数控机床毕业设计说明书

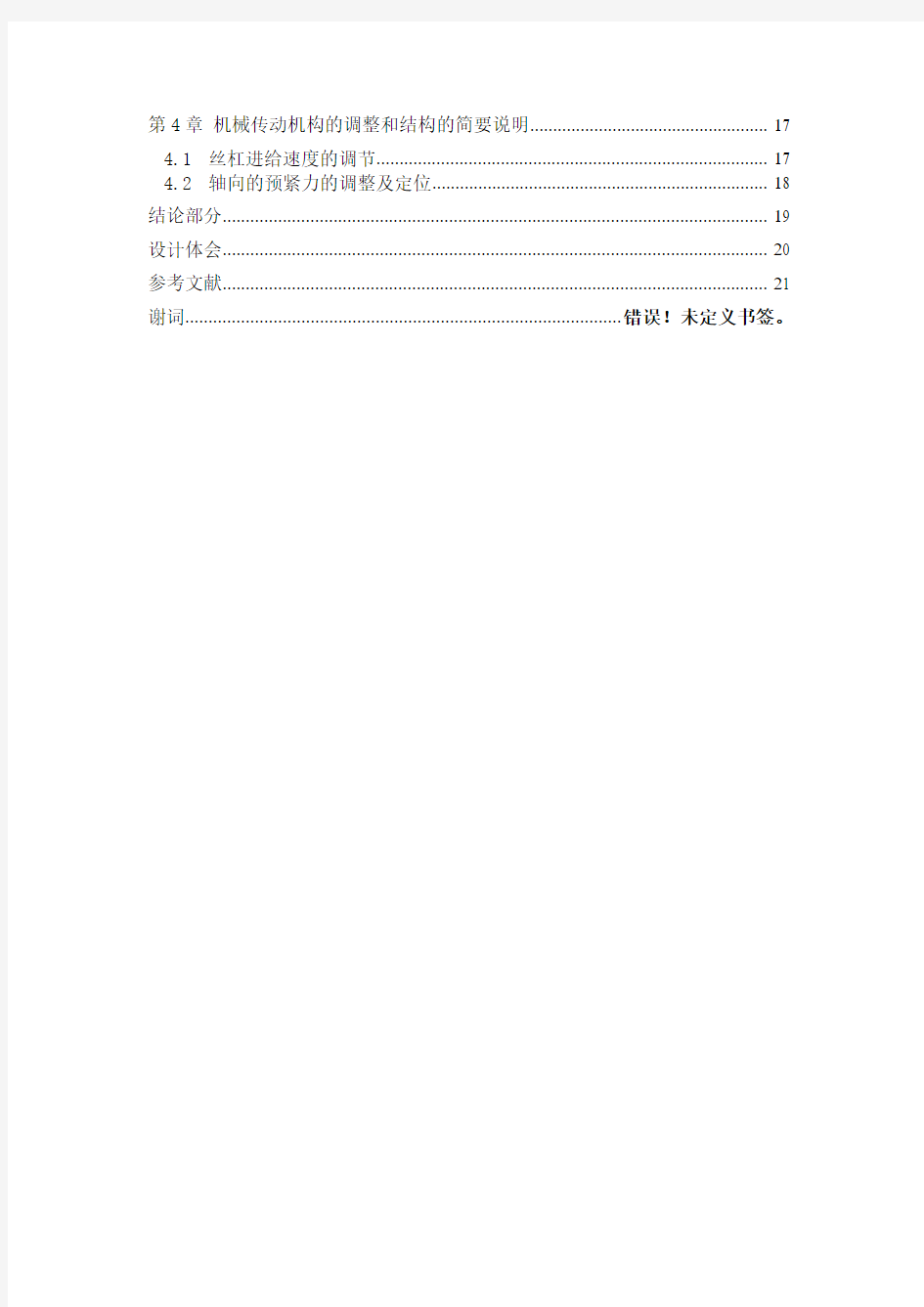
目录
摘要 (3)
ABSTRACT (3)
前言部分 (5)
第1章绪论 (6)
1.1机床总体方案的设计 (6)
1.1.1 课程设计任务书 (6)
1.1.2 总体方案设计 (6)
1.2开环伺服进给系统机械部分设计 (6)
1.2.1 滚珠丝杠螺母副的计算选型 (6)
1.2.2 步进电动机的计算和选型 (6)
第2章机床机电一体化改造总体方案的设计 (7)
2.1课程设计任务书 (7)
2.1.1 题目 (7)
2.1.2 原始数据: (7)
2.1.3 主要技术参数: (7)
2.1.4 课程设计的内容及要求: (7)
2.2总体方案设计 (7)
2.2.1 系统的运动方式的确定 (7)
2.2.2 伺服系统的选择 (7)
2.2.3 执行机构传动方式的确定 (7)
2.2.4 数控系统的选择 (8)
第3章开环伺服进给系统机械部分设计 (8)
3.2计算切削力 (8)
3.3滚珠丝杠螺母副的计算选型( (9)
3.3.1 计算进给牵引力 (9)
3.3.2 计算最大动负载 (9)
3.3.3 滚珠丝杠螺母副的选型 (10)
3.3.4 传动效率计算 (10)
3.3.5 刚度计算 (10)
3.3.6 稳定性校核 (12)
3.3.7纵向滚珠丝杠副的几何参数 (12)
3.4齿轮传动比计算 (12)
3.5步进电动机的计算和选型 (13)
3.5.1 等效转动惯量计算 (13)
3.5.2 电机力矩计算 (14)
3.5.3 计算步进电动机空载起动频率和切削时的工作频率 (16)
第4章机械传动机构的调整和结构的简要说明 (17)
4.1丝杠进给速度的调节 (17)
4.2轴向的预紧力的调整及定位 (18)
结论部分 (19)
设计体会 (20)
参考文献 (21)
谢词..............................................................................................错误!未定义书签。
摘要
本设计是把普通数控的改造经济型数控机床,经济型数控机床就是指价格低廉、操作使用方便、比较适合我国国情的,动化的机床。:分析和总结了现有数控维修教学和实训中存在的主要问题,针对存在的问题,简单介绍了虚拟数控机床的功能,着重阐述了虚拟数控机床在数控维修教学不同模块中的使用。是使用数控机床可以降低工人劳动强度,节省劳动力(一个人可看管多台机床),减少工装,缩短新产品试制周期和生产周期,可对市场需求做出快速反应,在设计时候具体进行了详细的各种部件的选型和计算。机床计算机数据控的基本原理,数控机床的组成、分类及发展,CNC装置的硬件、软件及其接口,插补原理、刀具补偿与速度控制,伺服驱动系统及位置控制,加工程序编制等。比如:导轨设计选型、滚珠丝杠副选型与计算,进行传动系统误差分析、驱动电机的选型与计算、驱动电机与滚珠丝杆的联接,驱动电机与进给传动系统的动态特性分析等。
关键词:车床数控传动系统数控维修虚拟数控机床教学
Abstract
This design is the common lathe with economical CNC machine tool, economic type CNC machine tools is low price, convenient operation and use, is suitable for the national conditions of our country, the move of the machine tool. The use of CNC machine tool can reduce the labor intensity of workers, labor saving ( a person can control more than one machine), reduce tooling, shorten new product development cycle and the production cycle, the rapid response to market demand, in the design of specific detail when the various parts of the design and calculation of. Machine computer data control principle, the composition of CNC machine tools, classification and development, CNC hardware, software and interface, interpolation theory, compensation of cutting tools and speed control, servo drive system and position control, processing procedures for the preparation and. For example: guide design, selection and calculation of ball screw transmission system, error analysis, selection and calculation of driving motor, driving motor and ball screw coupling, the drive motor and the feed drive system dynamic characteristics analysis.
Key words: lathe numerical control drive system
前言部分
计算机技术和先进制造技术的发展,推动了机械加工在各方面的变革和进步。典型的数控机床已成为现代加工器械的鲜明代表。考虑到企业的生产效率和投入成本,普通车床的数控化改造将是一个极为有意义的课题。
数控车床改造的设计是机电一体化系统课程设计的主要内容。作为机械设计制造及其自动化专业的学生,这次设计是本人在学习完“机电一体化系统设计”、“数控机床”等专业课程之后进行的一个重要的实践性教学环节。通过综合运用所学的机械、电子、自动控制、微机等知识,进行一次机电结合的全面训练,以培养独立分析问题,解决问题和进行机电一体化系统初步设计的能力。此设计过程为期三个星期,在赵洪兵的指导下,本人将对普通车床进行开环控制纵向进给的改造。
动轨迹信息记录在程序介质上,然后送人数控系统经过译码和运算,控制机床刀具与工件的相对运动,加工出所需工件的一类机床即为数控机床。数控加工的基本过程。数控机床是用数字信息进行控制的机床。凡是用代码化的数字信息将刀具移
在数控机床加工工件前,要分析零件图,拟定零件加工工艺方案,明确加工工艺参数,然后按编程规则编制数控加工程序。当加工零件的几何信息和工艺信息转换为数字化信息后,可以用不同方法输入到机床的数控系统中,经检查无误即可启动机床,运行数控加工程序数控装置会自动完成数控加工程序发出的各种控制指令。如果不出现故障,直到加工程序运行结束,零件加工完毕为止。数控加工的控制过程与计算机控制打印机的打印过程,特别是与计算机控制绘图机的绘图.
由于学生水平有限,在设计乃至计算过程中难免会有一些错误,望各位老师及同学指点赐教。不胜感激。
第1章绪论
1.1 机床总体方案的设计
1.1.1 课程设计任务书
(1)题目《φ400mm的数控车床总体设计及纵向进给设计》(2)原始数据
(3)主要技术参数
(4)课程设计的内容及要求
1.1.2 总体方案设计
(1)系统的运动方式的确定
(2)伺服系统的选择
(3)执行机构传动方式的确定
(4)数控系统的选择
1.2 开环伺服进给系统机械部分设计
1.2.1 滚珠丝杠螺母副的计算选型(纵向进给丝杠)
(1)计算进给牵引力
m ()
F N
(2)计算最大动负载C
(3)滚珠丝杠螺母副的选型
(4)传动效率计算
(5)刚度计算
(6)稳定性校核
1.2.2 步进电动机的计算和选型
(1)等效转动惯量的计算
(2)电机力矩计算
(3)计算步进电动机空载起动频率和切削时的工作频率
第2章机床机电一体化改造总体方案的设计
2.1 课程设计任务书
2.1.1 题目:φ400mm车床总体设计及纵向进给设计
2.1.2 原始数据:
最大回转直径:400毫米在床身上D=400毫米在床鞍上 D=210 毫米
最大工件长度 900mm
主电动机功率 7.5千瓦;转速1450转/分
2.1.3 主要技术参数(均为纵向):
最大进给速度 1.0米/分
最大快移速度 4米/分
起动加速时间 30毫秒
移动部件重量 80公斤
机床定位精度 0.015毫米
2.1.4 课程设计的内容及要求:
能按时独立完成毕业设计规定的全部内容,方案选择正确,论据充分,对设计中的主要问题分析深入,解决合理,有独立见解,能很好运用所学理论和提供的资料解决设计中的问题,能独立查阅和正确引用中外文参考资料,说明书文字通顺、清楚、选用数据论证合理、计算准确,图面整洁。
2.2 总体方案设计
2.2.1 系统的运动方式的确定
由于改造后的经济型数控车床具有定位、直线插补、圆弧插补、暂停、循环加工、螺纹加工等功能,所以应该选用连续控制系统。
2.2.2 伺服系统的选择
应任务书的要求,采用步进电机开环控制系统。
2.2.3 执行机构传动方式的确定
为了保证一定的传动精度和平稳性,尽量减小摩擦力,选用滚珠丝杠螺母副。同时,若直接将电机与滚珠丝杠联必会引起丝杠温度过高即磨损加剧使其寿命降低。故在其两者之间加一消隙齿轮箱,一使丝杠速度降低,二则消除系统传动中的间隙,提高传动精度,并有效减少反向运动死区现象,消隙齿轮箱与丝杠可采用联轴器形式连接,这样便确定了如下图2-1所示的传动方案。
电机消隙齿轮箱滚珠丝杠螺母副工作台
2.2.4 数控系统的选择
根据机床要求,本着经济耐用的原则,确定采用8位机。MCS—51系列单片机主要有三种型号的产品:8031、8051和8751。由于MCS—51系列单片机的特点之一是硬件设计简单,系统结构紧凑,故对于简单的应用场合,MCS—51系统的最小系统用一片8031外扩一片EPROM就能满足开环控制的要求。8031单片机内含4kb EEPROM程序存储器,具有功耗低、抗干扰能力强的特点,数据存储器WM0016DRH是一种多功能非易失性SRAM,8031单片机高速高抗干扰自保持,不怕掉电,上下电百万次数据无丢失,断电保护10年有效,既可高速连续读写,也可任意地址单字节操作,无需拼凑页面,随机读写不需等待,立即有效,输入输出TTL/CMOS兼容,上电复位输出,掉电保护,内置看门狗,电源监测,不用外加电路和电池,且引脚与标准SRAM兼容。8031单片机价格低,使用灵活,其特点具具体如下:
(1)具有功能很强的8位中央处理单元(CPU);
(2)片内有时钟发生电路(6MH或12MH);
(3)片内具有128字节的RAM;
(4)具有21个特殊寄存器。
(5)可扩展64K字节的外部数据存储器和64K字节的外部程序存储器;
(6)具有4个I/O口,32根I/O线;
(7)具有2个16位定时器/计数器;
(8)具有5个中断源,配备2个中断优先级;
(9)具有一个全双功串行接口;
(10)具有位寻址能力,适用逻辑运算。
从上述特性可看出这种8031芯片集成度高、功能强,只需增加少量外围器件就可以构成一个完整的微机系统。故应选用8031单片机。
第3章开环伺服进给系统机械部分设计
3.1 确定系统脉冲当量
根据机床精度要求确定脉冲当量,纵向:0.01mm/步,横向0.005mm/步。3.2 计算切削力
确定切削力(纵车外圆):
主切削力()Z F N 按经验公式估算:
1.5
1.5
m ax 0.670.67400
5360Z F D N
==?=
按切削力各分力比例:z y ::1:0.25:0.4x F F F = 取:53600.251340x F N =?= y 53600.42144F N =?=
3.3 滚珠丝杠螺母副的计算选型(纵向进给丝杠) 3.3.1 计算进给牵引力m
()F N
纵向进给为综合型导轨
m ()'()x z F N K F f F G =++
1.1513400.16(5360800)2530N =?+?+=
式中K ——考虑颠覆力矩影响的实验系数,综合导轨取 1.15K =;
'f ——滑动导轨摩擦系数:0.150.18 G
——溜板及刀架重力:g 8010800N kg G m kg N =?=?=
3.3.2 计算最大动负载C
3
C=
w m L f F
6
6010
n T L ??=
1000s
v n L =
式中0L ——滚珠丝杠导程,初选06L m m =;
s v ——最大切削力下的进给速度,可取最大进给速度的(1
1
2
3
),此处
取 1.0min 0.50.5min s v r r =?=;
T
——使用寿命,按15000h ;
w
f ——运转系数,按一般运转取 1.2 1.5w f = ;
L
——寿命,以610转为1单位。
100010000.5
83.3min 6
s
v n r L ??=
=
=
6
6
606088.315000
75.010
10
n T L ????=
=
=
3375.0 1.2253012801.6w m C L f F N ==??=
3.3.3 滚珠丝杠螺母副的选型
查阅附录A 表A-2,可采用1W 4006L 外循环螺纹调整浴巾的双螺母滚珠丝杠副,1列2.5圈,其额定动负载为164000N ,进度等级按表4-6选为3级(大致相当于老标准E 级)。
3.3.4 传动效率计算
tan tan()
γηγ?=
+
式中γ——螺旋升角,1W 4006L ,244'γ=
?——摩擦角,取10',滚动摩擦系数0.0030.004
12801.6C N =
tan tan 244'0.94tan()
tan(244'10')
γηγ?===++
3.3.5 刚度计算
先画出此纵向进给滚珠丝杠支承方式草图,如图3-1所示。最大牵引力为2530N ,支承间距1500L m m =,丝杠螺母及轴承均进行预紧,预紧力为最大轴向负荷的13。
图3-1 纵向进给系统计算简图
(1)丝杠的拉伸或压缩变形量1δ
查《课程设计指导书》P17,图4-2,根据
2530,40m F N D m m ==,查出
5
1.210
L
L δ-=?,可算出
5
2
10
1500 1.210
1500 1.810
L
m m
L δδ--=
?=??=?
由于两端均采用向心推力球轴承,且丝杠又进行了 预拉伸,故其拉压刚度可以提高4倍。其实际变形量1'()m m δ为:
2
111'0.4510
4
δδ-=
?=?
(2) 滚珠与螺纹滚道间接触变形2δ
查《课程设计指导书》P18图4-3,W 系列 2.5圈滚珠和螺纹滚道接触变形量
2=6.4m δμ,因进行预紧,2211'=
6.4=3.22
2
m
δδμ=
?
(3)支承滚珠丝杠轴承的轴向接触变形3δ
采用51107(旧代号为8107)型推力球轴承,135d m m =,滚动体直径
6.35Q d m m =,滚动体数量
z=18。
3
3
22
32
2
253
0.00240.0024 6.3518
m
Q F d Z
δ=?
=?
??
0.0075m m
=
注:此公式中的m F 单位应为kgf 。
因施加预紧力,故
3311'0.00750.00382
2
m m
δδ=
=
?=
据以上计算:
123'''0.00450.00320.00380.0115mm δδδδ=++=++=<定位精度
3.3.6 稳定性校核
滚珠丝杠两端采用推力轴承,不会产生失稳现象,不需要作稳定性校核。
3.3.7纵向滚珠丝杠副的几何参数
表3-1 1W 4006L 滚珠丝杠的几何参数
名称 符号
参 数 螺
纹
滚
道
公称直径 0d 40 导 程
0L
6
接触角 β
244'
钢球直径(mm) q d
3.969 滚道法面半径 R
0.52q R d =
2.064 偏心距 e 2
sin q
d e R β=-
()
0.056
螺纹升角 γ
tan L act d γπ=?(
)
244'
螺
杆
螺杆外径
d
0(0.20.25)q d d d =-
39 螺杆内径 1d 1022d d e R =+- 35.984
螺杆接触直径 z d 0cos z q d d d β
=-? 36.0355 螺 母
螺母螺纹直径
D
022D d e R
=-+
44.016 螺母内径
1D
10(0.20.25)q D d d =-
40.7938
3.4 齿轮传动比计算
已取得纵向进给脉冲当量0.01p δ=,滚珠丝杠导程06L m m =,初选步进电动机步距角0.6 。可计算出传动比i
可选定齿轮齿数为:
12
3636
z i z =
=
故,取1236z z ==,模数m 取2.5。有关参数表3-2。
表3-2 传动齿轮的几何参数 齿 轮 编 号 1z
2
z
3z
齿数
32
32 24 分度圆 d m z
=
80 80 60 齿顶圆
2a d d m =+
85 85
60
齿根圆 2 1.25f d d m =-? 73.75 73.75 53.75 齿宽 ()610m
20 20
15 中心距
()122A d d =+
80
70
3.5 步进电动机的计算和选型 3.5.1 等效转动惯量计算
计算简图见图3-1,传动系统折算到电机轴上的总的转动惯量2()J kg cm ∑?可由下式计算:
2
2
01122
(
)[()(
)]2M S L Z G J J J J J Z g
π
∑=++++
式中J ∑——步进电机转子转动惯量2()kg cm ?
1J 、2J ——齿轮1Z 、2Z 的转动惯量2
()kg cm ?
S
J ——滚珠丝杠转动惯量2()kg cm ?。
参考同类型机床,初选反应式步进电机1103503B Y G ,其转子惯量2
18M J kg cm
=?
3
43
4
12110.7810
0.7810
82
J J d L --==???=???
2
6.390kg cm
=?
3
4
2
0.7810
415029.952S J kg cm
-=???=?
800G N
=
式中1d 、2d ——齿轮1Z 、2Z 的分度圆直径; 2L 、2L ——齿轮1Z 、2Z 的齿宽。
代入上式:
2
2
01122[()]2M
S L Z G J J J J J Z g π∑????=++++ ? ?????
2
2
328000.618 6.390[(6.39029.952)]329.82π????=++++ ? ???
??
2
61.477kg cm
=?
考虑步进电机与传动系统惯量匹配问题。
2
43.477M J J J kg cm
∑=-=?
43.477 2.415318
M
J J =
=<
基本满足惯量匹配的要求。
3.5.2 电机力矩计算
机床在不同的工况下,其所需转矩不同,下面分别按各阶段计算: (1)快速空载起动力矩M 起
在快速空载起动阶段加速力矩占的比例较大,具体计算公式如下:
0f
M M M
M =++a max 起
2
2
m ax m ax 210
10
60602a
a
n n M J J J t t πεπ
--∑∑∑??=?=?
?=?
??a max
将前面的数据带入,式中各符号意义同前。
m ax
m ax 40000.6666.7m in 360
0.01
360
b p
v n r θδ=
?
=
?
=。
起动加速时间30a t m s =
2
2
m ax 210
2666.710
61.47760600.03
a
n M J t ππ--∑????=?
=?
??a max
1429.98N c m =?
折算到电机轴上的摩擦力矩f M :
()()
00021'22Z f
f F G L F L M
i
z z πηπη+?==
()0.1653608000.6
117.720.81
N cm π?+?=
=???
附加摩擦力矩0M :
()()
()10
220
300
211122po m F L F L M i
z z ηηπηπη
=
-=-
()1
2
3
25306
10.920.8 1.25
π??=
-?? 80.50.1915.3N m
=?=?
上述三项合计:
0f
M M M
M =++a max 起
1429.98117.715.31562.98N cm =++=?
(2)快速移动时所需力矩M 快
0117.715.3133f
M M
M N cm
=+=+=?快
(3)最大切削负载时所需力矩M 切
0002x f t f
F L M M
M M M
M i
πη=++=++
切
13400.6117.715.320.81
π?=++
??
117.715.3160.03293.03N cm =++=?
从上面计算可以看出,M 起、M 快和M 切三种工况下,以快速空载起动所需力矩最大,此项作为初选步进电动机的依据。
从课程设计指导书P36表4-13查出,当步进电动机为三相六拍时,
m ax
0.866
q j M M
λ==。
最大静力矩m ax
1562.980.8661804.8j M N cm
==?。
按此最大静转矩从下表3-3
110BYG3503型最大静转矩为20N m ?。大于所需最大静转矩,可作为初选型号,但还必须进一步校核步进电动机起动矩频特性和运行矩频特性。
如下表3-3所示。
3.5.3 计算步进电动机空载起动频率和切削时的工作频率
m ax
10001000 4.06666.7160060600.01
k p v f H z H z δ?=
=
=>?
100010000.4666.760600.01
s e p
v f H z δ?=
=
=?
从上表3-3查出110BYG3503型步进电动机空载起动频率为1600H z ,图3-2(https://www.360docs.net/doc/b116469236.html,/docc/product2.htm )查出运行频率为15000H z ,且根据下图3-2)蓝色背景区所示可知其运行距频特性。
表3-3 110BYG350系列电机的技术参数 型 号 步
距
角 相数 电压 线电流 静转矩 空载起动频率 空载
运行频率 转动惯量 机身长
单 位
度
V
A N.m KHZ KHZ (kg .cm 2) (mm)
110BYG3501 0.6 3 110-220 5 12 1600 >=30 11 144 110BYG3502 0.6 3 110-220 5 16 1600 >=30 15 182 110BYG3503 0.6 3 110-220 5 20 1600 >=30 18
261
图3-2 110BYG3503型步进电动机矩频特性
从图3-2看出,当步进电动机起动时,若1600f H z =起,则18M N m =?,能满足此机床所要求的空载起动力矩()1562.98N cm ?可直接起动。
当快速运动和切削进给时,根据图3-2,步进电动机运行矩频特性知,
666.7e f H z
=时,18.3M N m =?左右,大于m ax
1804.8j M
N cm
=?,完全可以满足
要求。
第4章 机械传动机构的调整和结构的简要说明 4.1 丝杠进给速度的调节
由于系统为开环系统,故采用脉冲信号的变化来控制步进电机的转速,进而
通过齿轮箱到丝杠轴,对大托板的纵向进给速度进行控制。
4.2 轴向的预紧力的调整及定位
由装配图可知,在丝杠轴的两端各装有一对锁紧螺母(预紧螺母),可有这对螺母对丝杠轴的轴向预紧进行调整,并起到定位作用。每组支承部件的另一端,即与锁紧螺母对应的那端采用端盖定位。在丝杠副的一端也采用端盖定位,另一端为锁紧螺母,既预紧又定位。
结论部分
经过计算、校核、设计,表明改造任务的初步设计合理,数据准确,现改造
方案已设计成图纸——见装配图(图01)和零件图(图02)。
该改造设计相对普通车床来说,提高了自动化程度,加入了计算机控制,操作、结构简单化,既能降低能耗,又能提高了工作效率。但是设计者由于能力有限,经验寒酸,时间紧迫,设计及图纸中难免有不妥甚至是重大错误,望老师和同学指正。
设计体会
课程设计是培养学生综合运用所学知识,发现、提出、分析和解决实际问题,锻炼实践能力的重要环节,是对学生实际工作能力的具体训练和考察过程。回顾起此次课程设计,我感慨颇多。
在毕业设计的日子里,可以说得是苦多于甜,但是总体来讲,效果还是很好的,不仅巩固了以前所学的知识,还学到了很多在书本上无法学到的知识。整个设计过程不能说是困难重重,难免会遇到过各种各样的问题,和第一次课程设计相比,力不从心的感觉不再那么强烈,但在设计的过程中还是发现了自己许多不足之处,使自己认识到对以前所学知识理解得不够深刻,掌握得不够牢固,比如说螺钉的画法根本没有掌握,全篇的螺钉没有一个画对,箱体壁厚取值太小,电机无法固定,并出现设计太随意,尺寸随意取,以至于设计方案难以加工。
通过这次课程设计使我懂得了理论与实际相结合的重要性,只有理论知识是远远不够的,只有把所学的理论知识与实践相结合起来,从理论中得出结论,才能真正为社会服务,从而提高自己的实际动手能力和独立思考的能力。通过这次课程设计之后,一定把以前所学过的知识重新温故。
这次课程设计终于顺利完成了,虽然很累,但看到老师每天都来给我们指导,并且还带大四的毕业设计,又要忙评估的事情,就又感觉到累其实是充实。是他让我学到了很多书本上无法学到的知识,在此,对他孜孜不倦的指导和和蔼可亲的态度表示崇高的敬意的真挚的感谢!同时,对给过我帮助的所有同学和其他指导老师表示忠心的感谢!
数控机床毕业设计板式样
项目5 型腔加工训练一 训练目的 ●根据工艺要求掌握内型腔和封闭凹槽加工方案。 ●合理选用刀具及合理的切削用量。 ●运用环切法切削内型腔。 ●掌握内型腔的加工刀具、走刀路线、去除余量的方法和编程技巧。任务1 工艺分析及理 1.零件图样的分析 零件图 图1-5-1
毛坯图 图1-5-2 如图1-5-1所示,零件材料为硬铝,切削性能较好,加工部分由内型腔和岛内型腔构成,图中主要尺寸注明公差要考虑精度问题。零件毛坯100mm×120mm ×20mm的方料,已完成上下平面及周边侧面的加工,如图1-5-2所示。 2.选择加工机床 用立式三坐标数控铣床或加工中心较为合适。机床型号:XK6325(FANUC-oi MC系统)或VMA600。这里选用VMA600加工中心。 3.加工工艺分析 本零件在加工中心上一次装夹即可完成所有加工内容,故确定一道工序,四个工步完成零件加工。 工步一用φ16的高速钢键槽铣刀环切法粗铣十字形凹槽。侧面留单边余量0.1mm。深度留0.1mm精加工余量。 工步二用φ16的高速钢立铣刀环切法精加工十字形凹槽到图纸尺寸要求。 工步三用φ8的高速钢键槽铣刀粗铣方形凹槽,侧面留单边余量0.1mm。深度方向留0.1mm精加工余量。 工步四用φ8的高速钢立铣刀精铣方形凹槽到图纸尺寸要求。 4.走刀路线 工步一环切法粗铣十字形凹槽。走刀路线如图1-5-3。从A(-10,0)点下
至切削深度,按A→C→D→E→F→H→I→J→K→M→N→L→P→Q→R →S→T→Z→D→E →F→H→B→O的路线进给,从O(0,0)点抬刀。 图1-5-3 粗铣十字形凹槽走刀路线 工步二环切法精铣十字形凹槽。走刀路线如图1-5-3所示。从A(-10,0)点下至切削深度,A→C建立左刀补,C→E直线切入,按E→F→H→I→J→K→M →N→L→P→Q→R →S→T→Z→D→E →F→H的路线进给,H→B直线切出,从B →O取消刀补,O点抬刀。 工步三粗铣封闭方型凹槽,方型凹槽内轮廓走刀路线(经旋转45度角后得到)如图1-5-4。O(0,0)→A(0,-40)建立左刀补,A点下刀至切削深度,按A→B→C→D→E→F→H→I→J→A的路线进给,A点抬刀,A→O点取消刀补。 方型凹槽外轮廓走刀路线(经旋转45度角后得到)如图1-5-4。O(0,0)→K(0,-40)建立右刀补,K点下刀至切削深度,按K→M→N→U→V→W→Q→P →S→K的路线进给,K点抬刀,K→O点取消刀补。
广州数控数控车床操作编程说明书
广州数控980TD 编程操作说明书 第一篇 编程说明 第一章:编程基础 GSK980TD 简介 广州数控研制的新一代普及型车床CNC GSK980TD 是 GSK980TA 的升级产品,采用了32位高性能CPU 和超大规模可编程器件FPGA ,运用实时多任务控制技术和硬件插补技术,实现μm 级精度运动控制和PLC 逻辑控制。 技术规格一览表 运动控制 控制轴:2轴(X 、Z );同时控制轴(插补轴):2轴 (X 、Z ) 插补功能:X 、Z 二轴直线、圆弧插补 位置指令范围:~;最小指令单位:
机床数控系统和数控机床 数控机床是由机床数控系统(Numerical Control Systems of machine tools)、机械、电气控制、液压、气动、润滑、冷却等子系统(部件)构成的机电一体化产品,机床数控系统是数控机床的控制核心。机控系统由控制装置(Computer Numerical Controler简称CNC)、伺服(或步进)电机驱动单元、伺服(或步进)电机等构成。 数控机床的工作原理:根据加工工艺要求编写加工程序(以下简称程序)并输入CNC,CNC加工程序向伺服(或步进)电机驱动单元发出运动控制指令,伺服(或步进)电机通过机械传动构完成机床的进给运程序中的主轴起停、刀具选择、冷却、润滑等逻辑控制指令由CNC传送给机床电气控制系统,由机床电气控制系统完成按钮、开关、指示灯、继电
器、接触器等输入输出器件的控制。目前,机床电气控制通常采用可编程逻辑控制器(Programable Logic Controler 简称PLC),PLC具有体积小、应用方便、可靠性高等优点。由此可见,运动控制和逻辑控制是数控机床的主要控制任务。 GSK980TD车床CNC同时具备运动控制和逻辑控制功能,可完成数控车床的二轴运动控制,还具有内置式PLC功能。根据机床的输入、输出控制要求编写PLC程序(梯形图)并下载到GSK980TD,就能实现所需的机床电气控制要求,方便了机床电气设计,也降低了数控机床成本。 实现GSK980TD车床CNC控制功能的软件分为系统软件(以下简称NC)和PLC软件(以下简称PLC)二个模块,NC模块完成显示、通讯、编辑、译码、插补、加减速等控制,PLC模块完成梯形图解释、执行和输入输出处理。 编程基本知识 1、坐标轴定义 数控车床示意图 GSK980TD使用X轴、Z轴组成的直角坐标系,X轴与主轴轴线垂直,Z轴与主轴轴线方向平行,接近工件的方向为负方向,离开工件的方向为正方向。 按刀座与机床主轴的相对位置划分,数控车床有前刀座
数控车床使用说明书
Y C K-6032/6036数控车床使用维修说明书
目录 前言 .......................................... 错误!未定义书签。第一章机床特点及性能参数. (2) 1.1机床特点 (2) 4.1 准备工作 4.2 上电试运行 (8) 第五章主轴系统 (9) 5.1 简介 (9) 5.2 主轴系统的机构及调整 (10)
5.2.1 皮带张紧 (10) 5.2.2 主轴调整 (11) 5.3 动力卡盘 (11) 第六章刀架系统 (11) 第十一章机床电气系统 (14) 11.1主要设备简要 (15) 11.2 操作过程: (15) 11.3 安全保护装置: (15)
11.4 维修: (15) 第十二章维护、保养及故障排除 (18)
前言 欢迎您购买我厂产品,成为我厂的用户。 本说明所描述的是您选用的我厂YCK-6032/6036标准型全功能数控车床。该车床结构紧凑,自动化程度高,是一种经济型自动化加工设备,主要用于批量加工各种轴类、套类及盘类零件的外圆、内孔、切槽,尤其适用轴承行业轴承套圈等多工序零件加工。
第一章机床特点及性能参数 1.1机床特点 YCK-6032/6036全功能数控车床是顺应市场要求向用户推荐的优秀产品,该机性能优异,各项指标均达国际水平,具有较高的性价比,可替代同类进口产品。 YCK-6032/6036整机布局紧凑合理,其高转速、高精度和高刚性,为用户在使用中提 本机标准配置为排刀架,刚性好,可靠性高,故障率低,重复定位精度为 0.007mm,相邻刀位移动时间为0.3秒,车、镗、钻、扩、铰等工具可同时安装使用。 另外,本机可选配八工位、十工位、十二工位液压转盘刀塔。 本机进给系统全部由伺服电机(可选配步进电机)直连驱动,刚性、动态特性好,系统的最小设定单位为0.001mm,快速移动速度为X轴15m/min,Z轴15m/min,
Creo2.0数控加工说明书
《综合性实验》任务书 一、设计题目:零件的CAD/CAM综合设计 二、设计目的 综合性实验是开设《三维CAD》、《机械CAD/CAM》、《机械制造学》、《数控机床》课程之后进行的一个综合性、实践性教学环节。在系统学习CAD/CAM技术的基本原理、基本方法以及机床数控技术的基础上,着重培养学生借助计算机进行机械产品的设计、制造和系统集成的综合应用能力。其目的: 1.掌握产品的计算机辅助设计过程和方法,培养利用计算机进行结构设计的能力。 2.掌握零件的计算机辅助制造过程和方法,培养数控编程及加工仿真的能力。 3.通过应用PRO/ENGINEER,训练和提高CAD/CAM的综合运用能力。 三、设计任务 本设计以某一具体的机械零件为设计对象(零件图见附图)。主要设计任务: 1.三维CAD造型:熟悉并掌握机械CAD/CAM软件PRO/ENGINEER的草绘模块、零件模块进行三维CAD造型。 2.拟定工艺路线:根据三维几何模型,拟定该零件的数控加工工艺路线(需选择毛坯、机床、刀具、切削用量、夹具辅具量具等); 3. 数控加工程序设计:在Pro/Engineer软件平台下,设计数控加工程序,包括描述选择确定数控加工的部位、加工方法、加工机床、刀具、切削用量等,根据数控机床的具体情况选定数控系统的种类与型号,生成数控加工程序; 4. 数控加工仿真:在Pro/Engineer软件平台下,根据前面得到的数控加工程序进行数控加工仿真,考虑工件由毛坯成为零件过程中形状、尺寸的变化,检查刀具与被切工件轮廓的干涉情况和检查刀具、夹具、机床、工件之间的运动碰撞等,完成几何模型的计算机仿真加工; 5. 数控程序与程序传输:根据数控机床的具体情况选定数控系统的种类与型号,生成通过了计算机仿真的合格零件的数控加工程序,并将数控加工程序传输给加工中心机床;6.编写设计说明书。 四、设计要求 1、要求设计过程在计算机上完成。 2、设计说明书用计算机打印(A4纸,1万字左右)。 正文:宋体五号,单倍行距; 页眉:宋体小五号,内容包括班级,姓名,“综合性实验课程设计说明书”字样; 页脚:右下脚页码。 3、设计结果应包括:课程设计说明书(应包含设计任务书、设计思路、设计步骤、设 计过程的说明和阶段结果。附零件三维图、加工代码、零件原图纸等内容) 4、严禁抄袭和请人代做,一经发现,成绩计为零分并上报教务处。 五、设计内容及时间分配 1.准备工作:布置设计任务,认真阅读设计任务书,收集资料。(1天) 2.熟悉PRO/ENGINEER,并进行零件的三维造型。(4天) 3.进行零件的数控加工。(3天) 4.编写课程设计说明书。(1天)
数控技术毕业设计
毕业设计 标题︰轴类零件工艺设计学生姓名︰ 系部︰机械工程系专业︰数控技术 班级︰ 指导老师︰ 校外指导老师︰
目录 摘要 (4) 1.绪论 (5) 1.1数控技术的现状与发展趋势 (5) 2. 零件工艺分析 (6) 2.1零件的用途 (6) 2.2零件图工艺分析 (6) 2.3零件毛坯及材料的选择 (7) 3.加工设备及辅助工具的选择 (9) 3.1机床的选择 (9) 3.2刀具的选择 (9) 3.3量具的选择 (10) 3.4夹具的选择 (10) 4.拟定工艺方案 (11) 4.1加工工序的划分 (11) 4.2加工顺序的确定 (11) 4.3加工路线的确定 (12) 4.4零件定位基准的确定 (14) 4.5装夹方式的确定 (15) 4.6工作坐标原点与换刀点的确定 (16) 5.切削用量选择 (17) 5.1背吃刀量的确定 (17) 5.2主轴转速的确定 (17) 5.3进给速度的确定 (19) 6.切削液的选择 (20)
7.工艺文件的制定及程序编制 (21) 7.1数控加工工艺卡 (21) 7.2刀具卡 (22) 7.3程序编制 (23) 8.机械加工精度及零件表面质量 (31) 8.1机械加工精度 (31) 8.2零件表面质量 (31) 结论 (33) 参考文献 (34) 附录 (35) 后记 (36)
摘要 数控加工工艺是数控编程与操作的基础,合理的工艺是保证数控加工质量、发挥数控机床效能的前提条件。因此本文主要是对轴类零件的数控加工工艺进行分析,详细地阐述了轴类零件的加工工艺分析及制定加工方案的整个设计过程。该轴类零件的结构特点是由圆柱、圆弧、椭圆弧、螺纹、槽等组成内外表面的回转体。零件的加工过程是首先用粗基准定位,加工出精基准表面;然后采用精基准定位,加工零件的其他表面。工艺路线的拟订是制订工艺规程的关健,它与定位基准的选择有密切关系。其次在机床、刀具、夹具切削用量的选择中,着重考虑到其对零件的加工的因素,为工艺设计节省了大量的时间。提高了设计效率。本文内容大致介绍了数控技术的发展趋势、对零件加工工艺步骤分析以及数控编程等。利用计算机辅助设计-AuToCAD绘制椭圆轴的二维图,用G代码指令进行手工编程并制定了相关的工艺文件,最后对机械加工精度及零件表面质量进行分析。 关键词:数控技术、轴类零件、工艺设计、程序编制
CA6140普通车床的数控化改造毕业设计论文
摘要 普通机床的经济型数控改造主要是在合理选择数控系统的前提下,然后再对普通车床进行适当的机械改造,改造的内容主要包括: (1) 床身的改造,为使改造后的机床有较好的精度保持性,除尽可能地减少电器和机械故障的同时,应充分考虑机床零部件的耐磨性,尤其是机床导轨。 (2) 拖板的改造,拖板是数控系统直接控制的对象,所以对其改造尤显重要。这中间最突出一点就是选用滚珠丝杠代替滚动丝杠,提高了传动的灵敏性和降低功率步进电机力矩损失。 (3) 变速箱体的改造,由于采用数控系统控制,所以要对输入和输出轴以及减速齿轮进行设计,从而再对箱体进行改造。 (4) 刀架的改造,采用数控刀架,这样可以用数控系统直接控制,而且刀架体积小,重复定位精度高,安全可靠。 通过对机床的改造并根据要求选用步进电机作为驱动元件,这样改造后的机床就能基本满足现代化的加工要求。 关键字:普通车床数控改造步进电机经济型数控系统数控刀架
一绪论 我国数控机床的研制是从1958年开始的,经历了几十年的发展,直至80年代后引进了日本、美国、西班牙等国数控伺服及伺服系统技术后,我国的数控技术才有质的飞跃,应用面逐渐铺开,数控技术产业才逐步形成规模。 由于现代工业的飞速发展,市场需求变的越来越多样化,多品种、中小批量甚至单件生产占有相当大的比重,普通机床已越来越不能满足现代加工工艺及提高劳动生产率的要求。如果设备全部更新替换,不仅资金投入太大,成本太高,而且原有设备的闲置又将造成极大的浪费。如今科学技术发展很快,特别是微电子技术和计算机技术的发展更快,应用到数控系统上,它既能提高机床的自动化程度,又能提高加工精度,所以最经济的办法就是进行普通机床的数控改造。 机床数控化改造的优点:(1)改造闲置设备,能发挥机床原有的功能和改造后的新增功能,提高了机床的使用价值,可以提高固定资产的使用效率;(2)适应多品种、小批量零件生产;(3)自动化程度提高、专业性强、加工精度高、生产效率高;(4)降低对工人的操作水平的要求;(5)数控改造费用低、经济性好;(6)数控改造的周期短,可满足生产急需。因此,我们必须走数控改造之路。 普通车床(如C616,C618,CA6140)等是金属切削加工最常用的一类机床。普通机床刀架的纵向和横向进给运动是由主轴回转运动经挂轮传递而来,通过进给箱变速后,由光杠或丝杠带动溜板箱、纵溜箱、横溜板移动。进给参数要靠手工预先调整好,改变参数时要停车进行操作。刀架的纵向进给运动和横向进给运动不能联动,切削次序也由人工控制。 对普通车床进行数控化改造,主要是将纵向和横向进给系统改为用微机控制的、能独立运动的进给伺服系统;刀架改造成为能自动换刀的回转刀架。这样,利用数控装置,车床就可以按预先输入的加工指令进行切削加工。由于加工过程中的切削参数,切削次序和刀具都会按程序自动调节和更换,再加上纵向和横向进给联动的功能,数控改装后的车床就可以加工出各种形状复杂的回转零件,并能实现多工序自动车削,
数控车床说明书
数控车床设计方案 一、选定题目——数控车床 数控机床的特点 1. 适应性强,适合加工单件或小批量复杂工件在数控机床上加工不同形状的工件,只需重新编制新工件的加工程序,就能实现新工件的加工。 2. 加工精度高,生产质量稳定数控机床的脉冲当量普遍可达 0.001mm/p,传动系统和机床机构都具有很高的刚度和热稳定性,进给系统采用间隙措施,并对反向间隙与丝缸螺距误差等由数控系统实现自动补偿,所以加工精度高。 3. 生产率高工件加工所需时间包括机动时间和辅助时间。数控机床能有效的减少这两部分时间。数控机床主轴转速和进给量的调速都比普通机床的范围大,机床刚性好,快速移动和停止采用了加速、减速措施,数控机床更换工件时,不需要调整机床。同一批工件加工质量稳定,无需停机检验,故辅助时间大大减少。 4. 减轻劳动强度,改善劳动条件数控机床加工是自动进行的工件过程不需要人的干预,加工完毕自动停车,这就使工人的劳动条件大为改善。 5. 良好的经济效益机床价格昂贵,分摊到每个工件的设备费用较大,但是机床可节省许多其他的费用。例如,工件加工前不用划分工序,工件的安装、调整、加工和检验所花费的时间少,特别不用设计制造专用工装夹具,加工精度稳定,减少废品率。 6. 有利于生产管理的现代化数控机床使用数字信息与标准代码处理、传递信息,特别在数控机床上使用计算机控制。
二、主要技术指标 1. 用途:指数控车床的工艺范围,包括加工对象的材料、质量、形状及尺寸等。 2. 生产率:包括加工对象的种类、批量及其所要求生产率。 3. 性能指标:包括加工对象所要求的精度或数控车床的精度、刚度、热变形、噪声等。 4. 主要参数:即确定数控车床的加工空间和主要参数。 5. 驱动方式:数控车床驱动方式分为步进电动机驱动与伺服电动机驱动。驱动方式的确定不仅与机床的成本有关,还将直接影响传动方式的确定。 6. 成本及生产周期:无论是订货还是工厂规划的产品,都将确定成本及生产周期方面的指标。 三、系统方案设计 (一) 数控车床基本组成 1) 数控机床是一种利用数控技术,按照事先编好的程序实现动作的机床,它由程序载体、输入装置、数控装置、伺服系统、位置反馈和机床机械部件组 成。 2) 数控车床结构由主轴传动机构、进给传动机构、工作台、床身等部分组成。 3) 数控车床由数控装置、床身、主轴箱、刀架进给系统、尾座、液压系统、冷却系统、润滑系统、排屑器等部分组成。详见下图:
数控机床进给系统设计
数控机床进给系统设计
第一章、数控机床进给系统概述 数控机床伺服系统的一般结构如图图1-1所示: 图1-1数控机床进给系统伺服 由于各种数控机床所完成的加工任务不同,它们对进给伺服系统的要求也不尽相同,但通常可概括为以下几方面:可逆运行;速度范围宽;具有足够的传动刚度和高的速度稳定性;快速响应并无超调;高精度;低速大转矩。 1.1、伺服系统对伺服电机的要求 (1)从最低速到最高速电机都能平稳运转,转矩波动要小,尤其在低速如0.1r /min 或更低速时,仍有平稳的速度而无爬行现象。 (2)电机应具有大的较长时间的过载能力,以满足低速大转矩的要求。一般直流伺服电机要求在数分钟内过载4-6倍而不损坏。 (3)为了满足快速响应的要求,电机应有较小的转动惯量和大的堵转转矩,并具有尽可能小的时间常数和启动电压。电机应具有耐受4000rad/s2以上的角加速度的能力,才能保证电机可在0.2s以内从静止启动到额定转速。 (4)电机应能随频繁启动、制动和反转。 随着微电子技术、计算机技术和伺服控制技术的发展,数控机床的伺服系统已开始采用高速、高精度的全数字伺服系统。使伺服控制技术从模拟方式、混合方式走向全数字方式。由位置、速度和电流构成的三环反馈全部数字化、软件处理数字PID,使用灵活,柔性好。数字伺服系统采用了许多新的控制技术和改进伺服性能的措施,使控制精度和品质大大提高。 数控车床的进给传动系统一般均采用进给伺服系统。这也是数控车床区别于普通车床的一个特殊部分。 1.2、伺服系统的分类 数控车床的伺服系统一般由驱动控制单元、驱动元件、机械传动部件、执行件和检测反
馈环节等组成。驱动控制单元和驱动元件组成伺服驱动系统。机械传动部件和执行元件组成机械传动系统。检测元件与反馈电路组成检测系统。 进给伺服系统按其控制方式不同可分为开环系统和闭环系统。闭环控制方式通常是具有位置反馈的伺服系统。根据位置检测装置所在位置的不同,闭环系统又分为半闭环系统和全闭环系统。半闭环系统具有将位置检测装置装在丝杠端头和装在电机轴端两种类型。前者把丝杠包括在位置环内,后者则完全置机械传动部件于位置环之外。全闭环系统的位置检测装置安装在工作台上,机械传动部件整个被包括在位置环之内。 开环系统的定位精度比闭环系统低,但它结构简单、工作可靠、造价低廉。由于影响定位精度的机械传动装置的磨损、惯性及间隙的存在,故开环系统的精度和快速性较差。 全闭环系统控制精度高、快速性能好,但由于机械传动部件在控制环内,所以系统的动态性能不仅取决于驱动装置的结构和参数,而且还与机械传动部件的刚度、阻尼特性、惯性、间隙和磨损等因素有很大关系,故必须对机电部件的结构参数进行综合考虑才能满足系统的要求。因此全闭环系统对机床的要求比较高,且造价也较昂贵。闭环系统中采用的位置检测装置有:脉冲编码器、旋转变压器、感应同步器、磁尺、光栅尺和激光干涉仪等。 数控车床的进给伺服系统中常用的驱动装置是伺服电机。伺服电机有直流伺服电机和交流伺服电机之分。交流伺服电机由于具有可靠性高、基本上不需要维护和造价低等特点而被广泛采用。 直流伺服电动机引入了机械换向装置。其成本高,故障多,维护困难,经常因碳刷产生的火花而影响生产,并对其他设备产生电磁干扰。同时机械换向器的换向能力,限制了电动机的容量和速度。电动机的电枢在转子上,使得电动机效率低,散热差。为了改善换向能力,减小电枢的漏感,转子变得短粗,影响了系统的动态性能。 交流伺服已占据了机床进给伺服的主导地位,并随着新技术的发展而不断完善,具体体现在三个方面。一是系统功率驱动装置中的电力电子器件不断向高频化方向发展,智能化功率模块得到普及与应用;二是基于微处理器嵌入式平台技术的成熟,将促进先进控制算法的应用;三是网络化制造模式的推广及现场总线技术的成熟,将使基于网络的伺服控制成为可能。 1.3、主要设计任务参数 车床控制精度:0.01mm(即为脉冲当量);最大进给速度:V max=5m/min。最大加工直径为D =400mm,工作台及刀架重:110㎏;最大轴,向力=160㎏;导轨静摩擦系数=0.2; max 行程=1280mm;步进电机:110BF003;步距角:0.75°;电机转动惯量:J=1.8×10-2㎏.m2。
数控机床毕业设计论文设计
题目数控机床的组成加工原理与工艺 系部:机电工程系 专业:机电一体化 指导老师: 班级: 学生:
目录 绪论 (1) 第一章数控车床的基本组成和工作原理 (4) 1.1 任务准备 (4) 1.1.1 机床结构 (4) 1.2 工作原理 (6) 1.3 数控车床的分类 (6) 1.4 数控车床的性能指标 (7) 1.5 数控车床的特点 (8) 第二章数控车床编程与操作....... . (10) 2.1 数控车床概述 (10) 2.1.1数控车床的组 (10) 2.1.2数控车床的机械构成 (11) 2.1.3数控系统 (11) 2.1.4数控车床的特点 (12) 2.1.5数控车床的分类 (13) 2.1.6数控车床(CJK6153)的主要技术 (13) 2.1.7数控车床(CJK6153)的润滑 (13) 2.2 数控车床的编程方法 (13) 2.2.1设定数控车床的机床坐标系 (13) 2.2.2设定数控车床的工件坐标系 (14) 第三章数控车床加工工艺分析 (20) 3.1 零件图样分析......................................... (20) 3.2 工艺分析 (21) 3.3 车孔的关键技术 (21)
3.4 解决排屑问题 (21) 3.5 加工方法 (22) 第四章当前数控机床技术发展趋势 (24) 4.1 是精密加工技术有所突破 (24) 4.2 是技术集成和技术复合趋势明显 (24) 结束语 (25) 参考文献 (26)
绪论 数控机床是数字控制机床(Computer numerical control machine tools)的简称,是一种装有程序控制系统的自动化机床。该控制系统能够逻辑地处理具有控制编码或其他符号指令规定的程序,并将其译码,从而使机床动作数控折弯 机并加工零件。 数控机床的操作和监控全部在这个数控单元中完成,它是数控机床的大脑。与普通机床相比,数控机床有如下特点:●加工精度高,具有稳定的加工质量; ●可进行多坐标的联动,能加工形状复杂的零件;●加工零件改变时,一 般只需要更改数控程序,可节省生产准备时间;数控折弯机 ●机床本身的精度高、刚性大,可选择有利的加工用量,生产率高(一般为普通机床的3~5倍);●机床自动化程度高,可以减轻劳动强度;●对操作人员的素质要求较高,对维修人员的技术要求更高。数控机床一般由下列几个部分组成:●主机,他是数控机床的主题,包括机床身、立柱、主轴、进给机构等机械部件。他是用于完成各种切削加工的机械部件。数控机床●数控装置,是数控机床的核心,包括硬件(印刷电路板、CRT显示器、键盒、纸带阅读机等)以及相应的软件,用于输入数字化的零件程序,并完成输入信息的存储、数据的变换、插补运算以及实现各种控制功能。●驱动装置,他是数控机床执行机构的驱动部件,包括主轴驱动单元、进给单元、主轴电机及进给电机等。他在数控装置的控制下通过电气或电液伺服系统实现主轴和进给驱动。当几个进给联动时,可以完成定位、直线、平面曲线和空间曲线的加工。 ●辅助装置,指数控机床的一些必要的配套部件,用以保证数控机床的运行,如冷却、排屑、润滑、照明、监测等。它包括液压和气动装置、排屑装置、交换工作台、数控转台和数控分度头,还包括刀具及监控检测装置等。●编程及其他附属设备,可用来在机外进行零件的程序编制、存储等。自从1952年美国麻省理工学院研制出世界上第一台数控机床以来,数控机床在制造工业,特别是在汽车、航空航天、以及军事工业中被广泛地应用,数控技术无论在硬件 和软件方面,都有飞速发展。
数控车床使用说明书
YCK-6032/6036 数控车床使用维修说明书
目录 前言 (1) 第一章机床特点及性能参数 (2) 1.1 机床特点 (2) 第二章机床的吊运与安装 (5) 2.1 开箱 (5) 2.2 机床的吊运 (6) 2.3 机床安装 (7) 2.3.1 场地要求 (7) 2.3.2 电源要求 (7) 第三章机床的水平调整 (8) 第四章机床试运行 (9) 4.1 准备工作 (9) 4.2 上电试运行 (9) 第五章主轴系统 (10) 5.1 简介 (10) 5.2 主轴系统的机构及调整 (11) 5.2.1 皮带张紧 (11) 5.2.2 主轴调整 (12) 5.3 动力卡盘 (12)
第六章刀架系统 (13) 第七章进给系统 (13) 第八章液压系统 (14) 8.1 液压系统原理 (14) 8.2 液压油 (15) 第九章润滑系统 (15) 9.1 移动部件的润滑 (15) 9.2 转动部件润滑 (15) 9.3 润滑油 (16) 第十章机车冷却系统及容屑装置 (17) 第十一章机床电气系统 (18) 11.1 主要设备简要 (18) 11.2 操作过程: (18) 11.3 安全保护装置: (19) 11.4 维修: (19) 第十二章维护、保养及故障排除 (24)
欢迎您购买我厂产品,成为我厂的用户 本说明所描述的是您选用的我厂YCK-6032/6036 标准型全功能数控车床。该车床结构紧凑,自动化程度高,是一种经济型自动化加工设备,主要用于批量加工各种轴类、套类及盘类零件的外圆、内孔、切槽,尤其适用轴承行业轴承套圈等多工序零件加工。该机床采用45 °斜床身,流畅 的排屑性能及精确的重复定位功能,可实现一台设备同时完成多道工序,提高了劳动效率,为工厂节省了人力资源,并且尺寸精度大大提高,一次装料可进行多次循环加工,可实现一人操作,看护多台机床。避免了传统车床自动送料车床的二次加工,使得多工序的产品能够一次性加工完成,实现了大批量多品种高精度零件的自动化生产。
GSK980TD数控车床中文使用说明书
GSK980TA/D编程教材 《一》编程的基本概念 《二》常用G代码介绍 《三》单一固定循环 《四》复合型固定循环 《五》用户宏程序 《六》螺纹加工 《七》T代码及刀补 《八》F代码及G98、G99 《九》S代码及G96、G97 (注意:本教材仅供学习参考,实际操作编程时应以广数GSK980T车床数控系统使用手册为准) 2007年9月 《一》编程的基本概念: 一个完整的车床加工程序一般用于在一次装夹中按工艺要求完成对工件的加工,数控程序包括程序号、程序段。 (一)程序号:相当于程序名称,系统通过程序号可从存储器中多个程序中识别所要处理的程序,程序号由字母O及4位数字组成。 (二)程序段:相当于一句程序语句,由若干个字段组成,最后是一个分号(;)录入时在键入EOB键后自动加上。整个程序由若干个程序段构成,一个程序段用来完成刀具的一个或一组动作,或实现机床的一些功能。(三)字段(或称为字):由称为“地址”的单个英语字母加若干位数字组成。根据其功能可分成以下几种类型的字段: ▲程序段号:由字母N及数字组成,位于程序段最前面,主要作用是使程序便于阅读,可以省略,但某些特殊程序段(如表示跳转指令的目标程序段)必须标明程序段号。 为了便于修改程序时插入新程序段,各句程序段号一般可间隔一些数字(如 N0010、N0020、N0030)。 ▲ 准备功能:即G代码,由字母G及二位数字组成,大多数G代码用以指示刀具的运动。(如G00、G01、G02) ▲ 表示尺寸(坐标值)的字段:一般用在G代码字段的后面,为表示运动的G代码提供坐标数据,由一个字母与坐标值(整数或小数)组成。字母包括: 表示绝对坐标:X、Y、Z 表示相对坐标:U、V、W 表示园心坐标:I、J、K (车床实际使用的坐标只有X、Z,所以Y、V、J都用不着) ▼表示进给量的字段:用字母F加进给量值组成,一般用在插补指令的程序段中,规定了插补运动的速度。 ▼S代码:表示主轴速度的字段。用字母S加主轴每分钟转速(或主轴线速度:米/分)组成。
数控机床课程设计说明书
目录 1、前言 (2) 2、控制系统硬件的基本组成 (2) 2.1系统扩展 (2) 2.1.1 8031芯片引脚 (3) 2.1.2 数据存储器的扩展 (6) 2.1.3 数据存储器的扩展 (7) 3、控制系统软件的组成及结构 (9) 3.1 监控程序 (10) 3.1.1 系统初始化 (10) 3.1.2 命令处理循环 (10) 3.1.3 零件加工程序(或作业程序)的输入和编辑 (10) 3.1.4 指令分析执行 (10) 3.1.5 系统自检 (11) 3.2 数控机床控制系统软件的结构 (11) 3.2.1 子程序结构 (12) 3.2.2 主程序加中断程序结构 (12) 3.2.3 中断程序结构 (12) 4 、心会得体 (13) 5 、参考文献 (14)
1 、前言 数控车床又称数字控制(Numbercal control,简称NC)机床。它是基于数字控制的,采用了数控技术,是一个装有程序控制系统的机床。它是由主机,CNC,驱动装置,数控机床的辅助装置,编程机及其他一些附属设备所组成。数控机床控制系统的作用是使数控机床机械系统在程序的控制下自动完成预定的工作,是数控机床的主要组成部分。 2、控制系统硬件的基本组成 数控机床控制系统由硬件系统和软件系统两大部分组成。控制系统在使用中的控制对象各不相同,但其硬件的基本组成是一致的。控制系统的硬件基本组成框图如图1所示。 图1 控制系统硬件基本组成框图 在图1中,如果控制系统是开环控制系统,则没有反馈回路,不带检测装置。 以单片机为核心的控制系统大多采用MCS-51系列单片机中的8031芯片单片机,经过扩展存储器、接口和面板操作开关等,组成功能较完善、抗干扰性能较强的控制系统。 2.1系统扩展 以8031单片机为核心的控制系统必须扩展程序存储器,用以存放程序。同时,单片机内部的数据存储器容量较小,不能满足实际需要,还要扩展数据存储
数控机床自动润滑系统毕业设计
江西城市职业学院2011届毕业设计 题目:数控机床自动润滑系统设计 分院:机电工程学院 班级:数控08—1班 学号: 080744080104 学生姓名: XXXX 起讫日期: 指导教师:职称: 教研室主任: 审核日期:
数控机床自动润滑系统 摘要 机床润滑系统的设计、调试和维修保养,对于提高机床加工精度、延长机床使用寿命等都有着十分重要的作用。但是在润滑系统的电气控制方面,仍存在以下问题:一是润滑系统工作状态的监控。数控机床控制系统中一般仅设邮箱釉面监控,以防供油不足,而对润滑系统易出现的漏油、油路堵塞等现象,不能及时做出反应。二是设置的润滑循环和给油时间单一,容易造成浪费。数控机床在不同的工作状态下,需要的润滑剂量是不一样的,如在机床暂停阶段就比加工阶段所需要的润滑油量要少。针对上述情况,在数控机床电气控制系统中,对润滑控制部分进行了改进设计,时刻监控润滑系统的工作状况,以保证机床机械部件得到良好的润滑,并且还可以根据机床的工作状态,自动调整供油、循环时间,以节约润滑油。 数控机床中润滑系统为间歇供油工作方式。因此,润滑系统中的压力采用定期检查方式,即在润滑泵每次工作以后检查。如果出现故障,如漏油、油泵失效、油路堵塞,润滑系统内的压力就会突然下降或升高,此时应立即强制机床停止运行,进行检查,以免事态扩大。油面过低以往习惯的处理方法是将“油面过低”信号与“压力异常”报警信号归为一类,作为紧急停止信号。一旦PMC系统接收到上述信号,机床立即进入紧急停止状态,同时让伺服系统断电。但是,与润滑系统因油路堵塞或漏油现象而造成“压力异常”的情况不同,如果润滑泵油箱内油不够,短时间不至于影响机床的性能,无需立即使机床停止工作。但是,出现此现象后,控制系统应及时显示相应的信息,提醒操作人员及时添加润滑油。如果操作人员没有在规定时间内予以补充,系统就会控制机床立即进入暂停状态。只有及时补给润滑油后,才允许操作人员运行机床,继续中断的工作。针对“油面过低”信号,这样的处理方法可以避免发生不必要的停机,减少辅助加工时间,特别是在加工大型模具的时候。在设计时,我们将“油面过低”信号归为电气控制系统“进给暂停”类信号,采用“提醒——警告——暂停,禁止自动运行”的报警。一旦油箱内油过少,不仅在操作面板上有红色指示灯提示,在屏幕上也同时显示警告信息,提醒操作人员。如果该信号在规定的时间内没有消失,则让机床迅速进入进给暂停状态,此时暂停机床进行任何自动操作。操作人员往油箱内添加足够的润滑油后,只需要按“循环启动”按钮,就可以解除此状态,让机床继续暂停前的加工操作。 该系统采用PLC进行控制。正常情况下,按下启动按钮,润滑电动机M立即运行,20S
广州数控980TD数控车床入门说明书
广州数控980TD编程操作说明书 第一篇编程说明 第一章:编程基础 1.1GSK980TD简介 广州数控研制的新一代普及型车床CNC GSK980TD是GSK980TA的升级产品,采用了32位高性能CPU和超大规模可编程器件FPGA,运用实时多任务控制技术和硬件插补技术,实现μm级精度运动控制和PLC逻辑控制。 技术规格一览表
1.2 机床数控系统和数控机床 数控机床是由机床数控系统(Numerical Control Systems of machine tools)、机械、电气控制、液压、气动、润滑、冷却等子系统(部件)构成的机电一体化产品,机床数控系统是数控机床的控制核心。机控系统由控制装置(Computer Numerical Controler简称CNC)、伺服(或步进)电机驱动单元、伺服(或步进)电机等构成。 数控机床的工作原理:根据加工工艺要求编写加工程序(以下简称程序)并输入CNC,CNC加工程序向伺服(或步进)电机驱动单元发出运动控制指令,伺服(或步进)电机通过机械传动构完成机床的进给运程序中的主轴起停、刀具选择、冷却、润滑等逻辑控制指令由CNC传送给机床电气控制
系统,由机床电气控制系统完成按钮、开关、指示灯、继电器、接触器等输入输出器件的控制。目前,机床电气控制通常采用可编程逻辑控制器(Programable Logic Controler 简称PLC),PLC具有体积小、应用方便、可靠性高等优点。由此可见,运动控制和逻辑控制是数控机床的主要控制任务。 GSK980TD车床CNC同时具备运动控制和逻辑控制功能,可完成数控车床的二轴运动控制,还具有内置式PLC功能。根据机床的输入、输出控制要求编写PLC程序(梯形图)并下载到GSK980TD,就能实现所需的机床电气控制要求,方便了机床电气设计,也降低了数控机床成本。 实现GSK980TD车床CNC控制功能的软件分为系统软件(以下简称NC)和PLC软件(以下简称PLC)二个模块,NC模块完成显示、通讯、编辑、译码、插补、加减速等控制,PLC模块完成梯形图解释、执行和输入输出处理。 1.3编程基本知识 1、坐标轴定义 数控车床示意图 GSK980TD使用X轴、Z轴组成的直角坐标系,X轴与主轴轴线垂直,Z轴与主轴轴线方向平行,接近工件的方向为负方向,离开工件的方向为正方向。
数控机床毕业论文
数控车床应用与发展前景 摘要 随着计算机技术的高速发展,现代制造技术不断推陈出新。在现代制造系统中,数控技术集微电子、计算机、信息处理、自动检测、自动控制等高新技术于一体,具有高精度、高效率、柔性自动化等特点,对制造业实现自动化、集成化、智能化、起着举足轻重的作用。 数控加工作为一种高效率高精度的生产方式,尤其就是形状复杂精度要求很高的模具制造行业,以及成批大量生产的零件。因此数控加工在航空业、电子行业还有其她各行业都广泛应用。然而在数控加工从零件图纸到做出合格的零件需要有一个比较严谨的工艺过程,必须合理安排加工工艺才能快速准确的加工出合格的零件来。
目录 摘要 前言 第一章数控车床的基本组成与工作原理1、1 任务准备 1、1、1 机床结构 1、2 工作原理 1、3 数控车床的分类 1、4 数控车床的性能指标 1、5 数控车床的特点 第二章数控车床编程与操作 2、1 数控车床概述 2、1、1数控车床的组成 2、1、2数控车床的机械构成 2、1、3数控系统 2、1、4数控车床的特点 2、1、5数控车床的分类 2、1、6数控车床(CJK6153)的主要技术 2、1、7数控车床(CJK6153)的润滑 2、2 数控车床的编程方法 2、2、1设定数控车床的机床坐标系
2、2、2设定数控车床的工件坐标系 第三章数控车床加工工艺分析 3、1 零件图样分析 3、2 工艺分析 3、3 车孔的关键技术 3、4 解决排屑问题 3、5 加工方法 第四章当前数控机床技术发展趋势 4、1 就是精密加工技术有所突破 4、2 就是技术集成与技术复合趋势明显 结束语语 参考文献 致谢 前言 高速加工技术发展迅速,在高档数控机床中得到广泛应用。应用新的机床运动学理论与先进的驱动技术,优化机床结构,采用高性能功能部件,移动部件轻量化,减少运动惯性。在刀具材料与结构的支持下,从单一的刀具切削高速加工,发展到机床加工全面高速化,如数控机床主轴的转速从每分钟几千转发展到几万转、几十万转;快速移动速度从每分钟十几米发展到几十米与超过百米;换刀时间从十几秒下降到10秒、3秒、1秒以下,换刀速
数控车床毕业设计
数控车床毕业设计
南京工程学院继续教育学院毕业论文典型轴类零件数控车削加工设计姓名:钱春花 学号:07323 专业:机电一体化 学历:大专 指导教师: 姜爱国
函授站:无锡交通高等职业技术学校 中国·南京 2012年5月 目录 前言(引言) 1.课题选择及说明 1.1 选题目标 1.2 课题说明 1.3图纸
2.加工内容和加工要求分析 2.1 加工结构及分布 2.2 加工要求分析 2.3 加工重点和难点分析 2.4加工内容和要求分析表 3.1加工方案设计初步考虑 3.1 加工过程设计 3.2 加工设计其它方案及优化4.加工设备选用 4.1机床选用: 4.2刀具选择 4.3夹具选用: 4.4量具 4.4工具清单 5.加工程序 6.操作加工要点 6.1加工准备 6.2工件加工 6.3对工件加工操作的改进 7.课题设计小结 7.1设计内容总结 7.2设计效果论证 7.4设计不足分析和可能的优化展望 7.3设计体会 参考文献资料
1.课题选择及说明 1.1 选题目标 通过典型轴零件数控车床加工设计,进一步提高工艺分析、工艺设计及工艺技术文件的编写、程序编写,提高综合数控加工技能。 是专业各门课程综合应用,提高专业能力。 设计与工作实际相结合,提高工作适应能力。 目的: 1、通过零件加工工艺设计进一步掌握零件加工的过程和每一步的加工要求,在设计过程中,充分利用在校所学内容,使之融会贯通,加深对所学内容的理解和掌握。 2、设计过程中必须认真考虑加工三要素的设定,它们是加工中最重要的三个参数。合理设置可以提高加工精度,缩短加工时间,节约生产成本。通过设计可以更深一点地理解并掌握三要素的设定方法。 3、设计中涉及了车断面、车外圆、车椭圆、镗孔、车内外螺纹等加工方式。通过对如上常用加工方式的工艺设计,熟悉了这些加工方式的加工特点,工艺设计的方法。 4、在此次设计过程中,肯定会遇到各种各样的困难,这也能提高我遇到问题解决问题的能力。对今后的工作以及生活都大有益处。 意义: 1、随着全国产业机械化的提高,相应的机械零件的加工精度要求也随之愈加严格,对零件加工工艺进行合理设计能更好的在现有的加工条件下使加工精度得以最大化。 2、在制造业要求“成本最低化,利益最大化”的大前提下,零件加工工艺也有充分的必要性。它可以缩短加工时间,提高生产效率,降低原材料的报废率,从另一方面讲,也有效的降低了工人们的劳动强度。
数控机床毕业论文1
辽宁建筑职业学院机械工程系 毕业论文 题目: 班级: 姓名: 学号:
目录 目录 (1) 摘要 (2) 一、绪论 (4) 二、数控机床概述 (4) (一)数控机的简介 (4) (二)数控机床的组成 (5) (三)数控技术的特点 (5) (四)数控机床的主要技术指标 (6) (五)数控机床使用中应注意的事项 (7) 三、数控机床各部故障分析及维修 (8) (一)数控机床主轴伺服系统故障检查及维修 (8) (二)机床PLC初始故障的诊断 (8) (三)数控设备检测元件故障及维修 (9) (四)数控机床加工精度异常故障及维修 (9) 四、数控机床的保养及维护 (9) (一)数控机床的保养知识 (10) (二)数控机床系统的维护 (11) (三)机械部件的维护 (12) 五、结论 (12) 参考文献 (14)
论文题目:附图:
摘要 机械制造业是国民经济的支柱产业,可以说,没有发达的制造业,就不可能有国家的真正繁荣和富强。而机械制造业的发展规模和水平,则是反映国民经济实力和科学技术水平的重要指标之一。制造自动化技术是先进制造技术的重要组成部分,其核心是数控技术。数控技术是综合应用计算机、自动化控制、自动检测及精密机械等高新技术的产物。它的出现及所带来得巨大效益,已引起了世界各国科技与工业界的普遍重视。数控维修技术不仅是保障数控机床正常运行的前提,对数控技术的发展和完善也起到了巨大的推动作用,因此,它已经成为一门专门的学科。同时也表明,数控维修技术是制造业竞争和发展的基础,也是机械制造业技术水平的标志。论文主要研究了根据数控机床的特点,数控机床常见的故障及诊断方法,数控机床的保养知识和讲解了数控车床的维修方法与注意的事项。研究结果表明:数控加工在当前制造行业中占据着主导地位,在各行各业中都有他的出现,它的发展将带动制造业的飞速发展,同时也将影响社会的发展进程。 因此,做好数控设备的维护工作,提高数控设备的维修效率,是现代制造业的—项重要工作本文的特色在于:通过分析数控机床的维修维护,提高了加工效率,最终为企业带来了效益。 关键词:数控技术;数控机床;常见故障;诊断方法;维修方法