精益生产之八大浪费篇
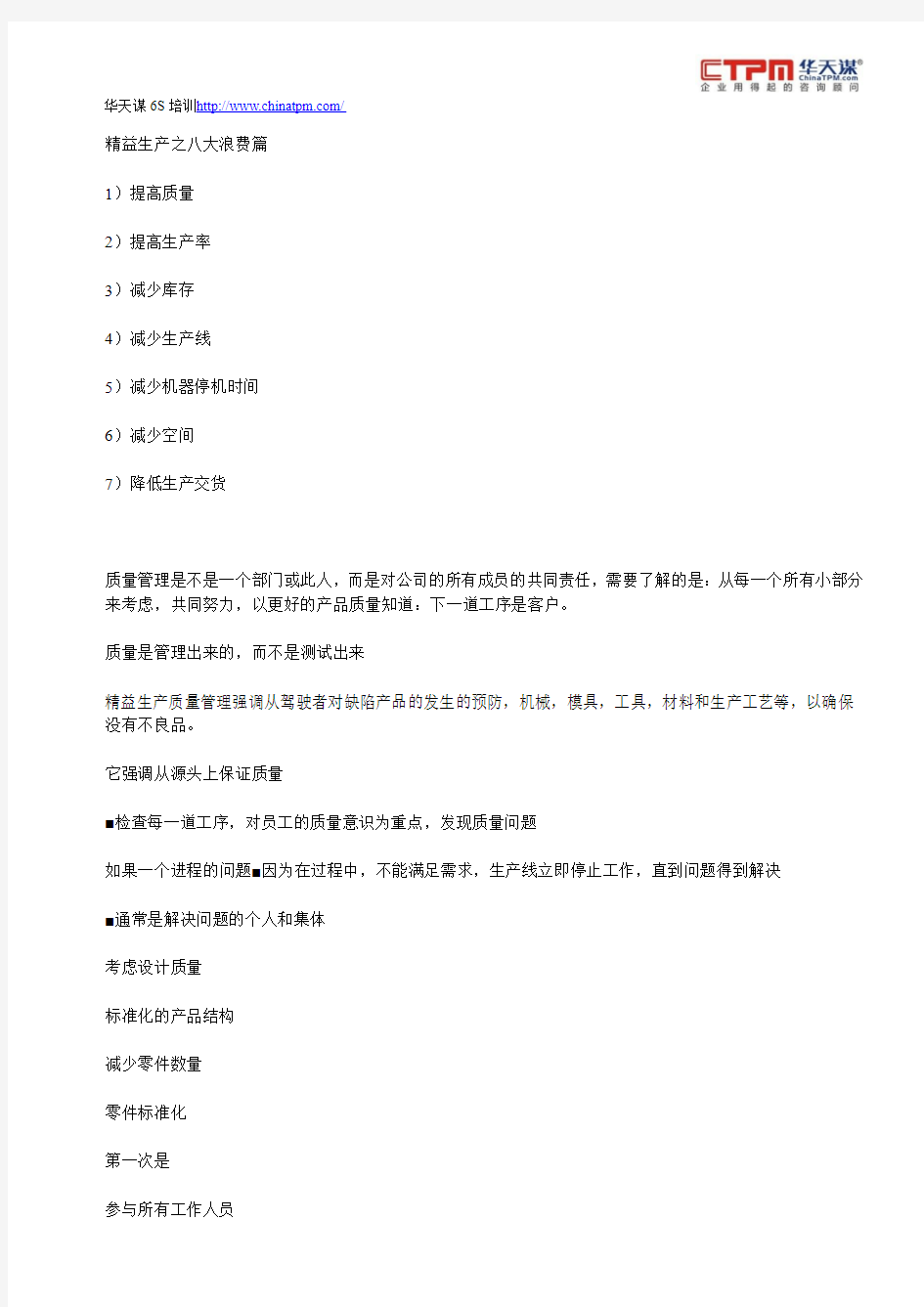

精益生产之八大浪费篇
1)提高质量
2)提高生产率
3)减少库存
4)减少生产线
5)减少机器停机时间
6)减少空间
7)降低生产交货
质量管理是不是一个部门或此人,而是对公司的所有成员的共同责任,需要了解的是:从每一个所有小部分来考虑,共同努力,以更好的产品质量知道:下一道工序是客户。
质量是管理出来的,而不是测试出来
精益生产质量管理强调从驾驶者对缺陷产品的发生的预防,机械,模具,工具,材料和生产工艺等,以确保没有不良品。
它强调从源头上保证质量
■检查每一道工序,对员工的质量意识为重点,发现质量问题
如果一个进程的问题■因为在过程中,不能满足需求,生产线立即停止工作,直到问题得到解决
■通常是解决问题的个人和集体
考虑设计质量
标准化的产品结构
减少零件数量
零件标准化
第一次是
不要隐藏的股票,以稳定的质量
什么是质量(辅酶Q)的费用
质量成本
访问前成本
评估成本
损失成本
内部损失成本
外部损失成本
自我和互检的工作通常被称为“双重检查”,主要是自我管理的实施。(1)自我和质证进程的实施
一,教育经营者自律,灌输“双检查”的重要性;
乙,在现场不定期抽查,监督的“双重检查”的执行情况;
C,有一些问题,强调了“双检查”是符合双方的责任有关。
研发,建立明确的问责制,评估和实施奖励和处罚
一线主管如何与公司的质量好
一)强大的反应能力,以质量和加工能力;
二)了解,下一道工序是顾客;
三)按标准作业规范;
四)车间做自我检查;
f)设备,工具,检测设备的正确使用和维护;
克)组织材料的控制和环境;
八)热爱工作,有高度的责任感;
质量改进和提升网站
1)设施使用各种灯光,广告牌,以显示正常,生产过程
不,提高快速反应能力素质
2)质量信息反馈机制的建立异常
3质量,工程,采购等部门)紧密合作
4)跨部门小组成立,以改善质量
5)PDCA循环使用,以改善和提高质量
七大手法,以提高现场质量---
清单
分层法
因果图
柏拉图
直方图
控制图
分散
六标准差工具
统计过程控制(SPC),质量功能展开(QFD)
失效模式与效应分析(FMEA),因果矩阵(原因和影响矩阵),英国标准(英国标准),过程能力分析(过程能力分析),
实验设计(DOE),测量系统分析(MSA),
价值链分析(价值链分析),崔京图(单位:kJ方法),
流程图(流程图),统计推论(推论统计),
(描述统计)描述性统计,
鱼骨图,直方图,柏拉图,连通图,采样,控制图,相关分析,回归分析,传播方式,方差分析
全因子实验,
模块化设计,
公差设计,
概念工程,
舞台/栅工艺,
SIPOC(供应商输入过程输出客户),
就业选配计划,
挥发性有机化合物,
筛选研究,
假设检验
对废物的定义
在JIT生产,废物和垃圾的社会影响通常是指不同。JIT的关注,任何产品的价值比绝对最低必要的材料,设备,人力,空间和时间部分被浪费数量的增加。因此,生产废物的JIT模式不只是增加价值的活动,不也包括资源比“绝对最低”的界限使用。
在许多公司的各种废物尚未流行,5S活动,如表1-1所示。为了防止植物废料,首次发现不合理的,然后才想办法解决问题,这需要的5S,JIT的执行和其他更先进的管理方法。
表1-1是不是5S活动实施的五个营业损失浪费
废物性能
危害
设备布局不合理
半成品的产品大量增加的处理,无效操作
设备的保养不当
容易出现故障,维修费用增加,影响质量
随意放置物品
易于混合,费时寻找,容易呆料
可怜的通道
做得不好,容易出现风险,增加处理
八种常见污水厂
首先,(不良品,废物修理)质量缺陷
◆任何不良品产生,是由材料,机械,劳力和其他废物造成的。
◆早期发现不良品,容易识别坏消息来源,从而减少不良品的生产。
◆关键是把事情在第一时间,以“零缺陷”
由于不利的厂品,对需要处理的时间,人力和物力资源浪费,以及由此产生的相关损失。这些废物包括:物质损失的,有缺陷的产品成为废物;设备,人员和工作时间的损失,额外的修复,鉴定,考试的额外损失,有时需要减少加工产品,或运输延误所造成的信贷额度下降。
二,加工(加工废弃物)
◆定义:是指项目的进展是不必要的,并已完全做精密加工,也被过度废物处理已知的,主要包含两层含义:第一,如高精密加工及以上的额外精度处理,实时浪费资源,第二个是需要付出额外的时间和辅助设备,同时也增加了电力,空气压力,石油,能源生产,废物管理还增加了时间。
◆有一些处理可以省略,相反,重组或合并。
◆很多时候,而目前的实际应用,以更好地
第三,垃圾运动
12个行动浪费:
◆◆◆游手好闲,不符合一方面免费停◆◆左,右汇率比步行◆
◆◆点转折移动变换大型国有◆◆◆长延时弯曲法律行动◆未知的不必要的重复动作技能
四,交通(废物运输)
◆中国有很多企业管理者认为,处理是必要的,而不是一种浪费。因此,许多人视而不见废物处理,更不用说摧毁它。从JIT的角度来看,处理是不会产生的行动,而不是所生产的是浪费了工作的价值增值。
◆使用“传送带”的方法来克服,对不对?这种方法成本很高,以减少工人和消费的身体,事实上,不排除将他们自己的浪费。
1,取放废物; 2,等待时间;三,过度浪费的产品; 4,浪费的空间。
◆体现废物处理安置,堆放,移动和其他行动,浪费了整行,而带来的浪费空间的项目,时间,工具,浪费和其他不良后果的人类居住的运动要求。
第五,库存的浪费
库存过剩掩盖问题,减少库存风险问题
◆精益说:“股票是一切罪恶的根源”,所有的改善行动都直接或间接地和消除库存有关。
①不必要的搬运,包装,放置,防护处理,找到这样的一种浪费FIFO操作的困难②
③④利息和管理费损失将降低商品价值,产品成为呆滞
⑤占用厂房面积,在多余的工厂,仓库和施工设备能力和人员配置的需要⑥造成误判
◆无形的损失造成的股票,而不是物理损失亚洲,精益库存隐藏的,而“问题”的精益生产被认为是财富生产的问题,这个问题可以继续被发现如果解决,将有利于将继续产生
1,没有管理的紧张,阻碍改善:
2,一个以上的股票,由于机械故障,不良品,不良后果不会立即显现出来,因此不会产生对策。
3,由于库存充足,有问题可以在存货上,解决问题可以慢慢甚至没有解决,至少是掩盖,不急了,将不承担更高层次的原因,该部门的成绩也出来了。按照以前的管理思路,人们认为股票是一件坏事,虽然,但它是必要的。准时的角度来看,库存是没有必要,甚至认为库存是邪恶的。由于许多股票会失败,不良品,缺勤,小停止,错误的计划,时间过长,质量不稳定,调整,容量都蒙面的不平衡。
例如,有些生产线故障,停机,停线,但由于脱销和库存不至于,这样的失败会造成停机,停线的问题掩盖,延迟故障排除。如果您降低库存,这些问题可以彻底暴露于水平面,然后逐步解决这些库存的浪费。
第六,过渡生产(制造浪费太多或太早)
◆租置计划强调,“即时生产。”
1,早期花了材料成本,劳动力成本只,并不能带来任何好处。
2,“等待的浪费”隐藏起来,使管理者忽视的发生和存在的等待。
3,在产品积压,对L /吨的生产周期较长的无形)和更大的工作空间会现场,在不知不觉中吞噬我们的利润。
4,导致处理,包装废弃物,先进先出困难。创建过多或过早提前在生产成本,花,不仅没有好处,但也隐藏的等待造成的浪费,失去了持续改进的机会。有的企业以较强的生产能力,生产量不浪费不中断生产,在产品的增加,使产品周期较短的时间,更大的空间,但也增加了运输,废物的积累。此外,过多或过早制造,带来了大量库存,增加的利息负担将不可避免地增加货币贬值的风险。
七,等待的浪费
◆◆生产工作从各种开关来了,他们往往束手无策◆原料短缺,设备闲置
◆拖延的过程中,没有什么下游设备故障◆◆进程不平衡的生产线
◆工作和休息制造业未送达通知或设计◆分配不均
由于原材料供应中断,作业调度的不平衡和不正确的生产造成任何的等待,等待着被称为废物。生产线,不同品种之间切换,如果没有足够的准备工作将不可避免地造成浪费的等待,在每天的工作量太大,有时忙的变化,有时造成人员,设备闲置;上游的过程中出现问题,导致下游过程中做什么。此外,该生产线的工作和休息的差距存在,而且还造成浪费的一个重要原因等待。
八,废弃物管理
废物管理是指问题后,才采取适当的补救措施,管理人员和其他废弃物。废物管理不作为的问题而发生事前管理,科学的管理应该是一个相当明确,合理的规划,以及促进东西加强管理,控制和反馈过程,这样就可以在相当大程度上降低发病废物管理
如何消除时间,人力的浪费,管理
■找出那些高价值和低价值的工作
■应用20/80原则
■工作计划管理和时间管理,目标管理,有利于
什么是公司在浪费时间
1)对于一个生产周期很长一段时间
2)购买的时间较长
4)生产线切换时间过长时,转换模型
5)更换,更换时间过长
6)工作计划是不合理的,在一段时间的浪费
7)在工作量的变化过大,有人员,设备闲置。
8)经常由于材料或物质上的延误发生过程缺乏该机器或生产线闲置停止拉; 10)机械设备经常发生故障;
11)没有取得生产线之间的平衡。
12)与部门之间缺乏协调,导致对决策的浪费时间;
13)会议过多,造成浪费。
如何消除浪费时间
■根据浪费的时间原因,具体的解决方案,以对付
■要建立和完善的制度和操作流程。
时间标准和适时调整■建设提升
■有效的执行(后续行动,监测)
■定期审查,评价和持续改进。
消除浪费工作人员的意义:
1)提高工作效率
2)降低劳动力成本
3)减少工作人员的懈怠,推卸发生感觉的类型,和其他废物,以减少由此产生的发掘潜力的富余人员
1)如何识别过剩的生产线员工
2)如何探讨盈余管理
工作人员就如何消除浪费
1)对于潜在过剩分析现有员工
一,职位和丁吁庵
乙,在合理的位置
C中,工作量的饱和度
2)消除无用的工作
一,明确了工作的那些谁是没有好
乙,精简工作流程,合并
3)改善运营和设备,提高生产效率,实现为数不多工作人员就如何消除浪费
1)重新调整组织结构,精简人员
2)扩大的责任,控制幅度
3)全权
如何减少浪费的八大管理
1,管理不能是废物要素的有效利用
2,没有目标,没有计划浪费造成的管理成本
3,缺乏协调衔接的废物
4,效率低下造成的浪费效率
5,根据他们的个人意愿的混乱所造成的浪费
6,缺乏责任感和主动性的等待浪费
7,敷衍应付废物
8,监督和其他废弃物管理
1,我无法控制喜欢做技术工作- 而不是在人员管理好
2,我的贡献。对个人的努力来完成任务依靠习惯- 孤军奋战,而不是在建设好建立有效的工作网络,团队
3,主要由我,我真的不担心。事无巨细,而不是在授权抓住良好
4,有否虽然尚未完成的目标,但缺乏目标控制
5,我喜欢自由的一步,一步。不好,不用于计划
6,不敢说什么有问题。战斗是普遍
7,谁可以帮我还没有系统化的管理技能培训,知识缺乏
8啊,阿弥陀佛,幸好没有变化,没有任何失误。
八高管经常犯错误
(1)掌握和缺乏责任感,拒绝承担个人责任
(2)“自私”的思想严重,把重点放在个人和部门利益的唯一
(3)管理的一个单一,缺乏具体的领导
(四)未能妥善培训和指导下属
(5)角色错位
(6)缺乏自律,休闲风格,忽视的负面影响
(7)缺乏跟踪和监测
(8)人员的错误,窝藏人的能力不足
八,主管成功标准
(一)明确目标
(2)做正确的事
(3)共同得主
(5)沟通无界限
(六)对业主本身
(七)客户端
(8)追求卓越
行政人员的类型
强迫压制类型:顽固守旧,过压工作人员,威胁的恐惧使他的地位雇员
哥们义气型:员工的待遇往往称兄道弟,约哥们义气,工作情绪,原则之不足,不能发挥其应有的作用负责
教练型:也就是说,技术和管理,了解和注重员工培训和团队建设的团队,明确的目的,主动发现和解决问题
劳模类型:工作可以感受到,勤奋,只知道自己的工作,而不是管理人员,不适合领导
大萨巴类型:不开心是经理,做一天和尚撞一天钟,工作,只是没有责任感,采取无为而治的做法,虚幻
顺从型:强调绝对服从忠诚度较高的是,毫无疑问和阻力,但不会采取主动做的事情,一切听从上级的指示,但他们尽量不要在成功的目的了。往往是一个创新和管理能力不足
型的生产技术:技术业务专家,但缺乏人际交往能力,工作方法简单,常用于治疗机的方法对工作人员
精益生产的目标(四低两短):
废物的最低限额,
在股票最低
去除率最低,
机器故障率很低,
生产的前置时间最短,
为了在最短的时间。
精益生产是为了满足客户多样化,高品质,低成本,短交期的需求,并制定了新的生产方式。
追求精益生产的7“零”的终极目标
零切换时间
零库存
零浪费
零不良
零故障
零停滞
零灾害
精益两个核心:
第一:消除一切浪费,取消非增值活动,实现“降低成本”
第二:快速应对市场变化
JIT的精益生产技术,以实现具体的:
(1)生产的同步是通过“过程在收到”(也称为拉),后工序只在需要时获得手术前处理的必要,之前收到的过程只能按照数量和种类走生产
(2)生产,通过均衡的生产(同时生产品种)或通过程序实现了平衡。在所使用的机器,通过专用设备平衡普遍性和设置标准,以实现业务
(3)灵活的单位生产是通过设置生产线,拆卸改变生产线和生产线,和简单的方式来实现固定分裂。产量有所改变,以增加或减少操作次数,缩短了生产周期因应市场的“干草诹访精神
精益生产方法,以达到特定的
真正的知识收集,协作的手走(推)生产控制系统
三及时生产方式的实施细节
其次,因为只有在后期制作过程中需要,没有必要避免和减少商品库存
第三,生产订单只发给到最后一步,最终产品生产的数量和显示订单号(市场需求)是一致的
通过精益生产方式转变的机制解决订单频繁
精益生产流程生产---
单位工程和单件流(一piecr流)
单一的生产好多了,最好是在同一时刻平等每批生产过程中允许一个产品的好处没有大型和高速机的质量和机械问题,将立即无重复的操作,减少库存,减少了使用空间
在缓冲库存的情况下,这个问题必须立即解决,从而提高质量,生产和客户需求紧密相连,可以缩短交货时间,提高应变能力
该机组的选择
到不同的生产工艺单位联合机
设备必须是生产单位的细胞产品的能力,最好是移动机器
建议:
选择卷的功能大致相同的机器
使用现有的机器,购买新机器之前,应当考虑重新设计单位
根据调整生产节拍生产
灵活的配置工作人员
缩短开关时间的工作,四个阶段的快速开关-----
缩短开关时间,必须一步一个脚印,一步一步一步做的:
第一阶段:有点分钟控制在十分钟
第二阶段:从几个小时或几十分钟下降到原来的一半
第四阶段:“爆炸性”的一分钟
缩短运行规则,提高了开关时间
小批量和同步生产,势必要对操作开关变得十分频繁。开关时间缩短工作成为一个关键问题。模具刀具夹具切换开关参考变化
大会的开关元件材料
一般加工前的准备工作
精益全面维修设备----(TPM)的
全部生产和可意保全是指达到以下六点:
全面投产,以确保安全---保持良好的工作状态设备的安全和稳定的状态。
1,定期安全2,预测安检后保存3,4,提高保全5,6安全防范,自我保护
不合适的设备维修理念:
1,坏,再修,不坏,无论
2,花时间去维护,收效甚微
3,各自运作,互相干扰
4,操作员只需使用,保养,维修人员只
5,无火灾的概念
6,知道什么时候必然彻底失败
7,所有设备的定期检修,定期更换
8,全参与者没有必要保持生产
设备利用率,可固定利率:
固定利率=可用于时间/天,所需时间
固定率可高达百分之一百可以为目标,追求使用率,视情况而定,而不是到了百分之百的追求的心。要移动移动,停止停止
制造商和供应商
■将工作中心的外部供应商
■数量将交频率的变化,直接在车间交付
■省略进货检验
■实现供应商的质量和可靠性要求
■使用远程仓库,部分供应商交货近端
■倾向于使用单一供应商
■帮助供应商发展即时生产系统
控制道路交付十大供应商
计划审计法
强制法生产会议
绩效管理法
标记现行法律
批量采购法
供应商承认法
法律责任
进度控制方法
预警方法:3至5天管理,航运法律提示
十项措施,改善商品供应的质量,品检厂外巡回
审计和评估
质量审查将参与
客户投诉和索赔回收系统
产品质量信息反馈
失败的代价索赔法律
标记法和罚方法
进货检验质量信息反馈
质量改进
供应商控制点
常驻代表
监督检查
检查的主要或特殊程序
与客户联合检查
在控制了局势的重大变化
辅导
进货检验
控制
管理工具来实现精益生产---生产管理看板(1)单广告牌管理
遵循一个广告牌管理的基本原则
②广告牌广告牌在这个过程中收集箱B是自动发送到生产订单,即“有几个部分要绘制,应立即被添加到生产和。”因此,在生产过程中B的广告牌指示“部分的名称”,“生产多少”等信息,加工和生产的各种零部件。处理后,进程B就怎么做的重视只是把广告牌的零件盒生产的机械,最后,把它们的广告牌上的档案库中的指定产品的生产,去获得的部分以复加。
②当进程B,生产工人,他也需要使用这些产品所需的零件。在这一点上,他将获得一个前程序所需的零件。接收相同的时间,他会把附着在零件盒中取出过程的广告牌,广告牌收集箱。同样,这个广告牌就会自动处理到生产订单的操作人员发出。并依此类推,直到原材料的采购或加工订单。
③当进程B,生产工人,他也需要使用这些产品所需的零件。在这一点上,他将获得一个前程序所需的零件。接收相同的时间,他会把附着在零件盒中取出过程的广告牌,广告牌收集箱。同样,这个广告牌就会自动处理到生产订单的操作人员发出。并依此类推,直到原材料的采购或加工订单。
(2)两种管理的基本原则,广告牌
1,当总装配生产线C接到命令,运营商开始使用组件的总装配工艺的产品组装保存。同时,在挂零件盒工人取料机在离广告牌,将其放置收集箱广告牌。
2,经办人员看到广告牌后的收集箱,就像收到取料机的指示。因此,他将采取过程之前组件库来接收广告这个广告牌的材料和一个空框,在产品B的表示品牌。
3,移动广告牌下取料机人员收集到的资料显示后需要拆除广告牌上的零部件生产原盒立即挂的部分,并投入生产过程中乙广告卡收集箱。与此同时,他给我带来一个广告牌在回收部分去框,并在指定地点将空箱吊。最后,他将获得的零件和回收广告牌- 与大会返回
线
4,进程B,生产工人看到广告牌中的板生产募捐箱,他们了解到,“那里是获得零部件,生产,立即添加。”因此,运营商将根据生产看板的资料表明,生产和加工所需的必要组件数量
5,零部件加工完成后,将广告牌挂在生产在短短的零件盒放的过程中,和他们一起送到指定的广告牌库中的项目后,工作人员删除过程总是需要前来领取。
操作使用五个广告牌的规则
没有广告牌不能生产,也不湾
后工序只能来自于广告牌
考试结束前只能生产过程
广告牌的部分不能与实物一起到手术后穷人。
精益生产管理八大浪费和解决方法(详细版)
精益生产管理八大浪费与解决方法(详细版) 一、制造过早(多)的浪费二、库存的浪费 三、不良修正的浪费四、加工过剩的浪费 五、搬运的浪费六、动作的浪费企业管理问题解决-请点击 七、等待的浪费八、管理的浪费八大浪费简要版-请点击 八大浪费是丰田生产方式中非常重要的一个观念。丰田人认为要消除浪费,持续改善,企业才能保持良性运转,竞争力才会提升。在丰田改善是探入人心的,有个说法就是跟他们谈话5分钟没有听到他们讲3次改善就不算丰田人。改善的对象是浪费,认识浪费是改善的第一步,企业现场林林总总,哪些是有价值的,哪些是浪费,不是一般人可以一目了然的。丰田人在长期作业和改善过程中对于浪费的内容进行了总结,共七种,被称为七种浪费。它们分别是制造过早(多)的浪费、库存的浪费、不良修正的浪费、加工过剩的浪费、搬运的浪费、动作的浪费、等待的浪费共七种。后来人们又加了一种浪费-管理的浪费,合称八种浪费。下面我们从实用性角度剖析这八种浪费。 一、精益生产管理中制造过早(多)的浪费 定义:所谓制造过早(多)就是前制程制造太早/过多,大于客户(或后制程)当期的最小需要量。 制造过早(多)浪费是八大浪费中的首恶,在精益生产中则被视为最大的浪费。福特式思维告诉大家,在同样的时间内,生产量越多,效率越高,成本越低,企业越赚钱,所以企业自然有大批量连续生产的初始动力。作为一个整体的企业是如此,那么企业内各部门也是如此,特别是在一些制程较短,关联性较低的企业中,普遍实施计件工资,那么从最基础的员工开始就有多做、早做,甚至偷做
的动力,在这种情况下,告知企业里所有人早(多)做是罪恶当然得不到掌声回应。那么我们就来看看制造过早(多)的浪费。 制造过早(多)浪费的后果主要有三大类。 1.直接财务问题。表现为库存、在制品增加,资金回转率低,制造时间变长,占用资金及利息,会造成库存空间的浪费,在现金流量表上很明显。 2.产生次生问题。会产生搬运、堆积的浪费;先进先出的工作产生困难;产品积压造成不良发生,物流阻塞制程时间变长,现场工作空间变小,有滞留在库的风险,有不良品的风险。 3.掩盖问题。为什么“制造过早(多)浪费是八大浪费中的首恶,在精益生产中则被视为最大的浪费”?因为它带给人们一个安心的错觉,掩盖了各种问题,以及隐藏了由于等待所带来的浪费,没有改善的动力,失去了持续改善的时机。 1.制造过早(多)浪费的产生原因。 (1)生产计划方面。 1)信息准确度问题。信息不准,计划失当,信息传递不准确,导致生产计划作业进行盲目,最终导致制造过早(多)浪费的产生。 2)生产计划管控机制方面。让某些制程、生产线、工站甚至作业员有生产伸缩的充分空间和提高产出的利益驱动。比如有的不排班生产计划,也不排日生产计划,而是排周生产计划,一天内的生产排配权利下放到制程、生产线、工站甚至作业员,这时候如果有多余的产能、人力、设备稼动过剩,则很自然地就会提前安排生产,安排满稼动生产,从而造成制造过早(多)。特别是在某些企业中(如玩具),较有可能安排计件生产,多劳多得,那么过量过早生产的积极性就更大了。 除非在实施了拉动生产的精益生产管理企业里面,一般的企业还是用MRP在做推式生产。这时候生产计划的排配,生产进度的精确控制是企划部门最基础的功能,不能因为制造能力弱,各制程衔接性差就放松对生产计划实施进度的管控。 (2)内部制造能力弱的补偿问题。 制造过早(多)多数时候是出于补偿内部制造能力弱的考虑。制造能力弱,特别是制造中的品质差,换型时间长,在市场信息牛鞭效应的驱动下,为了弥补自身能力不足,而提前过量生产以满足客户需求。 如一个企业制造能力弱,多制程时的合计良品率在50%-70%之间分布,那么面对100K的P/O时,它就需要备143-200K的原料,为了安全起见,这时候一般会选择安全系数较高的200K,甚至220K,当这220K投到制程中去的时候,造成生产过多就不可避免了。在这里,制造过多是制造能力弱的补偿,同时制造能力提升也是消除制造过多的必要前提。 对于制造过早是补偿制造能力弱的论断,用制造前置时间(L/T)可以清晰地衡量出来。 (3)产能不平衡及流程不顺方面。 1)制造过程中由于各功能制造单位、制程产能不平衡,不可避免地造成加工能力低的制程前在制品(WIP)堆积,同时给后工站的作业带来了极大的不便。图1是T公司制造的一个产能平衡图,T公司制造有冲压、清洗、打磨、焊接、
精益生产与八大浪费
大纲: 一、制造过早(多)的浪费二、库存的浪费 三、不良修正的浪费四、加工过剩的浪费 五、搬运的浪费六、动作的浪费 七、等待的浪费八、管理的浪费 八大浪费是丰田生产方式中非常重要的一个观念。丰田人认为要消除浪费,持续改善,企业才能保持良性运转,竞争力才会提升。在丰田改善是探入人心的,有个说法就是跟他们谈话5分钟没有听到他们讲3次改善就不算丰田人。改善的对象是浪费,认识浪费是改善的第一步,企业现场林林总总,哪些是有价值的,哪些是浪费,不是一般人可以一目了然的。丰田人在长期作业和改善过程中对于浪费的内容进行了总结,共七种,被称为七种浪费。它们分别是制造过早(多)的浪费、库存的浪费、不良修正的浪费、加工过剩的浪费、搬运的浪费、动作的浪费、等待的浪费共七种。后来人们又加了一种浪费-管理的浪费,合称八种浪费。下面我们从实用性角度剖析这八种浪费。 一、制造过早(多)的浪费 定义:所谓制造过早(多)就是前制程制造太早/过多,大于客户(或后制程)当期的最小需要量。 制造过早(多)浪费是八大浪费中的首恶,在精益生产中则被视为最大的浪费。福特式思维告诉大家,在同样的时间内,生产量越多,效率越高,成本越低,企业越赚钱,所以企业自然有大批量连续生产的初始动力。作为一个整体的企业是如此,那么企业内各部门也是如此,特别是在一些制程较短,关联性较低的企业中,普遍实施计件工资,那么从最基础的员工开始就有多做、早做,甚至偷做的动力,在这种情况下,告知企业里所有人早(多)做是罪恶当然得不到掌声回应。那么我们就来看看制造过早(多)的浪费。 制造过早(多)浪费的后果主要有三大类。
1.直接财务问题。表现为库存、在制品增加,资金回转率低,制造时间变长,占用资金及利息,会造成库存空间的浪费,在现金流量表上很明显。 2.产生次生问题。会产生搬运、堆积的浪费;先进先出的工作产生困难;产品积压造成不良发生,物流阻塞制程时间变长,现场工作空间变小,有滞留在库的风险,有不良品的风险。 3.掩盖问题。为什么“制造过早(多)浪费是八大浪费中的首恶,在精益生产中则被视为最大的浪费”因为它带给人们一个安心的错觉,掩盖了各种问题,以及隐藏了由于等待所带来的浪费,没有改善的动力,失去了持续改善的时机。 1.制造过早(多)浪费的产生原因。 (1)生产计划方面。 1)信息准确度问题。信息不准,计划失当,信息传递不准确,导致生产计划作业进行盲目,最终导致制造过早(多)浪费的产生。 2)生产计划管控机制方面。让某些制程、生产线、工站甚至作业员有生产伸缩的充分空间和提高产出的利益驱动。比如有的不排班生产计划,也不排日生产计划,而是排周生产计划,一天内的生产排配权利下放到制程、生产线、工站甚至作业员,这时候如果有多余的产能、人力、设备稼动过剩,则很自然地就会提前安排生产,安排满稼动生产,从而造成制造过早(多)。特别是在某些企业中(如玩具),较有可能安排计件生产,多劳多得,那么过量过早生产的积极性就更大了。 除非在实施了拉动生产的精益企业里面,一般的企业还是用MRP在做推式生产。这时候生产计划的排配,生产进度的精确控制是企划部门最基础的功能,不能因为制造能力弱,各制程衔接性差就放松对生产计划实施进度的管控。 (2)内部制造能力弱的补偿问题。 制造过早(多)多数时候是出于补偿内部制造能力弱的考虑。制造能力弱,特别是制造中的品质差,换型时间长,在市场信息牛鞭效应的驱动下,为了弥补自身能力不足,而提前过量生产以满足客户需求。
精益生产与八大浪费
作者:小江分类:精益生产管理类时间:2014-04-25 15:33:47 大纲: 一、制造过早(多)的浪费二、库存的浪费 三、不良修正的浪费四、加工过剩的浪费 五、搬运的浪费六、动作的浪费 七、等待的浪费八、管理的浪费八大浪费简要版请点击 [ 八大浪费是丰田生产方式中非常重要的一个观念。丰田人认为要消除浪费,持续改善,企业才能保持良性运转,竞争力才会提升。在丰田改善是探入人心的,有个说法就是跟他们谈话5分钟没有听到他们讲3次改善就不算丰田人。改善的对象是浪费,认识浪费是改善的第一步,企业现场林林总总,哪些是有价值的,哪些是浪费,不是一般人可以一目了然的。丰田人在长期作业和改善过程中对于浪费的内容进行了总结,共七种,被称为七种浪费。它们分别是制造过早(多)的浪费、库存的浪费、不良修正的浪费、加工过剩的浪费、搬运的浪费、动作的浪费、等待的浪费共七种。后来人们又加了一种浪费-管理的浪费,合称八种浪费。下面我们从实用性角度剖析这八种浪费。
一、制造过早(多)的浪费 定义:所谓制造过早(多)就是前制程制造太早/过多,大于客户(或后制程)当期的最小需要量。 制造过早(多)浪费是八大浪费中的首恶,在精益生产中则被视为最大的浪费。福特式思维告诉大家,在同样的时间内,生产量越多,效率越高,成本越低,企业越赚钱,所以企业自然有大批量连续生产的初始动力。作为一个整体的企业是如此,那么企业内各部门也是如此,特别是在一些制程较短,关联性较低的企业中,普遍实施计件工资,那么从最基础的员工开始就有多做、早做,甚至偷做的动力,在这种情况下,告知企业里所有人早(多)做是罪恶当然得不到掌声回应。那么我们就来看看制造过早(多)的浪费。 制造过早(多)浪费的后果主要有三大类。 1.直接财务问题。表现为库存、在制品增加,资金回转率低,制造时间变长,占用资金及利息,会造成库存空间的浪费,在现金流量表上很明显。 — 2.产生次生问题。会产生搬运、堆积的浪费;先进先出的工作产生困难;产品积压造成不良发生,物流阻塞制程时间变长,现场工作空间变小,有滞留在库的风险,有不良品的风险。
精益生产之八大浪费篇
精益生产之八大浪费篇 1)提高质量 2)提高生产率 3)减少库存 4)减少生产线 5)减少机器停机时间 6)减少空间 7)降低生产交货 质量管理是不是一个部门或此人,而是对公司的所有成员的共同责任,需要了解的是:从每一个所有小部分来考虑,共同努力,以更好的产品质量知道:下一道工序是客户。 质量是管理出来的,而不是测试出来 精益生产质量管理强调从驾驶者对缺陷产品的发生的预防,机械,模具,工具,材料和生产工艺等,以确保没有不良品。 它强调从源头上保证质量 ■检查每一道工序,对员工的质量意识为重点,发现质量问题 如果一个进程的问题■因为在过程中,不能满足需求,生产线立即停止工作,直到问题得到解决 ■通常是解决问题的个人和集体 考虑设计质量 标准化的产品结构 减少零件数量 零件标准化 第一次是
不要隐藏的股票,以稳定的质量 什么是质量(辅酶Q)的费用 质量成本 访问前成本 评估成本 损失成本 内部损失成本 外部损失成本 自我和互检的工作通常被称为“双重检查”,主要是自我管理的实施。(1)自我和质证进程的实施 一,教育经营者自律,灌输“双检查”的重要性; 乙,在现场不定期抽查,监督的“双重检查”的执行情况; C,有一些问题,强调了“双检查”是符合双方的责任有关。 研发,建立明确的问责制,评估和实施奖励和处罚 一线主管如何与公司的质量好 一)强大的反应能力,以质量和加工能力; 二)了解,下一道工序是顾客; 三)按标准作业规范; 四)车间做自我检查;
f)设备,工具,检测设备的正确使用和维护; 克)组织材料的控制和环境; 八)热爱工作,有高度的责任感; 质量改进和提升网站 1)设施使用各种灯光,广告牌,以显示正常,生产过程 不,提高快速反应能力素质 2)质量信息反馈机制的建立异常 3质量,工程,采购等部门)紧密合作 4)跨部门小组成立,以改善质量 5)PDCA循环使用,以改善和提高质量 七大手法,以提高现场质量--- 清单 分层法 因果图 柏拉图 直方图 控制图 分散 六标准差工具 统计过程控制(SPC),质量功能展开(QFD) 失效模式与效应分析(FMEA),因果矩阵(原因和影响矩阵),英国标准(英国标准),过程能力分析(过程能力分析),
精益生产之如何改善八大浪费
第四章 八大浪費 第一節 浪費概述 精益生產的特點是消除一切浪費,去掉生產中一切無用的東西,精簡產品開發設計,生產,管理中一切不產生附加價值的工作,旨在以最優品質,最低成本和最高效率對市場需求作出最迅速的響應,實現“七個零”的終極目標. 多賺一塊錢不如自己節約一塊錢容易!畢竟,賺錢得看別人的臉色,省錢卻只需要看自己的心意﹗賺 錢之道,首先需要避免浪費,這是毋庸質疑的 .如果不把水桶的漏洞補起來,注入再多的水都無法裝滿水桶.因此,減少浪費就是增加企業利潤,提高競爭力的最佳選擇. 一. 浪費定義 精益生產中的浪費定義與我們平常所說的浪費有許多的差別: 凡是超出增加產品價值所必需的絕對值最少量的物料,設備,人力,場地和時間的部分都是浪費.所以,精益生產所講的浪費不僅僅是指不增加價值的活動,還包括盡管增加價值,但所用的資源超過了“絕對值最少量”的界限的活動. .例如: ,搬 ,因而 都是浪費. 二. 浪費形態 在實際的工作中﹐我們可以從下面三種形態來深入理解浪費的涵義﹕ 7个“零 ”目标 ☆ 零切换浪费 ☆ 零库存 ☆ 零浪费 ☆ 零不良 ☆ 零故障 ☆ 零停滞 ☆ 零事故 精益生产追求的目标
2. 浪費----指有能力,但是未給予充足的工作量的未飽和狀態; 這種形態在實際的工作中主要表現在人員的工作量不飽和,利用率低下;或者機器設備的稼動率過低等方面. 3. 不均衡----指有時超負荷作業,有時又不飽和的狀態. 這種狀態主要表現在各個時間段工作量的差異上面. 三. 八大浪費 精益生產從現場出發,認為工廠中最為常見的浪費主要有八大類,分別是:製造過早(多)的浪費;庫 問題的解決有九 草擬行動 究,以取得較之前更為合理的作業方法與過程,在各個階段中,我們可能用到的手法具體如下表所示: 解決問題的九大步驟
精益生产之_八大浪费.doc
精益生产之_八大浪费1 1.不良、修理的浪费 所谓不良、修理的浪费,指的是由于工厂内出现不良品,需要进行处置的时间、人力、物力上的浪费,以及由此造成的相关损失。这类浪费具体包括:材料的损失、不良品变成废品;设备、人员和工时的损失;额外的修复、鉴别、追加检查的损失;有时需要降价处理产品,或者由于耽误出货而导致工厂信誉的下降。 2.加工的浪费 加工的浪费也叫过分加工的浪费,主要包含两层含义:第一是多余的加工和过分精确的加工,例如实际加工精度过高造成资源浪费;第二是需要多余的作业时间和辅助设备,还要增加生产用电、气压、油等能源的浪费,另外还增加了管理的工时。 3.动作的浪费 动作的浪费现象在很多企业的生产线中都存在,常见的动作浪费主要有以下12种:两手空闲、单手空闲、作业动作突然停止、作业动作过大、左右手交换、步行过多、转身的角度太大,移动中变换“状态”、不明技巧、伸背动作、弯腰动作以及重复动作和不必要的动作等,这些动作的浪费造成了时间和体力上的不必要消耗。 4.搬运的浪费 从精益生产的角度看,搬运是一种不产生附加价值的动作,而不产生价值的工作都属于浪费。搬运的浪费具体表现为放置、
堆积、移动、整列等动作浪费,由此带来物品移动所需空间的浪费、时间的浪费和人力工具的占用等不良后果。 国内目前有不少企业管理者认为搬运是必要的,不是浪费。因此,很多人对搬运浪费视而不见,更谈不上去消灭它。也有一些企业利用传送带或机器搬运的方式来减少人工搬运,这种做法是花大钱来减少工人体力的消耗,实际上并没有排除搬运本身的浪费。 5.库存的浪费 按照过去的管理理念,人们认为库存虽然是不好的东西,但却是必要的。精益生产认为,库存是没有必要的,甚至认为库存是万恶之源。由于库存很多,将故障、不良品、缺勤、点点停、计划有误、调整时间过长、品质不一致、能力不平衡等问题全部掩盖住了。 例如,工厂生产线出现故障,造成停机、停线,但由于有库存而不至于断货,这样就将故障造成停机、停线的问题掩盖住了,耽误了故障的排除。如果降低库存,就能将上述问题彻底暴露于水平面,进而能够逐步地解决这些库存浪费。 6.制造过多过早的浪费 制造过多或过早,提前用掉了生产费用,不但没有好处,还隐藏了由于等待所带来的浪费,失去了持续改善的机会。有些企业由于生产能力比较强大,为了不浪费生产能力而不中断生产,增加了在制品,使得制品周期变短、空间变大,还增加了搬运、堆积的浪费。此外,制造过多或过早,会带来庞大的库存量,利
精益生产管理八大浪费与解决方法(详细版)4.doc
精益生产管理八大浪费与解决方法(详细 版)4 大纲: (一)制造过早(多)的浪费(二)库存的浪费 (三)不良修正的浪费(四)加工过剩的浪费 (五)搬运的浪费(六)动作的浪费 (七)等待的浪费(八)管理的浪费 八大浪费是丰田生产方式中非常重要的一个观念。丰田人认为要消除浪费,持续改善,企业才能保持良性运转,竞争力才会提升。在丰田改善是探入人心的,有个说法就是跟他们谈话5分钟没有听到他们讲3次改善就不算丰田人。改善的对象是浪费,认识浪费是改善的第一步,企业现场林林总总,哪些是有价值的,哪些是浪费,不是一般人可以一目了然的。丰田人在长期作业和改善过程中对于浪费的内容进行了总结,共七种,被称为七种浪费。它们分别是制造过早(多)的浪费、库存的浪费、不良修正的浪费、加工过剩的浪费、搬运的浪费、动作的浪费、等待的浪费共七种。后来人们又加了一种浪费-管理的浪费,合称八种浪费。下面我们从实用性角度剖析这八种浪费。 (一)制造过早(多)的浪费 定义:所谓制造过早(多)就是前制程制造太早/过多,大于客户(或后制程)当期的最小需要量。
制造过早(多)浪费是八大浪费中的首恶,在精益生产中则被视为最大的浪 费。福特式思维告诉大家,在同样的时间内,生产量越多,效率越高,成本越低,企业越赚钱,所以企业自然有大批量连续生产的初始动力。作为一个整体的企业是如此,那么企业内各部门也是如此,特别是在一些制程较短,关联性较低的企业中,普遍实施计件工资,那么从最基础的员工开始就有多做、早做,甚至偷做 的动力,在这种情况下,告知企业里所有人早(多)做是罪恶当然得不到掌声回应。那么我们就来看看制造过早(多)的浪费。 制造过早(多)浪费的后果主要有三大类。 1.直接财务问题。表现为库存、在制品增加,资金回转率低,制造时间变长,占用资金及利息,会造成库存空间的浪费,在现金流量表上很明显。 2.产生次生问题。会产生搬运、堆积的浪费;先进先出的工作产生困难;产品积压造成不良发生,物流阻塞制程时间变长,现场工作空间变小,有滞留在库的风险,有不良品的风险。 3.掩盖问题。为什么“制造过早(多)浪费是八大浪费中的首恶,在精益生产中则被视为最大的浪费”?因为它带给人们一个安心的错觉,掩盖了各种间题,以及隐藏了由于等待所带来的浪费,没有改善的动力,失去了持续改善的时机。 1.制造过早(多)浪费的产生原因。
精益生产与八大浪费
精益生产与八大浪费-标准化文件发布号:(9556-EUATWK-MWUB-WUNN-INNUL-DDQTY-KII
作者:小江分类:精益生产管理类时间:2014-04-25 15:33:47 大纲: 一、制造过早(多)的浪费二、库存的浪费 三、不良修正的浪费四、加工过剩的浪费 五、搬运的浪费六、动作的浪费 七、等待的浪费八、管理的浪 费八大浪费简要版请点击 八大浪费是丰田生产方式中非常重要的一个观念。丰田人认为要消除浪费,持续改善,企业才能保持良性运转,竞争力才会提升。在丰田改善是探入人心的,有个说法就是跟他们谈话5分钟没有听到他们讲3次改善就不算丰田人。改善的对象是浪费,认识浪费是改善的第一步,企业现场林林总总,哪些是有价值的,哪些是浪费,不是一般人可以一目了然的。丰田人在长期作业和改善过程中对于浪费的内容进行了总结,共七种,被称为七种浪费。它们分别是制造过早(多)的浪费、库存的浪费、不良修正的浪费、加工过剩的浪费、搬运的浪费、动作的浪费、等待的浪费共七种。后来人们又加了一种浪费-管理的浪费,合称八种浪费。下面我们从实用性角度剖析这八种浪费。
一、制造过早(多)的浪费 定义:所谓制造过早(多)就是前制程制造太早/过多,大于客户(或后制程)当期的最小需要量。 制造过早(多)浪费是八大浪费中的首恶,在精益生产中则被视为最大的浪费。福特式思维告诉大家,在同样的时间内,生产量越多,效率越高,成本越低,企业越赚钱,所以企业自然有大批量连续生产的初始动力。作为一个整体的企业是如此,那么企业内各部门也是如此,特别是在一些制程较短,关联性较低的企业中,普遍实施计件工资,那么从最基础的员工开始就有多做、早做,甚至偷做的动力,在这种情况下,告知企业里所有人早(多)做是罪恶当然得不到掌声回应。那么我们就来看看制造过早(多)的浪费。 制造过早(多)浪费的后果主要有三大类。 1.直接财务问题。表现为库存、在制品增加,资金回转率低,制造时间变长,占用资金及利息,会造成库存空间的浪费,在现金流量表上很明显。 2.产生次生问题。会产生搬运、堆积的浪费;先进先出的工作产生困难;产品积压造成不良发生,物流阻塞制程时间变长,现场工作空间变小,有滞留在库的风险,有不良品的风险。 3.掩盖问题。为什么“制造过早(多)浪费是八大浪费中的首恶,在精益生产中则被视为最大的浪费”因为它带给人们一个安心的错觉,掩盖了各种问
精益生产管理八大浪费与解决方法
精益生产管理八大浪费与解决方法(详细 版) 大纲: 一、制造过早(多)的浪费三、不良修正的浪费 五、搬运的浪费 七、等待的浪费、库存的浪费 四、加工过剩的浪费 六、动作的浪费 八、管理的浪费 八大浪费是丰田生产方式中非常重要的一个观念。丰田人认为要消除浪费,持续改善,企业才能保持良性运转,竞争力才会提升。在丰田改善是探入人心的,有个说法就是跟他们谈话5分钟没有听到他们讲3次改善就不算丰田人。改善的对象是浪费,认识浪费是改善的第一步,企业现场林林总总,哪些是有价值的,哪些是浪费,不是一般人可以一目了然的。丰田人在长期作业和改善过程中对于浪费的内容进行了总结,共七种,被称为七种浪费。它们分别是制造过早(多)的浪费、库存的浪费、不良修正的浪费、加工过剩的浪费、搬运的浪费、动作的 浪费、等待的浪费共七种。后来人们又加了一种浪费-管理的浪费,合称八种浪F面我们从实用性角度剖析这八种浪费 工 厂常 见的八 大 浪 费 等待浪费] 邈亘良更] 不良浪费I 动作浪费 加工浪费 库存浪费 制造过多(过早)浪费] 事后骨理浪費 一、制造过早(多)的浪费 定义:所谓制造过早(多)就是前制程制造太早/过多,大于客户(或后制程)当期的最小需要量。
制造过早(多)浪费是八大浪费中的首恶,在精益生产中则被视为最大的浪费。福特式思维告诉大家,在同样的时间内,生产量越多,效率越高, 成本越低,企业越赚钱,所以企业自然有大批量连续生产的初始动力。作为一个整体的企业是如此,那么企业内各部门也是如此,特别是在一些制程较短,关联性较低的企业中,普遍实施计件工资,那么从最基础的员工开始就有多做、早做,甚至偷做的动力,在这种情况下,告知企业里所有人早(多)做是罪恶当然得不到掌声回应。那么我们就来看看制造过早(多)的浪费。 制造过早(多)浪费的后果主要有三大类。 1.直接财务问题。表现为库存、在制品增加,资金回转率低,制造时间变长,占用资金及利息,会造成库存空间的浪费,在现金流量表上很明显。 2.产生次生问题。会产生搬运、堆积的浪费;先进先出的工作产生困难;产 品积压造成不良发生,物流阻塞制程时间变长,现场工作空间变小,有滞留在库的风险,有不良品的风险。 3.掩盖问题。为什么制造过早(多)浪费是八大浪费中的首恶,在精益生产中则被视为最大的浪费”因为它带给人们一个安心的错觉,掩盖了各种问题,以及隐藏了由于等待所带来的浪费,没有改善的动力,失去了持续改善的时机。 1.制造过早(多)浪费的产生原因。 (1)生产计划方面。 1)信息准确度问题。信息不准,计划失当,信息传递不准确,导致生产计划作业进行盲目,最终导致制造过早(多)浪费的产生。 2)生产计划管控机制方面。让某些制程、生产线、工站甚至作业员有生产伸缩的充分空间和提高产出的利益驱动。比如有的不排班生产计划,也不排日生产计划,而是排周生产计划,一天内的生产排配权利下放到制程、生产线、工站甚至作业员,这时候如果有多余的产能、人力、设备稼动过剩,则很自然地就会提前安排生产,安排满稼动生产,从而造成制造过早(多)。特别是在某些企业 中(如玩具),较有可能安排计件生产,多劳多得,那么过量过早生产的积极性就更大了。 除非在实施了拉动生产的精益企业里面,一般的企业还是用MRPt做推式生产。这时候生产计划的排配,生产进度的精确控制是企划部门最基础的功能,不能因为制造能力弱,各制程衔接性差就放松对生产计划实施进度的管控。
精益生产和工厂常见的八大浪费
《精益生产之JIT实务》培训讲义(节选)【课程目录】 第一讲推行JIT的必要性 1.厂里最常见的八大浪费 2. JIT简介 第二讲新经理上任秘籍 1.进式控制系统与拉动式控制系统 2.JIT生产计划 第三讲优秀部门经理角色认知 1.看板的机能和使用规则 2.看板的种类 3.看板组织生产过程 第四讲如何与上司正确相处 1.“一个流”生产概述 2.“一个流”生产的八大要素 3. 缩短作业切换时间 第五讲如何带领部属(上) 1. 实施柔性化生产所采取的措施 2. 弹性的作业人数 第六讲如何带领部属(中) 1. 进行生产均衡化的原因 2. 生产均衡化的好处 3. 生产均衡化在企业里的运用 第七讲如何带领部属(下) 1. 准时制采购的目的 2. 准时制采购的特点 3.供应商的选择与评鉴 第八讲权力与威信
1. 传统品质管理与JIT的品质管理 2. JIT生产的要求 3. 关于设备的保养 第九讲如何做优秀的教练 1. 适合推行JIT生产方式的国内企业 2. 推行JIT生产方式的要点 第十讲冲突处理 1. 嘉陵股份有限公司JIT生产方式 2. 东莞某外资企业推行JIT案例 广东某涂料企业JIT不完全推行案例 【内容摘要】 第1讲推行JIT的必要性 【本讲重点】 工厂中常见的八大浪费 什么是JIT生产方式 工厂中常见的八大浪费 浪费的定义 在JIT生产方式中,浪费的含义与社会上通常所说的浪费有所区别。对于JIT来讲,凡是 超出增加产品价值所绝对必须的最少量的物料、设备、人力、场地和时间的部分都是浪费。因此,JIT生产方式所讲的浪费不仅仅是指不增加价值的活动,还包括所用资源超过“绝 对最少”界限的活动。 各种各样的浪费现象在很多尚未实行5S活动的企业中普遍存在,如表1-1所示。为了杜 绝工厂中的浪费现象,首先需要发现不合理的地方,然后才是想办法解决问题,这就需要 推行5S、JIT等较为先进的管理方法。 表1-1
精益生产中的八大浪费和五大原则
精益生产中的八大浪费和五大原则 2014-7-31 16:13:05 互联网 企业生产管理过程中,出现许多的浪费现象,这些浪费严重占用了企业的流动资金,丰田公司对这些浪费定义为精益生产中的八大浪费。分别是: 1、生产过剩。过早或过多地生产出产品,这通常会造成其他的浪费,例如人员过多、因存货过多而导致储存与输送成本。存货可能指的是实物存货,或是排队等候的大批信息。 2、在现场等候的时间。员工只是在一旁监视自动化机器,还是必须站在一旁等候下一个处理步骤、工具、供应、零部件等,或是因为存货用完、整批处理延迟、机器设备停工、生产力停滞不前等因素造成员工暂时没有工作可做。 3、不必要的运输。在流程中把在制品从一地搬运到另一地(即便只是短距离);或是必须进出仓库或在流程之间搬运原材料、零部件或最终成品。 4、过度处理或不正确的处理。采取不必要的步骤以处理零部件;因为工具与产品设计不良,导致不必要的动作及产生瑕疵而造成缺乏效率的处理;当产品超出必要的质量时,也会造成浪费。有时,必须做一些额外的“工作”,以填补多出的时间,避免无所事事地等候。 5、存货过剩。过多的原材料、在制品或者最终的成品,导致较长的提前期,堆积过时品、毁损品、较高的运输与储存成本及延迟。此外,过多的存货还造成其他的隐性问题,例如生产不均衡、供应者延迟递送、瑕疵品、机器设备停工、拉长准备期等。 6、不必要的移动搬运。员工在执行工作的过程中,必须做一些不必要、不能创造价值的动作,例如寻找、前往取得或堆放零部件和工具等等。此外,走动也是浪费。 7、瑕疵。生产出瑕疵品或必须修改的东西。修理或重做、报废、更换、检验等都代表浪费的处理、时间和精力。 8、未被使用的员工创造力。由于未使员工参与未能倾听员工意见而造成未能善用员工的时间、构想、技能,从而使员工失去改进和学习的机会。 精益生产的五个原则: 1、价值观:精益生产认为产品的价值需由最终的用户来确定,价值只有满足特定的用户需求才有存在的意义。 2、价值流:是指从原材料到成品赋予价值的全部活动。识别价值流是精益生产的起步点,并按照最终用户立场寻求全过程的整体最佳状态。 3、流动:精益生产强调要求各个创造价值的活动需要流动起来,强调的是动。 4、拉动:拉动生产亦即按用户需求拉动生产,而不是把产品强行推给用户。 5、尽善尽美:用尽善尽美的价值创造过程为用户提供尽善尽美的价值。 综上所述,这些浪费的存在降低了企业的生产效率,降低生产产品的
精益生产八大浪费
精益生产八大浪费 精益生产的管理模式中,不是工作越多越有价值,而是浪费越少越有价值。 精益生产八大浪费包括:产品缺陷、过量生产、等待时间、运输、库存、过程、动作以及忽视员工创造力。下面带我们简单了解一下: 第一是产品缺陷浪费,很容易理解吧。 第二是过量生产,生产大量产品卖不出去是种浪费,‘10号要的东西,1号就做出来,这是浪费,因为这10天是没人给你付钱的,要占用你的资金场地,还有风险’。 第三是等待浪费,一切形式的等待都是浪费,领导的职位越高造成的等待浪费越大,‘这事为什么还没有处理啊,等着领导签字呢’。‘等待’不仅仅是等物料、等设备,还有等检验、批准。人才没有利用好也是浪费,我们不多说了。 还有运输浪费,我们物流发展趋势是包装原料厂在我们公司周边建厂,运输是浪费、不增值的,这也是为什么珠三角招商引资多,因为它二十公里内几乎所有材料都能买到。这也是浦东机场的建立给昆山的电子行业造成重大损失原因。因为原来电子芯片都是空运到虹桥机场,虹桥机场距离昆山特别近,浦东机场远了,就远了两个小时的车程,但电子厂品运转的很快,这个距离就给昆山造成很大损失。 精益是从系统上看问题。库存、多余的动作也是浪费。还有一个是过度加工是浪费,如果我们的产品比客户要求的更多,是不是浪费?如果我们给客户做的更多,但是没有给客户带来价值,这就是浪费;如果给客户带来价值,就不是浪费。老年手机为什么便宜,因为它不要求太多功能,只要求字大一点、声音高一点,这样做是不是降低成本。如果把苹果给老人,他头大了,不会用。 日本Kaizen:不花钱的改善,小的改善,持续的改善。真的有不花钱的改善吗?日本以前有很多番茄酱企业,如何让自己的多卖钱呢?提高产品质量,但是差异很小,然后有一个员工发现,但是商场里面的番茄酱瓶子口很小,做饭时需要用小勺挖好几次,很不方便。后来他就建议把番茄酱的瓶口制作成广口瓶,这样可以用大勺挖一次就够了。结果变成大口以后,他们产品销量一下就上去了。这样的改善需要花钱吗?不需要,却取得了很好的收益。这样的建议都是普通工人提出来的,不是科研人员工程师提出来的,这样的例子还有很多,这里不多讲了。
精益生产管理八大浪费与解决方法(详细版)
精益生产管理八大浪费与解决方法 八大浪费是丰田生产方式中非常重要的一个观念。丰田人认为要消除浪费,持续改善,企业才能保持良性运转,竞争力才会提升。在丰田改善是探入人心的,有个说法就是跟他们谈话5分钟没有听到他们讲3次改善就不算丰田人。改善的对象是浪费,认识浪费是改善的第一步,企业现场林林总总,哪些是有价值的,哪些是浪费,不是一般人可以一目了然的。丰田人在长期作业和改善过程中对于浪费的内容进行了总结,共七种,被称为七种浪费。它们分别是制造过早(多)的浪费、库存的浪费、不良修正的浪费、加工过剩的浪费、搬运的浪费、动作的浪费、等待的浪费共七种。后来人们又加了一种浪费-管理的浪费,合称八种浪费。下面我们从实用性角度剖析这八种浪费。 一、精益生产管理中制造过早(多)的浪费 定义:所谓制造过早(多)就是前制程制造太早/过多,大于客户(或后制程)当期的最小需要量。 制造过早(多)浪费是八大浪费中的首恶,在精益生产中则被视为最大的浪费。福特式思维告诉大家,在同样的时间内,生产量越多,效率越高,成本越低,企业越赚钱,所以企业自然有大批量连续生产的初始动力。作为一个整体的企业
是如此,那么企业内各部门也是如此,特别是在一些制程较短,关联性较低的企业中,普遍实施计件工资,那么从最基础的员工开始就有多做、早做,甚至偷做的动力,在这种情况下,告知企业里所有人早(多)做是罪恶当然得不到掌声回应。那么我们就来看看制造过早(多)的浪费。 制造过早(多)浪费的后果主要有三大类。 1.直接财务问题。表现为库存、在制品增加,资金回转率低,制造时间变长,占用资金及利息,会造成库存空间的浪费,在现金流量表上很明显。 2.产生次生问题。会产生搬运、堆积的浪费;先进先出的工作产生困难;产品积压造成不良发生,物流阻塞制程时间变长,现场工作空间变小,有滞留在库的风险,有不良品的风险。 3.掩盖问题。为什么“制造过早(多)浪费是八大浪费中的首恶,在精益生产中则被视为最大的浪费”?因为它带给人们一个安心的错觉,掩盖了各种问题,以及隐藏了由于等待所带来的浪费,没有改善的动力,失去了持续改善的时机。 1.制造过早(多)浪费的产生原因。 (1)生产计划方面。 1)信息准确度问题。信息不准,计划失当,信息传递不准确,导致生产计划作业进行盲目,最终导致制造过早(多)浪费的产生。 2)生产计划管控机制方面。让某些制程、生产线、工站甚至作业员有生产伸缩的充分空间和提高产出的利益驱动。比如有的不排班生产计划,也不排日生产计划,而是排周生产计划,一天内的生产排配权利下放到制程、生产线、工站甚至作业员,这时候如果有多余的产能、人力、设备稼动过剩,则很自然地就会提前安排生产,安排满稼动生产,从而造成制造过早(多)。特别是在某些企业
【详细版】精益生产的八大浪费、产生原因和消除方法
『原创』精益生产的八大浪费、产生原因和消除方法(详细版)大纲: 一、制造过早(多)的浪费二、库存的浪费 三、不良修正的浪费四、加工过剩的浪费 五、搬运的浪费六、动作的浪费 七、等待的浪费八、管理的浪费 八大浪费是丰田生产方式中非常重要的一个观念。丰田人认为要消除浪费,持续改善,企业才能保持良性运转,竞争力才会提升。在丰田改善是探入人心的,有个说法就是跟他们谈话5分钟没有听到他们讲3次改善就不算丰田人。改善的对象是浪费,认识浪费是改善的第一步,企业现场林林总总,哪些是有价值的,哪些是浪费,不是一般人可以一目了然的。丰田人在长期作业和改善过程中对于浪费的内容进行了总结,共七种,被称为七种浪费。它们分别是制造过早(多)的浪费、库存的浪费、不良修正的浪费、加工过剩的浪费、搬运的浪费、动作的浪费、等待的浪费共七种。后来人们又加了一种浪费-管理的浪费,合称八种浪费。下面我们从实用性角度剖析这八种浪费。 一、精益生产管理中制造过早(多)的浪费
定义:所谓制造过早(多)就是前制程制造太早/过多,大于客户(或后制程)当期的最小需要量。 制造过早(多)浪费是八大浪费中的首恶,在精益生产中则被视为最大的浪费。福特式思维告诉大家,在同样的时间内,生产量越多,效率越高,成本越低,企业越赚钱,所以企业自然有大批量连续生产的初始动力。作为一个整体的企业是如此,那么企业内各部门也是如此,特别是在一些制程较短,关联性较低的企业中,普遍实施计件工资,那么从最基础的员工开始就有多做、早做,甚至偷做的动力,在这种情况下,告知企业里所有人早(多)做是罪恶当然得不到掌声回应。那么我们就来看看制造过早(多)的浪费。 制造过早(多)浪费的后果主要有三大类。 1.直接财务问题。表现为库存、在制品增加,资金回转率低,制造时间变长,占用资金及利息,会造成库存空间的浪费,在现金流量表上很明显。 2.产生次生问题。会产生搬运、堆积的浪费;先进先出的工作产生困难;产品积压造成不良发生,物流阻塞制程时间变长,现场工作空间变小,有滞留在库的风险,有不良品的风险。 3.掩盖问题。为什么“制造过早(多)浪费是八大浪费中的首恶,在精益生产中则被视为最大的浪费”?因为它带给人们一个安心的错觉,掩盖了各种问题,以及隐藏了由于等待所带来的浪费,没有改善的动力,失去了持续改善的时机。 1.制造过早(多)浪费的产生原因。 (1)生产计划方面。 1)信息准确度问题。信息不准,计划失当,信息传递不准确,导致生产计划作业进行盲目,最终导致制造过早(多)浪费的产生。 2)生产计划管控机制方面。让某些制程、生产线、工站甚至作业员有生产伸缩的充分空间和提高产出的利益驱动。比如有的不排班生产计划,也不排日生产计划,而是排周生产计划,一天内的生产排配权利下放到制程、生产线、工站甚至作业员,这时候如果有多余的产能、人力、设备稼动过剩,则很自然地就会提前安排生产,安排满稼动生产,从而造成制造过早(多)。特别是在某些企业中(如玩具),较有可能安排计件生产,多劳多得,那么过量过早生产的积极性就更大了。 除非在实施了拉动生产的精益生产管理企业里面,一般的企业还是用MRP在做推式生产。这时候生产计划的排配,生产进度的精确控制是企划部门最基础的功能,不能因为制造能力弱,各制程衔接性差就放松对生产计划实施进度的管控。 (2)内部制造能力弱的补偿问题。
精益生产八大浪费五大原则
精益生产中的八大浪费和五大原则 企业生产管理过程中,出现许多的浪费现象,这些浪费严重占用了企业的流动资金,丰田公司对这些浪费定义为精益生产中的八大浪费。分别是: 1、生产过剩。过早或过多地生产出产品,这通常会造成其他的浪费,例如人员过多、因存货过多而导致储存与输送成本。存货可能指的是实物存货,或是排队等候的大批信息。 2、在现场等候的时间。员工只是在一旁监视自动化机器,还是必须站在一旁等候下一个处理步骤、工具、供应、零部件等,或是因为存货用完、整批处理延迟、机器设备停工、生产力停滞不前等因素造成员工暂时没有工作可做。 3、不必要的运输。在流程中把在制品从一地搬运到另一地(即便只是短距离);或是必须进出仓库或在流程之间搬运原材料、零部件或最终成品。 4、过度处理或不正确的处理。采取不必要的步骤以处理零部件;因为工具与产品设计不良,导致不必要的动作及产生瑕疵而造成缺乏效率的处理;当产品超出必要的质量时,也会造成浪费。有时,必须做一些额外的“工作”,以填补多出的时间,避免无所事事地等候。 5、存货过剩。过多的原材料、在制品或者最终的成品,导致较长的提前期,堆积过时品、毁损品、较高的运输与储存成本及延迟。此外,过多的存货还造成其他的隐性问题,例如生产不均衡、供应者延迟递送、瑕疵品、机器设备停工、拉长准备期等。 6、不必要的移动搬运。员工在执行工作的过程中,必须做一些不必要、不能创造价值的动作,例如寻找、前往取得或堆放零部件和工具等等。此外,走动也是浪费。 7、瑕疵。生产出瑕疵品或必须修改的东西。修理或重做、报废、更换、检验等都代表浪费的处理、时间和精力。 8、未被使用的员工创造力。由于未使员工参与未能倾听员工意见而造成未能善用员工的时间、构想、技能,从而使员工失去改进和学习的机会。 精益生产的五个原则: 1、价值观:精益生产认为产品的价值需由最终的用户来确定,价值只有满足特定的用户需求才有存在的意义。 2、价值流:是指从原材料到成品赋予价值的全部活动。识别价值流是精益生产的起步点,并按照最终用户立场寻求全过程的整体最佳状态。 3、流动:精益生产强调要求各个创造价值的活动需要流动起来,强调的是动。 4、拉动:拉动生产亦即按用户需求拉动生产,而不是把产品强行推给用户。 5、尽善尽美:用尽善尽美的价值创造过程为用户提供尽善尽美的价值。 综上所述,这些浪费的存在降低了企业的生产效率,降低生产产品的品质,提高了企业的生产成本,因此企业想要发展壮大就必须要把这八大浪费消除,而实施精益生产管理是消除这些的重要手段。