橡胶配合加工技术讲座第4讲聚异戊二烯橡胶_IR_续完_
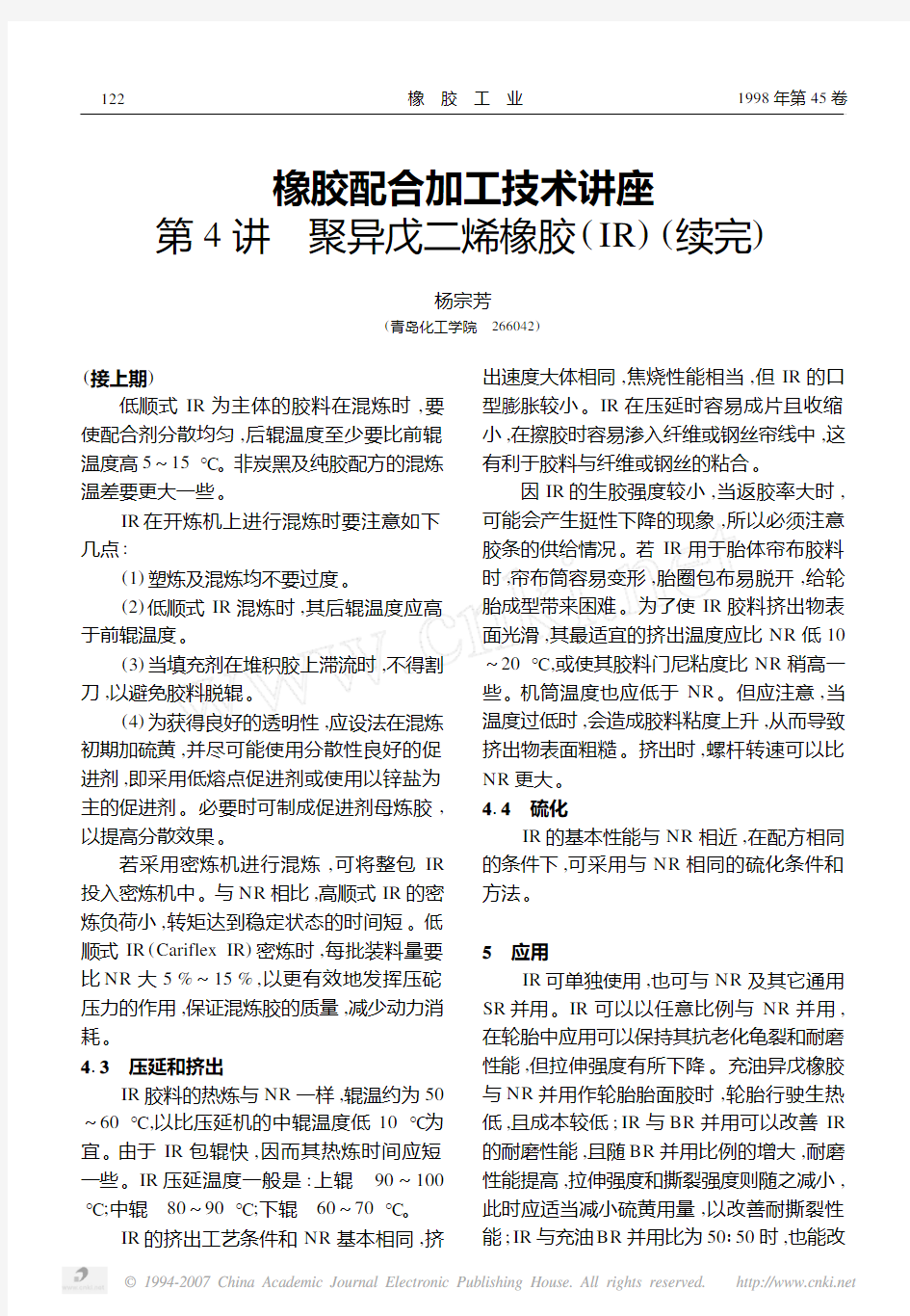

橡胶配合加工技术讲座
第4讲 聚异戊二烯橡胶(IR)(续完)
杨宗芳
(青岛化工学院 266042)
(接上期)
低顺式IR为主体的胶料在混炼时,要使配合剂分散均匀,后辊温度至少要比前辊温度高5~15℃。非炭黑及纯胶配方的混炼温差要更大一些。
IR在开炼机上进行混炼时要注意如下几点:
(1)塑炼及混炼均不要过度。
(2)低顺式IR混炼时,其后辊温度应高于前辊温度。
(3)当填充剂在堆积胶上滞流时,不得割刀,以避免胶料脱辊。
(4)为获得良好的透明性,应设法在混炼初期加硫黄,并尽可能使用分散性良好的促进剂,即采用低熔点促进剂或使用以锌盐为主的促进剂。必要时可制成促进剂母炼胶,以提高分散效果。
若采用密炼机进行混炼,可将整包IR 投入密炼机中。与NR相比,高顺式IR的密炼负荷小,转矩达到稳定状态的时间短。低顺式IR(Cariflex IR)密炼时,每批装料量要比NR大5%~15%,以更有效地发挥压砣压力的作用,保证混炼胶的质量,减少动力消耗。
413 压延和挤出
IR胶料的热炼与NR一样,辊温约为50~60℃,以比压延机的中辊温度低10℃为宜。由于IR包辊快,因而其热炼时间应短一些。IR压延温度一般是:上辊 90~100℃;中辊 80~90℃;下辊 60~70℃。
IR的挤出工艺条件和NR基本相同,挤出速度大体相同,焦烧性能相当,但IR的口型膨胀较小。IR在压延时容易成片且收缩小,在擦胶时容易渗入纤维或钢丝帘线中,这有利于胶料与纤维或钢丝的粘合。
因IR的生胶强度较小,当返胶率大时,可能会产生挺性下降的现象,所以必须注意胶条的供给情况。若IR用于胎体帘布胶料时,帘布筒容易变形,胎圈包布易脱开,给轮胎成型带来困难。为了使IR胶料挤出物表面光滑,其最适宜的挤出温度应比NR低10~20℃,或使其胶料门尼粘度比NR稍高一些。机筒温度也应低于NR。但应注意,当温度过低时,会造成胶料粘度上升,从而导致挤出物表面粗糙。挤出时,螺杆转速可以比NR更大。
414 硫化
IR的基本性能与NR相近,在配方相同的条件下,可采用与NR相同的硫化条件和方法。
5 应用
IR可单独使用,也可与NR及其它通用SR并用。IR可以以任意比例与NR并用,在轮胎中应用可以保持其抗老化龟裂和耐磨性能,但拉伸强度有所下降。充油异戊橡胶与NR并用作轮胎胎面胶时,轮胎行驶生热低,且成本较低;IR与BR并用可以改善IR 的耐磨性能,且随BR并用比例的增大,耐磨性能提高,拉伸强度和撕裂强度则随之减小,此时应适当减小硫黄用量,以改善耐撕裂性能;IR与充油BR并用比为50∶50时,也能改
善抗老化龟裂性能,生热也较低。IR用于制造载重轮胎和越野轮胎时,完全可以替代NR。
目前,世界各国都在向生产子午线轮胎过渡,这有助于扩大IR在子午线轮胎生产中的应用。但IR硫化胶的拉伸强度和撕裂强度均不及NR,在航空轮胎和大型轮胎中仍不能完全替代NR。IR还广泛用于生产帘布胶、输送带、机械配件制品、胶管、胶带、海绵、胶粘剂、电线电缆、运动器械、医用橡胶制品和胶鞋等。例如:
(1)IR用于轮胎内胎的胶料配方为:NR 40;IR 20;BR 20;SBR 20;硫黄 1;促进剂 111;氧化锌 5;硬脂酸 2;防老剂 215;炭黑 48;软化剂 9;石蜡 115;树脂 2。
(2)IR用于轮胎胎面的胶料配方为:NR 30;IR 20;BR 40;SBR 10;活化胶粉 5;硫黄 112;促进剂 111;氧化锌 4;硬脂酸 3;防老剂 315;炭黑 53;软化剂 5;石蜡 1。
(3)IR用于轮胎胎体的胶料配方为:NR 50;IR 30;BR 10;SBR 10;硫黄 213;促进剂 1115;氧化锌 5;硬脂酸 215;防老剂 3;炭黑 35;软化剂 10;石蜡 015。
IR轮胎内胎、胎面和胎体的胶料性能分别见表2~4。
6 其它异戊橡胶
611 充油异戊橡胶
在IR中填充不同用量的油(如环烷油、芳烃油),不仅能改善IR的物理性能,还可降低成本。
IR充油后硬度、定伸应力和拉伸强度均降低,扯断伸长率增大,其性能变化随充油量的增大而增大。油的相对分子质量对IR胶料的物理性能有一定影响,使用相对分子质量低的油,胶料的物理性能稍有下降。油中芳香组分的质量分数对硫化胶的性能影响不明显。
充油异戊橡胶和未充油的IR一样,在高温混炼时配合剂的分散不好,因而由于混炼操作程序不同,胶料的性能有差异。通常先经破胶的生胶,若在混炼时容易发粘,则说明填充剂分散良好。在密炼机中加工时,可加入适量的增粘剂。混炼时配合剂按一般顺序加入。若与NR或SBR并用,应先将NR 或SBR塑炼,然后加入充油异戊橡胶。
表2 IR轮胎内胎胶料性能
性 能内胎胶料
硫化仪数据(147℃)
t10/min913
t90/min1817
硫化时间(137℃)/min2030
拉伸强度/MPa19162018
扯断伸长率/%668637
300%定伸应力/MPa611714
邵尔A型硬度/度5657
扯断永久变形/%2419
撕裂强度/(kN?m-1)9295
100℃×48h老化后
拉伸强度/MPa—1915
扯断伸长率/%—520
表3 IR轮胎胎面胶料性能
性 能胎面胶料
硫化仪数据(147℃)
t10/min514
t90/min1617
硫化时间(142℃)/min304060
拉伸强度/MPa221122162115
扯断伸长率/%564560543 300%定伸应力/MPa9169171115
邵尔A型硬度/度666666
扯断永久变形/%161512
撕裂强度/(kN?m-1)98109—
回弹值/%3131—
磨耗量01060109—100℃×48h老化后
拉伸强度/MPa12141412—
扯断伸长率/%248284—
注:磨耗量的单位为cm3?(1161km)-1。
表4 IR轮胎胎体胶料性能
性 能胎体胶料
硫化仪数据(147℃)
t10/min615
t90/min1116
硫化时间(137℃)/min203040
拉伸强度/MPa221426192514
扯断伸长率/%614557553 300%定伸应力/MPa618811814
邵尔A型硬度/度575959
扯断永久变形/%262222
撕裂强度/(kN?m-1)8593—
H抽出力/N117138—
回弹值/%5555—100℃×48h老化后
拉伸强度/MPa13111119—
扯断伸长率/%352324—
填料填充量大的胶料,硫化剂易于分散;填充量小的胶料或纯胶胶料,采用低熔点的促进剂对分散较为有利。加入黑油膏或者用硫黄或促进剂制成母炼胶则有利于分散。充油异戊橡胶具有很好的流动性,适用于复杂的模型制品,可以单用,也可与NR,SBR及CR并用,直接制造模压胶鞋、胶带、轮胎、透明橡胶制品和低填充量橡胶制品。
612 反式21,42聚异戊二烯橡胶
反式21,42聚异戊二烯橡胶又叫做合成的巴拉塔橡胶。
60年代初,英国登录普公司和加拿大宝兰山公司相继实现了工业化,均为中等规模,日本可乐丽公司于1974年建成年产200t 的生产装置,前苏联则在80年代实现工业化。我国吉林化学工业公司研究院于1982年研制出了反式聚异戊二烯橡胶,并在中试装置上进行了试生产,所得产品已加工成医用夹板作临床试用。
尽管反式21,42聚异戊二烯橡胶与NR 的化学组成一样,但由于它们的立体结构或基团的空间排列不同,因而性能上有很大差异,这些差异主要归结于顺式异构体在室温下是非结晶型聚合物,具有低硬度和低拉伸强度,而反式异构体则在低于60℃的温度下即迅速结晶,是具有高硬度和高拉伸强度的结晶型聚合物。反式21,42聚异戊二烯橡胶具有极好的耐臭氧性,除浓硫酸和浓硝酸外,它对浓氢氟酸、盐酸、碱类、植物油和脂肪都非常稳定。纯反式21,42聚异戊二烯橡胶在室温下溶于大多数芳烃、氯代烃、醚和二硫化碳,基本上不溶于直链饱和烃、酯类和酮类。反式21,42聚异戊二烯橡胶对水的吸收以及水在其中的扩散速度极低,故适于制作各种耐臭氧、耐水和耐酸制品。
反式21,42聚异戊二烯橡胶可以采用注射成型、挤出成型和压延成型等工艺。胶料冷却后,恢复结晶,因而硬度和拉伸强度亦恢复。反式21,42聚异戊二烯橡胶也可以采取一般硫化工艺,经过硫化交联处理,其耐热和耐化学稳定性提高。反式21,42聚异戊二烯橡胶主要用来制造高尔夫球皮层。还可用作压敏胶粘剂、热封涂层、改性剂(以使热塑性塑料获得较高耐冲击性和扯断伸长率)以及海底电缆、电线、医用夹板等。但由于其生产成本较高,目前尚未广泛应用。
7 聚戊烯橡胶
711 聚戊烯橡胶
聚戊烯橡胶是一种不饱和聚合物,用齐格勒2纳塔催化剂在溶液中由环戊烯进行开环聚合而成,其直链结构随催化体系的不同而异。
聚戊烯橡胶的相对分子质量分布较宽,其粘合性能优于其它通用SR。此外,聚戊烯橡胶的线形分子链较长,因而弹性复原性较差;其热塑性较好,因而具有较好的压型性。
聚戊烯橡胶可用一般硫化体系硫化,所用促进剂可比BR和IR都少,胶料可高温长时间硫化而无硫化返原现象。
聚戊烯橡胶的低温性能好,拉伸强度、定
伸应力、撕裂强度随温度下降而增大,而扯断伸长率变化不大。其弹性及耐磨性略优于NR,并有良好的耐热老化性能。
712 高反式聚戊烯橡胶
高反式聚戊烯橡胶反式结构的质量分数为90%以上,平均相对分子质量约为30万,门尼粘度约为125,玻璃化温度为-90℃。其生胶具有结晶性和自补强性,强度大,抗撕裂性和耐热性能良好,耐臭氧性能优于NR 而次于CR。
高反式聚戊烯橡胶可与顺式IR和EPR 等并用,以改善并用胶的性能。可用于轮胎、胶带、胶管等。
8 结语
据分析,在较长时间内,NR价格仍将居高不下,世界NR的短缺状况将持续到2010年。在国内,1995年全国橡胶总消耗量为142万t,其中NR约为75万t(进口占3119万t)。2000年全国橡胶总消耗量预计将达到180万~190万t,国产NR的产量可达约45万t,届时若SR的使用比例按50%计,则NR的缺口将达到45万~50万t,比目前NR的年进口量高50%以上,这将对我国橡胶加工业产生巨大的压力。
国内一些轮胎厂在完全不改变原生产装置的情况下,在胎面胶中以20%~30%的IR、在胎体帘布胶中以30%~40%的IR替代NR生产。实践证明,IR替代部分NR生产轮胎是完全可行的。另外,用IR替代NR 与SBR并用生产轮胎内胎,其工艺稳定,成品性能可满足G B1191—82要求,透气性能基本不变,平均每条轮胎可降低生产成本0176元,经济效益显著。
90年代初期,我国橡胶界对发展IR的必要性认识不足,加之受原料资源等因素的制约,其基础研究受到一定的影响。为了充分利用石油化工资源,希望今后加强IR的基础研究,适度发展IR,以弥补我国NR的不足。
轮胎胎面胶
目录 摘要 一?汽车轮胎胎面胶国内外生产情况 二?胎面胶的制造(加工原理, 加工方法) 1、胎面挤出联动装置 2、挤出口型板的制备 胎面挤出工艺 1、胎面胶挤出用胶的热炼和供胶 2、胎面胶挤出 三?配方组成,及配方的计算。 四?胎面胶的加工工艺,及工艺简述和工艺流图。五?产品的应用,发展趋势。
摘要 随着汽车工业和交通运输业的高速发展公路建设特别是高速公路的迅猛发展, 迫切需要各种高性能轮胎。先后出现了所谓的安全轮胎、节能轮胎、高性能轮胎、冬季轮胎、全天候轮胎或者全季节轮胎以及环境轮胎等各种新型轮胎。进入90年代后,绿色运动的广泛开展使人们对节油效益有了更多的了解,出现了所谓“绿色轮胎”。近几十年来国内外对轮胎性能研究的重点集中在滚动损失,抗湿滑性和耐磨性等3个方面,特别是抗湿滑。这3种性能也被称为汽车轮胎 的三大行驶性能。由于子午线轮胎结构的采用,使胎面耐磨性能比斜交轮胎提了 30%~%,因此耐磨性已不再成为子午线轮胎的性能指标。考虑到汽车行驶的安全性,尤其是雨天和冰面上的安全性,对轮胎的高性能研究主要集中在滚动损失和湿抓着力上。然而,抗湿滑性与低滚动阻力往往是相互矛盾的,一般而言,提高胎面胶料的滞后损失可改善湿抓着力但增大了滚动阻力;而降低滚动阻力的同时湿抓着力又降低了。如何平衡这一对矛盾是胎面胶的研究热点。研究表明,控制滚动损失的温度和频率与控制湿抓着力的温度和频率不同,后者是在较低温度和较高频率时发生的,所以在某种程度上是可以得到平衡的。传统胎面胶主要有顺丁橡胶(BR)、天然橡胶(NR)和丁苯橡胶(SBR),其中BR的滚动损小,但湿抓着性很差;SBR的湿抓着性较好,但滚动阻力大;而NR的性能介于两者间。要减小胎面的滚动损失而又不牺牲湿抓着力,传统单一的聚合物材料显得无能力[1]。所以要开发新型 聚合物,或者采用并用胶,或者通过对现有的胎面材料进行化学改性来平衡这对矛盾。使胎面胶在0℃左右的tanδ尽量高,而在60℃左右的tan δ尽量低。从而得到理想的效果
【精品】橡胶英才网轮胎胶料配方设计
轮胎胶料配方设计 第一节轮胎各部件胶料配方设计 一、胎面胶、胎侧胶配方设计 1、胎面胶、胎侧胶性能要求 (1)胎面胶性能要求由于胎面是轮胎与路面直接接触的部位,承受着轮胎最苛刻的外应力作用,经常出现的损坏形式为胎面磨光、刺扎损坏、花纹崩花及裂口, 导致胎体爆破,影响轮胎的使用寿命。因此,胎面胶应具有优越的耐磨性,较高的 拉伸强度和撕裂强度,良好的耐老化、耐屈挠、耐热、抗刺扎和抗花纹沟裂口等性 能。 (2)胎侧胶性能要求胎侧即轮胎两侧,是侧向变形最大的部位,胎侧胶较薄, 用以保护胎体免受机械损伤及日光、风雨的侵蚀,其损坏形式为屈挠龟裂、机械损 伤。因此,胎侧胶应具有良好的强伸性能及耐屈挠龟裂、耐大气老化等性能。胎面胶、胎侧胶可用一种胶料制备,但一种胶料难以同时满足各种不同性能的
要求.目前大中型载重轮胎已普遍采用分层出形的复合胎面胶,既利于提高产品质 量,又可降低成本。分层压出形式常用的有以下三种形式。 ①胎冠上层用一种胶料,胎冠下层胶与胎侧共用一种胶料。 ②胎冠上、下层用一种胶料,胎侧用另一种胶料。 ③胎冠、胎肩、胎侧分别采用三种胶料。 2、胎面胶、胎侧胶配方 (1)胎面胶配方特点胎面胶与胎冠上层胶配方相同。 ①常用生胶品种有NR、SBR和BR.NR具优异的弹性、拉伸强度和耐磨性能, 是轮胎胶料中理想的胶种,虽然使用中出现裂口较快,但其扩展速率比SBR和BR 慢。SBR具有优良的耐磨和耐老化性能.BR的弹性更优于NR并具有良好的耐磨性 和生热低的特点,适宜用于轮胎胎面胶较料中。 通常大型轮胎如工程机械轮胎胎面以NR单用为宜.中小型轮胎胎面胶则以NR 为主,掺用SBR或BR,拖拉机轮胎胎面也可采用三胶并用的配方.
橡胶术语
合成橡胶术语 2 合成橡胶术语terms of synthetiC rubber 2.1 通用橡胶general rubbers 2.1.1 丁苯橡胶styrene butadiene rubber (SBR) 丁二烯、苯乙烯的橡胶状共聚物。 2.1.1.1乳聚丁苯橡胶emulsion polymerized styrene butadiene rubber 丁二烯、苯乙烯在乳液体系中进行共聚制得的橡胶。 2.1.1.1.1热聚丁苯橡胶hot polymerized styrene butadiene rubber 聚合温度为50℃左右,该胶支化较多且含有大量的微凝胶。 2.1.1.1.2冷聚丁苯橡胶cold polymerized styrene butadiene rubber聚合温度为5℃左右,其硫化胶性能优于高温丁苯橡胶。 2.1.1.1.3填充丁苯橡胶filled styrene butadiene rubber填充油、炭黑等的丁苯橡胶。 2.1.1.1.4高苯乙烯橡胶high styrene rubber苯乙烯含量为50%~80%的丁苯橡胶,兼具塑料与橡胶的性能。 2.1.1.1.5羧基丁苯橡胶carboxyliC styrene butadiene rubber用丙烯酸,甲基丙烯酸等不饱和有机羧酸作为第三单体制得主链上带有羧基的丁苯橡胶。 2.1.1.1.6液体丁苯橡胶liquid styrene butadiene rubber分子量小于10000在室温下呈液态的丁苯橡胶。 2.1.1.2溶聚丁苯橡胶solution polymerized styrene butadiene rubber丁二烯、苯乙烯在溶液体系中进行共聚制得的丁苯橡胶。品种有:无规立构溶聚丁苯橡胶、有规立构溶聚丁苯橡胶。 2.1.1.3热塑丁苯橡胶thermoplastic styrene butadiene rubber(SBS) 苯乙烯与丁二烯的嵌段共聚物,从几何结构上又可分为星型及线型。 2.1.1.4充油热塑丁苯橡胶oil-extended thermoplastic styrene butadiene rubber 添加填充油的热塑性丁苯橡胶。 2.1.2 聚丁二烯橡胶polybutadiene rubber(BR) 丁二烯为单体聚合制得的橡胶。 2.1.2.1 顺式聚丁二烯橡胶cis-poiybutadiene rubber 丁二烯经定向聚合制得的顺式-1,4聚丁二烯橡胶,该胶按其顺式—1,4结构含量不同分为: 高顺式聚丁二烯橡胶;顺式—1,4结构含量为90%。 中顺式聚丁二烯橡胶:顺式—1,4结构含量为65%。 低顺式聚丁二烯橡胶:顺式—1,4结构含量为35%。 2.1.2.2 反式聚丁二烯橡胶rans-polybutadiene rubber丁二烯经定向聚合制得的高反式—1,4结构含量的聚丁二烯橡胶。 2.1.2.3 乙烯基聚丁二烯橡胶 2.1.2. 3.1 中乙烯基聚丁二烯橡胶medium vinyl polybutadiene rubber 乙烯基含量为35%~55%的聚丁二烯橡胶。 2.1.2.1.2 高乙烯基聚丁二烯橡胶high vinyl polybutadiene rubber 乙烯基含量为65%~85%的聚丁二烯橡胶。 2.1.2.4 液体聚丁二烯橡胶。liquid polybutadiene rubber 分子量低,在室温下呈液态的聚丁二烯橡胶,可分为带活性基团和不带活性基团的两种。 2.1.2.5 充油聚丁二烯橡胶oil—extended polybutadiene rubber 添加填充油的聚丁二烯橡胶。 2.1.9 聚异戊二烯橡胶polyisoprene rubber(1R) 以异戊二烯为单体用立体定向聚合方法制得的有规立构橡胶,它的分子结构与天然橡胶相同,性能也很接近,所以又称合成天然橡胶。 2.1. 3.1 顺式—1,4聚异戊二烯橡胶cis—1,4polyisoprene rubber 以异戊二烯为单体,用定向聚合制得的一种高顺式—1,4结构含量的橡胶。 2.1. 3.2 反式—1,4聚异戊二烯橡胶trans—1,4 polyisoprene rubber 以异戊二烯为单体,用定向聚合制得的一种高反式—1,4结构含量的橡胶。 2.1. 3.3 液体聚异戊二烯橡胶liquid polyisoprene rubber 分子量低,在室温下呈液态的异戊二烯橡胶。 2.1. 3.4 填充聚异戊二烯橡胶filled polyisoprene rubber 填充油、炭黑等的聚异戊二烯橡胶。 2.1.4 丁基橡胶butyl rubber (isobutylene isoprene rubber
橡胶加工工艺基础知识
橡胶加工工艺基础知识 一、塑炼 橡胶受外力作用产生变形,当外力消除后橡胶仍能保持其形变的能力叫做可塑性。增加橡胶可塑性工艺过程称为塑炼。橡胶有可塑性才能在混炼时与各种配合剂均匀混合; 在压延加工时易于渗入纺织物中;在压出、注压时具有较好的流动性。此外,塑炼还能使橡胶的性质均匀,便于控制生产过程。但是,过渡塑炼会降低硫化胶的强度、弹性、耐磨等性能,因此塑炼操作需严加控制。 橡胶可塑度通常以威廉氏可塑度、门尼粘度和德弗硬度等表示。 1、塑炼机理 橡胶经塑炼以增加其可塑性,其实质乃是使橡胶分子链断裂,降低大分子长度。断裂作用既可发生于大分子主链,又可发生于侧链。由于橡胶在塑炼时,遭受到氧、电、热、机械力和增塑剂等因素的作用,所以塑炼机理与这些因素密切相关,其中起重要作用的则是氧和机械力,而且两者相辅相成。通常可将塑炼区分为低温塑炼和高温塑炼,前者以机械降解作用为主,氧起到稳定游离基的作用;后者以自动氧化降解作用为主,机械作用可强化橡胶与氧的接触。 塑炼时,辊筒对生胶的机械作用力很大,并迫使橡胶分子链断裂,这种断裂大多发生在大分子的中间部分。 塑炼时,分子链愈长愈容易切断。顺丁胶等之所以难以机械断链,重要原因之一就是因为生胶中缺乏较高的分子量级分。当加入高分子量级分后,低温塑炼时就能获得显著的效果。 氧是塑炼中不可缺少的因素,缺氧时,就无法获得预期的效果。生胶塑炼过 塑炼时,设备与橡胶之间的摩擦显然使得胶温升高。热对塑炼效果极为重要,而且在不同温度范围内的影响也不同。 由于低温塑炼时,主要依靠机械力使分子链断裂,所以在像章区域内(天然胶低于110℃)随温度升高,生胶粘度下降,塑炼时受到的作用力较小,以致塑炼效果反而下降。 相反,高温塑炼时,主要是氧化裂解反应起主导作用,因而塑炼效果在高温区(天然胶高于110℃)将随温度的升高而增大,所以温度对塑炼起着促进作用。各种橡胶由于特性不同,对应于最低塑炼效果的温度范围也不一样,但温度对塑炼效果影响的曲线形状是相似的。由前已知,不论低温塑炼还是高温塑炼,使用化学增塑剂皆能提高塑炼效果。接受剂型增塑剂,如苯醌和偶氮苯等,它们在低温塑炼时起游离基接受剂作用,能使断链的橡胶分子游离基稳定,进而生成较短的分子;引发剂型增塑剂,如过氧化二苯甲酰和偶氮二异丁腈等,它们在高温下分解成极不稳定的游离基,再引发橡胶分子生成大分子游离基,并进而氧化断裂。此外,如硫醇类及二邻苯甲酰胺基苯基二硫化物类物质,它们既能使橡胶分子游离基稳定,又能在高温下引发橡胶形成游离基加速自动氧化断裂,所以,这类化学增塑剂称为混合型增塑剂或链转移型增塑剂。 2、塑炼工艺 生胶在塑炼前通常需进行烘胶、切胶、选胶和破胶等处理。烘胶是为了使生胶硬度降低以便切胶,同时还能解除结晶。烘胶要求温度不高,但时间长,故需注意不致影响橡胶的物理机械性能;例如天然胶烘胶温度一般为50~60℃,时间则需长达数十小时。生胶自烘房中取出后即切成10~20公斤左右的大块,人工选除其杂质后再用破胶机破胶以便塑炼。按塑炼所用的设备类型,塑炼可大致分为三种方法。 1、开炼机塑炼 其优点是塑炼胶料质量好,收缩小,但生产效率低,劳动强度大。此法适宜于胶料变化多和耗胶量少的工厂。 开炼钢机塑炼属于低温塑炼。因此,降低橡胶温度以增大作用力是开炼机塑炼的关键。与温度和机械作用有关的设备特性和工艺条件都是影响塑炼效果的重要因素。 为了降低胶温,开炼钢机的辊筒需进行有效的冷却,因此辊筒设有带孔眼的水管,直接向辊筒表面喷水冷却以降低辊筒需进行有效的冷却,这样可以满足各种胶料塑炼时对辊温的基本要求。此外,采用冷却胶片的方法也是有效的,例如使塑炼形成的胶片通过一较长的运输带(或导辊)经空气自然冷却后再返回辊上,以及薄通塑炼(缩小辊距,使胶片变薄,以利于冷却)皆可。分段塑炼的目的也是为了降低胶温,其操作是将全塑炼过程分成若干段,来完成,每段塑炼后生胶需充分停放冷却。塑炼一般分为2~3段,每段停放冷却4~8小时。胶温随塑炼时间的延长而增高,若不能及时冷却,则生胶可塑性仅在塑炼初期显著提高,随后则变化很少,这种现象是由于生胶温度升高而软化,分子易滑动和机械降解效率降低所致。胶温高还会产生假可塑性,一旦停放冷却后,可塑性又降低。两个辊筒的速比愈大则剪切作用愈强;因此,塑炼效果愈好。缩小辊间距也可以增大机械剪切作用,提高塑炼效果。 2、密炼机塑炼(高温、间断) 密炼机塑炼的生产能力大,劳动强度较低、电力消耗少; 1 / 5
丁苯橡胶的配合及加工工艺
丁苯橡胶的配合及加工工艺 肖标 (安徽工业大学,安徽马鞍山 243002) 摘要:丁苯橡胶(SBR)是以丁二烯和苯乙烯为单体合成的共聚物,是目前世界上产量最高,消费量最大的通用合成橡胶(SR)品种[1]。它采用自由基引发的乳液聚合或阴离子溶液聚合工艺而得到的,工业上多采用乳液聚合法。本文将介绍丁苯橡胶的结构与种类、性能、应用、配合、加工工艺、研究进展以及未来展望等,对其生产工艺以及工艺条件控制进行深刻的探讨,最后对其国内外的供需现状和发展前景作出简单探讨。 关键词:丁苯橡胶、性能、乳液聚合、生产工艺、工艺条件控制 第一章绪论 1.1 丁苯橡胶的结构与种类 1.1.1丁苯橡胶的结构 聚合反应:CH 2=CH-CH=CH 2 +C 6 H 5 -CH=CH 2 ——→ -[CH 2-CH=CH-CH 2 ]x-[CH(C 6 H 5 )-CH 2 ]-y 典型丁苯橡胶的结构特征 1)大分子宏观结构包括 单体比例、平均相对分子质量及分布、分子结构的线性或非线性,凝胶含量等。 2)微观结构主要包括 丁二烯链段中顺式—1,4、反式—1,4和1,2—结构(乙烯基)的比例[2],苯乙烯、丁二烯单元的分布等。 3)无定形聚合物 因掺杂有苯乙烯链节,所以丁苯橡胶的主体结构不规整,不易结晶。 4)丁二烯的微观结构的变化对丁苯橡胶性能的影响不大 在丁苯橡胶硫化时,丁二烯链节中顺式—1,4和反式—1,4两种结构会发生异构而相互转化,最后可达到一个平衡态。又在低温丁苯和高温丁苯中1.2—丁二烯链节[1]的含量相差不太大.所以丁二烯微观结构的变化对丁苯橡胶性能的影响不大。 5)苯乙烯含量与玻璃化转变温度 丁苯橡胶的玻璃化温度取决于苯乙烯均聚物的含量。乙烯基的含量越低,玻璃化温度越低。可以按需要的比例从100%的丁二烯(顺式、反式的玻璃化温度都是-100℃)调够到100%的聚苯乙烯(玻璃化温度为90℃)。玻璃化温度对硫化橡胶的性质起重要作用,大部分乳液聚合丁苯橡胶含苯乙烯为23.5%,这种含量的丁苯橡胶具有较好的综合物理机械性能。 6)低温丁苯橡胶性能优于高温丁苯橡胶 高温(50℃)聚合时.支化较严重.凝胶物含量较高;在同等分子量下.分子量分布较宽。低温聚合下由于它的分子量分布较窄,硫化时不被硫化的低分子量部分较少,可均匀硫化.从而使交联密度较高。故由低温丁苯橡胶所得硫化胶的物理机械性能(如拉伸强度、弹性及加工性)均较高温丁苯为优.
端羟基聚异戊二烯及其共聚物的合成与表征(健宝开元)
研究?开发 弹性体,2009212225,19(6):5~8 CHINA EL ASTOM ERICS 收稿日期:20090611 作者简介:金玉顺(1968),女,吉林省吉林市人,副教授,博士,主要从事高分子合成及生物高分子方面的研究工作。3基金项目:北京市属市管高等学校人才强教计划资助项目;北京市教委科技发展计划资助项目(KM200810017007) 端羟基聚异戊二烯及其共聚物的合成与表征 3 金玉顺,郭文莉,李树新,商育伟 (北京石油化工学院材料科学与工程系,北京102617) 摘 要:以仲丁基锂为引发剂,引发异戊二烯本体负离子聚合,再用环氧丙烷甲醇终止法合成了端羟基聚异戊二烯;然后利用端羟基聚异戊二烯的活性端羟基,引发丙交酯的开环聚合制备了聚乳酸聚 异戊二烯共聚物,并采用IR 、1 H NMR 、T G 等测试手段对产品进行了表征。结果表明,通过改变仲丁 基锂及环氧丙烷的用量,可合成相对分子质量及羟基含量可控的且1,4结构质量分数超过87.5%的端羟基聚异戊二烯。 关键词:端羟基聚异戊二烯;聚乳酸;负离子聚合;共聚物 中图分类号:TQ 333.3 文献标识码:A 文章编号:100523174(2009)0620005204 端羟基聚异戊二烯液体橡胶是以异戊二烯为主链结构,分子链端带有羟基(—O H )的液体橡胶。由于其聚合组分简单、产品透明度好、粘度低、价格低廉,所以用途非常广泛。端羟基聚异戊二烯的合成方法有自由基聚合和负离子聚合两大类。自由基聚合方法[1~4]是最常用的,其操作简单且成本比较低,但是产品的分子链线性不好,分子链的微观结构不易调节。为此,人们开发了负离子法合成遥爪聚合物的工艺路线,并对其合成做了大量的工作[5] 。负离子法能控制聚合物的相对分子质量且相对分子质量分布窄,所以常用于端羟基聚异戊二烯的合成[6]。本课题采用负离子聚合方法制备了1,4结构含量较高的端羟基聚异戊二烯,然后利用端羟基聚异戊二烯的活性羟基,引发L 丙交酯单体开环聚合,制备了聚乳酸聚异戊二烯共聚物(PLLA PI ),并研究了该共聚物的结构与性能。 1 实验部分 1.1 主要原材料 异戊二烯:化学纯,北京化工厂;环己烷:化学 纯,北京化工厂;仲丁基锂:实验纯,美国New J ersey ;环氧丙烷:化学纯,国药集团化学试剂有 限公司;甲醇:分析纯,天津市大茂化学试剂厂;异丙醇:分析纯,北京化工厂;L 丙交酯:聚合级,济南健宝开元生物材料有限公司;二氯甲烷:分析纯,北京化工厂。1.2 试样制备 1.2.1 端羟基聚异戊二烯的合成 将干燥的聚合瓶脱气,注入5.0mL 异戊二烯和1.0mL 仲丁基锂,在水浴锅中于30℃反应1h 。然后向聚合瓶中注入2.0mL 环氧丙烷,30 ℃下反应4h ,最后注入脱气甲醇终止。倒入异丙醇中沉淀,得到白色粘稠状物质。1.2.2 PLLA PI 的合成 准确称取5g 干燥过的L 丙交酯放入安瓿瓶中,按照一定的比例加入备好的引发剂端羟基聚异戊二烯,用微量注射器注入已配制好的催化剂(辛酸亚锡的二氯甲烷溶液),放入真空干燥箱中干燥,然后将安瓿瓶用机械真空泵抽真空10min ,瓶内压强降至670Pa ,然后用酒精喷灯熔 封,放入温控箱中,加热熔融使得催化剂和单体混合均匀,反应到规定时间后取出。待自然降温后,将试管击破,聚合物粗品置于一烧杯中,用三氯甲烷溶解后,边搅拌边注入冷的甲醇溶液(甲醇与三氯甲烷的体积比约为3∶1),瓶内有沉淀形成,抽滤,于真空烘箱中烘干,保存。
聚异戊二烯系橡胶及其用途
聚异戊二烯系橡胶及其用途 案《原料》 豪,{羽 9 聚异戊二烯系橡胶及其用途 l 1前言 竖一 (天津市胶鞋厂) 聚异戊二烯橡胶简称异戊橡胶(IR),它 的研究起源于天然橡胶的研究而工业化生 产则是在其单体和齐格勒型催化剂有了确实 保证之后才得实现的这种催化剂首先由 美国的Goodrich化学公司在1954年割成, 我国先用叔丁基铝/四氯化钛催化剂台成出 该胶,后又采用有机酸稀土盐三元催化体系 进行合成.该法特点:催化剂可配成均相,聚 合比较稳定,不挂胶,溶剂回收使用好,较易 控制成胶质量等总体上,该胶的工业化生产 始于60年代,且在60年代后期和70年代初 得到迅速发展此后由于”能源危机的冲击 和天然橡胶的竞争,西方国家对该胶的生产 出现重大滑坡一直延续至今,俄罗斯和东欧 各国由于缺乏天然橡胶资源,坚持大力开发 和生产异戊橡胶.目前俄罗斯仍为世界上最 大的生产国家 2生产技术概况 2.1异戊二烯单体的生产概况 目前生产异戊二烯(IR)的西方国家主 要自美,法,日荷,意,南非和巴西等国.采用 裂解碳五馏份抽提法,烯醛二步法和炔酮法 等j种生产方法.其中抽提法约占总能力的 80,美国和西欧全部采用此法.【j本抽提法 约占其总能力的76.南非是唯一以煤为原 料(炔酮洼)生产异戊二烯单体的国家.而俄 罗斯主要异戊烷脱氢法制取,其余”烯醚 :一谥 做弓弓 2.2聚异戍二烯橡胶的生产概况 聚异戊二烯橡胶的生产技术主要采用已
定型的溶液连续聚合法.工业采用的催化体系有:由四氯化钛/烷基铝组成的齐格勒/纳塔(钛铝)催化剂,有机锂催化剂和稀士催化体系.由此合成的聚异戊二烯橡胶分别简称钛胶(Ti—IR),锂胶(u—IR)和稀土胶(Ln — IR)目前,髂荷兰shell公司等生产锂胶 外.世界上大多数公司仍生产钛胶为主此外,也有俄罗斯等国生产的稀士胶 3异戊橡胶生产技术进展 对已有生产技术的改进:如采用低温法 配制催化剂,可减少催化剂用量和聚合釜数量,延长聚合釜运转周期.以氢调节聚合物分子量及其分布,从而可降低凝胶含量,在铝钛催化剂中加入第三组份,生产无凝胶或低凝胶(含量小于5—7)品种.采用等温聚合工 艺-可提高溶液中聚合物的浓度,成胶的可塑性和其它性能上的一致性. 新品种和耨工艺的开发:如采用稀士催 化体系合成异戊橡胶,其顺式一1.4结构高达∞.5,乇,无凝胶,分子量分布易于调节,定伸和抗撕强度高于钛胶,耐疲劳和抗裂口增长超过天然胶.另又开发出稀土丁戊橡胶;再之,意,俄和我国业已分别开发出异戊胶的本体聚合技术,可合成高顺式,高分子量和基本上无凝胶的异戊橡胶 对异戊橡胶的改性:异戊橡胶虽有人造 或合成天然胶之称,但某些性能,特别是生胶强度和粘台性能仍不及天然胶对此国外做, , ~ ,. 9 《原村料》 了大量的改性工作,主要在改善异戊胶的加工和物机性能,以及合成新型材料两方面,如在该歧大分子中引人羰基,羟基,环氧基,硝基等官能团以提高生胶强度,降低冷流等性能,或以加氢,氯化,环化,与其它单体共聚等方法制备新颖材料. 4异戊系列橡胶的品种和用途 4.1顺式一1,4一聚异戊二烯橡胶
橡胶配方大全
橡胶配方设计的原则 橡胶配方设计的原则可以概况如下: 1、保证硫化胶具有指定的技术性能,使产品优质; 2、在胶料和产品制造过程中加工工艺性能良好,使产品达到高产; 3、成本低、价格便宜; 4、所用的生胶、聚合物和各种原材料容易得到; 5、劳动生产率高,在加工制造过程中能耗少; 6、符合环境保护及卫生要求; 任何一个橡胶配方都不可能在所有性能指标上达到全优。在许多情况下,配方设计应遵循如下设计原则: ① 在不降低质量的情况下,降低胶料的成本; ②在不提高胶料成本的情况下,提高产品质量。要使橡胶制品的性能、成本和加工工艺可行性三方面取得最佳的综合平衡。用最少物质消耗、最短时间、最小工作量,通过科学的配方设计方法,掌握原材料配合的内在规律,设计出实用配方。橡胶配方的表示形式 天然橡胶(NR)基础配方
注:硫化时间为140℃×10min,20min,40min,80min。NBS为美国国家标准局编写 丁苯橡胶(SBR)基础配方 Phr指每百质量份橡胶的分量数 注:硫化时间为145℃×25min,35min,50min 氯丁橡胶(CR)基础配方 注:硫化时间为150℃×15min,30min,60min 丁基橡胶(IIR)基础配方
注:硫化时间为150℃×20min,40min,80min;150℃×25min,50min,100min 丁腈橡胶(NBR)基础配方 注:硫化时间为150℃×10min,20min,80min 顺丁橡胶(BR)基础配方 注:硫化时间为145℃×25min,35min,50min 异戊橡胶(IR)基础配方 注:硫化时间为15℃×20min,30min,40min,60min。纯胶配方采用天然橡胶基础配方。 三元乙丙橡胶(EPDM)基础配方
橡胶基本工艺流程
一、基本工艺流程 橡胶制品种类繁多,但生产工艺过程却基本相同。以一般固体橡胶——生胶为原料的橡胶制品的基本工艺过程包括:塑炼、混炼、压延、压出、成型、硫化6个基本工序。当然,原材料准备、成品整理、检验包装等基本工序也少不了。橡胶的加工工艺过程主要是解决塑性和弹性性能这个矛盾的过程。通过各种工艺手段,使得弹性的橡胶变成具有塑性的塑炼胶,再加入各种配合剂制成半成品,然后通过硫化使具有塑性的半成品又变成弹性高、物理机械性能好的橡胶制品。 二、原材料准备 1.橡胶制品的主要原料是以生胶为基本材料,而生胶就是生长在热带,亚热带的橡胶树上通过人工割开树皮收集而来。 2.各种配合剂,是为了改善橡胶制品的某些性能而加入的辅助材料。 3.纤维材料有(棉、麻、毛及各种人造纤维、合成纤维和金属材料、钢丝)是作为橡胶制品的骨架材料,以增强机械强度、限制制品变型。在原材料准备过程中配料必须按照配方称量准确。为了使生胶和配合剂能相互均匀混合,需要对材料进行加工。生胶要在60--70℃烘房内烘软后再切胶、破胶成小块,配合剂有块状的。如石蜡、硬脂酸、松香等要粉碎。粉状的若含有机械杂质或粗粒时需要筛选除去液态的如松焦油、古马隆需要加热、熔化、蒸发水分、过滤杂质, 配合剂要进行干燥不然容易结块、混炼时若不能分散均匀硫化时产生气泡会影响产品质量。 三、塑炼 生胶富有弹性,缺乏加工时必需的可塑性性能,因此不便于加工。为了提高其可塑性,所以要对生胶进行塑炼,这样在混炼时配合剂就容易均匀分散在生胶中,同时在压延、成型过程中也有助于提高胶料的渗透性渗入纤维织品内和成型流动性。将生胶的长链分子降解形成可塑性的过程叫做塑炼。生胶塑炼的方法有机械塑炼和热塑炼两种。机械塑炼是在不太高的温度下通过塑炼机的机械挤压和摩擦力的作用使长链橡胶分子降解变短由高弹性状态转变为可塑状态。热塑炼是向生胶中通入灼热的压缩空气在热和氧的作用下使长链分子降解变短从而获得可塑性。 四、混炼 为了适应各种不同的使用条件、获得各种不同的性能,也为了提高橡胶制品的性能和降低成本必须在生胶中加入不同的配合剂。混炼就是将塑炼后的生胶与配合剂混合、放在炼胶机中通过机械拌合作用使配合剂完全、均匀地分散在生胶中的一种过程。混炼是橡胶制品生产过程中的一道重要工序,如果混合不均匀就不能充分发挥橡胶和配合剂的作用影响产品的使用性能。混炼后得到的胶料人们称为混炼胶它是制造各种橡胶制品的半成品材料,俗称胶料通常均作为商品出售购买者可利用胶料直接加工成型、硫化制成所需要的橡胶制品。根据配方的不同?混炼胶有一系列性能各异的不同牌号和品种?提供选择。 五、成型 在橡胶制品的生产过程中利用压延机或压出机预先制成形状各式各样、尺寸各不相同的工艺过程?称之为成型。成型的方法有 1.压延成型 适用于制造简单的片状、板状制品。它是将混炼胶通过压延机压制成一定形状、一定尺寸的胶片的方法叫压延成型。有些橡胶制品?如轮胎、胶布、胶管等所用纺织纤维材料必须涂上一层薄胶在纤维上涂胶也叫贴胶或擦胶??涂胶工序一般也在压延机上完成。纤维材料在压延前需要进行烘干和浸胶烘干的目的是为了减少纤维材料的含水量以免水分蒸发起泡?和提高纤维材料的温度以保证压延工艺的质量。浸胶是挂胶前的必要工序目的是为了提高纤维材料与胶料的结合性能。 2.压出成型 用于较为复杂的橡胶制品?象轮胎胎面、胶管、金属丝表面覆胶需要用压出成型的方法制造。它是把具有一定塑性的混炼胶放入到挤压机的料斗内在螺杆的挤压下通过各种各样的口型也叫样板进行连续造型的一种方法。压出之前胶料必须进行预热使胶料柔软、易于挤出从而得到表面光滑、尺寸准确的橡胶制品。 3.模压成型 也可以用模压方法来制造某些形状复杂如皮碗、密封圈的橡胶制品?借助成型的阴、阳模具将胶料放置在模具中加热成型。
轮胎材料配方介绍
. . 第三节 材料和配方 一、轮胎原材料 1、橡胶 橡胶是轮胎胶料的基体,在配方胶料中橡胶的比率会超过50%,也就是说轮胎胶料中主要的成分是橡胶。子午线轮胎中采用的橡胶分为天然橡胶和合成橡胶两种。 (1)、天然橡胶 天然橡胶是原产于热带地区的一种乔木——橡胶树的产物。 当割开橡胶树干, 便有乳白似的胶 液从树皮里流出, 因此在有些地方 称为“流泪的树”。 含有橡胶的植物有 二千多种,但最有价值的是三叶橡胶树(如上图),原产于巴西亚马逊河一带。因此这些树的学名为巴西橡胶树(Hevea brasiliensis)。 巴西虽然是巴西橡胶树的原产地,但由于南美叶疾病的危害和劳动力缺乏,种植面积却很小。目前巴西橡胶树的种植地区主要集中在东南亚,占世界种植面积的80%以上。 天然橡胶的采集是通过割开橡胶树干,使乳白似的胶液从树皮里流出,收集后使它凝固,再经过一系列工序,就成为半透明的橡胶块。 据记载,世界上最早应用天然橡胶的是古代美洲的印第安人。他们常用当地橡胶树产出的胶汁制作雨衣、瓶罐及玩具之类的东西。1492年,哥伦布率领船队横渡大西洋,想寻找通向中国和印度的海路,不料由于航行的错误而跑到了美洲。就在这次闻名世界的航行中,他把印第安人制作的橡胶用具和玩的橡胶球带回了欧洲,使欧洲人第一次见到了橡胶。 中国在1904年开始种植橡胶树,主要产地在海南省和云南省。 目前轮胎生产使用的天然橡胶主要分为烟片胶和标准橡胶两种,烟片胶常用的为1号烟片胶(RSS1)和3号(RSS3)胶;标准橡胶为标准橡胶10号和20号。 天然橡胶的主要的化学成分为一种以异戊二烯为主要成份的高分子化合物。烟片胶和标准橡胶性质是相同的只是在加工方面的区别,由于标准橡胶产品具有良好的均一性,加工方便,目前子午胎使用的天然橡胶多为标准橡胶。 烟片胶的生产过程为: 鲜胶乳—→加保存剂—→过滤除杂质—→加水稀释—→澄清—→加酸凝固—→凝块压片—→熏烟干燥—→分级—→包装。 标准胶的生产过程为: 鲜胶乳—→加保存剂—→过滤除杂质—→加水稀释—→澄清—→加酸凝固—→凝块压片—→造粒—→干燥—→分级—→包装。 烟片胶的生产已有大约100年的历史,是一种传统的生产工艺,熏烟是通过烧木产生的烟气和热量来熏干胶片制成烟片胶的一种方法。 标准橡胶产生于60年代。由于传统的制胶方法在工艺、设备和分级制度上都束缚了天然橡胶事业的发展,特别是天然橡胶产量大的国家。因此,马来西亚于1965年开始实行标准橡胶计划,目前标准橡胶已成为天然橡胶最主要的品种。 标准橡胶与烟片胶相比的优势在于:
异戊二烯应用市场前景及其生产技术进展
异戊二烯应用市场前景及其生产技术进展 牟克云 (中石化长岭分公司技术开发处) 摘要:异戊二烯是合成橡胶的重要单体。主要用于合成异戊橡胶、SIS。其次,用作合成丁基橡胶的一种共聚单体,以改进丁基橡胶的硫化性能,异戊二烯还用于制造农药、医药、香料及黏结剂等。本文对异戊二烯国内外应用现状及应用前景进行了分析。同时还介绍了目前生产异戊二烯的几种方法,并进行了对比。文章结尾就本公司发展该项目提出自己的看法和建议。 关键词:异戊二烯市场生产技术工业化 1 异戊二烯性质及应用领域 异戊二烯﹙2-methylbutadiene﹚别名异戊间二烯、2-甲基-1,3-丁二烯,分子式为C5H8,分子量为。CAS号:78-79-5。 异戊二烯在常温下是一种无色易挥发、刺激性油状液体。不溶于水、溶于苯,易溶于乙醇、乙醚、丙酮。与空气形成爆炸性混合物,爆炸极限>%。异戊二烯因含有共扼双键,化学性质活泼,易发生均聚和共聚反应,能与许多物质发生反应生成新的化合物。 表1 异戊二烯性质 性质指标 分子量 化学结构式C5H8 外观无色易挥发、刺激性油状液体 相对密度D2020 折光率N20D 沸点()/℃
凝固点/℃ 闪点/℃-48 自燃点/℃220 溶解性不溶于水、溶于苯,易溶于乙醇、乙醚、丙酮 异戊二烯是合成橡胶﹙SR﹚的重要单体。主要用于合成异戊橡胶﹙IR﹚、SIS﹙苯乙烯—异戊二烯—苯乙烯嵌段共聚物的简称﹚。其次,用作合成丁基橡胶﹙IIR﹚的一种共聚单体,以改进IIR的硫化性能,异戊二烯还用于制造农药、医药、香料及黏结剂等。 2 国内外异戊二烯应用领域及市场情况 异戊二烯可从裂解C5馏分中分离获得,也可通过异戊烯、异戊烷脱氢或异丁烯和甲醛反应制取。在美国和日本,异戊二烯主要是从裂解C5馏分中分离获得的;而在俄罗斯则是通过异戊烯、异戊烷脱氢及异丁烯—甲醛合成法获得的。目前,用于生产SIS、IR、IIR的异戊二烯占异戊二烯总量的95%以上,其余部分用于生产维生素、药物、香料、环氧硬化剂等精细化工产品。目前,美国、西欧用于生产SIS的异戊二烯的量已超过异戊橡胶的量。目前我国异戊二烯还大部分应用在精细化工领域。 国外异戊二烯利用状况 2. 1. 1 美国异戊二烯的利用情况 表2为美国异戊二烯的消费情况。 表2 美国异戊二烯的消费情况(单位:万吨/年) 用途2000年2001年2002年2003年2004年预计2009年 异戊橡胶 SIS 丁基橡胶 其它 总计 从表2可看出,美国异戊二烯主要用于SIS和IR的消费,少量用于生产IIR产品。
液体聚异戊二烯橡胶企业标准-内容
液体聚异戊二烯橡胶 1、范围 本标准规定了液体聚异戊二烯橡胶的技术要求、实验方法、检验规则、标志、包装、运输、贮存。 本标准适用于我公司生产的聚异戊二烯液体橡胶,用于汽车密封胶、橡胶增塑剂、橡胶型压敏胶的混合过程,提高初粘力。 2、规范性引用文件 下列文件中的条款通过本标准的引用而成为本标准的条款。凡是注日期的引用文件,其随后所有的修改单(不包括勘误的内容)或修订版均不适用于本标准,然而,鼓励根据本标准达成协议的各方面研究使用这些文件的最新版本。凡是不注日期的引用文件其最新版本适用于本标准。 GB/T 2794 胶黏剂粘度的测定 HG/T 3075 胶黏剂产品包装、标志、运输和贮存的规定 SH/T 1149 合成胶乳取样法 JJF 1070 定量包装商品净含量计量检验规则 国家质量监督检验检疫总局令第75号《定量包装商品计量监督管理办法》 3、技术 3.1 技术要求 液体聚异戊二烯橡胶的技术要求应符合表1规定 3.2 净含量及偏差 国家质量监督检验检疫总局令第75号《定量包装商品计量监督管理办法》规定执行。 4、试验方法 4.1 外观 将试样放在100ml比色管中,(其液面高度为比色管高度的一半)用目测方法检验。4.2 粘度 粘度按GB/T 2794 规定的方法检测。 4.3净含量 按JJF 1070规定执行。 5、检验规则 5.1 检验分类 液体聚异戊二烯橡胶检验只有一种出厂检验 5.2 组批与抽样 组批与抽样按SH/T 1149 规定执行。 5.3 检验项目 检验项目为技术要求的全部项目。
Q/PSJH 004-2011 5.4 合格判定 经检验产品符合标准规定为合格,否则为不合格。合格产品附合格证方可出厂。检验中出现不合格项允许对该项目加倍抽样复检,复检合格判该批产品合格。 6、标志、包装、运输、贮存 6.1 标志 液体聚异戊二烯橡胶产品标志应符合HG/T 3075中第2章规定,并增加产品标准代号。 6.2 包装 液体聚异戊二烯橡胶包装应符合HG/T 3075中第1章规定。 6.3 运输、贮存 液体聚异戊二烯橡胶运输、贮存应符合HG/T 3075中第3章规定。按此规定贮存,本产品的贮存期限为24个月。 ?????????????????
橡胶生产技术工艺
橡胶生产技术工艺 1 综述 橡胶制品的主要原料是生胶、各种配合剂、以及作为骨架材料的纤维和金属材料,橡胶制品的基本生产工艺过程包括塑炼、混炼、压延、压出、成型、硫化 6 个基本工序。橡胶的加工工艺过程主要是解决塑性和弹性矛盾的过程,通过 各种加工手段,使得弹性的橡胶变成具有塑性的塑炼胶,在加入各种配合剂制 成半成品,然后通过硫化是具有塑性的半成品又变成弹性高、物理机械性能好 的橡胶制品。 2 橡胶加工工艺 2.1 塑炼工艺 生胶塑炼是通过机械应力、热、氧或加入某些化学试剂等方法,使生胶由强韧的弹性状态转变为柔软、便于加工的塑性状态的过程。生胶塑炼的目的是降低它的弹性,增加可塑性,并获得适当的流动性,以满足混炼、亚衍、压出、成型、硫化以及胶浆制造、海绵胶制造等各种加工工艺过程的要求。掌握好适当的塑炼可塑度,对橡胶制品的加工和成品质量是至关重要的。在满足加工工艺要求的前提下应尽可能降低可塑度。随着恒粘度橡胶、低粘度橡胶的出现,有的橡胶已经不需要塑炼而直接进行混炼。在橡胶工业中,最常用的塑炼方法有机械塑炼法和化学塑炼法。机械塑炼法所用的主要设备是开放式炼胶机、密闭式炼胶机和螺杆塑炼机。化学塑炼法是在机械塑炼过程中加入化学药品来提高塑炼效果的方法。开炼机塑炼时温度一般在80℃以下,属于低温机械混炼方法。密炼机和螺杆混炼机的排胶温度在120℃以上,甚至高达160-180℃,属于高温机械混炼。生胶在混炼之前需要预先经过烘胶、切胶、选胶和破胶等处理才能塑炼。几种胶的塑炼特性:天然橡胶用开炼机塑炼时,辊筒温度为30-40℃,时间约为15-20min;采用密炼机塑炼当温度达到120℃以上时,时间约为3- 5min。丁苯橡胶的门尼粘度多在35-60 之间,因此,丁苯橡胶也可不用塑炼,但是经过塑炼后可以提高配合机的分散性顺丁橡胶具有冷流性,缺乏塑炼效果。顺丁胶的门尼粘度较低,可不用塑炼。氯丁橡胶得塑性大,塑炼前可薄通3-5次,薄通温度在30-40℃。乙丙橡胶的分子主链是饱和结构,塑炼难以引起分子的裂解,因此要选择门尼粘度低的品种而不用塑炼。丁腈橡胶可塑度小,韧性大,塑炼时生热大。开炼时要采用低温40℃以下、小辊距、低容量以及分段塑炼,这样可以收到较好的效果。 2.2 混炼工艺
Al_OH_3准纳米材料在硅橡胶配方中的应用_李俭
第17卷 第4期郑州轻工业学院学报(自然科学版) V ol.17 N o.4 2002年12月 JOURNA L OF ZHENG ZHOU INSTIT UTE OF LIGHT INDUSTRY (Natural Science ) Dec.2002 收稿日期:2002-05-29 作者简介:李俭(1963— ),女,河南省新密市人,郑州祥和集团绝缘设备制造有限公司工程师,主要从事橡胶加工工艺研究. 文章编号:1004-1478(2002)04-0028-03 Al (OH )3准纳米材料在硅橡胶配方中的应用 李 俭, 郭慧豪 (郑州祥和集团绝缘设备制造有限公司,河南郑州450048) 摘要:研究了A1(OH )3的粒径,A1(OH )3与滑石粉、偶联剂的用量对胶料综合性能的影响.结果表 明,准纳米A1(OH )3补强效果明显,加入量越大(14010份~22010份)补强效果越好;同时加入A1(OH )3用量510%的K H550作为偶联剂、1010份滑石粉作为填充剂可有效提高胶料的强度性能 和混炼工艺性能,其硫化曲线与常用硅橡胶配方的硫化曲线基本一致,且成本大幅度降低.关键词:硅橡胶;氢氧化铝;纳米材料中图分类号:T Q33 文献标识码:A 0 引言 近年来,硅橡胶以其独特优异的性能而被广泛应用,获得了飞速发展.但硅橡胶自身的强度极低,一般采用白炭黑作为补强填料,白炭黑的价格很高,成本因素在很大程度上限制了其在硅橡胶配方中的应用.由于对应用于高电压领域的硅橡胶材料的阻燃性、耐电弧烧蚀性能有非常高的要求,因此需在常规硅橡胶配方中加入大量的氢氧化铝作为阻燃剂. 硅橡胶主链是由硅和氧组成的长链结构,硅橡胶和白炭黑的补强作用机理在于硅橡胶分子链和白炭黑聚集体表面上的羟基之间能形成物理化学作用,从而使彼此孤立的分子链之间形成物理结晶点,使硅橡胶强度得到很大提高[1].白炭黑的补强作用在于其表面羟基,而且补强效果与羟基个数即聚集体比表面积有直接的联系,也就是说,白炭黑的粒径越小、比表面积越大,其补强效果越好.在元素周期表中,硅和铝位于相邻位置,元素铝和硅在化学性质上表现出很大的相似性,如铝有一定的非金属性,铝的氧化物和氢氧化物都是两性物质,同时氢氧化铝表面也有一定的羟基,因此氢氧化铝对硅橡胶也应有一定的补强作用,但普通氢氧化铝填料由于粒子大其补强效果很微弱[2].近年来纳米材料技术飞速发展,从而也带动了氢氧化铝制造技术的发展,使氢氧化铝的粒子可以造得很细(粒径在准纳米范围内),与白炭黑的粒径相近.因此准纳米氢氧化铝微粉也具有很好的补强效果. 本文通过详尽的实验,研究了氢氧化铝微粉的粒子大小、加入量、偶联剂、特殊填料等在硅橡胶配方中的作用,找出了适宜的配比,使胶料的成本大大降低,具有明显的应用价值. 1 实验 111 原料及仪器设备 原料:110—2甲基乙烯基硅橡胶,四川成都晨光二厂产;K H550,晨光研究院产;氢氧化铝微粉,山西铝厂产;氢氧化铝填料,新乡意达铝厂产;DCP ,上海虹桥化工厂产;MgO (分析纯),海中化工厂产;滑石粉,市售;甲基硅油,四川成都晨光二厂产.
阳离子聚合制备丁基橡胶
常熟理工学院 ------材料科学与工程专业聚合物合成工艺课程设计 题目:阳离子聚合制备丁基橡胶 姓名:龙叶梅 学号:150208147 专业:材料科学与工程专业 班级:08级材料( 1 )班 指导教师左晓兵 起止日期2010.12—2011.01
目录 一.工艺背景 (4) 1.丁基橡胶发展简介 (4) 2.丁基橡胶的性质及用途 (4) 3.合成工艺研究的意义 (5) 二.设计思路及拟要解决的问题 (5) 1.丁基橡胶合成设计思路 (5) 2. 制备丁基橡胶需要解决的问题 (5) 三.合成工艺基本原理介绍 (6) 1.阳离子聚合反应的特点 (6) 2. 聚合反应机理 (6) 四.聚合体系各组分及其作用 (8) 1. 单体 (8) 2.溶剂 (9) 3.引发剂 (10) 五.工艺过程 (10) 1.配方 (10) 2.聚合工艺过程 (10) 六.聚合物合成工艺流程图 (13) 七.聚合物合成工艺的关键工艺条件分析 (14) 1.异戊二烯的影响 (14) 2.杂质 (14)
3.单体浓度和配料比 (14) 4.聚合温度 (15) 5.催化剂 (15) 6.溶剂 (15) 八.发展状况 (16) 1. 国际发展状况 (16) 2. 国内发展状况 (16) 九.参考文献 (17)
阳离子聚合制备丁基橡胶的合成工艺 一、工艺背景 1、丁基橡胶发展简介 异丁烯在三氟化硼和助引发剂水的作用下,室温时只能得到低分子量聚合物,当反应温度降至-75℃以下,则可得到高分子量的聚异丁烯,这是一个阳离子型连锁聚合反应。 由于生成的聚异丁烯是饱和的,没有双键供硫化交联之用,所以这种聚异丁烯与其他任何一种未经硫化过的橡胶一样,具有一系列严重的缺点,如热塑性、冷流性和热机械强度差,没有使用价值,1937年成功合成了异丁烯—异戊二烯的共聚物。这种弹性体称为丁基橡胶,由于共聚物中含有双键,可以硫化,故获得广泛应用。 丁基橡胶的生产始于20 世纪40 年代,1943 年Exxon公司实现了丁基橡胶的工业化生产。1944 年,加拿大Polysar 公司采用美国技术在Sarnia 建成丁基橡胶生产装置。1959 年后,法国、英国、日本也开始生产丁基橡胶。1 9 9 1 年,Bayer 公司购买Polysar 全部合成橡胶业务,Exxon 公司也收购了在法国的丁基橡胶生产装置,从此世界丁基橡胶的生产基本上被Exxon 和Bayer 两大公司所垄断。1982 年,前苏联在陶里亚蒂建成世界唯一的溶液聚合法丁基橡胶生产装置,所用聚合反应器由苏联合成橡胶研究院和意大利PI 公司合作开发。 目前,我国只有北京燕山石油化工公司合成橡胶厂一家生产企业,产量不能满足国内实际生产的需求,每年都要大量进口,开发利用前景广阔。 2、丁基橡胶的性质及用途 | 丁基橡胶具有优良的气密性和良好的耐热、耐老化、耐酸碱、耐臭氧、耐溶剂、电绝缘、减震及低吸水等性能。最突出的是气密性和水密性。它对空气的透过率仅为天然橡胶的1/7,丁苯橡胶的1/5,而对蒸汽的透过率则为天然橡胶的1/200,丁苯橡胶的1/140。因而当前其主要应用领域是汽车轮胎和药用瓶塞; 广泛应用于内胎、水胎、硫化胶囊、气密层、胎侧、电线电缆、防水建材、减震材料、药用瓶塞、食品( 口香糖基料) 、橡胶水