PCB CAM工艺 Genesis2000 化学沉金+金手指流程
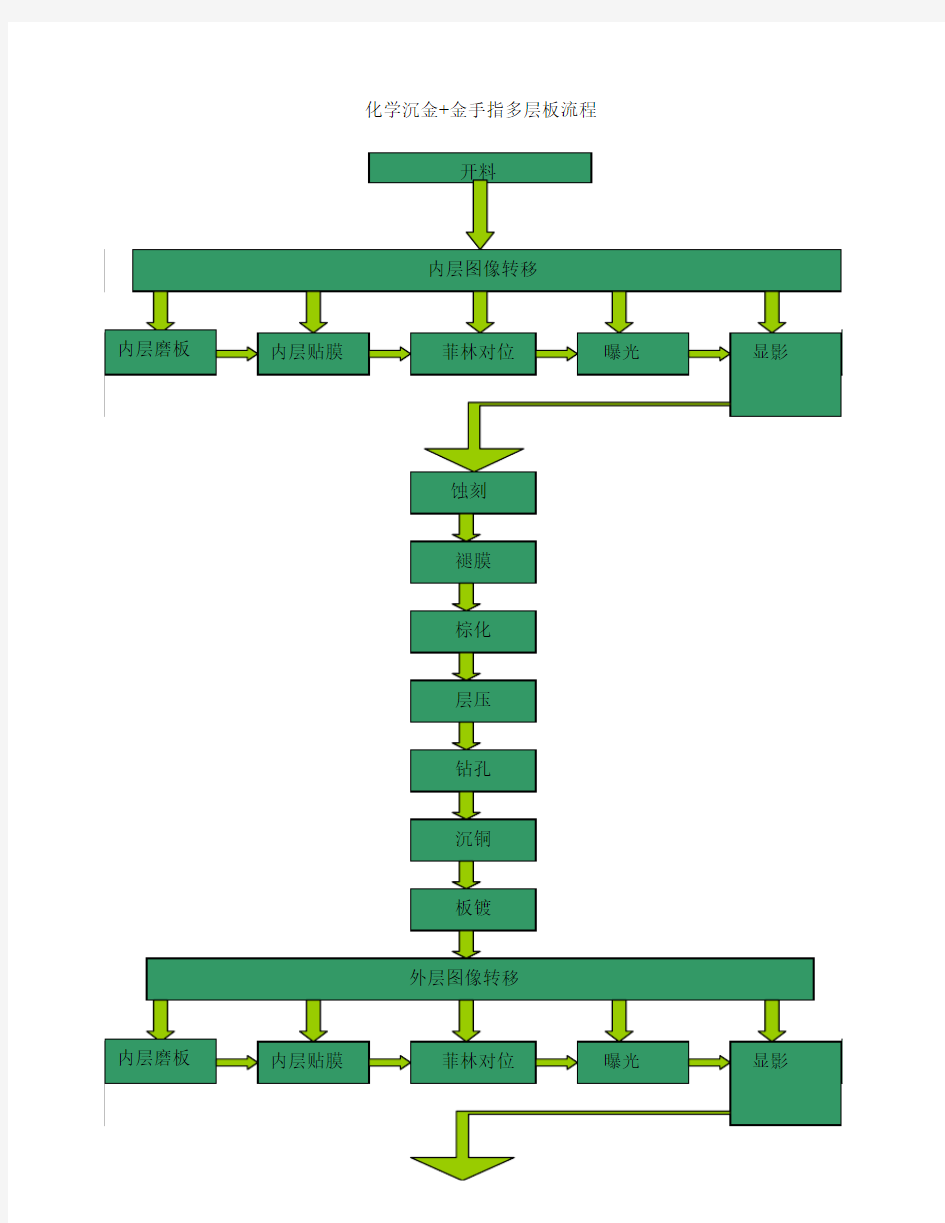
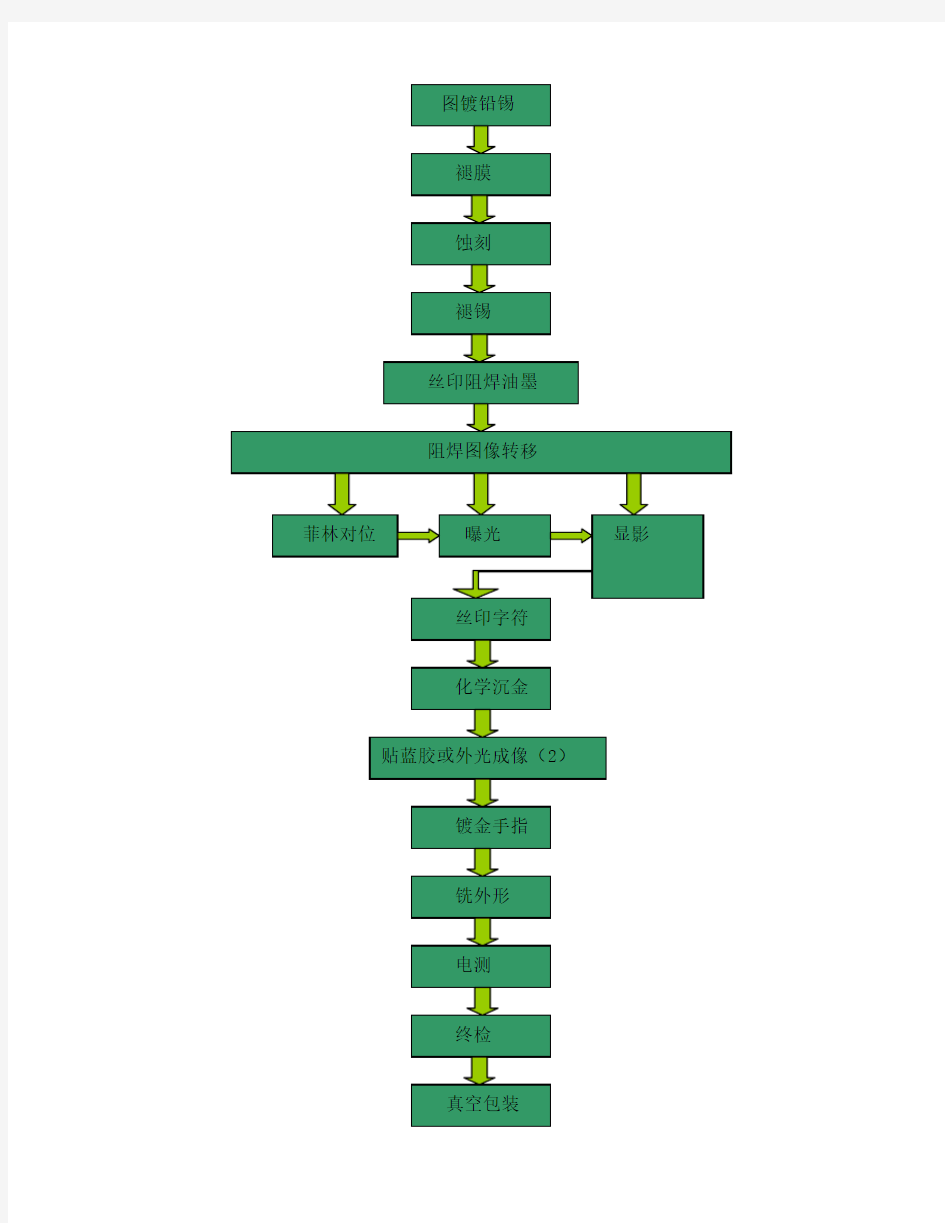
化学沉金+金手指多层板流程
废水处理工艺
线路板废水 一、线路板废水的分类 1、磨板废水 磨板废水来源于磨板机的清洗工序,主要含铜粉、火山灰等。 2、铜氨络合废水 铜氨络合废水来源于碱性蚀刻的清洗工序,废水中主要污染物为铜离子(以络合态存在)、氨氮等。 3、化学沉铜废水(属于废液,不单独处理) 化学沉铜废水来源于化学沉铜的清洗工序,废水中主要污染物为铜离子(以络合态存在)、有机物等。 4、化学镀镍废水 典型的化学镀镍工艺以次磷酸盐为还原剂,废水中主要污染物为镍离子(以络合态存在)、磷酸盐(包括次磷酸盐、亚磷酸盐)及有机物。 5、含氰废水 含氰废水来源于电镀金、化学沉金、化学沉银的清洗工序,废水中主要污染物为氰化物、重金属离子(以络合态存在)等。 6、油墨废水 油墨废水来源于显影、脱膜工序,含有大量感光膜、抗焊膜渣等成分,COD 较高。 7、有机废水 除以上所列废水外,其它CODcr浓度高于150mg/l的废水均应纳入有机废水处理系统,主要包括除油、脱脂和网版清洗等工序产生的废水,废水中主要污染物为有机物。 8、综合废水 除以上所列废水外,其它各类废水统称为综合废水,主要污染物为酸碱、重金属离子、悬浮物等。 9、废液 线路板废液中含有高浓度的酸、碱、重金属等,线路板废液应委托有资质的危险废物处理单位进行处理处置或综合利用。
二、各项废水的处理工艺设计 1、磨板废水 ⑴工艺选择 由于磨板废水中污染浓度相对较低、污染物种类少,经回收铜粉和简单沉淀处理后可直接回用于磨板清洗工序,也可将沉淀后磨板废水排入回用水处理系统作深度处理后回用。 ⑵工艺流程图 磨板废水→铜粉回收机→调节池→沉淀池→定期回收沉淀铜粉 ↓ 回用至磨板清洗工序或排入回用水处理系统 图1 磨板废水工艺流程图 2、铜氨络合废水 ⑴工艺选择 铜氨络合废水一般先采用硫化物进行破络和混凝沉淀,然后排入有机废水处理系统的pH回调池或经折点加氯除氨后直接排放。 ⑵化学反应机理 铜氨络合废水破络反应的化学方程式如下: [Cu(NH 3) 4 ]2+ +S2-→CuS+4NH 3 ↑ ⑶工艺流程图 碱+硫化物 FeSO 4 PAM 污泥脱水系统 pH↓ORP ↓↓↑铜氨络合废水→调节池→破络池→快混池→慢混池→沉淀池 ?↓ 排放←折点加氯←pH回调池有机废水 图2 铜氨络合废水工艺流程图 ⑷主要工艺控制参数 pH调整池内控制pH值10-10.5。 ORP值控制100-150mV。
PCB沉锡工艺研究
PCB沉锡工艺研究 PCB沉锡工艺是为有利于SMT与芯片封装而特别设计的在铜面上以化学方式沉积锡金属镀层,是取代Pb-Sn合金镀层制程的一种绿色环保新工艺,已广泛使用与电子产品(如线路板、电子器件)与五金件、装饰品等表面处理。 一、沉锡工艺特点 1.在155℃下烘烤4小时(即相当于存放一年),或经8天的高温高湿试验(45℃、相对湿度93%),或经三次回流焊后仍具有优良的可焊性; 2.沉锡层光滑、平整、致密,比电镀锡难形成铜锡金属互化物,无锡须; 3.沉锡层厚度可达0.8-1.5μm,可耐多次无铅焊冲击; 4.溶液稳定,工艺简单,可通过分析补充而连续使用,无需换缸; 5.既适于垂直工艺也适用于水平工艺; 6.沉锡成本远低于沉镍金,与热风整平相当; 7.对于喷锡易短路的高密度板有明显的技术优势,适用于细线高密度IC封装的硬板和柔性板; 8.适用于表面贴装(SMT)或压合(Press-fit)安装工艺; 9.无铅无氟,对环境无污染,免费回收废液。 二、沉锡工艺流程顺序: 三、Final Surface Cleaner表面除油: 1.开缸成分: M401酸性除油剂……….100ml/L 浓H2SO4…………………50ml/L DI水……………………..其余 作用:除去电路板表面油污,氧化层和手指印。此除油剂与目前市面上常见的所有阻焊油墨都兼容。 2.操作参数: 温度:30-40℃,最佳值:35℃ 分析频率:除油剂,每天一次 控制:除油剂80-120ml/L,最佳值:100ml/L 铜含量:小于1.5g/L
补充:M401,增加1%含量需补充10ml/L 过滤:20μ滤芯连续过滤,换缸时换滤芯。 寿命:铜含量超过1.5g/L或每升处理量达到500呎。 四、Microetch微蚀: 1.开缸成分: Na2S2O4……………….120g/L H2SO4…………………40ml/L DI水………………….其余 程序:①向缸中注入85%的DI水; ②加入计算好的化学纯H2SO4,待冷却至室温; ③加入计算好的Na2S2O4,搅拌至全溶解; ④补DI水至标准位置。 2.操作参数: 温度:室温即可 分析频率:H2S04,每班一次 铜含量,每天一次 微蚀率,每天一次 控制:铜含量少于50g/L 微蚀率:30-50μ,最佳值:40μ 补充:Na2S2O4,每补加10g/L,增加1%的含量 H2SO4,每补加4ml/L,增加1%的含量 寿命:铜含量超过50g/L时稀释至15g/L,并补充Na2S2O4 和H2SO4 五、Predip预浸: 1.开缸:10% M901预浸液;其余:DI水 用途:在沉锡前湿润微蚀出的铜面,此预浸液对任何阻焊油墨都没有攻击性; 2.操作参数: 温度:室温 分析频率:酸当量,每天一次 铜含量:每周一次 补充:酸当量,每添加100ml/LM901,增加0.1当量 液位:以DI水补充 过滤:20μ滤芯连续过滤 寿命:与沉锡缸同时更换 3.废水处理:与后处理废液中和后过滤出固体物质。 六、Chemical Tin沉锡: 1.设备:预浸和化学锡缸均适用; 缸体: PP或PVC缸均可; 摆动:PCB架在缸内摆动,避免气体搅拌; 过滤:10μ滤芯连续过滤; 通风:建议15MPM通风量; 加热器:钛氟龙或石英加热器; 注意:不能有钢铁材料在缸内 2.开缸:100% Sn9O2 沉锡液开缸,此沉锡液对任何阻焊油墨都没有攻击性; 3.操作参数:
化学沉铜工艺.
化学沉铜工艺 化学沉铜工艺 随着电子工业需要更可靠、性能更佳、更为节约的电镀添加剂产品,J-KEM 国际公司为未来的电子产品开发了一种新型化学沉铜工艺。通过引入最新一代的化学技术到整个的工艺过程中,是针对新的终端用户的可靠性需求而专门设计的。 从一开始,你就会发现新型J-KEM 整孔剂与传统的整孔剂相比迈进了一大步。普通的整孔剂的选择性不高并且在内层形成光屏蔽(轻微势垒)从而只能生成弱Cu-Cu键。J-KEM 整孔剂的化学活性和前者是完全不同的,它具有极高的效率,可使之形成100%Cu-Cu结合力和高的环氧树脂和玻璃纤维吸收。 在整个J-KEM工艺过程中,J-KEM有机钯活化剂是一个关键性的改进。通过创新的使用有机添加剂,新型钯活化剂配方与传统钯活化剂相比显示出绝对优越的催化性能。 因此,即使工作液中钯的浓度极低,如30ppm,大多数高的纵横比材料,以薄铜沉积后,进行背光测试仍可得到极佳的效果。 J-KEM化学沉铜技术操作稳定、易于控制,沉积层结晶细致、结构致密。沉积显示出侧面增长性能,可使铜在孔洞中很好覆盖。 J-KEM化学沉铜镀液可以提高铜沉积层和孔壁以及线路板表面的结合能力。 J-KEM化学沉铜镀液使用独特的有机钯活化剂配制而成,既可用于垂直电镀,又可用于水平电镀。 J-KEM碱性催化体系是一个独特的优化工艺过程,为柔性印刷电路板最大程度的降低了碱度和高温,并且结合了整孔体系高吸收性能、有机钯活化剂特性以及化学沉铜自催化性能等几个特点,J-KEM化学沉铜液是用于P.I.结合的尤为突出的工艺过程。 工艺特征:
? 在所有基体表面的深孔壁均可很好的覆盖; ? 对于HARB’s、基层板和盲孔具有优越的性能;? 极为而突出的孔壁结合力; ? 新一代钯活化剂可在极低浓度下(30 ppm)使工作;? 适合于垂直和水平镀; ? J-KEM化学沉铜是柔性印刷电路板的最佳工艺;? 经济节约。 化学沉铜工艺流程 J-KEM 7756**为可选工艺。
喷锡与沉锡异同点及化学沉锡常见问题分析
喷锡与沉锡异同点及化学沉锡常见问题分析 PCB沉锡工艺是为有利于SMT与芯片封装而特别设计的在铜面上以化学方式沉积锡金属镀层,是取代Pb-Sn合金镀层制程的一种绿色环保新工艺,已广泛应用于电子产品、五金件、装饰品等。印刷线路板有两个较为常用的工艺:喷锡和沉锡。喷锡,主要是将PCB板直接侵入到熔融状态的锡浆里面,在经过热风整平后,在PCB铜面会形成一层致密的锡层,厚度一般为1um-40um。沉锡,主要是利用置换反应在PCB板面形成一层极薄的锡层,锡层厚度大约在在0.8um-1.2um之间,沉锡工艺更普遍应用在线路板表面处理工艺当中。 化学沉锡常见技术问题分析 化学沉锡是PCB沉锡工艺的一种,应用较为普遍,其工作原理是通过改变铜离子的化学电位使镀液中的亚锡离子发生化学置换反应,其实质是电化学反应。被还原的锡金属沉积在铜基材的表面上形成锡镀层,且其浸锡镀层上吸附的金属络合物对锡离子还原为金属锡起催化作用,以使锡离子继续还原成锡,其化学反应方程式为2Cu+4TU+Sn2→2Cu+(TU)2+Sn。 化学沉锡层的厚度大约在在1um-40um之间,表面结构较为致密,硬度较大,不容易刮花;喷锡在生产过程中只有纯锡,所以表面容易清洗,正常温度下可以保存一年,并且在焊接的过程中不易出现表面变色的问题;沉锡,锡厚大约在在0.8um-1.2um之间,表面结构较为松散,硬度小,容易造成表面刮伤;沉锡是经过复杂的化学反应,药剂较多,所以不容易清洗,表面容易残留药水,导致在焊接中易出现异色问题,保存时间较短,正常温度下可以保存三个月,如果时间久会出现变色。 化学沉锡板的主要缺陷表现为锡面发暗、锡面污染导致的可焊性不良问题,经过大量数据分析及现场调查,基本确定造成原因主要由以下几个方面,首先,生产过程药液拖带消耗:因锡槽药水具有粘度较大特性,致使生产带出量较大,从而导致锡槽药液消耗量大。同时,由于锡槽槽液大量带入硫脲洗槽,造成硫脲洗槽铜含量上升快,影响生产板清洗效果,易
电路板生产工艺及废水处理.
电路板工艺及废水处理1004 一、电路板的生产工艺: 印刷电路板的生产,根据其特点可以分为单面板、双面板两种工艺,多层板比双面板多了内层制作和压合工序。 可以不涉及通孔电镀,而在单面板生产厂生产。 上述工序前有*的,在生产时先要进行表面清洗,此工序包括机械磨刷和酸性化学清 洗,俗称为磨板。 2、双面电路板的工艺流程(省略检查和部分小工序)
3多层电路板的工艺流程 多层电路板(包括HDI)大部分工艺流程与双面板相同,仅增加内层生产与压合部分。其流程如下: 二、电路板生产的废水处理: 1、电路板废水概况: 印刷电路板生产工艺复杂,产生的废水的种类多,成分复杂,其中对生态环境和人体健康危害较大的主要污染物是重金属污染物。铜是印刷电路板废水中常见的重金属,且浓度高,形态多。去除印刷电路板废水中铜的传统处理方法存在的主要问题是:处理后出水达不到国家排放标准、产生的污泥量大、会造成二次污染、处理成本高等。做2007年中国印制电路行业协会的调查中,还在认为处理得不够完善。但随着金属铜的价格上涨,低含量的铜也受到重视,能够稳定的达到排放1.0PPM的要求。 广东省质量技术监督局已在2009年5月发布了DB44/T 622-2009“印制电路板行业废水治理工程技术规范”,为不断发展的广东电路板行业的废水处理工程做出了规定。
电路板行业中高浓度的废液(如蚀刻液、剥锡液),现在技术上完全可以循环使用。主要的排放污染物是以铜为代表的重金属、有机物(COD)。 1、铜(重金属)污染的产生和处理方法 电路板是由覆铜板加工而成,加工过程中还要反复清洗铜面,电镀铜又是通孔导电的唯一方式,所以铜发生在电路板生产的所有工序中,最困难处理的是在化学镀铜液中含有EDTA等络合剂,需要单独预先破坏络合剂,才能使铜离子在后续的处理中沉淀除去。 各种重金属在用碱调节PH8-9时,大部分除去,再加入适量的硫化钠或重金属离子捕集剂,经混合、反应、沉淀与过滤,出水中各种重金属离子均可以达到国家一级排放标准。 2、显影、退膜浓废液(COD): 在感光线路油墨、感光防焊油墨的显影,感光线路油墨的除去时,产生含有大量有机物的浓乳化液,此种废液必须单独处理:先酸化和加破乳剂使其分离,再用高级氧化法将有机物减少到达标。 上述技术已经成熟,有多家环保工程公司可以设计、安装和运作。但分开收集不同种类的废液并进行预处理,是排污能够达标的关键。 江门市兴维经贸有限公司:邹卫 2010-4-29
(完整版)PCB化学镀铜工艺流程解读(一)
PCB化学镀铜工艺流程解读(一) 化学镀铜(Eletcroless Plating Copper)通常也叫沉铜或孔化(PTH)是一种自身催化性氧化还原反应。首先用活化剂处理,使绝缘基材表面吸附上一层活性的粒子通常用的是金属钯粒子(钯是一种十分昂贵的金属,价格高且一直在上升,为降低成本现在国外有实用胶体铜工艺在运行),铜离子首先在这些活性的金属钯粒子上被还原,而这些被还原的金属铜晶核本身又成为铜离子的催化层,使铜的还原反应继续在这些新的铜晶核表面上进行。化学镀铜在我们PCB制造业中得到了广泛的应用,目前最多的是用化学镀铜进行PCB的孔金属化。PCB孔金属化工艺流程如下: 钻孔→磨板去毛刺→上板→整孔清洁处理→双水洗→微蚀化学粗化→双水洗→预浸处理→胶体钯活化处理→双水洗→解胶处理(加速)→双水洗→沉铜→双水洗→下板→上板→浸酸→一次铜→水洗→下板→烘干 一、镀前处理 1.去毛刺 钻孔后的覆铜泊板,其孔口部位不可避免的产生一些小的毛刺,这些毛刺如不去除将会影响金属化孔的质量。最简单去毛刺的方法是用200~400号水砂纸将钻孔后的铜箔表面磨光。机械化的去毛刺方法是采用去毛刺机。去毛刺机的磨辊是采用含有碳化硅磨料的尼龙刷或毡。一般的去毛刺机在去除毛刺时,在顺着板面移动方向有部分毛刺倒向孔口内壁,改进型的磨板机,具有双向转动带摆动尼龙刷辊,消除了除了这种弊病。 2.整孔清洁处理 对多层PCB有整孔要求,目的是除去钻污及孔微蚀处理。以前多用浓硫酸除钻污,而现在多用碱性高锰酸钾处理法,随后清洁调整处理。 孔金属化时,化学镀铜反应是在孔壁和整个铜箔表面上同时发生的。如果某些部位不清洁,就会影响化学镀铜层和印制导线铜箔间的结合强度,所以在化学镀铜前必须进行基体的清洁处理。最常用的清洗液及操作条件列于表如下:
镀铜的工艺过程.
/yiw紫气东来 化学镀铜化还原反应。
体钯活化液过早聚沉。因此,在活化处理前要先在含有Sn2+的酸性溶液中进行预浸处理1~2min,取出后直接浸入胶体钯活化液中进行活化处理。配制时应首先将盐酸与水相混合,然后再加入SnCl2?2H2O ,搅拌溶解,这样可防止SnCl2水解。 酸基胶体钯预浸液配方: 氯化亚锡(SnCl2.2H2O)70~100g/L 盐酸37%(体积)200-300ml/L 盐基胶体钯预浸液配方: SnCl2.2H2O30g/L HCl30ml/l NaCl200g/l O ║ H2N-C-NH250g/l b.活化处理-在室温条件下处理3~5min,在处理过程中应不断移动覆铜箔板,使活化液在孔内流动,以便在孔壁上形成均匀的催化层。 c.解胶处理-活化处理后,在基材表面吸附着以钯粒子为核心,在钯核的周围,具有碱式锡酸盐的胶体化合物。在化学镀铜前,应将碱式锡酸盐去除,使活性的钯晶核充分暴露出来,从而使钯晶核具有非常强而均匀的活性。经过解胶处理再进行化学镀铜,不但提高了胶体钯的活性,而且也显著提高化学镀铜层与基材间的结合强度。常用的解胶处理液是5%的氢氧化钠水溶液或1%氟硼酸水溶液。解胶处理在室温条件下处理 1~2min,水洗后进行化学镀铜。 d.胶体铜活化液简介: 明胶2g/l CuSO4.5H2O20g/l DMAB(二甲胺基硼烷)5g/l 水合肼10 g/l 钯20ppm PH7.0 配制过程:首先分别将明胶和硫酸铜用温水(40度C)溶解后将明胶加入至硫酸铜的溶液中,用25%H2SO4将PH值调至2..5当温度为45度C 时,将溶解后DMAB在搅拌条件下缓慢加入上述的混合溶液中,并加入去离子稀释至1升,保温40~45度C,并搅拌至反应开始(约5~10分钟)溶液的颜色由蓝再变成绿色。放置24小时颜色变成红黑色后加入水合肼,
化学沉铜
化学沉铜 化学铜被广泛应用于有通孔的印制线路板的生产加工中,其主要目的在于通过一系列化学处理方法在非导电基材上沉积一层铜,继而通过后续的电镀方法加厚使之达到设计的特定厚度,一般情况下是1mil(25.4um)或者更厚一些,有时甚至直接通过化学方法来沉积到整个线路铜厚度的。化学铜工艺是通过一系列必需的步骤而最终完成化学铜的沉积,这其中每一个步骤对整个工艺流程来讲都是很重要。 本章节的目的并不是详述线路线路板的制作过程,而是特别强调指出线路板生产制作中有关化学铜沉积方面的一些要点。至于对那些想要了解线路板生产加工的读者,建议参阅其它文章包括本章后的所列举一部分的参考书目。 镀通孔(金属化孔)的概念至少包涵以下两种含义之一或二者兼有: 1.形成元件导体线路的一部分; 2.形成层间互连线路或印制线路; 一般线路板都是在非导体的复合基材(环氧树脂-玻璃纤维布基材,酚醛纸基板,聚酯玻纤板等)上通过蚀刻(在覆铜箔的基材上)或化学镀电镀(在覆铜箔基材或物铜箔基材上)的方法生产加工而成的。 PI聚亚酰胺树脂基材:用于柔性板(FPC)制作,适合于高温要求; 酚醛纸基板:可以冲压加工,NEMA级,常见如:FR-2,XXX-PC; 环氧纸基板:较酚醛纸板机械性能更好,NEMA级,常见如:CEM-1,FR-3; 环氧树脂玻纤板:内以玻璃纤维布作增强材料,具有极佳的机械性能,NEMA级,常见如:FR-4,FR-5,G-10,G-11; 无纺玻纤聚酯基板:适合于某些特殊用途,NEMA级,常见如:FR-6; 化学铜/沉铜 非导电基材上的孔在完成金属化后可以达到层间互连或装配中更好的焊锡性或二者兼而有之。非导电基材的内部可能会有内层线路---在非导电基材层压(压合)前已经蚀刻出线路,这种过程加工的板子又称多层板(MLB)。在多层板中,金属化孔不仅起着连接两个外层线路的作用,同时也起着内层间互联的作用,加入设计成穿过非导电基材的孔的话(当时尚无埋盲孔的概念)。 现在生擦和许多线路板在制程特点上都采用层压基板下料,也就是说,非导体基材的外面是压合上去一定厚度电解法制作的铜箔。铜箔的厚度是用每平方英尺的铜箔重量(盎司)来表示的,这种表示方法转化为厚度即为表13.1所示: 表13.1基材铜箔常见厚度对照: OZ/ft2 铜箔厚度 0.5 0.7mil(17.5um) 0.25 0.35mil(8.75um) 1 1.4mil(35um) 2 2.8mil(70um) 非导体基材有不同厚度因为要求不同,可能会要求很强的刚性也可能要求很薄的以致柔性也很好的基材. 在加成法生产加工中,使用的是无铜箔基材.这样化学通的作用不仅是孔金属化,而且同时也是为后续电镀创造一个表面基材导体化电镀基底,或者甚至完全靠化学铜沉积至特定厚度并形成整个表面的线路图形. 现在好多板子是采用不同基材生产加工的,无论是双面板还是多层线路板.对不同基材类型的前处理加工也稍有不同,值得加以注意和讨论. 在讨论化学铜槽本身的原则方法对于
含铬废水处理
含铬废水处理技术 关键词:含铬废水来源危害处理方法 一、电镀废水的来源: 1、清洗:为了防止电镀过程中对下一种溶液的污染,避免溶液的成分或Ph值等的变化,保证镀件的使用性能,避免在制件上生成难以除去的物质,所以要进行清洗。而清洗是电镀废水的最主要来源。 2、镀液过滤,为了保证镀液性能及镀层质量,必须保证镀液的清洁,所以要进行镀液的过滤。 3、在电镀操作过程中,常带有镀液及处理液的带出,由于挂具设计不合理、装挂方式不考究、操作时不在槽子上方停留,增加镀液的带出量。 4、溶液的废弃:在电镀生产过程中所采用的许多溶液都有一定的寿命,要对溶液进行更换。 二、电镀废水的危害: 酸碱废水:排水江河危害水中微生物的生活,而影响水质,排入农田会破坏土壤的团粒结构影响土壤肥力及透力、蓄水性,影响农作物的生长,鱼类、牲畜等食用了酸碱费水,对其肉质、乳汁将产生影响,危害人体健康,渗入地下后,影响工业生产。 含氰废水:氢氰酸和氰化物能通过皮肤、肺、胃,特别是从粘膜呼吸进入体内,与三价铁离子络合和含铁呼吸酶结合,引起组织的呼吸麻痹,造成窒息死亡。 含铬废水:含铬废水可以有致癌的作用,对人体的皮肤有危害,对呼吸系统有损害作用。 三、处理方法: 化学法处理含铬废水: 1、沉淀法:是使溶液中含有的离子状物质变为新的固体物而分离出去的方法。 2、氧化还原法:在化学反应中若发生了电子的转移,即原子或离子的氧化数发生了变化则为氧化还原法。 工艺流程图: 化学还原法处理含铬废水有槽内处理、间歇处理、连续处理和气浮处理4种方式。这里以间歇处理为主。 间歇处理工艺流程:
反应池容积一般按2~4h的废水量设计,反应池设有空气搅拌或水力、机械搅拌,投药方式采用干投,反应池设有两格,交替使用。 化学还原法其它工艺: 化学法综合处理流程:
铝材废水处理方法整理
铝材生产及废水处理 1铝制品生产工艺流程 抛光 铝制品→铝板→裁板分条→冲压喷砂→氧化→镐光/批花/车纹/镭雕→清洁检验拉丝 1.1阳极氧化工艺流程 铝工件→上挂具→脱脂→水洗→碱蚀→水洗→出光→水洗→阳极氧化→水洗→去离子水洗→染色或电解着色→水洗→去离子水洗→封闭→水洗→下挂具 2铝制品生产废水来源 成型铝材的脱脂、碱蚀、酸洗、氧化、封孔及着色等工序产生的大量清洗废水和少量废液。 2.1酸性废水 1)脱脂、酸蚀水洗 主要含氢氧化钠、少量油脂,呈酸性 2)中和水洗 主要含硫酸,呈酸性 3)阳极氧化水洗 主要含有硫酸和铝离子,呈酸性 4)电泳水洗 电泳涂漆工序:纯水洗——热水洗——纯水洗——电泳——纯水洗——纯水洗——滴干——烘干 主要含盐和Al3+,呈碱性 5)除油 主要含硫酸、少量油脂,呈酸性 2.2碱性废水 1)碱蚀水洗 主要含AlO2-,呈碱性 2)模具碱洗 主要含Al3+呈碱性 2.3含锡含镍含氟废水 1)着色水洗 主要含有Sn2+、Ni2+,呈弱酸性 2)封孔水洗 主要含Ni2+、F-
1)钝化 主要含六价铬,呈酸性 2.5其他废水 1)热水洗 含少量Ni2+、F- 2)离子交换树脂再生 主要含盐酸、碱 3)酸、碱雾处理系统 主要含酸碱洗液 车间地面冲洗 主要含SS呈中性 4)铬酸雾处理系统 主要是酸气洗液,呈酸性 3铝材工业废水治理 铝材工业废水一般采用中和调节及混凝沉淀法。 调节池→反应池→絮凝沉淀池→污泥处理(板框压滤机) 目前主要使用的方法有三类: 1)化学法:中和沉淀法、硫化物沉淀法、铁氧体沉淀法、化学还原法、电 化学还原法; 2)物理化学法:混凝、气浮、吸附、膜分离; 3)生物法:生物絮凝、生物化学法、植物生态修复。 3.1含氟工业废水 3.1.1钙盐沉淀法 铝材生产含氟废水,一般采用钙盐沉淀法,生成CaF2沉淀。 (为使生成的沉淀快速絮凝沉淀,可在废水中单独或并用添加无机盐絮凝剂三氯化铁、聚合氯化铁、聚合硫酸铁等或高分子絮凝剂如聚丙烯酰胺。) 3.1.2改进技术 钙盐联合使用镁盐、铝盐、磷酸盐后,除氟效果增加,形成了新的更难溶解的含氟化合物。
沉铜工序作业指导书
沉铜工序作业指导书 目的 建立详细的作业规范,籍以稳定品质,提升生产效率,并作为设备保养、员工操作的依据,此文件同时也是本岗位新员工培训之教材。 适用范围 本作业规范适用于本公司电镀班沉铜工序。 职责 工艺部职责:负责沉铜线全面的工艺技术管理和工艺过程的控制,工艺及生产问题的解决,员工的培训,保证生产过程的顺利进行; 生产计划部职责: 负责生产组织与管理,员工的培训与培养,工艺过程和设备的日常维护和保养,产品产量和质量的保障; 品质部职责:负责对工艺过程、设备的维护和保养以及工序产品质量进行监控; 机修班职责:生产设备的管理、维护和维修; 电镀班:负责组织员工按本作业指导书进行操作及对工艺与设备进行日常维护和保养. 作业内容 工艺流程 4.1.1双面板沉铜流程(行车用1#程序) 磨板→上料→除油(清洁整孔)→溢流水洗→溢流水洗→微蚀→水洗→酸洗→水洗→预浸→活化→水洗→水洗→加速→水洗→沉铜→水洗→转板电加厚铜 4.1.2多层板沉铜流程(行车用2#程序) 磨板→上料→膨胀→溢流水洗→除胶渣→回收水洗→溢流水洗→溢流水洗→中和→溢流水洗→溢流水洗→接双面板流程 工艺流程说明 4.2.1磨板:清洁板面氧化、污渍、残胶等使板面粗化,增加结合力。如有刮伤、残胶等 缺陷应先用细砂纸打磨后再过磨板机。 咬蚀树脂,以除去钻孔产生的碎屑污物。4.2.2膨胀:使环氧树脂软化膨松,便于KMnO 4 4.2.3除胶渣:在高温强碱的环境下,利用KMnO 的强氧化性咬蚀膨松软化的环氧树脂。 4 、MnO42-等;4.2.4中和:用来还原多层板带出的高锰酸根,并完全除去孔内残留的MnO 2 4.2.5除油:清洁孔壁,调整孔壁基材表面的静电荷,提高孔壁对胶体钯的吸附能力。
沉锡工艺工作和问题处理WI
汕头超声印制板公司工作指示 CHINA CIRCUIT TECHNOlOGY (SHANTOU) CORPORATION WORK INSTRUCTION 标题:沉锡工艺工作与问题处理 TITlE:WORK INSTRUCTION FOR TECHNICS WORK TASK AND PROMBLEM TREATMENT 文件编号:WI-Y1-ME-A 版本:0 D O C U M E N T N O.:VERSION NO.: 生效日期:页数:E F F E C T I V E D A T E: PAGES: 编写:日期: DRAFTED BY:DATE: 审核:日期: AUDITED BY:DATE: 批准:日期:APPROVED BY:DATE:
工作指示修改表
1.目的 使新工艺人员了解沉锡的工艺工作要点及问题的处理 2.适用范围 沉锡工艺人员 3. 注意内容 3.1. 工艺控制注意事项: 1.锡缸加药顺序及方法:首先添加基本剂LP,然后添加基本剂2000,循环20min后添加锡溶液C,循环10min后才能添加添加剂。 2.锡缸要特别提防含铁的物质进入,以免造成药水的报废; 3.当药水中铜离子浓度较高时,用铜离子处理器进行冷却过滤,除掉铜离子,以免造成品质问题及药水报废; 4.更换锡缸棉芯时由于气体未排尽使药水变得浑浊时,须及时将过滤桶中的气体排走,以免造成药水报废;
3.3沉锡添加药水配制发红的调查和完善 甲磺酸与Sn2+可以络合,有稳定Sn2+的作用; 硫脲与Ag+有强的络合能力; 当SF-C加入没有混合均匀即加入添加剂,即Sn2+和Ag+ 都没有被充分的络合情况下( Sn2+为还原剂和Ag+为氧化 剂),导致局部发生如下反应: 2Ag++Sn2+=2Ag↓+Sn4+ 生成单质银沉淀。 采取的完善措施 延长加药间隔时间。 安排专人配药,全部白天配制 培训员工树立正确操作意识,增强节约观念
喷锡、熔锡、滚锡、沉锡、银及化学镍金制程术语手册
喷锡、熔锡、滚锡、沉锡、银及化学镍金制程术语手册 1、Blue Plaque 蓝纹 熔锡或喷锡的光亮表面,在高温湿气中一段时间后,常会形成一薄层淡蓝色的钝化层,这是一种锡的氧化物层,称为Blue Plaque。 2、Copper Mirror Test 铜镜试验 是一种对助焊剂(Flux)腐蚀性所进行鉴别的试验。可将液态助焊剂滴在一种特殊的铜镜上(在玻璃上以真空蒸着法涂布500A厚的单面薄铜膜而成),或将锡膏涂上,使其中所含的助焊剂也能与薄铜面接触。再将此试样放置24 小时,以观察其铜膜是否受到腐蚀,或蚀透的情形( 见IPC-TM-650 之2.3.32节所述)。此法也可测知其它化学品的腐蚀性如何。 3、Flux 助焊剂 是一种在高温下,具有活性的化学品,能将被焊物体表面的氧化物或污化物予以清除,使熔融的焊锡能与洁净的底金属结合而完成焊接。Flux原来的希腊文是Flow(流动)的意思。早期是在矿石进行冶金当成"助熔剂",促使熔点降低而达到容易流动的目的。 4、Fused Coating 熔锡层 指板面的镀锡铅层,经过高温熔融固化后,会与底层铜面产生"接口合金共化物"层(IMC),而具有更好的焊锡性,以便接纳后续零件脚的焊接。这种早期所盛行有利于焊锡性所处理的板子,俗称为熔锡板。 5、Fusing Fluid助熔液 当"熔锡板"在其红外线重熔(IR Reflow)前,须先用"助熔液"进行助熔处理,此动作类似"助焊处理",故一般非正式的说法也称为助焊剂(Flux)前处理。事实上"助焊"作用是将铜面氧化物进行清除,而完成焊接式的沾锡,是一种清洁作用。而上述红外线重熔中的"助熔"作用,却是将红外线受光区与阴影区的温差,藉传热液体予以均匀化,两者功能并不相同。 6、Fusing 熔合 是指将各种金属以高温熔融混合,再固化成为合金的方法。在电路板制程中特指锡铅镀层的熔合成为焊锡合金,谓之Fusing制程。这种熔锡法是早期(1975年以前)PCB业界所盛行加强焊接的表面施工法,俗称炸油(Oil Fusing )。此法可将镀层中的有机物逐出,而使焊锡成为光泽结实的金属体,且又可与底铜形成IM C而有助于下游的组装焊接。 7、Hot Air Levelling 喷锡 是将印过绿漆半成品的板子浸在熔锡中,使其孔壁及裸铜焊垫上沾满焊锡,接着立即自锡池中提出,再以高压的热风自两侧用力将孔中的填锡吹出,但仍使孔壁及板面都能沾上一层有助于焊接的焊锡层,此动制程称为"喷锡",大陆业界则直译为"热风整平"。由于传统式垂直喷锡常会造成每个直立焊垫下缘存有"锡垂" (Solder Sag)现象,非常不利于表面黏装的平稳性,甚至会引发无脚的电阻器或电容器,在两端焊点力量的不平衡下,造成焊接时瞬间浮离的墓碑效应(Tombstoning),增加焊后修理的烦恼。新式的"水平喷锡"法,其锡面则甚为平坦,已可避免此种现象。 8、Intermatallic Compound(IMC) 接口合金共化物 当两种金属之表面紧密地相接时,其接口间的两种金属原子,会出现相互迁移(Migration) 的活动,进而出现一种具有固定组成之"合金式"的化合物;例如铜与锡之间在高温下快速生成的Cu6Sn5(Eta Phase),与
沉锡PCB贴装后锡面发黑分析及改善
沉锡PCB贴装后锡面发黑原因分析及改善 1、前言 近年来,随着印制线路板(Printed circuit boar d,以下简称PCB)的无铅化的推行,化学沉锡(Immersion Tmatchin)具有成本较低、储存时间长、可焊性良好的优点而备受欢迎。化学沉锡是通过置换反应在铜表面沉积一层厚度约为1μm左右的锡层,其表面颜色为无光泽的淡白色,但由于其表面结构较为疏松、硬度小,易造成划伤、氧化、药水残留等缺陷。另外,在回流焊处理后,锡面发黄、发黑等异色问题不但影响印制板的美观,且对其可焊性、耐腐蚀性能等均有不同程度的影响,文章通过一例锡面发黑异色导致可焊性不良的案例,从失效分析的角度出发,探究了锡面发黑的原因和机理,为业内同行提供参考。 2、锡面发黑失效分析 2.1 案例背景 沉锡表面处理的印制板在经过回流焊贴装过程后,锡面才由正常的淡白色,转变为发黑异色现象,所以在PCB板的生产制程中难以对此进行有效的拦截,当产品流到客户端进行SMT贴装之后,才出现相应的品质问题,这会给PCB生产厂商造成客诉等不良影响,甚至会造成大量的经济损失。
以下是一例沉锡表面发黑的失效分析案例,该化学沉锡表面处理的PCB在出货前锡面颜色为正常的淡白色,但在客户端经过回流后,其焊盘表面出现上锡不良和锡面发黑的现象,如下图1所示: 图1 异色不良样品与正常样品锡面外观 a-1.上锡不良焊盘(50X);a-2.上锡不良焊盘(100X); b-1.发黑PCBA外观图;b-2.正常沉锡表面颜色。 由上图1所示,不良PCBA锡面发黑与正常沉锡表面所呈现的淡白色明显不一致,且焊接面有退润湿现象,现通过失效分析手段来排查可焊性不良的原因,并探究锡面发黑的机理。 2.2 失效原因排查
化学镀铜沉铜工艺流程介绍
化学镀铜/沉铜工艺流程介绍 2008-1-29 来源: 中国有色网 化学镀铜(Eletcroless Plating Copper)通常也叫沉铜或孔化(PTH)是一种自身催化性氧化还原反应。首先用活化剂处理,使绝缘基材表面吸附上一层活性的粒子通常用的是金属钯粒子(钯是一种十分昂贵的金属,价格高且一直在上升,为降低成本现在国外有实用胶体铜工艺在运行),铜离子首先在这些活性的金属钯粒子上被还原,而这些被还原的金属铜晶核本身又成为铜离子的催化层,使铜的还原反应继续在这些新的铜晶核表面上进行。化学镀铜在我们PCB制造业中得到了广泛的应用,目前最多的是用化学镀铜进行PCB的孔金属化。PCB孔金属化工艺流程如下: 钻孔→磨板去毛刺→上板→整孔清洁处理→双水洗→微蚀化学粗化→双水洗→预浸处理→胶体钯活化处理→双水洗→解胶处理(加速)→双水洗→沉铜→双水洗→下板→上板→浸酸→一次铜→水洗→下板→烘干 一、镀前处理 1.去毛刺 钻孔后的覆铜泊板,其孔口部位不可避免的产生一些小的毛刺,这些毛刺如不去除将会影响金属化孔的质量。最简单去毛刺的方法是用200~400号水砂纸将钻孔后的铜箔表面磨光。机械化的去毛刺方法是采用去毛刺机。去毛刺机的磨辊是采用含有碳化硅磨料的尼龙刷或毡。一般的去毛刺机在去除毛刺时,在顺着板面移动方向有部分毛刺倒向孔口内壁,改进型的磨板机,具有双向转动带摆动尼龙刷辊,消除了除了这种弊病。 2 整孔清洁处理 对多层PCB有整孔要求,目的是除去钻污及孔微蚀处理。以前多用浓硫酸除钻污,而现在多用碱性高锰酸钾处理法,随后清洁调整处理。
孔金属化时,化学镀铜反应是在孔壁和整个铜箔表面上同时发生的。如果某些部位不清洁,就会影响化学镀铜层和印制导线铜箔间的结合强度,所以在化学镀铜前必须进行基体的清洁处理。最常用的清洗液及操作条件列于表如下: 清洗液及操作条件 配方 组分 1 2 3 碳酸钠(g/l) 40~60 —— 磷酸三钠(g/l) 40~60 —— OP乳化剂(g/l) 2~3 —— 氢氧化钠(g/l)— 10~15 — 金属洗净剂(g/l)—— 10~15 温度(℃) 50 50 40 处理时间(min) 3 3 3 搅拌方法空气搅拌机械移动空气搅拌 机械移动空气搅拌机械移动 3.覆铜箔粗化处理 利用化学微蚀刻法对铜表面进行浸蚀处理(蚀刻深度为2-3微米),使铜表面产生凹凸不平的微观粗糙带活性的表面,从而保证化学镀铜层和铜箔基体之间有牢固的结合强度。以往粗化处理主要采用过硫酸盐或酸性氯化铜水溶液进行微蚀粗化处理。现在大多采用硫酸/双氧水(H2SO4/H202 )其蚀刻速度比较恒定,粗化效果均匀一致。由于双氧水易分解,所以在该溶液中应加入合适的稳定剂,这样可控制双氧水的快速分解,提高蚀刻溶液的稳定性
沉铜工艺
化学镀铜(PTH) Chapter 1 沉铜原理(Shipley) 一概述 化学镀铜:俗称沉铜,是一种自身催化氧化还原反应,可以在非导电的基体上进行沉积,化学镀铜的作用是实现孔金属化,从而使双面板,多层板实现层与层之间的互连,随着电子工业的飞速发展对线路板制造业的要求越来越高,线路板的层次越来越多,同一块板的孔数越来越多,孔径越来越小,这些孔的金属化质量将直接影响到电气的性能和和可靠性。 二去钻污原理: 1 去钻污的必要性: 由于钻孔过程钻嘴的转速很高,可达16~~18万rpm,而环氧玻璃基材为不良导体,钻孔时会在短时间内产生高温,高温会在孔壁上留下许多树脂残渣,从而形成一层薄的环氧树脂钻污,由于此树脂钻污与孔壁的结合力不牢,当直接沉铜时,就会影响化学铜与孔壁的结合力,特别是多层板,会影响化学铜层与内层铜的导通,去钻污就是清除这些残渣,改善孔壁结构。 2 去钻污方法的选择: 利用碱性KMnO4溶液作强氧化剂,在高温下将孔壁树脂氧化,这种处理不仅可以除掉这些钻污,而且还可以改善孔壁树脂表面结构,经过碱性KMnO4处理后的树脂表面被微蚀形成许多孔隙,呈蜂窝状,这样大大促进了化学铜与孔壁树脂的结合力,此法是目前去钻污流程使用最广泛的方法,具有高稳定性,既经济又高效,管理操作简便。 3 去钻污原理: ①溶胀:Swelling 利用有机溶剂渗入到孔壁的树脂中,使其溶胀,形成结构疏松的环氧树脂,从而有利于碱性KMnO4的氧化除去,一般的溶胀剂都是有机物,反应条件要求高温及碱性环境。需采用不锈钢工作液槽。 MLB211膨胀剂是淡黄色,不混浊,不易燃的水溶液,含有有机物(10%左右的已烯基丁二醇—丁乙酸),对树脂有一定的溶解作用,但主要作用是使环氧树脂溶胀,溶胀剂不与树脂起直接反应,但随着长时间的高温处理,溶胀剂易老化而需更换,换缸视生产量而定,一般为6000m2/次。 ②去钻污Desmearing: 反应原理:在碱性及高温条件下,KMnO4对溶胀的树脂起氧化作用。 4MnO4-+C+4OH-→4MnO42- +CO2 +2H2O 此反应需在316不锈钢或钛材料工作槽中进行,同时存在副反应: 2MnO4- +2 OH-→2MnO42-+1/2 O2+ H2O 4MnO4-+ 2H2O→4MnO2 + 3O2+4OH- KMnO4的再生:要提高KMnO4工作液的使用效率,必须考虑将溶液中的MnO42-再生转变为MnO4 -,目前普遍采用的是电解再生法,再生器利用的是阴极为大面积的不锈钢柱形圆筒,阳极为钛材料,其与阴极的面积比很小,MnO4-2-在阳极表面发生的反应为MnO4-2--e→MnO4-。使用450~~550A的整流器,由于MnO42-不断地氧化成MnO4-,因此工作液中不需大量添加KMnO4原料,它的少量添加是为了平衡工作液的带出损耗,因而大大降低了生产成本,使用较长时间的工作液在槽底会形成沉淀,需定期清除,以保证处理效果。 MLB214D为树脂蚀刻促进剂,可提高KMnO4的树脂蚀刻能力,提高工作液的润湿性,减少孔内气泡,其为白色粉末状固体。 ③还原: 工作原理:经碱性KMnO4处理过的板面残留有MnO4-,其具有的氧化性会对后续的工作槽污染,会令其失去应有的作用,需对其进行还原中和处理。反应为MnO4-+ H2O2 +H+→MnO42- +H2O +O2 MLB216是浅黄色,不易燃,强酸性的水溶液,其PH值低于1.0。 三化学沉铜原理 1 除油:(Conditioner)
沉铜工序作业指导书讲解
沉铜工序作业指导书 1.0目的 建立详细的作业规范,籍以稳定品质,提升生产效率,并作为设备保养、员工操作的依据,此文件同时也是本岗位新员工培訓之教材。 2.0适用范围 本作业规范适用于本公司电镀班沉铜工序。 3.0职责 3.1工艺部职责:负责沉铜线全面的工艺技术管理和工艺过程的控制,工艺及生产问题的解 决,员工的培训,保证生产过程的顺利进行; 3.2生产计划部职责: 负责生产组织与管理,员工的培训与培养,工艺过程和设备的日常维 护和保养,产品产量和质量的保障; 3.3品质部职责:负责对工艺过程、设备的维护和保养以及工序产品质量进行监控; 3.4机修班职责:生产设备的管理、维护和维修; 3.5电镀班:负责组织员工按本作业指导书进行操作及对工艺与设备进行日常维护和保养. 4.0作业内容 4.1工艺流程 4.1.1双面板沉铜流程(行车用1#程序) 磨板→上料→除油(清洁整孔)→溢流水洗→溢流水洗→微蚀→水洗→酸洗→水洗 →预浸→活化→水洗→水洗→加速→水洗→沉铜→水洗→转板电加厚铜 4.1.2多层板沉铜流程(行车用2#程序) 磨板→上料→膨胀→溢流水洗→除胶渣→回收水洗→溢流水洗→溢流水洗→中和 →溢流水洗→溢流水洗→接双面板流程 4.2 工艺流程说明 4.2.1磨板:清洁板面氧化、污渍、残胶等使板面粗化,增加结合力。如有刮伤、残胶等 缺陷应先用细砂纸打磨后再过磨板机。 咬蚀树脂,以除去钻孔产生的碎屑污物。 4.2.2膨胀:使环氧树脂软化膨松,便于KMnO 4 的强氧化性咬蚀膨松软化的环氧树脂。 4.2.3除胶渣:在高温强碱的环境下,利用KMnO 4
4.2.4中和:用来还原多层板带出的高锰酸根,并完全除去孔内残留的MnO 、MnO42-等; 2 4.2.5除油:清洁孔壁,调整孔壁基材表面的静电荷,提高孔壁对胶体钯的吸附能力。4.2.6微蚀:去除氧化层,提高铜箔表面与化学铜之间的结合力。 4.2.7酸洗:清洁铜面,减少铜离子对活化缸的污染。 4.2.8预浸:为防止板材将水带到随后的活化槽中,使活化液的浓度和PH值变化影响活化效果。 4.2.9活化:在绝缘基体上吸附一层具有催化能力的金属颗粒,使经过活化的基体表面具 有催化还原金属的能力,从而使化学镀铜反应在整个催化处理过的基体表面 顺利进行。 4.2.10加速:除去部分包围着钯核的碱式锡酸盐化合物,使钯核完全露出,增强胶体钯的活性。 4.2.11沉铜:通过催化作用在孔壁及小铜面沉积一层细致的铜层,使孔壁的树脂以及玻璃纤维表面具有导电性。
废水废气固废处理方案
废水防治对策 废水水量水质分析 根据工程分析,企业产生的废水主要为工艺废水和生活污水,項目水量及水质情况见表10-1 为确保经废水处理后,第一类污染因子在车间排放口达标排放,其他污染因子也达标排放且要求废水处理后有60%的中水回用于生产,必须首先对废水进行分质分类收集、分质处理、分质回收。废水分类收集的要求见表10-2.
设计废水量按工程分析预计废水生产量的120%左右计,预留一定的余量。 废水处理方案及可达性分析 一、废水处理方案: 1、废水处理原理: ①含铬废水(表中第5类): 废水中的六价铬主要以Cr2072-、Cr042-二种形式存在,在酸性条件下,主要以Cr2072-存在;在碱性条件下,主要以Cr042-存在。含铬废水处理釆用焦亚硫酸盐还原法,其基本原理是在酸性条件(pH=2.5~3.0)下,使废水中的六价铬还原成三价铬,然后加碱调节废水pH至8~9,同时投加混凝剂,使其形成氢氧化铬沉淀而除去,达到废水净化之目的。釆用焦亚硫酸钠处理的还原反应式如下: Na2S205+H20 — 2NaHS03 H2Cr207+3NaHS03+3H2S04— Cr2(S04)3+3Na2S04+4H20 形成氢氧 化铬沉淀反应为: Cr2(S04)3+6Na0H—2Cr(0H)3|+3Na2S04 理论上投药比(W/W)六价铬:Na2S205为1 : 3.6,实际使用时为1 : 4~5. ②含氰废水(表中第4类): 废水经格栅井后进入调节池(设液位自控仪),均质均量后废水经泵提升至一级破氰池,加碱控制池内pHll~12,同时投加次氯酸钠,使CN-氧化成CNO-经一级不完全破氰反应后的废水溢流进入二级破氰池,加酸控制池内pH 8左右,同时投加次氯酸钠,使 CNO-氧化成C02、N2,完全破氰后的废水汇入综合隔油调节池进行进一步的处理。 破氰反应池内均设气力搅拌系统、pH控制系统、ORP控制系统。一级破氰池 ORP 达到300mV时反应基本完成,二级破氰池OPR需达到650V。 ③混合废水(表中第2类及第7类): 废水中含氰、铜、镍、铬、有机污染物等,无法将各污染因子单独分出,只有先破氰再还原铬,再沉淀,原理同上。 ④含镍废水(表中第3类): 釆用离子交换吸附技术,利用离子交换剂与不同离子结合力强弱的差异,将溶质暂时交换到离子交换剂上,饱和后出售给有资质回收单位。