机械制造工艺学第一章
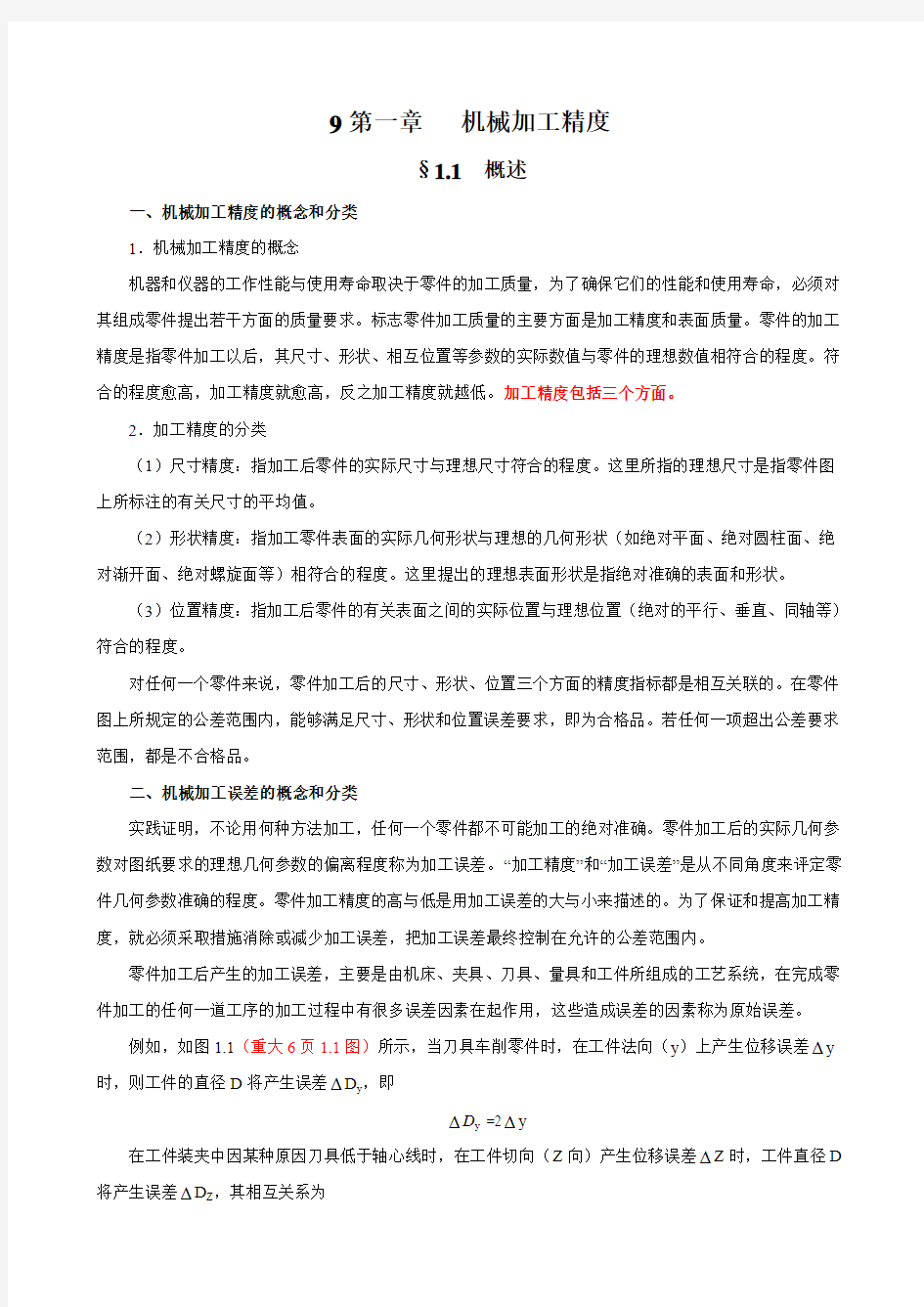
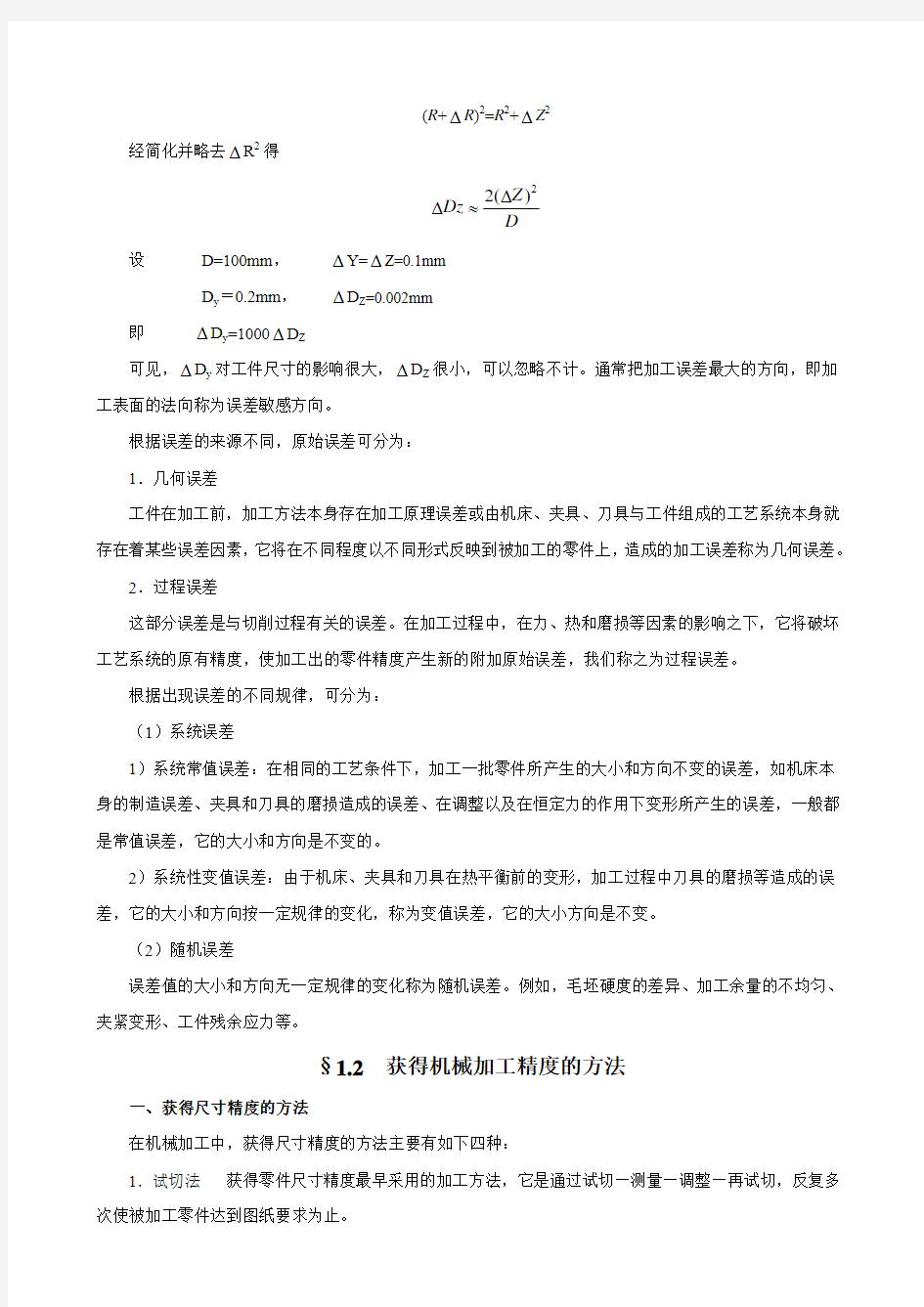
9第一章机械加工精度
§1.1概述
一、机械加工精度的概念和分类
1.机械加工精度的概念
机器和仪器的工作性能与使用寿命取决于零件的加工质量,为了确保它们的性能和使用寿命,必须对其组成零件提出若干方面的质量要求。标志零件加工质量的主要方面是加工精度和表面质量。零件的加工精度是指零件加工以后,其尺寸、形状、相互位置等参数的实际数值与零件的理想数值相符合的程度。符合的程度愈高,加工精度就愈高,反之加工精度就越低。加工精度包括三个方面。
2.加工精度的分类
(1)尺寸精度:指加工后零件的实际尺寸与理想尺寸符合的程度。这里所指的理想尺寸是指零件图上所标注的有关尺寸的平均值。
(2)形状精度:指加工零件表面的实际几何形状与理想的几何形状(如绝对平面、绝对圆柱面、绝对渐开面、绝对螺旋面等)相符合的程度。这里提出的理想表面形状是指绝对准确的表面和形状。
(3)位置精度:指加工后零件的有关表面之间的实际位置与理想位置(绝对的平行、垂直、同轴等)符合的程度。
对任何一个零件来说,零件加工后的尺寸、形状、位置三个方面的精度指标都是相互关联的。在零件图上所规定的公差范围内,能够满足尺寸、形状和位置误差要求,即为合格品。若任何一项超出公差要求范围,都是不合格品。
二、机械加工误差的概念和分类
实践证明,不论用何种方法加工,任何一个零件都不可能加工的绝对准确。零件加工后的实际几何参数对图纸要求的理想几何参数的偏离程度称为加工误差。“加工精度”和“加工误差”是从不同角度来评定零件几何参数准确的程度。零件加工精度的高与低是用加工误差的大与小来描述的。为了保证和提高加工精度,就必须采取措施消除或减少加工误差,把加工误差最终控制在允许的公差范围内。
零件加工后产生的加工误差,主要是由机床、夹具、刀具、量具和工件所组成的工艺系统,在完成零件加工的任何一道工序的加工过程中有很多误差因素在起作用,这些造成误差的因素称为原始误差。
例如,如图1.1(重大6页1.1图)所示,当刀具车削零件时,在工件法向(y)上产生位移误差?y 时,则工件的直径D将产生误差?D y,即
?D y =2?y
在工件装夹中因某种原因刀具低于轴心线时,在工件切向(Z向)产生位移误差?Z时,工件直径D 将产生误差?D Z,其相互关系为
(R +?R )2=R 2+?Z 2
经简化并略去?R 2得
2
2()Z Dz D
??≈ 设 D=100mm , ?Y=?Z=0.1mm
D y =0.2mm , ?D Z =0.002mm
即 ?D y =1000?D Z
可见,?D y 对工件尺寸的影响很大,?D Z 很小,可以忽略不计。通常把加工误差最大的方向,即加
工表面的法向称为误差敏感方向。
根据误差的来源不同,原始误差可分为:
1.几何误差
工件在加工前,加工方法本身存在加工原理误差或由机床、夹具、刀具与工件组成的工艺系统本身就
存在着某些误差因素,它将在不同程度以不同形式反映到被加工的零件上,造成的加工误差称为几何误差。
2.过程误差
这部分误差是与切削过程有关的误差。在加工过程中,在力、热和磨损等因素的影响之下,它将破坏
工艺系统的原有精度,使加工出的零件精度产生新的附加原始误差,我们称之为过程误差。
根据出现误差的不同规律,可分为:
(1)系统误差
1)系统常值误差:在相同的工艺条件下,加工一批零件所产生的大小和方向不变的误差,如机床本
身的制造误差、夹具和刀具的磨损造成的误差、在调整以及在恒定力的作用下变形所产生的误差,一般都
是常值误差,它的大小和方向是不变的。
2)系统性变值误差:由于机床、夹具和刀具在热平衡前的变形,加工过程中刀具的磨损等造成的误
差,它的大小和方向按一定规律的变化,称为变值误差,它的大小方向是不变。
(2)随机误差
误差值的大小和方向无一定规律的变化称为随机误差。例如,毛坯硬度的差异、加工余量的不均匀、
夹紧变形、工件残余应力等。
§1.2 获得机械加工精度的方法
一、获得尺寸精度的方法
在机械加工中,获得尺寸精度的方法主要有如下四种:
1.试切法 获得零件尺寸精度最早采用的加工方法,它是通过试切—测量—调整—再试切,反复多
次使被加工零件达到图纸要求为止。
试切法能达到很高的精度,但调整、试切、测量等时间较长,只适用于小批生产。
2.调整法在成批生产条件下采用的一种加工方法。方法是预先用样板、样件或根据试切工件来调整好刀具和工件在机床上的相对位置,然后加工一批工件,这批工件在加工中不再调整,也不试切,即可达到工件的尺寸要求。
3.定尺寸刀具法在加工过程中,采用刀具(或组合刀具)的相应尺寸来保证工件被加工部位尺寸的方法。
定尺寸刀具法的加工精度,取决于刀具的制造精度和磨损程度,与操作人员的技术水平的高低无关,生产率较高。例如定尺寸拉削、钻、扩、铰或用镗刀块加工内孔等。
4.自动获得尺寸法在加工过程中,通过尺寸测量装置、进给装置和控制机构,组成自动控制系统,实现在加工过程中对尺寸测量、刀具的补偿调整和切削加工等一系列工作自动完成,从而获得所需尺寸要求精度的一种加工方法。例如在无心磨床上磨削轴承外圈时,就是利用测量装置控制导轮架进行微量的补偿进给,来保证工件的尺寸精度。另外,在数控机床上,通过数控装置、测量装置及伺服电机驱动机构,控制刀具在加工时应具有的准确位置,来保证零件的尺寸精度。
二.形状精度的获得方法
1.轨迹法这种方法是依靠刀尖运动轨迹来获得所要求零件的表面几何形状。形状精度取决于刀具和工件的相对运动精度。如图1-2(重大7页图1.4)车圆锥面。
2.成形法利用成形刀具对工件进行加工的方法。如利用成形铣刀加工齿轮,图1-3(重大8页图1.5)是用成形体车刀加工球面。用成形法方法获得的形状精度主要取决于刀具刀刃的形状精度和刀具与工件相对运动的轨迹。这种方法不仅生产率较高,同时还可以简化机床结构。
3.展成法利用工件和刀具的相互作啮合运动,也就是展成运动,来包络出整个工件的形状。例如滚齿、插齿等,这种方法加工出来的工件形状精度较高,生产率也较高。如图1-4(图2-5)重大(|一6,)图所示展成法加工。
三.位置精度的获得方法
1.一次安装方法有位置精度要求的零件,应在一次安装中加工出来,以保证其位置精度。精度的高低取决于机床本身运动精度,如盘形齿轮坯的内孔与端面的垂直度、轴类零件的外圆表面与端面的垂直度、箱体孔系加工中各孔之间同轴度、平行度和垂直度等。
2.多次安装法零件在加工中要经过多次安装才能完成加工,其有关表面的位置精度是由加工表面与工件定位基准面之间的位置精度来保证的。(请参考夹具设计一章中的有关论述)
多次安装涉及到工件找正的问题,根据工件安装方式不同可分为:
(1)直接安装找正法例如在车床上加工外形不规则的内孔,就应该用四爪卡盘安装工件,用百分表找正工件位置。如图1-5(重大8页图1.7)这种方法精度较高,但对工人的操作水平要求也较高,只适
用于单件小批生产。
(2)划线找正法这种方法是在毛坯上事先划出中心线、对称线及待加工表面的加工线,然后按照加工线在机床上找正工件在机床上的相对位置,再夹紧加工。这种方法精度不高,主要适用于形状不复杂、单件小批量生产。
(3)夹具安装法在夹具中定位并夹紧,从而保证加工表面与定位基准面之间的位置精度。这种方法迅速准确、精度高、适用于成批大量生产。
四.加工经济精度与加工方法的选择
1.加工经济精度
不同的加工方法所获得加工精度是不相同的,即使是同一种加工方法,由于加工条件不同,所能达到得加工精度也有所不同。如果是手工操作,在很大程度上取决于工人的技术水平。例如精车一般可达到
IT7-IT8级,若由技师加工可达IT6-IT7级,但是,加工的成本也提高了(如技师的工资等)。
生产中工件的加工精度是用可以控制的加工误差的大小来表示的。加工误差小,加工精度高;加工误差大,则加工精度低。统计资料表明,任何一种加工方法,加工误差与加工成本之间的关系如图1-6(重大9页图1.9)所示。这条曲线可分为三部分:
AB段:加工误差小、精度高,但成本太高,不经济。
CD段:曲线几乎与横坐标平行,说明零件的精度低,成本低,但是任何一种加工方法不能无限制的降低成本,它必须有一个最低成本,才能保证加工质量,过分强调降低成本只能造成不经济,成本降低了,质量没有了,结果是成本反而提高了。
从图中可以看出,对同一种加工方法来讲,加工误差小到一定程度后(如图中B点的左侧),加工成本再提高很多,但加工误差却降低很少;加工误差大到一定程度后(如图中C的右侧),即使加工误差再大,加工成本也降低不了多少。这就说明一种加工方法,在A点的左侧或B点的右侧的应用都是不经济的。
加工经济精度是指在正常条件下(采用符合质量标准的设备、工艺装备和标准技术等级的工人,不延长加工时间)所能保证的加工精度和表面粗糙度。
2、加工方法的选择:加工经济精度是通过几种不同加工方法相互比较的结果。图1-7(重大9页图1.10)所表示的车、磨外圆两种方法的比较。显然,当零件的公差小于?A时,采用磨削比较经济;当零件的公差大于?A时,采用车削比较经济。?A是磨削加工经济精度的下限,也是车削加工经济精度的上限。当然还要看其工件的材料,有色金属如果用磨削加工来提高精度和表面质量就不行,就目前而言,车削加工是提高有色金属零件加工精度和表面质量的唯一方法。
应当指出,加工经济精度是变化的,它随着工艺技术的发展,设备、工装的改进而改变。各种加工方法的加工经济精度和粗糙度的参考数据见表1.1。重大9页表1.1。
二.影响加工精度的因素
零件的加工过程可能出现各中不同类型的原始误差,它们会引起系统各环节相互位置关系的变化而造
成误差。图1-8(清华164页3-1)为活塞销孔精镗工序的示意图,活塞如果装夹、调整不当,就会引起
活塞镗削误差。
(1)装夹误差 在卧式镗床上镗活塞的销孔。采用的装夹方法是,以活塞止口和端面为定位基准,
在夹具中定位,并用菱形销插入经半精镗过的销孔中作调整定位。夹紧力作用在活塞的顶部,这就产生了
设计基准(3)与定位基准(6)不重合,以及定位止口与夹具上的定位凸台,菱形销孔与配合间隙不恰当
而产生定位误差,同时还存在因夹紧力F 过大导致设计基准变形,引起夹紧误差。这两种误差统称为工件
夹紧误差。
(2)调整误差 工件装夹前后,必须对机床、刀具和夹具进行调整,并进行试切,再进行微量精确
调整,才能使工件和刀具之间保持相对的正确位置,同样以活塞加工为例,装夹前需要对夹具在工作台上
的位置进行调整,菱形销与主轴的同轴度进行调整;以及对刀调整(刀块伸出长度必须保证销孔的直径),要知道调整不可能绝对的精确,这就会产生调整误差。另外,机床、刀具、夹具本身就存在着制造误差,
这类原始误差称为工艺系统的几何误差。
(3)加工误差 由于在加工过程中要产生切削力、切削热和摩擦,它们会引起工艺系统的受力变形、
受热变形和磨损,这些都会引起在调整时已获得的工件与刀具的相对位置的变化,造成种种加工误差。这
类在加工过程中产生的原始误差称为工艺系统的动误差。
除此之外,工件在毛坯制造(铸、锻、焊、轧制)、切削加工和热处理时,在力和热的作用下产生的
应力,将会引起工件变形而产生加工误差。现将在加工过程中可能出现的种种原始误差归纳如下:
???????????????????????????????与工艺系统初始状原理误差定位误差工件相对于刀具在静止状态下已调整误差 存在的误差刀具误差态有关的原始误差夹具误差机床主轴回转误差工件相对于刀具在运动原始误差机床导轨导向误差状态下已存在的误差机床传动误差 (几何误差)
工艺系统受力变形(包括加紧变形)工艺系统受拉变形 与工艺过程有关的原始误差刀具????????????????????????????????????
磨损 测量误差 工件残余应力引起的变形
(-).影响尺寸精度的主要因素
1.尺寸测量精度
零件尺寸精度的获得,首先受到测量仪器精度的限制。零件的加工尺寸就目前的加工方法来讲,可以
获得非常精确的尺寸。但是,由于尺寸的测量精度不高而无法分辨。过去钢球加工采用滚磨和滚研方法,
可以获得很高的精度,但没有相应的测量工具就不能进行精确尺寸的测量和尺寸分组。过去只能测量出尺
寸精度为0.5μm 的钢球,现在可以制造出0.1μm 的钢球或者更高。从生产工艺上来看方法没有什么变化,
只是尺寸的测量仪器精度有了相应的提高,测量方法采用了光波干涉原理,将被测尺寸与激光光波长相比
较,其测量精度可达到0.01μm 。不过这种方法主要用于实体基准——精密量块和精密刻度尺的测量。对于
一般机器零件的测量,主要还是采用万能量具量仪进行测量。
机械加工中尺寸的测量方法有:
(1)绝对测量和直接测量 测量示值直接表示出被测尺寸的实际值,这类量具有游标卡尺、百分尺、
百分表和测量仪。
(2)相对测量 测量值只反映被测尺寸相对于某个定值基准的差值,而被测尺寸的实际值等于基准
与偏差值的代数和。
(3)间接测量 测量示值只与被测尺寸有关的一些尺寸或几何参数,测出后还必须再按它们之间的
函数关系计算出被测零件的尺寸。如采用三针和百分尺测量螺纹中径。采用弓高弦长规测量非整圆样板或
大尺寸圆弧直径等。
2.影响尺寸测量精度的主要因素
(1)测量工具本身精度的影响
对零件尺寸进行测量时,选用的测量工具存在一定的制造误差,因而其本身的精度必然对被测量零件
尺寸的测量精度产生直接影响。测量工具精度主要由示值误差、示值稳定性、 回程误差和灵敏度等四个
方面综合起来的极限误差,对被测零件造成测量误差。
(2)测量过程中测量部位目测或估计不准的影响
当用外径百分尺测量轴颈d 时,如见1-9a (哈工大144页图4-2)所示,通过几何关系,我们可以推
算出测量误差d ?为:
2
'22(1cos )4sin 2d d d r r r ???=-=?=-= 因角?很小,sin 22?
?
≈,
故 224()2
d r r ?
??≈= 当测量孔径D 时,见图1-9b ,可以通过几何关系计算出其测量误差D ?为:
'D D D D D ?=-==
22sin 11cos 2(
1)()cos cos cos D D D ?????-=-== 因角?很小,sin 22?
?
≈,cos 1?≈
故 22
D D ??≈ 由上述分析可知,当φ角一定时,被测工件的尺寸越大,造成的测量误差就越大。因此测量时,应注
意保持正确的测量部分,也可以多次测量取平均值。
目测刻度尺寸时,如果观测方向和目视方向不垂直,是斜视,也会造成目测误差。
(3)量具的正确使用、保养及维修。
从市场和厂家买来的量具,由于运输、材质、制造等多方面的原因,造成量具的刻度对零性不准,引
起测量不准确;经过长期使用,由于磨损保管不当造成测量不准;由于量程精度等级与被测件不相适应造
成测量不准产生测量误差。因此量具的正确使用和保养与维修也是确保降低测量误差的一个重要方面。厂
家必须有自己的二级计量站或挂靠单位,并与省级计量站保持紧密联系,制订出量具的使用期限及合理使
用维修规程。
一般的规程是:
①从市场、厂家购置的量具必须经过二级检测站检测合格后登记入库再行使用;
②规定各量具安全使用期限,任何人和部门不得使用过期的量具;
③合理选择量具,选择量具时必须保证量具的精度要与被测工件相适应,还要注意到量具的量程与被
测工件相适应,也就是说不能用高精度的量具去测低精度粗糙表面。久而久之就降低了量具的精度等级。
低精度的量具测不出高精度工件的尺寸。量具的量程也要和被测工件相适应,不能用大量程去测小尺寸的
工件,也不能用小量程去测大尺寸的零件。违背了上述规程都会造成测量误差。
同时,在操作时,对百分表类的量仪,最好使用其线点系数较好的标准段对零件进行测量,精度等级
最好选大于等于被测零件尺寸公差两倍的量仪进行测量。
④测量地点和时间。由于测量地点和时间不对也会造成很大的测量误差,也就是说被测件必须在不受
力状态、冷却后才进行测量,绝对不允许在机床上进行测量。如果在机床上测量,由于受夹紧力和切削热
的影响,测不出真实的尺寸。
⑤首检制度。批量生产首检制度是保证工件质量的重要措施,同时还要经常抽检进行质量跟踪。
⑥多次反复测量,对被测工件进行反复测量,然后进行数据处理得到较为接近零件的真实值。
3.微量进给精度
产生微量进给精度的主要原因是:一方面进给机构中各相互运动的零件表面之间存在摩擦力,即机床
导轨与工作台之间的摩擦力。这些摩擦力促使进给机构产生相应的弹性变形,转动进给手轮时,就会阻止
工作台移动,使工作台的移动量与手轮转动的格数(μm)不准确。另一方面是丝杠与螺母存在着间隙,传递力不能使工作台在一开始就移动,造成移动的距离与手轮转动的格数与工作台移动的距离不相符造成误差。
提高微量进给精度的方法是:
(1)提高进给机构的传动刚度,降低弹性变形,消除丝杠与螺母的传动间隙,缩短传动链都能有效地减少微量进给造成的误差。
(2)减少进给机构各传动副之间的摩擦力和静、动摩擦因数的差值。例如采用滚动丝杠螺母、滚动导轨或静压螺母、静压导轨、变滑动摩擦为滚动摩擦。因滚动摩擦因数很小,且几乎不随速度的提高而下降,故可以显著提高微量进给程度。
除此之外,还可以选择理想的润滑油,让它的张力小、吸附力强,能在相对滑动向上形成一层不易被刮掉的薄油膜层;采用新型导轨材料(如聚四氟乙烯)。
(二).影响形状精度的主要因素
在机械加工中,获得零件加工表面形状精度的基本方法是成形运动法,如果零件的形状精度要求超过现有机床设备的成形运动精度时,还可以采取非成形运动来获得零件的形状精度。
虽然组成零件的几何形面的种类繁多,但就其加工时所采用的成形运动而言,不外乎由回转运动和直线运动这两种基本形式所组成。例如圆柱面和锥面是由一个回转运动和一个直线运动形成,球面是由两个回转运动形成,平面是由二个直线运动形成,渐开线是由两个回转运动和一个直线运动形成等。要想获得准确的表面,就要求各形成运动以及它们之间的关系均匀准确,例如加工圆柱面必须首先要保证回转运动和直线运动本身的运动的准确性,同时还应当保证它们之间的相互位置关系的准确性,也就说必须保证回转运动的轴线与刀具直线运动平行,否则加工后不是一个圆柱面,而是一个锥面。采用成形刀具加工时还必须保证刀具的制造安装精度,因此影响形状精度的主要因素是:
(1)各成形运动本身的运动精度;
(2)各成形运动之间的相互位置关系的精度;
(3)各成形运动之间速度关系的精度;
(4)成形刀具的制造安装精度。
1.主轴回转运动的精度对零件形状精度的影响
(1)主轴回转精度
主轴是机床的关键部件,它既传递转矩又承受切削力。主轴回转精度的高低直接影响到被加工零件的形状精度的高低。
所谓回转精度是指主轴实际回转轴心线的位置与理想回转轴线的位置的符合程度。理想的情况是主轴回转位置是不变化的。如图1-10(a)(哈159页4-17)所示,中心O点的速度始终为零,把O点称为理
想的回转中心。理想的回转中心是不存在的,但是由于主轴箱、轴承、箱体的制造装配误差以及加工时受
力、受热产生的变形和磨损等原因,实际上主轴的回转轴线随时都在变化,如图1-10(b )的O 1所示,此
时的中心称为瞬时回转中心。通常把实际回转轴线作误差运动时的对称中心线称为回转轴线的平均线。
主轴回转误差是指主轴的实际回转轴线与平均回转轴线在加工误差敏感方向上的最大变动量。主轴回
转运动的误差可分解为三种基本形式,如图1-11(重大11页图1-12)所示,其中a )为径向跳动,b )为
轴向窜动,c )为轴的角度摆动。
1)径向跳动和漂移 径向跳动又可分为纯径向跳动和漂移两种情况。纯径向跳动是指主轴实际回转
轴线相对主轴平均回转轴线在空间作平行移动,即系统性常值误差。漂移也是径向跳动,只不过主轴实际
回转轴线的跳动方向和跳动量是一个随时间变化的量值,实质就是一个系统性变值误差。
主轴纯径向跳动对形状精度的影响随加工方法不同而异。在镗床上镗孔情况如图1-12(重大11页图1
-13)所示,设镗床主轴轴心线在Y 坐标方向作简谐振动,主轴每转一周其轴心线在Y 坐标轴上振动一
个周期。若振幅为A ,当镗刀转过一个φ角时,刀尖的坐标为
cos cos ()cos Y A R A R ???=+=+
sin Z R ?=
由上两式可得
22
221()Y Z R A R
+=+ (1-2) 这是一个椭圆方程式,即如果镗床主轴有径向跳动,所镗得的孔是一个椭圆。
车削时,主轴轴线若与上述镗床主轴为纯径向跳动相同,则对工件的形状精度(圆度)影响很小,见
图1-14(重大12页)。
设主轴轴心线沿Y 坐标方向作谐振运动,则在工件1处(轴心线偏移最大处)切出的半径比在2、4
两点处切出的半径小一个振幅A ;而在3点处切出的半径则刚好要比2、4切出的半径大一个振幅A 。结
果是在上述四点处工件的直径是相等的,故工件表面近似一个真圆。
主轴如果有漂移,使工件产生圆度误差和表面波度。
2)纯轴向窜动 主轴的轴向窜动对内外圆加工精度无影响。但在加工端面时会引起端跳动,即轴线
与端面不垂直如图(图1-14)所示(重大12页1-15)对螺纹加工会造成螺距的周期误差。
3)纯角度摆动 主轴实际回转轴线与平均回转轴线成一交角运动时如图(1-丶15a )所示(重大12
页1-16),对工件的形状精度影响很大。车外圆时,会产生圆柱度误差(锥度),镗孔时将呈椭圆形(图
1-15b )(重大12页)。
(2)影响主轴回转精度的因素
由于主轴所使用的轴承不同,影响主轴回转精度也有所不同。
①滑动轴承的影响
影响滑动轴承因素有:主轴颈和轴瓦内孔的圆度误差以及轴颈和轴瓦内孔的配合情况。对于车床、轴瓦内孔的圆度误差影响较小,而轴颈的圆度误差影响很大。这是因工件转动而切削力方向不变,而回转轴颈总是与轴瓦的某一部分接触,所以轴心线的径向跳动取决于轴颈的圆度,图1-16a所示(重大13页1-17a)。
对于镗床,与车床的情况刚好相反,轴瓦内孔的圆度误差起主要作用,而轴颈的圆度误差影响很小。这是由于刀具转动,切削力方向是变化的,所以轴瓦的内孔总是依次与轴颈某一固定点接触,如图1-16b (重大13页1-17b)所示。
②滚动轴承的影响。车床和镗床采用滚动轴承,由于滚动轴承是由内圈、外圈和滚动体组成,影响因素更多。分析轴承内、外圈滚道的圆度误差和波度对回转精度的影响时,可视外圈滚道相当于轴承孔,内圈滚道相当于轴。因此,对工件回转类机床(车床),滚动轴承内圈滚道圆度误差对主轴回转精度影响较大,主轴每转一周径向跳动两次,加工出来的工件是椭圆。对刀具回转类机床(如镗床等)外圈滚道对主轴的回转精度影响较大,主轴每回转一周径向跳动一次,镗出来的孔也是椭圆。
影响滚动轴承的因素很多,除上述内外滚道的影响外,还有:
a. 主轴箱轴内孔不圆会引起轴承外圈变形;
b. 主轴颈不圆会引起滚动轴承内圈变形;
c. 箱体前后轴承孔的同轴度误差较大也会产生主轴径向跳动和端跳动;
d. 止推轴承滚道的端面跳动会引起主轴窜动,向心推力轴承的内外滚道倾斜也会使主轴产生径向跳动和轴向窜动,使工件的端平面与轴线不垂直;
e. 滚动体尺寸误差引起回转轴径向跳动,最大尺寸的滚动体通过承载区一次,就会使主轴发生一次最大的径向跳动。
(3)提高主轴回转精度的措施
①提高轴承精度
轴承是影响主轴回转精度的重要因素,对于精密机床采用精密滚动轴承,多用油楔动压和静压轴承,如磨床、砂轮主轴用的是三瓦块油楔动压轴承。
②提高主轴及主轴箱体制造精度
主轴回转精度在很大程度上取决于主轴和箱体的精度以及装配质量。
③高速主轴部件要进行动平衡以消除激振力。
④滚动轴承采用预紧
轴向加适当的预紧载荷,消除轴承间隙,使滚动体产生微量弹性变形,可提高刚度和使用寿命。
2.机床导轨误差对刀具直线运动及零件形状精度的影响。
(1)导轨误差对加工零件精度的影响
1)对一般机床而言,导轨在水平面内的直线度误差?1如图1-17(重大15页20图)所示,要求?1
为1000:0.02。此误差对普通车床和外圆磨床,它将直接反映在被加工件的法线(敏感)方向产生椭圆,
其误差值?r 几乎等于导轨水平面内的直线度误差?1,如图1-18a (哈163页4-23图)。
②导轨在垂直平面内的直线度误差?2一般也为1000:0.02,见图1-18b .误差对于普通车床和外圆磨
床发生在被加工件的切线方向,对加工件的形状精度影响很小,可以忽略不计,除加工圆锥面。
③导轨与导轨之间在垂直方向内的平行度误差?n (扭曲)为1000:0.02(如图1-18c 所示)(哈164
页),导轨发生扭曲,工作台的直线进给将发生摆动。刀尖本身的成形运动将是一条空间曲线。如果导轨
的平行误差为?n 时,被加工零件造成的直线误差?r =?y =n B
H ?。 一般车床H/B =2/3,外圆磨床为H/B≈1,故?n 对工件的表面形状的影响不可忽视。
④平面磨床导轨误差对形状精度的影响。
对平面磨床而言,对形状精度起主要作用的是砂轮架和工作台导轨在垂直面内的直线度误差和两导轨
之间在垂直方向的平行度误差,这些误差几乎是1:1的反映在工件的不平度误差上;导轨在水平面内的
直线度误差,由于不在加工方向的敏感方向,所以影响极小。
(2)提高直线运动精度的主要措施:
①选用合理的导轨形状和导轨组合形式,并尽可能地增加工作台与床身导轨的配合长度。虽然导轨的
形状和导轨的组合形式多种多样,但从导轨的承载情况、制造精度和在使用过程中的精度保持性等方面综
合分析认为,可获得直线运动精度高和精度保持性好的导轨形状和导轨组合形式是90°的双三角形导轨。
②提高导轨的制造精度
在选用合理的导轨形状和导轨组合形式的基础上,提高导轨的直线运动精度的关键在提高导轨的加工
精度和安装质量,采用耐磨性好的合金铸铁导轨,提高导轨的耐磨性,安装时首先选用良好的基础,然后
进行安装调试,在使用中还要进行定期检查、维护与保养。
③采用新型导轨,如静压导轨、卸载导轨和双V 型导轨。
(3)各成形运动之间相互位置关系对形状精度的影响。
要想获得加工零件表面的形状准确,不仅要求各成形运动准确,同时还要求它们之间相互位置关系也
要准确,否则就要影响被加工件的表面形状精度。
1)车床加工外圆,如图1-19a (哈166页4.25a )所示,要想获得准确的圆柱表面,除了工件回转轴
线精度和刀具的直线运动准确外,还要求工件的回转轴线与刀具的直线运动要平行,否则,加工出来的外
圆表面就不会是一个准确的圆柱面。
若刀具的直线运动在xoy 平面内与工件的回转轴线不平行,则加工出来就是一个锥面(如图1-19b ),
而且随误差增大,锥度也就越大。例如,机床刀具直线运动与工件的回转轴线的平行度误差?为400:0.01,
加工工件的长度为L =400mm ,直径d =40mm 时,则加工后两端的直径误差?d 为
mm L y d 02.0400
40001.022=??=??=? L y d ??=?2 (1-3)
式中d ?——直径误差;
y ?——法向误差;
L ——工件长度。
若刀具的直线运动的轨迹与工件回转轴线不在xoy 平面内,而在空间交错平行,则零件加工后的表面
是一个双曲面。如图1-19c 所示。通过几何运算反映在X 处截面的加工误差
20
2x h r r ?= (1-4) 但是这种情况产生的误差不在法线方向,故影响很小,可以忽略不计。例如,同样加工上述零件各运
动面之间的平行度误差?同样为400:0.01,计算轴加工后的最大误差?d ,依据题意,刀具在工件中心处
高于回转轴线的最大距离应为h x
根据(1-3)式 0.012000.005400
r mm ??== 这个地方有个公式 ,请加上见哈大167
再根据(1-1)式 2
20.00520.0000012540
d r mm ??=?= 计算结果证明,完全可以忽略不计。
2)在车床上加工端面时,如果刀具运动的轨迹与工件回转轴线不垂直,则加工后工件的端面会出现
两种情况:凸起或凹陷。如图1-20a (哈167页4-26a )所示,其平面度误差为
tan 2
d α?=
工 (1-5) 式中d 工为工件直径,mm 3)在卧式镗床上镗孔时,若工件作直线位移运动(进给)的轨迹与镗杆回转轴线不平行,有一交角α,
则平行度误差为tan α,加工出来的孔是椭圆,如图1-20b (哈167页)所示,加工后的圆度误差为
(1cos )2
d α?=-刀 因α很小 2
cos 12αα≈-
故 24d α?≈
刀 (1-6)
式中d 刀为镗刀直径,mm
B 为工件直径,mm 3)在立式铣床上加工平面,如果工作台的直线进给运动与刀具的回转轴线不垂直,有垂直度误差tan α,则加工后工件表面将产生不平度误差。如图1-21|哈168页图4.27所示,加工后工件表面的平面度误差为
sin sin 2d b αα??==-???刀
1sin 2
d α?=???刀 (1-8) 式中d 刀为镗刀直径,mm
提高成形运动之间相互位置关系精度的主要措施:
主要是保证机床各有关部件的制造精度,再通过安装时调试、检测、精修来达到。在工作中同样要注意保养和维护。
4)各成形运动的速度关系对形状精度的影响
(1)车床加工外圆对工件的转速与刀具移动的速度没有特殊的要求,快、慢只对表面质量有所影响。但是车床加工螺纹就要求工件的转速与刀具的移动速度要按一定的比例关系进行传动,这就是所谓的内联传动。否则就会产生螺旋线误差?P 周。又如滚齿机加工齿轮、插齿机加工直齿轮、斜齿轮,都要求刀具的运动和工件运动按一定比例关系进行运动,这就是所谓的差运动。否则,加工出来的齿轮就不是渐开线齿轮,会产生齿形误差和圆周齿距的误差。
(2)提高各成形运动之间速度关系的主要措施
①提高机床各传动链元件的加工精度和装配精度;
②缩短传动链,减少传动误差;
③消除传动副间隙;
④采取校正机构,在精密螺纹加工机床上,都加有校正装置,以保证丝杠加工精度。
4.刀具、夹具的制造精度及安装对工件形状精度的影响
(1)刀具的制造与安装
这里讲的刀具是成形刀具,对于单刃刀具、车刀、刨刀及单刃镗刀与工件的形状精度没有直接影响。 成形刀具指:成形车刀、成形铣刀及成形砂轮。
定尺寸刀具指:键槽铣刀、三面刃盘铣刀、多刃浮动镗刀、拉刀、铰刀、最常用钻头。如果安装不正确,不仅会使工作尺寸精度不准确,对位置精度、形状精度也有很大的影响。
展成刀具指齿轮滚刀、插齿刀和花键滚刀。如果制造和刃磨以及安装不正确,对工件的尺寸精度、形状精度、位置精度都有很大的影响。
(2)刀具的磨损
任何坚硬的刀具材料只要用于加工都会有磨损,只不过是快和慢的问题。磨损过程分为三个阶段:初期磨损阶段、正常磨损阶段和急剧磨损阶段。如图1-22所示(切削原理)。对定尺寸刀具来讲,磨损直接影响到工件的尺寸精度;对成形刀具来讲,不但影响尺寸精度,还要影响形状精度。
减少刀具磨损的措施是尽量选用耐磨性材料,正确的规定刀具磨损标准;在加工中采用合理的刀具角度和切削用量;按加工性质不同采用合理的冷却润滑液;必要时可对刀具尺寸磨损采取补偿。
(3)夹具的制造精度与安装精度
使用夹具的目的是保证在批量生产中零件的位置精度、尺寸精度和形状精度,从而达到提高生产率、降低劳动强度。但是如果夹具制造误差达不到要求或者安装调试时不准确,同样会造成较大的位置误差,同时影响工件的尺寸精度和形状精度。
三.工艺系统原有误差对位置精度的影响及其控制
1.影响位置精度的主要因素
在机械加工中,获得工件加工表面之间位置精度的方法有一次安装找正法和多次安装找正法,不管用什么方法都要选择一个工艺基准面,选择工艺基准面总的原则是从有位置精度要求的加工面中选择。
影响精度的主要因素有以下几个方面:
①机床的几何精度;
②工件的找正精度;
③夹具制造和安装精度;
④工件加工表面之间位置检测精度。
(1)机床的几何精度
当零件上各加工表面在多刀机床(如多刀车床、多刀刨床、多轴钻床及加工中心)上一次装夹中,同时或顺序地由多把刀具加工获得时,其各表面的位置精度主要取决于有关部件之间的位置精度,而与工件的装夹精度无关。
(2)工件的找正精度
当工件的各加工表面有位置精度要求,是靠多次安装来实现时,工件加工后的位置精度与找正精度有关,同时与操作者的个人技术有着密切的关系,此时零件各有关表面之间的位置精度不再与机床的几何精度有关。常采用百分表来找正,提高工件的找正精度。
(3)夹具的制造精度与安装精度
在成批大量生产中,常用专用夹具来保证工件各加工面的位置精度和尺寸精度,这意味着工件表面与定位基准之间的精度转化为夹具在机床上的找正,因此,夹具的制造和安装精度直接影响工件的位置精度。
(4)工件加工表面的位置精度、检测精度
当零件各有关表面的位置精度要求甚高,又不能通过各种装夹方法来保证时,只能采用非成形运动法来实现。此时加工后零件有关表面的位置精度主要取决于对加工表面之间位置的检测精度。例如精密量块和研磨精度,其各表面的平行度只能通过不断检测其平行度误差并进行不断修研来达到。
四.工艺系统受力变形对零件加工精度的影响及控制。
工艺系统是指机床、夹具、刀具及工件等环节组成,它是一弹性系统。在加工时由于切削力、夹紧力、零件自重力和惯性力的共同作用,工艺系统各组成环节会产生弹性变形,同时系统各元件接触处的间隙还要产生位移和接触变形,从而破坏了刀具与工件已获得的准确位置关系,而产生了加工误差。因此,研究工艺系统的受力变形,采取措施消除或减少工艺系统受力变形是提高工件加工精度的重要途径。
1.工艺系统刚度对加工精度的影响。
(1)工件结构及材料刚度不足产生变形
刚度是指材料在载荷作用下抵抗弹性变形的能力,如果工艺系统的刚度很大,弹性就变很小,对零件加工精度影响就很小。
根据材料力学,任何物体或构件在外力的作用下要产生弹性变形,在弹性范围内变形量与静载荷F 方向的弹性变形量成正比,即
F K y
= (1-9) 比值K 称为刚度,单位为N/mm 2。工艺系统的刚度又分静刚度和动刚度。当外力为静载荷时,工艺系统将产生静变形,产生单位变形所需沿变形方向的静载荷值称为工艺系统的静刚度;当外力为动载荷时,工艺系统将发生振动,产生单位振幅所需的激振力幅值为工艺系统的动刚度。我们只研究静刚度,简称工艺系统刚度。用K xt 表示
y xt n F K y = (1-10)
式中,F y —加工表面法线方向的切削力(总切削力的径向分力),N ;
Y n —在F x (相当于进给力F f )、F y (相当于背吃刀力F p )、F z (相当于切削力F c )综合作用下的法向位移,mm 。
工艺系统的刚度又分为正刚度和负刚度。当加工条件改变后,它会引起F x 、F y 、F z 各切削力之间的大小和方向都将发生变化,各切削力的综合作用结果可能会使工艺系统沿F y (法线)方向的总变形为负值,
如图1-23a (重大19图1-25)所示。在这种情况下,工艺系统因工件的刚度不够可能产生振动、啃刀及折刀现象,结果是工件不仅尺寸精度误差大,而且形状精度和表面质量也会严重下降。如果改变进给方向,如图1-23b (重大19图1-25)所示,总变形量为正值,称为工艺系统正刚度。
我们在加工细长轴时,由于工件刚度不够,在背吃刀力的作用下,工件会产生变形,如图1-24(清华183 3-28a )所示,加工后工件变成了腰鼓形;解决的方法是光轴用跟刀架,阶梯轴用中心架,可以减少变形。在磨削内孔时,由于刀杆细长、刚度不够、背吃刀又很大,磨削完后工件内孔成喇叭口形。减小变形的方法是提高刀杆的刚度或者减少背吃刀量,孔的磨削最好采用珩磨。如图1-25b 。清华3-28b
(2)机床刚度不足引起的变形对加工精度的影响
假定工件短粗,刀具伸出长度很短,也就说工件和刀具受力变形都很小,可以忽略不计,只考虑机床头、尾座和刀架受力产生位移,分析受力变形产生的位移。现在以车光轴为例,如图1-26(重大20页1-28)所示,假定切削过程中,切削力大小不变,则工艺系统的受力变形取决于机床的床头(包括前顶尖)、尾座(包括后顶尖)和刀架的变形。
设法向切削力F y 作用在工件x 处,机床头架所受的力F A 为y L x F L -
,尾架所受的力F B 为y x F L
,刀架所受的力为F y 。分别求出刀架的变形为 y F y
K =刀架刀架
头架的变形为 ()y F L x y
K L
-=头头 尾架的变形为 ()y
F x y K L =尾尾 这时刀具在工件x 处相对于工件法向的总位移为
x y y y =+刀架机床
由图中几何关系:
()x y y L
?=-尾头 x y y =?+头
则 ()
x x y y y y L =+-尾头头 所以 ()x y y y y y L
=+-尾刀架头头机床+
将y 头、y 尾、y 刀架各公式带入(1-9)式整理后得
22111()()y L x x y F K L
K L K ??-=++????机床尾头刀架 故得机床刚度
221111()()y F K L x x y K L K L K ==-++机床机床尾头刀架
这说明,随着切削力作用点位置的变化,工艺系统的变形是变化的。
当x =0 11()y y F K K =+机床头刀架
变形最大 当x =L 11(
)y y F K K =+机床尾刀架 变形最大 当x =L/2 111()44y y F K K K =++机床尾头刀架
变形最小 变形最大的地方,从工件上切去的金属层最薄;变形小的地方,从工件上切除的金属层最厚。因此由于机床受力变形加工出来的工件呈马鞍形,如图1-27(清华185页3-30)所示。
当x =()K L K K +尾尾头,机床变形量最小,min 1()y y y F K K K ==++机床尾头刀架
。 ①为机床不变形的理想情况;②为只考虑主轴箱和尾座的变形情况;③为包括考虑刀架变形,主轴箱、尾座变形在内的情况。
工件变形量y ,如果只用卡盘装夹,不用后顶尖,可根据材料力学悬臂梁来计算,如图1-27a
3()3y F L x y EI -=工件 (1-11)
式中 E ——材料的弹性模量,N/mm 2,对于钢材通常取E ≈2×105 N/mm 2
I ——材料截面的惯性矩,mm 4
工件的刚度
3
3()y F EI K y L x ==-工件工件 当两头都用顶尖时,工件的变形可按材料力学中简支梁计算,如图1-27b
22()3y F L x x y EIL -= 工件
工件的刚度 223()y F EIL K y L x x
==- 工件工件 当刀尖处于工件中心位置时,工件变形最大,工件刚度最小。
刀具的刚度对于车刀变形甚微,可以忽略不计。
(3)工艺系统总的变形y n
2222()111()()3y n y F L x x L x x y y y F K L K L K EIL ??--=+=+++????
工件
机床尾头刀架 工艺系统总的刚度 22
221111()()()3y n F K L x x L x x y y K L K L K EIL ==--++++ 工件机床尾头刀架 (1-12)
(4)机床部件刚度的特点
图1-28是通过对机床刀架作静刚度的测量画出来的曲线,从曲线图上可以看出,机床部件的刚度有如下特点:
①变形与受力的关系不是线性关系,反映刀架的变形不是纯粹的弹性变形。
②加载曲线与卸载曲线互不重合,两曲线所包围的面积表示加载与卸载损失的能量,这些能量用于克服零部件的摩擦和接触弹性变形所作的功。
③卸载后变形没有恢复到原点,加载曲线与卸载曲线不构成封闭曲线,这是因为残余变形影响的结果。在反复加载—卸载后,残余变形逐渐接近于零。
④部件的实际刚度远远比按实体估算的刚度要小,图中(1-28重大22页1-30)第一次加载的平均刚度值大约为4.6×103N/mm ,只相当于一个30×30×200mm 3铸铁悬臂梁的刚度值。这说明机床部件的刚度是一非线性关系,刚度K =d F /d y 不是一个常数,而我们通常说的刚度是一个平均刚度值。
2.影响机床部件刚度的因素
(1)接触表面的接触变形
零件加工后,表面并不是绝对的平整光洁,它总存在着宏观几何尺寸和微观的表面粗糙度,所以零件表面的实际接触面积只是理论接触面积的一小部分(如图1-29所示重大22页1-31),而真正接触的状态又是这一部分中的那些凸峰。在外力作用下,接触点产生很大的接触应力,因而产生很大的接触变形,这种接触变形不但有表层的弹性变形,而且还有局部的塑性变形。这就是部件刚度曲线不呈直线,而且远比估计刚度小的重要原因之一。
(2)摩擦力的影响
机床部件受力发生变形时,零件连接表面会产生错动,加载时摩擦力阻碍变形发生,卸载时摩擦力阻
碍变形的恢复,结果造成加载曲线与卸载曲线不重合。
(3)接合面间隙的影响
机床部件受力后,首先是消除各部件存在的间隙,使部件产生较大的位移,相互错动使刚度下降。间隙消除后,相应表面的接触才开始有接触变形和弹性变形,这时表现为刚度较大,如图1-30所示(重大23页图1-33)。如果是单向受力,加载后间隙消除,对部件变形和刚度的影响不大。但对切削力经常发生变化的镗削、铣削等加工来讲,间隙引起的位移,使刀具与工件相对位置不断改变,产生较大的加工误差。
(4)薄弱环节的影响
机床部件中总有一些刚度很低的零件存在,受力后这些部件将产生很大的变形,从而大大的降低了整个部件的刚度。例如刀架部件中的锲铁与导轨配合不好(如图1-31a )(重大23页1-32),或轴承衬套因形状误差而与壳体接触不良(如图1-31b )(清华192页3-41),因锲铁和轴承衬套极易变形,造成整个部件刚度大大降低。
3.工艺系统受力变形对加工精度的影响
(1)由于切削力作用点位置变化引起的加工位置误差。工艺系统的刚度随切削力作用点位置变化而变化,从而引起工艺系统的变形不断变化,使加工表面产生几何形状误差。在外圆加工中会产生锥度、马鞍形、腰鼓形等圆柱度误差。
(2)误差的复映规律
在加工过程中,如果毛坯形状误差或硬度很不均匀,引起工件在加工时切削力的大小会发生很大的变化,工艺系统的变形也就因切削力的变化而变化,结果引起工件产生加工误差。现以车外圆为例,如图1-32(重大23页1-34)所示,工件在加工前有圆度误差,是个椭圆,切削时,工件每转一转,背吃刀量发生变化,最大的背吃刀量为a P1,最小的背吃刀量为a P2,假定毛坯的硬度是均匀的,则a P1处的切削力为F y1为最大,a P2处的切削力为最小F y2。车削前毛坯具有圆度误差为?m =a P1-a P2时,车削后由于工艺系统受力变形而使工件产生相应的圆度误差为?g =y 1-y 2,我们把这种现象称为“误差复映”。
如果工艺系统的刚度为K ,则工件的圆度误差
12
121()y y g y y F F K ?=-=
- 由切削原理可知: ()E F y y y y n x y F p F C a f HB =
式中 y F C ——与刀具几何参数及切削条件(刀具材料、工件材料、切削种类、切削液等)有关的
系数;
p a ——背吃刀量;mm
f ——进给量;mm/r
HB ——工件材料的布氏硬度;
y E y 、y
F n ——指数 在工件材料硬度一致,刀具、切削条件和进给量一定的情况下,()E F y y y y n F C f
HB C =是一个常数。
在车削加工中,1y xF ≈,于是切削分力F y 可以写成 p
y a F C = 所以得
1
1p y a F C = 2
2p y a F C = 代入(1-12)式得
12()p p C C g a a m m K K
ε?=
-=?=? 式中 ε=C /K 称ε为误差复映系数。由加工后的工件圆度误差?ε总是小于毛坯圆度误差?m ,所以ε是一个小于1的正数。它定量地反映了毛坯误差加工后所减小的程度。减小C 或增大K 都能使ε减小。例如,减小进给量和背吃刀量不但可以减小C ,同时使ε减小,同时还提高加工精度,但是使切削加工时间长、生产率低。看来增大工艺系统的刚度K ,不但减小了加工误差?ε,而且在保证加工精度的情况下还能提高生产率。
采用多次走刀可以减少复映误差?ε。设ε1、ε2、ε3……分别为第一次、第二次、第三次……走刀的误差复映系数,则走刀的误差复映系数为
11g m ε?=?
2212g g m εεε?=?=?
33123g g m εεεε?=?=?
…………
总的误差复映系数ε总
ε总=ε1ε2ε3…
由于ε是个小于1的正数,多次走刀后ε总就变成一个远远小于1的系数,多次走刀当然可以减小加工误差,提高工件的加工精度,但生产率就意味着很低,同样不可取。
由上分析,可以得出以下几点结论:
①被加工件加工前的尺寸误差或形状误差,都会按一定的比例复映到加工后工件表面上产生尺寸误
机械制造工艺学第三版王先逵第五章习题解答.docx
机械制造工艺学习题解答 第五章:机械加工表面质量及其控制(第3 版P267) 5-1 机械加工表面质量包括哪些具体内容? 答:(P229)机械加工表面质量,其含义包括两个方面的内容: A.加工表面层的几何形貌,主要由以下几部分组成:⑴表面粗糙度; ⑵波纹度;⑶纹理方向;⑷表面缺陷。 B.表面层材料的力学物理性能和化学性能,主要反映在以下三个方面:⑴表面层金属冷作硬化;⑵表面层金属的金相组织变化;⑶表面层金属的残余应力。 5-2 为什么机器零件一般总是从表面层开始破坏的?加工表面质量对机器使用性能有哪些影响? 答:(P231)(1)由于表面是零件材料的边界,常常承受工作负荷所引起的最大应力和外界介质的侵蚀,表面上有着引起应力集中而导致破坏的微小缺陷,所以这些表面直接与机器零件的使用性能有关。(2)加工表面质量对机器的耐磨性、耐疲劳性、耐蚀性、零件配合质量都有影响。 5-3 车削一铸铁零件的外圆表面,若进给量f=0.40mm/r ,车刀刀尖圆弧半径re=3mm ,试估算车削后的表面粗糙度。
答上根据教材P2站舍式,表面粗桂度的佶算直为 5-4高速精镯呆谓工件的内孔时,采用主値角κ,=75%副?‰∕=15o fi?W 1-6 什么是机械加工工艺过程?什么是机械加工工艺系统? 机械加工工艺过程是机械产品生产的过程的一部分,是直接生产过程,其原意是指采取 金属切削刀具来加工工件或磨具来加工工件,使之达到所要求的形状、尺寸、表面粗糙度和 力学物理性能,成为合格零件的生产过程。 机械加工工艺系统是零件进行机械加工时,必须具备一定的条件,即要有一个系统来支 持。通常,一个系统是由物质分系统、能量分系统和信息分系统所组成。 1-7 什么是工序、安装、工位、工步和走刀? 1.工序:一个(或一组)工人在一个工作地点对一个(或同时对JL 个)工件连续完成的那 一部分工艺过程。 2.安装:如果在一个工序中需要对工件进行几次装夹,则每次装夹下完成的那部分工序 内容称为一个安装。 3.工位:在工件的一次安装中,通过分度(或移位)装置,使工件相对于机床床身变换加 工置,则把每一个加工位置上的安装内容称为工位。 4.工步:加工表面、切削刀具、切削速度和进给量都不变的情况下所完成的工位内容, 称为一个工步。 5.走刀:切削刀具在加工表面上切削一次所完成的工步内容,称为一次走刀。 1-8 某机床厂年产 CA6140 车床2000台,已知机床主轴的备品率为14%,机械 加工废品率为4%,试计算机床主轴的年生产纲领并说明属于何种生产类型,工 艺过程有何特点?若一年工作日为282天,试计算每月(按26天计算)的生产 批量。 (1)机床主轴的年生产纲领 N=Qn(1+%+%)=20001(1+14%+4%)=2360αβ??台 机床主轴属于中型机械,查表属于大批生产的生产类型。 (2)工艺过程特点 a)采用模锻制造毛坯,毛坯精度高,加工余量小。 b)采用专用机械加工设备流水线生产 c)采用专用工装 d)采用详细的工艺规程,用工序卡、操作卡及调整卡管理生产。 (3)生产批量 n 217.589217?'==≈N A 236026=台F 282 1-10 何谓六点定位原理?何谓完全定位和不完全定位?何谓欠定位和过定 位?试举例说明之。 六点定位原理:采用6个按一定规则布置的约束点来限制工件的6个自由度,实现完全 定位,称之为六点定位原理。 完全定位:限制了6个自由度。 不完全定位:仅限制了1—5个自由度。 5-4 装配尺寸链是如何构成的?装配尺寸链封闭环是如何确定的?它与工艺尺寸链的封闭环有何区别? (在机器的装配关系中),装配尺寸链由相关零件的尺寸或相互位置关系构成。 装配尺寸链的封闭环就是装配所要保证的装配精度或技术要求。装配精度(封闭环)是 零部件装配后才最后形成的尺寸或位置关系。 装配尺寸链——全部组成环为不同零件设计尺寸所形成的尺寸链。工艺尺寸链——全部组成环为同一零件工艺尺寸所形成的尺寸链。工艺尺寸指工艺尺寸,定位尺寸与基准尺寸等。 5-5 在查找装配尺寸链时应注意哪些原则? (1)装配尺寸链应进行必要的简化机械产品的结构通常都比较复杂,对装配精度有影响的因素很多,在查找尺寸链时,在保证装配精度的前提下,可以不考虑那些影响较小的因素,使装配尺寸链适当简化。 (2)装配尺寸链组成的“一件一环”由尺寸链的基本理论可知,在装配精度既定的条件, 组成环数越少,则各组成环所分配到的公差值就越大,零件加工越容易、越经济。这样,在产品结构设计时,在满足产品工作性能的条件下,应尽量简化产品结构,使影响产品装配精度的零件数尽量减少。 在查找装配尺寸链时,每个相关的零、部件只应有一个尺寸作为组成环列人装配尺寸链,即将连接两个装配基准面间的位置尺寸直接标注在零件图上。这样,组成环的数目就等于有关零、部件的数目,即“一件一环”,这就是装配尺寸链的最短路线(环数最少)原则。 (3))装配尺寸链的“方向性”在同一装配结构中,在不同位置方向都有装配精度的要求时,应按不同方向分别建立装配尺寸链。 5-6 保证装配精度的方法有哪几种?各适用于什么装配场合? 保证产品装配精度的方法有:互换法、选择法、修配法和调整法。 互换装配法是在装配过程中,零件互换后仍能达到装配精度要求的装配方法。产品采用互换装配法时,装配精度主要取决于零件的加工精度,装配时不经任何调整和修配,就可以达到装配精度。 根据零件的互换程度不同,互换法又可分为完全互换法和大数互换法。 完全互换法常用于高精度的少环尺寸链或低精度多环尺寸链的大批大量生产装配中。 大数互换法适用于大批大量生产,组成环较多、装配精度要求又较高的场合。 选择装配法是将尺寸链中组成环的公差放大到经济可行的程度,然后选择合适的零件进行装配,以保证装配精度的要求。 选择装配法装配方法常应用于装配精度要求高而组成环数又较少的成批或大批量生产中。 选择装配法有三种不同的形式:直接选配法、分组装配法和复合选配法。 直接选配法不宜用于生产节拍要求较严的大批大量流水作业中。 分组装配法应用于在大批大量生产中对于组成环数少而装配精度要求又高的部件。 复合选配法应用于配合件公差可以不等,装配速度较快、质量高、有一定生产 节拍的要求的场合。如发动机气缸与活塞的装配多采用此种方法。 在成批生产或单件小批生产中,当装配精度要求较高,组成环数目又较多时,若按互换法装配,对组成环的公差要求过严,从而造成加工困难。而采用分组装配法又因生产零件数 量少,种类多而难以分组。这时,常采用修配装配法来保证装配精度的要求。 修配法是将尺寸链中各组成环按经济加工精度制造。装配时,通过改变尺寸链中某一预 机械制造工艺学部分习题解答1 第一章绪论(第3版P21-24) 1-6什么是机械加工工艺过程?什么是机械加工工艺系统? 答:机械加工工艺过程是机械产品生产的过程的一部分,是直接生产过程,其原意是指采取金属 切削刀具来加工工件或磨具来加工工件,使之达到所要求的形状、尺寸、表面粗糙度和力学物理性能, 成为合格零件的生产过程。 机械加工工艺系统是零件进行机械加工时,必须具备一定的条件,即要有一个系统来支持。通常, 一个系统是由物质分系统、能量分系统和信息分系统所组成。 1-7什么是工序、安装、工位、工步和走刀? 1.工序:一个(或一组)工人在一个工作地点对一个(或同时对几个)工件连续完成的那一部分工艺 过程。 2.安装:如果在一个工序中需要对工件进行几次装夹,则每次装夹下完成的那部分工序内容称为一 个安装。 3.工位:在工件的一次安装中,通过分度(或移位)装置,使工件相对于机床床身变换加工置,则把 每一个加工位置上的安装内容称为工位。 4.工步:加工表面、切削刀具、切削速度和进给量都不变的情况下所完成的工位内容,称为一个工步。 5.走刀:切削刀具在加工表面上切削一次所完成的工步内容,称为一次走刀。 1-8某机床厂年产CA6140车床2000台,已知机床主轴的备品率为14%,机械加工废品率为4%,试计算机床主轴的年生产纲领。从生产纲领来分析,试说明属于何种生产类型?工艺过程有何特点? 若1年工作日为250天,试计算每月(按21天计算)的生产批量。 答:(1)机床主轴的年生产纲领 N=Qn(1+α%+θ%)=2000×1×(1+14%+4%)=2360件/年 机床主轴属于中型机械,查表1-5(教材P12)属于大批生产的生产类型。 (2)工艺过程特点(根据表1-6(P12)) a)采用模锻制造毛坯,毛坯精度高,加工余量小;b)采用专用机械加工设备流水线生产;c)采用专用工装夹具;d)采用详细的工艺规程,用工序卡、操作卡及调整卡管理生产。 (3)生产批量 件 1-9试述工件装夹的含义。在机械加工中有哪几类装夹方式?简述每种装夹方法的特点及其应用场合。 答:工件装夹的含义是定位和夹紧,也称为安装。在机械加工中有三类装夹方式。 (1)夹具中装夹:该方法由夹具保证定位和夹紧,易于保证加工精度,操作简单方便,效率高, 机械制造工艺学第三版王先逵第五章习题 解答 机械制造工艺学习题解答 第五章:机械加工表面质量及其控制(第3版P267) 5-1机械加工表面质量包括哪些具体内容? 答:(P229)机械加工表面质量,其含义包括两个方面的内容:A.加工表面层的几何形貌,主要由以下几部分组成:⑴表面粗糙度;⑵波纹度;⑶纹理方向;⑷表面缺陷。 B.表面层材料的力学物理性能和化学性能,主要反映在以下三个方面:⑴表面层金属冷作硬化;⑵表面层金属的金相组织变化;⑶表面层金属的残余应力。 5-2为什么机器零件一般总是从表面层开始破坏的?加工表面质量对机器使用性能有哪些影响? 答:(P231)(1)由于表面是零件材料的边界,常常承受工作负荷所引起的最大应力和外界介质的侵蚀,表面上有着引起应力集中而导致破坏的微小缺陷,所以这些表面直接与机器零件的使用性能有关。 (2)加工表面质量对机器的耐磨性、耐疲劳性、耐蚀性、零件配合质量都有影响。 5-3车削一铸铁零件的外圆表面,若进给量f=0.40mm/r,车刀刀尖圆弧半径re=3mm,试估算车削后的表面粗糙度。 5-6为什么提高砂轮速度能减小磨削表面的粗糙度数值,而提高工件速度却得到相反的结果? 答:(P224)砂轮速度越高,单位时间内通过被磨表面的磨粒数就越多,工件材料来不及变形,因而工件表面粗糙度值越小。而工件速度增大,单位时间内通过被磨表面的磨粒数减少,塑性变形增加,表面粗糙度值将增大。 5-7为什么在切削加工中一般都会产生冷作硬化现象? 答:(P240)机械加工过程中产生的塑性变形,使晶格扭曲、畸变,晶粒间产生滑移,晶粒被拉长,进一步变形受到阻碍,这些都会使表面层金属的硬度增加,统称为冷作硬化(或称为强化)。 5-8为什么切削速度越大,硬化现象越小?而进给量增大,硬化现象增大? 答:(P240-241)增大切削速度,(1)刀具与工件的作用时间减少,使塑性变形的扩展深度减小,因而冷硬层深度减小;(2)温度增高,弱化倾向增大,冷硬程度降低。而进给量增大时,硬化现象增大的原因是随着进给量的增大,切削力也增大,表层金属的塑性变形加剧,冷硬程度增大。但是,这种情况只是在进给量比较大时才是正确的。 5-11什么是回火烧伤、淬火烧伤和退火烧伤? 答:(P243)磨削淬火钢时,在工件表面形成的瞬时高温将使表层金属产生以下三种金相组织变化:1)如果磨削区的温度未超过淬火钢的相变温度(碳钢的相变温度为720℃,但已超过马氏体的转变温度(中碳钢为300℃,工件表面金属的马氏体将转化为硬度较低的回火组织(索氏体或托氏体),这称为回火烧伤。 2)如果磨削区温度超过了相变温度,再加上冷却液的急冷作用,表层金属会出现二次淬 机械制造工艺学复习题及参考答案 第一章 1.1什么叫生产过程、工艺过程、工艺规程? 答案: 生产过程是指从原材料变为成品的劳动过程的总和。 在生产过程中凡属直接改变生产对象的形状、尺寸、性能及相对位置关系的过程,称为工 艺过程。 在具体生产条件下,将最合理的或较合理的工艺过程,用文字按规定的表格形式写成的工艺文件,称为机械加工工艺规程,简称工艺规程。 1.3结合具体实例,说明什么是基准、设计基准、工艺基准、工序基准、定位基准、测量基准、装配基准。 答案: 基准是指用以确定生产对象几何要素间的几何关系所依据的点、线、面。 设计基准是指在零件图上标注设计尺寸所采用的基准。 工艺基准是指在零件的工艺过程中所采用的基准。 在工序图中,用以确定本工序被加工表面加工后的尺寸、形状、位置所采用的基准,称为 工序基准。 在加工时,用以确定工件在机床上或夹具中正确位置所采用的基准,称为定位基准。 在加工中或加工后,用以测量工件形状、位置和尺寸误差所采用的基准,称为测量基准。 在装配时,用以确定零件或部件在产品上相对位置所采用的基准,称为装配基准。 1.6什么是六点定位原理?什么是完全定位与不完全定位?什么是欠定位与过定位?各举例说明。 答案: 六点定位原理:在夹具中采用合理布置的6个定位支承点与工件的定位基准相接触,来限制工件的6个自由度,就称为六点定位原理。 完全定位:工件的6个自由度全部被限制而在夹具中占有完全确定的唯一位置,称为完全 定位。 不完全定位:没有全部限制工件的6个自由度,但也能满足加工要求的定位,称为不完全 定位。 欠定位:根据加工要求,工件必须限制的自由度没有达到全部限制的定位,称为欠定位。 过定位:工件在夹具中定位时,若几个定位支承重复限制同一个或几个自由度,称为过定位。 (举例在课本page12、13)。 1.10何谓零件、套件、组件和部件?何谓套装、组装、部装、总装和装配? 答案: 零件是组成机器的最小单元,它是由整块金属或其它材料构成的。 机械制造工艺学习题解答第五章:机械加工表面质量及其控制(第3版P267) 5-1机械加工表面质量包括哪些具体内容? 答:(P229)机械加工表面质量,其含义包括两个方面的内容: A.加工表面层的几何形貌,主要由以下几部分组成:⑴表面粗糙度;⑵波纹度;⑶纹理方向;⑷表面缺陷。 B.表面层材料的力学物理性能和化学性能,主要反映在以下三个方面:⑴表面层金属冷作硬化;⑵表面层金属的金相组织变化;⑶表面层金属的残余应力。 5-2为什么机器零件一般总是从表面层开始破坏的?加工表面质量对机器使用性能有哪些影响? 答:(P231)(1)由于表面是零件材料的边界,常常承受工作负荷所引起的最大应力和外界介质的侵蚀,表面上有着引起应力集中而导致破坏的微小缺陷,所以这些表面直接与机器零件的使用性能有关。 (2)加工表面质量对机器的耐磨性、耐疲劳性、耐蚀性、零件配合质量都有影响。 5-3车削一铸铁零件的外圆表面,若进给量f=r,车刀刀尖圆弧半径 re=3mm,试估算车削后的表面粗糙度。 5-6为什么提高砂轮速度能减小磨削表面的粗糙度数值,而提高工件速度却得到相反的结果? 答:(P224)砂轮速度越高,单位时间内通过被磨表面的磨粒数就越多,工件材料来不及变形,因而工件表面粗糙度值越小。而工件速度增大,单位时间内通过被磨表面的磨粒数减少,塑性变形增加,表面粗糙度值将增大。 5-7为什么在切削加工中一般都会产生冷作硬化现象? 答:(P240)机械加工过程中产生的塑性变形,使晶格扭曲、畸变,晶粒间产生滑移,晶粒被拉长,进一步变形受到阻碍,这些都会使表面层金属的硬度增加,统称为冷作硬化(或称为强化)。 5-8为什么切削速度越大,硬化现象越小?而进给量增大,硬化现象增大? 答:(P240-241)增大切削速度,(1)刀具与工件的作用时间减少,使塑性变形的扩展深度减小,因而冷硬层深度减小;(2)温度增高,弱化倾向增大,冷硬程度降低。而进给量增大时,硬化现象增大的原因是随着进给量的增大,切削力也增大,表层金属的塑性变形加剧,冷硬程度增大。但是,这种情况只是在进给量比较大时才是正确的。 5-11什么是回火烧伤、淬火烧伤和退火烧伤? 答:(P243)磨削淬火钢时,在工件表面形成的瞬时高温将使表层金属产生以下三种金相组织变化:1)如果磨削区的温度未超过淬火钢的相变温度(碳钢的相变温度为720℃,但已超过马氏体的转变温度(中碳钢为300℃,工件表面金属的马氏体将转化为硬度较低的回火组织(索氏体或托氏体),这称为回火烧伤。2)如果磨削区温度超过了相变温度,再加上冷却液的急冷作用,表层金属会出现二次淬火马氏体织织,硬度比原来的回火马氏 机械制造工艺学第三版第五章答案 : 篇一:机械制造工艺学第三版王先逵第五章习题解答 机械制造工艺学习题解答 第五章:机械加工表面质量及其控制(第3版P267) 5-1机械加工表面质量包括哪些具体内容? 答:(P229)机械加工表面质量,其含义包括两个方面的内容: A.加工表面层的几何形貌,主要由以下几部分组成:⑴表面粗糙度; ⑵波纹度;⑶纹理方向;⑷表面缺陷。 B.表面层材料的力学物理性能和化学性能,主要反映在以下三个方面:⑴表面层金属冷作硬化;⑵表面层金属的金相组织变化;⑶表面层金属的残余应力。 5-2为什么机器零件一般总是从表面层开始破坏的?加工表面质量对机器使用性能有哪些影响? 答:(P231)(1)由于表面是零件材料的边界,常常承受工作负荷所引起的最大应力和外界介质的侵蚀,表面上有着引起应力集中而导致破坏的微小缺陷,所以这些表面直接与机器零件的使用性能有关。 (2)加工表面质量对机器的耐磨性、耐疲劳性、耐蚀性、零件配合质量都有影响。 5-3车削一铸铁零件的外圆表面,若进给量f=0.40mm/r,车刀刀尖圆弧半径re=3mm,试估算车削后的表面粗糙度。 5-6为什么提高砂轮速度能减小磨削表面的粗糙度数值,而提高工件速度却得到相反的结果? 答:(P224)砂轮速度越高,单位时间内通过被磨表面的磨粒数就越 多,工件材料来不及变形,因而工件表面粗糙度值越小。而工件速度增大,单位时间内通过被磨表面的磨粒数减少,塑性变形增加,表面粗糙度值将增大。 5-7为什么在切削加工中一般都会产生冷作硬化现象? 答:(P240)机械加工过程中产生的塑性变形,使晶格扭曲、畸变,晶粒间产生滑移,晶粒被拉长,进一步变形受到阻碍,这些都会使表面层金属的硬度增加,统称为冷作硬化(或称为强化)。 5-8为什么切削速度越大,硬化现象越小?而进给量增大,硬化现象增大? 答:(P240-241)增大切削速度,(1)刀具与工件的作用时间减少,使塑性变形的扩展深度减小,因而冷硬层深度减小;(2)温度增高,弱化倾向增大,冷硬程度降低。而进给量增大时,硬化现象增大的原因是随着进给量的增大,切削力也增大,表层金属的塑性变形加剧,冷硬程度增大。但是,这种情况只是在进给量比较大时才是正确的。 5-11什么是回火烧伤、淬火烧伤和退火烧伤? 答:(P243)磨削淬火钢时,在工件表面形成的瞬时高温将使表层金属产生以下三种金相组织变化:1)如果磨削区的温度未超过淬火钢的相变温度(碳钢的相变温度为720℃,但已超过马氏体的转变温度(中碳钢为300℃,工件表面金属的马氏体将转化为硬度较低的回火组织(索氏体或托氏体),这称为回火烧伤。 2)如果磨削区温度超过了相变温度,再加上冷却液的急冷作用,表层金属会出现二次淬火马氏体织织,硬度比原来的回火马氏体高;在它的下层,因冷却较慢,出现了硬度比原来的回火马氏体低的回火组织(索氏体或托氏体),这称为淬火烧伤。 3)如果磨削区温度超过了相变温度,而磨削过程又没有冷却液,组织,表层金属的硬度将急剧下降,这称为退火烧伤。 5-12为什么磨削容易产生烧伤?如果工件材料和磨削用量无法改 机械制造工艺学第三版王先逵第 五章习题解答 机械制造工艺学习题解答 第五章:机械加工表面质量及其控制(第3版P267) 5-1机械加工表面质量包括哪些具体内容? 答:(P229)机械加工表面质量,其含义包括两个方面的内容: A.加工表面层的几何形貌,主要由以下几部分组成:⑴表面粗糙度; ⑵波纹度;⑶纹理方向;⑷表面缺陷。 B.表面层材料的力学物理性能和化学性能,主要反映在以下三个方面:⑴表面层金属冷作硬化;⑵表面层金属的金相组织变化;⑶表面层金属的残余应力。 5-2为什么机器零件一般总是从表面层开始破坏的?加工表面质量对机器使用性能有哪些影响? 答: ( P231) (1)由于表面是零件材料的边界,常常承受工作负荷所引起的最大应力和外界介质的侵蚀,表面上有着引起应力集中而导致破坏的微小缺陷,所以这些表面直接与机器零件的使用性能有关。 (2)加工表面质量对机器的耐磨性、耐疲劳性、耐蚀性、零件配合质量都有影响。 5-3车削一铸铁零件的外圆表面,若进给量f=0.40mm/r ,车刀刀尖圆弧半径re=3mm试估算车削后的表面粗糙度。 5-4高速精镯呆谓工件的内孔时,采用主値角K ,=75%副偏角输一1即前锋利尖刀,当加工表面粗糙度 要求R 尸3」—.3 Um.时.问: ⑴衽不考虑工祥材料塑性变形对表而粗糙度影哨的杀件下「进骼量f 应选择多大了 (2)分析室际加工表面粗糙度与计算值是否相同,为什么? ⑶ 进给量f 越小’表面祖糙度值是胥越小? 备 ⑴根据教材P2阳公式,H = -------- ---- 可以导出:/ = H(cctK r +cotKj cot + COtk r 耽 H=23.2nm.则 匸0,QQ32 (1 tan75+l.tanl53 =0,013mm (2)分析实际加工表面粗粒度与计算渲不同'其頰因是材料有塑性变形,还有弹性恢复锌匚 ⑶在主谍甬因健角前定的皤况下,建给量子越丿卜表面粗穗愛值就越小, 5-6为什么提高砂轮速度能减小磨削表面的粗糙度数值, 而提高工件 速度却得到相反的结果? 答:(P224)砂轮速度越高,单位时间内通过被磨表面的磨粒数就越 多,工件材料来不及变形,因而工件表面粗糙度值越小。而工件速度 增大,单位时间内通过被磨表面的磨粒数减少, 塑性变形增加,表面 粗糙度值将增大。 5-7为什么在切削加工中一般都会产生冷作硬化现象? 答:(P240)机械加工过程中产生的塑性变形,使晶格扭曲、畸变, 晶粒间产生滑移,晶粒被拉长,进一步变形受到阻碍,这些都会使表 面层金属的硬度增加,统称为冷作硬化(或称为强化)。 0.00667mm =听&jjm H 0.4: 机械制造工艺学习题解答 第五章:机械加工表面质量及其控制(第3版P267) 5-1机械加工表面质量包括哪些具体内容? 答:(P229)机械加工表面质量,其含义包括两个方面的内容: A.加工表面层的几何形貌,主要由以下几部分组成:⑴表面粗糙度;⑵波纹度;⑶纹理方向;⑷表面缺陷。 B.表面层材料的力学物理性能与化学性能,主要反映在以下三个方面: ⑴表面层金属冷作硬化;⑵表面层金属的金相组织变化;⑶表面层金属的残余应力。 5-2为什么机器零件一般总就是从表面层开始破坏的?加工表面质量对机器使用性能有哪些影响? 答:(P231)(1)由于表面就是零件材料的边界,常常承受工作负荷所引起的最大应力与外界介质的侵蚀,表面上有着引起应力集中而导致破坏的微小缺陷,所以这些表面直接与机器零件的使用性能有关。 (2)加工表面质量对机器的耐磨性、耐疲劳性、耐蚀性、零件配合质量都有影响。 5-3车削一铸铁零件的外圆表面,若进给量f=0、40mm/r,车刀刀尖圆弧半径re=3mm,试估算车削后的表面粗糙度。 5-6为什么提高砂轮速度能减小磨削表面的粗糙度数值,而提高工件速度却得到相反的结果? 答:(P224)砂轮速度越高,单位时间内通过被磨表面的磨粒数就越多,工件材料来不及变形,因而工件表面粗糙度值越小。而工件速度增大,单位时间内通过被磨表面的磨粒数减少,塑性变形增加,表面粗糙度值将增大。 5-7为什么在切削加工中一般都会产生冷作硬化现象? 答:(P240)机械加工过程中产生的塑性变形,使晶格扭曲、畸变,晶粒间产生滑移,晶粒被拉长,进一步变形受到阻碍,这些都会使表面层金属的硬度增加,统称为冷作硬化(或称为强化)。 5-8为什么切削速度越大,硬化现象越小?而进给量增大,硬化现象增大? 答:(P240-241)增大切削速度,(1)刀具与工件的作用时间减少,使塑性变形的扩展深度减小,因而冷硬层深度减小;(2)温度增高,弱化倾向增大,冷硬程度降低。而进给量增大时,硬化现象增大的原因就是随着进给 机械制造工艺学》习题参考答案 常同立、杨家武、佟志忠编着清华大学出版社 第一章机械制造工艺预备 1-1 参考答案要点:现代机械产品的开发与改进是极其复杂的持续的动态过程,大致可以用图 1.1描述。机械产品开发与改进系统可以描述为一个负反馈系统,它描述了机械产品依据用户需求反馈信息,不断改进和不断发展的动态过程。 机械产品开发与改进系统中包含产品决策、产品设计、工艺编制、产品制造、市场检验等环节。上述环节之中任何一个环节的断裂,都会导致系统的崩溃。因此上述环节都具有与系统同等的重要性,每个组成环节都具有无可替代的重要性。因此学习机械制造工艺学很重要,很有意义。 图1.1 机械产品开发与改进系统 1- 2 参考答案要点:按照专业教学指导委员会制定大纲,机械制造工艺学研究内容主要包含两个部分,即机械加工工艺学和机器装配工艺学。它们分别以机械加工工艺过程和机器的装配工艺过程为研究对象。其中机械加工工艺过程指冷加工工艺过程。机械制造的工艺过程特指零件的机械加工工艺过程和机器的装配工艺过程。 此外,机械制造工艺学还包括非常规加工方法概述,随着技术发展进步,非常规制造方法越来越多在工程实际中获得应有,并取得效果。 1- 3 参考答案要点:生产过程是指机械产品从原材料开始到成品之间各相互关联的劳动过程的总和。工艺过程是指在生产过程中,通过改变生产对象的形状、相互位置和性质等,使其成为成品或半成品的过程。 工艺规程参看第二章机械制造工艺规程。工艺规程在生产中的作用参看第二章机械制造工艺规程作用。 1- 4 参考答案要点:人们按照产品的生产纲单件或小批量生中批量生产大批或大量生产 领、投入生产的批量,可将生产分为:单产 件生产、批量生产和大量生产三种类型。 各种生产类型的工艺特征如下表:工艺 特点 毛坯的制造方法铸件用木模手工部分铸件用金属铸件广泛用金属 造型;锻件用自模造型;部分锻模机器造型,锻 由锻件用模锻件广泛用模锻 机械制造工艺学》习题参考答案 常同立、杨家武、佟志忠编着清华大学出版社 第二章机械加工工艺规程制定 2-1 参考答案要点:机械工艺规程在指导生产上发挥重要作用,主要体现在如下几个方面: 1)工艺规程是指导生产的主要技术文件; 2)工艺规程是生产组织和管理工作的基本依据; 3)工艺规程是新、扩建工厂或车间的基本资料。 机械加工工艺规程应遵循如下原则: 1)机械加工工艺规程制定应保证零件设计图样上所有技术要求能够实现; 机械制造工艺学第三版王先逵第五章习题解答 WTD standardization office【WTD 5AB- WTDK 08- WTD 2C】 机械制造工艺学习题解答第五章:机械加工表面质量及其控制(第3版P267) 5-1机械加工表面质量包括哪些具体内容? 答:(P229)机械加工表面质量,其含义包括两个方面的内容: A.加工表面层的几何形貌,主要由以下几部分组成:⑴表面粗糙度;⑵波纹度;⑶纹理方向;⑷表面缺陷。 B.表面层材料的力学物理性能和化学性能,主要反映在以下三个方面:⑴表面层金属冷作硬化;⑵表面层金属的金相组织变化;⑶表面层金属的残余应力。 5-2为什么机器零件一般总是从表面层开始破坏的?加工表面质量对机器使用性能有哪些影响? 答:(P231)(1)由于表面是零件材料的边界,常常承受工作负荷所引起的最大应力和外界介质的侵蚀,表面上有着引起应力集中而导致破坏的微小缺陷,所以这些表面直接与机器零件的使用性能有关。 (2)加工表面质量对机器的耐磨性、耐疲劳性、耐蚀性、零件配合质量都有影响。 5-3车削一铸铁零件的外圆表面,若进给量f=r,车刀刀尖圆弧半径 re=3mm,试估算车削后的表面粗糙度。 5-6为什么提高砂轮速度能减小磨削表面的粗糙度数值,而提高工件速度却得到相反的结果? 答:(P224)砂轮速度越高,单位时间内通过被磨表面的磨粒数就越多,工件材料来不及变形,因而工件表面粗糙度值越小。而工件速度增大,单位时间内通过被磨表面的磨粒数减少,塑性变形增加,表面粗糙度值将增大。 5-7为什么在切削加工中一般都会产生冷作硬化现象? 答:(P240)机械加工过程中产生的塑性变形,使晶格扭曲、畸变,晶粒间产生滑移,晶粒被拉长,进一步变形受到阻碍,这些都会使表面层金属的硬度增加,统称为冷作硬化(或称为强化)。 5-8为什么切削速度越大,硬化现象越小?而进给量增大,硬化现象增大? 答:(P240-241)增大切削速度,(1)刀具与工件的作用时间减少,使塑性变形的扩展深度减小,因而冷硬层深度减小;(2)温度增高,弱化倾向增大,冷硬程度降低。而进给量增大时,硬化现象增大的原因是随着进给量的增大,切削力也增大,表层金属的塑性变形加剧,冷硬程度增大。但是,这种情况只是在进给量比较大时才是正确的。 5-11什么是回火烧伤、淬火烧伤和退火烧伤? 答:(P243)磨削淬火钢时,在工件表面形成的瞬时高温将使表层金属产生以下三种金相组织变化:1)如果磨削区的温度未超过淬火钢的相变温度(碳钢的相变温度为720℃,但已超过马氏体的转变温度(中碳钢为300℃,工件表面金属的马氏体将转化为硬度较低的回火组织(索氏体或托氏体),这称为回火烧伤。 2)如果磨削区温度超过了相变温度,再加上冷却液的急冷作用,表层金属会出现二次淬火马氏体织织,硬度比原来的回火马氏体 机械制造工艺学复习提纲 第一章绪论 1.何谓生产过程,工艺过程,工艺系统; 生产过程:从原材料变成成品的劳动过程的总和。 工艺过程:在生产过程中,直接改变生产对象的形状、尺寸、性能及相对位置关系的过程。 工艺系统:由工件、机床、工具、夹具组成 2.何谓工序,安装,工步,走刀; 工序:一个(或一组)工人在一个工作地点对一个(或同时对JL个)工件连续完成的那一部分工艺过程。 安装:如果在一个工序中需要对工件进行几次装夹,则每次装夹下完成的那部分工序内容称为一个安装。 工步:加工表面、切削刀具、切削速度和进给量都不变的情况下所完成的工位内容,称为一个工步。 走刀:切削刀具在加工表面上切削一次所完成的工步内容,称为一次走刀 3.工件在机床或夹具中的装夹主要有哪三种方式? 直接找正装夹、划线找正装夹、夹具装夹 4.何谓六点定位原理?何谓完全定位,不完全定位,欠定位,过定位? 六点定位原理:在夹具中采用合理布置的6个定位支承点与工件的定位基准相接触,来限制工件的6个自由度. 完全定位:工件的6个自由度全部被限制而在夹具中占有完全确定的唯一位置. 不完全定位:没有全部限制工件的6个自由度,但也能满足加工要求的定位. 欠定位:根据加工要求,工件必须限制的自由度没有达到全部限制的定位. 过定位:工件在夹具中定位时,若几个定位支承重复限制同一个或几个自由度. 5.基准分类? 设计基准、工艺基准:工序,测量,装配,定位:(原有,附加):(粗基准,精基准 6.作业:1-11;1-12; P24 第二章机械加工工艺规程设计 1.零件结构工艺性分析举例:表2-3;P28 2.何谓定位基准,粗基准,精基准? 定位基准:在加工时,用以确定工件在机床上或夹具中正确位置所采用的基准。 粗基准:工件在机械加工中第一道工序用未加工的毛坯表面做定位基准 精基准:用工件的已加工表面做定位基准 3.粗基准的选择原则?精基准选择原则? 粗基准的选择原则:保证相互位置要求、保证加工面加工余量合理分配、便于工件装夹、一般不得重复使用。 精基准选择原则:基准重合原则、统一基准原则、互为基准原则、自为基准原则、便于装夹原则。4.何谓加工经济精度?机械制造工艺学(王先逵)第一章参考答案(部分)
机械制造工艺学(王先逵)第五章参考答案(部分)
第三版机械制造工艺学第一章习题解答
机械制造工艺学第三版王先逵第五章习题解答说课材料
机械制造工艺学课后习题与参考答案
机械制造工艺学第三版王先逵第五章习题解答
【最新试题库含答案】机械制造工艺学第三版第五章答案
机械制造工艺学第三版王先逵第五章习题解答
机械制造工艺学第三版王先逵第五章习题解答
机械制造工艺学清华大学出版社课后习题答案
机械制造工艺学第三版王先逵第五章习题解答
机械制造工艺学复习提纲及答案