薄壁零件夹持变形与装夹方法的改进分析
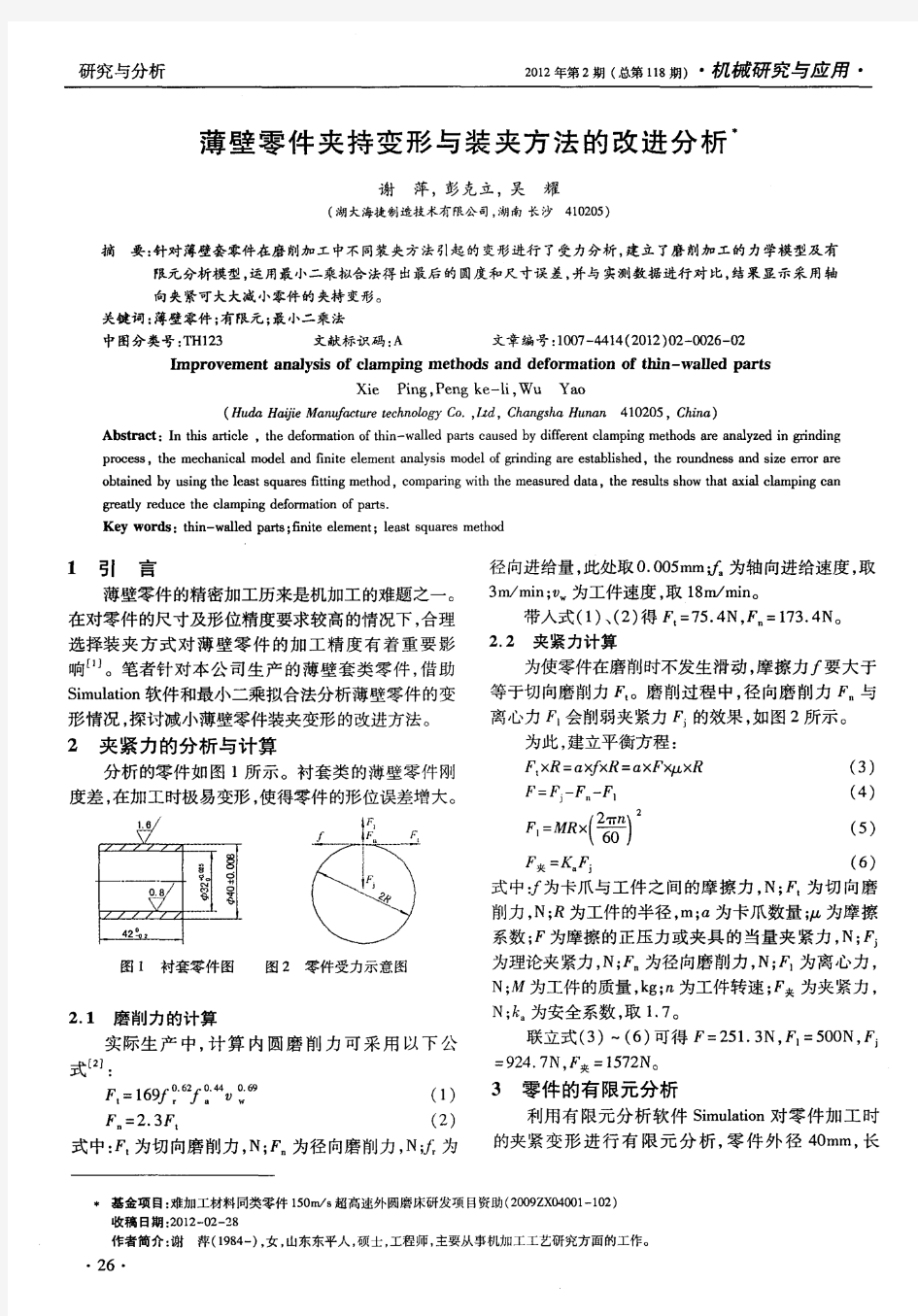

薄壁零件装夹变形原因及控制
薄壁零件装夹变形原因及控制 精密薄壁零件是目前制造业发展的一个重要方向,薄壁零件的装夹是其生产制 造中的一个重要环节,但由于工艺不合理,对薄壁零件认识不够等因素造成的装夹变形时有发生。该文分析了薄壁零件装夹变形的产生原因,并提出了一些控制对策。 薄壁零件,装夹变形,原因,对策 薄壁零件的加工变形,一直是机械加工制造业的一个难题,很多国内外学者都对薄壁零件的加工变形问题进行了分析了研究,使得薄壁零件的加工技术有了一定的突破。实际工作中,要想通过合理的对策解决薄壁零件的加工变形问题,就要首先认清产生变形的原因。 1.薄壁零件装夹变形的成因及区分 薄壁零件出现变形有很多的原因,在设计零件的过程中,不仅要考虑零件设计结构的工艺性,还要提高零件结构的刚性,防止在加工中出现变形,尽可能保证零件结构对称、薄壁厚度均匀,选择毛坯时,最好选择没有内应力的原材料。在制造系统中,零件加工变形的主要因素有, 工件的装夹条件。由于薄壁零件的刚性比较差,加工时不恰当的选择央紧力与 支承力的作用点,导致附加应力,夹、 1 压的弹性变形会一定程度上影响零件表面的尺寸精度和形状、位置精度,导致 变形。 加工残余应力。在零件加工过程中,由于刀具对已加工面的挤压、刀具前刀面 与切屑、后刀面与已加工表面之间的摩擦等综合作用,导致零件表层内部出现新的加工残余应力。由于不稳定的残余应力的存在,一旦零件受到外力作用,零件就会在外力与残余应力的作用下产生局部塑性变形,重新分配截面内的应力,去除外力作用
后,零件就会受到内部残余应力的作用出现变形。这种由于切削过程中残余应力的重新分布,造成的零件的变形,会严重影响加工质量。 切削力和切削热、切削振动。为了避免被加工材料产生弹性变形、塑性变形以及刀具与切屑和工件之间的摩擦,切削过程会产生切削力和切削热,在两者作用下,很容易导致零件振动和变形,进而影响零件的质量。另外,造成零件变形的影响因素还有机床、工装的刚度,切削刀具及其角度、切削参数和零件冷却散热情况等。其中造成零件变形的主要因素是切削力、夹紧力以及残余应力。 2.控制零件变形的工艺措施 由于零件的整体刚性在加工薄壁零件过程中随着零件壁厚逐渐减小,零件的刚性也会降低,进而导致加工零件的变形增大。因而,在对零件进行切削过程中,最大程度地利用零件的未加工部分,支撑正在切削部分,保证切削时处在最 2 佳刚性状态。如,腔内有腹板的腔体类零件,在加工过程中,铣刀以螺旋线方式从毛坯中间位置下刀进而降低垂直分力对腹板的压力,从深度方向铣到尺寸,再从中间扩张到四周至侧壁。如果内腔深度很大,根据上面的方法进行多层加工。这种方式能够尽可能的降低切削变形,减少了由于零件刚性的降低而出现的切削振动现象。 采用辅助支撑。在加工薄壁结构的腔类零件过程中,控制零件的变形就要首先解决由于装夹力造成的变形。因而,可利用腔内加膜胎(橡胶膜胎或硬膜胎)的方式来增加零件的刚性,避免零件在加工过程中出现变形,另外,还可以采用填充法石蜡、低熔点合金等工艺方法,来增加零件的支撑,从而减小变形、提高零件的精度。 设计工艺加强筋,提高刚性。对于薄壁零件来说,为了减少变形,可以增加零件的工艺筋条,从而达到加强刚性的目的,这是工艺设计中避免变形的提高刚性常用的手段之一。如在加工长槽过程中,在圆支管右端上下二槽口留3mm加强筋,进行消除
薄壁零件的加工实用工艺和夹具设计
摘要: 本文系统设计了薄壁零件的数控车削加工工艺。通过探讨薄壁零件在加工中存在的易变形、零件尺寸精度、位置精度及表面粗糙度不易保证等技术问题,对加工难点进行分析,给出了加工工艺路线和加工方案,通过优化、完善夹具设计和切削参数,防止了薄壁零件加工变形、保证了较好的尺寸精度和位置精度,从而有效解决薄壁零件的车削加工难题。 由于薄壁零件刚性差、强度弱,在加工中极易变形,是零件的形位公差增大,不易保证零件的加工质量。因此对薄壁零件的装夹,切削加工过程中刀具的合理选用及切削量的选择,提出了严格要求。 在普通车床上加工形状较复杂、有一定精度要求、且需要多把刀具进行加工的批量零件时,不仅需要频繁换刀和装夹,花费大量的人力和时间,而且加工出来的零件质量取决于加工人员的技术水平, 产品质量得不到充分的保证。而运用数控车床,结合传统的加工工艺,不但能大大缩短加工时间、提高加工精度,而且成品率高、产品质量稳定。 所以,在运用数控机床加工过程中为保证被加工薄壁件的必要的精度,有同轴度要求的外圆柱面或有垂直度要求的外圆与端面,尽可能在一次装夹中完成;需要编制其加工路线、合理的选择个阶段的加工参数并编写高质量的数控加工程
序。为完全保证零件的形位公差需要设计其装夹的夹具,为此,对零件图纸、零件加工及时效处理等方面都认真地进行了分析和研究。 图1-1 由图1-1可看出,?64mm的外圆对?60mm的孔的同轴度,?64的外圆的圆度和表面质量以及孔尺寸精度的加工是该薄壁零件最主要的加工难点。因为该零件刚性差、强度弱,在加工中极易变形,表面质量、垂直度及同轴度难以保证。镗削孔时应一次装夹中加工出来,以保证该零件的尺寸精度。针对薄壁零件壁薄、刚性差、易变形的特点,可设计该薄壁零件专用夹具装夹,以保证零件的
‘壳盖’薄壁铝合金件加工工艺
‘壳盖’薄壁铝合金件加工工艺 “壳盖”薄壁铝合金件加工工艺分析中国航空工业集团公司航宇救生装备有限公司(湖北襄阳441002) 袁开波 “壳盖”零件是一个薄壁的铝合金零件,其形状及尺寸如图1所示.零件的主要特点就是壁薄,由于是铝合金件,其强度差,加工时容易变形,要高效率加工合格的零件,加工过程中编制好工艺路线,做好准确的装夹与定位,就至关重要,同时要控制由于切削对零件产生的变形。 图1“壳盖” 注:未注圆角,凸R1.8mm,凹R1mm,未注壁厚0.8mm. 一、工艺分析 考虑到此零件的内、外形均为圆环形状,其主要的加工方法为数车工序完成,数车工序为分别加工内、外形2个步骤。这里就要考虑加工完第一工序后,在进行第二工序加工时的装夹与定位问题。既要能准确装夹与定位,又要使第二工序的加工操作方便。在经过多次的工艺路线分析及相配合的夹具结构设计之后,确定了先加工内形面,并在其端面上制出装夹定位的位置,然后进行外形面的加工。 二、工艺路线
在加工零件的内形面之后,“壳盖”需要安装在一种辅助夹具上,才能进行第二工序的加工,如图2所示。 (a) 第一工序图 (b) 第二工序简图 图2 “壳盖”工艺路线简图 1.第一工序的加工 “壳盖”在第一工序中要完成如图2(a)所示的加工内容,注意保持各个孔与 M64×0.75螺孔的同轴度。由于“壳盖”壁薄,偏心更易使“壳盖”产生变形。 2. 第二工序的加工 如图2(b)所示,型腔口部的M64×0.75螺纹段位为装夹部分,用M64X0.75螺纹与辅助夹具进行定位与连接。其夹具的设计,如图2(b)所示。从图中可以看出,辅助夹具的设计,其型面尺寸与零件的内形面是一致的,零件扣在夹具上,并通过M64X0.75螺纹拧紧,以保证零件内形面与夹具相贴合,这样,在加工外形面时,零件不会产生变形。 3.安装在辅助夹具上“壳盖”切削时加紧状况的分析 零件在装夹后,车刀切削时,零件的状态是否会松动,可通过图3做一个装夹及切削的状况分析。
薄壁零件加工方法和工艺分析
薄壁零件加工方法和工 艺分析 集团标准化工作小组 [Q8QX9QT-X8QQB8Q8-NQ8QJ8-M8QMN]
薄壁零件的工艺分析及加工方法 单位名称:陕西长岭电子科技有限责任公司 作者:安小康 2017年 3月 2 日 薄壁零件的工艺分析及加工方法 作者:安小康 职业技能鉴定等级:二级 单位名称:陕西长岭电子科技有限责任公司 单位地址:宝鸡市渭滨区清姜璐75号 2017年 3月 2 日 目录 摘要 (1) 关键词 (1) 1工艺方案分析 (2) 薄壁零件图 (2) 零件图分析 (2) 确定加工方法 (2) 2工件装夹 (3) 定位基准选择 (3) 确定零件定位基准 (3) 装夹方式选择 (3) 确定装夹方式 (3)
3刀具和切削用量选择 (3) 4零件加工 (5) 5加工注意事项 (7) 安全文明生产 (7) 刀具的选择 (7) 削用量的要求 (7) 6影响薄壁加工因素及解决方法 (8) 受力变形 (8) 受热变形 (9) 振动变形 (9) 总结 (10) 参考文献 (11) 摘要 薄壁工件因为具有重量轻、节约材料、结构紧凑等特点,薄壁零件 已日益广泛地应用在各工业部门。但薄壁零件的加工是比较棘手的,原 因是薄壁零件刚性差、强度弱,在加工中极容易变形,不易保证零件的 加工质量。 薄壁零件的加工问题,一直是较难解决的。薄壁件目前一般采 用数控车削的方式进行加工,为此要对工件的装夹、刀具几何参数、程 序的编制等工艺分析方面进行试验,合理的选择加工方法从而有效地克 服了薄壁零件加工过程中出现的变形,保证加工精度。
关键词:薄壁工件工艺分析程序编制加工方法 1工艺方案分析 薄壁零件图 零件图分析 该零件图是薄壁套类零件由外圆、内孔、外螺纹组成。尺寸标注完整,表面粗糙度为,选用毛坯是45号钢。毛坯尺寸Φ35mm×50mm,表面无热处理等要求。 确定加工方法 确定加工方法的原则是保证加工表面加工精度和表面粗糙度。薄壁类零件应按粗、精加工工序。薄壁件通常需要加工工件的内、外表面。内表面的粗加工和精加工都会导致工件变形,所以应按粗精加工分序。内外表面粗加工后,再内外表面精加工,均匀的去除工件表面多余部分,这样有利于消除切削变形。加工方法多种多样,应结合零件的形状,尺寸,位置,选择合理快捷的加工方法。尺寸公差要求较高,公差值较小。取其基本尺寸加工编程便可。 2工件装夹 定位基准选择 定位基准选择极为重要,他影响到工件加工的尺寸,位置精度从而影响到工件整体的加工质量。 确定零件定位基准 根据基准重合原则以工件左端面或者右端面作为定位基准 装夹方式选择
零件装夹变形分析与解决措施
零件装夹变形分析与解决措施 零件变形主要表现在装夹变形;切削力、切削热使零件产生变形;加工方法和技巧不当使零件产生变形;材料应力释放零件原因导致的变形等。如果在生产过程中工件产生变形,那么肯定就会影响工件的形位精度,尺寸精度以及表面粗糙度,所以提高易变形零件加工质量和加工效率的关键就是装夹方法以及车削,铣削时的加工方法和技巧。 标签:装夹方法;刀具选择;切削用量 1 为什么会产生零件装夹变形 我们在加工生产中会遇到各种各样的问题,譬如在加工薄壁易变型零件时,就必须根据其不同的特点,找出薄弱环节,选用不同的工艺方法和夹紧方法来保证加工要求。很多时候我们要具体问题具体分析,找到切实可行的办法来应对遇到的实际问题。 1.1 工件装夹不当为什么会产生变形? 在我们生产实际操作中,如果我们采用三爪卡盘夹紧薄壁外圆,就会由于夹紧面积过小,夹紧力不均匀分布,那么拆卸以后,被卡爪夹紧部分就可能因弹性变形而涨大,最终导致零件出现多角形变化。 1.2 相对位置调整时候偏差,产生壁厚不均的现象 经过多年的工作实践,我发现由于夹具、刀具,工件和机床主轴旋转中心的位置调整相对不准确,导致工件几何形状变化和壁厚不均匀现象。我们遇见很多薄壁零件对于均匀性要求非常高,但对其尺寸精度要求却不高这种现象。此时工件如果采用常规刚性定位,就会误差非常大,壁的厚度很容易超差。这样工件在装夹过程中,假设我们没有根据实际特性,也就是工件刚度较低(薄壁件),或者不注意夹紧力的方向和施力点,那么支撑点和压紧点不能够重合就形成力矩效应,最终会引起零件变形。 1.3 为什么要强调零件壁厚差重要性 有一部分薄壁零件对均匀性要求非常高,而对其尺寸精度要求却不高。这种工件和彩刚性定位,就会误差很大,壁厚非常容易超差。在装夹过程中的工件,假设刚度较低(薄壁件)或者夹紧力方向,施力点选择不恰当,支撑点与压紧点不重合必然形成力矩效应将会引起零件变形。 1.4 选用什么样的刀具至关重要 我们选择什么样的刀具,会直接影响零件精度以及表面粗糙度。比如我们在
薄壁零件加工方法和工艺分析
薄壁零件的工艺分析及加工方法 单位名称:陕西长岭电子科技有限责任公司 作者:安小康 2017年3月 2 日 薄壁零件的工艺分析及加工方法 作者:安小康 职业技能鉴定等级:二级 单位名称:陕西长岭电子科技有限责任公司 单位地址:宝鸡市渭滨区清姜璐75号 2017年3月2 日 目录 摘要 (1) 关键词 (1) 1工艺方案分析 (2) 薄壁零件图 (2) 零件图分析 (2) 确定加工方法 (2) 2工件装夹 (3) 定位基准选择 (3) 确定零件定位基准 (3) 装夹方式选择 (3) 确定装夹方式 (3)
3刀具和切削用量选择 (3) 4零件加工 (5) 5加工注意事项 (7) 安全文明生产 (7) 刀具的选择 (7) 削用量的要求 (7) 6影响薄壁加工因素及解决方法 (8) 受力变形 (8) 受热变形 (9) 振动变形 (9) 总结 (10) 参考文献 (11) 摘要 薄壁工件因为具有重量轻、节约材料、结构紧凑等特点,薄壁零件已日益广泛地应用在各工业部门。但薄壁零件的加工是比较棘手的,原因是薄壁零件刚性差、强度弱,在加工中极容易变形,不易保证零件的加工质量。 薄壁零件的加工问题,一直是较难解决的。薄壁件目前一般采用数控车削的方式进行加工,为此要对工件的装夹、刀具几何参数、程序的编制等工艺分析方面进行试验,合理的选择加工方法从而有效地克服了薄壁零件加工过程中出现的变形,保证加工精度。
关键词:薄壁工件工艺分析程序编制加工方法 1工艺方案分析 薄壁零件图 零件图分析 该零件图是薄壁套类零件由外圆、内孔、外螺纹组成。尺寸标注完整,表面粗糙度为,选用毛坯是45号钢。毛坯尺寸Φ35mm×50mm,表面无热处理等要求。 确定加工方法 确定加工方法的原则是保证加工表面加工精度和表面粗糙度。薄壁类零件应按粗、精加工工序。薄壁件通常需要加工工件的内、外表面。内表面的粗加工和精加工都会导致工件变形,所以应按粗精加工分序。内外表面粗加工后,再内外表面精加工,均匀的去除工件表面多余部分,这样有利于消除切削变形。加工方法多种多样,应结合零件的形状,尺寸,位置,选择合理快捷的加工方法。尺寸公差要求较高,公差值较小。取其基本尺寸加工编程便可。 2工件装夹 定位基准选择 定位基准选择极为重要,他影响到工件加工的尺寸,位置精度从而影响到工件整体的加工质量。 确定零件定位基准 根据基准重合原则以工件左端面或者右端面作为定位基准 装夹方式选择
工序和装夹方法的确定
工序和装夹方法的确定 1.工序的划分 加工工序的划分按要求进行。对于数控车削加工来说以下两种原则使用较多: (1)按所用刀具划分工序采用这种方式可提高车削加工的生产效率。 (2)按粗、精加工划分工序采用这种方式可保持数控车削加工的精度。如图1所示的零件,应先切除整个零件的大部分余量,再将表面精车一遍,以保证加工精度和表面粗糙度的要求。 图1 车削加工的零件 2.确定零件装夹方法和夹具选择 数控车床上零件安装方法与普通车床一样,要尽量选用已有的通用夹具装夹,且应注意减少装夹次数,尽量做到在一次装夹中能把零件上所有要加工表面都加工出来。零件定位基准应尽量与设计基准重合,以减少定位误差对尺寸精度的影响。 数控车床多采用三爪自定心卡盘夹持工件;轴类工件还可采用尾座顶尖支持工件。由于数控车床主轴转速极高,为便于工件夹紧,多采用液压高速动力卡盘,因它在生产厂已通过了严格平衡,具有高转速(极限转速可达4000~6000r/min)、高夹紧力(最大推拉力为2000~8000N)、高精度、调爪方便、通孔、使用寿命长等优点。还可使用软爪夹持工件,软爪弧面由操作者随机配制,可获得理想的夹持精度。通过调整油缸压力,可改变卡盘夹紧力,以满足夹持各种薄壁和易变形工件的特殊需要。为减少细长轴加工时受力变形,提高加工精度,以及在加工带孔轴类工件内孔时,可采用液压自动定心中心架,其定心精度可达0.03㎜。此外,数控车床加工中还有其他相应的夹具,它们主要分为两大类,即用于轴类工件的夹具和用于盘类工件的夹具。 (1)用于轴类零件的夹具 用于轴类工件的夹具有自动夹紧拨动卡盘、拨齿顶尖、三爪拨动卡盘和快速可调万能卡盘等。
浅析薄壁零件加工中变形振动分析和消振措施
薄壁零件加工中 变形振动分析和消振措施 摘要:车削过程中,工艺系统由于受到各种力的作用,工件和刀具之间常会发生相对振动。它不仅使加工表面产生波纹,严重恶化加工精度和表面质量。特别是最后一刀精车,当切削速度提高,常常会发生刺耳的响声,使车削无法继续加工下去。所以,在加工薄壁零件中,不仅要考虑装夹中工件受力变形的问题,还要注意解决加工中振动问题 关键词:薄壁零件加工变形振动措施 车削薄壁零件在加工中很容易出现问题,如果我们在加工中善于总结经验,就能在加工中找出它的共性、个性和矛盾突出点。变被动为主动。从而才能够加工出合格的产品。要想解决薄壁零件加工中出现的问题,我想从以下几个方面来加以分析。 一、薄壁零件装夹分析 1、薄壁零件的加工特点 薄壁零件以日益广泛地应用个工业部门生产机器零件中,车削薄壁零件的关键是变形、振动问题。工件产生变形振动的原因大多是由于切削力、夹紧力、定位误差和弹性变形。其中影响最大的是切削力和夹紧力。 我们在实践过程中减小切削力和切削热主要采取方法是:合理地选择切削用量、合理地选择刀具几何角度、减小夹紧力引起的变形,主要改变和改善夹紧力对零件的作用。 2、车削薄壁零件时采用的装夹方式 以上讲的薄壁零件加工特点是车削中变形和振动问题。由于薄壁零件的刚性差,车削中容易变形。所以在装夹时要考虑到夹紧力的方向和着力点。夹紧力的方向应选择在有利于减小夹紧力的部位。如薄壁零件为套类,则可将径向夹紧力改为轴向夹紧力;薄壁零件为盘类,
则可该轴向夹紧力为径向夹紧力;当薄壁零件径向和轴向刚性都很差时,保证夹紧力方向与切削力方向一致,就能使较小夹紧力起到较大夹紧力的作用。还要夹紧力着力点应落在支承点正对面和切削力部位的附近以减小变形振动。 二、减小薄壁套装夹中变形的措施 1、合理确定夹紧力的大小、方向、作用点。 粗、精车加工分开,当粗精车加工使用同一夹具时,粗加工余量大,切削力大。因而需要较大的夹紧力。而精车时余量小,切削力小,所需要的夹紧力也就小。 1)改变夹紧力的作用方向。 也就是变径向夹紧力为轴向夹紧力。因为薄壁套轴向承载能力比径向大,在可能的情况下,尽可能是夹紧力与切削力的方向一致。这样可以减小夹紧力。 2)增大夹紧力的作用面积。 当我们加工薄壁套零件完毕时,卸下来时会发现零件发生变形。这是由于三爪夹紧力作用于工件受力面积太小而导致的结果。我们可以把工件小面积上局部受力变为大面积的均匀受力。就可以大大地减小工件夹紧力变形。在实际生产过程中,小批量生产我们都采用结构简单容易制作的扇形卡爪,开缝套来增大夹紧力作用面积以减小变形。 另外引起薄壁套零件在加工中除了夹紧力大小影响工件变形以为,我们还要关注在车削过程中,切削力和切削热对零件加工的影响。影响切削力大小和切削程度高低主要因素是切削用量选择和刀具几何角度选择。 3)切削用量中对切削力影响最大的是背吃刀量。 对切削热影响最大的是切削速度和刀具锋利状况。因此车削薄壁套零件应减小背吃刀量和适当降低切削速度,同时应适当增大进给量。 4)车刀几何角度中对切削力影响最大的是主偏角、前角和刃倾角。增大前角使车刀锋利,排屑顺利,减小切屑与前刀面之间的摩擦,减小切削力和切削热。
薄壁零件加工方法和工艺分析解析
薄壁零件的工艺分析及加工方法 单位名称:南京交通技师学院 作者:陈晓 2014年10月25 日
薄壁零件的工艺分析及加工方法 作者:陈晓 职业技能鉴定等级:二级 单位名称:南京交通技师学院 单位地址:中山门外马群狮子坝168号 指导老师:赵亲云 2014年10月25 日
目录 摘要 (1) 关键词 (1) 1工艺方案分析 (2) 1.1薄壁零件图 (2) 1.2零件图分析 (2) 1.3确定加工方法 (2) 2工件装夹 (3) 2.1定位基准选择 (3) 2.2确定零件定位基准 (3) 2.3装夹方式选择 (3) 2.4确定装夹方式 (3) 3刀具和切削用量选择 (3) 4零件加工 (5) 5加工注意事项 (7) 5.1安全文明生产 (7) 5.2刀具的选择 (7) 5.3削用量的要求 (7) 6影响薄壁加工因素及解决方法 (8) 6.1受力变形 (8) 6.2受热变形 (9) 6.3振动变形 (9)
总结 (10) 参考文献 (11)
摘要 薄壁工件因为具有重量轻、节约材料、结构紧凑等特点,薄壁零件已日益广泛地应用在各工业部门。但薄壁零件的加工是比较棘手的,原因是薄壁零件刚性差、强度弱,在加工中极容易变形,不易保证零件的加工质量。 薄壁零件的加工问题,一直是较难解决的。薄壁件目前一般采用数控车削的方式进行加工,为此要对工件的装夹、刀具几何参数、程序的编制等工艺分析方面进行试验,合理的选择加工方法从而有效地克服了薄壁零件加工过程中出现的变形,保证加工精度。 关键词:薄壁工件工艺分析程序编制加工方法
1工艺方案分析 1.1薄壁零件图 1.2零件图分析 该零件图是薄壁套类零件由外圆、内孔、外螺纹组成。尺寸标注完整,表面粗糙度为1.6,选用毛坯是45号钢。毛坯尺寸Φ35mm×50mm,表面无热处理等要求。 1.3确定加工方法 确定加工方法的原则是保证加工表面加工精度和表面粗糙度。薄壁类零件应按粗、精加工工序。薄壁件通常需要加工工件的内、外表面。内表面的粗加工和精加工都会导致工件变形,所以应按粗精加工分序。内外表面粗加工后,再内外表面精加工,均匀的去除工件表面多余部分,这样有利于消除切削变形。加工方法多种多样,应结合零件的形状,尺寸,位置,选择合理快捷的加工方法。尺寸公差要求较高,公差值较小。取其基本尺寸加工编程便可。
薄壁零件加工方法研究
薄壁零件加工方法研究 【摘要】在实际生产加工中,薄壁零件由于其刚性差、易变形等特点,导致其尺寸精度、形位精度及表面质量难以得到保证,给加工增加了不少难度。本文对切削加工中常见问题进行分析,提出相应方案加以解决改善,并对几种新型的切削加工方法进行了简单介绍。 【关键词】薄壁零件;加工变形;工艺措施;误差补偿;高速切削 薄壁零件通常也叫薄壳零件,这类零件的壁厚和它的轴向或径向尺寸比较相差很悬殊,一般认为零件的壁厚与零件最大尺寸比值小于1/20时,就属于薄壁零件。由于这类零件具有重量轻,节省材料,结构紧凑,占空间位置少等特点,因此在机械、航空航天、船舶等很多领域中有较广泛的应用。当然这类零件的加工方法有多种,例如车削、冲压、焊接、滚压等,但对于一些截面比较复杂而尺寸精度和表面粗糙度要求又比较高的薄壁零件,经常采用车削的方法来加工,因此车床上车削加工薄壁零件是一种很重要很普遍的加工方法。 在实际车削加工过程中,由于薄壁零件的毛坯刚性差、强度弱,所以容易发生变形,导致零件的几何精度、位置精度、表面质量等受到影响,易保证零件的加工质量,给车削加工带来一定的困难。因此如何提高薄壁零件的加工精度,减少加工变形,保证产品合格率是业界内越来越关心的话题。因此对薄壁零件切削过程中的常见问题及解决方法作如下讨论。 1.工件装夹不当产生变形 薄壁零件在夹紧力的作用下容易产生变形,影响工件的尺寸精度和形状精度。车削时为了方便,常采用三爪自定心卡盘装夹工件,如图所示,用三爪自定心卡盘装夹薄壁圆柱零件外圆加工内孔时的示意图。当卡爪夹紧工件时,由于卡爪和工件外圆表面间的接触面太小,导致夹紧力分布不均匀,在夹紧力的作用下,工件与卡爪接触的部位产生弹性变形,使零件呈现出三棱形如图1。三棱形内孔经过车削加工为圆柱孔后,不松开卡爪测量孔的尺寸,完全能符合零件图所规定的尺寸要求如图2。但由于内孔的加工是在工件已产生弹性变形的状态下车出来的,加工完毕松开卡爪后,卸下的工件外圆因弹性变形恢复成圆形,而已加工出的圆柱孔则变成三棱形,如图3所示。 同理用一般三爪卡盘的卡爪涨紧薄壁件的内孔加工外圆表面时,也会出现类似的变形情况。 为避免出现这种情况,可用措施如下: 1.1采用开口过渡环 根据工件的外径做一个开口过渡环,将其装配在工件在外面,三爪卡盘直接
薄壁零件装夹变形的有限元分析
薄壁零件装夹变形的有限元分析 摘要:本文应用分析软件ABAQUS的接触功能,从薄壁零件装夹简化模型面—面接触模型入手,建立了三维接触模型,进行了有限元分析,并以薄壁零件的变形量为评价指标,得出有限元分析结果,以全面了解和掌握精密薄壁零件装夹变形情况,为实际加工过程提供参考依据。 关键词:薄壁零件;精车夹具;装夹变形;有限元分析 目前对装夹技术的研究主要集中在装夹方案的理论分析和装夹过程的误差分析,而工程技术人员在进行具体工装设计时,主要依靠设计人员的经验进行定位和夹紧方案的设计[1]。由于经验设计所取安全系数比较大,造成夹具材料消耗多,夹紧变形大,设计周期长。随着轻量化设计技术的推广,有限元分析工具在产品工装设计中的应用将越来越广。薄壁零件是一类生产中常见的典型零件,其结构特点是刚性差,对夹紧力要求非常严格,既要保证夹紧可靠,同时又要保证夹紧变形小。为实现薄壁零件加工夹具的快速设计和轻量化设计,本文以某薄壁舱体精车夹具为例,应用有限元方法,分析了双锥涨簧夹具机构的夹紧力、夹紧变形,为薄壁类回转零件的夹具设计提供了参考依据。 2.加工夹具设计 [2]根据零件形状特征及精车要求,内孔dl采用双锥涨簧结构定位夹紧,右端内孔d2采用单锥涨簧结构定位夹紧,如图2所示。两套涨簧全线支承薄壁加工零件内孔,使零件加工处于正确的理想尺寸状态。根据大直径薄壁件刚性弱的特点,为保证零件1.8mm的壁厚均匀,达到加工零件的同轴度Ф0.06 mm 设计要求,涨簧设计采用全圆柱面接触,以增加零件整体加工刚性。如图3所示为螺母旋紧带动活动锥体挤压双锥涨簧、涨簧变形而夹紧工件的过程。1.轴2固定锥本3.销 4.双锥涨簧 5.活动锥体Ⅰ 6.导向键7单锥涨簧8.活动锥体Ⅱ9.螺母 3.装夹变形接触问题分析中有限元方法的应用 在机械结构设计中,零件间的接触和配合是很常见的。对于精密薄壁零件的装夹过程而言,螺母旋紧带动活动锥体挤压双锥涨簧、涨簧变形而夹紧工件的过程即是典型的接触问题。目前,在解决接触问题方面已广泛采用有限元方法来确定接触表面上的应力、变形以及接触区域的大小。分析过程是:首先假设接触状态和可能的接触区域,然后按这些状态所对应的边界条件,依照两接触体间的接触面积和压力分布随外载荷变化而变化的特点来建立方程并求解;其结果应满足假定接触状态对应的判定条件,否则需要修改接触状态,继续求解,直到满足相应的判定条件为止。所以接触问题的求解是一个迭代求解过程,需要较大的计算资源,为进行有效的计算,理解问题的特性和建立合理的模型是很重要的。
浅谈薄壁零件的铣削加工技术要点终审稿)
浅谈薄壁零件的铣削加 工技术要点 文稿归稿存档编号:[KKUY-KKIO69-OTM243-OLUI129-G00I-FDQS58-
浅谈薄壁零件的铣削加工技术要点 摘要:薄壁零件的数控铣削加工因薄壁件自身的特点决定了其加工难度极大,制造工艺复杂。本文就薄壁件的特点及加工方法理论进行分析,提出薄壁零件的数控铣削加工中变形控制的相应措施及改善方法。 关键词:薄壁零件加工;数控铣;加工变形 薄壁零件在工程上应用广泛,具有重量轻、强度高、造型美观等突出特点,薄壁零件按照空间几何形态通常可分为以细长轴为代表的二维薄壁构件和以薄壁件为代表的三维薄壁零件。此类零件的共同特点是受力形式复杂,刚度低,加工时极易引起误差变形或工件颤振,从而降低工件的加工精度。特别是当零件的形状和加工精度要求较高时,对振动、切削力大小及波动、切削温度、装夹方式均十分敏感,往往未加工到规定的尺寸,零件已经超出了精度要求,因此,薄壁零件的加工制造难度极大,成为国际上公认的复杂制造工艺问题。 1 薄壁零件加工技术发展的现状 薄壁零件在现代工业技术中占有很重要的战略意义,国内外的学者专家都做了很深入的研究。欧美等制造业比较发达的国家针对薄壁零件的结构特点,应用的技术主要有:(1)从加工工艺系统的整体刚度考虑,提出充分利用零件的整体刚性变形控制方案;(2)在机床方面,提出了平行双主轴联动精度控制方案;(3)在装夹方面,提出了用低熔点合金填充或使用真空夹具精加工零件的方案;(4)在切削用量方面,提出了变进给速度加工方法,通过工艺方法实验与计算机模拟仿真相结
合,提高效率和可靠性;(5)采用有限元仿真预测加工变形,再利用数控补偿技术进行适当主动误差补偿,从而提高薄壁零件的加工精度。而在我国,由于缺少高精的理论计算和相关的试验数据,在这方面的研究还处于起步阶段,无论是振动加工技术还是高速切削技术都是处于摸索阶段,缺少必要的工艺技术数据,在实践中应用还不深入精准。在实际生产加工中,大多采用低转速、小进给、多次空走刀等方法控制加工变形,应用手工或三坐标检验。 2 薄壁零件的加工方法 随着工业的高速发展,各类薄壁零件已?越来越多的应用于各种机器与场合。由于薄壁零件的结构形状特殊性,在其加工过程中受工件材料等诸多因素的影响。引起变形的因素有很多,如加工过程中的受力变形、工件内部产生的残余应力变形、加工中的工件装夹变形等等,所以,在薄壁件的加工中,变形是不可避免的。薄壁件的实际加工中,虽然工件的变形是必然存在的,但我们可以对变形进行控制,可以采取一些相应有效的措施,使变形量降到最小,达到零件加工的误差的范围内。 采用小进给量、大切削速度的高速加工切削形式,可降低加工中工件受到的切削力,同时使大部分的切削热被高速飞离工件的切屑带走,进而降低工件温度,减小工件的热变形。在薄壁件的加工过程中,相对普通数控加工,高速切削加工可省去半精加工、实效处理等其它环节的辅助时间,进而缩短了工件的加工周期,提高了生产效率。 3 薄壁零件的加工变形的控制措施
薄壁零件加工及如何减少变形
薄壁零件加工及如何减少变形 摘要:金属零件,尤其是薄壁零件在加工过程中由于材质本身的状态及加工过程中热应力等因素的影响,变形是不可避免的。本文就此讨论如何减少薄壁零件的加工过程中的变形。实践证明,通过选择合理的装夹方式、刀具的几何角度、切削用量、冷却液等,是完全可以减少薄壁零件在加工过程中的变形,保证零件的加工质量的。 关键词:变形热应力切削用量切削液几何角度数铣 1 概述 零件在加工过程中由于各种因素导致变形是无法消除的,零件在加工中变形的大小除与零件本省材质、结构有关外,也与加工中零件的装夹方式、刀具选用、切削用量及冷却也的选择等有很大的关系。材质、结构与其用途有关,有时是无法取代的。但作为工艺员在零件材料一定的情况下,我们就必须从加工中想办法。我们知道,采用正确的装夹方式、合理选用刀具、切削用量、冷却液是减少零件变形的关键之所在。其中又尤以薄壁零件变形最大,最难控制,主要原因是薄壁零件刚性差、强度弱,在加工中极易产生变形,使零件的形位误差增大,不易保证零件的加工质量。薄壁零件也因为重量轻、节约材料、结构紧凑,应用极为广泛。为此,对薄壁零件加工以及加工过程中零件的装夹,刀具的选用、切削用量、冷却液的选用等作一些探讨和分析,为今后更好的加工薄壁零件,保证零件的加工质量提供一些建议。 2 工艺分析 2.1 零件材料的组成 该零件材料为ZL1,他的成分见表1 2.2零件结构分析 零件总体结构比较简单,但属于薄壁类形腔零件,大部分壁厚仅有3㎜。加工中要去除大部分材料,加工中会产生大部分铣削热量,从而,导致零件产生热变形,这一点是我们制定工艺方案前必须考虑的。 2.3工艺流程的分析 钳:按零件外形及内腔尺寸,单面放1.5㎜划外形、内腔线为下一道工序提供依据 铣:参照钳工划线,单面留余量1.5㎜余量铣外形及内腔、铣厚度二面,本工序加工中去掉大部分材料,因此,余量放得多,保证后序加工由于变形不能保证加工
‘壳盖’薄壁铝合金件加工工艺
'壳盖’薄壁铝合金件加工工艺 壳盖”薄壁铝合金件加工工艺分析中国航空工业集团公司航宇救生装备有限公司(湖北襄阳441002)袁开波 “壳盖”零件是一个薄壁的铝合金零件,其形状及尺寸如图1所示.零件的主 要特点就是壁薄,由于是铝合金件,其强度差,加工时容易变形,要高效率加工合格的零件,加工过程中编制好工艺路线,做好准确的装夹与定位,就至关重要,同时要控制由于切削对零件产生的变形。 图1冗盖 注:未注圆角,凸R1.8mm凹R1mm未注壁厚0.8mm. 、工艺分析 考虑到此零件的内、外形均为圆环形状,其主要的加工方法为数车工序完成,数车工序为分别加工内、外形2个步骤。这里就要考虑加工完第一工序后,在进行第二工序加工时的装夹与定位问题。既要能准确装夹与定位,又要使第二工序的加工操作方便。在经过多次的工艺路线分析及相配合的夹具结构设计之后,确定了先加工内形面,并在其端面上制出装夹定位的位置,然后进行外形面的加工。 、工艺路线
在加工零件的内形面之后,“壳盖”需要安装在一种辅助夹具上,才能进行第 工序的加工,如图 2所示 (a)第一工序图(b)第二工序简图 图2 “壳盖”工艺路线简图 1. 第一工序的加工 “壳盖”在第一工序中要完成如图2(a)所示的加工内容,注意保持各个孔与M64X 0.75螺孔的同轴度。由于“壳盖”壁薄,偏心更易使“壳盖”产生变形。 2. 第二工序的加工 如图2(b)所示,型腔口部的M64X 0.75螺纹段位为装夹部分,用M64X0.75螺纹与辅助夹具进行定位与连接。其夹具的设计,如图2(b)所示。从图中可以看 出,辅助夹具的设计,其型面尺寸与零件的内形面是一致的,零件扣在夹具上,并通过M64X0.75螺纹拧紧,以保证零件内形面与夹具相贴合,这样,在加工外形面时,零件不会产生变形。 3. 安装在辅助夹具上“壳盖”切削时加紧状况的分析 零件在装夹后,车刀切削时,零件的状态是否会松动,可通过图3做一个装夹 及切削的状况分析 从图3(a)中,显示零件在装夹到夹具上时,是顺时针方向旋紧。从图3(b)中 4 一
第二节 工件的装夹方法
教师姓名 授课形式讲授授课时数1授课日期年月日授课班级 授课项目及任务名称 第五章车削 第二节工件的装夹方法 教学目标知识目 标 掌握车床附件的各种装夹方法 技能目 标 学会正确快速的在车床上装夹工件。 教学重点车床附件的结构和装夹方法。教学难点车床附件的装夹方法。 教学方法教学手段 借助于多媒体课件和相关动画及视频,详细教授车床附件的结构和功用。教师先通过PPT课件进行理论知识讲解,再利用相关动画和视频进行演示,让学生能够将理论知识转化成实践经验。同时学生根据所学内容,完成知识的积累,为以后的实践实训打下基础。 学时安排1.花盘装夹约5分钟; 2.弯板装夹约5分钟;3.四爪卡盘安装约15分钟;4.中心架安装约5分钟; 5.顶尖安装约15分钟; 教学条件多媒体设备、多媒体课件。 课外作业查阅、收集CA6140车床附件装夹的相关资料。检查方法随堂提问,按效果计平时成绩。 教学后记
授课主要内容 第二节工件的装夹方法 一、用花盘装夹工件 被加工表面回转轴线与基准面互相垂直的复杂工件或形状不规则、无法使用三爪或四爪卡盘状夹的工件,可以在花盘上装夹。 二、用弯板装夹工件 通常弯板可以和花盘一起使用,使用时把弯板用螺钉牢固在花盘上,工件则安装在弯板上。 为防止转动时因重心偏向一边而产生振动,在工件的另一边要加平衡铁。 三、用四爪卡盘安装工件 四个卡爪盘地装夹范围较大,但由于校正比较繁琐,且在装夹偏心工件时,夹紧作用估有所降低,因此一般仅适用于加工偏心距较小、精度要求不高、形状短而大或者形状比较复杂工件的单件偏心。 四、用中心架装夹工件 工件两端为顶尖夹持,中部装有中心架,工件旋转由拨盘、卡箍驱动。 五、顶尖装夹工件 对于较长的、同轴度要求高的且需要调头加工的轴类工件常用两顶尖安装,其装在主轴上的称为前顶尖,装在尾架上的称为后顶尖。
箱体零件加工工艺设计及装夹变形分析
箱体是机器和部件的基础零件,由它将机器和部件中许多零件连接成一个整体,并使之保持正确的相互位置,彼此能协调地运动。箱体类零件由箱座、箱盖组成,其结构较为复杂,其上通常有一些尺寸精度和位置精度要求都比较高的定位销孔,用作相关零件定位或在加工过程中定位,故机械加工劳动量相当大,困难也相当大,对工艺人员工艺、夹具设计提出很高要求。 保证零件加工质量的前提下,提高生产率,降低成本,是国内外现代机械加工工艺的主要发展方向之一。本文通过对箱体零件图及结构形式的分析基础上,对箱体零件进行工艺分析、工艺说明及加工过程仿真和精度分析。同时以此箱体零件为例进行工艺过程设计,编写相应工艺卡片;其次再对箱体表面的孔的加工进行专用夹具设计与精度和误差分析。实践证明,该工艺与夹具结果能满足生产要求。 关键词:箱体零件加工工艺定位夹具设计
Box is the basis of machines and components parts, which makes many parts are linked into a whole, and make it maintain the correct mutual position, in a coordinated manner with each other movements. Box-type parts are composed of the box seat, lid, whose structure is more complicated, It usually have some higher positioning pin hole on the size accuracy and position precision requirements, used as a related parts positioning or in the machining process positioning, so the mechanical processing needs quite large work. There, it is difficult for process workers to design the process and fixture. At the premise of ensure parts processing quality, improve productivity and reduce the cost is one of the main development direction in modern machining technology at home and abroad. This article based on the analysis of body parts graph and the structure to have processing process simulation and precision analysis about the parts and process description. At the same time, to make the box as an example we design the process design, and make the corresponding process cards. And then to design the special fixture for the machining the hole at the surface of the boxes and analyses the precision and the error. The practice proved that this process and fixture can satisfy the production requirements. Key words: Case accessories; Processing technology; Fixed position; Fixture design
薄壁零件的装夹及加工
薄壁零件的装夹及加工 江苏工贸技师学院 摘要:薄壁零件的车削,应设计合理的加工工艺,选择合适的刀具和切削参数。并详细分析影响薄壁加工精度的因素。经过三种方法实际加工,证明其改进方法是可行的。 关键词:薄壁零件加工影响因素改进 前言 由于薄壁零件具有重量轻,节约材料,结构紧凑等特点,被广泛地应用于各种生产过程里。但同时由于薄壁零件刚性差,强度较弱,在加工时容易变形,所以不容易保证其加工质量。因此优化薄壁零件的装夹方式,刀具的合理选用,切削用量的选择,都可以减少薄壁零件的变形,从而加工出合格的薄壁零件。 一.影响薄壁零件加工精度的主要因素 1.薄壁零件受力变形 如图1所示,其薄壁零件外径直径为31mm.内径直径为30mm。壁厚为0.5mm,而且均有公差0.02mm。由于壁薄强度弱,如卡盘在加紧时用力过大,就会使薄壁零件产生变形,造成零件的精度变差。当在卡盘上的夹紧力过小,在切削加工时就有可能使零件松动造成工件刀具的同时损坏。
图1 2.切削用量的选择 薄壁零件在车削加工时,变形的原因是多方面的,装夹工件时的夹紧力,切削时的切削里力,工件阻碍刀具切削时的弹性变形和塑性变形,使切削区温度升高而产生热变形,而切削力的大小与切削用量是密切相关的,其中背吃刀量和进给量同时增大时,切削力也同时增大,工件变形的程度也同时增大。 而减少背吃刀量,增大进给量切削力虽下降,但工件表面粗糙度会增大,使强度不好的薄壁零件内应力增加,同样会使零件变形。 因此粗加工时背吃刀量和进给量可以取大些,精加工时背吃刀量一般控制在0.2—0.5mm之间,进给量控制在0.1—0.2mm之间,精车时用尽量高地切削速度,但不宜过高。 合理选用三要素就能减少切削力,以此减小其变形。 3.刀具的几何角度的选择 在薄壁零件的车削中,合理的刀具几何角度,对车削力的大小,车削中产生的热变形是非常重要的,刀具前角大小决定切削变形与刀具前角的锋利度,前角大,切削变形和摩擦力减小,切削力减小,但前角太大,会使刀具的楔角减小,刀具强度减弱,刀具散热请况变差,磨损加快,因此,刀具的选择至关重要。针对后面提到的加工图1零件以及芯轴所需用到的刀具如下表:
夹具的选择、工件装夹方法的确定
一、夹具的选择、工件装夹方法的确定 1.夹具的选择 数控加工对夹具主要有两大要求:一是夹具应具有足够的精度和刚度;二是夹具应有可靠的定位基准。选用夹具时,通常考虑以下几点: 1)尽量选用可调整夹具、组合夹具及其它通用夹具,避免采用专用夹具,以缩短生产准备 时间。 2)在成批生产时才考虑采用专用夹具,并力求结构简单。 3)装卸工件要迅速方便,以减少机床的停机时间。 4)夹具在机床上安装要准确可靠,以保证工件在正确的位置上加工。 2.夹具的类型 数控车床上的夹具主要有两类:一类用于盘类或短轴类零件,工件毛坯装夹在带可调卡爪的卡盘(三爪、四爪)中,由卡盘传动旋转;另一类用于轴类零件,毛坯装在主轴顶尖和尾架顶尖间,工件由主轴上的拨动卡盘传动旋转。 数控铣床上的夹具,一般安装在工作台上,其形式根据被加工工件的特点可多种多样。 如:通用台虎钳、数控分度转台等。 3.零件的安装 数控机床上零件的安装方法与普通机床一样,要合理选择定位基准和夹紧方案,注意以 下两点: 1)力求设计、工艺与编程计算的基准统一,这样有利于编程时数值计算的简便性和精确性。 2)尽量减少装夹次数,尽可能在一次定位装夹后,加工出全部待加工表面。 二、刀具的选择及对刀点、换刀点的设置 1.刀具的选择 与普通机床加工方法相比,数控加工对刀具提出了更高的要求,不仅需要刚性好、精度高,而且要求尺寸稳定,耐用度高,断屑和排屑性能好;同时要求安装调整方便,这样来满足数控机床高效率的要求。数控机床上所选用的刀具常采用适应高速切削的刀具材料(如高速钢、超细粒度硬质合金)并使用可转位刀片。(1)车削用刀具及其选择数控车削常用的车刀一般分尖形车刀、圆弧形车刀以及成型车刀三类。 1)尖形车刀尖形车刀是以直线形切削刃为特征的车刀。这类车刀的刀尖由直线形的主副切削刃构成,如90°内外圆车刀、左右端面车刀、切槽(切断)车刀及刀尖倒棱很小的各 种外圆和内孔车刀。 尖形车刀几何参数(主要是几何角度)的选择方法与普通车削时基本相同,但应结合数控加工的特点(如加工路线、加工干涉等)进行全面的考虑,并应兼顾刀尖本身的强度。2)圆弧形车刀圆弧形车刀是以一圆度或线轮廓度误差很小的圆弧形切削刃为特征的车刀。该车刀圆弧刃每一点都是圆弧形车刀的刀尖,应此,刀位点不在圆弧上,而在该圆弧的圆心 上。 圆弧形车刀可以用于车削内外表面,特别适合于车削各种光滑连接(凹形)的成型面。