太阳能电池制备工艺流程-
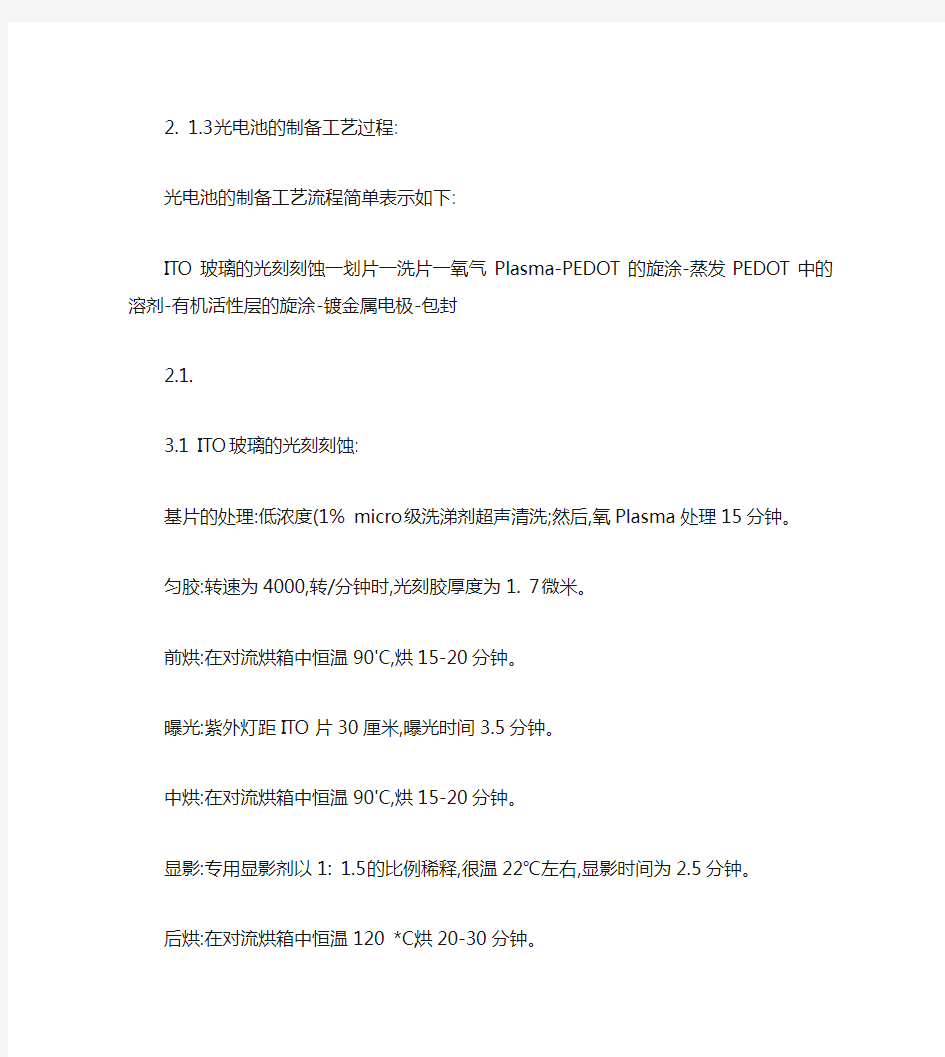
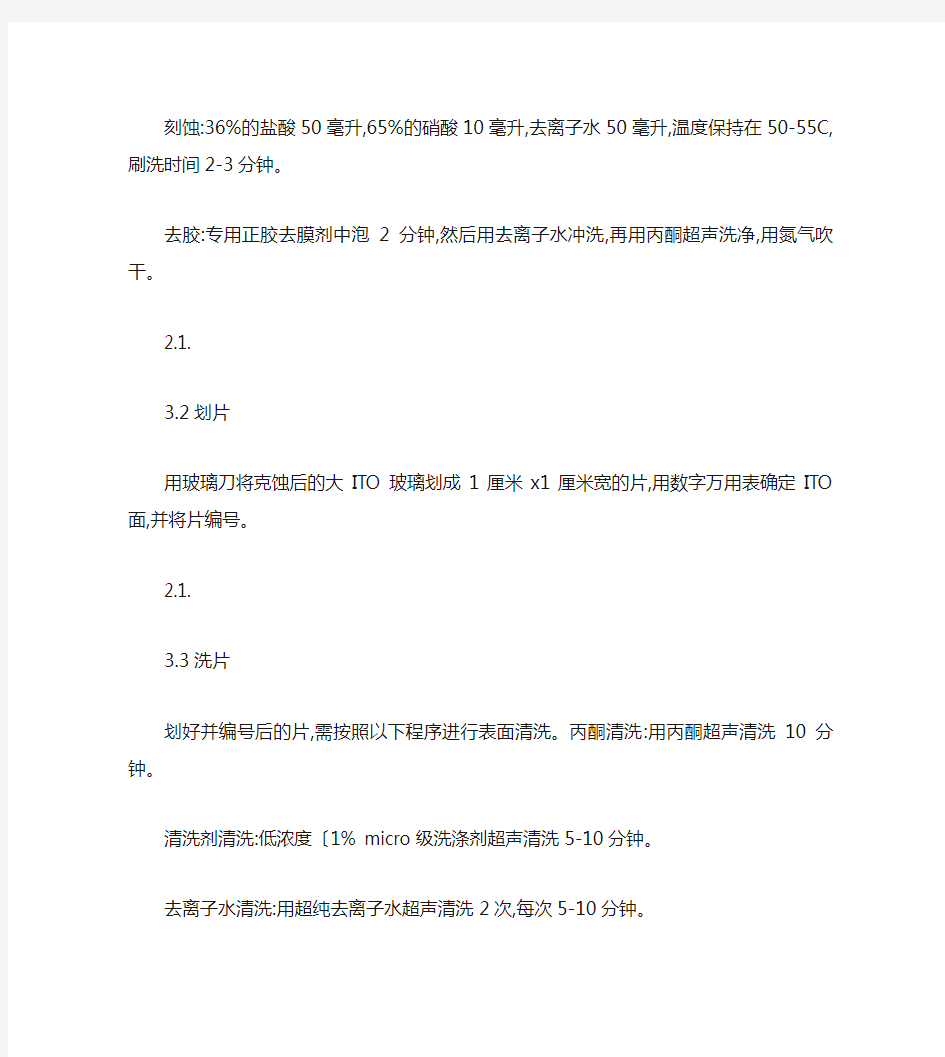
2. 1.3光电池的制备工艺过程:
光电池的制备工艺流程简单表示如下:
ITO玻璃的光刻刻蚀一划片一洗片一氧气Plasma-PEDOT的旋涂-蒸发PEDOT 中的溶剂-有机活性层的旋涂-镀金属电极-包封
2.1.
3.1 ITO玻璃的光刻刻蚀:
基片的处理:低浓度(1% micro级洗涕剂超声清洗;然后,氧Plasma处理15分钟。
匀胶:转速为4000,转/分钟时,光刻胶厚度为1. 7微米。
前烘:在对流烘箱中恒温90'C,烘15-20分钟。
曝光:紫外灯距ITO片30厘米,曝光时间3.5分钟。
中烘:在对流烘箱中恒温90'C,烘15-20分钟。
显影:专用显影剂以1: 1.5的比例稀释,很温22℃左右,显影时间为2.5分钟。
后烘:在对流烘箱中恒温120 *C,烘20-30分钟。
刻蚀:36%的盐酸50毫升,65%的硝酸10毫升,去离子水50毫升,温度保持在50-55C,刷洗时间2-3分钟。
去胶:专用正胶去膜剂中泡2分钟,然后用去离子水冲洗,再用丙酮超声洗净,用氮气吹干。
2.1.
3.2划片
用玻璃刀将克蚀后的大ITO玻璃划成1厘米x1厘米宽的片,用数字万用表确定ITO面,并将片编号。
2.1.
3.3洗片
划好并编号后的片,需按照以下程序进行表面清洗。丙酮清洗:用丙酮超声清洗10分钟。
清洗剂清洗:低浓度〔1% micro级洗涤剂超声清洗5-10分钟。
去离子水清洗:用超纯去离子水超声清洗2次,每次5-10分钟。
异丙醇清洗:用异丙醇超声清洗5-10分钟。后用氮气吹干,并放入真空烘箱内保存。
2.1.
3.4氧气Plasma
制片前,ITO片需氧Plasma l0-15分钟。Plasma真空条件为2-3mPa,氧气流量4-5 ml/s。
2.1.
3.5 PEDOT的旋涂
用匀胶机旋涂PEDOT,匀胶前用表面轮廓仪测定厚度并观察表面,以确定按照需要厚度所需的匀胶速度。
2.1.
3.6蒸发PEDOT中的溶剂
在真空烘箱中以80-85℃的温度恒温烘2-3小时,以蒸发其中的溶剂。
2.1.
3.7有机活性层的旋涂
在半导体试验手套箱内旋涂,半导体试验手套箱内为高纯氮气以获得低氧低湿度状态,手套箱内氧含量少于5 ppm,相对湿度低于1 ppm.旋涂前先用表面轮廓仪测厚,以确定所需厚度的旋转速度。
2.1.
3.8镀金属电极
金属电极是在真空镀膜机内高温蒸镀,真空镀膜机安装在半导体试验手套箱内。蒸镀过程中用微型测厚仪测厚。
镀膜工艺过程:
装片:检查分子泵进出口开关是否关紧,往微型镀膜机内通一定量的氮气使镀膜机内气压与手套箱内气压一致,打开镀膜机钟罩检查金属网内是否有所需镀膜的金属,将片装上装片模板,将模板置于架上并放进镀膜机内,然后关上钟罩;用机械泵抽真空微型镀膜机与分子泵:开启机械泵,打开微型镀膜机与机械泵之间的阀门,抽真空5分钟后关上此阀门,打开机
械泵与分子泵之间的阀门,约5分钟后进行下一步;分子泵抽真空微型镀膜机:向分子泵内通冷却水,打开分子泵与微型镀膜机之间的阀门,开启分子泵,5分钟左右分子泵显示运行正常,开启真空计并观察读数是否低于1.0 X 10-3Pa,抽真空致真空低于2.0 X 10-5Pa后开始镀膜。
常用AL电极的真空镀膜条件:
金属参数:Bulk Density 2.73 Gm/cm3阻抗因子(Z-Factor1.080
镀前:温度43C;真空2.0 X l0-4 Pa
厚度少于50 nm时:电压2. 8 V;电流41 A;速度低于l nm/s
厚度大于50nm时:电压8. 9 V;电流60 A;速度高于10 nm/s
镀后:温度54 C;真空1.0 X 10-3 Pa
常用Ba的真空镀膜条件:
金属参数:Bulk Density 3.5 Gm/cm 3 阻抗因子(Z-Factor 2.100
镀前:温度43 C;真空2.0 X 10-4 Pa
电压1.34 V;电流91 A;速度0.03-0.05 nm/s
镀后:温度54 C;真空1.0 X 10-3 Pa
2.1.
3.9包封:用聚碳酸酯在紫外固化炉中固化包封,固化时间1-2分钟。
光伏系统设计计算公式
光伏发电系统设计计算公式 1、转换效率: η= Pm(电池片的峰值功率)/A(电池片面积)×Pin(单位面积的入射光功率) 其中:Pin=1KW/㎡=100mW/cm2。 2、充电电压: Vmax=V额×1.43倍 3.电池组件串并联 3.1电池组件并联数=负载日平均用电量(Ah)/组件日平均发电量(Ah) 3.2电池组件串联数=系统工作电压(V)×系数1.43/组件峰值工作电压(V) 4.蓄电池容量 蓄电池容量=负载日平均用电量(Ah)×连续阴雨天数/最大放电深度 5平均放电率 平均放电率(h)=连续阴雨天数×负载工作时间/最大放电深度 6.负载工作时间 负载工作时间(h)=∑负载功率×负载工作时间/∑负载功率 7.蓄电池: 7.1蓄电池容量=负载平均用电量(Ah)×连续阴雨天数×放电修正系数/最大放电深度×低温修正系数 7.2蓄电池串联数=系统工作电压/蓄电池标称电压 7.3蓄电池并联数=蓄电池总容量/蓄电池标称容量 8.以峰值日照时数为依据的简易计算 8.1组件功率=(用电器功率×用电时间/当地峰值日照时数)×损耗系数 损耗系数:取1.6~2.0,根据当地污染程度、线路长短、安装角度等; 8.2蓄电池容量=(用电器功率×用电时间/系统电压)×连续阴雨天数×系统安全系数 系统安全系数:取1.6~2.0,根据蓄电池放电深度、冬季温度、逆变器转换效率等; 9.以年辐射总量为依据的计算方式 组件(方阵)=K×(用电器工作电压×用电器工作电流×用电时间)/当地年辐射总量 有人维护+一般使用时,K取230;无人维护+可靠使用时,K取251;无人维护+环境恶劣+要求非常可靠时,K取276; 10.以年辐射总量和斜面修正系数为依据的计算 10.1方阵功率=系数5618×安全系数×负载总用电量/斜面修正系数×水平面年平均辐射量 系数5618:根据充放电效率系数、组件衰减系数等;安全系数:根据使用环境、有无备用电源、是否有人值守等,取1.1~1.3; 10.2蓄电池容量=10×负载总用电量/系统工作电压;10:无日照系数(对于连续阴雨不超过5天的均适用) 11.以峰值日照时数为依据的多路负载计算 11.1电流: 组件电流=负载日耗电量(Wh)/系统直流电压(V)×峰值日照时数(h)×系统效率系数 系统效率系数:含蓄电池充电效率0.9,逆变器转换效率0.85,组件功率衰减+线路损耗+尘埃等0.9.具体根据实际情况进行调整。 11.2功率:
太阳能电池板的生产工艺流程
太阳能电池板的生产工艺流程 太阳能电池板的生产工艺流程 封装是太阳能电池生产中的关键步骤,没有良好的封装工艺,多好的电池也生产不出好的太阳能电池板。电池的封装不仅可以使电池的寿命得到保证,而且还增强了电池的抗击强度。产品的高质量和高寿命是赢得客户满意的关键,所以太阳能电池板的封装质量非常重要。 (1)流程 电池检测——正面焊接——检验——背面串接——检验——敷设(玻璃清洗、材料切割、玻璃预处理、敷设)——层压——去毛边(去边、清洗)——装边框(涂胶、装角键、冲孔、装框、擦洗余胶)——焊接接线盒——高压测试——组件测试——外观检验——包装入库。 (2)组件高效和高寿命的保证措施 高转换效率、高质量的电池片;高质量的原材料,例如,高的交联度的EVA、高黏结强度的封装剂(中性硅酮树脂胶)、高透光率高强度的钢化玻璃等; 合理的封装工艺,严谨的工作作风, 由于太阳电池属于高科技产品,生产过程中一些细节问题,如应该戴手套而不戴、应该均匀地涂刷试剂却潦草完事等都会严重地影响产品质量,所以除了制定合理的工艺外,员工的认真和严谨是非常重要的。 (3)太阳能电池组装工艺简介 ①电池测试:由于电池片制作条件的随机性,生产出来的电池性能不尽相同,所以为了有效地将性能一致或相近的电池组合在一起,所以应根据其性能参数进行分类;电池测试即通过测试电池的输出参数(电流和电压)的大小对其进行分类。以提高电池的利用率,做出质量合格的太阳能电池组件。如果把一片或者几片低功率的电池片装在太阳电池单体中,将会使整个组件的输出功率降低。因此,为了最大限度地降低电池串并联的损失,必须将性能相近的单体电池组合成组件。 ②焊接:一般将6~12个太阳能电池串联起来形成太阳能电池串。传统上,一般采用银扁线构成电池的接头,然后利用点焊或焊接(用红外灯,利用红外线的热效应)等方法连接起来。现在一般使用60%的Sn、38%的Pb、2%的Ag 电镀后的铜扁丝(厚度约为100~200μm)。接头需要经过火烧、红外、热风、激
太阳能板制作工艺
太阳能电池板(组件)生产工艺 组件线又叫封装线,封装是太阳能电池生产中的关键步骤,没有良好的封装工艺,多好的电池也生产不出好的组件板。电池的封装不仅可以使电池的寿命得到保证,而且还增强了电池的抗击强度。产品的高质量和高寿命是赢得可客户满意的关键,所以组件板的封装质量非常重要。 流程: 1、电池检测—— 2、正面焊接—检验— 3、背面串接—检验— 4、敷设(玻璃清洗、材料切割、玻璃预处理、敷设)—— 5、层压—— 6、去毛边(去边、清洗)—— 7、装边框(涂胶、装角键、冲孔、装框、擦洗余胶)—— 8、焊接接线盒—— 9、高压测试——10、组件测试—外观检验—11、包装入库 组件高效和高寿命如何保证: 1、高转换效率、高质量的电池片; 2、高质量的原材料,例如:高的交联度的EVA、高粘结强度的封装剂(中性硅酮树脂胶)、高透光率高强度的钢化玻璃等; 3、合理的封装工艺 4、员工严谨的工作作风; 由于太阳电池属于高科技产品,生产过程中一些细节问题,一些不起眼问题如应该戴手套而不戴、应该均匀的涂刷试剂而潦草完事等都是影响产品质量的大敌,所以除了制定合理的制作工艺外,员工的认真和严谨是非常重要的。 太阳电池组装工艺简介: 工艺简介:在这里只简单的介绍一下工艺的作用,给大家一个感性的认识. 1、电池测试:由于电池片制作条件的随机性,生产出来的电池性能不尽相同,所以为了有效的将性能一致或相近的电池组合在一起,所以应根据其性能参数进行分类;电池测试即通过测试电池的输出参数(电流和电压)的大小对其进行分类。以提高电池的利用率,做出质量合格的电池组件。 2、正面焊接:是将汇流带焊接到电池正面(负极)的主栅线上,汇流带为镀锡的铜带,我们使用的焊接机可以将焊带以多点的形式点焊在主栅线上。焊接用的热源为一个红外灯(利用红外线的热效应)。焊带的长度约为电池边长的2倍。多出的焊带在背面焊接时与后面的电池片的背面电极相连 3、背面串接:背面焊接是将36片电池串接在一起形成一个组件串,我们目前采用的工艺是手动的,电池的定位主要靠一个膜具板,上面有36个放置电池片的凹槽,槽的大小和电池的大小相对应,槽的位置已经设计好,不同规格的组件使用不同的模板,操作者使用电烙铁和焊锡丝将“前面电池”的正面电极(负极)焊接到“后面电池”的背面电极(正极)上,这样依次将36片串接在一起并在组件串的正负极焊接出引线。 4、层压敷设:背面串接好且经过检验合格后,将组件串、玻璃和切割好的EVA 、玻璃纤维、背板按照一定的层次敷设好,准备层压。玻璃事先涂一层试剂(primer)以增加玻璃和EVA的粘接强度。敷设时保证电池串与玻璃等材料的相对位置,调整好电池间的距离,为层压打好基础。(敷设层次:由下向上:玻璃、EVA、电池、EVA、玻璃纤维、背板)。 5、组件层压:将敷设好的电池放入层压机内,通过抽真空将组件内的空气抽出,然后加热使EVA熔化将电池、玻璃和背板粘接在一起;最后冷却取出组件。层压工艺是组件生产的关键一步,层压温度层压时间根据EVA的性质决定。我们使用快速固化EVA 时,层压循环时间约为25分钟。固化温度为150℃。 6、修边:层压时EVA熔化后由于压力而向外延伸固化形成毛边,所以层压完毕应
晶体硅太阳能电池的制造工艺流程
晶体硅太阳能电池的制造 工艺流程 This model paper was revised by the Standardization Office on December 10, 2020
提高太阳能电池的转换效率和降低成本是太阳能电池技术发展的主流。 晶体硅太阳能电池的制造工艺流程说明如下: (1)切片:采用多线切割,将硅棒切割成正方形的硅片。 (2)清洗:用常规的硅片清洗方法清洗,然后用酸(或碱)溶液将硅片表面切割损伤层除去30-50um。 (3)制备绒面:用碱溶液对硅片进行各向异性腐蚀在硅片表面制备绒面。 (4)磷扩散:采用涂布源(或液态源,或固态氮化磷片状源)进行扩散,制成PN+结,结深一般为-。 (5)周边刻蚀:扩散时在硅片周边表面形成的扩散层,会使电池上下电极短路,用掩蔽湿法腐蚀或等离子干法腐蚀去除周边扩散层。 (6)去除背面PN+结。常用湿法腐蚀或磨片法除去背面PN+结。 (7)制作上下电极:用真空蒸镀、化学镀镍或铝浆印刷烧结等工艺。先制作下电极,然后制作上电极。铝浆印刷是大量采用的工艺方法。 (8)制作减反射膜:为了减少入反射损失,要在硅片表面上覆盖一层减反射膜。制作减反射膜的材料有MgF2 ,SiO2 ,Al2O3,SiO ,Si3N4 ,TiO2 ,Ta2O5等。工艺方法可用真空镀膜法、离子镀膜法,溅射法、印刷法、PECVD法或喷涂法等。 (9)烧结:将电池芯片烧结于镍或铜的底板上。 (10)测试分档:按规定参数规范,测试分类。
由此可见,太阳能电池芯片的制造采用的工艺方法与半导体器件基本相同,生产的工艺设备也基本相同,但工艺加工精度远低于集成电路芯片的制造要求,这为太阳能电池的规模生产提供了有利条件。
太阳能电池板与蓄电池配置计算公式
太阳能电池板与蓄电池配置计算公式(图) 太阳能电池板与蓄电池配置计算公式 一:首先计算出电流: 如:12V蓄电池系统; 30W的灯2只,共60瓦。 电流=60W÷12V=5A 二:计算出蓄电池容量需求: 如:路灯每夜累计照明时间需要为满负载7小时(h); (如晚上8:00开启,夜11:30关闭1路,凌晨4:30开启2路,凌晨5:30关闭) 需要满足连续阴雨天5天的照明需求。(5天另加阴雨天前一夜的照明,计6天) 蓄电池=5A×7h×(5+1)天=5A×42h=210AH 另外为了防止蓄电池过充和过放,蓄电池一般充电到90%左右;放电余留20%左右。 所以210AH也只是应用中真正标准的70%左右。 三:计算出电池板的需求峰值(WP): 路灯每夜累计照明时间需要为7小时(h); ★:电池板平均每天接受有效光照时间为4.5小时(h); 最少放宽对电池板需求20%的预留额。 WP÷17.4V=(5A×7h×120%)÷4.5h WP÷17.4V=9.33 WP=162(W)
光伏发电系统计算方法 光伏系统的规模和应用形式各异,如系统规模跨度很大,小到几瓦的太阳能庭院灯,大到MW级的太阳能光伏电站。其应用形式也多种多样,在家用、交通、通信、空间应用等诸多领域都能得到广泛的应用。尽管光伏系统规模大小不一,但其组成结构和工作原理基本相同。 太阳能发电系统由太阳能电池组、太阳能控制器、蓄电池(组)组成。如输出电源为交流220V或11 0V,还需要配置逆变器。各部分的作用为: (一)太阳能电池板:太阳能电池板是太阳能发电系统中的核心部分,也是太阳能发电系统中价值最高的部分。其作用是将太阳的辐射能力转换为电能,或送往蓄电池中存储起来,或推动负载工作。 (二)太阳能控制器:太阳能控制器的作用是控制整个系统的工作状态,并对蓄电池起到过充电保护、过放电保护的作用。在温差较大的地方,合格的控制器还应具备温度补偿的功能。其他附加功能如光控开关、时控开关都应当是控制器的可选项; (三)蓄电池:一般为铅酸电池,小微型系统中,也可用镍氢电池、镍镉电池或锂电池。其作用是在有光照时将太阳能电池板所发出的电能储存起来,到需要的时候再释放出来。 (四)逆变器:在很多场合,都需要提供220VAC、110VAC的交流电源。由于太阳能的直接输出一般都是12VDC、24VDC、48VDC。为能向220VAC的电器提供电能,需要将太阳能发电系统所发出的直流电能转换成交流电能,因此需要使用DC-AC逆变器。在某些场合,需要使用多种电压的负载时,也要用到DC-DC逆变器,如将24VDC的电能转换成5VDC的电能(注意,不是简单的降压)。 光伏系统的设计包括两个方面:容量设计和硬件设计。 在进行光伏系统的设计之前,需要了解并获取一些进行计算和选择必需的基本数据:光伏系统现场的地理位置,包括地点、纬度、经度和海拔;该地区的气象资料,包括逐月的太阳能总辐射量、直接辐射量以及散射辐射量,年平均气温和最高、最低气温,最长连续阴雨天数,最大风速以及冰雹、降雪等特殊气象情况等。 蓄电池的设计包括蓄电池容量的设计计算和蓄电池组的串并联设计。首先,给出计算蓄电池容量的基本方法。 (1)基本公式
太阳能电池片生产工艺常用化学品及其应用
太阳能电池片生产工艺常用化学品及其应用 一般来说,半导体工艺是将原始半导体材料转变为有用的器件的一个过程,太阳能电池工艺就是其中的一种,这些工艺都要使用化学药品。 1.常用化学药品 太阳能电池工艺常用化学药品有:乙醇(C2H5OH)、氢氧化钠(NaOH)、盐酸(HCl)、氢氟酸(HF)、异丙醇(IPA)、硅酸钠(Na2SiO3)、氟化铵(NH4F)、三氯氧磷(POCl3)、氧气(O2)、氮气(N2)、三氯乙烷(C2H3Cl3)、四氟化碳(CF4)、氨气(NH3)和硅烷(SiH4),光气等。 2.电池片生产工艺过程中各化学品的应用及反应方程式: 2.1一次清洗工艺 2.1.1去除硅片损伤层: Si + 2 NaOH + H2O = Na2SiO3 + 2 H2 ↑ 28 80 122 4 对125*125的单晶硅片来说,假设硅片表面每边去除10um,两边共去除20um,则每片去处的硅的重量为:△g=12.5*12.5*0.002*2.33 = 0.728g。(硅的密度为2.33g/cm3) 设每片消耗的NaOH为X克,生成的硅酸钠和氢气分别为Y和Z克,根据化学方程式有: 28 :80 = 0.728 :XX= 2.08g 28 :122 = 0.728 :Y Y=3.172g 28 :4 = 0.728 :Z Z= 0.104g 2.1.2制绒面: Si + 2 NaOH + H2O = Na2SiO3 + 2 H2 ↑ 28 80 122 4 由于在制绒面的过程中,产生氢气得很容易附着在硅片表面,从而造成绒面的不连续性,所以要在溶液中加入异丙醇作为消泡剂以助氢气释放。另外在绒面制备开始阶段,为了防止硅片腐蚀太快,有可能引起点腐蚀,容易形成抛光腐蚀,所以要在开始阶段加入少量的硅酸钠以减缓对硅片的腐蚀。 2.1.3 HF酸去除SiO2层 在前序的清洗过程中硅片表面不可避免的形成了一层很薄的SiO2层,用HF酸把这层SiO2去除掉。 SiO2 + 6 HF = H2[SiF6] + 2 H2O 2.1.4HCl酸去除一些金属离子,盐酸具有酸和络合剂的双重作用,氯离子能与Pt 2+、Au 3+、Ag +、Cu+、Cd 2+、Hg 2+等金属离子形成可溶于水的络合物。 2.2扩散工艺 2.2.1扩散过程中磷硅玻璃的形成: Si + O2=SiO2 5POCl3=3 PCl5 + P2O5(600℃) 三氯氧磷分解时的副产物PCl5,不容易分解的,对硅片有腐蚀作用,但是在有氧气的条件下,可发生以下反应: 4PCl5 + 5O2=2 P2O5 + 10Cl2↑(高温条件下) 磷硅玻璃的主要组成:小部分P2O5,其他是2SiO2·P2O5或SiO2·P2O5。这三种成分分散在二氧化硅中。 在较高温度的时候,P2O5作为磷源和Si反应生成磷,反应如下:
太阳能电池板与蓄电池配置计算公式
太阳能电池板与蓄电池配置计算公式 一:首先计算出电流: 如:12V蓄电池系统; 30W的灯2只,共60瓦。 电流=60W-12V= 5A 二:计算出蓄电池容量需求: 如:路灯每夜累计照明时间需要为满负载7小时(h); (如晚上8:00 开启,夜11:30 关闭1 路,凌晨4:30 开启2 路,凌晨5:30 关闭) 需要满足连续阴雨天5 天的照明需求。(5 天另加阴雨天前一夜的照明,计6 天) 蓄电池=5A X7h X(5 + 1)天=5A X42h= 210AH 另外为了防止蓄电池过充和过放,蓄电池一般充电到90%左右;放电余留20%左右。 所以210AH也只是应用中真正标准的70%左右。 三:计算出电池板的需求峰值(WP): 路灯每夜累计照明时间需要为7小时(h); ★:电池板平均每天接受有效光照时间为小时(h) ; 最少放宽对电池板需求20%的预留额。 W- = (5A X7h X120%— WP-= WP=162(W)
光伏发电系统计算方法 光伏系统的规模和应用形式各异,如系统规模跨度很大,小到几瓦的太阳能庭院灯,大到MV级的太阳能光伏电站。其应用形式也多种多样,在家用、交通、通信、空间应用等诸多领域都能得到广泛的应用。尽管光伏系统规模大小不一,但其组成结构和工作原理基本相同。 太阳能发电系统由太阳能电池组、太阳能控制器、蓄电池(组)组成。如输出电源为交流220V或11 0V,还需要配置逆变器。各部分的作用为: (一)太阳能电池板:太阳能电池板是太阳能发电系统中的核心部分,也是太阳能发电系统中价值最高的部分。其作用是将太阳的辐射能力转换为电能,或送往蓄电池中存储起来,或推动负载工作。 (二)太阳能控制器:太阳能控制器的作用是控制整个系统的工作状态,并对蓄电池起到过充电保 护、过放电保护的作用。在温差较大的地方,合格的控制器还应具备温度补偿的功能。其他附加功能如光控开关、时控开关都应当是控制器的可选项; (三)蓄电池:一般为铅酸电池,小微型系统中,也可用镍氢电池、镍镉电池或锂电池。其作用是在有光照时将太阳能电池板所发出的电能储存起来,到需要的时候再释放出来。 (四)逆变器:在很多场合,都需要提供220VAC 110VAC的交流电源。由于太阳能的直接输出一般 都是12VDC 24VDC 48VDC为能向220VAC的电器提供电能,需要将太阳能发电系统所发出的直流电 能转换成交流电能,因此需要使用DC-AC逆变器。在某些场合,需要使用多种电压的负载时,也要用到DC-DC逆变器,如将24VDC的电能转换成5VDC的电能(注意,不是简单的降压)。光伏系统的设计包括两个方面:容量设计和硬件设计。
单晶硅太阳能电池详细工艺
单晶硅太阳能电池 1.基本结构 2.太阳能电池片的化学清洗工艺 切片要求:①切割精度高、表面平行度高、翘曲度和厚度公差小。②断面完整性好,消除拉丝、刀痕和微裂纹。③提高成品率,缩小刀(钢丝)切缝,降低原材料损耗。④提高切割速度,实现自动化切割。 具体来说太阳能硅片表面沾污大致可分为三类: 1、有机杂质沾污:可通过有机试剂的溶解作用,结合兆声波清洗技术来去除。 2、颗粒沾污:运用物理的方法可采机械擦洗或兆声波清洗技术来去除粒径≥ 0.4 μm颗粒,利用兆声波可去除≥ 0.2 μm颗粒。 3、金属离子沾污:该污染必须采用化学的方法才能将其清洗掉。硅片表面金属杂质沾污又可分为两大类:(1)、沾污离子或原子通过吸附分散附着在硅片表面。(2)、带正电的金属离子得到电子后面附着(尤如“电镀”)到硅片表面。
1、用 H2O2作强氧化剂,使“电镀”附着到硅表面的金属离子氧化成金属,溶解在清洗液中或吸附在硅片表面。 2、用无害的小直径强正离子(如H+),一般用HCL作为H+的来源,替代吸附在硅片表面的金属离子,使其溶解于清洗液中,从而清除金属离子。 3、用大量去离子水进行超声波清洗,以排除溶液中的金属离子。 由于SC-1是H2O2和NH4OH的碱性溶液,通过H2O2的强氧化和NH4OH 的溶解作用,使有机物沾污变成水溶性化合物,随去离子水的冲洗而被排除;同时溶液具有强氧化性和络合性,能氧化Cr、Cu、Zn、Ag、Ni、Co、Ca、Fe、Mg等,使其变成高价离子,然后进一步与碱作用,生成可溶性络合物而随去离子水的冲洗而被去除。因此用SC-1液清洗抛光片既能去除有机沾污,亦能去除某些金属沾污。在使用SC-1液时结合使用兆声波来清洗可获得更好的清洗效果。 另外SC-2是H2O2和HCL的酸性溶液,具有极强的氧化性和络合性,能与氧化以前的金属作用生成盐随去离子水冲洗而被去除。被氧化的金属离子与CL-作用生成的可溶性络合物亦随去离子水冲洗而被去除。 3.太阳能电池片制作工艺流程图 具体的制作工艺说明 (1)切片:采用多线切割,将硅棒切割成正方形的硅片。 (2)清洗:用常规的硅片清洗方法清洗,然后用酸(或碱)溶液将 硅片表面切割损伤层除去30-50um。 (3)制备绒面:用碱溶液对硅片进行各向异性腐蚀在硅片表面制备 绒面。 (4)磷扩散:采用涂布源(或液态源,或固态氮化磷片状源)进行 扩散,制成PN+结,结深一般为0.3-0.5um。
太阳能电池板日发电量简易计算方法
太阳能电池板日发电量简易计算方法 太阳能电池板日发电量 简易计算方法 太阳能交流发电系统是由太阳电池板、充电控制器、逆变器和蓄电池共同组成;太阳能直流发电系统则不包括逆变器。为了使太阳能发电系统能为负载提供足够的电源,就要根据用电器的功率,合理选择各部件。太阳能发电系统的设计需要考虑如下因素: Q1、太阳能发电系统在哪里使用?该地日光辐射情况如何? Q2、系统的负载功率多大? Q3、系统的输出电压是多少,直流还是交流? Q4、系统每天需要工作多少小时? Q5、如遇到没有日光照射的阴雨天气,系统需连续供电多少天? 下面以(负载)100W输出功率,每天使用6个小时为例,介绍一下计算方法: 1. 首先应计算出每天消耗的瓦时数(包括逆变器的损耗): 若逆变器的转换效率为90%,则当输出功率为100W时,则实际需要输出功率应为100W/90%=111W;若按每天使用6小时,则耗电量为111W*6小时=666Wh,即0.666度电。 2. 计算太阳能电池板: 按每日有效日照时间为5小时计算,再考虑到充电效率和充电过程中的损耗,太阳能电池板的输出功率应为666Wh÷5h÷70% =190W。其中70%是充电过程中,太阳能电池板的实际使用功率。 3. 180瓦组件日发电量 180×0.7×5=567WH=0.63度 1MW日发电量=1000000×0.7×5=3500,000=3500度 例2:安10w灯,每天照明6小时,3个连雨天,如何计算太阳能电池板wp?以及12V 蓄电池ah? 每天的用电量: 10W X 6H= 60WH, 计算太阳能电池板: 假设你安装点的平均峰值日照时数为4小时. 则:60WH/4小时, = 15WP 太阳能电池板. 再计算充放电损耗, 以及每天需要给太阳能电池板的补充: 15WP/0.6= 25WP, 也就是一块25W的太阳能电池板就够了. 再计算蓄电池. 60WH/12V=5AH. 每天要用12V5AH的电量. 三天则为12V15AH.
太阳能电池片生产工艺简介解读
培训资料 前道 一制绒工艺 制绒目的 1?消除表面硅片有机物和金属杂质。 2.去处硅片表面机械损伤层。 3?在硅片表面形成表面组织,增加太阳光的吸收减少反射。 工艺流程 来料,开盒,检查,装片,称重,配液加液,制绒,甩干,制绒后称重,绒面检查,流出。 单晶制绒1号机 2号机 基本原理 1#超声 去除有机物和表面机械损伤层。 目前采用柠檬酸超声,和双氧水与氨水混合超声。
3#4#5#6#制绒 利用NaOH 溶液对单晶硅片进行各向异性腐蚀的特点来制备绒面。当各向异性因子((100) 面与(111)面单晶硅腐蚀速率之比)=10 时,可以得到整齐均匀的金字塔形的角锥体组成的绒面。绒面具有受光面积大,反射率低的特点。可以提高单晶硅太阳能电池的短路电流,从而提高太阳能电池的光转换效率。 化学反应方程式:Si+2NaOH+H 2O=Nasio 3+2H 2 f 影响因素 1.温度 温度过高,首先就是IPA 不好控制,温度一高,IPA 的挥发很快,气泡印就会随之出现,这样就大大减少了PN 结的有效面积,反应加剧,还会出现片子的漂浮,造成碎片率的增加。可控程度:调节机器的设置,可以很好的调节温度。 2.时间金字塔随时间的变化:金字塔逐渐冒出来;表面上基本被小金字塔覆盖,少数开始成长;金字塔密布的绒面已经形成,只是大小不均匀,反射率也降到比较低的情况;金字塔向外扩张兼并,体积逐渐膨胀,尺寸趋于均等,反射率略有下降。可控程度:调节设备参数,可以精确的调节时间。 3.IPA 1.协助氢气的释放。 2.减弱NaOH 溶液对硅片的腐蚀力度,调节各向因子。纯NaOH 溶液在 高温下对原子排列比较稀疏的100 晶面和比较致密的111 晶面破坏比较大,各个晶面被腐蚀而消融,IPA 明显减弱NaOH 的腐蚀强度,增加了腐蚀的各向异性,有利于金字塔的成形。乙醇含量过高,碱溶液对硅溶液腐蚀能力变得很弱,各向异性因子又趋于1。 可控程度:根据首次配液的含量,及每次大约消耗的量,来补充一定量的液体,控制精度不高。 4.NaOH 形成金字塔绒面。NaOH 浓度越高,金字塔体积越小,反应初期,金字塔成核密度近似不受NaOH 浓度影响,碱溶液的腐蚀性随NaOH 浓度变化比较显著,浓度高的NaOH 溶液与硅反映的速度加快,再反应一段时间后,金字塔体积更大。NaOH 浓度超过一定界限时,各向异性因子变小,绒面会越来越差,类似于抛光。 可控程度:与IPA 类似,控制精度不高。 5.Na 2SiO 3 SI 和NaOH 反应生产的Na2SiO3 和加入的Na2SiO3 能起到缓冲剂的作用,使反应不至于很剧烈,变的平缓。Na 2SiO 3使反应有了更多的起点,生长出的金字塔更均匀,更小一点Na2SiO3 多的时候要及时的排掉,Na2SiO3 导热性差,会影响反应,溶液的粘稠度也增加,容易形成水纹、花蓝印和表面斑点。 可控程度:很难控制。 4#酸洗 HCL 去除硅片表面的金属杂质盐酸具有酸和络合剂的双重作用,氯离子能与多种金属离子形成可溶与水的络合物。 6#酸洗 HF 去除硅片表面氧化层,SiO2+6HF=H 2[siF6]+2H 2O。控制点 1.减薄量定义:硅片制绒前后的前后重量差。 控制范围
单晶硅太阳能电池制作工艺
. 单晶硅太阳能电池/DSSC/PERC技术 2015-10-20
单晶硅太阳能电池
2.太阳能电池片的化学清洗工艺切片要求:①切割精度高、表面平行度高、翘曲度和厚度公差小。②断面完整性好,消除拉丝、刀痕和微裂纹。③提高成品率,缩小刀(钢丝)切缝,降低原材料损耗。④提高切割速度,实现自动化切割。 具体来说太阳能硅片表面沾污大致可分为三类: 1、有机杂质沾污:可通过有机试剂的溶解作用,结合兆声波清洗技术来去除。 2、颗粒沾污:运用物理的方法可采机械擦洗或兆声波清洗技术来去除粒径≥0.4 μm颗粒,利用兆声波可去除≥0.2 μm颗粒. 3、金属离子沾污:该污染必须采用化学的方法才能将其清洗掉。硅片表面金属杂质沾污又可分为两大类:(1)、沾污离子或原子通过吸附分散附着在硅片表面。(2)、带正电的金属离子得到电子后面附着(尤如“电镀”)到硅片表面。 1、用H2O2作强氧化剂,使“电镀”附着到硅表面的金属离子氧化成金属,溶解在清洗液中或吸附在硅片表面 2、用无害的小直径强正离子(如H+),一般用HCL作为H+的来源,替代吸附在硅片表面的金属离子,使其溶解于清洗液中,从而清除金属离子。 3、用大量去离子水进行超声波清洗,以排除溶液中的金属离子。由于SC-1是H2O2和NH4OH的碱性溶液,通过H2O2的强氧化和NH4OH的溶解作用,使有机物沾污变成水溶性化合物,随去离子水的冲洗而被
排除;同时溶液具有强氧化性和络合性,能氧化Cr、Cu、Zn、Ag、Ni、Co、Ca、Fe、Mg等,使其变成高价离子,然后进一步与碱作用,生成可溶性络合物而随去离子水的冲洗而被去除。因此用SC-1液清洗抛光片既能去除有机沾污,亦能去除某些金属沾污。在使用SC-1液时结合使用兆声波来清洗可获得更好的清洗效果。另外SC-2是H2O2和HCL的酸性溶液,具有极强的氧化性和络合性,能与氧化以前的金属作用生成盐随去离子水冲洗而被去除。被氧化的金属离子与CL-作用生成的可溶性络合物亦随去离子水冲洗而被去除。 具体的制作工艺说明(1)切片:采用多线切割,将硅棒切割成正方形的硅片。(2)清洗:用常规的硅片清洗方法清洗,然后用酸(或碱)溶液将硅片表面切割损伤层除去30-50um。(3)制备绒面:用碱溶液对硅片进行各向异性腐蚀在硅片表面制备绒面。(4)磷扩散:采用涂布源(或液态源,或固态氮化磷片状源)进行扩散,制成PN+结,结深一般为0.3-0.5um。(5)周边刻蚀:扩散时在硅片周边表面形成的扩散层,会使电池上下电极短路,用掩蔽湿法腐蚀或等离子干法腐蚀去除周边扩散层。(6)去除背面PN+结。常用湿法腐蚀或磨片法除去背面PN+结。(7)制作上下电极:用真空蒸镀、化学镀镍或铝浆印刷烧结等工艺。先制作下电极,然后制作上电极。铝浆印刷是大量采用的工艺方法。(8)制作减反射膜:为了减少入反射损失,要在硅片表面上覆盖一层减反射膜。制作减反射膜的材料有MgF2 ,SiO2 ,Al2O3 ,SiO ,Si3N4 ,TiO2 ,Ta2O5等。工艺方法可用真空镀膜法、离子镀膜法,溅射法、印刷法、PECVD 法或喷涂法等。(9)烧结:将电池芯片烧结于镍或铜的底板上。(10)测试分档:按规定参数规范,测试分类。 生产电池片的工艺比较复杂,一般要经过硅片检测、表面制绒、扩散制结、
太阳能系统计算公式
太阳能系统计算公式 Xzczxc119 太阳能系统计算中需要知道的参数: 1)总负载功率:W 2)设备使用电压:V 3)每天的光照时间:H光 4)每天放电时间:H放 5)连续阴雨天数:D 6)太阳能电池板转换功率、逆变器转换功率、蓄电池转换功率:80%(默认) 7)线缆损耗:100%+20%(默认) 8)蓄电池放电预留:20%(默认) 下面开始计算: 1)设备使用总电流I=W/V 2)蓄电池容量mAh=I×H放×(D+1)÷80%【蓄电池放电预留】×120%【线缆损耗】 3)蓄电池组数量n=V/12【蓄电池电压】 4)蓄电池总容量mAh总=mAh×n 5)太阳能电池板功率WP÷18V【太阳能电池板充电电压】=(I×H放×120%【电池板 功率】)÷H光 6)太阳能电池板实际WP实际=WP×120%【线缆损耗】 7)电池板数n电池板=V/12【电池板电压】 8)电池板总功率WP总功率=WP实际×n电池板 40瓦备选方案配置 1、LVD灯,单路、40W,24V系统; 2、当地日均有效光照以4h计算; 3、每日放电时间10小时,(以晚7点-晨5点为例) 4、满足连续阴雨天5天(另加阴雨前一夜的用电,计6天)。
电流=40W÷24V =1.67 A 计算蓄电池=1.67A ×10h ×(5+1)天=1.67A ×60h=100 AH 蓄电池充、放电预留20%容量;路灯的实际电流在2A以上(加20%损耗,包括恒流源、线损等) 实际蓄电池需求=100AH 加20%预留容量、再加20%损耗100AH ÷80% ×120% =150AH 实际蓄电池为24V /150AH,需要两组12V蓄电池共计:300AH 计算电池板: 1、LVD灯40W、电流:1.67 2、每日放电时间10小时(以晚7点-晨5点为例) 3、电池板预留最少20% 4、当地有效光照以日均4h计算 WP÷17.4V =(1.67A ×10h ×120%)÷4 h WP =87W */一般太阳能电池板为18伏充电电压,这里选用了17.4/* 实际恒流源损耗、线损等综合损耗在20%左右 电池板实际需求=87W ×120%=104W 实际电池板需24V /104W,所以需要两块12V电池板共计:208W
太阳能电池板制作方法
太阳能电池板制作方法? 首先,你想亲手做这个太阳能电池板是几乎很难实现的,因为他要有很多的仪器和设备才能完成。 其次,你连什么是太阳能电池板都不知道又怎么做?你下面所说的问题全是太阳能发电系统的内容,太阳能电池板只是系统工程中的一个主要部件。 太阳能发电系统(太阳能发电装置)是主要部件有以下几种,1。太阳能电池板、蓄电池、太阳能充电控制器、逆变器。当然还有其它很多的附件。 以下就是太阳能电池板的制作方法。 太阳能电池板(组件)生产工艺 组件线又叫封装线,封装是太阳能电池生产中的关键步骤,没有良好的封装工艺,多好的电池也生产不出好的组件板。电池的封装不仅可以使电池的寿命得到保证,而且还增强了电池的抗击强度。产品的高质量和高寿命是赢得可客户满意的关键,所以组件板的封装质量非常重要。 流程: 1、电池检测—— 2、正面焊接—检验— 3、背面串接—检验— 4、敷设(玻璃清洗、材料切割、玻璃预处理、敷设)—— 5、层压—— 6、去毛边(去边、清洗)—— 7、装边框(涂胶、装角键、冲孔、装框、擦洗余胶)—— 8、焊接接线盒—— 9、高压测试——10、组件测试—外观检验—11、包装入库组件高效和高寿命如何保证: 1、高转换效率、高质量的电池片; 2、高质量的原材料,例如:高的交联度的EVA、高粘结强度的封装剂(中性硅酮树脂胶)、高透光率高强度的钢化玻璃等; 3、合理的封装工艺 4、员工严谨的工作作风; 由于太阳电池属于高科技产品,生产过程中一些细节问题,一些不起眼问题如应该戴手套而不戴、应该均匀的涂刷试剂而潦草完事等都是影响产品质量的大敌,所以除了制定合理的制作工艺外,员工的认真和严谨是非常重要的。 太阳电池组装工艺简介: 工艺简介:在这里只简单的介绍一下工艺的作用,给大家一个感性的认识. 1、电池测试:由于电池片制作条件的随机性,生产出来的电池性能不尽相同,所以为了有效的将性能一致或相近的电池组合在一起,所以应根据其性能参数进行分类;电池测试即通过测试电池的输出参数(电流和电压)的大小对其进行分类。以提高电池的利用率,做出质量合格的电池组件。 2、正面焊接:是将汇流带焊接到电池正面(负极)的主栅线上,汇流带为镀锡的铜带,我们使用的焊接机可以将焊带以多点的形式点焊在主栅线上。焊接用的热源为一个红外灯(利用红外线的热效应)。焊带的长度约为电池边长的2倍。多出的焊带在背面焊接时与后面的电池片的背面电极相连
太阳能电池片功率计算公式
太阳能电池片功率计算公式 电池片制造商在产品规格表中会给出标准测试条件下的太阳电池性能参数:一般包括有短路电流Isc;开路电压Voc;最大功率点电压Vap;最大功率点电 流Iap;最大功率Pmpp; 转换效率Eff等。标准测试条件下,最大功率Pmpp与转换效率之间有如下关系: Pmpp = 电池面积(m2)*1000(W/m2)*Eff 举例如下: 产品类型转化效率(%)功率(W) 单晶125*125 15 2.22855 单晶156*156 15 3.58425 多晶125*125 15 2.34375 多晶156*156 15 3.6504 注1:测试条件符合AM1.5太阳光谱的辐照强度1000W/m2,电池温度25℃,测试方法 符合IEC904-1,容许偏差Efficiency ±5% REL。 注2:AM1.5 AM是air mass的简称,意思是大气质量。 AM1.5是一种条件,它描述太阳光入射于地表之平均照度,其太阳总辐照度为1000W/m2;太阳电池的标定温度为25±1℃。 注3:IEC904-1 IEC:国际电工委员会,international electrotechnical commission。 IEC904等同于GB/T6495。 注4:REL:rate of energy loss 能量损耗率
太阳能电池功率 一:首先计算出电流: 如:12V蓄电池系统;30W的灯2只,共60瓦。 电流= 60W÷12V= 5 A 二:计算出蓄电池容量需求: 如:路灯每夜照明时间9.5小时,实际满负载照明为 7小时(h); 例一:1 路 LED 灯 (如晚上7:30开启100%功率,夜11:00降至50%功率,凌晨4:00后再100%功率,凌晨5:00 关闭) 例二:2 路非LED灯(低压钠灯、无极灯、节能灯、等) (如晚上7:30两路开启,夜11:00关闭1路,凌晨4:00开启2路,凌晨5:00关闭) 需要满足连续阴雨天5天的照明需求。(5天另加阴雨天前一夜的照明,计6天)蓄电池= 5A× 7h×( 5+1)天= 5A× 42h =210 AH 另外为了防止蓄电池过充和过放,蓄电池一般充电到90%左右;放电余留5%-20%左右。 所以210AH也只是应用中真正标准的70%-85%左右。另外还要根据负载的不同,测出实际的损耗,实际的工作电流受恒流源、镇流器、线损等影响,可能会在5A的基础上增加15%-25%左右。 三:计算出电池板的需求峰值(WP): 路灯每夜累计照明时间需要为 7小时(h); ★:电池板平均每天接受有效光照时间为4.5小时(h); 最少放宽对电池板需求20%的预留额。 WP÷17.4V=(5A× 7h× 120%)÷ 4.5h WP÷17.4V= 9.33 WP = 162(W) ★:4.5h每天光照时间为长江中下游附近地区日照系数。 另外在太阳能路灯组件中,线损、控制器的损耗、及镇流器或恒流源的功耗各有不同,实际应用中可能在15%-25%左右。所以162W也只是理论值,根据实际情况需要有所增加。
晶硅太阳能电池片的制作过程
晶硅太阳能电池板的制作过程 1、表面制绒单晶硅绒面的制备是利用硅的各向异性腐蚀,在每平方厘米硅表面形成几百万个四面方锥体也即金字塔结构。由于入射光在表面的多次反射和折射,增加了光的吸收,提高了电池的短路电流和转换效率。硅的各向异性腐蚀液通常用热的碱性溶液,可用的碱有氢氧化钠,氢氧化钾、氢氧化锂和乙二胺等。大多使用廉价的浓度约为1%的氢氧化钠稀溶液来制备绒面硅,腐蚀温度为 70-85℃。为了获得均匀的绒面,还应在溶液中酌量添加醇类如乙醇和异丙醇等作为络合剂,以加快硅的腐蚀。制备绒面前,硅片须先进行初步表面腐蚀,用碱性或酸性腐蚀液蚀去约20~25μm,在腐蚀绒面后,进行一般的化学清洗。经过表面准备的硅片都不宜在水中久存,以防沾污,应尽快扩散制结。 2、扩散制结太阳能电池需要一个大面积的PN结以实现光能到电能的转换,而扩散炉即为制造太阳能电池PN结的专用设备。管式扩散炉主要由石英舟的上下载部分、废气室、炉体部分和气柜部分等四大部分组成。扩散一般用三氯氧磷液态源作为扩散源。把P型硅片放在管式扩散炉的石英容器内,在850---900摄氏度高温下使用氮气将三氯氧磷带入石英容器,通过三氯氧磷和硅片进行反应,得到磷原子。经过一定时间,磷原子从四周进入硅片的表面层,并且通过硅原子之间的空隙向硅片内部渗透扩散,形成了N型半导体和P型半导体的交界面,也就是PN结。这种方法制出的PN结均匀性好,方块电阻的不均匀性小于百分之十,少子寿命可大于10ms。制造PN结是太阳电池生产最基本也是最关键的工序。因为正是PN结的形成,才使电子和空穴在流动后不再回到原处,这样就形成了电流,用导线将电流引出,就是直流电。 3、去磷硅玻璃该工艺用于太阳能电池片生产制造过程中,通过化学腐蚀法也即把硅片放在氢氟酸溶液中浸泡,使其产生化学反应生成可溶性的络和物六氟硅酸,以去除扩散制结后在硅片表面形成的一层磷硅玻璃。在扩散过程中,POCL3与O2反应生成P2O5淀积在硅片表面。P2O5与Si反应又生成SiO2和磷原子,这样就在硅片表面形成一层含有磷元素的SiO2,称之为磷硅玻璃。去磷硅玻璃的设备一般由本体、清洗槽、伺服驱动系统、机械臂、电气控制系统和自动配酸系统等部分组成,主要动力源有氢氟酸、氮气、压缩空气、纯水,热排风和废水。氢氟酸能够溶解二氧化硅是因为氢氟酸与二氧化硅反应生成易挥发的四氟化硅气体。若氢氟酸过量,反应生成的四氟化硅会进一步与氢氟酸反应生成可溶性的络和物六氟硅酸。 4、等离子刻蚀由于在扩散过程中,即使采用背靠背扩散,硅片的所有表面包括边缘都将不可避免地扩散上磷。PN结的正面所收集到的光生电子会沿着边缘扩散有磷的区域流到PN结的背面,而造成短路。因此,必须对太阳能电池周边的掺杂硅进行刻蚀,以去除电池边缘的PN结。通常采用等离子刻蚀技术完成这一工艺。等离子刻蚀是在低压状态下,反应气体CF4的母体分子在射频功率的激
太阳能电池方阵组合的计算
太阳能电池方阵组合的计算 太阳能电池方阵是根据负载需要将若干个组件通过串联和并联进行组合连接,得到规定的输出电流和电压,为负载提供电力的。方阵的输出功率与组件串并联的数量有关,串联是为了获得所需要的工作电压,并联是为了获得所需要的工作电流。 一般独立光伏系统电压往往被设计成与蓄电池的标称电压相对应或者是它的整数倍,而且与用电器的电压等级一致,如220v、110v、48v、36v、24v、12v等。交流光伏发电系统和并网光伏发电系统,方阵的电压等级往往为110v 或220v。对电压等级更高的光伏发电系统,则采用多个方阵进行串并联,组合成与电网等级相同的电压等级,如组合成600v、10kv等,再通过逆变器后与电网连接。 方阵所需要串联的组件数量主要由系统工作电压或逆变器的额定电压来确定,同时要考虑蓄电池的浮充电压、线路损耗以及温度变化等因素。一般带蓄电池的光伏发电系统方阵的输出电压为蓄电池组标称电压的1.43倍。对于不带蓄电池的光伏发电系统,在计算方阵的输出电压时一般将其额定电压提高10%,再选定组件的串联数。 例如,一个组件的最大输出功率为108w,最大工作电压为36.2v,设选用逆变器为交流三相,额定电压380v,逆变器采取三相桥式接法,则直流输出电压up=uab/0.817=380/0.817≈465v。再来考虑电压富余量,太阳能电池方阵的输出电压应增大到1.1×465=512v,则计算出组件的串联数为512v/ 36.2v≈14块。 下面再从系统输出功率来计算太阳能电池组件的总数。现假设负载要求功率是30kw,则组件总数为30000w/108w≈277块,从而计算出模块并联数为277/14≈19.8,可选取并联数为20块。结论:该系统应选择上述功率的组件14串联20并,组件总数为14×20=280块,系统输出最大功率为 280×108w≈30.2kw。 ①短路电流(Isc):当将太阳能电池的正负极短路、使U=O时,此时的电流就是 电池片的短路电流,短路电流的单位是安培(A),短路电流随着光强的变化而变化。 ②②开路电压(Uoc):当将太阳能电池的正负极不接负载、使,=0时,此时太 阳能电池正负极间的电压就是开路电压,开路电压的单位是伏特(V)。单片太阳能电池的开路电压不随电池片面积的增减而变化,一般为0.5~0.7V。 ③峰值电流(Im):峰值电流也叫最大工作电流或最佳工作电流。峰值电流是指 太阳能电池片输出最大功率时的工作电流,峰值电流的单位是安培(A)。 ④峰值电压(Um):峰值电压也叫最大工作电压或最佳工作电压。峰值电压是
多晶硅太阳能电池生产工艺.docx
太阳能电池光电转换原理主要是利用太阳光射入太阳能电池后产生电子电洞对,利用P-N 接面的电场将电子电洞对分离,利用上下电极将这些电子电洞引出,从而产生电流。整个生产流程以多晶硅切片为原料,制成多晶硅太阳能电池芯片。处理工艺主要有多晶硅切片清洗、磷扩散、氧化层去除、抗反射膜沉积、电极网印、烧结、镭射切割、测试分类包装等。 生产工艺主要分为以下过程: ⑴ 表面处理(多晶硅片清洗、制绒) 与单晶硅绒面制备采用碱液和异丙醇腐蚀工艺不同,多晶硅绒面制备采用氢氟酸和硝酸配成的腐蚀液对多晶硅体表面进行腐蚀。一定浓度的强酸液对硅表面进行晶体的各相异性腐蚀,使得硅表面成为无数个小“金字塔”组成的凹凸表面,也就是所谓的“绒面”,以增加了光的反射吸收,提高电池的短路电流和转换效率。从电镜的检测结果看,小“金字塔”的底边平均约为10um 。主要反应式为: 32234HNO 4NO +3SiO +2H O Si +???→↑氢氟酸 2262SiO 62H O HF H SiF +→+ 这个过程在硅片表面形成一层均匀的反射层(制绒),作为制备P-N 结衬底。处理后对硅片进行碱洗、酸洗、纯水洗,此过程在封闭的酸蚀刻机中进行。碱洗是为了清洗掉硅片未完全反应的表面腐蚀层,因为混酸中HF 比例不能太高,否则腐蚀速度会比较慢,其反应式为:2232SiO +2KOH K SiO +H O →。之后再经过酸洗中和表面的碱液,使表面的杂质清理干净,形成纯净的绒面多晶硅片。 酸蚀刻机内设置了一定数量的清洗槽,各股废液及废水均能单独收集。此过程中的废酸液(L 1,主要成分为废硝酸、氢氟酸和H 2SiF 6)、废碱液(L 2,主要成分为废KOH 、K 2SiO 3)、废酸液(L 3,主要成分为废氢氟酸以及盐酸)均能单独收集,酸碱洗后均由少量纯水洗涤,纯水预洗废液(S 1、S 2、S 3)和两级纯水漂洗废水(W 1),收集后排入厂区污水预处理设施,处理达标后通过专管接入清流县市政污水管网。 此过程中使用的硝酸、氢氟酸均有一定的挥发性,产生的酸性废气(G 1-1、G 1-2),经设备出气口进管道收集系统,经厂房顶的碱水喷淋系统处理达标后排放。G 1-2与后序PECVD 工序产生的G 5(硅烃、氨气)合并收集后经过两级水吸收处理后经排气筒排放。