激光深熔焊接的主要工艺参数
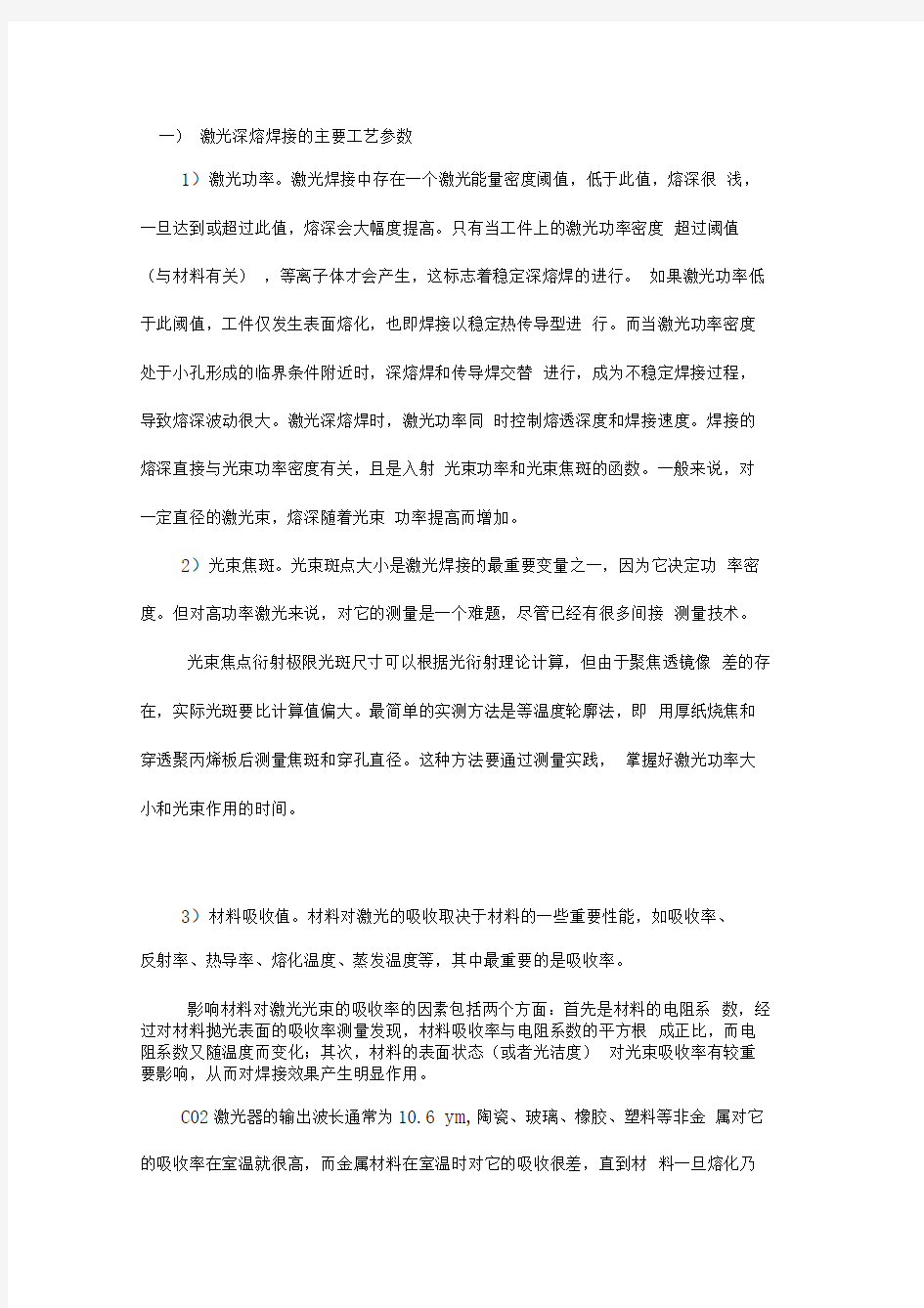

一)激光深熔焊接的主要工艺参数
1)激光功率。激光焊接中存在一个激光能量密度阈值,低于此值,熔深很浅,一旦达到或超过此值,熔深会大幅度提高。只有当工件上的激光功率密度超过阈值(与材料有关),等离子体才会产生,这标志着稳定深熔焊的进行。如果激光功率低于此阈值,工件仅发生表面熔化,也即焊接以稳定热传导型进行。而当激光功率密度处于小孔形成的临界条件附近时,深熔焊和传导焊交替进行,成为不稳定焊接过程,导致熔深波动很大。激光深熔焊时,激光功率同时控制熔透深度和焊接速度。焊接的熔深直接与光束功率密度有关,且是入射光束功率和光束焦斑的函数。一般来说,对一定直径的激光束,熔深随着光束功率提高而增加。
2)光束焦斑。光束斑点大小是激光焊接的最重要变量之一,因为它决定功率密度。但对高功率激光来说,对它的测量是一个难题,尽管已经有很多间接测量技术。
光束焦点衍射极限光斑尺寸可以根据光衍射理论计算,但由于聚焦透镜像差的存在,实际光斑要比计算值偏大。最简单的实测方法是等温度轮廓法,即用厚纸烧焦和穿透聚丙烯板后测量焦斑和穿孔直径。这种方法要通过测量实践,掌握好激光功率大小和光束作用的时间。
3)材料吸收值。材料对激光的吸收取决于材料的一些重要性能,如吸收率、
反射率、热导率、熔化温度、蒸发温度等,其中最重要的是吸收率。
影响材料对激光光束的吸收率的因素包括两个方面:首先是材料的电阻系数,经过对材料抛光表面的吸收率测量发现,材料吸收率与电阻系数的平方根成正比,而电阻系数又随温度而变化;其次,材料的表面状态(或者光洁度)对光束吸收率有较重要影响,从而对焊接效果产生明显作用。
C02激光器的输出波长通常为10.6 ym,陶瓷、玻璃、橡胶、塑料等非金属对它的吸收率在室温就很高,而金属材料在室温时对它的吸收很差,直到材料一旦熔化乃
至气化,它的吸收才急剧增加。采用表面涂层或表面生成氧化膜的方法,提高材料对光束的吸收很有效。
4)焊接速度。焊接速度对熔深影响较大,提高速度会使熔深变浅,但速度过低又会导致材料过度熔化、工件焊穿。所以,对一定激光功率和一定厚度的某特定材料有一个合适的焊接速度范围,并在其中相应速度值时可获得最大熔深。图10-2 给出了1018 钢焊接速度与熔深的关系。
5)保护气体。激光焊接过程常使用惰性气体来保护熔池,当某些材料焊接可不计较表面氧化时则也可不考虑保护,但对大多数应用场合则常使用氦、氩、氮等气体作保护,使工件在焊接过程中免受氧化。
氦气不易电离(电离能量较高),可让激光顺利通过,光束能量不受阻碍地直达工件表面。这是激光焊接时使用最有效的保护气体,但价格比较贵。
氩气比较便宜,密度较大,所以保护效果较好。但它易受高温金属等离子体电离,结果屏蔽了部分光束射向工件,减少了焊接的有效激光功率,也损害焊接速度与熔深。使用氩气保护的焊件表面要比使用氦气保护时来得光滑。
氮气作为保护气体最便宜,但对某些类型不锈钢焊接时并不适用,主要是由于冶金学方面问题,如吸收,有时会在搭接区产生气孔
使用保护气体的第二个作用是保护聚焦透镜免受金属蒸气污染和液体熔滴 的溅
射。特别在高功率激光焊接时,由于其喷出物变得非常有力,此时保护透 镜则更为必要。
保护气体的第三个作用是对驱散高功率激光焊接产生的等离子屏蔽很有效。 金属
蒸气吸收激光束电离成等离子云,金属蒸气周围的保护气体也会因受热而 电离。如果等离子体存在过多,激光束在某种程度上被等离子体消耗。等离子 体作为第二种能量存在于工作表面,使得熔深变浅、焊接熔池表面变宽。通过 增加电子与离子和中性原子三体碰撞来增加电子的复合速率,以降低等离子体 中的电子密度。中性原子越轻,碰撞频率越高,复合速率越高;另一方面,只 有电离能高的保护气体,才不致因气体本身的电离而增加电子密度。
表 常用气体和金属的原子 (分子 )量和电离能
原子(分子 )量 4 40 28 27 24 56 电离能 (eV) 24.46 15.68 14.5 5.96 7.61
7.83
从表可知,等离子体云尺寸与采用的保护气体不同而变化,氦气最小,氮 气次
之,使用氩气时最大。等离子体尺寸越大,熔深则越浅。造成这种差别的 原因首先由于气体分子的电离程度不同,另外也由于保护气体不同密度引起金 属蒸气扩散差别。
氦气电离最小,密度最小,它能很快地驱除从金属熔池产生的上升的金属 蒸气。
所以用氦作保护气体,可最大程度地抑制等离子体,从而增加熔深,提 高焊接速度;材料 氮铝 镁铁
氩
由于质轻而能逸出,不易造成气孔。当然,从我们实际焊接的效果看,用氩气保护的
效果还不错。
等离子云对熔深的影响在低焊接速度区最为明显。当焊接速度提高时,它的影响就会减弱。
保护气体是通过喷嘴口以一定的压力射出到达工件表面的,喷嘴的流体力
学形状和出口的直径大小十分重要。它必须以足够大以驱使喷出的保护气体覆
盖焊接表面,但为了有效保护透镜,阻止金属蒸气污染或金属飞溅损伤透镜,
喷口大小也要加以限制。流量也要加以控制,否则保护气的层流变成紊流,大气卷入熔池,最终形成气孔。
为了提高保护效果,还可用附加的侧向吹气的方式,即通过一较小直径的
喷管将保护气体以一定的角度直接射入深熔焊接的小孔。保护气体不仅抑制了
工件表面的等离子体云,而且对孔内的等离子体及小孔的形成施加影响,熔深
进一步增大,获得深宽比较为理想的焊缝。但是,此种方法要求精确控制气流量大小、方向,否则容易产生紊流而破坏熔池,导致焊接过程难以稳定。
6)透镜焦距。焊接时通常采用聚焦方式会聚激光,一般选用
63~254mm(2.5” ~10”焦距的透镜。聚焦光斑大小与焦距成正比,焦距越短,光
斑越小。但焦距长短也影响焦深,即焦深随着焦距同步增加,所以短焦距可提高功率
密度,但因焦深小,必须精确保持透镜与工件的间距,且熔深也不大。
由于受焊接过程中产生的飞溅物和激光模式的影响,实际焊接使用的最短焦深多为焦距126mm(5 )。当接缝较大或需要通过加大光斑尺寸来增加焊缝时,可选择254mm (10 )焦距的透镜,在此情况下,为了达到深熔小孔效应,需要更高的激光输出功率(功率密度)。
当激光功率超过2kW时,特别是对于10.6 ym的C02激光束,由于采用
特殊光学材料构成光学系统,为了避免聚焦透镜遭光学破坏的危险,经常选用反射聚
焦方法,一般采用抛光铜镜作反射镜。由于能有效冷却,它常被推荐用于高功率激光束聚焦。
7)焦点位置。焊接时,为了保持足够功率密度,焦点位置至关重要。焦点与工件表面相对位置的变化直接影响焊缝宽度与深度。图2-6 表示焦点位置对1018 钢熔深及缝宽的影响。
在大多数激光焊接应用场合,通常将焦点的位置设置在工件表面之下大约所需熔深的1/4 处。
8)激光束位置。对不同的材料进行激光焊接时,激光束位置控制着焊缝的最终质量,特别是对接接头的情况比搭接结头的情况对此更为敏感。例如,当淬火钢齿轮焊接到低碳钢鼓轮,正确控制激光束位置将有利于产生主要有低碳组分组成的焊缝,这种焊缝具有较好的抗裂性。有些应用场合,被焊接工件的几何形状需要激光束偏转一个角度,当光束轴线与接头平面间偏转角度在100 度以内时,工件对激光能量的吸收不会受到影响。
9)焊接起始、终止点的激光功率渐升、渐降控制。激光深熔焊接时,不管
焊缝深浅,小孔现象始终存在。当焊接过程终止、关闭功率开关时,焊缝尾端
将出现凹坑。另外,当激光焊层覆盖原先焊缝时,会出现对激光束过度吸收,导致焊件过热或产生气孔。
为了防止上述现象发生,可对功率起止点编制程序,使功率起始和终止时间变成可调,即起始功率用电子学方法在一个短时间内从零升至设置功率值,并调节焊接时间,最后在焊接终止时使功率由设置功率逐渐降至零值。
1. 激光深熔焊特征及优、缺点
(一)激光深熔焊的特征
激光熔覆技术介绍
激光熔覆是一种新型的涂层技术,是涉及到光、机、电、材料、检测与控制等多学科的高新技术,是激光先进制造技术最重要的支撑技术,可以解决传统制造方法不能完成的难题,是国家重点支持和推动的一项高新技术。目前,激光熔覆技术已成为新材料制备、金属零部件快速直接制造、失效金属零部件绿色再制造的重要手段之一,已广泛应用于航空、石油、汽车、机械制造、船舶制造、模具制造等行业。 为推动激光熔覆技术的产业化,世界各国的研究人员针对激光熔覆涉及到的关键技术进行了系统的研究,已取得了重大的进展。国内外有大量的研究和会议论文、专利介绍激光熔覆技术及其最新的应用:包括激光熔覆设备、材料、工艺、监测与控制、质量检测、过程的模拟与仿真等研究内容。但到目前为止,激光熔覆技术还不能大面积工业化应用。分析其原因,这里有政府导向的因素、激光熔覆技术本身成熟程度的限制、社会各界对激光熔覆技术的认可程度等因素。因此,激光熔覆技术欲实现全面的工业化应用,必须加大宣传力度,以市场需求为导向,重点突破制约发展的关键因素,解决工程应用中涉及到的关键技术,相信在不远的将来,激光熔覆技术的应用领域及其强度将不断的扩大。下面介绍激光熔覆技术几个发展的动态,以飨读者。 激光熔覆的优势 激光束的聚焦功率密度可达1010~12W/cm2,作用于材料能获得高达1012K/s的冷却速度,这种综合特性不仅为材料科学新学科的生长提供了强有力的基础,同时也为新型材料或新型功能表面的实现提供了一种前所未有的工具。激光熔覆所创造的熔体在高温度梯度下远离平衡态的快速冷却条件,使凝固组织中形成大量过饱和固溶体、介稳相甚至新相,已经被大量研究所证实。它提供了制造功能梯度原位自生颗粒增强复合层全新的热力学和动力学条件。同时激光熔覆技术制备新材料是极端条件下失效零部件的修复与再制造、金属零部件的直接制造的重要基础,受到世界各国科学界和企业的高度重视和多方面的研究。 目前,利用激光熔覆技术可以制备铁基、镍基、钴基、铝基、钛基、镁基等金属基复合材料。从功能上分类:可以制备单一或同时兼备多种功能的涂层如:耐磨损、耐腐蚀、耐高温等以及特殊的功能性涂层。从构成涂层的材料体系看,从二元合金体系发展到多元体系。多元体系的合金成分设计以及多功能性是今后激光熔覆制备新材料的重要发展方向。 最新的研究表明,在我国工程应用中钢铁基的金属材料占主导地位。同时,
激光焊接的工作原理及其主要工艺参数(精)
激光焊接的工作原理及其主要工艺参数 目前常用的焊接工艺有电弧焊、电阻焊、钎焊、电子束焊等。电弧焊是目前应用最广泛的焊接方法,它包括手弧焊、埋弧焊、钨极气体保护电弧焊、等离子弧焊、熔化极气体保护焊等。但上述各种焊接方法都有各自的缺点,比如空间限制,对于精细器件不易操作等,而激光焊接不但不具有上述缺点,而且能进行精确的能量控制,可以实现精密微型器件的焊接。并且它能应用于很多金属,特别是能解决一些难焊金属及异种金属的焊接。 激光指在能量相应与两个能级能量差的光子作用下,诱导高能态的原子向低能态跃迁,并同时发射出相同能量的光子。激光具有方向性好、相干性好、单色性好、光脉冲窄等优点。激光焊接是利用大功率相干单色光子流聚焦而成的激光束为热源进行的焊接,这种焊接通常有连续功率激光焊和脉冲功率激光焊。激光焊接从上世纪60年代激光器诞生不久就开始了研究,从开始的薄小零器件的焊接到目前大功率激光焊接在工业生产中的大量的应用,经历了近半个世纪的发展。由于激光焊接具有能量密度高、变形小、热影响区窄、焊接速度高、易实现自动控制、无后续加工的优点,近年来正成为金属材料加工与制造的重要手段,越来越广泛地应用在汽车、航空航天、造船等领域。虽然与传统的焊接方法相比,激光焊接尚存在设备昂贵、一次性投资大、技术要求高的问题,但激光焊接生产效率高和易实现自动控制的特点使其非常适于大规模生产线。 2. 激光焊接原理 2.1激光产生的基本原理和方法 光与物质的相互作用,实质上是组成物质的微观粒子吸收或辐射光子。微观粒子都具有一套特定的能级,任一时刻粒子只能处在与某一能级相对应的状态,物质与光子相互作用时,粒子从一个能级跃迁到另一个能级,并相应地吸收或辐射光子。光子的能量值为此两能级的能量差△E,频率为ν=△E/h。爱因斯坦认为光和原子的相互作用过程包含原子的自发辐射跃迁、受激辐射跃迁和受激吸收跃迁三种过程。我们考虑原子的两个能级E1和E2,处于两个能级的原子数密度分别为N1和N2。构成黑体物质原子中的辐射场能量密度为ρ,并有E2 -E1=hν。 2.1.自发辐射 处于激发态的原子如果存在可以接纳粒子的较低能级,即使没有外界作用,粒子也有一定的概率自发地从高能级激发态(E2)向低能级基态(E1)跃迁,同时辐射出能量为(E2-E1)的光子,光子频率ν=(E2-E1)/h。这种辐射过程称为自发辐射。自发辐射发出的光,不具有相位、偏振态上的一致,是非相干光。 2.2.受激辐射 除自发辐射外,处于高能级E2上的粒子还可以另一方式跃迁到较低能级。当频率为ν=(E2-E1)/h的光子入射时,也会引发粒子以一定的概率,迅速地从能级E2跃迁到能级E1,同时辐射一个与外来光子频率、相位、偏振态以及传播方向都相同的光子,这个过程称为受激辐射。 2.3.受激吸收 受激辐射的反过程就是受激吸收。处于低能级E1的一个原子,在频率为的辐射场作用下吸收一个能量为hν的光子,并跃迁至高能级E2,这种过程称为受激吸收。自发辐射是不相干的,受激辐射是相干的。 由受激辐射和自发辐射的相干性可知,相干辐射的光子简并度很大。普通光源在红外和可见光波段实际上是非相干光源。如果能够创造这样一种情况:使得腔内某一特定模式的ρ很大,而其他所有模式的都很小,就能够在这一特定模式内形成很高的光子简并度,使相干
焊接工艺参数
手工电弧焊的焊接工艺参数选择 选择合适的焊接工艺参数,对提高焊接质量和提高生产效率是十分重要. 焊接工艺参数(焊接规范)是指焊接时,为保证焊接质量而选定的诸多物理量. 1、焊接电源种类和极性的选择 焊接电源种类:交流、直流 极性选择:正接、反接 正接:焊件接电源正极,焊条接电源负极的接线方法。 反接:焊件接电源负极,焊条接电源正极的接线方法。 极性选择原则:碱性焊条常采用直流反接,否则,电弧燃烧不稳定, 飞溅严重,噪声大,酸性焊条使用直流电源时通常采用直流正接。 2、焊条直径 可根据焊件厚度进行选择。一般厚度越大,选用的焊条直径越粗,焊条直径与焊件的关系见下表: 焊件厚度(mm) 2 3 4-5 6-12 >13 焊条直径(mm) 2 3.2 3.2-4 4-5 4-6 3、焊接电流的选择 选择焊接电流时,要考虑的因素很多,如:焊条直径、药皮类型、工件厚度、接头类型、焊接位置、焊道层次等。但主要由焊条直径、焊接位置、焊道层次来决定。 (1)焊条直径焊条直径越粗,焊接电流越大。下表供参考 焊条直径(mm) 1.6 2.0 2.5 3.2 4.0 5.0 6.0 焊接电流(A)
25-45 40-65 50-80 100-130 160-210 260-270 260-300 (2)焊接位置平焊位置时,可选择偏大一些焊接电流。横、立、仰焊位置时,焊接电流应比平焊位置小10~20%。角焊电流比平焊电流稍大一些。 (3)焊道层次 打底及单面焊双面成型,使用的电流要小一些。 碱性焊条选用的焊接电流比酸性焊条小10%左右。不锈钢焊条比碳钢焊条选用的焊接电流小左右等。 总之,电流过大过小都易产生焊接缺陷。电流过大时,焊条易发红,使药皮变质,而且易造成咬边、弧坑等到缺陷,同时还会使焊缝过热,促使晶粒粗大。 (4)电弧电压 电弧电压主要决定于弧长。电弧长,则电弧电压高;反之,则低。 在焊接过程中,一般希望弧长始终保持一致,而且尽可能用短弧焊接。所谓短弧是指弧长焊条直径的0.5~1.0倍,超过这个限度即为长弧。 (5)焊接速度 在保证焊缝所要求尺寸和质量的前提下,由操作者灵活掌握。速度过慢,热影响区加宽,晶粒粗大,变形也大;速度过快,易造成未焊透,未熔合,焊缝成型不良好等缺陷。 (6)速度以及电压与焊工的运条习惯有关不用强制要求,但是根据经验公式,可知当电流小于600A时,电压取20+0.04I。当电流大于600A时电压取44V。 参考资料:https://www.360docs.net/doc/1610718776.html,/jl 16 回答者: trilsen 焊接工艺参数的选择 手工电弧焊的焊接工艺参数主要有焊条直径、焊接电流、电弧电压、焊接层数、电源种类及极性等。 1.焊条直径 焊条直径的选择主要取决于焊件厚度、接头形式、焊缝位置和焊接层次等因素。在一般情况下,可根据表6-4按焊件厚度选择焊条直径,并倾向于选择较大直径的焊条。另外,在平焊时,直径可大一些;立焊时,所用焊条直径不超过5mm;横焊和仰焊时,所用直径不超过4mm;开坡口多层焊接时,为了防止产生未焊透的缺陷,第一层焊缝宜采用直径为3.2mm 的焊条。
透明塑料的激光焊接
透明塑料的激光焊接 在许多工业应用中,热塑性元件的激光焊接已经成为一项标准的加工方式。当使用二极管激光器、Nd:YAG激光器或光纤激光器时,标准的操作是在重合处进行投射式激光焊接。聚焦激光辐射穿透上层透明的塑料,被下层材料吸收,吸收的辐射能在表面转化成热能,由于热能的传导,就在上层形成接点。 原色或者有色的塑料在近红外波段的吸收较低。炭黑是一种树脂添加剂,它可以在很广的波段(从可见到红外)有效提高塑料对激光的吸收率。然而,如果使用了炭黑,塑料就只能做成深色,无法做成透明的塑料元件。 由英国剑桥焊接研究所(TWI)开发的Clearweld工艺使得透明或者有色塑料能够有效地吸收近红外光。它采用了特殊的近红外吸收材料作为元件表面的涂层,或者作为添加剂掺入下层的树脂中。这些材料在可见光范围内的吸收较小,在近红外区(800~1100 nm)的吸收较大。目前,在最大的吸收波长附近,具有各种不同的窄吸收带宽的吸收材料,它们可以被用来调整塑料的光学特性,以便适应各种常见的近红外激光器。除了取决于所使用的激光波长,最佳的吸收材料还取决于具体应用上的要求,比如加工参数、材料特性和目标元件所需的颜色。 Clearweld涂层工艺 带有吸收范围在940~1100 nm吸收剂的涂层为低粘性、基于溶剂的液体物质,被应用于各种配料系统中。典型的溶剂是乙醇和丙酮。涂层的用量以纳升/平方毫米(nL/mm2)为单位。溶剂可作为载体,挥发得很快,从而在塑料表面形成一层吸收材料薄膜。通常,干燥时间在1至7秒。也可以使用辅助干燥的方法,例如使用红外线灯对零件的预加热或者后加热,令溶剂的挥发更为迅速。涂层过程可以与焊接过程分开进行。 当涂层应用到材料表面时,一个均匀的吸收剂薄层就沉积在材料的表面。在激光辐射以前,干燥后的涂层在可见波段有些许颜色。进行焊接时,激光辐射被涂层吸收,同时被转化成热能。由于热传导,临近于涂层的表面材料被加热而熔化,固化后就形成了焊点。在加热的过程中,吸收剂分解,涂层就完全失去了可见波段的颜色(见图1)。 添加剂
手工电弧焊的工艺参数
手工电弧焊的工艺参数 2006-12-15 15:56 选择合适的焊接工艺参数,对提高焊接质量和提高生产效率是十分重要. 焊接工艺参数(焊接规范)是指焊接时,为保证焊接质量而选定的诸多物理量. 1、焊接电源种类和极性的选择 焊接电源种类:交流、直流 极性选择:正接、反接 正接:焊件接电源正极,焊条接电源负极的接线方法。 反接:焊件接电源负极,焊条接电源正极的接线方法。 极性选择原则:碱性焊条常采用直流反接,否则,电弧燃烧不稳定, 飞溅严重,噪声大,酸性焊条使用直流电源时通常采用直流正接。 2、焊条直径 可根据焊件厚度进行选择。一般厚度越大,选用的焊条直径越粗,焊条直径与焊件的关系见下表:焊件厚度(mm)234-56-12>13 焊条直径(mm)2 3.2 3.2-44-5 4-6 3、焊接电流的选择 选择焊接电流时,要考虑的因素很多,如:焊条直径、药皮类型、工件厚度、接头类型、焊接位置、焊道层次等。但主要由焊条直径、焊接位置、焊道层次来决定。 (1)焊条直径焊条直径越粗,焊接电流越大。下表供参考 焊条直径(mm) 1.6 2.0 2.5 3.2 4.0 5.0 6.0焊接电流(a)25-4540-6550-80100-130160-210260-270260-300 (2)焊接位置平焊位置时,可选择偏大一些焊接电流。横、立、仰焊位置时,焊接电流应比平焊位置小10~20%。角焊电流比平焊电流稍大一些。 (3)焊道层次 打底及单面焊双面成型,使用的电流要小一些。 碱性焊条选用的焊接电流比酸性焊条小10%左右。不锈钢焊条比碳钢焊条选用的焊接电流小%20左右等。总之,电流过大过小都易产生焊接缺陷。电流过大时,焊条易发红,使药皮变质,而且易造成咬边、弧坑等到缺陷,同时还会使焊缝过热,促使晶粒粗大。 (4)电弧电压 电弧电压主要决定于弧长。电弧长,则电弧电压高;反之,则低。 在焊接过程中,一般希望弧长始终保持一致,而且尽可能用短弧焊接。所谓短弧是指弧长焊条直径的 0.5~1.0倍,超过这个限度即为长弧。 (5)焊接速度 在保证焊缝所要求尺寸和质量的前提下,由操作者灵活掌握。速度过慢,热影响区加宽,晶粒粗大,变形也大;速度过快,易造成未焊透,未熔合,焊缝成型不良好等缺陷。
激光复合焊应用说明
激光复合焊应用说明 大族激光科技产业集团股份有限公司 https://www.360docs.net/doc/1610718776.html,
目录 1激光电弧复合焊设备说明 (3) 2激光电弧复合焊原理 (3) 3操作说明 (4) 4基本焊接工艺说明 (5)
1激光电弧复合焊设备说明 激光电弧复合焊设备主要由以下部分组成,包括:激光器、弧焊机及送丝机、机器人(机床)及控制器、复合焊接头等,如下图所示。弧焊机和激光器与机器人(机床)控制器相连形成一个整体。 2激光电弧复合焊原理 在激光电弧复合焊接过程中,焊丝、激光束、母材及焊接方向之间的关系如下图所示: 激光电弧复合焊原理图 在上图中,d1为焦点与工件的距离;d2为焊丝与激光光斑中心的距离(光丝距离),为保证焊接质量,需调整上述两参数;d3为电极与母材表面之间的距离,决定了焊丝的干伸长度。 d1值的大小决定了激光照射在母材表面光斑的大小,影响焊接的深度,同时与激光焊接时表面成型及飞渐情况有关。 d2距离的大小决定了电弧熔池与激光熔池两者之间的关系,为了得到最佳
的焊接效率及表面成形,特别是在进行全透焊接时,控制d2的大小很重要。 d3距离过大一方面会使送丝变得不稳定,另一方面会使电弧过长,易产生电弧摆动,出现烧边现象,使得焊接过程不稳定;过小则焊接电弧太短,易形成短路。一般控制d3约15mm,在焊接过程中所通过焊接电源的弧长修正进行微调,从而保证焊接的稳定性。 焊接方向为前送丝,即电弧在前,激光在后(铝合金焊接相反),焊接方向与焊缝成型及间隙适应性有关,同时前送丝可减少焊接烟尘对未焊接头的污染(吹气方向决定)。 送丝角度约45度,角度对弧焊的深度有一定的影响,相对小角度而言,大角度可获得较大的熔深。 在进行确定材料的焊接时,首先需确定激光焊接深度的参数及电弧稳定焊接的参数,特别是电弧焊接的参数,因为电弧稳定与否直接影响焊缝的外观。根据不同的工艺需求,还需确定激光与电弧熔池之间的位置关系,即d2的大小。d2确定的是激光与电弧之间相互作用的效果,如下图所示: d2约为2mm时(图C),激光与电弧相互作用的效果最为明显,即电弧对母材的加热更有利于激光的吸收,同时电弧对激光等离子云起到一定的抑制效果,可增加激光的熔深,而激光对电弧又可起到一定的引导作用,使电弧更加稳定。所以激光与电弧不是简单的叠加,而是相互作用,合适的距离可使激光与电弧的作用最为明显,从而获得最大的熔深。 3操作说明 本司采用的弧焊机为福尼斯TPS系列焊机,与自熔焊接相比,复合焊操作主要是增加了弧焊机、送丝机、复合焊接头的操作。 弧焊机的操作详见《RCU5000i操作说明》。 送丝机的操作详见《送丝机操作说明》。 复合焊接头由激光焊接头和弧焊枪组合而成,见下图:
激光焊接的工作原理及其主要工艺参数
激光焊接的工作原理及其主要工艺参数摘要:焊接技术主要应用在金属母材热加工上,常用的有电弧焊,电阻焊,钎焊, 电子束焊,激光焊等多种,本文详细介绍了激光焊接的工作原理与工艺参数,还讨论了激光焊接技术在现代工业中的应用,并与其他焊接方法进行对比。研究表明激光焊接技术将逐步得到广泛应用。 关键词:焊接技术;激光焊接;工作原理;工艺参数。 1. 引言 目前常用的焊接工艺有电弧焊、电阻焊、钎焊、电子束焊等。电弧焊是目前应用最广泛的焊接方法,它包括手弧焊、埋弧焊、钨极气体保护电弧焊、等离子弧焊、熔化极气体保护焊等。但上述各种焊接方法都有各自的缺点,比如空间限制,对于精细器件不易操作等,而激光焊接不但不具有上述缺点,而且能进行精确的能量控制,可以实现精密微型器件的焊接。并且它能应用于很多金属,特别是能解决一些难焊金属及异种金属的焊接。 激光指在能量相应与两个能级能量差的光子作用下,诱导高能态的原子向低能态跃迁,并同时发射出相同能量的光子。激光具有方向性好、相干性好、单色性好、光脉冲窄等优点。激光焊接是利用大功率相干单色光子流聚焦而成的激光束为热源进行的焊接,这种焊接通常有连续功率激光焊和脉冲功率激光焊。激光焊接从上世纪60年代激光器诞生不久就开始了研究,从开始的薄小零器件的焊接到目前大功率激光焊接在工业生产中的大量的应用,经历了近半个世纪的发展。由于激光焊接具有能量密度高、变形小、热影响区窄、焊接速度高、易实现自动控制、无后续加工的优点,近年来正成为金属材料加工与制造的重要手段,越来越广泛地应用在汽车、航空航天、造船等领域。虽然与传统的焊接方法相比,激光焊接尚存在设备昂贵、一次性投资大、技术要求高的问题,但激光焊接生产效率高和易实现自动控制的特点使其非常适于大规模生产线。 2. 激光焊接原理 2.1激光产生的基本原理和方法 光与物质的相互作用,实质上是组成物质的微观粒子吸收或辐射光子。微观粒子都具有一套特定的能级,任一时刻粒子只能处在与某一能级相对应的状态,物质与光子相互作用时,粒子从一个能级跃迁到另一个能级,并相应地吸收或辐射光子。光子的能量值为此两能级的能量差△E,频率为ν=△E/h。爱因斯坦认为光和原子的相互作用过程包含原子的自发辐射跃迁、受激辐射跃迁和受激吸收跃迁三种过程。我们考虑原子的两个能级E1和E2,处于两个能级的原子数密度分别为N1和N2。构成黑体物质原子中的辐射场能量密度为ρ,并有E2 -E1=hν。 2.1.自发辐射 处于激发态的原子如果存在可以接纳粒子的较低能级,即使没有外界作用,粒子也有一定的概率自发地从高能级激发态(E2)向低能级基态(E1)跃迁,同时辐射出能量为(E2-E1)的光子,光子频率ν=(E2-E1)/h。这种辐射过程称为自发辐射。自发辐射发出的光,不具有相位、偏振态上的一致,是非相干光。 2.2.受激辐射 除自发辐射外,处于高能级E2上的粒子还可以另一方式跃迁到较低能级。当频率为ν=(E2-E1)/h的光子入射时,也会引发粒子以一定的概率,迅速地从能级E2跃迁到能级E1,同时辐射一个与外来光子频率、相位、偏振态以及传播方向都相同的光子,
焊接工艺参数
焊接工艺参数 集团标准化小组:[VVOPPT-JOPP28-JPPTL98-LOPPNN]
焊接工艺指导书 电弧焊工艺 1 接口 焊条电弧焊的接头主要有对接接头、T形接头、角接接头和搭接接头四种。 1.1 对接接头 对接接头是最常见的一种接头形式,按照坡口形式的不同,可分为I形对接接头(不开坡口)、V形坡口接头、U形坡口接头、X形坡口接头和双U形坡口接头等。一般厚度在6mm以下,采用不开坡口而留一定间隙的双面焊;中等厚度及大厚度构件的对接焊,为了保证焊透,必须开坡口。V形坡口便于加工,但焊后构件容易发生变形;X形坡口由于焊缝截面对称,焊后工件的变形及内应力比V形坡口小,在相同板厚条件下,X形坡口比V形坡口要减少1/2填充金属量。U形及双U形坡口,焊缝填充金属量更少,焊后变形也很小,但这种坡口加工困难,一般用于重要结构。 1.2 T形接头 根据焊件厚度和承载情况,T形接头可分为不开坡口,单边V形坡口和K形坡口等几种形式。T形接头焊缝大多数情况只能承受较小剪切应力或仅作为非承载焊缝,因此厚度在30mm以下可以不开坡口。对于要求载荷的T形接头,为了保证焊透,应根据工件厚度、接头强度及焊后变形的要求来确定所开坡口形式。 1.3 角接接头 根据坡口形式不同,角接接头分为不开坡口、V形坡口、K形坡口及卷边等几种形式。通常厚度在2mm以下角接接头,可采用卷边型式;厚度在2~8mm以下角接接头,往往不开坡口;大厚度而又必须焊透的角接接头及重要构件角接头,则应开坡口,坡口形式同样要根据工件厚度、结构形式及承载情况而定。 1.4 搭接接头 搭接接头对装配要求不高,也易于装配,但接头承载能力低,一般用在不重要的结构中。搭接接头分为不开坡口搭接和塞焊两种型式。不开坡口搭接一般用于厚度在12mm 以下的钢板,搭接部分长度为3~5δ(δ为板厚) 2 焊条电弧焊工艺参数选择 2.1 焊条直径 焊条直径可根据焊件厚度、接头型式、焊缝位置、焊道层次等因素进行选择。焊件厚度越大,可选用的焊条直径越大;T形接头比对接接头的焊条直径大,而立焊、仰焊及横焊比平焊时所选用焊条直径应小些,一般立焊焊条最大直径不超过5mm,横焊、仰焊不超过4mm;多层焊的第一层焊缝选用细焊条。焊条直径与厚度的关系见表4 2.2 焊接电流是焊条电弧焊中最重要的一个工艺参数,它的大小直接影响焊接质量及焊缝成形。当焊接电流过大时,焊缝厚度和余高增加,焊缝宽度减少,且有可能造成咬边、烧穿等缺陷;当焊接电流过小时,焊缝窄而高,熔池浅,熔合不良,会产生未焊透、夹渣等缺陷。选择焊接电流大小时,要考虑焊条类型、焊条直径、焊件厚度以及接头型式、
激光焊接方式的分类
激光焊接方式的分类 激光焊接工艺方法不同可进行如下分类: 1、片与片间的焊接。 包括对焊、端焊、中心穿透熔化焊、中心穿孔熔化焊等4种工艺方法。 对焊要求对缝质量较高,一般采用自动化焊接或手动焊接。 参考机型: →激光通用焊接机(氙灯泵浦Nd:YAG激光器):AHL-W200、AHL-W400 →光纤传输激光焊接机:AHL-FW200、AHL-FW400 2、丝与丝的焊接。 包括丝与丝对焊、交叉焊、平行搭接焊、T型焊等4种工艺方法。 对这种焊接一般不适合自动焊接,采用手动焊接或半自动焊接。 参考机型: →激光通用焊接机(氙灯泵浦Nd:YAG激光器):AHL-W200、AHL-W400 →光纤传输激光焊接机:AHL-FW200、AHL-FW400 →激光点焊机(氙灯泵浦Nd:YAG激光器):AHL-W75、AHL-W90 →激光模具烧焊机(氙灯泵浦Nd:YAG激光器):AHL-W120II、AHL-W180III、AHL-W180IV 3、金属丝与块状元件的焊接。采用激光焊接可以成功的实现金属丝与块状元件的连接,块状元件的尺寸可以任意。在焊接中应注意丝状元件的几何尺寸。 参考机型: →激光点焊机(氙灯泵浦Nd:YAG激光器):AHL-W75、AHL-W90 →激光模具烧焊机(氙灯泵浦Nd:YAG激光器):AHL-W120II、AHL-W180III、AHL-W180IV 4、不同块的组焊及密封焊。在组件物体上缝上进行密封焊接及组焊,如传感器等 参考机型: →激光通用焊接机(氙灯泵浦Nd:YAG激光器):AHL-W200、AHL-W400 →光纤传输激光焊接机:AHL-FW200、AHL-FW400 →激光模具烧焊机(氙灯泵浦Nd:YAG激光器):AHL-W180III、AHL-W180IV 5、块状物件补焊。采用激光将激光焊丝熔化沉积到基材上。一般适合模具等产品修补。参考机型: →激光模具烧焊机(氙灯泵浦Nd:YAG激光器):AHL-W180III、AHL-W180IV →激光点焊机(氙灯泵浦Nd:YAG激光器):AHL-W75、AHL-W90 激光焊接的工艺参数。 1、功率密度。功率密度是激光加工中最关键的参数之一。采用较高的功率密度,在微秒时间范围内,表层即可加热至沸点,产生大量汽化。因此,高功率密度对于材料去除加工,如打孔、切割、雕刻有利。对于较低功率密度,表层温度达到沸点需要经历数毫秒,在表层汽化前,底层达到熔点,易形成良好的熔融焊接。因此,在传导型激光焊接中,功率密度在范围在104~106W/CM2。 2、激光脉冲波形。激光脉冲波形在激光焊接中是一个重要问题,尤其对于薄片焊接更为重要。当高强度激光束射至材料表面,金属表面将会有60~98%的激光能量反射而损失掉,且反射率随表面温度变化。在一个激光脉冲作用期间内,金属反射率的变化很大。 3、激光脉冲宽度。脉宽是脉冲激光焊接的重要参数之一,它既是区别于材料去除和材料熔化的重要参数,也是决定加工设备造价及体积的关键参数。 4、离焦量对焊接质量的影响。激光焊接通常需要一定的离做文章一,因为激光焦点处光斑中心的功率密度过高,容易蒸发成孔。离开激光焦点的各平面上,功率密度分布相对均匀。 离焦方式有两种:正离焦与负离焦。焦平面位于工件上方为正离焦,反之为负离焦。按几何光学理论,当正负离焦平面与焊接平面距离相等时,所对应平面上功率密度近似相同,但实际上所获得的熔池形状不同。负离焦时,可获得更
激光熔覆
第五章 激光延寿技术 5.1激光熔覆表面处理技术 2、熔覆层的气孔和裂纹问题 熔覆层中的气孔是常见的缺陷。空气和保护气中的水分以及涂层(或粉)中吸附的水分是产生气孔的主要原因。在激光加热时,金属表面的预涂层中的水将逐步分解。分解出的水分和空气及保护气中的水分可以在激光作用的高温区直接分解产生H 。 同时,涂层中的碳粉也会和金属氧化物发生氧化还原反应产生二氧化碳。 这些H 溶入过热的激光熔覆的熔池中,随后在熔池的冷却结晶过程中析出而形成气泡,这些气泡如不能上浮逸出则成为焊接气孔。由于激光熔覆速度高,熔池的体积又很小,因此熔池的冷却结晶速度极快,不利于气泡的上浮逸出。 从冶金原理知道,对于一般熔覆火花,为防止产生气孔,可以从两方向着手:第一,限制氢溶入焊接熔池,或者减少氢的来源,或者减少氢与熔池的作用时间。第二,尽量促使氢从熔池析出,即在熔池凝固之前使氢以气泡形式及时排出。可以采取的办法:减少氢的来源即是彻底清除涂层中的水分,并加强对熔池的保护;减少熔池吸氢时间也就是减少熔池的存在时间,其中焊接速度是主要参数;对表面进行激光重熔处理。产生裂纹的原因为工艺原因、显微组织因素和残余应力。可以采取合适的办法降低裂纹的发生。如选择合适的熔覆材料,使熔覆层内的残余应力降低;优化激光熔覆技术的工艺方法和参数;合理设计熔覆层等。图2(a ,b )是应用不同的掺杂和工艺参数获得熔覆层的裂纹检测。图2掺杂5%,10%合金。 HO H O H +→)(2汽2 CO M C O M y x +→+
图2 掺杂5%,10%合金粉末在不同功率下熔覆层裂纹检测 3、激光熔覆工艺参数与优化 脉冲激光可调参数较多,包括单脉冲能量、脉冲宽度、脉冲频率、光斑尺寸、光斑重叠率及激光扫描速度等,这些参数并不是孤立存在的,它们之间的关系以及对溶覆涂层质量的影响较复杂,因此在选择激光工艺参数时需综合考虑各参量,以获得满意的处理效果。 1.1激光工艺参数对熔覆层尺寸的影响 对工件表面进行激光溶覆处理后,表面粗糙度通常较大,因此在实际使用之前,往往需对工件表面进行磨抛处理,这就需要表面培覆层有一定的加工余量,以确保激光擦覆层在磨抛后仍有一定的强化深度。脉冲激光培覆工艺参数中对溶覆层尺寸影响最大的是单脉冲能量、脉冲频率和激光扫描速度,因此应该对这几个工艺参数与强化层尺寸之间的关系进行研究,例如采用粉体材料是50%镍+50%纳米Al 2O 3,采用单道熔覆。 1.2激光工艺参数对溶覆层表面质量的影响 脉冲激光作用下的熔覆层是由多个脉冲重叠而成,因此与连续激光熔覆相比,培覆层表面的粗链度较高,这就导致培覆后需磨抛去除的厚度较大。在激光溶覆过程中,应尽量减少磨抛去除厚度,增加表面光洁度。脉冲激光的工艺参数较多,而影响表面光洁度的主要参数是激光扫描速度和脉冲频率。 脉冲频率与激光扫描)%(560)(323C O B WO Ni a +++) %(1060)(323C O B WO Ni b +++
激光焊接的工艺参数及特性分析讲解
激光焊接的工艺参数及特性分析 一、激光焊接的工艺参数:1、功率密度。功率密度是激光加工中最关键的参数之一。采用较高的功率密度,在微秒时间范围内,表层即可加热至沸点,产生大量汽化。因此,高功率密度对于材料去除加工,如打孔、切割、雕刻有利。对于较低功率密度,表层温度达到沸点需要经历数毫秒,在表层汽化前,底层达到熔点,易形成良好的熔融焊接。因此,在传导型激光焊接中,功率密度在范围在104~106W/cm2。2、激光脉冲波形。激光脉冲波形在激光焊接 一、激光焊接的工艺参数: 1、功率密度。功率密度是激光加工中最关键的参数之一。采用较高的功率密度,在微秒时间范围内,表层即可加热至沸点,产生大量汽化。因此,高功率密度对于材料去除加工,如打孔、切割、雕刻有利。对于较低功率密度,表层温度达到沸点需要经历数毫秒,在表层汽化前,底层达到熔点,易形成良好的熔融焊接。因此,在传导型激光焊接中,功率密度在范围在104~106W/cm2。 2、激光脉冲波形。激光脉冲波形在激光焊接中是一个重要问题,尤其对于薄片焊接更为重要。当高强度激光束射至材料表面,金属表面将会有60~98%的激光能量反射而损失掉,且反射率随表面温度变化。在一个激光脉冲作用期间内,金属反射率的变化很大。 3、激光脉冲宽度。脉宽是脉冲激光焊接的重要参数之一,它既是区别于材料去除和材料熔化的重要参数,也是决定加工设备造价及体积的关键参数。 4、离焦量对焊接质量的影响。激光焊接通常需要一定的离焦,因为激光焦点处光斑中心的功率密度过高,容易蒸发成孔。离开激光焦点的各平面上,功率密度分布相对均匀。离焦方式有两种:正离焦与负离焦。焦平面位于工件上方为正离焦,反之为负离焦。按几何光学理论,当正负离做文章一相等时,所对应平面上功率密度近似相同,但实际上所获得的熔池形状不同。负离焦时,可获得更大的熔深,这与熔池的形成过程有关。实验表明,激光加热50~200us材料开始熔化,形成液相金属并出现问分汽化,形成市压蒸汽,并以极高的速度喷射,发出耀眼的白光。与此同时,高浓度汽体使液相金属运动至熔池边缘,在熔池中心形成凹陷。当负离焦时,材料内部功率密度比表面还高,易形成更强的熔化、汽化,使光能向材料更深处传递。所以在实际应用中,当要求熔深较大时,采用负离焦;焊接薄材料时,宜用正离焦。 二、激光焊接工艺方法: 1、片与片间的焊接。包括对焊、端焊、中心穿透熔化焊、中心穿孔熔化焊等4种工艺方法。
常用焊接参数的选择
常用焊接参数的选择: 1. 手工电弧焊工艺规范参数主要有:焊接电流、焊条直径和焊接层次。 1焊接电流焊条与电流匹配参数 · 1.6 2.0 2.5 3.2 4.0 5.0 5.8 5.8电流(A)25~4.40~60 50~80100~130160~ 210 200~ 270 260~ 300 注:立焊、横焊、仰焊时焊接电流应比平时小10%~20%。 2)焊条直径焊条直径一般根据构件厚度及焊接位置来选择。平焊时焊条直径可以选择大些,立焊时焊条直径不大于5mm,仰焊和横焊时最大焊条直径为4mm,多层焊及坡口第一层焊缝使用的焊条直径为3.2~4mm. 焊条直径的选择 焊件厚度(mm)2336~12≥13 焊条直径(mm)2 3.2 3.2~44~54~6 2. 埋弧自动焊埋弧自动焊焊接规范的主要参数有:焊接电源、电弧电压、焊接速度、焊丝直径及焊丝伸出长度等。 焊丝的直径大,焊缝的熔宽会增加,熔深则稍有下降;焊丝直径越小,熔深相应增加。一般大型工件多采用4~5mm直径的焊丝。 不同的焊丝直径应用不同的焊接电流范围 焊件厚度(mm)23456 焊条电流(A)200~400 300~600500~800700~1000800~1200 焊接电流与相应的电弧电压 焊接电流(A)600~700700~850850~10001000~1200 电弧电压(V)36~3838~4040~4242~44 焊接速度的变化,将直接影响电弧热量的分配情况,即影响线能量的大小。在其他参数不变时,焊接速度增加,热输入量减少,熔宽明显变窄。当焊接速度超过40m/h时,由于热输入量减少的影响,焊接缝会出现磁偏吹、吹边、气孔等缺陷。焊接速度过低时,易产生类似过高的电弧电压的缺陷。 3. CO2气体保护焊主要规范参数:焊接电流、电弧电压、焊丝直径、焊接速度、焊丝伸出长度、气体流量等。 焊丝直径主要是根据工件厚度来选择。一般薄板采用¢0.8~1.0mm的焊丝焊接。中厚板应选用¢1.2~2.0mm的焊丝焊接。 不同直径的焊丝选用焊接电流的范围
焊接工艺参数选择
焊接工艺参数的选择 手工电弧焊的焊接工艺参数主要条直径、焊接电流、电弧电压、焊接层数、电源种类及极性等。 1.焊条直径 焊条直径的选择主要取决于焊件厚度、接头形式、焊缝位置和焊接层次等因素。在一般情况下,可根据表6-4按焊件厚度选择焊条直径,并倾向于选择较大直径的焊条。另外,在平焊时,直径可大一些;立焊时,所用焊条直径不超过5mm;横焊和仰焊时,所用直径不超过4mm;开坡口多层焊接时,为了防止产生未焊透的缺陷,第一层焊缝宜采用直径为3.2mm的焊条。 表6-4 焊条直径与焊件厚度的关系mm 焊件厚度 ≤2 3~4 5~12 >12 焊条直径 2 3.2 4~5 ≥15 2.焊接电流 焊接电流的过大或过小都会影响焊接质量,所以其选择应根据焊条的类型、直径、焊件的厚度、接头形式、焊缝空间位置等因素来考虑,其中焊条直径和焊缝空间位置最为关键。在一般钢结构的焊接中,焊接电流大小与焊条直径关系可用以下经验公式进行试选: I=10d2 (6-1) 式中 I ——焊接电流(A); d ——焊条直径(mm)。 另外,立焊时,电流应比平焊时小15%~20%;横焊和仰焊时,电流应比平焊电流小10%~15%。 3.电弧电压 根据电源特性,由焊接电流决定相应的电弧电压。此外,电弧电压还与电弧长有关。电弧长则电弧电压高,电弧短则电弧电压低。一般要求电弧长小于或等于焊条直径,即短弧焊。在使用酸性焊条焊接时,为了预热部位或降低熔池温度,有时也将电弧稍微拉长进行焊接,即所谓的长弧焊。 4.焊接层数 焊接层数应视焊件的厚度而定。除薄板外,一般都采用多层焊。焊接层数过少,每层焊缝的厚度过大,对焊缝金属的塑性有不利的影响。施工中每层焊缝的厚度不应大于4~5mm。
激光深熔焊接的主要工艺参数
一)激光深熔焊接的主要工艺参数 1)激光功率。激光焊接中存在一个激光能量密度阈值,低于此值,熔深很浅,一旦达到或超过此值,熔深会大幅度提高。只有当工件上的激光功率密度超过阈值(与材料有关),等离子体才会产生,这标志着稳定深熔焊的进行。如果激光功率低于此阈值,工件仅发生表面熔化,也即焊接以稳定热传导型进行。而当激光功率密度处于小孔形成的临界条件附近时,深熔焊和传导焊交替进行,成为不稳定焊接过程,导致熔深波动很大。激光深熔焊时,激光功率同时控制熔透深度和焊接速度。焊接的熔深直接与光束功率密度有关,且是入射光束功率和光束焦斑的函数。一般来说,对一定直径的激光束,熔深随着光束功率提高而增加。 2)光束焦斑。光束斑点大小是激光焊接的最重要变量之一,因为它决定功率密度。但对高功率激光来说,对它的测量是一个难题,尽管已经有很多间接测量技术。 光束焦点衍射极限光斑尺寸可以根据光衍射理论计算,但由于聚焦透镜像差的存在,实际光斑要比计算值偏大。最简单的实测方法是等温度轮廓法,即用厚纸烧焦和穿透聚丙烯板后测量焦斑和穿孔直径。这种方法要通过测量实践,掌握好激光功率大小和光束作用的时间。 3)材料吸收值。材料对激光的吸收取决于材料的一些重要性能,如吸收率、 反射率、热导率、熔化温度、蒸发温度等,其中最重要的是吸收率。 影响材料对激光光束的吸收率的因素包括两个方面:首先是材料的电阻系数,经过对材料抛光表面的吸收率测量发现,材料吸收率与电阻系数的平方根成正比,而电阻系数又随温度而变化;其次,材料的表面状态(或者光洁度)对光束吸收率有较重要影响,从而对焊接效果产生明显作用。 C02激光器的输出波长通常为10.6 ym,陶瓷、玻璃、橡胶、塑料等非金属对它的吸收率在室温就很高,而金属材料在室温时对它的吸收很差,直到材料一旦熔化乃
激光熔覆_图文讲解
一、激光熔覆的原理 激光溶覆是利用高能激光束辐照,通过迅速熔化、扩展和凝固,在基材表面熔覆一层具有特殊物理、化学或力学性能的材料,构成一种新的复合材料,以弥补基体所缺少的高性能。能充分发挥二者的优势,克服彼此的不足。 可以根据工件的工况要求,熔覆各种(设计)成分的金属或非金属,制备耐热、耐蚀、耐磨、抗氧化、抗疲劳或具有光、电、磁特性的表面覆层。通过激光熔覆,可在低熔点材料上熔覆一层高熔点的合金,亦可使非相变材料 (AI 、Cu 、Ni 等)和非金属材料的表面得到强化。 在工件表面制备覆层以改善表面性能的方法很多,在工业中应用较多的是堆焊、热喷涂和等离子喷焊等,与上述表面强化技术相比,激光熔覆具 有下述优点: (1 )熔覆层晶粒细小,结构致密,因而硬度一般较高,耐磨、耐蚀等性能 亦更为优异。 (2 )熔覆层稀释率低,由于激光作用时间短,基材的熔化量小,对熔覆层的冲淡率低(一般仅为 5%-8%),因此可在熔覆层较薄的情况下,获得所要求的 成分与性能,节约昂贵的覆层材料。 (3 )激光熔覆热影响区小,工件变形小,熔覆成品率高。 (4 )激光熔覆过程易实现自动化生产,覆层质量稳定,如在熔覆过程中熔覆厚度可实现连续调节,这在其他工艺中是难以实现的。 由于激光熔覆的上述优点,它在航空、航天乃至民用产品工业领域中都有较广阔的应用前景,已成为当今材料领域研究和开发的热点。 激光熔覆技术应用过程中的关键问题之一是熔覆层的开裂问题,
尤其是大工件的熔覆层,裂缝几乎难以避免,为此,研究者们除了改进设备,探索合适工艺,还在研制适合激光熔覆工艺特点的熔覆用合金粉末和其他熔覆材 料。 二、激光熔覆工艺方法 激光熔覆工艺方法有两种类型: 1、二步法(预置法) 该法是在激光熔覆处理前,先将熔覆材料置于工作表面,然后采用激光将其熔化,冷凝后形成熔覆层。预置熔覆材料的方式包括: (1 )预置涂覆层:通常是应用手工涂敷,最为经济、方便、它是用粘结剂将熔覆用粉末调成糊状置于工件表面,干燥后再进行激光熔覆处理。但此法生产效率低,熔覆厚度不一致,不宜用于大批量生产。 (2 )预置片:将熔覆材料的粉末加入少量粘结剂模压成片,置于工件需熔覆部位,再进行激光处理。此法粉末利用率高,且质量稳定,适宜于一些深孔零件,如小口径阀体,采用此法处理能获得高质量涂层。 2、一步法(同步法) 这是在激光束辐照工件的同时向激光作用区送熔覆材料的工艺, 它又有两种方/法。 同步送粉法:使用专用喷射送粉装置(见图)将单种或混合粉末送入熔池,控制粉末送入量和激光扫描速度即可调整熔覆层的厚度。由于松散的粉末对激光的吸收率大,热效率高,可获得比其他方法更厚的熔覆层,容易 实现自动化。国外实际生产中采用较多。 同步送丝法:此法工艺原理虽与同步送粉法相同,但熔覆材料是预先加工成丝材或使用填充丝材。此法便利且不浪费材料,更易保证熔覆层的成分均匀性,尤其是当熔覆层是复合材料时,不会因粉末比重或粒度大小的不同而影响覆层质量,且通过对丝材进行预热的精细处理可提高熔覆速率。但是丝材表面光滑,对激光的反射较强,激光利用率相时较低;此外,线材制造过程较 复杂,且品种规格少。
激光焊接工艺参数
激光焊接原理与主要工艺参数 1.激光焊接原理 激光焊接可以采用连续或脉冲激光束加以实现,激光焊接的原理可分为热传导型焊接和激光深熔焊接。功率密度小于104~105 W/cm2为热传导焊,此时熔深浅、焊接速度慢;功率密度大于105~107 W/cm2时,金属表面受热作用下凹成“孔穴”,形成深熔焊,具有焊接速度快、深宽比大的特点。 其中热传导型激光焊接原理为:激光辐射加热待加工表面,表面热量通过热传导向内部扩散,通过控制激光脉冲的宽度、能量、峰功率和重复频率等激光参数,使工件熔化,形成特定的熔池。 用于齿轮焊接和冶金薄板焊接用的激光焊接机主要涉及激光深熔焊接。下面重点介绍激光深熔焊接的原理。 激光深熔焊接一般采用连续激光光束完成材料的连接,其冶金物理过程与电子束焊接极为相似,即能量转换机制是通过“小孔”(Key-hole)结构来完成的。在足够高的功率密度激光照射下,材料产生蒸发并形成小孔。这个充满蒸气的小孔犹如一个黑体,几乎吸收全部的入射光束能量,孔腔内平衡温度达2500 0C左右,热量从这个高温孔腔外壁传递出来,使包围着这个孔腔四周的金属熔化。小孔内充满在光束照射下壁体材料连续蒸发产生的高温蒸汽,小孔四壁包围着熔融金属,液态金属四周包围着固体材料(而在大多数常规焊接过程和激光传导焊接中,能量首先沉积于工件表面,然后靠传递输送到内部)。孔壁外液体流动和壁层表面张力与孔腔内连续产生的蒸汽压力相持并保持着动态平衡。光束不断进入小孔,小孔外的材料在连续流动,随着光束移动,小孔始终处于流动的稳定状态。就是说,小孔和围着孔壁的熔融金属随着前导光束前进速度向前移动,熔融金属充填着小孔移开后留下的空隙并随之冷凝,焊缝于是形成。上述过程的所有这一切发生得如此快,使焊接速度很容易达到每分钟数米。 2. 激光深熔焊接的主要工艺参数 1)激光功率。激光焊接中存在一个激光能量密度阈值,低于此值,熔深很浅,一旦达到或超过此值,熔深会大幅度提高。只有当工件上的激光
大族激光价值分析完结篇
补充: 此文又臭又长,慎入。 ---------------------------------------------------------------------------------------------------------------------------人的思维具有跳跃性,喜欢先入为主,又容易被锚定以及自我强化,想当然,冲动,以偏概全。文字记录能帮助细化推理过程,推敲结论的合理性,帮助理顺逻辑,能纠错完善思路,记录的过程可以连点成线,连线成面,提炼精要,避免盲人摸象。就以这篇大族激光的企业价值分析作为今年的阶段性小结,作为未来的起点。 分析具体思路囊括为五个大项(盈利的确定性,生意模式,企业价值创造经营态势,风险,其他补充)。其中盈利的确定性又分为: 商业价值,市场潜力及供需格局,竞争力,业绩增长驱动力,成本费用,产能外延,经验变量七个方面。 生意模式又分为: 经营存续,现金创造,经营周期(时间相关)三个方面。 (一)盈利的确定性 (1)商业价值潜在的巨大商业价值是盈利确定性的因素之一。必须认识到企业商业价值的大小需要结合特定的时代背景,一个尚且吃不饱穿不暖的社会,很难想象娱乐业有多大的商业价值。几乎所有的企业都可以归类到下面两大类: 一种是满足人的需求;一种是满足企业的需求(如提高生产效率等)。毫无疑问,激光行业属于第二类。激光的应用可以简单分为两类,一类是提高企业效率。 只要中国的手机产业链/新能源行业/太阳能/led等行业继续向前发展,一方面进入存量市场格局的行业硬件创新必然是未来的方向,另一方面充分竞争
的行业也必然会倒逼生产力提高。而激光行业必将在这个两个方面起到重要作用,加上本届政府经济发展的核心强调从量到质的转变(从以往摊大饼到重视生产力提高),激光行业目前阶段在中国大有可为。 有趣的是虽然大族激光营收从2012年到2016年增加了60%,但其市场份额从2012年到2016年市场份额是不断下降的,查看华工科技也发现了同样的趋势(不同之处是华工2016年激光营收较2012年只增长15%左右)。这一方面说明这几年国内激光市场高速增长吸引了众多企业的加入,激光行业呈现出比较分散的市场。另一方面也可能预示着随着竞争的白热化国内激光企业的行业洗牌可能就在不久的将来。 据一位从事超快激光器研究的业内朋友得知,这几年随着激光市场的景气,中低端市场激光设备已经有了价格战的味道,以紫外激光器为例,2013年左右紫外激光器价格大概一台20~30万人民币左右,到2017年一台紫外激光器价格已经下滑到5万人民币了,可见激光企业已经过了往年躺着就能赚钱的好日子了。如果说供不应求为供需格局的最佳组合(比如天齐,赣锋,亨通,福晶,巨石,隆基),其次需求增长,供应也在快速扩展也算是不错的格局(比如,新能源电池隔膜)。通过上述分析,激光行业随着需求增长,供应端也在不断扩大但多为中低端市场,供需模式介于供不应求和供应需求同步扩大之间。需要注意到两种截然不同的供需格局: 一种是巨大需求,但市场过于分散;另一种是行业中占据明显竞争优势,具有压倒性的占有率,但行业需求并不清晰。 前者要关注经验模式和特色上的创新(比如装修行业的过于分散痛点),或者整合能力强的企业;后者更需要关注教育市场扩大需求,打破天花板。从发达国家的情况来看,激光行业集中度非常高,这说明激光设备最终是可能形成较高的门槛的。根据optech的数据,德国通快在2015年占据了全球30%的激光加工市场份额,是激光加工的世界龙头,作为国内全领域龙头的大族激光未来在国内市场份额都有望进一步提高。 假如国内激光市场未来3年(到20年)总规模保持20%的复合增速,再假设大族激光的市场占有率提升到25%左右,那大族激光预期的营业规模大约为200亿左右。2017年预计公司营业收入在120亿左右,其中国内收入110亿,那根