磷酸装置中旋流板除雾器的设计
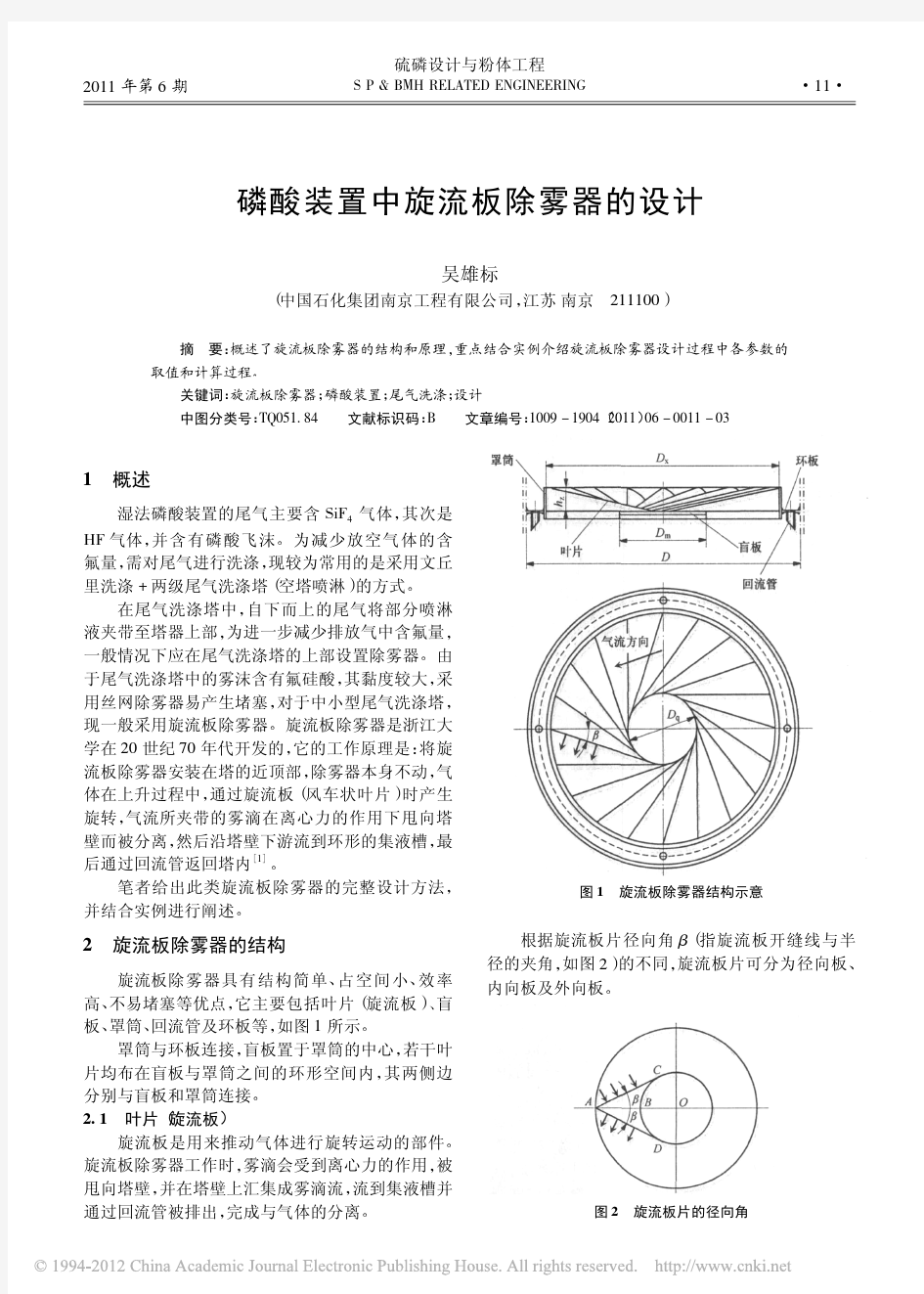

除雾器设计
1 除雾器 1)除雾器功能简介[孙琦明湿法脱硫工艺吸收塔及塔内件的设计选型中国环保产业 2007.4 研究进展18-22] 除雾器用来分离烟气所携带的液滴。在吸收塔内,由上下二级除雾器(水平式或菱形)及冲洗水系统(包括管道、阀门和喷嘴等)组成。经过净化处理后的烟气,在流经两级卧式除雾器后,其所携带的浆液微滴被除去。从烟气中分离出来的小液滴慢慢凝聚成较大的液滴,然后沿除雾器叶片往下滑落至浆液池。在一级除雾器的上、下部及二级除雾器的下部,各有一组带喷嘴的集箱。集箱内的除雾器清洗水经喷嘴依次冲洗除雾器中沉积的固体颗粒。经洗涤和净化后的烟气流出吸收塔,最终通过烟气换热器和净烟道排入烟囱。 2)除雾器本体 除雾器本体由除雾器叶片、卡具、夹具、支架等按一定的结构形成组装而成。其作用是捕集烟气吕中的液滴及少量的粉尘,减少烟气带水,防止风机振动。除雾器叶片是组成除雾器的最基本、最重要的元件,其性能的优劣对整个除雾系统的运行有着至关重要的影响。除雾器叶片通常由高分子材料(如聚丙稀、FRP等)或不锈钢(如317L)2大类材料制作而成。除雾器叶片种类繁多。按几何形状可分为折线型(a、d)和流线型(b、c),按结构特征可分为2通道叶片和3通道叶片。 除雾器布置形式通常有:水平型、人字型、V字型、组合型等大型脱硫吸收塔中多采用人字型布置,V字型布置或组合型布置(如菱形、X型)。吸收塔出口水平段上采用水平型
除雾器从工作原理上可分为折流板和旋流板两种形式。在大湿法中折流板除雾器应用的较多。折流板除雾器中两板之间的距离为30~50mm,烟气中的液滴在折流板中曲折流动与壁面不断碰撞凝聚成大颗粒液滴后在重力作用下沿除雾器叶片往下滑落,直到浆液池,从而除去烟气所携带的液滴。折流板除雾器从结构形式上,又可分为平板式和屋顶式两种。屋脊式除雾器设计流速大,经波纹板碰撞下来的雾滴可集中流下,减轻产生烟气夹带雾滴现象,除雾面积也比水平式大,因 此除雾效率高,出口排放的液滴浓度≤50 3 mg。一般常规设计要求除雾器出 /m 口排放的液滴浓度≤753 mg。本工程吸收塔选择除雾效果相对好的屋脊式除 /m 雾器。 3).除雾器冲洗系统 除雾器冲洗系统主要由冲洗喷嘴、冲洗泵、管路、阀门、压力仪表及电气控制部分组成。作用是定期清除除雾器叶片捕集的液滴、粉尘,保持叶片表面清洁,防止叶片结垢和堵塞。除雾器堵塞后,会增加烟气阻力,结垢严重时会导致除雾器变形、坍塌和折断。对于正常的二级除雾器,第2级除雾器后端面仅在必要时才进行冲洗,避免烟气携带太多液滴。旁路取消后,为避免浆液在第2级除雾器上部沉积引起堵塞,要求厂家在除雾器设计时,增加了二级除雾器后端面手动冲洗系统,防止除雾器堵塞时无法进行清除。除雾器冲洗水阀门是动作十分频繁的阀门,应选择质量可靠的产品。除雾器冲洗水喷头距除雾器间距。按0.5 m~0.6m 计,两层除雾器之间还设有上下冲水的两层水管,其间隔应考虑到便于安装维修。加上两层波形除雾器高度,最底部上冲水管至最上部下冲水管总高差约3.4 m~3.5 m。以上尺寸适于平铺波纹板式除雾器。如用菱形除雾器,其空问高度将可降l m左右。 4)除雾器的主要性能及设计参数 ①烟气流速:烟气流速是以空床气速u表示,也有用空床气体动能因子F,它是一个重要技术参数,其取值大小会直接影响到设备的除雾效率和压降损失,也是设备设计或核算生产能力的重要依据。通过除雾器断面的烟气流速过高或过低都不利于除雾器的正常运行,流速的增加将造成系统阻力增加,使得能耗增加。同时流速的增加有一定的限度,流速过高会造成二次带水,从而降低除雾效率。常将通过除雾器断面的最高且又不致二次带水时的烟气流速定义为临界气流速度,该速度与除雾器结构、系统带水负荷、气流方向、除雾器布置方式
分离原理
分离器工作原理.闪蒸原理 核心提示:气液分离器的工作原理是什么?饱和气体在降温或者加压过程中。一部分可凝气体组分会形成小液滴·随气体一起流动。气液分离器作用就是处理含有少量凝液的气体,实现凝液回收或者气相净化。其结构一般就是一个压力容器,内部有相关进气构件、液滴捕集构件。一般气体由上部出口,液相由下部收集。汽液分离罐是利用丝网除沫。... 气液分离器的工作原理是什么?饱和气体在降温或者加压过程中。 一部分可凝气体组分会形成小液滴·随气体一起流动。气液分离器作用就是处理含有少量凝液的气体,实现凝液回收或者气相净化。其结构一般就是一个压力容器,内部有相关进气构件、液滴捕集构件。一般气体由上部出口,液相由下部收集。汽液分离罐是利用丝网除沫。 或折流挡板之类的内部构件。 将气体中夹带的液体进一步凝结。 排放,以去除液体的效果。基本原理是利用气液比重不同。 在一个忽然扩大的容器中。 流速降低后,在主流体转向的过程中,气相中细微的液滴下沉而与气体分离,或利用旋风分离器,气相中细微的液滴被入口高速气流甩到器壁上。 碰撞后失去动能而与转向气体分离。分离器的结构与原理相辅相成,分离器不止是分离气液也分离气固,如旋风除尘器原理是利用离心力分离气体中的固体.气液分离器。 根据分离器的类型不同,有旋涡分离。 折留板分离,丝网除沫器。 旋涡分离主要是根据气体和液体的密度。 做离心运动时,液体遇到器壁冷凝分离。基本都是利用沉降原理的,瞬间扩大管道半径,造成压降,温度等的变化,达到分离的目的.使用气液分离器一般跟后系统有关。 因为气体降温减压后会出现部分冷凝而后系统设备处理需要纯气相或液相,所以主反应后装一个气液分离器静止分离出气相和液相给后系统创造条件。工厂里常见的气液分离器是利用闪蒸的原理。 闪蒸就是介质入渗入渗出一个大的容器,瞬间减压气化并实现气液分离,出口气相中含饱和水。 而游离的水和比重大的液滴会由于重力作用分离出来。 另外分离器一般带捕雾网。 通过捕雾网可将气相中部分大的液滴脱除。气液分离器无非就是让互相混杂的气相液相各自聚合成股。 液滴碰撞聚结,气体除去液滴后上升。 从而达到分离的目的。原理是利用气液比重不同,在一个忽然扩大的容器中,流速降低后,在主流体转向的过程中。
旋流板式气液分离器的放大规律解读
第3卷第5期过程工程学报 Vol.3 No.5 2003年10 月 The Chinese Journal of Process Engineering Oct. 2003 收稿日期:2003–03–12, 修回日期:2003–05–06 基金项目:中国石油化工股份有限公司科技开发资助项目(编号: 300023 作者简介:魏伟胜(1962–, 男, 广东省五华县人, 硕士, 高级工程师, 主要研究催化反应工程, E-mail: weiws@https://www.360docs.net/doc/8d6953101.html,. 旋流板式气液分离器的放大规律 魏伟胜,樊建华,鲍晓军, 石冈 [石油大学(北京中国石油天然气集团公司催化重点实验室, 北京 102200] 摘要:对旋流板式气液分离器在3种规模、18种旋流板结构下进行了模型实验研究,考察了旋流板结构参数(径向角、仰角和叶片数量对分离效率和压降的影响,并建立了预测分离器压降的关联式,为旋流板结构参数的确定提供了依据. 工业应用的标定结果表明分离器压降预测式是准确的,它可用于工业气液分离器的放大设计. 关键词:气液分离;旋流板;分离效率;压降 中图分类号:TQ028.4 文献标识码:A 文章编号:1009–606X(200305–0390–06 1前言 旋流板式气液分离器是一种典型的基于离心分离原理的气液分离器[1,2]. 分离器的主体为一圆柱形筒体,上部和下部均有一段锥体,见图1. 在筒体中部放置的锥形旋流板是除雾的关键部件,其结构如图2所示(详细结构可参考文献[3]. 旋流板由许多按一定仰角倾斜的叶片放置一圈,当气流穿过叶片间隙时就成为旋转气流,气流中夹带的液滴在惯性的作用下以一定的仰角射出而被甩向外侧,汇集流到溢流槽内,从而达到气液分离的目的. 叶片在竖直方向的倾斜程度用仰角α表示,在径向的排列方式用径向角β表示. 叶片数量、仰角α和径向角β是旋流板的3个重要参数.
低温分离器用于天然气井口气脱水脱烃装置选型和设计方案
高效低温分离器用于天然气井口气脱水脱烃装置选型和设计方案 诺卫能源技术(北京)有限公司 在井口天然气项目中,均建设有天然气脱水脱烃橇块装置。脱水脱烃橇块装置,主要作用是脱除原气携带的易凝析液,包括水和多碳烃。关于井口天然气脱水脱烃橇块装置原气分离核心设备,主要涉及到前冷分离器和后冷分离器,尤其是后冷分离器的选型和设计。设计院了解诺卫能源技术公司在国内外不少天然气项目上设计提供过诸多类型的天然气分离器,故而向诺卫能源技术公司请求提供技术方案。 这里,提供一套天然气处理厂脱水脱烃单元简易流程图,供大家一起分享,分 析和讨论。 附天然气脱水脱烃单元简易流程图: 从流程图可知,前冷分离器,即原料气分离器,主要用于脱除原料天然气中经 前冷器后形成的凝析油液滴液沫。后冷分离器,即低温分离器,主要用于脱除天然气经乙二醇喷淋脱水后气相挟带的乙二醇/水液滴液沫。 原料气分离器和低温分离器,均用于高效脱除气流中携带的液滴液沫。相对而言,原料气经前冷形成的液滴液沫量相对较少,而低温分离器则需要处理带液量高的乙二醇喷淋洗涤的天然气。从处理气流中不同带液量工况来看,原料气分离器宜采用立式结构,而低温分离器则宜采用卧式结构。 故建议设计院和天然气处理厂在今后的新项目中,将原来采用的立式结构的低 温分离器调整为卧式结构。卧式结构的分离器,在相同壳体尺寸的分离器储液能力要大不少。
由于天然气原气来自于集气单元,天然气不仅含有凝析油和水,还含有高粘性 凝胶质和颗粒物,脱水脱烃装置这种工况下的分离器内件,建议采用多因子旋流子母分离除沫器或羽叶高效除沫除雾分离器等高稳定分离效率和高抗堵塞性能的动 力学高效气液除沫分离技术设备,不宜采用传统的丝网式、滤网式、滤芯式除沫分离内件设备。后者的内件很容易堵塞,运行压降高,内件更换维护频繁,运行维护费用高,且还需设置备机以便在滤芯更换期间切换使用。 并且,由于上游集气单元及更前端工况变化,工况波动大。且工艺设计工况, 与设备实际运行工况差别较大。因而,必须选用操作弹性大、分离效率高、运行稳定性高的动力学高效气液除沫除雾分离器,如G50型羽叶除沫除雾分离内件或G54型多因子旋流子母分离除沫内件。上世纪中叶以来的第一代雪弗龙简易光板折流板、旋流板、大直径旋风分离器等,都不太适应大幅波动的工况。 大型特大型天然气处理厂往往采用TEG脱水工艺。TEG脱水工艺装置属于塔 系脱水,包含吸收塔、闪蒸塔、再生塔、汽提塔等塔系混成处理,适于大型、特大型天然气生产和集输处理,比如20亿立方以上规模项目,即采用TEG脱水方式,我们为客户在SNG项目提供的脱水技术即为TEG法。TEG脱水塔系,操作压力 不能太高,否则,塔体设备壁厚太大,投资太高。而乙二醇法脱水工艺适于井口高压超高压工况尤其是井口天然气脱水脱烃,装置易于小型橇块化,国内外不少井口气处理工艺均沿用该工艺。不排除未来的TEG改进工艺用于这类工况压力很高的 井口气项目。 关于动力学分离技术及其内件设计计算,需要提醒大家如下: 国内外有的厂家也开始模仿采用诺卫能源技术公司公司的羽叶除沫除雾分离内件。但是,羽叶除沫除雾分离技术,是基于其精准动力学分离系统平台设计技术获得的设计结果和组态形式。必须根据不同温度和压力工况下的气相组成和平均分子
吸收塔的设计和选型
XXXXXXXXXXXXXXXXXXXXX-环境工程部 XXXXXXXXXXXXXXXXXXXXXXXXXXXXXXX. Environmental Engineering Department 脱硫塔设计及选型指导手册 Guide Handbook for design and selection of desulphurizing tower 签署: 日期:
目录 1.1吸收塔的设计 (3) 1.1.1 吸收塔的直径和喷淋塔高度设计 (3) 1.1.2吸收塔喷淋系统的设计(喷嘴的选择配置) (13) 1.1.3 吸收塔底部搅拌器及相关配置 (16) 1.1.4 吸收塔材料的选择 (17) 1.1.5吸收塔壁厚的计算(包括计算壁厚和最小壁厚) (17) 1.1.6吸收塔封头选择计算 (19) 1.1.7吸收塔裙式支座选择计算 (21) 1.1.8吸收塔配套结构的选择 (21) 1.2吸收塔最终参数的确定 (22) 1.2.1设计条件 (22) 1.2.2吸收塔尺寸的确定 (22) 1.2.3吸收塔的强度和稳定性校核 (24)
1.1吸收塔的设计 吸收塔是脱硫装置的核心,是利用石灰石和亚硫酸钙来脱去烟气中二氧化硫气体的主要设备,要保证较高的脱硫效率,必须对吸收塔系统进行详细的计算,包括吸收塔的尺寸设计,塔内喷嘴的配置,吸收塔底部搅拌装置的形式的选择、吸收塔材料的选择以及配套结构的选择(包括法兰、人孔等)。 1.1.1 吸收塔的直径和喷淋塔高度设计 本脱硫工艺选用的吸收塔为喷淋塔,喷淋塔的尺寸设计包括喷淋塔的高度设计、喷淋塔的直径设计 1.1.1.1 喷淋塔的高度设计 喷淋塔的高度由三大部分组成,即喷淋塔吸收区高度、喷淋塔浆液池高度和喷淋塔除雾区高度。但是吸收区高度是最主要的,计算过程也最复杂,次部分高度设计需将许多的影响因素考虑在内。而计算喷淋塔吸收区高度主要有两种方法: (1) 喷淋塔吸收区高度设计(一) 达到一定的吸收目标需要一定的塔高。通常烟气中的二氧化硫浓度比较低。吸收区高度的理论计算式为 h=H0×NTU (1) 其中:H0为传质单元高度:H 0=G m /(k y a)(k a 为污染物气相摩尔差推动力的总传质系数,a 为塔内单位体积中有效的传质面积。) NTU 为传质单元数,近似数值为NTU=(y 1-y 2)/ △y m ,即气相总的浓度变化除于平均推动力△y m =(△y 1-△y 2)/ln(△y 1/△y 2)(NTU 是表征吸收困难程度的量,NTU 越大,则达到吸收目标所需要的塔高随之增大。 根据(1)可知:h=H0×NTU= )ln() ()(*** 2 2* 11* 22*112 121y y y y y y y y y y a k G y y y a k G y m m y m ------=?- a k y =a k Y =9.81×1025.07.04W G -]4[
以溢流锥降液旋流板技术原理及应用简况
一、旋流板技术的原理及应用简况 1970年代我们为浙江松门盐场海水提溴装置的设计、开车而进行Φ300湍球塔试验时,发现空塔气速大于3m/s后,雾沫夹带愈来愈严重,以至无法坚持实验。我们分析:一般的除雾方法不能适应或结构复杂,另一方面,气速高,正好利用离心原理除雾。于是制作了形状像风车叶轮的旋流除雾板(参看图2顶部),放在塔的近顶部,它本身不动,而是使气流通过它以后发生旋转,其中夹带的雾滴在离心力的作用下甩向塔壁,能得到分离。试用下来效果良好,保证了湍球塔试验的进行。 72年初对旋流板除雾器的性能及结构作了进一步的试验和改进,在空塔气速3~5m/s下,测得其除雾效率在99%以上,压降约10~30mm水柱【1】。对应于板的开孔率约30%,穿孔气速约10~17m/s,相当于旋风分离器内的中、低速。它比旋风器简单,阻力也较小。试验中还观察到:由于旋流叶片的折流作用,一小部分雾滴直接碰撞到叶片上而被分离。 在除雾试验取得成功的基础上,考虑到旋流板负荷高(空速大)、压降低的特点,如用于气液接触,有可能突破一般塔板的负荷上限: (1)雾沫夹带。从旋流板良好的除雾性能,可以估计到它的夹带限应比一般塔板高很多。 (2)淹塔或液泛。气、液在塔板上接触以后,由于离心力的作用,不仅气流内的液滴易于分离,而且液流内的气泡也易于分离,应能提高溢流管的通过能力 及淹塔限。 (3)压降。旋流板因开孔率大而自身的阻力压降相当小,作塔板使用时属喷射型,液层薄,湿板压降也应当比较小。 从传质、传热的角度看,喷射型塔板的效率一般较低,而且旋流板现为片型结构,片与片间的距离较大,这是不利的因素;但在离心力场内,液滴与气流间有附加的相对运动,这是有利因素。板效率究竟有多大?有关因素的影响如何?是它能否实际应用的关键之一,需通过试验考察。 还考虑到用作塔板时,有利于除雾板的主要特征是: (1)通过塔板的液滴负荷要大得多。 (2)不仅要求除雾,更主要的是提供尽可能良好的气液接触机会。 1975年仍在Φ300塔中,对不同结构的旋流塔板用空气—水系统进行了流体力学及传
LPG气液分离器原理
气液分离器的工作原理 饱和气体在降温或者加压过程中,一部分可凝气体组分会形成小液滴·随气体一起流动。 气液分离器作用就是处理含有少量凝液的气体,实现凝液回收或者气相净化。 其结构一般就是一个压力容器,内部有相关进气构件、液滴捕集构件。 一般气体由上部出口,液相由下部收集。 汽液分离罐是利用丝网除沫,或折流挡板之类的内部构件,将气体中夹带的液体进一步凝结,排放,以去除液体的效果。 基本原理是利用气液比重不同,在一个突然扩大的容器中,流速降低后,在主流体转向的过程中,气相中细微的液滴下沉而与气体分离,或利用旋风分离器,气相中细微的液滴被进口高速气流甩到器壁上,碰撞后失去动能而与转向气体分离。 QQ截图未命名.gif (93.74 KB) 分离器的结构与原理相辅相成,分离器不止是分离气液也分离气固,如旋风除尘器原理是利用离心力分离气体中的固体. 气液分离器,根据分离器的类型不同,有旋涡分离,折留板分离,丝网除沫器, 旋涡分离主要是根据气体和液体的密度,做离心运动时,液体遇到器壁冷凝分离。 基本都是利用沉降原理的,瞬间扩大管道半径,造成压降,温度等的变化,达到分离的目的. 使用气液分离器一般跟后系统有关,因为气体降温减压后会出现部分冷凝而后系统设备处理需要纯气相或液相,所以
主反应后装一个气液分离器静止分离出气相和液相给后系统创造条件。。。 工厂里常见的气液分离器是利用闪蒸的原理,闪蒸就是介质进入一个大的容器,瞬间减压气化并实现气液分离,出口气相中含饱和水,而游离的水和比重大的液滴会由于重力作用分离出来,另外分离器一般带捕雾网,通过捕雾网可将气相中部分大的液滴脱除。 气液分离器无非就是让互相混杂的气相液相各自聚合成股,液滴碰撞聚结,气体除去液滴后上升,从而达到分离的目的。 原理是利用气液比重不同,在一个突然扩大的容器中,流速降低后,在主流体转向的过程中,气相中细微的液滴下沉而与气体分离,或利用旋风分离器,气相中细微的液滴被进口高速气流甩到器壁上,碰撞后失去动能而与转向气体分离。算过一个气液分离器就是一个简单的压力容器,里面有相应的除沫器一清除雾滴。 气液分离器其基本原理是利用惯性碰撞作用,将气相中夹带的液滴或固体颗粒捕集下来,进而净化气相或获得液相及固相。其为物理过程,常见的形式有丝网除雾器、旋流板除雾器、折板除雾器等。 单纯的气液分离并不涉及温度和压力的关系,而是对高速气流(相对概念)夹带的液体进行拦截、吸收等从而实习分离,旋流挡板等在导流的同时,为液体的附着提供凭借,就好像空气中的灰尘要有物体凭借才能停留下来一样。而不同分离器在设计时,还优化了分离性能,如改变温度、压力、流速等 气液分离是利用在制定条件下,气液的密度不同而造成的分离。 我觉得较好的方法是利用不同的成分其在不同的温度或压力下熔沸点的差异,使其发生相变,再通过不同相的物理性质的差异进行分离 饱和气体在降温或者加压过程中,一部分可凝气体组分会形成小液滴·随气体一起流动。 气液分离器作用就是处理含有少量凝液的气体,实现凝液回收或者气相净化。 其结构一般就是一个压力容器,内部有相关进气构件、液滴捕集构件。 一般气体由上部出口,液相由下部收集。 化工厂中的分离器大都是丝网滤分离气液,这种方法属于机械式分离,原理就是气体分子小可以通过丝网空隙,而液态分子大,被阻分离开, 还有一种属于螺旋式分离,气体夹带的液体由分离器底部螺旋式上升,液体被碰撞“长大”最终依靠重力下降,有时依靠降液管引至分离器底部 气液分离器,出气端一般在上,因为比重低,内部空气被抽离,或在出气端连气泵 而液体经旋转,再次冷凝下降从下部排出 利用气体与液体的密度不同。。从而将气体与液体进行隔离开来 1、气液分离器有多种形式。 2、主要原理是:根据气液比重不同,在较大空间随流速变化,在主流体转向的过程中,气相中细微的液滴
羽叶分离器用于加氢脱硫单元循环氢脱硫塔严重带液问题解决方案
羽叶分离器用于加氢脱硫单元循环氢脱硫塔严重带液问题解决方案 诺卫能源技术(北京)有限公司罗力 最近,有企业咨询其加氢脱硫单元循环氢脱硫塔严重带液,寻求解决之道。其实,塔顶气相带液严重的问题,不仅在石化行业加氢装置胺法脱硫塔上存在,在低温甲醇洗脱硫塔、焦炉气钛箐钴湿法脱硫塔、LNG项目MDEA脱碳塔、天然气TEG 脱水塔、粉煤气化水洗塔、硫酸磷酸尾气洗涤塔、化工蒸馏塔、闪蒸塔等装置均不同程度存在,严重者塔内跑液超过300升/小时,企业运行成本居高不下。大家一起来从工艺原因和设备原因进行分析。 先从工艺上看,塔内操作温度波动、压力波动和气体流量波动因素,可以从显示仪表上查证。温度升高、压力降低,即便压缩机显示的流量不变,塔内实际工况气体体积流速、线速度已经增大,这可是仪表无法直接显示的。实际上,工况波动往往难免,则需要从设备技术上对症下药加以预防。 再从技术设备工装上分析。目前,不少行业技术革新很慢,还在沿用上世纪中叶技术,只有近年发展起来的一些新兴行业试图挑战传统行业而采用新技术设备。多数传统行业企业前述塔系气相采出口气液分离内件,仍然在采用十分简陋的丝网除沫器、筛网除沫器、鲍尔环填料除沫器等分离介质搭桥形成的“孔格”阻挡拦截式分离。先不说这些内件本身易于腐蚀断碎堵塞过流通道,单就入口原料气携带的包括催化剂破碎颗粒物和反应形成的凝胶质也会堵塞过流通道。其次,这类传统阻挡拦截式气流除沫分离技术内件,其操作弹性上限为额定负荷110%;而实际运行工况中,由于温度升高、压力降低、气流增速,以及前述因素导致的气流带液量增
加,往往会突破110%额定负荷上限,造成分离内件间或“液涌”,塔内液随气流逃出塔系。再者,如果塔系出口管线下游设备还设置有分离器,再如果分离器内件与塔内除沫分离内件同属一代设备,分离器只能起到缓冲罐储存段塞流作用,而较难实现对气相中液沫拦截捕集。 我们把视线切换到国内近年新兴行业上,如煤制烯烃、煤制油等新型煤化工项目,其气液分离多采用羽叶式分离技术,又如国外甲醇合成四大工艺包戴维、鲁奇、卡萨利、拓普索,均被推荐或指定采用。羽叶气液分离技术及设备,较上述传统 分离技术设备体现出的技术经济优势有:1、羽叶分离器属于动力学分离技术,不 是象传统分离技术通过介质表面孔径阻挡拦截方式实现分离,从而其抗堵塞能力很优秀、定量分离能力和效率也很强。2、不需要备机,分离内件可以在大修期间简 易维护,不需更换新内件,运行成本极低。3、羽叶气液分离技术,其操作弹性区 间为10%~125%,G50型羽叶叶片专利技术内件操作弹性上限超过额定负荷140%,较上述传统分离技术大幅提升。4、从内件组态结构上看,气流通过内件组时,分 离下来的液体与分离纯化后的气流分别处于两个独立的流道、且分离后的液体和气体在独立的两个流道中以相互垂直的方向流动,两者不见面、不在形成“二次挟带和返混”;不像传统丝网分离内件分离出来的液滴又如下暴雨般落回上升的气流,被气流重新带回丝网内件进行分离,如此反复。羽叶叶片专利技术内件结构,决定其性能远优于传统分离技术。我方已为国内外诸多项目直接或间接提供分离技术方案设计和核心设备制造供货,该设备在中国大型项目上的应用,如中石化中天合创煤制烯烃项目、GE承包的邯钢焦化厂焦炉气改造项目、神华宁煤煤制油项目等, 已有十分成功应用。 国内传统项目数量多、规模也不小,在当下经济技术转型时期,建议国内类似项目业主和设计院,可抓住机会实现技术升级换代,形成我国类似项目新的技术升
旋流板除雾器计算
旋流板除雾器计算 3.3.2.4除雾板 本设计中采用旋流板除雾器,其工作原理是使烟气通过旋流板,气流旋转将液滴抛向塔壁,从而聚集落下。 (1)除雾板盲板直径:除雾板盲板直径可大些,即Dm/D?0.4,可使雾滴易于甩上塔壁。本设计中取Dm=0.6D=2940mm, (2)除雾板叶片数: 叶片数可适当减少,即m,12,18左右。本设计中取m=16. (3)径向角:径向角为20?,用作除雾板的塔板要求为“外向板”,即叶片外端的钝角翘起,使气流朗向塔酸方向,可将带上的液墒抛向培壁,从而聚集落下。 (4)叶片仰角:25? (5)除雾板叶片外径:叶片外端直径径和塔径之间的距离可减小,D,1.1Dx。故本设计中Dx=D/1.1?4454.5454取整得Dx=4500mm。 (6)除雾板塔段高度:除雾板塔段的高度按经验可不超过(0.8,1)(D-Dm)。故本设计中除雾板塔段高度h=0.8(D-Dm)=1568,取整1600mm(即除雾板到下层旋流板的塔板间距为1600mm)。 3.3.2.5塔高计算: (1)吸收区高度h0的计算: 根据文献资料的经验值,旋流板塔的停留时间常在2.5s-5.5s之间,由于本设计采用NaOH吸收,故停留时间取4.5s。故吸收区的高度h0=u*t=3×4.5=13.5(m).由于每层的塔板间距hx取860mm,故塔板数n=h0/hx=13500/860=16段。 (2)椭圆封头高度h1的计算: 由于塔径为4900mm,按照椭圆封头长短轴之比为2:1的比例计算得,椭圆封头高度h1=0.5*2500=1225mm。
(3)塔顶空间高度h2的计算: 根据经验,本设计中塔顶空间高度h2取2500mm (4)除雾段高度h3的计算 除雾板塔段的高度按经验可不超过(0.8,1)(D-Dm)。故本设计中除雾板塔段高度h=0.8(D-Dm)=1600mm(即除雾板到下层旋流板的塔板间距为1600mm)。 (5)塔底空间高度 塔底空间既最后一层旋流板到椭圆封头的距离。由于气体进口的直径为 1750mm,人孔直径为800mm,最后一层旋流板到人孔中心线的距离为2300,气体进口接管到人孔中心线的距离为2050mm,气体进口接管到椭圆封头的高度为 2500mm。塔底空间的总高度为6850mm。 (6)塔底椭圆封头高度 计算同塔顶椭圆封头高度,故塔底封头高度h5=h1=1225mm (7)支座高度的计算支座高度取1900mm, 塔高的计算结果见下表2-3 3.3.2.8烟囱计算 根据《烟囱设计手册》,烟囱设计需考虑的主要因素有: 1. 烟囱的平面位置。 2. 烟囱高度。 3. 烟囱上,下口的内直径。 4. 烟道平面布置。 5. 烟道剖面尺寸。 6. 烟道与烟囱的连接位置。 7. 烟囱上安装设备的有关资料。 8. 烟气的成分,浓度,湿度,最高温度和流速。
环保设备大全
环保设备大全 LD型系列电除尘器 循环流化床烟气脱硫系统 ECA-Ⅲ固定床型有机废气净化装置 ECA-Ⅱ固定床型有机废气净化装置 ECA-Ⅰ转轮型有机废气净化装置 HP5000在线式二氧化硫、烟尘排放监测系统 HR-LZC型系列滤筒组合式除尘器 BSG-2型净化塔 焚烧炉、压缩机、粉碎机 PPDC A/S系列气箱式脉冲袋收尘器 HX-1410旋风除尘器 MDC PDC 煤磨防爆防静电袋收尘器 SYKE型铅烟尘净化装置 SYFW-型活性炭纤维 DGS-B型玻璃钢酸雾净化塔 SYWFL-4型活性炭纤维有机废气净化器 BYP系列油烟净化装置 GZA高压静电除尘器 湿式除尘器 长袋低压脉冲布袋除尘器 FMT型脉冲筒式除尘器 KDE系列电除尘器 玻璃纤维膨体纱滤布 玻璃纤维针刺毡 3216园筒滤袋 208涤纶绒布 涤纶针刺滤气呢 JSC湿法脱硫除尘器 JSDC立窑水电复合式除尘器 JDZ系列高效抗结露组合式双转子选粉机 RL生物除臭系列
脉冲袋式除尘器PPW、LFX系列 FU系列链式输送机 LFEF系列立窑(烘干机)玻纤袋除尘器 JLWZ-GX001型污染治理设施运行记录仪 YJS-1000-A油烟净化器 JJB系列高频静电油烟净化机 花岗岩水膜除尘器 华东YJ-JD-A系列复合式油烟净化器 半干法脱酸工艺——全球75%垃圾焚烧项目采用的技术迪斯DLMC、DLMV系列除尘器 离子猫除味器 迪斯(振动清灰)除尘器 水泥机立窑烟尘治理装置 HNPSC系列内外喷淋式水膜脱硫除尘器 冲击式文丘里水膜脱硫除尘器 KSR系列高效悬浮物快速分离器 红林汽车电子节能、降污 脱硫除尘器 煤气化炉 旋流板塔湿法烟气脱硫除尘装置 电子式系列油烟净化器 康康系列柴油内燃机稀薄燃烧器 FYJ系列复合式餐饮业油烟净化器 环佳牌汽车排气催化转化器 KVB/MIP 3086EPA型测尘仪 煤火探测系统(CFDS) KVB烟气连续监测系统(CEMS) YGS-36多管喷淋除尘器设备 AZFC-1型和AZFC-1A型矿用智能测定仪 XWC-3型微机大气含尘浓度测定仪 湿式电除尘器
旋流板除雾器计算
3.3.2.4除雾板 本设计中采用旋流板除雾器,其工作原理是使烟气通过旋流板,气流旋转将液滴抛向塔壁,从而聚集落下。 (1)除雾板盲板直径:除雾板盲板直径可大些,即Dm/D≥,可使雾滴易于甩上塔壁。本设计中取Dm==2940mm, (2)除雾板叶片数: 叶片数可适当减少,即m=12~18左右。本设计中取m=16.(3)径向角:径向角为20°,用作除雾板的塔板要求为“外向板”,即叶片外端的钝角翘起,使气流朗向塔酸方向,可将带上的液墒抛向培壁,从而聚集落下。(4)叶片仰角:25° (5)除雾板叶片外径:叶片外端直径径和塔径之间的距离可减小,D=。故本设计中Dx=D/≈取整得Dx=4500mm。 (6)除雾板塔段高度:除雾板塔段的高度按经验可不超过~1)(D-Dm)。故本设计中除雾板塔段高度h=(D-Dm)=1568,取整1600mm(即除雾板到下层旋流板的塔板间距为1600mm)。 3.3.2.5塔高计算: (1)吸收区高度h0的计算: 根据文献资料的经验值,旋流板塔的停留时间常在之间,由于本设计采用NaOH 吸收,故停留时间取。故吸收区的高度h0=u*t=3×=(m).由于每层的塔板间距hx取860mm,故塔板数n=h0/hx=13500/860=16段。 (2)椭圆封头高度h1的计算: 由于塔径为4900mm,按照椭圆封头长短轴之比为2:1的比例计算得,椭圆封头高度h1=*2500=1225mm。 (3)塔顶空间高度h2的计算: 根据经验,本设计中塔顶空间高度h2取2500mm (4)除雾段高度h3的计算 除雾板塔段的高度按经验可不超过~1)(D-Dm)。故本设计中除雾板塔段高度h=(D-Dm)=1600mm(即除雾板到下层旋流板的塔板间距为1600mm)。 (5)塔底空间高度 塔底空间既最后一层旋流板到椭圆封头的距离。由于气体进口的直径为1750mm,人孔直径为800mm,最后一层旋流板到人孔中心线的距离为2300,气体进口接管到人孔中心线的距离为2050mm,气体进口接管到椭圆封头的高度为2500mm。塔底空间的总高度为6850mm。 (6)塔底椭圆封头高度 计算同塔顶椭圆封头高度,故塔底封头高度h5=h1=1225mm (7)支座高度的计算
旋流板旋流筒除沫器用于锅炉烟气湿法脱硫除沫产生的麻烦问题探讨
旋流板旋流筒除沫器用于锅炉烟气湿法脱硫除沫产生的麻烦问题探讨 诺卫能源技术(北京)有限公司 旋流管/旋流板除沫器,只能用于对含有固气流的初级粗略除沫除尘,这是国内外专业分离技术领域共识。然而,国内一些旋流管/旋流板除沫器厂家却向一些不太了解动力学分离技术的客户推销其旋流同/旋流板除沫器用于精密定量分离场合,结果是排放超标近10倍,让业主陷入困境。 本案例是客户工厂的燃煤锅炉烟道气湿法脱硫末端含尘湿气工况:温度60℃、压力95kPaA(绝压)、气体流量67100Nm^3/h,原气含尘量200~500mg/Nm^3,带液~5%。 业主反映说,有公司向其拍胸脯表示采用其旋流筒/旋流板处理完全能达到要求。业主本身对旋流筒/旋流板除沫器在国内外应用情况不了解,且考虑到当地环保局对工厂锅炉烟气排放治理期限很急很紧,就付款让前述某家公司依据工况和除沫器安装运行要求进行设计供货。这家旋流筒/旋流板除沫器制造厂向业主提供了19支直径300mm长度2500mm旋流管/旋流板除沫器组成的内件组安装在直径2000mm 的不锈钢材质塔体截面上。在环保局在场测定的试运行结果是,除沫器出口气体残留液沫和粉尘总量超过150mg/Nm^3。 业主紧急向我方求助,帮助业主进行问题诊断:1、如果采用国内外通用的直 径300mm旋流筒/旋流板除沫器来处理上述工况气流,最少需要多少支旋流管/旋 流板,能够99.9%分离脱除掉的液沫最小直径是多少微米?2、采用国内外旋流筒/旋流板除沫器,依据前述工况能否实现前述工艺技术和安装要求?3、如国内外旋
流筒/旋流板除沫器无法在上述工况下满足工艺技术和安装要求,请推荐取代上述旋流筒/旋流板除沫器内件的技术方案。请有技术能力的专业分离技术公司和专业人士围绕上述情况展开热烈讨论。 本次先回答上述第一问题,即:如果采用国内外通用的直径300mm旋流筒/ 旋流板除沫器来处理上述工况气流,最少需要78支直径300mm旋流筒/旋流板,能够99.9%分离脱除掉的液沫最小直径是21微米。 关于动力学分离技术及其内件设计计算,需要提醒大家如下: 国内外有的厂家也开始模仿采用诺卫能源技术公司公司的羽叶除沫除雾分离 内件。但是,羽叶除沫除雾分离技术,是基于其精准动力学分离系统平台设计技术获得的设计结果和组态形式。必须根据不同温度和压力工况下的气相组成和平均分子量、基于空气为参照系统的气相比较压缩因子、气相粘度、气相密度、气相流量,以及液相密度、液相粘度、液相表面张力和上限液相流量等流体动力学参数,在其精准动力学分离系统平台设计技术获得的设计结果和组态形式。 同样的工况和工艺数据,非专业公司计算设计得到的结果,与专业的动力学分离技术公司在其动力学分离精准计算设计平台上获得的设计结果,相差很大。其中最主要的设计计算差异之一,在于其工况下的气相压缩因子差别。 须知,精准可靠的动力学分离技术及其内件,必须通过事先模型平台实验验证。事前模型平台试验,最安全最易得的气相介质就是空气。因此,国际上的动力学分离事前模型,都是以空气为介质的系统。用动力学分离系统平台模型去无限逼近真实工况,就必须将真实工况下的气相以接近大气压下的空气为参照体系,来获得相对于大气压下空气的压缩因子。这个压缩因子,与手册上查的以理想气体为参照体系的压缩因子值是大不相同的!!
脱硫吸收塔的直径和喷淋塔高度设计
吸收塔的直径和喷淋塔高度设计 脱硫工艺选用的吸收塔为喷淋塔,喷淋塔的尺寸设计包括喷淋塔的高度设计、喷淋塔的直径设计 喷淋塔的高度设计 喷淋塔的高度由三大部分组成,即喷淋塔吸收区高度、喷淋塔浆液池高度和喷淋塔除雾区高度。但是吸收区高度是最主要的,计算过程也最复杂,次部分高度设计需将许多的影响因素考虑在内。而计算喷淋塔吸收区高度主要有两种方法: (1) 喷淋塔吸收区高度设计(一) 达到一定的吸收目标需要一定的塔高。通常烟气中的二氧化硫浓度比较低。吸收区高度的理论计算式为 h=H0×NTU (1) 其中:H0为传质单元高度:H 0=G m /(k y a)(k a 为污染物气相摩尔差推动力的总传质系数,a 为塔内单位体积中有效的传质面积。) NTU 为传质单元数,近似数值为NTU=(y 1-y 2)/ △y m ,即气相总的浓度变化除于平均推动力△y m =(△y 1-△y 2)/ln(△y 1/△y 2)(NTU 是表征吸收困难程度的量,NTU 越大,则达到吸收目标所需要的塔高随之增大。 根据(1)可知:h=H0×NTU=)ln() ()(***2 2*11*22*112121y y y y y y y y y y a k G y y y a k G y m m y m ------=?- a k y =a k Y =×1025.07.04W G -]4[ 82.0W a k L ?=]4[ (2) 其中:y 1,y 2为脱硫塔内烟气进塔出塔气体中SO 2组分的摩尔比,kmol(A)/kmol(B) *1y ,*2y 为与喷淋塔进塔和出塔液体平衡的气相浓度,kmol(A)/kmol(B) k y a 为气相总体积吸收系数,kmol/(m 3.h ﹒kp a ) x 2,x 1为喷淋塔石灰石浆液进出塔时的SO 2组分摩尔比,kmol(A)/kmol(B) G 气相空塔质量流速,kg/(m 2﹒h) W 液相空塔质量流速,kg/(m 2﹒h) y 1×=mx 1, y 2×=mx 2 (m 为相平衡常数,或称分配系数,无量纲) k Y a 为气体膜体积吸收系数,kg/(m 2﹒h ﹒kPa) k L a 为液体膜体积吸收系数,kg/(m 2﹒h ﹒kmol/m 3) 式(2)中?为常数,其数值根据表2[4]
旋流板塔大型设计
旋流板塔大型化的设计与研究 陈昭宜谢珊李丹 (湖南大学环境工程系,长沙,410082) [内容摘要]以邯郸热电厂大型机组烟气脱硫为例,分析了旋流板在大型设备中应用的可行性与经济性,论述了旋流板大型化设计的原理与方法。 [关键词]脱硫、旋流板、大型化 一.概述 我国是一个能源结构以燃煤为主的国家。大气污染属煤烟型,烟气中大量的SO2对大气造成了严重的污染,致使我国酸雨逐年加重,酸雨面积不断扩大,其覆盖面积已达国土面积的30%。为了控制大气中SO2的含量应严格控制产生SO2污染的主要来源—电站的SO2的排放。目前,国内对于中小型电站的烟气脱硫已有一些进展,对于大型电站的烟气处理尚处于不成熟阶段。但随着国家将逐渐取缔小型电站,大中型电站的烟气处理成为急待解决的问题。 对于电站烟气处理,国内采用的工艺流程之一是文丘里加旋流板,而国外多采用文丘里加喷淋等。考虑到不同传质机理的脱硫组合效果更佳,笔者提出了文丘里加旋流板加喷淋的设想,该工艺在山西,广西,海南等地的锅炉和小型电站有成功的应用实例。旋流板是我国自行研究成功的一种喷射型塔板,这种板型由于开孔率较大,允许气流高速通过,因此处理能力较大,而压降较小,操作弹性亦较大。同时,它不仅可以脱硫,还起到气体分布均匀的作用。工艺流程中采用旋流板,可以省去一个气体分布均匀装置,还可以提高脱硫除尘效率。但是应用于大型设备的实际工艺流程中,往往因设备的放大,导致了严重失真的尴尬境地,严重影响了脱硫除尘效果。为了使旋流板可以不失真的应用于大型设备,对于旋流板的设计与研究,是一个新的课题,很值得研究。现以邯郸热电厂大型机组烟气脱硫为例,简述一下我们的研究成果。 二.设计条件和设计原则 1.设计条件 邯郸热电厂#11号机组于1998年11月建成投产,装机容量为200MW,锅炉最大蒸发量为670t/h,每台锅炉配置了两台双室器电场干式高压静电除尘器,除尘效率>=99%,现进行第二期改造工程,完成脱硫任务。 烟气经电除尘器除尘后的性能参数: 烟气量 66.5万m3/h 烟气温度 T S=405.5K
湿式除尘器课程设计
湿式除尘器课程设计 Document number:WTWYT-WYWY-BTGTT-YTTYU-2018GT
一设计题目 某小型燃煤电站锅炉烟气除尘系统设计二设计资料 设计耗煤量:h。 排烟温度:560℃ 空气过剩系数:α= 烟气密度(标态):m3 室外空气平均温度;24℃; 锅炉出口前烟气阻力:1025Pa; 现场气象资料: ①海拔高度: ②当地平均大气压: ③年平均气温:℃ ④最大风载:32kg/㎡ ⑤最大雪载:24kg/㎡ ⑥地震烈度:7度 三设计目的 要求设计烟尘浓度排放≤200mg/m3。
本设计的目的在于进一步巩固和加深理解课程理论,培养运用所学理论知识进行净化系统设计的初步能力,包括工程设计的基本方法和步骤,技术资料的查找与应用以及绘图能力的训练,综合运用本课程及其有关课程的理论知识解决工程中的实际问题。 四设计要求 (一)编制一份设计说明书,主要内容包括: 1)引言 2)方案选择和说明(附流程简图) 3)除尘(净化)设备设计计算 4)附属设备的选型和计算(集气罩、管道、风机、电机) 5)设计结果列表 6)设计结果讨论和说明 7)注明参考文献和设计资料 (二)绘制除尘(净化)系统平面布置图、立面布置图、轴测图 (三)绘制除尘(净化)主体设备图 五设计内容 引言 我国是以煤为主要能源的国家。随着国民经济的发展,能源的消耗量逐步上升,大气污染物的排放量相应增加。而就我国的经济和技术发展就我国的经济和技术发展
水平及能源的结构来看,以煤炭为主要能源的状况在今后相当长时间内不会有根本性的改变。 我国的大气污染仍将以煤烟型污染为主。因此,控制燃煤烟气污染是我国改善大气质量、减少酸雨和SO2危害的关键问题。湿式除尘器是借含尘气体与液滴或液膜的接触、撞击等作用,使尘粒从气流中分离出来的设备。湿式除尘器按结构与净化机理可分为水膜式除尘器(麻石水膜除尘器)、喷射式除尘器(文丘里除尘器)、板式除尘器(旋流板式除尘器)、冲击式除尘器(冲击水浴式除尘器)、填充式除尘器。根据除尘设备的阻力与耗能可分为低耗能和高耗能除尘器。湿式除尘器的特点是构造简单、净化效率高、本身无运动部件、故障少、适合高温高湿气体除尘,但除尘后有水的处理问题和设备的腐蚀问题。 湿式除尘器要得到较高的除尘效率,必须造成较高的气液相对运动速度和非常细小的液滴,文氏管就是为了适应这个要求而发展起来的。文氏管是在意大利物理学家文丘里首次研究了收缩管道对流体流动的效率的影响后命名的。文丘里管是在1886年美国科姆斯·霍舍尔为了增加流体的速度从而引起压力的减小而发明的。 文氏管除尘器于1946年开始在工业中应用。文氏管是一种高能耗高效率的湿式除尘器。含尘气体以高速通过喉口,水在喉口处被湍流运动的气流雾化,尘粒与水滴之间相互碰撞使尘粒沉降,这种除尘器结构简单,对微米的尘粒除尘效率可达99%以上,但其费用较高。该除尘器常用于高温烟气降温和除尘,也可用于吸收气体污染物。
脱硫吸收塔的直径和喷淋塔高度设计
吸收塔的直径和喷淋塔高度设计 脱硫工艺选用的吸收塔为喷淋塔,喷淋塔的尺寸设计包括喷淋塔的高度设计、喷淋塔的直径设计 1.1 喷淋塔的高度设计 喷淋塔的高度由三大部分组成,即喷淋塔吸收区高度、喷淋塔浆液池高度和喷淋塔除雾区高度。但是吸收区高度是最主要的,计算过程也最复杂,次部分高度设计需将许多的影响因素考虑在内。而计算喷淋塔吸收区高度主要有两种方法: (1) 喷淋塔吸收区高度设计(一) 达到一定的吸收目标需要一定的塔高。通常烟气中的二氧化硫浓度比较低。吸收区高度的理论计算式为 h=H0×NTU (1) 其中:H0为传质单元高度:H 0=G m /(k y a)(k a 为污染物气相摩尔差推动力的总传质系数,a 为塔内单位体积中有效的传质面积。) NTU 为传质单元数,近似数值为NTU=(y 1-y 2)/ △y m ,即气相总的浓度变化除于平均推动力△y m =(△y 1-△y 2)/ln(△y 1/△y 2)(NTU 是表征吸收困难程度的量,NTU 越大,则达到吸收目标所需要的塔高随之增大。 根据(1)可知:h=H0×NTU=)ln() ()(***2 2*11*22*112121y y y y y y y y y y a k G y y y a k G y m m y m ------=?- a k y =a k Y =9.81×1025.07.04W G -]4[ 82.0W a k L ?=]4[ (2) 其中:y 1,y 2为脱硫塔内烟气进塔出塔气体中SO 2组分的摩尔比,kmol(A)/kmol(B) *1y ,*2y 为与喷淋塔进塔和出塔液体平衡的气相浓度,kmol(A)/kmol(B) k y a 为气相总体积吸收系数,kmol/(m 3.h ﹒kp a ) x 2,x 1为喷淋塔石灰石浆液进出塔时的SO 2组分摩尔比,kmol(A)/kmol(B) G 气相空塔质量流速,kg/(m 2﹒h) W 液相空塔质量流速,kg/(m 2﹒h) y 1×=mx 1, y 2×=mx 2 (m 为相平衡常数,或称分配系数,无量纲) k Y a 为气体膜体积吸收系数,kg/(m 2﹒h ﹒kPa) k L a 为液体膜体积吸收系数,kg/(m 2﹒h ﹒kmol/m 3)