2010年上半年我国炼铁技术发展评述
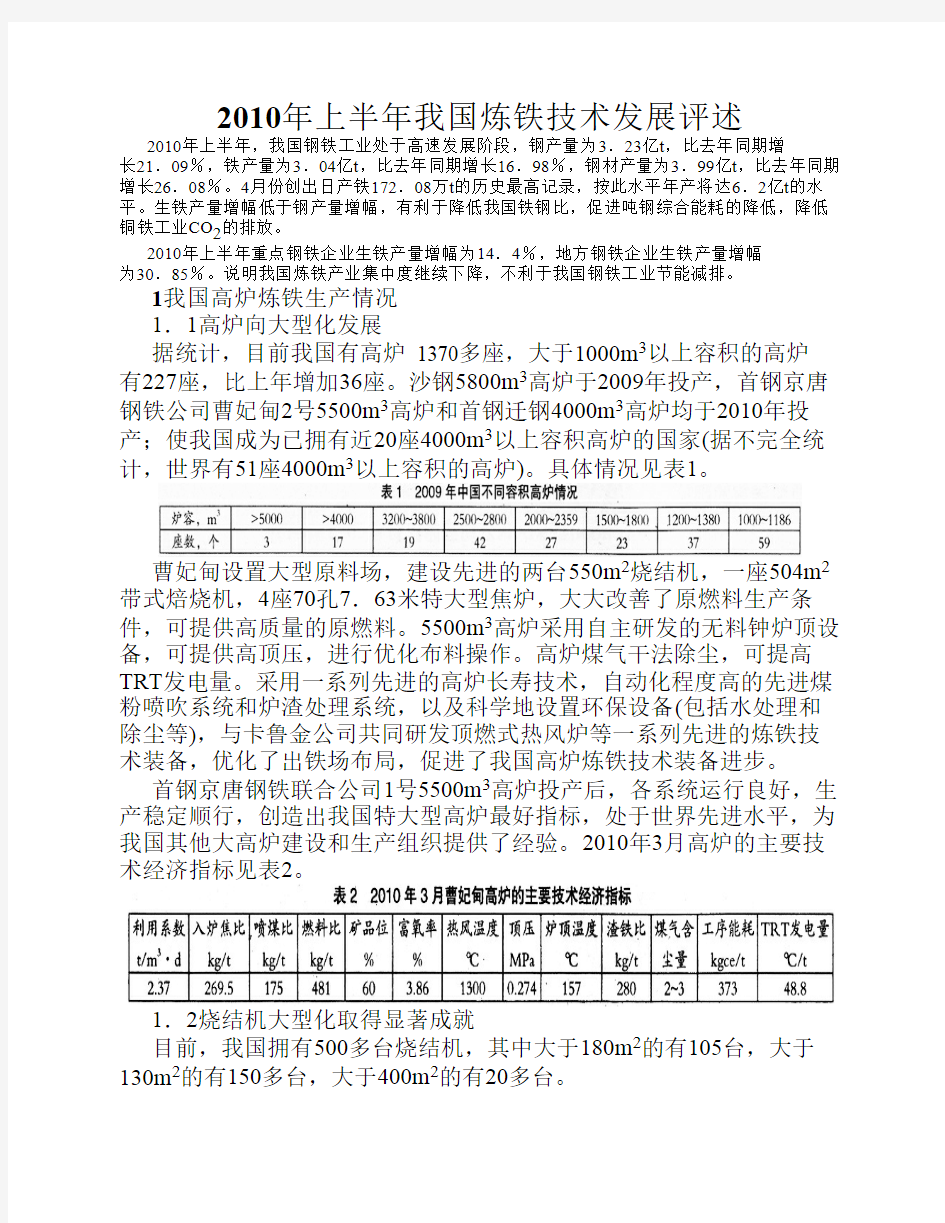

2010年上半年我国炼铁技术发展评述2010年上半年,我国钢铁工业处于高速发展阶段,钢产量为3.23亿t,比去年同期增
长21.09%,铁产量为3.04亿t,比去年同期增长16.98%,钢材产量为3.99亿t,比去年同期增长26.08%。4月份创出日产铁172.08万t的历史最高记录,按此水平年产将达6.2亿t的水平。生铁产量增幅低于钢产量增幅,有利于降低我国铁钢比,促进吨钢综合能耗的降低,降低铜铁工业CO2的排放。
2010年上半年重点钢铁企业生铁产量增幅为14.4%,地方钢铁企业生铁产量增幅
为30.85%。说明我国炼铁产业集中度继续下降,不利于我国钢铁工业节能减排。
1我国高炉炼铁生产情况
1.1高炉向大型化发展
据统计,目前我国有高炉 1370多座,大于1000m3以上容积的高炉
有227座,比上年增加36座。沙钢5800m3高炉于2009年投产,首钢京唐钢铁公司曹妃甸2号5500m3高炉和首钢迁钢4000m3高炉均于2010年投产;使我国成为已拥有近20座4000m3以上容积高炉的国家(据不完全统计,世界有51座4000m3以上容积的高炉)。具体情况见表1。
曹妃甸设置大型原料场,建设先进的两台550m2烧结机,一座504m2带式焙烧机,4座70孔7.63米特大型焦炉,大大改善了原燃料生产条件,可提供高质量的原燃料。5500m3高炉采用自主研发的无料钟炉顶设备,可提供高顶压,进行优化布料操作。高炉煤气干法除尘,可提高TRT发电量。采用一系列先进的高炉长寿技术,自动化程度高的先进煤粉喷吹系统和炉渣处理系统,以及科学地设置环保设备(包括水处理和除尘等),与卡鲁金公司共同研发顶燃式热风炉等一系列先进的炼铁技术装备,优化了出铁场布局,促进了我国高炉炼铁技术装备进步。
首钢京唐钢铁联合公司1号5500m3高炉投产后,各系统运行良好,生产稳定顺行,创造出我国特大型高炉最好指标,处于世界先进水平,为我国其他大高炉建设和生产组织提供了经验。2010年3月高炉的主要技术经济指标见表2。
1.2烧结机大型化取得显著成就
目前,我国拥有500多台烧结机,其中大于180m2的有105台,大于130m2的有150多台,大于400m2的有20多台。
曹妃甸550m2的烧结机于2009年8月投产,是目前我国最大的现代化烧结机。太钢正在建设660m2的巨型烧结机。大型现代化烧结机的烧结矿质量好,工序能耗低,在多方面有着许多优越性。如一台500m2烧结机要比2台250m2烧结机工序节能20%。
近年来,我国烧结生产技术不断进步,大力推广优化配矿、自动称重、燃料分加、小球烧结、厚料层、高铁低硅烧结、热风烧结等先进技术,促进了烧结矿质量提高,工序能耗降低。新建烧结机已可实现漏风率在20%~30%。
目前,我国投产和在建的已有近120台(套)烧结机进行烟气脱硫,总面积达13800m2,各烧结厂采用了十多种不同的脱硫工艺设备,减
少SO2的污染。目前,尚没有一种万能的烧结烟气脱硫技术,因此,企业要根据自己的具体情况选择烧结烟气脱硫技术。脱硫设备总体投资成本在20万元/m2~40万元/m2,使烧结运行成本增加8元/t~15元
/t。烧结余热回收工作已在宝钢、马钢和济钢等企业大力开展,并取得显著成绩。
1.3链篦机—回转窑生产球团工艺已成为生产球团的主体工艺
目前,我国已拥有2.1亿t/a的生产球团矿能力,链篦机—回转窑生产球团工艺占球团生产总能力的57%。我们推荐广泛使用链篦机—回转窑工艺装备生产球团矿,实现球团矿高质量,低能耗。曹妃甸2009年投产的504t/a带式焙烧机是一座现代化大型生产球团设备,球团矿质量高,能满足5500m3高炉的需求。
2高炉炼铁部分技术经济指标取得进步
2010年上半年,全国重点钢铁企业高炉燃料比(未含小块焦比)
为517kg/t,比上年同期下降1kg/t;入炉焦比为369kg/t,比上年同期下降4kg/t;喷煤比为148kg/t,比上年同期升高3kg/t;热风温度为1152℃,比上年同期下降38℃;利用系数为2.590t/m3·d,比上年同期下降0.014t/m3·d。2010年上半年,重点企业高炉部分技术经济指标得到改善,具体情况见表3。
从表3可以看出,我国部分高炉技术经济指标已经达到或接近国际先进水平,充分表现出我国高炉炼铁生产技术水平已处于比较先进的水平。但是,从落后值的情况可以看出我国仍有一批应淘汰的落后技术装备还在运行之中。
目前,我国炼铁工业是多层次的,先进与落后并存,处于不同发展阶段。为促进我国炼铁生产技术进步,实现节能减排目标,提升炼铁企业的市场竞争力,我们应当加大推广成熟、先进、实用的炼铁技术装备。同时,也应加大淘汰落后炼铁能力(国家已明令要坚决淘汰400m3以下小高炉,约有2500万t)的工作。现已分解到14个省相关企业,于2012年前完成淘汰落后任务。
我国有870多家炼铁企业,造成产业集中度低,高炉平均炉容小,炼铁企业之间生产指标差距大。要加大贯彻落实国家公布的“钢铁工业振兴规划”的目标和任务,利用产业政策和市场经济的手段,加快炼铁企业的优化重组整合。
从2010年上半年发展形势看,我国炼铁企业技术发展有向两头发展的趋势。即先进的更先进,落后的继续下滑。主要是在落实炼铁精料方针的工作向两极分化。一些企业认为购买劣质低价矿石,可降低生产成本,造成炼铁指标全面下降。这需要经济上进行平衡。有一个合理科学经济的购买铁矿品位值。同时也要从国家利益考虑,不能再进口低于60%品位的铁矿石。低品位矿会带来炼铁能耗升高,污染物排放增加,不符合国家节能减排的大方针。还会造成因进口量大,有促进进口矿价格涨价的负面影响。
3高炉燃料比(不包括小块焦比)下降
2010年上半年重点钢铁企业高炉燃料比为517kg/t,比上年降低21 kg/t。重点钢铁企业中,有32家燃料比下降。但是,有37家燃料比在上升。这说明炼铁企业技术发展很不平衡。钢铁企业实现减量化用能的重点工作是在要努力降低炼铁燃料比上下功夫。降低燃料比的技术因素见表4。
2010年上半年重点钢铁企业燃料比下降的原因:人炉焦比为369 kg /t,比上年下降5 kg/t。焦炭质量得到改善:M40为84.37%,比去年升高0.25%。烧结矿质量也得到改善:转鼓强度为78.46%,比去年提高1.27%,烧结矿碱度为1.885,比去年提高0.074,烧结矿合格率为94.18%,比上年高0.28%,高炉大型化取得新进展。
2010年上半年,重点钢铁企业有32个企业高炉燃料比下降,与去年相比,燃料比降幅较大的企业有:天管、兴澄、西林、通钢、涟钢、韶钢、张店、川威、酒钢、南昌、沙钢、北台、新兴铸管、津两、北台、本钢。
2010年上半年燃料比较低的企业有:首钢京唐钢铁联合公司、宝钢、首钢、新冶钢、沙钢、兴澄、青钢、本钢、马钢股份、太钢、邯钢、通钢、鞍钢、邢钢等企业。
高炉工序能耗占钢铁联合企业总能耗的50%以上,高炉炼铁用能
有78%是来自碳素燃烧(就是燃料比)。所以,降低高炉燃料比是钢铁企业节能减排工作的重点,也是减少污染物排放的主要手段。2010年上半
年重点企业高炉燃料比降低,为我国吨钢综合能耗降低做出了重要贡献。我们应当大力推广能够大幅度降低燃料比企业的好经验。
下面分类介绍降低燃料比变化的几类情况:
(1)焦比和煤比同时下降,使燃料比下降。
焦比和煤比同时下降,使燃料比下降的企业有8家。高炉原燃料质量得到改善,热风温度的提高,操作水平提高等因素,可以实现焦比和煤比同时下降,使燃料比下降。
(2)焦比下降幅度大于煤比升高的幅度,使燃料比下降。
降低炼铁燃料比的主要体现是要降低焦比。提高喷煤比后,要实现煤粉高的置换比,才会使燃料比不会升高。这也是最经济的提高喷煤比的标准。提高热风温度是提高喷煤比的重要条件,也是提高煤粉置换比的重要条件。大多数钢铁企业通过这种办法来降低炼铁燃料比,这也符合炼铁技术发展的大方向。提高炼铁精料水平是降低燃料比的重要手段和有效的措施,特别是焦炭质量的提高会有较大的效应。2010年上半年有19个企业实现了焦比下降幅度大于煤比升高的幅度。
(3)煤比下降的幅度大于焦比升高的幅度,风温提高,燃料比下降。这是高炉操作水平提高的体现,主要措施是要进行科学布料、提高煤气利用率、降低生铁含硅量等。
(4)2010年上半年全国重点钢铁企业之中有37家燃料比与去年相比升高了,燃料比升高的企业数目多于降低的数目。体现出重点钢铁企业炼铁生产向两极分化,这种现象应引起高度重视。有10个企业是煤比和焦比同时升高,有10个企业是焦比升幅大于煤比降幅。有11个企业是煤比升幅大于焦比降幅。对此现象要作具体分析,其中主要原因是原燃料质量恶化,高炉顺行状态不好,不得以降低煤比,提高焦比,以维持高产。
4焦比下降
2010年上半年,全国重点钢铁企业高炉焦比与去年相比下降5kg/t。降低焦比,提高煤比,是降低炼铁生产成本的重要手段,也是炼铁系统结构优化的中心环节。有40个企业的焦比下降。
支撑焦比下降的重要技术条件是:提高入炉矿含铁品位,改善原燃料质量(特别是提高焦炭的质量),提高热风温度,提高高炉操作水平以及设备的大型化等等。
但是,2010年上半年有27家企业的炼铁焦比是上升了。
5喷煤比提高
2010年上半年,全国重点钢铁企业高炉喷煤比为148kg/t,比去年提高3kg/t。与去年相比,有47家企业喷煤比提高,喷煤比提高较多的企业有:略钢、天管、张店、承钢、新余、徐州、天钢、天铁、苏钢、水
钢等。高风温是提高喷煤比的重要条件。
提高喷煤比的技术条件是:高风温,富氧,脱湿鼓风,入炉矿含铁品位高,渣铁比低,炉料透气性好,优化高炉操作,炉内煤气分布均匀,各风口煤粉喷吹均勺,喷吹煤质量好(可磨性,流动性,可燃烧性,含碳量高,含有害杂质低等),矿石冶金性能好等。
2010年上半年全国重点钢铁企业中,喷煤比较高的企业有:德龙、长治、莱钢、武钢、宝钢、唐钢、鞍钢、太钢、湘钢、天铁、新兴铸管、合钢、泰钢、柳钢、国丰、济源等。
6热风温度呈下降趋势
2010年上半年,全国重点钢铁企业高炉热风温度为1168℃,比去年下降6℃,这是近年没有出现过的逆转现象。今年上半年有46个企业热风温度得到提高,提高50℃以上的企业有:苏钢、天管、重钢、兴澄、新余、海鑫、涟钢、承钢。
提高热风温度的技术措施是:热风炉拱顶使用耐高温的硅砖,热风炉拱顶在烧炉和送风时的温差小于100%~150℃,热风炉送风时间要控制在40min~60min,热风炉蓄热砖要用高蓄热面积的砖(由7孔改为19—37孔砖),并涂能吸热材料,提高热风炉废气温度(400℃~450℃),单烧高炉煤气的热风炉采用煤气和空气双预热技术,送风系统要能承受高风温,高炉能够使用和接受高风温等。目前我国一些企业热风温度偏低和热风炉寿命偏低的主要原因是使用的耐火砖质量差。为降低投资,购买质量差的耐火砖,致使风温提不上来,造成高炉长期得不到高风温,炼铁焦比高,其经济代价太大,得不偿失。要用技术经济的方法进行科学计算,确定合理经济的热风炉投资。
2010年上半年,全国重点钢铁企业高炉热风温度较高的企业有:京唐公司、太钢、宝钢、攀钢、三明、鞍钢、唐钢、津西、敬业、济源、新兴铸管、天管、天钢等。
7高炉休风率下降
2010年上半年,全国重点钢铁企业高炉休风率为1.6%,比去年下降0.057%。休风率较低的企业有:包钢、衡管、本钢、三明、通钢、龙门、邢钢、攀钢、新兴铸管、马钢股份、锡兴、达钢、宣钢。
高炉休风率低是高炉操作水平高和设备运行状态良好等方面的体现。高炉操作要使生产稳定顺行,不出现大的失误;设备管理要实行定检定修制度,不能等设备坏了再去更换,造成高炉休风率高,炼铁企业实行现代化管理,就会使高炉休风率低。
8炼铁系统工序能耗下降
表5是2010年上半年炼铁系统工序能耗。
从表5可以看出2010年上半年全国重点钢铁企业炼铁系统工序能耗取得了较好的成绩。由于炼铁工序能耗占钢铁联合企业总能耗的50%,所以高炉炼铁工序能耗下降对吨钢综合能耗有较大的影响。2010年上半年炼铁工序能耗较低的企业有:宣化、新余、太钢、凌钢、国丰、建龙、杭钢、安阳。
9存在问题和差距
①全国生铁产能快速增长,增加了能源消耗和污染物排放量,对环保产生负面影响,也影响到进口铁矿石和煤炭的价格。
②炼铁企业之间技术发展水平不平衡,使我国炼铁工业整体技术水平下降。
⑧2010年上半年,全国重点钢铁企业部分炼铁技术经济指标出现下滑。这与铁产量的增长、炼铁原燃料涨价和劣化、高炉操作指导方针等因素有关。
④2010炼铁企业要加强对生产过程的技术经济问题研究,特别是经济性的研究,要用系统工程的方法去分析,要加强调查研究,做出准确科学的判断。
炼铁企业因炼铁原燃料价格上涨,为降低成本,一些企业在购买低价低品位矿,造成炼铁燃料比和焦比升高、产量下降、污染物排放增多。高炉炼铁是以精料为基础,精料技术水平对高炉生产指标的影响率
在70%,购买低价低品位矿要有个度。
⑤我国冶金装备平均容量偏小,造成企业能耗高,污染物排放多,生产效率偏低。我国冶金装备应向大型化、高效化、自动化、长寿化、生产过程环境友好方向发展。我国钢铁工业要在提高产业集中度上下大工夫。国家政策要予以支持,创造出良好的市场环境,使企业有积极性去进行优化组合。高炉大型化要有相应的原燃料质量保证为提前。否则,大型化的高炉生产难以实现设定的目标。
炼铁的发展
炼铁的发展 由于人类对铁的需要量不断增加,人们把视线投向了地球本身,希望能在地球中找到所需要的铁,而不再是坐等“天外来客”的馈赠。为此人们作了不懈的努力。当人们学会了从矿石中提炼出铁以后,青铜时代就让位于铁器时代。在人类历史上,起过革命作用的原材料中铁应该居首位,无论在世界的哪个地区,冶铁技术的发明都是划时代的重大事件。 据研究,铁的大量出现是在公元前八世纪。在霍萨巴德的王宫贡物中(公元前720-705年)就发现了160吨铁,其中多是铁棒。公元前800年,欧洲转入早期铁器时期。炼铁知识传到不列颠,大约是在公元前500年。与此同时,约公元前400年,已由伊朗自东传到印度,也可能传到中国。欧洲早期铁器时代带触角木剑柄的剑与中国商周青铜剑之间就有很大的相似性。 制铁技术分为两部分:即冶炼和热锻。可能首先掌握并用于陨铁。 纯铁的熔点为1540℃。这个温度在公元19世纪前是不可能达到的。因此早期生产的锻铁都是固态铁。用木炭火在约1200℃的温度下,把铁矿石还原成基本上是纯的固态铁。还原出来的铁呈团块状,称为“坯铁”。这是一种固态铁、渣和未烧完木炭屑的混合物。有时要把这种坏铁破碎,靠敲击使小铁块相互分开。这种小铁块可以与其它部分区别开来。因为它们是可锻的,在敲击下变平。然后把它们放在锻炉加热,经过热锻,小铁块就能被锻接成大块。 早期的冶铁技术,大多采用“固体还原法”,即冶铁时,将铁矿石和木炭一层夹一层地放在炼炉中,点火焙烧,在650 ̄1000℃温度下,利用炭的不完全燃烧,产生一氧化碳,遂使铁矿石中的氧化铁被还原成铁。但是由于炭火温度不够高,致使被还原出的铁只能沉到炉底而不能保持熔化状态流出。人们只好待把铁炼成,炼炉冷却后,再设法将铁取出。这种铁块表面因夹杂渣滓而显粗糙,有的还不如青铜坚韧。后人们发现,炼出的铁反复加热,压延锤打,才能柔韧不脆。人们还发现再将红热的锻铁猛淬入冷水会变成坚韧的好铁,这种铁比青铜好。 最原始的炼铁炉是碗式炉。它只不过是在地上或岩石上挖出一个坑,风可以从鼓风器通过风嘴直接鼓入,碎矿石和木炭混装或分层装在烧红的炭火上,最高温度至少应达1150℃。这种炼炉没有出渣口,炉渣向下流到底部结成渣饼或渣底,有时则结成圆球,即渣球或渣粒。坯铁留在渣上面,在冶炼过程结束后,打
略谈中国冶金技术的发展历程
略谈中国古代冶金技术的发展历程 摘要:中国作为一个拥有着五千年历史的文明古国,又是一个以农业为本的国家,这也意味着中国的冶金技术会随着农业生产技术的发展而发展,下面这篇文章会从冶炼的金属的种类,冶炼火源的燃料来源以及冶炼技术等三方面来略谈中国古代冶金技术的发展历程。 摘要:中国古代冶金技术发展历程 关于中国冶金技术的发展的历史,是科学技术研究的重要部分,它直接关系到了生产工具的改进,也就意味着古代社会生产力的提高和发展。中国古代之所以能够比欧洲早一千年出现封建社会,其中一个很重要的原因,就是由于中国古代社会生产力很早得到了比较高度的发展,这和当时中国冶金技术的高度发展是密不可分的。中国最迟到春秋晚期已发明生铁冶铸技术,这项发明比欧洲要早一千九百多年,欧洲直到封建社会中期(14世纪)才推行这种技术。中国最迟在战国早期已创造铸铁柔化处理技术,已能把生铁铸件经过柔化处理变为可锻铸铁(即韧性铸铁),这又早于欧洲两千三四百年,欧洲要迟至封建社会末期(18世纪中叶)才应用这种技术。当时我国由于生铁冶铸技术的发明,铁的生产率大为提高;又由于铸铁柔化处理技术的创造,使得白口铁铸造的工具变为韧性铸铁,大大提高了工具的机械性能(就是增强了工具的使用寿命)。中国战国、秦、汉时期,生铁冶炼技术有较快的发展,铸造铁器技术又有了长足的进步,铸铁柔化处理技术也达到了先进水平,因而韧性铸铁的工具特别是农具得到了广泛使用,这样当然有助于农业生产的发展。至少到公元前一世纪西汉前后,中国人民就创造了生铁炒炼成熟铁或钢的技术,这项发明又比欧洲要早两千多年,欧洲要到封建社会末期(18世纪中叶)才创造“炒钢”技术。最迟在公元5——6世纪南北朝时代,我国人民又发明了“灌钢”冶炼法,这种以生铁水灌注熟铁的炼钢方法是中国人民独特的创造,这在世界钢铁冶炼技术发展史上是值得大书特书的。到唐宋时代,这种炒钢和灌钢技术以及锻造技术又有进一步发展。汉代开始冶铁开始使用煤炭做燃料,到了北宋时期,已经有了以煤做为燃料冶铁的明确记载。淬火技术在战国中期就得以运用。供风形式也由自然通风到人力皮囊鼓风再发展到了东汉初期南阳太守杜诗创造出的水利鼓风装置—水排。宋代又进一步发明了长方形的木风箱,进一步加大了供风力度,提高了冶炼温度,增强了冶炼的质量。 一、冶炼金属种类的发展与变化 金虽然在化学性质上比铜要更为稳定并且也更易被冶炼,但是中国的金矿储量比较少,所以中国最早冶炼的金属是铜,铜的化学性质比较稳定,并且易开采和冶炼,中国是世界上最早掌握黄铜冶炼技术的文明,姜寨遗址出土的黄铜片和黄铜环就是冶炼而成,距今6700年。中国的青铜冶炼掌握的也较早,目前我国最早的冶炼青铜器为甘肃马家窑遗址出土的青铜刀,距今也有5000年。比黄铜更为普遍使用的是青铜,青铜文化在世界各地区都有发展,青铜是加入了锡或铅的铜合金,在中国古代人们已经能够准确的掌握青铜的含锡铅比例。可根据铸造期望的不同,按比例加锡、铅。《周礼·考工记》里明确记载了制作不同的不同合金比例:六分其金而锡居一,谓之钟鼎齐(剂)。五分其金而锡居一,谓之斧斤齐(剂)。四分其金而锡居一,谓之戈戟齐(剂)。三分其金而锡居一,谓之大刃齐(剂)。五分其金而锡居二,谓之削杀矢(箭头)之齐(剂)。金锡半,谓之鉴燧(铜镜)之齐(剂)。青铜的化学性能稳定,耐腐蚀,可长期保存。此外,
钢铁冶炼技术的发展
钢铁冶炼技术的发展 我国古代冶铁术发展得很早。中国和埃及、巴比伦、印度都是最先进入铁时代的国家。中国最早在什么年代开始会炼铁尚无定论,但从考古发现知道,早在3300年前,人们就有意识地使用铁了。1972年,河北出土一把商代的铜钺,铜钺上有铁刃,已经全部锈成氧化铁。其年代在公元前14世纪前后,属殷墟文化早期。这说明当时的人们认识到了铁的部分功能,并且能够进行锻造加工。还有一些考古发现的那个年代的铁刃铜兵器。这些发现都表明,最迟在商朝中叶,我国人民已经掌握了铁的锻造工艺。从考古发掘的结果来看,我国最早人工冶炼的铁器约出现于公元前6世纪,即春秋末期。出土铁器中农具和手工业工具占绝大部分;铁器的质地既有锻成的块炼铁,也有铸造的生铁。人类冶炼铁矿石制作铁器,推测是在公元前1500~2000年间。这个时期的炼铁方法,是把铁矿石放在简单的火坑里,加上木炭燃烧加热升温,得到的温度在铁的液化点之下,产品铁块中含有渣,再把铁块中的渣用锻打的方式挤出,锻成块炼铁。这种由铁矿石直接得到产品的方法实际上就是直接炼铁法。为了得到液态的铁水,需要提高炉子的温度,想提高炉温就需要增大炉子高度,从而产生了现代高炉的雏形。炉子高了,炉内的料层对空气流通的阻力增大,因此必须强制向炉内鼓风,从而发展出了各种各样的鼓风方式。到了15世纪(意大利文艺复兴时代),强制送风的高炉(熔矿炉)在莱茵河上游出现。用这种方法得到了熔融状态的铁水。由于这种方法使用大量的木炭作为还原剂及燃料,造成了森林的枯竭,为此1709年前后英国人A.Darby开发出了用煤制造的焦碳代替木炭的高炉,这种还原方法一直持续至今。另外,继续增大鼓风效率,使得原始炼铁炉的高度继续增加,渐渐演变成为现代的高炉。现代的巨型高炉和最早形成的高炉相比,规模、生产率和装备条件上有天壤之别,但冶炼原理仍然基本相同。为了使铁能够锻造,需要把生铁中所含的碳去掉一部分或大部分,于是出现了当时的炼钢法—炒钢法。我国东汉时期就有了炒钢的文字记载,地下发掘出的实物也证明,至迟在东汉时炒钢就出现了。生铁中的碳被氧化后熔点升高,而温度升高炉内金属逐渐成为半熔的状态,取出锻打成坯,挤出其中的渣子。含有一些碳的就是钢,碳非常低的就是熟铁。由于很难控制金属中的碳,大多一直炒到底成为熟铁,炒钢法也称为炒熟铁法。炒钢法的出现标志着钢铁冶炼技术进入了一个新阶段—“二步法”诞生,也就是铁矿石在高炉中用焦炭还原并且渗碳成为生铁,生铁经过氧化脱碳成为熟铁或钢。欧洲产业革命迎来了钢的大生产时代,发明了几种钢的熔融精炼法。1856年发明酸性底吹转炉法(贝塞麦法)、1879年发明碱性底吹转炉法(托马斯法)、1856年发明平炉法(西门子-马丁法)、1899年发明电炉法(埃鲁法);从此进入了以铁水作为原料高效精炼钢水的大生产时代。
我国高炉喷煤技术的现状及发展趋势
邯钢1000m3高炉提高喷煤比的探索 刘伟,樊泽安,王飞,徐俊杰 (河北钢铁集团邯郸钢铁公司炼铁部,河北邯郸056015) 摘要:邯钢4#高炉(有效容积1000m3)经过不断探索,加强原燃料管理、高炉的操作和维护,使喷煤比逐月提高、焦比和综合焦比不断下降。喷煤比由2008年的130.6 kg/t提高到2009年6月的163.1 kg/t,焦比由361kg/t下降到了305kg/t,综合焦比由524kg/t下降到了500kg/t,取得了良好的经济效益。 关键词:高炉;喷煤比;探索 引言 邯钢4#高炉有效容积917m3,2007年、2008年虽然炉况长期稳定顺行,但由于燃料变化比较大,有时甚至一天就变换数次焦炭,各项指标未达到最好水平,平均日产2600t上下,一级品率70%,焦比361kg/t,煤比130kg/t,焦丁比16kg/t风温1100℃,平均[Si]0.61%。进入2009年以来,4#高炉以“低耗高产”举措应对当前市场挑战,进一步探索好的经济技术指标成效显著,通过监督改善原燃料质量、适时调整煤气流分布、降低入炉焦比、提高富氧、增加喷煤、高风温协调互补、适当提高炉渣碱度等措施,基本实现了全捣固焦冶炼的长期稳定顺行,并实施了低硅冶炼,取得了很好的经济技术指标。2009年4月以来,平均日产达到2700t以上,利用系数达到3.0,一级品率93.45%,焦比降到305kg/t,煤(全无烟煤)比达到160kg/t以上,中焦比达到18kg/t,焦丁比达到16kg/t,风温达到1135℃,平均[Si]达到0.43%以下。通过优化高炉操作技术经过不断实践和探索,在喷吹全无烟煤的情况下煤比达到160kg/t以上实属难得(见表1)。 表1 4高炉生产指标 利用系/t. (m-2. d-1) 煤 比 /kg.t-1 入 炉焦比 /kg.d-1 焦 丁比 /kg.d-1 中 焦比 /kg.d-1 风 温/℃ R 2 [ Si]/% 20 08 2.88 6 1 30.6 361 14 20 1 107 1 .15 .61 20 09.4 3.0 1 51.7 327 16 18 1 132 1 .13 .44 20 3.001308 17 18 110
炼铁高炉冶金技术的应用与发展
炼铁高炉冶金技术的应用与发展 改革开放以来,随着我国经济社会的高速发展,我国的冶金技术取得了巨大的进步,使得冶金炼铁效率得到了极大的提高,钢铁的生产质量也有了质的飞跃,有效的支撑了我国社会主义事业的发展,满足了经济社会发展的需要。 标签:炼铁高炉;冶金技术;应用;发展 前言 近年来,我国炼铁行业在经济快速发展的带动下,各方面都取得不错的进步,冶金技术在炼铁高炉中的普遍应用,更是明显的提高了经济效益,不仅促进了炼铁的发展,还促进了炼铁技术向节能环保方面的发展,在一定程度上提高了企业的竞争力,适应了经济市场的环境变化。因此,对炼铁高炉中的冶金技术有必要进行总结和进一步研究。 1 冶金技术及我国高炉炼铁的发展概况 从上世纪70年代末,我国全面引进先进的钢铁生产装备和技术开始,到现在发展了30多年,其技术日臻完善,提高了钢铁生产的效率。进入新世纪以来我国高炉炼铁利用系数呈现先升后降的趋势,显示出我国钢材业由供不应求逐渐转向供大于需的局面。并且根据有关数据显示,随着市场竞争和环保的需求,我国高炉炼铁的燃料也出现喷煤比高,焦比和燃料比降低的态势。而一些先进的高炉炼铁的燃料比已经低于490.00kg/t,焦比将近300kg/t,而高炉煤比则控制在一定的范围内,说明随着先进的冶金技术大规模的应用于高炉炼铁,我国高炉炼铁技术已经有了一个质的提升。 冶金技术主要是指从铁矿石等矿物中提取金属及其金属化合物,然后使用科学的加工方法将提取出的金属或其化合物制成具有一定性能的金属材料的过程和工艺。通常,常见的现代冶金技术主要有三种,即湿法冶金技术、电冶金技术和火法冶金技术。 首先,湿法冶金技术是指在溶液里进行冶金的过程,其温度一般要求不高。湿法冶金技术的步骤主要有:第一,浸出,是指使用能与矿石中金属反应的溶液,对矿石进行浸泡反应,金属通常以离子的形式呈现在溶液中,然后提取分离出来的金属。需要注意的是,在对比较复杂的矿石提取时,需要对矿石进行预处理,使金属成为混合物后在进行浸出提取。第二,净化,该过程主要对分离出来的含有金属的溶液进行处理,去除杂质的过程。第三,制备金属,对不含杂质的溶液进行电离、氧化还原反应等方法提取出所需要金属的过程。 其次,电冶金技术是指利用电能将所需金属提取出来的一种方法。电冶金技术可以分为电热和电化冶金两种,电热冶金主要是指将电能转化为热能来提取金属的过程,而电化冶金技术是指将溶液或熔体中的金属通过电化学反应进行提
北欧国家高炉炼铁技术发展趋势
北欧国家高炉炼铁技术发展趋势 1 技术发展 芬兰鲁基(Ruukki)公司的1号高炉于2010年大修,2号高炉将于2011年大修。另外,2011年烧结厂关闭后,这两座高炉将全部使用球团矿冶炼。 在钢铁联合企业,高炉炼铁是能耗最高的环节。为了保持竞争力,必须减少高炉能耗和还原剂的使用。例如,鲁基和瑞典欧维克(Ovako)公司开发了喷吹重油技术来降低焦比,而瑞典SSAB公司乌克瑟勒松德(Oxelosund)厂采用了氧煤喷枪。同时,由于使用了高品位的铁矿石,北欧高炉普遍实现了低渣量冶炼。 2 氧煤喷枪 喷吹燃料代替部分焦炭,可以大幅度提高高炉利用系数和能源效率。喷吹燃料的高效燃烧是根本性的,是高喷吹量的主要问题。为了改善煤的燃烧,瑞典国家冶金研究院于20世纪90年代初开发了氧煤喷枪。通过单风口喷吹试验,SSAB公司乌克瑟勒松德厂4号高炉全部更换为氧煤喷枪。氧煤枪是内管走煤粉、外管通旋流氧气的同轴套管式直管,氧气对枪管同时起冷却作用。单风口大量喷煤试验表明燃烧十分稳定。乌克瑟勒松德4号高炉换成氧煤枪后,喷煤量由35kg/t增加到喷煤系统最大能力135kg/t。SSAB报告显示,在没有炉顶加压和没有无料钟布料条件下,高炉操作稳定,燃料比(煤+焦)较低,约为465kg/t。另外,由于减少了炉尘量,电除尘效果得到改善,高炉透气性提高。 试验高炉 1997年瑞典矿业公司(LKAB)投资500万欧元,在位于吕勒奥市的瑞典国家冶金研究院建造了试验高炉,这也是北欧研发投入最大的项目。该试验高炉工作容积为9立方米,日产铁水35吨。虽然当时建造试验高炉的目的只是为了LKAB公司内部球团的研究开发,但经过5个炉役的试验,其潜能就得到了发挥。LKAB公司和客户以及其他厂商(包括北欧和欧盟国家)在此做了大量研发项目的试验,包括矿石、焦炭、新型无料钟炉顶、高喷油和富氧、杂料喷吹、测量技术等,至今共进行了25个炉役的试验,每次试验平均运行8个星期。 风口喷吹造渣剂 风口喷吹碱性造渣剂是很有意义的技术开发,工作人员对喷吹高炉炉尘和转炉渣进行了实验室研究和半工业试验。 工作人员在试验高炉和SSAB公司吕勒奥3号高炉上进行了高炉炉尘喷吹试验,主要目的是为了循环利用和回收炉尘中的碳等能源。尽管存在管道磨损问题,但试验表明了该技术的可行性和有效性。喷吹转炉渣时,沿高炉高度方向,从炉腹到风口,炉渣的化学性能得到改善,特别是在使用高铁球团的低渣量冶炼时更是如此。通过风口喷吹造渣剂可以消除极端炉渣成分不合理而对高炉操作产生的影响。煤粉中的酸性灰分在回旋区外围形成不透液的凝固层,阻碍风口高度的煤气流分布。 同样,在使用高铁球团时加入石灰石和其他碱性熔剂,由于炉渣碱度特别高,炉腹渣的黏度和熔点会升高,也影响气流分布。通过喷吹转炉渣和其他碱性物料,可调节高炉炉渣成分,消除风口酸性渣和炉腹碱性渣的极端状况。 在LKAB试验高炉上成功进行了转炉渣喷吹试验,吨铁喷吹量为36.9kg,取得了渣比从136kg/t降低到101kg/t、焦比下降11kg/t的良好效果。同时,铁水硅含量降低了28%,并保持稳定。此外,排碱量和铁水硫含量并未受到明显影响。研究表明,与单独喷煤相比,煤粉和转炉渣混合喷吹会使回旋区疏松、深度变长。影响大规模试验的因素是须将大量转炉渣磨细。 2 含铁原料有效利用 目前北欧国家炼铁所用的铁矿石绝大部分来自瑞典LKAB公司位于拉普兰地区(Lapland)的高品位磁铁矿,该矿区的大规模开采始于20世纪初期,球团矿生产始于1955
中国古代冶金技术的发展
中国古代冶金技术的发展 最早利用的金属,大约在距今5000年前,中国已进入了冶炼红铜的时期。最初是利用孔雀石类氧化铜矿石,将它与木炭混合加热还原,得到金属铜。冶铸青铜中国几乎在开始冶炼红铜的同时就出现了青铜,主要中国古代在铜、钢铁、金、银、锡、铅、锌、汞等金属的冶炼史上均居于世界的前列。红铜是中国先民是铜锡合金,其中往往含有铅和其他金属。由于其硬度比铜大而且坚韧,熔点也较低,容易铸造,所以得到了较快发展。最初冶炼青铜,将红铜和锡矿石、木炭一起合炼而制得的;后来才逐渐发展到先炼出锡、铅,然后再与铜合炼。 炼铁中国先民用铁是从陨铁开始的,中国开始冶铁的时间大约在春秋时期。由于那时已经有了丰富的冶铸青铜的经验,进步很快,生铁和“块炼铁”几乎同时出现。块炼铁冶炼温度低,夹杂物多,但含碳量低,接近于熟铁,熔点高,质地柔软,适于锻造器物;生铁的冶炼温度高,含硫、磷量较大,质地硬脆,但耐磨,适于铸造器物。中国古代的生铁先后发展出了四个品种,即白口铁、灰口铁、麻口铁和韧性铸铁。白口铁发展最早,其中的碳以碳化铁形态存在,质硬脆耐磨,适宜铸造犁铧之类。因其中硅含量高,促使碳石墨化,因此脆性减小,而其中的石墨片又具有润滑作用,所以这种生铁正适合铸造轴承材料。麻口铁介于白口铁和灰口铁之间。韧性铸铁是将白口铁加热,长期保温而得,碳以团絮状石墨析出,而基体相当于低碳或中碳钢,所以这种铸铁的出现,表明工匠已掌握了退火柔化处理技术。在战国时期,工匠
在锻打块炼铁的过程中,由于炭火中碳的渗入而炼成了最早的渗碳钢,并掌握了淬火工艺。在西汉后期又发明了以生铁为原料的炒钢技艺,并从而得到熟铁。大约在晋、南北朝时发明了将生铁和熟铁按一定比例配合冶锻的方法,以调节铁中的含碳量,而创造了“团钢”冶炼工艺。 那时冶铁已采用碱性熔剂这种工艺是利用金属铁将胆矾溶液中的铜离子置换出来,还原为金属铜,再熔炼成锭。炼银银虽有以游离状态或银金合金状态存在于自然界的,但很少,主要以硫化矿形式存在,并多与铅矿共生。这种银最初大概就是从冶炼到的铅中发现的。所以银的利用较黄金晚。天然黄金中总混有一些银,又常有人以银掺入黄金谋利,所以提纯黄金,使它与白银分离,在古代成为一门专门的技艺。中国曾先后利用黄矾-树脂法、矾盐法、硫黄法、硼砂法、矾硝法、矾硝盐法来分离金和银。炼汞在自然界中虽有游离态汞存在,但量很少,主要以硫化汞状态存在。战国时期,中国已用水银作外用药。同时中国发明了利用水银的鎏金术。这种技艺发展到西汉初年已达到极高的水平。方士们在密闭的设备中升炼水银,先后利用过石灰石、黄矾、赤铜、黑铅、铁和炭末来促进硫化汞的分解。南宋时期发明了蒸馏水银的工艺,设计了专用的装置。中国古代在铜、钢铁、金、银、锡、铅、锌、汞等金属的冶炼史上均居于世界的前列。冶金术的发明,金属之使用,极大地促进了生产力的提高和人类社会的发展,也极大地改善了人类自身的面貌。
现有主要炼铁工艺的优缺点和研发方向
现有主要炼铁工艺的优缺点和研发方向 摘要:当前,钢铁企业炼铁工艺中,热效率已经很高,工艺技术设备也已完善,大型化、长寿化的高炉炼铁工艺作为我国主要炼铁设备,将继续在炼铁领域占统治地位。在我国社会主义市场经济体制改革不断深入的背景下,钢铁企业要不断进行自主创新,提高炼铁工艺基础管理水平,积极引进或开发最新炼铁工艺,特别是节能减排技术,切实保证产品质量,促进企业经济效益和社会效益的提高。 关键词:炼铁工艺;优缺点;发展 一、钢铁企业炼铁工艺发展现状及问题 近几年随着我国市场经济的快速发展和科学技术的不断进步,钢铁企业高炉炼铁工艺不断优化,具有热效率高、技术完善、设备使用寿命长等优点,同时我国炼铁技术取得了一定的成就,比如提高转炉炉龄,提高转炉作业率,强化供氧技术等等;特别是“十二五”规划以来,我国钢铁企业重视炼铁工艺优化,重点进行节能减排技术的开发,比如滚筒法连续处理工艺等,大力引进先进设备,生铁产量逐年提高,说明我国节能减排工作取得了一定的进展。但是,目前我国钢铁企业炼铁工艺中还是存在一定的问题: 一是我国炼铁工艺的能耗、废弃物回收利用和环境治理等与国家炼铁水平还是有很大的差距。 二是炼铁工艺管理不够规范,比如说辅料、铁合金等的分类管理。 三是当下炼铁中的二氧化碳的排放量高于国际水平,产品质量没达到国际水平。 四是炼铁工艺设计缺乏创新,一定程度上影响了炼铁工艺的使用。 二、高炉炼铁工艺 在当前,主要的钢铁生产都是以高炉流程生产的.高炉流程是现代钢铁生产流程的龙头。因此,就对高炉炼铁工艺的优缺点进行分析: 高炉反应器的优点是热效率高、技术完善,设备已大型化、长寿化,单座高炉年产铁最高可达400万吨左右,一代炉役的产铁量可达5000万吨以上,可以说,没有现代化的大型高炉就没有现代化的钢铁工业大生产。在今后相当长时期内,高炉流程在我国将继续是主要产铁设备,继续占统治地位.我国已完全掌握现代先进高炉技术,单位建设投资和生产成本相对较低. 但目前人们对高炉工艺流程有种种不满: 一是高炉必须要用较多焦炭,而炼焦煤越来越少,焦炭越来越贵;
中国炼铁技术发展评述
中国炼铁技术发展评述 王维兴 近年来,中国炼铁处于高速发展阶段。2007年全国生铁产量达到4.6944亿t,占世界总产量的49.74%,比上年度增长15.19%,其增幅低于钢产量的同期增幅。2007年,全国重点钢铁企业(指71家)产铁3.69亿t,比上年增长13.74%,其他企业产铁1.20亿t,增长19.60%。地方企业铁产量增速高于大中型钢铁企业。2008年前8月全国产铁3.2912亿t,比上年度增长6.50%,降低了发展势头。近2个月发展势头有较大的减缓,市场变得疲软:高炉炼铁技术经济指标出现全面下滑,这是近年来所没过有的,对钢铁企业节能减排产生较大的负面影响,各级领导应引起高度重视,及时采取有效措施,否则难以完成国家提出的节能减排任务。要认识到,炼铁系统的能耗占企业总能耗的70%。 预计,2008年我国钢产量将达到5.2亿t,生铁产量将达到4.9亿t。今年,我国炼铁生产能力将超过6亿t,尚有约6000万t的生产能力属于淘汰之列(主要是300m3以下容积的小高炉)。近两个月,因金融危机和市场变化,钢材销售不畅,一些企业出现亏损,进行停产压产,生产形势发展出现大逆转。全国高炉炼铁形势发生了巨大变化,产量下降,生产指标进行调整,进入理性发展阶段(前一阶段为粗放式经营)。 1 中国高炉结构 上述情况表明,地方炼铁厂的发展势头仍处于高于全国大中型钢铁企业的发展。马钢和太钢建成4063m3高炉,使我国拥有7座4000m3级高炉。目前在建的有4座4000m3级高炉(本钢、鞍钢、太钢、莱钢),沙钢、京唐公司在建5800m3级高炉和5500m3级高炉。一批大于2500m3级高炉在建设,大大地推动了我国高炉大型化进程,但一批小于1000m3级高炉也在建设。 我国有1300多座高炉,大于1000m3容积的高炉约有150座,300~1000m3高炉约500多座,小于300m3的约有600多座。全国约有980多家炼铁企业。这说明,我国炼铁产业集中度低,高炉平均炉容偏小,是处于不同层次、不同结构、多种生产技术水平共同发展阶段,且处于高速发展阶段。预计我国生铁产量的顶峰为6亿t以上。淘汰落后进展缓慢,难度较大。近两个月,一些企业停了部分
炼铁技术第一章到第三章作业参考答案
第一章到第三章作业答案 1、试述高炉炼铁的生产过程,画出现代高炉炼铁生产工艺流程图; 答高炉炼铁的生产过程的描述: 冶炼过程中,炉料(矿石、熔剂、焦炭)按照确定的比例通过装料设备分批地从炉顶装入炉内,高温热风从下部风口鼓入,与焦炭反应生成高温还原性煤气;炉料在下降过程中被加热、还原、熔化、造渣,发生一系列物理化学变化,最后生成液态渣、铁聚集于炉缸,周期地从高炉排出。煤气流上升过程中,温度不断降低,成分不断变化,最后形成高炉煤气从炉顶排出。 现代高炉炼铁生产工艺流程图 2、根据物料存在形态的不同,高炉内可划分为哪六个区(带)? 答根据物料存在形态的不同,可将高炉划分为六个区(带),从上到下依次是块状带、软熔带、滴落带、燃烧带、中心焦堆、渣铁盛聚带。 3、解释名词: 干焦比:指每冶炼一吨生铁所消耗的干焦量,kg焦/t铁; 有效容积利用系数:指每立方米高炉有效容积在一昼夜生产的生铁吨数,t/(m3.d) 焦负荷:每批炉料中铁、锰矿石的总质量与焦炭重量之比,或单位重量的焦炭上所负载的矿石重量。是用以评估燃料利用水平,调节炉料分布的重要参数。 有效熔剂性:按照炉渣碱度要求,扣除熔剂自身所含的酸性氧化物所消耗的碱性氧化物后,剩余的碱性氧化物含量(%)。 4、高炉常用的天然铁矿石有哪几种?评价铁矿石质量的标准有哪些? 答:天然铁矿石按其主要矿物分为磁铁矿、赤铁矿、褐铁矿、菱铁矿; 评价铁矿石质量的标准有铁矿石的成分(矿石品位、脉石成分、有害杂质和有益元素的含量)、粒度和强度、还原性、化学成分稳定性以及铁矿石的软熔性等。 5、焦炭在高炉生产中起什么作用,高炉冶炼过程对焦炭质量提出哪些要求? 答焦炭在高炉生产中的作用:作发热剂、作还原剂、做料柱的骨架。 高炉冶炼对焦炭质量要求:(1)含碳量高,灰分低。(2)有害杂质少。(3)成分稳定,挥发分
我国钢铁工业主要技术发展方向_王国栋(上)
世界金属导报/2017年/12月/5日/第F01版 我国钢铁工业主要技术发展方向 王国栋 编者按:本报今年11月21日第44期刊登了对中国工程院院士王国栋的专访。王院士在访谈中就钢铁工业技术发展方向、存在的问题、解决问题的途径等进行了系统阐述。本文是对上文中提出的钢铁工业应当主要把握的技术发展方向的进一步深化,详细介绍了11个钢铁技术发展方向。 钢铁工业作为最主要的原材料工业,最根本任务就是以最低的资源能源消耗,以最低的环境生态负荷,以最高的效率和劳动生产率向社会提供足够数量且质量优良的高性能钢铁产品,满足社会发展、国家安全、人民生活的需求。要完成这样一个任务,我认为,钢铁工业应当把握以下几个主要技术发展方向: 1流程创新绿色发展 1.1钢铁生产全流程一体化控制 钢铁工业是典型的流程工业,最终产品质量的优劣,是由全流程的各个环节共同确定的。要想获得稳定、优良的材料质量,必须针对每一个工艺环节,进行全流程、一体化控制。控制要素包括温度(含冷却速度)、变形条件、成分、夹杂物(洁净度、种类)控制水平、排放、能源消耗等等; 1)减量化、低成本、低排放的钢铁材料与生产工艺设计 谈钢铁材料开发,离不开材料开发的四面体关系。材料的“成分、工艺、组织、性能”这四个要素构成的四面体关系告诉我们,材料的工艺和成分决定材料的组织与性能。过去通常的办法是:如果材料的性能达不到要求,可以增添某一种或某几种合金元素,或者采用后续的热处理工艺进行调整。这两种办法都是“增量化”的办法,或者消耗昂贵的合金元素,或者消耗能源与资源。 但是,材料设计的绿色化新理念要求我们做到“减量化、低成本、高性能”。在钢铁材料开发过程中,我们要把这个绿色化新理念全面融入四面体关系中。要做到:①资源节约型的成分设计,尽量减少合金元素含量,或使用廉价元素代替昂贵元素;②要采用节省资源和能源、减少排放、环境友好的减量化加工工艺方法;③从市场中发现新的组织和性能需求,逆向倒推,促进工艺技术创新和新型材料的创制;④量大面广产品的升级换代和高端产品的规模化生产,都要遵循绿色化理念。由此可见,关键工艺技术的创新与开发,在新材料的开发中占据了越来越重要的地位,材料和产品开发特别要注重关键共性工艺技术的创新。 我们现在使用的钢铁材料和它们的生产工艺,是过去几十年来不断开发出来的,由于开发当时技术水平和支撑条件的限制,在节省资源和能源方面以及减少排放和污染方面考虑不周,甚至未予考虑,急切需要改进、甚至颠覆的地方很多,技术创新、提升水平的空间很大。今天,环境、生态问题已经迫在眉睫,资源、能源问题更是刻不容缓,过去几十年发展起来的技术必须进行脱胎换骨的改造与提升;另一方面,技术进步和研究条件已经发生了翻天覆地的变化,为对这些产品及其生产过程进行改造甚至重造,提供了极好的支撑条件。我们已经有条件进行这样一场革命! 2)实行“精料方针”和“源头治理” 钢铁生产过程最重要的任务就是除去钢中的杂质,生产具有必要洁净度控制的和规定化学成分的钢铁产品。现有的冶炼过程虽然对作为原料的铁矿石和作为燃料的煤炭进行了粗略的处理,仍然有大量的有害元素残留于钢中,然后在后续的炼铁、炼钢、精炼过程中一点点除去。针对这种情况,行业里提出了“精料方针”,期望在入炉冶炼之前,尽量提高原料的洁净度。但是,碍于种种条件的限制,仍然是“泥沙俱下”,大量的有害元素进入到炉中,在随后的冶炼过程中,不得不建设大量的巨型设备,采用各种复杂的工艺,一点点地去除钢中的各种有害杂质,极大地增加了冶炼的负担和
流态化还原炼铁技术
流态化还原炼铁技术 流态化(fluidization)是一种由于流体向上流过固体颗粒堆积的床层而使得 固体颗粒具有一般流体性质的物理现象,是现代多相相际接触的工程技术。使用流态化技术的流化床反应器因具有相际接触面积大,温度、浓度均匀,传热传质条件好,运行效率高等优点而应用于现代工业生产。 高炉炼铁技术在矿产资源受限和环保压力增大等形势下,将面临着前所未有的挑战。铁矿石对外依存度过高、铁矿石粒度越来越小和焦炭资源枯竭等状况,迫使人们加快步伐探索改进或替代高炉工艺的非高炉型炼铁工艺。以气固流态化还原技术为代表的非高炉炼铁工艺逐步受到重视。 新工艺的建立和发展需要理论研究作为支撑。目前国内对于流态化还原炼铁 过程中的气固两相流规律的认识还不够深入,特别是对不同属性铁矿粉的流态化特性、不同操作条件下的流态化还原特性,以及反应器结构对流态化还原过程的影响等相关研究还不够充分,基于流态化还原技术的新工艺要成熟应用于大规模工业生产还有明显距离。 发展流态化技术须重视基础研究 流态化技术可以把固体散料悬浮于运动的流体之中,使颗粒与颗粒之间脱离接触,从而消除颗粒间的内摩擦现象,使固体颗粒具有一般流体的特性,以期得到良好的物理化学条件。流态化技术很早就被引入冶金行业,成为非高炉炼铁技术气基还原流程中的一类重要工艺。流态化技术在直接还原炼铁过程中主要有铁矿粉磁化焙烧、粉铁矿预热和低度预还原、生产直接还原铁的冶金功能。 我国从上世纪50年代后期开始流态化炼铁技术的研究。1973年~1982年,为 了开发攀枝花资源,我国进行了3次流态化还原综合回收钒钛铁的试验研究。中国科学院结合资源特点对贫铁矿、多金属共生矿的综合利用,开展了流态化还原过程和设备的研究;钢铁研究总院于2004年提出低温快速预还原炼铁方法(FROL TS),并
炼铁技术发展
**炼铁发展综述 摘要:**公司自2005年以来,推行稳本固基、苦练内功、转变思维、审时度势,随机应变等一系列管理理念,以提高高炉装备水平为保障,通过狠抓“精料”工作、积极探索炼铁新技术、开创性的发展炼铁新理论,以及计算机辅助管理,使炼铁生产获得了高水平发展,高炉主要技术经济指标显著改善。 关键词:炼铁管理理念技术进步精整炉料高炉装备高炉操作制度 The Development of Iron-making of**Steel Abstract: Since 2005, the implementation of ** Steel iron company is stabilization of the solid base, Obtain, change thinking,, deal with the situation and act according to circumstances and a series of management concepts in order to improve the level of equipment for the protection of blast furnace, by implementing the "concentrate materials " work , and actively explore new iron-making technology, pioneering the development of new iron-making theory, as well as computer-aided management, which makes it reach a high level development of iron production , main technical and economic indicators of blast furnace improve significantly. Key words:iron-making,management concepts,technological improvement,finishing furnace, blast furnace equipment ,blast furnace operating system 近几年,**炼铁的快速发展,引起了业界同行的关注,特别是08年金融危机来临后,**炼铁凭借其铁前低成本优势,使得**钢铁能率先走出困境,成为行业的少有赢利企业,短短几年里,高炉经济技术指标由同行垫底走向处于领先水
2016年我国炼铁技术经济指标述评
2016年我国炼铁技术经济指标述评 1 2016年炼铁生产情况 2016年,我国生铁产量为70073.66万吨,比上年增加0.74%。中钢协会员企业生铁产量为61827.57万吨,比上年下降0.03%;其他单位生铁产量8246.03万吨,比上年增加6.90%。生铁价格的上升和企业利润的增加,促使一些已停产的高炉恢复了生产,导致生铁产量增长。2016年,中钢协会员单位生铁产量占全国生铁产量的88.23%,比上年下降2.13%。我国生铁产量占世界生铁产量60.44 %。 2016年,中钢协会员单位有121家(2015年统计的单位是71家,2016年增加一批小炼铁企业及生产铸造铁的企业),其中有65家单位生铁产量比上年增长,有51家单位生铁产量下降;唐山凯恒钢铁、粤裕丰、陕西略钢和华菱锡钢特钢等企业停产。 据统计,2016年我国有16家企业生铁产量超过1000万吨,24家企业生铁产量在500-1000万吨,48家企业产量在100-500万吨;产量低于100万吨的企业有5家,其中3家是生产铸造铁的企业。 2016年,河北省生铁产量为18176.77万吨,比上年下降0.52%,居全国首位;江苏省为7300.12万吨,比上年增加0.10%,居第二位;辽宁为5411.86万吨,比上年增加1.73%,居第四位;山东省为4884.97万吨,比上年增加7.95%,居第四位;安徽省2130.37万吨,与上年降低2.74%,居第五位。 2 炼铁技术经济指标下滑 2016年下半年以后,煤炭、焦炭价格连续上升,造成高炉炼铁用焦炭质量下降,引起高炉生产不稳定,再加上管理不善,导致2016年中钢协会员单位炼铁技术经济指标下滑。与上年相比,2016年焦比上升4.35kg/t,煤比下降0.92kg/t,燃料比上升3.86kg/ t,热风温度下降27.11℃,休风率上升0.60个百分点,详见表1。
高炉炼铁工艺流程(经典之作)
本次将高炉炼铁工艺流程分为以下几部分: 一、高炉炼铁工艺流程详解 二、高炉炼铁原理 三、高炉冶炼主要工艺设备简介 四、高炉炼铁用的原料 附:高炉炉本体主要组成部分介绍以及高炉操作知识 工艺设备相见文库文档: 一、高炉炼铁工艺流程详解 高炉炼铁工艺流程详图如下图所示:
炼铁过程实质上是将铁从其自然形态——矿石等含铁化合物中还原出来的过程。 炼铁方法主要有高炉法、直
接还原法、熔融还原法等,其原理是矿石在特定的气氛中(还原物质CO、H2、C;适宜温度等)通过物化反应获取还原后的生铁。生铁除了少部分用于铸造外,绝大部分是作为炼钢原料。 高炉炼铁是现代炼铁的主要方法,钢铁生产中的重要环节。这种方法是由古代竖炉炼铁发展、改进而成的。尽管世界各国研究发展了很多新的炼铁法,但由于高炉炼铁技术经济指标良好,工艺简单,生产量大,劳动生产率高,能耗低,这种方法生产的铁仍占世界铁总产量的95%以上。 炼铁工艺是是将含铁原料(烧结矿、球团矿或铁矿)、燃料(焦炭、煤粉等)及其它辅助原料(石灰石、白云石、锰矿等)按一定比例自高炉炉顶装入高炉,并由热风炉在高炉下部沿炉周的风口向高炉内鼓入热风助焦炭燃烧(有的高炉也喷吹煤粉、重油、天然气等辅助燃料),在高温下焦炭中的碳同鼓入空气中的氧燃烧生成的一氧化碳和氢气。原料、燃料随着炉内熔炼等过程的进行而下降,在炉料下降和上升的煤气相遇,先后发生传热、还原、熔化、脱炭作用而生成生铁,铁矿石原料中的杂质与加入炉内的熔剂相结合而成渣,炉底铁水间断地放出装入铁水罐,送往炼钢厂。同时产生高炉煤气,炉渣两种副产品,高炉渣铁主要矿石中不还原的杂质和石灰石等熔剂结合生成,自渣口排出后,经水淬处理后全部作为水泥生产原料;产生的煤气从炉顶导出,经除尘后,作为热风炉、加热炉、焦炉、锅炉等的燃料。炼铁工艺流程和主要排污节点见上图。
国内外高炉炼铁技术的发展 (2)
国内外高炉炼铁技术的发展现状和趋势 邹忠平、项钟庸、赵瑞海、罗云文 1 前言 21进入世纪以来,钢铁工业受到金融危机的冲击,世界环境有了很大的变化。随着我国钢铁产能的增加(图1),炼铁原料质量下降,资源和能源价格上扬,二氧化碳排放等问题,炼铁作为钢铁工业集中消耗能源、资源的部门首当其冲。 在德国,钢铁企业已经承诺将在2012年前比1990年降低CO 2排放量22%;在京都议定书中日本计划钢铁厂排放的CO 2量比1990年减少10.5 %。我国生铁产量已经超过世界产量的一半,必然会对我国高炉炼铁提出相应的要求。 在新世纪对炼铁技术的展望,离不开资源、能源和经济等形势的变化,这些主要课题。21世纪也是高炉炼铁“变革的世纪”,期望在新时期钢铁产业能够进入资源、能源和环境的和谐,这是确立炼铁业持续发展的重要关键,也必须从这个理念和观点展开高炉炼铁技术的研究和开发。 5296252119544955417854100576415743060393650397213178107867799460392670 97411052910721115111185212532131031489317074213662518540416471424706773787491745978527498745281097884808982098297830784278677861751 29833040010000 200003000040000500006000070000 80000900001000001994 199619982000 20022004200620082010 年份 生铁产量/万t 世界 中国日本 图1 世界、我国和日本的生铁产量 我国许多高炉已经感到当前形势的变化,并采取了相应的措施。对高炉炼铁技术发展的方向有了新的认识,为振兴炼铁工业打下了基础。为此很有必要综观世界高炉炼铁技术发展及今后的方向十分必要。 我国高炉在大型化、高效化、低排放过程中,对高炉设计、生产出现了一系
直接还原炼铁技术的最新发展doc
直接还原炼铁技术的最新发展 作者: 胡俊鸽,吴美庆,毛艳丽, 钢铁研究 摘要撰写人TsingHua 出版日期:2006年4月30日 直接还原铁可以作为电炉、高炉和转炉的炉料。DRI代替优质废钢更适合于生产对氮和有害元素有严格要求的钢种,如用于石油套管、钢丝绳、电缆线等的钢种。近年,由于钢铁市场升温,废钢资源呈现世界性紧缺。2003年,我国钢铁企业生产回收的废钢铁和非生产回收废钢铁合计为1502万t;而全年炼钢消耗废钢与辅助炼钢消耗废钢之和为4 750万t。显然,国内的废钢缺口很大。未来几年,随着国际市场废钢资源的短缺,世界对废钢的需求量将不断增长。当今,在废钢资源全球性紧缺、国际市场价格频频上扬的情况下,对于我国来说,寻找废钢替代品已迫在眉捷。直接还原铁和热压块铁是最好的废钢替代品。1直接还原炼铁技术发展状况2003年世界直接还原铁总量为4900万t。比2002年增加了10%,不同工艺所生产直接还原铁所占份额如下:Midrex 为64.6%,HyLⅢ为18.4%,HyLⅠ为1.3%,Finmet为5.2%,其他气基为0.4%,煤基为10.2%。直接还原工艺根据还原剂不同可分为气基和煤基。气基直接还原工艺中,竖炉Midrex、Arex(Midrex改进型)和HyLⅢ工艺、反应罐法Hy LⅠ、流化床法Fior和Finmet工艺,都已获得了工业应用,流化床法Fior、Cir cored和碳化铁法在工业上应用不久就停产了。煤基直接还原法中,获得工业应用的有回转窑法和转底炉法(Inmet-co、Fastmet、Sidcomet、DRylron),新开发的多层转底炉Primus工艺已于2003年2月投产。 1.1气基直接还原工艺气基还原工艺可分为使用球团矿或者块矿的工艺和使用铁矿粉的工艺。各种气基直接还原铁工艺发展状况如表1所示。表1各种气基直接还原铁工艺发展状况工艺装备工艺特点所用原料目前状况研究发展F ior(委内瑞拉)4个流化床反应器生产能耗高于竖炉Midrex和HyLⅢ铁矿粉Side tur厂于1976年投产,1985年开始,年产量达到35万t~41万t。由于市场原因于2000年停产。由委内瑞拉和奥钢联进一步发展成FinmetFinmet(奥钢联和委内瑞拉)4个流化床反应器铁矿靠重力从较高反应器流向较低反应器直接使用矿粉,是Fior 的进一步改进,比Fior能耗低、人员需求少。与Fior相比,其还原气体中H2含量少,CO没被氧化去。在Finmet工艺中,矿粉在流化床第一段被还原过程产生的热气体预热,其较高的CO含量可以提高热平衡,并使HBI的w(C)达3%。铁矿
金属冶炼技术的发展
金属冶炼技术的发展 目前,已发现86种金属元素。除金、银外,绝大多数金属元素都以化合态(氧化物、硫化物、砷化物、碳酸盐、硅酸盐、硫酸盐等)形式存在。要获得各种金属及其合金材料,首先要将金属元素从矿物中提取出来,再对粗炼金属产品进行精炼、提纯或合金化处理。 将金属从化合态转变为游离态(单质)的过程称为金属冶炼。金属冶炼的原理是氧化还原反应。不同金属活泼性不同,越活泼的金属,越难将其从化合物中还原为单质,越需要更高的反应温度和更强的还原手段。 (1)热还原法(干法冶金) 用碳、一氧化碳、氢气、活泼金属等作为还原剂与金属氧化物在高温下发生氧化还原反应可以将还原出的金属单质以液体形式分离出来。早在3000 多年前,我国就能够以孔雀石[主要成分是碱式碳酸铜CuCO3·Cu(OH)2或Cu2(OH)2CO3]为原料冶炼铜。孔雀石与点燃的木炭接触,被分解为氧化铜,并进一步被还原为金属铜: CuCO3·Cu(OH)2=加热2CuO+CO2↑+H2O C+2CuO=加热2Cu+CO2↑ 铁、锰、钨的冶炼和高炉炼铁也都属于热还原法: 4Al+ 3MnO2=高温2Al2O3+3Mn Fe2O3+3CO=高温2Fe+3CO2 活泼的金属钾也可以在特殊条件下,通过热还原法制得: Na+ KCl=高温真空K + NaCl 一些不活泼金属的氧化物,在高温下就可以分解还原为单质: 2HgO(s) =加热2Hg(l)+O2(g) 从矿石中利用热还原法冶炼的金属通常含有较多的杂质,需要精炼。例如,从铁矿石中冶炼得到的生铁含有碳、磷、硫、硅等杂质,含碳量可达2%以上。用氧气等氧化剂氧化除去过多的碳和杂质,制备含有不同含量杂质的不同型号的钢。 (2)置换法(湿法冶金) 在酸、碱、盐的水溶液中通过置换反应,利用溶剂萃取或离子交换从矿石中提取所需金属组分可以从低品位、难熔化或微粉状的矿石中提炼金属。我国古代湿法冶铜技术是先用硫酸与含氧化铜的矿石反应,得到含硫酸铜的溶液,再用铁置换出铜。 CuO+H2SO4=CuSO4(aq)+ H2O CuSO4(aq)+ Fe=Cu+ FeSO4(aq) 难于分离的金属如镍-钻、锆-铪、钽-铌及稀土金属也可以利用湿法冶金的技术(溶剂萃取或离子交换)进行分离。 (3)电解法 将熔融的金属盐通过电解可以制备金属单质。电解法相对成本较高,易造成环境污染,但提纯效果好、适用于多种金属。不能用还原法、置换法冶炼的活泼金属(如钠、钙、钾、镁等)和需要提纯精炼的金属(如精炼铝、铜等)均可通过电解法获得。 2NaCl(熔融)=电解2Na(s)+ Cl2(g) MgCl2(熔融)=电解Mg(s) +Cl2(g) 2Al2O3(熔融)=电解4Al(s)+ 3O2(g) 1973年,Aluminium Company of America的Alcoa分公司创造了氯化铝电解制铝法,在难以导电的氯化铝中加入某些物质组成纯氯化物的电解质体系,如NaCl-KCl-AlCl3系、NaCl-KCl-LiCl-AlCl3系以及氟化物NaCl-CaCl2-CaF2-AlC13混合体系等,可以增强熔融电解液的导电性,在双极性电极多室电解槽可以电解制得金属铝。(氯化铝中铝和氯之间的化学