零件的结构工艺性分析
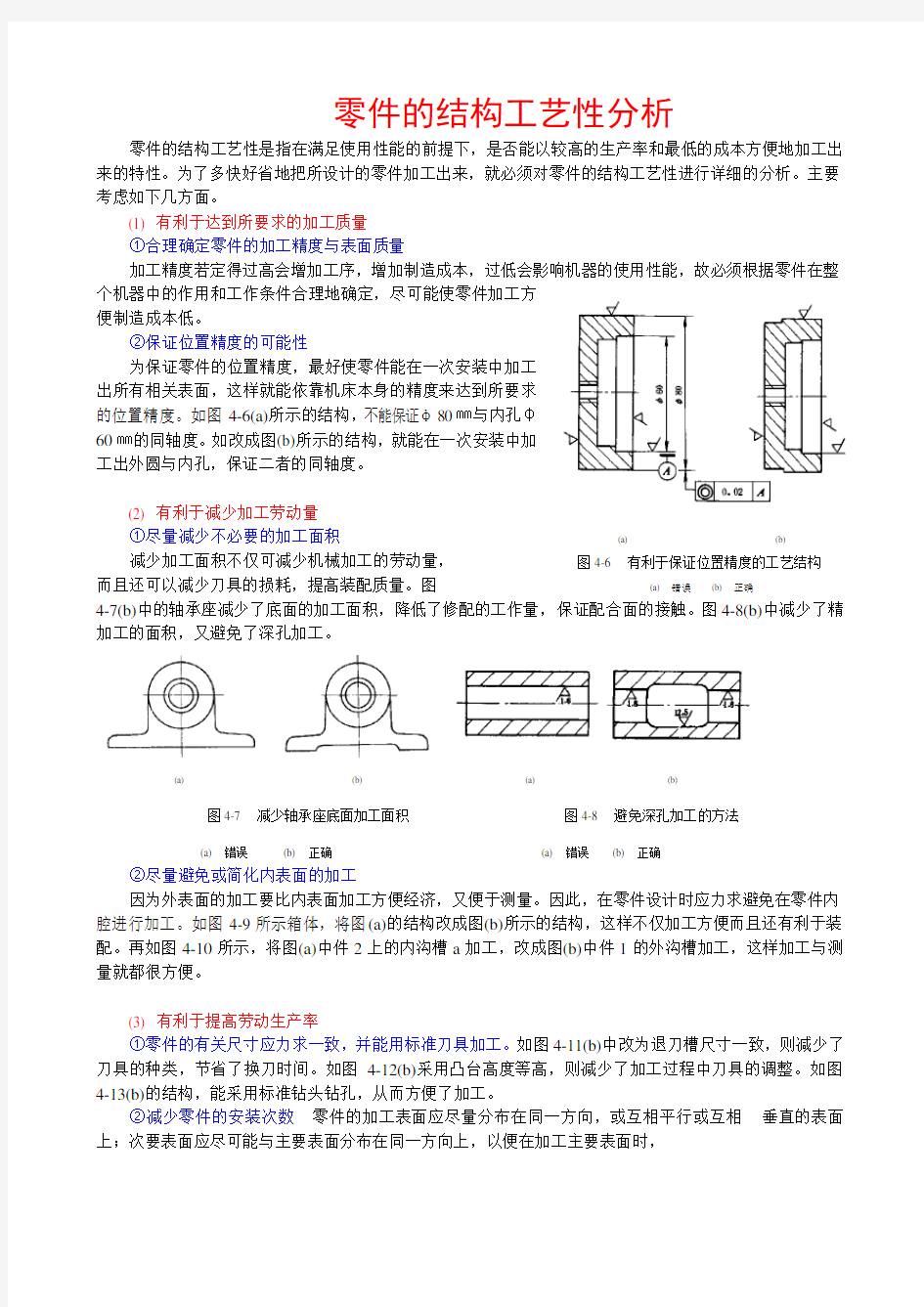
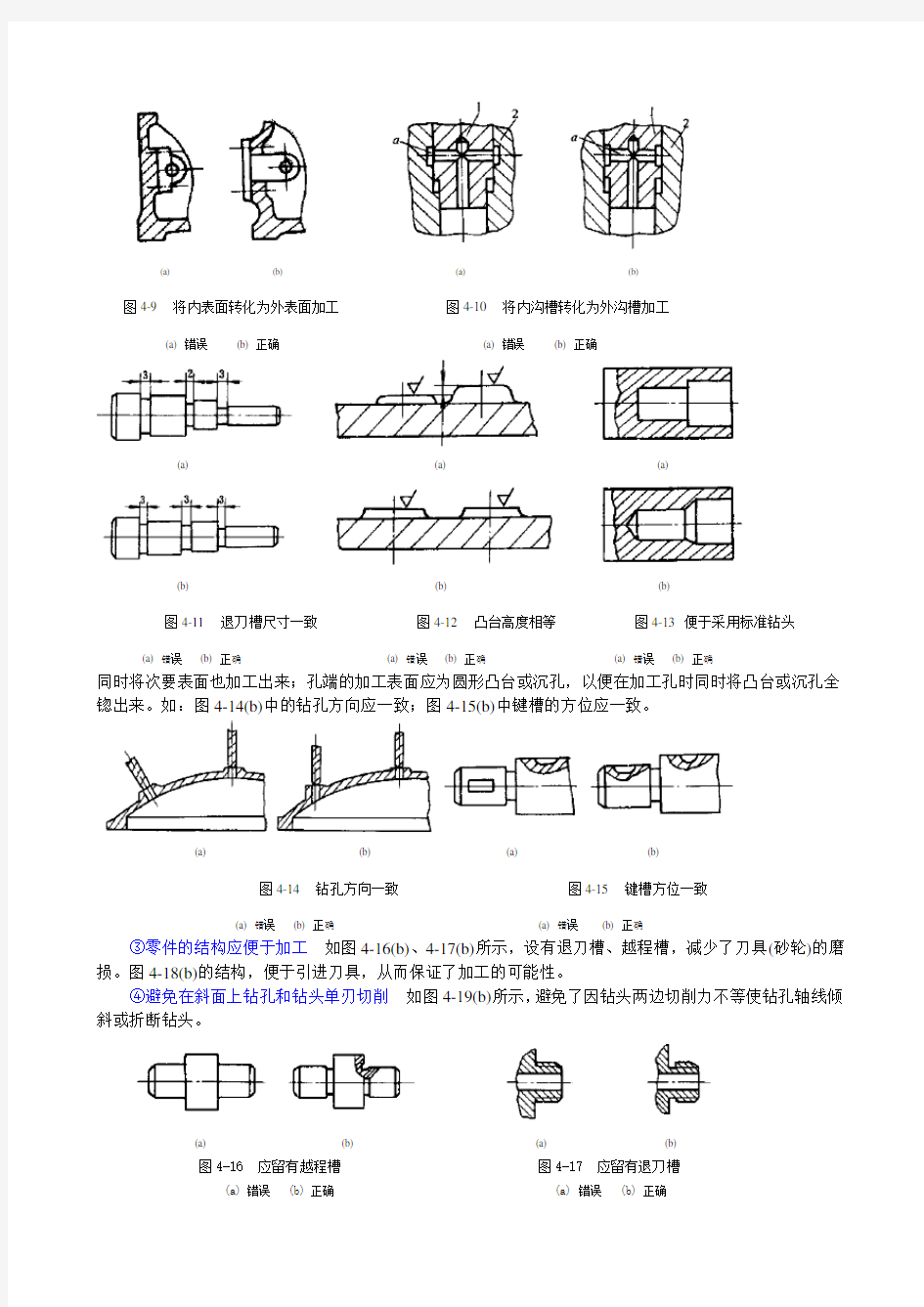
零件的结构工艺性分析
零件的结构工艺性是指在满足使用性能的前提下,是否能以较高的生产率和最低的成本方便地加工出来的特性。为了多快好省地把所设计的零件加工出来,就必须对零件的结构工艺性进行详细的分析。主要考虑如下几方面。
(1) 有利于达到所要求的加工质量
①合理确定零件的加工精度与表面质量
加工精度若定得过高会增加工序,增加制造成本,过低会影响机器的使用性能,故必须根据零件在整个机器中的作用和工作条件合理地确定,尽可能使零件加工方
便制造成本低。
②保证位置精度的可能性
为保证零件的位置精度,最好使零件能在一次安装中加工
出所有相关表面,这样就能依靠机床本身的精度来达到所要求
的位置精度。如图4-6(a)所示的结构,不能保证φ80㎜与内孔φ
60㎜的同轴度。如改成图(b)所示的结构,就能在一次安装中加
工出外圆与内孔,保证二者的同轴度。
(2) 有利于减少加工劳动量
①尽量减少不必要的加工面积(a) (b)
减少加工面积不仅可减少机械加工的劳动量,图4-6 有利于保证位置精度的工艺结构
而且还可以减少刀具的损耗,提高装配质量。图(a) 错误(b) 正确
4-7(b)中的轴承座减少了底面的加工面积,降低了修配的工作量,保证配合面的接触。图4-8(b)中减少了精加工的面积,又避免了深孔加工。
(a) (b) (a) (b)
图4-7 减少轴承座底面加工面积图4-8 避免深孔加工的方法
(a) 错误(b) 正确(a) 错误(b) 正确
②尽量避免或简化内表面的加工
因为外表面的加工要比内表面加工方便经济,又便于测量。因此,在零件设计时应力求避免在零件内腔进行加工。如图4-9所示箱体,将图(a)的结构改成图(b)所示的结构,这样不仅加工方便而且还有利于装配。再如图4-10所示,将图(a)中件2上的内沟槽a加工,改成图(b)中件1的外沟槽加工,这样加工与测量就都很方便。
(3) 有利于提高劳动生产率
①零件的有关尺寸应力求一致,并能用标准刀具加工。如图4-11(b)中改为退刀槽尺寸一致,则减少了刀具的种类,节省了换刀时间。如图4-12(b)采用凸台高度等高,则减少了加工过程中刀具的调整。如图4-13(b)的结构,能采用标准钻头钻孔,从而方便了加工。
②减少零件的安装次数零件的加工表面应尽量分布在同一方向,或互相平行或互相垂直的表面上;次要表面应尽可能与主要表面分布在同一方向上,以便在加工主要表面时,
(a) (b) (a) (b)
图4-9 将内表面转化为外表面加工图4-10 将内沟槽转化为外沟槽加工
(a) 错误(b) 正确(a) 错误(b) 正确
(a) (a) (a)
(b) (b) (b)
图4-11 退刀槽尺寸一致图4-12 凸台高度相等图4-13 便于采用标准钻头
(a) 错误(b) 正确(a) 错误(b) 正确(a) 错误(b) 正确
同时将次要表面也加工出来;孔端的加工表面应为圆形凸台或沉孔,以便在加工孔时同时将凸台或沉孔全锪出来。如:图4-14(b)中的钻孔方向应一致;图4-15(b)中键槽的方位应一致。
(a) (b) (a) (b)
图4-14 钻孔方向一致图4-15 键槽方位一致
(a) 错误(b) 正确(a) 错误(b) 正确
③零件的结构应便于加工如图4-16(b)、4-17(b)所示,设有退刀槽、越程槽,减少了刀具(砂轮)的磨损。图4-18(b)的结构,便于引进刀具,从而保证了加工的可能性。
④避免在斜面上钻孔和钻头单刃切削如图4-19(b)所示,避免了因钻头两边切削力不等使钻孔轴线倾斜或折断钻头。
(a) (b) (a) (b)
图4-16 应留有越程槽图4-17 应留有退刀槽
(a) (b) (a) (b)
4-18 钻头应能接近加工表面图4-19 避免在斜面上钻孔和钻头单刃切削
(a) 错误(b) 正确(a) 错误(b) 正确
⑤便于多刀或多件加工如图4-20(b)所示,为适应多刀加工,阶梯轴各段长度应相似或成整数倍;直径尺寸应沿同一方向递增或递减,以便调整刀具。零件设计的结构要便于多件加工,如图4-21所示,图(b)结构可将毛坯排列成行便于多件连续加工。
(a) (b)
图4-20 便于多刀加工
(a) 错误(b) 正确
(a) (b)
图4-21 便于多件连续加工
(a) 错误(b) 正确
装配结构工艺性分析
一、分析研究产品的零件图样和装配图样 在编制零件机械加工工艺规程前,首先应研究零件的工作图样和产品装配图样,熟悉该产品的用途、性能及工作条件,明确该零件在产品中的位置和作用;了解并研究各 项技术条件制订的依据,找出其主要技术要求和技术关键,以便在拟订工艺规程时采用适当的措施加以保证。 工艺分析的目的,一是审查零件的结构形状及尺寸精度、相互位置精度、表面粗糙度、材料及热处理等的技术要求是否合理,是否便于加工和装配;二是通过工艺分析,对零件的工艺要求有进一步的了解,以便制订出合理的工艺规程。 如图3-8 所示的汽车钢板弹簧吊耳,使用时,钢板弹簧与吊耳两侧面是不接触的,所以吊耳内侧的粗糙度可由原来的设计要求R a3.2 μm 建议改为R a12.5 μ m. 。这样在铣削时可只用粗铣不用精铣,减少
铣削时间。 再如图3-9 所示的方头销,其头部要求淬火硬度55~60HRC ,所选用的材料为T 8A ,该零件上有一孔φ2H7 要求在装配时配作。由于零件长度只有15mm ,方头部长度仅有4mm ,如用T 8A 材料局部淬火,势必全长均被淬硬,配作时,φ 2H7 孔无法加工。若建议材料改用20Cr 进行渗碳淬火,便能解决问题。 二、结构工艺性分析 零件的结构工艺性是指所设计的零件在满足使用要求的前提下,制造的可行性和经济性。下面将从零件的机械加工和装配两个方面,对零件的结构工艺性进行分析。 (一)机械加工对零件结构的要求 1 .便于装夹零件的结构应便于加工时的定位和夹紧,装夹次数要少。图3 -10a 所示零件,拟用顶尖和鸡心夹头装夹,但该结构不便于装夹。若改为图b 结构,则可以方便地装置夹头。 2 .便于加工零件的结构应尽量采用标准化数值,以便使用标准化刀具和量具。同时还注意退刀和进刀,易于保证加工精度要求,减少加工面积及难加工表面等。表3-8b 所示为便于加工的零件结构示例。
分析零件图——零件图的审查
分析零件图——零件图的审查 在制订零件的机械加工工艺规程之前,对零件进行工艺性分析,以及对产品零件图提出修改意见,是制订工艺规程的一项重要工作。 首先应熟悉零件在产品中的作用、位置、装配关系和工作条件,搞清楚各项技术要求对零件装配质量和使用性能的影响,找出主要的和关键的技术要求,然后对零件图样进行分析。 (1) 检查零件图的完整性和正确性 在了解零件形状和结构之后,应检查零件视图是否正确、足够,表达是否直观、清楚,绘制是否符合国家标准,尺寸、公差以及技术要求的标注是否齐全、合理等。 (2) 零件的技术要求分析 零件的技术要求包括下列几个方面:加工表面的尺寸精度;主要加工表面的形状精度;主要加工表面之间的相互位置精度;加工表面的粗糙度以及表面质量方面的其它要求;热处理要求;其它要求(如动平衡、未注圆角或倒角、去毛刺、毛坯要求等)。 要注意分析这些要求在保证使用性能的前提下是否经济合理,在现有生产条件下能否实现。特别要分析主要表面的技术要求,因为主要表面的加工确定了零件工艺过程的大致轮廓。 (3) 零件的材料分析 即分析所提供的毛坯材质本身的机械性能和热处理状态,毛坯的铸造品质和被加工部位的材料硬度,是否有白口、夹砂、疏松等。判断其加工的难易程度,为选择刀具材料和切削用量提供依据。所选的零件材料应经济合理,切削性能好,满足使用性能的要求。 (4) 合理的标注尺寸 ①零件图上的重要尺寸应直接标注,而且在加工时应尽量使工艺基准与设计基准重合,并符合尺寸链最短的原则。如图4-1中活塞环槽的尺寸为重要尺寸,其宽度应直接注出。
②零件图上标注的尺寸应便于测量,不要从轴线、中心线、假想平面等难以测量的基准标注尺寸。如图4-2中轮毂键槽的深度,只有尺寸c的标注才便于用卡尺或样板测量。 ③零件图上的尺寸不应标注成封闭式,以免产生矛盾。如图4-3所示,已标注了孔距尺寸a±δ和角度α±δα,则则x、y轴的坐标尺寸就不能随便标注。有时为了方便加工,可按尺寸链计算出来,并标注在圆括号内,作为加工时的参考尺寸。 ④零件上非配合的自由尺寸,应按加工顺序尽量从工艺基准注出。如图4-4的齿轮轴,图(a)的表示方法大部分尺寸要经换算,且不能直接测量。而图(b) 图4-1 直接标注重要尺寸图4-2 键槽深度的标注图4-3 孔中心距的标注 (a) (b)
零件的工艺性分析
零件的工艺性分析 一、分析研究产品的零件图样和装配图样在编制零件机械加工工艺规程前,首先应研究零件的工作图样和产品装配图样,熟悉该产品的用途、性能及工作条件,明确该零件在产品中的位置和作用;了解并研究各项技术条件制订的依据,找出其主要技术要求和技术关键,以便在拟订工艺规程时采用适当的措施加以保证。工艺分析的目的,一是审查零件的结构形状及尺寸精度、相互位置精度、表面粗糙度、材料及热处理等的技术要求是否合理,是否便于加工和装配;二是通过工艺分析,对零件的工艺要求有进一步的了解,以便制订出合理的工艺规程。 如图3-8 所示的汽车钢板弹簧吊耳,使用时,钢板弹簧与吊耳两侧面是不接触的,所以吊耳内侧的粗糙度可由原来的设计要求R a3.2 μ m 建议改为R a12.5 μ m. 。这样在铣削时可只用粗铣不用精铣,减少铣削时间。 再如图3-9 所示的方头销,其头部要求淬火硬度55~60HRC ,所选用的材料为T 8A ,该零件上有一孔φ 2H7 要求在装配时配作。由于零件长度只有15mm ,方头部长度仅有4mm ,如用T 8A 材料局部淬火,势必全长均被淬硬,配作时,φ 2H7 孔无法加工。若建议材料改用20Cr
进行渗碳淬火,便能解决问题。 二、结构工艺性分析零件的结构工艺性是指所设 计的零件在满足使用要求的前提下,制造的可行性和经济性。下面将从零件的机械加工和装配两个方面,对零件的结构工艺性进行分析。(一)机械加工对零件结构的要求 1 .便于装夹零件的结构应便于加工时的定位和夹紧,装 夹次数要少。图3 -10a 所示零件,拟用顶尖和鸡心夹头装夹,但该结构不便于装夹。若改为图b 结构,则可以方便 地装置夹头。 2 .便于加工零件的结构应尽量采用标准化数值,以便使用标准化刀具和量具。同时还注意退刀和进刀,易于保证加工精度要求,减少加工面积及难加工表面等。表3-8b 所示为便于加工的零件结构示例。 3 .便于数控机床加工被加工零件的数控工艺性 问题涉及面很广,下面结合编程的可能性与方便性来作工艺性分析。 编程方便与否常常是衡量数控工艺性好坏的一个 指标。例如图3-11 所示某零件经过抽象的尺寸标注方法,若用APT 语言编写该零件的源程序,要用几何定义语句描
机械零件结构工艺性分析与工艺路线的拟定
目录 一、零件结构工艺性分析2 1. 零件的技术要求2 2.确定堵头结合件的生产类型3 二、毛坯的选择4 1.选择毛坯4 2.确定毛坯的尺寸公差4 三、定位基准的选择6 1.精基准的选择6 2.粗基准的选择6 四、工艺路线的拟定7 1.各表面加工方法的选择7 2.加工阶段的划分8 3.加工顺序的安排8 4.具体技术方案的确定9 五、工序内容的拟定10 1.工序的尺寸和公差的确定10 2.机床、刀具、夹具及量具的选择12 3.切削用量的选择及工序时间计算12 六、设计心得35 七、参考文献36
一、零件结构工艺性分析 1.零件的技术要求 1.堵头结合件由喂入辊轴和堵头焊接在一起。其中喂入辊 轴:材料为45钢。堵头:材料为Q235-A。且焊缝不得有夹渣、气孔及裂纹等缺陷。 2.零件的技术要求表:
2. 确定堵头结合件的生产类型 根据设计题目年产量为10万件,因此该左堵头结合件的生产类型为大批量生产。
二、毛坯的选择 1.选择毛坯 由于该堵头结合件在工作过程中要承受冲击载荷,为增强其的强度和冲击韧度,堵头选用锻件,材料为Q235-A,因其为大批大量生产,故采用模锻。喂入辊轴由于尺寸落差不大选用棒料,材料为45钢。 2.确定毛坯的尺寸公差 喂入辊轴: 根据轴类零件采用精轧圆棒料时毛坯直径选择可通过零件的长度和最大半径之比查的毛坯直径 206 L8.24 == R25 查表得毛坯直径为:φ55 根据其长度和直径查得端面加工余量为2。故其长度为206+2+2=210mm
堵头: 1.公差等级: 由于堵头结合件用一般模锻工艺能够达到技术要求,确定该零件的公差等级为普通级。 2.重量: 锻件重量的估算按下列程序进行: 零件图基本尺寸-估计机械加工余量-绘制锻件图-估算锻件重量。并按此重量查表确定公差和机械加工余量 据粗略估计锻件质量: 11.6f Kg M = 3.形状复杂系数: 锻件外廓包容体重量按公式:2N d h 4 M π ρ= g g 计算 293 186.5101104 7.851021.65Kg N M π -= ?????= 形状复杂系数: f 11.6 0.5421.6M S M N === 故形状复杂系数为S2(一般)级。 4.锻件材质系数: 由于该堵头材料为Q235-A 所含碳元素的质量分数分别为C=0.14%—0.22%,小于0.65% 所含合金元素的质量分数分别为Si 0.3%≤、S 0.05%≤、P 0.045%≤故合金元素总的质量分数为0.3%0.05%0.045%0.395%3%++≤<%。故该锻件的材质系数为M1级。 5.锻件尺寸公差 根据锻件材质系数和形状复杂系数查得锻件尺寸公差为 ( 2.41.2+-) 。 6.锻件分模线形状: 根据该堵头的形装特点,选择零件轴向方向的对称平面为分模面,属于平直分模线。
零件的工艺性分析
零件的工艺性分析-标准化文件发布号:(9456-EUATWK-MWUB-WUNN-INNUL-DDQTY-KII
零件的工艺性分析 如图所示为接触环零件图,材料为08钢,厚度1mm,大批量生产。制定工件冲压工艺规程,设计其模具,编制零件的加工工艺规程。 6.5+0.1-0 1.1冲压件的工艺性分析 1.1.1结构与尺寸 1、由该冲压零件图可知,该零件结构简单、规则,而且尺寸较小,使得排样时废料较少。 2、冲压件的内、外的转角无太尖锐的尖角,部分区域以圆弧过渡,减少了冲压时某些尖角出出现崩刃和过快磨损现象。 3、对于08钢材料,其悬臂宽度b=1.5mm ,厚度t=1mm ,应满足b ≥1.5t ,当板料t>1mm 时按1mm 考虑,经计算悬臂宽度满足条件;臂长l 为:3.25和 1.3均小于5倍臂宽;凹槽宽度1.65>1.5t ,最小孔径d 为1.85>0.9t ,均满足要求。 结合以上分析,该冲压件的结构与尺寸均适宜于冲压加工。 1.1.2 精度 冲压件的经济精度一般不高于IT11,查表可知,该零件的基本尺寸公差除9.4接近于IT11级外,其余尺寸均低于IT12级,也没有其他特殊的要求。分析可知可知,利用普通冲裁方式可以达到零件图样要求。
1.1.3材料 根据本次设计课题材料要求为08钢,根据附表可得金属材料的力学性能:软态,带料,抗剪强度b=255MPa,伸长率占10=38%,分析可知,此材料具有较高的弹性和良好的塑性,其冲裁加工性能较好,适合冲裁加工。 1.1.4批量 课题要求该零件需大批量生产,综上分析可知,该零件在冲压加工下操作简便, 而且劳动强度低,生产效率高,成本较低,适合冲裁加工。 结论:该零件的工艺性较好,可以冲裁加工。 1.2冲裁工艺方案的确定 1.2.1工艺方案分析与选择 根据冲压零件图,分析其形状特点,确定该零件加工包括落料,冲孔两个基本工序,分析可知由以下3种工艺方案选择: (1)先落料,再冲孔。采用单工序模生产。 (2)落料—冲孔复合冲压,采用复合模生产。 (3)冲孔—落料连续冲压,采用连续模(级进模)生产。 结合单工序模、复合模以及级进模的优缺点比较可知: 方案(1)制造时上午周期短,成本也较低,但需要两道工序,导致生产效率低,且零件平面度差。难以满足零件大批量生产的需要。 方案(2)生产效稍低,因零件的孔边距太小,导致模具强度不能保证,操作较为困难,且不能保证安全性。 方案(3)生产效率高,操作方便,安全性好,通过设计合理的模具结构和排样方案可以达到较好的零件质量和避免模具强度不够的问题。 综合以上分析,并参考相关资料,可知该零件采用级进冲裁方案较好。1.3模具确定 1.3.1模具类型 根据冲压零件的冲裁方案以及设计要求,模具应采用硬质合金模。 1.3.2操作与定位方式
冲压件工艺性分析(DOC)
一、止动件冲压件工艺性分析 1、零件材料:为Q235-A 钢,具有良好的冲压性能,适合冲裁; 2、零件结构:相对简单,有2个φ20mm 的孔;孔与孔、孔与边缘之间的距离也满足要求,最小壁厚为14mm (φ20mm 的孔与边框之间的壁厚) 3、零件精度:全部为自由公差,可看作IT14级,尺寸精度较低,普通冲裁完全能满足要求。 查表得各零件尺寸公差为: 外形尺寸:01130-、062.048-、074.060-、03.04-R 、074.060-R 内型尺寸:052.0020+ 孔中心距:60±0.37 二、冲压工艺方案的确定 完成该零件的冲压加工所需要的冲压基本性质的工序只有落料、冲孔两道工序。从工序可能的集中与分散、工序间的组合可能来看,该零件的冲压可以有以下几种方案。 方案一:落料-冲孔复合冲压。采用复合模生产。 方案二:冲孔-落料级进冲压。采用级进模生产。 方案一只需一副模具,工件的精度及生产效率都较高,工件最小壁厚14mm 大于凸凹模许用最小壁厚3.6mm--4.0mm ,模具强度好,制造难度中等,并且冲压后成品件可通过卸料板卸下,清理方便,操作简单。
方案二也只需一副模具,生产效率高,操作方便,工件精度也能满足要求,但是模具结构复杂,制造加工,模具成本较高。 结论:采用方案一为佳 三、模具总体设计 (1)模具类型的选择 由冲压工艺分析可知,采用复合模冲压,所以模具类型为复合模。(2)定位方式的选择 因为该模具采用的是条料,控制条料的送进方向采用导料板,无侧压装置。控制条料的送进步距采用挡料销定距。而第一件的冲压位置因为条料长度有一定余量,可以靠操作工目测来定。 (3)卸料、出件方式的选择 因为工件料厚为1.5mm,相对较薄,卸料力也比较小,故可采用弹性卸料。又因为是倒装式复合模生产,所以采用上出件比较便于操作与提高生产效率。 (4)导向方式的选择 为了提高模具寿命和工件质量,方便安装调整,该倒装式模采用导柱导向方式。 四、排样方案确定及材料利用率 (1)排样方式的确定及其计算 设计倒装式复合模,首先要设计条料排样图,采用直排。 方案一:搭边值取2mm和3mm(P33表2-9),条料宽度为135mm
零件结构的工艺性
零件结构的工艺性 一、零件结构工艺性概念 机械加工零件的结构工艺性 由于一般情况下切削加工的劳动耗费最多.因而零件结构的切削加工工艺性更为重要。下面将就单件小批生产中对它考虑的一般原则及实例进行简要分析。 ①尽量减少不必要的加工面积 减少加工面积不仅可减少机械加工的劳动量,而且还可以减少刀具的损耗,提高装配质量。图 2(b)中的轴承座减少了底面的加工面积,降低了修配的工作量,保证配合面的接触。图3(b)中减少了精加工的面积,又避免了深孔加工。 (a) (b) 图2 减少轴承座底面加工面积 设计零件 设计结构 选择材料 确定尺寸 使用性能:能用、好用、耐用 工艺要求:好做、好装、好修
(a) 错误(b) 正确 (a) (b) 图3 避免深孔加工的方法 (a) 错误 (b) 正确 ②尽量避免或简化内表面的加工 因为外表面的加工要比内表面加工方便经济,又便于测量。因此,在零件设计时应力求避免在零件内腔进行加工。如图4所示,将图(a)中件2上的内沟槽a加工,改成图(b)中件1的外沟槽加工,这样加工与测量就都很方便。 3、有利于提高劳动生产率 (a) (b) 图5 退刀槽尺寸一致 (a) 错误(b) 正确 ①零件的有关尺寸应力求一致,并能用标准刀具加工。如图5(b)中改为退刀槽尺寸一致,则减少了刀具的种类,节省了换刀时间。如图6(b)采用凸台高度等高,则减少了加工过程中刀具的调整。如图7(b)
的结构,能采用标准钻头钻孔,从而方便了加工。 (a) (b) 图6 凸台高度相等 (a) 错误(b) 正确 (a) (b) 图7 便于采用标准钻头 (a) 错误(b) 正确 ②减少零件的安装次数:零件的加工表面应尽量分布在同一方向,或互相平行或互相垂直的表面上;次要表面应尽可能与主要表面分布在同一方向上,以便在加工主要表面时,同时将次要表面也加工出来;孔端的加工表面应为圆形凸台或沉孔,以便在加工孔时同时将凸台或沉孔全锪出来。如:图8(b)中的钻孔方向应一致;图9(b)中键槽的方位应一致。
典型零件的机械加工工艺分析
第4章典型零件的机械加工工艺分析 本章要点 本章介绍典型零件的机械加工工艺规程制订过程及分析,主要内容如下: 1.介绍机械加工工艺规程制订的原则与步骤。 2.以轴类、箱体类、拨动杆零件为例,分析零件机械加工工艺规程制订的全过程。 本章要求:通过典型零件机械加工工艺规程制订的分析,能够掌握机械加工工艺规程制订的原则和方法,能制订给定零件的机械加工工艺规程。 §4.1 机械加工工艺规程的制订原则与步骤§4.1.1机械加工工艺规程的制订原则 机械加工工艺规程的制订原则是优质、高产、低成本,即在保证产品质量前提下,能尽量提高劳动生产率和降低成本。在制订工艺规程时应注意以下问题: 1.技术上的先进性 在制订机械加工工艺规程时,应在充分利用本企业现有生产条件的基础上,尽可能采用国内、外先进工艺技术和经验,并保证良好的劳动条件。 2.经济上的合理性 在规定的生产纲领和生产批量下,可能会出现几种能保证零件技术要求的工艺方案,此时应通过核算或相互对比,一般要求工艺成本最低。充分利用现有生产条件,少花钱、多办事。 3.有良好的劳动条件 在制订工艺方案上要注意采取机械化或自动化的措施,尽量减轻工人的劳动强度,保障生产安全、创造良好、文明的劳动条件。 由于工艺规程是直接指导生产和操作的重要技术文件,所以工艺规程还应正确、完整、统一和清晰。所用术语、符号、计量单位、编号都要符合相应标准。必须可靠地保证零件图上技术要求的实现。在制订机械加工工艺规程时,如果发现零件图某一技术要求规定得不适当,只能向有关部门提出建议,不得擅自修改零件图或不按零件图去做。 §4.1.2 制订机械加工工艺规程的内容和步骤 1.计算零件年生产纲领,确定生产类型。 2.对零件进行工艺分析 在对零件的加工工艺规程进行制订之前,应首先对零件进行工艺分析。其主要内容包括: (1)分析零件的作用及零件图上的技术要求。 (2)分析零件主要加工表面的尺寸、形状及位置精度、表面粗糙度以及设计基准等; (3)分析零件的材质、热处理及机械加工的工艺性。
零件的结构工艺性分析
零件的结构工艺性分析 零件的结构工艺性是指在满足使用性能的前提下,是否能以较高的生产率和最低的成本方便地加工出来的特性。为了多快好省地把所设计的零件加工出来,就必须对零件的结构工艺性进行详细的分析。主要考虑如下几方面。 (1) 有利于达到所要求的加工质量 ①合理确定零件的加工精度与表面质量 加工精度若定得过高会增加工序,增加制造成本,过低会影响机器的使用性能,故必须根据零件在整个机器中的作用和工作条件合理地确定,尽可能使零件加工方 便制造成本低。 ②保证位置精度的可能性 为保证零件的位置精度,最好使零件能在一次安装中加工 出所有相关表面,这样就能依靠机床本身的精度来达到所要求 的位置精度。如图4-6(a)所示的结构,不能保证φ80㎜与内孔φ 60㎜的同轴度。如改成图(b)所示的结构,就能在一次安装中加 工出外圆与内孔,保证二者的同轴度。 (2) 有利于减少加工劳动量 ①尽量减少不必要的加工面积(a) (b) 减少加工面积不仅可减少机械加工的劳动量,图4-6 有利于保证位置精度的工艺结构 而且还可以减少刀具的损耗,提高装配质量。图(a) 错误(b) 正确 4-7(b)中的轴承座减少了底面的加工面积,降低了修配的工作量,保证配合面的接触。图4-8(b)中减少了精加工的面积,又避免了深孔加工。 (a) (b) (a) (b) 图4-7 减少轴承座底面加工面积图4-8 避免深孔加工的方法 (a) 错误(b) 正确(a) 错误(b) 正确 ②尽量避免或简化内表面的加工 因为外表面的加工要比内表面加工方便经济,又便于测量。因此,在零件设计时应力求避免在零件内腔进行加工。如图4-9所示箱体,将图(a)的结构改成图(b)所示的结构,这样不仅加工方便而且还有利于装配。再如图4-10所示,将图(a)中件2上的内沟槽a加工,改成图(b)中件1的外沟槽加工,这样加工与测量就都很方便。 (3) 有利于提高劳动生产率 ①零件的有关尺寸应力求一致,并能用标准刀具加工。如图4-11(b)中改为退刀槽尺寸一致,则减少了刀具的种类,节省了换刀时间。如图4-12(b)采用凸台高度等高,则减少了加工过程中刀具的调整。如图4-13(b)的结构,能采用标准钻头钻孔,从而方便了加工。 ②减少零件的安装次数零件的加工表面应尽量分布在同一方向,或互相平行或互相垂直的表面上;次要表面应尽可能与主要表面分布在同一方向上,以便在加工主要表面时,
零件的结构工艺性分析(格式)
毕业设计(论文) 零件的结构工艺性分析 学 院 工业制造与管理学院 年 级 专 业 学 号 2 学生姓名 指导老师 刘俊蓉 2013 年 3 月
毕业论文(设计)诚信承诺书
四川科技职业学院毕业设计(论文)评审表(指导教师用)
说明:在“A、B、C、D、E”对应的栏目下划“√”四川科技职业学院毕业设计(论文)任务书
摘要 数控技术是用数字信息对机械运动和工作过程进行控制的技术,它是继传统的机械制造技术、计算机技术、现代控制技术、传感检测技术、网络通讯技术和光电技术一体的现代制造业的基础技术,具有高精度、高效率、柔性自动化等特点,对制造业实现柔性自动化、集成化和智能化起着举足轻重的作用。数控装备则是以数控技术为代表的新技术对传统制造业和新兴制造业的渗透而形成的机电一体化的产品。数控技术制造自动化的基础,是现在制造装备的灵魂核心,是国家工业和国防工业现代化的重要手段,关系到国家的战略地位,体现国家的综合水平,其水平高低和数控装备的多少是衡量一个国家工业现代化的标志。 零件的结构工艺性是指在满足使用性能的前提下,是否能以较高的生产率和最低的成本方便地加工出来的特性。为了多快好省地把所设计的零件加工出来,就必须对零件的结构工艺性进行详细的分析。机械零部件的工艺性不足是现代工业生产中提高效益、确保产品质量的关键。零部件的结构应满足在制造、维修全过程中符合科学性、可行性和经济性的要求。工艺性具有整体性、相对性和灵活性的特点。本论文就数控加工对典型的轴类零件进行的零件结构工艺性分析,主要是对零件图的分析、毛胚的选择、零件的热处理、工艺路线的制定、数控加工工艺文件的填写、数控加工过程的编写。设计合理的加工工艺过程,充分发挥数控加工的优质、高效、低成本的特点,以及对零件的加工工艺进行分析。 关键词:零件;结构;工艺性;数控加工
零件结构的工艺性说课讲解
零件结构的工艺性
零件结构的工艺性 一、零件结构工艺性概念 机械加工零件的结构工艺性 由于一般情况下切削加工的劳动耗费最多.因而零件结构的切削加工工艺性更为重要。下面将就单件小批生产中对它考虑的一般原则及实例进行简要分析。 ①尽量减少不必要的加工面积 减少加工面积不仅可减少机械加工的劳动量,而且还可以减少刀具的损耗,提高装配质量。图 2(b)中的轴承座减少了底面的加工面积,降低了修配的工作量,保证配合面的接触。图3(b)中减少了精加工的面积,又避免了深孔加工。 (a) (b) 图2 减少轴承座底面加工面积 设计零件 设计结构 选择材料 确定尺寸 使用性能:能用、好用、耐用 工艺要求:好做、好装、好修
(a) 错误 (b) 正确 (a) (b) 图3 避免深孔加工的方法 (a) 错误 (b) 正确 ②尽量避免或简化内表面的加工 因为外表面的加工要比内表面加工方便经济,又便于测量。因此,在零件设计时应力求避免在零件内腔进行加工。如图4所示,将图(a)中件2上的内沟槽a加工,改成图(b)中件1的外沟槽加工,这样加工与测量就都很方便。 3、有利于提高劳动生产率 (a) (b) 图5 退刀槽尺寸一致 (a) 错误 (b) 正确 ①零件的有关尺寸应力求一致,并能用标准刀具加工。如图5(b)中改为退刀槽尺寸一致,则减少了刀具的种类,节省了换刀时间。如
图6(b)采用凸台高度等高,则减少了加工过程中刀具的调整。如图7(b)的结构,能采用标准钻头钻孔,从而方便了加工。 (a) (b) 图6 凸台高度相等 (a) 错误 (b) 正确 (a) (b) 图7 便于采用标准钻头 (a) 错误 (b) 正确 ②减少零件的安装次数:零件的加工表面应尽量分布在同一方向,或互相平行或互相垂直的表面上;次要表面应尽可能与主要表面分布在同一方向上,以便在加工主要表面时,同时将次要表面也加工出来;孔端的加工表面应为圆形凸台或沉孔,以便在加工孔时同时将凸台或沉孔全锪出来。如:图8(b)中的钻孔方向应一致;图9(b)中键槽的方位应一致。
机械设计中零部件定位配合的工艺性分析概要
机械设计中零部件定位配合的工艺性分析3 谷莉,孟刚,曹锈鸽 (兰州城市学院培黎工程技术学院,甘肃兰州730070 摘要:在机械设计中,正确地选择定位配合的形式和确定零部件定位配合的精度,是一项重要的设计内容之一。论述了零件定位配合的类型及在零件定位配合设计中主要应考虑的因素。根据分析结论可为设计人员提供一定的参考依据。 关键词:零件;定位配合;类型;设计;因素 中图分类号:T H16文献标识码:A文章编号:1006-4414(200903-0073-03 Ana lyz i n g of the technology of parts′positi on f i x i n g i n m echan i ca l desi gn Gu L i,Meng Gang,Cao Xiu-Ge (B ailie engineering and technology school of L anzhou city college,L anzhou Gansu 730070,China Abstract:I n mechanical design courses,it is one of the most i m portant design contents t o choose the p r oper f or m and t o make sure the p recisi on of parts′positi on fixing.The types and main fact ors considering in parts′positi on fixing are discussed.The result may p r ovide the references f or designer. Key words:parts;positi on fixing;types;design;fact ors 零件的定位配合从功能的角度上是指相互联接的零件具有良好的对中性,且兼有其他功能或工艺特性、要求其配合时保持相互位置不变、提供配合中相对位置改变的可能、要求配合中装拆方便。 定位配合的本身不能传递载荷,一般也不具有相对运动的条件。从设计角度看,这种配合形式主要由过度配合构成,也可由小间隙的配合和小过盈量配合构成,在工
塑件成型工艺性分析3(1)
一、塑件成型工艺性分析 1、塑件的分析 (1)外形尺寸该塑件壁厚为3mm,塑件外形尺寸不大,塑件熔体流程不太长,适合于注射成型。 (2)精度等级每个尺寸的公差都不一样,有的属于一般精度,有的属于高精度,就按实际公差进行计算。 (3)脱模斜度 ABS属无定形塑料,成型收缩率较小,选择该塑件上型芯和凹模的统一脱模斜度为1度。 2、ABS的性能分析 (1)使用性能综合性能好,冲击强度、力学强度较高,尺寸稳定,耐化学性,电气性能好;易于成型和机械加工,其表面可镀铬,适合制作一般机械零件、减摩零件、传动零件和结构零件。 (2)成型性能 1)无定型塑料。其品种很多,各品种的机电性能及成型特性也各有差异,应按品种来确定成型方法及成型条件。 2)吸湿性强。含水量应小于0.3%(质量)。必须充分干燥,要求表面光泽的塑件应要求长时间预热干燥。 3)流动性中等。溢边料0.04mm左右。 4)模具设计时要注意浇注系统,选择好进料口位置、形式。推出力过大或机械加工时塑件表面呈白色痕迹。 (3)ABS的主要性能指标其性能指标见下表
ABS性能指标 3、ABS的注射成型过程及工艺参数 (1)注射成型过程 1)成型前的准备。对ABS的色泽、粒度和均匀度等进行检验,由于ABS吸水性较大,成型前应进行充分的干燥。 2)注射过程。塑件在注射机料和筒内经过加热、塑化达到流动状态后,由模具的浇注系统进入模具型腔成型,其过程可分为充模、压实、保压、倒流和冷却五个阶段。 3)塑件的后处理。的介质为空气和水,处理温度为60~75C?,理时间为16~20s。 (2)注射工艺参数 1)注射机:螺杆式,螺杆转数为30r/min 2)料筒温度(C O):后段150~170; 中段160~180;
结构工艺性的概念
结构工艺性概念 任何零件、部件或整个产品的结构设计都是根据其用途和使用要求来设计的,但是结构方面是否完善合理,很大程度上还是看这种结构能否满足工艺方面的要求。如果所设计的产品结构没有考虑到工艺方面的要求,就会在生产过程中降低生产率、延长生产周期、提高产品成本,使产品在市场上失去竞争能力。因此,产品的结构工艺性的问题在结构设计中是一个十分重要的问题。 结构工艺性的意义:在满足产品使用要求的前提下,所拟定的结构以及所规定的技术要求必须能适应现代制造工艺水平,使生产过程便于实现并能保证其经济性。 所谓产品结构工艺性就是指设计的产品结构在具体生产条件下便于制造,能够采用最有效的工艺方法。也就是说,如果所设计产品结构的工艺性好,则便于应用先进的、生产率高的工艺过程和工艺方法,使产品的制造也是最经济的。此外,产品结构工艺性也可以认为零件(或部件)在加工或装配时的方便程度和经济程度。因此,结构工艺性可分为零件结构的工艺性和装配的工艺性。 产品的结构工艺性与生产批量有关,满足大量生产的结构工艺性,不一定能满足单件和小批量生产。另外,随着科学技术的发展和制造工艺的不断进步,结构工艺性的具体内容也是不断变化的。因此,企图定量地来评定结构工艺性,通过一些技术经济指标的计算来进行判断,虽然可能(比如:使用计算机),但还不是完善的。下面主要是定性地说明评定结构工艺性的一些基本原则,也是工艺人员对结构工艺性进行分析的依据。 对整个来说,结构工艺性需从以下几方面来考虑: 1)零件总数,虽然零件的复杂程度可能差别很大,但一般来说,组成产品的零件总数愈少,特别是不同名称的零件数目愈少则结构的工艺性愈好。另外,在一定零件总数中利用生产上已经掌握的零件和组合件的数目愈多(即设计的产品结构具有继承性),或是标准的、
结构工艺性的概念
结构工艺性的概念 文稿归稿存档编号:[KKUY-KKIO69-OTM243-OLUI129-G00I-FDQS58-
结构工艺性概念 任何零件、部件或整个产品的结构设计都是根据其用途和使用要求来设计的,但是结构方面是否完善合理,很大程度上还是看这种结构能否满足工艺方面的要求。如果所设计的产品结构没有考虑到工艺方面的要求,就会在生产过程中降低生产率、延长生产周期、提高产品成本,使产品在市场上失去竞争能力。因此,产品的结构工艺性的问题在结构设计中是一个十分重要的问题。 结构工艺性的意义:在满足产品使用要求的前提下,所拟定的结构以及所规定的技术要求必须能适应现代制造工艺水平,使生产过程便于实现并能保证其经济性。 所谓产品结构工艺性就是指设计的产品结构在具体生产条件下便于制造,能够采用最有效的工艺方法。也就是说,如果所设计产品结构的工艺性好,则便于应用先进的、生产率高的工艺过程和工艺方法,使产品的制造也是最经济的。此外,产品结构工艺性也可以认为零件(或部件)在加工或装配时的方便程度和经济程度。因此,结构工艺性可分为零件结构的工艺性和装配的工艺性。 产品的结构工艺性与生产批量有关,满足大量生产的结构工艺性,不一定能满足单件和小批量生产。另外,随着科学技术的发展和制造工艺的不断进步,结构工艺性的具体内容也是不断变化的。因此,企图定量地来评定结构工艺性,通过一些技术经济指标的计算来进行判断,虽然可能(比如:使用计算机),但还不是完善的。下面主要是定性地说
明评定结构工艺性的一些基本原则,也是工艺人员对结构工艺性进行分析的依据。 对整个来说,结构工艺性需从以下几方面来考虑: 1)零件总数,虽然零件的复杂程度可能差别很大,但一般来说,组成产品的零件总数愈少,特别是不同名称的零件数目愈少则结构的工艺性愈好。另外,在一定零件总数中利用生产上已经掌握的零件和组合件的数目愈多(即设计的产品结构具有继承性),或是标准的、通用的零件数目愈多,则结构工艺性就愈好。 2)材料的需要量,制造整个产品所需各种材料的数量,特别是贵重材料或稀有材料的数量也是影响结构工艺性的一个重要因素,这点对产品非常重要,因为它影响产品的价格,另外当材料困难时就会影响产品的生产。此外,加工性能差的材料应减少使用。 3)零件各种制造方法的比例,尽量多的采用无切削或少切削的加工工艺,如冷挤压、冷冲压、精密铸造等,这样可以提高劳动效率和降低成本。显然,产品中采用这些工艺的零件比例数字愈大,则结构工艺就愈好,如果需要采用切削加工工艺,最好能采用加工费用低的方法制造的零件数愈多,则产品的工艺性也愈好。 4)零件的平均精度,产品中所有零件要加工的尺寸平均精度愈低,则工艺性愈好,另外,也可将不同尺寸按精度等级分类,然后进行比较。 5)技术经济指标,要求产品生产的劳动总量要少,生产成本要低,金属材料或各种特种材料消耗量要少,则结构工艺性就愈好。
零件的工艺性分析培训资料
零件的工艺性分析
零件的工艺性分析 一、分析研究产品的零件图样和装配图样在编制零件机械加工工艺规程前,首先应研究零件的工作图样和产品装配图样,熟悉该产品的用途、性能及工作条件,明确该零件在产品中的位置和作用;了解并研究各项技术条件制订的依据,找出其主要技术要求和技术关键,以便在拟订工艺规程时采用适当的措施加以保证。工艺分析的目的,一是审查零件的结构形状及尺寸精度、相互位置精度、表面粗糙度、材料及热处理等的技术要求是否合理,是否便于加工和装配;二是通过工艺分析,对零件的工艺要求有进一步的了解,以便制订出合理的工艺规程。 如图 3-8 所示的汽车钢板弹簧吊耳,使用时,钢板弹簧与吊耳两侧面是不接触的,所以吊耳内侧的粗糙度可由原来的设计要求R a3.2 μ m 建议改为R a12.5 μ m. 。这样在铣削时可只用粗铣不用精铣,减少铣削时间。 再如图 3-9 所示的方头销,其头部要求淬火硬度 55~60HRC ,所选用的材料为 T 8A ,该零件上有一孔φ 2H7 要求在装配时配作。由于零件长度只有 15mm ,方头部长度仅有 4mm ,如用 T 8A 材料局部淬火,势必全长均
被淬硬,配作时,φ 2H7 孔无法加工。若建议材料改用 20Cr 进行渗碳淬火,便能解决问题。 二、结构工艺性分析零件的结构工艺性是指所设计的零件在满足使用要求的前提下,制造的可行性和经济性。下面将从零件的机械加工和装配两个方面,对零件的结构工艺性进行分析。(一)机械加工对零件结构的要求 1 .便于装夹零件的结构应便于加工时的定位和夹紧,装夹次数要少。图 3 -10a 所示零件,拟用顶尖和鸡心夹头装夹,但该结构不便于装夹。若改为图 b 结构,则可以方便地装置夹头。 2 .便于加工零件的结构应尽量采用标准化数值,以便使用标准化刀具和量具。同时还注意退刀和进刀,易于保证加工精度要求,减少加工面积及难加工表面等。表 3-8b 所示为便于加工的零件结构示例。 3 .便于数控机床加工被加工零件的数控工艺性问题涉及面很广,下面结合编程的可能性与方便性来作工艺性分析。 编程方便与否常常是衡量数控工艺性好坏的一个指标。例如图 3-11 所示某零件经过抽象的尺寸标注方法,若
零件的工艺性分析
零件的工艺性分析 如图所示为接触环零件图,材料为08钢,厚度1mm,大批量生产。制定工件冲压工艺规程,设计其模具,编制零件的加工工艺规程。 1.1冲压件的工艺性分析 1.1.1结构与尺寸 1、由该冲压零件图可知,该零件结构简单、规则,而且尺寸较小,使得排样时废料较少。 2、冲压件的内、外的转角无太尖锐的尖角,部分区域以圆弧过渡,减少了冲压时某些尖角出出现崩刃和过快磨损现象。 3、对于08钢材料,其悬臂宽度b=1.5mm ,厚度t=1mm ,应满足b ≥1.5t ,当板料t>1mm 时按1mm 考虑,经计算悬臂宽度满足条件;臂长l 为:3.25和1.3均小于5倍臂宽;凹槽宽度1.65>1.5t ,最小孔径d 为1.85>0.9t ,均满足要求。 结合以上分析,该冲压件的结构与尺寸均适宜于冲压加工。 1.1.2 精度 冲压件的经济精度一般不高于IT11,查表可知,该零件的基本尺寸公差除9.4接近于IT11级外,其余尺寸均低于IT12级,也没有其他特殊的要求。分析可知可知,利用普通冲裁方式可以达到零件图样要求。 1.1.3材料 根据本次设计课题材料要求为08钢,根据附表可得金属材料的力学性能:软态,带料,抗剪强度 b=255MPa ,伸长率占10=38%,分析可知,此材料具有较高的弹性和良好的塑性,其冲裁加工性能较好,适合冲裁加工。 1.1.4批量 课题要求该零件需大批量生产,综上分析可知,该零件在冲压加工下操作简便, 而且劳动强度低,生产效率高,成本较低,适合冲裁加工。 0 6.5+0.1-0
结论:该零件的工艺性较好,可以冲裁加工。 1.2冲裁工艺方案的确定 1.2.1工艺方案分析与选择 根据冲压零件图,分析其形状特点,确定该零件加工包括落料,冲孔两个基本工序,分析可知由以下3种工艺方案选择: (1)先落料,再冲孔。采用单工序模生产。 (2)落料—冲孔复合冲压,采用复合模生产。 (3)冲孔—落料连续冲压,采用连续模(级进模)生产。 结合单工序模、复合模以及级进模的优缺点比较可知: 方案(1)制造时上午周期短,成本也较低,但需要两道工序,导致生产效率低,且零件平面度差。难以满足零件大批量生产的需要。 方案(2)生产效稍低,因零件的孔边距太小,导致模具强度不能保证,操作较为困难,且不能保证安全性。 方案(3)生产效率高,操作方便,安全性好,通过设计合理的模具结构和排样方案可以达到较好的零件质量和避免模具强度不够的问题。 综合以上分析,并参考相关资料,可知该零件采用级进冲裁方案较好。 1.3模具确定 1.3.1模具类型 根据冲压零件的冲裁方案以及设计要求,模具应采用硬质合金模。 1.3.2操作与定位方式 虽然该冲压零件的生产批量较大,但如果能够合理安排生产送料方式,将能够能够在达到批量要求的同时,降低模具成本,因此采用手工送料方式。同时考虑零件尺寸较小,材料厚度较薄,采用导料板导向、侧刃定距的定位方式。为减少料头和料尾的材料消耗和提高定距的可靠性,采用双侧刃前后对角布置。 1.3.3卸料与出件方式 考虑零件厚度较薄,采用弹性卸料方式。为了便于操作、提高生产率,冲裁件和废料采用由凸模直接从凹模洞口退下的下出件方式。即倒装式模。1.3.4模架类型及精度 由于零件厚度薄,冲裁间隙很小,又是级进模,因此采用导向平稳的对角导柱模架。考虑零件精度要求不是很高,但冲裁间隙较小,因此采用I级模架精度。
轴套零件的工艺分析和编程毕业设计
; 零件图
轴套三维图
轴套三维图
轴套类零件的工艺设计与加工 摘要:随着数控技术的发展,数控技术的应用不但给传统制造业带来了革命性的变化,使制造业成为工业化的象征,而且随着数控技术的不断发展和应用领域的扩大,它对国计民生的一些重要行业的发展起着越来越重要的作用。随着科技的发展,数控技术也在不断的发展更新,现在数控技术也称计算机数控技术,加工软件的更新快,CAD/CAM 的应用是一项实践性很强的技术。如像UG , PRO/E , Cimitron , MasterCAM ,CAXA制造工程师等。 数控技术是技术性极强的工作,尤其在模具领域应用最为广泛,所以这要求从业人员具有很高的机械加工工艺知识,数控编程知识和数控操作技能。本文主要通过c车削加工配合件的数控工艺分析与加工,综合所学的专业基础知识,全面考虑可能影响在车削加工中的因素,设计其加工工艺和编辑程序,完成配合要求。 关键词: 车削;CAD/CAM;配合件零件加工
前言 毕业设计是专业教学工作的重要组成部分和教学过程中的重要实际性环节。 毕业设计的目的是:通过设计,培养我们综合运用所学的基础理论知识,专业理论知识和一些相关软件的学习,去分析和解决本专业范围内的一般工程技术问题的能力,培养我们建立正确的工艺设计思维,学会查找工具书,掌握数控工艺设计的一般程序,规范和方法。 本次设计选择的课题为轴类零件的车削加工工艺设计及其数控加工程序编制。 这次毕业设计让我们对机械制图的基础知识有了进一步的了解,同时也 为我们从事绘图工作奠定了一个良好的基础。并锻炼了自己的动手能力,达到了学以致用的目的。它是一次专业技能的重要训练和知识水平的一次全面体验,是学生毕业资格认定的重要依据,同时也为我们将来走向工作岗位奠定了必要的理论基础和实践经验。
冲压件工艺性分析
一、止动件冲压件工艺性分析 1、零件材料:为Q235-A 钢,具有冲裁; 2、零件结构良好的冲压性能,适合:相对简单,有2个φ20mm 的孔;孔与孔、孔与边缘之间的距离也满足要求,最小壁厚为14mm (φ20mm 的孔与边框之间的壁厚) 3、零件精度:全部为自由公差,可看作IT14级,尺寸精度较低,普通冲裁完全能满足要求。 查表得各零件尺寸公差为: 外形尺寸:0 1130-、062.048-、074.060-、03.04-R 、074.060-R 型尺寸:052.0020+ 孔中心距:60±0.37 二、冲压工艺方案的确定 完成该零件的冲压加工所需要的冲压基本性质的工序只有落料、冲孔两道工序。从工序可能的集中与分散、工序间的组合可能来看,该零件的冲压可以有以下几种方案。 方案一:落料-冲孔复合冲压。采用复合模生产。 方案二:冲孔-落料级进冲压。采用级进模生产。 方案一只需一副模具,工件的精度及生产效率都较高,工件最小壁厚14mm 大于凸凹模许用最小壁厚3.6mm--4.0mm ,模具强度好,制造难度中等,并且冲压后成品件可通过卸料板卸下,清理方便,操作简单。
方案二也只需一副模具,生产效率高,操作方便,工件精度也能满足要求,但是模具结构复杂,制造加工,模具成本较高。 结论:采用方案一为佳 三、模具总体设计 (1)模具类型的选择 由冲压工艺分析可知,采用复合模冲压,所以模具类型为复合模。(2)定位方式的选择 因为该模具采用的是条料,控制条料的送进方向采用导料板,无侧压装置。控制条料的送进步距采用挡料销定距。而第一件的冲压位置因为条料长度有一定余量,可以靠操作工目测来定。 (3)卸料、出件方式的选择 因为工件料厚为1.5mm,相对较薄,卸料力也比较小,故可采用弹性卸料。又因为是倒装式复合模生产,所以采用上出件比较便于操作与提高生产效率。 (4)导向方式的选择 为了提高模具寿命和工件质量,方便安装调整,该倒装式模采用导柱导向方式。 四、排样方案确定及材料利用率 (1)排样方式的确定及其计算 设计倒装式复合模,首先要设计条料排样图,采用直排。 方案一:搭边值取2mm和3mm(P33表2-9),条料宽度为135mm