计(论文)题目:
支架铸造工艺设计
下 达 日 期: 2012 年 12 月 3 日
开 始 日 期: 2012 年 12 月 3 日
完 成 日 期: 2012 年 1 月 8 日
指 导 教 师:
李明
学 生 专 业: 材料成型与控制技术
班
级:
材料 1003 班
学 生 姓 名:
教 研室主任:
杨兵兵
材 料 工 程 学院
陕西工业职业技术学院
SHAANXI POLYTECHNIC INSTITUTE
毕业论文
前言
铸造是指熔炼金属,制造铸型,并将熔融金属浇入铸型,凝固后获得具有 一定形状、尺寸和性能金属零件毛坯的成形方法。在金属加工领域中,铸造 是世界历史上最悠久的工业之一。青铜冶炼技术的发明,使人类进入了青铜 器时代。伴随着青铜冶炼技术的同时,出现了铸造技术。我国的铸造技术已 有近 6000 年悠久的历史,是世界上较早掌握铸造技术的文明古国之一。2500 多年以前(公元 513 年)就铸出 270kg 的铸铁邢鼎。我国是最早应用铸铁的 国家之一,自周朝末年开始就有了铸铁,铁制农具发展很快,秦、汉以后, 我国农田耕作使用了铁制农具,如耕地的犁、锄、镰、锹等,表明我过当时 已具备有相当先进的铸造生产水平,到宋朝我国已使用铸铁炮和铸造地雷。
从商朝起,我国就已创造了灿烂的青铜文化,所谓“钟鸣鼎食”,成了当 时贵族权势和地位的标志。 我国最大的钟是明朝永乐大钟,现存于北京大钟寺内,铸于明朝永乐年间(公 元 1418-1422 年),全高 6.75m,钟口外径 3.3m,钟唇厚 0.185m,重 46.5t。 据考证钟体铸型为泥范,芯分七段。先铸成钟钮,然后再使钟钮与钟体铸接 成一体。钟体的内外铸满经文,约 227000 余字。大钟至今完好,声音优雅悦 耳,声闻数十里,是世界上罕见的古钟之一。我国古代的钟、鼎等文物,有 不少是用熔模远铸造的,其工艺复杂。铸工精湛、铸件精美,不难看出我国 古代熔模铸造工艺已达到相当高的水平。 1953 年在河北省兴隆县古燕国铸冶作坊遗址的挖掘中,发现距今 2200-2350
2
右铰接支架铸造工艺设计
华中科技大学专业课程设计报告题目:右铰接支架铸件工艺设计 学院:材料学院 班级: 分组组别号: 1 组员: 评分: 评分人:
目录 任务书 (3) 摘要 (4) 1.零件分析 (5) 1.1.设计要求 (5) 1.2.UG三维设计 (5) 1.1.材料信息 (6) 1.2.UG厚度分析 (6) 2.铸造方案确定 (7) 2.1.造型方法 (7) 2.2.金属合金球化与孕育处理 (8) 2.3.分型面 (8) 2.4.浇注位置确定 (9) 3.铸造工艺参数设计 (10) 3.1.铸件尺寸公差 (10) 3.2.铸件重量公差 (11) 3.3.机械加工余量 (11) 3.4.铸造收缩率 (12) 3.5.起模斜度 (12) 3.6.最小铸出孔 (12) 3.7.铸型、砂芯设计 (13) 铸型设计 (13) 砂芯设计 (15) 4.浇注系统设计 (16) 4.1.浇注温度 (16) 4.2.浇注时间 (16) 4.3.浇道截面积计算 (17) 方案一 (17) 方案二 (19) 5.数值模拟与工艺优化 (20) 5.1.模拟条件及材料物性参数 (20) 5.2.铸件模拟 (21) 5.3.冒口设计 (22) 5.4.方案设计与优化 (22) 方案一 (22)
方案一优化设计 (24) 方案二 (25) 比较总结 (26) 6.砂箱设计 (27) 6.1.设计原则 (27) 6.2.尺寸设计 (27) 7.铸件清理 (30) 8.铸造工艺卡 (32) 8.1.方案一 (32) 8.2.方案二 (33) 9.总结 (33) 10.参考文献 (34) 11.附图 (34)
支座铸造工艺设计
热加工工艺课程设计 圆形支座铸造工艺设计 院系:机电工程学院 专业:材料成型及控制工程 班级:材料三班 姓名:张文丁 学号:1103040306 指导老师:廖艳春 时间:2014年6月13日
摘要 热加工技术是机械类个专业一门重要的综合性技术学科。在机械制造过程中,由于加工过程十分复杂,加工工序繁多,工艺过程不仅有铸造成型,锻压成形,焊接成形,还有非金属的模压成形,挤压成形等。因此选着合适的工艺是保证产品质量的重要依据。本次课程设计,将进行铸造工艺的总结和学习。 铸造主要是将液态金属或合金浇注到与零件尺寸、形状相适应的铸型型腔里,待其冷却凝固后获得毛坯或零件的方法,是机械类零件和毛坯成型的主要工艺方法,尤其适合于制造内腔和外形复杂的毛坯或零件。 本文主要分析了支座的结构并根据其结构特点确定了它的铸造工艺,支座是支撑零部件的载体其主要承受了轴向的压缩作用的机械零件。在日常生产中对支座的选用异常广泛,因为它具有经济型良好、结构稳定性好、结构简单美观实用等特点,所以在机器零件的设计,加工过程中支座都起着不可代替的作用。 确定支座的铸造工艺过程主要包括:1)铸型及方法选择、2)分型面选择、3)浇注位置的确定、4)工艺参数的确定、5)浇注系统的设计、7)绘制铸造工艺图、8)绘制铸件图型面,型芯的数量、形状、尺寸及固定方法,加工余量,收缩率,浇注系统,起模斜度,冒口和冷铁的尺寸和位置等。
目录 绪论 (1) 一、零件的简介 (2) 1.1 零件的介绍 (2) 1.2确定零件的材料及牌号 (2) 二、铸造工艺方案的确定 (3) 2.1铸件的结构特点 (3) 2.2铸件的工艺分析 (4) 2.3分型面选择 (4) 2.4 确定出最佳浇注位置 (6) 三、工艺参数确定 (8) 3.1工艺参数的确定 (8) 3.1.1铸件尺寸公差 (9) 3.1.2 机械加工余量 (9) 3.1.3铸造收缩率 (9) 3.1.4起模斜度 (10) 3.1.5铸造圆角 (10) 3.1.6反变形量 (10) 3.2 砂芯设计 (10) 3.2.1 芯头的设计 (10) 3.2.2 砂头的定位结构 (11) 3.2.3 芯座 (11) 四、浇注系统及冒口、冷铁、出气孔等设计 (11) 4.1 浇注系统的设计 (11) 4.1.1选择浇注系统类型 (12) 4.1.2横浇道及内浇道 (12) 4.2 冒口的设计 (12) 4.3 冷铁的设计 (13) 4.4 出气孔的设计 (13) 五、铸造工艺图绘制 (14) 六、铸件图的绘制 (15) 七、支座铸造工艺卡 (16) 总结 (17) 致谢 (18) 参考文献: (19)
钛合金在体育器材中的应用
钛合金在体育器材中的应用 发布时间: 2007-06-01 | 钛(Ti)发现于1789年,1908年挪威和美国开始用硫酸法生产钛白,1910年在试验室中第一次用钠法制得海绵钛,1948年美国杜邦公司才用镁法成吨生产海绵钛,这标志着海绵钛即钛工业化生产的开始。 钛及其合金具有密度小、比强度和比刚度高、抗腐蚀和疲劳、耐高温、可焊接等一系列优越性,是21世纪最有发展前途的轻合金结构材料之一。 近年来,世界钛工业和钛材加工技术获得了飞速发展。海绵钛、变形钛合金和铁合金加工材的生产和消费都达到了很高的水平,其应用领域几乎扩展到了所有的军事和民用工业部门。 目前,钛合金主要用于航天航空和军事工业上。据统计,钛在航天航空上的应用约占钛总产量的70%,主要用作发动机构件和机架构件。在其他工业领域,钛合金主要用作电站冷却系统中的热交换器;油、气钻井用具及配件;化学化工部门中的防腐设备与器材;发电设备,以及环保与污染控制设备等。另外,钛在体育运动器材方面有着巨大的应用潜力。影响钛材广泛应用的主要问题仍是成本太高和新型的多用途的钛合金材料研制开发太少。 1. 钛合金及其特性 1.1 钛的性质 钛的导热性能较差,其热导率比不锈钢的略低。工业纯钛在250K时其热导率达到最大值(17.56W/(m﹒K)),约在580K时达最小值(16.89W/(m﹒K))。 钛合金的化学活性高,在空气中加热时易产生氧化皮。在加热和酸洗时容易吸氢并产生氢脆。钛合金可进行压力加工、机械切削加工和焊接及其他接合加工。钛合金具有耐海水或淡水腐蚀的优异性能。 1.2 钛合金及其分类 按照亚稳定状态相组成进行钛合金分类的方法是一种比较科学的方法,可把铁合金大体分为六种类型: a型、近a型、马氏体a+p型、近亚稳定p型、亚稳定R型。表1是按照上述分类方法对现有工业钛合金所进行的分类。 1.3 钛合金的工艺特性 钛合金结晶组织,物理和化学性质的特点使其具有与钢、铝合金和重金属合金工艺性能根本不同的综合工艺性能。钛合金一般倾向于熔炼直径达900mm以上、重量达10~15t的圆断面大铸锭。真空电弧熔炼的一个重要特点是将熔化、铸造和凝固过程结合为一个整体。熔炼过热度大,易形成粗大的铸造组织,因此必须用大变形量来达到需要的性能水平。 2. 钛合金的应用领域 (1)钛的最大用户是航空航天工业,主要用于飞机发动机、机架、起落架、火箭和导弹等。21世纪以来,世界两个飞机制造公司——波音和空中客车都增加了飞机的产量,年民航飞机交货量近千架。 (2)在工业领域,钛是石油、化工、轻纺、冶金、电力等几乎所有工业领域都十分受欢迎的结构材料。用于制造化学化工耐蚀反应器、电解用铁阳极、钛阴极板、氯碱生产用钛阳极、氧气冷却热交换器等,电镀行业中的钛网篮、吊挂装置、钛阳极等,发电厂用冷凝器、蒸汽涡轮发电机、涡轮叶片等,石油钻井设备和海下输油管等。
钛合金
各位老师,大家上午好。我今天试讲的内容为“铸造钛合金及其成形工艺”,分四个部分进行讲述。 一、铸造钛合金的分类 二、钛合金的特性 三、钛合金的铸造性能 四、钛合金的成形方法 一、铸造钛合金的分类 钛是同素异构体,熔点1720℃,882℃为同素异构转变温度。α-Ti是低温稳定结构,呈密排六方晶格;β-Ti是高温稳定结构,呈体心立方晶格。不同类型的钛合金,就是在这两种不同结构中添加不同种类、不同数量的合金元素,使其改变相变温度和相分含量而得到的。室温下钛合金有三种基体组织(α、β、α+β),故钛合金也相应分为三类。 1.α钛合金 它是α相固溶体组成的单相合金。耐热性高于纯钛,组织稳定,抗氧化能力强,500~600℃下仍保持其强度,抗蠕变能力强,但不能进行热处理强化。牌号有TA7、TA8等。 2.β钛合金 它是β相固溶体组成的单相合金。不经热处理就有较高的强度,淬火时效后合金得到了进一步强化,室温强度可达1373~1668MPa,但热稳定性较差,不宜在高温下使用。牌号有TB1、TB2等。 3.α+β钛合金 它由α及β相组成,α相为主,β相少于30%。此合金组织稳定,高温变形性能好,韧性和塑性好,能通过淬火与时效使合金强化,热处理后强度何必退火状态提高50%~100%,高温强度高,可在400~500℃下长期工作,热稳定性稍逊于α钛合金。牌号有TC1、TC4、TC6等。 二、钛合金的特性 钛及钛合金是一种新型的、很有发展潜力和应用前景的结构材料,具有许多优良特性,主要体现在如下几个方面: 1. 比强度高。钛合金的密度仅为钢的60%左右,约4.5g/cm3,但强度却高于钢,如抗拉强度为686—1176MPa,是现代工程金属材料中最高的。 几种金属材料在不同温度下的比强度,可以看出,用钛合金代替钢和铝合金而降低重量是相当可观的。资料介绍,自20世纪60年代中期起,美国将81%的钛合金用于航空工业,其中40%用于发动机构件,36%用于飞机骨架,甚至的蒙皮、紧固件及起落架等也使用钛合金,大大提高了飞机的飞行性能。 由于高的比强度,钛合金可能易于替代那些空间受限的铝合金及钢构件,如苏-27飞机起落架臂就采用钛合金。 2. 热强性好 往钛合金中加入合金强化元素后,大大提高了钛合金的热稳定性和高温强度,如在300~350℃下,其强度为铝合金强度的3~4倍。 3. 高温和低温性能优良。 在高温下,钛合金仍能保持良好的机械性能,其耐热性远高于铝合金,且工作温度范围较宽,目前新型耐热钛合金的工作温度可达550—600℃;在低温下,钛合金的强度反而比在常温时增加,且具有良好的韧性,低温钛合金在-253℃时还能保持良好的韧性。 4.钛的抗腐蚀性强。钛在550℃以下的空气中,表面会迅速形成薄而致密的氧化钛膜,
模具支架铸造工艺设计说明书
球墨铸铁模具支座 一、生产条件及技术要求 1、生产性质试制研发。 2、材质材质为QT400—15。 3、零件图 4、主要技术要求力学性能:σb>400MPa;δ≥15%;130-180HBW。金属组织:球化等级≤4级;石墨大小5.8级;φ(P)≤20%;ω(Fe3C)≤3%. 二、造型、制芯 1、造型采用手工造型;砂箱尺寸600mm*620mm*250mm,每型4件。 2、制芯设备芯盒制芯。
三、熔炼工艺 1、铁液的化学成分ω(C)=3.6%-3.9%;ω(Si) ≤3.0%;ω(Mn)<0.5%; ω(P) ≤0.07%;ω(S)<0.03%;ω(Mg) 残=0.03%-0.05%;ω(Re) 残 =0.01%-0.03%。 2、球化剂稀土镁硅铁合金,加入量为铁液质量分数的1.5%-1.7%。 3、出炉温度 1420-1440℃。 4、浇注温度 1320-1380℃。 5、孕育剂 75Si-Fe合金孕育,加入量为包内铁液质量分数的0.3%-0.7%。 6、熔炼设备0.5t无芯工频感应电炉熔炼原铁液;在100Kg铁液包中进行球化 处理;转50Kg浇包进行浇注。 四、主要工艺参数 1、加工余量 2-3mm,模具支座面机械加工余量取3mm;模具支座底面及侧面机械 加工余量取2mm。 2、收缩率 1%。 3、拔模斜度 1°。 4、砂型硬度砂型硬度大于40(C型硬度计)。 5、吃砂量吃砂量为30-60mm。 6、型砂性能湿压强度为0.12-0.14MPa,透气性≥100cm2/(Pa*s),紧实率为40%-48%(夏季),41%-47%(冬季)。 7、铸造圆角铸造圆角为R2。 五、铸造工艺方案 1、浇注位置及分型面的选择由于本铸件采用试制研发的方案进行设计,其可能的分型面的选取有如下图所示的6种:
机械制造工艺学课程设计张紧轮支架
1 零件的分析 (5) 1.1零件的作用 (5) 1.2零件的工艺分析 (5) 2零件的生产类型 (5) 2.1生产纲领 (5) 2.2生产类型 (6) 3毛坯的确定 (6) 3.1确定毛坯类型及其制造方法 (6) 3.2估算毛坯加工的机械加工余量 (6) 4定位基准选择 (6) 4.1选择精基准 (6) 4.2选择粗基准 (6) 5制定机械加工工艺路线 (6) 5.1选择加工方法 (6) 5.2加工工艺路线 (7) 6加工余量及尺寸的确定 (8) 6.1确定粗加工支架上端面的加工余量及工序尺寸 (8) 6.2确定支架底面的加工余量及工序尺寸 (9) 6.3确定精加工支架上端面的加工余量及工序尺寸 (11) 6.4确定支架右侧面的加工余量及工序尺寸 (12) 6.5确定支架右侧面φ18孔的加工余量及工序尺寸 (13)
6.6确定支架下端面的加工余量及工序尺寸 (15) 6.7确定支架小侧面的加工余量及工序尺寸 (17) 6.8确定支架2*φ13孔的加工余量及工序尺寸 (17) 7切削用量和时间定额的确定 (19) 8课程设计总结 (21) 参考文献 (22) 附1紧轮支架零件图 附2毛坯图 附3机械加工工艺过程综合卡片 附4夹具零件图 附5夹具装配图
机械制造工艺学 课程设计任务书 题目:设计紧轮支架零件的机械加工工艺规程 及工艺装备(年产量为8000件) 容: 1.紧轮支架零件图 1 2.毛坯图 1 3.机械加工工艺过程综合卡片 1 4.夹具装配图 1 5.夹具零件图 1 6.课程设计说明书 1份 专业机械工程 班级机工100x班 学生 xxx、xxx 指导教师 xxx 2012年 11 月 1 日
口腔修复治疗中应用铸造支架50例临床报告
口腔修复治疗中应用铸造支架50例临床报告 目的:探讨铸造支架用于口腔修复治疗的临床疗效。方法:选择2012年1月-2013年12月笔者所在医院收治的50例行覆盖义齿修复的患者,根据所用铸造支架的金属材料分为钴铬合金组(n=26)和钛合金组(n=24),比较两组修复后固定力、咀嚼效率、满意度、并发症的发生率。结果:两组修复后固定力、咀嚼效率均高于修复前(P<0.05);但两组修复前、修复后固定力、咀嚼效率比较,差异均无统计学意义(P>0.05)。修复后两组患者舒适程度、义齿外观、语言功能得分均高于修复前(P<0.05),但两组比较差异均无统计学意义(P>0.05)。两组均有1例出现并发症。结论:铸造支架在口腔修复中安全、有效,可以增强固定力,提高咀嚼效率,提高患者满意度。钛合金和钴铬合金材料制作的铸造支架其疗效和副作用均无明显差异。 标签:钛合金;钴铬合金;口腔修复;固定力;咀嚼效率 牙列缺损的修复方式有多种,铸造支架因具有性能稳定、轻巧、坚固、异物感小等特点,被广泛应用于义齿修复。其制作材料要求质量高,设计要求合理,工艺较为复杂。为探讨铸造支架在口腔修复治疗中的应用效果,对2012年1月-2013年12月笔者所在医院收治的50例应用铸造支架进行口腔修复患者的临床资料进行分析,现报道如下。 1 资料与方法 1.1 一般资料 选择2012年1月-2013年12月笔者所在医院收治的50例行覆盖义齿修复的患者,根据所用铸造支架的金属材料分为钴铬合金组和钛合金组。钴铬合金组26例患者中,男12例,女14例,年龄21~75岁,平均(50.23±3.24)岁;病程3个月~6年,平均(10.23±3.04)个月。钛合金组24例患者中,男12例,女性12例,年龄19~75岁,平均(50.71±3.09)岁;病程3个月~6年,平均(10.61±3.21)个月。两组患者性别、年龄、病程等比较差异均无统计学意义(P>0.05),具有可比性。两组基牙均选择活动度0.8 cm,牙槽骨未吸收或吸收的程度控制在1/3根长以内,残冠或残根经过完善根管治疗。 1.2 方法 钴铬合金组支架材料选用进口钴铬合金材料,钛合金组选用进口钛合金材料。主要步骤包括基牙预备、根帽制作、义齿制作、试戴及完成义齿覆盖。对患者根管治疗10 d 左右,磨平基牙根面,制作防旋转沟槽;将硅橡胶注入根管,覆盖整个根面,用印模法制作出基牙以及颌弓印模,灌注超硬石膏模型。在模型上设计画线然后用琼脂复制耐火材料模型,在模型上设计制作蜡型,包埋,高温烧结,铸造,喷沙打磨。试戴支架后常规排牙煮盒打磨再次试戴。
悬臂支架铸造工艺设计说明书
xxxxxxxxxxxxxxxxxx 课程设计报告 课程设计名称:悬臂支架铸造工艺设计 学生姓名:xxxxxxxxxxxxxxx 学院:xxxxxxxxxxxxx 专业及班级:xxxxxxxxxxxxxx 学号:xxxxxxxx 指导教师:xxxxx xxxxxxxxxxxxxxx
摘要 铸造生产通常是指用熔融的合金材料制作产品的方法,将液态合金注人预先制备好的铸型中使之冷却、凝固,而获得毛坯或零件,这种制造过程称为铸造生产,简称铸造,所铸出的产品称为铸件。大多数铸件作为毛坯,需要经过机械加工后才能成为各种机器零件;有的铸件当达到使用的尺寸精度和表面粗糙度要求时,可作为成品或零件直接应用。 本课程设计是为了获得ZG270-500悬臂支架的合理铸造工艺设计方案,初步设计悬臂支架的铸造工艺方案,包括选择铸件的浇注位置及分型面,确定型芯的数量、定位方式、下芯顺序、芯头形状及尺寸,确定工艺参数(如机械加工余量、起模斜度、铸造圆角级收缩率等)以及浇注系统、冒口、冷铁的形状和尺寸及在砂型中的布置等,通过Pro/e进行仿真,根据模拟结果进行分析,铸造工艺方案的合理性,然后将所确定的工艺方案用文字和铸造工艺符号在CAD零件图上表示出来,绘制铸造工艺图。 关键词:铸造工艺设计,悬臂支架,Creo,CAD。
Usually refers to using the molten alloy casting production material products, the method of the liquid alloy preparation beforehand good mold in injection cooling and solidification, and blank or parts, the manufacturing process is referred to as casting production, referred to as "casting, casting out products are referred to as casting.As most of the casting blank, need after mechanical processing can be all kinds of machine parts;Some castings when to use the dimensional accuracy and surface roughness requi rem ent s, can be di rect l y appli ed as fini shed products or parts. This course is designed to obtain reasonable ZG270-500 cantilever casting process design, preliminary design of cantilever casting process, including selection of casting pouring position and parting surface, determine the number of cores, positioning way, the core order, core head shape and size, determine the process parameters (such as machining allowance, mould level Angle, casting the rounded shrinkage rate, etc.) and the pouring system, riser and chill the shape and size and arrangement in the sand mold, etc, through the Creo simulation, according to the result of simulation is analyzed, the rationality of the casting process, then determine the processing plan in words and casting process representation in the CAD drawing, mapping the casting process. Keywords: casting process design; cantilever; Creo; CAD.
支架铸造课程设计说明书
南昌航空大学铸造工艺专业课程设计 题目:支架铸造工艺设计 院系:航空制造工程学院 专业:材料成型及控制工程 学号: 09033104 姓名:石婷 指导老师:戴斌煜 日期: 2012年11月30日
目录 1设计任务的分析 (1) 1.1铸件的结构特点 (1) 1.2铸件的材料及性能 (1) 1.3铸件的技术要求 (1) 2铸造工艺方案的确定 (1) 2.1铸件在金属型中的位置 (1) 2.2铸件的凝固顺序 (2) 2.3浇注位置与分型面的选择 (2) 2.3.1浇注位置的选择 (2) 2.3.2分型面的选择 (2) 2.4铸造工艺参数的确定 (3) 2.5浇注系统类型的形式 (3) 2.6熔化与浇注 (5) 3浇注系统的计算 (5) 3.1浇注时间的确定 (5) 3.2浇注系统截面积计算 (5) 3.3冒口设计计算 (6) 4金属型的设计 (6) 4.1金属型设计 (6) 4.1.1 金属型类型 (6) 4.1.2主要结构形式 (7) 4.1.3金属型壁厚 (7) 4.1.4型腔尺寸计算 (7) 4.1.5刚度强度 (8) 4.1.6耐用性 (8) 4.1.7 标准 (8) 4.1.8其他尺寸要求 (8) 4.1.9金属芯设计 (8) 4.1.10型腔的排气 (8) 4.2锁紧机构 (8) 4.3金属模材质选择 (9) 5.铸造工艺 (9) 5.1金属型的准备 (9) 5.1.1金属型的清理 (9)
5.1.2金属型的涂料 (9) 5.1.3金属型的预热 (9) 5.2浇注温度和速度 (10) 参考文献 (11) 设计总结 (12)
1设计任务的分析 1.1铸件的结构特点 铸件为支架,最大尺寸280mm,属小型铸件,支架基本壁厚为5mm,最大壁厚为18mm,有三个直径为11mm的孔,可采用机加工方法得到,不铸出。有四个内凹空腔。 1.2铸件的材料及性能 材料为ZL201-T4,铸造铝铜合金,属Al-Mn-Cu-Ti合金,抗拉强度295MPa,硬度HB70,密度2.78g/cm3,熔化温度548-650℃。(GB/T1173-1995) 1.3铸件的技术要求 机加工余量:铸件最大尺寸为280mm,所以铸件机加工等级为D-F,D-1.3mm,E-1.4mm (GB/T 6414-1999) 工艺余量:铸件支架壁厚5mm,设置冒口及高于铸件的浇口,作为充填铸型所必需的重力和补缩之用,作为工艺余量。 质量等级:金属型铝合金铸件尺寸公差合格品≤CT8,表面粗糙度要求的有6.3和3.2,其余面不用加工。 未注圆角半径2mm;铸造斜度0o30′;铸件收缩率1.6。重要加工表面不得有铸造缺陷;应使铸件内外表面无气孔、缩孔缩松、裂纹、浇不足等缺陷;表面应光洁美观。 2铸造工艺方案的确定 2.1铸件在金属型中的位置 考虑因素:①保证铸件的顺序凝固,将铸件薄壁部分放在下面,粗大部分放在上面,以使冒口对铸件起到良好的补缩作用。 ②主要工作面最好放在下面,以保证铸件质量。 根据铸件的特点,采用金属型铸造,左右半型分开制造。
轴托架铸造工艺设计
轴托架铸造工艺设计 1 生产条件及技术要求 铸件材质:HT200 铸件形状:地面有两个凸台,中部空心,上部弧形的架体,结构如图1所示。 铸件尺寸:地面厚度5mm,凸台高度7mm 铸件重量:5kg 使用条件: 轴托架于将轴累零件托起,底面有两凸台,中部空心且形状不规则,上部半圆形凹槽用于轴类零件的防治、、放置。 主要技术要求: 轴托架为小型薄壁铸件,根据其用途,轴托架应具有一定的力学性能,能承担一定载荷,使用HT200铸造可满足使用要求;轴托架架体外形尺寸精度要求不高,但应保证底面的平行度及厚度以及凸台的高度仪满足装配要求,且应具有一定的表面光洁度以满足美观要求;与轴类零件配合的半圆形凹槽需铸后机加工,以满足尺寸配合要求。 图1 轴托架结构简图
2 铸造工艺方案 铸造工艺种类:砂型铸造,三箱造型 铸型设计及分型面选择: 设计铸型如图2所示,铸件的中部空心结构、上部半圆形结构用型芯造出。根据铸件结构及形状,选用三箱造型,铸造分箱面即模型分型面,如图2中虚线所示。 砂芯选择: 铸件的中部空心、上部半圆形结构需用型芯造出,共需两个型芯。其中用于造出中部空心结构的砂芯形状与铸件中空部分形状相同,矩形平面处应有固定装置以便起模后将砂芯固定在上箱型砂中,固定装置应避开直浇道且与横浇道干涉较少;用于造出上部半圆形结构的型芯为半圆柱形,其直径尺寸应小于铸件半圆形结构的尺寸,留出3mm的加工余量,半圆柱体矩形纵截面中部应有固定装置以便起模后将型芯固定在下箱型砂中。 浇注位置选择: 考虑到铸件主体为中空薄壁结构,浇口设在轴托架矩形平面中心位置上方,通过设置横浇道使液态金属沿架壁均匀下流。 凝固原则: 使用树脂自硬砂型,最大限度地利用石墨化膨胀,实现铸件自补缩;采用浇注系统当主冒口,并在上箱型砂处扎若干个透气孔。 造型方法: 铸件为小型铸件,直接在小砂箱中三箱造型,制作直浇道后起模,装入型芯并制作横浇道,之后合箱浇注。 图2 模型、分模面及分箱面示意图
铸造工艺设计说明书
“永冠杯”第三届中国大学生铸造工艺设计大赛 参赛作品 铸件名称:B件---铰接支架 自编代码:AB33510A 方案编号:
目录 摘要 (1) 1 零件简介 (2) 1.1零件名称及用途 (2) 1.2零件的技术要求 (2) 1.3零件的结构 (2) 2铸造工艺方案 (3) 2.1材料选择 (3) 2.2工艺方案的选择 (3) 2.3工艺参数的确定 (5) 2.3.1铸件的尺寸公差 (5) 2.3.2铸件的质量公差 (5) 2.3.3机械加工余量 (5) 2.3.4模样的起模斜度 (5) 2.3.5铸造收缩率 (5) 2.3.6最小铸出孔 (5) 2.4浇注系统的设计 (6) 2.4.1浇注系统的选择 (6) 2.4.2浇注系统尺寸的计算 (6) 2.4.3浇注系统设计的校核 (8) 2.5砂芯设计 (9) 2.5.1砂芯设计的要点 (9) 2.5.21#砂芯 (10) 2.5.32#砂芯 (11) 2.6冒口设计 (12) 2.6.1冒口设计的说明 (12) 2.6.2冒口的尺寸计算 (12) 2.7出气孔的设计 (13)
3砂箱的设计 (13) 4铸件充型及凝固过程数值模拟 (14) 4.1ViewCast 模拟软件 (14) 4.2充型过程模拟 (14) 4.3铸造凝固过程数值模拟 (17) 4.4铸造工艺改进方案 (18) 结论 (19) 参考文献 (20) 附图1 ——铸造工艺图 附图2 ——合箱图 附图3 ——铸造工艺卡片 附图4 ——砂箱图
摘要 该铸件为驾驶室右铰接支架,通过分析零件的结构特点和性能要求,选用粘土砂湿型手工造型方法,采用两箱造型,确定了浇注位置和分型面等工艺方案,使零件整体位于下箱。确定了机械加工余量、起模斜度、铸件收缩率等工艺参数。根据各铸造工艺参数用Pro/Engineer软件画出铸件的三维实体图。根据零件的形状特征,选用两个竖直放置的砂芯,1#砂芯采用盖板砂芯的形式固定。选用了封闭式底注式浇注系统,采用了两个内浇道,用奥赞公式计算了浇注系统各部分的截面面积和尺寸,根据工艺方案在铸件顶部放置了两个用于补缩的暗冒口。用Viewcast软件对铸件进行充型过程和凝固过程数值模拟,根据模拟结果对工艺方案优化。最后达到充型过程平稳,没有缩松缩孔的效果。 关键词:球墨铸铁;工艺优化;浇注系统;数值模拟;