第2讲CAXA数控车零件外轮廓粗精加工的CAM方法(精)
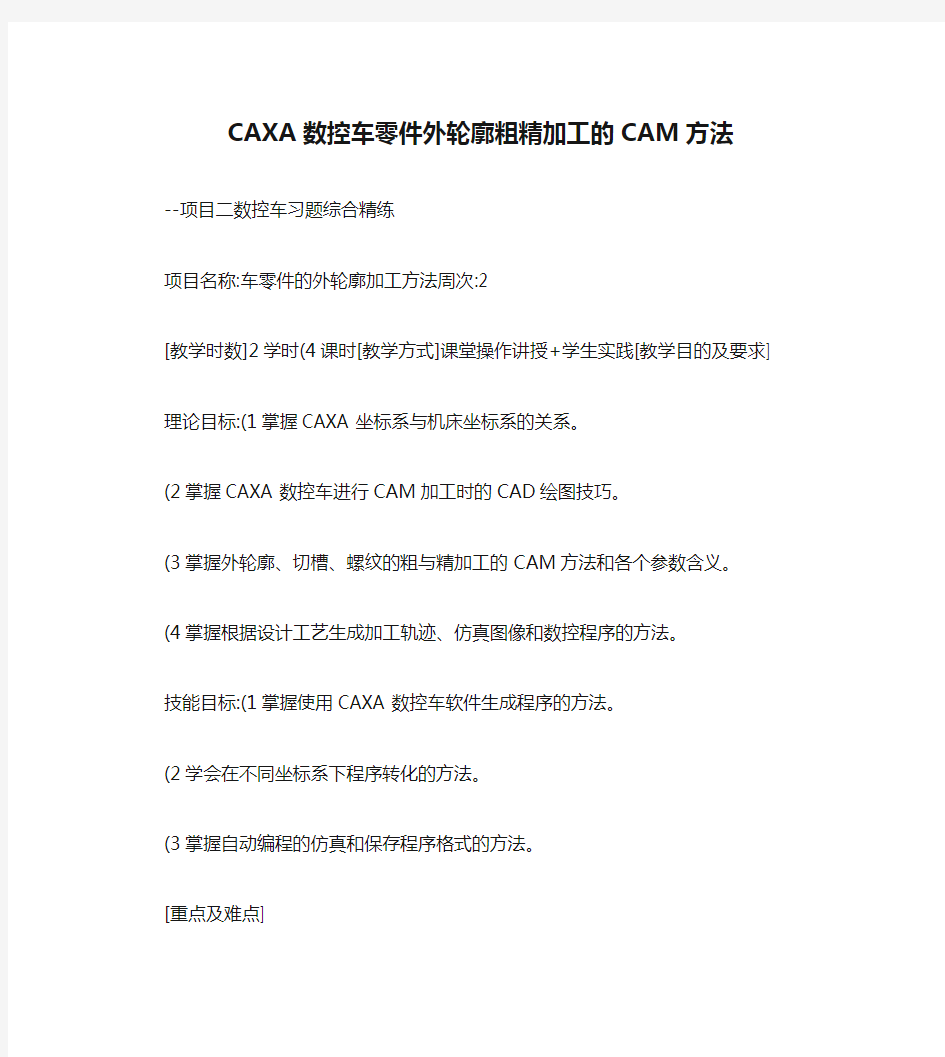

CAXA数控车零件外轮廓粗精加工的CAM方法
--项目二数控车习题综合精练
项目名称:车零件的外轮廓加工方法周次:2
[教学时数]2学时(4课时[教学方式]课堂操作讲授+学生实践[教学目的及要求] 理论目标:(1掌握CAXA坐标系与机床坐标系的关系。
(2掌握CAXA数控车进行CAM加工时的CAD绘图技巧。
(3掌握外轮廓、切槽、螺纹的粗与精加工的CAM方法和各个参数含义。(4掌握根据设计工艺生成加工轨迹、仿真图像和数控程序的方法。
技能目标:(1掌握使用CAXA数控车软件生成程序的方法。
(2学会在不同坐标系下程序转化的方法。
(3掌握自动编程的仿真和保存程序格式的方法。
[重点及难点]
(1粗精加工的各个参数含义。
(2CAXA的编程原点针对元件的意义。
(3切槽加工的精度注意事项。
[教学内容:顺序+时间分配]
一、具体讲授所含章节
2.1 简单成型面的粗、精加工--------------------------------(约50分钟
(1刀具参数的含义
(2进退刀数的含义
(3加工工艺参数的含义
(4轨迹的颜色含义
(5仿真录像和干涉的方法
(6生成程序并保存的方法
2.2 外沟槽的加工---------------------------------------(约20分钟 2.3 外螺纹的加工---------------------------------------(约30分钟
2.4 自主练习数控车习题库--------------------------------(约100分钟
二、重点讲授内容
(一项目要求:。
分组完成完成图2-1~2-7所示的“机械零件”的CAM图纸造型,选择不同的刀具并生成加工轨迹和程序。
2-1、毛坯尺寸Φ85×300mm,材料45钢件。
2-2、毛坯尺寸Φ40×78mm,材料45钢,要求控制总长76mm。
2-3、毛坯尺寸Φ70×120mm,材料45钢。
2-4、毛坯:φ40×95 材料:45钢
2-5、毛坯:直径φ30×100
2-6、毛坯尺寸Φ50×100,材料45钢,要求控制总长98mm尺寸。
2-7、毛坯尺寸Φ50×125,材料45钢,要求控制总长120±0.02mm。
(二项目实施:
(1零件的每部分加工可能需要制作多个CAM图形,需要分别命名保存。例如图2-1需要修改绘制“外轮廓粗(精加工图”、“端面粗(精加工图”、“切槽粗(精加工图”、“螺纹粗(精加工图”四部分。
(2每次加工所选的刀具应该从自己机床刀库内选算。
(3为了防止大家互相复制作业,每个人的加工工艺参数不能相同:每位同学取自己学号的后两位设为A;粗加工的切削量为0.1*A,主轴转速为500*A,精加工加工余量为0.02*A,切削量为0.01*A,主轴转速为1000*A。以此生成各自的加工程序。
[复习作业题]:(一论述:
(1自动编程技术比我们以前所学的手动编程技术有哪些优势?
(2在自动编程过程中,计算机辅助(CA实际上帮助我们做了哪些工作?
(3对比手动编制的程序,计算编出来的程序与人编制的程序有什么不同?
为什么会出现这种那个情况?(二)电子作业:(1)完成以上所有零件的加工图形绘制,并生成各自的程序保存。(三)预习作业(1)主子程序指令,怎样用主子程序指令将不同的程序粘结一体?(2)VNUC 的对刀和程序导入方法。(3)怎样用 G54 指令移动机床的编程加工坐标系。 [课后总结]:后总结]
机械加工方法与零件的粗糙度及精度等级之间的对应表
机械加工方法与零件的粗糙度及精度等级之间的对 应表 序号=1 Ra值不大于\μm=100 表面状况=明显可见的刀痕 加工方法=粗车、镗、刨、钻 应用举例=粗加工的表面,如粗车、粗刨、切断等表面,用粗镗刀和粗砂轮等加工的表面,一般很少采用 ----------------------------------------------------------- 序号=2 Ra值不大于\μm=25、50 表面状况=明显可见的刀痕 加工方法=粗车、镗、刨、钻 应用举例=粗加工后的表面,焊接前的焊缝、粗钻孔壁等 ----------------------------------------------------------- 序号=3 Ra值不大于\μm=12.5 表面状况=可见刀痕 加工方法=粗车、刨、铣、钻 应用举例=一般非结合表面,如轴的端面、倒角、齿轮及皮带轮的侧面、键槽的非工作表面,减重孔眼表面 ----------------------------------------------------------- 序号=4 Ra值不大于\μm=6.3 表面状况=可见加工痕迹 加工方法=车、镗、刨、钻、铣、锉、磨、粗铰、铣齿 应用举例=不重要零件的配合表面,如支柱、支架、外壳、衬套、轴、盖等的端面。紧固件的自由表面,紧固件通孔的表面,内、外花键的非定心表面,不作为计量基准的齿轮顶圈圆表面等 ----------------------------------------------------------- 序号=5 Ra值不大于\μm=3.2 表面状况=微见加工痕迹 加工方法=车、镗、刨、铣、刮1~2点/cm^2、拉、磨、锉、滚压、铣齿 应用举例=和其他零件连接不形成配合的表面,如箱体、外壳、端盖等零件的端面。要求有定心及配合特性的固定支承面如定心的轴间,键和键槽的工作表面。不重要的紧固螺纹的表面。需要滚花或氧化处理的表面 ----------------------------------------------------------- 序号=6
加工中心加工工艺规范
加工中心加工工艺规范 一、龙门加工中心加工工艺规范 操作者必须接受有关龙门加工中心的理论和实践的培训,并且通过考核获得上岗证,才能具备操作龙门加工中心加工的资格。 1、加工前准备 1.操作者必须根据机床使用说明书熟悉机床的性能,加工范围和精度,并且熟悉机床及其数控装置和计算机各部分的作用及其操作方法。 2.检查各开头、旋钮和手柄是否在正确位置。 2、加工要求 1.进行首件加工前,必须经过程序检查、轨迹检查、单程序段试切及工件检查等步骤。 2.加工时,必须正确输入程序,不得擅自更改别人的程序。 3.加工过程中,操作者必须监视显示装置,发现报警信号时,应及时停机排除故障。 4.加工中不得任意打开控制系统及计算机柜。 5.本工序是关键加工工序,所加工的工件经自检合格后,必须送检验员专检。 3、刀具与工件装夹 1.刀具安装应注意刀具使用顺序,刀具安放位置须与程序要求顺序和位置一致。 2.工件装夹应牢固可靠,注意避免在工作中刀具与工件、刀具与刀具发生干涉。 4、加工参数设定 1.主轴转速定义:N=1000*V/3.14*D N--主轴转速(rpm/min) V--加工速度(m/min) D--刀具直径(mm),加工速度在刀具资料中查出 2.进给速度设定:F=N*M*F’ F-进给速度(mm/min),N-主轴转速(rpm/min),M-刀具刃数值,F’-刀具加工量(mm/刃口) 5、工件碰数 对一件装夹好的工件,可以利用碰数头对其进行碰数定工件的加工零件,步骤如下:(机械式碰数头应在旋转状态下,转数450-600rpm/min) 1.手动移动工作台X轴,使碰数头碰工件的一侧面,当碰数头刚碰到工件,红灯发亮,这时就设定这点相对座标值为零。 2.手动移动工作台X轴,使碰数头碰工件的另一侧面,当碰数头刚碰到工件,记下这时的相对座标值。 3.把这时的相对座标值除以2,所得数值就是工件X轴上的中间值。
粗加工的目的
普通车床靠齿轮和普通丝杠螺母传动。由于各运动副间存在间隙,加上手工操作不准确,因此重复精度较低。普通车床测量时需停车后手工测量,测量误差较大,而且效率低下。适合批量较小,精度要求不高,零活类零件。它投资较数控低,但对工人的操作技能要求较高,因此工资水平高。低水平工人的废品率和生产率会让你头疼。 数控车床靠步进电机带动滚珠丝杠传动,由于滚珠丝杠可以有过盈量,传动无间隙,精度主要靠机床本身和程序保证。在加工过程中可以自动测量,并能自动补偿刀具磨损及其他原因产生的误差。所以加工质量好,精度稳定。还可以用编程的方法车出形状复杂,普通车床难以加工的零件。适合精度高,批量大,形状复杂的零件。但小批量生产也很好用。它的维修费用较普通车床高。 立车主要用于大件,它的主轴是垂直的。立车也有数控的。 由于高技术水平的人才越来越缺,现在新上的企业多采用数控,以提高生产率和产品质量,降低废品率和成本。 粗加工的目的是追求高效,要求单位时间有最大切除量,对加工精度和表面质量要求并不是很高,因吃刀量大,加工表面的余量也不是很均匀。而半精加工的目的是把粗加工后的残留加工面加工平滑,在工件加工面上留下比较均匀的加工余量,为精加工的高速切削加工提供最佳的加工条件。 追问: 首先谢谢你的帮助,我还想问下,为什么有的活就不用半精加工这一步,也就是开粗之后直接光刀,而有的就用,能告诉我在什么时候才用半精加工这个环节吗? 回答: 这与被加工零件的最终精度有关,如果零件要求精度不高(例如有些零件表面无需磨削加工),就可以在粗加工后直接光刀,如果零件加工精度要求高的话,就必须在粗加工后增加半精加工以使加工余量变的较为均匀,而且可以尽可能的保证加工表面的形位公差要求。
加工中心的刀具及参数选择
加工中心的刀具及参数选择 刀具的选择和切削用量的确定是数控加工工艺中的重要内容,它不仅影响数控机床的加工效率,而且直接影响加工质量。CAD/CAM技术的发展,使得在数控加工中直接利用CAD的设计数据成为可能,特别是微机与数控机床的联接,使得设计、工艺规划及编程的整个过程全部在计算机上完成,一般不需要输出专门的工艺文件。现在,许多CAD/CAM软件包都提供自动编程功能,这些软件一般是在编程界面中提示工艺规划的有关问题,比如,刀具选择、加工路径规划、切削用量设定等,编程人员只要设置了有关的参数,就可以自动生成NC程序并传输至数控机床完成加工。因此,数控加工中的刀具选择和切削用量确定是在人机交互状态下完成的,这与普通机床加工形成鲜明的对比,同时也要求编程人员必须掌握刀具选择和切削用量确定的基本原则,在编程时充分考虑数控加工的特点。本文对数控编程中必须面对的刀具选择和切削用量确定问题进行了探讨,给出了若干原则和建议,并对应该注意的问题进行了讨论。 一、数控加工常用刀具的种类及特点 数控加工刀具必须适应数控机床高速、高效和自动化程度高的特点,一般应包括通用刀具、通用连接刀柄及少量专用刀柄。刀柄要联接刀具并装在机床动力头上,因此已逐渐标准化和系列化。数控刀具的分类有多种方法。根据刀具结构可分为: ①整体式; ②镶嵌式,采用焊接或机夹式连接,机夹式又可分为不转位和可转位两种;
③特殊型式,如复合式刀具,减震式刀具等。 根据制造刀具所用的材料可分为: ①高速钢刀具; ②硬质合金刀具; ③金刚石刀具; ④其他材料刀具,如立方氮化硼刀具,陶瓷刀具等。 从切削工艺上可分为: ①车削刀具,分外圆、内孔、螺纹、切割刀具等多种; ②钻削刀具,包括钻头、铰刀、丝锥等; ③镗削刀具; ④铣削刀具等。 为了适应数控机床对刀具耐用、稳定、易调、可换等的要求,近几年机夹式可转位刀具得到广泛的应用,在数量上达到整个数控刀具的30%~40%,金属切除量占总数的80%~90%。数控刀具与普通机床上所用的刀具相比,有许多不同的要求,主要有以下特点: ⑴刚性好(尤其是粗加工刀具),精度高,抗振及热变形小; ⑵互换性好,便于快速换刀; ⑶寿命高,切削性能稳定、可靠; ⑷刀具的尺寸便于调整,以减少换刀调整时间; ⑸刀具应能可靠地断屑或卷屑,以利于切屑的排除; ⑹系列化,标准化,以利于编程和刀具管理。 二、数控加工刀具的选择 刀具的选择是在数控编程的人机交互状态下进行的。应根据机床的加工能力、工件材料的性能、加工工序、切削用量以及其它相关因
例子2:3段粗加工精加工
W3: (指定工作罐号3) M68; 在UPH-2/UH-2的情况下 顺序模式 格式:M68; 随机模式 格式M68W_; W_: 指定要把工作卸载到上面的罐号 (在自动工作交换机范围内指定) 自由模式(只用于UPH-2/UH-2) 格式M68(W_);() 可省略 W指令没出现:顺序模式 W指令出现:随机模式 例如:如果工作被卸载到罐号3上(卸载模式:自由模式)M68W3: (指定工作罐号3) 库索引 连同M66-M68指定罐号,只会引起库罐被索引。 格式: M66P_;或M67P_;或M68P_; P_:被索引的罐号 小心:在这种情况下,不能指定工作改变指令W_。
预防措施 如果在加工期间或加工之后,指定了自动工作交换机M模式,那么它必须在执行完加工电源关闭(M18)和电极丝切割(M17,W-PG1不需要)之后再执行。
一旦完成自动工作交换机M代码,轴(X-C轴)在各自的位置上,列示如下: 轴 W-PG1 UPH-1/UPH-2/UH-2 X 第三参考点 第三参考点 Y 第三参考点 第三参考点 U --- 垂直位置 V --- 垂直位置
Z 参考点 第三参考点 C 第三参考点 第三参考点 对于UPH-1/UPH-2/UH-2,如果它处于上(UP)位置,自动工作交换机控制操作在工作罐下移之后,就会启动。
9.21 接近(M71) 尽管可以在条件主屏幕上打开/关闭接近功能,还是可以在程序中通过M71指令进行控制。 关于接近功能的应用,请参考基础操作2.6.1 接近功能 接近功能打开 格式:可省略 M71: 打开接近功能 S_: 指定接近1条件(MGW_K无效) 默认:保持当前的接近1条件 A_:指定接近2条件(MGW_K无效) 默认:保持当前的接近2条件 注意1:必须在M17区前面指定接近功能打开。 注意2:在用户条件区(E9000-E9999),必须提前输入接近1和接近2条件。(J型电源单元)。 接近功能关闭 M17L1:关闭接近功能。
第四章数控加工中心操作编程练习题
第四章数控加工中心操作与编程练习题 思考与练习题 1、数控加工中心按功能特征可分为哪几类?按自动换刀装置的型式可分为哪几类?加工中 心有什么特点? 答:按功能特征分类: (1)镗铣加工中心 (2)钻削加工中心 (3)复合加工中心 按所用自动换刀装置分类: (1)转塔头加工中心 (2)刀库+ 主轴换刀加工中心 (3)刀库+ 机械手+ 主轴换刀加工中心 (4)刀库+ 机械手+ 双主轴转塔头加工中心 2、刀库通常有哪几种形式?哪种形式的刀库装刀容量大? 答:加工中心常用的刀库有鼓轮式和链式刀库两种;链式刀库装刀容量大。 3、自动换刀装置的换刀过程可分为哪两部分?在程序中分别用什么代码控制? 答:自动换刀装置的换刀过程由选刀和换刀两部分组成。当执行到Txx指令即选刀指令后,刀库自动将要用的刀具移动到换刀位置,完成选刀过程,为下面换刀做好准备;当执行到M06指令时即开始自动换刀,把主轴上用过的刀具取下,将选好的刀具安装在主轴上。 4、顺序方式和任选方式的选刀过程各有什么特点? 答:顺序选刀方式是将加工所需要的刀具,按照预先确定的加工顺序依次安装在刀座中,换刀时,刀库按顺序转位。这种方式的控制及刀库运动简单,但刀库中刀具排列的顺序不能错。 任选方式是对刀具或刀座进行编码,并根据编码选刀。它可分为刀具编码和刀座编码两种方式。刀具编码方式是利用安装在刀柄上的编码元件(如编码环、编码螺钉等)预先对刀具编码后,再将刀具放在刀座中;换刀时,通过编码识别装置根据刀具编码选刀。采用这种方式编码的刀具可以放在刀库的任意刀座中;刀库中的刀具不仅可在不同的工序中多次重复使用,而且换下来的刀具也不必放回原来的刀座中。刀座编码方式是预先对刀库中的刀座(用编码钥匙等方法)进行编码,并将与刀座编码相对应的刀具放入指定的刀座中;换刀时,根据刀座编码选刀,使用过的刀具也必须放回原来的刀座中。 5、画图表示并说明主轴移动方式自动换刀的实现过程?这种方式适用于哪类加工中心?答:
各种加工方式对应的粗糙度等级
1级 Ra值不大于口m=100 表面状况=明显可见的刀痕 加工方法=粗车、镗、刨、钻 应用举例=粗加工的表面,如粗车、粗刨、切断等表面,用粗镗刀和粗砂轮等加工的表面,一般很少采用 2级 Ra值不大于口m=25 50 表面状况=明显可见的刀痕 加工方法=粗车、镗、刨、钻 应用举例=粗加工后的表面,焊接前的焊缝、粗钻孔壁等 3级 Ra值不大于口m=12.5 表面状况=可见刀痕 加工方法=粗车、刨、铣、钻 应用举例=一般非结合表面,如轴的端面、倒角、齿轮及皮带轮的侧面、键槽的非工作表面,减重孔眼表面 4级 Ra值不大于口m=6.3 表面状况=可见加工痕迹 加工方法=车、镗、刨、钻、铣、锉、磨、粗铰、铣齿 应用举例=不重要零件的配合表面,如支柱、支架、外壳、衬套、轴、盖等的端面。紧固件的自由表面,紧固件通孔的表面,内、外花键的非定心表面,不作为计量基准的齿轮顶圈圆表面等 5级 Ra值不大于口m=3.2 表面状况=微见加工痕迹 加工方法=车、镗、刨、铳、舌I」1?2点/cm A2、拉、磨、锂、滚压、铳齿 应用举例=和其他零件连接不形成配合的表面,如箱体、外壳、端盖等零件的端面。要求有定心及配合特性的固定支承面如定心的轴间,键和键槽的工作表面。不重要的紧固螺纹的表面。需要滚花或氧化处理的表面 6级 Ra值不大于口m=1.6 表面状况=看不清加工痕迹 加工方法=车、镗、刨、铳、铰、拉、磨、滚压、舌I」1?2点/期人2铳齿 应用举例=安装直径超过80mm 的G 级轴承的外壳孔,普通精度齿轮的齿面,定位销孔,V 型带轮的表面,外径定心的内花键外径,轴承盖的定中心凸肩表面 7级 Ra值不大于口m=0.8 表面状况=可辨加工痕迹的方向 加工方法=车、镗、拉、磨、立铳、舌I」3?10点/cmA2、滚压 应用举例=要求保证定心及配合特性的表面,如锥销与圆柱销的表面,与G 级精度滚动 轴承相配合的轴径和外壳孔,中速转动的轴径,直径超过80mm 的E、D 级滚动轴承配
CAXA数控车零件外轮廓粗精加工的CAM方法教案
CAXA数控车零件外轮廓粗精加工的CAM方 法教案 CAXA数控车零件外轮廓粗精加工的CAM方法 CAXA数控车零件外轮廓粗精加工的CAM方法 --项目二数控车习题综合精练 项目名称:车零件的外轮廓加工方法周次:2 [教学时数]2学时 [教学方式]课堂操作讲授+学生实践[教学目的及要求] 理论目标:掌握CAXA坐标系与机床坐标系的关系。掌握CAXA数控车进行CAM加工时的CAD绘图技巧。 掌握外轮廓、切槽、螺纹的粗与精加工的CAM方法和各个参数含义。掌握根据设计工艺生成加工轨迹、仿真图像和数控程序的方法。技能目标:掌握使用CAXA数控车软件生成程序的方法。 学会在不同坐标系下程序转化的方法。掌握自动编程的仿真和保存程序格式的方法。 [重点及难点] 粗精加工的各个参数含义。 CAXA的编程原点针对元件的意义。切槽加工的精度注意事项。 [教学内容:顺序+时间分配] 一、具体讲授所含章节简单成型面的粗、精加工-------------------------------- (1)刀具参数的含义
(2)进退刀数的含义 (3)加工工艺参数的含义 (4)轨迹的颜色含义 (5)仿真录像和干涉的方法 (6)生成程序并保存的方法 外沟槽的加工--------------------------------------- 外螺纹的加工--------------------------------------- 自主练习数控车习题库-------------------------------- 二、重点讲授内容项目要求:。 分组完成完成图2-1~2-7所示的“机械零件”的CAM图纸造型,选择不同的刀具并生成加工轨迹和程序。 2-1、毛坯尺寸Φ85×300mm,材料45钢件。 2-2、毛坯尺寸Φ40×78mm,材料45钢,要求控制总长76mm。 2-3、毛坯尺寸Φ70×120mm,材料45钢。 2-4、毛坯:φ40×95 材料:45钢 2-5、毛坯:直径φ30×100 2-6、毛坯尺寸Φ50×100,材料45钢,要求控制总长98mm尺寸。 2-7、毛坯尺寸Φ50×125,材料45钢,要求控制总长120±。项目实施: 零件的每部分加工可能需要制作多个CAM图形,需要分别命名保存。例如图2-1需要修改绘制“外轮廓粗加工图”、“端面粗加工图”、“切槽粗加工图”、“螺纹粗加工图”四部分。 每次加工所选的刀具应该从自己机床刀库内选算。
加工中心培训教程
加工中心培训教程 Ⅰ安全知识 一、一般的警告和注意 1.我公司机床没有安全防护门,为了安全,在自动和MDI方式下必须合上安全门才能执行程序。机床设有三色报警灯,机床正常并且主轴和驱动轴静止时用绿灯指示,当机床处于运动中时用黄灯指示,而当有报警或程序执行完毕时将点亮红色灯。 2.急停用于危险状况下终止机床轴运动和外围运动设备,系统MDI键盘上的RESET按钮用于CNC复位或者消除系统报警。这两种情况都不会引起坐标位置的丢失,但将使系统终止正在运行 的程序而进入复位状态(坐标系回刀G54、刀具补偿丢失、模态代码回到开机状态)。 3.零件加工前,一定要首先检查程序的坐标系、刀补数据等。执行程序必须从程序开始部分执行。加工前,一定要通过试车保证机床正确工作,例如在机床上不装工件和刀具时利用单程序段、进给倍率检查机床的正确运行。如果未能确认机床动作的正确性,机床有可能发生误动作,从而引起工件或机床本身的损坏,甚至伤及用户。 4.当使用刀具补偿功能时,请仔细检查补偿方向和补偿量。如果指定了不正确的数据操作机床,机床有可能发生误动作,从而引起工件或机床本身的损坏,甚至伤及用户。 5.在机床通电后,CNC单元尚未出现位置显示或报警画面之前,请不要碰MDI 面板上的任何键。BEIJING- FANUC Oi-MB 操作说明书MDI 面板上的有些键专门用于维护和特殊的操作。按下这其中的任何键,可能使CNC 装置处于非正常状态。在这种状态下启动机床,有可能引起机床的误动作。 二、与编程相关的警告和注意 在编程之前,请认真阅读FANUC操作说明书和编程说明书,以确保完全熟悉其内容。 1.坐标系的设定 如果没有设置正确的坐标系,即使指定了正确的指令,机床仍有可能发生误动作。这种误动作有可能损坏刀具、机床、工件甚至伤害用户。 2.非线性插补定位 当使用G0进行非线性插补定位时(在起点和终点之间,利用非线性运动进行定位),在编程之前请仔细确认刀具路径的正确性。这种定位包括快速移动,如果刀具和工件发生了碰撞,有可能损坏刀具、机床、工件甚至伤害用户。 FANUC 系统G0运动是非直线运动,从A 点到B点先沿Y向45°移动到X点的水平线,再 沿X 向直线移动到目标B点。 3.英制/公制转换 输入的英制和公制之间转换并不转换例如工件的原点、参数和当前的位置这些数据的测量单位。因此,在启动机床之前,要确定采用何种测量单位。如果试图采用不正确的数据进行操作会导致刀具、机床、工件的损坏,甚至伤及用户。 4.绝对值/增量值方式 如果用绝对坐标编制的程序在增量方式下运行时,或者反过来,机床有可能发生误动作。 5.平面选择
第2讲CAXA数控车零件外轮廓粗精加工的CAM方法(精)
CAXA数控车零件外轮廓粗精加工的CAM方法 --项目二数控车习题综合精练 项目名称:车零件的外轮廓加工方法周次:2 [教学时数]2学时(4课时[教学方式]课堂操作讲授+学生实践[教学目的及要求] 理论目标:(1掌握CAXA坐标系与机床坐标系的关系。 (2掌握CAXA数控车进行CAM加工时的CAD绘图技巧。 (3掌握外轮廓、切槽、螺纹的粗与精加工的CAM方法和各个参数含义。(4掌握根据设计工艺生成加工轨迹、仿真图像和数控程序的方法。 技能目标:(1掌握使用CAXA数控车软件生成程序的方法。 (2学会在不同坐标系下程序转化的方法。 (3掌握自动编程的仿真和保存程序格式的方法。 [重点及难点] (1粗精加工的各个参数含义。 (2CAXA的编程原点针对元件的意义。 (3切槽加工的精度注意事项。 [教学内容:顺序+时间分配] 一、具体讲授所含章节 2.1 简单成型面的粗、精加工--------------------------------(约50分钟 (1刀具参数的含义
(2进退刀数的含义 (3加工工艺参数的含义 (4轨迹的颜色含义 (5仿真录像和干涉的方法 (6生成程序并保存的方法 2.2 外沟槽的加工---------------------------------------(约20分钟 2.3 外螺纹的加工---------------------------------------(约30分钟 2.4 自主练习数控车习题库--------------------------------(约100分钟 二、重点讲授内容 (一项目要求:。 分组完成完成图2-1~2-7所示的“机械零件”的CAM图纸造型,选择不同的刀具并生成加工轨迹和程序。 2-1、毛坯尺寸Φ85×300mm,材料45钢件。
开粗加工工艺规范
1.目的 规范工件开粗、调质、去应力加工工艺,防止工件变形,减少加工工步,提升加工效率。 2.适用范围 本规范适用于江苏新泉模具有限公司 3.引用文件 无 4.术语定义 反中粗:为了避免工件在开粗和热处理后造成应力集中,二次加工变形而采用的机械加工工艺; 5.职责分工 5.1工程师职责要求:工程师下发开粗图形前必须做到以下 5.1.1产品收缩率必须确定,产品数据必须是客户下达的可以开粗的数据; 5.1.2热流道热嘴的位置必须确定; 5.1.3产品柱位出司筒针、镶芯(未镶拼)的位置必须按照要求做出圆台; 5.1.4产品落差大的斜面上的顶杆也必须留出圆台; 5.1.5加工顺序为开粗后加工水路的,后续水路加工的平台必须留出; 5.1.6必须保证精加工图不可以比开粗图多铁。 5.1.7对于硬模,热处理前,图形状态必须是达到精加工图状态,螺纹, 水路,顶杆孔都加工完成。 5.2机加工主管职责要求: 编制加工工艺卡:开粗、反中粗加工余量审核,特殊加工工艺要求的制定,生产计划按照作业规范安排; 5.3 质量部按照平台稽核处理。
6. 作业流程图 无 7. 作业内容说明 7.1开粗余量定义: 7.1.1无需热处理的材料(2738、718等),开粗后,不需要调质、时效 去应力,直接进行半精、精加工; 余量设置(表一) 模板长度 开粗余量 反中粗余量 ﹥1500mm 2mm 1、原则上按照0.3mm 设置。 2、厂内加工工件由编程根据编程工艺、刀具选择等方面,可自 行更改。 3、外放工件由机加工主管根据 外协厂家资质把中粗余量交接到位。 ≦1500mm 1mm 1000mm 以下 0.5mm 1、 工件(细长件、扁平件等)可适当增加开粗余量,放置工件变形 2、 开粗时顶杆和司筒孔要留台,水路留台 7.1.2需热处理的材料(P20、S50C 锻打、调质工件等),开粗后→调质→ NC 反中粗→去应力→精捆五面。 吊环孔 型腔开粗 反中粗余量 3D 设计 调质吊环孔 模板长度 开粗余量 M30 M24 保险杠A0 10mm 2mm M36 M30 M42 M36 >1500mm 8mm 1mm M48 M42 M56 M48 ≤1500mm 5mm 1mm M64 M56
谈车削加工中的粗车和精车
谈车削加工中的粗车和精车 辉县市职业中专王其华 【摘要】:车削加工实质就是按照零件图纸尺寸的要求,在确保公差质量的情况下,将毛坯多余的材料快速去除的过程。加工既要保证质量又要保证效率,工艺上将车削分为粗车和精车,工序中讲究先粗后精的原则。粗车是尽可能快的去除多余的余量以提高效率,精车是保证工件的精度以达到技术参数要求,二者之间既有联系又有区别。 【关键字】:粗车精车切削用量加工工艺【正文】: 车削加工实质就是按照零件图纸尺寸的要求,在确保公差质量的情况下,将毛坯多余的材料快速去除的过程。加工既要保证质量又要保证效率,工艺上将车削分为粗车和精车,工序中讲究先粗后精的原则。粗车是尽可能快的去除多余的余量以提高效率,精车是保证工件的精度以达到技术参数要求,二者之间既有联系又有区别。下面结合我的实践和认识谈一下我个人的看法: 一、什么是粗车和精车。 “粗车”是加工工艺中的粗加工工序,主要是将工件表面的多余材料切削,一般对产品尺寸、粗糙度要求不高。粗加工主要是切除加工表面的大部分加工余量,在允许范围内应尽量选择大的切削深度和进给量。而切削速度则相应选低点。粗车所能达到的加工精度为IT12~ITll,表面粗糙度Ra为50~12.5μm。 “精车”是加工工艺中的精加工工序,需要保证产品的尺寸公差,行位公差,表面粗糙度的相应要求。精加工主要是达到零件的全部尺寸和技术要求,半精车和精车应尽量选取较小的切削深度和进给量,而切削速度则可以取高点。精车要求切削深度要小,走刀量也要小,精车完毕后,不但工件的直径几何尺寸要合格,而且对表面的粗糙度要求也较高,而且也要合格。精车的加工精度可达IT8~IT6级,表面粗糙度Ra可达1.6~0.8μm行位公差,表面粗糙度的相应要求。精加工主要是达到零件的全部尺寸和技术要求,半精车和精车应尽量选取较小的切削深度和进给量,而切削速度则可以取高点。精车要求切削深度要小,走刀量也要小,精车完毕后,不但工件的直径几何尺寸要合格,而且对表面的粗糙度要求也较高,而且也要合格。精车的加工精度可达IT8~IT6级,表面粗糙度Ra可达1.6~0.8μm。
在数控车床上实现椭圆的粗、精加工
数控车床加工对象为各种类型的回转面,其中对于圆柱面、锥面、圆弧面、球面等的加工,可以利用直线插补和圆弧插补指令完成,而对于椭圆等一些非圆曲线构成的回转体,加工起来具有一定的难度。这是因为大多数的数控系统只提供直线插补和圆弧插补两种插补功能,更高档的数控系统提供双曲线、正弦曲线和样条曲线插补功能,但是一般都没有椭圆插补功能。因此,在数控机床上对椭圆的加工大多采用小段直线或者小段圆弧逼近的方法来编制椭圆加工程序。 在这里结合工作实践对车削椭圆轮廓的宏程序的编制方法进行探讨。 一、椭圆宏程序的编制原理 数控系统的控制软件,一般由初始化模块、输入数据处理模块、插补运算处理模块、速度控制模块、系统管理模块和诊断模块组成。其中插补运算处理模块的作用是依据程序中给定的轮廓的起点、终点 等数值对起点终点之间的坐标点进行数据密化,然后由控制软件,依据数据密化得到的坐标点值驱动刀具依次逼近理想轨迹线的方式来移动,从而完成整个零件的加工。 依据数据密化的原理,我们可以根据曲线方程,利用数控系统具备的宏程序功能,密集的算出曲线上的坐标点值,然后驱动刀具沿着这些坐标点一步步移动就能加工出具有椭圆、抛物线等非圆曲线轮廓的工件。 二、椭圆宏程序的编制步骤 宏编程一般步骤: 1.首先要有标准方程(或参数方程)一般图中会给出。 2.对标准方程进行转化,将数学坐标转化成工件坐标标准方程中的坐标是数学坐标,要应用到数控车床上,必须要转化到工件坐标系中。 3.求值公式推导利用转化后的公式推导出坐标计算公式 4.求值公式选择根据实际选择计算公式 5.编程公式选择好后就可以开始编程了 三、加工实例 下面分别就工件坐标原点与椭圆中心重合,偏离等2种情况进行编程说明。 (1)工件坐标原点与椭圆中心重合 椭圆标准方程为 ① 转化到工件坐标系中为
B类宏程序的应用——椭圆粗、精加工
非圆曲线编程是手工编程中的难点,本文以椭圆加工为例,介绍了循环功能(WHILE语句)在椭圆宏程序编程中的应用。 椭圆是数控车加工中相对较难却又比较典型的非圆曲线,目前数控系统还没有提供完善的非圆曲线插补功能,因此在实际操作中椭圆的编程多采用变量来完成。虽然随着计算机辅助编程的进一步普及,手工编写宏程序越来越少,但作为初学者,根据不同情况,掌握各种非圆曲线,特别是椭圆曲线的编程仍然是必要的。 一、循环功能WHILE语句 椭圆宏程序编制中重要的循环功能语句是WHILE语句,其格式如下: WHILE[条件表达式] DO m(m=1,2,3) ; END m ; 说明:如果指定的条件表达式满足时,则执行DO到END 之间的程序。否则,转道END后面的程序段。DO后面的标号和END 后面的标号是指程序执行范围的标号,标号值为1,2,3。 二、椭圆标准方程与参数方程 编制椭圆宏程序要熟悉椭圆标准方程和参数方程,它们均表达出了椭圆上点的坐标及两坐标之间的关系。例如:图1中, 椭圆的标准方程为(20mm为长半轴的长,14mm为短半轴的长,椭圆的中心即为坐标系的原点),参数方程为X=20cosФ,Y=14sinФ(Ф为角度参数)。 宏程序编制中,编程坐标系是Z 、X 轴,所以在应用椭圆标准方程或参数方程时,要从X、Y轴相应转换为编程坐标系中的Z 、X轴。如上例椭圆在X、Z坐标系中的标准方程则为: (图2),参数方程相应转换为X=14sinФ,Z=20cosФ。 变量编程时,注意椭圆上点的坐标在椭圆坐标系和在编程坐标系中的不同表达,两者之间的联系在于椭圆原点在编程坐标系中的值。椭圆坐标系原点在椭圆圆心,编程坐标系及原点
开粗加工工艺规范
开粗加工工艺规范 Document serial number【KKGB-LBS98YT-BS8CB-BSUT-BST108】
1.目的 规范工件开粗、调质、去应力加工工艺,防止工件变形,减少加工工步,提升加工效率。 2.适用范围 本规范适用于江苏新泉模具有限公司 3.引用文件 无 4.术语定义 反中粗:为了避免工件在开粗和热处理后造成应力集中,二次加工变形而采用的机械加工工艺; 5.职责分工 5.1工程师职责要求:工程师下发开粗图形前必须做到以下 5.1.1产品收缩率必须确定,产品数据必须是客户下达的可以开粗的数据; 5.1.2热流道热嘴的位置必须确定; 5.1.3产品柱位出司筒针、镶芯(未镶拼)的位置必须按照要求做出圆台; 5.1.4产品落差大的斜面上的顶杆也必须留出圆台; 5.1.5加工顺序为开粗后加工水路的,后续水路加工的平台必须留出; 5.1.6必须保证精加工图不可以比开粗图多铁。 5.1.7对于硬模,热处理前,图形状态必须是达到精加工图状态,螺 纹,水路,顶杆孔都加工完成。 5.2机加工主管职责要求:
编制加工工艺卡:开粗、反中粗加工余量审核,特殊加工工艺要求的制定,生产计划按照作业规范安排; 5.3质量部按照平台稽核处理。 6.作业流程图 无 7.作业内容说明 7.1开粗余量定义: 7.1.1无需热处理的材料(2738、718等),开粗后,不需要调质、时 效去应力,直接进行半精、精加工; 余量设置(表一) 质→NC反中粗→去应力→精捆五面。
300毫米以下工件,余量0.5毫米/单边 300~600毫米工件,余量1毫米/单边 600毫米以上工件,余量2毫米/单边 7.2需热处理的材料(P20、S50C锻打、调质工件等)工件加工工艺规范: 7.2.1杀底面粗飞侧面加工调质吊环孔(公制粗牙螺纹:先比设计吊环 孔加工小一号); 7.2.2型腔粗飞四面分中底面垫刀取数正面开粗(工件长度L≦1500mm 开粗单边留5mm余量,工件长度﹥1500mm开粗单边留8mm余 量,细长工件特殊指示),四周单边留5mm铣一段基准; 7.2.3调质(调质处理包括:淬火加硬---高温回火去应力); 7.2.4质检检测硬度; 7.2.5调质后NC反中粗,反中粗余量设置见上面表二,用反中粗图形 加工(反中粗时对称检测型腔余量,并观察是否均匀,防止工件 加工有偏差。),铣精捆边四侧面底面基准(工件四角长100mm 深20mm),特例保险杠A0反中粗到2MM余量; 7.2.6工件时效去应力:回火处理或振动; 7.2.7精捆侧面和底面到净数,精捆工件底面需要考虑型腔反中粗Z向 抬起的1mm; 7.2.8加工侧面吊装孔(三维图形要求); 7.2.9检验出货(调质硬度、基准面垂直度、基准面平面度); 7.2.10工件检测合格后单边取数按正常工艺加工; 7.2.11P20、S50C反中粗图形要求:
数控加工中心的基本操作
数控加工中心的基本操作 主讲苏清
什么是加工中心 加工中心是一种功能较全的数控加工机床。它能把铣削、镗削、钻削、攻螺纹和切削螺纹等功能集中在一台设备上,使其具有多种工艺手段。它的综合加工能力较强,工件一次装夹后能完成较多的加工内容,而且加工精度较高,就中等加工难度的批量工件,其效率是普通设备的5~10倍,特别是它能完成许多普通设备 不能完成的加工,对形状较复杂,精度要求高的单件加工或中小批量多品种生产更为适用。
加工中心的加工特点 加工中心与其它数控机床相比,具有以下特点: 1、加工的工件复杂、工艺流程较长,能排除人为 干扰因素,具有较高的生产效率和质量稳定性。 2、工序集中、具有自动换刀装置,工件在一次装 夹后能完成有高精度要求的铣、钻、镗、扩、铰、攻丝等复合加工。 3、在具有自动交换工作台时,一个工件在加工时, 另一个工作台可以实现工件的装夹,从而大大缩 短辅助时间,提高加工效率。 4、刀库容量越大,加工范围越广,加工的柔性化 程度越高。
加工中心的组成 从主体上看,加工中心主要由以下几大部分组成: 1.基础部件 2.主轴部件 3.数控系统 4.自动换刀系统 5.辅助装置
基础部件是加工中心的基础结构,它主要由床身、工作台、立柱三大部分组成。 这三大部分不仅要承受加工中心的静载 荷,还要承受切削加工时产生的动载荷。 所以要求加工中心的基础部件,必须有 足够的刚度,通常要求这三大部件都是 铸造而成。
主轴部件由主轴箱、主轴电动机、主轴和主轴轴承等零部件组成。主轴是加工中心切削加工的功率输出部件,它的起动、停止、变速、变向等动作均由数控系统控制;主轴的旋转精度和定位准确性,是影响加工中心加工精度的重要因素。
粗镗加工步骤介绍(精)
粗镗加工步骤 调试步骤: 1、铣盘与玉米铣刀刀长顾宏富处对出,机床上不得修改。 2、X向与Y向坐标铰刀铰出,并作记录,做不同工件时根据图纸对 应偏出所要数据,输入对应OFFSET。 3、Z向坐标必须调出29号玉米铣刀得出。具体方法是:MDI转速开, 试切大面,OFFSET对应坐标Z0测量,然后减去玉米铣刀刀长,玉米铣刀刀长数值查看OFFSET对应刀补。 4、拉杆孔端面毛刺去干净,保证工件底面贴平,(顶针别顶的太用力 了)装夹牢靠,查看是否有缝隙。若在精加工发现大面平面度大于50丝的,一块100元,查不出谁做的,整个工序的人每人100元。 5、调出对应程序,明确加工工序。头板:全部做掉。二板:无顶出 孔,全部做掉,有特殊情况会通知。有顶出孔,大面只点出,若要做大面,请确认做否。 6、粗镗刀试切。只要有余量供模板镗的出的,就不偏坐标。经卡尺 确认的确是镗不出的,可选择偏,原则上只偏X向,数值为 0.5-1mm,若要偏1mm以上的,必须让领导知道。对偏的值一律 输入OFFSET的00坐标,并及时在模板上作好记号,标好方向与偏的数值。若未作记录留向下一道工序的模板,一块100元,查不出谁做的,整个工序的人每人100元,所扣得钱全部奖给在精加工发现问题的人。 7、按程序调试好其他的刀。注意换刀调出后一定要跟上程序段:
G91G28Z0M19。 8、清理工件,掉下工件,敲好钢印,不敲钢印的不许开工时,并准 备好首检。 程序调试后开始批量生产后注意事项: 1、敲好钢印。 2、装夹问题:拉杆孔端面毛刺去干净,保证工件底面贴平,(顶针别 顶的太用力了)装夹牢靠,查看是否有缝隙。 3、做之前看一下OFFSET的00坐标,一定要都是0才能做。切记。 4、试镗。确定镗不出了才偏坐标,1mm内的自己偏就好,不用吊下, 偏1mm以上的一定要让领导知道。对偏了做的,一定要作好记录。 试镗时还要看一下深度,太浅或太深了在OFFSET的00坐标得Z 坐标改一下。保证点孔部会大了,也不会小了。
--6 等高精加工
6. 等高精加工 等高精加工 等高精加工方式類似於粗加工中之外行輪廓加工, 其依據所指定之Z 軸向高度產生X-Y 平面之加工路徑. 故此方式較適合於較陡峭之區域或直壁邊上. 點取等高精加工圖形選鈕 ,將顯示如下之對話框: 對話框中之各選項說明如下. 每層下刀 最小刀間距選項為設定等高加入時Z 軸之每層加工深度。 當 刀痕高度計算選項關閉時, 等高精修之每層加工深度等於 最小刀間距所設定之數值. 當刀痕高度計算設定開啟時, 系統將自動計算每次加工Z 深度 , 使得連續之Z 軸進給深 度將不會超過 刀痕高度 之設定值. 當計算出之數值小於最小刀間距時, 系統將自動設定為最小刀間距. 依區域加工 當 依區域加工選項開啟時, 刀具路徑順序將依區域加工亦即一封閉區域中每層皆加工完畢後再移動至其他區域故可減少提刀次數, 反之若將其關閉則加工順序乃依每層加工指定。 方向 此參數提供有 逆銑 、順銑 或 雙向 三個加工方向指定. 刀具 刀痕 刀 痕高 度
邊界修剪 當邊界修剪參數設定為關閉時,則模型整體將被加工. 若欲使用特定邊界來限制加工區域則可將此參數其設定如下. 1) 保留外部: 加工區域為輪廓邊界之外部. 2) 保留內部: 加工區域為輪廓邊界之內部. 等高精修範例 此將藉由一範例說明各參數之使用方法. ?開啟模型“ chamber.tri”. ?素材設定為最大/最小尺寸 +2 mm. ?設定刀具為直徑 = 10mm 球刀. ?將提刀高度和刀具起始點依新素材重新設定. ?點取等高精修圖形選鈕並指定每層下刀為2mm,後點取對話框中執行選鈕計算等高精修路徑。 計算完成之路徑顯示如上圖. 課後練習: ?於Examples目錄中載入模型mouse.tri. ?素材 = 最大/最小尺寸+10mm,刀具 = 6mm (直徑) 球刀. ?設定等高精修最小刀間距=6mm,依區域加工選項關閉. ?使用線性模擬功能模擬等高精修路徑選擇下拉功能表線性模擬—精加工. ?將依區域加工選項設定為開啟,並計算路徑 . ?使用線性模擬功能模擬等高精修路徑並觀察其變化.
铣床、加工中心高速、高精加工的参数调整
铣床、加工中心高速、高精加工的参数调整 使用铣床或加工中心机床加工高精度零件(如模具)时,应根据实际机床的机械性能对CNC系统(包括伺服)进行调整。在FANUC的AC 电机的参数说明书中叙述了一般调整方法。本文是参数说明书中相关部分的翻译稿,最后的“补充说明”叙述了一些实际调试经验和注意事项,仅供大家参考。 对于数控车床,可以参考此调整方法。但是车床CNC系统无G08和G05功能,故车床加工精度(如车螺纹等)不佳时,只能调整HRV参数和伺服参数。Cs控制时还可调整主轴的控制参数。 目录 使用αi电机…………………………………………………P 2 使用α电机……………………………………………………P22 补充说明………………………………………………………P24 1 3.4.1伺服HRV控制的调整步骤 ⑴概述 i系列CNC(15i/16i/18i)的伺服因为使用了HRV2和HRV3控制(21i为选择功能),改善了电流回路的响应,因此可使速度回路和位置回路设定较高而稳定的增益值。
图 3.4.1(a) 使用伺服HRV控制后的效果 速度回路和位置回路的高增益,可以改善伺服系统的响应和刚性。因此可以减小机床的加工形状误差,提高定位速度。 由于这一效果,使得伺服调整简化。HRV2控制可以改善整个系统的伺服性能。伺服用HRV2调整后,可以用HRV3改善高速电流控制,因此可进行高精度的机械加工。 若伺服HRV控制与CNC的预读(Look-ahead)控制,AI轮廓控制,AI纳米轮廓控制和高精度轮廓控制相结合,会大大改善加工性能。关于这方面的详细叙述,请见3.4.3节“高速、高精加工的伺服参数调整”。 2 图3.4.1(b) 伺服HRV控制的效果实例 ⑵适用的伺服软件系列号及版本号 90B0/A(01)及其以后的版本(用于15i,16i,18i和21i,但必须使用320C5410伺服卡)。
机械加工方法与零件的粗糙度及精度等级之间的对应表
机械加工方法与零件的粗糙度及精度等级之间的对应表序号=1 Ra值不大于\μm=100 表面状况=明显可见的刀痕 加工方法=粗车、镗、刨、钻 应用举例=粗加工的表面,如粗车、粗刨、切断等表面,用粗镗刀和粗砂轮等加工的表面,一般很少采用 ----------------------------------------------------------- 序号=2 Ra值不大于\μm=25、50 表面状况=明显可见的刀痕 加工方法=粗车、镗、刨、钻 应用举例=粗加工后的表面,焊接前的焊缝、粗钻孔壁等 ----------------------------------------------------------- 序号=3 Ra值不大于\μm=12.5 表面状况=可见刀痕 加工方法=粗车、刨、铣、钻 应用举例=一般非结合表面,如轴的端面、倒角、齿轮及皮带轮的侧面、键槽的非工作表面,减重孔眼表面 ----------------------------------------------------------- 序号=4 Ra值不大于\μm=6.3
表面状况=可见加工痕迹 加工方法=车、镗、刨、钻、铣、锉、磨、粗铰、铣齿 应用举例=不重要零件的配合表面,如支柱、支架、外壳、衬套、轴、盖等的端面。紧固件的自由表面,紧固件通孔的表面,内、外花键的非定心表面,不作为计量基准的齿轮顶圈圆表面等 ----------------------------------------------------------- 序号=5 Ra值不大于\μm=3.2 表面状况=微见加工痕迹 加工方法=车、镗、刨、铣、刮1,2点/cm^2、拉、磨、锉、滚压、铣齿应用举例=和其他零件连接不形成配合的表面,如箱体、外壳、端盖等零件的端面。要求有定心及配合特性的固定支承面如定心的轴间,键和键槽的工作表面。不重要的紧固螺纹的表面。需要滚花或氧化处理的表面 ----------------------------------------------------------- 序号=6 Ra值不大于\μm=1.6 表面状况=看不清加工痕迹 加工方法=车、镗、刨、铣、铰、拉、磨、滚压、刮1,2点/cm^2铣齿应用举例=安装直径超过80mm的G级轴承的外壳孔,普通精度齿轮的齿面,定位销孔,V 型带轮的表面,外径定心的内花键外径,轴承盖的定中心凸肩表面----------------------------------------------------------- 序号=7 Ra值不大于\μm=0.8 表面状况=可辨加工痕迹的方向