SMT工艺质量控制
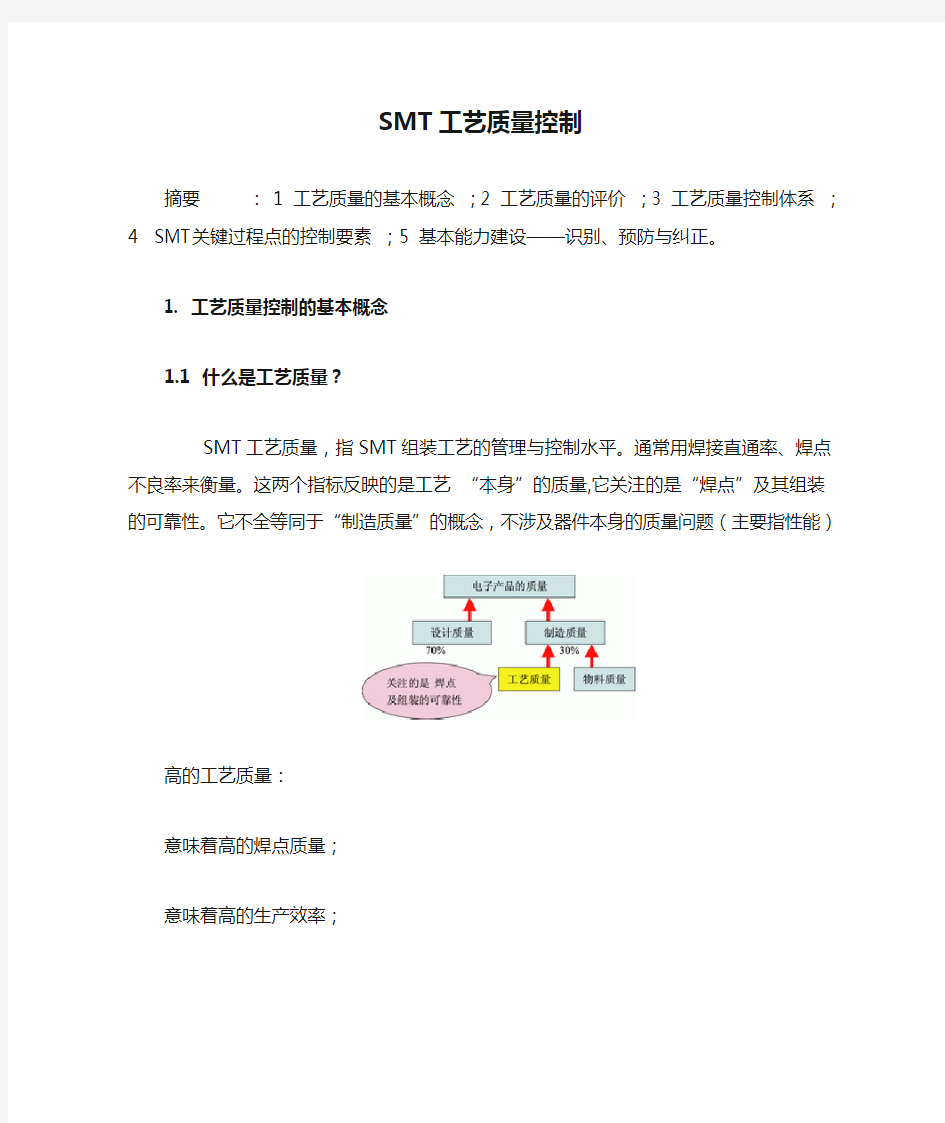

SMT工艺质量控制
摘要:1 工艺质量的基本概念;2 工艺质量的评价;3 工艺质量控制体系;4 SMT关键过程点的控制要素;5 基本能力建设——识别、预防与纠正。
1. 工艺质量控制的基本概念
1.1 什么是工艺质量?
SMT工艺质量,指SMT组装工艺的管理与控制水平。通常用焊接直通率、焊点不良率来衡量。这两个指标反映的是工艺“本身”的质量,它关注的是“焊点”及其组装的可靠性。它不全等同于“制造质量”的概念,不涉及器件本身的质量问题(主要指性能)
高的工艺质量:
意味着高的焊点质量;
意味着高的生产效率;
1.2 什么是工艺质量控制?
工艺质量控制,就是要对影响SMT工艺质量的所有因素进行有效的管理和控制,使SMT的焊接缺陷率处于可接受的水平和稳定状态。
没有稳定的工艺质量,不可能有稳定的制造质量,也不可能有高的生产效率。
工艺质量控制的目的:
建立稳定的工艺!
1.3 工艺质量控制体系
现代工艺质量控制体系的建立,基于“零缺陷”和“第一次把事情做好”的原则,强调“预防”为主的做法。同时,随着SMD的越来越小,PCBA组装密度的越来越高,先前通过维修解决不合格产品的做法越来越不可行。在这样的情况下,许多企业对如何提高焊接的一次合格率进行了广泛的探索,逐步形成了一套控制体系——重视PCBA的可制造性设计、严格对物料工艺质量的控制、进行正确的的工艺试制、实施规范化的SMT工序管理、利用AOI(自动光学检查)和计算机技术进行实时工艺监控等,我们把这些行之有效的“做法”,称之为工艺质量的控制体系。
2. 工艺质量的评价
1) 直通率
直通率,也称首次通过率(First Time
Yield),指在某个时间段首次通过生产线的PCBA合格率,用百分比表示。
YFT=(通过检查的PCBA数/检查的PCBA总数)×100
直通率是以测试结果进行统计的一个指标,反映了来料、工艺的综合质量。它是一个以时间段为单位、以不合格产品为缺陷单位统计的一个数据。
需要注意的是在同一工艺条件下,不同密度和大下的板其直通率相差很大。也就是直通率与板上安装的元件多少、封装的工艺性有很大关系,元件越多,直通率越低。
2) 焊点不良率
焊点不良率,一般用百万焊点中的不良焊点数表示,单位PPM。
PPM=(∑dt/∑Ot)×106
∑ds 为焊点缺陷数
∑Ot 为总焊点数
焊点不良率,是针对不符合要求的焊点进行统计的一个指标,反映了SMT工艺的结果质量。相对于组装DPMO而言,它不需要对印刷、贴片工序进行缺陷统计和再流焊接后对焊点缺陷原因进行甄别,比较简单,易于操作。但另一方面,它不能完全反映组装全过程各工序的控制水平,不能从过程数据中提取到各工序的DPMO数据,不利于过程的改进。
3) 综合制造指标
综合制造指标,一般用制造过程每百万机会缺陷数表示。根据IPC-7912的定义的理解,SMT 组装DPMO可以用下式表示:
DPMO=[(∑ds+ ∑dp + ∑dt)/(∑Os+ ∑Op + ∑Ot)]×106
其中:
∑ds 为焊膏印刷缺陷数(以印刷缺陷的板数计)
∑dp 为贴片缺陷数(以贴装缺陷的元件数计)
∑dt 为焊点缺陷数(以焊点缺陷数计)
∑Os 为焊膏印刷缺陷机会数(以印刷板数计)
∑Op 为贴片机会数(以贴装元件数计)
∑Ot 为焊点机会数(以焊点数计)
此计算公式,将SMT组装作为一个过程进行评价,数据的处理比较烦琐,需要收集SMT的各工序的工艺缺陷数据,并按照不重复统计的原则进行计算。
所谓不重复统计的原则,就是如果属于印刷缺陷,不计入贴片、焊接缺陷,如果属于贴片缺陷,不计入焊接缺陷。DPMO能够真实地反映工艺的控制水平。
3. 工艺质量控制体系构成
4. SMT工序控制
5. 工序控制基础
5.1 焊膏印刷
1) 重要性认识
调查发现焊接缺陷类型的分布是:焊点开路占46%;短路占22%;其次是焊料不足占17%;其它缺陷类型依次是对准不良、脱焊、焊料过多等,这些缺陷类型约占全部缺陷类型的15%左右。
2) 基本认识
(1)钢网厚度的选取首先取决于“脱模性”。
(2)印刷厚度总会比钢网厚(焊粉直径、绿油、间隙、脱模是否拉尖),一般为钢网厚度的120~150%,甚至到200%,这与测试方法有关。
(3)刮刀的移动速度、角度及压力以及PCB的脱网速度,是一组重要参数,严重影响印刷质量。
5.2 贴片
1) 注意点
(1) 贴片精度检测与调试
(2) 飞片率控制,一般原因:
片容、片阻表面不平;吸嘴真空开闭时机不对;静电;喂料器问题;吸嘴磨损;一般要求3/1000内。
(3) 要控制吸嘴压力,特别是大尺寸片容,很容易开裂;
(4) 静电敏感器件贴装,要注意顺序,一定要在最后装,吸取、贴片动作需严防静电,可采用离子风吹。
2) 贴片精度
设备精度≠贴片精度
贴片精度与机器定位精度、元件定心精度等有关。设备的验收最好用一盘料带密集实贴后用测量放大镜测量。
一个创新性的观点——以焊膏印刷图形中心为贴片中心
松下的APC技术(Advanced Process Control)
3) 0201的贴装
5.3 再流焊接
1) 工艺曲线设置基础
1 理解温度曲线的深刻含义,了解一般参数的设置范围。
2 收集再流焊接的经验数据,建立基础工艺数据库。
3 焊接工艺质量的鉴定:
焊点起始处的润湿状况;
焊料与被焊金属间是否形成合金层(IMC);
元件、PCB有无热损伤(表观与测试)。
关键器件的焊接结果——BGA、QFN、Chip C(通过可靠性测试结果了解)
4 热风加热方式优于红外加热,可以实现温度高精度控制。
2) 良好焊点的标志—金属间化合物(IMC)
6. 新产品导入
作者简介
贾忠中
1985年毕业于东南大学机械系。1985年至1998年在信息产业部第二研究所从事SMT设备及工艺研究、开发等工作;SMT设备多项获部组成果奖,发表论文多篇。
1998年至今在中兴通讯公司历任工艺部长。
SMT工序质量控制
电子器件产品检测示意图: 一.主流的封装方式有回流焊接和波峰焊它们的主要检测流程如图; 二.回流焊缺陷与质量检测与产品管制
(一)工艺流程图 从回流焊工艺流程可看出,一件产品回流焊接要经历至少5次检查: 1. 印刷质量检查 Inspect the printed PCB(对印刷质量进行检查,不得有漏印刷、印刷偏移等) 2. 贴装质量检查 SMT quality inspection (检查元件贴装质量,不良进行修正) 3. 首件检查 Check the components (根据工艺指导书核对所有贴装元器件的参数、规格、极性、工艺 要求等,首件确认OK后方可批量生产) 4.. AOI自动光学检测 Automated Optical Inspection (对回流焊接或固化完成的产品使用AOI采用光 学对比法检测,不良品需进行维修后再次进行AOI检测) 5. FQA抽检 Spot check (以国际标准:GB/T2828.1-2003相关规定进行抽样检查) 通过至少4次人工检测与一次机器检测才对能对产品质量保证,才能消除缺陷,达到质量检验效果,因为焊接工艺的每步都会带来缺陷与焊接不良。 (二)回流焊的缺陷和焊接质量检验
1. 回流焊的常见缺陷和可能原因 回流焊的焊接质量检验标准一般可采用IPC标准IPC-A-610,电子装联的接受标准。其中包括了SMT焊接元件的焊接检验标准。 回流焊常见的缺陷一般的原因和建议解决措施可归纳为下表
2. 回流焊后的质量检验方法与比较 回流焊的焊接质量的方法目前常用的有目检法,自动光学检查法(AOI),电测试法(ICT),X-ray 光检查法,以及超声波检测法。 1)目检法 简单,低成本。但效率低,漏检率高,还与人员的经验和认真程度有关。 2)自动光学检查法(AOI) 自动化。避免人为因素的干扰。无须模具。可检查大多数的缺陷,但对BGA,DCA等焊点不能看到的元件无法检查。 3)电测试法(ICT) 自动化。可以检查各种电气元件的正确连接。但需要复杂的针床模具,价格高,维护复杂。对焊接的工艺性能,例如焊点光亮程度,焊点质量等无法检验。另外,随着电子产品装连越来越向微型化,高密度以及BGA,CSP方向发展,ICT的测针方法受到越来越多的局限。 4)X-ray光检查法 自动化。可以检查几乎全部的工艺缺陷。通过X-Ray的透视特点,检查焊点的形状,和电脑库里标准的形状比较,来判断焊点的质量。尤其对BGA,DCA元件的焊点检查,作用不可替代。无须测试模具。但对错件的情况不能判别。缺点价格目前相当昂贵。 5)超声波检测法 自动化。通过超声波的反射信号可以探测元件尤其时QFP,BGA等IC芯片封装内部发生的空洞,分层等缺陷。它的缺点是要把PCB板放到一种液体介质才能运用超声波检验法。较适合于实验室运用。 (三)工程物资的质量管控方法 为了使产品质量合格,要对产品进行实时管控,可行方法如下:
SMT工艺标准规范标准与制程程序.docx
\\ SMT 工艺与制程 一SMT生产环境 二生产排序 三焊膏部分 四胶水部分 五组件 (SMD)的基本知识 六 PCB板的基本要求 七 SMT基本工艺、制程文件 唐海 2013/4/29
一SMT生产环境 1.无尘: SMT设备气动部件很多,清洁的环境有利于气路的顺畅,与稳定运行; SMT贴片设备的组件认识系统主要为相机识别或激光识别, 它们镜头是否清洁无尘直接影响到设备的装着率和贴片精度; SMT 设备的功率电器部件较多, 无尘与良好的通风环境能保证其寿命 ; 无 尘能保证 PCB板的清洁 , 保证印刷质量与点胶质量; 无尘的其体等级要求根据生产品的类型与精度要求来确定。 2.温度: ( 20---28℃)设备的机械、电器部件在高速、长时间运转下都会发 热 , 要较低的环境温度保证其正常运行 ; 在此温度范围内能保证锡膏的性能与点胶的质量 ; SMT 的作业人员为防静电而穿了防静电衣帽 , 需要合适的温度环境 . 3.湿度: ( 40---70%RH )湿度对静电的影响非常大; 湿度对锡膏的印刷有很大影响 ; 湿度对设备机械、电器部件有影响 . 4.防静电: A.静电物质由于受外力的作用,会产生电子的得失,物质中电子的得失破坏了电平衡 , 产生了静电 . 静电能击穿很多电子器件 , 是 IC 等电子器件的头号杀手 . B.影响静电的产生因素 物质的材料特性 , 有的容易产生静电 , 有的不容易产生静电 ; 物质摩擦的作用力的大小与方向; 环境湿度会影响静电产生的大小, 越干燥 , 越易产生静电 ;
C.静电的防护 所有元器件的操作都必需在静电安全工作台上进行; SMD采用防静电包装 ,SMD物料仓要有更严的防静电保护; SMT的作业人员必须有静电防护, 穿防静电工作服或戴防静电手腕带, 接触芯片时避免接触它的引脚或端子, 根据要求再作静电防护 ; SMT的各种设备必须有良好的防静电保护, 做防静电油漆 , 加防静电皮 , 和设备良好的接地 ; 控制好 SMT生产环境的湿度 , 工作场地做防静电油漆 , 加防静电地皮 ; PCBA的存放与搬运也要注意防静电 , 用防静电胶盆等来装 PCB . 5.通风: SMT回流焊会排出很多废气,需要良好的通风保持生产环境. 6.照明 : 方便目检员检测半成品,作业人员观察与作业. 7.振动 : 小的振动有利于保护贴片精度,设备的正常使用. 8.地板的承载能力 : SMT设备一般都有较大振动,如果生产车间不在一楼 应考虑楼板的承受能力和防止共振 . 9.设备的布局 : 主要考虑设备的振动是否会相互影响,是否方便作业与正体 的美观 , 产品的升级伴随的辅助设备的增加 . 二生产排序 1.先生产锡膏面 , 再生产胶水面 2.先生产少料面 , 再生产多料面 3. PCB 胶水贴片回焊炉目检ICT IPQC 4. PCB印刷IPQC抽检贴片IPQC抽检回焊炉
SMT工艺质量控制的基本概念
SMT工艺质量控制 摘要:1 工艺质量的基本概念;2 工艺质量的评价;3 工艺质量控制体系;4 SMT 关键过程点的控制要素;5 基本能力建设——识别、预防与纠正。 1. 工艺质量控制的基本概念 1.1 什么是工艺质量? SMT工艺质量,指SMT组装工艺的管理与控制水平。通常用焊接直通率、焊点不良率来衡量。这两个指标反映的是工艺“本身”的质量,它关注的是“焊点”及其组装的可靠性。它不全等同于“制造质量”的概念,不涉及器件本身的质量问题(主要指性能) 高的工艺质量:
意味着高的焊点质量; 意味着高的生产效率; 1.2 什么是工艺质量控制? 工艺质量控制,就是要对影响SMT工艺质量的所有因素进行有效的管理和控制,使SMT 的焊接缺陷率处于可接受的水平和稳定状态。 没有稳定的工艺质量,不可能有稳定的制造质量,也不可能有高的生产效率。 工艺质量控制的目的: 建立稳定的工艺! 1.3 工艺质量控制体系
现代工艺质量控制体系的建立,基于“零缺陷”和“第一次把事情做好”的原则,强调“预防”为主的做法。同时,随着SMD的越来越小,PCBA组装密度的越来越高,先前通过维修解决不合格产品的做法越来越不可行。在这样的情况下,许多企业对如何提高焊接的一次合格率进行了广泛的探索,逐步形成了一套控制体系——重视PCBA的可制造性设计、严格对物料工艺质量的控制、进行正确的的工艺试制、实施规范化的SMT工序管理、利用AOI(自动光学检查)和计算机技术进行实时工艺监控等,我们把这些行之有效的“做法”,称之为工艺质量的控制体系。 2. 工艺质量的评价 1) 直通率 直通率,也称首次通过率(First Time Yield),指在某个时间段首次通过生产线的PCBA合格率,用百分比表示。 YFT=(通过检查的PCBA数/检查的PCBA总数)×100 直通率是以测试结果进行统计的一个指标,反映了来料、工艺的综合质量。它是一个以时间段为单位、以不合格产品为缺陷单位统计的一个数据。
SMT工艺质量控制的基本概念(doc 13页)
SMT工艺质量控制的基本概念(doc 13页)
SMT工艺质量控制 摘要: 1 工艺质量的基本概念;2 工艺质量的评价;3 工艺质量控制体系;4 SMT关键过程点的控制要素;5 基本能力建设——识别、预防与纠正。 1. 工艺质量控制的基本概念 1.1 什么是工艺质量? SMT工艺质量,指SMT组装工艺的管理与控制水平。通常用焊接直通率、焊点不良率来衡量。这两个指标反映的是工艺“本身”的质量,它关注的是“焊点”及其组装的可靠性。它不全等同于“制造质量”的概念,不涉及器件本身的质量问题(主要指性能) 高的工艺质量: 意味着高的焊点质量; 意味着高的生产效率;
1.2 什么是工艺质量控制? 工艺质量控制,就是要对影响SMT工艺质量的所有因素进行有效的管理和控制,使SMT的焊接缺陷率处于可接受的水平和稳定状态。 没有稳定的工艺质量,不可能有稳定的制造质量,也不可能有高的生产效率。 工艺质量控制的目的: 建立稳定的工艺! 1.3 工艺质量控制体系 现代工艺质量控制体系的建立,基于“零缺陷”和“第一次把事情做好”的原则,强调“预防”为主的做法。同时,随着SMD的越来越小,PCBA组装密度的越来越高,先前通过维修解决不合格产品的做法越来越不可行。在这样的情况下,许多企业对如何提高焊接的一次合格率进行了广泛的探索,逐步形成了一套控制体系——重视PCBA的可制造性设计、严格对物料工艺质量的控制、进行正确的的工艺试制、实施规范化的SMT工序管理、利用AOI(自动光学检查)和计算机技术进行实时工艺监控等,我们把这些行之有效的“做法”,称之为工艺质量的控制体系。
2. 工艺质量的评价 1) 直通率 直通率,也称首次通过率(First Time Yield),指在某个时间段首次通过生产线的PCBA合格率,用百分比表示。 YFT=(通过检查的PCBA数/检查的PCBA总数)×100 直通率是以测试结果进行统计的一个指标,反映了来料、工艺的综合质量。它是一个以时间段为单位、以不合格产品为缺陷单位统计的一个数据。 需要注意的是在同一工艺条件下,不同密度和大下的板其直通率相差很大。也就是直通率与板上安装的元件多少、封装的工艺性有很大关系,元件越多,直通率越低。 2) 焊点不良率 焊点不良率,一般用百万焊点中的不良焊点数表示,单位PPM。 PPM=(∑dt/∑Ot)×106 ∑ds 为焊点缺陷数
SMT生产流程、注意事项及质量控制点
SMT生产流程、注意事项及质量控制点 SMT就是表面组装技术(Surface Mounted Technology)的缩写,是目前电子组装行业里最流行的一种技术和工艺。表面组装技术是一种无需在印制板上钻插装孔,直接将表面组装元器件贴﹑焊到印制电路板表面规定位置上的电路装联技术。具体的说,表面组装技术就是一定的工具将表面组装元器件引脚对准预先涂覆了了粘剂接剂和焊膏的焊盘图形上,把表面组装组件贴装元器件贴装到未钻安装孔的PCB表面上,然后经过波峰焊或再流焊使表面组装元器件和电路之间建立可靠的机械和电气连接。 一、SMT的特点: 1. 组装密度高、电子产品体积小、重量轻,贴片元件的体积和重量只有传统插装元件的1/10左右,一般采用SMT之后,电子产品体积缩小40%~60%,重量减轻60%~80%。 2. 可靠性高、抗振能力强。焊点缺陷率低。 3. 高频特性好。减少了电磁和射频干扰。 4. 易于实现自动化,提高生产效率。 5. 降低成本达30%~50%。节省材料、能源、设备、人力、时间等。 二、为什么要用表面贴装技术(SMT)?
1. 电子产品追求小型化,以前使用的穿孔插件元件已无法缩小。 2. 电子产品功能更完整,所采用的集成电路(IC)已无穿孔元件,特别是大规模、高集成IC,不得不采用表面贴片元件。 3. 产品批量化,生产自动化,厂方要以低成本高产量,出产优质产品以迎合顾客需求及加强市场竞争力。 4. 电子元件的发展,集成电路(IC)的开发,半导体材料的多元应用。 5. 电子科技革命势在必行,追逐国际潮流。 三、SMT工艺流程及作用 1.单面板生产流程 供板印刷红胶(或锡浆) 贴装SMT元器件回流固化(或焊接) 检查测试包装 2.双面板生产流程 (1) 一面锡浆﹑一面红胶之双面板生产流程: 供板丝印锡浆贴装SMT元器件回流焊接检查供板(翻面) 丝印红胶贴装 SMT元器件回流固化波峰焊接检查包装 (2) 双面锡浆板生产流程 供板第一面(集成电路少,重量大的元器件少) 丝印锡浆贴装SMT元器件回流焊接检查供板第二面(集成电路多﹑重量大的元器件多)
外发SMT质量管控要求
外发SMT质量管控要求 一、目的: 建立我公司外发SMT 质量管控要求,识别物料管理、工艺控制、异常处理等控制项,推动品质稳定及持续提升 (一)新机种导入管控 1:安排试产前召集生产部、品质部、工艺等相关部门试产前会议,主要说明我司试产机种生产工艺流程、要求各工位之品质重点 2:制造部按生产工艺流程进行或工程人员安排排线试产过程中,各部门担当工程师(工艺)须上线进行跟进,及时处理试产过程中出现的异常并进行记录 3:品质部需对试产机种进行首件核对与各项性能与功能性测试,并填写相应的试产报告(试产报告以邮件发送至我司工程) (二)ESD管控 1.加工区要求:仓库、贴件、测试车间满足ESD控制要求,地面铺设防静电材料,加工台铺设防静电席,表面阻抗104-1011Ω,并接静电接地扣(1MΩ±10%); 2.人员要求:进入车间需穿防静电衣、鞋、帽,接触产品需佩戴有绳静电环; 3.转板用架、包装用泡棉、气泡袋,需要符合ESD要求,表面阻抗<1010Ω, 4.转板车架需外接链条,实现接地; 5.设备漏电压<0.5V,对地阻抗<6Ω,烙铁对地阻抗<20Ω,设备需评估外引独立接地线;(三)MSD管控 1.BGA.IC.管脚封装材料,易在非真空(氮气)包装条件下受潮,SMT回流时水分受热挥发,出现焊接异常,需用100%烘烤。 2.BGA 管制规范 (1)真空包装未拆封之BGA 须储存于温度低于30°C,相对湿度小于70%的环境,使用期限为一年. (2)真空包装已拆封之BGA 须标明拆封时间,未上线之BGA,储存于防潮柜中,储存条件≤25°C、65%RH,储存期限为72hrs. (3)若已拆封之BGA但未上线使用或余料,必须储存于防潮箱内(条件≤25℃,65%R.H.)若退回大库房之BGA由大库房烘烤后,大库房改以抽真空包装方式储存 (4)超过储存期限者,须以125°C/24hrs烘烤,无法以125°C烘烤者,则以80°C/48hrs 烘烤(若多次烘烤则总烘烤时数须小于96hrs),才可上线使用 (5)若零件有特殊烘烤规范者,另订入SOP. 3.PCB存储周期>3个月,需使用120℃2H-4H烘烤 (四)PCB管制规范 1 PCB拆封与储存 (1)PCB板密封未拆封制造日期2个月内可以直接上线使用 (2)PCB板制造日期在2个月内,拆封后必须标示拆封日期 (3)PCB板制造日期在2个月内,拆封后必须在5天内上线使用完毕. 2 PCB 烘烤 (1)PCB 于制造日期2个月内密封拆封超过5天者,请以120 ±5℃烘烤1小时 (2)PCB如超过制造日期2个月,上线前请以120 ±5℃烘烤1小时 (3)PCB如超过制造日期2至6个月,上线前请以120 ±5℃烘烤2小时 (4)PCB如超过制造日期6个月至1年,上线前请以120 ±5℃烘烤4小时 (5)烘烤过之PCB须于5天内使用完毕,位使用完毕则需再烘烤1小时才可上线使用
SMT生产质量控制的方法和措施
SMT生产质量控制的方法和措施 鲜飞 在电子产品竞争日趋激烈的今天,提高产品质量已成为SMT生产中的最关键因素之一。产品质量水平不仅是企业技术和管理水平的标志,更与企业的生存和发展休戚相关。本文将结合本单位生产实际情况,就如何控制SMT生产现场的生产质量做番讨论。 1、生产质量过程控制 1、1 质量过程控制点的设置 为了保证SMT设备的正常进行,必须加强各工序的加工工件质量检查,从而监控其运行状态。因而需要在一些关键工序后设立质量控制点,这样可以及时发现上段工序中的品质问题并加以纠正,杜绝不合格产品进入下道工序,将因品质引起的经济损失降低到最小程度。质量控制点的设置与生产工艺流程有关,我们生产的产品IC卡电话机是一单面贴插混装板,采用先贴后插的生产工艺流程,并在生产工艺中加入以下质量控制点,如图1所示。 1)烘板检测内容 a.印制板有无变形;b.焊盘有无氧化;c、印制板表面有无划伤; 检查方法:依据检测标准目测检验。 2)丝印检测内容 a.印刷是否完全; b.有无桥接; c.厚度是否均匀;d.有无塌边;e.印刷有无偏差; 检查方法:依据检测标准目测检验或借助放大镜检验。 3)贴片检测内容 a.元件的贴装位置情况;b.有无掉片;c.有无错件; 检查方法:依据检测标准目测检验或借助放大镜检验。 4)回流焊接检测内容 a.元件的焊接情况,有无桥接、立碑、错位、焊料球、虚焊等不良焊接现象.b.焊点的情况. 检查方法:依据检测标准目测检验或借助放大镜检验. 5)插件检测内容 a.有无漏件;b.有无错件;e.元件的插装情况;
检查方法:依据检测标准目测检验。 图 1 质量过程控制点的设置 1.2 检验标准的制定 每一质量控制点都应制订有相应的检验标准,内容包括检验目标和检验内容,质检员应严格依照检验标准开展工作。若没有检验标准或内容不全,将会给生产质量控制带来相当大的麻烦。如判定元件贴偏时,究竟偏移多少才算不合格呢?质检员往往会根据自己的经验来判别,这样就不利于产品质量的均一、稳定。制定每一工序的质量检验标准的,应根据其具体情况,尽可能将所有缺陷列出,最好采用图示的方法,以便于质检员理解、比较。例如表1是回流焊接后焊锡球缺陷的检验标准。 表 1 焊锡球缺陷的检验标准 1.3 质量缺陷数的统计 在SMT生产过程中,质量缺陷的统计十分必要,它将有助于全体职工包括企业决策者在内,能了解到企业产品质量情况。然后作出相应对策来解决、提高、稳定产品质量。其中某些数据可以作为员工质量考核、发放奖金的参考依据。 在回流焊接和波峰焊接的质量缺陷统计中,我们引入了国外的先进统计方法—PPM质量制,即百万分率的缺陷统计方法。计算公式如下: 缺陷率[PPM]=缺陷总数/焊点总数*106 焊点总数=检测线路板数×焊点
SMT过程控制工具
SMT过程控制的几种实用工具 (时间:2007-8-20 18:20:14 共有 700 人次浏览) SMT过程控制的几种实用工具 SMT组装过程的质量控制决定印制板组件的产品质量,其目的是限制及减少种种因素的影响,保证建立稳定的组装过程,为此SMT组装厂需要制定良好的过程控制计划,应用监测产品与过程的可靠方法。但是不少SMT组装厂在实际生产过程中,至今还没有对对印制板组装全过程的质量水平进行量化评估,仍然仅仅采用统计印制板组件不合格个数方法。显然,因为缺陷已经产生,仅计印制板组件不合格数只能是一种消极的行为。测量评估组装过程的质量水平,有利于予防缺陷的产生,是一种积极,具有前摄性的措施。 实施过程控制计划计更应该着重于测量组装过程的质量水平,将精力集中在缺陷的予防上。本文将讨论有关过程控制的一些基本概念及工具,检测方法,表征质量水平的量度。 组装过程的质量控制可分为四个层面; l 予防与发现;工艺是否处于或超出控制之中。组装工艺具有能力生产可接受的产品,或丧失能力。如后者,需要进入以下三个层面的操作。 l 缺陷分析;有效分析及调查工艺及成品问题的原因,具备必需的技术及工具。 l 问题的解决;解决造成问题的技能与工具(因果分析图,直方图,管理图等)隔离引起问题的原因。 l 纠正措施;针对已被暴露的原因,提出与实施永久的解决方法。 过程控制的基本概念 过程控制有利于达到及维持组装过程所要求的工艺能力。应用数理统计方法,实施过程控制的顺序,如表1所示; 导致组装工艺过程变化是一些确定的因素,如操作差错(即未执行工艺文件)。于是如果工艺不重复,其结果(X bar R图所示)反映操作的变化,不是工艺变化。工艺超出控制的可能性,有时在测量之前,工程师努力试图工艺正确运行,以防止出现低‘记分’。然而,这一步有些徒劳的(self-defeating),SPC能用于稳定新工艺,也能改进现行工艺。 基本过程控制必须根准确测量与观察才能达到。控制图如直方图,离散性,记录及显示的数据,可变量数据(如粘接剂电胶点直径)是工艺的焦点,可由测量得到,属性数据可由观察达到,是产品焦点。一般,采集及分析属性数据是反应性行为,采集及分析可变量数据是更具前摄性的步序。 工具 过程控制依赖于用于测量,数据处理分析的统计工具。众知,七种质量控制工具(QC)是过程质量计划的基本部分,因为他们用于采集,显示及分析数据: 检查表(Check sheets);用于收集数据。简单,容易使用,有效显示各种结果。 排列图(Pareto charts);直方图以递减顺序显示缺陷的类别,可用于在众多因素分离出少数有价值的因素。
委外加工质量控制方案
文件编号: 委外加工质量控制方案 版本:V1.0 编写/日期: 审核/日期: 批准/日期: 文件修订记录
一、 目的: 确定外包业务质量控制要求,识别外部加工过程关键质量控制点,提前预防与控制,确保外包过程质量受控,持续交付符合要求的产品。 二、适用范围: 适用公司任何制造过程外包的控制,常规包含( PCBA-贴片 \ 成品-整机组装调试 \ 半成品模块组织 ) 三、委外加工质量控制方案: 3.1 委外加工过程及质量控制要求 x x x x x QCP1:控制要求--委外前SQA 审计确认 1、 委外商必须在“合格供应商”名录; 2、 委外商必须具备相应加工能力 ◆ 设备:SMT 设备满足单板加工与检测能力, 整机制造设备已通过LUSTER 工艺工程师确认; ◆ 人:关键工序人员能力通过LUSTER 工艺部 门培训与考核 3、 新机种导入或新供应商初次导入情况, “LUSTER 工艺工程师”必须现场跟线,确保试制过程无问题及风险; 4、 新机种导入或新供应商初次导入情况,必须 执行“试产爬坡计划”,小量-批量至少执行3次爬坡要求。 控制点不符合要求处理说明: ◆ 通知委外商停产整顿; ◆ 委外商被审计发现不符合加工要求 的对采购主管作通报处分 ◆ 审计发现如因标准未对齐,导致加工 问题,对工艺主管作通报处分 资料包清单按FOAN-ISC-007-008《委外生产交付操作流程》要求执行
3.2 SQA 现场审计频率要求 重点关注整机委外商的现场审计活动,审计范围聚集4M1E 标准要求,审计周期以月度为单位,在委外商正常生产时,随机组织抽样审计活动,每次审计要求输出《委外商制造现场审计报告》 ; 3.3委外加工过程异常改进要求 LUSTER SQA 出具《质量问题整改单》后,要求在3个工作日完成问题定位与输出解决方案,问题会滚入下一轮现场审计闭环关注点。 四、相关流程与制度 4.1、FOAN-ISC-007-008 委外生产交付操作流程 4.2、FOAN-ISC-007-005 委外生产报表需求规定 4.3、SMT 过程常规标准要求 按LUSTER –SOP 要求执行 QCP6:整机调试要求 ◆ 按LUSTER-SOP 《生产规格》要求执行 ◆ 记录调试异常、异常维修原因,以《生产过程维修记录》体现;维修替换的器件必须保留; QCP7:整机测试要求 ◆ 按LUSTER-SOP-《检验规格》要求执行 ◆ 记录检验异常、异常维修原因,以《生产过程维修记录》体现;维修替换的器件必须保留; 控制点不符合要求处理说明: ◆ 无生产过程记录,交付产品按不合格 批次处理 ◆ 无异常与维修记录,损耗物料全部折 成现款从加工费内扣除 按LUSTER-SOP 要求执行 ◆ 首次试产提供批次《试产报告》反馈至LUTSTER 质量部与工艺部; (描述制造全过程问题记录,识别产品硬件设计、工艺设计不足而影响SMT 效率问题) ◆ 正常批量后,要求以月度提供质量报告;包含“产品各工序直通率趋势,单工序异常统计 报告及异常维修记录”。
外发SMT代工质量管控要求范文
外发SMT代工质量管控要求范文 一、目的: 建立外发SMT质量管控要求,识别物料管理、工艺控制、异常处理等控制项,推动品质稳定及持续提升。 二、范围: 适用于外发SMT贴件厂家 三、内容: (一)新机种导入管控 1:安排试产前召集生产部、品质部、工艺等相关部门试产前会议,主要说明试产机种生产工艺流程、要求各工位之品质重点 2:制造部按生产工艺流程进行或工程人员安排排线试产过程中,各部门担当工程师(工艺)须上线进行跟进,及时处理试产过程中出现的异常并进行记录 3:品质部需对试产机种进行手件核对与各项性能与功能性测试,并填写相应的试产报告(试产报告以邮件发送至我司工程) (二)ESD管控 1.加工区要求:仓库、贴件、后焊车间满足ESD控制要求,地面铺设防静电材料,加工台铺设防静电席,表面阻抗104-1011Ω,并接静电接地扣(1MΩ±10%);
2.人员要求:进入车间需穿防静电衣、鞋、帽,接触产品需佩戴有绳静电环; 3.转板用架、包装用泡棉、气泡袋,需要符合ESD要求,表面阻抗<1010Ω, 4.转板车架需外接链条,实现接地; 5.设备漏电压<0.5V,对地阻抗<6Ω,烙铁对地阻抗<20Ω,设备需评估外引独立接地线; (三)MSD管控 1.BGA.IC.管脚封装材料,易在非真空(氮气)包装条件下受潮,SMT 回流时水分受热挥发,出现焊接异常,需用100%烘烤。 2.BGA 管制规范 (1)真空包装未拆封之BGA 须储存于温度低于30°C,相对湿度小于70%的环境,使用期限为一年. (2)真空包装已拆封之BGA 须标明拆封时间,未上线之BGA,储存于防潮柜中,储存条件≤25°C、65%RH,储存期限为72hrs. (3)若已拆封之BGA但未上线使用或余料,必须储存于防潮箱内(条件≤25℃,65%R.H.)若退回大库房之BGA由大库房烘烤后,大库房改以抽真空包装方式储存 (4)超过储存期限者,须以125°C/24hrs烘烤,无法以125°C烘烤者,则以80°C/48hrs烘烤(若多次烘烤则总烘烤时数须小于96hrs),才可上线使用. (5)若零件有特殊烘烤规范者,另订入SOP.
SMT核心工艺技术、质量控制与案例解析
SMT核心工艺技术、质量控制与案例解析 招生对象 --------------------------------- 研发部经理,研发主管,R&D工程师,SMT工程经理,制程主管,质量工程部主管,制程工程师(PE),NPI主管,NPI工程师,设备课主管,设备工程师(ME),生产部主管,QE(质量工程师),PIE工程师,及SMT工艺技术管理的相关人员等。 【主办单位】中国电子标准协会 【咨询热线】0 7 5 5 – 2 6 5 0 6 7 5 7 1 3 7 9 8 4 7 2 9 3 6 李生【报名邮箱】martin#https://www.360docs.net/doc/fd8831070.html, (请将#换成@) 课程内容 --------------------------------- 前言:随着电子元器件的小尺寸化和组装的高密度化,SMT的工艺窗口越来越小,组装的难度越来越大,如何建立一个稳固而耐用的工艺,已经成为SMT的核心问题。而当前SMT 组装高可靠性、高组装良率、低成本、低制损要求,令工程技术和管理人员很有压力。SMT 的核心工艺技术,是以提高产品质量、降低产品成本为导向的。SMT对电子产品质量影响最大的莫过于工艺缺陷,是否有能力准确地定位、分析、解决电子制造工艺缺陷成为提高电子产品质量的关键。 为此,中国电子标准协会特举办为期二天的“SMT核心工艺、质量控制与案例解析”。本课程全面地讲解了实际生产中遇到的、由各种因素引起的工艺问题和质量问题,对于工程技术和管理人员处理生产现场问题、提高组装的可靠性和质量具有重要作用。欢迎报名参加! 二、课程特点: 本课程结合了《SMT核心工艺解析与案例分析》和《SMT工艺质量控制》两本书中的精华部分,以及贾忠中老师新近在一些手机板上设计和制程中遇到的、还未曾公开的典型案例,并由贾忠中老师亲自主讲。贾忠中老师总结多年的工作经验和实例,他深入浅出并整合SMT 业界最新的工艺技术、质量控制方法以及实践成果打造而成,是业内少见的系统讲解SMT核心工艺、质量控制与案例分析的精品课程。 三、参加对象: 研发部经理,研发主管,R&D工程师,SMT工程经理,制程主管,质量工程部主管,制程工程师(PE),NPI主管,NPI工程师,设备课主管,设备工程师(ME),生产部主管,QE(质量工程师),PIE工程师,及SMT工艺技术管理的相关人员等。 四、课程收益: 1.掌握SMT电子组装的相关核心技术、质量控制方法;