脂肪腈加氢胺化过程中Pd_C催化剂失活原因探讨

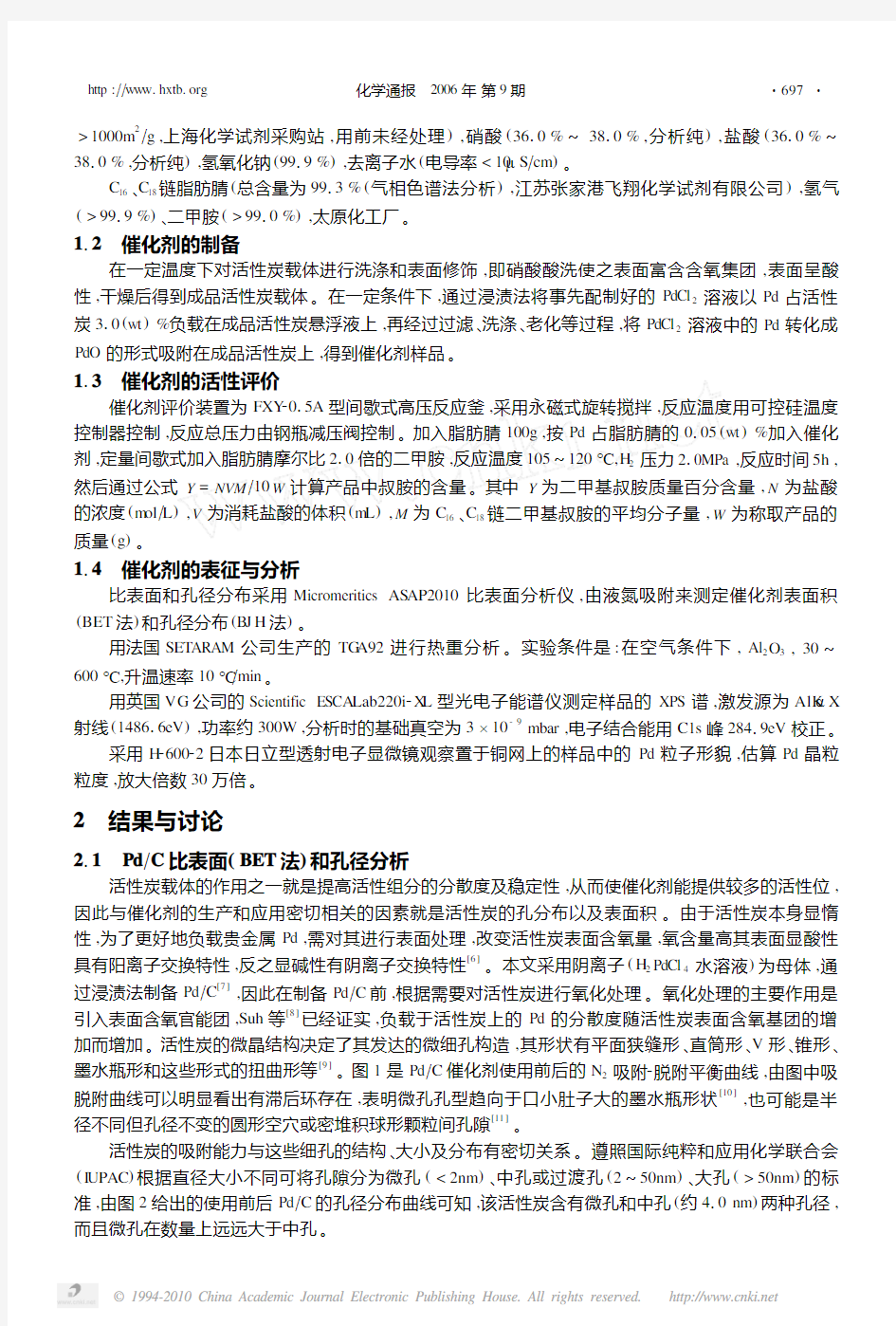
脂肪腈加氢胺化过程中PdΠC催化剂失活原因探讨
张建远 康保安3
(中国日用化学工业研究院表面活性剂国家工程研究中心 太原 030001)
摘 要 以活性炭为载体,负载氯化钯溶液,制备钯Π炭催化剂,在循环使用于催化脂肪腈加氢制备单烷基二甲基叔胺时发现,催化剂活性持续下降。通过氮吸附、热重分析、X射线能谱和透射电子显微镜等手段,
对催化剂失活前后的表面积、孔径分布变化、催化剂的失重状况、Pd的价态变化以及Pd晶粒的粒径变化研究
表明,导致钯Π炭催化剂失活的原因主要是反应过程中积炭的生成、Pd的价态变化和Pd晶粒粒径的增大。
关键词 钯Π炭催化剂 失活 积炭 脂肪腈 叔胺
Study on PdΠC C atalysts Deactivation during the Process of F atty Nitrile H ydroamination
Zhang Jianyuan,K ang Bao′an3
(China Research Institute of Daily Chemical Industry,National Engineering Research Center for Sur factants,T aiyuan030001)
Abstract The hydrogenation of fatty nitriles to produce alkyl2dimethyl tertiary amines was catalyzed by the PdΠC catalysts prepared by the PdCl2s olution carried on the active carbon.The results indicated that the activity of PdΠC catalysts was continuously decreased as increasing of the used times.The sur face area,pore size distribution,the state of losing weight of the catalysts,the change of the valence state of Pd and the change of the particle diameter Pd crystalloid were investigated by the N22ads orption,TG,XPS and TE M.I t was found that the formation of carbon during reaction,change of
the valence state of Pd and chang of the particle diameter of Pd crystalloid before and after using were the cause of PdΠC deactivation mainly.
K ey w ords PdΠC,Deactivation,Carbon deposition,Fatty nitrile,T ertiary amine
脂肪腈加氢胺化是指以脂肪腈为原料在加氢条件下反应生成对应的伯、仲、叔胺等的反应。长链烷基二甲基叔胺是一类重要的有机中间体,由其衍生得到的阳离子和两性离子表面活性剂在石油化工、农业化学品、医药卫生及日化等行业都有广泛应用[1]。脂肪腈直接制取叔胺的工艺路线已由H oechst公司研究多年并已申请专利[2],其关键是催化剂。H oechst专利采用Cu2Cr2碱金属ΠSiO2催化剂,本文则采用PdΠC催化剂。研究表明,PdΠC催化剂在制备长链烷基二甲基叔胺的过程中活性与选择性优异,但在PdΠC催化剂回用过程中,活性持续下降,对此进行了探讨。K rishnankutty等[3,4]认为,PdΠC失活分四种情况: Pd表面无污染物但内部有少量炭化物生成,可以进行化学吸附和生成氢化物;Pd完全被炭包裹,不能发生化学吸附和生成氢化物;Pd部分被炭覆盖且Pd内部生成大量炭化物,降低了Pd的化学吸附和氢化物的生成以及Pd部分被炭覆盖但内部无炭化物生成,抑制了化学吸附但可以生成氢化物。Albers等[5]则认为Pd催化剂失活的主要原因是生成的积炭致使Pd粒子粒径增大。本文的实验表明,脂肪腈加氢胺化过程中造成PdΠC催化剂失活的原因不光是由于积炭的生成,覆盖了钯局部表面,造成活性炭孔道堵塞;而且使用前后Pd晶粒粒径的增大和Pd的价态变化也是造成PdΠC催化剂失活的原因。
1 实验部分
111 试剂与原料
PdCl2(粉状)(Pd>5910(wt)%,Fe<0101(wt)%,昆明贵研铂业有限公司),活性碳(化学纯,比表面
张建远 男,26岁,硕士生,现从事催化有机合成研究。 3联系人,E2mail:K BAbaoankang@1631com
2005212215收稿,2006204225接受
>1000m2Πg,上海化学试剂采购站,用前未经处理),硝酸(3610%~3810%,分析纯),盐酸(3610%~3810%,分析纯),氢氧化钠(9919%),去离子水(电导率<10μSΠcm)。
C16、C18链脂肪腈(总含量为9913%(气相色谱法分析),江苏张家港飞翔化学试剂有限公司),氢气(>9919%)、二甲胺(>9910%),太原化工厂。
112 催化剂的制备
在一定温度下对活性炭载体进行洗涤和表面修饰,即硝酸酸洗使之表面富含含氧集团,表面呈酸性,干燥后得到成品活性炭载体。在一定条件下,通过浸渍法将事先配制好的PdCl
2溶液以Pd占活性
炭310(wt)%负载在成品活性炭悬浮液上,再经过过滤、洗涤、老化等过程,将PdCl
2溶液中的Pd转化成PdO的形式吸附在成品活性炭上,得到催化剂样品。
113 催化剂的活性评价
催化剂评价装置为FXY2015A型间歇式高压反应釜,采用永磁式旋转搅拌,反应温度用可控硅温度控制器控制,反应总压力由钢瓶减压阀控制。加入脂肪腈100g,按Pd占脂肪腈的0105(wt)%加入催化
剂,定量间歇式加入脂肪腈摩尔比210倍的二甲胺,反应温度105~120℃,H
2压力210MPa,反应时间5h,然后通过公式Y=NVMΠ10W计算产品中叔胺的含量。其中Y为二甲基叔胺质量百分含量,N为盐酸
的浓度(m olΠL),V为消耗盐酸的体积(m L),M为C
16、C18链二甲基叔胺的平均分子量,W为称取产品的质量(g)。
114 催化剂的表征与分析
比表面和孔径分布采用Micromeritics AS AP2010比表面分析仪,由液氮吸附来测定催化剂表面积(BET法)和孔径分布(B J H法)。
用法国SET ARAM公司生产的TG A92进行热重分析。实验条件是:在空气条件下,Al
O3,30~
2
600℃,升温速率10℃Πmin。
用英国VG公司的Scientific ESC A Lab220i2X L型光电子能谱仪测定样品的XPS谱,激发源为AlKαX 射线(148616eV),功率约300W,分析时的基础真空为3×10-9mbar,电子结合能用C1s峰28419eV校正。
采用H260022日本日立型透射电子显微镜观察置于铜网上的样品中的Pd粒子形貌,估算Pd晶粒粒度,放大倍数30万倍。
2 结果与讨论
211 PdΠC比表面(BET法)和孔径分析
活性炭载体的作用之一就是提高活性组分的分散度及稳定性,从而使催化剂能提供较多的活性位,因此与催化剂的生产和应用密切相关的因素就是活性炭的孔分布以及表面积。由于活性炭本身显惰性,为了更好地负载贵金属Pd,需对其进行表面处理,改变活性炭表面含氧量,氧含量高其表面显酸性具有阳离子交换特性,反之显碱性有阴离子交换特性[6]。本文采用阴离子(H
PdCl4水溶液)为母体,通
2
过浸渍法制备PdΠC[7],因此在制备PdΠC前,根据需要对活性炭进行氧化处理。氧化处理的主要作用是引入表面含氧官能团,Suh等[8]已经证实,负载于活性炭上的Pd的分散度随活性炭表面含氧基团的增加而增加。活性炭的微晶结构决定了其发达的微细孔构造,其形状有平面狭缝形、直筒形、V形、锥形、
墨水瓶形和这些形式的扭曲形等[9]。图1是PdΠC催化剂使用前后的N
2吸附2脱附平衡曲线,由图中吸脱附曲线可以明显看出有滞后环存在,表明微孔孔型趋向于口小肚子大的墨水瓶形状[10],也可能是半径不同但孔径不变的圆形空穴或密堆积球形颗粒间孔隙[11]。
活性炭的吸附能力与这些细孔的结构、大小及分布有密切关系。遵照国际纯粹和应用化学联合会(I UPAC)根据直径大小不同可将孔隙分为微孔(<2nm)、中孔或过渡孔(2~50nm)、大孔(>50nm)的标准,由图2给出的使用前后PdΠC的孔径分布曲线可知,该活性炭含有微孔和中孔(约410nm)两种孔径,而且微孔在数量上远远大于中孔。
图1 未用过(a)与使用过(b)的PdΠC氮吸附2脱附平衡曲线Fig.1 Equilibrium of N2adsorption2desorption
of unused(a)and used(b)PdΠ
C
图2 未用过(a)与使用过(b)的PdΠC孔径分布曲线Fig.2 Pore size distribution of unused(a)and used(b)PdΠC
比较图2的两组曲线,通过B J H脱附曲线可以得到以下信息:使用过的PdΠC与新鲜的PdΠC相比,其微孔和中孔体积都有所减少,而且微孔的减少比例远大于中孔。由表1可知用过的与未用过的PdΠC 比较,表面积减少2710%,体积减少2610%,孔径增大1716%,微孔体积减少3314%;而新鲜的PdΠC与活性炭比较,其表面积减少2018%,体积减少2018%,孔径只增大310%,微孔体积只减少1518%。
表1 活性炭和PdΠC使用前后表面积等的变化
T ab.1 Ch ange of surface area ect.before and after used PdΠC and active carbon
催化剂表面积(BET)Π(m2Πg)体积(BET)Π(cm3Πg)平均吸附孔径(BET)Πnm微孔体积(t2plot)Π(cm3Πg)
PdΠC92814213132144012566 PdΠC(用过的)68713157192187011708活性炭117218269142137013049
根据这些数据可以得出:在负载活性组分Pd的过程中,Pd主要吸附于活性炭的孔结构中及附近外表面,而吸附使活性炭微孔结构占有一定优势,因此使得平均孔径增大。使用过的PdΠC与新鲜的PdΠC 相比,表面积和体积减少比例大约相等,但平均孔径却增大1716%,微孔体积减少3314%,可以断定在反应过程中,可能有某种物质覆盖了一部分活性组分Pd,同时主要使该部分活性炭微孔孔道被堵塞[12],抑制了氢气与活性组分Pd的接触,而且孔道堵塞不利于反应过程中热量传递与扩散,造成局部过热,使部分Pd晶粒发生熔结,使得Pd粒径变大,活性接触点减少,从而造成PdΠC在连续回用过程中活性持续下降(表2)。
表2 PdΠC使用次数及其活性变化
T ab.2 PdΠC used times and its ch ange of activity
PdΠC使用次数12345
YΠ%92168817871684147318
212 PdΠC的热重(TG)分析
通过N
22吸附分析PdΠC的表面积、体积、平均吸附孔径和微孔体积的变化,发现用过的PdΠC表面的Pd及活性炭的孔道可能被某种物质覆盖和堵塞,为进一步确认,作了PdΠC的热重(TG)分析。
图3是活性炭和使用前后的PdΠC的热重分析曲线图,a、c和e是热重分析曲线,b、d和f是微商热重(DTG)分析曲线。从图中可以看出,活性炭的第一个失重峰位于83℃(DTG)左右,失重温度范围为46~100℃(TG),失重约占总重1310%,可以断定该温度范围内失去的是活性炭中的水;活性炭的第二个失重峰应该大于600℃,由于热重分析时最高温度设定为600℃,使得第二个燃烧峰没有完全,据李福祥等[13]报道,活性炭的燃烧峰出现在622℃,由此可以断定第二个失重峰应该是活性炭的燃烧放热峰,从其失重程度也可以看出。比较图中的活性炭与使用前的PdΠC的热重分析曲线图,可以看到PdΠC的第
一个峰位于78℃左右,失重温度范围为38~100℃,约失重1314%,失去的是PdΠC中的水;第二个出峰位置主要位于442℃左右,失重温度范围为372~520℃,根据谢炳林等[14]对钯Π炭催化剂在不同气氛中的热处理考察中指出的载体炭的燃烧放热峰集中在360~600℃范围内,可以断定该峰应该是载体活性炭的失重峰。比较图中使用前后PdΠC的热重分析曲线可以发现,在低于100℃温度范围内没有出峰,因此用过的PdΠC不含有水分,但却于220℃左右出了一个新的失重峰,失重的温度范围在198~244℃之间,约失重1110%,R ostrup-Nielsen[15]指出该温度范围内的失重是PdΠC反应后积炭的燃烧放热所致,而谢炳炎等[14]认为当积炭含量超过5%时,造成催化剂失活的主要原因是孔道堵塞,这与前面N
22吸附中提到PdΠC失活的原因相符合,从而也证明了用过的PdΠC失活的物质是积炭;另外可能也与PdΠC中水分的彻底流失有关,Cerveny等[16]在催化氢化中提到了在腈加氢胺化中水对催化剂活性的影响,适量水的存在可以提高催化剂的活性,这可能和制备PdΠC的机理有关,水的存在有利于活性炭表面含氧基团的存在,同时有利于Pd2+吸附在这些基团上,可以产生活性位使氢被活化,还有利于反应过程中活性炭微孔中的能量和活化H+的传递;第二个出峰位置在427℃左右,失重温度范围为376~531℃,与使用前
的PdΠC比较可推测该放热峰是载体活性炭的燃烧放热峰
。
图3 活性炭(a,b)与使用前(c,d)后(e,f)
的PdΠC的热重分析曲线
Fig.3 TG analysis of active carbon(a,b)and before(c,d)and after(e,f)used
PdΠC 图4 未用过(a)与使用过(b)的PdΠC
Pd3d XPS谱图
Fig.4 Pd3d XPS profile of unused(a)
and used(b)PdΠC
213 PdΠC的XPS分析与TEM分析
由PdΠC催化剂使用前后的Pd3d的XPS谱图(图4)可以看出,PdΠC催化剂使用前后的Pd3d的结
合能不同,PdΠC使用前Pd3d
5Π2
和Pd3d3Π2对应的特征峰的结合能分别为33716eV和34219eV,表明Pd3d
是Pd(Ⅱ);而PdΠC使用后Pd3d
5Π2
和Pd3d3Π2对应的特征峰的结合能分别为33518eV和34019eV,表明Pd 3d是Pd(0)[17,18]。可见Pd的价态由使用前的Pd(Ⅱ)变为使用后的Pd(0),说明PdΠC催化剂使用前后Pd的价态变化是PdΠC催化剂的失活的另外一个原因。这主要是因为脂肪腈制备叔胺是催化加氢还原反应,因此在反应过程中,由于Pd(Ⅱ)比Pd(0)的d带空穴更多,使得Pd2+的吸电子能力更强,更容易使氢被活化,催化加氢速度更快,从而反应活性更高。
由图5可以看出未用过的PdΠC催化剂上的活性组分Pd在活性炭上呈球形分布,粒径主要分布在4
~8nm之间。K rishnankutty等[19]用TE M测得PdΠC2H NO
3中Pd的粒径在613nm左右。由图6可以看出用过的PdΠC催化剂的Pd晶粒粒径在8~15nm之间,而且部分Pd晶粒被覆盖,与积炭覆盖活性组分Pd 的推论相符。Pd晶粒粒度增大与部分Pd晶粒被覆盖,导致与氢接触的活性位减少,从而降低催化剂的反应活性。比较图5和6,发现Pd晶粒的平均粒径增大约1倍,根据P ollmann等[20]报道的未用过的Pd2 Pt的粒径为316nm,失活的为616nm,表明Pd粒径增大也是导致PdΠC催化剂失活的一个原因。
图5 未用过的Pd ΠC 表面的透射电子显微镜照片
Fig.5 TEM analysis the surface of unused Pd ΠC 图6 用过的Pd ΠC 表面的透射电子显微镜照片Fig.6 TEM analysis the surface of used Pd ΠC 3 结论
根据N 22吸附、热重分析、XPS 和TE M 分析,发现造成Pd ΠC 催化剂的失活原因主要包括:(1)脂肪腈的加氢胺化制备长链烷基二甲基叔胺的过程中积炭的生成,致使活性炭的微孔孔道堵塞,使得部分Pd 晶粒被覆盖,抑制了加氢胺化,致使Pd ΠC 催化剂反应活性降低;(2)Pd ΠC 催化剂使用后Pd 的价态发生变
化(由反应前的Pd (Ⅱ
)变成反应后的Pd (0)),而在反应过程中Pd (Ⅱ)的催化加氢反应活性强于Pd (0)是Pd ΠC 催化剂失活的另外一个原因;(3)Pd ΠC 催化剂使用后Pd 晶粒粒径增大,使得与氢接触的活性位减少,是Pd ΠC 催化剂失活的又一个原因。
参
考文献
[1] 李秋小,张高勇,彭少逸.催化学报,2001(1):7~101
[2] AG H oechst ,USP :3444205,19691
[3] N K rishnankutty ,J Li ,M A Vannice.Appl.Catal.A :G en.,1998,173:137~144.
[4] N K rishnankutty ,M A Vannice.J.Catalysis ,1995,155:327~3351
[5] P Albers ,J Pietsch ,S F Parker.J.M ol.Catal.A :Chem ical ,2001,173:275~2861
[6] F R odriguez-Reinos o.Carbon ,1998,36:159~1751
[7] M G urrath ,T K uretzky ,H P Boehm et al.Carbon ,2000,38:1241~12551
[8] D J Suh ,T J Park ,S K Ihm.Carbon ,1993,31:427~4351
[9] 化工百科全书(第15卷).北京:化学工业出版社,1997:723~7411
[10] 畅延庆,陈大伟,吴征等.化学通报,2003,66:w0841
[11] J.R.安德森,K.C.普拉特著.催化剂表征与测试.北京:烃加工出版社,1989:106~1101
[12] P Albers ,J Pietsch ,S F Parker.J.M ol.Catal.A :Chem ical ,2001,173:275~2861
[13] 李福祥,孟鑫,吕志平等.应用化学,2005,(1):34~381
[14] 谢炳炎,蔡海林,徐竹生等.燃料化学学报,1992,20:213~2171
[15] J R R ostrup-Nielsen.Catalysis T oday ,1997,37:225~2321
[16] L Cerveny (edit ).S tudies in Surface and Catalysis ,V ol.27.Amsterdam -Ox ford-New Y ork-T oky o :E lsevier ,1986:1111
[17] S Hermans ,M W enkin ,M Devillers.J.M ol.Catal.A :Chem ical ,136,1998:59~681
[18] A Y S takheev ,O P Tkachenko ,G I K apustin et al.Russian Chem ical Bulletin ,International Edition ,2004,53(3):528~5371
[19] N K rishnankutty ,M A Vannice.Chem.M ater.,1995,7:754~7631
[20] J P ollmann ,R Franke ,J H ormes et al.J.E lectron S pestroscopy and Related Phenomena ,1998,94:219~2271
关于加氢裂化催化剂失活的原因分析
关于加氢裂化催化剂失活的原因分析 【摘要】近二十年来,我国的加氢裂化催化剂不断发展,步入了一个新的发展阶段。本文通过回顾加氢裂化工艺的发展路程,着重介绍研究开发的催化剂的应用情况,以此来分析加氢裂化催化剂失活的原因。求得解决方法使其得以恢复。 【关键词】加氢裂化催化剂失活 1 前言 加氢裂化发展迅猛的主要原因就是所需的加工原料应用范围广泛,大致包括重质柴油、焦化蜡油、减压馏分油、脱沥青油、重油催化裂化轻循环油和常压渣油等等,涉及了从石脑油到渣油的范围。数字显示,1998年加工能力分布,世界为200Mt/a,占原油蒸馏能力的5%;我国为13.68 Mt/a,占原油蒸馏能力的5.6%。关于加氢裂化催化剂失活的问题,要在生产中采取相应措施恢复催化剂活性,保证装置的正常运作。本文最后还通过分析我国汽油、柴油、煤油和润滑油的发展需求,讨论加氢裂化催化剂在今后的发展方向和动力。 2 加氢裂化催化剂失活原因 催化剂失活是一种催化剂反应率与时间增长呈现反比例的现象。催化剂失活的三种类型主要是:催化剂中毒失活、催化剂烧结失活和催化剂阻塞失活。催化剂的中毒失活是指一些有害物质堵塞孔道导致催化剂活性和选择性下降的过程。催化剂烧结失活是指由于高温造成催化剂烧结,在其表面形成炭质,活性组织被载体包围覆盖,孔道被结焦现象阻塞,这就导致了反应物分子难以进入活性中心。催化剂积碳失活是因为催化剂的使用使其表面产生了碳的沉积物,因此导致催化剂的活性下降。对于上面三种失活方式,在现实的加氢裂化装置中得到了体现。 在一些加氢裂化装置投产时加入了加氢裂化催化剂,一段时间后产生的现象是第一床层没有升温,起初大家认为是因为温度没有达到活性炭的要求。但长时间之后温度不断升高,入口最高温度竟然到达了376℃,这足以说明第一床层的催化剂失活。几年后发现第二床层的催化剂升温速度减慢,催化剂活性降低。经调查分析,所研究的中国石油吉林化学股份公司炼油厂所用的是大庆油,油质好,生产反应平稳,排除结焦和烧结的原因。经过分析发现原因是对催化剂的使用不恰当,产生催化剂中毒失活。到了2000年时,加氢裂化反应装置的前两层都失去了活性,后两层也先后出现了裂化反应,因此必须持续保持一种高温状态来保证生产的进行。但这样使操作难度加大,加速了催化剂活性降低。 3 加氢裂化催化剂活性的恢复 根据加氢裂化催化剂失活的三种类型来分析催化剂活性恢复的问题。专家表示,加氢裂化催化剂中毒失活是可逆的,尤其是其中的氮中毒现象。如果保持裂化段温度恒定不变,降低精制油氮含量会使转化率上升,并且随着不断的运转而
催化剂的失活与再生
催化剂的失活与再生 [摘要]:本文重点论述了近年来国外对催化剂失活的研究成果,并阐述了经使用失活及再生后的催化剂在物化性质、孔结构、活性及选择性方面均有不同程度的改变。 [关键词]:催化剂;失活;再生;加氢 催化剂在使用过程中催化剂活性会逐渐降低即催化剂失活,失活的速度与原料的性质、操作条件、产品的要求以及催化剂本身的特性均有密切的关系。 关于催化剂的失活,归纳起来失活的原因一般分为结焦失活(造成催化剂孔堵塞)、中毒失活(造成催化剂酸性中心中毒)和烧结失活(造成催化剂晶相的改变)等。工业加氢催化剂失活的主要原因是焦炭生成和金属堵塞,造成催化剂孔结构堵塞和覆盖活性中心。同时伴随着活性中心吸附原料中的毒物,活性金属组分迁移或聚集、相组成的变化、活性中心数减少、载体烧结、沸石结构塌陷与崩溃等。 不同用途的催化剂失活的主要原因有所不同,重油加氢处理催化剂失活,是因结焦、金属聚集、活性中心数减少;渣油加氢催化剂失活是因重金属硫化物沉积和结焦。而分子筛型加氢裂化催化剂失活,主要是因结焦,焦炭覆盖活性中心和堵塞孔道, S/N杂质和重金属有机物化学吸附,使酸性中心中毒或沸石结构破坏,金属迁移和聚集等[1]。
1 催化剂失活的原因 影响催化剂失活的原因很多。Camaxob等把它们基本归纳为两类: 一是化学变化引起的失活; 二是结构改变引起的失活。Hegedus等归纳为三类: 即化学失活、热失活和机械失活。Hughes则归纳为中毒、堵塞、烧结和热失活[2]。本文将它们划分为中毒、烧结和热失活、结焦和堵塞三大类来进行讨论。 1.1中毒引起的失活 1.1.1毒物分析 催化剂的活性由于某些有害杂质的影响而下降称为催化剂中毒, 这些物质称为毒物。在大部分情况下, 毒物来自进料中的杂质, 如润滑油中含有的杂质[3], 也有因反应产物(如平行反应或连串反应的毒产物)强烈吸附于活性位而导致的催化剂中毒[4,5]。 通常所说的毒物都是相对于特定的催化剂和特定的催化反应而言的, 表1列出了一些催化剂上进行反应的毒物[6]。 1.1.2中毒类型 既然中毒是由于毒物和催化剂活性组份之间发生了某种相互作用, 则可以根据这种相互作用的性质和强弱程度将毒物分成两类: (1)暂时中毒(可逆中毒) 毒物在活性中心上吸附或化合时, 生成的键强度相对较弱可以
MTBE催化剂失活原因及应对措施
MTBE催化剂失活原因及应对措施 MTBE作为汽油调合组分迄今使用已20余年,其辛烷值高(RON:117;MON:101),敏感性高,与汽油互溶好,可以任何比例与汽油互溶,而不发生相分离,是生产无铅、含氧、低芳、低烯的高辛烷值汽油的优良调合组分。 MTBE作为汽油添加剂,不仅有较高的净辛烷值,而且对于直馏汽油、催化裂化汽油、催化重整汽油等各种汽油有着良好的调和效应,有较高的调和辛烷值,在汽油中加入少量的MTBE就能使汽油辛烷值有较大的增加。此外还可以减少汽车尾气中的污染物含量。随着市场对高辛烷值汽油需求的增加,如何能够保证催化剂的活性,延长催化剂的使用周期,避免更换催化剂所带来的损失,生产出更多MTBE显得尤为重要。 1、MTBE合成反应原理 MTBE全称为甲基叔丁基醚,是目前国内仍在普遍应用的汽油添加剂,主要用于提高汽油的辛烷值。 MTBE合成反应原理为:在一定的温度和压力下,在催化剂的作用下,异丁烯与甲醇反应生成甲基叔丁基醚。反应方程式如下: (CH3)2-C=CH2+CH3OH→CH3(CH3)2COCH3 2、MTBE装置反应系统工艺流程简述 在MTBE催化剂的作用下,利用气分装置混合碳四组分中的异丁烯和来自罐区的甲醇在反应器内发生化学反应,生成MTBE。生成的MTBE与未反应的碳四和甲醇共沸物再经过分离塔分离,从而得到MTBE产品。未反碳四和甲醇共沸物则进入萃取塔,根据未反碳四和甲醇在萃取水中的溶解度不同将甲醇萃取出来,甲醇溶液在回收塔内分馏成合格的甲醇后回收。 衡量催化剂活性的一个重要指标是交换容量。催化剂在使用过程中,由于多种原因会使树脂催化剂的组织结构发生变化,从而使催化剂失去活性,甲醇和异丁烯之间的醚化反应不能发生。 3、催化剂失活的原因分析 (1)原料中的水含量 如果原料中含有水,水和异丁烯生成叔丁醇(TBA),聚集在催化剂的表面,使催化剂的反应面积减少,影响到催化剂的催化效果。 (2)原料中的碳五含量 原料中碳五的含量高时,由于碳五中含有异戊烯等不饱和烯烃,因此在反应条件下会同时产生一些副反应。随着原料中的碳五含量的增加,在MTBE中的副产物TBA、
催化剂的失活原因
催化剂的失活原因 催化剂的失活原因一般分为中毒、烧结和热失活、结焦和堵塞三大类。 1、中毒引起的失活 (1)暂时中毒(可逆中毒) 毒物在活性中心上吸附或化合时,生成的键强度相对较弱可以采取适当的方法除去毒物,使催化剂活性恢复而不会影响催化剂的性质,这种中毒叫做可逆中毒或暂时中毒。 (2)永久中毒(不可逆中毒) 毒物与催化剂活性组份相互作用,形成很强的的化学键,难以用一般的方法将毒物除去以使催化剂活性恢复,这种中毒叫做不可逆中毒或永久中毒。 (3)选择性中毒 催化剂中毒之后可能失去对某一反应的催化能力,但对别的反应仍有催化活性,这种现象称为选择中毒。在连串反应中,如果毒物仅使导致后继反应的活性位中毒,则可使反应停留在中间阶段,获得高产率的中间产物。 2、结焦和堵塞引起的失活 催化剂表面上的含碳沉积物称为结焦。以有机物为原料以固体为催化剂的多相催化反应过程几乎都可能发生结焦[7]。由于含碳物质和/或其它物质在催化剂孔中沉积,造成孔径减小(或孔口缩小),使反应物分子不能扩散进入孔中,这种现象称为堵塞。所以常把堵塞归并为结焦中,总的活性衰退称为结焦失活,它是催化剂失活中最普遍和常见的失活形式。通常含碳沉积物可与水蒸气或氢气作用经气化除去,所以结焦失活是个可逆过程。与催化剂中毒相比,引起催化剂结焦和堵塞的物质要比催化剂毒物多得多。 在实际的结焦研究中,人们发现催化剂结焦存在一个很快的初期失活,然后是在活性方面的一个准平稳态,有报道称结焦沉积主要发生在最初阶段(在0.15s内),也有人发现大约有50%形成的碳在前20s内沉积。结焦失活又是可逆的,通过控
制反应前期的结焦,可以极大改善催化剂的活性,这也正是结焦失活研究日益活跃的重要因素。 3、烧结和热失活(固态转变) 催化剂的烧结和热失活是指由高温引起的催化剂结构和性能的变化。高温除了引起催化剂的烧结外,还会引起其它变化,主要包括: 化学组成和相组成的变化,半熔,晶粒长大,活性组分被载体包埋,活性组分由于生成挥发性物质或可升华的物质而流失等。事实上,在高温下所有的催化剂都将逐渐发生不可逆的结构变化,只是这种变化的快慢程度随着催化剂不同而异。 烧结和热失活与多种因素有关,如与催化剂的预处理、还原和再生过程以及所加的促进剂和载体等有关。 当然催化剂失活的原因是错综复杂的,每一种催化剂失活并不仅仅按上述分类的某一种进行,而往往是由两种或两种以上的原因引起的。
催化装置催化剂失活与破损原因分析及解决措施
催化装置催化剂失活与破损原因分析及解决措施 张志亮 薛小波 随着全厂加工原油结构的改变,为了平衡全厂重油压力,今年以来催化装置持续提高掺渣比,目前控制在25%左右。催化原料的重质化、劣质化,对催化装置催化剂造成较大影响。出现了催化剂重金属中毒加剧、失活严重、破损加重等现象,从而导致装置催化剂单耗上升、产品收率下降、各项经济指标下降。通过在显微镜下研究催化剂的颗粒度分布、粒径的大小及形状,找到影响催化剂失活和粉碎的主要原因,通过采取多种措施,调整操作、精细管理等方式,提高装置催化剂活性、降低催化剂破损,保证装置在高掺渣率条件下,优质良好运行。 1、催化剂失活原因分析 催化剂失活主要分为两种:一、暂时性失活;二、永久性失活。暂时性失活主要由于催化剂孔径和活性中心被焦炭所堵塞,可在高温下烧焦基本得到恢复。而永久性失活是指催化剂结构发生改变或者活性中心发生化学反应而不具有活性,其中包括催化剂重金属中毒和催化剂水热失活。 1.1 催化剂的重金属中毒失活 原料中重金属浓度偏高很容易使催化剂发生中毒而破裂,尤其是钠、钒和镍。由于钠离子和钒离子在催化剂表面易形成低熔点氧化共熔物,这些共熔物接受钠离子生成氧化钠,氧化钠不仅能覆盖于催化剂表面减少活性中心,而且还能降低催化剂的热稳定性;其中重金属中Ni 对催化剂的污染尤为突出,平衡剂中Ni 含量每上升1000ppm ,催化剂污染指数上升1400ppm 。 平衡剂性质分析 1020304050607080Fe V Na Ca Ni 活性 2011年 2012年 图1 2012年与2011年平衡催化剂性质分析对比 从图1中可以看出:2012年平衡剂与2011年同期对比,平衡剂活性有所下降,从同期的62%降至今年的60%左右。金属Fe 、Na 、Ca 含量基本持平,V 的含量下降了37%,但是Ni 浓度大幅上升,上升了55%。对比污染指数: 2011年为8840ppm ,2012年为11970ppm ,同比上升了35.4%,
催化剂的失活状态
催化剂的失活状态 在理想状态下,催化剂将在无限长的时间内降低氮氧化物的排放。但是在SCR装置的运行中,总会由于烟气中的碱金属、砷、催化剂的烧结、催化剂孔的堵塞、催化剂的腐蚀以及水蒸气的凝结和硫酸盐、硫铵盐的沉积等原因,使催化剂活性降低或中毒,缩短了使用寿命。催化剂失活是一个复杂的物理和化学过程,通常的失活状态可分为三种类型: (1)催化剂中毒失活; (2)催化剂的热失活和烧结; (3)催化剂积炭等堵塞失活。 1、碱金属引起的催化剂中毒失活 飞灰中的可溶性碱金属主要包括Na和K这两种物质,在水溶液离子状态下,能渗透到催化剂深层,直接与催化剂活性颗粒反应,使酸位中毒以降低其对NH3的吸附量和吸附活性,继而降低催化剂活性。 2、催化剂的烧结和热失活 催化剂在高温下反应一定时间后,活性组分的晶粒长大,比表面积缩小,这种现象称为催化剂烧结。因烧结引起的失活的是工业催化剂,特别是负载型金属催化剂失活的主要原因。高温除一起催化剂烧结外,还会引起化学组成和相组成的变化、活性组被载体包埋,活性组分由于生成挥发性物质或可升华物质而损失等,这些变化称为热失
活。有时难以区分烧结和热失活,烧结引起的催化剂变化,往往也包含热失活的因素在内。通常温度越高,催化剂烧结越严重。 3、催化剂的积炭失活 催化剂使用过程中,因表面逐渐形成炭的沉积物而使催化剂活性下降的过程称为积炭失活。随着积炭量的增加,催化剂的比表面积、孔容、表面酸度及活性中心数均会相应下降,积炭量达到一定程度后将导致催化剂的失活。积炭越快,催化剂的使用周期越短。与催化剂中毒相比,引起催化剂积炭失活的积炭物量比毒物量要多得多,积炭在一定程度上有延缓催化剂中毒作用,但催化剂的中毒会加剧积炭的发生。与单纯的因物理堵塞而导致的催化剂失活相比,积炭失活还涉及反应物分子在气相和催化剂表面的一系列化学反应问题。积炭的同时往往伴随金属硫化物及金属杂质的沉积,单纯金属硫化物或金属杂质在催化剂表面的沉积也与单纯的积炭一样,会因覆盖催化剂表面活性位或限制反应物的扩散而使催化剂失活。故通常将积灰、积硫及金属沉积物引起的失活,都归属于积炭失活。
VOCs催化剂失活原因分析
VOCs催化剂失活原因分析 原创:罗孟飞铂锐催化 VOCs催化剂在使用的失活问题是催化燃烧设备的一个非常重要的问题,不但关系到VOCs的处理效果,而且关系到运行成本。根据本人30多年的经验,总结如下: 1.催化燃烧设备设计缺陷 催化床是催化燃烧设备的关键单元,从催化剂的角度,不但要求催化床中的催化剂数量满足设计要求,而且要求在设备运行中通过催化床的每一个部位(局部)的流速和温度的相同,这样才能保证每一块催化剂的空速和温度是一致的。如果催化床中流速和温度不一致,使得温度低、流速快的局部催化剂负荷过大,使用寿命大大缩短,然而导致VOCs净化效果的下降。因此做到催化床气流分布和温度分布的均匀是保证高净化效率和长使用寿命的关键。可见气流分配和温度均一化是催化剂反应床设计的核心技术。
2.催化剂表面结炭 在实验室中通常采用模型反应来评价催化剂性能,如甲苯、乙酸乙酯、丙酮等等,也可以采用混合溶剂来测试催化剂的性能,一般很难观察到表面积炭。然而在实际使用中,VOCs的组分非常复杂,有大分子的,小分子的,有高沸点的,低沸点,挥发性有机物的性质差别很大。还含有少量的漆雾、粉尘等物质。特别是漆雾和高沸点有机物的存在,使得在催化剂表面形成结炭,结果使得催化剂活性的下降。因此在催化剂设计中,要添加阻止催化剂表面结炭的元素,以提高催化的使用寿命。对于高漆雾的有机废气,在催化床前段应增加除漆雾设备。 3. VOCs废气中的粉尘
如果VOCs废气中含有较多粉尘,由于通过催化剂的气流速度快,一方面粉尘摩擦催化剂表面导致催化剂表面活性物质的流失,另一方面也有可能沉积在催化剂表面。这两个因素均会导致催化剂活性下降。因此对于高粉尘有机废气,前段应增加除尘设备。 4. VOCs废气中的SOx和NOx 很多涂装线是采用天然气燃烧加热,天然气燃烧过程会产生少量的SOx和NOx。实践证明少量的SOx和NOx对催化剂性能是没有影响的,可以放心使用。通常所说的S对贵金属催化剂有影响,我认为是有机硫。实际上贵金属是SO2氧化生成SO3的工业催化剂,也是NO氧化成NO2的催化剂,因此不存在SOx和NOx的中毒。5.Pb、As、P、F等物质的中毒 含Pb等重金属物质,容易与贵金属形成合金,导致催化剂中毒,As、P、F等物质也容易导致贵金属催化剂中毒,在使用过程要特别注意。 6. 催化剂高温烧结 催化剂反应温度过高会导致催化剂表面活性组分的烧结(粒子变大),催化剂比表面下降、过渡金属氧化物之间的固相反应,及其相变的发生,这些均为导致催化剂活性的下降,因此在使用过程应避免催化剂的高温冲击。相比之下,贵金属催化剂的热稳定性较高,而稀土-过渡金属氧化物催化剂的热稳定性较低。催化剂最高使用温度与催化剂性能有关。
工业催化剂的失活与再生大作业
工业催化剂的失活 题目:工业催化剂的失活 学院:求是学部 专业: 2010级化学工程与工艺 姓名:刘妍君 学号: 3010207414
工业催化剂的失活 刘妍君 (天津大学求是学部,3010207414) 摘要:工业催化剂在其使用过程中,其活性和选择性皆会逐渐下降,甚至会失去继续使用的价值,这就是催化剂的失活过程。通常将失活过程划分为以下三种类型:催化剂积炭等堵塞失活、催化剂中毒失活、催化剂的热失活和烧结失活。这里将对各类催化剂失活的含义、特征、类型、主要失活机理和影响因素逐一进行阐述。 关键词:催化剂失活 1 积碳失活 催化剂在使用过程中,因表面逐渐形成炭的沉积物从而使催化剂活性下降的过程称为积炭失活。 积炭一定程度上可延缓催化剂的中毒作用,但催化剂的中毒却会加剧积炭的发生。与单纯的因物理沉积物堵塞而导致的催化剂失活相比,积炭失活还涉及反应物分子在气相和催化剂表面上一系列的化学反应问题。 积炭的同时往往伴随着金属硫化物及金属杂质的沉积。单纯的金属硫化物或金属杂质在催化剂表面的沉积也与单纯的积炭一样同样会因覆盖催化剂表面活性位,或限制反应物的扩散等而使催化剂失活。故通常将积尘、积硫及金属沉积物引起的失活,都归属积炭失活一类。 1.1催化剂积炭形成机理 在大多数涉及烃类的反应中,反应物分子、产物分子和反应中间物都有可能成为生炭的母体,它们或者相互结合,或者相互缩合成一类高分子量的碳化物沉积在催化剂上。积炭既可以通过平行反应、连串反应产生,也可以通过复杂反应的顺序产生。 催化剂上的积炭按形成方式可分为非催化积炭和催化积炭两大类。 1.1.1非催化积炭 非催化积炭指的是气相结炭或非催化表面上生成炭质物的焦油和固体炭质物的过程。气相结炭一般认为是烃类按自由基聚合反应或缩合反应机理进行的,在气相中生成的炭通常统称为烟炱。 非催化表面上的焦油,是烃类在热裂化中凝聚缩合的高分子芳烃化合物,主要是一些高沸点的多环芳烃,有的还含有杂原子;芳烃中既有液体物质,又有固体物质。非催化形成的表面炭,是气相生成的烟炱和焦油产物的延伸,它是在无催化活性表面上形成的焦炭,无论是随原料加入或由气相反应所生成的高分子中间物,都会在反应器内的任何表面凝聚;非催化表面起着收集凝固焦油和烟炱的作用,并促进这些物质的浓缩,从而进一步发生非催化反应。由于高温下高分子量的中间物在任何表面上都会缩合,因此通过控制气相焦油和烟炱的生成可使非催化积炭减小。 此外非催化结炭还包括烃类原料中的残炭,它们通常是沥青质、多环芳烃,会直接沉积
固体催化剂失活原因分析及保护与再生
固体催化剂失活原因分析及保护与再生 摘要固体催化剂在我国的工业市场中占的比例相当大,绝大部分的产品都需要使用固体催化剂才能有效快速的做出来。因而固体催化剂在工业中的重要性可想而知。但是随着催化剂在使用的过程中不断地增加,它的有效性也慢慢的减弱。因此,本文将探讨固体催化剂失活的原因,随着提出较为合理的保护措施与再生等方法。 关键词固体催化剂;失活;原因;再生 固体催化剂对我们的工业有着较为重要的影响,而现在催化剂的失活已经造成工业在生产加工时效率的低下,严重影响了部分工业的增收,保护固体催化剂已经是迫在眉睫的问题了。因此,本文将对固体催化剂失活的原因进行分析与总结。 1固体催化剂失活的原因 固体催化剂失活的原因是多样化的,本文结合实际情况,对催化剂失活的现状展开了调查,得出了以下几种失活的方面: 1.1由于毒素影响失活 固体催化剂失活很重要的一部分原因来自于毒素的侵害,毒素的侵入又分为暂时侵入和永久侵入以及间接侵入三种情况,本文将针对这3种情况进行具体的分析: 1)毒素的暂时侵入 当固体催化剂在进行浓雾催化的过程中,会释放出催化的活力,然而就在催化的过程中容易造成催化剂的原子被毒性破坏,从而让毒素侵入催化剂的化学元素当中,造成催化剂失活,但是这样的现在不是永久性的失活,可以采用较为稳妥的除毒办法,除去催化剂中的毒素。 2)毒素的永久侵入 这种侵入类型是相当严重的,一旦被侵入进去很容易造成催化剂永久失活,导致无效反应。因为毒素很容易与催化的物质产生一种新的化学物质,这种化学物质容易变异,多种去除办法都不能让催化剂正常的使用。 3)间接性毒素侵入 由于有些催化剂在物质材料的构成上会有对某种化学反应有抵制作用,对某些反应又有促进等作用,这就形成了一种奇怪的现象,一方面抑制某一类工业化
催化剂
本文主要讲述工程上的催化剂失活的主要原因,在文中用一些例子讲述了这些原因和方法,这些方法中涉及了国内外传统的和某些先进的方法。在化学反应里能改变其他物质的化学反应速率(既能提高也能降低),而本身的质量和化学性质在化学反应前后都没有发生改变的物质叫催化剂(也叫触媒)。根据定义我们知道催化剂能改变化学反应进行的速度,因此在工业生产中具有重要的作用,但是我们也都知道在工业生产中催化剂并不能一直保持稳定不变的活性,因此研究催化剂的失活与再生便有着重要的意义。催化剂失活是指在恒定反应条件下进行的催化反应的转化率随时间增长而下降的的现象叫催化剂失活。催化剂失活的过程大致可分为三个类型:催化剂积碳等堵塞失活,催化剂中毒失活,催化剂的热失活和烧结失活。下面就三种失活方式做简要解释:积碳失活:催化剂在使用过程中,因表面逐渐形成碳的沉积物从而使催化剂的活性下降的过程称积碳失活。中毒失活:催化剂的活性和选择性由于某些有害物质的影响而下降的过程称为催化剂中毒。热失活和烧结失活:催化剂由于高温造成烧结或者活性组分被载体包埋,活性组分由于生成挥发性物质或可升华的物质而损失造成的活性降低的现象。 一、积炭失活催化剂表面上的含碳沉积物称为结焦。以有机物为原料以固体为催化剂的多相催化反应过程几乎都可能发生结焦。由于含碳物质和/或其它物质在催化剂孔中沉积,造成孔径减小(或孔口缩小),使反应物分子不能扩散进入孔中,这种现象称为堵塞。所以常把堵塞归并为结焦中,总的活性衰退称为结焦失活,它是催化剂失活中最普遍和常见的失活形式。通常含碳沉积物可与水蒸气或氢气作用经气化除去,所以结焦失活是个可逆过程。与催化剂中毒相比,引起催化剂结焦和堵塞的物质要比催化剂毒物多得多。在实际的结焦研究中,人们发现催化剂结焦存在一个很快的初期失活,然后是在活性方面的一个准平稳态,有报道称结焦沉积主要发生在最初阶段(在0.15s内),也有人发现大约有50%形成的碳在前20s内沉积。结焦失活又是可逆的,通过控制反应前期的结焦,可以极大改善催化剂的活性,
简述催化剂失活
简述各类催化剂失活 的含义、特征、类型、主要失活机理和影响因素 天津大学 化工学院 09化工一班 王一斌 3009207018
摘要 本文主要讲述工程上的催化剂失活的主要原因,在文中用一些例子讲述了这些原因和方法,这些方法中涉及了国内外传统的和某些先进的方法。 在化学反应里能改变其他物质的化学反应速率(既能提高也能降低),而本身的质量和化学性质在化学反应前后都没有发生改变的物质叫催化剂(也叫触媒)。根据定义我们知道催化剂能改变化学反应进行的速度,因此在工业生产中具有重要的作用,但是我们也都知道在工业生产中催化剂并不能一直保持稳定不变的活性,因此研究催化剂的失活与再生便有着重要的意义。 催化剂失活是指在恒定反应条件下进行的催化反应的转化率随时间增长而下降的的现象叫催化剂失活。催化剂失活的过程大致可分为三个类型:催化剂积碳等堵塞失活,催化剂中毒失活,催化剂的热失活和烧结失活。下面就三种失活方式做简要解释:积碳失活:催化剂在使用过程中,因表面逐渐形成碳的沉积物从而使催化剂的活性下降的过程称积碳失活。 中毒失活:催化剂的活性和选择性由于某些有害物质的影响而下降的过程称为催化剂中毒。 热失活和烧结失活:催化剂由于高温造成烧结或者活性组分被载体包埋,活性组分由于生成挥发性物质或可升华的物质而损失造成的活性降低的现象。
正文 一、积炭失活 催化剂表面上的含碳沉积物称为结焦。以有机物为原料以固体为催化剂的多相催化反应过程几乎都可能发生结焦。由于含碳物质和/或其它物质在催化剂孔中沉积,造成孔径减小(或孔口缩小),使反应物分子不能扩散进入孔中,这种现象称为堵塞。所以常把堵塞归并为结焦中,总的活性衰退称为结焦失活,它是催化剂失活中最普遍和常见的失活形式。通常含碳沉积物可与水蒸气或氢气作用经气化除去,所以结焦失活是个可逆过程。与催化剂中毒相比,引起催化剂结焦和堵塞的物质要比催化剂毒物多得多。 在实际的结焦研究中,人们发现催化剂结焦存在一个很快的初期失活,然后是在活性方面的一个准平稳态,有报道称结焦沉积主要发生在最初阶段(在0.15s 内),也有人发现大约有50%形成的碳在前20s 内沉积。结焦失活又是可逆的,通过控制反应前期的结焦,可以极大改善催化剂的活性,这也正是结焦失活研究日益活跃的重要因素。 结焦机理分为酸结焦、脱氢结焦、离解结焦。 酸结焦:烃类原料在固体酸催化剂上或固体催化剂的酸性部位上通过酸催化聚合反应生成碳质物质。 ()y x m n CH H C → 脱氢结焦:烃类原料在金属和金属氧化物的脱氢部位上分解生成碳或含碳原子团。 yC H C m n → 离解结焦:一氧化碳或二氧化碳在催化剂的解离部位上解离生成碳。 222 2O C CO CO C CO +?+? 二、中毒失活 催化剂所接触的流体中的少量杂质吸附在催化剂的活性位上,使催化剂的活性显著下降甚至消失,称之为中毒。使催化剂中毒的物质称为毒物。 (1)暂时中毒(可逆中毒) 毒物在活性中心上吸附或化合时,生成的键强度相对较弱可以采取适当的方法除去毒物,使催化剂活性恢复而不会影响催化剂的性质,这种中毒叫做可逆中毒或暂时中毒。 (2)永久中毒(不可逆中毒) 毒物与催化剂活性组份相互作用,形成很强的化学键,难以用一般的方法将毒物除去以使催化剂活性恢复,这种中毒叫做不可逆中毒或永久中毒。 (3)选择性中毒 催化剂中毒之后可能失去对某一反应的催化能力,但对别的反应仍有催化活性,这种现象称为选择中毒。在连串反应中,如果毒物仅使导致后继反应的活性位中毒,则可使反应停留在中间阶段,获得高产率的中间产物。
贵金属催化剂失活的三个主要原因
贵金属催化剂失活的三个主要原因 2016-04-16 12:31来源:内江洛伯尔材料科技有限公司作者:研发部 汽车尾气废催化剂 催化剂失活指催化剂在使用中会因各种因素而失去活性的现象,贵金属催化剂的失活原因一般分为中毒、烧结和热失活、结焦和堵塞三大类。 1、中毒引起的失活 (1)暂时中毒(可逆中毒) 毒物在活性中心上吸附或化合时,生成的键强度相对较弱可以采取适当的方法除去毒物,使催化剂活性恢复而不会影响催化剂的性质,这种中毒叫做可逆中毒或暂时中毒。 (2)永久中毒(不可逆中毒) 毒物与催化剂活性组份相互作用,形成很强的的化学键,难以用一般的方法将毒物除去以使催化剂活性恢复,这种中毒叫做不可逆中毒或永久中毒。 (3)选择性中毒 催化剂中毒之后可能失去对某一反应的催化能力,但对别的反应仍有催化活性,这种现象称为选择中毒。在连串反应中,如果毒物仅使导致后继反应的活性位中毒,则可使反应停留在中间阶段,获得高产率的中间产物。 2、结焦和堵塞引起的失活 催化剂表面上的含碳沉积物称为结焦。以有机物为原料以固体为催化剂的多相催化反应过程几乎都可能发生结焦[7]。由于含碳物质和/或其它物质在催化剂孔中沉积,造成孔径减小(或孔口缩小),使反应物分子不能扩散进入孔中,这种现象称为堵塞。通常含碳沉积物可与水蒸气或氢气作用经气化除去,所以结焦失活是个可逆过程。 3、烧结和热失活(固态转变) 催化剂的烧结和热失活是指由高温引起的催化剂结构和性能的变化。高温除了引起催化剂的烧结外,还会引起其它变化,主要包括:化学组成和相组成的变化,半熔,晶粒长大,活性组分被载体包埋,活性组分由于生成挥发性物质或可升华的物质而流失等。
钯碳催化剂失活原因及对策
钯碳催化剂失活原因及对策 2016-04-25 12:34来源:内江洛伯尔材料科技有限公司作者:研发部 钯碳在PTA生产装置中,加氢反应器为固定床反应器,片状的把碳催化剂充填在反应器的中、下部,床层上部至反应器顶部有较大的空间,CTA水溶液从反应器上部进人,通过一个分布器向下均匀喷淋,将把碳催化剂床层完全浸没在CTA水溶液中。反应器底部装有筛网管,筛网的规格约为12目,用于支撑催化剂和防止细碳颗粒通过。 钯碳催化剂失活分为:钯碳催化剂的磨损流失,钯碳催化剂的结垢,钯碳催化剂中毒,钯碳催化荆的烧结,加氮反应条件等几个方面的影响。金属把微晶一般分布在活性炭靠近表面的微孔内,任何磨擦都会导致催化剂磨损,产生细小的活性炭颗粒,造成活性组分金属把流失,从而导致催化剂的活性下降;氧化反应的副反应会生成一些高分子有机物以及金属腐蚀产物,这些副产物的粘性较大,会随CTA进人加氢反应器,吸附在催化剂表面和微孔内,覆盖了一部分催化剂活性中心,阻碍了加氢反应。在氧化单元开、停车时,CTA中这些粘性物质的含量更高,会导致催化剂失活;原料中的CO、Cl-以及一些有机杂质等造成的催化剂暂时失活,称为暂时性中毒, 硫会造成催化剂永久性中毒。硫化物(如HZS、硫酸盐等)随原料和辅料进人反应系统后,与把反应生成硫化二钯(dPZS)或硫化四钯(dP4)S〔’〕,这两种反应产物又被HZ 还原成大晶粒的金属单质钯,这种大晶粒把的活性比高度分散状态下的微晶把(新鲜催化剂中,70%左右的把晶粒尺寸在2.5nm以下,称为微晶钯)低得多。由于微晶钯的浓度降低,把碳催化剂的活性随之降低,甚至严重失活,这种失活是不可逆的;烧结分为热力学烧结和化学烧结:反应温度过高、反应温度不稳定和催化剂床层局部过热会加速晶粒的迁移,增加晶粒之间相遇而被俘获的几率,由此引起的烧结为热力学烧结;Cr3+、Fe,3+、CO2+、Cu2+等金属离子和Cl-、Br-等非金属离子会与把反应,由此引起的烧结为化学烧结,催化剂的热力学烧结表现为金属钯微晶成长和载体活性炭微孔结构的改变,催化剂载体活性炭的烧结则表现为比表面积减少,孔容、孔径重新分布,平均孔径增大和总孔隙率降低,导致活性中心微晶把比例减少。 延长钯碳催化剂活性的方法有运输、储存和充填方式的合理运用,尽量减少钯碳催化剂的摩擦;通过热水水洗,将覆盖在催化剂表面以及微孔中的对苯二甲酸(TA)和其它杂质除去,使催化剂的活性得到恢复;通过调整反应温度和反应压力来调整H2的分压,从而对加氢反应加以控制,将产品中杂质的含量限制在一定范围内;原辅料质量控制在相应得范围内,不影响催化剂本身的性能最好。
浅析加氢裂化催化剂的失活与再生
浅析加氢裂化催化剂的失活与再生 摘要:加氢裂化技术具有原料适应性强、产品方案灵活、液体产品收率高、产品质量好等诸多优点,催化剂则是加氢裂化技术的核心。从不同角度研究再生前后催化剂的各种性能的变化,探讨催化剂失活的原因。 关键词:加氢裂化;催化剂;失活;再生 加氢裂化技术是重油深度加工的主要工艺,也是唯一能在原料轻质化的同时直接生产车用清洁燃料和优质化工原料的工艺技术。由于加氢裂化技术具有原料适应性强、产品方案灵活、液体产品收率高、产品质量好等诸多优点,加上世界范围内原油劣质化的El益严重,而市场对清洁燃料和优质化工原料的需要量不断增加,这些都有利地促进了加氢裂化技术的迅速发展。因此,近年来加氢裂化技术已逐步发展成为现代炼油和石化企业有机结合的技术,受到世界各国炼油企业及研究机构的重视[1]。 加氢裂化催化剂是一种既具加氢功能又具裂化功能的双功能催化剂。加氢裂化技术的核心是催化剂。 加氢裂化催化剂在使用过程中催化活性和选择性会逐渐降低即催化剂失活。催化剂失活机理分三类[2-5]: 中毒、结焦及烧结, 另外还涉及因结焦或重金属沉积使催化剂孔道堵塞, 金属组分升华, 金属组分与载体生成非活性相。加氢裂化催化剂中毒主要指碱性氮如吡啶类化学吸附在酸性中心上, 不仅失去活性且堵塞孔口、孔道; 结焦是在催化剂表面生成炭青质, 覆盖在活性中心上, 大量的焦碳导致孔堵塞, 阻止反应物分子进入孔内活性中心。对于加氢裂化催化剂是指较小金属聚集或晶体变大。总之催化剂失活分为永久性和暂时性两种, 对于结焦和杂质中化学吸附造成酸碱中和均属于暂时性中毒,而重金属沉积、金属晶态变化与聚集、催化剂及其载体孔结构的倒塌等则属于永久性中毒。对于暂时性中毒 (或失活) 可通过通空气烧焦而恢复活性, 对于永久性中毒则不能。 一般而言,催化剂在运转过程中其表面积炭(又称结焦)是催化剂暂时失活的重要原因。在加氢裂化中,伴随着某些聚合、缩合等副反应。随着运转时间的延长,原料中的含硫、氮杂环烃、稠环芳烃和烯烃在催化剂表面吸附经热解缩合等反应生成积炭,覆盖了催化剂的活性中心,导致催化剂活性逐渐衰退[6,7]。为了弥补催化剂活性下降,达到预定的目的产品质量和产率要求,往往是通过提高催化剂床层的反应温度来实现的。但由于其最高操作温度受催化剂的选择性和反应器的最高允许使用温度的制约,当催化剂活性下降到一定的程度而无
催化剂失活原因
催化剂的失活原因一般分为中毒、烧结和热失活、结焦和堵塞三大类。 1、中毒引起的失活 (1)暂时中毒(可逆中毒) 毒物在活性中心上吸附或化合时,生成的键强度相对较弱可以采取适当的方法除去毒物,使催化剂活性恢复而不会影响催化剂的性质,这种中毒叫做可逆中毒或暂时中毒。 (2)永久中毒(不可逆中毒) 毒物与催化剂活性组份相互作用,形成很强的的化学键,难以用一般的方法将毒物除去以使催化剂活性恢复,这种中毒叫做不可逆中毒或永久中毒。 (3)选择性中毒 催化剂中毒之后可能失去对某一反应的催化能力,但对别的反应仍有催化活性,这种现象称为选择中毒。在连串反应中,如果毒物仅使导致后继反应的活性位中毒,则可使反应停留在中间阶段,获得高产率的中间产物。 2、结焦和堵塞引起的失活 催化剂表面上的含碳沉积物称为结焦。以有机物为原料以固体为催化剂的多相催化反应过程几乎都可能发生结焦。由于含碳物质和/或其它物质在催化剂孔中沉积,造成孔径减小(或孔口缩小),使反应物分子不能扩散进入孔中,这种现象称为堵塞。所以常把堵塞归并为结焦中,总的活性衰退称为结焦失活,它是催化剂失活中最普遍和常见的失活形式。通常含碳沉积物可与水蒸气或氢气作用经气化除去,所以结焦失活是个可逆过程。与催化剂中毒相比,引起催化剂结焦和堵塞的物质要比催化剂毒物多得多。 在实际的结焦研究中,人们发现催化剂结焦存在一个很快的初期失活,然后是在活性方面的一个准平稳态,有报道称结焦沉积主要发生在最初阶段(在0.15s内),也有人发现大约有50%形成的碳在前20s内沉积。结焦失活又是可逆的,通过控制反应前期的结焦,可以极大改善催化剂的活性,这也正是结焦失活研究日益活跃的重要因素。 3、烧结和热失活(固态转变) 催化剂的烧结和热失活是指由高温引起的催化剂结构和性能的变化。高温除了引起催化剂的烧结外,还会引起其它变化,主要包括:化学组成和相组成的变化,半熔,晶粒长大,活性组分被载体包埋,活性组分由于生成挥发性物质或可升华的物质而流失等。 事实上,在高温下所有的催化剂都将逐渐发生不可逆的结构变化,只是这种变化的快慢程度随着催化剂不同而异。 烧结和热失活与多种因素有关,如与催化剂的预处理、还原和再生过程以及所加的促进剂和载体等有关。 当然催化剂失活的原因是错综复杂的,每一种催化剂失活并不仅仅按上述分类的某一种进行,而往往是由两种或两种以上的原因引起的。