电子凸轮追剪方案

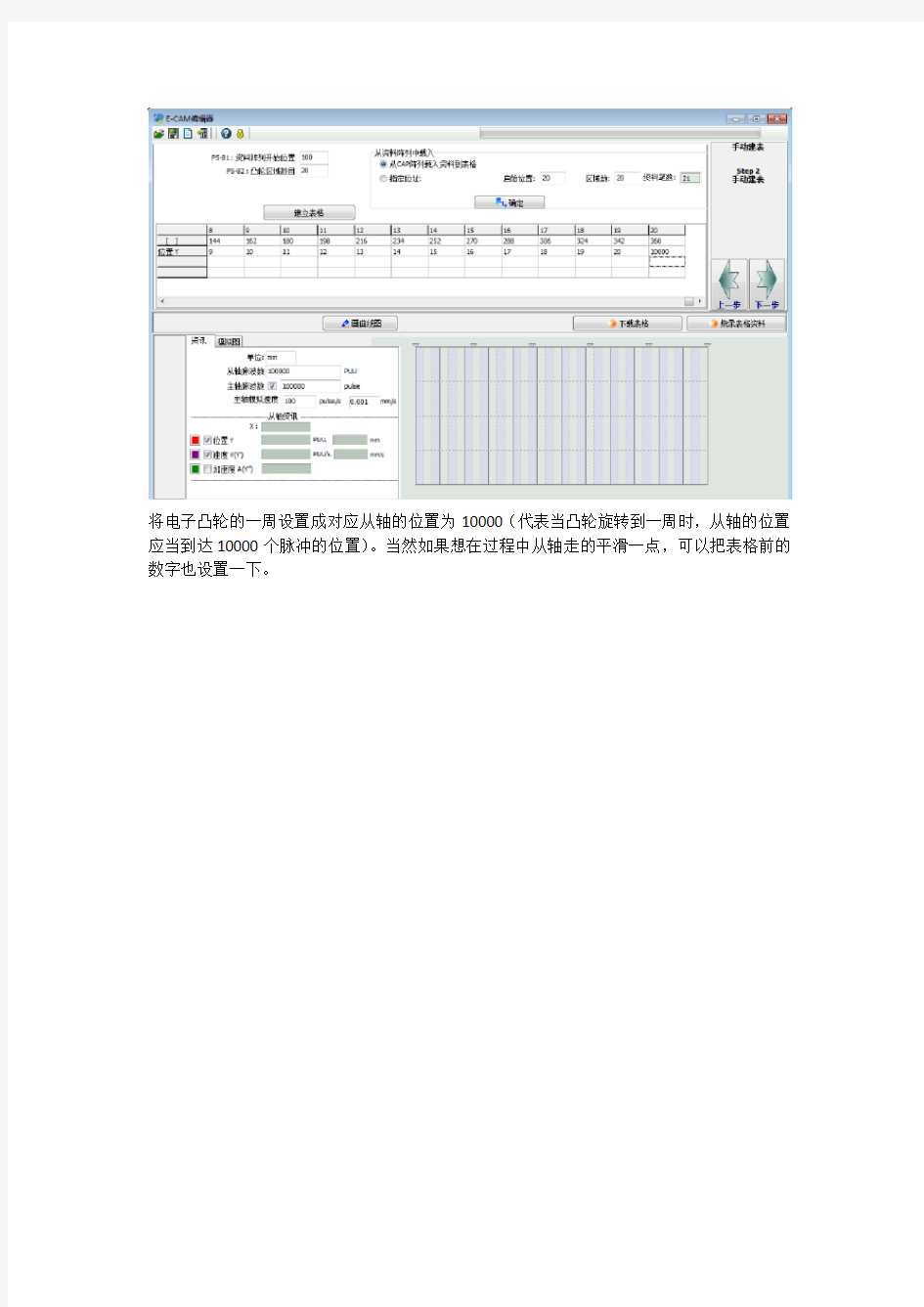
电子凸轮
现在应用如下:
上面的圆为从轴伺服控制的切刀,下面的圆为主轴编码器的输入,假设,主轴编码器是1000PLS/R ,1000个脉冲对应主传送带1m ,那么也就是说,如果我们要切1M长度的布,当主轴编码器反馈1000个脉冲时,从轴必须正好转一圈,才能保证刀正好切在1M的位置上。在A2伺服建立电子凸轮表如下:
将电子凸轮的一周设置成对应从轴的位置为10000(代表当凸轮旋转到一周时,从轴的位置应当到达10000个脉冲的位置)。当然如果想在过程中从轴走的平滑一点,可以把表格前的数字也设置一下。
凸轮轮基本尺寸的设计
第四节 凸轮机构基本尺寸的设计 在设计凸轮的轮廓曲线时,不仅要保证从动件能够按给定要求实现预期的运动规律,还应该保证凸轮机构具有合理的结构尺寸和良好的运动、力学性能。对于基圆半径、偏距和滚子半径等基本尺寸,在进行凸轮轮廓曲线的设计之前都是事先给定的。如果这些基本参数选择不当,就会存在凸轮机构的结构是否合理、运动是否失真以及受力状况是否良好等问题。因此,本节主要讨论有关凸轮机构基本尺寸的设计问题,为正确、合理选择这些基本参数提供一定的理论依据。 一、凸轮机构的压力角 凸轮机构的压力角是指不计摩擦时,凸轮与从动件在某瞬时接触点处的公法线方向与从动件运动方向之间所夹的锐角,常用α表示。压力角是衡量凸轮机构受力情况好坏的一个重要参数,是凸轮机构设计的重要依据。 1.直动从动件凸轮机构的压力角 如图6—29所示为直动从动件盘形凸轮机构的压力角示意图。其中,图6—29a 为尖底从动件的压力角示意图,图6—29b 为平底从动件的压力角示意图。现以滚子从动件凸轮机构为例,来说明直动从动件盘形凸轮机构压力角的计算方法。根据图6—30中的几何关系,可得压力角的表达为 图6—29直动从动件的压力角图 6—30偏置直动从动件的压力角 (6—34) 由三心定理,P 点为瞬心,ωOP v v P ==,?ω d d s v OP = = (由从动件速度公式? ωd d s v =) 式中,“ ”号与从动件的偏置方向有关。图6—30所示应该取“-”号,反之,如果从动件导路位于凸轮 回转中心O 的左侧,则应该取“+”号。显然,这种情况属于从动件的偏置方向选择不合理,因为增大了凸轮机构的压力角,降低了机械效率,甚至可能会导致凸轮机构发生自锁。因此,正确选择从动件的偏置方向有利于减小机构的压力角。此外,压力角还与凸轮的基圆半径和偏距等有关。(当v 、ω、s 一定时,若凸轮基圆半径增大,则压力角α将减小,但机构尺寸随之增大;若凸轮基圆半径减小,压力角α将增大,
PacDrive3,面向未来的自动化解决方案
PacDrive3,面向未来的自动化解决方案 灵活机器控制 一直以来,缩短设备和工程的开发时间这个目标,是产生“灵活机器控制”的推动力。“灵活机器控制”是一种理念,它将各种互相补足的控制平台通过一个软件解决方案整合到MachineStruxure 里。从简单的驱动器到高性能运动控制器的整个控制器系列,都能通过同一个平台来进行编程并投入运行。该理念无需新的工具或培训:无论各自原先采用的控制平台是哪一种,它都能让用户在同一个熟悉而舒适的软件环境下完成工程设计。集成了大量经过验证的应用功能块的综合软件库, 可将为用户提供需要的各种支持。 整体自动化解决方案 凭借PacDrive3,MachineStruxure 为自动化 解决方案提供了一个硬件平台,包括逻辑和运动控 制器件。PacDrive3 可广泛的应用到包装机械和 其他生产系统中,就像在拆卸和组装系统中一样。 PacDrive3 控制器的可扩展性能够满足少到几根 轴的小型伺服系统的需求,也可支持多达99 个伺 服电机或30 个机器人的高性能解决方案,适用于 各种不同等级的自动化应用。 PacDrive3 基于成熟的运动和逻辑控制技 术,将逻辑控制、运动控制和机器人控制功能整合 在同一个硬件平台内。PacDrive3程序符合
IEC-61131-3的程序结构标准,这种全集成的系统架构,可广泛的应用到包装机械和其他系统中,比如拆卸和组装系统。sercos III 将PacDrive3自动化解决方案的整个通信过程整合在一个基于以太网的全集成自动化总线上。PacDrive3系统的组成部分来自于HMI、自动控制设备和电气设备等组成的综合自动化产品线,以便于为高要求的工业应用提供完整的单源解决方案。开创性工程系统设计 多年来,PacDrive 一直在不断的追寻降低软件和硬件复杂度的技术途径。我们一贯的目标是控制设计、安装和调试中不断提高的工程成本。PacDrive3 为实现这个目标带来了崭新的可能性,也为长期稳定的发展引入了新的技术途径。 不断提升的扩展性带来更好的性能 针对复杂控制系统和简单机械应用两种配置,PacDrive3 将多轴同步运动控制,逻辑控制和机器人控制功能整合到一起,并为这个平台提供强大的扩展性能。既可满足控制99 根轴或30 个机器人系统的高端应用,也同时为简单机械应用提供了更经济的4 轴或8 轴的新型控制器。这种途径为简单应用和复杂系统带来了更高效的整体解决方案。 基于以太网的全集成通信 增加sercos III 后,施耐德电气为PacDrive 应用打造了首个完全基于以太网的通信解决方案,实现了驱动器和现场设备的通信。sercos III 还为集成安全自动化*功能扫清了道路。sercos III 不受限于某个具体的厂商,它是一个真正的,标准的现场通讯总线,同时也是目前市场上最强大的基于以太网的通信解决方案之一。 灵活的驱动器设计 通过创新的驱动器设计可实现灵活的驱动系统架构:一个由单轴和双轴模块式LXM62伺服驱动器通过共用电源的方式组成的多轴系统,相比4 轴以上的多轴系统,在成本和所占空间上都有降低。通过插接式连接器和快速连接总线,亦可减少安装费用。对于轴数少的紧凑型应用,新开发的书本式LXM52伺服驱动器带来了更高性价比的自动化方案。 一个开发工具,一个项目 SoMachine Motion 是针对整个工程设计的新型软件开发平台,包括PacDrive3 调试和诊断功能。SoMachine Motion 将运动控制和传动系统设计的工具(ECAM),程序开发(包括EPAS 的ETEST,Vijeo Designer)、诊断和数据处理(Assitants)等工具都整合在一个工具包内。一个安全系统编辑器也被整合进了SoMachineMotion,进行安全自动化* 软件开发。EDESIGN 是一种用软件功能块进行图形化编程工具的核心,以进一步简化软件工程设计。
光洋电子凸轮简易操作说明书
光洋电子凸轮简易操作说明书1 一面板功能说明: 14 程序组:程序组编号的指定/待殊功能的解除。15 功能:特殊功能编号的指定。16 原点:原点补偿角度的选择。17 输出→:输出编号按递增顺序指定。18输出:输出编号按递减顺序指定。 19方式:选定哪种方式被选定的方式指示灯亮。20执行:方式的确定;清除的执行。 21消除:输出设定的消除选择;原点补偿的消除选择;解除消除选择;解除输出设定的读出状态。 22背面DIP开关:SW1 角度增加方向选择,CW从编码器的轴侧看顺时钟方向回转角度增加;CCW则反时钟方向回转角度增加。SW2 编码器分辨率的选择,360使用回转360度的编码器;720 使用720度的编码器。SW3 凸轮输出/RUN输出的选择;凸轮把所有输出作为凸轮输出使用的情况,RUN 把特定的输出作为输出使用。 二、基本操作: 1切换动作方式:用方式键选择方式。从当前方式开始顺序选取择设定→学习→调整→运转→设定→;按执行键切换到选定方式。 2 按程序组键指定程序组号。(在兴世机上通常用) 3指定输出号:按→输出或←输出键指定输出。每按一次键,输出显示的灯亮位置发生变化。 4读出输出设定:指定程序组号和输出号后,按读出↑或读出↓输出区设定情况,ON/OFF角度交替读出 5消去输出设定:先把要消去的输出设定读出,然后按消去实行键就可以削去该输出设定。 6消去指定输出号内的全部设定:先指定程序组号和输出号,然后按消去→输出实行或消去←输出实行键即可。 7写入输出设定:先指定程序组号和输出号,按+ 或—键设定需要的角度,按写入键输入。请先按开的角度后按关的角度的顺序设定。 8设定原点补偿:先指定程序组号,转动编码器到机械原点的位置停止,按原点键选择原点的角度,按写入键原点成为0度。 9消去原点补偿:先指定程序组号,按消去原点实行键即可消去原点补偿,显示编码器的输出角度。10切换特殊功能:按FUN 键特殊功能顺序变换。→0→1→2→3→4→5→6→7→8→9→A→按BANK 键(程序组),解除特殊功能。注:设定方式以外,FUN号只有0右选择、切换。 特殊功能0:进角设定的读出、写入、消去和调整。 A读出进角设定:先指定输出号,然后按读出↓或读出↑键,交替读出进角度设定和进角回转速度设定
凸轮测量测头转换及当量升程表计算方法2008
凸轮测量测头转换及当量升程表计算方法2008-6-5 来源:中国机床商务网摘要:通过凸轮测量实例,对凸轮测量时的测头转换所引发的当量转角—升程表问题进行了分析,指出测头转换应保证凸轮受检位置不变,并以S195 型柴油机配气凸轮为例,推导出了当量转角、当量升程的计算通式并给出由平面测头转换为?15mm 滚柱测头测量的当量转角—升程表。 1 概述 凸轮轴是影响发动机配气机构工作质量的关键部件,它的功能是保证发动机气门组有准确、平稳的良好运动规律。凸轮的测量,主要是为评定凸轮轴上各凸轮的几何精度和装机后的动力特性提供依据,所以,在对凸轮进行测量时,应按设计要求选择与凸轮机构从动件(挺柱)相同形式和形状的测头,按设计要求给出的转角—升程表进行测量,以正确反映凸轮机构的运动规律。 2 测头转换 测头转换,不是指简单地将一种测头换成另一种测头,而是指采用不符合设计要求形式和形状的测头进行凸轮测量时测量参数的转换。在测量中,把不符合设计要求形式和形状的测头卸下,装上符合设计要求形式和形状的测头的一组操作称为测头换装。测头转换和测头换装是两个截然不同的概念。 无论是确定凸轮的检测位置,还是测量凸轮的升程,都应采用与凸轮机构从动件(挺柱)相同形式和形状的测头。例如,S195 型柴油机的配气凸轮的从动件是平面挺柱,测量时应采用平面测头:供油凸轮的从动件是滚柱挺柱,测量时应采用与滚柱挺柱直径相同的滚柱测头。可是,常常是当同一根凸轮轴上各凸轮的从动件设计要求不同时,本应分别采用符合设计要求的不同形式和形状的测头进行测量,可是一些测量者为了省去在测量过程中换装测头的麻烦,竟用同一测头去测量凸轮轴上各个凸轮,这对某一个凸轮而言就引发了测头转换问题,尤其是在凸轮自动测量时,这种转换测头形式和形状的现象更为普遍。 图1 凸轮受检点相同时测头不同凸轮转角不同 图2 将平面测头转换为滚柱测头时当量转角和当量升程的求解 测头形式和形状转换后,改用当量升程表测量,原理上并不存在问题。但是现行当量升程表,一般均以设计转角为依据而不是以设计受检点为依据来计算。也就是说,如果测头转换后与转换前的转角一致,则凸轮受检点将不同:如果测头转换前后受检点相同,则凸轮转角不同。例如,S195 型柴油机配气凸轮的“敏感点”m,采用设计要求的平面测头测量时,凸轮转角ap=46°07'16"(图1a):采用?15mm 滚柱测头时,凸轮转角aG=16°53' (图1b):采用刀口测头时,凸轮转角aD= 6°52'28"(图1c)。即凸轮同一受检点的ap≠aG≠aD。由此可知,测头形式和形状转换后,如仍按设计转角来计算当量升程,则凸轮设计受检点的位置就被篡改了,从而会由于测头转换前后受检点处凸轮形状误差不同,影响凸轮测量数据的准确性,甚至可能造成对凸轮合格性的判断错误(误废或误收)。 3 当量升程表 当遇到由于测量工艺条件的限制无法采用符合设计要求的形式和形状的测头时,例如,摩托车发动机顶置凸轮轴式的配气凸轮,必须将摇臂与凸轮型面接触的摆动式柱面的气门升程转换成对心移动式平面测头的凸轮升程(转换计算见杨光兴等所著《摩托车发动机原理与设计》(武汉测绘科技大学1993年出版社中第297页),采用平面测头才有利于凸轮的加工和测量。又如S195型柴油机凸轮轴,设计要求配气(进、排)凸轮用平面测头测量,供油凸轮用?15mm 滚柱测头测量,如果统一采用?15mm滚柱测头,这时配气凸轮测量就进行了测头转换。同一根凸轮轴上各凸轮统一采用一种测头测量,有利于凸轮自动测量。
电子凸轮说明书
兴世机械电子凸轮简要说明 一.安全和注意 1.注意事项 本电子凸轮并不是完全的绝对值编码器,它在第一转(没有找到原点时)不 会输出信号. 2.安全操作 请在完全了解明白该手册后,再安装和操作本电子凸轮. 二.安装 1.控制器安装 直接嵌入面板安装,用配带的金属扣固定. 2.编码器安装 编码器用配套的联轴器安装,请保证编码器轴和设备驱动轴的同心度.
三.接线 1.接线端子位置: 2.电源 24V:24V供电电源. 0V:电源公共端.
3.编码器接线 BLK: Black 黑色线 RED:Red 红色线 WHI: White 白色线A相脉冲+ GRY:Grey 灰色线A相脉冲- BLU: Blue 蓝色线B相脉冲+ BRN: Brown 棕色线B相脉冲- YLW: Yellow 黄色线Z相脉冲+ GRN: Green 绿色线Z相脉冲- 其它端子不用接线. 如果需要更换电子凸轮旋转方向,请交换WHI和GRY(白色线和灰色线). 4.输出信号接线 COM:输出信号的公共点,每8个通道共用一个.并且每8个通 道内部共用一个保险. 0-31: 输出通道.NPN集电极开路输出,最高电压300V/最大电 流150mA/最大功率100mW.
5.控制信号接线 24V:控制信号输入电源. ST:启动,当信号为ON时,控制使能输出,并可以设定参数. B0- B2:程序组选择信号.可以选择0-7程序组,如下表: 端子接0V时激活(ON),悬空不接或接24V无效(--). B0 B1 B2 NO. -- -- -- 0 ON -- -- 1 -- ON -- 2 ON ON -- 3 -- -- ON 4 ON -- ON 5 -- ON ON 6 ON ON ON 7 程序组信号在ST信号跳变沿读取. 四.控制 1.启动 ST:启动信号,引脚为0V时激活.激活后读取程序组并使能凸轮输出.
自动车床凸轮设计详细教程..
自动车床主要靠凸轮来控制加工过程,能否设计出一套好的凸轮,是体现自动车床师傅的技术高低的一个标准。凸轮设计计算的资料不多,在此,我将一些基本的凸轮计算方法送给大家。凸轮是由一组或多组螺旋线组成的,这是一种端面螺旋线,又称阿基米德螺线。其形成的主要原理是:由A点作等速旋转运动,同时又使A点沿半径作等速移动,形成了一条复合运动轨迹的端面螺线。这就是等速凸轮的曲线。 凸轮的计算有几个专用名称: 1、上升曲线——凸轮上升的起点到最高点的弧线称为上升曲线 2、下降曲线——凸轮下降的最高点到最低点的弧线称为下降曲线 3、升角——从凸轮的上升起点到最高点的角度,即上升曲线的角度。我们定个代号为φ。 4、降角——从凸轮的最高点到最低点的角度,即下降曲线的角度。代号为φ1。 5、升距——凸轮上升曲线的最大半径与最小半径之差。我们给定代号为h,单位是毫米。 6、降距——凸轮下降曲线的最大半径与最小半径之差。代号为h1。 7、导程——即凸轮的曲线导程,就是假定凸轮曲线的升角(或降角)为360°时凸轮的升距(或降距)。代号为L,单位是毫米。 8、常数——是凸轮计算的一个常数,它是通过计算得来的。代号为K。 凸轮的升角与降角是给定的数值,根据加工零件尺寸计算得来的。 凸轮的常数等于凸轮的升距除以凸轮的升角,即K=h/φ。由此得h=Kφ。 凸轮的导程等于360°乘以常数,即L=360°K。由此得L=360°h/φ。 举个例子: 一个凸轮曲线的升距为10毫米,升角为180°,求凸轮的曲线导程。(见下图) 解:L=360°h/φ=360°×10÷180°=20毫米
升角(或降角)是360°的凸轮,其升距(或降距)即等于导程。 这只是一般的凸轮基本计算方法,比较简单,而自动车床上的凸轮,有些比较简单,有些则比较复杂。在实际运用中,许多人只是靠经验来设计,用手工制作,不需要计算,而要用机床加工凸轮,特别是用数控机床加工凸轮,却是需要先计算出凸轮的导程,才能进行电脑程序设计。 要设计凸轮有几点在开始前就要了解的. 在我们拿到产品图纸的时候,看好材料,根据材料大小和材质将这款产品 的 主轴转速先计算出来. 计算主轴转速公式是[切削速度乘1000]除以材料直径. 切削速度是根据材质得来的,在购买材料时供应商提供.单位是米/分钟. 材料硬度越大,切削速度就越小,切的太快的话热量太大会导致材料变形, 所以切削速度已知的. 切削速度乘1000就是把米/分钟换算成毫米/分钟,在除以材料直径就是 主 轴每分钟的转速了.材料直径是每转的长度,切削速度是刀尖每分钟可以移动的 距离. 主轴转速求出来了,就要将一个产品需要多少转可以做出来,这个转的圈数求出来.主轴转速除以每个产品需要的圈数就是生产效率.[单位.个/分钟] 每款不同的产品,我们看到图纸的时候就先要将它的加工工艺给确定下来. 加工工艺其实就是加工方法,走芯机5把刀具怎么安排,怎么加工,哪把刀具 先做,按顺序将它安排,这样就是确定加工工艺.
电子凸轮参数说明
电子凸轮功能使用说明 电子凸轮是指根据从轴的同步参数设定,从轴位置与主轴位置同步的功能。根据设定的凸轮曲线、离合器、各种补偿等来运算从轴相对于主轴的位置。 时间 ISD210电子凸轮型伺服支持最大8192点的凸轮表,凸轮表数量可以设定为1、2或者4个,不同凸轮表在运行过程中可以动态切换。电子凸轮的主轴来源可以选择位置脉冲输入、全闭环输入、内部定位指令或者时间轴。多台伺服通过主轴脉冲的级联,可以实现针对同一个主轴的多轴联动电子凸轮。 凸轮曲线的生成规则支持整体曲线生成,这种模式下曲线各个点二次连续;也支持指定顶点后的分段生成,用户可根据自己的需要选择等速度、等加速度、简谐等多生成规则。 电子凸轮运行过程中,支持对主轴和凸轮输出的动态调整,支持对主轴的速度补偿,支持可变齿轮,解决运行过程中各种误差调整和跟随问题。 0>电子凸轮结构图
1>全局开关 Pn[837] 电子凸轮开关 电子凸轮开关Pn[837] 电子凸轮使能开关 0‐不使能 1‐使能 只有凸轮开关使能时,才能使用电子凸轮的各项功能。凸轮开关关闭时,当前主轴位置、当前凸轮相位将被复位。 2>主轴 Pn[838] 主轴来源选择 Pn[839] 时间轴周期脉冲量 Pn[840]、Pn[841] 当前主轴位置 主轴来源选择Pn[838] 选择电子凸轮的主轴 0‐位置指令脉冲,可以来自低速脉冲口,也可以来自高速脉冲口,由参数 Pn[407]‐Pn[416]配置 1‐全闭环口脉冲,可以来自CN6上的全闭环脉冲,RS422电平标准,AB相 2‐定位指令,可以来自PLC内部定位指令,主轴来源选择定位指令时,电子凸
NSD电子凸轮(VS-5EX)使用说明
NSP-92007-2-PDF Electronic Rotary Cam Switch System VS-5E Series SPECIFICATIONS & INSTRUCTION MANUAL
2. Storage Thank you very much for purchasing our product. Before operating this product, be sure to carefully read this manual so that you may fully understand the product, safety instructions and precautions. - Please submit this manual to the operators actually involved in operation. - Please keep this manual in a handy place. Signal Words Safety precautions in this guide are classified into DANGER and CAUTION. This product is not designated to be used under any situation affecting human life. When considering the use of this product for special purposes, such as for medical equipment, aerospace equipment, unclear power control systems,traffic systems, etc., please consult NSD. Application Limitation 4. Installation (Please read this safety guide carefully before operation) GENERAL SAFETY RULES
凸轮计算方法
凸轮计算方法 图片: 自动车床主要靠凸轮来控制加工过程,能否设计出一套好的凸轮,是体现自动车床师傅的技术高低的一个标准。凸轮设计计算的资料不多,在此,我将一些基本的凸轮计算方法送给大家。 凸轮是由一组或多组螺旋线组成的,这是一种端面螺旋线,又称阿基米德螺线。其形成的主要原理是:由A点作等速旋转运动,同时又使A点沿半径作等速移动,形成了一条复合运动轨迹的端面螺线。这就是等速凸轮的曲线。 凸轮的计算有几个专用名称: 1、上升曲线——凸轮上升的起点到最高点的弧线称为上升曲线 2、下降曲线——凸轮下降的最高点到最低点的弧线称为下降曲线 3、升角——从凸轮的上升起点到最高点的角度,即上升曲线的角度。我们定个代号为φ。 4、降角——从凸轮的最高点到最低点的角度,即下降曲线的角度。代号为φ1。 5、升距——凸轮上升曲线的最大半径与最小半径之差。我们给定代号为h,单位是毫米。 6、降距——凸轮下降曲线的最大半径与最小半径之差。代号为h1。
7、导程——即凸轮的曲线导程,就是假定凸轮曲线的升角(或降角)为360°时凸轮的升距(或降距)。代号为L,单位是毫米。 8、常数——是凸轮计算的一个常数,它是通过计算得来的。代号为K。 凸轮的升角与降角是给定的数值,根据加工零件尺寸计算得来的。 凸轮的常数等于凸轮的升距除以凸轮的升角,即K=h/φ。由此得h=Kφ。 凸轮的导程等于360°乘以常数,即L=360°K。由此得L=360°h/φ。 举个例子: 一个凸轮曲线的升距为10毫米,升角为180°,求凸轮的曲线导程。(见下图) 解:L=360°h/φ=360°×10÷180°=20毫米 升角(或降角)是360°的凸轮,其升距(或降距)即等于导程。 这只是一般的凸轮基本计算方法,比较简单,而自动车床上的凸轮,有些比较简单,有些则比较复杂。在实际运用中,许多人只是靠经验来设计,用手工制作,不需要计算,而要用机床加工凸轮,特别是用数控机床加工凸轮,却是需要先计算出凸轮的导程,才能进行电脑程序设计
盘形凸轮的四种设计方法
盘形凸轮的四种设计方法 深圳市百特兴科技有限公司 周杰平 摘要:详细介绍运用SolidWorks 绘制盘形凸轮的不同方法,包括插件法、解析法、折弯法及仿真法。 关键词:盘形凸轮,插件法,解析法,折弯法,仿真法,余弦加速度, SolidWorks,EXCEL。 凸轮/连杆机构以其快速、稳定的特点,在很多的场合尤其是传统的制程设备中得以运用。但其缺点也很明显:适应性较差,结构相对比较复杂,开发周期长,凸轮加工精确要求比较高等,非标设备大多由伺服马达/步进马达、丝杆/同步带、气缸/油缸等替代。近年来,由于对设备产能要求越来也高,传统的凸轮/连杆机构又受到用户青睐。以动力电池制造设备中塑封制程为例。进口设备核心机构采用凸轮/连杆机构,产能在140件/分钟以上,国产设备采用伺服/丝杆驱动,产能则在50件/分钟左右。更为重要的是前者用于制程的有效时间更长,确保了品质的可靠性。凸轮的设计将成为机构设计工程是不可缺少的技能。 本文以盘形凸轮为研究对象,分别介绍几种不同的设计方法。 一、基本参数 1.1、凸轮基本参数 项目 代号 参数值 基圆直径 D 150 凸轮厚度 W 15 辊子直径 d 25 升程 h 50 表1 1.2、从动杆运动规律 动作 运动角度数 (Φ) 起始角度位置 终止角度位置 结束半径 运动规律 推程 120 0 120 125 余弦加速度 远休止角 30 120 150 125 回程 90 150 240 75 余弦加速度 近休止角 120 240 360 75 表2 注:余弦加速度(简谐运动)方程: S=h*[1-cos(πφ/Φ)]/2
图1 二、SolidWorks 插件法 2.1、如图2,打开SolidWorks,新建零件,关闭草图。菜单栏Toolbox -> 凸轮 如菜单栏无Toolbox,先加入插件。 图2 图3 2.2、设置。如图3 凸轮类型为圆形,推杆类型为平移,如果是偏心的,可作相应的选择;开始半径为基圆半径,开始角度根据<表2>填写;旋转方向为顺时针 2.3、运动如图4
细纱机电子凸轮说明书
细纱机电子凸轮成形 一、电子凸轮成形系统优势: 1、传统的机械凸轮成形在调整工艺参数的时候,需要更换部件,工作量大, 停机时间长。而电子凸轮操作简便灵活,停机时间短。 2、机械凸轮经过长时间运行后,会出现凸轮磨损,因而造成凸轮打顿,影 响成形质量。而电子凸轮不存在此类现象。 3、电子凸轮的成形由于是通过程序软件设计实现卷绕成形的,参数设置范 围广,成形要好于机械凸轮,这点从络筒机的速度可以得到验证,在相同情况下比较,通过电子凸轮成形的满纱管在络筒机上的运行速度要大大高于机械凸轮。 4、电子凸轮提高了细纱机二次开车的留头率,由于电子凸轮在编程上的灵 活性,通过调整钢领板落纱下降速度、开车下降速度和落纱停车位置等,可以提高二次开车的细纱留头率。 5、解决纬纱脱圈问题 纺纬纱,常规机械凸轮成型很难满足布机的工艺要求,造成在布机上脱圈现象严重,使用电子凸轮成形后,可以按照特殊工艺要求纺保险纱,从而解决了布机脱圈问题。在实际应用中获得用户认可,效果非常好。 6、纺纱动程可以任意调整 在纺不同的纱,工艺要求不同,有的纱脱圈可以通过加大纺纱动程解决,由于机械凸轮纺纱动程不可以任意修改,而电子凸轮成形的动程可以任意修改,在防止脱圈办法更多。 7、增加满管顶部缠绕圈功能 电子凸轮可以在落纱的时候,上升到纱管顶部适当的位置,完成缠绕几圈,以便络筒机能快速准确的找头。这个是传统机械凸轮无法做到的,该功能可根据用户需求增加使用。 二、电子凸轮成形系统的组成: 1、电气部分主要由交流伺服系统、PLC可编程控制器、开关电源、触摸屏 和接近开关组成,系统的输入部分由细纱机信号接入,即风机启动,主机启动,中途落纱,钢领板下降信号。系统的输出通过PLC输出模块给主机,即下纲领板信号、关主电机信号、满纱信号、主机刹车信号和伺服故障信号。 所有工艺参数和点动操作都在触摸屏上完成。 2、机械部分主要由星型涡轮减速机构、伺服电机、链轮、链条和辅助部件 构成。 三、调试说明: . 1、首先将电气部分安装到位,按照图纸正确接线,伺服驱动器的输入信号与主机输入信号共用,伺服输入信号的24V电源来自主机的24V电源,输入
考研机械凸轮典型计算例题
图示凸轮机构中,凸轮为一半径R= 20 mm的偏心圆盘,圆盘的几何中心A到转动中心O的距离为e = 10 mm,滚子半径r g = 5 mm,凸轮角速度。试求:(14分) ①凸轮的理论廓线和基圆;②图示位置时机构的压力角; ③凸轮从图示位置转过时的位移S;④图示位置时从动件2的速度v。 ①凸轮的理论廓线和基圆 理论廓线。对于滚子推杆的凸轮机构而言,理论廓线是过滚子中心的一条封闭廓线。题目中给出的是工作廓线,要得到理论廓线,只需要把工作廓线往外偏移一个滚子的半径即可。由于这里工作廓线就是一个以C为圆心,半径为20mm的圆;而滚子的半径是5mm,所以理论廓线就是以C为圆心,半径为20+5=25mm的圆.如下图所示。 基圆。首先我们知道,基圆是在理论廓线上定义的;其次我们懂得,它是以转动中心O 为圆心的,与理论廓线内切的一个半径最小的圆。按照该定义,我们以O为圆心做一个与理论廓线内切的最小的圆如下图,显然,它的半径是10+5=15mm. ②图示位置时机构的压力角; 对于该机构而言,压力角是滚子的中心B点的受力方向与运动方向的夹角。 B点的速度方向。由于B点是推杆与滚子的连接点,所以它也就是推杆上的B点。由于推杆在上下平移,推杆上任何一点的轨迹都是沿着推杆的直线,所以任何一点的速度方向都是推杆直线的方向,因此推杆上的B点速度方向也在该直线上。 B点的受力方向。推杆上的B点与理论廓线接触,在忽略摩擦的前提下,其受力方向其实就是理论力学中的光滑接触面中的反力方向。光滑接触面的反力是公法线方向。由于推杆的B点是尖点,无所谓法线,所以公法线方向就是理论廓线在该点的法线方向。而理论廓线是一个圆,圆上任何一点的法线方向都是从从该点指向圆心的。所以BC的方向就是公法线方向。 显然,速度方向与力的方向重合,所以压力角是0度。这是我们最希望的压力角。压力角越小,则凸轮机构的传力性能越好。
AN130006_伺服驱动器电子凸轮曲线自学习使用方法
能的 1>自 2(定 2>下线速本文档说明的基础上阅读自学习相关参Pn[438]:全Pn[838]:主定位指令) Pn[858]:凸Pn[859]:目Pn[887]:凸设定凸Pn[888]:凸设定凸Pn[889]‐Pn[设定曲设定为Pn[891]:凸0到1下图为典型电速度需要稳定伺服明如何使用电读本文档。 参数 全闭环口脉冲主轴来源选择凸轮表数量,目标目标凸轮凸轮曲线学习凸轮曲线学习凸轮曲线学习凸轮曲线学习[890]:凸轮曲曲线学习时凸为负值时凸轮凸轮曲线学习跳变是启动凸电池卷绕结构定。 服驱动器电子电子凸轮型驱冲逻辑方向,择,在凸轮曲必须为2 轮表数量,必习输出力矩 过程中凸轮习旋转速度 过程中凸轮曲线学习凸轮轮轴的脉冲轮电机输出反习启动控制 凸轮曲线学习 构,运行时,卷子凸轮曲线自动器中的曲线0‐正 1‐负,曲线学习过程必须为0或1 轴输出的转矩轴输出的速度轮轴脉冲量 量,设定为正向转矩 习过程,学习 卷绕轴旋转,自学习使用方线自学习功能重新上电生中置1(全闭矩 0‐100% 度限制 1‐10正值时学习过习完成后自动 为了达到较方法 能。应在充分效 环口),在凸000RPM 过程中凸轮电动清0 较好的张力控 分理解电子凸凸轮运行过程电机输出正向控制效果,物轮功程中置转矩, 料的
主轴编码器为AB相增量编码器,其AB相信号接入驱动器CN6接口,信号连接关系为: 驱动器CN6 全闭环编码器 PIN2 A+ PIN3 A‐ PIN4 B+ PIN5 B‐ PIN12 +5V PIN11 GND 3>自学习过程 启动自学习前,驱动器必须处于凸轮模式,卷绕轴处于卷绕开始位置,设定卷绕轴在学习过程中的旋转速度Pn[888],转矩限制Pn[887],根据实际工艺的需要设定学习过程中凸轮轴的运行距离Pn[889]‐Pn[890](根据卷绕圈数计算)。 以上参数设定完成后,将Pn[891]置1,卷绕轴会根据设定参数旋转,学习过程结束后,Pn[891]恢复为0,整个卷绕过程主轴运行的距离会保存到Pn[856]‐Pn[857],凸轮曲线保存到ROM中,可以在后台软件中上载确认: 4>曲线的使用 将主轴来源选择Pn[838]更改为2(定位指令),定义一条第一速度定位指令,运行的目标
考研机械凸轮典型计算例题
图示凸轮机构中,凸轮为一半径R=20 mm 的偏心圆盘,圆盘的几何中心 A 到转动中心O 的距离为 e = 10 mm ,滚子半径r g = 5 mm ,凸轮角速度。试求:(14 分) ①凸轮的理论廓线和基圆;②图示位置时机构的压力角; ③凸轮从图示位置转过时的位移S;④图示位置时从动件 2 的速度v。 ① 凸轮的理论廓线和基圆 理论廓线。对于滚子推杆的凸轮机构而言,理论廓线是过滚子中心的一条封闭廓线。题 目中给出的是工作廓线,要得到理论廓线,只需要把工作廓线往外偏移一个滚子的半径即可。由于这里工作廓线就是一个以 C 为圆心,半径为20mm 的圆;而滚子的半径是5mm ,所以理论廓线就是以 C 为圆心,半径为20+5=25mm 的圆.如下图所示。 基圆。首先我们知道,基圆是在理论廓线上定义的;其次我们懂得,它是以转动中心O 为圆心的,与理论廓线内切的一个半径最小的圆。按照该定义,我们以O 为圆心做一个与理论廓线内切的最小的圆如下图,显然,它的半径是10+5=15mm. ②图示位置时机构的压力角; 对于该机构而言,压力角是滚子的中心 B 点的受力方向与运动方向的夹角。
B 点的速度方向。由于 B 点是推杆与滚子的连接点,所以它也就是推杆上的 B 点。由于推杆在上下平移,推杆上任何一点的轨迹都是沿着推杆的直线,所以任何一点的速度方向都 是推杆直线的方向,因此推杆上的 B 点速度方向也在该直线上。 B 点的受力方向。推杆上的 B 点与理论廓线接触,在忽略摩擦的前提下,其受力方向其 实就是理论力学中的光滑接触面中的反力方向。光滑接触面的反力是公法线方向。由于推杆的B 点是尖点,无所谓法线,所以公法线方向就是理论廓线在该点的法线方向。而理论廓 线是一个圆,圆上任何一点的法线方向都是从从该点指向圆心的。所以BC 的方向就是公法线方向。 显然,速度方向与力的方向重合,所以压力角是0 度。这是我们最希望的压力角。压力 角越小,则凸轮机构的传力性能越好。 ③凸轮从图示位置转过时的位移S; 对于这种问题,总是用反转法通过作图测量出来的。 使用反转法,我们给整个凸轮机构(包括机架)一个与凸轮转向相反,速度相同的角速 度,从而使得凸轮静止,而机架围绕凸轮的转动中心转动,此时,推杆会一方面跟随机架转动,另外,又相对机架做平移。按照理论力学的说法,若取机架为动系,则推杆在做一个牵 连运动为定轴转动,而相对运动为平移运动的平面运动。
凸轮机构基本参数的设计
凸轮机构基本参数的设计 前节所先容的几何法和解析法设计凸轮轮廓曲线,其基圆半径r0、直动从动件的偏距e或 摆动从动件与凸轮的中心距a、滚子半径rT等基本参数都是预先给定的。本节将从凸轮机 构的传动效率、运动是否失真、结构是否紧凑等方面讨论上述参数的确定方法。 1 凸轮机构的压力角和自锁 图示为偏置尖底直动从动件盘形凸轮机构在推程的一个位置。Q为从动件上作用的载荷(包 括工作阻力、重力、弹簧力和惯性力)。当不考虑摩擦时,凸轮作用于从动件的驱动力F是 沿法线方向传递的。此力可分解为沿从动件运动方向的有用分力F'和使从动件紧压导路的有 害分力F''。驱动力F与有用分力F'之间的夹角a(或接触点法线与从动件上力作用点速度方 向所夹的锐角)称为凸轮机构在图示位置时的压力角。显然,压力角是衡量有用分力F'与有 害分力F''之比的重要参数。压力角a愈大,有害分力F''愈大,由F''引起的导路中的摩擦阻 力也愈大,故凸轮推动从动件所需的驱动力也就愈大。当a增大到某一数值时,因F''而引 起的摩擦阻力将会超过有用分力F',这时无论凸轮给从动件的驱动力多大,都不能推动从动 件,这种现象称为机构出现自锁。机构开始出现自锁的压力角alim称为极限压力角,它的 数值与支承间的跨距l2、悬臂长度l1、接触面间的摩擦系数和润滑条件等有关。实践说明, 当a增大到接近alim时,即使尚未发生自锁,也会导致驱动力急剧增大,轮廓严重磨损、 效率迅速降低。因此,实际设计中规定了压力角的许用值[a]。对摆动从动件,通常取[a]=40~ 50;对直动从动件通常取[a]=30~40。滚子接触、润滑良好和支承有较好刚性时取数据的上 限;否则取下限。 对于力锁合式凸轮机构,其从动件的回程是由弹簧等外力驱动的,而不是由凸轮驱动的,所 以不会出现自锁。因此,力锁合式凸轮机构的回程压力角可以很大,其许用值可取[a]=70~ 80。
自动车床凸轮设计教程
1.自动车床主要靠凸轮来控制加工过程,能否设计出一套好的凸轮,是体现自动车床师傅的技术高低的一个标准。凸轮设计计算的资料不多,在此,我将一些基本的凸轮计算方法送给大家。凸轮是由一组或多组螺旋线组成的,这是一种端面螺旋线,又称阿基米德螺线。其形成的主要原理是:由A点作等速旋转运动,同时又使A点沿半径作等速移动,形成了一条复合运动轨迹的端面螺线。这就是等速凸轮的曲线。 凸轮的计算有几个专用名称: 1、上升曲线——凸轮上升的起点到最高点的弧线称为上升曲线 2、下降曲线——凸轮下降的最高点到最低点的弧线称为下降曲线 3、升角——从凸轮的上升起点到最高点的角度,即上升曲线的角度。我们定个代号为φ。 4、降角——从凸轮的最高点到最低点的角度,即下降曲线的角度。代号为φ1。 5、升距——凸轮上升曲线的最大半径与最小半径之差。我们给定代号为h,单位是毫米。 6、降距——凸轮下降曲线的最大半径与最小半径之差。代号为h1。 7、导程——即凸轮的曲线导程,就是假定凸轮曲线的升角(或降角)为360°时凸轮的升距(或降距)。代号为L,单位是毫米。 8、常数——是凸轮计算的一个常数,它是通过计算得来的。代号为K。 凸轮的升角与降角是给定的数值,根据加工零件尺寸计算得来的。 凸轮的常数等于凸轮的升距除以凸轮的升角,即K=h/φ。由此得h=Kφ。 凸轮的导程等于360°乘以常数,即L=360°K。由此得L=360°h/φ。 举个例子: . .
一个凸轮曲线的升距为10毫米,升角为180°,求凸轮的曲线导程。(见下图) 解:L=360°h/φ=360°×10÷180°=20毫米 升角(或降角)是360°的凸轮,其升距(或降距)即等于导程。 这只是一般的凸轮基本计算方法,比较简单,而自动车床上的凸轮,有些比较简单,有些则比较复杂。在实际运用中,许多人只是靠经验来设计,用手工制作,不需要计算,而要用机床加工凸轮,特别是用数控机床加工凸轮,却是需要先计算出凸轮的导程,才能进行电脑程序设计。 要设计凸轮有几点在开始前就要了解的. 在我们拿到产品图纸的时候,看好材料,根据材料大小和材质将这款产品 的 主轴转速先计算出来. 计算主轴转速公式是[切削速度乘1000]除以材料直径. 切削速度是根据材质得来的,在购买材料时供应商提供.单位是米/分钟. 材料硬度越大,切削速度就越小,切的太快的话热量太大会导致材料变形, 所以切削速度已知的. 切削速度乘1000就是把米/分钟换算成毫米/分钟,在除以材料直径就是 主 轴每分钟的转速了.材料直径是每转的长度,切削速度是刀尖每分钟可以移动的 距离. 主轴转速求出来了,就要将一个产品需要多少转可以做出来,这个转的圈数求出来.主轴转速除以每个产品需要的圈数就是生产效率.[单位.个/分钟] . .
H3U编程手册-电子凸轮-gfk
第1章电子凸轮 H3U包括H3U-3232MT和H3U-0808PMRTA两种型号机型,其中0808PMRTA具有3轴电子凸轮功能。同时还具备手摇轮功能,手摇轮也称电子齿轮。 如下举例均以Y轴作为例子,不同之处在于特殊软元件的地址不同。 H3U-0808PMRTA的3轴电子凸轮模块架构如下图: X轴Y轴Z轴电子凸轮输出 3轴电子凸轮模块可实现电子凸轮表跟随或电子齿轮功能,主轴输入可选择外部输入或内部虚拟,外部输入可任意选择X、Y或Z轴的高速输入作为电子凸轮模块的主轴输入。内部虚拟主轴以X轴作为虚拟对象,因此只有Y轴和Z轴可以使用内部虚拟主轴。 3轴电子凸轮模块的基本功能一致,以Y轴为例,单轴电子凸轮模块的基本架构如下图: 电子凸轮功能实现步骤如下: 1.建立凸轮表 2.设置主轴选择 3.设置周期/非周期选择
4.设置同步输出 5.设置延时启动 6.设置硬件触发启动/停止使能 7.停止模式设置 8.选择凸轮表/电子齿轮 9.启动电子凸轮 1.1 建立凸轮表 电子凸轮的本质是从轴跟随主轴的运动,主轴和从轴的运动关系可以用凸轮表数据或电子齿轮比表示。使用电子凸轮表数据,可以建立最大360个关键点数据。使用电子齿轮比,主轴和从轴之间只有一个固定的比例关系。 若使用电子齿轮,只需设定电子齿轮比分子和分母(SD144,SD145),无需设定凸轮表数据。若使用电子凸轮,需要先设定电子凸轮表数据。 1.1.1 新建凸轮表, 在AutoShop软件的工程管理一栏中右击CAM图标,在弹出的菜单中选择“新建”,即可新建一个凸轮表。通过AutoShop软件最大可设置16个凸轮表,其中的3个凸轮表可以下载到PLC中运行,其它凸轮表只保存在工程文件中。 下载到PLC中的凸轮表通过ID来区分,右击工程管理一栏中新建好的凸轮表图标,在弹出的菜单中选择“属性”,即可查看或设定凸轮表ID。凸轮表ID为1、2、3的分别对应凸轮表1、2、3,可以下载到PLC中运行,其它ID为-1。在凸轮属性对话框中可以修改ID。
纺织与PLC自动化
近十多年来我国纺织机械行业的机电一体化水平有了较明显的提高,在新型纺织机械上普遍采用了机电一体化技术。这项技术的内容包含了先进的信息处理和控制技术,即以计算机为核心,有PLC、工控机、单片机、人机界面、现场总线等组成的控制系统;先进的驱动技术,有变频调速,交流伺服,步进电机等;检测传感技术和执行机构;精密机械技术等。棉纺织设备较有代表性的机电一体化产品,例如新型的粗纱机、分条整经机、浆纱机,这类机器均采用了机电一体化技术,其特点是: (1)由计算机控制多台变频器,交流伺服驱动器,再分别控制多台电动机的同步传动系统。(粗纱机为二、三或四台电机的三种方案,分条整经机为五台电机,浆纱机为七台电机) (2)均采用传感技术,检测纱线张力,通过计算机实现张力控制。 (3)采用计算机软件来完成粗纱的卷绕成形功能和实现经轴、织轴的理想卷绕。 纺织机械应用了机电一体化技术后机构简化,性能改善,质量提高,操作方便,提升了设备的档次和水平。 (1)粗纱机采用计算机控制多电机分部传动后的效果: ①简化了复杂的机械结构,取消了锥轮变速装置、三自动成形机构、计长装置等。 ②应用触摸屏人机界面,操作十分方便。 ③计算机储存多品种的最佳工艺,更换品种十分方便。 ④产品质量好,粗纱条干水平达到乌斯特公报5%的水平。 ⑤主机速度和生产效率提高,断头减少。 (2)分条整经机采用计算机、变频器、交流伺服组成的控制系统后的效果: ①经轴卷绕张力从定性控制发展到定量控制,自动控制内外圈张力,实现理想的内紧外松,产品质量好。 ②对绞精度有明显的提高。 ③采用触摸屏人机界面,操作简单方便。 ④主机价格是进口价格的三分之一,降低了纺织厂的投资。 (3)浆纱机采用计算机控制多电机分部传动后的效果: ①简化了复杂的机械结构,取消了长边轴传动和PIV机械无级变速器。 ②伸长率和织轴卷绕张力得到了有效控制,提高了产品质量。 ③回潮率检测后,通过计算机与全机速度调节相连,保证回潮率的良好控制,有利于后道工序的稳定生产。 ④采用触摸屏人机界面,操作简单方便。 ⑤机器生产效率有较明显的提高。 自动络筒机和无梭织机也是纺织行业中机电一体化水平高的产品,其特点将在后面进行专题介绍。 1 先进的通用自动化装置在纺织机械上应用的状况 上面举例的三种设备,主要是采用了先进的通用自动化装置应用于纺织机械上来提高机电一体化水平,产生了好的效果。因此先进的通用自动化装置应用状况,也可从一方面反映出纺织设备的机电一体化技术现状。 1.1 PLC的应用 PLC在纺织设备上应用已普及,清花、梳棉、并条、精梳、粗纱、络筒、并纱、捻线、整经、浆纱、无梭织机等均已采用。 纺织设备上用的PLC,其1/0点数范围:8~1024点,约85%以上为8~112点。 PLC的年需用量,2002年约24000台,比2000年增长33%。