4线切分轧制技术分析
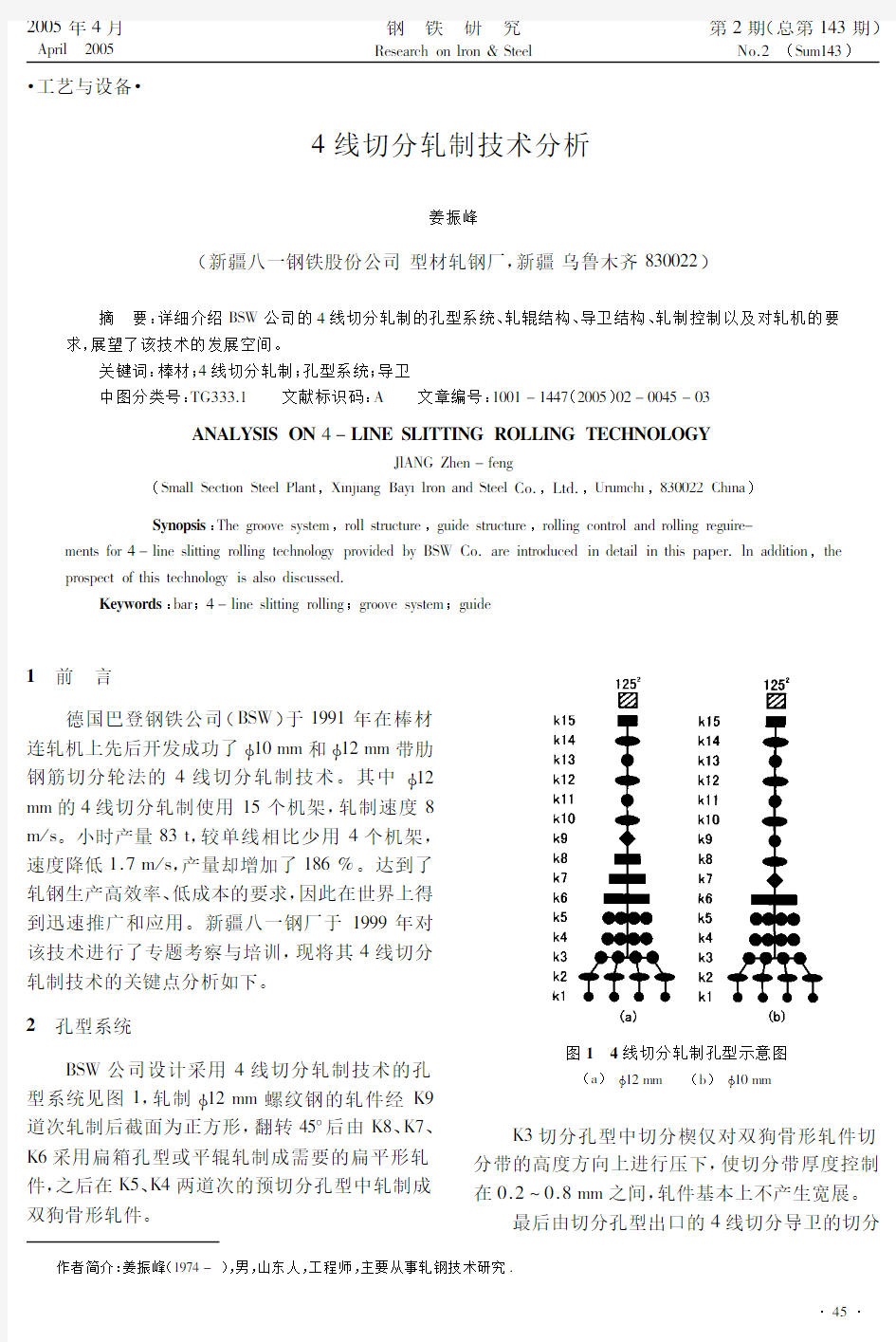

2005年4月
ApriI 2005
钢铁研究Research on Iron &SteeI
第2期(总第143期)
No.2(Sum143)
?工艺与设备?
4线切分轧制技术分析
姜振峰
(新疆八一钢铁股份公司型材轧钢厂,新疆乌鲁木齐830022)
摘
要:详细介绍BSW 公司的4线切分轧制的孔型系统、轧辊结构、导卫结构、轧制控制以及对轧机的要
求,展望了该技术的发展空间。
关键词:棒材;4线切分轧制;孔型系统;导卫中图分类号:TG333.1
文献标识码:A
文章编号:1001-1447(2005)02-0045-03
ANALYSIS ON 4-LINE SLITTING ROLLING TECHNOLOGY
JIANG Zhen -feng
(SmaII Section SteeI PIant ,Xinjiang Bayi Iron and SteeI Co.,Ltd.,Urumchi ,830022China )Synopsis :The groove system ,roII structure ,guide structure ,roIIing controI and roIIing reguire-ments for 4-Iine sIitting roIIing technoIogy provided by BSW Co.are introduced in detaiI in this paper.In addition ,the prospect of this technoIogy is aIso discussed.
Keywords :bar ;4-Iine sIitting roIIing ;groove system ;guide
作者简介:姜振峰(1974-),男,山东人,工程师,主要从事轧钢技术研究.
1前言
德国巴登钢铁公司(BSW )于1991年在棒材
连轧机上先后开发成功了!10mm 和!12mm 带肋钢筋切分轮法的4线切分轧制技术。其中!12
mm 的4线切分轧制使用15个机架,
轧制速度8m /s 。小时产量83t ,
较单线相比少用4个机架,速度降低1.7m /s ,产量却增加了186%。达到了轧钢生产高效率、低成本的要求,因此在世界上得到迅速推广和应用。新疆八一钢厂于1999年对该技术进行了专题考察与培训,现将其4线切分轧制技术的关键点分析如下。2
孔型系统
BSW 公司设计采用4线切分轧制技术的孔型系统见图1,轧制!12mm 螺纹钢的轧件经K9道次轧制后截面为正方形,翻转45 后由K8、K7、K6采用扁箱孔型或平辊轧制成需要的扁平形轧件,之后在K5、K4两道次的预切分孔型中轧制成双狗骨形轧件。
图14线切分轧制孔型示意图
(a )!12mm
(b )!10mm
K3切分孔型中切分楔仅对双狗骨形轧件切
分带的高度方向上进行压下,使切分带厚度控制在0.2~0.8mm 之间,轧件基本上不产生宽展。
最后由切分孔型出口的4线切分导卫的切分
?
54
?
轮将轧件切分成4个单体。切分!10mm螺纹钢时,轧件断面小,仅用1道扁箱孔型。值得注意的是,该工艺在切分孔型后仅有两道必要的成形工艺,减少了轧制道次。
3轧机结构及布置
4线切分技术对轧机精度要求较高,切分时辊跳值要小于0.3mm,轧辊轴向窜动要小于0.1 mm。BSW公司使用的轧机为自行改造的预应力轧机,上下轴承座可分离预装,靠4根拉杆坚固并预加应力。若使用刚度大、应力线超短的短应力线轧机效果会更好。
BSW公司棒材线共有15架轧机,布置形式为粗轧7架,精轧8架。粗轧机组布局紧凑,单槽轧制,其中1、2架水平布置,辊径!560mm,3~7架平-立交替布置,辊径!470mm。精轧机组8架均为水平布置,辊径!350mm,13~15架轧机间设置有2个允许轧件4线通过的活套器。
4组合轧辊结构
BSW公司为解决4线切分轧制时轧槽磨损快,精度难控制的问题,在K1、K2使用钴(质量分数)达30的Kafix碳化钨硬质合金组合轧辊,K3使用Kafix高速钢组合轧辊。
图2Kafix组合轧辊的结构
1.轧辊轴
2.隔离环
3.碳化钨辊环
4.多楔锁紧环
5.液压螺母
6.迷宫
7.液压螺母活塞
8.压力环
Kafix组合轧辊的辊环与轧辊轴的连接采用液压锁紧设计,轧辊结构见图2。这种连接方式成功地解决了使用整体碳化钨辊环受冲击时易碎裂的难题。安装时在一根带轴肩的锻钢辊轴上,用一高压液压螺母(压力>200Mpa)将几片碳化钨辊环和隔离环固定在轧辊轴上,通过一特殊设计的多楔锁紧环将压力传递到辊环的端面,靠压力产生的摩擦力轧制力矩。这样在轧制过程中,辊环的4个接触面均处于压应力状态,最大限度地避免了辊环受冲击破碎。
多楔锁紧环的作用是消除压力环和液压螺母之间的间隙。在辊环、隔离环、压力环、锁紧环、液压螺母均安装到位后,给液压螺母打压200~250 Mpa,轧辊轴和辊环受到约400kN的预紧力。液压螺母通过活塞将压力传递到辊轴外侧的压力环上,高压使压力环和液压螺母缸体之间产生间隙,旋转中间的多楔锁紧环填充该间隙,卸压后使该压力永久保持[1]。
5切分次序
在使用切分轮法4线切分轧制时,轧件切分次序的选择极为重要。BSW公司的生产实践表明,最佳的4线切分次序如图3所示,出切分孔型K3的轧件中间部分的连接带SI要第一步切分,使之一分为二。第二步同时切分外侧的两个连接带S2,使轧件分为4根。
图3四线切分轧制的切分次序图
这种切分次序满足了轧件切分过程中要对称受力、对称分配面积的要求,轧制最为稳定。
6切分导卫结构
4线切分轧制除孔型设计外,最重要的是切分导卫的应用。
6.1K3切分入口导卫结构
BSW公司K3切分孔型的4线切分入口导卫的结构见图4,导卫主要由导卫体、支臂和导板组成。
轧制中轧件进入导板后即受到第一列导辊夹持,耐磨滑块1限制其抖动和扭转,之后轧件再度受到第二列导辊和耐磨滑块2进一步夹持和限制,使轧件能够完全消除抖动和扭转直到进入轧机的切分孔型。这种重复组合的摩擦方式,最大限度地保证了轧件运行的稳定性和轧件导入孔型的精确度,满足了孔型精确切分的需要。
?
6
4
?
图44线切分入口导卫示意图
l.导板 2.第一列导辊 3.导卫体 4.耐磨滑块l
5.支臂
6.耐磨滑块2
7.第二列导辊
6.24线切分出口导卫结构
4线切分出口导卫的结构主要由导卫体、切分插件、切分轮、分料盒组成,见图5。
图54线切分出口导卫示意图
l.分料盒 2.导卫体 3.第二列切分轮 4.调节螺栓
5.第一列切分轮
6.插件
切分插件直接连接轧辊切分孔型,第一列切分轮的中间有一组切分楔,见图6(a),将通过的4根并联轧件从中部一分为二,进入第二列切分轮。第二列切分轮有两组切分楔,见图6(b),分布在切分轮的两侧,使通过的轧件再次一分为二,变成4个单根轧件,进入分料盒。
图6切分轮结构示意图
(a)第一列切分轮(b)第二列切分轮
l.轮轴 2.切分楔 3.轴承座
分料盒内有3个导向楔,限制4根轧件的行
走位置,保证轧制顺利进行。4线切分出口导卫的设计非常紧凑,结构合理,底座尺寸可随意改变,能安装在各种导卫横梁上。
7生产调整及控制
(l)孔型充满度控制。设计预切和切分孔型应特别注意孔型4部分面积的配比,根据中间2根轧件与边部轧件温度与受力的不同,中间2孔的面积应比边部小约5%。实际调整时,要严格控制辊缝,K5、K4预切孔应保证93%以上的孔型充满度,K3切分孔应保证95%以上的孔型试验度,禁止带“耳子”轧制。
(2)导卫的对中。4线切分轧制时,切分出口导卫是最容易出问题的地方,要求预切分及切分孔型入口导卫必须严格对中轧线和孔型,确保切分出口导卫的顺利切分,并随时检查导卫的间隙和磨损状况。
(3)活套及张力控制。4线切分轧制时,切分后易出现4根轧件的起套高度有差异。主要原因是:
(l)冷却水使4根轧件产生的温降不同;(2)轧件进入切分轮位置先后的不同;(3)边部轧件温度低于中间的2根轧件,使边部轧件的拉伸应力大于中间轧件。若对成品长度造成影响,应及时调整导卫和水量。同时调整各机架间的速度,处理好堆拉关系,减少尺寸波动。BSW公司的生产精度可将4根轧件的成品长度差控制在1l50mm以内。
8结语
BSW公司在改造的设备上开发4线切分轧制技术,并已成为世界上4线切分轧制技术经验最丰富的供应商,非常值得我们借鉴。国内对该技术也极为关注,有的钢厂已开始相关方面的研究和尝试。其中,新疆八钢已具备设计开发能力,正在进行相关的设备改造工作。广钢于2000年初引进了该技术。据预测,2005年国内优质小型材产量将突破6000万t,生产厂不乏先进的棒材生产线,基础优势较BSW公司优越的多。这些都为我国进一步开展4线切分轧制技术的研究,尽早地掌握、开发和应用4线及4线以上的切分轧制技术提供了有利条件。
[参考文献]
[l]姜振峰,赵坤.硬质合金组合轧辊的结合分析[J].轧钢,2003,20(6):49~5l.(收稿日期:2004-03-l5)
?
7
4
?
4线切分轧制技术分析
作者:姜振峰, JIANG Zhen-feng
作者单位:新疆八一钢铁股份公司,型材轧钢厂,新疆,乌鲁木齐,830022
刊名:
钢铁研究
英文刊名:RESEARCH ON IRON AND STEEL
年,卷(期):2005,33(2)
被引用次数:2次
参考文献(1条)
1.姜振峰;赵坤硬质合金组合轧辊的结合分析[期刊论文]-轧钢 2003(06)
本文读者也读过(10条)
1.兰方海涟钢棒材厂三线切分轧制存在的问题及解决措施[会议论文]-2009
2.孔利明.KONG Li-ming(Φ)12mm热轧带肋钢筋三切分轧制工艺实践[期刊论文]-新疆钢铁2007(3)
3.曹杰.阎军.章静螺纹钢三切分轧制轧件尺寸影响因素的分析[期刊论文]-重型机械2003(5)
4.梁元成.赵文革.康庄.LIANG Yuan-cheng.ZHAO Wen-ge.KANG Zhuang棒材3线切分轧制技术的应用与改进[期刊论文]-轧钢2000,17(1)
5.田鹏松.张力.郭淑萍棒材3线切分轧制技术改进[会议论文]-2008
6.黄文初.梁辉.Huang Wenchu.Liang Hui固定转速比连轧与多切分轧制生产实践[期刊论文]-河南冶金2008,16(2)
7.张忠峰.ZHANG Zhong-feng四线切分轧制常见工艺问题及解决措施[期刊论文]-轧钢2010,27(1)
8.曲辉祥.王慧玉.赵瑞明.QU Hui-xiang.WANG Hui-yu.ZHAO Rui-mingφ16mm带肋钢筋二线切分轧制孔型与导卫设计[期刊论文]-轧钢2005,22(6)
9.曹杰.阎军.章静.杨启文.朱银森.阮本龙螺纹钢三切分轧制有限元分析[期刊论文]-钢铁2004,39(8)
10.刘建萍.LIU Jian-ping萍钢五切分轧制技术的研发[期刊论文]-江西冶金2008,28(2)
引证文献(2条)
1.喻云龙1种直条棒材生产新工艺[期刊论文]-钢铁研究 2010(2)
2.郑治龙.王华.王晓东切分轧制技术及其在棒材生产中的应用[期刊论文]-南方金属 2006(6)
本文链接:https://www.360docs.net/doc/4b11286512.html,/Periodical_gtyj200502013.aspx
棒材切分轧制导卫系统的应用与改进
棒材切分轧制导卫系统的应用与改进 2006-7-12 11:39:18未知来源供稿 1 前言 莱芜钢铁集团有限公司(简称莱钢)由意大利DANIELI公司引进的全连续式棒材及轻型材生产线,以生产圆钢、带肋钢筋为主,年产量近60万t。该生产线共有18架轧机,粗轧6架为悬臂式,中、精轧12架均为卡盘式;采取平立交替布置,其中14#、18~轧机为平立可转换机架。该生产线设计可进行带肋钢筋切分轧制。切分轧制与传统轧制在工艺上的不同之处是把一支轧件利用轧辊孔型切分成两支以上的并联轧件,再利用切分导卫将并联轧件切分成单支轧件。该套轧机全部从国外引进,装备水平高,其工艺件种类繁多,结构复杂。尤其是切分轧制,因其工艺的特殊性,对导卫系统的要求更为严格。而在实际生产过程中,出现的问题也比较多。为了保证正常生产,除了加强工艺件的基础管理之外,还在工艺件国产化和适应性改进等方面进行了探索。 2 切分轧制导卫系统 在切分轧制过程中,导卫系统除了保证轧件准确地进入孔型进行轧制之外,还有切分并联轧件的作用。在实际生产中,导卫系统在保证轧制过程中轧件变形的稳定性以及弥补孔型设计的不足等方面也起着重要作用。该生产线切分轧制的导卫系统根据安装位置不同,立式机架入口采用滚动导卫,水平机架入口采用滑动导卫;出口除切分机架为切分导卫外,其余均采用滑动导卫,其中中、精轧出口采用出口导管。滚动导卫一般为两轮,但切分轧制的专用滚动导卫为四轮。 粗轧轧制速度低,来料断面大,对导卫的冲击较大,采用简单的滑动导卫。而中、精轧机一般采用带导卫盒的滑动导卫,调整方便。滚动导卫对轧件摩擦小、夹持作用强,除了保证对轧件的导向作用外,还可以有效地避免倒钢。切分轧制专用的四轮滚动导卫对轧件则具有一定的矫直作用。为了方便调整,滚动导卫内部设计有专门的调整机构,以调节导轮的中心距,使导轮能够准确地夹持轧件。同时为保证滚动导卫能够较长时间正常运行,对导轮轴承的润滑以及导轮、夹板的冷却要求非常严格。切分导卫主要包括切分导嘴、切分轮、分
如何对个股进行系统技术分析
如何对个股进行系统技术分析?——个股案例分析一则 9月20号笔者在微博中给战友们提出了一只个股的处理问题:给大家一个问题,000503今天该怎么处理?为什么?后市又怎么处理,看看大家现在到底水平如何。 很多战友针对此问题提出了自己的看法和策略,从中看出战友们水平的确参差不齐且差距较大,从战友们给出的答案中可以看出很多战友都被很多技术分析给缠着那,但技术分析工具一堆,工具并不决定炒股是赚是赔,关键是使用工具的人。所以,研判股票要有一个综合性的判断,根据判断对未来走势的可能性作出相应分析,针对可行性制定相应的策略,如此基本上可置于不败之地。那种一根筋的就知道傻着死多或死空,那种完全不知道什么叫技术分析、什么是操盘系统的,不赔钱实在对不起股市这个名字。 博文中曾经提到过相关内容,很多战友来信找不到相关内容,所以就借假期将微博中笔者22号的分析给发到博文中和战友们分享。图和文字都是22号当天原版从微博中摘出来的,图现在已经走出来了一些,战友们可以将当时的分析和后面这些天股票的走势对比一下,而且可以继续对比下去。这里能否赚钱的关键实际上并不在股票的走势,而在于个人根据走势所作的抉择是否正确,这才是最重要的。 说000503。图中,股票从上一轮下跌后,在密集交易区1位置横盘了 一周多破位,然后横盘走了一个三重顶,跌破颈线后根据《黄金游戏》除了倍量法外另一种从跌破颈线算起的方法最后走到了7.8见底。然后
在下面做了个小双底展开新的上涨。小双底颈线在8.6元,以此计算小双底后股票至少到9.4元。8月3号高点9.41。 结果第二天重新突破了9.4,这意味着小双底形成后很可能要走两倍量高度,但上面就是大的颈线在9.8元。根据压力高低先取低的原则,那么9.8就决定了后市能否继续上涨。但股票以涨停长阳方式突破颈线,突破确立,就差回踩。之后果然上面上冲止步于前面下跌时的第一个密集交易区高点,下落以颈线为支撑。 而且,突破9.8大颈线之后,按照小双底颈线两倍量计算目标价位是10.2元,结果股价冲高的高点是8月9号的10.35,与此误差不大。继续按照小双底向上计算,后面三倍、四倍量、五倍量的股价目标区域分别在11、11.8、12.6。但主力狡猾,最终是以收盘跌破颈线后再向下洗盘然后探底中阳线保守确认对颈线突破。 一下洗掉很多浮筹?但在围绕大颈线回踩的过程中还是形成了密集交易区2。突破大的颈线后,按照大的颈线的目标价位是11.8元,与小
棒材生产线工艺流程
轧钢生产工艺流程 1、棒材生产线工艺流程 钢坯验收→加热→轧制→倍尺剪切→冷却→剪切→检验→包装→计量→入库 (1)钢坯验收〓钢坯质量是关系到成品质量的关键,必须经过检查验收。 ①、钢坯验收程序包括:物卡核对、外形尺寸测量、表面质量检查、记录等。 ②、钢坯验收依据钢坯技术标准和内控技术条件进行,不合格钢坯不得入炉。 (2)、钢坯加热 钢坯加热是热轧生产工艺过程中的重要工序。 ①、钢坯加热的目的 钢坯加热的目的是提高钢的塑性,降低变形抗力,以便于轧制;正确的加热工艺,还可以消除或减轻钢坯内部组织缺陷。钢的加热工艺与钢材质量、轧机产量、能量消耗、轧机寿命等各项技术经济指标有直接关系。 ②、三段连续式加热炉 所谓的三段即:预热段、加热段和均热段。 预热段的作用:利用加热烟气余热对钢坯进行预加热,以节约燃料。(一般预加热到300~450℃) 加热段的作用:对预加热钢坯再加温至1150~1250℃,它是加热炉的主要供热段,决定炉子的加热生产能力。 均热段的作用:减少钢坯内外温差及消除水冷滑道黑印,稳定均匀加热质量。 ③、钢坯加热常见的几种缺陷 a、过热 钢坯在高温长时间加热时,极易产生过热现象。钢坯产生过热现象主要表现在钢的组织晶粒过分长大变为粗晶组织,从而降低晶粒间的结合力,降低钢的可塑性。 过热钢在轧制时易产生拉裂,尤其边角部位。轻微过热时钢材表面产生裂纹,影响钢材表面质量和力学性能。 为了避免产生过热缺陷,必须对加热温度和加热时间进行严格控制。 b、过烧 钢坯在高温长时间加热会变成粗大的结晶组织,同时晶粒边界上的低熔点非金属化合物氧化而使结晶组织遭到破坏,使钢失去应有的强度和塑性,这种现象称为过烧。 过烧钢在轧制时会产生严重的破裂。因此过烧是比过热更为严重的一种加热缺陷。过烧钢除重新冶炼外无法挽救。 避免过烧的办法:合理控制加热温度和炉内氧化气氛,严格执行正确的加热制度和待轧制度,避免温度过高。 c、温度不均 钢坯加热速度过快或轧制机时产量大于加热能力时易产生这种现象。温度不均的钢坯,轧制时轧件尺寸精度难以稳定控制,且易造成轧制事故或设备事故。 避免方法:合理控制炉温和加热速度;做好轧制与加热的联系衔接。 d、氧化烧损 钢坯在室温状态就产生氧化,只是氧化速度较慢而已,随着加热温度的升高氧化速度加快,当钢坯加热到1100—1200℃时,在炉气的作用下进行强烈的氧化而生成氧化铁皮。氧化铁皮的产生,增加了加热烧损,造成成材率指标下降。 减少氧化烧损的措施:合理加热制度并正确操作,控制好炉内气氛。 e、脱碳 钢坯在加热时,表面含碳量减少的现象称脱碳,易脱碳的钢一般是含碳量较高的优质碳素结
棒材三切分轧制要点
棒材三切分轧制要点 3、Φ14*3三切分螺纹钢轧制调试工作,特提出工艺要求如下: 1、原料工严把原料质量关,杜绝有肉眼可见缺陷的钢坯入炉。 2、看火工按工艺规程要求,严格控制钢坯出炉温度,既要防止钢坯高温氧化甚至脱碳现象,影响钢材性能,又要防止低温钢轧制损坏设备甚至造成轧制事故。 3、导卫的调整与安装3、1 导卫在上线前必须对油路、水路、轴承等进行检查,确保油路、水路畅通,零部件完好,并对导卫加油。3、2导卫上线前的调整应坚持以下原则:①、粗轧滚动导卫的开口度比标准料型大22mm为宜;精轧滚动导卫的开口度比标准料型大0、 10、5mm,以用手转动其中一个轮子时,另一个轮子也能转动,且无明显阻力为宜。⑤、要特别注意切分刀片中心线必须与切分轮两切分刃在同一直线上,并与铲嘴内孔中心线吻合。⑥、铲嘴在设计时已经考虑到来料与轧槽形状,在现场安装时铲嘴离轧槽的距离控制在135。范围内。3、3导卫在安装时尤其是 15、16架进口导卫,必须保证导卫中心线与孔型中心线相吻合,以保证切分开的料型尺寸上的一致性。
4、轧辊在安装时必须保证轧辊装配的正确性以及轧机安装前轧辊轴承的加油工作;保证轧辊安装时上下轧槽的对正、磨槽以及轧辊两端辊缝的一致性,要求精轧机两边辊缝差小于0、1mm。 5、必须保证各机架孔型中心线对正轧制线,以防止轧槽偏磨,保证料型的正确性。 6、料型控制6、1轧制过程中的料型控制严格执行《工艺技术规程》要求。6、2第一次轧制前,中轧、 13、 14、15架必须各试轧21150℃ 7、轧制过程中1#剪必须切头、尾。 8、轧制初始阶段应投入活套。 9、保证裙板平直以及上位与下位的准确性。 10、调整倍尺剪时,必须保证倍尺剪剪臂原位水平及剪切位置的垂直,以防止倍尺轧件的头尾弯曲。 11、试生产前,冷床输入辊道中有问题的辊子和电机应换完。 12、利用检修时间调整对齐辊道,保证对齐辊道平直;3#台操作工应选择合适的对齐辊道速度。
山东省SDCORS系统技术分析
山东省SDCORS系统技术分析 在CORS出现之前,用户使用RTK的方法都是1个基准站+N个移动站的作业模式,基准站得自己架设,一般都是临时性的,而作业范围局限在十几公里以内。随着GPS定位技术和信息技术的综合发展,GPS定位模式已经发展到基于网络通讯条件下的大区域实时动态定位测量模式。山东省CORS系统(简称SDCORS)是利用现代卫星定位、计算机网络、数字通讯等技术进行多方位、高深度集成的成果。本文介绍了CORS技术的技术原理和山东省SDCORS系统的概况和特点。 标签:SDCORS CORS技术技术分析 1 CORS技术原理 连续运行卫星导航定位参考站系统CORS(continuous Operation Reference Stations)是由多个GPS基准站组成。系统主要通过因特网和无线通信网络向系统覆盖的服务区内用户提供基准站坐标和基准站GPS观测数据,用户通过因特网下载CORS若干基准站数据进行事后精密定位,也可以接收数据播发站对载波相位观测数据进行实时精密定位。 CORS系统是从“台站网”的思想演化而来的。上世纪80年代,加拿大提出“主动控制系统(Active Con2trol System)”理论是最早的台站网理论,其主要思想是在某一区域范围内建立永久性的参考站点组成主动控制系统,用于向用户提供改进后的预报星历和其他改正参数,进而提高流动站的定位精度。 在CORS出现之前,用户使用RTK的方法都是1个基准站+N个移动站的作业模式,这种作业模式叫做单基准站模式(Single-base),基准站得自己找点架设,一般都是临时性的,而作业范围都是十几公里,如果有个较大的测区,则需要多次的架设临时基准站。而CORS的特点之一通俗的讲,就是大的测绘部门架设几个或者几十个上百个永久的基准站,覆盖一个比较大的区域,那么下次出去做外业测量就不用再架设基准站了。 如果只是简单的的架设固定基准站,则相当于我们现在的信标台,拿着移动站走到哪里,只会接收距离最近的基准站发送的改正电文,则还是单站模式,而且作用距离会受到很大的限制,我们知道一台基准站的作业距离比如说是S公里,则两台基准站的距离就不能超过2S,而且,在中间会出现接收不到信息的盲区,这样的话,想控制一个区域,架站必然很密,费用必然很高,而且如果一台基准站的观测条件不好,则在一片区域里就无法测量了。 针对这两个问题,业界现在主要有两种处理方法,一种是天宝的VRS技术,另外一种是徕卡的主辅站技术,这两种技术都是同一种思想,就是将全网架设的所有基准站的数据发送到一个数据处理中心,经过解算,然后统一发送改正数据,也就不是单基准站作业模式了,这样可以让基准站间的距离增大,而且避免了一
轧钢孔型设计软件v10说明
热轧圆钢及线材孔型设计软件使用说明书 热轧圆钢及线材孔型设计 说明书(V1.0) 二零零四年七月 版权所有 1
目录 第1章绪论…………………………………………………………… 1.1概述……………………………………………………………… 1.2软件功能………………………………………………………… 1.3运行环境………………………………………………………… 1.4用户界面………………………………………………………… 第2章工艺参数输入………………………………………………… 2.1概述……………………………………………………………… 2.2钢号及成分……………………………………………………… 2.3原料面积计算…………………………………………………… 2.4成品面积计算………………………………………………………… 2.5延伸系数计算…………………………………………………… 2.6轧制速度输入…………………………………………………… 2.7轧机形式/温度……………………………………………………2.8保存/返回………………………………………………………… 第3章孔型参数输入………………………………………………… 3.1概述……………………………………………………………… 3.2孔型形状………………………………………………………… 3.3翻钢形式………………………………………………………… 3.4延伸系数………………………………………………………… 3.5轧辊直径/材质………………………………………………… 3.6速比……………………………………………………………… 3.7轧件温度………………………………………………………… 3.8延伸系数修改………………………………………………… 2
Φ14棒材生产中三切分轧制技术研究
龙源期刊网 https://www.360docs.net/doc/4b11286512.html, Φ14棒材生产中三切分轧制技术研究 作者:侯杰 来源:《商品与质量·学术观察》2013年第02期 摘要:本文叙述了棒材生产中φ14螺纹钢三切分的工艺选择、调试时出现的问题、改进方案及效果。 关键词:螺纹钢三切分工艺方案 1、前言 切分轧制是在轧机上利用特殊的轧辊孔型和导卫或者其他切分装置,将原来的一根坯料纵向切成两根以上的轧件,进而轧制多根成品或中间坯的轧制工艺。采用切分轧制技术可缩短轧制节奏,提高机时产量,显著提高生产效率,降低能耗和成本。目前切分轧制技术已发展到五切分轧制,且两线切分轧制技术和三线切分轧制技术作为成熟技术已经普遍应用在小规格螺纹钢的生产中。 本文所述棒材厂从2005年开始逐步应用切分轧制技术,现已成功开发了φ14、φ16、φ18螺纹钢二切分、φ12螺纹钢三切分轧制技术。2010年,为了实现147万吨的年产量目标,棒材厂决定充分发挥切分技术的产能优势,在Ф12螺纹钢三切分的基础上实施Ф14螺纹钢的三切分轧制。 2、设备配置情况 车间的工艺布置为粗轧7架平轧闭口轧机、中轧为平立交替的6架两辊闭口轧机、精轧为平立交替6架预应力轧机。、 3、工艺方案的选择 3.1 工艺布局的确定 在Φ12螺纹三切工艺和Φ14螺纹两切分工艺的经验基础上,对一道预切与两道预切的方案进行了比较: 如采用一道预切,则预切分孔(K4)的压下和延伸比较大,轧制负荷大、轧制不稳定, 且其切分楔处的压下系数远大于槽底的压下系数,造成切分楔处磨损严重;来料进预切分孔时的对中性差,进而导致预切料型进切分孔时不均匀,这样3支成品之间的尺寸不均匀,负差也不易控制。
棒材三切分轧制要点
棒材三切分轧制 为顺利完成Φ12*3、Φ14*3三切分螺纹钢轧制调试工作,特提出工艺要求如下: 1、原料工严把原料质量关,杜绝有肉眼可见缺陷的钢坯入炉。 2、看火工按工艺规程要求,严格控制钢坯出炉温度,既要防止钢坯高温氧化甚至脱碳现象,影响钢材性能,又要防止低温钢轧制损坏设备甚至造成轧制事故。 3、导卫的调整与安装 3.1 导卫在上线前必须对油路、水路、轴承等进行检查,确保油路、水路畅通,零部件完好,并对导卫加油。 3.2导卫上线前的调整应坚持以下原则:①、粗轧滚动导卫的开口度比标准料型大2—4mm 为宜;中轧滚动导卫的开口度比标准料型大1—2mm为宜;精轧滚动导卫的开口度比标准料型大0.1—0.5mm为宜。②、15、16架双排轮前面两个辊的开口度必须与后边两个辊的开口度一致。调整时可先调前面两个辊的开口度与后边两个辊的开口度一致,然后再调内支撑臂后端的调整螺丝左右两个螺丝可同时、同步改变前后两组辊的开口度。④、切分导卫切分轮间隙应调整适当,控制在0.3—0.5mm,以用手转动其中一个轮子时,另一个轮子也能转动,且无明显阻力为宜。⑤、要特别注意切分刀片中心线必须与切分轮两切分刃在同一直线上,并与铲嘴内孔中心线吻合。⑥、铲嘴在设计时已经考虑到来料与轧槽形状,在现场安装时铲嘴离轧槽的距离控制在1—2mm。⑦、分料盒离切分轮越近越好。⑧、扭转导卫的扭转角控制在30。—35。范围内。 3.3导卫在安装时尤其是15、16架进口导卫,必须保证导卫中心线与孔型中心线相吻合,以保证切分开的料型尺寸上的一致性。 4、轧辊在安装时必须保证轧辊装配的正确性以及轧机安装前轧辊轴承的加油工作;保证轧辊安装时上下轧槽的对正、磨槽以及轧辊两端辊缝的一致性,要求精轧机两边辊缝差小于0.1mm。 5、必须保证各机架孔型中心线对正轧制线,以防止轧槽偏磨,保证料型的正确性。 6、料型控制 6.1轧制过程中的料型控制严格执行《工艺技术规程》要求。 6.2第一次轧制前,中轧、13、14、15架必须各试轧2—3根小样,并测试各架次料型尺寸,要特别注意考虑小样与正常轧制时轧件尺寸及变形条件的差别。 6.3在小样试完并符合要求后,成品机架以10m/s的速度全线贯穿一根,要求使用1#剪碎断头部4米及尾部3米,岗位工注意测量各道次红坯尺寸及17、18架间轧件的扭转角度。6.4在轧制过程中,必须控制好13架出口料型厚度及14架出口料型宽度。 6.5轧制过程中钢温应控制在1050—1150℃ 7、轧制过程中1#剪必须切头、尾。 8、轧制初始阶段应投入活套。 9、保证裙板平直以及上位与下位的准确性。
数据挖掘系统设计技术分析
数据挖掘系统设计技术分析 【摘要】数据挖掘技术则是商业智能(Business Intelligence)中最高端的,最具商业价值的技术。数据挖掘是统计学、机器学习、数据库、模式识别、人工智能等学科的交叉,随着海量数据搜集、强大的多处理器计算机和数据挖掘算法等基础技术的成熟,数据挖掘技术高速发展,成为21世纪商业领域最核心竞争力之一。本文从设计思路、系统架构、模块规划等方面分析了数据挖掘系统设计技术。 【关键词】数据挖掘;商业智能;技术分析 引言 数据挖掘是适应信息社会从海量的数据库中提取信息的需要而产生的新学科。它可广泛应用于电信、金融、银行、零售与批发、制造、保险、公共设施、政府、教育、远程通讯、软件开发、运输等各个企事业单位及国防科研上。数据挖掘应用的领域非常广阔,广阔的应用领域使用数据挖掘的应用前景相当光明。我们相信,随着数据挖掘技术的不断改进和日益成熟,它必将被更多的用户采用,使企业管理者得到更多的商务智能。 1、参考标准 1.1挖掘过程标准:CRISP-DM CRISP-DM全称是跨行业数据挖掘过程标准。它由SPSS、NCR、以及DaimlerChrysler三个公司在1996开始提出,是数据挖掘公司和使用数据挖掘软件的企业一起制定的数据挖掘过程的标准。这套标准被各个数据挖掘软件商用来指导其开发数据挖掘软件,同时也是开发数据挖掘项目的过程的标准方法。挖掘系统应符合CRISP-DM的概念和过程。 1.2ole for dm ole for dm是微软于2000年提出的数据挖掘标准,主要是在微软的SQL SERVER软件中实现。这个标准主要是定义了一种SQL扩展语言:DMX。也就是挖掘系统使用的语言。标准定义了许多重要的数据挖掘模型定义和使用的操作原语。相当于为软件提供商和开发人员之间提供了一个接口,使得数据挖掘系统能与现有的技术和商业应用有效的集成。我们在实现过程中发现这个标准有很多很好的概念,但也有一些是勉为其难的,原因主要是挖掘系统的整体概念并不是非常单纯,而是像一个发掘信息的方法集,所以任何概念并不一定符合所有的情况,也有一些需要不断完善和发展中的东西。 1.3PMML
φ12四切分轧制汇总
1工艺确定 孔型系统K7~K3采用圆-平辊-立箱-预切-切分,粗中轧、成品及成品前孔型不变。同时考虑各个道次工艺参数分配的合理性,负荷均衡,尽量减少孔型磨损的不均匀性,达到换辊次数最少、轧机产量高、生产顺行的目的。依据切分位置和设备性能,切分方式选用切分轮法,在16架出口实行先切两侧再切中间的方式,将轧件切分为4条,然后轧制成成品 2孔型设计 K6K7 K2K1 1)K7选择圆孔型,根据面积推算,设计尺寸为φ45 mm 。 2)根据经验,K6直接设计为平孔。 3)K5为立箱孔型,根据三切分生产经验及有利于料型控制的原则,将侧壁斜度设计为0.12,圆角设计为R3,槽底宽设计为19.5。 4)K4为预切分孔型,根据三切经验,此道次延伸系数最佳范围在1.25~1.32之间,在设计时,考虑稳定性等原因,中间两线比两侧略大,一般在2%~3%之间。切分楔设计非常关键,两楔间距过小,此处压下系数远大于槽底压下系数,造成磨损严重;过大,会造成切分孔切
分楔磨损过快,甚至崩槽,在成品表面形成折叠,根据经验,一般设计为6~8mm。预切分楔角度设计时应考虑与K3孔切分楔角度的配合及耐磨性,一般设计为78°~88°,切分楔圆角半径一般选为1.4~1.8,过小不耐磨。 5)K3为切分孔型,其作用是对轧件4线料型进行规整、加工切分带,为切分做好料型准备。根据三切经验,此道次延伸系数最佳范围为1.10~1.25,设计要点是切分楔角度、切分带厚度、基圆尺寸。切分带厚度必须控制在0.8~1.0 mm之间,过厚过宽,在K2道次压不合,造成成品孔型较早出现轧痕,同时切分轮受力过大,出现导卫烧轴承事故;过薄,切分带直接被碾到K2料表面,在成品道次出现折叠现象。切分楔角度一般选为45°~55°,切分楔圆角半径设计为r0.7~r1.0,过小强度不够。 3关键道次导卫设计 1)K4道次:进口设计为双排4轮滚动导卫,同时导轮设计为“V”形,这样有利于夹持轧件,确保轧件运行中的稳定性、对中性。出口设计为箱式出口,内腔尺寸比轧件大5~10 mm,长度为540 mm,有利于提高轧件的稳定性。 2)K3道次:同K4道次一致,进口设计为双排4轮滚动导卫。出口切分导卫示意图见图3。 3)16~18架轧机间导槽设计:为减少16~18架轧机间故障,用4线导槽代替6#、7#活套器,同时设计时考虑了便于观察导卫对中及防止翘头功能。7#导槽设计与6#导槽设计一致。4)成品轧机后至3#飞剪间导槽、导管设计:在成品轧机与3#飞剪之间设计4线导管及固定底座,导槽中心距为135 mm,同时考虑快速更换,将螺栓固定方式改为打楔铁形式。 4常见故障原因分析及解决措施 4.1 16架顶出口 主要原因为轧辊切分楔崩掉、切小头、导卫安装不正。 采取的主要措施:1)优化15#、16#孔型设计,合理分配预切分楔、切分楔的压下量和切分角设计,见图4。2)确保16架轧机进口、切分楔、切分轮、切分刀安装在同一条直线上。3)改进16架轧辊冷却水管,改善预切分楔和切分楔的水冷效果,延缓其磨损。4)消除导卫在横移过程中传动丝杠的间隙,以解决导卫固定不对中问题。 4.2 切分刀黏钢 主要原因为钢温过高、切分带过厚、切分导卫冷却不好、料型不符合工艺要求。主要解决措施:1)严格按工艺要求控制钢温,开轧温度控制在 1 000~1 050 ℃,最高不得超过1 080 ℃。2)调整料型符合工艺要求,且保证轧机弹跳严格控制在0.2 mm以下,两侧辊缝差值不超0.1 mm。3)改进导卫冷却方式 4.3 4线差 4条钢材倍尺长度差在0.8~1.2 m之间,因4线长度差较大,造成冷剪切损大,平均影响成材率降低1.23%;同位置纵肋高度相差在0.5~1.5 mm,4线重量偏差最大与最小可相差2.0%,对成品质量影响较大。主要原因有孔型设计不完善,预切、切分孔型4线面积分配不合理;轧机间张力关系控制较差,中间料型发生变化;轧辊加工精度差;轧辊材质差, 不耐磨,料型不稳定。主要解决措施:1)重新优化预切、切分孔型,选择合理的4线配比(见图4)。2)轧钢工与CP2操作工配合好,确保张力调整至最佳。3)提高轧辊加工精度,轧槽加工精度在0.1 mm以内。4)预切、成品前道次轧辊选用碳化钨材质,可提高料型的稳定性,从而提高生产的稳定性
大型软件系统技术路线分析
大型软件系统技术路线分析 纵观全球大型软件系统软件系统技术发展路线,历经了二十多年的时间,逐步从vb、.NET向J2EE java全面迁移,迄今为止,所有的集团客户和高端政府机关在大型软件系统技术的选择上,几乎清一色的选择JAVA品台,而且面向集团化的大型软件系统定位的企业,如九思软件、东软集团,也统统在此路线上完成系统的架构和功能设计。 在国外,JAVA技术已成为解决大型应用的事实标准,符合J2EE规范的应用服务器则是构建面向对象的多层企业应用的中间核心平台。因其具有易移植性,广开放性、强安全性和支持快速开发等特性,成为面向对象开发组织应用的首选平台。参照文档如下: 基于J2EE应用服务器支持EJB组件开发技术,包括消息队列、负载均衡机制和交易管理等。支持中大型网站和中大型组织应用等需要大规模跨平台、网络计算的领域。 软件构造有几个不可逆转的发展方向:XML数据结构、面向对象的构件技术、网络化应用。其中Java 因为与平台无关、安全、稳定、易开发、好维护、很强的网络使用性等, 而成为主流环境。 J2EE是企业级应用的标准。 J2EE平台提供了一个基于组件的方法,来设计、开发、装配及部署企业级应用程序,并提供了多层的分布式的应用模型、组件再用、一致化的安全模型以及灵活的事务控制机制。使之具有重用的能力,并集成了基于XML的数据交换一个统一的安全模式及灵活的事务控制。 J2EE应用程序由组件构成。一个J2EE组件是自包含的,与其相关的语气它组件通信的类及文件集成到J2EE应用程序的功能软件单元。J2EE规范定义了下面一些组件: 1)、运行在客户端的应用客户程序及小程序。 2)、运行于服务器网络的Servlet&Jsp组件。 3)、运行于服务端的企业逻辑组件。 J2EE组件用Java语言编写,通过相同的方法编译。J2EE组件与标准Java类的不同之处在于J2EE组件集成到了应用程序中,与J2EE规范兼容,并部署到负责运行、管理的J2EE 服务器上。 基于J2EE企业级应用服务器的结构 基于J2EE的企业级应用服务器是基于Web Services 的新一代应用服务器。在设计上突出了XML的应用,比如XML在本地化的存储及各种处理;通过SOAP与 .NET及通过IIOP 与CORBA的连接等。
螺纹钢筋切分扁方孔型系统优化设计
螺纹钢筋切分扁方孔型系统优化设计 潘建洲 (福建三钢(集团)闽光股份有限公司棒材厂,三明 365000) 摘要: 结合三钢棒材线实际,Φ16/Φ18螺纹切分精轧孔型选择采用扁方孔型系统,通过对切分孔型优化设计,合理选择轧辊材质,能有效地减少工艺事故、提高产量和改善指标,具有显著优越性。 关键词: 螺纹切分孔型设计 1前言 随着小规格螺纹钢筋(主要指Ф18mm以下,下同)切分轧制技术的发展,改变了小规格材产量不高、生产效率低下的状况,同时也带来了工艺故障复杂、指标下降等一些问题。工艺设计对于切分轧制成功与否关系重大,孔型设计又是工艺设计中最重要的一环,是工艺设计的核心内容。孔型设计合理,能有效地减少工艺故障、提高指标、降低轧辊导卫消耗。 对于孔型系统的选择,目前国内大多采用了梅花方和扁方孔型系统,由于两种孔型系统各有利弊,只有根据生产线工艺装备、产品要求等实际情况,确定孔型系统的选用。基于梅花方孔型系统的论述较多,扁方孔型系统设计论述较少,本文就扁方孔型系统设计作一讨论,以期对此类切分生产线有所帮助。 2三钢闽光公司棒材厂螺纹钢切分情况 三钢棒材厂始建于1992年,1995年底开始投入生产,设计年产Φ12—40mm螺纹钢筋和光面圆钢30万吨,经过3次重大技术改造,目前年产达到80万吨以上,生产原料为150*150*12000mm连铸小方坯,采用热装热送工艺,装备有:2座蓄热式加热炉、17架连轧机、7.8*102 m步进式冷床、4900KN冷剪机,并从国外引进倍尺飞剪、自动打捆机等设备,是一条具有九十年代国际先进水平的连续棒材轧钢生产线。 该线精轧6架(12#-17#)呈H/V交替布置,其中15#轧机可通过液压装置实现快捷方便地平立互换,从立式机架出成品(K1前后无平立交叉导管),精轧全部采用“霍太克”导卫。 采用扁方孔型系统生产Φ16、Φ18两种规格,并多次对切分孔型进行改进,逐步消除了K3进出口故障较多、产品表面质量缺陷等设计上的不足,生产更趋稳定,指标明显提高。 精轧孔型如下: 图1 Φ16、Φ18 mm螺纹钢筋孔型图
4线切分轧制技术分析
2005年4月 ApriI 2005 钢铁研究Research on Iron &SteeI 第2期(总第143期) No.2(Sum143) ?工艺与设备? 4线切分轧制技术分析 姜振峰 (新疆八一钢铁股份公司型材轧钢厂,新疆乌鲁木齐830022) 摘 要:详细介绍BSW 公司的4线切分轧制的孔型系统、轧辊结构、导卫结构、轧制控制以及对轧机的要 求,展望了该技术的发展空间。 关键词:棒材;4线切分轧制;孔型系统;导卫中图分类号:TG333.1 文献标识码:A 文章编号:1001-1447(2005)02-0045-03 ANALYSIS ON 4-LINE SLITTING ROLLING TECHNOLOGY JIANG Zhen -feng (SmaII Section SteeI PIant ,Xinjiang Bayi Iron and SteeI Co.,Ltd.,Urumchi ,830022China )Synopsis :The groove system ,roII structure ,guide structure ,roIIing controI and roIIing reguire-ments for 4-Iine sIitting roIIing technoIogy provided by BSW Co.are introduced in detaiI in this paper.In addition ,the prospect of this technoIogy is aIso discussed. Keywords :bar ;4-Iine sIitting roIIing ;groove system ;guide 作者简介:姜振峰(1974-),男,山东人,工程师,主要从事轧钢技术研究. 1前言 德国巴登钢铁公司(BSW )于1991年在棒材 连轧机上先后开发成功了!10mm 和!12mm 带肋钢筋切分轮法的4线切分轧制技术。其中!12 mm 的4线切分轧制使用15个机架, 轧制速度8m /s 。小时产量83t , 较单线相比少用4个机架,速度降低1.7m /s ,产量却增加了186%。达到了轧钢生产高效率、低成本的要求,因此在世界上得到迅速推广和应用。新疆八一钢厂于1999年对该技术进行了专题考察与培训,现将其4线切分轧制技术的关键点分析如下。2 孔型系统 BSW 公司设计采用4线切分轧制技术的孔型系统见图1,轧制!12mm 螺纹钢的轧件经K9道次轧制后截面为正方形,翻转45 后由K8、K7、K6采用扁箱孔型或平辊轧制成需要的扁平形轧件,之后在K5、K4两道次的预切分孔型中轧制成双狗骨形轧件。 图14线切分轧制孔型示意图 (a )!12mm (b )!10mm K3切分孔型中切分楔仅对双狗骨形轧件切 分带的高度方向上进行压下,使切分带厚度控制在0.2~0.8mm 之间,轧件基本上不产生宽展。 最后由切分孔型出口的4线切分导卫的切分 ? 54 ?
棒材四切分问题及解决方法
棒材四切分问题及解决方法 编写作者:邱世浦 一切分刀粘钢 切分刀粘钢是指切分轧制生产过程中,切分刀两侧或一侧粘渣,最终导致切分故障的 现象,切分刀粘钢的原因主要有以下几个方面; 1.开轧温度过高。如果开轧温度过高,在精轧区切分过程中,切分楔处压下量非常 大时,因急剧变形产生大量的热,造成局部金属温度迅速升高和切分带形状不规矩, 引起切分刀粘钢。 2.来料过大或过小,切分轧制遵循斧头原理,来料必须与16架切分楔处角度匹配。15料形过大或过小,都会造成切分困难,导致切分带过大,轧件前进过程中,切分带与切分刀发生摩擦,引起粘钢。 3.切分轮切偏或没对准轧槽。切分导卫安装,必须保证切分楔,切分轮,切分刀三 点一线, 对中良好,如果安装不正,导致料与切分轮不能对正而切偏,造成切分带过大,与切 分刀发生摩擦,引起粘钢。 4. 切分刀冷却不好,切分导卫必须保证充分冷却,尤其是切分刀,正常生产过程中因坯料,轧槽磨损等原因,造成轧件表面带细小氧化铁皮,切分带形状不规矩,与切分 刀摩擦粘在两边,如果冷却效果不好,就会越粘越多,最终导致冲出导卫堆钢,和下 游轧机无法调整。 5. 切分刀间距不合适,轧件进入切分盒后,成一定的角度,如切分刀间距未设定好,就会出现轧件件与切分刀发生摩擦而粘钢。 6. 切分孔型设计不合理,15,16架孔型系统设计非常重要,切分角设计必须匹配。 7.轧机刚性差,弹跳大,料形控制差。 8.切分刀长度不合适,三切分更为明显,离切分轮过近造成排渣不方便,引起粘钢。 9.切分轮角度设计不合理,切分不顺利。 10. 12到18架料形没有控制好,料发生便斜扭转,过大过小,头大尾大造成粘刚。 11.钢坯自身有问题有夹杂气泡开花。 12.关键架次轧槽老化或蹦槽。
棒材生产工艺
2、轧钢工艺 2.1 产品大纲及金属平衡 2.1.1 产品大纲 本车间设计为2条年产量80万吨的高速线材生产线。 主要产品规格为: 圆钢: Φ5.0—Φ20mm 光面线材 螺纹钢: Φ6.0—Φ18mm 螺纹钢筋 生产钢种为:普通碳素结构钢、优质碳素结构钢、锚螺钢、合金钢、不锈钢、 轴承钢等。 按品种规格和钢种分类的产品大纲见表2—1、2—2。 产 品 大 纲 表 2—1 产 品 大 纲 表 2—2 序号 产品规格范围 年产量(t ) 比例(%) 序号 钢种 代表钢号 年产量(t ) 比例(%) 1 普通碳素结构钢 Q235 400000 25 2 优质碳素结构钢 45# 80# 480000 30 3 焊条钢 320000 20 4 弹簧钢 60Mn 60Si 2Mn 64000 4 5 合金结构钢 40Gr 160000 10 6 冷镦优质钢 ML25—ML45 80000 10 7 不锈钢 8000 0.5 8 轴承钢 8000 0.5 7 合计(t ) 1600000 100 8 比例(%) 100
1 ф5-ф5.5 160000 10 2 ф6.0—ф9 400000 25 3 ф10—ф13 720000 45 4 ф14—ф18 240000 15 5 ф20 80000 5 合计100 2.1.2 产品质量及标准 (1)产品交货状态: 均以盘卷状态交货 (2)产品执行标准 —GB/T14981-94热轧盘条尺寸、外形、重量及允许偏差 —GB700-88碳素结构钢 —GB/T699-1999优质碳素结构钢技术条件 —GB6478-86冷镦钢技术条件 —GB/T3077-1999合金结构钢技术条件 —GB1222-84弹簧钢 2.1.3 原料 车间所用原料为连铸坯,全部由潍钢炼钢供给,钢坯规格尺寸为:150×150×12000mm,净重为2075kg,最小坯料长度为8000mm。 坯料应满足国家标准YB2011—83中规定和YB/T004—91中规定的内容。 连铸坯年需要量为166.4万吨。 2.1.4 金属平衡 车间原料用量为166.4万吨,成品量为160万吨,成材率为96%,金属平衡见表2—2。 车间金属平衡表表2-3 产品炉内烧损及二次氧化切损及轧废 原料量(t) 数量所占数量所占数量所占
二切分轧钢生产
切分轧制生产实践 摘要:本文对轧厂切分轧制技术做了总结,对生产操作中孔型设计、导卫装置等做了详细分析,为提高产品的成材率及各种规格质量进行了深入探讨。 关键词:螺纹钢生产;二切分;轧制技术要求 1 前言 轧钢厂2002年引进的小型棒材轧机,对Ф12、Φ14、Φ16mm三种规格带肋钢筋采用二切分轧制,轧机小时产量达到70t,接近其它规格平均85t的水平,且与其它产品共用150mm方连铸坯,经Ф500×1/Ф400×2/Ф350×4/Ф300×6十三架轧机15道次轧出成品。粗轧和中轧道次孔型具有共用性,缩短更换规格停机时间,提高了轧机作业率。 目前,轧厂φ16mm以下规格的建筑用带肋钢筋都采用切分工艺轧制,既保证了轧制小规格具备的条件,又保证了产品质量和产量,更好地满足市场的要求,取得了明显的经济效益。 2切分轧制技术特点 切分轧制是国家推广的新技术,也是今后发展方向。据不完全统计,在小型棒材的产品中,直径小于φ16mm规格的钢筋约占总量的60%。而棒材生产率随产品直径的减小而降低,因此要使各种规格产品的生产率基本相等,必须采用切分轧制,从而导致了棒材切分轧制技术的广泛应用。 切分轧制的技术关键在于切分设备的可靠性、孔型设计的合理性、切分后轧件形状的正确性以及产品质量的稳定性。 切分轧制具有以下明显的技术特点: 2.1 均衡不同规格产品的生产能力 使现有加热炉、轧机、冷床及其它辅助设备的生产能力有效利用和充分发挥。因此,减少了厂房面积,减少了设备投资。 2.2 大幅度提高轧制小规格产品的机时产量 采用切分轧制由于缩短了轧件长度,从而缩短了轧制周期,提高了轧机生产率。 2.3 节约能源、降低成本 采用切分轧制变形量小,电机负荷分配均衡,电机效率趋于最佳状态,电量消耗趋于最低。节约大量能源,且由于轧制成品长度减短,钢坯的出炉温度可适当降低。 但切分轧制也存在一些问题,主要表现在:棒材切分带容易产生毛刺,如调整不当有可能形成折叠,影响产品质量;对坯料的质量要求较严格,切分后坯料中心部位的缩孔、疏松等易暴露在轧件表面;对导卫、切分装置精度要求很高,在操作上应调整好进、出口导卫及切分轮间距,确保轧件对称地切分。 3切分工艺 3.1切分工艺布置 2×Ф12~16mm带肋钢筋产品的孔型系统如图1所示。图1中k6、k5、k4、k3孔型分别为菱形、菱方、预切分、切分孔型。 该产品采用150mm方坯,轧制15道次。粗轧孔型与中轧孔型具有共用性,精轧为切分孔型系统。
航空发动机机械系统技术分析
航空发动机机械系统技术分析 摘要:国内外出现的机械系统问题主要是设计、制造、装配、使用和实验方面。国内机械系统问题的主要原因是接触后磨损易发、零部件数量多结构复杂;制造 和设计水平低、进行试验的方法落后等;国内的技术环境给予的重视程度和投资 力度都不高等因素的共同影响。所以要机械系统运行顺畅,必须对管理、加工、 试验等相关工作人员进行专业能力的培养。 关键词:航空发动机;机械系统;分析 引言 航空发动机机械系统技术专业性强,而且具有较强的复杂性,在运行过程中 容易出现多种故障,因此需要对其进行专业性分析和探究。本文主要介绍了航空 发动机机械系统技术主要的四个部分,分别是传动技术、润滑技术、密封技术和 主轴轴承技术,分析了以上四个部分技术的发展现状及其未来发展趋势。 1机械传动系统技术分析 传动系统是航空发动机机械系统技术的一个关键组成部分,也是一个研究重点。当前航空发动机机械系统技术的一个发展趋势就是要确保传动系统满足高速 和重载工作条件,不仅如此,还需要能够实现减少传动系统整体体积和质量的效果,这种设计有助于提高航空发动机整体使用寿命和稳定性,还可以降低成本, 提高经济效益。 国外专家对航空发动机传动系统的研究比较深入,已经建立了比较完整的计 算分析系统,还可以对相关设备的强度和性能进行检测,并将具体部件的受力变 形情况纳入整体考虑范围,还可以实现对传统系统动态和静态运行的有效分析, 从而准确模拟机械系统的工作情况。近年来,随着齿轮动态技术的进一步发展, 带动了传动系统相应技术的研究,具体包括其噪音、振动以及声震粗糙度等,能 够准确评估分析齿轮因为形态误差导致的噪音等问题;还可以针对齿轮构件的使 用特点进行分析,在此基础上得出齿轮的S-N曲线,准确预测具体齿轮的寿命, 这有助于提高齿轮的整体应用效果。针对喷油润滑,相关研究人员通过进行磨损 实验,分析不同喷油状态下齿轮在运行过程中温度变化情况以及磨损情况,并得 到最佳的喷油方案,提高齿轮使用寿命。以上这些实验研究得到大量数据,为后 续传动系统设计运行提供了大量依据,一方面能够提高其整体使用效果,另一方 面还可以达到良好经济性。 我国航空发动机传动系统技术的不足之处在于齿轮咬合仿真、传动机匣与相 应附件的一体化设计等方面,此外,传动系统的整体动态设计以及新型传动技术 的应用也存在一定局限性,难以满足实际需要。由于航空发动机整体结构比较复杂,存在众多附件,而且其转速存在差异,导致针对航空发动机的传动系统设计 也比较困难,受到多个因素影响。 2机械润滑系统技术分析 随着航空发动机设计技术的发展进步,润滑系统越来越精细化。关于润滑系 统的设计有“二向流动、复杂换热、弹流润滑等比较困难复杂”的知识。对此,全 世界国家自20世纪到21世纪欧美、德国、法国、比利时、意大利、英国等欧洲 国家联合开展为了商用以及军用航空发动机传动润滑系统的研究,改进创新了润 滑系统中的材料和技术,获得了巨大的技术进步。主要包括“航空发动机抽成腔内的流动与换热、润滑系统着火与防火、金属海绵高校离心通风其等技术”,而且已经在一些商用发电机中进行了使用。未来航空发动机的负荷会不断提高,如果发
棒材轧制过程作业指导书
棒材轧制过程作业指导书 1.范围 本作业指导书适用于棒材轧制过程控制点的控制。 2.引用文件 《棒材机组轧制技术规程》 3.控制要求 3.1过程控制点:各道次槽孔的辊缝值,特别是K1道次的控制。 3.2控制特性:圆钢的外径,螺纹钢的内径。 3.3适用规格:适用于大批量生产的产品。圆钢Φ12~Φ40mm,螺纹钢Φ 12~Φ40mm。 4.作业内容: 4.1辊缝的调整控制。 4.1.1当轧槽因需更换后,轧钢操作工按规程中轧钢要求,将辊缝设定在标 准值。(可用轧铁丝的方法测量),并在粗、中轧测量轧槽、槽底尺寸,精轧因辊缝小不宜测出槽底尺寸,以轧铁丝测得的辊缝为依据,进行全线红条尺寸的控制。其中,粗轧槽底尺寸偏差小于2mm,中轧槽底尺寸偏差小于1mm,精轧槽底尺寸偏差小于0.7mm,成品尺寸以产品标准要求为控制原则。 4.1.2在轧制过程中,轧钢操作工还应根据轧槽磨损情况及时调整辊缝值, 使红条尺寸符合工艺要求。 4.1.3轧件外形尺寸的检查,可用木条来检查轧件的外形是否有耳子、凸疤、 欠充满缺陷。并及时调整。 4.2速度的控制。 为保证轧制顺利,轧钢工及CP2操作工必须观察每架次速度的变化,并在CP2操作室中进行及时调整。以保证1~11架间微张力轧制,
11~18架间活套轧制(当甩机架时,活套轧制范围为11~K1机架间)。 同时,要通过速度的调整,控制各机架间张力关系和活套量,防止因拉钢尺寸变化或活套量过大而堆钢。 4.3导卫装置的控制。 4.3.1导卫装置应满足工艺要求。对滚动导卫导轮间隙、润滑、冷却状况要 注意检查,发现问题及时更换。 4.3.2过桥、流槽应无凸起、毛刺,以防止划伤轧件。 4.3.3过桥、流槽磨损严重时要及时更换或修复,避免造成堆钢事故。 4.4取样制度。 4.4.1取样人员:由轧钢调整工按要求取样。 4.4.2取样部位:成品倍尺棒材的尾部。 5.取样时间间隔:正常轧制时,为防突发事故的发生,要求每10分钟 取2米超过轧辊周长以上的长样进行检测,并将轧件尺寸参数报CP2操作人员,由CP2操作人员负责通知调整。当K1换槽、换辊或间隔轧制时取样人员要将是否调整、是否过钢信息反馈CP2,经CP2操作人员确认后方能继续轧制。 5.1过程控制点记录。 以轧钢调整工取样的结果对轧机进行调整,使产品实物质量满足产品标准的要求。取样人员每20分钟做一次记录,记录成品道次的内径值。 6.相关记录: