立式退火炉炉辊安装调整技术探讨
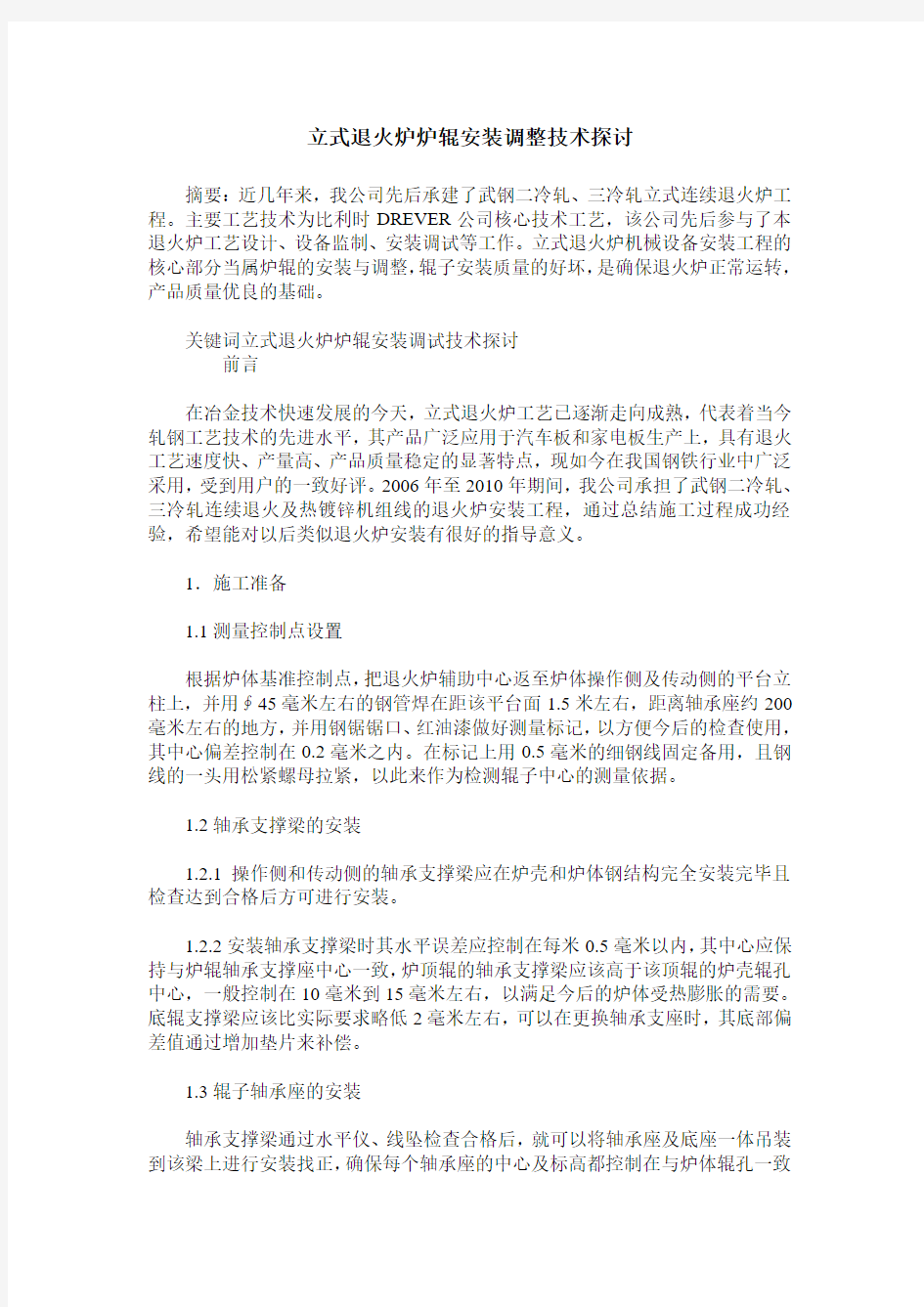
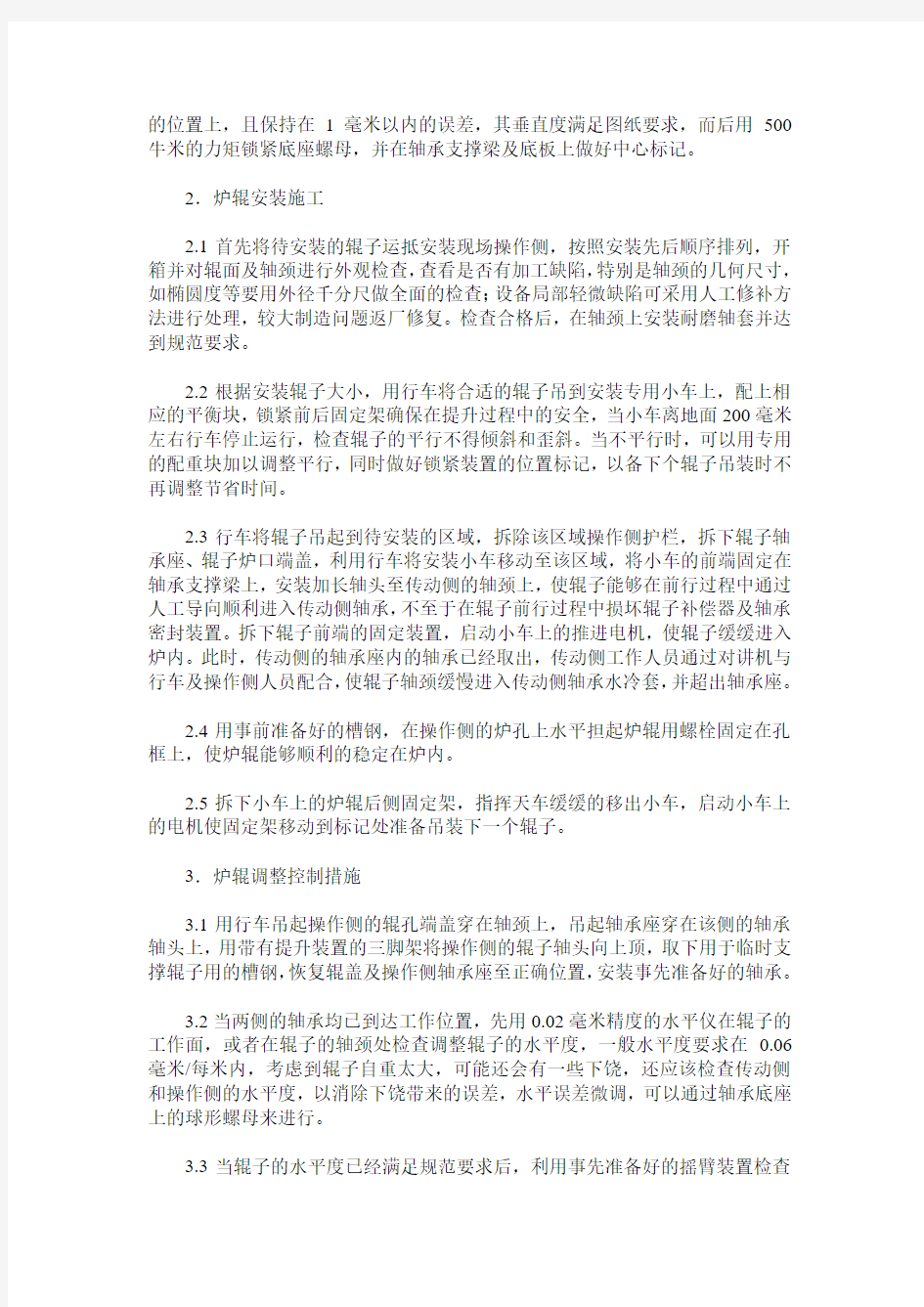
立式退火炉炉辊安装调整技术探讨
摘要:近几年来,我公司先后承建了武钢二冷轧、三冷轧立式连续退火炉工程。主要工艺技术为比利时DREVER公司核心技术工艺,该公司先后参与了本退火炉工艺设计、设备监制、安装调试等工作。立式退火炉机械设备安装工程的核心部分当属炉辊的安装与调整,辊子安装质量的好坏,是确保退火炉正常运转,产品质量优良的基础。
关键词立式退火炉炉辊安装调试技术探讨
前言
在冶金技术快速发展的今天,立式退火炉工艺已逐渐走向成熟,代表着当今轧钢工艺技术的先进水平,其产品广泛应用于汽车板和家电板生产上,具有退火工艺速度快、产量高、产品质量稳定的显著特点,现如今在我国钢铁行业中广泛采用,受到用户的一致好评。2006年至2010年期间,我公司承担了武钢二冷轧、三冷轧连续退火及热镀锌机组线的退火炉安装工程,通过总结施工过程成功经验,希望能对以后类似退火炉安装有很好的指导意义。
1.施工准备
1.1测量控制点设置
根据炉体基准控制点,把退火炉辅助中心返至炉体操作侧及传动侧的平台立柱上,并用∮45毫米左右的钢管焊在距该平台面1.5米左右,距离轴承座约200毫米左右的地方,并用钢锯锯口、红油漆做好测量标记,以方便今后的检查使用,其中心偏差控制在0.2毫米之内。在标记上用0.5毫米的细钢线固定备用,且钢线的一头用松紧螺母拉紧,以此来作为检测辊子中心的测量依据。
1.2轴承支撑梁的安装
1.2.1操作侧和传动侧的轴承支撑梁应在炉壳和炉体钢结构完全安装完毕且检查达到合格后方可进行安装。
1.2.2安装轴承支撑梁时其水平误差应控制在每米0.5毫米以内,其中心应保持与炉辊轴承支撑座中心一致,炉顶辊的轴承支撑梁应该高于该顶辊的炉壳辊孔中心,一般控制在10毫米到15毫米左右,以满足今后的炉体受热膨胀的需要。底辊支撑梁应该比实际要求略低2毫米左右,可以在更换轴承支座时,其底部偏差值通过增加垫片来补偿。
1.3辊子轴承座的安装
轴承支撑梁通过水平仪、线坠检查合格后,就可以将轴承座及底座一体吊装到该梁上进行安装找正,确保每个轴承座的中心及标高都控制在与炉体辊孔一致
经验谈:如何安装与调整镀锌线立式连续退火炉炉辊
经验谈:如何安装与调整镀锌线立式连续退火炉炉辊(2006/11/20 13:25)(引用地址:https://www.360docs.net/doc/54894606.html,/lyxx/default.asp)目录:公司动态 浏览字体:大中小 邯钢冷轧厂镀锌线立式连续退火炉与2004年6月开始设备安装,2005年6月28日烘炉检查完毕。由比利时DREVER公司设计,并负责设备安装监理、调试。炉辊的安装是炉子安装中最重要、最复杂、要求最高的部分。炉辊的安装质量,决定了板带在炉内的运行情况。这就意味着:炉辊的安装质量,决定了镀锌线生产的连续性。 炉子结构和主要参数 适合生产CQ、DQ、DDQ、HSS和FH材质的钢板。包括退火炉和冷却塔。 所配备设备的主要特性有:预热段能够利用加热段排放废气的余热加热钢带,多功能的加热和均热段采用全辐射管加热,喷冷段可以向均衡段提供横向温度均匀的板带,均衡段能够保持和均匀带钢温度,并且在镀锌部分和喷冷段之间提供一个缓冲空间,出口段包括一套热张紧辊,它为进入锌锅的带钢提供高张力以保证带钢通过气刀时的稳定性,锅后冷却段采用空气冷却,终冷段用于降低水淬之前的带钢温度,水冷段包括喷淋系统、水淬槽、挤干辊和干燥器。 炉内有转向辊17根,张力辊2根,张力计辊3根,纠偏辊2套(4根),导向辊4根,电加热器6套。冷却塔上有挤干辊4根,水淬槽辊1根,导向辊2根。 炉内气体为95﹪氮气与5﹪氢气的混和气体。 炉辊的安装和调整 1 确定辊子几何轴线点的步骤 主钢结构安装、调整完成后,在辊子所在的每个水平线上,确定出几何轴线点,以确保辊子沿炉子轴线上处在精确位置。 这项工作必须由一名有经验的测量员来承担。开始工作前,测量员必须作预备报告。 几何轴线用一根在两个支撑臂之间拉紧的钢丝来表示,支撑臂支撑焊接在主钢结构上。 安排这些支撑位置时,测量员会给出明确的说明。这些支撑不能给炉子其它部件的安装带来阻碍。 支撑臂和钢丝将置于操作侧。钢丝的位置通过每根辊子的轴心,并距每根棍子轴承座100mm。 一旦几何中心线确定后,测量员将提交一份最终报告,详细描述辊子及其它与他布置的
连续退火炉基础知识
连续退火炉Continuous Annealing Furnace基础知识 1.炉型的选择和应用,采用什么炉子退火,主要根据产品种类和 钢种特性决定(表6-21) 表6-21各类不锈钢退火炉型选择 钢种热轧后冷轧后 马氏体钢罩式炉(BAF)连续退火炉 铁素休钢罩式炉(BAF)连续退火炉 奥氏体钢连续退火炉连续退火炉热轧后的马氏体钢通过BAF在大于A3温度条件下退火。使热轧后的马氏体组织在保温的条件下充分转化奥氏体组织,然后缓冷至一定温度这时完全转变为铁素体组织,消除了热轧后的马氏体组织。另外,在保温期间碳化物也得到均匀分布。 热轧后的铁素体钢几乎总有一些马氏体,因此往往也选用BL 炉。当然,对于单相铁素体钢,热轧后不存马氏体,采用AP(H)炉退火更合理。 热轧后奥氏体钢需通过退火使碳化物溶解和快速冷却防止再析出,所以只能用AP(H)炉。 至于冷却后不锈钢的退火,都是通过再结晶消除加工硬化而过到过到目的的。奥氏体不锈钢除此之外,还要使冷轧时产生的形变
马氏体转变为奥氏体,因此都用AP(C) BA 这样的连续炉退火。如果用BL 炉,则存在以下问题:1. 不管在什么条件下退火,由于退火时间长表面都会氧化,生成不均匀的铁鳞,存在显著的退火痕迹 2. 退火温度较高时,容易粘结和发生层间擦伤等表面缺陷。 ⑵退火条件 ①退火条件的确定按下面的程序框图确定退火条件。 应注意的事项: 用记的加工制造方法变化或对材质的要求变动时,应修订退火条件。初期阶段没有充分把握,应按用户对退火产品的质量评价判定退火条件是否合适。 再结晶特性调查用碳矽棒热处理作实验(画出硬度曲线、 晶粒度曲线、确认金相组织)退火温度设定设定退火温度上、下限值及退火时间 出炉口目标材料温度的设定设定材温仪表指示值的目标值 (上、下限温度) 各段炉温和机组速度设定根据理论计算进行初步设定 机组实际运行试验确认燃烧状况(烧咀负荷等)和 通板状况(机组速度、除鳞性 前后操作状况) 判定性能是否合格根据检查标准判定 退火条件确定 前部工序,如炼钢、热轧、甚至冷轧的条件发生变化,需要修改
退火炉温度控制系统
本科生课程设计 题目:退火炉温度控制系统 课程:电力拖动自动控制系统 专业:电气工程及其自动化 班级: 学号: 姓名: 指导教师: 完成日期: 2015年3月20日
任务书 一、课程设计的目的 通过电力拖动自动控制系统的设计、了解一般交直流调速系统设计过程及设计要求,并巩固交直流调速系统课程的所学内容,初步具备设计电力拖动自动控制系统的能力。为今后从事技术工作打下必要的基础。 二、课程设计的要求 1、熟悉交直流调速系统设计的一般设计原则,设计内容以及设计程序的要求。 2、掌握控制系统设计制图的基本规范,熟练掌握电气控制部分的新图标。 3、学会收集、分析、运用自动控制系统设计的有关资料和数据。 4、培养独立工作能力、创造能力及综合运用专业知识解决实际工程技术问题的能力。 三、课程设计的内容 退火炉温度控制系统由一台上位机操作台、一台SIEMENS S7-200 PLC控制柜、一台变频器控制柜,3台风机,3台水煤浆输送泵组成。加热段的三个炉段,各段于炉顶设一支热电偶,根据热电偶采集的炉温信号,与设定值比较,经PID 计算后输出控制信号变频器调节水煤浆流量,改变烧嘴的输出功率,实现温度自动控制。同时根据助燃风量的改变及空/燃比例阀的配比,手动调节助燃风流量燃气的流量,实现最佳空/燃配比。 四、进度安排:共1.5周 本课程设计时间共1.5周,进度安排如下: 1、设计准备,熟悉有关设计规范,熟悉课题设计要求及内容。(1.5天) 2、分析控制要求、控制原理设计控制方案(1.5天) 3、绘制控制原理图、控制流程图、端子接线图。(2天) 4、编制程序、梯形图设计、程序调试说明。(1.5天) 5、整理图纸、写课程设计报告。(1.5天) 五、课程设计报告内容 完成下列课题的课程设计及报告(课题工艺要求由课程设计任务书提供)退火炉温度控制系统
课程设计退火炉温度控制系统
课程设计设计题目: 退火炉温度控制系统 学院: 专业: 班级: 姓名: 学号: 指导老师: 日期:
摘要 退火炉是金属热处理中的重要设备,它把压力容器加热到一定温度并维持一段时间,然后让其自然冷却。其目的在于消除压力容器的整体压力。提高压力容器的使用寿命。温度是退火炉的主要被控变量,是保证其产品质量的一个重要因素。退火炉温度控制的稳定性和控制精度直接影响产品的质量。 本文以AT89C51单片机为控制核心,采用模块化的设计方案,包括硬件设计与软件设计两部分。硬件设计包括温度检测模块,按键模块,执行模块,LED显示模块,单片机最小系统。本设计要求采用电热丝加热,通过A/D转换将采集到的温度数据输入单片机中,与系统给定值比较,从而对退火炉的温度进行控制,通过按键输入控制信号,三位LED显示炉温。最后设计出最少拍无纹波控制器,通过MATLAB 仿真检验是否有纹波。
目录 第1章绪论 (3) 1.1设计背景与算法 (3) 第2章课程设计的方案?5 2.1概述?5 2.2系统组成总体结构 (5) 第3章程序设计与程序清单 (7) 3.1单片机最小系统设计 (7) 3.1.1单片机选择 (7) 3.1.2时钟电路设计 (8) 3.1.3复位电路设计?9 3.2程序清单与电路图 (11) 3.3温度控制电路................................ 错误!未定义书签。第4章控制算法?18 4.1程序框图? 18 4.2算法设计 (19) 第5章课程设计总结?错误!未定义书签。
第1章 绪论 1.1 设计背景与算法 背景:退火炉是冶金和机械行业常用的热处理工业设备。一般说来,退货处理工艺师冶金和机械产品的最后处理工序,它的处理效果将直接影响产品的质量。因此,对退火炉的基本要求就是根据退火处理工艺曲线,提供准确的升温,保温及降温操作,同时保证颅内各处的温度均匀。在目前实际生产中,退火炉的种类很多,按燃料分有燃油炉、燃气炉、电炉等。电炉按台数计算占80%,燃油炉和燃气炉占20%。 退火是金属热处理中的重要工序,它是将金属缓慢加热到一定温度,保持足够时间,然后以适宜速度冷却(通常是缓慢冷却,有时是控制冷却)的一种金属热处理工艺。目的是使经过铸造、锻轧、焊接或切削加工的材料或工件软化,改善其塑性和韧性,使其化学成分均匀化,并去除其参与应力,或得到预期的物理性能。温度控制是热处理质量控制的重要技术措施,是退火控制的核心。智能温控将大大提高热处理质量,消除认为的不稳定因素,提高温度控制的精确程度,满足特殊材料的热处理要求。 同时,退火炉采用自动化技术控制温度,对保护生态环境方面也具有重要意义。退火炉的炉温动态特性直接影响产品的质量,生产过程中对钢材的温升曲线有较高的要求,温度过低,达不到退火的预期目的;温度过高将导致过热,甚至过烧。通过对退火炉中生产过程的优化控制和自动工艺管理控制,不但可以缩短生产周期,提高产量和质量,还可以减少人为因素造成的废品率。热处理后产生的废气对自然环境的污染很大,退火炉的燃料如果是欠氧燃烧,燃料燃烧不充分,则会产生大量黑烟,而过氧燃烧又会产生氮氧化合物等有害气体。若通过对燃烧过程进行有效控制,使燃烧在合理的空燃比下运行,则可以极大的减少退火炉对周边环境的污染,对构建科持续发展型社会就有积极的意义。 目前世界各国对能源消耗和大气环境的污染越来越重视,而我国既是钢铁大国又是能源大国,因此研究高性能退火炉温度控制系统具有极为重要的现实意义。 算法:在数字随动控制系统中,要求系统的输出值尽快地跟踪给定值的变化,最少拍控制是满足这一要求的一种离散化设计方法。 最少拍控制是一种直接数字设计方法。所谓最少拍,就是要求闭环系统对于某种特定的输入在最少个采样周期内达到无静差的稳态,是系统输出值尽快地跟踪期望值的变化。 闭环Z传函具有形式 z z z z N N ---+++=Φφφφ 221)(1
热镀锌线立式连续退火炉炉辊安装调整技术
龙源期刊网 https://www.360docs.net/doc/54894606.html, 热镀锌线立式连续退火炉炉辊安装调整技术作者:包佳侯剑谷媛媛杨春福 来源:《中国科技纵横》2014年第09期 【摘要】热镀锌立式连续退火炉炉辊安装主要包括轴承支撑梁,炉辊轴承座,炉辊辊盖,膨胀节,炉辊,炉辊轴承等几部分的安装。炉辊的安装是炉子安装中最重要,最复杂,要求最高的部分。炉辊安装结构复杂,小件散件多,设备布局紧凑,安装精度要求高。其安装质量决定了钢带在炉内的运行情况。这就意味着炉辊的安装质量,决定了镀锌线生产的连续性。本文详细阐述了扬子江1420冷轧工程(即沙钢)热镀锌线立式连续退火炉炉辊安装调整的方法,过程中的要点,及应该注意的事项。 【关键词】热镀锌退火炉炉辊 1 引言 中国二十冶施工的连续退火炉是世界上安装质量优良的炉子,施工进度相当快,有着多年丰富的经验,达到了国内外先进水平。曾在国内外多个钢厂完成过大型冷轧连续退火机组的安装及冷轧连续退火炉的改造工作,进行过早期和换代后两种不同类型连续退火炉的安装,编制过安装工法和检查标准。在此,我们对热镀锌线立式连续退火炉的炉辊安装及调整技术进行总结,希望其能对此后类似的工程施工有所帮助。 2 设备概况 炉辊安装是整个退火炉安装过程中至关重要的部分,其安装质量决定了能否保证镀锌线的连续生产,通常是炉体最精密的安装工作,也是气密性、炉辊单体试车的紧前工作,影响到退火炉的烘炉。炉辊调整的精度也直接影响到炉体带钢的纠偏调整,对后期炉体内带钢的顺直通过影响重大。因此炉辊调整是否精确,调整速度快慢,将直接影响到整个热镀锌线的总工期。炉辊设备主要由辊子,传动装置及辊子附件组成,辊子附件包括轴承座,轴承,膨胀节等。 3 炉辊的安装及调整 3.1 示意图(图1) 3.2 安装前提条件 (1)炉区主体钢结构安装完成;(2)确定所有螺栓终紧并达到规定扭矩值;(3)炉壳安装、焊接完成,并通过现场外方专家及监理验收检查并确认合格。(4)炉区结构安装完成,验收后,在钢结构平台上设置炉辊安装、调整、验收用的辅助点及参考线(确认所有结构螺栓已经终紧,并达到螺栓扭矩要求;(5)技术说明:底(顶)层参考线标高比炉辊标高高200mm;两侧参考线距炉体中心各为1970mm。
连续退火炉内气氛控制
连续退火炉内气氛控制 叶波 摘要连续退火炉内存在着氧气、氢气、水蒸气等,这些气体的含量及退火炉内的气氛压力直接影响着带钢的质量和退火炉的安全。因为上述的影响,就需要检测炉内各种气体的含量和炉内气氛的压力,通过分析气体的含量和压力来控制连续退火炉,以达到安全性能最佳,并生产出高质量的连退板。 关键字连续退火气氛检测控制 Continuous annealing furnace atmosphere in control YE Bo ( ) Continuous annealing furnace exist in oxygen, hydrogen, water vapor and so on, these gas content and annealing furnace atmosphere pressure within the directly affect the quality of the strip and annealing furnace safety. Because the influence, need to test the content of various gas furnace and furnace atmosphere in pressure, through the analysis of the gas content and the pressure to control continuous annealing furnace, in order to achieve safety performance is the best, and produce the high quality even back plate. Atmosphere detection control
退火炉热平衡计算与热处理工艺设置
退火炉热平衡计算与热处理工艺设置 东北特钢集团大连特殊钢丝公司徐效谦 内容摘要:通过热平衡计算,根据装炉量对电井炉升温工艺实行分段控制,能有效地改善退火钢丝加热过程的温差,显著提高退火后钢丝的力学性能均匀性。 关键词:退火炉热平衡计算均匀性 退火炉热处理均匀性是一项重要指示,一般认为热处理均匀取决于热处理炉的上、中、下或前、后各区的加热能力的分布状况,实际上加热能力的均匀分布只是一个基本要求,热量的传输效率才是决定热处理均匀性的关键因素。保证单位时间供给的热量与炉料吸收的热量基本平衡,是提高热处理均匀性唯一的控制要点,控制目标是单位时间热量的传输效率应大于95%。热处理均匀性与热量的传输效率成正比关系,传输效率越低,热处理均匀性越差。这个基本原理我们是通过长期实践才逐渐认识到的。 一Ⅲ型井式退火炉基本状况 钢丝Ⅲ型强对流气体保护井式退火炉原设计为自动升温,即控制仪表一段控制温度直接设置为工艺规定的退火温度,由仪表控制升温时间。第2和第3段同时设置温度和时间两项工艺参数。实际运行结果是:退火钢丝抗拉强度偏高,以针丝为例,企业标准Q/LD30-2004中GCr15Ⅰ组要求抗拉强度为Rm:560~680MPa,而在生产过程中测得实验结果为Rm:670~730MPa,同炉钢丝软硬不均,抗拉强度差大。为此需对退火炉进行热平衡计算,在升温阶段同时设定升温温度和升温时间,强化退火效果、改善钢丝抗拉强度均匀性。Ⅲ型退火炉主要技术参数如表1,装料架计算参数如表2。 表1周期炉主要技术参数 表2 装料架计算参数 二Ⅲa型井式退火炉工艺参数及热平衡计算 1.加热时间计算方法 (1)配置功率除以安全系数1.2,即为有效使用功率。有效使用功率中扣除N4~N6三项消耗功率,余数为加热功率,见第三节。 N有效=N总/1.2;
课程设计退火炉温度控制系统
课程设计设计题目:退火炉温度控制系统 学院: 专业: 班级: 姓名: 学号: 指导老师: 日期:
摘要 退火炉是金属热处理中的重要设备,它把压力容器加热到一定温度并维持一段时间,然后让其自然冷却。其目的在于消除压力容器的整体压力。提高压力容器的使用寿命。温度是退火炉的主要被控变量,是保证其产品质量的一个重要因素。退火炉温度控制的稳定性和控制精度直接影响产品的质量。 本文以AT89C51单片机为控制核心,采用模块化的设计方案,包括硬件设计与软件设计两部分。硬件设计包括温度检测模块,按键模块,执行模块,LED显示模块,单片机最小系统。本设计要求采用电热丝加热,通过A/D转换将采集到的温度数据输入单片机中,与系统给定值比较,从而对退火炉的温度进行控制,通过按键输入控制信号,三位LED显示炉温。最后设计出最少拍无纹波控制器,通过MATLAB 仿真检验是否有纹波。
目录 第1章绪论 (3) 1.1设计背景与算法 (3) 第2章课程设计的方案 (5) 2.1概述 (5) 2.2系统组成总体结构 (5) 第3章程序设计与程序清单 (7) 3.1单片机最小系统设计 (7) 3.1.1单片机选择 (7) 3.1.2时钟电路设计 (8) 3.1.3复位电路设计 (9) 3.2程序清单与电路图 (11) 3.3温度控制电路 (16) 第4章控制算法 (18) 4.1程序框图 (18) 4.2算法设计 (19) 第5章课程设计总结................................................ - 22 -
第1章 绪论 1.1 设计背景与算法 背景:退火炉是冶金和机械行业常用的热处理工业设备。一般说来,退货处理工艺师冶金和机械产品的最后处理工序,它的处理效果将直接影响产品的质量。因此,对退火炉的基本要求就是根据退火处理工艺曲线,提供准确的升温,保温及降温操作,同时保证颅内各处的温度均匀。在目前实际生产中,退火炉的种类很多,按燃料分有燃油炉、燃气炉、电炉等。电炉按台数计算占80%,燃油炉和燃气炉占20%。 退火是金属热处理中的重要工序,它是将金属缓慢加热到一定温度,保持足够时间,然后以适宜速度冷却(通常是缓慢冷却,有时是控制冷却)的一种金属热处理工艺。目的是使经过铸造、锻轧、焊接或切削加工的材料或工件软化,改善其塑性和韧性,使其化学成分均匀化,并去除其参与应力,或得到预期的物理性能。温度控制是热处理质量控制的重要技术措施,是退火控制的核心。智能温控将大大提高热处理质量,消除认为的不稳定因素,提高温度控制的精确程度,满足特殊材料的热处理要求。 同时,退火炉采用自动化技术控制温度,对保护生态环境方面也具有重要意义。退火炉的炉温动态特性直接影响产品的质量,生产过程中对钢材的温升曲线有较高的要求,温度过低,达不到退火的预期目的;温度过高将导致过热,甚至过烧。通过对退火炉中生产过程的优化控制和自动工艺管理控制,不但可以缩短生产周期,提高产量和质量,还可以减少人为因素造成的废品率。热处理后产生的废气对自然环境的污染很大,退火炉的燃料如果是欠氧燃烧,燃料燃烧不充分,则会产生大量黑烟,而过氧燃烧又会产生氮氧化合物等有害气体。若通过对燃烧过程进行有效控制,使燃烧在合理的空燃比下运行,则可以极大的减少退火炉对周边环境的污染,对构建科持续发展型社会就有积极的意义。 目前世界各国对能源消耗和大气环境的污染越来越重视,而我国既是钢铁大国又是能源大国,因此研究高性能退火炉温度控制系统具有极为重要的现实意义。 算法:在数字随动控制系统中,要求系统的输出值尽快地跟踪给定值的变化,最少拍控制是满足这一要求的一种离散化设计方法。 最少拍控制是一种直接数字设计方法。所谓最少拍,就是要求闭环系统对于某种特定的输入在最少个采样周期内达到无静差的稳态,是系统输出值尽快地跟踪期望值的变化。 闭环Z 传函具有形式 z z z z N N ---+++=ΦφφφΛ221)(1
冶钢热处理连续退火炉改造方案
冶钢热处理连续退火炉改造方案 1
冶钢热处理连续退火炉改造方案 〔初稿〕 二〇〇六年三月 2
目录 概述 (1) 一、改造方案设计 (1) 1.1热处理退火炉改造方框图 (2) 1.2改造测量点统计 (3) 二.DCS集散系统控制方案 (4) 2.1重庆重庆川仪控制系统有限公司控制方案 (4) 2.2浙江中控技术有限公司控制方案 (9) 三.外围设备改造方案 (11) 3.11#连续退火炉 (11) 3.1.1外围设备说明 (11) 3.1.2方框图 (12) 3.22#连续退火炉 (13) 3
3.2.1外围设备说明 (13) 3.2.2方框图 (14) 3.3其它退火炉 (15) 3.3.1外围设备说明 (15) 3.3.2方框图 (17) 3.4煤气净化站 (18) 3.4.1外围设备说明 (18) 3.4.2方框图 (20) 四.附录 (21) 附1:连续退火炉蝶阀直径明细表 (22) 附2:热处理厂测量网络分布图 (23) 概述 1.冶钢热处理厂1#、2#连续退火炉燃烧控制系统是八十年代重庆自动化研究所安装的286计算机控制系统,当前已全部瘫痪多年,生产仅仅靠人工手动控制,1~12段温度波动在规定设定值的±10℃,生产出的钢材质量极不稳定,而且煤气与空气配比控制不是 4
很理想,造成煤气未完全燃烧而被排放,能源浪费很大,为了新冶 钢早日实现产量型转向质量型;质量型转向稳定型;稳定型转向品 牌型;经过品牌转向自主创新型;以自主创新型转向专业化服务型; 向高、精、尖发展先进企业的目标,达到集约化的目的,建议实施 以1#、2#连续退火炉燃烧控制系统为中心,安装一套DCS集散 系统,改造分二步进行,第一部完成1#、2#连续退火炉燃烧控制 系统,第二部可辐射厂房内所有的1~8#罩式退火炉、13#退火 炉、14#高温炉、15#、16#氮基炉、煤气净化站及能源计量系统 等所有生产设施。因煤气净化站点离连续退火炉控制室有200 米距离,若微弱信号衰减较大,准备采用MOX转换器,光纤电缆传 输方式,来保证信号的稳定性和可靠性,最后在连续退火炉控制站 提供数据能上新冶钢内部网络,并向有关单位进行OPC发布。 让热处理厂全部测量信息达到共享和远程控制,随着自动化程度 的提高,从人力、物力计算,生产成本可大幅度下降,产品质量控 制可得到保证。 一、改造方案设计: 1.1 热处理退火炉改造方框图〔见第2页〕 第1页1.2改造测量点统计: 热处理区域测量点规格统计 5
浅谈连续退火机组退火炉设备安装
浅谈连续退火机组退火炉设备安装 摘要本文简要介绍了宝钢1800连续退火机组立式退火炉的施工方法,总结了退火炉施工的要领同时提出了施工中存在的问题和改进措施。 关键词连续退火机组立式退火炉设备安装 1.项目概况 宝钢1800连续退火机组是由日本新日铁设计,是目前最先进的冷轧带钢退火机组之一。该机组生产带钢宽度最大为1850mm,厚度为0.45~2.0毫米,设计年产量为96.46万吨,主要应用于国内的汽车板市场。 宝钢1800连续退火机组由入口段,炉子段,出口段三部分组成。炉子段有7个炉段,9个炉室,分别是:预热段(带钢温度170~220度)PHF炉;加热段(带钢温度750~870度)HF-1炉和HF-2炉;均热段(带钢温度750~870度)SF炉;缓冷段(带钢温度675~690度)SCF炉;一次冷却段(带钢温度675~400度)1C炉、过时效段(带钢温度370~400度)OA-1炉和OA-2炉;二次冷却段(带钢温度370~160度)2C炉和一套水淬系统,带钢经过炉子段的连续退火和淬水冷却后,利用淬水挤干辊和热风干燥器将带钢烘干,进入到出口立式活套。炉子段全长143.685米,标高在▽-4.100~▽+29.950之间,炉子段设备重量为3600余吨,炉子段工艺钢结构为1800余吨。 工期要求:整个连退机组炉子段施工日期为12个月。 2.炉子段机械设备安装 炉子段设备安装跟通用设备安装方法有所不同,因为炉子外壳及炉内设备属于板块状分体供货,需要到现场组装,相对复杂。 退火炉主要安装设备有:炉壳、保温钉、保温棉、不锈钢内衬板、高铝布、炉辊、炉辊轴承及轴承座、炉辊马达、辐射管、电子加热管、电阻带、喷箱、风机、风道、热交换器、烟道、烟囱等设备。 下面先讲述炉子段设备和结构的安装方法。 炉子段的设备和结构应该采取交替作业的方法穿插进行,同一作业面上一般是钢结构优先于设备安装,因为钢结构框架的形成有利于设备的定位和调整。 钢结构的安装应从底层立柱开始安装,从主轧线的下部立柱和横梁开始安装,先应该安装DS(驱动侧)的结构,然后再安装WS(操作侧)的结构。(方便吊装站位,一般运货通道在WS侧)。一般可以采用先预制模板在灌浆得方法,
全氢罩式退火炉安全控制
编订:__________________ 审核:__________________ 单位:__________________ 全氢罩式退火炉安全控制 Deploy The Objectives, Requirements And Methods To Make The Personnel In The Organization Operate According To The Established Standards And Reach The Expected Level. Word格式 / 完整 / 可编辑
文件编号:KG-AO-3471-53 全氢罩式退火炉安全控制 使用备注:本文档可用在日常工作场景,通过对目的、要求、方式、方法、进度等进行具体的部署,从而使得组织内人员按照既定标准、规范的要求进行操作,使日常工作或活动达到预期的水平。下载后就可自由编辑。 1概述 强对流全氢罩式退火炉(以下简称全氢罩式炉)是在原低氢罩式炉的基础上于70年代发展起来的,具有低能耗、高效率、退火产品品质优良等众多特点。国外在1984年开始大量应用于宽带钢卷的退火,至今已有近千座全氢罩式炉在世界各地建成。在奥地利的奥钢联、德国的克勒克纳冷轧厂和蒂森冷轧厂、美国的l-TV钢厂和USX钢厂等钢铁企业中,都可以见到正在工作的全氢罩式炉。 直到80年代末、90年代初,全氢罩式炉这项先进的生产工艺才随着国外生产工艺、控制技术的成熟逐步引进到国内,并迅速得到推广。国内已有鞍钢、武钢、本钢、上海益昌冷轧薄板厂、海南鹏达冷轧薄板厂等单位先后引进、建成了全氢罩式炉,生产、使
用情况良好。近年建设或改造的冷轧薄板厂正在大量采用全氢罩式炉,原有的低氢罩式炉正面临被全氢罩式炉替代的局面。 全氢罩式炉的安全性是至关重要的,这主要是由干在退火过程中采用了易燃、易爆的氢气充当退火产品的保护气体和热传导体,稍有不慎即有可能发生着火或爆炸事故。如果没有可靠的安全保障措施,即控制系统没有完善的控制策略,不仅全氢罩式炉的生产不能进行,而且还有破坏整个生产设施的可能。本文针对全氢罩式炉保护气体应用的安全性,介绍全氢保护气体控制过程的安全控制策略,以增强对这-问题的认识。 2全氢罩式炉设备及工艺过程简介 全氢罩式炉是用来消除由冷轧变形而使带钢产生的内应力的一种处理装置。通过使带钢升温、保温、降温的过程进行带钢的再结晶退火。 一座全氢罩式炉的基本设备包括: (1)一个带有底部循环风机的炉台及其附属介质
退火炉工作计划
昆钢镀锌彩涂工程镀锌机组退火炉 施工方案 编制:雍雄文审核:批准: 中国第十九冶昆明公司机装昆明工程处 2003年12月10日 目录 一、工程概况.........................................................2 二、编制依据 (2) 三、工程特点............................................................2 四、过程内容 (3) 五、施工工艺流程......................................................3 六、主要技术措施 (4) 七、施工工期安排.................................................9 八、人工计划......................................................9 九、机具计划.........................................................10 十、材料计划 (10) 十一、质量保证措施 (11) 十二、安全及文明施工 (11) 一、工程概况 退火炉是昆钢镀锌机组的一个主要设备,其组成主要为炉子支撑钢结构、炉体及管道系 统等。其中炉体沿长度方向分为五段,即预热段(phs)、无氧化加热段(nof)、辐射管加热 和均热段(rth)、喷射冷却段(ghs)、转向段(tds)。管道系统包括冷却水管道、压缩空气 管道、氮气管道、nh保护气体管道、助燃空气管道、cog煤气管道和排烟系统管道。设备制 作安装量约为700t。 二、编制依据 1、《钢结构制作、安装施工规程》(yb9254-95); 2、《钢结构工程施工质量验收规范》 (gb50205-2001); 3、《冶金机械设备安装工程施工验收规范—液压、气动及润滑系统》(ybj207-85); 4、《冶金机械设备安装工程施工验收规范—轧钢设备》—(yb9249-93) 5、《冶金机械 设备安装工程施工验收规范—通用规定》—(ybj201-83) 6、甲方提供的施工图纸、技术资 料及设计变更; 7、我方在类似钢结构安装工程上积累的经验,以及现有的技术力量和施工装备。 三、工程特点: 1、施工任务重。该项目包括了炉子设备及炉体钢结构的安装、炉子支撑钢结构及炉子所 有管道系统的制作安装。设备安装量为700t,制作量为300t。 2、施工难度大。炉子施工是 一个系统工程,需各工种密切配合,而施工较小,给施工组织带来了很大难度。 3、施工工期短。根据土建施工、到图时间及设备到货情况,预计12月才能进行钢结构 制作。到4月1日点火烘炉,施工工期不足5个月,施工工期很短。 四、工程内容 五、施工工艺流程(如下图) 六、主要技术措施 1、施工前的准备 1)、安装前,应按设备、构件明细表核对进场的设备、构件进行检查,核查质量证明 书、设计更改文件及交工所必需的技术资料。 2 )、安装前应清除附在设备表面的灰尘、油污和泥土等杂物,钢构件的柱、梁、支撑等 主要构件安装就位后应立即进行校正、固定,对不能形成稳定空间体系的构件应进行临时加
燃气台车式自动控制退火炉维护与操作手册(标准版)
( 安全管理 ) 单位:_________________________ 姓名:_________________________ 日期:_________________________ 精品文档 / Word文档 / 文字可改 燃气台车式自动控制退火炉维护与操作手册(标准版) Safety management is an important part of production management. Safety and production are in the implementation process
燃气台车式自动控制退火炉维护与操作手 册(标准版) 操作说明 一、点炉前准备 1.注意事项 (1)检查炉前轨道上是否有异物,如有应及时清除。 (2)检查各限位开关是否复位正常。 (3)检查炉体周围是否有与生产无关杂物,如有应及时清除。 (4)进入炉内观察炉内是否有异物,如有应及时清理,观察各烧嘴内部是否有异物或结焦,如有应及时清理。 (5)检查氮气总阀和分阀是否已经开启。 (6)检查各气动双位阀是否处于关闭状态。 2.送电
(1)打开控制柜,合总电源空开,观察总电压表显示是否380V 左右。 (2)观察各智能仪表是否显示正常。 (3)开启各烧嘴控制器电源,启动“点火”按钮后迅速进入炉内观察烧嘴内有无高压点火火花,如无火花应及时请维修工进行检修,没有检修切不可进入下一步。 3.进料 (1)开启炉门至限位动作,按压“炉门开”按钮时炉门应无动作。 (2)启动“台车进”按钮至限位动作,再次按压“台车进”按钮台车应无动作。 (6)启动“炉门关”按钮至限位动作,再次按压“炉门关”按钮炉门应无动作。 4.参数设定 (1)温控参数,在智能仪表上首先按向左键选择所要修改的参数位置,然后按向上键或向下键修改参数至工艺要求的设定温度。
全氢罩式退火炉安全控制
编号:SM-ZD-25258 全氢罩式退火炉安全控制Organize enterprise safety management planning, guidance, inspection and decision-making, ensure the safety status, and unify the overall plan objectives 编制:____________________ 审核:____________________ 时间:____________________ 本文档下载后可任意修改
全氢罩式退火炉安全控制 简介:该安全管理资料适用于安全管理工作中组织实施企业安全管理规划、指导、检查和决策等事项,保证生产中的人、物、环境因素处于最佳安全状态,从而使整体计划目标统一,行动协调,过程有条不紊。文档可直接下载或修改,使用时请详细阅读内容。 1概述 强对流全氢罩式退火炉(以下简称全氢罩式炉)是在原低氢罩式炉的基础上于70年代发展起来的,具有低能耗、高效率、退火产品品质优良等众多特点。国外在1984年开始大量应用于宽带钢卷的退火,至今已有近千座全氢罩式炉在世界各地建成。在奥地利的奥钢联、德国的克勒克纳冷轧厂和蒂森冷轧厂、美国的l-TV钢厂和USX钢厂等钢铁企业中,都可以见到正在工作的全氢罩式炉。 直到80年代末、90年代初,全氢罩式炉这项先进的生产工艺才随着国外生产工艺、控制技术的成熟逐步引进到国内,并迅速得到推广。国内已有鞍钢、武钢、本钢、上海益昌冷轧薄板厂、海南鹏达冷轧薄板厂等单位先后引进、建成了全氢罩式炉,生产、使用情况良好。近年建设或改造的冷轧薄板厂正在大量采用全氢罩式炉,原有的低氢罩式炉正面临被全氢罩式炉替代的局面。
退火炉各项操作注意事项
1、镀锌退火炉气密性检测操作 (1)镀锌退火炉第一次投入运行前或大修后再投入运行前应进行气密性检测操作。 (2)确认检测可用的压缩空气、氮气等铺助设备处于完好状态,随时可以启动。 (3)将加热炉的出口、入口用盲板封死,人孔、炉盖安装并紧固,炉体放散阀密封好,所有法兰处的螺栓紧固好。 (4)确认退火炉的气体检测孔、测温热电偶、板温计孔处于密封状态,并切断退火炉所有进气管道。 (5)准备好足够的检测工具如:U型玻璃水柱压力计、电焊机、洗衣粉、喷壶、刷子、记号笔、密封胶等。 2、检测操作方法 (1)打开气源,将检测用气送至退火炉炉膛内,并通过U型玻璃水柱压力计控制气源的进气量使炉膛压力控制在 1500Pa-5000Pa。 (2)在被检测部位采用涂刷和喷洒洗衣粉水的方法进行检测,重点是各密封部位、焊缝,并用记号笔标注。 (3)在第一轮检测结束后,停止检测和供气,处理泄露点,以上处理完毕后进行第二轮检测,方法与上面相同,直到达到退火
炉密封要求为止。 (4)镀锌退火炉密封性在1000Pa的压力下保持30分钟不低于200Pa,如达不到这一要求,还要进行继续进行检测。 3、点火操作 (1)对煤气管道的密封性进行检查,对发现泄漏处进行处理,重点是各处焊缝和法兰连接处以及各煤气阀门。 (2)对管道内的空气用氮气进行充分置换,然后用煤气对管道内的氮气进行充分置换,置换完毕检查各处置换气体阀门开关状态。 (3)先开启排烟风机5-10分钟在开启助燃风机,然后开启煤气主管电磁阀,助燃风主管压力6Mpa左右,煤气主管压力5Mpa-8Mpa 左右,煤气、助燃风支管上的手动调节阀的开度已定,请不要乱动,否则影响正常空燃比。 (4)点火时在退火炉头端或尾端点火,有连续的火焰喷出即为点火成功。 (5)如果某个烧嘴连续两次点火不成功的话,请检查烧嘴,不要盲目点火,以免损坏电气、烧嘴元件。 3、烘炉操作
全氢罩式退火炉安全控制
全氢罩式退火炉安全控 制 集团企业公司编码:(LL3698-KKI1269-TM2483-LUI12689-ITT289-
全氢罩式退火炉安全控制 1概述 强对流全氢罩式退火炉(以下简称全氢罩式炉)是在原低氢罩式炉的基础上于70年代发展起来的,具有低能耗、高效率、退火产品品质优良等众多特点。国外在1984年开始大量应用于宽带钢卷的退火,至今已有近千座全氢罩式炉在世界各地建成。在奥地利的奥钢联、德国的克勒克纳冷轧厂和蒂森冷轧厂、美国的l-TV钢厂和USX钢厂等钢铁企业中,都可以见到正在工作的全氢罩式炉。 直到80年代末、90年代初,全氢罩式炉这项先进的生产工艺才随着国外生产工艺、控制技术的成熟逐步引进到国内,并迅速得到推广。国内已有鞍钢、武钢、本钢、上海益昌冷轧薄板厂、海南鹏达冷轧薄板厂等单位先后引进、建成了全氢罩式炉,生产、使用情况良好。近年建设或改造的冷轧薄板厂正在大量采用全氢罩式炉,原有的低氢罩式炉正面临被全氢罩式炉替代的局面。 全氢罩式炉的安全性是至关重要的,这主要是由干在退火过程中采用了易燃、易爆的氢气充当退火产品的保护气体和热传导体,稍有不慎即有可能发生着火或爆炸事故。如果没有可靠的安全保障措施,即控制系统没有完善的控制策略,不仅全氢罩式炉的生产不能进行,而且还有破坏整个生产设施的可能。本文针对全氢罩式炉保护气体应用的安全
性,介绍全氢保护气体控制过程的安全控制策略,以增强对这-问题的认识。 2全氢罩式炉设备及工艺过程简介 全氢罩式炉是用来消除由冷轧变形而使带钢产生的内应力的一种处理装置。通过使带钢升温、保温、降温的过程进行带钢的再结晶退火。 一座全氢罩式炉的基本设备包括: (1)一个带有底部循环风机的炉台及其附属介质供给管路。 (2)一个底部敞开、其余封闭焊接成整体的保护罩(以下简称内罩)。将它扣在炉台上即与炉台构成一个封闭的小空问(以下简称退火空间),退火带钢就置于退火空间之中。在退火过程中,退火空间即充满纯氢气以保护带钢在高温下不至干氧化。 (3)一个制成罩形的加热装置(以下简称加热罩)。加热罩扣在内罩之上,两罩之间形成一个燃烧室,燃料在此燃烧,热量通过内罩传递到退火空间内。 (4)一个制成罩形的带冷却风机的冷却装置(以下简称冷却罩)。 (5)一套快冷装置。这种装置有两种,一种为在冷却罩内向内罩喷水的喷淋冷却装置,一种为将保护气体循环通过换热器进行快冷的底部循环快冷装置。 (6)一套全氢罩式炉过程控制系统。 全氢罩式炉一个生产周期包括:装带卷、扣内罩;退火空间冷密封试验;氮气吹扫;扣加热罩加热;带钢保温;退火空间热密封试验;加
退火炉纠偏装置技术改造方案探析
退火炉纠偏装置技术改造方案探析 发表时间:2017-11-02T10:18:54.427Z 来源:《基层建设》2017年第21期作者:刘凯[导读] 摘要:连续退火炉带钢跑偏问题的发生,容易造成工厂生产的重大事故,应予以重视。 广东广云新材料科技股份有限公司广东广州 510000 摘要:连续退火炉带钢跑偏问题的发生,容易造成工厂生产的重大事故,应予以重视。本文结合具体工程实例,从退火炉炉内跑偏原因分析入手,详细阐述了机组纠偏装置技术的改造方案,旨在提高纠偏装置的防跑偏效果,以供参考借鉴。 关键词:退火炉;带钢跑偏;改造;方案 带钢跑偏问题在连续退火炉的运行中发生率较高,由于跑偏故障给正常生产带来极大的影响,因此普遍使用纠偏装置来防治炉内的带钢跑偏。在为了达到理想的防跑偏效果,在退火炉的设计中,要充分考虑纠偏装置的合理配置,采取有效的改造措施进一步提升退火炉的纠偏能力,才能确保机组稳定、高效的运行。 1 工程简介 某厂退火炉分为预热、加热(Ⅰ、Ⅱ段)、均热、缓冷、闪冷、过时效、二冷、终冷共8段,带钢总长2300m。为防止带钢在炉内跑偏,保证机组稳定运行,实现带钢动态对中控制,除预热段外,炉内每段都设有一套双辊纠偏装置,加热段纠偏配置如图1所示。 2 炉内跑偏原因分析 自投产以来,在炉内一直存在带钢跑偏的问题,尤其是在加热段4#纠偏辊前跑偏尤为严重。作为目前国内少数能够生产2000mm宽度带钢的连续退火机组之一,承担了生产和开发极限宽规格冷轧产品的重任。随着极限宽薄产品订单量的增加,跑偏问题日益凸显,严重影响极限宽规格产品的产量和质量,也制约着产线的稳定运行和产能释放。频繁的跑偏降速容易引起炉内温度的剧烈波动,致使带钢发生瓢曲现象,甚至导致擦炉墙、断带等重大事故的发生。 退火炉内带钢跑偏的主要影响因素按照重要程度总结起来大致如下:(1)来料的板型,特别是单边浪或四分之一浪; (2)炉辊的安装精度,包括水平度、垂直度等; (3)炉辊的辊型和粗糙度; (4)张力控制的影响,包括实测张力是否准确,速度或张力设定值变化时,张力控制器能否及时响应等; (5)加热段辐射管的工作状态,尽量避免带钢两侧加热不均; (6)纠偏单元的工作状态等其他因素。 而作为退火炉的初始段,在预热段与加热段交汇区域,由于冷态带钢入炉进入加热段后温度变化大,内应力释放剧烈,而且冷态带钢在与炉辊接触时会吸收炉辊的热量,使炉辊与带钢接触部位的温度低于两端,从而导致炉辊的实际凸度低于初始凸度。再考虑到原料卷板型影响因素,因而预热段到加热段温度场急剧变化区域是带钢跑偏比较严重的部位。而原设计炉内第一个双辊纠偏位于加热段17#、18#辊处,也就意味着带钢入炉后近300m的带钢是否跑偏仅靠炉辊自纠偏能力和来料带钢板型来保证。理论上炉辊的凸度、粗糙度越大对抑制带钢跑偏的效果越好,但是大凸度易造成带钢热瓢曲风险,粗糙度增大的同时会影响带钢表面质量。退火炉炉辊凸度、粗糙度的选择既要满足宽幅带钢的生产需求,又要平衡窄带钢生产的要求,一般不能轻易调整。 为有效提升退火炉的纠偏能力,尽可能降低炉内带钢跑偏降速次数,提高生产线稳定运行速度,经过反复论证,结合长期积累的跑偏统计数据,在保证炉内辊系安装精度和张力控制稳定的基础上,计划将退火炉加热段9#炉辊改造为单辊型纠偏辊。 3 技术改造方案 退火炉原设计选用的纠偏装置为EMG公司板带对中系统,为双辊纠偏方式。主要由电感式测量传感器、数字控制器、电动缸几部分构成。该系统是一个连续的闭环调节系统,由炉内电感式传感器连续地测量行进板带的位置变化,将板带的位置偏差信号输入到数字控制器,电控系统的输出与电动缸相连。电动缸带动纠偏辊架进行左右移动或摆动,使板带侧向移动,以调整跑偏板带回到预定的中心线上,实现板带自动对中功能(见图2、图3),其系统工作稳定、故障率低。
退火炉工艺参数
博兴远大板业交流汇报材料 12月27日在张厂长的带领下,我厂夏汝滨、孔庆节、郭军、罗威等到博兴县开发区山东远大板业科技有限公司交流考察,参观了解了远大板业生产线,特别是了解了其连续退火生产线的相关参数。具体情况如下: 一、远大板业基本情况 山东远大板业科技有限公司建有浅槽紊流式酸洗机组两条,年产量120万吨;中国一重1420五连轧机组一条,年产80万吨;1250可逆轧机机组一条,年产15万吨;1250连续退火机组一条,年产30万吨;1250热镀锌机组一条,年产20万吨。2012年其连轧生产约20万吨,质量较稳定,效益尚可。连退机组生产约2000吨,产品划伤严重,判断炉辊已经结瘤,试验中。镀锌机组生产约5000吨,亏损较明显。 二、远大连续退火机组情况 远大连续退火生产线,年产能力30万吨。中国一重设计制作设备,产品规格:带钢厚度0.3-2.0mm,宽度700-1250,主要产品类别有碳素结构钢、优质碳素结构钢、低合金钢、中低牌号钢、高强钢等。主要用途:远大冷板可用于化工、染料、油类等包装用桶材料,用于家电的各种零部件的加工和生产,摩托的油缸、车门、底座及其它零部件的生产,农用车的车体、通风管道,车型建筑、防静电地板的面板、防盗门面板、大型除尘器内部栅板,自行车把手,五金材料,机械加工等行业。
该连续退火生产线的设备主要有:双开卷机、双切剪、窄搭接焊机、电解清洗装置、立式活套、立式退火炉、平整机、拉伸弯曲矫直机、双塔式圆盘剪、废边卷取机、静电涂油机、出口剪及双卷取机等。该机组采用全辐射立式炉连续退火技术,配备完整的加热冷却段、炉内张力和温度精确设定,保证带钢均匀退火,实现了从冷轧后钢卷到成品的连续化生产。即核心是通过退火工艺消除冷轧后硬化,达到所需要钢板性能。 主要参数: 工艺速度:180m/min(max) 退火炉参数: 预热炉长度:40 m 加热段温度:850℃(max) 加热段板温:780℃(max) 加热段长度:180 m 均热段长度:100 m 快冷炉长度:40 m 快冷炉带钢降温速度:50~70℃/s 时效炉长度:360 m 终冷长度:40 m 终冷炉带钢降温速度:50~70℃/s 钢带出炉温度:180℃(max) 钢带出水淬温度:70℃(max)