应力集中分析
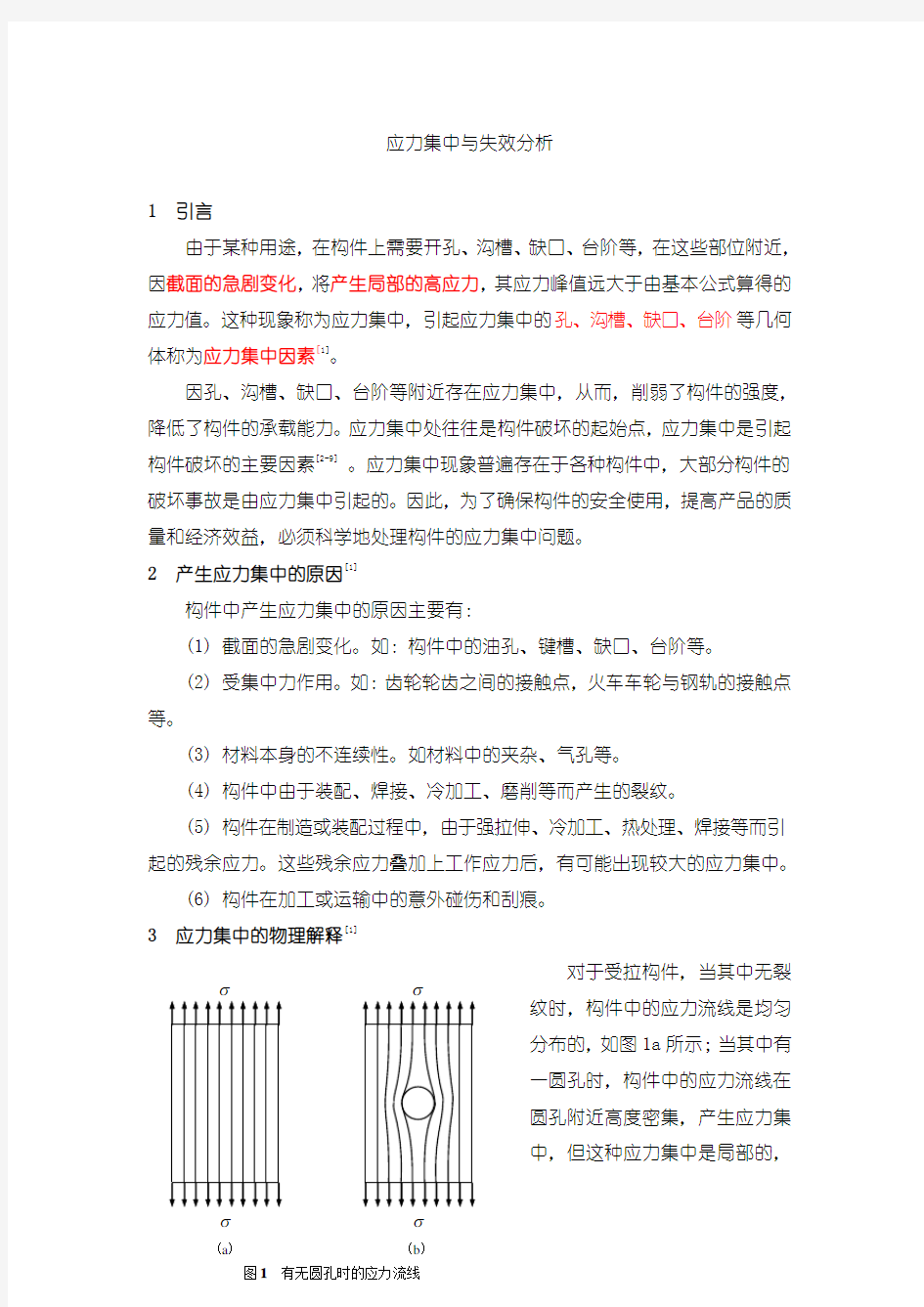
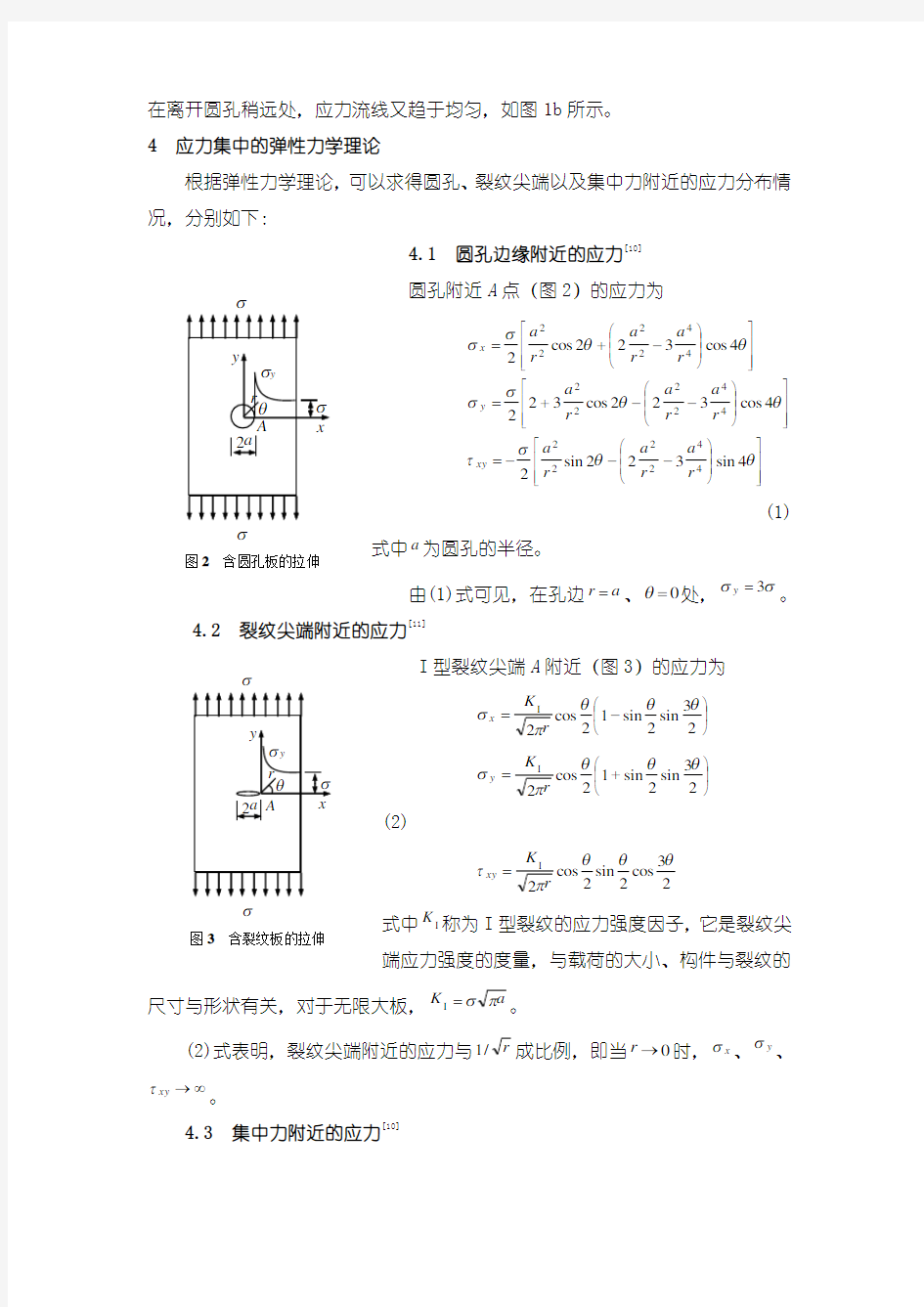
应力集中与失效分析
1 引言
由于某种用途,在构件上需要开孔、沟槽、缺口、台阶等,在这些部位附近,
因截面的急剧变化,将产生局部的高应力,其应力峰值远大于由基本公式算得的
应力值。这种现象称为应力集中,引起应力集中的孔、沟槽、缺口、台阶等几何
体称为应力集中因素[1]。
因孔、沟槽、缺口、台阶等附近存在应力集中,从而,削弱了构件的强度,
降低了构件的承载能力。应力集中处往往是构件破坏的起始点,应力集中是引起
构件破坏的主要因素[2-9]。应力集中现象普遍存在于各种构件中,大部分构件的
破坏事故是由应力集中引起的。因此,为了确保构件的安全使用,提高产品的质
量和经济效益,必须科学地处理构件的应力集中问题。
2 产生应力集中的原因[1]
构件中产生应力集中的原因主要有:
(1) 截面的急剧变化。如:构件中的油孔、键槽、缺口、台阶等。
(2) 受集中力作用。如:齿轮轮齿之间的接触点,火车车轮与钢轨的接触点
等。
(3) 材料本身的不连续性。如材料中的夹杂、气孔等。
(4) 构件中由于装配、焊接、冷加工、磨削等而产生的裂纹。
(5) 构件在制造或装配过程中,由于强拉伸、冷加工、热处理、焊接等而引
起的残余应力。这些残余应力叠加上工作应力后,有可能出现较大的应力集中。
(6) 构件在加工或运输中的意外碰伤和刮痕。
3 应力集中的物理解释[1]
对于受拉构件,当其中无裂Array纹时,构件中的应力流线是均匀
分布的,如图1a所示;当其中有
一圆孔时,构件中的应力流线在
圆孔附近高度密集,产生应力集
中,但这种应力集中是局部的,
在离开圆孔稍远处,应力流线又趋于均匀,如图1b 所示。
4 应力集中的弹性力学理论
根据弹性力学理论,可以求得圆孔、裂纹尖端以及集中力附近的应力分布情况,分别如下:
4.1 圆孔边缘附近的应力[10]
圆孔附近A 点(图2)的应力为 ???????????? ??---=???????????? ??--+=???????????? ??-+=θθστθθσσθθσσ4sin 322sin 24cos 322cos 3224cos 322cos 2442222442222
442222r a r a r a r a r a r a r a r a r a xy y x
(1)
式中a 为圆孔的半径。
由(1)式可见,在孔边a r =、0=θ处,σσ3=y 。
4.2 裂纹尖端附近的应力[11]
I 型裂纹尖端A 附近(图3)的应力为 ??? ??-=23sin 2sin 12cos 2I
θθθπσr
K x ??
? ??+=23sin 2sin 12cos 2I
θθθπσr K y (2)
23cos 2sin 2cos 2I
θ
θ
θ
πτr K xy =
式中I K 称为I 型裂纹的应力强度因子,它是裂纹尖端应力强度的度量,与载荷的大小、构件与裂纹的尺寸与形状有关,对于无限大板,a K πσ=I 。
(2)式表明,裂纹尖端附近的应力与r /1成比例,即当0→r 时,x σ、y σ、
∞→xy τ。
4.3 集中力附近的应力[10]
半无限体表面上受集中力作用(图4)时,受
力点A 附近的应力为 r F r F r F xy y x θθπτθθπσθπσ223cos sin 2cos sin 2cos 2=-=-=
(3) (3)式表明,受力点附近的应力与r /1成比例,即当0→r 时,x σ、y σ、∞→xy τ。
5 应力集中程度的表示方法[1]
工程上用应力集中系数来表示应力增高的程度。应力集中处的最大应力max σ与基准应力n σ之比,定义为理论应力集中系数,简称应力集中系数,即
n max
σσα= (4)
在(4)式中,最大应力max σ可根据弹性力学理论、有限元法计算得到,也可由实验方法测得;而基准应力n σ是人为规定的应力比的基准,其取值方式不是唯一的,大致分为以下三种:
(1) 假设构件的应力集中因素(如孔、缺口、沟槽等)不存在,以构件未减小时截面上的应力为基准应力。
(2) 以构件应力集中处的最小截面上的平均应力作为基准应力。
(3) 在远离应力集中的截面上,取相应点的应力作为基准应力。
6 重复应力集中[1]
两个应力集中因素相互重叠、共同作用引起的
应力集中,称为重复应力集中。例如,图5所示的
受拉板在圆孔边缘有一缺口,由圆孔产生的应力集
中因缺口的存在而进一步加剧,若缺口的尺寸与圆
孔的尺寸相比很小时,A 点的重复应力集中系数2
1,α可由圆孔的应力集中系数0.31=α与缺口的应力集中
系数09.32=α相乘得到,即18.92121=?=ααα,。
7 降低应力集中的方法[1]
工程中常用以下几种方法来降低应力集中程度:
7.1 修改应力集中因素的形状
(1) 用圆角代替尖角。将尖角改为圆角,能有效地缓和应力集中程度。一般来讲,圆角的曲率半径在可能的范围内愈大愈好。
(2) 采用流线形或抛物线形的表面过渡。有时圆角并不对应于最小的应力集中,如果采用流线形变化的截面,效果会更好。为了缩短流线形表面的变化长度,可以采用抛物线形表面过渡。
(3) 用椭圆孔代替圆孔。在保证构件正常工作的情况下,如果将圆孔改为椭圆孔,往往能提高构件的强度。例如,将图2所示的受拉平板中的圆孔改为椭圆孔,如图6所示,则椭圆孔边A 点的应力集中系数为
b a 21n max +==σσα (5)
当a b 2=时,由(5)式可得2=α,比圆孔(a b =)时的3=α降低了31/。由于椭圆孔难以加工,因此,工程上常简单地用两个圆弧来代替椭圆孔。
σσ
M
M
(a )(b )
图6 含椭圆孔板的拉伸 图7 圆孔的位置
对应力集中的影响
7.2 适当选择应力集中因素的位置
(1) 将应力集中因素选在构件中应力低的部位。例如,对于图7所示的纯弯梁,应尽量避免将圆孔设置在弯曲应力较大的截面边缘(图7a ),而应将其移到中性轴附近(图7b )。
(2) 使应力集中因素尽量远离构件的边界。例如,对于图8所示的有一圆孔
的有限宽受拉板,设圆孔的直径d 是板宽B 的51/,当圆孔在板的中心线上时(图8a ),A 点的应力集中系数5.2=α;当圆孔中心距板边为d 时(图8b ),1.3=α;当圆孔中心距板边为d 75.0时(图8c ),8.3=α。由此可见,当应力集中的位置位于构件的边界附近时,由于孔与边界相互干涉,会加剧应力集中的程度。
σσ
σσ
σσ
(a) (b)
(c)
图8 圆孔的位置对应力集中的影响
7.3 适当选择应力中集因素的方向
当受力构件中有椭圆孔、方孔、矩形孔、沟槽时,随着应力集中因素方向的改变应力集中系数将有很大的差异。例如,对于图9所示的有一椭圆孔的受拉板,
设椭圆孔的长短轴之比为4:1,当长轴与拉伸方向之间的夹角 0=θ时(图9a ),
A 点的应力集中系数5.1=α;当 45=θ时(图9b ),7.5=α;当 90=θ时(图9c ),0.9=α。
σ
σ σ
σ σ
σ
(a) (b)
(c)
图9 椭圆孔的方向对应力集中的影响
7.4 增加应力集中因素
一般来说,应力集中因素的存在将引起构件几何形状的不连续,产生应力集中。然而,如果有意识地增加某些新的应力集中因素,有时反而能使构件形状的改变有所缓和,从而降低应力集中。例如,对于图2所示的有一圆孔的无限大受拉板,A 点的应力集中系数3=α,若象图10所示那样在圆孔附近再增加一个同样大小的圆孔,则A 点的应力集中系数降低到63.2=α,原来的应力集中得到缓
和。
增加应力集中因素能使应力集中得以缓和,主
要是由于边界条件的不连续性得到改善。在增加应
力集中因素时,应适当选取它们之间的距离,以使
应力集中系数最小。减小应力集中因素的距离,对
缓和应力集中是有利的。间距过大,会使每个应力
集中因素以各自独立的形式产生应力集中,从而失去了增加应力集中因素的意义。
理论与实践都表明,应力集中发生在构件刚度急剧变化的部位。所以在构件截面突变的地方,除了用加大圆角来缓和应力集中外,另一种有效的措施是增加卸载槽。例如,对于图11a 所示的阶梯轴,A 处的刚度明显低于B 处,为了缓和刚度的剧变,除了加大圆角半径外,如图11b 所示在B 处开一卸载槽,能有效地降低应力集中。 A B A
B (a) (b)
图11 用卸载槽降低应力集中
7.5 表面削去法 在应力集中因素附近挖去构件表面一定厚度的
材料,降低这部分的刚度,可达到缓和应力集中的目的。
7.6 填充法
在构件的孔内填入由某种材料制成的柱销,也可以达到缓和应力集中的目的。这时在孔边缘产生的最大应力,随着构件与柱销材料的弹性模量1E 和2E 的比值而变。例如,对于图12所示的有一圆孔的受拉板,当12E E =时,A 点的应力集中系数由3下降到75.1;当12E E <时,降低应力集中的程度较小;当12E E >时,降低应力集中的效果最好。例如在铝制构件(GPa 751=E )中采用钢质柱销(GPa 2002=E ),则A 点的应力集中系数仅为3.1=α。
8 实例分析[4]
8.1 背景
黑龙江黑化集团股份有限公司的108kt/a 合成氨系统中的四台LG410/3型螺杆压缩机从1998年投入使用到2001年7月,曾发生7次转子折断事故(其中1999年3次,2001年4次),给企业造成了巨大的经济损失。
8.2 转子结构
该压缩机为无油润滑型,阳转子通过同步齿轮带动阴转子旋转,使阴阳转子不直接接触。为了降低排气温度并使转子和壳体不结垢,在压缩机入口处设有喷水装置。阳转子4齿,阴转子6齿。转子为组合式,主体材质为2Crl3,镶嵌部分材质为45钢,其结构如图13所示。
图13 转子结构 图14
转子折断截面形状
粗糙区
光滑区虚线为转子折断截面
8.3 事故经过
压缩机在运行过程中出现异常声响,用测振仪测试机体部分振动,显示振值高,达到μm 80。停车后盘车,机体部分发出咯噔-咯噔的金属碰撞声音。对压缩机解体,发现阴(阳)转子在图13所示的镶嵌截面处折断,未折断转子也在镶嵌截面处有明显裂纹或经着色探伤后发现有裂纹存在,阴转子同步齿轮防倒转齿断齿,阳转子同步齿轮与防倒转齿相啮合部位断齿。
8.4 前期处理过程
转子折断事故发生后,该公司组织相关人员会同设备制造厂对转子折断原因进行了分析。因为同步齿轮防倒转齿发生断齿,并且操作人员在之前的几次停车中发现转子有倒转情况,加之投产初期系统不稳定,开停车频繁,所以分析结果为:转子折断是因为倒转产生的。对此,该公司对机组进出口管路进行了几次改造。经过改造后,压缩机倒转的情况基本避免,但转子折断事故仍然继续发生,为此,该公司与生产厂进行了更深入的分析。
8.5 事故原因分析
转子折断截面形状如图14所示,断口分为两个区域:光滑区和粗糙区。光
滑区是因为在裂纹扩展过程中,裂
纹的两个侧面在交变载荷作用下,
时而压紧,时而分开,多次反复而
形成的;粗糙区呈颗粒状,是转子
突然折断形成的。该断口为典型的
疲劳断口。疲劳裂纹的形成主要在
应力集中的部位和构件表面。转子
折断截面处轴径变化最大,由230φ变为630φ,d D /达到74.2,应力集
中严重;转子与吸气侧壳体内壁间隙为24.1~02.1,与排气侧壳体内壁间隙为28.0~26.0,因此,该截面处圆角很小,应力集中严重;转子为镶嵌式结构,采用了较大的过盈配合,也造成该截面处应力集中严重;因为该截面处轴径变化大,圆角小,不易磨削加工,所以表面粗糙度较高,降低了材料的持久极限。在上述多种不利因素的共同作用下,
大大降低
图15 转子弯曲应力的径向力大小和波动情况
1.阴转子排气端径向力;
2.阳转子排气端径向力
3.阴转子吸气端径向力;
4.阳转子吸气端径向力
了材料的强度,使其持久极限远低于屈服极限。此截面成为转子的最危险截面。
螺杆压缩机转子的受力较复杂,图15示出了引起转子弯曲应力的径向力的大小和波动情况,从图中可以看出,阴转子上的径向力比阳转子大,排气端的径向力比吸气端大。这可能是在7次转子折断事故中,阴转子占5次的原因,在排气端折断超过吸气端的原因。压缩机开车时的起动力矩很大,是正常运转时的
1.5倍,而且变化突然,对压缩机转子尤其是应力集中部位的损坏很大。压缩机停车时发生倒转会损坏防倒转齿,防倒转齿断齿后,阴阳转子将直接接触,产生冲击载荷,对转子极为不利。
通过对转子的结构、表面质量、受力情况的综合分析,得出转子折断的主要原因是该截面处的应力集中过大和表面质量差,在足够大的交变应力作用下产生裂纹,裂纹逐渐扩展,截面逐步削弱,削弱到一定极限时,转子便突然断裂。辅助原因是频繁的开停车和倒转。
8.6 解决方法
由于该转子疲劳失效的主要原因是应力集
中程度高和表面质量差,因此,提高疲劳强度
就从减缓应力集中、提高表面质量入手。为了
减缓应力集中,在该截面轴根部车削一个8
r 的卸载槽,如图16所示。此卸载槽大大改善了
由过盈配合而引起的应力集中,同时使在该处
加工较大的圆角成为可能,使应力集中得到进一步缓和。为了提高该位置的表面质量,手工用油石对卸载槽进行打磨,消除一切刀痕和棱角。对折断后返回制造厂进行修复的转子,还要求对该位置进行表面强化处理,以提高疲劳强度。
8.7 解决效果
在对转子进行了上述处理后,从2001年7月至2005年9月,4台螺杆压缩机再也没有发生转子折断事故。在大修中对转子的该部位进行着色探伤,也没有发现裂纹存在。螺杆压缩机转子折断问题得到了圆满解决。
图16 转子卸载槽
基于弹性力学理论和有限元法分析应力集中问题的讨论
基于弹性力学理论和有限元法分析应力集中问题的讨论 材料在外形急剧变化的部位,局部应力可以超出名义应力的数倍,对于脆性材料局部过早开始破坏,从而,削弱了构件的强度,降低了构件的承载能力。因此在工程實际中,为了确保构件的安全使用,必须科学合理的分析计算应力集中现象,以便找寻到更好的避免措施。本文首先基于弹性力学理论分析带孔无限宽板的应力分布情况,将对象的受力转化成数学表达,结论应证了应力集中的几个特性。 标签:应力集中系数;有限元分析;无限宽板;弹性力学;Inventor运用;ANSYS 1、应力集中 1.1弹性力学中概念,指物体形状、材料性质不均匀导致的局部应力急剧增高的现象。 1.2应力集中系数 最大局部应力与名义应力的比值称为理论应力集中系数ɑ。可以明确地反应应力集中的程度。 最大局部应力σmax可根据弹性力学理论、有限元法计算得到,也可由实验方法测得;名义应力σn是假设构件的应力集中因素(如孔、缺口、沟槽等)不存在,构件截面上的应力。 2、孔周应力在理想状态下的弹性力学理论分析 2.1定义受单向均匀拉伸荷载的无限宽平板,孔径2α圆孔,建立如图一理想模型。 由于结构的对称性,仅分析图一上半段1/4部分x轴正向的状态: 1)圆孔右顶点单元,即当θ=0,r=α时,代入式(2)解算得σy=3σ; 2)距孔0.2倍孔半径外,即当θ=0,r=1.2α时,代入式(2)解算得σy=2.071σ; 3)距孔1倍孔半径外,即当θ=0,r=2α时,代入式(2)解算得σy=1.221σ; 4)距孔1.5倍孔半径外,即当θ=0,r=2.5α时,代入式(2)解算得σy=1.122σ; 5)距孔2倍孔半径外,即当θ=0,r=3α时,代入式(2)解算得σy=1.074σ;
峰值应力基本特性分析和讨论
2005年第4期 压力容器 峰值应力基本特性分析和讨论 丁伯民 (华东理工大学,上海200237) [摘要]对峰值应力是否仅是沿壁厚非线性分布的分量,是否都具有自限性进行分析、讨论。 [关键词]峰值应力;二次应力;非线性分量;自限性;应力集中系数;有限元 Fundamental Properties Analysis and Discussion for Peak Stress Ding Bomin (E ast China Univer sity of S cience and T echnology,S hanghai200237) [Abstract]T he problems of w hether the peak stress is the s tr ess component distributing along thickness in nonlinear and w h ether the peak stres s is self-lim itin g w ere analyz ed and discussed. [Keywords]peak stress,secondary stress,nonlinear component,s elf-limiting,factor of stress concentration,finite element 1前言 为制订我国的应力分析设计标准,从1983年讨论应力分析法容器设计规定讨论稿开始的二十余年来,对峰值应力仅是沿壁厚的非线性分布分量,其作用范围仅在壁厚的1/4范围以内,以及峰值应力和二次应力相同,其特征是具有自限性的表述,笔者一直提出异议。争议各方在国内外发表不同观点的文章至少有三、四十篇之多。全国化工设备设计技术中心站从去年开始,组织有关专家在杭、宁、沪三次进行座谈。 2有限元应用 将由三维有限元求得的总应力按照静力等效、等效力矩概念,仅把沿壁厚非线性分布部分划为峰值应力,把均布和线性分布部分划为P m(P L)或Q 的这一做法肯定是保守的。 由于峰值应力沿壁厚可以是均布、线性及非线性分布,所以如按这一方法划分,则就仅将沿壁厚非线性分布的分量从总应力中划出并划归为峰值应力,而将均布、线性分布的、原应属于峰值应力的分量划为P m(P L)或Q。在采用P m(P L)+P b+Q[3 [R]t进行校核时(不论要否疲劳分析,都要对这一强度范围进行校核),划为P m(P L)或Q的分量就加大了这一应力强度范围,从而使校核结果偏于保守。如以误划为P m(P L)、Q的峰值应力表示为P c m (P c L)、Q c,则其保守程度为[P m(P L)+P b+Q+P c m (P c L)、Q']/[P m(P L)+P b+Q]。以双向受R拉压平板上具有应力集中系数K=4的小圆孔或裂纹为例,由于总应力沿板厚基本上是均匀分布的,总应力K R中,P m=R,P b=0,Q=0,F=R(K-1),如将此沿壁厚均匀分布的峰值应力误划为P m,则其保守程度将达(P m+3P m)/P m=4,即增大了了三倍,应该说是保守了。 当然,压力容器中并无只有开孔而无接管的类似结构,但是和拉伸平板上小圆孔或裂缝相类似的例子却有的是,如对接接头处的咬边、余高、棱角值或错边等等,只是一般情况下对这种地方设计人员都只按规范规定,遵守有关的偏差要求,不大会去进行详细的应力分析,也不大会去用三维有限元计算罢了。但在遇到偏差超标时就要关注这些点了。已见到由日本购进的某冷凝器,发现环向接头错边超标,担心出事,用三维有限元进行应力分析,仅将总应力中沿壁厚非线性分量划为峰值应力进行评定,导致在设计和水压试验工况不合格,而实际上该冷凝器已完好运行2年的报导就是一例[1],又见到几例用ANSYS、NASTRAN软件对已满足GB150、T B4732所规定等面积补强方法的开孔接管,仅将总应力中沿壁厚的非线性分量划为峰值应力进行评定,得出大部不合格的结果则又是一例[2]。 3自限性问题 属于应力分析设计的ASMEⅧ-2,始终把材料、结构、设计计算(包括计算应力的方法和应力分类)、制造、检验、试验看作一个完整的整体,相互呼应,衔接、配合、协调,如改动其中任一者一定要注意是否会涉及到原与之相配合部分的脱节或矛盾。这里更 # 1 #
桩身应力测试分析报告
精心整理第一章工程概况
根据**院提供的岩土工程勘察报告,该场地工程地质条件如下:
三、检测桩位示意图 四、钢筋应力计在桩身埋设位置示意图 钢筋应力计在各试桩中位置示意图
二、测试设备及钢筋测力计的埋设 1、每桩钢筋应力计设置在各土层交界面处,每一个截面设2只钢筋测力计(基本呈180°对称布置),各钢筋应力计埋设截面的平、剖面图如前图; 2、JTM-V1000振弦式钢筋应力计采用焊接法固定在钢筋笼主筋上,并与桩身纵轴线平行;
3、连接在应力计的电缆线用柔性材料保护,绑扎在钢筋笼内侧并 引至地面; 4、所有应力计均用明显标记编号; 5、仪器设备:检测仪器设备采用JTM-V1000振弦式钢筋应力计、JTM-V10B 型频率读数仪、集线箱等组成。 三、测试原理 1位2ε c1j = εεs1j 3E cj 、E sj —砼弹性模量、钢筋弹性模量[E s 取2.0×108(kPa)] A cj 、A sj —同一截面处砼面积、钢筋总面积。 εcj 、εsj —同一截面处砼与钢筋的应变 4、钢筋应力计受力的计算公式: ) 2()(' 2 02 ----------------??=-?=Si Sij S i ij Sij A E F F k P ε
式中: P Sij —第i 量测截面处在j 级荷载下应力计所受轴向力(kN ) F ij —第i 量测截面处在j 级荷载下应力计的实测频率值(Hz) F i0—i 截面处钢筋应力计的初始频率值(Hz ) K A si ’—56f ij P ij —i A i 12、弦式钢筋应力计宜放在两种不同性质土层的界面处,以测量桩在不同土层中的分层摩阻力。在地面处(或以上)应设置一个测量断面作为钢筋应力计传感器标定断面。钢筋应力计埋设断面距桩顶和桩底的距离不宜小于1倍桩径。在同一断面处对称设置2个钢筋应力计。钢筋计应按主筋直径大小选择。仪器的可测频率范围应大于桩在最大加载时的频率的1.2倍; 3、使用前应对钢筋计逐个标定,得出压力(拉力)与频率之间的关系。带有接长 ) 3()(' -------------------------?= Si S Sij Sij A E P ε
含孔复合材料层板的力学性能研究
第25卷2006年第9期 9月 机械科学与技术 MECHANICALSCIENCEAND7IECHNOLOGY V01.25No.9 september2006 朱西平文章编号:1003-8728(2006)09-1126JD4 含孔复合材料层板的力学性能研究 朱西平,毛坤,韩小平,岳珠峰 (西北工业大学,西安710072) 摘要:对复合材料开口缝合补强结构进行了实验研究,测试了不同缝合参数(针距、行距、边距、单重和双重缝合)补强对含孔复合材料层板的破坏强度,研究了孔边应力集中和缝合补强对强度、模量等力学性能参数的影响,分析讨论了孔边及邻近区域应变集中及应变分布的规律,通过实验结果和分析讨论,对复合材料开口缝合补强结构提出合理的设计方法。 关键词:含孔复合材料层板;缝合补强;应变集中;缝合参数 中图分类号:TB33文献标识码:A AStudyofU舱MecllanicalPropemesofComp嬲溉L锄疵mt姻稍nIIIoles ZhuXiping,MaoKun,HanXiaoping,YueZhufeng (Non}1westemPolytechnicalUnivers毋,Xi’an710072) Abs仃act:nepapercarTiedoutanexperimentalstudyofstitchingreinforcementforcompositelaIIlinateswimholes.Thedamaqgetostitching parameters suchasstitchingneedledistance,IDwspace,edgedis-tance,sindestitchingordoublestitchingto出ecompositel锄inateswastested.TheillnuenceofthestI-essconcentrationneartlleholeregionandthestitchingreinforcementontllemechanicalpropeniessuchasstreng山andmoduluswasstudied.Thelawsofthestressconcentrationanddistributionwereinvestiga—tedanalyticallyandexperimentally.Theexperimentalresultsshowedadistincteffbctofstitchingrein—forcementoncompositelaminateswi山holes,forwhichareasonabledesignme山odwaspresented. KeywOrds:compositelaminatewit}lholes;stitchingreinforcement;sn.essconcen臼阻tion;stitchingpa—ranleter 工程实际中,复合材料的应用日益增多,由于结构装配或功能方面的需求,常常需要在复合材料层板上打孔或开口,承载时这些局部区域引起的应力集中对复合材料结构的承载能力、使用寿命可能会产生严重影响。因此,研究复合材料层合结构的开口处应力集中问题,具有工程实际意义。 Fu-Kuochang和LarryB.kssaId¨“o分别从理论分析、有限元数值计算和实验方面比较系统地研究了含孔洞层合板承受拉伸、压缩载荷时损伤、失效和破坏情况,提出一种损伤累积模型进行应力分析和破坏分析,并建立了噙孔洞层合板失效模型和破坏准则。kifcallsson瞪3采用三维有限元方法研究含孑L层合板的层间应力和损伤,给出沿厚度方向的法向应力分布,计算结果表明,在铺层界面和自由 收稿日期:2005—09—28 作者简介:朱西平(1957一),男(汉),陕西,副教授 E—mail:呷口甲@Tw巾u.edu.cn边缘上存在高的层间应力梯度。D.Amla和M.L.Mccain[61对含孔石墨/环氧层合板实施拉伸实验,得到含孔拉伸试件的表观应力集中因子,并采用声发射监控试件的破坏过程。Hwai-ChllIIgwll和BinMu¨’基于正交各向异性含孔板的应力集中因子计算公式,推广应用到双向加载含孔板以及受轴向载荷或内压的含孔圆柱,结合有限元数值计算,讨论了结构尺寸及其它因素对应力集中的影响。 王启智等睇“21分别采用了半解析半经验方法和有限元数值计算方法,推导出拉伸正交各向异性有限宽板偏心圆孔的应力集中系数表达式、有限域中高精度应力集中系数表达式以及带圆孔的有限宽板的动态应力集中系数表达式。 本文对复合材料开口缝合补强结构进行了实验研究,测试了不同缝合参数(针距、行距、边距、单重和双重缝合)补强的含孔复合材料层板的拉伸强度,研究了孔边应力集 中和缝合补强对强度、模量等力学性能参数的影响,分析讨 万方数据
管道应力分析基础知识
管道应力分析基础知识 2009-04-09 13:55 1. 进行应力分析的目的是 1) 使管道应力在规范的许用范围内; 2) 使设备管口载荷符合制造商的要求或公认的标准; 3) 计算出作用在管道支吊架上的荷载; 4) 解决管道动力学问题; 5) 帮助配管优化设计。 2. 管道应力分析主要包括哪些内容?各种分析的目的是什么? 答:管道应力分析分为静力分析和动力分析。 1) 静力分析包括: (l)压力荷载和持续荷载作用下的一次应力计算――防止塑性变形破坏; (2)管道热胀冷缩以及端点附加位移等位移荷载作用下的二次应力计算――防止疲劳破坏; (3)管道对设备作用力的计算――防止作用力太大,保证设备正常运行; (4)管道支吊架的受力计算――为支吊架设计提供依据; (5)管道上法兰的受力计算――防止法兰泄漏; (6)管系位移计算――防止管道碰撞和支吊点位移过大。 2) 动力分析包括: (l)管道自振频率分析――防止管道系统共振; (2)管道强迫振动响应分析――控制管道振动及应力; (3)往复压缩机气柱频率分析――防止气柱共振; (4)往复压缩机压力脉动分析――控制压力脉动值。 3. 管道应力分析的方法 管道应力分析的方法有:目测法、图表法、公式法、和计算机分析方法。选用什
么分析方法,应根据管道输送的介质、管道操作温度、操作压力、公称直径和所连接的设备类型等设计条件确定。 4. 对管系进行分析计算 1) 建立计算模型(编节点号),进行计算机应力分析时,管道轴测图上需要提供给计算机软件数据的部位和需要计算机软件输出数据的部位称作节点: (1)管道端点 (2)管道约束点、支撑点、给定位移点 (3)管道方向改变点、分支点 (4)管径、壁厚改变点 (5)存在条件变化点(温度、压力变化处) (6)定义边界条件(约束和附加位移) (7)管道材料改变处(包括刚度改变处,如刚性元件) (8)定义节点的荷载条件(保温材料重量、附加力、风载、雪载等) (9)需了解分析结果处(如跨距较长的跨中心点) (10) 动力分析需增设点 2) 初步计算(输入数据符合要求即可进行计算) (1) 利用计算机推荐工况(用CASWARII计算,集中荷载、均布荷载特别加入) (2) 弹簧可由程序自动选取 (3) 计算结果分析 (4) 查看一次应力、二次应力的核算结果 (5) 查看冷态、热态位移 (6) 查看机器设备受力 (7) 查看支吊架受力(垂直荷载、水平荷载) (8) 查看弹簧表
平面应力集中因素之分析
中华大学 专题报告 平面应力集中因素之分析Analysis of plane stress concentration factors 学系别:机械工程学系 学号姓名:I10406051 陈智峰 学号姓名:I10406052 林筠贵 学号姓名:I10406055 胡水泉 学号姓名:I10406046 陈毅 指导教授:陈精一博士 2016年6月
中文摘要 随着人类物质生活水平以及全球工业产品质量水准的提高,对于产品不仅仅只是在需求方面,更注重于产品的质量问题。而高水平制造出的工业产品,不仅体现在材料的性能上,也偏重于材料尺寸设计的最优化。运用计算机辅助分析软体所得出的结论进而判别是否符合设计标准,是提高工业产品生产效率和降低制造成本的关键。所以,对于一个高标准的产品来说,以合理化的尺寸设计来降低应力集中造成的结构破坏是提高产品制造水准的基础。而如何设计出合理化的产品尺寸,减少应力集中。就是吾人此次要探讨的问题之一——应力集中因素分析,本次研究采用单一变量法进行探讨材料的尺寸参数与应力集中因素的相关性,通过实验数据进行画图分析,再利用线性相关法进行处理并得出相关结论。 关键词:应力集中因素材料合理化设计单一变量法 ABSTRACT With the level of human material life and the global industrial product quality standards, the product is not only in terms of demand, but also focus on the quality of products. And the high level of industrial products produced, not only reflected in the performance of the material, but also emphasis on the optimization of the material size design. So, for a high standard product, the reasonable size design is the basis of improving the level of product manufacturing. And how to design the reasonable size of the product. I this is to explore the problem of stress concentration factor, this study using a single variable method to explore the size parameters of the material and the relevance of stress concentration factors. Through experimental data for drawing analysis. Using the linear correlation method for processing and draws the related conclusion.
应力集中分析
应力集中与失效分析 刘一华 (合肥工业大学土木建筑工程学院工程力学系,安徽合肥 230009) 1 引言 由于某种用途,在构件上需要开孔、沟槽、缺口、台阶等,在这些部位附近, 因截面的急剧变化,将产生局部的高应力,其应力峰值远大于由基本公式算得的 应力值。这种现象称为应力集中,引起应力集中的孔、沟槽、缺口、台阶等几何 体称为应力集中因素[1]。 因孔、沟槽、缺口、台阶等附近存在应力集中,从而,削弱了构件的强度, 降低了构件的承载能力。应力集中处往往是构件破坏的起始点,应力集中是引起 构件破坏的主要因素[2-9]。应力集中现象普遍存在于各种构件中,大部分构件的 破坏事故是由应力集中引起的。因此,为了确保构件的安全使用,提高产品的质 量和经济效益,必须科学地处理构件的应力集中问题。 2 产生应力集中的原因[1] 构件中产生应力集中的原因主要有: (1) 截面的急剧变化。如:构件中的油孔、键槽、缺口、台阶等。 (2) 受集中力作用。如:齿轮轮齿之间的接触点,火车车轮与钢轨的接触点 等。 (3) 材料本身的不连续性。如材料中的夹杂、气孔等。 (4) 构件中由于装配、焊接、冷加工、磨削等而产生的裂纹。 (5) 构件在制造或装配过程中,由于强拉伸、冷加工、热处理、焊接等而引 起的残余应力。这些残余应力叠加上工作应力后,有可能出现较大的应力集中。 (6) 构件在加工或运输中的Array意外碰伤和刮痕。 3 应力集中的物理解释[1] 对于受拉构件,当其中无裂 纹时,构件中的应力流线是均匀 分布的,如图1a所示;当其中有
一圆孔时,构件中的应力流线在圆孔附近高度密集,产生应力集中,但这种应力集中是局部的,在离开圆孔稍远处,应力流线又趋于均匀,如图1b 所示。 4 应力集中的弹性力学理论 根据弹性力学理论,可以求得圆孔、裂纹尖端以及集中力附近的应力分布情况,分别如下: 4.1 圆孔边缘附近的应力[10] 圆孔附近A 点(图2)的应力为 ???????????? ??---=???????????? ??--+=???????????? ??-+=θθστθθσσθθσσ4sin 322sin 24cos 322cos 3224cos 322cos 2442222442222 442222r a r a r a r a r a r a r a r a r a xy y x (1) 式中a 为圆孔的半径。 由(1)式可见,在孔边a r =、0=θ处,σσ3=y 。 4.2 裂纹尖端附近的应力[11] I 型裂纹尖端A 附近(图3)的应力为 ??? ??-=23sin 2sin 12cos 2I θθθπσr K x ?? ? ??+=23sin 2sin 12cos 2I θθθπσr K y (2) 23cos 2sin 2cos 2I θ θ θ πτr K xy = 式中I K 称为I 型裂纹的应力强度因子,它是裂纹尖端应力强度的度量,与载荷的大小、构件与裂纹的尺寸与形状有关,对于无限大板,a K πσ=I 。 (2)式表明,裂纹尖端附近的应力与r /1成比例,即当0→r 时,x σ、y σ、 ∞→xy τ。
基于元ANS的压力容器应力分析报告
压力容器分析报告
目录 1 设计分析依据 0 1.1 设计参数 0 1.2 计算及评定条件 0 1.3 材料性能参数 0 2 结构有限元分析 (1) 2.1 理论基础 (1) 2.2 有限元模型 (1) 2.3 划分网格 (1) 2.4 边界条件 (2) 3 应力分析及评定 (2) 3.1 应力分析 (2) 3.2 应力强度校核 (2) 4 分析结论 (3) 4.1 上封头接头外侧 (4) 4.2 上封头接头内侧 (5) 4.3 上封头壁厚 (7) 4.4 筒体上 (9) 4.5 筒体左 (10) 4.6 下封头接着外侧 (12) 4.7 下封头壁厚 (14)
1 设计分析依据 (1)压力容器安全技术监察规程 (2)JB4732-1995 《钢制压力容器-分析设计标准》-2005确认版 1.1 设计参数 表1 设备基本设计参数 1.2 计算及评定条件 (1)静强度计算条件 表2 设备载荷参数 载荷进行计算,故采用设计载荷进行强度分析结果是偏安全的。 1.3 材料性能参数 材料性能参数见表3,其中弹性模型取自JB4732-95表G-5,泊松比根据JB4732-95的公式(5-1)计算得到,设计应力强度分别根据JB4732-95的表6-2、表6-4、表6-6确定。 表3 材料性能参数性能
2 结构有限元分析 2.1 理论基础 传统的压力容器标准与规范,一般属于“常规设计”,以弹性失效准则为理论基础,由材料力学方法或经验得到较为简单的适合于工程应用的计算公式,求出容器在载荷作用下的最大主应力,将其限制在许用值以内,即可确认容器的壁厚。对容器局部区域的应力、高应力区的应力不做精细计算,以具体的结构形式限制,在计算公式中引入适当的系数或降低许用应力等方法予以控制,这是一种以弹性失效准则为基础,按最大主应力理论,以长期实践经验为依据而建立的一类标准。 塑性理论指出,由于弹性应力分析求得的各类名义应力对结构破坏的危险性是不同的,随着工艺条件的苛刻和容器的大型化,常规设计标准已经不能满足要求,尤其是在应力集中区域。若不考虑应力集中而只按照简化公式进行设计,不是为安全而过分浪费材料就是安全系数不够。基于各方面的考虑,产生了“分析设计”这种理念。采用以极限载荷、安定载荷和疲劳寿命为界限的“塑性失效”与“弹性失效”相结合的“弹塑性失效”准则,要求对容器所需部位的应力做详细的分析,根据产生应力的原因及应力是否有自限性,分为三类共五种,即一次总体薄膜应力( Pm) 、一次局部薄膜应力( Pc) 、一次弯曲应力( Pb) 、二次应力( Q) 和峰值应力( F) 。 对于压力容器的应力分析,重要的是得到应力沿壁厚的分布规律及大小,可采用沿壁厚方向的“校核线”来代替校核截面。而基于弹性力学理论的有限元分析方法,是一种对结构进行离散化后再求解的方法,为了获得所选“校核线”上的应力分布规律及大小,就必须对节点上的应力值进行后处理,即应力分类,根据对所选“校核线”上的应力进行分类,得出各类应力的值,若满足强度要求,则所设计容器是安全的。 按照JB4732-1995进行分析,整个计算采用ANSYS13.0软件,建立有限元模型,对设备进行强度应力分析。 2.2 有限元模型 由于主要关心容器开孔处的应力分布规律及大小,为减少计算量,只取开孔处作为分析对象,且取其中较为关心的大孔进行分析校核。分析设计所用的几何模型如图1所示。在上下封头和筒体之间存在不连续的壁厚,由于差距和影响量较小,此处统一采用上下封头的设计厚度。 图1 压力容器模型 2.3 划分网格 在结构的应力分析中,采用ANSYS13.0中的solid187单元进行六面体划分,如图2所示。图3~图5
复合材料整体成型关键技术现状分析研究
复合材料整体成型关键技术现状分析研究 摘要:复合材料具有减轻结构重量,适合整体成型,提升结构安全性,降低生产成本等诸多优势,目前复合材料已经成为航空工业的研究热点,未来航空市场的竞争,很大一部分也是先进复合材料应用的竞争,目前在这块市场上,我国的基础实力较为薄弱,而发达国家对于先进的复合材料技术对我国高度保密,因此充分利用专利信息,研究复合材料整体成型技术的发展现状具有非常重要的意义。本文从专利的角度对航空复合材料整体成型技术的应用进行了分析,并从几个关键技术点上进行重点专利分析,以期能给复合材料的研发应用提供指导。 关键词:复合材料自动铺放液态成型热压罐真空袋挤压成型 中图分类号:tb33 文献标识码:a 文章编号: 1674-098x(2011)12(a)-0000-00 复合材料整体成型技术正广泛的应用在航空航天及其他技术领域,由于复合材料的整体成型具有降低制造成本,减轻结构重量,提升航天器的经济环保性等诸多优点。飞机上的复合材料使用量已经成为衡量其先进性的重要标准[1]。 飞机设计领域向来有为减轻每1g重量而奋斗的原则,因此发展复合材料成型技术的符合民机技术发展的趋势,也反映了目前低碳节能,绿色环保的飞机设计理念的要求。
目前如空客公司的a350,波音公司的b787的复合材料的用量已经达到了50%。当前各国都将先进复合材料制造技术作为研发重点,而从“产品未动,专利先行”的角度出发,大量复合材料技术都可以在专利文献中找到,因此积极利用专利信息开展现状分析,挖掘具有借鉴价值的专利具有十分积极的意义。 1复材整体成型技术发展概况 现代先进复合材料起源于20世纪60年代,70年代复合材料开始应用在飞机结构上,复合材料的加入对飞机结构轻质化、模块化起着中重要的作用。近年来先进复合材料在现代飞机上的用量不断扩大,已经成为铝,钢、钛之外的第四大航空结构材料[2]。复合材料整体成型技术经过了几个阶段的发展,已经逐渐从次承力件过度到主承力件,波音空客两大民机巨头在民机市场竞争 日趋激烈,在复合材料方面也不断抢占技术制高点,推出的机型中无一不把提高复合材料用量作为经济性,先进性的象征性指标。从专利领域来看,近几年两大航空企业的复合材料相关专利的申请量也在不断剧增,波音公司凭借其一直以来在复合材料应用领域的雄厚基础,申请了大量极具技术价值的基础专利,同时针对这些基础专利不断进行改进形成新的专利申请。空客公司作为后起竞争者凭借欧洲航空工业在复材领域的雄厚基础,不断进行大胆创新,在该领域申请的大量的专利也大有后来居上的态势。可见现代民机企业都在不遗余力的提升复合材料的研发力度。 当前复合材料的成型技术主要包括真空袋-热压罐成型技术,自
ANSYS静力学分析APDL建模实例-应力集中
计算分析模型如图所示, 习题文件名: scf 材料参数:E=205GPa, v = 0.3 力载:4500N 注意单位的一致性:使用N, mm, MPa单位制 建模教程 在ANSYS工作文件夹新建“stress concentration factor”目录,以存放模型文件。 注意定期保存文件,注意不可误操作,一旦误操作,不可撤销。 1.1 进入ANSYS 开始→程序→ANSYS 14.5→Mechanical APDL Product Launcher14.5→然后在弹出的启动界面输入相应的working directory及文件名scf 如通过Mechanical APDL 14.5进入,则进入预设的working directory working directory必须设置在电脑最后一个分区(因为教学用电脑只有最后一个分区不受系统保护) 至此ANSYS静力学分析模块启动,ANSYS在“stress concentration factor”目录下自动创建了.log、.err等必要的文件。 2.2设置计算类型 ANSYS Main Menu: Preferences →select Struct ural → OK 2.3选择单元类型 ANSYS Main Menu: Preprocessor →Element Type→Add/Edit/Delete →Add →select Solid Quad 4 node 182 →OK (back to Element Types window)→
Options… →select K3: Plane Strs w/thk →OK→Close (the Element Type window) 2.4定义实常数 ANSYS Main Menu: Preprocessor →Real Constants →Add/Edit/Delete →Add →OK
CAE应力集中问题的考察
应力集中问题的考察---无倒角情况 前面考察了一个应力集中的问题。算例表明,当台肩处没有倒角时,在台肩处存在应力集中,且用有限元无法得到真实的应力解。 这里再考察一个类似的例子如下图。该结构左边固定,而在下面直线上施加竖直向下的分布力系,现在逐渐加密网格,考察台肩处应力值的改变。 (1)使用5mm的单元尺寸对该面进行网格划分 得到的有限元模型如下 计算结束后,绘制该面的米塞斯应力云图如下,此时,固定端的上下边沿显现出最大值。 (2)使用2mm的单元尺寸对该面进行网格划分 得到的有限元模型如下
计算结束后,绘制该面的米塞斯应力云图如下,此时,固定端的上下边沿显现出最大值,但应力值上升。 (3)使用1mm的单元尺寸对该面进行网格划分 得到的有限元模型如下 计算结束后,绘制该面的米塞斯应力云图如下,此时,应力最大值点已经转移到台肩处,应力大幅度增加。 (4)继续使用1mm的单元尺寸对该面进行网格划分,但是对上述应力最大值点局部加密网格。 得到的有限元模型如下
计算结束后,绘制该面的米塞斯应力云图如下,此时,应力最大值点仍旧在台肩处,应力暴增。 (5)继续使用1mm的单元尺寸对该面进行网格划分,但是对上述应力最大值点局部加密网格第二次。 得到的有限元模型如下 计算结束后,绘制该面的米塞斯应力云图如下,此时,应力最大值点仍旧在台肩处,应力继续暴增。 5)继续使用1mm的单元尺寸对该面进行网格划分,但是对上述应力最大值点局部加密网格第三次。 得到的有限元模型如下
计算结束后,绘制该面的米塞斯应力云图如下,此时,应力最大值点仍旧在台肩处,应力以几倍的速度上升,结果已经毫无意义。 【评论】 ?有限元软件无法计算尖锐转角处的应力。 ?CAE分析中,如果我们得到的模型中存在尖锐转角,那么一定要高度警惕,需要仔细询问该模型是否已经经过了简化。 ?如果我们得到了一个尖锐转角的模型,而又确信该处并非我们所关注的地方,那么在计算时,就不要对此处加密网格,而只是在我们所关心的地方加密网格。 ?如果我们得到的是有倒角的模型,那么当我们对之做简化而删去倒角时,一定要谨慎。 这可能会导致计算中的应力无限增大,此时我们会得到虚假的结果,从而导致误判。 应力集中问题的考察--倒斜角情况 前面两篇文章考察了没有倒角情况下的应力集中问题。结果表明,当没有倒角时,台肩处应力会无限增大,因此有限元无法计算此处的应力。 在机械零件中,经常使用倒斜角的情况,那么,有限元软件能够对此处的应力进行正确计算吗? 我们使用了一个例子如下。该轴是一个阶梯轴,在截面变化处有一个45度的斜角。该轴的左端面固定,而右端面施加1MPa的分布拉伸载荷,现在我们考察轴肩处的应力情况。
压力容器应力分析报告模板
目录 前言 (3) 1 设计参数 (4) 1.1 基本设计参数 (4) 1.2 设备简图 (5) 1.3 管口载荷参数 (6) 1.4 主要材料参数 (7) 2 分析步骤 (7) 2.1 主体受压元件 (8) 2.2 上封头组件 (9) 2.3 下锥壳组件 (16) 2.4 容器法兰 (21) 3 分析结果及应力评定 (23) 3.1 上封头组件 (23) 3.2 下锥壳组件 (28) 4 疲劳评定 (32) 4.1 交变载荷状态下应力分布云图 (32) 4.2 疲劳评定 (34) 5 结论 (36)
前言 本分析报告仅适用于xxxx,分析采用ANSYS软件,材料、应力分类及 评定按JB4732-1995《钢制压力容器—分析设计标准》(2005年确认)执行。 本分析报告中所有分析模型均取自“XXX”施工图(图号:XXXX)。 模型结构为连续结构,要求模型中所对应的焊接接头结构为全熔透结 构形式。 说明: 1、风载荷及地震载荷引起的应力强度变化很小,可不考虑; 2、S IV应由操作载荷计算得到,本分析报告按设计载荷计算求得,结果偏于保守(安全); 3、S IV控制值3S m t中的S m t应取工作载荷中最高、最低温度下的平均值,本分析报告中S m t按设计温度下取值,结果偏于保守(安全); 4、筒体和椭圆封头厚度在2.1节按JB4732第7章的公式计算,所以在 应力分析部分S I值不必再评定; 5、水压试验时容器任何点的液柱静压力未超过试验压力的6%,该容 器可不进行水压试验时的强度校核;水压试验次数(20次)远小于正常操 作时的设计循环次数(4.4×106),因此可省略水压试验的疲劳分析评定。
应力集中的分析
1.应力集中的现象及概念 材料在交变应力作用下发生的破坏称为疲劳破坏。通常材料承受的交变应力远小于其静载下的强度极限时,破坏就可能发生。另外材料会由于截面尺寸改变而引起应力的局部增大,这种现象称为应力集中。对于组织均匀的脆性材料,应力集中将大大降低构件的强度,这在构件的设计时应特别注意。 承受轴向拉伸、压缩的构件,只有在寓加力区域稍远且横截面尺寸又无急剧变化的区域内,横截面上的应力才是均匀分布的。然而工程中由于实际需要,某些零件常有切口、切槽、螺纹等,因而使杆件上的横截面尺寸发生突然改变,这时,横截面上的应力不再均匀分布,这已为理论和试验所证实。 如图 2-31[a] 所示的带圆孔的板条,使其承受轴向拉伸。由试验结果可知 : 在圆孔附近的局部区域内,应力急剧增大,而在离开这一区域稍远处,应力迅速减小而趋于均匀( 图 2 — 31[b]) 。这种由于截面尺寸突然改变而引起的应力局部增大的现象称为应力集 中。在 I — I 截面上,孔边最大应力与同一截面上的平均应力之比,用表示 称为理论应力集中系数,它反映了应力集中的程度,是一个大于 1 的系数。而且试验结果还表明 : 截面尺寸改变愈剧烈,应力集中系数就愈大。因此,零件上应尽量避免带尖角的孔或槽,在阶梯杆截面的突变处要用圆弧过渡。
在静荷作用下,各种材料对应力集中的敏感程度是不相同的。像低碳钢那样的塑性材料具有屈服阶段,当孔边附近的最大应力达到屈服极限时,该处材料首先屈服,应力暂时不再增大。如外力继续增加,增加的应力就由截面上尚未屈服的材料所承担,使截面上其它点的应力相继增大到屈服极限,该截面上的应力逐渐趋于平均,如图2-32 所示。因此,用塑性材料制作的零件,在静荷作用下可以不考虑应力集中的影响。而对于组织均匀的脆性材料,因材料不存在屈服,当孔边最大应力的值达到材料的强度极限时,该处首先断裂。因此用脆性材料制作的零件,应力集中将大大降低构件的强度,其危害是严重的。这样,即使在静载荷作用下一般也应考虑应力集中对材料承载能力的影响。然而,对于组织不均匀的脆性材料,如铸铁,其内部组织的不均匀性和缺陷,往往是产生应力集中的主要因素,而截面形状改变引起的应力集中就可能成为次要的了,它对构件承载能力不一定会造成明显的影响。 要想搞明白这个问题,我想先要搞明白什么是荷载力、什么是应力?简单地来说荷载力来源于动力源作用于工作终端,其力的大小为工作终端负荷加传动损耗,而应力则是由材料内部的分子发生错位(部分分子受拉力或热力作用其分子链被拉长、而有些分子则受压缩力或冷凝力的作用其分子被压缩,同时这两种变形的分子又相互作用在其过渡区域就会受两种作用力的影响,分子链也会受到破坏产生裂纹)而产生的作用力。人们在生产实践中发现材料在受力情况下都会发生变形,其变形量与受力的大小及受力的区城大小有关,卸载后的剩余应力与局剖的变形量成正比,对台阶轴而言若不加任何措施、由于作用区域小其作用力仅在轴的圆周面上产生作用,轴芯部分并不受力,这种现象本人称它为集肤效应。因此此时的轴肩处的圆周面受到剪切变形,分子链相继受到破坏并向轴芯延伸最终导至轴颈断裂。若在轴肩处采用圆弧过度等措施,相对来说增加了作用区域(两作用力之间的距离增加,材料所允许的扭转角度就变大,随着轴的扭转角度的增加使得轴芯部分有更多的分子链来参加传递动力,这样每个分子链的负荷也就变小很多,轴的寿命也得以延长,值得注意的是这并不意味着此轴可永久使用,因为材料在受力的情况下都会受损,只不过程度不同,程度大的寿命短、程度小的寿命长,这也就是人们常说的疲劳寿命。 现在再来解释过盈配合为什么在边缘处产生应力集中? 因为是过盈,所以内外圈在接触表面都要产生变形,而不接触的其它表面不会变形。这样接触面区域是压应力,而在接触边缘处轴的材料必然出现拉应力以阻止轮毂边缘和接触区外的材料进一步变形。但配合面的母线是直线,在外力作用下必然要产生相同的变形量,为了协
应力集中与失效分析
应力集中与失效分析 一、引言 由于构造和使用等方面的需要,往往需要在构件上开孔、沟槽、缺口、台阶等,然而,在这些部位附近,因截面尺寸的急剧变化,将产生局部的高应力,其应力峰值远大于由基本公式算得的应力值。这种受力构件由于外界因素或自身因素几何形状、外形尺寸发生突变而引起局部范围内应力显著增大的现象称为应力集中,引起应力集中的孔、沟槽、缺口、台阶等几何体称为应力集中因素。应力集中削弱了构件的强度,降低了构件的承载能力。从而,应力集中处往往是构件破坏的起始点,是引起构件破坏的主要因素。该现象普遍存在于各种构件中,大部分构件的破坏事故都是由应力集中引起的。因此,为了确保构件的安全使用,提高产品的质量和经济效益,必须科学地处理构件的应力集中问题。 二、产生应力集中的原因 构件中产生应力集中的原因主要有: (1) 截面尺寸的急剧变化。如:构件中的油孔、键槽、缺口、台阶等。 (2) 构件受到集中力作用。如:齿轮轮齿之间的接触点,火车车轮与钢轨的接触点等。 (3) 材料本身的不连续性。如材料中的夹杂、气孔等。 (4) 构件中由于装配、焊接、冷加工、磨削等而产生的裂纹。 (5) 构件在制造或装配过程中,由于强拉伸、冷加工、热处理、焊接等而引起的残余应力。这些残余应力叠加上工作应力后,有可能出现较大的应力集中。 (6) 构件在加工或运输中的意外碰伤和刮痕。 三、应力集中的物理解释 如图,在构件的中间开孔拉杆,故在外力作用下,部件中尺寸发生突然变化的截面上的应力并不是均匀分布的,在圆孔边缘的应力明显大于截面上的平均应力。 应力集中的程度可以用理论应力集中系数表示: 式中,为截面上的最大局部应力;为名义应力,即认为应力在截面上均匀分布而求得的力。设图中的板宽为b,圆孔直径为d,厚度为,则 可以由弹性理论或试验等方法确定。试验结果表明,截面尺寸改变的越急剧,角
有限元分析报告样本
《有限元分析》报告基本要求: 1. 以个人为单位完成有限元分析计算,并将计算结果上交;(不允许出现相同的分析模型,如相 同两人均为不及格) 2. 以个人为单位撰写计算分析报告; 3. 按下列模板格式完成分析报告; 4. 计算结果要求提交电子版,报告要求提交电子版和纸质版。(以上文字在报告中可删除) 《有限元分析》报告 一、问题描述 (要求:应结合图对问题进行详细描述,同时应清楚阐述所研究问题的受力状况和约束情况。图应清楚、明晰,且有必要的尺寸数据。) 一个平面刚架右端固定,在左端施加一个y 方向的-3000N 的力P1,中间施加一个Y 方向的-1000N 的力P2,试以静力来分析,求解各接点的位移。已知组成刚架的各梁除梁长外,其余的几何特性相同。 横截面积:A=0.0072 m2 横截高度:H=0.42m 惯性矩:I=0.0021028m4x 弹性模量: E=2.06x10n/ m2/ 泊松比:u=0.3 二、数学模型 (要求:针对问题描述给出相应的数学模型,应包含示意图,示意图中应有必要的尺寸数据;如进行了简化等处理,此处还应给出文字说明。) (此图仅为例题)
三、有限元建模(具体步骤以自己实际分析过程为主,需截图操作过程) 用ANSYS 分析平面刚架 1.设定分析模块 选择菜单路径:MainMenu—preference 弹出“PRreferences for GUI Filtering”对话框,如图示,在对话框中选取:Structural”,单击[OK]按钮,完成选择。 2.选择单元类型并定义单元的实常数 (1)新建单元类型并定 (2)定义单元的实常数在”Real Constants for BEAM3”对话框的AREA中输入“0。0072”在IZZ 中输入“0。0002108”,在HEIGHT中输入“0.42”。其他的3个常数不定义。单击[OK]按 钮,完成选择 3.定义材料属性 在”Define Material Model Behavier”对话框的”Material Models Available”中,依次双击“Structural→Linear→Elastic→Isotropic”如图