拜耳法氧化铝生产工艺流程框图

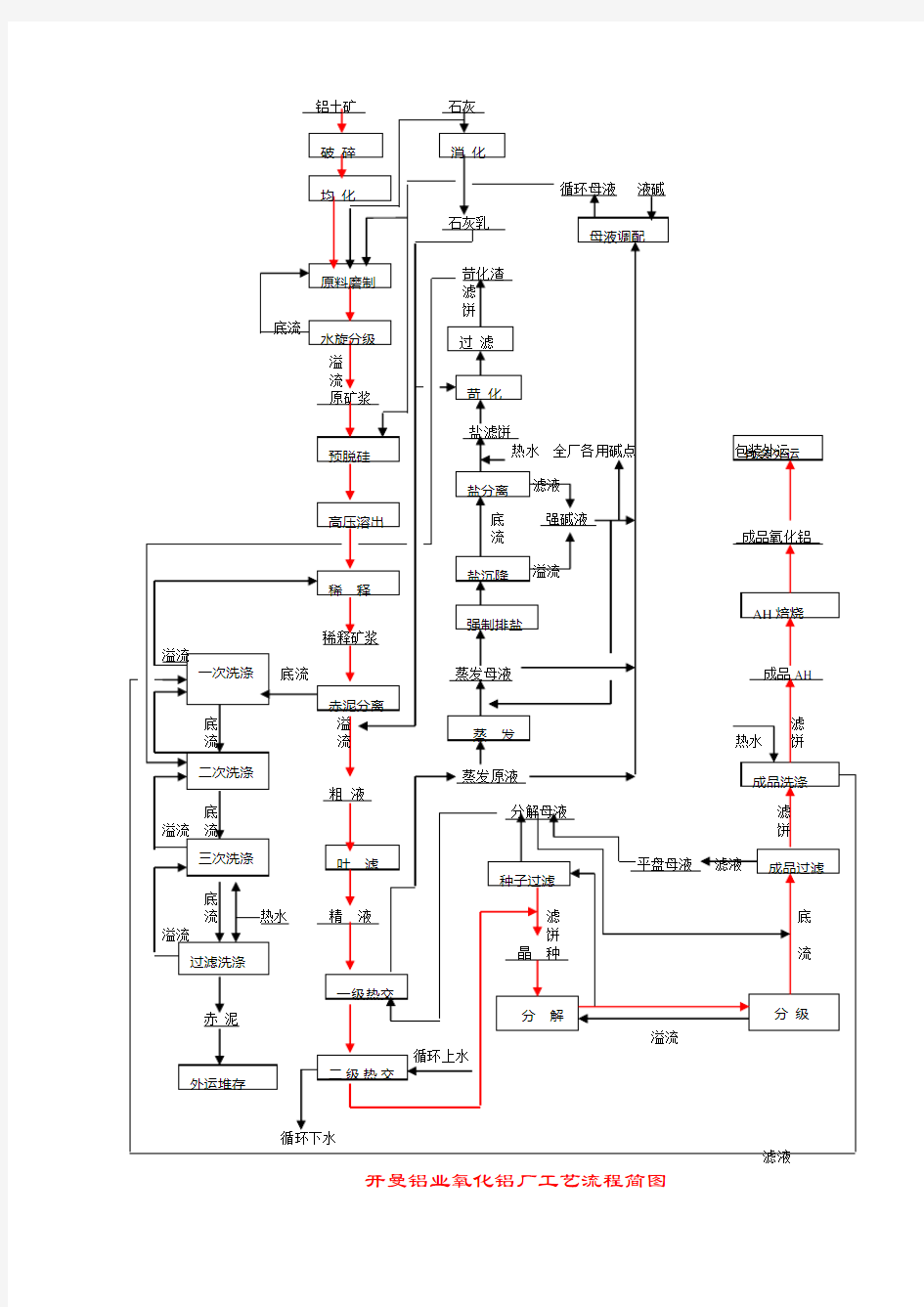
拜耳法氧化铝生产工艺流程框图
成品氧化铝
图一
焙烧
2O 3
图二 碱法生产氧化铝基本过程
开曼铝业氧化铝厂工艺流程简图
氧化铝厂主要生产车间
一车间:原料准备
包括:地磅房、破碎站、原矿堆场、均化库、石灰仓、石灰消化及原料磨等工段
a.石灰消化:3台ф1200x10500m化灰机,2用1备
b.石灰仓:3台ф14x18m
c.拜尔原料磨(棒球两段磨加水力漩流器):4组,每组配一级棒磨
ф3.2x4.5m及二级球磨ф3.6x8.5m,产能100t/h,用3备1。
二车间:高压溶出
包括:常压脱硅、高压泵房、管道化预热、溶出及稀释
a.常压脱硅:3台带加热管束搅拌的ф10x16m预脱硅加热槽及11台
机械搅拌的ф10x16m脱硅槽,1台ф6x6m赤泥洗液槽。其中预脱硅加热槽2用1备,脱硅槽10用1备。
b.高压泵房:36~6.8MPa,流量
400-500m3用1备。
c.溶出装置:2组。采用法铝技术,6级套管预热,4级压煮器预热,
新蒸汽间接加热,保温压煮器停留30分钟,10级闪蒸降温。每组配套预热管预热器长度2880m,19台ф2.8x16.8m压煮器,12台ф3.0-5.0x9.7m闪蒸器。2台ф12.5x13.5m溶出后槽,稀释料浆停留4.2小时,产能400-500kt/a.
三车间:赤泥沉降
包括:赤泥分离及洗涤、絮凝剂制备、控制过滤、赤泥贮槽及赤泥泵站、赤泥堆场、热水站
a.赤泥分离及洗涤:2组。采用高效深锥沉降槽技术及设备。每组配
6台ф14x16-18m高效沉降槽,其中分离槽1台,洗涤槽4台,备用槽1台。
b.控制过滤:7台226m2立式叶滤机,其中用6台备1台。
c.赤泥泵站:3台引进的高压隔膜泵,2用1备。
d.絮凝剂制备、热水站。
四车间:分解分级
包括:精液热交换、分解分级、中间降温、种子过滤
a.精液热交换(板式换热器):4组。每组为两级换热,第一级精液
与母液换热,配3台450m3 换热器,第二级精液与水换热,配1台230 m3 换热器。每两组换热器对应1组分解槽,用1组备1组。
b.种子过滤:8台120 m2立式过滤机,用5台备3台。
c.分解分级:2组。每组14台ф14x29.5-34.5m,4600 m3/台平底
机械搅拌分解槽,用13台备1台。每组分解槽配340 m2中间降温换热器6台及两组水力漩流器分级机。
五车间:蒸发
包括:蒸发原液槽及水洗、蒸发站、排盐苛化、循环母液、酸洗站
a.蒸发原液及水洗:3台ф13m原液槽
b.蒸发母液:3台ф13m母液槽
c.液体碱储槽:3台ф10m液体碱补碱槽
d.蒸发站:2组。每组采用蒸水量22t/h六效管式降膜蒸发器组,带
强制循环结晶排盐器。
六车间:焙烧
包括:成品过滤及洗涤、氢氧化铝仓、焙烧、氧化铝输送、氧化铝仓、氧化铝包装及堆栈
a.成品过滤:2台引进的62平盘过滤机
b.焙烧:2台丹麦smith技术的1350t/d气体悬浮焙烧炉,燃料为城
市煤气。
c.氢氧化铝仓:2400t容量。
d.氧化铝仓:4台7000t氧化铝仓。
e.氧化铝包装及储运:按1t大袋包装,包装堆栈厂房60x162m。
辅助车间:
检修车间、清理车间、循环水车间、电器车间、计控车间
工艺过程描述
一、原料车间:
由汽车运来的铝土矿经地磅站称重后,倒入卸矿站或铝矿原矿堆场,经胶带输送机送往破碎站,矿石粒度从200mm破碎到0~25mm,送入均化堆场堆存并凉干水分,在堆场内设有一个带棚的合格料场,经取料机平铺直取均化后,送入原料磨。
外构石灰由汽车运进厂,经斗式提升机卸入石灰仓,仓底设置板式给料机,胶带输送机,一部分石灰被送往原料磨磨头仓,另一部分石灰送往石灰消化工段。
在石灰消化工段,石灰与热水一同加入化灰机中,制备的石灰乳流进石灰乳槽,石灰乳用泵送往蒸发车间苛化工序,和沉降车间控制过滤工序。消化渣用胶带机送消化堆场,消化渣最终用汽车运出厂,送赤泥堆场堆存。
铝土矿、石灰经计量后与循环母液按比例,加入两段磨矿系统的棒磨机中磨制原矿浆,原矿浆用水力漩流器进行分级,分级机溢流为合格的原矿浆,送原矿浆槽,再用矿浆泵送往溶出车间的预脱硅工段。分级机底流返回两段磨矿系统中的球磨机进一步磨浆,然后仍进入水力漩流器进行分级,形成闭路磨浆系统。
二、溶出车间:
从原料车间送来的原矿浆进入常压脱硅工段的加热槽中,将温度从82~87℃提升到100~105℃,然后送入预脱硅槽中进行连续脱硅。经8小时后在预脱硅槽中的末槽用剩余循环碱液混合,调整经脱硅后的原矿浆的碱度和温度,合格原矿浆送至高压泵房的隔膜泵。脱硅槽底部设有返砂管、返砂泵,每班定期将粗砂返回原料磨工段。
原矿浆经隔膜泵送入6级单套管二次汽预热器预热至174~180℃,再经4级带机械搅拌的罐式预热器用二次汽预热至210~220℃,然后进入罐式加热器和保温溶出器,用新蒸汽间接加热至265℃进行保温溶出30~50分钟。溶出后矿浆经10级自蒸发降温,温度从260℃降至125℃,然后送入稀释槽与赤泥洗涤送来的赤泥洗液混合。稀释料浆用泵送往溶出后槽,停留4小时以上,以脱除溶液中的硅、铁、锌等杂质。
各级矿浆自蒸发器产生的二次汽用于预热矿浆和作预脱硅的热源,自蒸发的冷凝水逐级闪蒸后排出进入冷凝水罐。冷凝水汇总后送往热水站制备热水。新蒸汽冷凝水闪蒸至158℃送回锅炉房。二次汽剩余部分送入低压汽管网。
三、沉降车间:
溶出后的矿浆经赤泥洗液稀释后采用高效沉降槽进行分离和4次反向洗涤,絮凝剂经计量后分别加入分离和洗涤沉降槽。分离沉降槽底流含固率约为38~42%,用泵送往洗涤沉降槽,洗水从末槽加入,末次洗涤底流固体含量约为46%~53%,赤泥经浆化后用隔膜泵直接送往赤泥堆场进行干法堆存。
分离沉降槽溢流送控制过滤工段的粗液槽,控制过滤采用立式叶滤机,同时将少量石灰乳加进粗液槽中作为助滤剂,从叶滤机得到的精液送分解车间的精液热交换工段,叶滤渣入滤渣槽中,用泵返回一洗沉降槽。
氢氧化铝洗液加进一洗沉降槽,苛化渣加入二洗沉降槽中。
四、分解车间:
由控制过滤工段送来的精液进入分解车间的精液热交换工序,精液在此工段经两级换热,精液温度从100~105℃降为61~62℃,然后送种子过滤冲晶种。第一级为精液与分解母液换热,第二级为精液与水换热。
精液冲晶种后,制备成固含为800g/L的氢氧化铝料浆,用晶种泵送往1~2分解槽中,分解采用高浓度,高种子比工艺制备砂状氢氧化铝,在分解槽尾部适当位置设置二台水力漩流器分级机组,分级底流为粗颗粒氢氧化铝料浆,作为本车间产品送往焙烧车间成品过滤工序,分级溢流返回分解槽中,分解倒数第二槽为种子出料槽,在槽中上部适当位置出料自流进种子过滤工段,经过滤后晶中流进晶种槽中,过滤母液进锥形母液槽。
种分母液用泵输送,一部分送氢氧化铝分级,调配料浆固含比,另一部分送精液热交换工序与精液换热,热交换后母液温度从50~55℃升至85~90℃,送蒸发车间的蒸发原液槽。
为提高分解产出率,在分解槽顶部适当位置设有宽流道板式换热器,作为中间降温设备。
种子过滤采用氢氧化铝种子制备机,氢氧化铝分级采用氢氧化铝粒度分级机进行。
氢氧化铝粒度分级机的底流做为产品,泵送Al(OH)3分离洗涤工序的氢氧化铝成品分离洗涤机,分离所得母液去精滤,洗涤所得Al(OH)3洗液送去稀释,Al(OH)3滤饼去焙烧。
种子过滤和产品过滤Al(OH)3分离所得的种分母液送袋式过滤机
精滤回收氢氧化铝浮游物,精滤后的种分母液送去蒸发。部分种分母液经蒸发排盐后得到的蒸发母液,与未蒸发的种分母液及补充的液体苛性碱混合调配成N=245g/l的循环母液去源矿浆磨制工序。
母液蒸发后分离出的结晶碱用车送专用堆栈存放。
五、蒸发车间:
从分解车间送来的母液进入蒸发车间的蒸发原液槽,蒸发工段采用母液部分蒸发工艺,一部分母液进蒸发器中,另一部分母液直接送往循环母液调配槽。
蒸发站由一组六效降膜蒸发器和一台强制循环结晶蒸发器及三级闪蒸组成,蒸发采用逆流流程。原液由末效逐级送到前效蒸发,最后到一效。
一效的出料温度为140℃,此溶液进入三级闪蒸系统,逐级闪蒸降温,三闪出料温度92℃左右,三闪出料即为蒸发母液,送往循环母液调配槽制备循环母液。
由蒸发二闪出料引一定数量的母液进强制效,使其蒸浓到Na2O k320g/L以上,并从盐沉降槽底流中引入部分Na2CO3固体颗粒作为晶种,温度控制在103℃,加热蒸汽用一效产生的部分二次汽(或新蒸汽)做热源,控制好结晶条件,使从强制效母液中析出的碳酸钠主要为颗粒粗大、沉降及过滤性能较好的无水碳酸钠,结晶器出料去盐沉降槽,底流进盐过滤机,经过滤后的碳酸钠滤饼稀释后进苛化槽。苛化料浆送苛化分离过滤机,滤渣送往赤泥沉降车间的二洗沉降槽。强碱液返回四闪,经闪蒸后送循环母液调配槽制备循环母液。
生产补碱用NaOH浓度大于42%的液体苛性碱,循环母液储槽区域设有补碱设备。
六、焙烧车间
由分解分级来的氢氧化铝浆液经氢氧化铝浆液贮槽,用泵送入水平盘式过滤机,对氢氧化铝进行分离及洗涤,洗涤后滤饼含水率6~8%,用胶带输送机送往焙烧炉喂料箱或氢氧化铝仓,过滤后母液送种
子过滤的锥形母液槽,氢氧化铝洗液送赤泥洗涤工序。
从成品过滤或氢氧化铝仓来的氢氧化铝卸入焙烧工序的50m3喂料箱内,喂料箱内料位与仓下皮带计量给料机联锁,控制焙烧炉进料量。含水6~8%的氢氧化铝经胶带输送机,螺旋喂料机送入文丘里干燥器内,干燥后的氢氧化铝被气流带入第一级旋风预热器中,烟气和干燥的氢氧化铝在此进行分离,一级旋风出来的氢氧化铝进入第二级旋风预热器,并与从热分离器来的温度约为1000℃的烟气混合进行热交换,氢氧化铝温度达到320~360℃,附着水基本脱除,预焙烧过的氧化铝在第二级旋风预热器内与烟气分离卸入焙烧炉的锥体内,焙烧炉所用的燃烧空气预热到600~800℃从焙烧炉底进入,燃料与空气混合并燃烧、预焙烧的氧化铝及热空气在炉底充分混合,氧化铝的焙烧在炉内约1.4秒内完成。
焙烧好的氧化铝和热烟气在热分离器中分离。热烟气经上述的两级旋风预热器,文丘里干燥器与氢氧化铝进行热交换后,温度降为145℃,进入电除尘器,净化后的烟气用排风机送入烟囱排入大气。
热分离器出来的氧化铝经两段冷却后温度降至80℃,第一段冷却采用四级旋风冷却器,在四级旋风冷却过程中,氧化铝温度从1050℃降为260℃,燃料燃烧所需空气温度预热到800℃,第二段冷却采用沸腾床冷却机,用水间接冷却,使氧化铝温度从260℃降为80℃。从沸腾床冷却机出来的氧化铝用风力送入氧化铝仓,经包装送堆栈,氧化铝包装采用1吨大袋包装,包装好后的氧化铝用汽车运出厂。
电收尘器收下的粉尘,用螺旋输送泵送入第二级旋风冷却器中。因电除尘收下的粉尘较细,可作为多种氧化铝外销。
主要工艺条件:
1、破碎站:(1)进场粒度≤200mm;(2)出矿粒度≤25mm
2、均化堆场:(1)铝矿进厂粒度≤25mm;(2)堆高10m
(3)堆积角33~37℃;(4)堆场贮量10万吨
(5)堆场贮存时间20天
3、石灰消化:(1)石灰消化率80%;(2)消化渣含水率20%
(3)石灰乳浓度CaO 180g/L;(4)石灰进厂粒度≤25mm;
4、原料磨:(1)原矿产品细度100%<500um;99%<315um;70~75<63um;(2)循环母液浓度Na2O k 240g/L, Na2O C 22.3g/L, AL2O3 142.2g/L,
(3)循环母液Rp 0.593, Na2O C/Na2O t≤8.5%,温度88-90℃;(4)石灰添加量:以全CaO计为7%(以干铝土矿重量计)
(4)常压脱硅脱硅温度100-105℃,脱硅时间10小时,脱硅固含300-320g/L
5、高压泵房(1)泵工作压力6.0-6.8MPa(2)泵的工作温度95-98℃(3)净吸压头0.12MPa(4)进料矿浆固含200-240g/L
6、高压溶出(1)溶出温度260℃
(2)矿浆预热:全部间接加热,用二次蒸汽将矿浆温度预热至210-220℃,再用高压新蒸汽加热到260℃(3)保温溶出时间30分钟(4)矿浆自蒸发:采用十级闪蒸,料浆温度从260℃降至125℃(5)高压新蒸汽压力6-6.2MPa,温度290±10℃(7)氧化铝相对溶出率≥93% (8)溶出液Rp 1.18(9)赤泥碱比Na20/SiO2≤0.38
7、稀释:稀释料浆苛性碱浓度168g/L;稀释浆固含60-78g/l;稀释浆温度107℃,最高110℃
8、赤泥沉降分离洗涤:分解槽进料温度105℃,分离沉降槽底流含固量38-42%;溢流浮游物含量80-150mg/l,最大250mg/l;洗涤沉降槽温度90-95℃,沉降槽底含固量46-53%,分离及洗涤过程中水解损失1.5%
9、控制过滤:叶滤机进料含固80-150mg/L; 叶滤机滤液温度100℃,最高105℃,叶滤机固含<15mg/l,叶滤机产能1.1m3/m2.h
10、精液热交换:采用二级换热,第一级精液与分解母液换热,第二级为精液与水换热;进口温度100℃,最高105℃,出口温度60-62℃,分解母液进口50-55℃,分解母液出口85-90℃,水进口温度≤35℃,水出口48℃;
11、分解及分级:精液温度60-62℃,分解槽首槽固含800g/l,(3)种子应具有的质量:粒度为<44u占3-15%,最大25%;种子含附液滤≤20%,分解产出率≥99kg/m3;分解时间45-50小时,分解首槽温度50-55℃;水旋器进料固含325g/l;水旋器进料压力0.1-0.12MPa水旋器底流稀释后固含780-794g/l;水旋器底流粒度<44u为2-9%。12、成品过滤:(1)平盘过滤机的进料温度50-55℃;进料固含
780-794g/l;洗水加入量:0.75t/t氧化铝;洗水温度85℃;母液浮游物含量<2g/l;滤饼含水率6-8%,滤饼中可溶性碱Na2O≤0.06%。13、种子过滤:(1)立盘过滤机的进料温度50-55℃;滤饼含附液率,=20%,母液浮游物含量<2g/l;过滤机产能5-5.5t/m2.h,种子过滤进料固含620-750g/l。
14、焙烧:(1)焙烧炉产能1350t/日;焙烧系统压降600-800mmH2O 焙烧炉温度分布:废气145℃、二级预热器320℃、焙烧炉出口1050℃、热旋风器出口1050℃、一级旋风冷却器710℃、二级旋风冷却器560℃、三级旋风冷却器386℃、四级旋风冷却器215℃;沸腾冷却器排出氧化铝80℃,排出废气温度145-160℃;出口含尘量≤50mg/Nm3;焙烧过程中-45u细粒子增加量2-3%。
15、氧化铝包装及堆栈
16、蒸发及结晶碱分离
(1)蒸发器组蒸水能力220t/h.组
(2)蒸发原液温度85-90℃
(3)新蒸汽压力0.45-0.55MPa,温度190±20℃
(4)蒸发器组出料温度93℃
(5)循环母液温度90℃
(6)二次蒸汽冷凝水温度76℃,最大含碱量20mg/l
(7)结晶碱分离沉降槽温度100-103℃
(8)沉降槽底流固含>250g/l
(9)沉降槽溢流固含<0.5 g/l
(10)盐过滤机滤饼含水率35%
17、苛化
(1)苛化原液中NaCO3含量13.3%
(2)苛化温度95℃,时间4小时
(3)石灰添加量【CaO/Na2Oc】=1.2
(4)苛化效率≥78-80%
主要设备清单
引进设备清单万欧元
主要技术经济指标
自动化控制
在工厂综合办公大楼,设全厂生产信息调度中心,负责全厂生产
过程信息的监视、管理和调度。
生产流程的控制,采用DCS,以车间为单位,设立原料磨、溶出、沉降、分解、蒸发、焙烧及成品过滤七大自控室,将整个氧化铝厂的主要生产操作集中在这七大自控室,采用控制室CRT操作站集中控制和操作的方式,对整个生产过程的信息集中地进行监视和控制,充分利用DCS系统的优越性能,将七大自控室与全厂生产信息调度中心的网络连成一体,实现生产过程的监视、控制和管理的集中化和自动化。非生产流程的控制,采用PLC控制系统,以子项为单位,采用控制室CRT操作站集中控制和操作的方式,对整个生产过程的信息集中的进行监视和控制。
控制水平:
根据本工程工艺生产过程对控制技术和自动化管理的要求,其控制水平具有技术上的可靠性和先进性以及经济上的合理性。这不仅体现在所采用的控制设备和控制手段上,同时也体现在具有成熟适用技术和经验的控制策略和先进的控制软件上。也就是说所采用的控制设备和控制手段均先进可靠,并有较高的性价比,具有成熟的使用经验;所采用的控制策略及应用软件均经过实际生产的检验,并经过多次优化的先进可靠的技术,氧化铝生产和管理的自动化控制水平达到国际先进水平。
DCS系统
工程在生产主流程以车间为单位,采用先进的分布式控制系统,对车间的整个生产过程的信息集中地进行监视和控制。各车间的DCS 系统相互连接,并连接至全厂生产信息调度中心,形成全厂性的DCS 系统局域网。
系统设计原则:DCS在技术上要具备安全、先进性,并有技术的超前性,同时考虑经济上的合理性。
系统扩展性和可靠性:采用的DCS系统是容易扩展的,目前应能在系统工作的情况下进行扩展(比如扩展到另一组生产装置)。同时系统具有高可靠的结构,它对控制器。通讯功能、系统与过程的接口,
系统与供电之间,都有一个故障裕度。软件上的故障裕度包括系统内的各种程序冗余检查和全局数据库的诊断。
系统的开放性:采用的DCS是开放的,具备ODBC数据交换和ODA开放式数据存取功能,能与第三方供货商的网络进行通信。
过程输入/输出:系统提供丰富的工程输入/输出模块,通过这些模块将系统与过程接起来,为每一路输入/输出信号提供隔离通道,并为现场的变送器提供24VDC。
数据库管理:系统有一个实时数据库管理单元,实时数据库管理所提供的主要功能包括:模拟、数字及逻辑控制。随机数据存储,数据趋向与检索,数据历史处理、报表生成等。
控制功能:主要包括:
过程信息采集;模拟量调节控制;工艺数理模型的运算;数字、逻辑量的运算;顺序控制、批量控制。
监控功能:系统提供高水平的过程管理能力,多重变换控制以及数据库的优化,并通过一些广泛的、可扩展的功能模块、有效而容易地应用现成地工业软件包。
操作员接口:操作站是形式简明的、具有良好交互性的友好人机界面。它具有信息显示的功能和分配系统信息以及收到发往任何生产过程的操作命令。在控制室,所有操作站均有同样的显示组态或控制操作能力,亦可对各操作站进行操作任务的分配,使得操作任务共同承担。如果任一操作站出现故障,另外的操作站会自动承担其任务。控制配备:
DCS系统配备:根据本工程生产过程对控制技术和自动化管理的要求,以及各车间复杂的工艺数理模型的运算对DCS控制系统数学运算能力的要求,控制系统应配备中大型规模以上的国外品牌的DCS。现场仪表设备:
现场仪表设备担负着生产过程信息的采集和生产控制指令的执行的重要作用,地位非常重要。本工程的现场仪表设备将以氧化铝行业有成熟使用经验的国外产品及国内引进技术的产品为主。
专用控制软件:
本工程各车间的控制系统的应用软件,是根据各车间的具体控制要求专门编制,是氧化铝生产过程的核心技术的具体体现,关系到工厂的正常运转,生产技术经济指标的好坏及工厂自动化的实现等诸多重大问题,具有突出的重要地位。这些专用控制软件属专利产品,由于引进的费用高昂,拟由国内有经验的专业公司承担。
主要物料流量表
拜耳法氧化铝生产中的有机物
拜耳法氧化铝生产中的有机物 有机物的积累和危害是大多数拜耳法氧化铝厂必须面对的问题。溶液中有机物含量较高时,其所产生的负面影响往往是多方面的,工厂的产量、产品质量及其它技术经济指标将因此受到严重影响。文献[1]报道,仅澳大利亚每年由于有机物造成的氧化铝产量损失就达130万吨。某些有机物的存在使生产砂状氧化铝变得困难。因此,有机物问题成为氧化铝生产中的主要研究方向之一。国外就拜耳法生产中有机物的行为、对生产过程的影响及其排除方法等进行了长期的、大量的研究,取得了重要进展。 我国大多数氧化铝厂采用混联法或烧结法生产,有机物的影响很小或完全不存在。平果铝业公司氧化铝厂是我国目前唯一的采用纯拜耳法生产的工厂,投产较晚,原矿中的有机物含量也较低,有机物的影响需继续观察和研究。我国在“九五”期间进行的中、低品位铝土矿选矿研究取得了重大的进展,但除原矿中部分有机物进入精矿外,还有一定数量的浮选药剂被带入精矿,这种浮选药剂在拜耳法生产中的行为及其影响如何,尚未见诸文献报道,非常值得重视。 一、拜耳法溶液中的有机物 拜耳法溶液中的有机物主要来自铝土矿,絮凝剂、消泡剂、脱水剂等添加剂也会带入少量有机物。但据文献报道,其数量和影响均较小。铝土矿中的有机碳含量通常为0.1-0.3%,但亦可低至0.03%或高达0.6%(某些地表矿)。热带铝土矿中有机碳含量较高,一般为0.2~0.4%,而一水硬铝石型铝土矿中
的含量则较低,通常为0.1%。南美、非洲、澳大利亚铝土矿中的有机物含量较高,而欧洲、俄罗斯和中国的大多数铝土矿有机物含量较低。 铝土矿中的有机物分为腐殖质和沥青两种[2]。腐殖质主要成分为木质素转变的产物—腐殖酸。腐殖质成分复杂,其平均元素组成为,%:58%C,36%O2,4%H2,2%N2及其它杂质。腐殖质易溶于碱液。沥青中的C和H含量比腐殖质中的高,实际上不溶于碱液。据文献[3],铝土矿高压溶出时,腐殖质几乎全部溶入溶液,而沥青的溶出率不高于10%,在赤泥浆液稀释及沉降分离过程中,又全部析出进入赤泥。Jose G. Pulperiro等[4]报道,在铝土矿溶出条件下,60-90%的腐殖质溶解于强苛性碱溶液中,生成腐殖酸钠。不溶解的腐殖质是由于被铝土矿中不溶的无机物结合或吸附。 虽然原矿中有机物的含量一般不高,在铝土矿溶出时也非全部进入溶液,但由于种分母液与洗液是循环的,拜耳法流程中的有机物会逐渐积累,直至达到进出平衡为止。溶液中有机物的平衡浓度主要取决于铝土矿中有机物的含量及其组成,也与溶出条件等有关。一般情况下,拜耳溶液中有机碳含量为7-15g/L,在极端情况下可达25g/L[5]。文献[6]报道,处理热带铝土矿的德国施塔德氧化铝厂的溶出液中,有机碳含量甚至高达34g/L。 Β. Α. Зинченко[7]早期所作的乌拉尔氧化铝厂有机物的平衡表明:随铝土矿(一水硬铝石型)进入流程的有机物占全部有机物的88.5%,其余11.5%来自面粉(当时用作赤泥絮凝剂),而赤泥排走的有机物占全部有机物总量的83%,仅有17%进入溶液。进入溶液中的有机物主要随苏打结晶(据有关资料,苏打结晶中有机碳含量达0.5~1.5%)和氢氧化铝排出,二者分别占原矿中有机物总量的5.7%和4.5%,按对进入溶液中的有机物总量计算,则分别占33.5%和26.5%,其余则随苏打苛化后的石灰渣、蒸发母液等
氧化铝生产流程
氧化铝生产流程控制概述(1) 铝是世界上第二大常用金属,其产量和消费量仅次于钢铁,是国民经济中具有支撑作用和战略地位的金属原材料。氧化铝是铝冶炼的主要原料,每生产1吨原铝需要消耗近2吨氧化铝。此外,各种特殊性能的氧化铝也广泛应用于电子、石油、化工、耐火材料、陶瓷、造纸、制药等行业,因此,氧化铝生产在我国经济建设中占有十分重要的地位。 我国具有较丰富的铝土矿资源(保有储量约26亿吨),居世界第四位,具备发展铝工业的资源条件。我国的氧化铝是在建国后伴随着电解铝的生产和发展建立起来的,八十年代以来得到了较快发展。近年来,氧化铝价格的暴涨,激励投资者和氧化铝厂持续加速生产和扩张。国内目前已有中铝公司所属的山东、山西、河南、中州、贵州、平果、重庆与遵义(拟建)八大铝厂,广西华银(160万吨)、阳煤集团(120万吨)、鲁能晋北、山东信发(100万吨)、三门峡开曼、东方希望(80万吨)铝业等数十个大小氧化铝厂建成或在建。据专家估计,2006年我国的氧化铝产量将年增29-33%,达到1200-1300万吨。 氧化铝生产工艺类型 氧化铝是用不同的生产方法是从铝土矿中提取出来的白色粉末。氧化铝是典型的大型复杂流程性工业,全世界90%以上的氧化铝直接采用的是经济的拜耳法生产流程,而我国氧化铝企业因矿质的不同,而分别选用不同的生产工艺。 烧结法:适于矿石品位含硅高、难溶的、中等资源品位的一水硬铝石,流程长、工艺复杂。我国绝大部分老的氧化铝企业多采用这一方法进行氧化铝冶炼。山东铝厂、中州铝厂Ⅰ期、山西铝厂Ⅰ期
烧结法氧化铝生产过程主要包括熟料烧成、熟料溶出、精液制备、分解和蒸发等主要的生产工序。 来自原料磨的生料浆通过回转窑烧制成易于溶出的铝酸钠熟料,再经碳分母液和一次洗液浸泡后进行溶出;此后通过赤泥分离洗涤、粗液脱硅、硅渣分离等工序生成的精液分别送至碳分和种分工序进行分解反应,析出氢氧化铝;种分母液经蒸发形成的种蒸母液送拜尔法碱液调配后给原矿浆配料;碳蒸母液则返回至原料磨配料。析出的氢氧化铝送焙烧工序进行焙烧。与拜耳法相比,烧结法主要在熟料烧成和碳分分解的控制部分是完全不同的两个过程 拜尔法:拜尔法是Karl Joseph Bayer于1887年发明,他发现加入精种的铝酸钠溶液中可以分解出AL(OH)3,分解母液蒸发后可以在高温高压下溶出铝土矿中的AL(OH)3。该发现后来在实验中得到证实并应用于工业实践,是国外氧化铝最广泛采用的生产工艺。适于生产易溶的三水铝石和一水软铝石,处理中等品位铝土矿碱耗高、矿耗大是常规拜耳法生产氧化铝的缺点。贵州铝厂Ⅰ期、平果铝厂 拜尔法氧化铝生产过程主要包括预脱硅、溶出过程,赤泥洗涤、过滤过程,种分分解过程和氢氧化铝过滤、焙烧等主要的生产工序。 选矿拜尔法:可将A/S为4以上的铝土矿通过浮选成A/S为11.2的矿浆,可提高单管溶出系统的溶出率,工艺管道和罐内不易结巴。中州铝厂Ⅱ期 串联法:处理中低晶位铝土矿的适宜方法。先以较简单的拜尔法处理矿石,最大限度地提取矿石中的氧化铝,然后再用烧结法回收拜尔法赤泥中的 Al2O3和 Na2O,可降低氧化铝生产的综合能耗,Al2O3的总回收率高,
氧化铝生产工艺流程
氧化铝生产工艺流程及在线设备描述 我厂氧化铝生产工艺流程采用拜耳法工艺。其用的矿石、石灰用汽车运入卸矿站,通过板式输送机,胶带输送机及卸料车进入矿仓和石灰仓。磨头仓底部出料设有电子皮带计量装置。按规定的配料比与经过计量的循环母液加入磨机。磨矿过程采用一段球磨与水力旋流器分级闭路的一段磨矿流程,磨制合格的原矿浆送往原矿浆槽,再用泵送至溶出工序的矿浆槽。 矿浆槽内矿浆送入溶出系统,管道化溶出采用Φ159Φ×8/2 ∣Φ480×10×1150000管道化溶出器,三套管四层间接加热连续溶出设备(Φ159管走料,Φ480管供汽),通过四段预热和三段加热,使物料出口温度达145℃,送入保温罐保温一小时以上,经过三级闪蒸和稀释,完成溶出过程。 稀释矿浆在Φ16M高效沉降槽内进行液固分离,底流进入洗涤沉降槽,进行5~6次赤泥反向洗涤,末次洗涤沉降槽底流经泵送往赤泥堆场进行堆存。 将合成絮凝剂制备成合格的溶液,按添加量加入赤泥分离沉降槽,将制备好的合成絮凝剂按添加量加入赤泥洗涤沉降槽,以强化赤泥沉降、分离和洗涤效果。 分离沉降槽溢流用泵送入粗液槽,再送226m2立式叶滤机进行控制过滤,过滤时加入助滤剂(石灰乳或苛化渣),滤饼送二次洗涤槽,精液送板式热交换器。 精液经板式热交换器与分解母液和冷却水进行热交换,冷却至设定温度后,再与种子过滤滤饼(晶种)混合,然后用晶种泵送至种分分解槽首槽(1#或2#槽),经连续种分分解后,从11#槽(或12#槽)顶用立式泵抽取分解浆液进行旋流分级。分级溢流进13#(或12#)分解槽,底流再用部分分解母液稀释后自压或用泵至产品过滤机,分解11#槽的分解浆液,从槽上部出料自流或下部用泵至120m2种子过滤机,滤饼用精液冲入晶种槽,滤液入锥形母液槽。 AH浆液经泵送入80 m2平盘过滤机,进行成品过滤、洗涤、氢氧化铝滤饼经皮带送至氢氧化铝储仓或直接送至焙烧炉前小仓。母液送种子过滤机的锥形母槽。氢氧化铝洗液(白泥洗液)送溶出稀释槽。锥形母液槽的溢流进母液槽,底流送立盘过滤机过滤,滤液进母液槽,滤饼混合后作种分种子。母液槽内母液部分送氢氧化铝旋流分级底流作稀释液,其余经板式热交换器与精液进行热交换提温送至蒸发原液槽。 蒸发原液除少部分不经蒸发直接送母液调配槽外,大部分送六效管式降膜蒸发器内进行浓缩,经三次闪蒸后的蒸发母液送调配槽。在流程中Na2CO3高于规定指标时,需排盐,此时,蒸发二级闪蒸出部分母液送强制循环蒸发器内进行结晶蒸发,并加入部分盐晶种,作为蒸发结晶的诱导结晶,然后在析盐沉降槽进行分离,底流用排盐过滤机进行过滤分离,滤饼用热水溶解后,送入苛化槽内,添加石灰乳进行苛化,苛化渣送赤泥洗涤系统。排盐过滤机滤液和盐分离沉降槽溢流进强碱液槽,其一部分送入蒸发出料第三次闪蒸槽与蒸发母液混合,还有一部分送各化学清洗用点和种分槽化学清洗槽。新蒸汽含碱冷凝水和二次蒸汽冷凝水用作氢氧化铝洗水或送沉降热水站。生产补碱用NaOH浓度大于30%的液体苛性碱,循环母液储槽区域设有补碱设施。 焙烧炉前小仓料位与仓下皮带计量给料机连锁,控制焙烧炉进料量。含水6~8%的氢氧化铝经皮带、螺旋喂料机送入文丘里干燥器内,干燥后的氢氧化铝被汽流带入一级旋风预热器中,一级旋风出来的氢氧化铝进入第二级旋风预热器,并与从热分离器来的温度约1000℃的烟气混合后进行热交换,氢氧化铝的温度达320~360℃,结晶水基本脱除,预焙烧过的氧化铝在第二级旋风预热器与烟气分离卸入焙烧炉的锥体内,焙烧炉所用的燃烧空气经预热至600~800℃从焙烧炉底部进入,燃料、预焙烧的氧化铝及热空气在炉底充分混合并燃烧,氧化铝的焙烧在炉内约1.4秒钟时间完成。
拜耳法生产氧化铝的工艺流程#(精选.)
1拜耳法生产氧化铝的工艺流程概述 拜耳法系奥地利拜耳(K.J.Bayer)于 1888年发明。其原理是用苛性钠(NaOH)溶液加温溶出铝土矿中的氧化铝,得到铝酸钠溶液。溶液与残渣(赤泥)分离后,降低温度,加入氢氧化铝作晶种,经长时间搅拌,铝酸钠分解析出氢氧化铝,洗净,并在950~1200℃温度下煅烧,便得氧化铝成品。析出氢氧化铝后的溶液称为母液,蒸发浓缩后循环使用。 拜耳法的简要化学反应如下: 由于三水铝石、一水软铝石和一水硬铝石的结晶构造不同,它们在苛性钠溶液中的溶解性能有很大差异,所以要提供不同的溶出条件,主要是不同的溶出温度。三水铝石型铝土矿可在125~140℃下溶出,一水硬铝石型铝土矿则要在240~260℃并添加石灰(3~7%)的条件下溶出。 现代拜耳法的主要进展在于:①设备的大型化和连续操作; ②生产过程的自动化;③节省能量,例如高压强化溶出和流态化焙烧;④生产砂状氧化铝以满足铝电解和烟气干式净化的需要。拜耳法的工艺流程见图1。
拜耳法的优点主要是流程简单、投资省和能耗较低,最低者每吨氧化铝的能耗仅3×106千卡左右,碱耗一般为100公斤左右(以Na2CO3计)。 拜耳法生产的经济效果决定于铝土矿的质量,主要是矿石中的SiO2含量,通常以矿石的铝硅比,即矿石中的Al2O3与SiO2含量的重量比来表示。因为在拜耳法的溶出过程中,SiO2转变成方钠石型的水合铝硅酸钠(Na2O·Al2O3·1.7SiO2·nH2O),随同赤泥排出。矿石中每公斤SiO2大约要造成1公斤Al2O3和0.8公斤NaOH的损失。铝土矿的铝硅比越低,拜耳法的经济效果越差。 2 主要生产原理及过程 2.1 预脱硅与铝硅比的提高 拜耳法生产的经济效果决定于铝土矿的质量,主要是矿石中的SiO2含量,通常以矿石的铝硅比,即矿石中的Al2O3与SiO2
氧化铝的生产方法
氧化铝的生产工艺流程 氧化铝的生产工艺流程从矿石提取氧化铝有多种方法,例如:拜耳法、碱石灰烧结法、拜耳-烧结联合法等。拜耳法一直是生产氧化铝的主要方法,其产量约占全世界氧化铝总产量的95%左右。70年代以来,对酸法的研究已有较大进展,但尚未在工业上应用。 拜耳法 系奥地利拜耳(K.J.Bayer)于1888年发明。其原理是用苛性钠(NaOH)溶液加温溶出铝土矿中的氧化铝,得到铝酸钠溶液。溶液与残渣(赤泥)分离后,降低温度,加入氢氧化铝作晶种,经长时间搅拌,铝酸钠分解析出氢氧化铝,洗净,并在950~1200℃温度下煅烧,便得氧化铝成品。析出氢氧化铝后的溶液称为母液,蒸发浓缩后循环使用。拜耳法的简要化学反应如下: 由于三水铝石、一水软铝石和一水硬铝石的结晶构造不同,它们在苛性钠溶液中的溶解性能有很大差异,所以要提供不同的溶出条件,主要是不同的溶出温度。三水铝石型铝土矿可在125~140℃下溶出,一水硬铝石型铝土矿则要在240~260℃并添加石灰(3~7%)的条件下溶出。现代拜耳法的主要进展在于:①设备的大型化和连续操作;②生产过程的自动化;③节省能量,例如高压强化溶出和流态化焙烧;④生产砂状氧化铝以满足铝电解和烟气干式净化的需要。 拜耳法的工艺流程见图1。
拜耳法的优点主要是流程简单、投资省和能耗较低,最低者每吨氧化铝的能耗仅3×106千卡左右,碱耗一般为100公斤左右(以Na2CO3计)。拜耳法生产的经济效果决定于铝土矿的质量,主要是矿石中的SiO2含量,通常以矿石的铝硅比,即矿石中的Al2O3与SiO2含量的重量比来表示。因为在拜耳法的溶出过程中,SiO2转变成方钠石型的水合铝硅酸钠(Na2O·Al2O3·1.7SiO2·nH2O),随同赤泥排出。矿石中每公斤SiO2大约要造成1公斤Al2O3和0.8公斤NaOH的损失。铝土矿的铝硅比越低,拜耳法的经济效果越差。直到70年代后期,拜耳法所处理的铝土矿的铝硅比均大于7~8。由于高品位三水铝石型铝土矿资源逐渐减少,如何利用其他类型的低品位铝矿资源和节能新工艺等问题,已是研究、开发的重要方向。 碱石灰烧结法 适用于处理高硅的铝土矿,将铝土矿、碳酸钠和石灰按一定比例混合配料,在回转窑内烧结成由铝酸钠(Na2O·Al2O3)、铁酸钠(Na2O·Fe2O3、原硅酸钙(2CaO·SiO2)和钛酸钠(CaO·TiO2组成的熟料。然后用稀碱溶液溶出熟料中的铝酸钠。此时铁酸钠水解得到的NaOH也进入溶液。如果溶出条件控制适当,原硅酸钙就不会大量地与铝酸钠溶液发生反应,而与钛酸钙、Fe2O3·H2O 等组成赤泥排出。溶出熟料得到的铝酸钠溶液经过专门的脱硅过程,SiO2O形成水合铝硅酸钠(称为钠硅渣)或水化石榴石3CaO·Al2O3·xSiO2·(6-2x)H2O 沉淀(其中x≈0.1),而使溶液提纯。把CO2气体通入精制铝酸钠溶液,和加入晶种搅拌,得到氢氧化铝沉淀物和主要成分是碳酸钠的母液。氢氧化铝经煅烧成为氧化铝成品。水化石榴
氧化铝生产工艺
氧化铝生产工艺 在氧化铝生产行业,氧化铝的生产方法大约分四类:碱法、酸法、酸碱联合法、和热法,但目前用于工业生产的基本全部属于碱法。 用碱法生产氧化铝,是用碱(NaOH或Na2CO3)来处理铝矿石,使矿石中的氧化铝转变为铝酸钠溶液。矿石中的铁、钛等杂质和绝大部分的硅则成为不溶解的化合物,将不溶解的残渣(由于含氧化铁而成红色,故称赤泥)与溶液分离,经洗涤后弃去或综合利用,已回收利用其中的有用组分。纯净的铝酸钠溶液分解析出氢氧化铝,经与母液分离、洗涤后焙烧,得到氧化铝产品。 用碱法生产氧化铝又可分为:①拜尔法②烧结法③联合法,因我国的铝土矿资源的特殊性,主要为一水硬铝石,因此在早期建厂的生产氧化铝的方法均采用烧结法、混联法,后期建厂和扩建工程多采用拜尔法较多,拜尔法具有工艺流程简单,投入成本少,产品质量好等特点。 具体情况如下: 中国铝业山东分公司:1954年建厂,采用烧结法,后经四次扩建,主要采用拜尔法,2006年的总产量已达128万吨 中国铝业河南分公司:1965年建厂投产,主要采用混联法,1999年完成4次扩建,年产达80万吨,2005年新建年产70万吨的拜尔法生产线,2006年的年生产量已达到232万吨。 中国铝业贵州分公司:1978年完成一期拜尔法生产线,年产15万吨,后经扩建,采用混联法,2006年已达到年产120万吨。 中国铝业山西分公司:1987年一期烧结法投产,后经扩建,1992年完成二期混联法,年产达70万吨,2005年投产的拜尔法80万吨项目,到2006年已经达到年产219万吨目标。 中国铝业中州分公司:1992年一期投产烧结法,后经两次扩建选矿拜尔法生产线,2006年年产量达172万吨。 中国铝业广西分公司:1995年拜尔法投产使用,2006年总产量达94万吨。 中国铝业集团还有重庆、遵义准备建造氧化铝厂。 除中国铝业公司外,现已建或拟建的氧化铝项目29个,山东荏平氧化铝、山东魏桥氧化铝氧化铝、山西鲁能晋北氧化铝、山东龙口东海氧化铝、山东信发(100万吨)、河南开曼铝、东方希望铝业(三门峡)有限公司、广西华银(160万吨)、阳煤集团(120万吨)等众多氧化铝企业。据专家估计,2006年我国的氧化铝产量将年增29-33%,达到1200-1300万吨。
氧化铝工艺流程简介
氧化铝工艺流程简介 一、生产工艺简介 公司采用国际先进的拜耳法生产工艺,主要设备从德国、法国、荷兰、澳大利亚等国进口;生产指挥系统采用美国Rockwell公司的DCS控制系统。公司还建有庞大的生产ERP系统及信息管理系统,集生产调度、控制、信息采集、管理于一体。 二、生产工艺流程图
三、工艺流程简述 1、原料工序原料矿石堆场在建厂初期,为方便装卸矿石及避免大量杂质在倒运过程进入生产流程,堆场使用原矿石将地基提升50cm压实后用于储存铝土矿。原矿石由汽车运进厂的铝土矿经地磅站称重后和原矿堆场的铝土矿经破碎后一起倒入卸矿站,经胶带输送机送往均化堆场堆存,为避免斗轮取料机将杂质当做矿石取走,取料机斗轮离地面30cm,其间用矿石进行填充,再由胶带输送机将铝土矿送往原料磨的磨头仓。外购石灰由汽车运进厂,卸入石灰卸矿站,经胶带输送机送往石灰仓,一部分石灰通过胶带输送机送往原料磨磨头仓,另一部分石灰送往石灰消化工段。在石灰消化工段,石灰与热水一同加入化灰机中,制备的石灰乳流进石灰乳槽,石灰乳用泵送往蒸发车间苛化工序和沉降车间控制过滤工序。在原料磨工段,铝土矿、石灰及循环母液按比例加入原料磨中磨制原矿浆,原矿浆用水力漩流器进行分级,分级机溢流为合格的原矿浆,送入原矿浆槽,分级机底流返回原料磨。为应对磨机突发故障及流程稳定,矿浆槽必须保持一定液位。 2、溶出工序来自原料磨已研磨好的原矿浆首先进入溶出预脱硅槽,矿浆通过预脱硅槽的压差进行自溢流至末槽,同时为消除矿浆中的SiO2对溶出过程的影响,根据车间操作规程,矿浆在预脱硅槽首槽加热至100℃,且原矿浆在脱硅槽中停留8h以上,以达到预脱硅的目
氧化铝冶炼工艺流程简介
氧化铝的主要冶炼工艺介绍 氧化铝的冶炼工艺大致可以分为烧结法、拜耳法和烧结-拜耳联合法等。 一、烧结法 1.1烧结法的基本原理 将铝土矿与一定数量的纯碱、石灰(或者石灰石)、配成炉料在高温下进行烧结,使氧化硅和石灰化合成不溶于水的原硅酸钙,氧化铝与纯碱化合成可溶于水的固体铝酸钠,而氧化铁与纯碱化合成可以水解的铁酸钠,将烧结产物(熟料)用稀碱溶液溶出时固体铝酸钠便进入溶液,铁酸钠水解放出碱,氧化铁以水合物与原硅酸钙一道进入赤泥。在用二氧化碳分解铝酸钠溶液便可以析出氢氧化铝,经过焙烧后产出氧化铝。分离氢氧化铝后的母液成为碳分母液经过蒸发后返回配料。 1.2烧结法工艺过程简述 烧结法生产氧化铝有生料浆制备、熟料烧结、熟料溶出、赤泥分离以及洗涤、粗液脱硅、精液碳酸化分解、氢氧化铝的分离以及洗涤、氢氧化铝焙烧、母液蒸发等主要生产工序。 生料浆制备:将铝土矿、石灰(或石灰石)、碱粉、无烟煤以及碳分母液按一定的比例,送入原料磨中磨制成生料浆,经过料浆槽的三次调配成各项指标合格的生料浆,送熟料窑烧结。 熟料烧结:配合格的生料浆送入熟料窑内,在1200℃-1300℃的高温下发生一系列的物理化学变化,主要生产使氧化硅和石灰化合成不溶于水的熟料。熟料窑烧结过程通常在熟料窑(回转窑)内进行,氧化硅和石灰化合成不溶于水的原硅酸钙,氧化铝和纯碱化合成可溶于水的固体铝酸钠,而氧化铁与纯碱化合成可以水解的铁酸钠,并且烧至部分熔融,冷却后成外观为黑灰色的颗粒状物料即熟料。 熟料溶出:熟料经过破碎达到要求的粒度后,用稀碱溶液(生产上称调整液),在湿磨内进行粉碎性溶出,有用成分氧化铝和氧化钠进入溶液,成为铝酸钠溶液,而杂质铁和硅则进入赤泥。 赤泥分离和洗涤:为了减少溶出过程中的化学损失,赤泥和铝酸钠溶液必须快速分离,为了回收赤泥附液中所带走的有用成分氧化铝和氧化钠,将赤泥进行多次反向洗涤再排入堆场。
氧化铝生产工艺流程图
氧化铝生产工艺流程图 流程仿真技术原理 根据工艺过程所涉及到的基础物性数据,引用或创建特定的物性包,建立生产过程中的单元设备的数学模型和单元设备之间的模型,从而完成完整描述实际生产过程系统的数学模型[6,7]。通过一定的数学方法对过程中所涉及到的模型进行联列求解。通过装置的稳态和动态模型,进行不同方案和工艺条件的分析,为新工艺的规划、研究开发和技术可靠性进行分析,为生产实际提供优化操作指导。在动态模拟中,还可以通过不同控制策 略的比较,对生产过程进行优化控制[5]。 生产过程的数学模型通常为一大型非线性代数方程组,过程模拟实质就是通过求解该非线性方程组来预测在一定工艺条件下生产过程的性能。常用 的求解方法主要有序贯模块法、联立方程法和联立模块法[3]。 氧化铝生产工艺 氧化铝的生产方法有酸法、碱法和热法。目前氧化铝工业生产实际应用的是碱法。碱法又包括拜耳法、烧结法及各种形式的联合法。因拜耳法生产成本低,经济效益好,流程相对简单,应用最广,所以主要介绍一下拜耳法的生产工艺。 所谓拜耳法是因为它是由K.J.bayer在1889-1892年提出而得名的。拜耳法主要包括两个主要过程,一是Na2O与Al2O3摩尔比为1.8的铝酸钠在常温下,只要添加氢氧化铝作为晶种,不断搅拌,溶液种的Al2O3就可以呈氢氧化铝析出,直到其中Na2O:Al2O3的摩尔比提高到6为止,此即为铝酸钠溶液的晶种分解过程。另一过程是已经析出了大部分氢氧化铝的溶液。在加热时,又可以溶出铝土矿中的氧化铝水合物。此即利用种分母液溶出铝土矿的过程。交替使用这两个过程处理铝土矿,得到氢氧化铝产品,构成所谓拜耳法循环[8]。拜耳法的生产工艺流程图如图1 所示。
拜耳法氧化铝生产工艺流程框图
拜耳法氧化铝生产工艺流程框图 成品氧化铝 图一 焙烧 2O 3 图二 碱法生产氧化铝基本过程
开曼铝业氧化铝厂工艺流程简图
氧化铝厂主要生产车间 一车间:原料准备 包括:地磅房、破碎站、原矿堆场、均化库、石灰仓、石灰消化及原料磨等工段 a.石灰消化:3台ф1200x10500m化灰机,2用1备 b.石灰仓:3台ф14x18m c.拜尔原料磨(棒球两段磨加水力漩流器):4组,每组配一级棒磨 ф3.2x4.5m及二级球磨ф3.6x8.5m,产能100t/h,用3备1。 二车间:高压溶出 包括:常压脱硅、高压泵房、管道化预热、溶出及稀释 a.常压脱硅:3台带加热管束搅拌的ф10x16m预脱硅加热槽及11台 机械搅拌的ф10x16m脱硅槽,1台ф6x6m赤泥洗液槽。其中预脱硅加热槽2用1备,脱硅槽10用1备。 b.高压泵房:36~6.8MPa,流量 400-500m3用1备。 c.溶出装置:2组。采用法铝技术,6级套管预热,4级压煮器预热, 新蒸汽间接加热,保温压煮器停留30分钟,10级闪蒸降温。每组配套预热管预热器长度2880m,19台ф2.8x16.8m压煮器,12台ф3.0-5.0x9.7m闪蒸器。2台ф12.5x13.5m溶出后槽,稀释料浆停留4.2小时,产能400-500kt/a. 三车间:赤泥沉降 包括:赤泥分离及洗涤、絮凝剂制备、控制过滤、赤泥贮槽及赤泥泵站、赤泥堆场、热水站 a.赤泥分离及洗涤:2组。采用高效深锥沉降槽技术及设备。每组配 6台ф14x16-18m高效沉降槽,其中分离槽1台,洗涤槽4台,备用槽1台。 b.控制过滤:7台226m2立式叶滤机,其中用6台备1台。 c.赤泥泵站:3台引进的高压隔膜泵,2用1备。
拜耳法生产氧化铝
书山有路勤为径,学海无涯苦作舟 拜耳法生产氧化铝 所谓“拜耳法”系奥地利化学家K·J·Bayer 于1887 年发明的处理优质铝土矿 制取氧化铝的一种方法。拜耳法就是用含有大量游离苛性碱的循环母液处理铝 土矿,溶出其中的氧化铝得到铝酸钠溶液,往铝酸钠溶液中添加氢氧化铝晶 种,经过一定时间的搅拌分解就可以析出氢氧化铝,分解母液经蒸发后用于溶 出下一批铝土矿。拜耳法生产中经常用到苛性比、硅量指数、循环效率、晶 种系数等概念。拜耳法就是用碱溶出铝土矿中的氧化铝。工业上把溶液中以NaAlO2 和NaOH 形式存在的Na2O 叫做苛性碱(记作Na2Ok),以Na2CO3 形式存在的Na2O 叫做碳酸碱(记作Na2Oc),以Na2CO4 形式存在的Na2O 叫做硫酸碱(记作Na2O),所有形态的碱的总和称做全碱(记作Na2Ot)。苛性比就是铝酸钠溶液中的Na2Ok 与Al2O3 的摩尔比,记作αko。美国习惯用铝酸钠溶液中的Al2O3 与Na2Ok 的质量比表示,符号A/N。硅量指数指铝酸钠溶液中的Al2O3 与SiO2 含量的比,符号A/S。循环效率指铝酸钠溶液中的1t Na2O 在一次拜耳法循环中产出的Al2O3 的量(t),用E 表示。它表明碱的利 用率的高低。晶种系数(种子比)指添加晶种氢氧化铝中的Al2O3 数量与分解原液中的Al2O3 数量之比。分解离指分解出氢氧化铝中的Al2O3 数量占精液中所含Al2O3 数量之比。计算式为:η=(1-αa/αm)×100%式中αa,αm-分别表示分解精液和分解母液的苛性比值。拜耳法生产包括四个过程:(1)用 αk=3.4的分解母液溶出铝土矿中的氧化铝,使溶出液的αk=1.6~1.5;(2)稀释溶出液,洗涤分离出精制铝酸溶液(精液);(3)精液加晶种分解;(4) 分解母液蒸发浓缩至苛性碱的浓度达到溶出要求(230~280g/L)。拜耳法生产 氧化铝的工艺流程如图1 所示。图1 拜耳法生产氧化铝的工艺流程铝土矿的溶出是拜耳法的关键工序。铝土矿中的三水铝石在140℃就很快地溶入苛性碱
氧化铝的生产工艺流程
氧化铝的生产工艺流程 从矿石提取氧化铝有多种方法,例如:拜耳法、碱石灰烧结法、拜耳-烧结联合法等。拜耳法一直是生产氧化铝的主要方法,其产量约占全世界氧化铝总产量的95%左右。70年代以来,对酸法的研究已有较大进展,但尚未在工业上应用。 拜耳法 系奥地利拜耳(K.J.Bayer)于1888年发明。其原理是用苛性钠(NaOH)溶液加温溶出铝土矿中的氧化铝,得到铝酸钠溶液。溶液与残渣(赤泥)分离后,降低温度,加入氢氧化铝作晶种,经长时间搅拌,铝酸钠分解析出氢氧化铝,洗净,并在950~1200℃温度下煅烧,便得氧化铝成品。析出氢氧化铝后的溶液称为母液,蒸发浓缩后循环使用。 拜耳法的简要化学反应如下: 由于三水铝石、一水软铝石和一水硬铝石的结晶构造不同,它们在苛性钠溶液中的溶解性能有很大差异,所以要提供不同的溶出条件,主要是不同的溶出温度。三水铝石型铝土矿可在125~140℃下溶出,一水硬铝石型铝土矿则要在240~260℃并添加石灰(3~7%)的条件下溶出。 现代拜耳法的主要进展在于:①设备的大型化和连续操作;②生产过程的自动化;③节省能量,例如高压强化溶出和流态化焙烧;④生产砂状氧化铝以满足铝电解和烟气干式净化的需要。拜耳法的工艺流程见图1。 拜耳法的优点主要是流程简单、投资省和能耗较低,最低者每吨氧化铝的能耗仅3×106千卡左右,碱耗一般为100公斤左右(以Na2CO3计)。 拜耳法生产的经济效果决定于铝土矿的质量,主要是矿石中的SiO2含量,通常以矿石的铝硅比,即矿石中的Al2O3与SiO2含量的重量比来表示。因为在拜耳法的溶出过程中,SiO2转变成方钠石型的水合铝硅酸钠(Na2O·Al2O3·1.7SiO2·nH2O),随同赤泥排出。矿石中每公斤SiO2大约要造成1公斤Al2O3和0.8公斤NaOH的损失。铝土矿的铝硅比越低,拜耳法的经济效果越差。直到70年代后期,拜耳法所处理的铝土矿的铝硅比均大于7~8。由于高品位三水铝石型铝土矿资源逐渐减少,如何利用其他类型的低品位铝矿资源和节能新工艺等问题,已是研究、开发的重要方向。 碱石灰烧结法 适用于处理高硅的铝土矿,将铝土矿、碳酸钠和石灰按一定比例混合配料,在回转窑内烧结成由铝酸钠(Na2O·Al2O3)、铁酸钠(Na2O·Fe2O3、原硅酸钙(2CaO·SiO2)和钛酸钠(CaO·TiO2组成的熟料。然后用稀碱溶液溶出熟料中的铝酸钠。此时铁酸钠水解得到的NaOH也进入溶液。如果溶出条件控制适当,原硅酸钙就不会大量地与铝酸钠溶液发生反应,而与钛酸钙、Fe2O3·H2O 等组成赤泥排出。溶出熟料得到的铝酸钠溶液经过专门的脱硅过程,SiO2O形成水合铝硅酸钠(称为钠硅渣)或水化石榴石3CaO·Al2O3·xSiO2·(6-2x)H2O沉淀(其中x≈0.1),而使溶液提纯。把CO2气体通入精制铝酸钠溶液,和加入晶种搅拌,得到氢氧化铝沉淀物和主要成分是碳酸钠的母液。氢氧化铝经煅烧成为氧化铝成品。水化石榴石中的Al2O3可以再用含Na2CO3母液提取回收。
拜耳法生产氧化铝工艺
拜耳法生产氧化铝工艺 1. 拜耳法定义 所谓“拜耳法”系奥地利化学家K.J.Bayer于1887年发明的处理优质铝土矿制取氧化铝的一种方法。100多年来它已经有了许多改进,但仍然习惯地沿用着拜耳法这个名词。拜耳法在处理低硅铝土矿,特别是用在处理三水铝石型铝土矿时,流程简单,作业方便,产品质量高,其经济效果远非其它方法所能媲美。目前全世界生产的Al2O3和Al(OH)3,有90%以上是用拜耳法生产的。拜耳法包括两个主要过程,也就是拜耳提出的两项专利。 (1)一项是他发现Na2O和Al2O3分子比为1.8的铝酸钠溶液在常温下,只要添加Al(OH)3作晶种,不断搅拌,溶液中的Al2O3便可以呈Al(OH)3徐徐析出,直到其中Na2O和Al2O3 的分子比提高到6为止。这也就是铝酸钠溶液的晶种分解过程。 (2)另一项是他发现,已经析出大部分Al(OH)3的溶液,在加热时,又可以溶出铝土矿中的Al2O3水合物,这也就是利用种分母液溶出铝土矿的过程。交替使用这两个过程就能够一批批地处理铝土矿,从中得出纯的Al(OH)3产品,构成所谓拜耳法循环。拜耳法的实质也可用下列反应来表示。反应在不同条件下的交替进行: Al2O3(1或3)H2O+2NaOH+aq=2NaAl(OH)4+aq 2拜耳法基本原理及适用范围 2.1基本原理: (l)用NaOH溶液溶出铝土矿,所得到的铝酸钠溶液在添加晶种、不断搅拌的条件下,溶液中的氧化铝呈氢氧化铝析出,即种分过程。 (2)分解得到的母液,经蒸发浓缩后在高温下可用来溶出新的铝土矿,即溶出过程。 2.2适用范围氧化铝的生产方法有拜耳法、烧结法、拜耳—烧结联合法三种。各种方法的适用范围为: (3)拜耳法:7 第一章氧化铝的生产原理和方法 第一节氧化铝和铝矿 烧结法和拜耳法是目前工业生产氧化铝的主要方法。 国外生产氧化铝绝大多数采用拜耳法生产氧化铝,中国结合自己的资源情况,首创了拜耳-烧结混联法,极大地提高了氧化铝的总回收率。随着生产技术的不断提高,石灰拜耳法、选矿拜耳法等一些新的生产方法不断被应用到生产中来。 一、、氧化铝的特性 存在于自然界中的氧化铝称为刚玉(α-Al2O3),是在火山爆发过程中形成的。它在岩石中呈无色的结晶,也可与其他氧化物杂质(氧化铬和氧化铁等)染(形)成带色的结晶,红色的叫红宝石,蓝色的叫蓝宝石。 工业氧化铝是各种氧化铝水合物经加热分解的脱水产物,按照它们的生成温度可以分为低温氧化铝和高温氧化铝两类。 通常电解炼铝用的氧化铝是α-Al2O3和γ-Al2O3的混合物。α-Al2O3它属六角晶系,由于有完整坚固的晶格,所以它是所有氧化铝同质异晶体中化学性最稳定的一种,在酸或碱液中不溶解。γ-Al2O3属于立方晶系,具有很大的分散性,化学性质较为活泼,易与酸或碱溶液作用。 氧化铝的化学纯度 成品氧化铝除主要成分是Al2O3外,往往含有少量的SiO2、Fe2O3、Na2O和H2O等杂质。 氧化铝中残存的结晶水以灼减表示,它也是有害杂质。因为水与电解质中的AlF3作用而生成HF,造成了氟盐的损 失,并且污染了环境。此外,当灼减高或吸湿后的氧化铝与高温熔融的电解质接触时,则会引起电解质暴溅,危及操作人员的安全。 氧化铝质量的分级根据标准YS/7274-1998分为4个等级,如表1-2所示。 表1-2氧化铝质量等级标准 氧化铝的物理性质用于表征氧化铝物理性质的指标有:安息角、α-Al2O3含量、容量、粒度和比表面积以及磨损指数等。 二、铝土矿 地壳中铝的平均含量为8.7%左右,折合成氧化铝为16.4%,仅次于氧和硅,居于第三位,在金属元素中位于第一位。由于铝的化学性质活泼,它在自然界中以化合物状态存在。地壳中的含铝矿物约有250种左右,其中约40%是各种铝硅酸盐,最重要的含铝矿物只有14-15种,而铝土矿就是目前氧化铝生产的主要矿石资源,世界上生产的氧化铝95%左右是从铝土矿中提炼出来的。 评价铝土矿的质量不仅看它的化学成分、铝硅比的高低,而且还要看铝矿的类型。铝土矿中氧化铝的含量通常在45%-75%之间。铝土矿中的二氧化硅是碱法(尤其是拜耳法)生产氧化铝过程中最有害的杂质。我们通常把铝土矿中的氧化铝与二氧化硅的重量之比值称为铝土矿的铝硅比,以符号 铝土矿是目前氧化铝生产中最主要的原料,主要成分为Al 2O 3,SiO 2,Fe 2O 3,TiO 2等,氧化铝主要以三水铝石,一水软铝石,或一水硬铝石状态存在,按氧化铝水合物类型可分为三水铝石型,一水软铝石型,一水硬铝石型或各种混合型 衡量铝土矿质量的标准为:铝硅比、氧化铝含量、矿物类型。铝硅比是指矿石中Al 2O 3含量与SiO 2含量的质量比. 我国铝土矿的主要特点:是高铝、高硅、低铁的一水硬铝石型铝土矿。 生产氧化铝的方法:有碱法、酸法、酸碱联合法、热法。在工业上得到应用的只有 碱法 ,其重要的中间产物是铝酸钠溶液;碱法生产氧化铝主要有拜耳法、碱石灰烧结法和拜耳-烧结联合法,联合法流程有串联、并联和混联。 电解炼铝用的氧化铝必须在氧化铝的纯度和氧化铝的物理性质上符合一定的质量要求。 硅量指数是指铝酸钠溶液中Al 2O 3与SiO 2的质量比,以A/S 表示。 拜耳法的循环效率指一吨Na 2O 在一次拜耳法循环中所产出的Al 2O 3的量(吨),用E 表示,E 的数值越高说明碱的利用率越好。E=1.645×(MR m -MR a )/MR m ·MR a 拜耳法的循环碱量:指生产一吨氧化铝在循环母液中所必须含有的碱量(不包括碱损失),它是循环效率的倒数。 铝酸钠溶液的分子比(苛性比值)是指:铝酸钠溶液中Na 2O 与Al 2O 3的摩尔比,它表示铝酸钠溶液中氧化铝的饱和程度和稳定性。MR=1.645×[Na 2O]/[Al 2O 3] 铝酸钠溶液中的碱分为:苛性碱NaO k 、碳酸碱NaO c 和硫酸碱NaO s :苛性碱NaO k 和碳酸碱NaO c 的和称为全碱NaO T 氧化铝实际溶出率:铝土矿与NaOH 反应实际溶出到溶液中的Al 2O 3量与铝土矿中Al 2O 3总量之比 氧化铝理论溶出率:理论上矿石中可以溶出的Al 2O 3量与矿石中Al 2O 3总量之比。 氧化铝相对溶出率:氧化铝实际溶出率与理论溶出率之比 赤泥的产出率:每处理1t 铝土矿所生成的赤泥量 碱耗:铝土矿溶出过程,每溶出1tAl 2O 3所损失的碱量 铝酸钠溶液的稳定性通常是用从过饱和的铝酸钠溶液开始分解析出氢氧化铝所需时间的长短来衡量的。 配料分子比指:预期矿石中Al 2O 3充分溶出时,溶出液所应达到的分子比 氢氧化铝晶粒附聚:就是在范德华力、自粘力、附着力以及毛细管力和物质之间的紧密接触而形成的表面张力等力的作用下,氢氧化铝晶粒自发和定向的连接在一起的现象。 拜耳法溶出工艺目前分为:压煮器和管道化两大类溶出技术,其中管道化溶出技术是目前比较先进的溶出技术,根据我国一水硬铝石铝土矿的溶出特点,我国形成了具有自主知识产权的管道预热-停留罐溶出技术 一水碳酸钠的苛化是在拜耳法生产过程中,由于苛性碱与矿石中的碳酸盐以及空气中的二氧化碳作用的结果,母液每一次循环都有一部分苛性碱变成了一水碳酸钠。使这部分一水碳酸钠从新变成苛性碱称为一水碳酸钠的苛化。 熟料溶出的副反应指在熟料溶出过程中赤泥中的原硅酸钙2CaO·SiO 2可以与铝酸钠溶液发生一系列的化学反应,使已溶出来的Na 2O 和Al 2O 3又有一部分重新转入赤泥而损失。这些反应称为二次反应或副反应。二次反应所造成的Na 2O 和Al 2O 3的损失称为二次反应损失或副反应损失。 熟料溶出二次反应的主要产物是 水合铝硅酸钠、水化石榴石。 我国碱石灰烧结法采用:低苛性比值、高碳酸钠浓度、二段磨料溶出工艺。 碱比、钙比:碱石灰烧结法生料配方中,[N]/([A]+[F])称为碱比;[C]/[S]称为钙比。 饱和配方是指在烧结法配料过程中采用碱比等于1,钙比等于2的炉料配方称为饱和配方。在碱石灰烧结法生产氧化铝时,我国采用低碱高钙配方,这和我国生料掺煤工艺相符合。 判断熟料质量好坏的标准有:标准溶出率、熟料的密度和粒度、负二价硫含量S 2-。衡量熟料溶出过程好坏的标志是净溶出率 回转窑熟料烧结时,根据物料沿窑长的温度变化分为窑体分为:烘干带、预热带、分解带、烧成带、冷却带五个带。 烘干带:脱附着水干燥。 窑气800→250℃,炉料80 →200℃ 预热带:脱结晶水,Na 2SO 4开始分解 窑气1200→800℃,炉料200 →750℃ 分解带:Na 2CO 3+Al 2O 3→ Na 2O?Al 2O 3+CO 2↑ Na 2CO 3+Fe 2O 3→ Na 2O?Fe 2O 3+CO 2↑ Na 2CO 3+Al 2O 3?2SiO 2→ Na 2O?Al 2O 3?2SiO 2+ CO 2↑ 窑气1400→1200℃,炉料750 →1200℃ 烧成带: 2CaO+Na 2O?Al 2O 3?2SiO 2→Na 2O?Al 2O 3+2CaO?SiO 2 窑气1500℃以上 ,炉料1250-1300℃ 冷却带:熟料逐渐冷却到900-1000 ℃ 左右经下料口进入冷却机 碱石灰烧结法生产氧化铝的基本原理 将铝土矿与一定数量的苏打、石灰、循环母液配成炉料,在回转窑内进行高温烧结,炉料中的Al 2O 3与Na 2CO 3反应生成易溶于水或稀碱溶液的铝酸钠 (Na 2O ?Al 2O 3),杂质氧化铁生成易水解的铁酸钠(Na 2O ?Fe 2O 3),二氧化硅和氧化钛分别生成不溶性的原硅酸钙(2CaO ?SiO 2)和钛酸钙(CaO ?TiO 2) 。将烧结产物(熟料)用稀碱溶液溶出时Na 2O·Al 2O 3便进入溶液,Na 2O·Fe 2O 3水解放出碱,原硅酸钙(2CaO ?SiO 2)和钛酸钙(CaO ?TiO 2)不溶进入赤泥,从而实现杂质矿物与有用矿物的分离。 % 100)/()/)/(%100A Q A Q A Q ?-= ?-= 矿 泥 矿矿 矿泥 泥矿矿实(S A S A S A η%100)/A 1 1%100A ?- =?-= S A S (理η%1001 )/)/()/?--==矿泥 矿理实相((S A S A S A ηηη泥 矿泥 S S = η )/kg 1 /608 100008.60][3222O tAl O Na S A S A S O Na (损失-=?-= %100Al CaO CaO Al Al 323232?????? ? ? ?? -=熟 泥熟泥熟净 O O O A η 拜耳法氧化铝生产中的有机物 拜耳法氧化铝生产中的有机物 有机物的积累和危害是大多数拜耳法氧化铝厂必须面对的问题。溶液中有机物含量较高时,其所产生的负面影响往往是多方面的,工厂的产量、产品质量及其它技术经济指标将因此受到严重影响。文献[1]报道,仅澳大利亚每年由于有机物造成的氧化铝产量损失就达130万吨。某些有机物的存在使生产砂状氧化铝变得困难。因此,有机物问题成为氧化铝生产中的主要研究方向之一。国外就拜耳法生产中有机物的行为、对生产过程的影响及其排除方法等进行了长期的、大量的研究,取得了重要进展。 我国大多数氧化铝厂采用混联法或烧结法生产,有机物的影响很小或完全不存在。平果铝业公司氧化铝厂是我国目前唯一的采用纯拜耳法生产的工厂,投产较晚,原矿中的有机物含量也较低,有机物的影响需继续观察和研究。我国在“九五”期间进行的中、低品位铝土矿选矿研究取得了重大的进展,但除原矿中部分有机物进入精矿外,还有一定数量的浮选药剂被带入精矿,这种浮选药剂在拜耳法生产中的行为及其影响如何,尚未见诸文献报道,非常值得重视。 一、拜耳法溶液中的有机物 拜耳法溶液中的有机物主要来自铝土矿,絮凝剂、消泡剂、脱水剂等添加剂也会带入少量有机物。但据文献报道,其数量和影响均较小。铝土矿中的有机碳含量通常为0.1-0.3%,但亦可低至0.03%或高达0.6%(某些地表矿)。热带铝土矿中有机碳含量较高,一般为0.2~0.4%,而一水硬铝石型铝土矿中的 1 含量则较低,通常为0.1%。南美、非洲、澳大利亚铝土矿中的有机物含量较高,而欧洲、俄罗斯和中国的大多数铝土矿有机物含量较低。 铝土矿中的有机物分为腐殖质和沥青两种[2]。腐殖质主要成分为木质素转变的产物—腐殖酸。腐殖质成分复杂,其平均元素组成为,%:58%C,36%O2,4%H2,2%N2及其它杂质。腐殖质易溶于碱液。沥青中的C和H含量比腐殖质中的高,实际上不溶于碱液。据文献[3],铝土矿高压溶出时,腐殖质几乎全部溶入溶液,而沥青的溶出率不高于10%,在赤泥浆液稀释及沉降分离过程中,又全部析出进入赤泥。Jose G. Pulperiro等[4]报道,在铝土矿溶出条件下,60-90%的腐殖质溶解于强苛性碱溶液中,生成腐殖酸钠。不溶解的腐殖质是由于被铝土矿中不溶的无机物结合或吸附。 虽然原矿中有机物的含量一般不高,在铝土矿溶出时也非全部进入溶液,但由于种分母液与洗液是循环的,拜耳法流程中的有机物会逐渐积累,直至达到进出平衡为止。溶液中有机物的平衡浓度主要取决于铝土矿中有机物的含量及其组成,也与溶出条件等有关。一般情况下,拜耳溶液中有机碳含量为7-15g/L,在极端情况下可达25g/L[5]。文献[6]报道,处理热带铝土矿的德国施塔德氧化铝厂的溶出液中,有机碳含量甚至高达34g/L。 Β. Α. Зинченко[7]早期所作的乌拉尔氧化铝厂有机物的平衡表明:随铝土矿(一水硬铝石型)进入流程的有机物占全部有机物的88.5%,其余11.5%来自面粉(当时用作赤泥絮凝剂),而赤泥排走的有机物占全部有机物总量的83%,仅有17%进入溶液。进入溶液中的有机物主要随苏打结晶(据有关资料,苏打结晶中有机碳含量达0.5~1.5%)和氢氧化铝排出,二者分别占原矿中有机物总量的5.7%和4.5%,按对进入溶液中的有机物总量计算,则分别占33.5%和26.5%,其余则随苏打苛化后的石灰渣、蒸发母液等排出或循环。 1氧化铝生产工艺
氧化铝生产工艺复习资料
拜耳法氧化铝生产中的有机物