包钢链篦机回转窑球团矿生产工艺优化研究
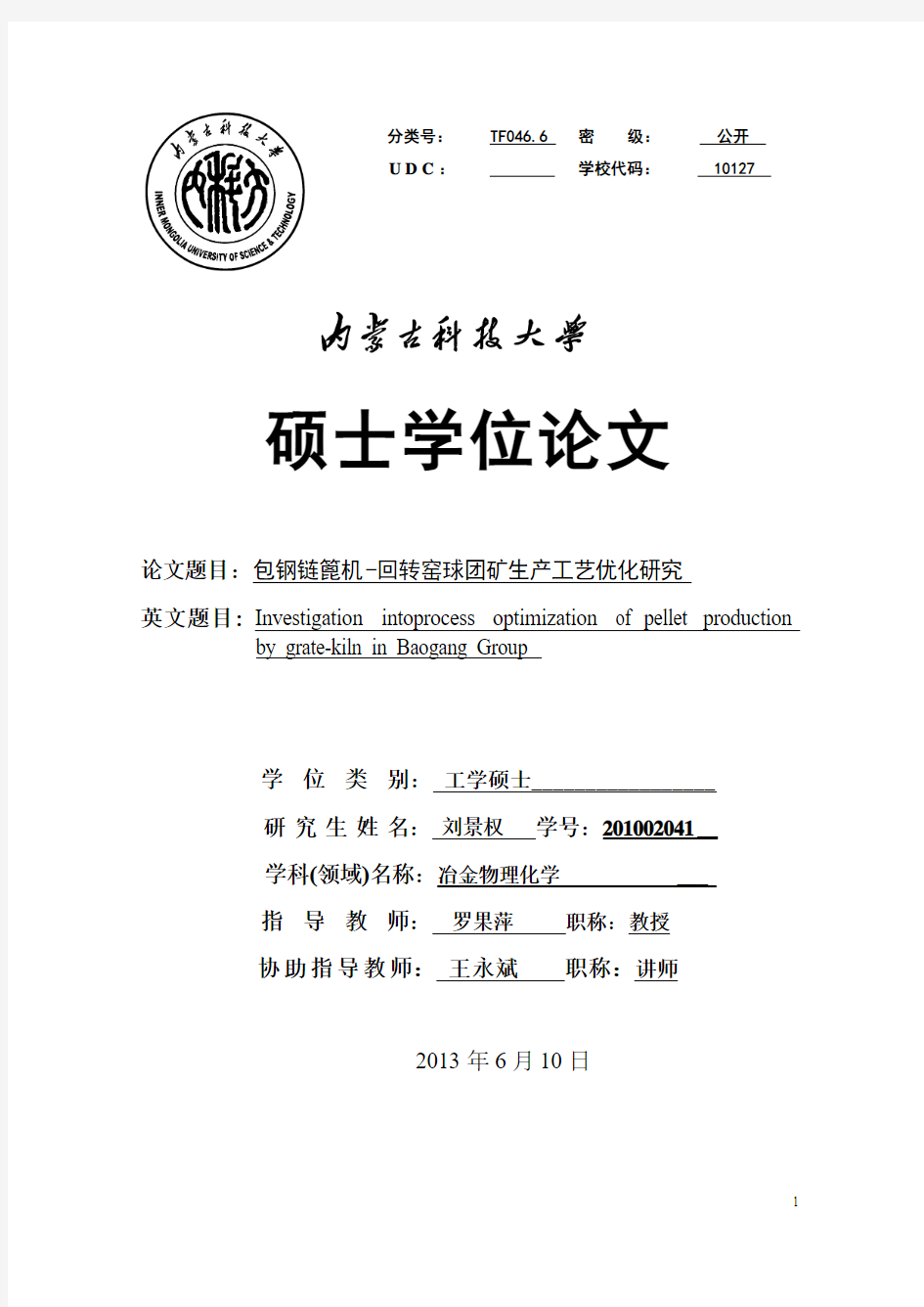

硕士学位论文
论文题目:包钢链篦机-回转窑球团矿生产工艺优化研究
英文题目: Investigation intoprocess optimization of pellet production
by grate-kiln in Baogang Group
学位类别: 工学硕士_________________ 研究生姓名: 刘景权 学号:201002041__ 学科(领域)名称:冶金物理化学 ___ 指导教师: 罗果萍 职称:教授 协助指导教师: 王永斌 职称:讲师
2013年6月10日
摘要
论文结合包钢西部球团生产实践,对其所用四种单一铁矿粉的球团质量、回转窑热工制度、合理配矿比及链篦机工艺制度的优化进行了系统的研究。论文针对性地对包钢西部球团现在所使用的四种铁矿粉的成球性能、生球落下强度、生球抗压强度、预热球抗压强度、成品球抗压强度、预热球矿相、成品球矿相进行了系统研究。并参考包钢西部球团的实际生产工艺,模拟工厂实际配矿比分别将焙烧温度设定为1200℃、1250℃和1300℃时,将焙烧时间分别设定为为20min、25min、30min、35min,研究焙烧温度和焙烧时间对球团矿连晶的影响。最后,按照工厂实际条件将大堆料的配比设定为40%,调整细粒度巴润精矿和粗粒度巴润矿的相对含量,分别在九种工艺制度下对五种选定配矿比进行正交实验。主要以预热球的强度为指标,对最佳配矿比和最佳工艺制度进行验证试验。并对适宜的造球工艺条件进行了研究。再通过对预热球矿相、成品球矿相的分析并结合球团理论知识从而探究包钢西部球团合理的配矿比及链篦机工艺制度的优化。
研究结果表明:对单一铁矿粉而言,成球性:细粒度巴润精矿>再磨矿>粗粒度巴润矿>大堆料;预热球强度:细粒度巴润精矿>再磨矿>大堆料>粗粒度巴润矿;成品球强度:细粒度巴润精矿>大堆料>再磨矿>粗粒度巴润矿。焙烧温度低时,延长焙烧时间对球团矿固结强度的影响较大,当焙烧温度高达1300℃时,焙烧时间对于球团矿固结强度的影响减弱,其主要原因在于高温下赤铁矿连晶已经充分发展,延长焙烧时间对球团矿连晶影响较小。不同配矿比的最优工艺各不相同,但预热二段的最佳温度均为1000℃,链篦机的最佳机速几乎均为1.5m/min。所以,在实际生产中尽量提高预热二段温度、降低机速、加大细粒度巴润精矿配比、限制粗粒度巴润矿的加入量都是提高预热球抗压强度的有效措施。生球水分含量7.5-8.0%、皂土加入量1.5-2.0%、粘结剂加入量0.75%为适宜的造球工艺条件。
关键词:链篦机-回转窑;球团矿;配矿比;工艺优化
Abstract
The thesis is partly based on the practice in Baogang Group and systematically studied the quality of the four kinds of fine iron ores, thermal conditions of grate-kiln, suitable iron ore proportion and process optimization of the grate-kiln. Important indexesincluding pelletizing ability, falling strength of green ball, compression strength of green ball, preheated ball and fired pellet, mineraogical phase of preheated and fired ball have all been thoroughly examined. Moreover, another study was also performedto clarify the effects of roasting time and temperature on interconnected crystal with reference to the practical situation in Baogang Group. Finally, a series of orthogonal test were carried out to find out the best ore proportion and production condition in terms of the strength of preheated ball. The tests were performed by fixing the bulk material proportion as 40% according to practical situation while adjusting the relative contents of fine Barun ore and coarse Barun ore. Thereby, the appropriate conditions for pelletization were clarified. After that, the suitable ore proportion and optimization of grate-kiln were decided by analyzing the mineraogical phase of preheated and fired ball with simultaneous incorporation of theoretical knowledge.
The study shows that:For pelletizing ability, fine Barun ore>regrinding ore>coarse Barun ore> Bulk materials;For preheated ball strength, fine Barun ore>regrinding ore>Bulk materials>coarse Barun ore;For fired ball strength, fine Barun ore>Bulk materials>regrinding ore>coarse Barun ore.The study also reveals that when roasting temperature is low, the extension of roasting time has a strong influence on the bond strength of pellet. As the roasting temperature rises, the influence gradually decreases. The reason lies in the fact that under high temperature condition, the interconnected crystal of hematite has become so strong that the extension of roasting time could not have an appreciable effect one it. On the other hand, liquid phase becomes more as the roasting time is prolonged. The optimum process varies with ore proportion. However, the best preheating temperature is invariably 1000 degrees while the rotation rate is almost 1.5m/min. All these indicate that in practical operation, the preheating temperature should be increased, rotation rate should be lowered down, adding more fine
Barun ore and restricting the coarseBarun ore to increase the compression strength of the preheated ball. The appropriate pelletizing parameters are that moisture of green ball 7.5-8.0%, bentonite addition 1.5-2.0%, and 0.75% binder addition.
Key Words: grate-kiln;pellet;expansion ratio;process optimization
目录
摘要 ................................................................................................................................ I Abstract .................................................................................................................................. II 引言 .. (1)
1文献综述 (2)
1.1我国高炉炉料发展历程 (2)
1.2国内外球团矿生产概况 (4)
1.3球团工艺概述 (6)
1.3.1竖炉工艺概述 (6)
1.3.2带式焙烧机概述 (7)
1.3.3链篦机-回转窑概述 (7)
1.4课题的背景及意义 (8)
1.5研究方案 (9)
2单一铁矿粉球团实验 (10)
2.1包钢西部球团矿原料结构 (10)
2.2单一铁矿粉粒度的测定实验 (12)
2.3单一铁矿粉成球性测定实验 (13)
2.4铁矿粉粒度组成与成球性能分析 (15)
2.5单一铁矿粉球强度实验 (16)
3回转窑热工制度对成品球抗压强度的影响 (21)
3.1实验方案 (21)
3.2结果分析 (21)
4合理配矿比及链篦机工艺制度的优化 (23)
4.1合理配矿原则 (23)
4.2实验方案设计 (25)
4.3不同配矿比球团实验及分析 (25)
4.3.1配矿比(451)球团实验及分析 (25)
4.3.2配矿比(442)球团实验及分析 (28)
4.3.3配矿比(433)球团实验及分析 (31)
4.3.4配矿比(424)球团实验及分析 (34)
4.3.5配矿比(415)球团实验及分析 (36)
4.4配矿比与链篦机工艺优化的关系 (40)
4.5水分、皂土、粘结剂的合理配比 (43)
结论 (46)
参考文献 (47)
在学研究成果 (50)
致谢 (51)
引言
随着我国钢铁工业的快速发展,高炉生产对含铁原料的要求不断提高,高炉“精料”已成为降低成本、提高炼铁竞争力的有效手段。高碱度烧结矿配加高品位的酸性球团矿被普遍认为是较为合理的高炉炉料结构。由于我国高质量酸性球团矿缺口较大,而国际市场球团矿价格日益升高,因而近年来链篦机—回转窑球团生产线在我国得到快速发展,提高链篦机-回转窑氧化球团生产能力和球团矿质量,已成为我国炼铁工业发展的必然趋势[1-4]。
球团矿生产中,铁矿粉占造球原料的90%以上,铁矿粉性能的好坏直接影响球团生产效率和成品球团矿的质量[5-6],从而影响球团生产经济技术指标。球团生产对铁精矿的最基本要求是:(1) 具有较小的粒度;(2) 具有适宜的水分含量;(3) 稳定的化学成分。此外,铁矿粉的成球性、生球强度和爆裂温度、预热干球强度等性能指针对提高链篦机—回转窑的产量和质量也至关重要。
铁矿球团矿因其强度好、粒度均匀、铁品位高、还原性好等诸多优点,在高炉的炉料中越来越受到现代炼铁工作者的喜爱,在炼铁炉料中的比例也随之升高。虽然铁矿酸性氧化球团矿可以采用竖炉、带式焙烧机、链篦机—回转窑三种工艺生产,但链篦机—回转窑因具备如下特点而更适合我国球团厂建设的国情[7-9]:(1)产能大、产品质量好;(2)可用煤作基本燃料;(3)对原料性质发生波动的适应性强;(4)链篦机的耐高温材质价格相对较低,国内已能解决。因而近年来链篦机—回转窑球团工艺在我国得到了快速发展。由于回转窑以煤作为燃料,因此生产成本低,价格波动小。但以煤作为燃料必须有几个要素做保证:(1)选择灰分低、灰分熔点高的煤种;
(2)控制煤粉粒度及控制给煤量;(3)采用合适的烧嘴控制火焰状况。
1文献综述
1.1我国高炉炉料发展历程
新中国成立之初,我们国家的高炉炉料主要是以含铁品位较低的天然块矿和低碱度烧结矿配合使用为主。在当时与其他国家相比高炉生产技术指标较差,高炉的综合利用系数很低,焦比较高,生产能力不足,生铁成本高[10-12]。
到了20世纪50年代,因受到前苏联炼铁进步的影响,我国自主开始生产R=1.20左右的自熔性烧结矿[13-16]。这段期间我国高炉以自熔性烧结矿为主要原料,高炉的综合利用系数有了很大提高,焦比降低、生产能力提升、生铁成本下降。
上世纪70年代,我国高炉的炉料结构又有了新的变化。高碱度烧结矿的大量生产和使用,使高炉炼铁进入了一个全新的时代。这也奠定了在接下来的很长一段时间内,我国高炉炉料以烧结矿为主的基础。同时高炉的综合利用系数再次得到提高。但美中不足的是炼铁工作者在实际生产中发现高碱度烧结矿在高炉炼铁中不可以单独使用。合理炉料结构的问题开始受到炼铁工作者的关注,最终广大的炼铁工作者普遍认为高碱度烧结矿配合酸性球团矿的使用将成为高炉炼铁的合理炉料结构[17-18]。与此同时日本通过高炉的解剖实验,针对不同炉料结构对高炉软熔带的影响,研究合理炉料结构对高炉冶炼的影响。
上世纪80年代,随着合理炉料结构对高炉冶炼影响的不断深入研究,球团烧结技术得到了长足的发展与进步。酸性球团矿的使用配比成了合理炉料结构的重点研究内容。炉料结构的好坏,将直接影响高炉生铁的产量、焦比综合利用系数等。所以,合理的炉料结构将可以大大改善高炉的冶炼强度。
合理的高炉炉料结构并不是一成不变的,炉料结构对高炉冶炼影响亦是千变万化的。使用何种炉料结构才是合理的主要取决于钢铁联合企业自身的铁矿石、煤炭资源条件和当地的地理环境以及炼钢、炼铁的工艺。对于一个大型的钢铁联合企是这样,对于一个大的钢铁工业国家也如此。就像我们国家的宝钢的入炉炉料中高碱度烧结矿约占77%,包钢的入炉炉料中高碱度烧结矿约占65-70%;新疆八一钢铁公司的入炉炉料中酸性球团矿占了65%。世界上一些钢铁大国如美国的高炉入炉炉料主要是以优质的球团矿为主。再如瑞典的SSAB公司入炉炉料中酸性球团矿占了100%。但日本的高炉入炉原料主要以优质的烧结为主。我们不断探究高炉合理炉料
结构的意义在于可持续高效率地利用我国及世界的铁矿石、煤炭资源条件和当地的地理环境以及炼钢、炼铁的新工艺等资源。这样可以保证我国的钢铁工业不断的可持续迅速发展。
随着我国的钢铁工业不断地可持续高速发展,对高炉炼铁原料的需求与日俱增[19-21]。对高炉炼铁原料的质量也随之严格,对铁矿石的需求量也不断增加。我国铁矿石资源的特点是总量虽多,但可供开采利用的不多。而且我国我国铁矿石资源贫矿居多、复合共生矿居多,如白云鄂博的铁矿石就是如此。白云鄂博矿石的特点是:含铁品味低、SiO2含量高,K、Na、F含量偏高的铁、稀土、鈮共生矿。所以我国的铁矿石资源供不应求,每年从巴西、南非、印度、澳大利亚等国进口铁矿石的数量必然将逐年增加。因此,铁矿石资源的高效利用已是迫在眉睫。
每年巴西、南非、印度、澳大利亚等国通过国际贸易向我国供应大量的富矿粉。从这些富矿粉的性质分析它们适合用来生产烧结矿。随着我国的钢铁工业不断地可持续高速发展,对高炉炼铁原料的需求与日俱增国内的铁矿资源严重不足以满足我国钢铁企业的需求。铁矿石的大量进口,在现阶段以及未来的很长一段时间里是不可逆转的。所以我国的高炉原料以烧结矿为就不足为奇了。但近几年链篦机一回转窑的技术逐渐成熟大大带动了球团的发展。虽说现阶段烧结矿仍是我国高炉的主要入炉原料,但近几年配加球团矿的比例正在逐年上升。
2002年首钢200万t球团生产线工业实验的成功,为我国改善高炉的炉料结构,以及球团的生产开辟了新的天地。在铁矿石原料产地使用链篦机-回转窑生产酸性球团矿降低球团生产成本可以大幅度降低,球团的生产能力有了显著的提高。近几年,包钢高炉中的球团矿加入量一般控制在30%以下,但和以前相比较不难发现炉料中的球团矿加入量有了稳步的提高。从包钢的实际生产来看,当包钢高炉中的球团矿加入量超过30%时可能就会出现高炉炉况不顺的情况。一些人认为:这可能是包钢的高炉炼铁工作者还不能适应高炉入炉原料中球团矿配比例增大的操作;另一些人则认为:包钢生产的球团矿的质量达不到高炉冶炼要求所以包钢高炉中的球团矿加入量超过30%。按照我国现阶段高炉冶炼的要求和水平,球团矿质量的要求应满足:球团的SiO2含量应不高于3.5%,球团的铁品位应不小于65%,球团的抗压强度应大于2500N/个,球团的耐磨指数应小于3.5%[19,20],但是包钢生产的球团现阶段还是不可能达到这个标准。
1.2国内外球团矿生产概况
从上世纪40年代开始出现的铁矿石球团矿,是一种强度好、粒度均匀、铁品位高、还原性好的人造富矿。球团矿是细粒度铁精矿粉进行造块的工艺,不同于铁矿石的烧结过程。它可以大量使用国产的大部分含铁品位很低的矿石再磨再选后的细粒度铁精矿粉进行造块。这是一种大量合理开发利用我国大多数贫矿资源的合理工艺,为我国钢铁行业的可持续发展奠定了技术的基础。
对细磨再选后精矿粉而言,采用烧结的办法来进行铁矿石造块,其强度比较低,而且焙烧时消耗的煤炭等能源相对球团矿要多。而且从造块生产过程中最终产品的产量、质量、能耗和环境保护多方面考虑,烧结造块的工艺对我国大部分含铁品位很低的矿石再磨再选后的铁精矿粉都不是十分适用的方法。
上世纪60年代之前只有少数的几个国家在生产球团矿,其中主要国家有:美国、加拿大、日本和瑞典等。在当时,这些国家一年的球团矿年总产量才1600万t。这可以算得上是世界球团矿生产发展开始的第一个阶段。但是随后球团矿生产的发展速度非常快,从上世纪60年代中期开始一直到上世纪70年代初,在不到十年的时间里,生产球团矿的国家就从少数的几个国家发展到了20多个。这些国家一年的球团矿年总产量大约为12000多万t。上世纪80年代初,这些国家一年的球团矿总产量大约为30000多万t。从这个时候开始,球团矿的生产技术工艺和各种生产设备都开始朝着大型化的方向大踏步迈进。这可以算得上是世界球团矿生产发展开始的第二个阶段。20世纪80年代以后,世界球团矿生产的发展开始进入了高速发展的第三个阶段。国外球团矿的生产,已不再单单的追求产量的提升。而是开始考虑如何提高球团矿的各项性能[13,14]、改善球团生产工艺和降低球团生产成本。主要表现在以下这些方面:(1)开发使用球团的新工艺;(2)研发和使用高效、新型的添加剂;(3)改善球团矿的矿物组成;(4)降低球团矿的生产成本。但是按照我国现阶段高炉冶炼的水平和要求,我国生产的球团矿质量大多数不能满足以下要求。优质的球团矿:球团的SiO2含量应不高于3.5%,球团的铁品位应不小于65%,球团的抗压强度应大于2500N/个,球团的耐磨指数应小于3.5%。但是到2006年底,我国的高炉入炉原料中球团矿的配矿比例只有18%左右[22],远远低于美国、加拿大、日本和瑞典这些钢铁工业发达的国家。
下面是国外一些企业生产的球团矿的化学成分(如表1.1所示)[22-26]:从上世纪末到现在,我国的竖炉和带式焙烧机的利用系数提高、以消耗标煤为参考指标的
工序能耗下降、铁矿粉含铁品位上升[27-28]。链篦机-回转窑球团生产装置在这些年得到大力发展。
从上世纪末到现在,球团生产工艺在我国飞速发展,上世纪90年代初期,我国可以生产球团矿的工厂仅仅只有15家,我国一年的球团矿总产量仅仅只有545万t;到上世纪90年代末期,我国可以生产球团矿的工厂已经发展到了22家,我国一年的球团矿总产量也提高到了1044万t;截止2003年,我国可以生产球团矿的工厂已经发展到了40家。此时,我国一年的球团矿总产量高达3000万t。其中,37家拥有竖炉的企业,共建成58座竖炉,这些竖炉的规格多在8m2左右,球团矿的年产量为2000万t;包钢和鞍钢还建成了两条带式焙烧机生产线,年生产能力为310万t;另外,首钢迁安厂的竖炉年产球团200万t,武钢矿业公司的程潮铁矿竖炉球团矿的年产量为120万t,柳钢年产量为120万t,昆钢年产量为120万t,鞍钢弓长岭的二期工程年产量为200万t,太钢峨口年产量为180万t,武钢鄂州建设的链篦机一回转窑生产线年产量为500万t [18];总之,目前国内大中型钢铁企业为了适应高炉炼铁的需要,都在新建或扩建球团厂[29-33]。到了2006年底,我国一年的球团矿总产量高达到7300万t。
表1.1国外球团矿的主要化学成分/%
球团矿名TFe SiO2CaO MgO Al2O3S FeO R
瑞典LKAB 66.80 2.00 0.20 1.45 0.45 0.002 0.90 0.10 印度MANDOVI 64.00 2.20 2.60 0.10 2.30 0.010 0.50 1.18
印度KIOLC 65.00 3.50 0.10 0.05 1.25 0.030 0.40 0.03 智利65.80 3.64 1.94 0.05 0.39 0.01 0.50 0.53 澳大利亚BHP 60.20 3.90 5.38 2.05 ——— 1.38 秘鲁65.60 4.32 0.51 0.85 0.42 0.011 1.30 0.12
美国64.10 4.95 2.36 1.88 0.47 0.003 0.50 0.88 加拿大QCM 65.20 5.30 0.40 0.40 0.50 0.001 0.40 0.07
加拿大IOC 65.70 4.90 0.50 0.30 0.30 0.01 0.40 0.10
澳大利亚63.40 5.40 0.55 0.09 2.84 —0.40 0.10
巴西CVRD 65.87 2.46 2.57 0.08 0.55 0.005 0.57 1.04
巴西Ferteco 65.20 3.00 2.40 0.10 1.00 0.01 0.40 0.80
为了达到高炉入炉炉料结构合理和“精料方针”的高炉冶炼目标,广大炼铁工作者们均将目光投向了球团矿的生产使用。为了使再磨再选的铁精矿粉球团工艺更加合理[34],广大炼铁工作者们从球团矿的基础理论到工业实验以及技术路线和经济效益等多方面进行深入的理论研究和探讨。并进行了大量的实验,这样一来,我国的球团企业的建设出现了一个飞速发展的良好势头。
1.3球团工艺概述
随着球团矿在高炉炉料中的配比不断增加,我国的高炉炼铁技术工艺和钢铁原料工业将会迈上一个意义深远的新台阶。球团焙烧若按工艺的种类来划分的话,应用最广的三大工艺为竖炉、带式焙烧机和链篦机-回转窑。
1.3.1竖炉工艺概述
竖炉球团焙烧工艺是世界上使用最早的球团焙烧工艺[35]。竖炉球团焙烧工艺将球团的干燥、预热、焙烧、冷却均放在竖炉操作完成。
所以竖炉球团焙烧工艺的优点[36-37]:操作工序简单、结构紧凑、投资便宜、维护检修方便、无需特殊材料、热效率高。
但竖炉球团焙烧工艺在理论上存在着固有的、难以克服的缺陷,所以竖炉球团焙烧工艺的缺点[38-40]:
(1)竖炉球团焙烧工艺的球团产品质量差,用竖炉球团焙烧工艺生存的成品球团矿的抗压强度较低、含粉率偏高和均匀性较差。这主要是因为在竖炉中均匀加入困难而导致的结果。
(2)竖炉球团焙烧工艺的单炉生产能力受到限制,规模很难大型化。这样一来就很难与我国高炉的大型化相匹配。因为当竖炉在焙烧放热效率低的球团时,竖炉球团焙烧的球团产量较低。
(3)竖炉球团焙烧工艺对原料的适应性较差。竖炉只能处理磁铁矿精矿球团和赤、磁铁矿混合精矿球团。
(4)竖炉球团焙烧工艺的只能使用气体燃料,这与可用煤作基本燃料的链篦机-回转窑相比就要差一些。
(5)竖炉球团焙烧工艺的冷却问题以及除尘问题还需进一步解决。竖炉下部的冷却带,不足以将球团冷却至120℃以下。
1.3.2带式焙烧机概述
带式焙烧机球团工艺来源于带式烧结机的启发。但带式焙烧机生产细磨铁精矿球团矿与带式烧结机生产铁矿粉烧结矿在固结原理上有着本质上的差别。所以,二者在工业生产技术上也有着天壤之别[41]。
带式焙烧机工艺的优点:
(1)带式焙烧机球团工艺将球团焙烧的整个工艺过程:干燥、预热、焙烧、冷却都放在带式焙烧机上完成。带式焙烧球团工艺具有操作过程简单、控制方便、布置紧凑、设备t位轻等优点。
(2)带式焙烧机具有占地面积小、工程量少、缩减成本、实现焙烧气体的循环利用、降低热耗、降低电耗等优点。
(3)带式焙烧机球团工艺可以适应扩大生产规模的要求和实现设备大型化的需求。最大的带式焙烧机已达到750m2,单机生产高达500万t以上。
(4)带式焙烧机球团工艺对原料的适应性优于竖炉,它可以处理各种矿石。带式焙烧机球团工艺,不会在升温过程中由于球团自身强度的变化和球与球之间的相对运动而产生粉末。因为在带式焙烧机上的整个焙烧过程中,球团都处于静料层状态。
(5)带式焙烧机球团工艺的热效率高主要得益于热系统的合理设置和管路短的设备特点。
带式焙烧机的缺点:
(1)带式焙烧机的制造需大量用到优质的耐高温特殊合金钢。现阶段我国自主研发优质的耐高温特殊合金钢在质量方面难以满足带式焙烧机的制造需。大量优质的耐高温特殊合金钢需从国外进口。
(2)带式焙烧机球团工艺在焙烧过程中,对原料的稳定性要求高。因为带式焙烧机结构紧凑,在焙烧过程中难以调整机速来改变球团在各阶段的停留时间。
(3)带式焙烧机球团工艺生产的球团存在着上下层质量不均匀的现象。球团在焙烧过程中,上下料层在焙烧机各段停留时间不一致,最终影响了成品球团矿的质量。
(4)带式焙烧机球团工艺对燃料的要求高。可以作为带式焙烧机燃料使用的仅仅只有高热值的煤气和重油。
1.3.3链篦机-回转窑概述
链篦机-回转窑因具备如下特点而更适合我国球团厂建设的国情[7-9]:(1)产能大、
产品质量好;(2)可用煤作基本燃料;(3)对原料性质发生波动的适应性强;(4)链篦机的耐高温材质价格相对较低,国内已能解决。因而近年来链篦机—回转窑球团工艺在我国得到了快速发展。由于回转窑以煤作为燃料,因此生产成本低,价格波动小。但以煤作为燃料必须有几个要素做保证:(1)选择灰分低、灰分熔点高的煤种;
(2)控制煤粉粒度及控制给煤量;(3)采用合适的烧嘴控制火焰状况。
1.4课题的背景及意义
链篦机-回转窑球团工艺具有适应性强、生产能力大、工艺灵活、可以采用廉价的煤作燃料等许多优点,近年来已经成为我国球团矿生产的主要工艺,大大促进了球团矿生产的发展。然而,回转窑结圈所带来的负面效应也已成为抑制回转窑顺行的首要因素,有效防止结圈、结块,确保回转窑生产顺行,成为球团厂实现优质高产所面临的首要问题。由于结圈原因十分复杂,每个企业的情况不尽相同,目前尚缺乏系统的、具有普遍意义的理论来指导生产实践。本课题将从包钢西区120万t球团厂回转窑的实际生产情况出发,从单一铁矿粉球团质量的研究,回转窑热工制度对球团强度的影响,合理配矿比及链篦机工艺制度的优化等方面入手,进而提出包钢链篦机-回转窑球团矿生产工艺优化的几点措施。并为为探明回转窑结圈形成的原因及影响结圈的因素,提出抑制回转窑结圈的有效措施提供一些理论依据。
包钢西区120万t球团矿生产工艺优化技术研究成果,不仅可直接应用于包钢链篦机—回转窑球团生产工艺,提高生产效率、改善球团矿质量和降低生产成本,而且有利于实现高炉炉料结构的合理化、降低高炉炼铁乃至整个钢铁产品成本,为包钢企业创造可观的经济效益,对于全面系统地优化选矿、造块、冶炼工艺,实现包钢炼铁生产的可持续发展具有重要的现实意义。
包钢西区120万t球团生产线是包钢钢联股份有限公司1000万t钢铁产能的原料配套项目,该项目的实施不仅优化了包钢高炉炉料结构,提高了炼铁产能,降低了消耗,而且充分利用了大中公司的铁矿资源及其它矿产资源,实现了包钢股份的资源战略。包钢西区120万t球团生产线采用了国内最先进的链篦机—回转窑—环冷机工艺,可年产粒度为8-16mm酸性氧化球团矿120万t,促进了包钢高炉炼铁指标进步和经济效益的提升。
1.5研究方案
单一铁矿粉球团质量的研究,物料成球性的强弱可用成球性指数K 来表示
分
毛分
W W W K -=
,采用压滤法测量最大分子水、容量法测量最大毛细水,测量各种铁
矿粉的成球性指数;采用coalter-LS230激光粒度分析仪测量各种物料的粒度组成,揭示物料粒度组成对成球性的影响;模拟包钢西区120万t 球团链篦机-回转窑实际生产工艺条件,对单一铁矿粉进行造球、干燥预热、高温焙烧,分别检测其生球质量、预热球强度、成品球强度,并检测其显微结构和矿物组成,分析单一铁矿粉球团质量与其粒度、化学成分和成球性指数的关系。
回转窑热工制度对成品球抗压强度的影响,影响回转窑成品球抗压强度的热工制度主要是焙烧时间和焙烧温度。模拟包钢西区120万t 球团链篦机-回转窑实际生产工艺条件及配料比,测定球团在不同热工制度下焙烧后的强度,揭示焙烧时间和焙烧温度对成品球抗压强度的影响规律。
链篦机球团强度研究改,变配矿比、添加剂用量、混合料水分含量等因素,测量生球落下强度、抗压强度以及爆裂温度,测量链篦机预热球强度;改变链篦机干燥与预热温度,测量链篦机预热球强度;模拟包钢西区链篦机—回转窑的实际工艺条件将不同配比原料造球、干燥、预热、焙烧,检测其预热球强度和成品球强度并进行结果分析。
2单一铁矿粉球团实验
2.1包钢西部球团矿原料结构
包钢西部球团矿的原料主要用四种铁精矿粉,分别为东料场大堆料、粗粒度巴润矿、再磨矿,以及细粒度巴润精矿(矿浆),用料结构多为大堆料:粗粒度巴润
矿:再磨矿=40%:30%:30%。这四种铁精矿的化学成分如表2.1所示。
从表中可以看出,大堆料、再磨矿和细粒度巴润精矿的FeO含量大于20%,为磁铁矿;粗粒度巴润矿的FeO含量为11.40%,为混合型精矿;其中粗粒度巴润矿
和细粒度巴润精矿的SiO2含量较少,分别为为2.33%和1.26%。含铁品位最高的为
大堆料和细粒度巴润精矿,品位分别为65.00%和66.60%。大堆料、再磨矿、细粒
表2.1球团矿原料成分/%
项目TFe FeO CaO MgO SiO2K2O Na2O F S P Al2O3大堆料65.00 27.80 1.23 0.87 3.43 0.082 0.099 0.031 0.46 0.160 0.530 再磨矿64.20 27.20 1.31 0.95 4.11 0.088 0.069 0.041 0.33 0.044 0.770 细粒度巴润精矿66.60 27.60 1.38 0.97 1.26 0.096 0.058 0.140 0.64 0.045 0.094 粗粒度巴润矿62.20 11.40 2.07 1.29 2.33 0.130 0.080 0.380 0.22 0.073 1.23 混料63.92 22.7 1.51 1.02 3.30 0.098 0.084 0.139 0.35 0.099 0.812 注:混料为:大堆料:粗粒度巴润矿:再磨矿=40%:30%:30%时混合料化学成分。
度巴润精矿中有害杂质元素S含量均高于0.30%,属高硫矿,S含量最高的为细粒
度巴润精矿,可达0.64%。四种铁矿粉都含有含量相对较高有害元素P、F。粗粒度
巴润矿的F含量最高达到0.380%,且其K2O和Al2O3的含量也居四种铁精矿粉之
首,含量分别达到0.130%和1.23%。原料成分和成品球团矿化学成分如表2.2所示。
表2.2 原料成分和成品球团矿化学成分/%
项目TFe FeO CaO MgO SiO2K2O Na2O F S P Al2O3原料成分63.92 22.70 1.51 1.02 3.30 0.098 0.084 0.139 0.35 0.099 0.812
成品球团矿62.60 0.300 1.69 1.11 5.12 0.130 0.130 0.011 0.02 0.045 0.730
铁精矿原料和成品球团矿化学成分分析比较:
(1)在铁精矿原料焙烧成品球团矿工艺过程中,FeO、P、S、F的含量都有不同程度的降低,其中FeO降低了22.40%,表明磁铁矿很大程度上已经氧化,有害
元素P、S、F在氧化球团焙烧过程中有较大程度的气化挥发,P、S和F的气化脱
除率分别为54.5%、94.3%和92.1%。
(2)在铁精矿原料焙烧成品球团矿工艺过程中,SiO2、Na2O、K2O、CaO、MgO的含量相对升高,其中SiO2含量升高最多为1.816%,主要是由于SiO2多以
稳定的硅酸盐脉石或硅酸盐液相的形式存在于球团矿中。
(3)在铁精矿原料焙烧成品球团矿工艺过程中,Na2O、K2O、CaO、MgO的含量相对升高,其原因在于它们主要以稳定的硅酸盐脉石形态存在于铁精矿中,在
球团焙烧过程中不易气化脱除。其中Na2O、K2O主要以低熔点硅酸盐及硅铝酸盐
形态存在,在球团焙烧过程中易于熔化形成液相;而CaO、MgO主要以高熔点钙
镁橄榄石和镁黄长石形态存在,在球团焙烧过程中可部分熔化形成液相,另一部分
则仍以脉石形态保留在球团矿中。
表2.3铁矿粉化学成分表/%
项目TFe FeO CaO MgO SiO2K2O Na2O F S P Al2O3大堆料65.00 27.80 1.23 0.87 3.43 0.082 0.099 0.031 0.46 0.16 0.53 再磨矿64.20 27.20 1.31 0.95 4.11 0.088 0.069 0.041 0.33 0.044 0.77 细粒度巴润精矿66.60 27.60 1.38 0.97 1.26 0.096 0.058 0.14 0.64 0.045 0.094 粗粒度巴润矿62.20 11.40 2.07 1.29 2.33 0.130 0.080 0.380 0.22 0.073 1.23
膨润土理化性质:膨润土俗名皂土,主要矿物组成是蒙脱石,晶体结构属于2:1型片状晶体结构,由两个硅氧四面体夹一层铝氧八面体构成。水分8.80%,吸水率
245,胶质价:225,蒙脱石69.51%,粒度(-200目):95.07%。
表2.4膨润土化学成分表/%
项目TFe FeO Fe2O3SiO2K2O Na2O CaO MgO Al2O3
膨润土 1.8 0.5 2.30 65.25 1.74 2.02 1.92 2.80 11.90
2.2单一铁矿粉粒度的测定实验
(1)采用coalter-LS230激光粒度分析仪测量各种物料的粒度组成,揭示物料粒度组成对成球性能的影响。
图2.1大堆料粒度图图2.2粗粒度巴润矿粒度图
图2.3再磨矿粒度图图2.4细粒度巴润精矿粒度图
图2.5皂土粒度图图2.6粘结剂粒度图
可见,细粒度巴润精矿粒度最细、大堆料粒度最粗、再磨矿和粗粒度巴润矿粒度相近。其中皂土粒度:-200目所占比例95.07%,-300目所占比例87.83%。粘结剂粒度:-200目所占比例99.56%,-300目所占比例94.23%。
表2.5单一铁矿粉粒度组成
项目 +60目 60~100 100~150 150~200 200~300 -200目 -300目 大堆料 1.61% 11.5% 16.48% 14.92% 22.27% 66.04% 47.36% 粗粒度巴润矿 0 4.92% 10.07% 12.33% 25.6% 80.5% 59.39% 再磨矿 4.96% 4.96% 10.8% 13.83% 22.6% 78.66% 60.12% 细粒度巴润精矿
1.52%
5.06%
6.98%
19.69%
90.69%
75.21%
2.3单一铁矿粉成球性测定实验
颗粒表面的亲水性及颗粒形状对成球性的影响最大,颗粒表面亲水性愈高,吸附水及薄膜水含量愈高,成球就愈好。物料的成球性的强弱可用成球性指数K 的大小来表示,如式 2.1所示。采用压滤法测量最大分子水、容量法测量最大毛细水,求得其成球性指数。
W K W W =
-分
毛分 (式2.1)
式中:分W —生球的最大分子水含量(%);毛W —生球的毛细水含量(%); 成球性指数可综合反映原料的亲水性、粒度组成、颗粒形貌及比表面积等特性。根据K 值大小将原料成球性难易程度划分为:K<0.2时无成球性;K=0.2-0.3时为弱成球性;K=0.35-0.6时为中等成球性;K=0.6-0.8时为良好成球性;K>0.8时为优等成球性。
实验采用压滤法测定原料中的最大分子水,所用设备如图2.7所示。压滤法是用机械压力将试样中的自由水和毛细水压出,用滤纸吸收出多余水分后,试样中剩余的水分的百分含量就是粉料的最大分子水。取一定量的造球原料,在容器内加水,使矿粉润湿至饱和状态,静置2小时,以保证颗粒表面可以充分润湿。
测定时,先把下压塞放入压模中再将滤纸放在下压塞上,将准备好的试样平铺在压模内的滤纸上,保证试样受压后的厚度小于2mm ;然后在试样上再加盖滤纸,盖好上压塞。准备工作完成之后把压模放在液压机上,增大压力到65.5kg/cm 2,恒压5min 后取出试样称重,质量记为m 1,然后将试样加热到105℃温度下烘干8小时,
关于链篦机
关于链篦机—回转窑工艺结圈实验方案自2000年大型“链篦机—回转窑工艺”(球团年产量>100万吨)在首钢改造成功以后,发展非常迅速,其产、质量高,对原料适应广,生产成本较低等优越性得到充分体现,但回转窑结圈的问题也表现突出。若回转窑结圈问题处理不好,将严重影响球团的产、质量,缩短回转窑窑衬寿命,甚至影响回转窑的整体结构,导致无法继续生产。结圈的防止和消除成为“链篦机—回转窑工艺”整个技术成功的关键,因此解决回转窑结圈成为球团生产的重要课题。而钒钛球团的结圈问题表现得更加突出(由于原料中含有一定量的钒、钛等元素,使钒钛矿具有特殊的焙烧性能),目前在我市众多的球团企业,除了钢企球团厂使用“链篦机—回转窑工艺”外,其余都使用竖炉生产工艺。因此我厂做好“链篦机—回转窑工艺”生产的前期研究准备工作非常重要。 一、“链篦机—回转窑工艺”结圈示意图及原因分析 1.“链篦机—回转窑工艺”结圈示意图 图1是回转窑结圈的典型示意图。根据回转窑各段温度的差异,可以把回转窑分为窑头、窑中、窑尾3个部分。距出料端0 ~ 7米为窑头段,7 ~ 17米为窑中段,17 ~ 3 5米为窑尾段。 如下图所示,窑头和窑尾段结圈物较均匀,厚度一般在50mm左右,对生产影响不大。窑中段结圈厚度一般在270~300mm,严重时可达1米,导致球团不能在回转窑中正常流动,加大回转窑的负荷,使得生产无法继续进行,必须停窑进行处理。
窑尾窑中窑头 图1 回转窑结圈示意图 窑中段是回转窑温度焙烧的高温段,温度一般在1280℃左右,而窑头段温度一般为1050~1250℃,窑尾段温度一般为900~1150℃,窑中段焙烧温度高,导致窑中段结圈严重。 2.回转窑结圈原因分析 经过我国12年来的大型“链篦机—回转窑工艺”生产实践,有研究认为:回转窑结圈主要是温度过高、煤灰带入的低熔点物质、窑内粉末在窑壁上固相扩散粘附和液相粘附不断积累形成的。回转窑中的粉末一部分从链篦机中随球团一起带入,一部分是由于球团在回转窑中受到摩擦剥落而产生的,还有一部分为煤燃烧的残留物。而造成球团粉末多的因素较多,详细结圈关系图如图2示。 因此,根据回转窑结圈的各种因素分析,在即将生产的“链篦机—回转窑工艺”中提前做好各项预防措施,以降低回转窑结圈对生产的影响。
链篦机-回转窑
链篦机--回转窑球团技术 1 简介 链篦机—回转窑球团技术是采用链篦机干燥、预热生球,回转窑固结、焙烧球团,环冷机上冷却成品球团的一种球团工艺。该技术生产的球团矿是一种优质的高炉原料,含铁品位高,冶金性能好,适合较长时间贮存和远距离运输等商品化优势。与烧结矿搭配使用,可有效的降低高炉焦比和提高高炉产量,能使高炉炉料结构合理化;工艺先进,二次能源利用充分,环境清洁;球团矿质量高、能耗低,经济效益和环境效益好。而竖炉球团的技术,球团质量不均匀、对原料适应性差,难于大规模生产。 根据我国钢铁和矿山企业的现状和特点,自 2002 年以来,我们研制开发建成了几十条中小型链篦机-回转窑球团生产线(详见业绩表)。这些工程以工艺先进、实用、投资省,建设快,投产达产快,效益好而得以迅猛发展。 2 先进的技术装备和控制水平 以提高产品质量、降低成本为目的,充分吸取国内同类型球团厂建设的经验和国外先进技术,使主要技术经济指标达到国内先进水平。主体生产线设备全部采用 PLC 系统实现集中联锁控制,关键生产岗位设有监控工业电视,达到国内先进的自动化程度。 3 工艺简述 磁铁矿粉和赤铁矿粉和膨润土在配料室按一定比例进行配比。配比完后的混合料在干燥机烘干 ( 水份由 10% 经过烘干后降至 8.0% 左右 ) 和混匀 , 在润磨机上对混合料进行润磨 , 通过拉式皮带机把润磨好的混合料送至造球盘造球 , 通过布料筛分系统均匀把生球布在链篦机上 , 生球在链篦机上进行干燥、预热,在回转窑中固化、焙烧,在环冷机上冷却(温度≤ 150℃ ),最后通过皮带机或链板机运至成品场储存。成品球团矿粒度 8~16mm,其中 10~16mm 的占90% 。返料、除尘灰均返回使用,能够充分回收和利用资源并确保生球的质量。
年产150万吨链篦机回转窑球团总包工程施工组织设计
年产150万吨链篦机回转窑球团项目 施 工 组 织 设 计 总承包单位: 建设单位: 日期:
目录 第一部分编制说明 第二部分工程概况及工程特点 第三部分施工部署 第四部分工程图纸设计 第五部分施工准备 第六部分主要资源配置计划 第七部分施工组织管理 第八部分主要施工方法及技术保证措施 一、土建工程施工方案 二、钢结构工程施工方案 三、设备安装工程施工方案 四、耐火材料砌筑工程施工方案 五、管道工程施工方案 第九部分确保工期的技术组织措施 第十部分确保工程质量的技术组织措施 第十一部分确保安全生产的技术组织措施 第十二部分确保文明施工及环境保护的组织措施第十三部分特殊环境施工措施 第十四部分降低环境污染及噪音的措施 第十五部分交工验收及移交 第一部分编制说明
一、编制原则 1、加强施工过程中的质量控制,确保工程质量等级达到优良。 2、科学、合理的安排施工顺序及施工进度,保证工程顺利完工。 3、合理规划临时用地,搞好文明施工,树立企业良好形象。 4、结合我公司成熟的同类工程施工经验,重点阐述主要分项工程施工工艺及方法。 二、编制依据 1、设计院提供的各专业设计图纸; 2、设计说明中明确采用的国家和冶金行业颁发的施工及验收规范、工程质量检验评定标准; 3、我公司类似工程的施工经验及现有的技术、装备能力; 第二部分工程概况及工程特点 一、工程概况 1、业主单位: 2、工程地点: 3、工程内容: 3.1球团工程承包范围及工作内容: 该生产线采用链篦机-回转窑-环冷机生产工艺,年产酸性氧化球团150万吨球团生产线总承包工程,建设内容包括配料室、烘干室、润磨室、造球室、布料系统、链篦机-回转窑-环冷机系统、成品储运系统及配套的公辅设施。 工作内容包括:设计、设备及材料采购土建工程及安装工程施
竖炉、链篦机回转窑生产工艺对比
竖炉、链篦机回转窑生产工艺对比 球团与烧结是钢铁冶炼行业中作为提炼铁矿石的两种常用工艺。球团矿就是把细磨铁精矿粉或其他含铁粉料添加少量添加剂混合后,在加水润湿的条件下,通过造球机滚动成球,再经过干燥焙烧,固结成为具有一定强度和冶金性能的球型含铁原料。球团生产主要分为竖炉焙烧工艺、带式焙烧工艺、链篦机回转窑焙烧工艺,以下主要针对竖炉、链篦机回转窑焙烧生产工艺进行对比分析。 一、我公司目前竖炉生产运行情况: 1、装备水平 设计有12㎡(已扩容至14㎡)、18㎡竖炉各一座,设计产能136.11万吨/年。 2、生产流程 生产流程包括原料准备、配料、混合、造球、干燥和焙烧、冷却、成品和返矿处理等工序,如下图所示。 3、竖炉球团生产的特点
竖炉法生产球团具有结构简单、制造材质无特殊要求、基建投资少、热效率高、操作维修方便等优点,由于其工艺方法在理论上存在着固有的、难以克服的缺陷,而使这一方法存在较多的缺点,具体如下: ⑴单炉规模很难大型化 目前我国生产的竖炉一般都在10-20m2,产量在40-70万t左右。如要扩大规模,其难度十分大。如要扩大其横向尺寸,上述所提到的炉内温度的分布势必更难做到合理和有效;如要增大长度方向上的尺寸,则会由于长度和温度(排料温度一般在400℃左右)方面的原因,将对排料辊的设计和制造带来更大的难度。 ⑵只能使用气体燃料 从目前工业生产实践的情况看,竖炉使用气体燃料时,焙烧效果要好些。虽也有烧油的实践,但成品球团矿的质量要更差些,而且产量也低,其效果不佳。 ⑶对原料的适应性差 从理论上和实践都可看出,竖炉焙烧只有在用磁铁矿作原料时才能成功。若采用赤铁矿或其他矿种作原料,往往在其升温过程中,球团的强度很难提高,几乎要到1200℃以上,球团的固结强度才能较迅速地上升,在此温度以前,球团在炉内由于强度低和往下运动时的摩擦和料柱的压力,会产生过量的粉末,在较高温度下极易产生粘结现象。 二、链篦机回转窑生产工艺 1、生产工艺简介 生产球团用的铁精粉和膨润土进厂储存于精粉料场和膨润土仓库,使用时,精粉由轮式装载机装入精粉矿仓,膨润土由人工加入膨润土矿仓,按合理配比配料,配合料经圆筒烘干机烘干混均后,由胶带机输送至润磨机进行混均和再磨,混均后的混合料再由胶带机输送至造球室缓冲料仓,皮带机给入圆盘造球机造球,生球经圆辊筛筛分,不合格的生球筛除,返回造球室混合料仓重新造球。合格生球均匀布至链篦机篦床上,经干燥、预热后,预热球经过铲料板、溜槽进入回转窑,氧化焙烧后的球团矿卸入环
链箅机_回转窑球团生产工艺
世界金属导报/2010年/8月/31日/第010版 原料炼铁 链箅机-回转窑球团生产工艺 廖建国 自1966年神户制钢公司在神户炼铁厂内建设了链算机-回转窑球团生产设备以来,已有许多采用相同生产工艺的球团生产设备建成投产本文就球团生产设备的开发过程和各种球团生产工艺的特征进行介绍,同时对链算机-回转窑球团生产工艺的优势和神户制钢公司的各工程项目的最新状况进行了分析 1前言 目前,世界主要的炼铁方法是采用高炉进行大规模生产的高炉炼铁法和采用电炉进行中小规模生产的电炉炼铁法。高炉炼铁使用的原料为块矿石、烧结矿和球团矿,电炉炼铁法使用的原料为废钢、还原球团矿和用还原球团矿生产的团矿等。烧结矿是钢铁原料,其粒度为1 5mm~30mm。烧结矿以1mm~3mm左右的铁矿石粉为原料,采用粉焦作燃料,利用粉焦的燃烧热使矿石粉部分熔融固结而成。而球团矿是采用比生产烧结矿更细的铁矿石粉通过造球机制成12mmm左右的球状物,经焙烧而成,它不仅可以用作高炉炼铁原料,而且在盛产天然气的国家还被广泛用作气基直接还原炼铁法的原料。 目前,世界上的高品位块状铁矿石资源越来越少,人们正在考虑采用选矿工艺提高低品位矿的品位后制成球团矿进行利用的方法,尤其是认为通过在高炉和直接还原炉增加球团矿的使用量,可以使球团生产设备在未来发挥重要的作用。 2球团矿生产设备 球团矿生产设备一般由以下4个工序构成: ·原料装入工序; ·原料预处理工序; ·造球工序; 焙烧工序。 2.1原料装入工序 由于球团生产设备的建设场地不同,因此作为原料的铁矿石、添加物、粘合剂等的加入方法不同。以往,球团厂大部分是建在靠近矿山的地方,生产工序为选矿、精矿处理,原料是通过火车或矿浆管线进行输送。另一方面,对远离矿山单独建设的球团厂来说,需要大量运送铁矿石,包括运送矿石的专用船、卸货码头、矿石的堆放场地,因此经济上不合算。 2.2原料预处理工序 铁矿石是造球用的原料,把铁矿石处理成细粉原料,可以满足造球要求的性能,其处理工序包括了选矿、脱水、粉碎、干燥和调湿等工序。 原料预处理工序一般是把低品位矿粉碎后,提高铁品位,然后去除硫、磷等杂质,再调整粒度。为提高磁铁矿品位和去除杂质,进行了磁力选矿,对赤铁矿进行了重力选矿和浮游选矿或湿式高磁力选矿。 粉碎方式大致有如下几种: (1)湿式粉碎——干式粉碎 (2)开路粉碎——闭路粉碎 (3)一段粉碎——多段粉碎 由于矿石的种类、性能和配比等不同,因此采用的粉碎方式不同,既要考虑经济性,又要进
球团矿实用工艺流程简介
概述 20世纪70年代,各种球团技术已得到大力推广和发展,其中以链篦机-回转窑球团生产线的发展最为显著。它具有对原料条件适应性强、产品质量好、能耗低、无污染,并适合大规模生产。 竖炉生产球团,产品质量不均匀、原料适应性差,大型化困难等因素,制约了球团的发展。 原料 磁铁矿或赤铁矿铁精粉,膨润土。 工艺流程简述 1.配料:磁铁矿粉/赤铁矿粉、膨润土在配料室按一定比例进行配料; 2.烘干混匀:配好的料送至烘干机进行烘干和混匀(水份由12%降至8.0%左右) ; 3.润磨:烘干后的料在润磨机上进行润磨; 4.造球:把润磨好的料或者烘干后的料送至造球机造球; 5.筛分布料:生球通过布料筛分均匀地布在链篦机链板上; 6、链篦机:生球在链篦机上进行脱水、干燥、预热,使球团能承受一定的高温并产生一定的强度后,再进回转窑中; 7、回转窑:球团在回转窑中得到焙烧,生成质量合格的球团矿,送往环冷机进行冷却; 8、环冷机:高温烟气通过热风管送至链篦机循环利用,达到节能降耗的目的。最终冷却后的烟气温度≤100℃; 9、成品:通过皮带机或链板机运至成品料场储存。 燃料
发生炉煤气、天然气、钢铁企业煤气、煤粉等均可。 球团矿的特点: 一种优质的高炉原料,俗称高炉的“顺气丸” 含铁品位高,有害元素少 粒度均匀,冷态强度高,无热爆现象 可较长时间贮存和远距离运输 与烧结矿搭配使用,可有效降低高炉焦比,提高高炉产量,使高炉炉料结构合理化,最终使高炉达到优质、高产、低耗、高效之目的 工业安全卫生及消防 建筑物设置防雷、防火安全设施 高温管道、风机采取必需的隔热措施 对生产过程中的粉尘、噪音进行治理,确保工人的身心健康。 节能 链篦机-回转窑-环冷机系统中热气体循环使用,对生球进行干燥、预热和焙烧,有效利用热能,降低能耗。 工业用水循环使用,实现零排放,节约水资源。工业用水循环利用,实现零排放 烟气通过两级除尘,达到国标排放标准 烟气通过热循环再利用,实现节能降耗
万吨链篦机回转窑球团工程施工组织设计方案
宣钢四万制氧机工程仪电控系统 施工工程 施工组织设计方案
目录 一、工程概况 二、工程量 三、编制依据 四、电气装置安装 五、仪控系统安装 六、施工准备 七、施工安全、环境保证措施 八、设备材料管理 九、设备和材料防护措施 十、冬季施工方案 十一、施工技术的质量控制措施十二、组织机构 十三、施工机具 十四、劳动力计划表
一、工程概况: 1、工程名称:宣钢四万制氧机工程仪电控系统施工 地点:宣钢东厂区 建设性质:技术改造 工期安排:2010年11月1日开工; 2011年1月30日竣工。 2、工程承包范围: 宣钢宣钢四万制氧机工程仪电控安装项目包括制氧设备的仪、电(高、低压)控系统安装。具体安装内容包括空气过滤器及压缩系统、空气预冷系统、空气纯化系统、空气分离系统(含制氩系统)、透平膨胀机系统、氧气压缩系统、氮压机二期、冷却水、液储、液体蒸发等系统的仪表、高、低压电气设备、电缆、柜子等安装;施工还包括分馏塔区域照明电气施工。 二、工程量 电气系统施工: 空压机系统:主电机20200KW,电压10KV,变频启动;低压辅助项目安装调试;氧透系统(两套):主电机一台6000KW,电压10KV,电抗器降压启动;一台4000 KW,电压10KV,电抗器降压启动;低压辅助项目安装调试; 氮透系统(两套):主电机一台3800KW,电压10KV,电抗器降压启动;一台2800 KW,电压10KV,直接启动;低压辅助项目安装调试; 预冷系统、纯化系统、分馏塔系统、液储系统:低压电气设备的安装、调试; 具体施工内容: 1.1.1高压电气系统施工:图纸76.18ⅡD9中的全部内容,原理图见D542。(1)高压配电室8面高压开关柜安装调试; (2)1台容量为10700KVA、电压等级为10KV/3KV的干式降压变压器安装调试;(3)1台容量为9700KVA、电压等级为10KV/3KV的干式升压变压器安装调试;(4)1套3600mm×1200 mm×2200 mm(宽×深×高)高压变频启动柜(3KV)、1面去磁柜、1面变频控制柜、1面励磁控制柜的安装调试; (5)3台10KV 2000/5A电流互感器安装(柜内)及相应铜母线(此母线施工方自采)的制作安装,两套氧透设备的12台10KV,500/5A电流互感器的安装(电机接线盒内)及相应铜母线(此母线施工方自采)的制作安装; (6)3台用于降压启动用的10KV干式铁芯电抗器安装; (7)3面空压机、氧透机旁操作柜安装; (8)3台S10-2500/10全密封变压器安装,变压器室内的3台负荷开关(FN3-10R)施工单位自采并安装; (9)2面直流屏安装调试; (10)5面UPS电源柜安装调试; (11)高压电气设备用高压电缆、控制电缆敷设接线; (12)电气设备交接试验、高压开关柜调试、高压电机系统调试、系统联动调试、试车;电气设备试验要求出具具有资质单位的试验报告。
60万吨链篦机回转窑球团工程施工设计方案完整版
(此文档为word格式,下载后您可任意编辑修改!) 宣钢四万制氧机工程仪电控系统 施工工程 施工组织设计方案
目录 一、工程概况 二、工程量 三、编制依据 四、电气装置安装 五、仪控系统安装 六、施工准备 七、施工安全、环境保证措施 八、设备材料管理 九、设备和材料防护措施 十、冬季施工方案 十一、施工技术的质量控制措施十二、组织机构 十三、施工机具 十四、劳动力计划表
一、工程概况: 1、工程名称:宣钢四万制氧机工程仪电控系统施工 地点:宣钢东厂区 建设性质:技术改造 工期安排:2010年11月1日开工; 2011年1月30日竣工。 2、工程承包范围: 宣钢宣钢四万制氧机工程仪电控安装项目包括制氧设备的仪、电(高、低压)控系统安装。具体安装内容包括空气过滤器及压缩系统、空气预冷系统、 空气纯化系统、空气分离系统(含制氩系统)、透平膨胀机系统、氧气压缩系统、氮压机二期、冷却水、液储、液体蒸发等系统的仪表、高、低压电气设备、电缆、柜子等安装;施工还包括分馏塔区域照明电气施工。 二、工程量 电气系统施工: 空压机系统:主电机20200KW,电压10KV,变频启动;低压辅助项目安装调试;氧透系统(两套):主电机一台6000KW,电压10KV,电抗器降压启动;一台4000 KW,电压10KV,电抗器降压启动;低压辅助项目安装调试; 氮透系统(两套):主电机一台3800KW,电压10KV,电抗器降压启动;一台2800 KW,电压10KV,直接启动;低压辅助项目安装调试; 预冷系统、纯化系统、分馏塔系统、液储系统:低压电气设备的安装、调试; 具体施工内容: 1.1.1高压电气系统施工:图纸76.18ⅡD9中的全部内容,原理图见D542。(1)高压配电室8面高压开关柜安装调试; (2)1台容量为10700KVA、电压等级为10KV3KV的干式降压变压器安装调试;(3)1台容量为9700KVA、电压等级为10KV3KV的干式升压变压器安装调试;(4)1套3600mm×1200 mm×2200 mm(宽×深×高)高压变频启动柜(3KV)、1面去磁柜、1面变频控制柜、1面励磁控制柜的安装调试; (5)3台10KV 20005A电流互感器安装(柜内)及相应铜母线(此母线施工方自采)的制作安装,两套氧透设备的12台10KV,5005A电流互感器的安装(电机接线盒内)及相应铜母线(此母线施工方自采)的制作安装;
链篦机回转窑球团总包工程施工组织设计概述(doc 168页)
链篦机回转窑球团总包工程施工组织设计概述(doc 168页)
年产150万吨链篦机回转窑球团项目 施 工 组 织 设 计 总承包单位: 建设单位: 日期:
目录 第一部分编制说明 第二部分工程概况及工程特点 第三部分施工部署 第四部分工程图纸设计 第五部分施工准备 第六部分主要资源配置计划 第七部分施工组织管理 第八部分主要施工方法及技术保证措施 一、土建工程施工方案 二、钢结构工程施工方案 三、设备安装工程施工方案 四、耐火材料砌筑工程施工方案 五、管道工程施工方案 第九部分确保工期的技术组织措施 第十部分确保工程质量的技术组织措施 第十一部分确保安全生产的技术组织措施 第十二部分确保文明施工及环境保护的组织措施第十三部分特殊环境施工措施 第十四部分降低环境污染及噪音的措施 第十五部分交工验收及移交
第一部分编制说明 一、编制原则 1、加强施工过程中的质量控制,确保工程质量等级达到优良。 2、科学、合理的安排施工顺序及施工进度,保证工程顺利完工。 3、合理规划临时用地,搞好文明施工,树立企业良好形象。 4、结合我公司成熟的同类工程施工经验,重点阐述主要分项工程施工工艺及方法。 二、编制依据 1、设计院提供的各专业设计图纸; 2、设计说明中明确采用的国家和冶金行业颁发的施工及验收规范、工程质量检验评定标准; 3、我公司类似工程的施工经验及现有的技术、装备能力; 第二部分工程概况及工程特点 一、工程概况 1、业主单位: 2、工程地点: 3、工程内容: 3.1球团工程承包范围及工作内容: 该生产线采用链篦机-回转窑-环冷机生产工艺,年产酸性氧化球团150万吨球团生产线总承包工程,建设内容包括配料室、烘干室、润磨室、造球室、布料系统、链篦机-回转窑-环冷机系统、成品储运系统及配套的公辅设施。
链篦机回转窑技术
目前,中国链篦机-回转窑球团厂使用的含铁原料基本上有以下几种: (1)钢铁公司所属矿山生产的铁精矿 如鞍钢所属矿山(弓长岭、大孤山)、本钢所属矿山(南芬、歪头山)、首钢所属矿山(水厂、大石河)、太钢所属矿山(峨口)、武钢所属矿山(程潮)等,上述矿山所产铁精矿质量较好,磁铁矿品位一般在67%~68%,且粒度细,是生产球团矿的良好原料。其中一些矿山采取了提铁降硅新工艺,使精矿品位大幅度提高,SiO2降至5%以下,而精矿粒度变得更细,更适合球团矿生产。 (2)地方中小企业及小矿山生产的铁精矿 这部分铁精矿大多为磁铁精矿,含硫、磷及有害杂质低,含铁品位通常在62%~64%左右,粒度偏粗,一般-200目占60%~70%,用作生产球团矿的原料时,需细磨处理。目前,国内球团厂常用的办法是采用润磨机或高压辊磨机处理,以提高铁精矿细度,增加其表面活性。 (3)进口赤铁精矿 从理论上讲,使用赤铁精矿、磁铁精矿或赤磁混合铁精矿作原料,采用链篦机-回转窑工艺均可生产出高质量的球团矿。国外球团厂使用赤铁精矿、磁铁精矿或赤磁混合铁精矿的都有。但相比之下,使用磁铁精矿作原料时所需热耗较低,单
位产量高;而使用赤铁精矿,相应的热耗高,单位产量低。这是由于两种铁矿物组成不同所导致的差异。磁铁矿的化学成分是Fe3O4,赤铁矿是Fe2O3。磁铁矿在预热过程中氧化为赤铁矿,同时大量放热,产生再结晶从而提高强度。而赤铁矿却不发生放热反应,需要在较高预热温度下,经过较长预热时间才能促进其再结晶过程进行。由于赤铁矿的这种特性,预热时间要长,特别是预热温度要高,焙烧温度也较高。因此,相同规格的设备,使用不同原料时,其产量、热耗、设备寿命均不同。相对而言,使用赤铁矿时工艺难度增加,对设备质量要求更高。因此,使用赤铁精矿的球团厂都寻求配加部分磁铁精矿的生产模式。 从以上情况看,关于球团原料问题,应做以下几方面的工作:第一,细磨精矿粉。使精矿粒度从目前的-200目占60%~70%提高到85%以上,铁品位提高到68%以上,同时降低SiO2含量到5%以下,以满足球团生产要求。 第二,加强赤铁精矿用于球团生产的研究。根据国情,寻求以赤铁精矿为主,配加磁铁精矿生产优质球团矿的技术条件。 第三,调整目前的原料深加工和炉料结构。降低国内磁铁精矿用于烧结的比例,增加进口赤铁矿粉用于烧结。充分利用国内资源优势,将大量优质铁精矿,尤其是磁铁精矿用于球团矿生产。
链篦机—回转窑操作规程
链篦机—回转窑氧化球团厂操作规程汇编 目录 第一部分岗位工作标准及规程 (4) 第一章主控岗位操作规程 (5) 1.1职责范围 (5) 1.2工作标准 (5) 第二章调度员岗位操作规程 (8) 2.1岗位职责 (8) 2.2调度规程 (8) 2.3作业标准 (9) 第三章配料岗位操作规程 (9) 3.1岗位职责 (9) 3.2操作规程 (9) 第四章皮带岗位操作规程 (10) 4.1岗位职责 (10) 4.2操作规程 (11) 第五章烘干机岗位操作规程 (12) 5.1岗位职责 (12) 5.2操作规程 (12) 第六章润磨机操作规程 (14)
6.1职责范围 (14) 6.2启动和停车顺序 (14) 6.3长期停磨 (15) 6.4正常运转时操作人员必须遵守和注意以下事项 (16) 6.5磨机调整 (17) 七章造球岗位操作规程 (17) 7.1操作标准 (17) 7.2技术操作额定及质量、消耗、效率指标 (18) 7.3开停机的技术操作规定及方法 (18) 7.4技术操作方法 (19) 7.5防止事故的规定及注意事项 (19) 第八章辊筛布料岗位工作标准 (20) 8.1岗位职责 (20) 8.2工作标准 (20) 第九章链篦机岗位操作规程 (22) 9.1技术操作标准 (22) 9.2技术操作定额及质量消耗、效率指标 (22) 9.3开停机的技术操作规定及方法 (23) 9.4技术操作方法 (25) 9.5防止事故的规定及注意事项 (26) 第十章回转窑岗位操作规程 (26)
10.1回转窑点火前的检查与准备工作 (26) 10.2转窑点火操作 (27) 10.3回转窑升温操作 (27) 10.4回转窑正常操作 (28) 10.5回转窑停窑降温操作 (28) 10.6回转窑保温操作 (29) 10.7回转窑停火操作 (29) 10.8回转窑事故的原因与处理 (30) 第十一章环冷机技术操作规程 (32) 11.1技术操作标准 (32) 11.2开停机的操作规定及方法 (32) 11.3操作要求 (33) 11.4事故的规定及注意事项 (33) 第十二章风机岗位操作规程 (34) 12.1职责范围 (34) 12.2技术操作标准 (35) 第十三章钳工操作规程 (37) 第十四章电工操作规程 (38) 14.1电气岗位操作规程 (38) 第十五章电气焊工岗位操作规程 (40) 第十六章煤气使用操作规程 (40)