数控铣床与加工中心刀具补偿讲解
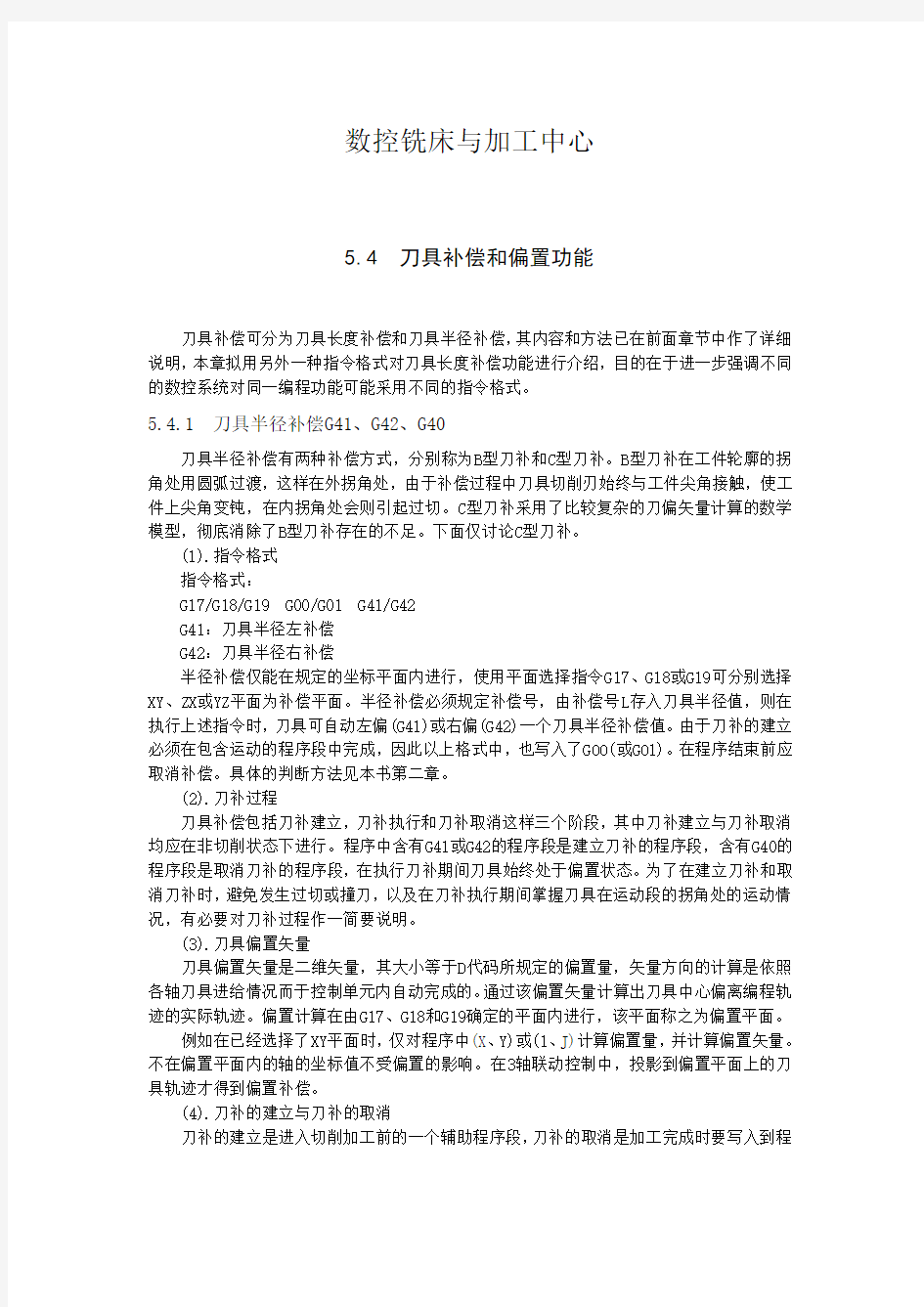

数控铣床与加工中心
5.4 刀具补偿和偏置功能
刀具补偿可分为刀具长度补偿和刀具半径补偿,其内容和方法已在前面章节中作了详细说明,本章拟用另外一种指令格式对刀具长度补偿功能进行介绍,目的在于进一步强调不同的数控系统对同一编程功能可能采用不同的指令格式。
5.4.1 刀具半径补偿G41、G42、G40
刀具半径补偿有两种补偿方式,分别称为B型刀补和C型刀补。B型刀补在工件轮廓的拐角处用圆弧过渡,这样在外拐角处,由于补偿过程中刀具切削刃始终与工件尖角接触,使工件上尖角变钝,在内拐角处会则引起过切。C型刀补采用了比较复杂的刀偏矢量计算的数学模型,彻底消除了B型刀补存在的不足。下面仅讨论C型刀补。
(1).指令格式
指令格式:
G17/G18/G19 G00/G01 G41/G42
G41:刀具半径左补偿
G42:刀具半径右补偿
半径补偿仅能在规定的坐标平面内进行,使用平面选择指令G17、G18或G19可分别选择XY、ZX或YZ平面为补偿平面。半径补偿必须规定补偿号,由补偿号L存入刀具半径值,则在执行上述指令时,刀具可自动左偏(G41)或右偏(G42)一个刀具半径补偿值。由于刀补的建立必须在包含运动的程序段中完成,因此以上格式中,也写入了GOO(或GO1)。在程序结束前应取消补偿。具体的判断方法见本书第二章。
(2).刀补过程
刀具补偿包括刀补建立,刀补执行和刀补取消这样三个阶段,其中刀补建立与刀补取消均应在非切削状态下进行。程序中含有G41或G42的程序段是建立刀补的程序段,含有G40的程序段是取消刀补的程序段,在执行刀补期间刀具始终处于偏置状态。为了在建立刀补和取消刀补时,避免发生过切或撞刀,以及在刀补执行期间掌握刀具在运动段的拐角处的运动情况,有必要对刀补过程作一简要说明。
(3).刀具偏置矢量
刀具偏置矢量是二维矢量,其大小等于D代码所规定的偏置量,矢量方向的计算是依照各轴刀具进给情况而于控制单元内自动完成的。通过该偏置矢量计算出刀具中心偏离编程轨迹的实际轨迹。偏置计算在由G17、G18和G19确定的平面内进行,该平面称之为偏置平面。
例如在已经选择了XY平面时,仅对程序中(X、Y)或(1、J)计算偏置量,并计算偏置矢量。不在偏置平面内的轴的坐标值不受偏置的影响。在3轴联动控制中,投影到偏置平面上的刀具轨迹才得到偏置补偿。
(4).刀补的建立与刀补的取消
刀补的建立是进入切削加工前的一个辅助程序段,刀补的取消是加工完成时要写入到程
序中的辅助程序段,如果处理得好则有利于简捷快速而又安全地使刀具进入切入位置和加工完了时退出刀具。刀补建立时的核心问题是刀具从何处下刀并进入到工件加工的起始位置,刀补取消时则主要应考虑刀具沿何方向退离工件。系统操作说明书中讨论了各种可能遇到的情况,为简化叙述,下面仅根据习惯的编程方法讨论刀补建立与刀补取消的问题。不使用这些方法一般也可以正确地完成刀补建立与刀补取消的过程,但特殊情况下可能出现过切或报警。
1)使用GOO或G01的运动方式均可完成刀补建立或取消的过程,事实上使用G01往往是出于安全的考虑。而如果不把刀补的建立(包括刀补的取消)建立在加工时的Z轴高度上,而采取先建立补偿再下刀或先提刀再取消补偿的方法,则既使在GOO的方式下建立(或取消)刀补也是安全的。
2)为了便于计算坐标,可以按图5-18所示两种方式来建立刀补,图5-18a为切线进入方式,图5-18b为法线进入方式。同样取消刀补通常也采用这种切线或法线的方式。
图5-18 两种刀补建立方式图5-19 内圆轮廓的补偿
3)在不便于直接沿着工件的轮廓线切向切入和切向切出时,可再增加一个圆弧辅助程序段。如图5-19所示的内圆轮廓形状,采用铣圆法加工。编程时根据孔加工的余量大小及刀具尺寸等情况,取一个适当大小的圆弧,设半径为r,并由此求出圆心点A的坐标和圆弧上B、C、E点的坐标。加工时先让刀具定位到大圆的圆心并下刀至孔深。若孔加工的编程轨迹为O→A →B→C→0→C→E→A→O,并于A--B段建立刀补,A--E段取消刀补,则实际加工的刀心运动轨迹为O→A→B′→C′→D′→C′→E′→A→O,这样就能十分方便地实现切向切入与切向切出,使加工时不致于在内孔的C点处产生明显的刀痕。实际处理时,∠BAC与∠EAC的值也可根据需要取30°、45°或60°,以减少空刀时间,但计算略繁。
对于外形轮廓的加工,若采用直线段实现切向切入与切向切出有困难时,也可以采用这种增加辅助圆弧程序段的办法。
(5).执行C型刀补过程中的刀心运动轨迹
为了能对刀补执行过程中,编程轨迹与刀心运动轨迹的关系有一个初步的了解,图5-20示出了几种用G42编程时典型的C型刀补编程轨迹与刀心运动轨迹之间的关系,图a为α≥180°由直线段到直线段在拐角处的转接情况,刀具沿内侧运动至S点转到后一段加工,在拐角处不产生过切;图b为90°≤α≤180°由直线段到圆弧段的转接情况;图C为1°≤α≤90°时由圆弧段到直线段在拐角处的转接情况。由图不难看出C型刀补在拐角处一律采用直线转接的型式,通过伸长直线段或增加直线段的方法实现转接,这就避免了B型刀补采用圆弧转接带来的不足。如使用G41时则刀具中心轨迹在编程轨迹的左侧,处理方法与上述一致。
图5-20 C型刀补过程的刀心运动轨迹
(6).使用刀具半径补偿注意事项
1) G41、G42、G40不能和G02、G03在一起程序段中使用,只能与GOO或G01一起使用,且刀具必须要移动。
2)在程序中用G42指令建立右刀补,铣削时对于工件将产生逆铣效果,故常用于粗铣;
用G41指令建立左刀补,铣削时对于工件将产生顺铣效果,故常用于精铣。
3)一般情况下,刀具半径补偿量应为正值,如果补偿值为负,则G41和G42正好相互替换。通常在模具加工中利用这一特点,可用同一程序加工同一公称尺寸的内外两个型面。
4)在补偿状态下,铣刀的直线移动量及铣削内侧圆弧的半径值要大于或等于刀具半径,否则补偿时会产生干涉,系统在执行相应程序段时将会产生报告,并停止执行。
5)若程序中建立了半径补偿,在加工完成后必须用G40指令将补偿状态取消,使铣刀的中心点回复到实际的坐标点上。亦即执行G40指令时,系统会将向左或向右的补偿值,往相反的方向释放,这时铣刀会移动一铣刀半径值。所以使用G40指令时最好是铣刀已远离工件。
(7).刀具半径补偿的应用
①编程时直接按工件轮廓尺寸编程。刀具在因磨损、重磨或更换后直径会发生改变,但不必修改程序,只需改变半径补偿参数。
②刀具半径补偿值不一定等于刀具半径值,同一加工程序,采用同一刀具可通过修改刀补的办法实现对工件轮廓的粗、精加工;同时也可通过修改半径补偿值获得所需要的尺寸精度。
【例5-3】:如图5-21为建立和取消刀具半径补偿示例。
程序如下:
G17 G90 G54 GOO XO Y0 S400; (→O)
G41 GOO X30.0 Y15.0 D01 M03; (O→P1,建立左刀补)
G01 Y50.0 F150; (P1→P2)
X65.O;(P2→P3)
Y25.0;(P3→P4)
X20.0;(P4→P5)
G40 G00 XO YO M05;(P5→P6,撤销刀补)
图5-21 刀具半径补偿示例图5-22 刀具走刀路线图
【例5-4】:如图5-22所示,试编制加工程序,已知立铣刀为Φ16mm,半径补偿号为D01 01000;(程序号)
G17 G90 G54 GOO X0 Y0 S500; (②)
Z5.0 M03; (③)
G41 G00 X60.0 Y30.0 D01; (④O→A)
G01 Z-27.0 F2000; (⑤)
Y80.0 F120; (⑥A→B)
G03 X100.0 Y120.0 R40.0; (⑦B→C)
G01 X180.0; (⑧C→D)
Y60,0; (⑨D→E)
G02 X160.0Y40.0R20,0; (⑩E→F)
G01 XS0.0; (11F→G)
GOO Z5.0; (12)
G40 XOYO M05; (G→O)
G91 G28 Z0; (Z轴回参考点)
M30; (程序结束)
5.4.2 刀具长度补偿G43、G44、G49
刀具长度补偿是用来补偿假定的刀具长度与实际的刀具长度之间的差值,系统规定除Z 轴之外,其他轴也可以使用刀具长度补偿,但同时规定长度补偿只能同时加在一个轴上,要对补偿轴进行切换,必须先取消对前面轴的补偿。
1.指令格式:
G43α___H___;(α指X、Y、Z任意一轴),刀具长度补偿“+”。
G44α___H___;刀具长度补偿“-”。
G49或H00:取消刀具长度补偿。
以上指令中用G43、G44指令偏移的方向,用H指令偏置量存储器的偏置号。执行程序前,需在与地址H所对应的偏置量存储器中,存入相应的偏置值。以z轴补偿为例,若指令 GOO G43 Z100.0 H01;并于H01中存入“-200.0”,则执行该指令时,将用Z坐标值100.与H01中所存“-200.”进行“+”运算,即100.0+(-200.0)=-100,并将所求结果作为Z轴移动值,取消长度补偿用G49或H00。若指令中忽略了坐标轴,则隐含为Z轴且为Z0。
2.刀具自参考点下刀时的补偿问题
一般情况下加工中心机床总是从参考点换刀的.对于立式加工中心而言,在使用G54~G59工件坐标系时,若仅于X、Y方向偏置G54坐标原点位置而Z轴方向不偏置,则Z轴方向上刀具刀位点与工件坐标系中Z=0平面之间的差值可以全部由刀具长度补偿加以解决,这是操作者在设置偏置值时一种常用的方法。此时G54的Z0平面与机床坐标系的Z0平面是一致的,即G54的20平面通过z轴方向机床参考点。编程人员在编写程序时全然不管操作者是怎样设置补偿值的,仍将G54的Z0平面规定在工件某一高度的位置上,操作人员不作z轴方向上的工件零点偏置的操作,而是将全部差值(包括z轴工件零点偏置值与装刀后主轴前端面到刀具刀位点的距离)让长度补偿功能一并加以解决。
以图5-23为例说明。设编程时编程员希望刀具自参考点下刀到工件坐标系中Z40.的位置,则程序段可以写成G90 GOO G43 Z40. H01;操作人员在安装刀具和工件后,直接测量主轴自参考点下移时刀位点到(补偿面)20平面的距离,若实测刀位点自Z轴参考点出发到达程序中G92 Z0平面位移为-320,直接将该值存于H01存储器中,执行该程序段时,刀具按
40.+(-320.)=-280.即按Z=-280.下刀与预期的下刀点完全一致。
图5-23 G43、G44、G49的应用
这种程序编写的一般形式为:
G90 G49 G54 GOO X___Y___;
G43 H___Z___M03 S___;
……
G90 G49 G28 Z0. T01 M06
……
我们可以采用工件零点偏置值与刀具长度补偿值分别测量输入的方法。将图中①所示的长度值(负值),作为工件零点偏置值存入工件零点偏置存储器中,而将图中②所示的长度值(正值)作为刀具长度补偿值存入H01存储器中,其效果是完全一样的。如果采用机外预调刀具对刀,则后一种方法可能更为方便。
【例5-5】:在立式加工中心上铣削如图5-24所示的工件上表面和外轮廓,分别用Φ25mm 面铣刀和Φ20mm立铣刀,走刀路线和切削用量如图5-25和5-26所示,在配置FANUC OM系统的立式加工中心上加工。试编制加工程序。
建立如图所示工件坐标系,编制加工程序如下:
图5-24 工件简图图5-25 XY平面走刀路径
图5-26 Z轴方向刀具走刀路线
01000; (程序号)
N100; (程序初始设定)
G17 G90 G40 G49 G21; (G代码初始设定)
G91 G28 Z0; (Z轴回参考点)
T01;(选择T01号刀)
M06;(主轴换上最初使用的T01号刀) N101(PACE MILL);(铣顶面程序)
T02; (选择T02号刀)
G90 G54 GOO X70.0 Y-45.0 S230; (①)
G43 Z5.0 H01 M03; (②)
G01 Z0 F2000; (③)
X-310.0 F275 (④)
GOO Y-135.0; (⑤)
C01 X70.0; (⑥)
GOO Z5.0 M05; (⑦)
G91 G28 Z0; (⑧)
G90 X150.0 Y200.0; (⑨)
G49; (取消长度补偿)
M06; (换T02号刀)
N102(END MILL) (铣轮廓程序)
T01; (选择T01号刀)
G90 G54 COOX20.0 Y20.0 S400; (⑩)
G43 Z5.01 H02 M03; (11)
Z-32.0 F2000 M08; (12)
G41 G01 XO Y1O.0 D22 F180; (13)
Y-120.0; (14)
X-120.0 Y-180.0; (15)
X-240.0; (16)
Y-90.O; (17)
G02 X150.0 Y0 R90.0; (18)
G01 X10.0; (19)
GOO Z5.0 M09; (20)
G40X20.0Y20.0M05; (21)
G91 G28 Z0; (22)
G90 X150.0 Y200.0; (23)
G49; (取消长度补偿)
M30; (程序结束)
5.4.3 刀具位置偏置(G45、G46、G47、G48)
指令格式:G45/G46/G47/G48 X___/Y___D___F___
刀具位置偏置是为了加工出规定的长度而设置的,如图5-27所示,共有四种指令,该指令是非模态代码:
G45___沿刀具运动方向上增加一个偏移量e(见图5-27a)。
C46___沿刀具运动方向上减少一个偏移量e(见图5-27b)。
G47___沿刀具运动方向上增加两倍偏移量e(见图5-27c)。
G48___沿刀具运动方向上减少两倍偏移量e(见图5-27d)。
图5-27 刀具位置补偿偏置
【例5-6】:加工如图5-28所示,使用立铣刀铣削工件侧面,工件轮廓形状如图中实线所示,立铣刀直径20m,补偿值为10mm,将此值存入D01中。
图5-28 G45~G48应用实例
加工程序如下:
N01 G91 G46 GOO X40 Y34 D01; (增量值编程,缩短1倍补偿值)
N02 G47 G01 X58 F120; (延长2倍补偿值)
N03 Y15;
N04 G48 X46;(缩短2倍补偿值)
N05 Y-15;
N06 G47 X35; (延长2倍补偿值)
N07 Y34; (延长1倍补偿值)
N08 m3 X-22 Y22 1-22; (延长1倍补偿值)
N09 G45 G01 X-105; (延长1倍补偿值)
N10 Y-10;
N11 G46 G02 X-22 Y-22 I-22;(缩短1倍补偿值) N12 G01 X-10;
N13 G47 Y-34; (延长2倍补偿值) N14 GOO G46 X-40 Y-34; (缩短1倍补偿值) N15 M02;
数控铣床与加工中心刀具补偿讲解
数控铣床与加工中心刀具补偿讲解
数控铣床与加工中心 5.4 刀具补偿和偏置功能 刀具补偿可分为刀具长度补偿和刀具半径补偿,其内容和方法已在前面章节中作了详细说明,本章拟用另外一种指令格式对刀具长度补偿功能进行介绍,目的在于进一步强调不同的数控系统对同一编程功能可能采用不同的指令格式。 5.4.1 刀具半径补偿G41、G42、G40 刀具半径补偿有两种补偿方式,分别称为B 型刀补和C型刀补。B型刀补在工件轮廓的拐角处用圆弧过渡,这样在外拐角处,由于补偿过程中刀具切削刃始终与工件尖角接触,使工件上尖角变钝,在内拐角处会则引起过切。C型刀补采用了比较复杂的刀偏矢量计算的数学模型,彻底消除了B型刀补存在的不足。下面仅讨论C型刀补。 (1).指令格式 指令格式: G17/G18/G19 G00/G01 G41/G42 G41:刀具半径左补偿
G42:刀具半径右补偿 半径补偿仅能在规定的坐标平面内进行,使用平面选择指令G17、G18或G19可分别选择XY、ZX或YZ平面为补偿平面。半径补偿必须规定补偿号,由补偿号L存入刀具半径值,则在执行上述指令时,刀具可自动左偏(G41)或右偏(G42)一个刀具半径补偿值。由于刀补的建立必须在包含运动的程序段中完成,因此以上格式中,也写入了GOO(或GO1)。在程序结束前应取消补偿。具体的判断方法见本书第二章。 (2).刀补过程 刀具补偿包括刀补建立,刀补执行和刀补取消这样三个阶段,其中刀补建立与刀补取消均应在非切削状态下进行。程序中含有G41或G42的程序段是建立刀补的程序段,含有G40的程序段是取消刀补的程序段,在执行刀补期间刀具始终处于偏置状态。为了在建立刀补和取消刀补时,避免发生过切或撞刀,以及在刀补执行期间掌握刀具在运动段的拐角处的运动情况,有必要对刀补过程作一简要说明。 (3).刀具偏置矢量 刀具偏置矢量是二维矢量,其大小等于D代
加工中心对刀与刀具补偿操作教程
加工中心对刀与刀具补偿操作教程 时间:2012-05-30 作者:模具联盟网点击: 1479 评论:0 字体:T|T 一、对刀 对刀方法与具体操作同数控铣床。 二、刀具长度补偿设置 加工中心上使用的刀具很多,每把刀具的长度和到 Z 坐标零点的距离都不相同,这些距离的差值就是刀具的长度补偿值,在加工时要分别进行设置,并记录在刀具明细表中,以供机床操作人员使用。一般有两种方法: 1、机内设置 这种方法不用事先测量每把刀具的长度,而是将所有刀具放入刀库中后,采用 Z 向设定器依次确定每把刀具在机床坐标系中的位置,具体设定方法又分两种。 ( 1 )第一种方法将其中的一把刀具作为标准刀具,找出其它刀具与标准刀具的差值,作为长度补偿值。具体操作步骤如下: ①将所有刀具放入刀库,利用 Z 向设定器确定每把刀具到工件坐标系 Z 向零点的距离,如图 5-2 所示的 A 、 B 、 C ,并记录下来; ②选择其中一把最长(或最短)、与工件距离最小(或最大)的刀具作为基准刀,如图 5-2 中的 T03 (或 T01 ),将其对刀值 C (或 A )作为工件坐标系的 Z 值,此时 H03=0 ; ③确定其它刀具相对基准刀的长度补偿值,即 H01= ±│ C-A │, H02= ±│ C-B │,正负号由程序中的 G43 或 G44 来确定。 ④将获得的刀具长度补偿值对应刀具和刀具号输入到机床中。 ( 2 )第二种方法将工件坐标系的 Z 值输为 0 ,调出刀库中的每把刀具,通过 Z 向设定器确定每把刀具到工件坐标系 Z 向零点的距离,直接将每把刀具到工件零点的距离值输到对应的长度补偿值代码中。正负号由程序中的 G43 或 G44 来确定。 2、机外刀具预调结合机上对刀 这种方法是先在机床外利用刀具预调仪精确测量每把在刀柄上装夹好的刀具的轴向和径向尺寸,确定每把刀具的长度补偿值,然后在机床上用其中最长或最短的一把刀具进行 Z 向对刀,确定工件坐标系。这种方法对刀精度和效率高,便于工艺文件的编写及生产组织。 三、刀具半径补偿设置 进入刀具补偿值的设定页面,移动光标至输入值的位置,根据编程指定的刀具,键入刀具半径补偿值,按 INPUT 键完成刀具半径补偿值的设定。 一、对刀 对刀方法与具体操作同数控铣床。 二、刀具长度补偿设置 加工中心上使用的刀具很多,每把刀具的长度和到 Z 坐标零点的距离都不相同,这些距离的差值就是刀具的长度补偿值,在加工时要分别进行设置,并记录在刀具明细表中,以供机床操
数控铣床与加工中心刀具补偿讲解
数控铣床与加工中心 5.4 刀具补偿和偏置功能 刀具补偿可分为刀具长度补偿和刀具半径补偿,其内容和方法已在前面章节中作了详细说明,本章拟用另外一种指令格式对刀具长度补偿功能进行介绍,目的在于进一步强调不同的数控系统对同一编程功能可能采用不同的指令格式。 5.4.1 刀具半径补偿G41、G42、G40 刀具半径补偿有两种补偿方式,分别称为B型刀补和C型刀补。B型刀补在工件轮廓的拐角处用圆弧过渡,这样在外拐角处,由于补偿过程中刀具切削刃始终与工件尖角接触,使工件上尖角变钝,在内拐角处会则引起过切。C型刀补采用了比较复杂的刀偏矢量计算的数学模型,彻底消除了B型刀补存在的不足。下面仅讨论C型刀补。 (1).指令格式 指令格式: G17/G18/G19 G00/G01 G41/G42 G41:刀具半径左补偿 G42:刀具半径右补偿 半径补偿仅能在规定的坐标平面内进行,使用平面选择指令G17、G18或G19可分别选择XY、ZX或YZ平面为补偿平面。半径补偿必须规定补偿号,由补偿号L存入刀具半径值,则在执行上述指令时,刀具可自动左偏(G41)或右偏(G42)一个刀具半径补偿值。由于刀补的建立必须在包含运动的程序段中完成,因此以上格式中,也写入了GOO(或GO1)。在程序结束前应取消补偿。具体的判断方法见本书第二章。 (2).刀补过程 刀具补偿包括刀补建立,刀补执行和刀补取消这样三个阶段,其中刀补建立与刀补取消均应在非切削状态下进行。程序中含有G41或G42的程序段是建立刀补的程序段,含有G40的程序段是取消刀补的程序段,在执行刀补期间刀具始终处于偏置状态。为了在建立刀补和取消刀补时,避免发生过切或撞刀,以及在刀补执行期间掌握刀具在运动段的拐角处的运动情况,有必要对刀补过程作一简要说明。 (3).刀具偏置矢量 刀具偏置矢量是二维矢量,其大小等于D代码所规定的偏置量,矢量方向的计算是依照各轴刀具进给情况而于控制单元内自动完成的。通过该偏置矢量计算出刀具中心偏离编程轨迹的实际轨迹。偏置计算在由G17、G18和G19确定的平面内进行,该平面称之为偏置平面。 例如在已经选择了XY平面时,仅对程序中(X、Y)或(1、J)计算偏置量,并计算偏置矢量。不在偏置平面内的轴的坐标值不受偏置的影响。在3轴联动控制中,投影到偏置平面上的刀具轨迹才得到偏置补偿。 (4).刀补的建立与刀补的取消 刀补的建立是进入切削加工前的一个辅助程序段,刀补的取消是加工完成时要写入到程序中的辅助程序段,如果处理得好则有利于简捷快速而又安全地使刀具进入切入位置和加工完了时退出刀具。刀补建立时的核心问题是刀具从何处下刀并进入到工件加工的起始位置,刀补取消时则主要应考虑刀具沿何方向退离工件。系统操作说明书中讨论了各种可能遇到的情况,为简化叙述,下面仅根据习惯的编程方法讨论刀补建立与刀补取消的问题。不使用这些方法一般也可以正确地完成刀补建立与刀补取消的过程,但特殊情况下可能出现过切或报警。 1)使用GOO或G01的运动方式均可完成刀补建立或取消的过程,事实上使用G01往往是出于安全的考虑。而如果不把刀补的建立(包括刀补的取消)建立在加工时的Z轴高度上,而采取先建立补偿再下刀或先提刀再取消补偿的方法,则既使在GOO的方式下建立(或取消)刀补也是安全的。
数控铣削刀具半径如何进行补偿
数控铣削刀具半径如何进行补偿 内容来源网络,由“深圳机械展(11万㎡,1100多家展商,超10万观众)”收集整理!更多cnc加工中心、车铣磨钻床、线切割、数控刀具工具、工业机器人、非标自动化、数字化无人工厂、精密测量、3D打印、激光切割、钣金冲压折弯、精密零件加工等展示,就在深圳机械展. 随着现在数控机床加工技术的发展,编程人员根据历年图纸上的轮廓尺寸进行编程,如果刀具中心沿着零件的被加工轮廓做运动,则在加工结束之后零件尺寸无法达到理想尺寸,这样就会出现编程轮廓与实际轮廓不一致的情况。本文就来具体介绍一下数控铣削刀具的半径如何进行补偿。 一般行业中,解决这个问题的方法是通过建立刀具半径补偿,编程人员只需按照零件图纸上的尺寸进行编程,就可以保证加工出加工图纸要求的理想尺寸。 刀具半径补偿功能应用的技巧 1、圆孔的加工 对于一般的圆孔来说,在数控铣床上可以通过一把离铣刀来完成,工艺及编程的分析如下。
(1)刀具的选择:对于此类的圆孔,工件材料若为 45 钢调质处理,可选一把硬质合金立铣刀。 (2)由于数控铣床良好的机械性能,一般优先采用顺铣。可以用“少吃走快”的方法,省去大部分的辅助工作时间。 (3)编程路径的确定。注意一定要采用圆弧过度的切向切入和切出法,过度圆弧的半径必须大于刀具的半径,且小于圆孔的半径,否则,刀具路径就不是理想的样子。 (4)粗精加工的安排和程序处理。精加工只需调用一次子程序,一次下刀到孔底,走刀量减小 5 倍,刀补值设定为理论值,其他不变,即可完成精加工。 2、内外壁的加工 要在一个平面上铣出一条封闭的沟槽,槽宽有精度要求。在数控铣床上也可用一把立铣刀完成。通过图形和工艺分析,加工思路也应该是“少吃走快”。现在关键的问题是图素较复杂,各节点计算难度大。我们需按尺寸标注,计算出内外壁各点坐标值,确定下刀点,按轨迹建立刀补编写一个程序。采用此方法加工内外壁的特点就是只需编写一个程序,通过不断修改刀补值来完成内外壁的粗精加工。
数控车床的刀尖圆弧半径教案例
《数控车床刀尖圆弧半径加工带圆弧锥轴类零件》教学案例一、教学背景 刀尖圆弧半径是影响零件的加工精度因素之一,本课题通过带圆锥轴类零件的加工,让学生掌握刀具刀尖圆弧半径补偿的基本原理及基本操作,以保证加工零件的加工精度。 本课题完成课时为4学时,学生人数为40人,分4人/组,每组完成一个工件。 教学目标:通过本课题的学习使学生掌握刀尖圆弧半径的补偿原理和方法,及补偿参数的设置,提高零件的加工精度。 时间资源:课前,课后和课内的设计和安排 材料资源:45#材料 信息资源:网络技术,多媒体技术,工具书,手册 人员资源:双师型工作团队。1位专业教师2位培训师。学生小组和组长。 设备资源:FANUC系统数控车床2—3人,台;外圆粗、精车刀、螺纹车刀、切槽刀每台机床各1把;刀架扳手、卡盘扳手、划线盘、角度样板每台机床1付,垫铁若干;游标卡尺、千分尺、螺纹环规、粗糙度样板每台机床各1把。 环境资源:数控实训车间、数控仿真机房 二、课程的实施 (一)复习导入新课 老师:同学们,见过外圆车刀吗?在哪见过? 学生:见过,在普车实习时,就见过,而且也用过 老师:不错,学过的知识没忘记。车刀的刀尖是尖吗? 学生:是,但不是绝对尖。 老师:答得好。请看下图,a图是理论刀尖,b图是实际刀尖。这就是我们今天要讲的新课知识,刀尖圆弧半径补偿。 (a) (b) 图1 圆头刀假想刀尖 (二)提出问题,探究新课 老师:看图回答问题。请大家思考,下图是用一假设带了刀尖的圆头刀在数控车床上加工的路径,两种刀具切削会带来什么影响?刀尖圆弧半径对加工零件的精度有影响吗?
学生:车圆锥面有影响 老师:答得好,观察能力强。那么有何影响? 学生:在切圆柱面时无影响;切圆锥面时,圆头刀切得浅一些,有尖定的切得深一些。 老师:分析得非常正确。请同学们看下图讨论的刀尖圆弧半径在数控加工中的影响。 学生:刀尖圆弧半径对圆柱没影响,对圆锥和圆弧有影响并产生了误差。 老师:很对。因为编制数控车床加工程序时,理论上是将车刀刀尖看成一个点,如图1a所示的P点就是理论刀尖。但为了提高刀具的使用寿命和降低加工工件的表面粗糙度,通常将刀尖磨成半径不大的圆弧(一般圆弧半径R是0.4—1.6之间),如图1b所示X向和Z向的交点P称为假想刀尖,该点是编程时确定加工轨迹的点,数控系统控制该点的运动轨迹。然而实际切削时起作用的切削刃是圆弧的切点A、B,它们是实际切削加工时形成工件表面的点。很显然假想刀尖点P与实际切削点A、B是不同点,所以如果在数控加工或数控编程时不对刀尖圆角半径进行补偿,仅按照工件轮廓进行编制的程序来加工,势必会产生加工误差。 如果不进行刀尖圆弧半径补偿,在加工过程中,会产生什么现象呢?(请看下图) 学生:图的右边产生了少切,左边产生的过切。 老师:答得非常好,棒极了。这就是在数控加工中产生的过切和少切现象。在编程过程中如何实现刀具圆弧半径补偿,这是这次课的重点内容。 (三)知识学习 1.在实际加工过程中可以使用刀尖圆弧是0吗?这样做的目的是激发学生的求知欲,可以适
数控机床刀具补偿功能
刀具补偿功能 (实际生产步骤) 在数控编程过程中,一般不考虑刀具的长度与刀尖圆弧半径,而只考虑刀位点与编程轨迹重合。但在实际加工过程中,由于刀尖圆弧半径与刀具长度各不相同,在加工中会产生很大的误差。因此,实际加工时必须通过刀具补偿指令,使数控机床根据实际使用的刀具尺寸,自动调节各坐标轴的移动量,确保实际加工轮廓和编程轨迹完全一致。数控机床根据刀具实际尺寸,自动改变机床坐标轴或刀具刀位点位置,使实际加工轮廓和编程轨迹完全一致的功能,称为刀具补偿功能。1.刀具半径补偿:(G40,G41,G42) G40:取消半径刀补 G41:刀具左补偿(沿着刀具前进的方向看,刀具在工件的左边) G42:刀具右补偿(·································右边) 数控机床加工时以刀具中心轴的坐标进行 走刀,依据G41或G42使刀具中心在原来 的编程轨迹的基础上伸长或缩短一个刀具 半径值,即刀具中心从与编程轨迹重合过 渡到与编程轨迹偏离一个刀具半径值,如图 刀具补偿指令是模态指令,一旦刀具补偿建立后一直有效,直至刀具补偿撤销。在刀具补偿进行期间,刀具中心轨迹始终偏离编程轨迹一个刀具半径值的距离。 刀具半径补偿仅在指定的2D 坐标平面内进行。而平面由G 指令代码
G17( xy平面)、G18( zx平面)、G19( yz平面)确定。刀具半径值则由刀具号H(D)确定 2.刀具长度补偿 所谓刀具长度补偿,就是把工件轮廓按刀具长度在坐标轴(车床为x、z轴)上的补偿分量平移。对于每一把刀具来说,其长度是一定的,它们在某种刀具夹座上的安装位置也是一定的。因此在加工前可预先分别测得装在刀架上的刀具长度在x和z方向的分量,即Δx刀偏和Δz 刀偏。通过数控装置的手动数据输入工作方式将Δx和Δz 输入到CNC 装置,从CNC 装置的刀具补偿表中调出刀偏值进行计算。数控车床需对x轴、z轴进行刀具长度补偿计算,数控铣床只需对z轴进行刀具长度补偿计算。
数控铣床与加工中心刀具补偿讲解
数控铣床与加工中心刀 具补偿讲解 IMB standardization office【IMB 5AB- IMBK 08- IMB 2C】
数控铣床与加工中心 刀具补偿和偏置功能 刀具补偿可分为刀具长度补偿和刀具半径补偿,其内容和方法已在前面章节中作了详细说明,本章拟用另外一种指令格式对刀具长度补偿功能进行介绍,目的在于进一步强调不同的数控系统对同一编程功能可能采用不同的指令格式。 5.4.1刀具半径补偿G41、G42、G40 刀具半径补偿有两种补偿方式,分别称为B型刀补和C型刀补。B型刀补在工件轮廓的拐角处用圆弧过渡,这样在外拐角处,由于补偿过程中刀具切削刃始终与工件尖角接触,使工件上尖角变钝,在内拐角处会则引起过切。C型刀补采用了比较复杂的刀偏矢量计算的数学模型,彻底消除了B型刀补存在的不足。下面仅讨论C型刀补。 (1).指令格式 指令格式: G17/G18/G19 G00/G01 G41/G42 G41:刀具半径左补偿 G42:刀具半径右补偿 半径补偿仅能在规定的坐标平面内进行,使用平面选择指令G17、G18或G19可分别选择XY、ZX或YZ平面为补偿平面。半径补偿必须规定补偿号,由补偿号L存入刀具半径值,则在执行上述指令时,刀具可自动左偏(G41)或右偏(G42)一个刀具半径补偿值。由于刀补的建立必须在包含运动的程序段中完成,因此以上格式中,也写入了GOO(或GO1)。在程序结束前应取消补偿。具体的判断方法见本书第二章。
(2).刀补过程 刀具补偿包括刀补建立,刀补执行和刀补取消这样三个阶段,其中刀补建立与刀补取消均应在非切削状态下进行。程序中含有G41或G42的程序段是建立刀补的程序段,含有G40的程序段是取消刀补的程序段,在执行刀补期间刀具始终处于偏置状态。为了在建立刀补和取消刀补时,避免发生过切或撞刀,以及在刀补执行期间掌握刀具在运动段的拐角处的运动情况,有必要对刀补过程作一简要说明。 (3).刀具偏置矢量 刀具偏置矢量是二维矢量,其大小等于D代码所规定的偏置量,矢量方向的计算是依照各轴刀具进给情况而于控制单元内自动完成的。通过该偏置矢量计算出刀具中心偏离编程轨迹的实际轨迹。偏置计算在由G17、G18和G19确定的平面内进行,该平面称之为偏置平面。 例如在已经选择了XY平面时,仅对程序中(X、Y)或(1、J)计算偏置量,并计算偏置矢量。不在偏置平面内的轴的坐标值不受偏置的影响。在3轴联动控制中,投影到偏置平面上的刀具轨迹才得到偏置补偿。 (4).刀补的建立与刀补的取消 刀补的建立是进入切削加工前的一个辅助程序段,刀补的取消是加工完成时要写入到程序中的辅助程序段,如果处理得好则有利于简捷快速而又安全地使刀具进入切入位置和加工完了时退出刀具。刀补建立时的核心问题是刀具从何处下刀并进入到工件加工的起始位置,刀补取消时则主要应考虑刀具沿何方向退离工件。系统操作说明书中讨论了各种可能遇到的情况,为简化叙述,下面仅根据习惯的编程方法讨论刀补建立与刀补取消的问题。不使用这些方法一般也可以正确地完成刀补建立与刀补取消的过程,但特殊情况下可能出现过切或报警。
刀具半径补偿指令G40、G41、G42,
刀具半径补偿指令G40、G41、G42, 1、刀具半径补偿的目的: 在编制轮廓铣削加工的场合,如果按照刀具中心轨迹进行编程,其数据计算有时相当复杂,尤其是当刀具磨损、重磨、换新刀具而导至刀具半径变化时,必须重新计算刀具中心轨迹,修改程序,这样不既麻烦而且容易出错,又很难保证加工精度,为提高编程效率,通常以工件的实际轮廓尺寸为刀具轨迹编程,即假设计刀具中心运动轨迹是沿工件轮廓运动的,而实际的刀具运动轨迹要与工件轮廓有一个偏移量(即刀具半径),利用刀具半径补偿功能可以方便地实现这一转变,简化程序编制,机床可以自动判断补偿的方向和补偿值大小,自动计算出实际刀具中心轨迹,并按刀心轨迹运动。 现代数控系统一般都设置若干个可编程刀具半径偏置寄存器,并对其进行编号,专供刀具补偿之用,可将刀具补偿参数(刀具长度、刀具半径等)存入这些寄存器中。在进行数控编程时,只需调用所需刀具半径补偿参数所对应的寄存器编号即可。实际加工时,数控系统将该编号所对应的刀具半径取出,对刀具中心轨迹进行补偿计算,生成实际的刀具中心运动轨迹。 2、刀具半径补偿的方法 (1)刀具半径指令从操作面板输入被补偿刀具的直径或(半径)值,将其存在刀具参数库里,在程序中采用半径补偿指令。刀具半径补偿的代码有G40、G41、G42,它们都是模态代码,G40是取消刀具半径补偿代码,机床的初始状态就是为G40。G41为刀具半径左补偿,(左刀补),G42为刀具半径右补偿(右刀补)。判断左刀具补偿和右刀具补偿的方法是沿着刀具加工路线看,当刀具偏在加工轮廓的左侧时,为左偏补偿,当刀具偏在加工轮廓的右侧时,为右偏补偿,如图1所示。 图1a中,在相对于刀具前进方向的左侧进行补偿,采用G41,这时相当于顺铣。图1b 中在相对于刀具前进方向的右侧进行补偿,采用G42,这时相当于逆铣。在数控机床加工中,一般采用顺铣,原因是从刀具寿命、加工精度、表面粗糙度而言顺铣的效果比较好,因而G41使用的比较多。 G17 XY (2)指令格式刀具半径补偿的格式:{G18 } {G00、G01}{G41、G42} ZX D G19 YZ XY 刀具半径补偿取消的格式:(G00、G01)G40{ ZX} YZ
刀具长度补偿
Bewise Inc. https://www.360docs.net/doc/8014575652.html, Reference source from the internet. 刀具长度补偿功能,是数控机床的一项重要功能,在准备功能中用G43、G44、G49表示,但是若使用得不好很容易造成撞车和废品事故。下面以加工中心为例,介绍生产实践中常用的几种刀具长度补偿方法。 1 刀具长度补偿功能的执行过程 典型的指令格式为G43 Z_H_;或G44 Z_H_。其中G43指令加补偿值,也叫正向补偿,即把编程的Z值加上H代码指定的偏值寄存器中预设的数值后作为CNC实际执行的Z坐标移动值。相应的,G44指令减去预设的补偿值,也叫负向补偿。 当指令G43时,实际执行的Z坐标值为Z’=Z_+(H_); 当指令G44时,实际执行的Z坐标值为Z’=Z_-(H_); 这个运算不受G90绝对值指令或G91增量值指令状态的影响。偏值寄存器中可预设正值或负值,因此有如下等同情况。 指令G43、H设正值等同于指令G44、H设负值的效果: 指令G43、H设负值等同于指令G44、H设正值的效果。 因此一般情况下,为避免指令输入或使用时失误,可根据操作者习惯采用两种方式: 只用指令G43,H设正值或负值: H只设正值,用指令G43或G44。 以下介绍使用较多的第一种情况。 指令格式中Z值可以为0,但H0或H00将取消刀具长度补偿,与G49效果等同,因为0号偏值寄存器被NC永远置0。 一般情况下,为避免失误,通过设定参数使刀具长度补偿只对Z轴有效。例如当前指令为G43X_H_;时,X轴的移动并没有被补偿。 被补偿的偏置值由H后面的代码指定。例如H1设20.、H2设-30.,当指令“G43 Z100.H1;”时,Z轴将移动至120.处:而当指令“G43 Z100. H2;”时,Z轴将移动至70.处。 G43(G44)与G00、G01出现在一个程序段时,NC将首先执行G43(G44)。 可以在固定循环的程序段中指令G43(G44),这时只能指令一个H代码,刀具长度补偿同时对Z值和R值有效。
数控加工中心刀具长度补偿的研究
加工中心刀具补偿的研究摘要:数控加工中心加工一个零件往往需要数把刀,为了简化编程,CNC系统采用刀具长度补偿可使在备制零件的加工程序时,不必考虑刀具的实际长度.阐述了刀具长度补偿的原理,研究了数控系统使用长度补偿旨令G43(G44)和H完成长度补偿功能,提出了刀具运行的实际位呈与编程中指令位置的计算方法.论述了刀具民数在CNC 系统中的存分配,分析了刀具长度补偿的方式、特点及CNC系统中刀具长度补偿功能与其他指令的关系.结果表明:使用刀具长度补偿功能提高了加工效率。 加工中心是一种综合加工能力较强的设备,加工中心设置有刀库和自动换刀装置,在加工过程中由程序自动选刀和换刀,由于加工中心常用来加工形状复杂、工序多、精度要求较高、需用多种类型的普通机床和众多刀具、夹具且经多次装夹和调整才能完工的零件,因而加工一个零件需用十几把刀具甚至更多,由于每把刀具的长度都是不同的,在对被加工零件设置工件坐标系零点(一般为工件的卜表面)后,如果更换的刀具比编程时的标准刀具稍长则将使零件产生过切的现象Ul,反之使零件产生欠切的现象. 利用数控系统的刀具长度补偿功能,可以解决上述问题. 刀具长度补偿指令一般用于刀具轴向(Z向)的补偿,它使刀具在Z方向上的实际位移量比程序给定值增加或减少一个偏置值t2],这样在编制零件的加工程序时,不必考虑刀具的实际长度以及各把刀具不同的长度尺寸.另外,当刀具磨损、更换新刀或刀具安装有误差时,也可使用刀具长度补偿指令,以补偿刀具在长度方向上的尺寸变化,而不需要重新编 制加工程序、重新对刀或重新调整刀具.大大简化了编程,减少了工时,提高了效率。 1 CNC系统执行刀具长度补偿功能分析 1.1刀具长度补偿功能的运行分析 刀具长度补偿是通过执行含有G43 ( G44)和H指令来实现,其指令格式为G43Z_H_或G44Z_H_,即把编程的Z坐标值加上(或减去)H_
数控铣床与加工中心刀具补偿讲解
数控铣床与加工中心 刀具补偿和偏置功能 刀具补偿可分为刀具长度补偿和刀具半径补偿,其内容和方法已在前面章节中作了详细说明,本章拟用另外一种指令格式对刀具长度补偿功能进行介绍,目的在于进一步强调不同的数控系统对同一编程功能可能采用不同的指令格式。 5.4.1 刀具半径补偿G41、G42、G40 刀具半径补偿有两种补偿方式,分别称为B型刀补和C型刀补。B型刀补在工件轮廓的拐角处用圆弧过渡,这样在外拐角处,由于补偿过程中刀具切削刃始终与工件尖角接触,使工件上尖角变钝,在内拐角处会则引起过切。C型刀补采用了比较复杂的刀偏矢量计算的数学模型,彻底消除了B型刀补存在的不足。下面仅讨论C型刀补。 (1).指令格式 指令格式: G17/G18/G19 G00/G01 G41/G42 G41:刀具半径左补偿 G42:刀具半径右补偿 半径补偿仅能在规定的坐标平面内进行,使用平面选择指令G17、G18或G19可分别选择XY、ZX或YZ平面为补偿平面。半径补偿必须规定补偿号,由补偿号L存入刀具半径值,则在执行上述指令时,刀具可自动左偏(G41)或右偏(G42)一个刀具半径补偿值。由于刀补的建立必须在包含运动的程序段中
完成,因此以上格式中,也写入了GOO(或GO1)。在程序结束前应取消补偿。具体的判断方法见本书第二章。 (2).刀补过程 刀具补偿包括刀补建立,刀补执行和刀补取消这样三个阶段,其中刀补建立与刀补取消均应在非切削状态下进行。程序中含有G41或G42的程序段是建立刀补的程序段,含有G40的程序段是取消刀补的程序段,在执行刀补期间刀具始终处于偏置状态。为了在建立刀补和取消刀补时,避免发生过切或撞刀,以及在刀补执行期间掌握刀具在运动段的拐角处的运动情况,有必要对刀补过程作一简要说明。 (3).刀具偏置矢量 刀具偏置矢量是二维矢量,其大小等于D代码所规定的偏置量,矢量方向的计算是依照各轴刀具进给情况而于控制单元内自动完成的。通过该偏置矢量计算出刀具中心偏离编程轨迹的实际轨迹。偏置计算在由G17、G18和G19确定的平面内进行,该平面称之为偏置平面。 例如在已经选择了XY平面时,仅对程序中(X、Y)或(1、J)计算偏置量,并计算偏置矢量。不在偏置平面内的轴的坐标值不受偏置的影响。在3轴联动控制中,投影到偏置平面上的刀具轨迹才得到偏置补偿。 (4).刀补的建立与刀补的取消 刀补的建立是进入切削加工前的一个辅助程序段,刀补的取消是加工完成时要写入到程序中的辅助程序段,如果处理得好则有利于简捷快速而又安全地使刀具进入切入位置和加工完了时退出刀具。刀补建立时的核心问题是刀具从何处下刀并进入到工件加工的起始位置,刀补取消时则主要应考虑刀
铣削加工中心刀具半径补偿的应用
铣削加工中心刀具半径补偿的应用 1 前言 1)刀具半径补偿的基本概念 图1 加工中的刀具半径补偿 在轮廓加工过程中,由于刀具总有一定的半径(如铣刀半径或线切割机的钼丝半径等),刀具中心的运动轨迹与所需加工零件的实际轮廓并不重合。如在图1中,粗实线为所需加工的零件轮廓,点划线为刀具中心轨迹。由图可见在进行内轮廓加工时,刀具中心偏离零件的内轮廓表面一个刀具半径值。在进行外轮廓加工时,刀具中心又偏离零件的外轮廓表面一个刀具半径值。这种偏移,称为刀具半径补偿。 2)采用刀具半径补偿的作用和意义 数控机床一般都具备刀具半径补偿的功能。在加工中,使用数控系统的刀具半径补偿功能,就能避开数控编程过程中的繁琐计算,而只需计算出刀具中心轨迹的起始点坐标值就可。同时,利用刀具半径补偿功能,还可以实现同一程序的粗、精加工以及同一程序的阴阳模具加工等功能。 3)刀具半径补偿指令的使用方式 根据ISO 标准规定,当刀具中心轨迹在编程轨迹前进方向的左边时,称为左刀补,用G41表示;刀具中心轨迹在编程轨迹前进方向的右边时,称为右刀补,用G42表示;注销刀具半径补偿时用G40表示。 2 刀具半径补偿过程 1)刀具半径补偿建立:当输入BS缓冲器的程序段包含有G41/G42命令时,系统认为此时已进入刀补建立状态。当以下条件成立时,加工中心以移动坐标轴的形式开始补偿动作。 有G41或G42被指定; 在补偿平面内有轴的移动; 指定了一个补偿号或已经指定一个补偿号但不能是D00; 偏置(补偿)平面被指定或已经被指定; G00或G01模式有效。
2)补偿模式:在刀具补偿进行期间,刀具中心轨迹始终偏离编程轨迹一个刀具半径值的距离。此时半径补偿在G00、G01、G02、G03情况下均有效。 3)取消补偿:使用G40指令消去程序段偏置值,使刀具撤离工件,回到起始位置,从而使刀具中心与偏程轨迹重合。当以下两种情况之一发生时加工中心补偿模式被取消。①给出G40同时要有补偿平面内坐标轴移动。②刀具补偿号为D00。 3 刀具半径补偿在加工中心中的应用 有了刀具半径自动补偿功能,除可免去刀心轨迹的人工计算外,还可利用同一加工程序去完成粗、精加工及阴阳模具加工等。 图2 G18指令的使用 1)不同平面内的半径补偿 刀具半径补偿用G17、G18、G19命令在被选择的工作平面内进行补偿。即当G18命令执行后,刀具半径补偿仅影响X、Z移动,而对Y轴没有作用。 铣削如图2所示圆柱面,使用刀具是半径为10mm的球形立铣刀。编程控制点有两个,即刀尖、球心,这里使用球心。O0001 N1 G9054G18G00X60.0Y0S1000M03; N2 Z0; N3 G91G01 G41X-20.0D01 F100; N4 G02X-80.0I40.0; N5 G40GG0lX20.0; ┇ ┇ N22vG90G00Z100.0; N23vX0 Y0M05; N24 M30; 2)实现同一程序的粗、精加工:刀具半径补偿除方便编程外,还可改变补偿大小的方法以用实现同一程序的粗精加工。 粗加工刀具补偿量=刀具半径+精加工余量,精加工刀具补偿量=刀具半径+修正量 3)实现同一程序的阴阳模具加工
刀具半径补偿的目的与方法
刀具半径补偿的目的与方法 (1)刀具半径补偿的目的 在车床上进行轮廓加工时,因为车刀具有一定的半径,所以刀具中心(刀心)轨迹和工件轮廓不重合。若数控装置不具备刀具半径自动补偿功能,则只能按刀心轨迹进行编程(图(1-11)中点划线),其数值计算有时相当复杂,尤其当刀具磨损、重磨、换新刀等导致刀具直径变化时,必须重新计算刀心轨迹,修改程序,这样既繁琐,又不易保证加工精度。当数控系统具备刀具半径补偿功能时,编程只需按工件轮廓线进行(图(4-10)中粗实线),数控系统会自动计算刀心轨迹坐标,使刀具偏离工件轮廓一个半径值,即进行半径补偿。 图(4-10)刀具半径补偿 a) 外轮廓b)内轮廓 (2)刀具半径补偿的方法 控刀具半径补偿就是将刀具中心轨迹过程交由数控系统执行,编程时假设刀具的半径为零,直接根据零件的轮廓形状进行编程,而实际的刀具半径则存放在一个可编程刀具半径偏置寄存器中,在加工工程中,数控系统根据零件程序和刀具半径自动计算出刀具中心轨迹,完成对零件的加工。当刀具半径发生变化时,不需要修改零件程序,只需修改存放在刀具半径偏置寄存器中的半径值或选用另一个刀具半径偏置寄存器中的刀具半径所对应的刀具即可。 G41指令为刀具半径左补偿(左刀补),G42指令为刀具半径右补偿(右刀补),G40指令为取消刀具半径补偿。这是一组模态指令,缺省为G40。 使用格式: 说明:(1)刀具半径补偿G41、G42判别方法,如图(4-11)所示,规定沿着刀具运动方向看,刀具位于工件轮廓(编程轨迹)左边,则为左刀补(G41),反之,为刀具的右刀补(G42)。
图(4-11)刀具半径补偿判别方法 (2)使用刀具半径补偿时必须选择工作平面(G17、G18、G19),如选用工作平面G17指令,当执行G17指令后,刀具半径补偿仅影响X、Y轴移动,而对Z轴没有作用。 (3)当主轴顺时针旋转时,使用G41指令车削方式为顺车,反之,使用G42指令车削方式为逆车。而在数控机床为里提高加工表面质量,经常采用顺车,即G41指令。 (4)建立和取消刀补时,必须与G01或G00指令组合完成,配合G02或G03指令使用,机床会报警,在实际编程时建议使用与G01指令组合。建立和取消刀补过程如图(4-12)所示,使刀具从无刀具半径补偿状态O点,配合G01指令运动到补偿开始点A,刀具半径补偿建立。工件轮廓加工完成后,还要取消刀补的过程,即从刀补结束点B,配合G01指令运动到无刀补状态O点。 图(4-12)刀具半径补偿的建立和取消过程 a) 左刀补的建立和取消b) 右刀补的建立和取消
数控铣编程中刀具半径补偿和长度补偿
数控铣编程中刀具半径补偿和长度补偿 【摘要】刀具中心轨迹与工作轨迹常不重合。通过刀具补偿功能指令,数控铣床系统可以根据输入补偿量或者实际的刀具尺寸,使数控铣床自动加工出符合程序要求的零件。刀具半径补偿即根据按轮廓编制的程序和预先设定的偏置参数,实时自动生成刀具中心轨迹的功能成为刀具半径补偿功能。 【关键词】数控铣床;刀具;半径补偿;长度补偿 1.刀具半径补偿 由于数控加工的刀具总有一定的半径,刀具中心运动轨迹并不等于所需加工零件的实际轮廓,而是偏移轮廓一个刀具半径值。在进行外轮廓加工时,使刀具中心偏移零件零件的外轮廓表面一个刀具半径值,加工内轮廓时,使刀具中心偏移零件内轮廓表面一个刀具半径值,这种偏移习惯上称为刀具半径补偿 数控铣床刀具类型0-9种,这些内容应当事前输入刀具编制文件。刀具半径补偿的轮廓切削。刀具半径补偿的灵活应用,灵活应用的思路使用刀具半径补偿功能。随着计算机技术和数控技术的发展都经历了B(Base)功能C极坐标法,法、矢量判断法。刀具补偿技术和C功能刀具半径技术。目前,数控系统中普遍采用的是C功能刀具半径补偿技术。 2.C功能刀具半径补偿的基本思想 数控系统C功能刀具半径补偿的硬件结构由缓冲寄存器CS、工作寄存器AS和输出寄存器OS等部分组成。在C功能刀补工作状态中,数控铣床装置内部总是同时存储着三个程序段的信息。进行补偿时,第一段加工程序先被读入BS,在BS中算得的第一段编程轨迹被送到CS暂存后,又将第二段程序读入BS,算出第二段的编程轨迹。接着对第一、第二两段编程轨迹的连接方式进行判别,根据判别结果,再对CS中的第一段编程轨迹进行相应的修正。修正结束后,顺序地将修正后的第一段编程轨迹由CS送到AS,第二段编程轨迹由BS送入CS。随后,由CPU将AS中的内容送到OS进行插补运算,运算结果送到伺服驱动装置予以执行。当修正了第一段编程轨迹开始被执行后,利用插补间隙,CPU又命令第三段程序读入BS。随后,又根据BS、CS中的第三、第二段编程轨迹的连接方式,对CS中的第二段编程轨迹进行修正。 3.功能刀具补偿类型及判别方法 通常数控铣床装置中能控制加工的轨迹通常只有直线和圆弧。所有编程轨迹一般由四种轨迹转接方式,你直线与直线转接、直线与圆弧转接、圆弧与直线转接和圆弧与圆弧转接。根据前后两段程序程序轨迹交角外在工作侧的角度(矢量的夹角)的不同,有伸长型、缩短型和插入型三种过渡(转接)类型。图2为直线转接情况;
如何用好加工中心刀具长度补偿功能
如何用加工中心刀具长度补偿功能 刀具补偿功能,是数控机床的一项重要功能,在准备功能中用G43、G44、G49表示,但是若使用得不好恨容易造成撞车和废品事故。下面以加工中心为例,介绍生产实践中常用的机种刀具长度补偿方法。 1、刀具长度补偿功能的执行过程 典型的指令格式为G43 Z_H_;或G44 Z_H_。其中G43指令加补偿值,也叫正向补偿,即把编程的Z值加上H代码的偏值寄存器中预设的数值后作为CNC实际执行的Z坐标移动值。相应的G44指令减去预设的补偿值,也叫负向补偿。 当指令G43时,实际执行的Z坐标值Z’=Z_+(H_); 当指令G44时,实际执行的Z坐标值为Z’=Z_-(H_); 这个运算不受G90绝对值指令或G91增量值指令状态的影响。偏值寄存器中可预设正值或负值,因此有如下等同情况。 1)指令G43、H设正值等同于指令G44、H设负值的效果; 2)指令G43、H设负值等同于指令G44、H设正值的效果 因此一般情况下,为避免指令输入或使用错误时失误,可根据操作者习惯采用两种方式:1)只用指令G43,H设正值或负值; 2)H只设正值,用指令G43或G44。 以下介绍使用较多的第一中情况: 指令格式中Z值可以为0,但H0或H00将取消刀具长度补偿,与G49效果等同,因为0号偏值寄存器被NC永远置0. 一般情况下,为避免失误,通过设定参数使用刀具长度补偿只对Z轴有效。例如当前指令为G43X_H_;时,X轴的移动并没有被补偿。 被补偿的偏置值由H后面的代码指定。例如H1设20.、H2-30.,当指令“G43 Z100.H1;”时,Z轴将移动至120处:而当指令“G43 Z100.H2;”时,Z轴将移动至70.处。G43(G44)与G00、G01出现在一个程序段时,NC将首先执行G43(G44)。 可以在固定循环的程序段中指令G43(G44),这时只能指令一个H代码,刀具长度补偿同时对Z值和R值有效。 在机床回参考点时,除非使用G27、G28、G30等指令,否则必须取消刀具长度补偿。为了安全,在一把刀加工结束或程序段结束时,都应取消刀具长度补偿。 现代数控机床基本上淘汰了纸带,用芯片存储程序和刀具长度补偿值,可以随时修改,但通过设置和修改补偿量避免和减少改动加工程序,避免和减少因此可能带来的误改、改不全等事故发生也是很有意义的。有些数控机床在出厂时因为参数设定不当,造成存储保护开关只能禁止改加工程序,这种情况是相当危险的。 2、利用刀具长度补偿功能简化编程 利用NC处理刀具长度补偿功能的原理,可以简化编程。在编制加工程序时,忽略不同刀具长度对编程的影响,可以只以一把假想长度的标准刀具进行编程,这个假想长度的标准刀
加工中心刀具长度补偿应用的探索
加工中心刀具长度补偿应用的探索 摘要:介绍加工中心刀具长度补偿指令的意义和原理,刀具长度补偿指令的格式及应用,介绍测量刀具长度补偿值的多种对刀方法及优缺点,刀具长度补偿应用过程中的一些注意事项。 关键词:刀具长度补偿;对刀;测量; 如图1所示,加工中心在同一个工件坐标系下,调用T01(中心钻)加工深度为5mm的定位孔;调用T02(?9.8麻花钻)加工深度为25mm的底孔,由于两把刀具的相对刀长相差90mm,因此麻花钻的加工深度将比指定深度深90mm 引起撞刀,造成工件报废和刀具的损坏。如果程序采用刀具长度补偿,可避免上述发生的问题,刀具长度补偿的应用包括刀具长度补偿值的测量和程序编制,以下就从这两个方面介绍。 1 .刀具长度补偿值的测量及设定 根据工件坐标系设置和基准刀具的选择方法,刀具长度补偿值的测量有以下三种方法(为方便理解,工件零点统一定在工件上表面): 1.1. 机内对刀测量法 机内对刀就是在机床上利用机床坐标系的坐标测量功能来完成刀具长度补偿值的测量。具体操作如下: 1.1.1.在工件坐标系设定画面中将“Z”轴零点偏置值置0,即Z向工件零点和机床零点重合。 1.1. 2.刀具依次装入主轴锥孔内,移动刀具使刀尖(刀位点)与工件上表面接触对刀,记录每一把刀具在机械坐标系中“Z”轴显示的坐标值,如图2所示。 1.1.3.对应刀具号将上一步测量的数据-334.54、-243.54、-308.1输入相应的H01、H02、H03刀具长度补偿寄存器中即可。 机内对刀测量刀具长度补偿值占用机床调试时间,因此效率低。当用同一把刀加工其它工件时就需重新设置刀具长度补偿值。 1.2 .机外对刀测量法 机外对刀是采用专用对刀仪测量刀具长度补偿值。它所测量的刀具长度补偿值为主轴下端面(刀具安装点)到刀尖(刀位点)的距离,该数据为正值。如图3所示,麻花钻的刀具长度补偿值为196.58mm。机外对刀操作过程如下:
数控车床刀具半径补偿G40G41G42 1教学内容
数控车床刀具半径补 偿 G40G41G42 1
精品文档
刀尖圆弧半径补偿 G40,G41,G42
当编写数控轨迹代码时,一般是以刀具中心为基准。但实际中,刀具通常
是圆形的,刀具中心并不是刀具与加工零件接触的部分,所以刀具中心的的轨
迹应偏离实际零件轨迹一个刀具半径的距离。简单的将零件外形的轨迹偏移一
个刀具半径的方法就是 B 型刀补,这样的方法虽然简单,但会出现一定的问
题,如产生过切现象。而且由于刀尖圆弧的影响,实际加工结果与工件程序会
存在误差,而
C 型刀补可实现刀具半径补偿解决上述问题、消除上述误
差。C 型刀补的基本思想是并不马上执行读入的程序,而是再读入下一段程
序,判断两段轨迹之间的转接情况,根据转接情况计算相应的运动轨迹(转接
向量)。由于多读了一段程序进行预处理,故 C 型刀补能进行更精确的补
偿、消除圆形刀具其中心不在刀尖上带来的误差,从而能实现精密加工。如图
所示。
刀尖圆角 R 造成的少切与过切
为了更好的理解和使用
C 型刀具半径补偿功能,就必须先理解下列
几个相关的基本概
假想刀尖概念
收集于网络,如有侵权请联系管理员删除
精品文档
下图中刀尖 A 点即为假想刀尖点,实际上不存在,故称之为假想刀尖(或 理想刀尖)。假想刀尖的设定是因为一般情况下刀尖半径中心设定在起始位置 比较困难,而假想刀尖设在起始位置是比较容易的,如下图所示。与刀尖中心 一样,使用假想刀尖编程时不需考虑刀尖半径。
图 1-1 刀尖半径中心和假想刀尖 注:对有机械零点的机床来说,一个标准点如刀架中心可以将其当作起点。从 这个标准点(起点)到刀尖半径中心或假想刀尖的距离就设置为刀具偏置值。 将标准点当作起点,从标准点到刀尖半径中心的距离设置为偏置值就如同将刀 尖半径中心设置为起点,而从标准点到假想刀尖的距离设置为偏置值就如同将 假想刀尖设置为起点。为了设置刀具偏置值,通常测量从标准点到假想刀尖的 距离比测量从标准点到刀尖半径中心的距离容易,所以通常就以标准点到假想
收集于网络,如有侵权请联系管理员删除
数控加工中巧用刀具半径补偿指令
数控加工中巧用刀具半 径补偿指令 Document serial number【UU89WT-UU98YT-UU8CB-UUUT-UUT108】
数控加工中巧用刀具半径补偿指令【论文摘要】:本文通过对刀具半径补偿功能的分析,总结出刀具半径补偿功能要点,给我们的编程和加工带来很大的方便。 【关键词】:刀具半径补偿 G41 G42 G40。 一、前言 零件加工程序通常是按零件轮廓编制的,而数控机床在加工过程中的控制点是刀具中心,因此在数控加工前数控系统必须将零件轮廓变换成刀具中心的轨迹。只有将编程轮廓数据变换成刀具中心轨迹数据才能用于插补。在数控铣床上进行轮廓加工时,因为铣刀有一定的半径,所以刀具中心(刀心)轨迹和工件轮廓不重合,如不考虑刀具半径,直接按照工件轮廓编程是比较方便的,而加工出的零件尺寸比图样要求小了一圈(加工外轮廓时),或大了一圈(加工内轮廓时),为此必须使刀具沿工件轮廓的法向偏移一个刀具半径,这就是所谓的刀具半径补偿指令。应用刀具半径补偿功能时,只需按工件轮廓轨迹进行编程,然后将刀具半径值输入数控系统中,执行程序时,系统会自动计算刀具中心轨迹,进行刀具半径补偿,从而加工出符合要求的工件形状,当刀具半径发生变化时也无需更改加工程序,使编程工作大大简化。实践证明,灵活应用刀具半径补偿功能,合理设置刀具半径补偿值,在数控加工中有着重要的意义。 二、刀具半径补偿方式有B功能刀具补偿和C功能刀具补偿两种。 1.B功能刀具半径补偿 早期的数控系统在确定刀具中心轨迹时,都采用读一段、算一段、再走一段的B 功能刀具半径补偿(简称B刀补)控制方法,它仅根据程序段的编程轮廓尺寸进行刀具半径补偿。对于直线而言,刀补后的刀具中心轨迹为平行于轮廓直线的直