全泥氰化炭浆工艺

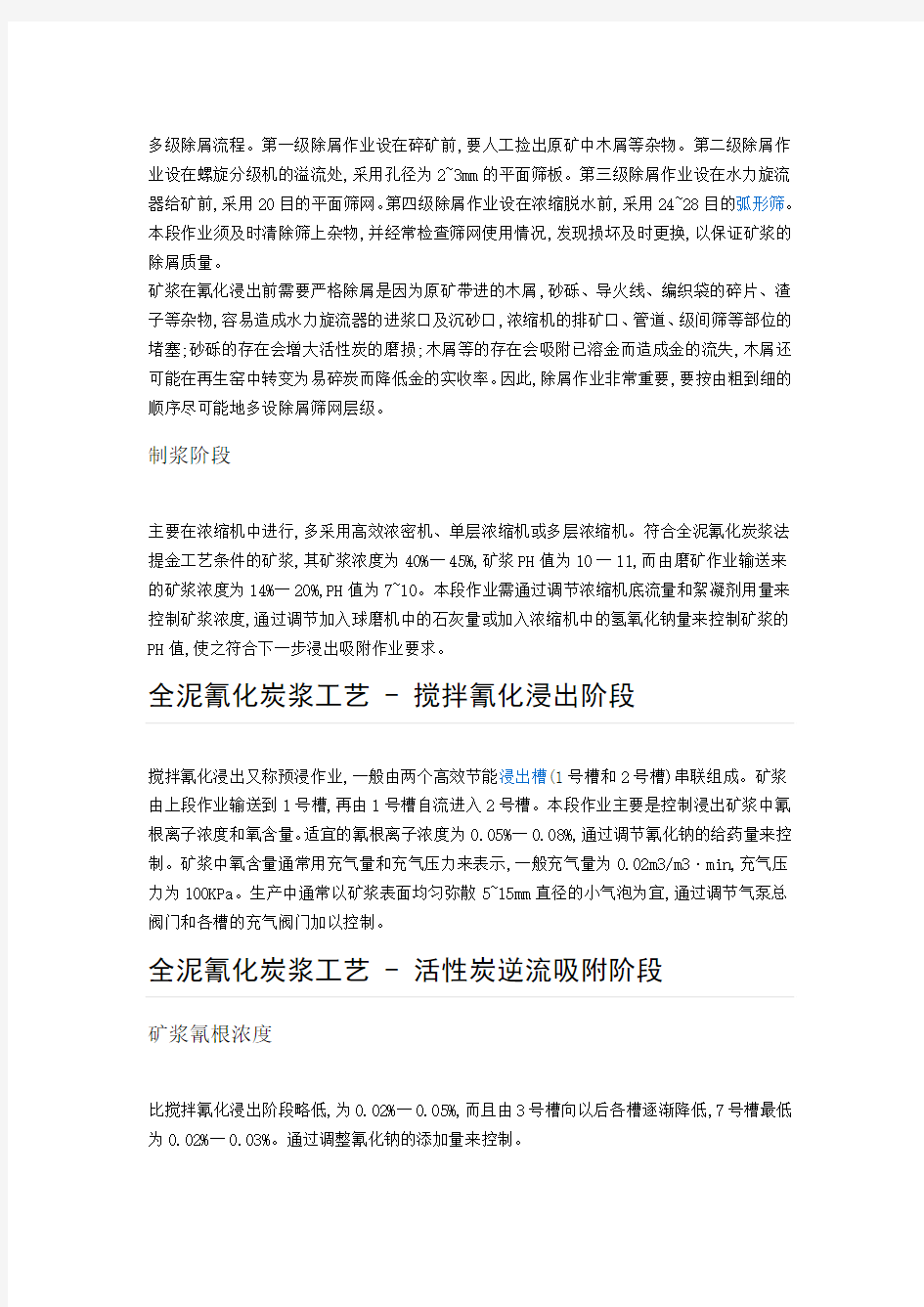
全泥氰化炭浆法提金冶炼工艺是指将金矿石全部磨碎泥化制成矿浆(一200目含量占90一95%以上)后,先进行氰化浸出,再用活性炭直接从矿浆中吸附已溶金载金、炭解吸电积金泥直接分离提纯熔炼的工艺方法。包括原料准备、搅拌氰化浸出活性炭逆流吸附、载金炭解吸电积、金泥分离提纯熔炼铸锭、活性炭活化再生和含氰污水处理等七个作业阶段。
破碎阶段
一般采用两段开路破碎或两段一闭路破碎流程(图2)。含金物料经过预先筛分,筛上粗物料进入一段破碎,破碎后再经二段筛分破碎后即进入磨矿作业。作业的目的主要控制各段破碎比和保证二段破碎产品的粒度,采用二段一闭路流程更能严格保证破碎物的粒度。一般各段破碎比为3~5,太大或太小均不利于提高破碎效率、降低成本和保护设备。二段破碎产品粒度应小于1~1.5cm,最大不超过3cm,可以通过调节破碎机排矿口尺寸来控制。生产中要贯彻“预先筛分,多破少磨”的原则。
磨矿阶段
多采用两段两闭路磨矿流程。第一段闭路磨矿分级流程由格子型球磨机和螺旋分级机组成。第二段闭路磨矿分级流程由溢流型球磨机和水力旋流器组成。将第二段闭路磨矿分级流程的预先分级和检查分级合并在一起有利于提高磨矿效率和保证产品细度。破碎好的含金物料经过第一段闭路磨矿分级流程后,矿浆中一200目含量为55%一65%。再经过第二段闭路磨矿分级流程后矿浆中一200目物料含量就可达90%一95%以上,符合全泥氰化工艺的细度要求。本段作业主要控制磨矿浓度、溢流浓度和溢流细度。一般磨矿浓度:第一段为75%一80%,第二段为60%~65%;溢流浓度:第一段为25%~30%,第二段为14%一20%;溢流细度(一200目含量):第一段为55%~65%,第二段为90写一95%以上。磨矿浓度的控制主要通过调节给水量、给矿量和返砂比等,若磨矿浓度偏高,则增加给水量、减少给图3两段两闭路磨矿流程矿量,增大返砂比等,反之亦然。溢流浓度的控制可以通过调节溢流给水量,溢流堰高低,进矿口,排矿口、溢流口大小等,而溢流细度的控制则要调节溢流堰高低、溢流口大小及钢球量、钢球配比、返砂比,磨矿浓度,溢流浓度等。总之,在磨矿作业中各项技术参数都是互相联系,相辅相成、相互制约的,因此在调节控制的过程中要综合考虑,协调作用。
除屑作业
多级除屑流程。第一级除屑作业设在碎矿前,要人工捡出原矿中木屑等杂物。第二级除屑作业设在螺旋分级机的溢流处,采用孔径为2~3mm的平面筛板。第三级除屑作业设在水力旋流器给矿前,采用20目的平面筛网。第四级除屑作业设在浓缩脱水前,采用24~28目的弧形筛。本段作业须及时清除筛上杂物,并经常检查筛网使用情况,发现损坏及时更换,以保证矿浆的除屑质量。
矿浆在氰化浸出前需要严格除屑是因为原矿带进的木屑,砂砾、导火线、编织袋的碎片、渣子等杂物,容易造成水力旋流器的进浆口及沉砂口,浓缩机的排矿口、管道、级间筛等部位的堵塞;砂砾的存在会增大活性炭的磨损;木屑等的存在会吸附已溶金而造成金的流失,木屑还可能在再生窑中转变为易碎炭而降低金的实收率。因此,除屑作业非常重要,要按由粗到细的顺序尽可能地多设除屑筛网层级。
制浆阶段
主要在浓缩机中进行,多采用高效浓密机、单层浓缩机或多层浓缩机。符合全泥氰化炭浆法提金工艺条件的矿浆,其矿浆浓度为40%一45%,矿浆PH值为10一11,而由磨矿作业输送来的矿浆浓度为14%一20%,PH值为7~10。本段作业需通过调节浓缩机底流量和絮凝剂用量来控制矿浆浓度,通过调节加入球磨机中的石灰量或加入浓缩机中的氢氧化钠量来控制矿浆的PH值,使之符合下一步浸出吸附作业要求。
搅拌氰化浸出又称预浸作业,一般由两个高效节能浸出槽(l号槽和2号槽)串联组成。矿浆由上段作业输送到1号槽,再由1号槽自流进入2号槽。本段作业主要是控制浸出矿浆中氰根离子浓度和氧含量。适宜的氰根离子浓度为0.05%一0.08%,通过调节氰化钠的给药量来控制。矿浆中氧含量通常用充气量和充气压力来表示,一般充气量为0.02m3/m3·min,充气压力为100KPa。生产中通常以矿浆表面均匀弥散5~15mm直径的小气泡为宜,通过调节气泵总阀门和各槽的充气阀门加以控制。
矿浆氰根浓度
比搅拌氰化浸出阶段略低,为0.02%一0.05%,而且由3号槽向以后各槽逐渐降低,7号槽最低为0.02%一0.03%。通过调整氰化钠的添加量来控制。
矿浆氧含量
比搅拌浸出阶段略低,通过调节各槽充气阀门控制。
底炭密度
底炭密度即为每升矿浆中活性炭的含量,一般为10~15g/L。为了保证金的回收率,通常7号槽的底炭密度略高,为15一20g/L。底炭密度可以通过调节加炭量、串炭量、提炭量来控制。
串炭速度
串炭速度又称串炭频率,是指单位时间内的串炭次数。根据对吸附系统中金的质量平衡研究,串炭速度与炭载金量的乘积是一个常数。为保持适宜的炭载金量,就要选择一定的串炭速度,一般为一天串炭一次。
串炭量
为保持吸附系统金总量平衡,保持槽内或槽之内炭的吸附性能,串炭量应与槽中储存的活性炭量之间有一个适宜的百分比,这个比值一般为10一20%。调节串炭时间的长短可以控制串炭量的大小。
炭载金量
在确保吸附率的前提下,炭载金量尽可能高,但炭载金量越高,金在吸附系统中的储存量就越多,资金周转就会受到影响,因此适宜的炭载金量、合理的串炭制度,对炭浆厂来说是非常重要的。一般最终载金炭金含量为4~69/kg,可以通过调节提炭量来控制。
尾液金含量
尾矿浆溶液中金含量一般为0.02~0.1g/m3,超过这一数值时则说明活性炭吸附有问题,吸附率降低了,可以通过增加底炭密度、降低载金炭含量、缩短串炭时间等方法来控制。
尾矿品位
一般为0.2~0.3g/t,最高不超过0.5g/t。此技术指标的调节控制较为复杂,在现有的设备工艺上可以通过提高磨矿细度、降低矿浆浓度、减少处理量、延长浸出时间等方法综合调节控制。
总之,上述各项技术指标都不是孤立的,而是互相联系的、统一的有机整体,任何一种调节方法所起的作用也不是单方面的,所以在生产操作中要根据具体情况,综合考虑,找出最佳的调控措施,以提高金的总回收率,达到最好的经济效益。
载金炭的解吸电积作业多采用加温加压解吸、高温常压电积联合闭路循环工艺流程,有较成熟的自动化控制程度较高的解吸电积装置。解吸电积液的配制:1%浓度的NaOH和1%浓度的NaCN混合溶液。电积槽阳极为带孔的不锈钢板,阴极为专用的优质钢棉。在生产操作中只要经常观察设备上的各种仪表并触动或旋动设备上的各种按钮或旋扭以控制解吸电积作业的温度、压力、流量、电压和解吸电积时间即可达到较理想的解吸电积效果。一般解吸温度为105℃,压力为2000Kpa,时间为14~16h(当解吸柱温度达到70℃时开始计时)。电积温度为70℃一80℃,电压为3~4V,电积液流量为300L/h。以上各项技术参数较容易控制而且比较稳定,例如烟台鑫海公司矿山设计院就是根据全泥氰化炭浆法来处理金矿,并加入一些创新工艺,最后所得金的品位有保证并且回收率有很大提高,受高度好评。
本阶段作业需在严格的监督和保卫条件下进行。按金银冶炼的正规方法应先将电积金泥进行火法粗炼,使其中的金银形成粗金银锭,然后再集中从金银锭中进一步分离提纯金和银。但是,为了加快资金周转,也可以采用把电积金泥直接分离提纯、熔炼铸锭的方法。
金泥的分离提纯(酸法)
l)先在金泥中加入一定量的盐酸,充分反应以除去残余钢毛和部分其它溅金属,过滤洗涤后再加入一定量的硝酸,充分反应除去大部分银和其它溅金属,再过滤洗涤。本步骤主要是控制酸的加入量、反应时间及洗涤程度。酸的用量与金泥含杂质多少有关,反应时间要根据反应条件和实际反应情况确定,但一般反应时应不少于.2一3h。洗涤程度至关重要,每次洗涤都必须达到中性,用热水洗涤要快些。
2)向洗涤好的金泥中分次加入3一4倍重量的王水,搅拌溶金,后期加热煮沸,使金以离子状态进入溶液中,过滤得含金溶液和沉渣。本步骤应注意初加王水时反应剧烈,要防止金液外溢。溶金反应时间,一般不低于2~3h,要注意观察沉渣颜色的变化。
3)向含金溶液中加入过量的无水亚硫酸钠即可得到海棉金。在此之前首先要把含金溶液赶酸至PH一6~7。加无水亚硫酸钠时要小量逐渐地加,直至过量,同时还要不断加热搅拌。
海棉金的熔炼铸锭(焦炭炉)
1)在海棉金中加入硼砂10%~15%、碳酸钠5%~10%、玻璃粉3%~5%,混匀后装入经过预热的石墨增祸内,置入炉中熔炼。熔炼总时间1.5~2.0h,熔炼温度1200~1300℃。本步要注意控制炉温和熔炼时间,并经常观察钳竭放置情况及竭内物料熔化情况。
2)熔化充分后,用夹钳取出增涡,将熔体倒入铸模内。本步骤应注意铸模须经过预热,并在内面均匀熏一层厚lmm的黑烟。浇铸时应注意先慢再快后慢顺序,浇铸时间10秒钟。取出金锭后先在稀硝酸或盐酸溶液中浸泡约5一10min,再用清水洗去酸,然后在酒精中浸泡片刻、取出擦干即可,金锭成色99.9%。
酸法活化再生
活性炭每使用一个循环—吸附~解吸—都要进行酸法活化再生。具体操作是用3%一5%浓度的盐酸溶液与脱金炭在酸洗容器中搅拌1.5~2h后用清水洗涤,再用1%浓度的NaOH溶液冲洗直到中性为止。酸法活化再生主要是除去吸附在活性炭上的钙、镁、钠等酸溶物。应该注意在酸处理过程中会产生剧毒的氢氰酸,必须采取适当的措施以保证安全。
火法活化再生
一般活性炭每使用5一10个循环就进行一次火法活化再生处理。火法活化再生是在钢管窖中进行的,钢管窖的加热区有两个。第一加热区温度为600℃,产生蒸汽气氛。第二加热区温度在650℃以上,炭在此区完成活化再生。具体操作是把湿炭从钢管窖的给料端加入,钢管在旋转过程中把炭输送到排料端排出,炭经空气冷却后即可投入使用。火法活化再生主要是通过热处理的办法来消除有机物结垢对炭的活性影响。
本段作业由两个污水处理槽串联组成,采用碱氯法处理。即在碱性条件下直接把漂白粉加入污水处理槽,搅拌、氧化分解污水中的氰化物,从而达到解毒、净化、消除污染的目的。实际生产中通过调节漂白粉用量来使污水中氰根浓度低于0.5mg/L,然后将污水泵入沉淀池或尾
矿库进行自然降解。全泥氰化炭浆法提金冶炼工艺对矿石的适应性强,具有工艺流程简化、工序简单、投资小、成本低、工艺过程稳定、易于操作、金的总回收率高等特点,是当前国内国际比较流行的金矿选矿工艺,也是金矿选矿发展的趋势。
氰化法提金的基本原理
氰化法提金的基本原理? (2006-1-10) 氰化法提金的基本原理?氰化法提金浸出的主要影响因素? 氰化法提金是从金矿石中提取金的主要方法之一。氰化物对金溶解作用机理的解释目前尚不一致,多数认为金在氰化溶中有氧存在的情况下可以生成一 种金的络合而溶解其基本反应式为: 4Au+8KCN+O 2+2H 2 O— 4KAu(CN) 2 +4KOH 一般认为金被氰化物溶解发生两步反应: 2Au+4KCN+O 2+2H 2 O— 2(CN 2+H 2 O+2KOH 2Au+4KCN+O 2 +H 2 O 2 —2KAu(CN) 2 +2KOH 金的表面在氰化物溶液中逐渐地由表及里地溶解。溶液中氧的浓度与金的溶解速度有关. 浸出时氰化物浓度一般为,金的溶解速度随氰化物浓度的提高而呈直线上升到最大值。然后缓慢上升,当氰化物浓度达时,金的溶解速度和氰化物浓度无关,甚至下降(因氰化物水解)。 金的溶解速度随氧浓度上升而增大,采用富氧溶被或高压充气氰化可以强化金的溶解。氰化试剂溶解金银的能力为:氰化铵>氰化钙氰化钠>氰化钾。氰化钾的价格最贵,目前多数使用氰化钠,氰化物的耗量取决于物料性质和操作因素,常为理论量的20-200倍. 物料性质影晌金的浸出率。氰化法虽是目前提金的主要方法,但某些含金矿物原料不宜直接采用氰化法处理,若矿石中铜、砷、锑、铋、硫、磷、磁铁矿、白铁矿等组分含量高时将大大增加氰化物耗量成消耗矿桨中的氧。降低金的浸出率,矿石中含碳高时,碳会吸附已溶金而随尾矿损失。预先氧化焙烧或浮选方法可除去有害杂质的影晌。氰化物水解反应为:KCN+H 2 OyKOH+HCN因此会挥发出有毒的HCN;加入石灰是氰化物水解减弱,上式反应向左方向进行,减少氰化物的损失。石灰还有中和酸类物质作用并可沉淀矿浆中得有害离子,使金的溶解处于最佳条件,常用石灰作保护碱。石灰加入量使矿浆值达到11~12 为宜,矿浆lang=EN-值过高时对溶金不利。金粒大小主要影晌氰化时间,粗拉金(>74微米)的溶解速度慢。所以氰化前采用混汞、重选或浮选预先回收粗粒金是合理的。在磨矿过程中使细金粒充分单体解离仍是提高金的浸出率重要因素。 氰化时矿泥含量和矿浆浓度直接影晌组分扩散速度。矿浆浓度应小于 30~33%。矿泥多时矿浆浓度应小于22-25%,但浓度不宜过低,否则增加氰化物的消耗。 氰化时间取决于物料性质、氰化方式及氰化条件而异。一般搅拌氰化浸出时
全泥氰化炭浆工艺讲解学习
全泥氟化炭浆工艺 全泥氟化炭浆工艺-概述 全泥氟化炭浆法提金冶炼工艺是指将金矿石全部磨碎泥化制成矿浆(一200目含量占90 — 95%以上)后,先进行氟化浸出,再用活性炭直接从矿浆中吸附已溶金载金、炭解吸电积金泥直接分离提纯熔炼的工艺方法。包括原料准备、搅拌氟化浸出活性炭逆流吸附、载金炭解吸电积、金泥分离提纯熔炼铸锭、活性炭活化再生和含氟污水处理等七个作业阶段。 全泥氧化炭浆工艺-原料准备阶段 破碎阶段 —般采用两段开路破碎或两段一闭路破碎流程(图2)。含金物料经过预先筛分,筛上粗物料进入一段破碎,破碎后再经二段筛分破碎后即进入磨矿作业。作业的目的主要控制各段破碎比和保证二段破碎产品的粒度,采用二段一闭路流程更能严格保证破碎物的粒度。一般各段破碎比为3?5,太大或太小均不利于提高破碎效率、降低成本和保护设备。二段破碎产品粒度应小于广1.5cm,最大不超过 3cm,可以通过
调节破碎机排矿口尺寸来控制。生产中要贯彻“预先筛分,多破少磨”的原则。磨矿阶段 多采用两段两闭路磨矿流程。第一段闭路磨矿分级流程由格子型球磨机和螺旋分级机组成。第二段闭路磨矿分级流程由溢流型球磨机和水力旋流器组成。将第二段闭路磨矿分级流程的预先分级和检查分级合并在一起有利于提高磨矿效率和保证产品细度。破碎好的含金物料经过第一段闭路磨矿分级流程后,矿浆中 -200目含量为55%- 65%O再经过第二段闭路磨矿分级流程后矿浆中一200目物料含量就可达90%- 9概以上,符合全泥氟化工艺的细度要求。本段作业主要控制磨矿浓度、溢流浓度和溢流细度。一般磨矿浓度:第一段为75%- 80%,第二段为60365%;溢流浓度:第一段为25%"30%,第二段为14%- 20%;溢流细度(一 200目含量):第一段为55%"65%,第二段为90写一95%以上。磨矿浓度的控制主要通过调节给水量、给矿量和返砂比等,若磨矿浓度偏高,则増加给水量、减少给图3两段两闭路磨矿流程矿量,増大返砂比等,反之亦然。溢流浓度的控制可以通过调节溢流给水量,溢流堰高低,进矿口,排矿口、溢流口大小等,而溢流细度的控制则要调节溢流堰高低、溢流口大小及钢球量、钢球配比、返砂比,磨矿浓度,溢流浓度等。总之,在磨矿作业中各项技术参数都是互相联系,相辅相成、相互制约的,因此在调节控制的过程中要综合考虑,协调作用。 除屑作业 多级除屑流程。第一级除屑作业设在碎矿前,要人工捡出原矿中木屑等杂物。第二级除屑作业设在螺旋分级机的溢流处,采用孔径为2飞mm的平面筛板。第三级除
全泥氰化炭浆工艺
全泥氰化炭浆法提金冶炼工艺是指将金矿石全部磨碎泥化制成矿浆(一200目含量占90一95%以上)后,先进行氰化浸出,再用活性炭直接从矿浆中吸附已溶金载金、炭解吸电积金泥直接分离提纯熔炼的工艺方法.包括原料准备、搅拌氰化浸出活性炭逆流吸附、载金炭解吸电积、金泥分离提纯熔炼铸锭、活性炭活化再生和含氰污水处理等七个作业阶段. 破碎阶段 ?一般采用两段开路破碎或两段一闭路破碎流程(图2).含金物料经过预先筛分,筛上粗物料进入一段破碎,破碎后再经二段筛分破碎后即进入磨矿作业。作业的目的主要控制各段破碎比和保证二段破碎产品的粒度,采用二段一闭路流程更能严格保证破碎物的粒度。一般各段破碎比为3~5,太大或太小均不利于提高破碎效率、降低成本和保护设备。二段破碎产品粒度应小于1~1.5cm,最大不超过3cm,可以通过调节破碎机排矿口尺寸来控制。生产中要贯彻“预先筛分,多破少磨"的原则。 磨矿阶段 多采用两段两闭路磨矿流程。第一段闭路磨矿分级流程由格子型球磨机和螺旋分级机组成。第二段闭路磨矿分级流程由溢流型球磨机和水力旋流器组成。将第二段闭路磨矿分级流程的预先分级和检查分级合并在一起有利于提高磨矿效率和保证产品细度。破碎好的含金物料经过第一段闭路磨矿分级流程后,矿浆中一200目含量为55%一65%。再经过第二段闭路磨矿分级流程后矿浆中一200目物料含量就可达90%一95%以上,符合全泥氰化工艺的细度要求.本段作业主要控制磨矿浓度、溢流浓度和溢流细度。一般磨矿浓度:第一段为75%一80%,第二段为60%~65%;溢流浓度:第一段为25%~30%,第二段为14%一20%;溢流细度(一200目含量):第一段为55%~65%,第二段为90写一95%以上.磨矿浓度的控制主要通过调节给水量、给矿量和返砂比等,若磨矿浓度偏高,则增加给水量、减少给图3两段两闭路磨矿流程矿量,增大返砂比等,反之亦然。溢流浓度的控制可以通过调节溢流给水量,溢流堰高低,进矿口,排矿口、溢流口大小等,而溢流细度的控制则要调节溢流堰高低、溢流口大小及钢球量、钢球配比、返砂比,磨矿浓度,溢流浓度等。总之,在磨矿作业中各项技术参数都是互相联系,相辅相成、相互制约的,因此在调节控制的过程中要综合考虑,协调作用。 除屑作业
几种氰化法的介绍
几种氰化法提金介绍 1.氰化法提金概述 氰化法提金是以氰化物的水溶液作溶剂,浸出含金矿石中的金,然后再从含金浸出液中提取金的方法。 氰化法提金主要包括如下两个步骤: (1)氰化浸出:在稀薄的氰化溶液中,并有氧(或氧化剂)存在的条件下,含金矿石中的金与氰化物反应生成一价金的络合物而溶解进入溶液中,得到浸出液。以氰化钾为例,反应式为: 4Au+8KCN+2H2O→4KAu(CN)2+4KOH 氰化浸出金的工艺方法有槽浸氰化法和堆浸氰化法两类。槽浸氰化法是传统的浸金方法,又分渗滤氰化法和搅拌氰化法两种;堆浸法是近20年来才出现的新技术,主要用于处理低品位氧化矿。 自1887发现氰化液可以溶金以来,氰化法浸出至今已有近百年的生产实践,工艺比较成熟,回收率高,对矿石适应性强,能就地产金,所以至今仍是黄金浸出生产的主要方法。 (2)沉积提金:从氰化浸出液中提取金。工艺方法有加锌置换法(锌丝置换法和锌粉置换法)、活性炭吸附法(炭浆法CIP和炭浸法CIL)、离子交换树脂法(树脂矿浆法RIP 和RIL)、电解沉积法、磁炭法等。锌粉(丝)置换法是较为传统的提金方法,在黄金矿山应用较多;炭浆法是目前新建金矿的首选方法,其产金量占世界产金量的50%以上;其余方法在黄金矿山也正日渐得到应用。 2.渗滤氰化法 渗滤氰化法是氰化浸出的工艺方法之一,是基于氰化溶液渗透通过矿石层而使含金矿石中的金浸出的方法,适用于砂矿和疏松多孔物料。 渗滤氰化法的主要设备是渗滤浸出槽,见图1。渗滤浸出槽通常为木槽、铁槽或水泥槽。槽底水平或稍倾斜,呈圆形、长方形或正方形。槽的直径或边长一般为5~12米,高度一般为2~2.5米,容积一般为50~150吨。 图1 渗滤氰化法的工艺过程: (1)装入矿砂及碱:要求布料均匀,粒度一致,疏松一致。有干法和湿法两种装法。干法适于水分在20%以下的矿砂,可用人工或机械装矿。湿法是将矿浆用水稀释后,用砂泵扬送或沿槽自流入槽内。 (2)渗滤浸出:装料完毕后即可把氰化液送入槽中。氰化液在槽中的流向有两种:一种是上进下出。即氰化液从槽顶注入,并在重力作用下自上而下通过矿砂层;一种是下进上出,好氰化液靠压力作用自下而上通过矿砂层。浸出完成后用水洗涤氰化尾矿。 (3)尾矿排出:有干法和湿法两种。干法通过槽底工作门排出氰化尾矿;湿法是用高压水冲刷氰化尾矿,让尾矿浆沿预先安排好的尾矿管(槽)流出。
【CN109970237A】一种氰化尾矿浆脱氰处理方法【专利】
(19)中华人民共和国国家知识产权局 (12)发明专利申请 (10)申请公布号 (43)申请公布日 (21)申请号 201910246516.7 (22)申请日 2019.03.28 (71)申请人 长春黄金研究院有限公司 地址 130000 吉林省长春市朝阳区南湖大 路6760号 (72)发明人 刘强 李哲浩 张宇 迟崇哲 (74)专利代理机构 吉林长春新纪元专利代理有 限责任公司 22100 代理人 魏征骥 (51)Int.Cl. C02F 9/04(2006.01) C02F 101/18(2006.01) C02F 103/10(2006.01) (54)发明名称 一种氰化尾矿浆脱氰处理方法 (57)摘要 本发明涉及一种氰化尾矿浆脱氰处理方法, 属于环保领域中污染物处理方法。包括氰化尾矿 浆固液分离洗涤处理与高压洗涤液脱氰处理两 个单元,氰化尾矿浆经固液分离洗涤处理单元处 理后,产生的压滤液和吹脱液返回至氰化选矿生 产流程,可保障氰化工艺选矿生产用水平衡,回 收尾矿浆中的金、银等有价金属,减少氰化生产 流程中的氰化钠、氧化钙等药剂消耗,产出的压 滤渣达到尾矿库处置或利用污染控制技术要求, 使氰化尾渣合法处置或利用;高效脱氰处理药剂 处理后洗涤液返回氰化尾矿浆固液分离洗涤处 理单元具有正向促进作用,具有处理效率高、处 理效果好、处理费用低、占地面积少等优点,在氰 化尾矿浆治理市场中具有广阔的应用前景。权利要求书1页 说明书5页CN 109970237 A 2019.07.05 C N 109970237 A
权 利 要 求 书1/1页CN 109970237 A 1.一种氰化尾矿浆脱氰处理方法,其特征在于,包括下列步骤: (1)氰化尾矿浆固液分离洗涤处理:将氰化尾矿浆泵入至带有洗涤、吹脱功能的压滤机内进行压滤、吹脱与高压洗涤,产生的压滤液和吹脱液返回至氰化选矿生产流程,保证生产用水,回收有价金属元素,产生的高压洗涤液进入下一步处理流程进行脱氰处理,高压洗涤后的压滤渣达到《黄金行业氰渣污染控制技术规范》(HJ943-2018)尾矿库处置或利用污染控制技术要求; (2)高压洗涤液脱氰处理:将高压洗涤液泵入至搅拌槽内,加入高效脱氰处理药剂搅拌或曝气处理,处理时间为0.5~2h,脱氰处理后的高压洗涤液返回至氰化尾矿浆固液分离洗涤处理单元,作为高压洗涤水使用。 2.根据权利要求1所述的一种氰化尾矿浆脱氰处理方法,其特征在于:所述步骤(1)中,压滤、吹脱与高压洗涤的工艺次序可根据氰化尾矿浆中的氰化物含量及分离洗涤脱氰的难易程度进行重复设定,保证洗涤后的压滤渣达到《黄金行业氰渣污染控制技术规范》(HJ943-2018)尾矿库处置或利用污染控制技术要求。 3.根据权利要求1所述的一种氰化尾矿浆脱氰处理方法,其特征在于:所述步骤(2)中,高效脱氰处理药剂是亚硫酸钠、硫酸铜、过硫酸钠、硫酸亚铁和硫酸锌,按照摩尔比为8:(1~2):(1~2):(1~5):(1~5)的比例混合均匀而成。 4.根据权利要求3所述的一种氰化尾矿浆脱氰处理方法,其特征在于:所述步骤(2)中,高效脱氰处理药剂以固体或配成5%~20%的质量浓度液体加入。 2
氰化炭浆法提金
氰化炭浆法提金(一) 人们早在1880年就开始用活性炭从含金溶液中回收金银。但作 为一种提金的新工艺直到20世纪70年代才得到迅速发展并臻于 完善。1973年美国霍姆斯特克炭浆厂投产以来,炭浆法工艺在 全世界范围内得到广泛应用,已有 40多个厂投产,许多新建的 大型黄金矿山都采用了炭浆法工艺。 炭浆法工艺是在常规的氰化浸出、锌粉置换法基础上改 革后 的回收金银的新工艺。主要 由浸出原料制备、搅拌浸出与 逆流炭吸附、载金炭解吸、电积电解或脱氧锌粉置换、熔炼铸锭 及活性炭的再生活化等主要作业组成。 KCN r IF 篆滾再曝城 「林严 til 貳门;/■ -T 一嚮…一丄」 pi tt
1浸出原料制备:通常是将原矿经两段(或三段)一闭 路碎矿、两段磨矿,制备成适合氰化浸出的矿浆。根据我国含金矿石的特性和生产实践,磨矿细度一般为80?90% -200目。磨好的矿浆一般经浸前浓缩机脱水,以提高浸出浓度。 2搅拌浸出与逆流炭吸附:浸出条件与常规氰化法相同,一般用5?8段浸出。炭的逆流吸附有两种方式,一种是在浸出 槽添加活性炭进行逆流吸附,边浸出边吸附,通常称为炭浸法 (CIL),张家口、潼关、红花沟等金矿的炭浆厂米用这种方式;另一种是在氰化浸出之后再加几个炭吸附槽进行4?6段逆流炭 吸附,通常称为炭浆法(CIP),灵湖、赤卫沟金矿炭浆厂采用这种方式。活性炭的添加量为每升矿浆15?40克,粒度6?16 目。采用空气提升器或串炭泵定时进行逆流串炭。炭吸附的总时 间一般为6?8小时,金的吸附率在99%以上。炭载金为3?7 千克/吨。 炭吸附槽的设计非常关键,其好坏直接影响到炭的磨损程度,从而影响到炭浆厂的技术经济指标。单纯就炭的磨损而言, 当然是空气搅拌槽最好,但它功率消耗高,增加生产成本。对机械搅拌槽来说,关键是确定叶轮的形状、转速和线速度,要尽量减少叶轮的剪 切力,以使炭的磨损减少到最小程度。据有关资料 报导,目前国内外比较理想的炭吸附槽是双叶轮、中空轴进气的机械搅拌槽
全泥氰化炭浆工艺讲解学习
全泥氰化炭浆工艺
全泥氰化炭浆工艺 - 概述 全泥氰化炭浆法提金冶炼工艺是指将金矿石全部磨碎泥化制成矿浆(一200目含量占90一95%以上)后,先进行氰化浸出,再用活性炭直接从矿浆中吸附已溶金载金、炭解吸电积金泥直接分离提纯熔炼的工艺方法。包括原料准备、搅拌氰化浸出活性炭逆流吸附、载金炭解吸电积、金泥分离提纯熔炼铸锭、活性炭活化再生和含氰污水处理等七个作业阶段。 破碎阶段 一般采用两段开路破碎或两段一闭路破碎流程(图2)。含金物料经过预先筛分,筛上粗物料进入一段破碎,破碎后再经二段筛分破碎后即进入磨矿作业。作业的目的主要控制各段破碎比和保证二段破碎产品的粒度,采用二段一闭路流程更能严格保证破碎物的粒度。一般各段破碎比为3~5,太大或太小均不利于提高破碎效率、降低成本和保护设备。二段破碎产品粒度应小于1~1.5cm,最大不超过 3cm,可以通过调节破碎机排矿口尺寸来控制。生产中要贯彻“预先筛分,多破少磨”的原则。 磨矿阶段 多采用两段两闭路磨矿流程。第一段闭路磨矿分级流程由格子型球磨机和螺旋分级机组成。第二段闭路磨矿分级流程由溢流型球磨机和水力旋流器组成。将第二段闭路磨矿分级流程的预先分级和检查分级合并在一起有利于提高磨矿效
率和保证产品细度。破碎好的含金物料经过第一段闭路磨矿分级流程后,矿浆中一200目含量为55%一65%。再经过第二段闭路磨矿分级流程后矿浆中一200目物料含量就可达90%一95%以上,符合全泥氰化工艺的细度要求。本段作业主要控制磨矿浓度、溢流浓度和溢流细度。一般磨矿浓度:第一段为75%一80%,第二段为60%~65%;溢流浓度:第一段为25%~30%,第二段为14%一20%;溢流细度(一200目含量):第一段为55%~65%,第二段为90写一95%以上。磨矿浓度的控制主要通过调节给水量、给矿量和返砂比等,若磨矿浓度偏高,则增加给水量、减少给图3两段两闭路磨矿流程矿量,增大返砂比等,反之亦然。溢流浓度的控制可以通过调节溢流给水量,溢流堰高低,进矿口,排矿口、溢流口大小等,而溢流细度的控制则要调节溢流堰高低、溢流口大小及钢球量、钢球配比、返砂比,磨矿浓度,溢流浓度等。总之,在磨矿作业中各项技术参数都是互相联系,相辅相成、相互制约的,因此在调节控制的过程中要综合考虑,协调作用。 除屑作业 多级除屑流程。第一级除屑作业设在碎矿前,要人工捡出原矿中木屑等杂物。第二级除屑作业设在螺旋分级机的溢流处,采用孔径为2~3mm的平面筛板。第三级除屑作业设在水力旋流器给矿前,采用20目的平面筛网。第四级除屑作业设在浓缩脱水前,采用24~28目的弧形筛。 本段作业须及时清除筛上杂物,并经常检查筛网使用情况,发现损坏及时更换,以保证矿浆的除屑质量。 矿浆在氰化浸出前需要严格除屑是因为原矿带进的木屑,砂砾、导火线、编织袋的碎片、渣子等杂物,容易造成水力旋流器的进浆口及沉砂口,浓缩机的排矿
氰化法提金工艺
氰化法提金工艺—锌粉置换篇 传统的氰化法提金工艺主要包括浸出、洗涤、置换(沉淀)三个工序。 ①浸出——矿石中固体金溶解于含氧的氰化物溶液中的过程。 ②洗涤——为回收浸出后的含金溶液,用水洗涤矿粒表面以及矿粒之间的已溶金,以实现固液分离的过程。 ③置换——用金属锌从含金溶液中使其还原、沉淀,回收金的过程。 20世纪以来,从氰化矿浆中回收金是先进行矿浆的洗涤,然后进行贵液的澄清、除气。从澄清的贵液中沉淀金,一直沿用锌粉置换法。20世纪60年代以来才发展起来的向矿浆中加入活性炭的“炭浆法”发展很快。随着对离子交换剂应用的研究,采用离子交换树脂从氰化液或氰化矿浆中吸附金的方法亦具有重要的实用价值。在氰化液的溶剂萃取提金方面也作过一些研究。当往氰化含金液中加人硫酸时,可用异戊醇来萃取金,萃取率随硫酸浓度的升高而增加。如在2mol/L的硫酸液中进行萃取,还可使金与砷、铁等杂质分离。使用氧代烷氧基磷酸酯从氰酸盐碱性液中萃取金,萃取指标令人满意;使用亚硫酸钠反萃取也获得了较好的结果等等。 1.氰化浸金 用含氧的氰化物溶液把矿石中的金溶解出来的过程叫氰化浸出。目前,无论从工艺、设备、管理或操作等方面都已日臻完善。如前所述,金在含有氧的氰化物溶液中的溶解,实质上是一个电化学腐蚀过程。 浸出过程中主要使用的药剂是氰化物和保护碱两种。 1)氰化物 工业上用于氰化法浸出金的氰化物主要有氰化钾(KCN)、氰化钠(NaCN)、氰化钙
[Ca(CN)2]和氰化铵(NH4CN)四种。 在生产中常用的氰化物是氰化钠,它是一种剧毒的白色粉末,商品氰化钠一般压制成球状或块状。 工业上也有用氰熔体作为浸出药剂的。它是将氰化钙、食盐和焦炭混合后在电炉中熔化而成的一种混合物。除了含40%-45%的Ca(CN)2和NaCN以外,还含有一些对氰化过程有害的杂质,如可溶性硫化物、碳以及一些不溶性杂质等。其特点是价格便宜,但用量大,约为氰化钠的2-2.5倍。为了消除有害杂质的影响,使用氰熔体时应进行预先处理。处理方法是通入空气强烈搅拌或往溶液中加入适量的铅盐。 在理论上,溶解1gAu只需消耗0.5g氰化钠,但在实际生产中,氰化物的消耗值为理论量的20-200倍,甚至更高一些。消耗量的多少主要取决于矿石中能与氰化物起反应的其他成分的含量。 2)保护碱 保护碱主要是为了保持氰化物溶液的稳定性,减少氰化物的水解损失。使碱在氰化浸出中的加入保持在浸出槽或者是氰化原矿的磨矿过程中。当矿石成分复杂,含有一些诸如磁黄铁矿之类对氰化过程有害的矿物时,保护碱在磨矿过程中加入,有利于这些有害矿物氧化或形成沉淀除去。 保护碱可以是氢氧化钾和氢氧化钠,但更常用的是价格便宜的石灰(氢氧化钙)。如若处理含金碲矿这类需要强碱度的矿石时,还是用氢氧化钠为好。 保护碱的加入量应当适量,一般维持矿浆的pH为10-11即可。此时,矿浆中CaO质量分数约为0.01%-0.02%。过低不利于防止氰化物水解,过高尽管能促使带负电荷的硅泥絮凝,有利于矿浆沉淀和液体净化,但对金的浸出速度有明显的不利影响。
氰化法提金的基本原理1121212
氰化法提金的基本原理?888 (2006-1-10) 氰化法提金的基本原理?氰化法提金浸出的主要影响因素? 氰化法提金是从金矿石中提取金的主要方法之一。氰化物对金溶解作用机理的解释目前尚不一致,多数认为金在氰化溶中有氧存在的情况下可以生成一种金的络合而溶解其基本反应式为:4Au+8KCN+O2+2H2O— 4KAu(CN)2+4KOH 一般认为金被氰化物溶解发生两步反应: 2Au+4KCN+O2+2H2O— 2(CN2+H2O+2KOH 2Au+4KCN+O2+H2O2—2KAu(CN)2+2KOH 金的表面在氰化物溶液中逐渐地由表及里地溶解。溶液中氧的浓度与金的溶解速度有关. 浸出时氰化物浓度一般为,金的溶解速度随氰化物浓度的提高而呈直线上升到最大值。然后缓慢上升,当氰化物浓度达时,金的溶解速度和氰化物浓度无关,甚至下降(因氰化物水解)。金的溶解速度随氧浓度上升而增大,采用富氧溶被或高压充气氰化可以强化金的溶解。氰化试剂溶解金银的能力为:氰化铵>氰化钙氰化钠>氰化钾。氰化钾的价格最贵,目前多数使用氰化钠,氰化物的耗量取决于物料性质和操作因素,常为理论量的20-200倍. 物料性质影晌金的浸出率。氰化法虽是目前提金的主要方法,但某些含金矿物原料不宜直接采用氰化法处理,若矿石中铜、砷、锑、铋、硫、磷、磁铁矿、白铁矿等组分含量高时将大大增加氰化物耗量成消耗矿桨中的氧。降低金的浸出率,矿石中含碳高时,碳会吸附已溶金而随尾矿损失。预先氧化焙烧或浮选方法可除去有害杂质的影晌。氰化物水解反应为:KCN+H2OyKOH+HCN因此会挥发出有毒的HCN;加入石灰是氰化物水解减弱,上式反应向左方向进行,减少氰化物的损失。石灰还有中和酸类物质作用并可沉淀矿浆中得有害离子,使金的溶解处于最佳条件,常用石灰作保护碱。石灰加入量使矿浆值达到11~12为宜,矿浆lang=EN-值过高时对溶金不利。金粒大小主要影晌氰化时间,粗拉金(>74微米)的溶解速度慢。所以氰化前采用混汞、重选或浮选预先回收粗粒金是合理的。在磨矿过程中使细金粒充分单体解离仍是提高金的浸出率重要因素。 氰化时矿泥含量和矿浆浓度直接影晌组分扩散速度。矿浆浓度应小于30~33%。矿泥多时矿浆浓度应小于22-25%,但浓度不宜过低,否则增加氰化物的消耗。 氰化时间取决于物料性质、氰化方式及氰化条件而异。一般搅拌氰化浸出时间常大于24小时,有时长达40小时以上,氰化碲时需72小时,渗滤氰化浸出需五天以上。 从氰化浸出液中提金的方法有哪些方法? 从氰化浸出液中提金的方法比较多,如果用炭浆法(CIP).炭浸法(CIC),磁碳法(MCIP)或树脂交换法可以去固液分离作业。一般氰化矿浆经固液分离得到贵液(含金溶液).从贵液中提金的方法有锌置换沉淀法、活性炭吸附法、离子交换树脂吸附法或电解沉积法。用金属锌丝或锌粉从贵液中把金置换沉淀是常用的方法。贵液在进入置换沉淀作业之前经澄清以除去其中的矿泥和悬浮物,因这些杂质对下一步的置换沉淀作业有害. 锌置换沉淀金的基本原理是:在贵液中的锌会溶解于溶液中而使金沉淀出来,贵液中的离子Au(CN)2-与Zn作用的反应式通常写成: 2KAu(CN) 2+3Zn+4KCN+2H2O 2Au↓+2K2Zn(CN)4+K2ZnO2+H2
黄金提炼工艺
金在矿石中的含量极低,为了提取黄金,需要将矿石破碎和磨细并采用选矿方法预先富集或从矿石中使金分离出来。黄金选矿中使用较多的是重选和浮选,重选法在砂金生产中占有十分重要的地位,浮选法是岩金矿山广为运用的选矿方法,目前我国80%左右的岩金矿山采用此法选金,选矿技术和装备水平有了较大的提高。 (一)破碎与磨矿 据调查,我国选金厂多采用颚式破碎机进行粗碎,采用标准型圆锥碎矿机中碎,而细碎则采用短头型圆锥碎矿机以及对辊碎矿机。中、小型选金厂大多采用两段一闭路碎矿,大型选金厂采用三段一闭路碎矿流程。为了提高选矿生产能力,挖掘设备潜力,对碎矿流程进行了改造,使磨矿机的利用系数提高,采取的主要措施是实行多碎少磨,降低入磨矿石粒度。(二)重选重选在岩金矿山应用比较广泛,多作为辅助工艺,在磨矿回路中回收粗粒金,为浮选和氰化工艺创造有利条件,改善选矿指标,提高金的总回收率,对增加产量和降低成本发挥了积极的作用。山东省约有10多个选金厂采用了重选这一工艺,平均总回收率可提高2%~3%,企业经济效益好,据不完全统计,每年可得数百万元的利润。河南、湖南、内蒙古等省(区)亦取得好的效果,采用的主要设备有溜槽、摇床、跳汰机和短锥旋流器等。从我国多数黄金矿山来看,浮—重联合流程(浮选尾矿用重选)适于采用,今后应大力推广阶段磨矿阶段选别流程,提倡能收、早收的选矿原则。 (三)浮选 据调查,我国80%左右的岩金矿山采用浮选法选金,产出的精矿多送往有色冶炼厂处理。由于氰化法提金的日益发展和企业为提高经济效益,减少精矿运输损失,近年来产品结构发生了较大的变化,多采取就地处理(当然也由于选冶之间的矛盾和计价等问题,迫使矿山就地自行处理)促使浮选工艺有较大发展,在黄金生产中占有相当的重要地位。通常有优先浮选和混合浮选两种工艺。近年来在工艺流程改造和药剂添加制度方面有新的进展,浮选回收率也明显提高。据全国40多个选金厂,浮选工艺指标调查结果表明,硫化矿浮选回收率为90%,少数高达95%~97%;氧化矿回收率为75%左右;个别的达到80%~85%。近年来,浮选工艺流程的革新改造以及科研成果很多,效果明显。阶段磨浮流程,重—浮联合流程等,是目前我国浮选工艺发展的主要趋势。如湘西金矿采用重—浮联合流程,进行阶段磨矿阶段选别,获得较好指标,回收率提高6%以上;焦家金矿、五龙金矿、文峪金矿、东闯金矿等也取得一定的效果。又如新城金矿,原流程为原矿直接浮选,由于含泥较高(矿石本身含泥高,再加采矿尾砂胶结充填强度不够,带入部分泥砂)使选矿指标连续下降。经考查试验,采用了泥砂分选工艺流程,回收率由93.05%提高到95.01%,精矿品位135g/t提高到140g/t,稳定了生产。金厂峪金矿由于原矿品位逐年下降,因此使浮选指标降低,经与沈阳黄金学院等单位合作试验研究采用分支浮选工艺,提高了浮选指标和精矿品位。这一科研成果(于1988年1月黄金总公司通过了技术鉴定),为浮选工艺改造得到了新的启示。当然,浮选法和其他方法一样不是万能的,不可能对所有含金矿石都有效,主要还要考虑矿石性质,在选择工艺流程时,需进行多方面的论证和试验。 近几年来,为提高分选效果,在工艺不断改进的同时,对药剂添加制度和混合用药方面也作了不少改进和研究,在加药实现自动控制方面也有新的进展。 (四)化选-水冶提金工艺 1.混汞法提金 混汞法提金工艺是一种古老的提金工艺,既简便,又经济,适于粗粒单体金的回收。我国不少黄金矿山还沿用这一方法。随着黄金生产的发展和科学技术进步,混汞法提金工艺也不断得到了改进和完善。由于环境保护要求日益严格,有的矿山取消了混汞作业,为重选、浮选和氰化法提金工艺所取代。 在黄金生产中,混汞法提金工艺仍有其重要的作用,在国内外均有应用实例。目前河北张家口、辽宁二道沟、吉林夹皮沟、山东沂南等不少金矿应用了此工艺。辽宁二道沟金矿原为单一浮选流程,根据矿石性质改为混汞加浮选联合流程,总回收率提高7.81%(混汞回收率达64.6%),尾矿品位由0.74g/t降到0.32g/t,年获效益为158万元。混汞法提金工艺关键在于如何采取防护措施,消除汞毒污染。 2.氰化法提金工艺
全泥氰化流程
全泥氰化炭浆法提金工艺流程及特点 全泥氰化炭浆法提金工艺是氰化提金的方法之一。是含金物料氰化浸出完成之后,一价金氰化物〔KAu(CN)2〕进行炭吸附的工艺过程。人们早已发现活性炭可以从溶液中吸附贵金属的特性,开始只从清液中吸附金,将载金炭熔炼以回收金。由于氰化矿浆须经固液分离得到清液和活性炭不能返回使用,此法在工业上无法与广泛使用的锌置换法竞争。后来用活性炭直接从低化矿浆中吸附金,这样就省去了固液分离作业;载金活性炭用氢氧化钠和氰化钠混合液解吸金银,活性炭经过活化处理可以返回使用。因此近年来炭浆法提金发展成为提金新工艺,我国在河南省灵湖金矿和吉林省赤卫沟金矿等建成了应用炭浆法提金工艺的生产工厂。 炭浆法提金工艺过程包括原料制备及活性炭再生等主要作业组成,其工艺流程见图8-2
(1)原料制备 把含金物料碎磨至适于氰化粒度,一般要求小于28目并除去木屑等杂质,经浓缩脱水使浸出矿浆浓度达到45~50%为宜; (2)搅拌浸出 与常规氰化法相同,一般为5~8个搅拌槽。 (3)炭吸附
氰化矿浆进入搅拌吸附槽(炭浆槽),河南省灵湖金矿在吸浆僧中装有格式筛和矿浆提升器,用它实现活性炭和矿浆逆向流动,吸附矿浆中已溶的金,桥式筛可以减少活性炭的磨损。目前桥式筛的筛孔易被活性炭堵塞,要用压缩空气清扫。 (4)载金炭解吸 目前可用四种方法解吸:(1)热苛性氰化钠溶液解吸;(2)除浓度苛性氰化钠溶液加酒精解吸;(3)在加温加压条件下用苛性氰化钠溶液解吸;(4)高浓度苛性氰化钠溶液解吸。 (5)电积法或常规锌粉置换沉淀金 载金炭解吸可得到含金达600克/米3的高品位贵液,经电积卖锌置换法得到金粉,并送熔炼得到金锭。 (6)活性炭的再生利用 解吸后的活性炭先用稀硫酸(硝酸)酸洗,以除去碳酸盐等聚积物,经几次返回使用后需进行热力活化以恢复炭的吸附活性。 炭浆法提金主要适用于矿泥含量高的含金氧化矿石,由矿石含泥高,固液分离困难,现有的过滤机不能使贵液和矿渣有效分离,因此常规的氰化法不能得到较好的技术经济指标。实践表明:炭浆法提金在工业生产上取得了好成果,灵湖金矿含金为8克/吨左右,金的总回收率达到93%~94%。 其他提取金矿方法:
全泥氰化炭浆工艺
全泥氰化炭浆法提金冶炼工艺就是指将金矿石全部磨碎泥化制成矿浆(一200目含量占90一95%以上)后,先进行氰化浸出,再用活性炭直接从矿浆中吸附已溶金载金、炭解吸电积金泥直接分离提纯熔炼得工艺方法。包括原料准备、搅拌氰化浸出活性炭逆流吸附、载金炭解吸电积、金泥分离提纯熔炼铸锭、活性炭活化再生与含氰污水处理等七个作业阶段。 破碎阶段 ?一般采用两段开路破碎或两段一闭路破碎流程(图2)。含金物料经过预先筛分,筛上粗物料进入一段破碎,破碎后再经二段筛分破碎后即进入磨矿作业.作业得目得主要控制各段破碎比与保证二段破碎产品得粒度,采用二段一闭路流程更能严格保证破碎物得粒度。一般各段破碎比为3~5,太大或太小均不利于提高破碎效率、降低成本与保护设备.二段破碎产品粒度应小于1~1、5cm,最大不超过3cm,可以通过调节破碎机排矿口尺寸来控制。生产中要贯彻“预先筛分,多破少磨”得原则。 磨矿阶段 ?多采用两段两闭路磨矿流程。第一段闭路磨矿分级流程由格子型球磨机与螺旋分级机组成。第二段闭路磨矿分级流程由溢流型球磨机与水力旋流器组成。将第二段闭路磨矿分级流程得预先分级与检查分级合并在一起有利于提高磨矿效率与保证产品细度.破碎好得含金物料经过第一段闭路磨矿分级流程后,矿浆中一200目含量为55%一65%。再经过第二段闭路磨矿分级流程后矿浆中一200目物料含量就可达90%一95%以上,符合全泥氰化工艺得细度要求。本段作业主要控制磨矿浓度、溢流浓度与溢流细度。一般磨矿浓度:第一段为75%一80%,第二段为60%~65%;溢流浓度:第一段为25%~30%,第二段为14%一20%;溢流细度(一200目含量):第一段为55%~65%,第二段为90写一95%以上。磨矿浓度得控制主要通过调节给水量、给矿量与返砂比等,若磨矿浓度偏高,则增加给水量、减少给图3两段两闭路磨矿流程矿量,增大返砂比等,反之亦然。溢流浓度得控制可以通过调节溢流给水量,溢流堰高低,进矿口,排矿口、溢流口大小等,而溢流细度得控制则要调节溢流堰高低、溢流口大小及钢球量、钢球配比、返砂比,磨矿浓度,溢流浓度等。总之,在磨矿作业中各项技术参数都就是互相联系,相辅相成、相互制约得,因此在调节控制得过程中要综合考虑,协调作用。 除屑作业
几种氰化法提金介绍
. 2016-12-06 廖德华紫金矿业HOT全球矿业资讯 1.氰化法提金概述 氰化法提金是以氰化物的水溶液作溶剂,浸出含金矿石中的金,然后再从含金浸出液中提取金的方法。 氰化法提金主要包括如下两个步骤: (1)氰化浸出:在稀薄的氰化溶液中,并有氧(或氧化剂)存在的条件下,含金矿石中的金与氰化物反应生成一价金的络合物而溶解进入溶液中,得到浸出液以氰化钾为例,反应式为:4Au+8KCN+2H2O→4KAu(CN)2+4KOH 氰化浸出金的工艺方法有槽浸氰化法和堆浸氰化法两类。槽浸氰化法是传统的浸金方法,又分渗滤氰化法和搅拌氰化法两种;堆浸法是近20年来才出现的新技术,主要用于处理低品位氧化矿。 自1887发现氰化液可以溶金以来,氰化法浸出至今已有近百年的生产实践,工艺比较成熟,回收率高,对矿石适应性强,能就地产金,所以至今仍是黄金浸出生产的主要方法。 (2)沉积提金:从氰化浸出液中提取金。工艺方法有加锌置换法(锌丝置换法和锌粉置换法)、活性炭吸附法(炭浆法CIP和炭浸法CIL)、离子交换树脂法(树脂矿浆法RIP和RIL)、电解沉积法、磁炭法等。锌粉(丝)置换法是较为传统的提金方法,在黄金矿山应用较多;炭浆法是目前新建金矿的首选方法,其产金量占世界产金量的50%以上;其余方法在黄金矿山也正日渐得到应用。 2.渗滤氰化法 渗滤氰化法是氰化浸出的工艺方法之一,是基于氰化溶液渗透通过矿石层而使含金矿石中的金浸出的方法,适用于砂矿和疏松多孔物料。 渗滤氰化法的主要设备是渗滤浸出槽。渗滤浸出槽通常为木槽、铁槽或水泥槽。槽底水平或稍倾斜,呈圆形、长方形或正方形。槽的直径或边长一般为5~12米,高度一般为2~2.5米,容积一般为50~150吨。 渗滤氰化法的工艺过程: (1)装入矿砂及碱:要求布料均匀,粒度一致,疏松一致。有干法和湿法两种装法。干法适于水分在20%以下的矿砂,可用人工或机械装矿。湿法是将矿浆用水稀释后,用砂泵扬送或沿槽自流入槽内。
全泥氰化提金工艺简介.
全泥氰化炭浆法提金冶炼工艺 全泥氰化炭浆法提金冶炼工艺是指将金矿石全部磨碎泥化制成矿浆(一200目含量占90一95%以上)后,先进行氰化浸出,再用活性炭直接从矿浆中吸附已溶金载金、炭解吸电积金泥直接分离提纯熔炼的工艺方法。包括原料准备、搅拌氰化浸出活性炭逆流吸附、载金炭解吸电积、金泥分离提纯熔炼铸锭、活性炭活化再生和含氰污水处理等七个作业阶段。 原料准备阶段 破碎阶段---一般采用两段开路破碎或两段一闭路破碎流程(图2)。含金物料经过预先筛分,筛上粗物料进入一段破碎,破碎后再经二段筛分破碎后即进入磨矿作业。作业的目的主要控制各段破碎比和保证二段破碎产品的粒度,采用二段一闭路流程更能严格保证破碎物的粒度。一般各段破碎比为3~5,太大或太小均不利于提高破碎效率、降低成本和保护设备。二段破碎产品粒度应小于1~1.5cm,最大不超过3cm,可以通过调节破碎机排矿口尺寸来控制。生产中要贯彻"预先筛分,多破少磨"的原则。 磨矿阶段---多采用两段两闭路磨矿流程。第一段闭路磨矿分级流程由格子型球磨机和螺旋分级机组成。第二段闭路磨矿分级流程由溢流型球磨机和水力旋流器组成。将第二段闭路磨矿分级流程的预先分级和检查分级合并在一起有利
于提高磨矿效率和保证产品细度。破碎好的含金物料经过第一段闭路磨矿分级流程后,矿浆中一200目含量为55%一65%。再经过第二段闭路磨矿分级流程后矿浆中一200目物料含量就可达90%一95%以上,符合全泥氰化工艺的细度要求。本段作业主要控制磨矿浓度、溢流浓度和溢流细度。一般磨矿浓度:第一段为75%一80%,第二段为60%~65%;溢流浓度:第一段为25%~30%,第二段为14%一20%;溢流细度(一200目含量):第一段为55%~65%,第二段为90写一95%以上。磨矿浓度的控制主要通过调节给水量、给矿量和返砂比等,若磨矿浓度偏高,则增加给水量、减少给图3两段两闭路磨矿流程矿量,增大返砂比等,反之亦然。溢流浓度的控制可以通过调节溢流给水量,溢流堰高低,进矿口,排矿口、溢流口大小等,而溢流细度的控制则要调节溢流堰高低、溢流口大小及钢球量、钢球配比、返砂比,磨矿浓度,溢流浓度等。总之,在磨矿作业中各项技术参数都是互相联系,相辅相成、相互制约的,因此在调节控制的过程中要综合考虑,协调作用。 除屑作业---多级除屑流程。第一级除屑作业设在碎矿前,要人工捡出原矿中木屑等杂物。第二级除屑作业设在螺旋分级机的溢流处,采用孔径为2~3mm的平面筛板。第三级除屑作业设在水力旋流器给矿前,采用20目的平面筛网。第四级除屑作业设在浓缩脱水前,采用24~28目的弧形筛。本段作业须及时清除筛上杂物,并经常检查筛网使用情况,发现损坏
氰化工艺过程技术管理
氰化工艺过程技术管理 一、浸出前的预备作业 浸前预备作业,是指浸出作业之前的浸前磨矿和浸前浓缩两个工序。 浸前浓缩的作用有两点:第一,是脱掉多余的水,保证浸出作业有合适浓、细度;第二,是脱除浮选精矿带来的大量浮选药剂。这些药剂是影响浸出效果的有害物质。如黄药可在金表面形成薄膜污染。2#油常在浸出槽表层或洗涤浓密机内形成泡沫层。甚至造成浸出槽跑槽现象。 浸前浓缩要控制浓密机溢流的混浊度。可适量地加些沉淀剂帮助细颗粒沉降,防止溢流跑浑带走细粒精矿造成金属流失,一般在设计中都考虑在浓密机溢流之后建一个沉淀池,池中沉积物定期用泵打回重新处理。注意沉淀剂不可加得过多,否则会给贵液过滤和置换带来不利影响,而且造成浪费。 浸前浓缩重点是控制规定的排矿浓度,一般在35%~55%之间。要求操作工经常用浓度壶手测浓密机底流排矿浓度。非连续排矿的浓密机要注意排矿浓度假象,因为排矿速度太快会出现暂时的局部抽空,排矿浓度会低于下限,这时,千万不可认为浓密机内已排空,以避免浓密机超负荷运转。应暂时停一会排矿,再打开排矿阀门连续排矿。 全泥氰化炭浆厂在浸出之前都安置了除屑筛,由于地下开采必然混入大量木头和杂物,木质可以吸收黄金,为了减少金的损失避免堵塞筛网,必须将杂质除掉。 浸前再磨是目前氰化厂必不可少的一项作业。一般根据小型试验的磨矿细度与浸出率关系确定工业生产的合适细度。因只有将金粒表面显露出来,才有可能与氰化物溶液作用而溶解,所以浸前磨矿是浸出前的关键作业。
精矿再磨一般都是使用长筒型小球磨机与旋流器形成闭路。开车前首先应对球磨机、砂泵、旋流器作详细检查,确认没有问题时放可按顺序开车。要经常清理球磨机排矿口筛网上的杂物,碎铁球等,防止异物进入旋流器造成沉砂口堵塞。 要定期检查测定旋流器底流矿浆浓度(磨矿浓度)、溢流浓、细度、要防止旋流器跑粗,当溢流跑粗时,应及时查找原因改正。一般情况下可能有如下几种原因: (一)球磨机缺球。 (二)给矿量过大,或磨矿浓度太小,磨矿效率低。 (三)旋流器工作浓度较高,分级效果不好。 (四)砂泵工作压力不稳,(如泵喘气)可加回流管解决。 (五)旋流器沉砂口直径较小或者堵塞,溢流管直径较大或磨损溢流管插入。 有的氰化厂在再磨过程中,向球磨机加入石灰乳和氰化物。这样做的好处是才浸出前调整了矿浆的pH值,变在球磨机内获得了可观的浸出率,延长了浸出时间。 浸前预备作业是获得较高浸出率的前提,对后部作业影响较大要求运转工必须严格地按照工艺条件和技术操作规定执行,不得马虎。 二、浸出作业 氰化浸出的管理,围绕着一个中心环节-提高金的浸出率。浸出率受诸多因素影响,这些因素可以分为不变因素与可变因素。不变因素一般指相对稳定、受人工操作影响少的因素。如矿石(精矿)本身含杂程度及可浸性,含泥及氧化程度浸出设备的搅拌能力,浸出时间(浸出槽
全泥氰化炭浆工艺 精品
全泥氰化炭浆工艺 目录 概述 原料准备阶段 搅拌氰化浸出阶段 活性炭逆流吸附阶段 载金炭解吸电积阶段 金泥的分离提纯、熔炼铸锭阶段 活性炭活化再生阶段 展开 概述 原料准备阶段 搅拌氰化浸出阶段 活性炭逆流吸附阶段 载金炭解吸电积阶段 金泥的分离提纯、熔炼铸锭阶段 活性炭活化再生阶段 展开 编辑本段 概述 全泥氰化炭浆法提金冶炼工艺是指将金矿石全部磨碎 炭浆法提金工艺流程图 泥化制成矿浆(一200目含量占90一95%以上)后,先进行氰化浸出,再用活性炭直接从矿浆中吸附已溶金载金、炭解吸电积金泥直接分离提纯熔炼的工艺方法。包括原料准备、搅拌氰化浸出活性炭逆流吸附、载金炭解吸电积、金泥分离提纯熔炼铸锭、活性炭活化再生和含氰污水处理等七个作业阶段。[1] 编辑本段 原料准备阶段 破碎阶段 一般采用两段开路破碎或两段一闭路破碎流程(图2)。含金物 常用破碎筛分流程 料经过预先筛分,筛上粗物料进入一段破碎,破碎后再经二段筛分破碎后即进入磨矿作业。作业的目的主要控制各段破碎比和保证二段破碎产品的粒度,采用二段一闭路流程更能严格保证破碎物的粒度。一般各段破碎比为3~5,太大或太小均不利于提高破碎效率、降低成本和保护设备。二段破碎产品粒度应小于1~1.5cm,最大不超过3cm,可以通过调节破碎机排矿口尺寸来控制。生产中要贯彻“预先筛分,多破少磨”的原则。[2]
磨矿阶段 多采用两段两闭路磨矿流程。第一段闭路磨矿分级流程由格子型球磨机和螺旋分级机组成。第二段闭路磨矿分级流程由溢流型球磨机和水力旋流器组成。将第二段闭路磨矿分级流程的预先分级和检查分级合并在一起有利于提高磨矿效率和保证产品细度。破碎好的含金物料经过第一段闭路磨矿分级流程后,矿浆中一200目含量为55%一65%。再经过第二段闭路磨矿分级流程后矿浆中一200目物料含量就可达90%一95%以上,符合全泥氰化工艺的细度要求。本段作业主要控制磨矿浓度、溢流浓度和溢流细度。一般磨矿浓度:第一段为75%一80%,第二段为60%~65%;溢流浓度:第一段为25%~30%,第二段为14%一20%;溢流细度(一200目含量):第一段为55%~65%,第二段为90写一95%以上。磨矿浓度的控制主要通过调节给水量、给矿量和返砂比等,若磨矿浓度偏高,则增加给水量、减少给图3两段两闭路磨矿流程矿量,增大返砂比等,反之亦然。溢流浓度的控制可以通过调节溢流给水量,溢流堰高低,进矿口,排矿口、溢流口大小等,而溢流细度的控制则要调节溢流堰高低、溢流口大小及钢球量、钢球配比、返砂比,磨矿浓度,溢流浓度等。总之,在磨矿作业中各项技术参数都是互相联系,相辅相成、相互制约的,因此在调节控制的过程中要综合考虑,协调作用。[3] 除屑作业 多级除屑流程。第一级除屑作业设在碎矿前,要人工捡出原矿中木屑等杂物。第二级除屑作业设在螺旋分级机的溢流处,采用孔径为2~3mm的平面筛板。第三级除屑作业设在水力旋流器给矿前,采用20目的平面筛网。第四级除屑作业设在浓缩脱水前,采用24~28目的弧形筛。本段作业须及时清除筛上杂物,并经常检查筛网使用情况,发现损坏及时更换,以保证矿浆的除屑质量。 矿浆在氰化浸出前需要严格除屑是因为原矿带进的木屑,砂砾、导火线、编织袋的碎片、渣子等杂物,容易造成水力旋流器的进浆口及沉砂口,浓缩机的排矿口、管道、级间筛等部位的堵塞;砂砾的存在会增大活性炭的磨损;木屑等的存在会吸附已溶金而造成金的流失,木屑还可能在再生窑中转变为易碎炭而降低金的实收率。因此,除屑作业非常重要,要按由粗到细的顺序尽可能地多设除屑筛网层级。[4] 制浆阶段 主要在浓缩机中进行,多采用高效浓密机、单层浓缩机或多层浓缩机。符合全泥氰化炭浆法提金工艺条件的矿浆,其矿浆浓度为40%一45%,矿浆PH值为10一11,而由磨矿作业输送来的矿浆浓度为14%一20%,PH值为7~10。本段作业需通过调节浓缩机底流量和絮凝剂用量来控制矿浆浓度,通过调节加入球磨机中的石灰量或加入浓缩机中的氢氧化钠量来控制矿浆的PH值,使之符合下一步浸出吸附作业要求。[5] 编辑本段 搅拌氰化浸出阶段 搅拌氰化浸出又称预浸作业,一般由两个高效节能浸出槽(l号槽和2号槽)串联组成。矿浆由上段作业输送到1号槽,再由1号槽自流进入2号槽。本段作业主要是控制浸出矿浆中氰根离子浓度和氧含量。适宜的氰根离子浓度为0.05%一0.08%,通过调节氰化钠的给药量来控制。矿浆中氧含量通常用充气量和充气压力来表示,一般充气量为0.02m3/m3·min,充气压力为100KPa。生产中通常以矿浆表面均匀弥散5~15mm直径的小气泡为宜,通过调节气泵总阀门和各槽的充气阀门加以控制。[5] 编辑本段 活性炭逆流吸附阶段 矿浆氰根浓度