化工原理课程设计任务-填料吸收塔
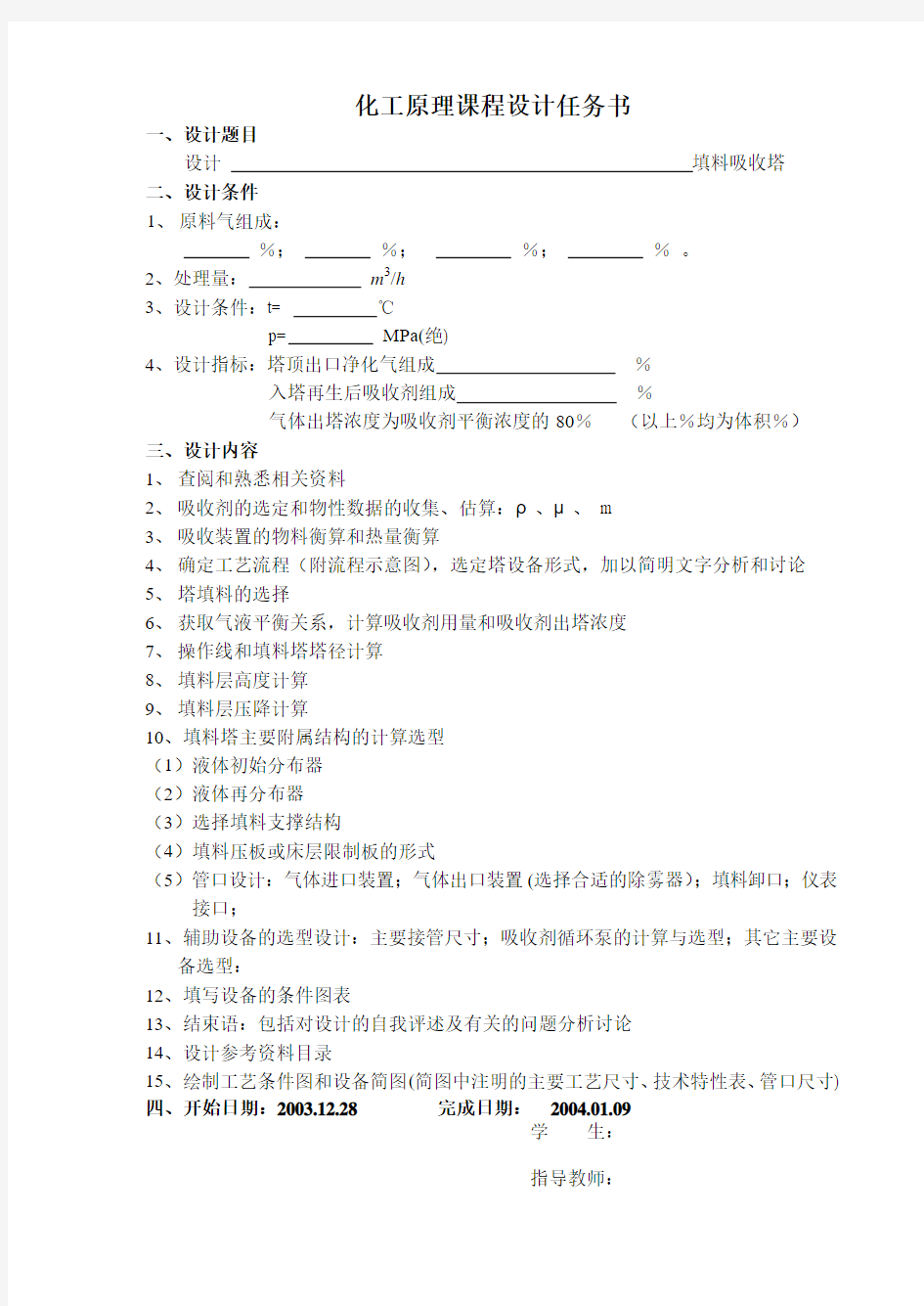
化工原理课程设计任务书
一、设计题目
设计填料吸收塔
二、设计条件
1、原料气组成:
%;%;%;%。
2、处理量:m3/h
3、设计条件:t= ℃
p= MPa(绝)
4、设计指标:塔顶出口净化气组成%
入塔再生后吸收剂组成%
气体出塔浓度为吸收剂平衡浓度的80%(以上%均为体积%)
三、设计内容
1、查阅和熟悉相关资料
2、吸收剂的选定和物性数据的收集、估算:ρ、μ、m
3、吸收装置的物料衡算和热量衡算
4、确定工艺流程(附流程示意图),选定塔设备形式,加以简明文字分析和讨论
5、塔填料的选择
6、获取气液平衡关系,计算吸收剂用量和吸收剂出塔浓度
7、操作线和填料塔塔径计算
8、填料层高度计算
9、填料层压降计算
10、填料塔主要附属结构的计算选型
(1)液体初始分布器
(2)液体再分布器
(3)选择填料支撑结构
(4)填料压板或床层限制板的形式
(5)管口设计:气体进口装置;气体出口装置(选择合适的除雾器);填料卸口;仪表接口;
11、辅助设备的选型设计:主要接管尺寸;吸收剂循环泵的计算与选型;其它主要设
备选型:
12、填写设备的条件图表
13、结束语:包括对设计的自我评述及有关的问题分析讨论
14、设计参考资料目录
15、绘制工艺条件图和设备简图(简图中注明的主要工艺尺寸、技术特性表、管口尺寸)
四、开始日期:2003.12.28 完成日期:2004.01.09
学生:
指导教师:
水吸收_低浓度二氧化硫_填料吸收塔_设计
水吸收低浓度SO2填料吸收塔设计 第一部分设计任务、依据和要求 一、设计任务及操作条件 1、混合气体(空气中含SO 2 气体的混合气体)处理量为90 kmol/h 2、混合气体组成:SO 2 含量为7.6%(摩尔百分比),空气为:92.4%(mol/%) 3、要求出塔净化气含SO 2为:0.145%(mol/%),H 2 O为:1.172 kmol/h 4、吸收剂为水,不含SO 2 5、常压,气体入塔温度为25°C,水入塔温度为20°C。 二、设计内容 1、设计方案的确定 2、填料吸收塔的塔径、填料层高度及填料层压强的计算。 3、填料塔附属结构的选型与设计。 4、填料塔工艺条件图。 三、H2O- SO2 在常压20 °C下的平衡数据
四、 气体与液体的物理性质数据 气体的物理性质: 气体粘度()0.0652/G u kg m h =? 气体扩散系数20.0393/G D m s = 气体密度31.383/G kg m ρ= 液体的物理性质:液体粘度 3.6/()L u kg m h =? 液体扩散系数625.310/L D m s -=? 液体密度 3998.2/L kg m ρ= 液体表面张力 4273/92.7110/L dyn cm kg h σ==? 五、 设计要求 1、设计计算说明书一份 2、填料塔图(2号图)一张
第二部分 SO2净化技术和设备 一、SO2的来源、性质及其危害: 1、二氧化硫的来源 二氧化硫的来源很广泛,几乎所有企业都要产生二氧化硫,最主要途径是含硫化石燃料的燃烧。大约一吨煤中含有5-50kg硫,一吨石油中含有5-30kg硫。这些燃料经燃烧都产生并排放出二氧化硫,占所有排放总量的96%. 二氧化硫的来源包括微生物活动,火山活动,森林火灾以及海水飞沫。主要有自然来源和人为来源两大类: 自然来源主要是火山活动,喷出的火山气体中含有大量的二氧化硫气体,地质深处的天然硫元素在火山喷发过程中燃烧氧化为二氧化硫,随火山灰一起喷射到大气中。地球上57%的二氧化硫来自自然界,沼泽、洼地、大陆架等处所排放的硫化氢,进入大气,被空气中的氧氧化为二氧化硫。自然排放大约占大气中全部二氧化硫的一半,通过自然循环过程,自然排放的硫基本上是平衡的。 人为来源则指在人类进行生产、生活活动中,使用含硫及其化合物的矿石进行燃烧,以及硫矿石的冶炼和硫酸、磷肥纸浆的生产等产生的工业废气,从而使其中一部分或全部的硫以二氧化硫的形式排放到大气中,形成二氧化硫污染。这部分二氧化硫占地球上二氧化硫来源的43%。随着化石燃料消费量的不断增加,全世界认为排放的二氧化硫在不断在增加,其中北半球排放的二氧化硫占人为排放总量的90%。我国的能源主要依靠煤炭和石油,而我国的煤炭、石油一般含硫量较高,因此,火力发电厂、钢铁厂、冶炼厂、化工厂和炼油厂排放出的大量二氧化硫和二氧化碳是造成我国大气污染的主要原因。由于我国部分地区燃用高硫煤,燃煤设备未能采取脱硫措施,致使二氧化硫排放量不断增加,造成严重的环境污染。 2、二氧化硫的性质 (1)物理性质: 二氧化硫又名亚硫酸酐,英文名称: sulfur dioxide 。无色气体,有强烈刺激性气味。分子量64.07 密度为1.4337kg/m3 (标准状况下),密度比空气大。溶解度:9.4g/mL(25℃)熔点-76.1℃(200.75K)沸点-10℃ (263K)
化工原理课程设计任务书 zong (修复的)共32页
2012年 06月 工业背景及工艺流程 乙醛是无色、有刺激性气味的液体,密度比水小,沸点20.8℃,易挥
发、易燃烧且能和水、乙醇、乙醚、氯仿等互溶,因其分子中具有羰基,反应能力很强,容易发生氧化,缩合,环化,聚合及许多类型加成反应。乙醛也是一种重要的烃类衍生物在合成工业有机化工产品上也是一种重要的中间体。其本身几乎没有直接的用途,完全取决于市场对它的下游产品的需求及下游产品对生产路线的选择,主要用于醋酸、醋酐、醋酸乙烯等重要的基本有机化工产品,也用于制备丁醇、异丁醇、季戊四醇等产品。这些产品广泛应用于纺织、医药、塑料、化纤、染料、香料和食品等工业。 国内乙醛生产方法有乙烯氧化法、乙醇氧化法和乙炔氧化法三种技术路线。工业上生产乙醛的原料最初采用乙炔,以后又先后发展了乙醇和乙烯路线。乙炔水化法成本高,因其催化剂——汞盐的污染难以处理等致命缺点,现以基本被淘汰。乙醇氧化或脱氢法制乙醛虽有技术成熟,不需要特殊设备,投资省,上马快等优点,但成本高于乙烯直接氧化法。乙烯直接氧化法制乙醛。由于其原料乙烯来源丰富而价廉,加之反应条件温和,选择性好,收率高,工艺流程简单及“三废”处理容易等突出优点,深受世界各国重视,发展非常迅速,现以成为许多国家生产乙醛的主要方法。 精馏方案的确定: 精馏塔流程的确定; 塔型的选择; 操作压力的选定; 进料状态选定; 加热方式等
所选方案必须: (1)满足工艺要求; (2)操作平稳、易于调节; (3)经济合理; (4)生产安全。 包括:流程的确定;塔型的选择;操作压力的选定;进料状态选定;加热方式等 操作压力选择 ●精馏可在常压、加压或减压下进行。 ●沸点低、常压下为气态的物料必须选用加压精馏;热敏性、高沸点 物料常用减压精馏。 进料状态的选择 ●一般将料液预热到泡点或接近泡点后送入塔内。这样可使: ● (1)塔的操作比较容易控制; ● (2)精馏段和提馏段的上升蒸汽量相近,塔径相似,设计制造比 较方便。 加热方式: ●(1)间接蒸汽加热 ●(2)直接蒸汽加热 ●适用场合:待分离物系为某轻组分和水的混合物。 ●优点:可省去再沸器;并可利用压力较低的蒸汽进行加热。操作 费用和设备费用均可降低。
化工原理课程设计水吸收氨填料吸收塔设计正式版分解
《化工原理》课程设计 水吸收氨气过程填料塔的设计学院 专业制药工程 班级 姓名 学号 指导教师 2013 年 1 月 15 日 目录 设计任务书 (4)
参考文献 (15) 对本设计的评述及心得 (15)
附表:附表附表
设计任务书 (一)、设计题目:水吸收氨气过程填料吸收塔的设计 试设计一座填料吸收塔,用于脱除混于空气中的氨气。混合气体的处理量为7500 m3/h,其中含氨气为5%(体积分数),要求塔顶排放气体中含氨低于%(体积分数)。采用清水进行吸收,吸收剂的用量为最小用量的倍。 (二)、操作条件 (1)操作压力常压 (2)操作温度 20℃. (三)填料类型 选用聚丙烯阶梯环填料,填料规格自选。 (四)工作日 每年300天,每天24小时连续进行。 (五)厂址 厂址为衡阳地区 (六)设计内容 1.吸收塔的物料衡算; 2.吸收塔的工艺尺寸计算;
3.填料层压降的计算; 4.液体分布器简要设计 5.吸收塔接管尺寸计算; 6.绘制吸收塔设计条件图; 7.对设计过程的评述和有关问题的讨论。 (七)操作条件 20℃氨气在水中的溶解度系数为H=(m3kPa)。 第一节前言 填料塔的有关介绍 填料塔洗涤吸收净化工艺不单应用在化工领域 ,在低浓度工业废气净化方面也能很好地发挥作用。工程实践表明 ,合理的系统工艺和塔体设计 ,是保证净化效果的前提。本文简述聚丙烯阶梯填料应用于水吸收氨过程的工艺设计以及工程问题。 填料塔是以塔内的填料作为气液两相间接触构件的传质设备,它是化工类企业中最常用的气液传质设备之一。 填料塔的主体结构如下图所示: 图1 填料塔结构图 填料塔不但结构简单,且流体通过填料层的压降较小,易于用耐腐蚀材料制造,所以它特别适用于处理量小、有腐蚀性的物料及要求压降小的场合。液体自塔顶经液体分布器喷洒于填料顶部,并在填料的表面呈膜状流下,气体从塔底的气体口送入,流过填料的空隙,在填料层中与液体逆流接触进行传质。因气液两相组成沿塔高连续变化,所
111水吸收二氧化硫填料吸收塔设计说明书完整版
吉林化工学院 化工原理课程设计 题目处理量为3100m3/h水吸收二氧化硫过程填料吸收塔的设计 教学院 专业班级 学生姓名 学生学号 指导教师 2011 年 12 月 5 日
课程设计任务书 1、设计题目:处理量为2550~3200m3/h水吸收二氧化硫过程填料吸收塔的设计 。 矿石焙烧炉送出的气体冷却到20℃后送入填料塔中,用20℃清水洗涤洗涤除去其中的SO 2入塔的炉气流量为3100m3/h,其中进塔SO2的摩尔分率为0.05,要求SO2的吸收率为95%。吸收塔为常压操作,因该过程液气比很大,吸收温度基本不变,可近似取为清水的温度。吸收剂的用量为最小用量的1.5倍。 2、工艺操作条件: (1)操作平均压力常压 (2)操作温度t=20℃ (3)选用填料类型及规格自选。 3、设计任务: 完成吸收塔的工艺设计与计算,有关附属设备的设计和选型,绘制吸收系统的工艺流程图和吸收塔的工艺条件图,撰写设计说明书。 处理量为3100m3/h水吸收二氧化硫过程填料吸收塔的设计 化工原理教学与实验中心 2011年11月
目录 摘要.................................................................................................................................IV 第一章绪论. (1) 1.1 吸收技术概况 (1) 1.2 吸收设备发展 (1) 1.3 吸收在工业生产中的应用 (3) 第二章吸收塔的设计方案 (4) 2.1 吸收剂的选择 (4) 2.2 吸收流程选择 (5) 2.2.1 吸收工艺流程的确定 (5) 2.2.2 吸收工艺流程图及工艺过程说明 (6) 2.3 吸收塔设备及填料的选择 (7) 2.3.1 吸收塔设备的选择 (7) 2.3.2 填料的选择 (8) 2.4 吸收剂再生方法的选择 (10) 2.5 操作参数的选择 (11) 2.5.1 操作温度的确定 (11) 2.5.2 操作压强的确定 (11) 第三章吸收塔工艺条件的计算 (12) 3.1 基础物性数据 (12) 3.1.1 液相物性数据 (12) 3.1.2 气相物性数据 (12) 3.1.3 气液两相平衡时的数据 (12) 3.2 物料衡算 (12) 3.3 填料塔的工艺尺寸计算 (13)
化工原理课程设计 吸收塔汇总
《化工原理》课程设计 课题: 设计水吸收半水煤气体混合物中的二氧化碳的填料吸收塔设计者:王涛 学号:1043082002 指导老师:曹丽淑
目录 第一章设计任务????????????????????????????????????????????????????????????????????????????????????????????3 1.1设计题目????????????????????????????????????????????????????????????????????????????????????????????3 1.2设计任务及操作条件???????????????????????????????????????????????????????????????????????????3 1.3设计内容???????????????????????????????????????????????????????????????????????????????????????????????3 第二章设计方案???????????????????????????????????????????????????????????????????????????????????????????4 2.1设计流程的选择及流程图??????????????????????????????????????????????????????????????????????4 第三章填料塔的工艺设计??????????????????????????????????????????????????????????????????????????????4 3.1气液平衡关系????????????????????????????????????????????????????????????????????????????????????????4 3.2吸收剂用量???????????????????????????????????????????????????????????????????????????????????????????5 3.3计算热效应???????????????????????????????????????????????????????????????????????????????????????????5 3.4定塔径??????????????????????????????????????????????????????????????????????????????????????????????????6 3.5喷淋密度的校核?????????????????????????????????????????????????????????????????????????????????????6 3.6体积传质系数的计算??????????????????????????????????????????????????????????????????????????????7 3.7填料层高度的计算??????????????????????????????????????????????????????????????????????????????????8 3.8附属设备的选择???????????????????????????????????????????????????????????????????????????????????9第四章设计结果概要??????????????????????????????????????????????????????????????????????????????????15第五章设计评价 ?????????????????????????????????????????????????????????????????????????????????? 17
填料吸收塔课程设计
一设计任务书 (一)设计题目 过程填料吸收塔的设计:试设计一座填料吸收塔,用于脱除焙烧水吸收SO 2 炉送出的混合气体(先冷却)中的SO2,其余为惰性组分,采用清水进行吸收。 (二)操作条件 (1)操作压力常压 (2)操作温度25℃ (三)设计内容 (1)吸收塔的物料衡算; (2)吸收塔的工艺尺寸计算; (3)填料层压降的计算; (4)液体分布器简要设计; (5)吸收塔接管尺寸计算; (6)绘制吸收塔设计条件图; (7)对设计过程的评述和有关问题的讨论。 二设计方案简介 2.1方案的确定 用水吸收SO 属中等溶解度的吸收过程,为提高传质效率,选用逆流吸收流 2 不作为产品,故采用纯溶剂。 程。因用水作为吸收剂,且SO 2 2.2填料的类型与选择 的过程,操作温度及操作压力较低,工业上通常选用塑料散对于水吸收SO 2 装填料。在塑料散装填料中,塑料阶梯环填料的综合性能较好,故此选用DN38聚丙烯阶梯环填料。
阶梯环是对鲍尔环的改进。与鲍尔环相比,阶梯环高度减少了一半,并在一端增加了一个锥形翻边。由于高径比减少,使得气体绕填料外壁的平均路径大为缩短,减少了气体通过填料层的阻力。锥形翻边不仅增加了填料的机械强度,而且使填料之间由线接触为主变成以点接触为主,这样不但增加了填料间的空隙,同时成为液体沿填料表面流动的汇集分散点,可以促进液膜的表面更新,有利于传质效率的提高。阶梯环的综合性能优于鲍尔环,成为目前所使用的环形填料中最为优良的一种。 2.3设计步骤 本课程设计从以下几个方面的内容来进行设计 (一)吸收塔的物料衡算;(二)填料塔的工艺尺寸计算;主要包括:塔径,填料层高度,填料层压降;(三)设计液体分布器及辅助设备的选型;(四)绘制有关吸收操作图纸。 三、工艺计算 3.1基础物性数据 3.1.1 液相物性数据 对低浓度吸收过程,溶液的物性数据可近似取纯水的物性数据。由手册查得,25℃时水的有关物性数据如下: 密度为ρ L =997.1 kg/m3 粘度为μ L =0.0008937 Pa·s=3.2173kg/(m·h) 表面张力为σ L =71.97 dyn/cm=932731 kg/h2 SO 2在水中的扩散系数为 D L =1.724×10-9m2/s=6.206×10-6m2/h (依Wilke-Chang 0.5 18r 0.6 () 1.85910 M T D V φ μ - =?计算,查《化学工程基础》) 3.1.2 气相物性数据 设进塔混合气体温度为25℃, 混合气体的平均摩尔质量为 M Vm=Σy i M i=0.1×64.06+0.9×29=32.506g/mol 混合气体的平均密度为
水吸收氨气过程填料吸收塔的设计说明
课程设计任务书 一、设计题目:水吸收氨气过程填料吸收塔的设计; 试设计一座填料吸收塔,采用清水吸收混于空气中的氨气。混合气体的处理量为2600m3/h,其中含氨为7%(体积分数),混合气体的进料温度为25℃。要求:氨气的回收率达到98%。(20℃氨在水中的溶解度系数为H=0.725kmol/(m3.kPa) 二、工艺操作条件: (1)操作平均压力常压 (2)操作温度 : t=20℃ (3)吸收剂用量为最小用量的倍数自己确定 (4)选用填料类型及规格自选。 三、设计容 (1)设计方案的确定和说明 (2)吸收塔的物料衡算; (3)吸收塔的工艺尺寸计算; (4)填料层压降的计算; (5)液体分布器简要设计; (6)绘制液体分布器施工图 (7)吸收塔接管尺寸计算; (8)设计参数一览表; (9)绘制生产工艺流程图(A4号图纸); (10)绘制吸收塔设计条件图(A4号图纸); (11)对设计过程的评述和有关问题的讨论。
目录 1. 设计方案简介 (1) 1.1设计方案的确定 (1) 1.2填料的选择 (1) 2. 工艺计算 (1) 2.1 基础物性数据 (1) 2.1.1液相物性的数据 (1) 2.1.2气相物性的数据 (1) 2.1.3气液相平衡数据 (1) 2.1.4 物料衡算 (1) 2.2 填料塔的工艺尺寸的计算 (2) 2.2.1 塔径的计算 (2) 2.2.2 填料层高度计算 (3) 2.2.3 填料层压降计算 (6) 2.2.4 液体分布器简要设计 (7) 3. 辅助设备的计算及选型 (8) 3.1 填料支承设备 (8) 3.2填料压紧装置 (8) 3.3液体再分布装置 (8) 4. 设计一览表 (9) 5. 后记 (9) 6. 参考文献 (9) 7. 主要符号说明 (10) 8. 附图(工艺流程简图、主体设备设计条件图)
化工原理课程设计简易步骤
《化工原理》课程设计说明书 设计题目 学生姓名 指导老师 学院 专业班级 完成时间
目录 1.设计任务书……………………………………………() 2.设计方案的确定与工艺流程的说明…………………() 3.精馏塔的物料衡算……………………………………() 4.塔板数的确定………………………………………() 5.精馏段操作工艺条件及相关物性数据的计算………() 6.精馏段的汽液负荷计算………………………………() 7.精馏段塔体主要工艺尺寸的计算…………………() 8.精馏段塔板主要工艺尺寸的计算…………………………() 9.精馏段塔高的计算…………………………………() 10.精馏段塔板的流体力学验算…………………………() 11.精馏段塔板的汽液负荷性能图………………………() 12.精馏段计算结果汇总………………………………() 13.设计评述……………………………………………() 14.参考文献………………………………………………() 15.附件……………………………………………………() 附件1:附图1精馏工艺流程图………………………() 附件2:附图2降液管参数图……………………………()附件3:附图3塔板布孔图………………………………()
板式塔设计简易步骤 一、 设计方案的确定及工艺流程的说明 对塔型板型、工艺流程、加料状态、塔顶蒸汽冷凝方式、塔釜加热方式等进行说明,并 绘制工艺流程图。(图可附在后面) 二、 精馏塔物料衡算:见教材P270 计算出F 、D 、W ,单位:kmol/h 三、 塔板数的确定 1. 汽液相平衡数据: 查资料或计算确定相平衡数据,并绘制t-x-y 图。 2. 确定回流比: 先求出最小回流比:P 266。再确定适宜回流比:P 268。 3. 确定理论板数 逐板法或梯级图解法(塔顶采用全凝器)计算理论板层数,并确定加料板位置:P 257-258。(逐板法需先计算相对挥发度) 确定精馏段理论板数N 1、提馏段理论板数N 2 4. 确定实际板数: 估算塔板效率:P 285。(①需知全塔平均温度,可由 t-x-y 图确定塔顶、塔底温度,或通过试差确定塔顶、塔底温度,再取算术平均值。②需知相对挥发度,可由安托因方程求平均温度下的饱和蒸汽压,再按理想溶液计算。) 由塔板效率计算精馏段、提馏段的实际板层数N 1’,N 2’:P 284式6-67。 四、 精馏段操作工艺条件及相关物性数据的计算 1. 操作压力m p :取2 F D m p p p += 2. 精馏段平均温度m t :查t-x-y 图确定塔顶、进料板温度,再取平均值。或由泡点方程试差法确定塔顶、进料板温度。 3. 平均摩尔质量M Vm 、M Lm :由P 8式0-27分别计算塔顶、进料板处的摩尔质量,再分别 取两处的算术平均值。汽相的摩尔分率查t-x-y 图。 4. 平均密度Vm ρ、Lm ρ: Lm ρ:用P 13式1-7分别计算塔顶、进料板处液相密度,再 取算术平均值。m Vm m Vm T R M p ??= ρ 5. 液体表面张力m σ:由B B A A m x x σσσ+=分别计算塔顶mD σ与进料板mF σ,再取 平均值。 6. 液体粘度m μ:与表面张力的计算类似。 五、 精馏段汽液负荷(Vs 、Ls )计算 V=(R+1)D L=RD
清水吸收二氧化硫化工原理课程设计毕业设计(论文)
摘要 在化工生产中,气体吸收过程是利用气体混合物中,各组分在液体中溶解度或化学反应活性的差异,在气液两相接触是发生传质,实现气液混合物的分离。在化学工业中,经常需将气体混合物中的各个组分加以分离,其目的是: ①回收或捕获气体混合物中的有用物质,以制取产品; ②除去工艺气体中的有害成分,使气体净化,以便进一步加工处理;或除去工业放空尾气中的有害物,以免污染大气。根据不同性质上的差异,可以开发出不同的分离方法。吸收操作仅为其中之一,它利用混合物中各组分在液体中溶解度或化学反应活性的差异,在气液两相接触时发生传质,实现气液混合物的分离。 一般说来,完整的吸收过程应包括吸收和解吸两部分。在化工生产过程中,原料气的净化,气体产品的精制,治理有害气体,保护环境等方面都要用到气体吸收过程。填料塔作为主要设备之一,越来越受到青睐。二氧化硫填料吸收塔,以水为溶剂,经济合理,净化度高,污染小。此外,由于水和二氧化硫反应生成硫酸,具有很大的利用。 本次化工原理课程设计,我设计的题目是:炉气处理量为m3 4200炉气吸过程填料吸收塔设计。本次任务为用水吸收二氧化硫常压填料塔。具体设计条件如下: 1、混合物成分:空气和二氧化硫; 2、二氧化硫的含量:0.05(摩尔分率) 3、操作压强;常压操作 4、进塔炉气流量:h 4200 m3 5、二氧化硫气体回收率:95% 吸收过程视为等温吸收过程。
目录 摘要 .................................................................................................................................................. I 第一章 设计方案的确定 (1) 1.1流程方案 (1) 1.2设备方案 (1) 1.3流程布置 (1) 1.4吸收剂的选择 (1) 第二章 填料的选择 (2) 2.1对填料的要求 (2) 2.2填料的种类和特性 (2) 2.3填料尺寸 (3) 2.4填料材质的选择 (3) 第三章 工艺计算 (4) 3.1气液平衡的关系 (4) 3.2吸收剂用量及操作线的确定 (4) 3.2.1吸收剂用量的确定 (4) 3.2.2操作线的确定 (5) 3.3塔径计算 (5) 3.3.1采用Eckert 通用关联图法计算泛点速率f u : (5) 3.3.2操作气速 (7) 3.3.3塔径计算 (7) 3.3.4喷淋密度U 校核 (7) 3.3.5单位高度填料层压降(Z P )的校核 (8) 3.4填料层高度计算 (9) 3.4.1传质系数的计算 (9) 3.4.2填料高度的计算 (12) 第四章 填料塔内件的类型与设计 (13) 4.1 塔内件的类型 (13) 第五章 辅助设备的选型 (16) 5.1管径的选择 (16) 5.2泵的选取: (17) 5.3风机的选型: (17) 第六章 填料塔附属高度计算 (17) 第七章 分布器简要计算 (18) 第八章 关于填料塔设计的选材 (18) 参考文献 (19) 附录 (20) 附图 (21) 致谢 (22)
填料精馏塔设计示例
4.3 填料精馏塔设计示例 4.3.1 化工原理课程设计任务书 1 设计题目 分离甲醇-水混合液的填料精馏塔 2 设计数据及条件 生产能力:年处理甲醇-水混合液0.30万吨(年开工300天) 原料:甲醇含量为70%(质量百分比,下同)的常温液体 分离要求:塔顶甲醇含量不低于98%,塔底甲醇含量不高于2% 建厂地址:沈阳 3 设计要求 (1)编制一份精馏塔设计说明书,主要内容: ①前言; ②流程确定和说明; ③生产条件确定和说明; ④精馏塔的设计计算; ⑤主要附属设备及附件的选型计算; ⑥设计结果列表; ⑦设计结果的自我总结评价与说明; ⑧注明参考和使用的设计资料。 (2)编制一份精馏塔工艺条件单,绘制一份带控制点的工艺流程图。 4.3.2 前言
在炼油、石油化工、精细化工、食品、医药及环保等部门,塔设备属于使用量大,应用面广的重要单元设备。塔设备广泛用于蒸馏、吸收、萃取、洗涤、传热等单元操作中。所以塔设备的研究一直是国内外学者普遍关注的重要课题。 塔设备按其结构形式基本上可分为两类:板式塔和填料塔。以前,在工业生产中,当处理量大时多用板式塔,处理量小时采用填料塔。近年来由于填料塔结构的改进,新型的、高负荷填料的开发,既提高了塔的通过能力和分离效能又保持了压降小以性能稳定等特点。因此填料塔已被推广到大型汽液操作中。在某些场合还代替了传统的板式塔。如今,直径几米甚至几十米的大型填料塔在工业上已非罕见。随着对填料塔的研究和开发,性能优良的填料塔必将大量用于工业生产中。 板式塔为逐级接触式汽液传质设备,它具有结构简单、安装方便、操作弹性大、持液量小等优点。同时也有投资费用较高、填料易堵塞等缺点。 本设计目的是分离甲醇-水混合液,处理量不大,故选用填料塔。 塔型的选择因素很多。主要因素有物料性质、操作条件、塔设备的制造安装和维修等。 1 与物性有关的因素 ①易起泡的物系在板式塔中有较严重的雾沫夹带现象或引起液泛,故选用填料塔为宜。因为填料不易形成泡沫。本设计为分离甲醇和水,故选用填料塔。 ②对于易腐蚀介质,可选用陶瓷或其他耐腐蚀性材料作填料,对于不腐蚀的介质,则可选金属性质或塑料填料,而本设计分离甲醇和水,腐蚀性小可选用金属填料。 2 与操作条件有关的因素 ①传质速率受气膜控制的系统,选用填料塔为宜。因为填料塔层中液相为膜状流、气相湍动,有利于减小气膜阻力。 ②难分离物系与产品纯度要求较高,塔板数很多时,可采用高效填料。 ③若塔的高度有限制,在某些情况下,选用填料塔可降低塔高,为了节约能耗,故本设计选用填料塔。 ④要求塔内持液量、停留时间短、压强小的物系,宜用规整填料。 4.3.3 流程确定和说明 1 加料方式 加料方式有两种:高位槽加料和泵直接加料。采用高位槽加料,通过控制液位高度,可以得到稳定的流量和流速。通过重力加料,可
化工原理课程设计-填料吸收塔的设计
化工原理课程设计-填料吸收塔的设计
课程设计 题目:填料吸收塔的设计 教学院:化学与材料工程学院 专业:化学工程与工艺(精细化工方向) 学号: 学生姓名: 指导教师: 2012 年 5 月31 日
《化工原理课程设计》任务书 2011~2012 学年第2学期 学生姓名:专业班级:化学工程与工艺(2009) 指导教师:工作部门:化工教研室 一、课程设计题目:填料吸收塔的设计 二、课程设计内容(含技术指标) 1. 工艺条件与数据 煤气中含苯2%(摩尔分数),煤气分子量为19;吸收塔底溶液含苯≥0.15%(质量分数);吸收塔气-液平衡y*=0.125x;解吸塔气-液平衡为y*=3.16x;吸 收回收率≥95%;吸收剂为洗油,分子量260,相对密度0.8;生产能力为每小时 处理含苯煤气2000m3;冷却水进口温度<25℃,出口温度≤50℃。 2. 操作条件 吸收操作条件为:1atm、27℃,解吸操作条件为:1atm、120℃;连续操作;解吸气流为过热水蒸气;经解吸后的液体直接用作吸收剂,正常操作下不再补充 新鲜吸收剂;过程中热效应忽略不计。 3. 设计内容 ①吸收塔、解吸塔填料层的高度计算和设计; ②塔径的计算; ③其他工艺尺寸的计算。 三、进度安排 1.5月14日:分配任务; 2.5月14日-5月20日:查询资料、初步设计; 3.5月21日-5月27日:设计计算,完成报告。 四、基本要求 1. 设计计算书1份:设计说明书是将本设计进行综合介绍和说明。设计说明 书应根据设计指导思想阐明设计特点,列出设计主要技术数据,对有关工艺流程 和设备选型作出技术上和经济上的论证和评价。应按设计程序列出计算公式和计 算结果,对所选用的物性数据和使用的经验公式、图表应注明来历。 设计说明书应附有带控制点的工艺流程图。 设计说明书具体包括以下内容:封面;目录;绪论;工艺流程、设备及操作 条件;塔工艺和设备设计计算;塔机械结构和塔体附件及附属设备选型和计算; 设计结果概览;附录;参考文献等。 2. 图纸1套:包括工艺流程图(3号图纸)。 教研室主任签名: 年月日
化工原理课程设计(水吸收氨填料吸收塔设计)(正式版)分解
《化工原理》课程设计水吸收氨气过程填料塔的设计 学院 专业制药工程 班级 姓名 学号 指导教师 2013 年 1 月 15 日
目录 设计任务书 (4) 第一节前言 (3) 1.1 填料塔的有关介绍 (4) 1.2 塔内填料的有关介绍............................. 错误!未定义书签。第二节填料塔主体设计方案的确定 .. (5) 2.1 装置流程的确定 (5) 2.2 吸收剂的选择 (5) 2.3 填料的类型与选择 (7) 2.4 液相物性数据 (6) 2.5 气相物性数据 (8) 2.6 气液相平衡数据 (7) 2.7 物料横算 (7) 第三节填料塔工艺尺寸的计算 (8) 3.1 塔径的计算 (8) 3.2 填料层高度的计算及分段 (9) 3.2.1 传质单元数的计算 (10) 3.2.2 传质单元高度的计算 (10) 3.2.3 填料层的分段 (11) 第四节填料层压降的计算 (12) 第五节填料塔内件的类型及设计 (13) 第六节填料塔液体分布器的简要设计 (13) 参考文献 (15) 对本设计的评述及心得 (15) 附表: 附表1填料塔设计结果一览表 (15) 附表2 填料塔设计数据一览 (15) 附件一:塔设备流程图 (17)
设计任务书 (一)、设计题目:水吸收氨气过程填料吸收塔的设计 试设计一座填料吸收塔,用于脱除混于空气中的氨气。混合气体的处理量为7500 m3/h,其中含氨气为5%(体积分数),要求塔顶排放气体中含氨低于0.02%(体积分数)。采用清水进行吸收,吸收剂的用量为最小用量的1.5倍。 (二)、操作条件 (1)操作压力常压 (2)操作温度 20℃. (三)填料类型 选用聚丙烯阶梯环填料,填料规格自选。 (四)工作日 每年300天,每天24小时连续进行。 (五)厂址 厂址为衡阳地区 (六)设计内容 1.吸收塔的物料衡算; 2.吸收塔的工艺尺寸计算; 3.填料层压降的计算; 4.液体分布器简要设计 5.吸收塔接管尺寸计算; 6.绘制吸收塔设计条件图; 7.对设计过程的评述和有关问题的讨论。 (七)操作条件 20℃氨气在水中的溶解度系数为H=0.725kmol/(m3?kPa)。
填料塔设计说明书
填 料 塔 设 计 说 明 书 设计题目:水吸收氨填料吸收塔学院:资源环境学院 指导老师:吴根义罗惠莉 设计者:海江 学号:7 专业班级:08级环境工程1班
一、设计题目 试设计一座填料吸收塔,用于脱出混于空气中的氨气。混合气体的处理为2400m3/h,其中含氨5%,要求塔顶排放气体中含氨低于0.02%。采用清水进行吸收,吸收剂的用量为最小量的1.5倍。 二、操作条件 1、操作压力常压 2、操作温度 20℃ 三、吸收剂的选择 吸收剂对溶质的组分要有良好地吸收能力,而对混合气体中的其他组分不吸收,且挥发度要低。所以本设计选择用清水作吸收剂,氨气为吸收质。水廉价易得,物理化学性能稳定,选择性好,符合吸收过程对吸收剂的基本要求。且氨气不作为产品,故采用纯溶剂。 四、流程选择及流程说明 逆流操作气相自塔底进入由塔顶排出,液相自塔顶进入由塔底排出,此即逆流操作。逆流操作的特点是传质平均推动力大,传质速率快,分离效率高,吸收剂利用率高。工业生产中多用逆流操作。 五、塔填料选择 阶梯环填料。阶梯环是对鲍尔环的改进,与鲍尔环相比,阶梯环高度减少了一半,并在一端增加了一个锥形翻边。由于高径比减少,使得气体绕填料外壁的平均路径大为缩短,减少了气体通过填料层的阻力。锥形翻边不仅增加了填料的机械强度,而且使填料之间由线接触为主变成以点接触为主,这样不但增加了填料间的间隙,同时成为液体沿填料表面流动的汇集分散点,可以促进液膜的表面更新,有利于传质效率的提高。阶梯环的综合性能优于鲍尔环,成为目前使用的环形填料中最为优良的一种 选用聚丙烯阶梯环填料,填料规格:
六、填料塔塔径的计算 1、液相物性数 对低浓度吸收过程,溶液的物性数据可近似取纯水的物性数据。由手册查得,20℃水的有关物性数据如下: 密度为:L ρ=998.2 kg/m3 粘度为:μL=0.001004 Pa·S=3.6 kg/(m·h) 表面力为σL=72.6 dyn/cm =940896 kg/h2 2、气相物性数据: 20℃下氨在水中的溶解度系数为:H=0.725kmol/(m3·kPa)。 混合气体的平均摩尔质量为: Mvm=0.05×17.03g/mol +0.95×29g/mol=28.40g/mol , 混合气体的平均密度为:ρvm =1.183 kg/m3 混合气体的粘度可近似取为空气的粘度,查手册得20℃空气的粘度为: μv=1.81×10-5 Pa·S=0.065 kg/(m·h) 3、气相平衡数据 20℃时NH3在水中的溶解度系数为H=0.725 kmol/(m3·kPa),常压下20℃时NH3在水中的亨利系数为E=76.41kPa 。 4、物料衡算: 亨利系数 S L HM E ρ= 相平衡常数 754.03 .10102.18725.02 .998=??=== P HM P E m S L ρ E ——亨利系数 H ——溶解度系数 Ms ——相对摩尔质量
化工原理课程设计任务书
(封面) XXXXXXX学院 化工原理课程设计任务书 题目: 院(系): 专业班级: 学生姓名: 指导老师: 时间:年月日
目录 1、工艺生产流程线 (4) 2、流程及方案的说明和论证 (4) 3、换热器的设计计算及说明 (5) 4、计算校核 (6) 5、设计结果概要表 (9) 6、设计评价及讨论 (11) 参考文献 (11) 附图:主体设备结构图和花版设计图
化工原理课程设计任务书 一、设计题目:列管式换热器设计。 二、设计任务:将自选物料用河水冷却至生产工艺所要求的温度。 /d; 三、设计条件:1.处理能力:G=29*300 t 物料 2. 冷却器用河水为冷却介质,考虑广州地区可取进口水温度为 20~30℃; 3.允许压降:不大于105 Pa; 4.传热面积安全系数5~15%; 5.每年按330天计,每天24小时连续运行。 四、设计要求:1.对确定的工艺流程进行简要论述; 2.物料衡算、热量衡算; 3.确定列管式换热器的主要结构尺寸; 4.计算阻力; 5.选择适宜的列管式换热器并进行核算; 6.用Autocad绘制列管式冷却器的结构图(3号图纸)、花板布 置图(4号图纸)。 7.编写设计说明书(包括:①封面;②目录;③设计题目(任务 书);④流程示意图;⑤流程及方案的说明和论证;⑥设计计 算及说明(包括校核);⑦主体设备结构图;⑧设计结果概要 表;⑨对设计的评价及问题讨论;⑩参考文献。) 备注:参考文献格式: 期刊格式为:作者姓名.出版年.论文题目.刊物名称.卷号(期号):起止页码 专著格式为:作者姓名.出版年.专著书名.出版社名.起止页码 例:潘继红等.管壳式换热器的分析和计算.北京:科学出版社,1996,70~90 陈之瑞,张志耘.桦木科植物叶表皮的研究.植物分类学报,1991,29(2):127~135 1.工艺生产流程: 物料通过奶泵被送入冷却器后,经管盖进行多次往返方向的流动。冷却后由出料管流出,不合格的物料由回流阀送回冷却器重新冷却,直至符合要求。经过处理的河水由冷却器的进口管流入,由出口管流出,其与牛奶进行逆流交换热量。 牛奶灭菌后温度高达110~115℃,然后进行第一阶段的冷却,冷却到均质温度55~75℃,而后进行均质。无菌均质后,牛奶经过第二阶段的冷却,最终由冷却水冷却至所需的出口温度。本实验所设计的就是第一阶段冷却的列管式换热器。
化工原理实验—吸收
填料吸收塔的操作及吸收传质系数的测定 一、实验目的 1.了解填料吸收塔的结构和流程; 2.了解吸收剂进口条件的变化对吸收操作结果的影响; 3.掌握吸收总传质系数K y a 的测定方法 4. 学会使用GC 二、实验原理 吸收操作是分离气体混合物的方法之一,在实际操作过程中往往同时具有净化与回收双重目的。因而,气体出口浓度y 2是度量该吸收塔性能的重要指标,但影响y 2的因素很多,因为吸收传质速率N A 由吸收速率方程式决定。 (一). 吸收速率方程式: 吸收传质速率由吸收速率方程决定 : m y A y aV K N ?=填 或 m y A y A K N ?= 式中: Ky 气相总传系数,mol/m 3.s ; A 填料的有效接触面积,m 2; Δy m 塔顶、塔底气相平均推动力, V 填 填料层堆积体积,m 3; K y a 气相总容积吸收传质系数,mol/m 2.s 。
从前所述可知,N A 的大小既与设备因素有关,又有操作因素有关。 (二).影响因素: 1.设备因素: V 填与填料层高度H 、填料特性及放置方式有关。然而,一旦填料塔制成,V 填就为一定值。 2.操作因素: a .气相总容积吸收传质系数K y a 根据双膜理论,在一定的气温下,吸收总容积吸收传质系数K y a 可表示成: a k m a k a K x y y +=11 又有文献可知:a y G A a k ?=和b x L B a k ?=,综合可得b a y L G C a K ?=,显然K y a 与气体流量及液体流量均有密切关系。比较a 、b 大小,可讨论气膜控制或液膜控制。 b .气相平均推动力Δy m 将操作线方程为:22)(y x x G L y +-= 的吸收操作线和平衡线方程为:y =mx 的平衡线在方格纸上作图,从图5-1中可得知: 2 12 1ln y y y y y m ???-?= ?
化工原理课程设计(氨气填料吸收塔设计)
化工原理课程设计任务书设计题目填料吸收塔设计—15 主要内容1、设计方案简介:对给定或选定的工艺流程、主要设备进行简要 论述; 2、主要设备的工艺设计计算:物料衡算、能量衡算、工艺参数的 选定、填料塔结构设计和工艺尺寸的设计计算; 3、辅助设备的选型 4、绘流程图:以单线图的形式描绘,标出主体设备和辅助设备的 物料方向、物流量、能流量。 5、吸收塔的设备工艺条件图 6、编写设计计算说明书 设计参数用清水吸收空气中的NH 3 气体,混合气体处理量5000m3/h,其中NH 3 含量为0.14kg/m3干空气(标态),干空气温度为25℃,相对湿度为 70%,要求净化气中NH 3 含量不超过0.07%(体积分数),气体入口温 度40℃,入塔吸收剂中不含NH 3 ,水入口温度30℃。 设计计划进度布置任务,学习课程设计指导书,其它准备……………0.5天主要工艺设计计算…………………………………………2.5天辅助设备选型计算/绘制工艺流程图……………………1.0天绘制主要设备工艺条件图…………………………………1.0天编写设计计算说明书(考核)……………………………1.0天合计:(1周)………………………………………………6.0天 主要参考文献1. 《化工原理课程设计》,贾绍义等编,天津大学出版社,2002.08 2.《化工原理》(上、下册),夏清,陈常贵主编,天津大学出版社, 2005.01 3. 《化工原理课程设计》,大连理工大学编,大连理工大学出版社, 1994.07 4.《化工工艺设计手册》(第三版)(上、下册),化学工业出版社, 2003.08 5.《化学工程手册》(第二版)(上、下卷),时钧等主编,化学工 业出版社,1998.11 6.《化工设备机械基础》,董大勤编,化学工业出版社,2003.01 7.《化工数据导引》,王福安主编,化工出版社,1995.10 8.《化工工程制图》,魏崇光等主编,化学工业出版社1994.05 9.《现代填料塔技术指南》,王树楹主编,中国石化出版社,1998.08 设计文件要求1.设计说明书不得少于7000字,A4幅面; 2.工艺流程图为A2幅面; 3.设备工艺条件图为A3幅面; 备注
化工原理课程设计换热器设计
化工原理 课 程 设 计 设计任务:换热器 班级:13级化学工程与工艺(3)班 姓名:魏苗苗 学号:90 目录 化工原理课程设计任务书 (2) 设计概述 (3) 试算并初选换热器规格 (6) 1. 流体流动途径的确定 (6)
2. 物性参数及其选型 (6) 3. 计算热负荷及冷却水流量 (7) 4. 计算两流体的平均温度差 (7) 5. 初选换热器的规格 (7) 工艺计算 (10) 1. 核算总传热系数 (10) 2. 核算压强降 (13) 设计结果一览表 (16) 经验公式 (16) 设备及工艺流程图 (17) 设计评述 (17)
参考文献 (18) 化工原理课程设计任务书 一、设计题目: 设计一台换热器 二、操作条件:1、苯:入口温度80℃,出口温度40℃。 2、冷却介质:循环水,入口温度℃。 3、允许压强降:不大于50kPa。 4、每年按300天计,每天24小时连续运行。 三、设备型式:管壳式换热器 四、处理能力:109000吨/年苯 五、设计要求: 1、选定管壳式换热器的种类和工艺流程。 2、管壳式换热器的工艺计算和主要的工艺尺寸的设计。 3、设计结果概要或设计结果一览表。
4、设备简图。(要求按比例画出主要结构及尺寸) 5、对本设计的评述及有关问题的讨论。 六、附表: 1.设计概述 热量传递的概念与意义 热量传递的概念 热量传Array递是指由于 温度差引起 的能量转移, 简称传热。由 热力学第二 定律可知,在 自然界中凡 是有温差存 在时,热就必 然从高温处 传递到低温 处,因此传热
是自然界和工程技术领域中极普遍的一种传递现象。 化学工业与热传递的关系 化学工业与传热的关系密切。这是因为化工生产中的很多过程和单元操作,多需要进行加热和冷却,例如:化学反应通常要在一定的温度进行,为了达到并保持一定温度,就需要向反应器输入或输出热量;又如在蒸发、蒸馏、干燥等单元操作中,都要向这些设备输入或输出热量。此外,化工设备的保温,生产过程中热能的合理利用以及废热的回收利用等都涉及到传热的问题,由此可见;传热过程普遍的存在于化工生产中,且具有极其重要的作用。总之,无论是在能源,宇航,化工,动力,冶金,机械,建筑等工业部门,还是在农业,环境等部门中都涉及到许多有关传热的问题。 应予指出,热力学和传热学既有区别又有联系。热力学不研究引起传热的机理和传热的快慢,它仅研究物质的平衡状态,确定系统由一个平衡状态变成另一个平衡状态所需的总能量;而传热学研究能量的传递速率,因此可以认为传热学是热力学的扩展。 传热的基本方式 根据载热介质的不同,热传递有三种基本方式: 热传导(又称导热)物体各部分之间不发生相对位移,仅借分子、原子和自由电子等微观粒子的热运动而引起的热量传递称为热传导。热传导的条件是系统两部分之间存在温度差。