加工轴承端盖4-Φ12孔——工艺装备钻床设计

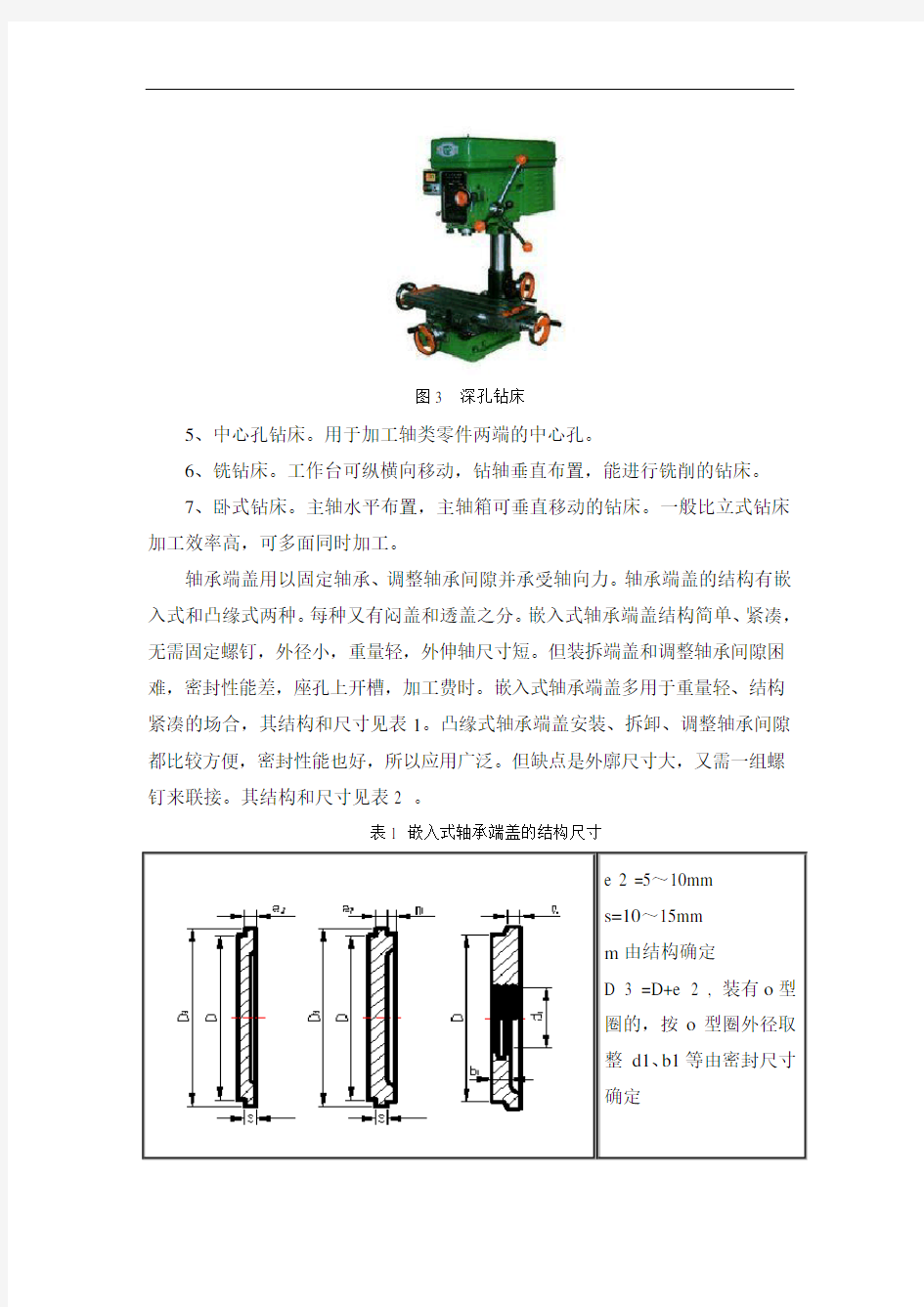
第一章绪论
1.1 课题的研究背景和意义
钻床是具有广泛用途的通用性机床,可对零件进行钻孔、扩孔、铰孔、锪平面和攻螺纹等加工。在钻床上配有工艺装备时,还可以进行镗孔,在钻床上配万能工作台还能进行钻孔、扩孔、铰孔。如图1所示为钻床的实物图。
图1 钻床实物图
钻床主要用钻头在工件上加工孔(如钻孔、扩孔、铰孔、攻丝、锪孔等)的机大型钻床车间床。机械制造和各种修配工厂必不可少的设备。根据用途和结构主要分为以下几类:
1、立式。工作台和主轴箱可以在立柱上垂直移动,用于加工中小型工件。
2、台式。简称台钻。一种小型立式钻床,最大钻孔直径为12~15毫米,安装在钳工台上使用,多为手动进钻,常用来加工小型工件的小孔等。
3、摇臂式。主轴箱能在摇臂上移动,摇臂能回转和升降,工件固定不动,适用于加工大而重和多孔的工件,广泛应用于机械制造中。
4、深孔钻床。用深孔钻钻削深度比直径大得多的孔(如枪管、炮筒和机床主轴等零件的深孔)的专门化机床,为便于除切屑及避免机床过于高大,一般为卧式布局,常备有冷却液立式钻床输送装置(由刀具内部输入冷却液至切削部位)及周期退刀排屑装置等。如图3所示。
图3 深孔钻床
5、中心孔钻床。用于加工轴类零件两端的中心孔。
6、铣钻床。工作台可纵横向移动,钻轴垂直布置,能进行铣削的钻床。
7、卧式钻床。主轴水平布置,主轴箱可垂直移动的钻床。一般比立式钻床加工效率高,可多面同时加工。
轴承端盖用以固定轴承、调整轴承间隙并承受轴向力。轴承端盖的结构有嵌入式和凸缘式两种。每种又有闷盖和透盖之分。嵌入式轴承端盖结构简单、紧凑,无需固定螺钉,外径小,重量轻,外伸轴尺寸短。但装拆端盖和调整轴承间隙困难,密封性能差,座孔上开槽,加工费时。嵌入式轴承端盖多用于重量轻、结构紧凑的场合,其结构和尺寸见表1。凸缘式轴承端盖安装、拆卸、调整轴承间隙都比较方便,密封性能也好,所以应用广泛。但缺点是外廓尺寸大,又需一组螺钉来联接。其结构和尺寸见表2 。
表1 嵌入式轴承端盖的结构尺寸
e 2 =5~10mm
s=10~15mm
m由结构确定
D 3 =D+e 2 , 装有o型
圈的,按o型圈外径取
整d1、b1等由密封尺寸
确定
表2 凸缘式轴承端盖的结构和尺寸
do =d3 +1mm ,d3—端盖联接螺栓直径,尺寸见右表。D1=D+2.5d3
D2 =D1 +2.5d3
e=1.2d3
e 1 ≥ e
m 由结构确定
D4 =D- (10~15 )mm
b1、d1由密封尺寸确定
b=5~10mm
h=(0.8~1)b 轴承外径
D
螺栓直径
d 3
端盖上螺栓数
目
45~65
70~100
110~140
150~230
6
8
10
12~16
4
4
6
6
当端盖与孔的配合处较长时,为了减少接触面,在端部铸出或车出一段较小的直径,但必须保留有足够的长度e1,一般此处的配合长度为e1=(0.10~0.15 )D,D为轴承外径,图中端面凹进δ值,也是为了减少加工面,如图4所示。
图4 轴承端盖端部结构
由于端盖多用铸铁铸造,所以要很好考虑铸造工艺。例如在设计穿通式轴承端盖图5时,由于装置密封件需要较大的端盖厚度(图5a),这时应考虑铸造工艺,尽量使整个端盖厚度均匀,如图5b和c所示是较好的结构。
图5 轴承端盖端部结构
1.2 轴承端盖的概述
轴伸出端的密封的作用是防止轴承处的润滑剂流出和箱外的污物、灰尘和水气进入轴承腔内,常见的密封种类有接触式密封和非接触式密封两大类,接触式密封有毡圈密封、O 形橡胶圈密封、唇形密封,非接触式密封有沟槽密封和迷宫密封。
下面主要介绍毡圈密封和O 形橡胶圈密封。
(1 )毡圈密封
将矩形毡圈压入梯形槽中使之产生对轴的压紧作用而实现密封,如图6。它的结构简单,价格低廉,安装方便,但接触面的摩擦磨损大,毡圈寿命短,功耗大,一般用在轴颈圆周速度v <5m/s 、工作温度t <90 0 C 、脂润滑的轴
承中。安装前,毡圈需用热矿物油(80~90° C )浸渍。
图6 毡圈密封装置
( 2 )O 形橡胶圈密封
利用安装沟槽使O形橡胶圈受到压缩而实现密封,在介质作用下产生自紧作用而增强密封效果。O形橡胶圈有双向密封的能力,其结构简单,O形橡胶圈为标准件,可直接选用。
1.3 本课题主要研究内容
1)总体设计及方案分析:总体方案设计、不同方案的分析及确定。主要为:夹具、多轴头及钻摸板(包括:主要结构工作原理分析、动力分析和运动分析)。
2)校核计算:在初步的结构设计的完成后,对设计方案进行进一步的校核、计算;对主要零、部件进行必要校核分析计算;对设备的使用及维护加以说明等。
3)经济性分析:从提高生产率、制造成本、经济效益、社会效益等方面对所完成的设计进行分析。
第二章电机的选型和传动零部件设计计算
1 设计计算任务要求
本设计题目是钻床工艺装备设计——加工端盖4-Φ12孔。具体的设计内容为利用摇臂钻床一次钻削端盖4-Φ12孔的相应夹具、多轴头及悬挂式钻模板。
通过设计该工装设备可以同时完成端盖4孔的钻削。用夹具装夹工件时,工件相对于刀具及机床的位置精度由夹具保证,使同一批工件的加工精度趋于一致,保证工件的加工精度,同时很大程度提高生产率。
本题目研究的内容在国内、外属于成熟装置,对于提高生产率保证加工精度具有明显优势。由于大批量生产的需要,设计制造并运用本套工装夹具,可以大幅提高生产率;同时采用本套夹具也使加工精度得到了提高,有很高的性价比。
该题目来源于生产实际,通过这次毕业设计我能够系统和全面地利用所学的专业知识,为今后工作奠定坚实的基础。
2 钻孔负载扭矩的计算和电机选型
2.1 钻孔切削参数的确定
钻孔的切削用量与钻孔深度有关,当加工铸铁件孔深为钻孔直径的6~8倍时,在组合机床上通常都是和其他浅孔一样采取一次走刀的办法加工出来,不过加工这种较深孔的切削用量要适当降低一些。其切削用量与多轴箱钻削浅孔时切削用量的关系大致按表1和表2所示递减规律,根据具体情况适当选择。降低进给量的目的是为了减小轴向切削力,以避免钻头折断。钻孔深度较大时,由于冷却排屑条件都较差,使刀具寿命有所降低。降低切削速度主要是为了提高刀具寿命,并使加工较深孔时钻头的寿命与加工其它浅孔时钻头的寿命比较接近。
表1 钻孔推荐切削用量
表2 钻孔推荐切削用量
2.2 切削用量确定
组合机床的正常工作与合理地选择切削用量,即确定合理的切削速度和工作进给量有很大的关系,切削用量选的恰当,能使组合机床以最少的停车损失,最高的生产效率,最长的刀具寿命和最好的加工质量,也就是多快好省的进行生产。组合机床大多为多刀加工,而且是多种刀具同时工作。计算最佳切削用量的工作比较复杂。
确定了在组合机床上完成的工艺内容后,就可以着手选择切削用量。目前组合机床的切削用量的选择,主要是参考现场采用的切削用量的情况,根据积累的经验来进行。由于组合机床有大量的刀具同时工作,为了能使机床能正常工作,不经常停车换刀,而达到较高的生产效率,所选的切削用量比一般的万能机床单刀加工要低一些。可概括地说:在多轴加工的组合机床上不宜最大的切削用量。
确定切削用量应注意的问题:
1、尽量做到合理利用所有的刀具,充分发挥其性能。由于连接于动力部件的主轴箱上同时工作时的刀具种类和直径大小不等,因此其切削用量的选择也各有特点。如钻孔要求切削速度高而每转进给量小;铰孔却要求切削速度低而每转进给量大等。同一主轴箱上的刀具每分钟进给量是相同的,要使每把刀具均能有合适的切削用量是困难的。一般情况下可先按各类刀具选择较合理的主轴转速n (转/分)和每转进给量f(毫米/分),然后进行适当的调整使各刀具的每分钟进给量相同,皆等于动力滑台的每分钟进给量vf。这样各类刀具都不是按最合理的切削用量而是按一个中间的切削用量工作。假如确实需要,也可按多数刀具选用一个统一的每分钟进给量,对少数刀具采用附加机构(增、减速)机构,使之按各自需要的合理进给量工作。以达到合理使用刀具的目的。
2、选择切削用量时,应考虑零件批量生产的影响。生产率要求不高时,就
没有必要将切削用量选得过高,以免降低刀具得耐用度,对于要求生产率高得大批量生产用组合机床,也只是提高那些耐用度低,刃磨困难,造价高得所谓“限制性”工序刀具得切削用量。但必须注意不能影响加工的精度,也不能使刀具耐用度降低。对于“非限制性”刀具,应采取不使刀具耐用度降低的某一极限值,这样可减少切削功率。组合机床通常要求切削用量的选择使刀具耐用度不低于一个工作班,最少不低于4小时。
3、切削用量的选择应有利于主轴箱设计。若能作到相邻主轴转速接近相等,则可以使主轴箱传动链简单;某些刀具带导向加工时,若不便冷却润滑,则应适当降低切削速度。
4、选择切削用量时,还必须考虑所选的动力滑台的性能。尤其采用液压动力滑台时,所选的每分钟进给量一般比动力滑台可实现的最小进给量大50%。否则,会由于温度和其他原因导致进给量不稳定,影响加工精度,甚至造成机床不能工作。
切削用量的选择必须从实际出发,根据加工精度、工件材料,工作条件、技术要求等进行分析,按照经济地满足加工要求地原则,合理地选择切削用量。一般常用查表法,参照生产现场同类工艺,通过工艺试验确定切削用量。
根据生产经验,在组合机床上进行孔加工的切削用量按表3选取:
表3 高速钢钻头切削用量
由上表可见,根据工件的材料与加工的孔径,可以选择合适的切削用量。
根据加工零件的材料及硬度:
切削深度(mm ) a p =d/2=10.2/2=5.1mm 每刃进给量(mm/r ) 2
f
f z =
f =(0.01~0.02)d ; 取0.015 f =0.015×
10.2=0.153 mm/r =
z f 2
f
=0.153/2=0.076mm/r 取v c =18m/min
1000
dn
v c π=
n=720r/min
主轴转速定为720r/min 。
参照《组合机床设计手册》组合机床切削用量计算图中推荐的切削力、转矩及功率公式:
表4 钻扩铰切削力、转矩及功率公式
由表4知:钻孔直径为12的切削力,切削转矩和切削功率为: F=26D 0.8HB 0.6=26×6.60.8×227.330.6=26×4.5251725.94144=3052.13(N ) T=10D 1.9f 0.8HB 0.6=10×6.61.9×0.80.8×227.330.6=10×36.06895×0.83651×25.94144
=7827.06 (N ﹒mm)
P=Tv/9740πD=7827.06×10/(9740×3.14×6.6)=0.388(KW) 2.3 电动机的初选
(1) 选择电动机类型
按工作要求和条件,选用三相异步电动机,电压380V ,Y 型。 (2) 选择电动机的容量
初选电动机型号为Y2—712—2,其主要参数如下表2-1:
表2-1 电动机参数
电动机输出转矩:
=d T 9550
m d n P N ?m=95502820
55.0 N ?m=1.86 N ?m 式中1η、2η分别为轴承、齿轮传动的传动效率。
取1η=0.98(滚子轴承), 2η=0.97(齿轮精度为8级,不包括轴承效率)。 (3) 确定电动机转速
根据机械设计手册,钻孔所必需满足的转速最低为:
n = 60min
r
根据传动比合理取值,取一级齿轮的传动比i '
1
≈2,二级涡轮蜗杆减速器传动比i '2≈20,则总传动比合理范围为i 'a ≈40,故电动机转速约为:
n 'd = i 'a ?n=4060?=2400min
r
2.4
确定传动装置的总传动比和分配传动比
由选定电动机满载转速n m 和工作机主动轴转速n,可得传动装置总传动比为
n
n i m
a =
(2-1) 总传动比为各级传动比1i ,、2i 、3i n i ???的乘积,即电动机型号为Y2-712-2,满载转速n m =2820min
r
。
(1) 总传动比 由上式(2-1):
n n i m a =
=
=60
2820
47 (2)分配减速器的各级传动比
按展开式布置。考虑润滑条件,得=1i 2,2i =19.5,则此时的输出转速为
n a m i n =
5
.1922820
?=
=72.31min r 2.5 确定各轴转速、转矩和功率
(1) 各轴转速
1i n n m =
min r
(2-2) 式中:m n ——电动机满载转速;
0i ——电动机至I 轴的传动比。
以及 II n =
1
01i i n i n m I
?= min r (2-3)
2
102i i i n i n n m II
III ??==
min r (2-4)
由式(2-3)~(2-5)得
I 轴 01i n n m =
=2
2820
=1410 min r
II 轴 II n = I n = 1410 min
r
III 轴 201m II III n n n i i i =
=?= 2820
219.5
? = 72.31 min r
(2) 各轴输入功率
d I P P =?3η kW (2-5)
12II I P P η=? kW , 1223ηηη=? (2-6) 23III II P P η=? kW,2323ηηη=? (2-7)
式中2η、3η分别为轴承、齿轮传动的传动效率。 由式(5)~(7)得
I 轴 d I P P =01η= 0.55 ×0.98 =0.54kW
II 轴 12II I P P η=? = 23d P ηη?? = 0.539?0.98?0.97 =0.51kW III 轴 III P 2323II II P P ηηη=?=??=0.51=??80.098.0 0.40 kW
I —III 轴的输出功率则分别为输入功率乘轴承效率0.98,例如I 轴输出功率为
=?=98.0'I I P P 0.53kW,其余类推。
(3) 各轴输入转矩
001I d T T i η=? N ?m (2-8)
其中d T 为电动机的输出转矩,按下式计算:
=d T 9550
m
d
n P N ?m (2-9) 所以
001I d T T i η=? = 9550
001d
m
P i n η?? N ?m (2-10) 112II I T T i η=??= 9550
010112d
m
P i i n ηη???? N ?m (2-11) 223III II T T i η=?? = 9550
012011223d
m
P i i i n ηηη?????? N ?m (2-12) 34IV III T T η=? = 9550
01201122334d
m
P i i i n ηηηη??????? N ?m (2-13) 由式(8)~(13) 电动机轴输出转矩 =d T 9550m d n P =9550?2820
55.0= 1.86 N ?m I —III 轴的输入转矩
I 轴 001I d T T i η=? = 9550
01d
m
P n η??0i =1.86?0.97× 2 = 3.61N ?m II 轴 I II T T =?1η=1T ×0.97=3.61?0.97 =3.50 N ?m
III 轴 223III II T T i η=??=212II T i ηη???= 3.50?19.5?0.98?0.80 = 53.51 N ?m
I~III 轴的输出转矩则分别为各轴的输入转矩乘轴承效率0.98,例如I 周的输出转矩为=?=98.0'I I T T 3.61×0.98=3.54 N ?m,其余类推。
运动和动力参数计算结果如下表2-2:
表2-2 运动和动力参数
2.6 电动机的校核
(1)转矩校核
加载在钻刀转轴上的负载为钻刀旋转刀架的重力,其中刀架厚度为15mm :
G 1=g ρν=5.6×310×[4×0.015×0.16×0.06+4π×(26.0-255.0)×0.03+4
π
×(22.0-212.0)
×0.03]×10=150N
刀盘的重量,其中转盘厚度为30mm :
G 2=g ρν+70×24=5.6×310×0.15×4
π
×266.0=4560N
则可得作用在轴3上的转矩
T /3 =μGd 3=0.004×(4560+150)×0.06 N ?m =1.13 N ?m
可得T /3 由上述计算可知电动机要满足刀库最低每分钟60转的要求,则此电动机转速应不低于n 'd = i 'a ?n=4060?=2400min r ,而此次选的电动机的转速为 n m =2820min r ,即n m > n 'd ,故此电动机的转速也满足转速要求。 综合考虑电动机和传动装置的尺寸、转矩、价格和带传动、减速器的传动比,可见此电动机比较合适,因此选定电动机型号为Y2-112-2。 3 齿轮传动的设计计算 1、选择齿轮类型、精度等级、材料及齿数 1)选用直齿轮 2)钻床为一般工作机器且轻质载荷,故选用7级精度(GB10095-88) 3)材料选择。选择小齿轮材料为40r C (调质),硬度为280HBS ,大齿轮材 料为45钢(调质)硬度为240HBS ,二者材料硬度差为40HBS 。 4)选小齿轮齿数1z =20,传动比为i = 2, 大齿轮齿数2z = 2?20 = 40。 2、按齿面接触强度设计 由设计计算公式进行试算,即 t d 1≥2.323 2 1)] [(1H E d Z u u KT σ±?Φ (1) 确定公式内的各计算数值 1)试选载荷系数t K =1.3。 2)计算小齿轮传递的转矩。 1T == ?1 15105.95n P 141054 .0105.955?? N ?mm=0.3657?410 N ?mm 3)由表选取齿宽系数d Φ= 1。 4)由表查得材料的弹性影响系数E Z = 189.8 2 1 a MP 5)由表按齿面硬度查得小齿轮的接触疲劳强度极限1lim H σ=600a MP ;大齿轮的接触疲劳强度极限2lim H σ=550a MP 。 6)计算应力循环次数。 1N = 60h jL n 1 = 60?1410?1?(2?8?365?8)= 1.441?9 102N =75 .510441.19 ?=0.251?910 7)由图取接触疲劳寿命系数1HN K =0.95;2HN K =0.96。 8)计算接触疲劳许用应力。 取失效概率为100,安全系数S = 1,由式得 [H σ]1= S K HN 1 lim 1σ=0.95?600a MP =570a MP [H σ]2= S K HN 2 lim 2σ=0.96?550a MP =528a MP (2) 计算 1)试算小齿轮分度圆直径t d 1,代入[H σ]中较小的值。 t d 1≥2.32321)][(1H E d Z u u KT σ+?Φ=2.3232 4 )528 8.189(2121103657.03.1+???mm=22.6mm 由于机床实际的尺寸关系,这里小齿轮的分度圆直径取为t d 1=40mm 2)计算圆周速度v 。 v=11601000t πd n ?=40514601000 π???s m =1.08s m 3)计算齿宽b 。 根据机床经验公式,齿宽为模数的6~8倍,这里模数先试取2,故b =(6~8)m = 16mm , 这里取b=20mm 4)计算齿宽与齿高之比h b 。 模数 t m = 1 1z d t = 40/20 mm = 2 mm 齿高 h = 2.25t m = 2.25?2 mm = 4.5 mm h b = 096 .5353 .54= 10.67 5)计算载荷系数。 根据v = 1.46s m , 7级精度,由图10—8查得动载系数v K = 1.06 [21]; 直齿轮,αH K =αF K =1 由表查得使用系数A K =1.25; 由表用插值法查得7级精度、小齿轮相对支承非对称布置时,βH K =1.420。 由 h b = 10.67, βH K =1.420查图得βF K =1.35;故载荷系数: K =A K v K αH K βH K =1.25?1.06?1?1.420 = 1.8815 6)按实际的载荷系数校正所得的分度圆直径,由式得: 1d =t d 13 t K K =40?33.18815.1=45.246mm 7)计算模数m : m = 11z d =20 246.45mm = 2.26mm 3、按齿根弯曲强度设计 弯曲强度的设计公式为 m ≥3 211)] [(2F Sa Fa d Y Y z KT σΦ (1) 确定公式内的各计算数值 1)由图查得小齿轮的弯曲疲劳强度极限1FE σ=500a MP 大齿轮的弯曲强度极限2FE σ=380a MP 2)由图取弯曲疲劳寿命系数1FN K =0.88,2FN K =0.90; 3)计算弯曲疲劳许用应力。 取弯曲疲劳安全系数S=1.4,由式得: [F σ]1= S K FE FN 11σ= 4.1500 88.0?a MP =314.29a MP [F σ]2= S K FE FN 22σ= 4 .1380 90.0?a MP =244.29a MP 4)计算载荷系数K 。 K=A K v K αF K βF K =1.25?1.06?1?1.35=1.789 5)查取齿形系数。 由表查得 1Fa Y =2.80;2Fa Y =2.40。 6)查取应力校正系数。 由表查得 1Sa Y =1.55;2Sa Y =1.67。 7)计算大、小齿轮的 ] [F Sa Fa Y Y σ并加以比较。 111][F Sa Fa Y Y σ=29.31455 .180.2?=0.01381 222][F Sa Fa Y Y σ=29 .24467 .140.2?=0.01640 大齿轮的数值大。 (2) 设计计算 m ≥3 2 4 01640.020 1103657.0789.12????? mm=0.81 mm 故可知上面所预选的模数m=2符合设计要求。 1z = m d t 1=2 40=20 大齿轮齿数 2z =2?20=40。 4、几何尺寸计算 (1)计算分度圆直径 1d =1z m=20?2=40 mm 2d =2z m=40?2=80 mm (2)计算中心距 a= 221d d +=2 80 40+mm = 60mm (3)计算齿轮宽度 根据机床实际设计取值,取1B =20mm,2B =15mm 。 5、结构设计及绘制齿轮零件图3-1 图3-1 齿轮配合 第三章夹具和钻模板及多轴箱的设计与绘图 1 夹具的设计 1.1 机床夹具的组成 尽管生产中使用的夹具种类繁多,结构多变,而且新型夹具又不断出现,然而机床夹具的结构仍具有许多共同之处。 1、定位元件及定位装置。 用于确定工件正确位置的元件或装置。凡是夹具都有定位元件,它是实现夹具基本功能的元件。 2、夹紧元件及夹紧装置。 用于固定工件已获得的正确位置的元件或装置。工件定位之后必须将其夹紧,使其在加工时,在切削力等的作用下不离开已获得的定位。夹具的夹紧机构千变万化,所有能用于夹紧的机构和原理都可以考虑。 3、导向元件。 确定刀具的位置并引导刀具的元件,称为导向元件。导向元件只有钻、镗类夹具才具备。导向元件也可供钻镗类夹具在机床上安装时作基准找正用。 4、对刀元件及定向元件。 确定刀具相对夹具定位元件的位置的元件,称为对刀元件。 5、夹具体。 夹具体用于将各种元件、装置联接于一体,并通过它将整个夹具安装在机床上。夹具体一般采用铸铁制造。它是保证夹具刚度和改善夹具动力学特性的重要部分。如果夹具体的刚性不好,加工时将会引起较大的变形和振动,产生较大的加工误差。 6、其他元件及装置。 根据加工需要设置的元件或装置,如分度装置、驱动定位销的传动装置、气缸及管路附件、液压缸及油路、电动装置等。 1.2 工件的定位 1、工件的定位原理 在制定工件的工艺规程时,已经初步考虑了加工工艺基准问题,有时还绘制 了工序简图。设计夹具时原则上应选该工艺基准为定位基准。无论是工艺基准还是定位基准,均应符合六点定位原理。 六点定位原理是采用六个按一定规则布置的约束点,限制工件的六个自由度,使工件实现完全定位。这里要清楚每个点都必须起到限制一个运动自由度的作用,而绝不能用一个以上的点来限制同一个自由度。 2、完全定位和不完全定位 根据工件加工表面的位置要求,有时需要将工件的六个自由度全部限制,称为完全定位。有时需要限制的自由度少于六个,称为不完全定位。 在加工中,有时为了使定位元件帮助承受切削力、夹紧力,为了保证一批工件进给长度一致,减少机床的调整和操作,常常会对无位置尺寸要求的自由度也加以限制,只要这种定位方案符合六点定位原理,是允许的,有时也是必要的。 3、欠定位与过定位 根据加工表面的位置尺寸要求,需要限制的自由度均已被限制,这就称为定位的正常情况,它可以是完全定位,也可以是不完全定位。 根据加工表面的位置尺寸要求,需要限制的自由度没有完全被限制,或某自由度被两个或两个以上的约束重复限制,称之为非正常情况,前者又称为欠定位,它不能保证位置精度,是绝对不允许的。后者称为过定位或重复定位,加工中一般是不允许的,它不能保证正确的位置精度,但在特殊场合下,如果应用得当,过定位不仅是允许的,而且会成为对加工有利的因素。 1.3 常用定位元件及其所能限制的自由度数 常用的定位元件有支承钉、支承板、定位销、锥面定位、V形块、定位套、锥度心轴等等。 1、支承钉 在分析所能限制的自由度时,都认为它们相当于一个几何点,形成一个定位副,所以只能限制一个自由度;两个支承钉组合形成直线定位副,限制两个自由度;三个支承钉组合形成平面定位副,限制三个自由度。支承钉组合多用于粗基准定位中。 2、支承板 这类定位元件多用于精基准平面定位且成组使用。使用时必须保证一组支承 板等高。故支承板的工作面装配后在一道工序中精磨,保证等高。一组支承板,与精基准面接触形成平面定位副,相当于三个支承钉或三个点定位副,限制三个自由度。一块长支承板定位时,形成线定位副,限制两个自由度。 3、定位销 这是工件以孔为基准时最常用的定位元件。根据定位销和基准孔的有效接触长度与孔径之比,可分为短定位销和长定位销两种。一般有效长度L小于(0.5~0.8)d时,可视为短销;有效长度L大于(0.8~1.2)d时,视为长销。分析短销所能限制的自由度时,从理论上讲,把它看成接触长度无限短的无间隙接触的定位副。短销只限制了工件的x、y移动两个自由度,而不能限制z的移动和转动自由度。在结构设计上,为了保证定位销的强度和提高耐磨性,则必须具有一定的接触长度,但应尽可能短些。 工件用长定位销定位,可以看成两个短销和工件基准孔的接触定位。长销能限制工件的两个移动和两个转动自由度。 为了安装方便,定位销和工件的基准孔之间留有一定的间隙,间隙的大小按加工工件的精度要求而定。 除上述两种圆柱定位销外,削边圆柱销也是常用的一种孔定位元件。削边销也分短销和长销两种。削边销是为了补偿工件的定位基准与夹具定位元件之间的实际尺寸误差,消除过定位而采用的。它的直径选择除留有必要的安装间隙外,还需要考虑补偿上述误差所需要的间隙。在分析削边销所能限制的自由度时,由于必要的间隙所引起的移动和转动可不予考虑,这样削边短销只能限制一个自由度,削边长销只能限制两个自由度。 4、锥面定位销 它的工作面是锥面,限制了三个移动自由度。在实际应用中,为了减少基准孔棱边的误差对定位的影响,常采用削边锥面定位销。削边锥面定位销用于粗基准孔的定位设计中,锥顶角一般取为。 5、V形块 工件以外圆柱面定位时,不管是粗基准还是精基准均可采用这种定位元件。它也分短V形块和长V形块两种。一般V形块和工件定位面的接触长度小于工件定位直径时,属于短V形块;大于1.5~2倍工件定位直径时,属于长V形块。 专业课程设计 (零件工艺设计部分) 姓名: 学号:20090.................. 班级:机械工程学院09级工业工程班指导教师:李方义、查黎敏 2013年1月17日 一、零件的工艺分析 1、端盖的用途 端盖是应用广泛的机械零件之一,是轴承座的主要外部零件。 端盖的一般作用是:轴承外圈的轴向定位;轴承工作过程的防尘和密封(除本身可以防尘和密封外,也常和密封件配合以达到密封的作用);位于车床电动机和主轴箱之间的端盖,主要起传递扭矩和缓冲吸震的作用,使主轴箱的转动平稳。因此该零件应具有足够的强度、刚度、耐磨性和韧性,以适应其的工作条件。该零件的主要工作表面为左右端面以及左端面的外圆表面,在设计工艺规程时必须重点考虑。端盖加工工艺的可行性与合理性直接影响零件的质量、生产成本、使用性能和寿命等。 2、端盖工艺性分析 该端盖主要由平面、外圆面以及孔系组成,其结构简单、形状普通,属于一般的盘盖类零件。端盖主要加工表面有左、右和凸台等三个端面,Φ47和Φ80两个外圆面,Φ34和Φ16两个内圆面,密封圈内槽以及六个均布的Φ7的通孔。要求其Φ7孔的右端加工平面对于基准A的垂直度公差是0.03mm,端盖的Φ47外圆面与基准A的同轴度误差为0.03mm,其次就是均布的φ7孔的加工端面要求为平面,可以防止加工过程中钻头偏斜以保证孔的加工精度。 其中,端面和内外圆面均要求车削加工,可以采用半精车和粗车,并且粗、精加工应分开进行,以保证表面粗糙度要求;φ7通孔的加工采用钻铰来达到精度要求。其余非配合表面加工精度较低,不需要高精度机床加工,通过粗车和半精车就可以在正常的生产条件下,采用较经济的方法加工出来;此外,该零件材料为铸铁HT200,切削加工性能较好。 综上所述,该端盖零件的工艺性能良好。 (1)工件的时效处理 对于毛坯为铸件的盖类零件,因其各部位厚度不均匀,存在较大的铸造内应力,容易造成变形等缺陷,因此必须安排人工时效处理。对于本端盖,其精度要求一般,则可利用粗、精加工工序间的自然停放和运输时间,得到自然时效处理的效果。其自然时效处理的时间越长越好,否则会影响端盖配合精度的稳定性。 对于特别精密的端盖,在粗加工和精加工工序间还应安排一次人工时效,以消除铸造内应力,提高精度稳定性。 (2)加工工艺的顺序应先面后孔 作为端盖上主要的两类加工表面——平面和孔,从定位稳定可靠的角度上分析,平面比孔要优越得多,同时还可以使孔的加工余量均匀;从加工难度上分析,平面比孔容易加工;从有利加工的进行上分析,采用先加工平面后加工分布在平面上的孔,由于铸件表面的凹凸不平和夹砂等缺陷已被切除,大大有利于孔加工的进行。 前言 随着科学技术的发展,各种新材料、新工艺和新技术的不断涌现,机械制造工艺正向着高质量、高生产率和低成本方向发展。各种新工艺的出现,已突破传统的依靠机械能、切削力进行切削加工的范畴,可以加工各种难加工材料、复杂的型面和某些具有特殊要求的零件。数控机床的问世,提高了更新频率的小批量零件和复杂的零件加工的生产率及加工精度。特别是计算机技术的迅速发展,极大的推动了机械加工工艺的进步使工艺过程的自动化达到了一个新的阶段。 工具是人类文明进步的标志。自20世纪末以来,现代制造技术与机械制造工艺自动化得到了很好的发展。但工具(含刀具、夹具、量具与辅具等)在不断的革新中,起功能仍然十分显著。机床夹具是一种装夹工件的工艺设备,它广泛地应用于机械制造过程的切削加工、热处理、装配、焊接和检测等工艺过程中。在各种金属切削机床上用于装夹工件的工艺设备成为机床夹具,如车床上使用的三爪自定心卡盘、四爪卡盘,铣床上使用的平口虎钳等。现代生产中,机床夹具是一种不可缺少的工艺装备,它直接影响着工件的加工精度、劳动生产率和产品的制造成本等。因此,无论是在传统制造还是现代制造工艺系统中,夹具都是重要的工艺装备。 一、夹具的功能 1.保证加工质量使用机床夹具的首要任务是保证加工精度,特别是保证被加工工件加工面与定位面之间以及被加工表面相互之间的位置精度。使用机床夹具后,这种精度主要靠夹具和机床来保证,不再依赖工人的技术水平。 2.提高生产效率,降低生产成本使用夹具后可减少划线、找正的辅助时间,且易实现多件、多工位加工。在现代机床加工中,广泛采用气动、液动等机动加紧装置,可是辅助时间进一步减少。 3.扩大机床工艺范围在机床上使用夹具可使加工变得方便,并可扩大机床的工艺范围。例如,在机床或钻床上使用镗模,可以代替镗床镗孔。又如,使用靠模夹具,可在车床或铣床上进行仿形加工。 4.减轻工人劳动强度,保证安全生产。 1.冲压工艺性分析及冲压模方案确定 工件名称:端盖 生产批量:大批量 材料:F 08 材料厚度:2mm 零件图 1.1 冲压工艺性分析 (1)冲压件为F 08钢板,是优质碳素结构钢,具有良好的可冲压性能; (2)该工件没有厚度不变的要求,因此工件的形状满足拉深工艺要求。各圆角尺寸R=1mm ,满足拉深对圆角半径的要求。由φ24+00.23mm 查参考文献[1]中表7.14可知它的尺寸精度为IT13级,满足拉深工序对工件的公差等级的要求。 (3)该零件的外形是圆形,比较简单、规则。工件中间有孔,且孔在平面上,。这部分可以用冲裁工序完成. (4)零件图上未标注尺寸偏差的,可按IT14级确定工件尺寸的公差。经查参考文献[1]中表7.14,各尺寸为: 6.1-00. 36mm R10036.0-mm R7036.0-mm 3.005+φmm 48435.0±mm 。 1.2 工艺方案及模具结构的确定 根据工件的根据工件的工艺性分析,可知冷冲压要完成的基本工序有:拉深、落料、冲孔和整形。由此制定两套工艺方案: 方案一:先落料,然后冲孔,再拉伸,三个简单模,此方案模具结构简单,使用寿命长,制造周期短,但是需要三道工序,三套模具才能完成零件的加工,生产率低,难以满足零件大批量生产的要求,而且工件尺寸的累积误差大,所需要的模具操作人员也比较多。 方案二:拉深、落料、冲孔复合模。此方案模具结构紧凑,工序集中,对压力机工作台面的面积要求较小,且内外形相对位置及零件尺寸的一致性非常好,制件面平直,并且制造精度高。缺点是结构复杂,安装、试和维修不方便,制造周期长。由零件图可知,圆筒件部分的拉深尺寸不大,亦可一次拉成,可以考虑采用复合模;又由于产品批量较大,工序分散的单一工序生产不能满足生产需求,应考虑集中的工艺方法。经综合分析论证,采用拉深、落料、冲孔复合模既能满足生产量的要求,又能保证产品质量和模具的合理性,故采用方案二。 2 模具的设计 2.1 落料模设计计算 2.1.1毛坯尺寸及排样 根据公式 D=rd dH dp 44.34)2(2-++δ 计算出展平后φ38mm 所变化成的直径大小。 D=20144.31.4204)638(??-??++ 目录 一、课程设计任务书………………………………………… 二、序言……………………………………………………… 三、零件工艺分析…………………………………………… 四、确定生产类型…………………………………………… 五、毛坯选择和毛坯图说明………………………………… 六、零件表面加工方法的选择……………………………… 七、工艺路线的制定………………………………………… 八、工序间尺寸、公差、表面粗糙度及毛坯尺寸的确定… 九、加工余量,切削用量,工时定额的确定……………… 十、心得与体会………………………………………………十一、参考资料书目…………………………………………… 蚌埠学院机械制造学课程设计任务书 层次:本科专业:2011机械设计制造与自动化本 6 任务书审定日期年月日指导教师(签字) 任务书下达日期2014 年 6 月 3 日学生(签字) 1轴承盖的工艺性分析 1.1轴承盖用途 轴承盖的主要作用是轴承外圈的轴向定位;防尘和密封,除它本身可以防尘和密封外,它常和密封件配合以达到密封的作用。还能在一定程度上防止滚动体保持架等易损件受外力作用而损坏。轴承盖零件图如图1所示。 图1 轴承盖零件图 1.2轴承盖的技术要求 零件的材料为HT150,灰铸铁生产工艺简单,铸造性能优良,但塑性较差、脆性高,不适合磨削,零件的主要技术要求分析如下: (1).由零件图可知,零件的底座底面、内孔、端面及轴承座的顶面有粗糙度要求,其余的表面精度要求并不高,也就是说其余的表面不需要加工,只需按照铸造时的精度即可。底座底面的精度为Ra6.3、内孔、端面及内孔的精度要求均为Ra12.5。轴承座在工作时,静力平衡。 (2).铸件要求不能有砂眼、疏松等缺陷,以保证零件的强度、硬度及疲劳度,在静力的作用下,不至于发生意外事故。 表1 轴承盖零件技术要求表 加工表面尺寸及偏差 /mm 公差/mm 及精度等级 表面粗糙度 Ra/μm 形位公差/mm 一、零件结构工艺性分析: (一)零件的技术要求: 1.轴承盖零件,材料为HT200。 2.零件的技术要求表: (二)确定轴承盖的生产类型: 根据设计题目年产量为10万件,因此该轴承盖的生产类型为大批生产。 二、毛坯的选择: (一)选择毛坯: 由于该轴承盖在工作过程中要承受冲击载荷,为增强强度和 冲击韧度,获得纤维组织,毛坯选用铸件。该轴承盖的轮廓尺寸大,且生产类型属大批生产,为提高生产率和铸件精度,宜采用模铸方法制造毛坯,毛坯拔模斜度为5°。 (二)确定毛坯的尺寸公差: 1.公差等级: 由轴承盖的功能和技术要求,确定该零件的公差等级为普通级。 2.铸件件材质系数: 由于该轴承盖材料为HT200。 3.锻件分模线形状: 根据该轴承盖的形位特点,选择零件方向的对称平面为分模面,属于平直分模线。 4.零件表面粗糙度: 由零件图可知,该轴承盖的各加工表面粗糙度Ra均大于等于6.3μm。 三、定位基准的选择: (一)精基准的选择: 根据该零件的技术要求和装配要求,选择该轴承盖轴孔φ100f8和轴承盖右端面作为精基准,零件上的很多表面都可以采用它们作基准进行加工,即遵循了“基准统一”的原则。轴孔φ100f8的轴线是设计基准,选用其作精基准定位加工轴的外圆表面和轴承盖外圆表面,实现了设计基准和工艺基准的重合,保证了被加工表面的垂直度要求。选用轴承盖左端面作为精基准同样遵循了“基准重合”的原则,选用轴承盖左端面作为精基准,夹紧可作用在轴承盖的右端面上,夹紧稳定可靠。 (二)粗基准的选择: 作为粗基准的表面应平整,没有飞边、毛刺或其他表面缺欠,该轴承盖轴的外圆表面、右堵头外圆表面作为粗基准,以保证为后序准备好精基准。 5.7 轴承部件的结构设计 绝大多数中、小型减速器均采用滚动轴承,滚动轴承是标准件,设计时只需要选择轴承的类型和型号并进行轴承的组合设计即可。 滚动轴承部件的结构设计主要考虑轴承的支承结构型式、支承刚度、以及轴承的固定、调整、拆装、密封及润滑等。下面就轴承端盖结构、调整垫片、轴承的润滑与密封等方面作一介绍。 1 .轴承端盖 轴承端盖用以固定轴承、调整轴承间隙并承受轴向力。 轴承端盖的结构有嵌入式和凸缘式两种。每种又有闷盖和透盖之分。 嵌入式轴承端盖结构简单、紧凑,无需固定螺钉,外径小,重量轻,外伸轴尺寸短。但装拆端盖和调整轴承间隙困难,密封性能差,座孔上开槽,加工费时。嵌入式轴承端盖多用于重量轻、结构紧凑的场合,其结构和尺寸见表 5.1 。 凸缘式轴承端盖安装、拆卸、调整轴承间隙都比较方便,密封性能也好,所以应用广泛。但缺点是外廓尺寸大,又需一组螺钉来联接。其结构和尺寸见表 5.2 。 表 5.1 嵌入式轴承端盖的结构尺寸 表 5.2 凸缘式轴承端盖的结构和尺寸 当端盖与孔的配合处较长时,为了减少接触面,在端部铸出或车出一段较小的直径,但必须保留有足够的长度 e1,一般此处的配合长度为e1= ( 0.10~0.15 ) D , D 为轴承外径,图中端面凹进δ值,也是为 了减少加工面。如图 5.8 所示。 图 5.8 轴承端盖端部结构 图 5.9 穿通式轴承端盖 由于端盖多用铸铁铸造,所以要很好考虑铸造工艺。例如在设计穿通式轴承端盖图 5.9 时,由于装置密 封件需要较大的端盖厚度(图 5.9a ),这时应考虑铸造工艺,尽量使整个端盖厚度均匀,如图 5.9b )、 c )所示是较好的结构。 2 .轴伸出端的密封 轴伸出端的密封的作用是防止轴承处的润滑剂流出和箱外的污物、灰尘和水气进入轴承腔内,常见的密 封种类有接触式密封和非接触式密封两大类,接触式密封有毡圈密封、 O 形橡胶圈密封、唇形密封,非 接触式密封有沟槽密封和迷宫密封。 下面主要介绍毡圈密封和 O 形橡胶圈密封。 ( 1 )毡圈密封 将矩形毡圈压入梯形槽中使之产生对轴的压紧作用而实现密封,如图5.10 。它的结构简单,价格低廉, 滚动轴承型号含义 现在网络上一般所写的轴承型号含义的文章都为介绍的滚动轴承型号含义的文章,滚动轴承型号含义一般有3部分组合:基本代号、前置代号和后置代号,关于这部分内容航五瑞在以前的文章中写过一篇“”,可以参考,这篇文章主要介绍了滚动轴承的基本代号构成,类型代号、尺寸系列代号和内径代号。在这里补充一下常见的滚动轴承前置代号和后置代号含义: 常见轴承前置代号含义 ?L:可分离轴承的可分离内圈或外圈 ?R:不带可分离内圈或外圈的轴承(滚针轴承仅适用于NA型) ?K:滚子和保持架组件 ?WS:推力圆柱滚子轴承轴圈 ?GS:推力圆柱滚子轴承座圈 ?F:凸缘外圈的向心球轴承(仅适用于内径小于等于10mm) ?KOW-:无轴圈推力轴承 ?KIW-:无座圈推力轴承 ?LR:带可分离的内圈或外圈与滚动体组件轴承 轴承后置代号含义 轴承的后置代号一般表示轴承的内部结构、密封、外部形状变化、保持架结构、轴承材料改变、公差等级、游隙代号、配置等内容,下面分别介绍。轴承内部结构代号含义 轴承保持架代号含义,包括了保持架材料、结构等内容。 1,轴承保持架材料 ?F:钢、球墨铸铁或粉末冶金实体保持架,用附加数字表示不同的材料。 ?F1:碳钢; ?F2:石墨钢; ?F3:球墨铸钢; ?F4:粉末冶金。 ?Q:青铜实体保持架,用附加数字表示不同的材料。 ?Q1:铝铁锰青铜; ?Q2:硅铁锌青铜; ?Q3:硅镍青铜; ?Q4:铝青铜。 ?M:黄铜实体保持架。 ?L:轻合金实体保持架,用附加数字表示不同的材料。 ?L1:LY11CZ ?L2:LY12CZ ?T:酚醛层压布管实体保持架。 ?TH:玻璃纤维增强酚醛树脂保持架(筐型)。 · 机械制造工艺学 课程设计说明书 设计题目:设计端盖的机械加工工艺规程 — ( 设计者: 郑四成 学号: 33 指导教师: 郭强 : ; 齐齐哈尔大学机电工程学院机电系 机电091班 2012年12月02日 ' 机械制造工艺学课程设计任务书 适用专业:机械电子工程 设计题目:设计端盖的机械加工工艺规程 一、设计前提:中批生产 二、设计内容: 1.零件图一张 、 2.课程设计说明书一份 3.机械加工工艺规程一套 三、课程设计工作计划 周一:绘制零件图 周二:撰写课程设计说明书草稿 周三:修订并完成科技设计说明书 周五:答辩 三、相关教材及参考书目: ¥ 1.<<机械制造工艺学>>,王启平主编,哈尔滨工业大学出版社 2.<<机械制造工艺学课程设计手册>>,<<机械制造工艺学设计手册>>,<<机械加工工艺手册>>,<<机械加工工艺人员手册>>等 — ! 年月日 : 目录 1端盖的零件图 (5) 2 零件的分析 (6) 零件的作用 (6) 零件的工艺分析 (6) 3 拟定机械加工工艺路线 (7) ( 4端盖的零件机械加工工艺卡片 (8) 5 课程设计说明书 (12) 选择毛坯 (13) 毛坯材料的分析 (13) 毛坯的结构简图 (13) 端盖的技术要求 (13) 该端盖的各项技术要求 (13) 审查端盖的工艺性 (14) ~ 定位基准的选择 (14) 粗基准的选择 (14) 精基准的选择 (14) 工序顺序的安排 (15) 机械加工工序 (15) 热处理工序 (15) 辅助工序 (15) 确定加工的设备、刀具、和夹具 (15) ] 6、设计总结 (16) 参考文献......................................................... .. (17) ? , 轴承部件的结构设计 绝大多数中、小型减速器均采用滚动轴承,滚动轴承是标准件,设计时只需要选择轴承的类型和型号并进行轴承的组合设计即可。 滚动轴承部件的结构设计主要考虑轴承的支承结构型式、支承刚度、以及轴承的固定、调整、拆装、密封及润滑等。下面就轴承端盖结构、调整垫片、轴承的润滑与密封等方面作一介绍。 1 .轴承端盖 轴承端盖用以固定轴承、调整轴承间隙并承受轴向力。 轴承端盖的结构有嵌入式和凸缘式两种。每种又有闷盖和透盖之分。 嵌入式轴承端盖结构简单、紧凑,无需固定螺钉,外径小,重量轻,外伸轴尺寸短。但装拆端盖和调整轴承间隙困难,密封性能差,座孔上开槽,加工费时。嵌入式轴承端盖多用于重量轻、结构紧凑的场合,其结构和尺寸见表 5.1 。 凸缘式轴承端盖安装、拆卸、调整轴承间隙都比较方便,密封性能也好,所以应用广泛。但缺点是外廓尺寸大,又需一组螺钉来联接。其结构和尺寸见表 5.2 。 表 5.1 嵌入式轴承端盖的结构尺寸 e 2 =5~10mm s=10~15mm m 由结构确定 D 3 =D+e 2 , 装有 o 型圈的,按 o 型圈外径取整 d1、 b1等由密封尺寸确定 表 5.2 凸缘式轴承端盖的结构和尺寸 do =d3 +1mm , d3—端盖联接螺栓直径,尺寸见右表。D1=D+2.5d3 D2 =D1 +2.5d3 e=1.2d3 e 1 ≥ e m 由结构确定 D4 =D- ( 10~15 ) mm b1、d1由密封尺寸确定 b=5~10mm h=(0.8~1)b 轴承外径 D 螺栓直径 d 3 端盖上螺栓数 目 45~65 70~100 110~140 150~230 6 8 10 12~16 4 4 6 6 当端盖与孔的配合处较长时,为了减少接触面,在端部铸出或车出一段较小的直径,但必须保留有足够的长度 e1,一般此处的配合长度为e1= ( 0.10~0.15 ) D , D 为轴承外径,图中端面凹进δ值,也是为了减少加工面。如图 5.8 所示。 轴承端盖设计 5.7 轴承部件的结构设计 绝大多数中、小型减速器均采用滚动轴承,滚动轴承是标准件,设计时只需要选择轴承的类型和型号并进行轴承的组合设计即可。 滚动轴承部件的结构设计主要考虑轴承的支承结构型式、支承刚度、以及轴承的固定、调整、拆装、密封及润滑等。下面就轴承端盖结构、调整垫片、轴承的润滑与密封等方面作一介绍。 1 .轴承端盖 轴承端盖用以固定轴承、调整轴承间隙并承受轴向力。 轴承端盖的结构有嵌入式和凸缘式两种。每种又有闷盖和透盖之分。 嵌入式轴承端盖结构简单、紧凑,无需固定螺钉,外径小,重量轻,外伸轴尺寸短。但装拆端盖和调整轴承间隙困难,密封性能差,座孔上开槽,加工费时。嵌入式轴承端盖多用于重量轻、结构紧凑的场合,其结构和尺寸见表 5.1 。 凸缘式轴承端盖安装、拆卸、调整轴承间隙都比较方便,密封性能也好,所以应用广泛。但缺点是外廓尺寸大,又需一组螺钉来联接。其结构和尺寸见表 5.2 。 表 5.1 嵌入式轴承端盖的结构尺寸 表 5.2 凸缘式轴承端盖的结构和尺寸 当端盖与孔的配合处较长时,为了减少接触面,在端部铸出或车出一段较小的直径,但必须保留有足够的长度 e1,一般此处的配合长度为e1= ( 0.10~0.15 ) D , D 为轴承外径,图中端面凹进δ值,也是为了减少加工面。如图 5.8 所示。 图 5.8 轴承端盖端部结构 图 5.9 穿通式轴承端盖 由于端盖多用铸铁铸造,所以要很好考虑铸造工艺。例如在设计穿通式轴承端盖图 5.9 时,由于装置密封件需要较大的端盖厚度(图 5.9a ),这时应考虑铸造工艺,尽量使整个端盖厚度均匀,如图 5.9b )、c )所示是较好的结构。 2 .轴伸出端的密封 轴伸出端的密封的作用是防止轴承处的润滑剂流出和箱外的污物、灰尘和水气进入轴承腔内,常见的密封种类有接触式密封和非接触式密封两大类,接触式密封有毡圈密封、 O 形橡胶圈密封、唇形密封,非接触式密封有沟槽密封和迷宫密封。 下面主要介绍毡圈密封和 O 形橡胶圈密封。 专业课程设计(零件工艺设计某些) 姓名: 学号: 班级: 指引教师: 3月2日 一、零件工艺分析 1、端盖用途 端盖是应用广泛机械零件之一,是轴承座重要外部零件。 端盖普通作用是:轴承外圈轴向定位;轴承工作过程防尘和密封(除自身可以防尘和密封外,也常和密封件配合以达到密封作用);位于车床电动机和主轴箱之间端盖,重要起传递扭矩和缓冲吸震作用,使主轴箱转动平稳。因而该零件应具备足够强度、刚度、耐磨性和韧性,以适应其工作条件。该零件重要工作表面为左右端面以及左端面外圆表面,在设计工艺规程时必要重点考虑。端盖加工工艺可行性与合理性直接影响零件质量、生产成本、使用性能和寿命等。 2、端盖工艺性分析 该端盖重要由平面、外圆面以及孔系构成,其构造简朴、形状普通,属于普通盘盖类零件。端盖重要加工表面有左、右和凸台等三个端面,Φ47和Φ80两个外圆面,Φ34和Φ16两个内圆面,密封圈内槽以及六个均布Φ7通孔。规定其Φ7孔右端加工平面对于基准A垂直度公差是0.03mm,端盖Φ47外圆面与基准A同轴度误差为0.03mm,另一方面就是均布φ7孔加工端面规定为平面,可以防止加工过程中钻头偏斜以保证孔加工精度。 其中,端面和内外圆面均规定车削加工,可以采用半精车和粗车,并且粗、精加工应分开进行,以保证表面粗糙度规定;φ7通孔加工采用钻铰来达到精度规定。别的非配合表面加工精度较低,不需要高精度机床加工,通过粗车和半精车就可以在正常生产条件下,采用较经济办法加工出来;此外,该零件材料为铸铁HT200,切削加工性能较好。 综上所述,该端盖零件工艺性能良好。 (1)工件时效解决 对于毛坯为铸件盖类零件,因其各部位厚度不均匀,存在较大锻造内应力, 轴承箱 安装使用说明书 中国·河北 河北同心风机配件有限公司 目录 一、用途 (1) 二、结构形式 (1) 三、产品安装 (2) 四、风机的安装调试和操作 (5) 五、风机的维护与保养 (6) 六、风机运转中的故障及消除 (6) 一、用途 轴承箱体广泛应用在通风机及其他机械产品的传递功率之用,对于风机而言介质不超过80℃时应采用油冷式,超过此温度应采用水冷方式,高温风机应采用高温轴承箱。 二、结构形式 轴承箱体按结构形式一般分为二大类;一类分为整体式(简称为箱体),另一类分为分体式(简称为瓦盒)。按风机的传动方式通常可分为D(双通)、F(一通一闷)二种。按润滑方式也可分为脂润滑(黄油)和油润滑(稀油)两种方式,根据使用风机的转速和机号大小而选用。 1、整体式(箱体) 通常有轴承盖、轴承座、侧盖和压盖组成,按风机介质不同可分为水冷和油冷两类。 其中实物箱体上标识“G”为固定端箱体,“F”为非固定端箱体。 2、分体式(瓦盒) 通常有轴承盖、轴承座、侧盖和压盖组成,按风机介质不同可分为水冷和油冷两类。 放油孔放水孔 本图为水冷式 三、产品安装: 1、安装前,先检查轴承箱外观有无碰裂等问题,如有碰裂不再安装;无碰裂的轴承箱方 可拆卸下两端侧盖,进行尺寸检验;检测轴承孔尺寸合格的,方可进行安装。 2、拆掉合箱螺栓,把轴承座上盖卸去,用干净的棉纱把轴承座上盖与底座的轴承位擦净,上盖、底座的结合面擦净,不得有污物。 3、把预装好的轴承与轴的组合件安放在轴承座上,固定端轴承顶紧。打胶:在轴承座的合箱面上,在螺栓孔的内部,均匀涂敷一层宽5~7mm的机械耐油密封胶,两端必须打到边,晾10分 钟,扣好上盖,安装紧固合箱螺栓。打胶参见照片。 ?? 绝大多数中、小型减速器均采用滚动轴承,滚动轴承是标准件,设计时只需要选择轴承的类型和型号并进行轴承的组合设计即可。 ????滚动轴承部件的结构设计主要考虑轴承的支承结构型式、支承刚度、以及轴承的固定、调整、拆装、密封及润滑等。下面就轴承端盖结构、调整垫片、轴承的润滑与密封等方面作一介绍。 1 .轴承端盖 ??? 轴承端盖用以固定轴承、调整轴承间隙并承受轴向力。 ???轴承端盖的结构有嵌入式和凸缘式两种。每种又有闷盖和透盖之分。 ?? 嵌入式轴承端盖结构简单、紧凑,无需固定螺钉,外径小,重量轻,外伸轴尺寸短。但装拆端盖和调整轴承间隙困难,密封性能差,座孔上开槽,加工费时。嵌入式轴承端盖多用于重量轻、结构紧凑的场合,其结构和尺寸见表 5.1 。 ? 凸缘式轴承端盖安装、拆卸、调整轴承间隙都比较方便,密封性能也好,所以应用广泛。但缺点是外廓尺寸大,又需一组螺钉来联接。其结构和尺寸见表 5.2 。 表 5.1 嵌入式轴承端盖的结构尺寸 表 5.2 凸缘式轴承端盖的结构和尺寸 D2 =D1 +2.5d3 e=1.2d3 e 1 ≥ e m 由结构确定 D4 =D- ( 10~15 ) mm b1、d1由密封尺寸确定b=5~10mm h=(0.8~1)b 70~100 110~140 150~230 8 10 12~16 4 6 6 ????当端盖与孔的配合处较长时,为了减少接触面,在端部铸出或车出一段较小的直径,但必须保留有足够的长度 e1,一般此处的配合长度为e1= ( 0.10~0.15 ) D , D 为轴承外径,图中端面凹进δ值,也是为了减少加工面。如图 5.8 所示。 图 5.8 轴承端盖端部结构 湖南科技大学 课程设计 课程设计名称:端盖铸造工艺设计 学生姓名: 学院: 专业及班级: 学号: 指导教师: 2015 年 7 月 7 日 铸造工艺课程设计任务书 一、任务与要求 1.完成产品零件图、铸件铸造工艺图各一张,铸造工艺图需要三维建模(完成3D图)。 2.完成芯盒装配图一张。 3.完成铸型装配图一张。 4. 编写设计说明书一份(15~20页),并将任务书及任务图放置首页。 二、设计内容为2周 1. 绘制产品零件图、铸造工艺图及工艺图的3D图(2天)。 2. 铸造工艺方案设计:确定浇注位置及分型面,确定加工余量、起模斜度、铸造圆角、收缩率,确定型芯、芯头间隙尺寸。(1天)。 3. 绘制芯盒装配图(1天)。 4. 绘制铸型装配图、即合箱图(包括流道计算共2天)。 5. 编制设计说明书(4天)。 三、主要参考资料 1. 张亮峰主编,材料成形技术基础[M],高等教育出版社,2011. 2. 丁根宝主编,?铸造工艺学上册 [M] ,机械工业出版社,1985. 3. 铸造手册编委会,铸造手册:第五卷[M] ,机械工业出版社,1996. 4. 沈其文主编, 材料成形工艺基础(第三版)[M],华中科技大学出版社,2003. 摘要 本设计是端盖的铸造工艺设计。端盖的材料为QT400-15,结构简单,无复杂的型腔。根据端盖的零件图进行铸造工艺性分析,选择分型面,确定浇注位置、造型、造芯方法、铸造工艺参数并进行浇注系统、冒口和型芯的设计。在确定铸造工艺的基础上,设计模样、芯盒和砂箱,并利用CAD、Pro/E等设计软件绘制端盖零件图、芯盒装配图。 关键词:铸造;端盖;型芯 机电及自动化学院 《机械制造工艺学》课程设计说明书设计题目:主轴承盖工艺规程设计 2011 年7月 前言 机械制造工艺学课程设计是在学完了机械制造工艺学(含机床夹具设计)和大部分专业课,并进行了实习的基础上进行的一个教学环节。这次设计使我们能综合运用机械制造工艺学中的基本理论,并结合生产实习中学到的实践知识,独立的分析和解决工艺问题,初步具备了设计一个中等复杂程度零件(主轴承盖)的工艺过程的能力和运用夹具设计的基本原理和方法,拟定加工工艺方案,完成零件机械加工工艺过程设计的能力,也是熟悉和运用有关手册、图表等技术及编写技术文件等技能的一次实践机会,形成规范解决问题的理念,为今后的毕业设 计及未来从事的工作打下良好的基础。 设计是一项复杂细致的工作,在设计过程中常遇到一些困难和问题,但通过指导老师的指点加上自己努力都一一解决,积累了一些经验和教训,也发挥了自己的主观能动性,由于能力有限,经验不足和错误之处请老师多加指导。 目录 任务介绍 (4) 主轴承盖工艺分析 (4) 主轴承盖工艺规程设计 (5) 3.1、确定主轴承盖毛坯的形式 (5) 3.2、基准选择 (5) 3.3制订工艺路线 (5) 3.4、加工余量、工序尺寸和毛坯尺寸的确定 (8) 3.5、各种机床与道具选择 (10) 3.6、确定切削用量和基本工时 (10) 3.7、计算时间定额和提高生产率的工艺途径简介 (15) 3.8、工艺方案的比较与技术经济分析 (16) 4、小结 (16) 5、参考文献 (17) 6、附件 (17) 1、任务介绍 本次《机械制造工艺学》课程设计,我的题目是“主轴承盖工艺规程设计”。材料为HT200,生产批量为中批量生产,其他要求要求及零件参数见主轴承盖零件图,要求设计该主轴承盖的机械加工工艺规程,具体要求内容为:(1)、根据生产类型,对零件进行工艺分析; (2)、选择毛坯种类及制造方法,绘制毛坯图; (3)、制订零件的机械加工工艺过程,选择工序加工设备及工艺装备,确定各工序切削用量及工序尺寸,并计算工序的工时定额; (7)、填写工艺文件; (8)、撰写设计说明书。 专业课程设计(零件工艺设计部分) 姓名: 学号: 班级: 指导教师: 2013年3月2日 一、零件的工艺分析 1、端盖的用途 端盖是应用广泛的机械零件之一,是轴承座的主要外部零件。 端盖的一般作用是:轴承外圈的轴向定位;轴承工作过程的防尘和密封(除本身可以防尘和密封外,也常和密封件配合以达到密封的作用);位于车床电动机和主轴箱之间的端盖,主要起传递扭矩和缓冲吸震的作用,使主轴箱的转动平稳。因此该零件应具有足够的强度、刚度、耐磨性和韧性,以适应其的工作条件。该零件的主要工作表面为左右端面以及左端面的外圆表面,在设计工艺规程时必须重点考虑。端盖加工工艺的可行性与合理性直接影响零件的质量、生产成本、使用性能和寿命等。 2、端盖工艺性分析 该端盖主要由平面、外圆面以及孔系组成,其结构简单、形状普通,属于一般的盘盖类零件。端盖主要加工表面有左、右和凸台等三个端面,Φ47和Φ80两个外圆面,Φ34和Φ16两个内圆面,密封圈内槽以及六个均布的Φ7的通孔。要求其Φ7孔的右端加工平面对于基准A的垂直度公差是0.03mm,端盖的Φ47外圆面与基准A的同轴度误差为0.03mm,其次就是均布的φ7孔的加工端面要求为平面,可以防止加工过程中钻头偏斜以保证孔的加工精度。 其中,端面和内外圆面均要求车削加工,可以采用半精车和粗车,并且粗、精加工应分开进行,以保证表面粗糙度要求;φ7通孔的加工采用钻铰来达到精度要求。其余非配合表面加工精度较低,不需要高精度机床加工,通过粗车和半精车就可以在正常的生产条件下,采用较经济的方法加工出来;此外,该零件材料为铸铁HT200,切削加工性能较好。 综上所述,该端盖零件的工艺性能良好。 (1)工件的时效处理 对于毛坯为铸件的盖类零件,因其各部位厚度不均匀,存在较大的铸造内应力,容易造成变形等缺陷,因此必须安排人工时效处理。对于本端盖,其精度要求一般,则可利用粗、精加工工序间的自然停放和运输时间,得到自然时效处理的效果。其自然时效处理的时间越长越好,否则会影响端盖配合精度的稳定性。 对于特别精密的端盖,在粗加工和精加工工序间还应安排一次人工时效,以消除铸造内应力,提高精度稳定性。 (2)加工工艺的顺序应先面后孔 作为端盖上主要的两类加工表面——平面和孔,从定位稳定可靠的角度上分析,平面比孔要优越得多,同时还可以使孔的加工余量均匀;从加工难度上分析,平面比孔容易加工;从有利加工的进行上分析,采用先加工平面后加工分布在平面上的孔,由于铸件表面的凹凸不平和夹砂等缺陷已被切除,大大有利于孔加工的进行。 第一章绪论 1.1 课题的研究背景和意义 钻床是具有广泛用途的通用性机床,可对零件进行钻孔、扩孔、铰孔、锪平面和攻螺纹等加工。在钻床上配有工艺装备时,还可以进行镗孔,在钻床上配万能工作台还能进行钻孔、扩孔、铰孔。如图1所示为钻床的实物图。 图1 钻床实物图 钻床主要用钻头在工件上加工孔(如钻孔、扩孔、铰孔、攻丝、锪孔等)的机大型钻床车间床。机械制造和各种修配工厂必不可少的设备。根据用途和结构主要分为以下几类: 1、立式。工作台和主轴箱可以在立柱上垂直移动,用于加工中小型工件。 2、台式。简称台钻。一种小型立式钻床,最大钻孔直径为12~15毫米,安装在钳工台上使用,多为手动进钻,常用来加工小型工件的小孔等。 3、摇臂式。主轴箱能在摇臂上移动,摇臂能回转和升降,工件固定不动,适用于加工大而重和多孔的工件,广泛应用于机械制造中。 4、深孔钻床。用深孔钻钻削深度比直径大得多的孔(如枪管、炮筒和机床主轴等零件的深孔)的专门化机床,为便于除切屑及避免机床过于高大,一般为卧式布局,常备有冷却液立式钻床输送装置(由刀具内部输入冷却液至切削部位)及周期退刀排屑装置等。如图3所示。 图3 深孔钻床 5、中心孔钻床。用于加工轴类零件两端的中心孔。 6、铣钻床。工作台可纵横向移动,钻轴垂直布置,能进行铣削的钻床。 7、卧式钻床。主轴水平布置,主轴箱可垂直移动的钻床。一般比立式钻床加工效率高,可多面同时加工。 轴承端盖用以固定轴承、调整轴承间隙并承受轴向力。轴承端盖的结构有嵌入式和凸缘式两种。每种又有闷盖和透盖之分。嵌入式轴承端盖结构简单、紧凑,无需固定螺钉,外径小,重量轻,外伸轴尺寸短。但装拆端盖和调整轴承间隙困难,密封性能差,座孔上开槽,加工费时。嵌入式轴承端盖多用于重量轻、结构紧凑的场合,其结构和尺寸见表1。凸缘式轴承端盖安装、拆卸、调整轴承间隙都比较方便,密封性能也好,所以应用广泛。但缺点是外廓尺寸大,又需一组螺钉来联接。其结构和尺寸见表2 。 表1 嵌入式轴承端盖的结构尺寸 e 2 =5~10mm s=10~15mm m由结构确定 D 3 =D+e 2 , 装有o型 圈的,按o型圈外径取 整d1、b1等由密封尺寸 确定 一、毕业设计题目轴承座端盖零件工艺规程及专用夹具设计 三、毕业设计内容要求: 零件图纸: 如图所示某轴承座端盖零件,年产量为10000件,设其备品率为7%,机械加工废品率为3%,试制定该零件的机械加工工艺过程并自行选定一工序进行专用夹具设计。 (看不清请自行将显示比例放大到200%以上) 1、计算生产纲领,确定生产类型 根据题目中给定的零件的年产量计算生产纲领,确定生产类型。 2、零件的分析 (1)熟悉零件图,了解零件的用途及工作条件。 (2)分析零件图上各项技术要求,确定主要加工表面。 (3)加工表面的尺寸精度和形状精度。 (4)主要加工表面间的相互位置精度。 (5)加工表面粗糙度及其它方面的表面质量要求。 (6)热处理要求及其它要求。 3、选择毛坯 (1)根据零件用途确定毛坯类型。 (2)根据生产批量确定毛坯制造方法。 (3)根据手册确定表面加工余量及余量公差。 4、工艺规程设计 (1)定位基准的选择(包括粗、精基准的选择) (2)零件表面加工方法的选择 (3)制定工艺路线 (4)确定机械加工余量及毛坯尺寸,设计毛坯——零件综合图 (5)工序设计 ①选择加工设备与工艺装备 a.选择机床 b.选择夹具 c.选择刀具 d.选择量具 ②工序尺寸的确定及计算 (6)选择切削用量、确定时间定额 (7)填写机械加工工艺规程卡片和机械加工工序卡片。 5、机床夹具设计 (1)拟定夹具的结构方案 ①确定夹具的类型 ②确定工件的定位方案 ③确定工件的夹紧形式 ④确定刀具的导向方式或对刀装置 ⑤确定其它机械,如分度、装卸用的辅助装置等。 ⑥夹具定位夹紧方案分析与论证(含夹紧力的计算)。 ⑦夹具体的结构类型的设计 (2)夹具总图设计 (3)夹紧力的计算及夹具精度的校核 (4)绘制夹具零件图样 6、编写说明书 说明书内容如下: (1)目录 (2)设计任务书。 (3)总论或前言 (4)对零件的工艺性分析(零件的作用结构特点、结构工艺性、关键表面的技术要求分析等)。 (5)工艺设计 H a r b i n I n s t i t u t e o f T e c h n o l o g y 设计说明书 设计课题:滚动轴承,轴系的组合结构设计 课程名称:机械学基础 姓名:潘瑞 学号: 班级:0936104 院系:英才学院自动化 设计要求: 一钢制圆轴,装有两胶带轮A和B,两轮有相同的直径D=360mm,重量为P=1kN,A轮上胶带的张力是水平方向的,B轮胶带的张力是垂直方向的,它们的大小如下图所示。设圆轴的许用应力[σ]=80MPa,轴的转速n=960r/min,带轮宽b=60mm,寿命为50000小时。 1). 按强度条件求轴所需的最小直径 2). 选择轴承型号(按受力条件及寿命要求) 3). 按双支点单向固定的方法,设计轴承与轴的组合装配结构,画出装配图(3号图纸) 4). 从装配图中拆出轴,并画出轴的零件图(3号图纸) 设计步骤: 一、根据强度条件计算轴所需的最小直径 1、先计算C、D支点处的受力 从而可得D点所受轴向力 从而可得D点所受轴向力 2、计算弯矩,求得最小直径 水平方向上: 0120 x ≤≤时 1 0 A M F x -?= 12.5 M x = 120300x <≤时 2(120)0A Cy M F x F x -?+?-= 25 5003 M x =-+ 竖直方向上: 0120x ≤≤时 10A M P x +?= 1M x =- 120210x <≤时 2(120)A Cy M P x F x +?-?- 229 41012 M x = - 210300x <≤时 3(120)()(120)0A Cy B B M P x F x F P x +?-?-++?-= 由弯矩图判断可得:C 点为危险点,故可得: 解得 223 32 323.1127037.7[] d mm π≥ +=?σ 所以,最小直径为37.7mm 。 二、轴材料的确定 根据已知条件的[σ]=80MPa ,为对称循环应力状态下的许用弯曲力,确定材料为合金钢。以上最小直径是按弯曲扭转组合强度计算而得来的,即在[σ]=80MPa 的合金钢情况下,37.3d mm ≥,强度足以达到要求。 三、受力条件及寿命要求选择轴承型号 由前面的受力分析可知:所要设计的轴仅受径向作用力,故优先考虑选择深沟球轴承。 分析:若选择深沟球轴承,0a F =, 0e =, 1X =, 0Y =,15388.4r F N =,21987.8r F N =, 1.4d f =, 所以: 根据题意 经查GB/T 276-1994,选择6412型深沟球轴承,60d mm =,109r C kN =。 带入验证: 所以,1010[]50000h h L L ≥=,符合要求,故选择6412。以下为深沟球轴承6412的相关参数如下表所示: 基本尺寸/mm|d: 60 其他尺寸/mm|r (min) 2.1 基本尺寸/mm|D: 150 基本额定载荷/kN|Cr: 109 轴承透盖工艺设计 一.确定轴承透盖的设计类型 此轴承盖有一个Φ55的台阶面,若大量生产宜采用模锻的毛坯类型来节约原材料。若单件小批量生产宜采用型钢进行下料的毛坯类型,此设计确定采用圆钢进行下料。 二.轴承闷盖加工工艺分析 1,对直径为Φ80mm,表面粗糙度Ra值为6.3μm,长为5mm的外圆表面,查[1]表3.4可知,半精车可达到其要求,所以确定该外圆表面的加工工序为半精车; 该圆上、下端面(其表面粗糙度Ra值为3.2μm) 查[1]表3.4可知,半精车可达到其要求,所以确定该圆上、下端面的加工工序就为:粗车---半精车 2,对直径为错误!未找到引用源。错误!未指定书签。mm,表面粗糙度Ra值为 1.6μm,长度为7mm的外圆表面,查表3.4可知,精车可达到其要求,所以确定该外圆的加工工序为粗车--半精车--精车; 该圆右端面(其表面粗糙度Ra值为3.2μm): 查表3.4可知,半精车可达到其要求,所以确定该圆右端面的加工工序为:粗车--半精车 3,对Φ49mm,表面粗糙度Ra值为6.3μm的端面,查表3.4可知,半精车车可达到其要求,所以确定该圆端面的加工工序为粗车--半精车;对Φ26mm的孔,表面粗糙度为3.2,查表3.4可知,粗车-半精车可达到其要求. 4,4×Φ7通孔的位置度,尺寸精度可表面粗糙度均未注公差 单件生产可钳工画线钻孔,批量可采用钻模钻孔,此实训确定采用钳工画线钻孔;三.确定轴承悶盖的加工工艺路线 根据上述轴承盖的加工工艺分析可知:该轴承盖的加工工序较为简单,可确定为下料—车--画线--钻孔 四.填写轴承盖的加工工艺过程卡 五.填写轴承盖加工工序的工序卡 机械制造技术基础 课程设计 题目:轴承盖的机械加工工艺说明书 班级: 姓名: 指导教师: 完成日期:2011/3/11 一、设计题目LX-31轴承盖的机械加工工艺规程及工艺装备设计 二、原始资料 (1) 被加工零件的零件图1张 (2) 生产类型:(中批或大批大量生产) 三、上交材料 1.绘制零件图1张2.毛坯图1张3.编制机械加工工艺过程综合卡片1套4.编制机械加工工艺卡片(仅编制所设计夹具对应的那道工序的机械加工工艺卡片)1套5.绘制夹具装配图(A0或A1)1张6.绘制夹具中1个零件图(A1或A2。装配图出来后,由指导教师为学生指定需绘制的零件图,一般为夹具体)。1张7.编写课程设计说明书(约5000-8000字)。1份四、进度安排 本课程设计要求在3周内完成。 1.第l~2天查资料,熟悉题目阶段。 2.第3~7天,完成零件的工艺性分析,确定毛坯的类型、制造方法和机械加工工艺规程的设计并编制出零件的机械加工工艺卡片。 3.第8~10天,完成夹具总体方案设计(画出草图,与指导教师沟通,在其同意的前提下,进行课程设计的下一步)。 4.第11~13天,完成夹具总装图的绘制。 5.第14~15天,零件图的绘制。 6.第16~18天,整理并完成设计说明书的编写。 7.第19天,完成图纸和说明书的输出打印。 8.第20~21天,答辩 五、指导教师评语 成绩: 指导教师 日期 摘要 机械制造技术基础课程设计,是以切削理论为基础,制 造工艺为主线,兼顾工艺装备知识的机械制造技术基本涉机能力培养的实践课程;是综合运用机械制造技术的基本知识,基本理论和基本技能,分析和解决实际工程问题的一个重要教学环节;是对学生运用掌握的“机械制造”技术基础 知识及相关知识的一次全面的应用训练。 机械制造技术基础课程设计,是已机械制造工艺装备为内容进行的设计。即以给定的一个中等复杂的程度的中小型机械零件为对象,在确定其毛胚制造工艺的基础上,编制其机械加工工艺规程,并对其一工序进行机床专用卡具设计。由于能力有限,设计尚有许多不足之处,恳请各位老师给予批评指正。 Abstract轴承端盖工艺设计.
轴承盖钻孔夹具课程设计说明书
轴承端盖冲压模具设计说明书
轴承盖课程设计说明书
机械设计 轴承端盖说明书
轴承端盖设计精编版
轴承型号含义说明
机械制造工艺学课程设计-端盖
轴承盖文档 (3)
轴承端盖设计教学内容
轴承端盖零件工艺部分课程设计样本
轴承箱使用说明书
轴承端盖设计
端盖铸造工艺设计
主轴承盖课程设计说明书
轴承端盖零件工艺部分课程设计
加工轴承端盖4-Φ12孔——工艺装备钻床设计
轴承座端盖零件工艺规程及专用夹具设计任务书
滚动轴承轴系的组合结构设计
轴承透盖工艺设计
轴承盖的机械加工工艺规程及工艺装备设计说明书