高酸值原油加工综述
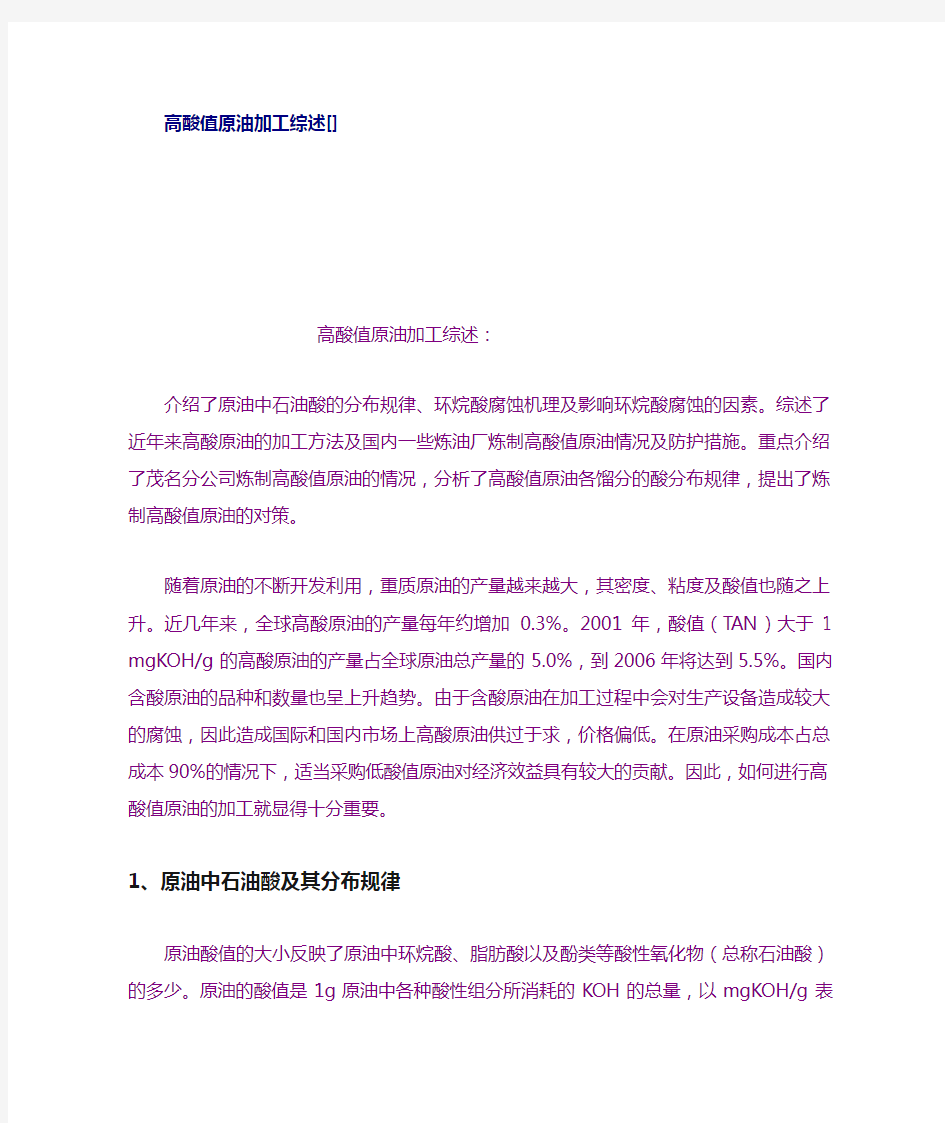

高酸值原油加工综述[]
高酸值原油加工综述:
介绍了原油中石油酸的分布规律、环烷酸腐蚀机理及影响环烷酸腐蚀的因素。综述了近年来高酸原油的加工方法及国内一些炼油厂炼制高酸值原油情况及防护措施。重点介绍了茂名分公司炼制高酸值原油的情况,分析了高酸值原油各馏分的酸分布规律,提出了炼制高酸值原油的对策。
随着原油的不断开发利用,重质原油的产量越来越大,其密度、粘度及酸值也随之上升。近几年来,全球高酸原油的产量每年约增加0.3%。2001年,酸值(TAN)大于1 mgKOH/g的高酸原油的产量占全球原油总产量的5.0%,到2006年将达到5.5%。国内含酸原油的品种和数量也呈上升趋势。由于含酸原油在加工过程中会对生产设备造成较大的腐蚀,因此造成国际和国内市场上高酸原油供过于求,价格偏低。在原油采购成本占总成本90%的情况下,适当采购低酸值原油对经济效益具有较大的贡献。因此,如何进行高酸值原油的加工就显得十分重要。
1、原油中石油酸及其分布规律
原油酸值的大小反映了原油中环烷酸、脂肪酸以及酚类等酸性氧化物(总称石油酸)的多少。原油的酸值是1g原油中各种酸性组分所消耗的KOH的总量,以mgKOH/g表示。原油酸性物质除了环烷酸外,还有脂肪酸、芳香酸、无机酸、硫醇、硫化氢和苯酚等。当原油酸值大于0.5 mgKOH/g即能引起设备腐蚀,故通常将酸值大于0.5 mgKOH/g的原油称之为高酸值原油。在原油的酸性物质中,以环烷酸最为重要,含量也高,它约占原油酸性物质的90%。
环烷酸是一种带有五元或六元环的十分复杂的羧酸混合物,相对分子量变化范围很大,但以300~400居多。低分子量的环烷酸在水中有一定溶解度,而高分子量环烷酸几乎不溶于水。环烷酸在原油中的分布规律十分特殊,中间馏分(250~500℃)环烷酸含量最高,而在低沸馏分和高沸馏分中环烷酸含量都比较低。也就是说环烷酸含量一般从煤油馏分开始逐渐增加,至柴油馏分其含量几乎达到最高峰,然后有所下降。
2、加工高酸值原油引起的腐蚀
加工高酸值原油的炼厂,设备的腐蚀主要是由环烷酸引起的。其蒸馏装置的高温部位腐蚀严重,腐蚀主要发生在高温部位的设备和管线,例如常压炉、减压炉的炉出口管弯头,炉出口阀门,转油线高速段和低速段、常压塔和减压塔的进料蒸发段、塔壁、塔盘、主梁、支梁等部位。环烷酸的腐蚀与硫腐蚀不同,它不是均匀腐蚀,而是局部腐蚀或点蚀,而且环烷酸腐蚀受酸值、温度、流速、介质、物态变化等多方面因素的影响,因此不容易检测。
2.1
环烷酸腐蚀机理
环烷酸在石油炼制过程中,随
原油一起被加热、蒸馏,并与其沸点相同的油品一起冷
凝,而且溶于其中,从而造成该馏分对设备材料的腐蚀。目前,一般认为环烷酸腐蚀的反应机理如下:
2RCOOH+Fe→Fe(RCOO)2 +H2
现场经验表明:环烷酸腐蚀经常发生在酸值大于0.5 mgKOH/g、温度在270~400℃之间高流速的工艺介质中。它与金属表面或硫化铁膜直接反应生成环烷酸铁。环烷酸铁是油溶性的,再加上介质的流动,使金属表面不断暴露并受到腐蚀。故环烷酸腐蚀的金属表面清洁、光滑无垢。在物料的高温高流速区域,环烷酸腐蚀呈顺流向产生的尖锐边缘的流线沟槽;在低流速区域,则呈边缘锐利的凹坑状。环烷酸腐蚀均发生在塔盘、塔壁、转油线等部位。另外,由于环烷酸盐具有表面活性,会造成原油严重乳化,从而引起装置操作波动,并造成塔顶腐蚀。
2.2
影响环烷酸腐蚀的因素
2.2.1温度的影响
环烷酸的腐蚀受温度影响很大。环烷酸在常温下对金属没有腐蚀性,但在高温下能和铁生成环烷酸铁,引起强烈的腐蚀。220℃环烷酸开始腐蚀,并随温度的升高腐蚀加剧。270~280℃腐蚀已经很严重,以后随温度上升而减弱,但在350~400℃腐蚀急剧增加。
2.2.2
流速的影响
流速和流态是影响环烷酸腐蚀的非常重要的因素。在炼油设备的弯头、三通和泵中产生的湍流加速设备的腐蚀。当气量大于60%,蒸汽流速大于60 m/s的射流,腐蚀最严重。在这样的条件下,某些设备,如炉管、弯头、管线的腐蚀速度可增大两个数量级。在高温、高流速的情况下,酸值在很低的水平(0.3 mgKOH/g),对碳钢仍有很高的腐蚀速率。
2.2.3原油硫含量的影响
环烷酸与金属的腐蚀反应产物为油溶性的Fe(RCOO)2,它能被油流所带走,因此不易在金属设备表面上形成保护膜,腐蚀产物易从金属表面解离下来,使腐蚀向纵深处发展。当金属长期与环烷酸接触,原油流速很大时,在金属表面可观察到特有的沟槽状腐蚀。这是区别环烷酸腐蚀与其它腐蚀的标记。若原油中含有活性硫化物时,高温下,活性硫化物开始分解,产生硫化氢。硫化氢与金属的反应为:
H2S+Fe→FeS+H2
生成的腐蚀产物FeS膜,在一定的条件下具有一定的保护作用。而在环烷酸中FeS 膜被溶解,其反应为:
FeS+2RCOOH →Fe(RCOO)2+H2S
生成的硫化氢又引起下游设备的腐蚀,如此形成的腐蚀循环,加剧了金属的腐蚀。
3、高酸原油加工的防腐对策
3.1、碱中和
3.1.1用NaOH或KOH水溶液脱酸
碱洗是经典的脱酸工艺。用氢氧化钠溶液与环烷酸进行中和反应,所得环烷酸钠盐从油品中分离出来,经酸化得到游离的环烷酸。反应过程可在瞬间完成,但在
反应过
程中容易产生乳化现象。大量的研究工作就是基于如何防止处理过程中生成乳化液以及破坏已形成的乳化液来展开的。研究表明:通过调整操作参数(油与碱液的混合强度、碱液浓度、操作温度、电精制电场强度),或采用非分散性接触技术以及加入添加剂等方法可以部分改善乳化现象。这种工艺的优点是:投资少,运行成本低,操作简单。但也存在一些缺点:碱液随同加工产品大量流失,氢氧化钠试剂不能再生,分离环烷酸所生成的硫酸钠污染严重;为防止废物污染所建的焚烧设备和防止二次污染的回收设备,增加了系统的投资;而且如果没有充分脱除油品中的碱液,残存在油品中的少量环烷酸皂对燃料油和润滑油的使用性能将带来不良影响。
3.1.2用氨/醇溶液脱酸
用氨水代替苛性碱将石油酸从油相中抽提出来,实质上是将石油酸转化为铵盐,从油品中分离出来;铵盐加热分解释放出氨气同时回收石油酸,氨气可以回收再利用。醇的加入主要是用于改善乳化现象。文献表明,采用氨水一甲醇溶液、氨水一乙醇溶液、氨水一异丙醇溶液等氨水一乙醇复合溶剂体系进行脱酸实验,最高脱酸率可达99﹪。另外,胺类、烷氧基胺或季铵盐类等也可以用作中和剂进行脱酸反应,得到较好的脱酸效果,但成本较高。氨/醇脱酸可以在较广的范围内选择操作条件,脱酸效果好,环境污染小,但溶剂回收能耗较高,脱酸油色度受到一定的影响。
3.1.3用金属氧化物及有机酸钠(或钾)盐脱酸
用氧化钙、磺酸钙或其它金属氧化物,以及小分子有机酸的碱金属盐同样可以脱酸,但是也存在产生大量的碱渣和含盐污水的问题。随着环保法规的日益健全和严格,污水和碱渣的治理问题越来越严重,碱中和法的劣势也越来越明显。
3.2抽提分离
采用选择性溶剂,可从石油馏分中提取环烷酸。文献指出,甲酰替二甲胺、乙睛、工业三甘醇等作为萃取溶剂都可有效地脱去油中的石油酸。利用甲酰替二甲胺作为选择性溶剂,采用连续4次抽提,当原油酸值为2.65 mgKOH/g时,酸值依次降低1.82 、0.40 、0.22 和0.08 mgKOH/g;采用工业三甘醇作为选择性溶剂,分离柴油馏分中的环烷酸,当溶剂比1:1.5时,环烷酸的分离度达到99.9%。除上述溶剂外,还可以采用的其它选择性溶剂,包括双甘醇、聚丙烯乙二醇、二甲基亚砜、N-甲基毗咯烷酮和乙二醇、聚丙二醇醚、三乙二醇醛等。但是,多数可选择溶剂对油中的芳烃尤其是多环芳烃也具有相当的溶解性,特别是对于重质馏分油,大分子的石油酸与烃类的性质差异缩小,给抽提剂的选择带来较大困难。因此,寻找选择性好、价廉
、沸点较低的溶剂(或混合溶剂)是这种技术能否具有实用性的关键。
3.3加氢法脱除原油中的环烷酸
无论是馏分油加氢脱硫、脱氮,还是渣油加氢处理,在加氢过程中都可以有效地
除去环烷酸,但由于环烷酸的强腐蚀性,在炼油过程中应尽可能早地将其脱除。在非常缓和的条件下(反应温度较低,氢压较小)采用传统的加氢催化剂进行加氢脱酸处理,脱酸效果显著。近年来,又开发出多种油溶性和水溶性的分散型催化剂如环烷酸钼、环烷酸钴、磷钼酸铵等,用于环烷酸的加氢脱酸反应,也取得了较好的脱酸效果。在油溶性催化剂中二烷基二硫代氨基甲酸钼和二烷基二硫代磷酸钼具有较高的催化活性,而在水溶性催化剂中,钼酸铵、磷钼酸铵和硫代钼酸铵同样具有较高的加氢活性和抑制生焦能力。加氢法脱除原油中的环烷酸可以说是最彻底的脱酸手段,而且避免了碱渣污染等问题,但是反应需要使用大量氢气,工艺建设投资和操作成本较高[1]。
3.4混炼
混炼是防止环烷酸腐蚀有效的而且是低成本的方法,它不需要额外的支出或投资,只需要对计划和运行进行合理安排。把混合原油酸值进行有目的的调整,做到合理、均衡地安排进入装置的混合原油酸值小于0.5 mgKOH/g时,就可以有效地控制环烷酸腐蚀。
3.5采用高温缓蚀剂技术
采用高温缓蚀剂技术也是解决高温环烷酸腐蚀的一种经济、简便有效的途径。目前国内解决炼油装置高温部位腐蚀的方法主要是更换材质,尤其对于低硫高酸值原油;而国外在重视选材的同时,也常采用注入高温缓蚀剂。用高温缓蚀剂抑制有机酸(主要是环烷酸)的腐蚀,其用量小,不影响油品质量,不影响后续加工,克服了原油注碱的缺点,可作为更换材质的补充。
高温缓蚀剂技术近几年发展较快,许多加工高酸、高硫原油的炼厂都在积极使用,防腐效果还是比较明显的,但是对一些高温高速部位使用的效果则较差。
3.6全面提高装置设备材质等级
3.6.1装置设备材质升级
选用耐腐蚀材料是防止环烷酸腐蚀最有效的措施之一。在没有理想的工艺防腐蚀手段的情况下,提高设备材质的耐蚀等级是减轻环烷酸腐蚀最有效的方法。提高材质耐蚀等级的实质就是采用加入一定量的合金元素如Cr、Ni、Ti的合金钢,以便形成有一定效果的氧化物保护膜,该氧化物保护膜对金属离子扩散有着强烈的阻滞作用,从而保护金属不受进一步腐蚀。对于有机酸腐蚀的环境,在设备选材时应充分考虑介质的温度、流速以及是否会出现涡流、湍流和相变等因素,对流速超过30 m/s、出现涡流、湍流和相变的部位应采用更高
级别的材质。据资料介绍,不同材质对环烷酸具有不同的耐蚀性。具体材料的耐蚀性为:碳钢<低合金钢(铬钼钢:Cr5Mo<Cr9Mo=<1Cr13<18-8不锈钢<含钼奥氏体不锈钢。所以选用含钼奥氏体不锈钢可有效地控制环烷酸的腐蚀;对于典型的含钼奥氏体不锈钢316和315L,含钼量应高于2.3%,低于此值将降低其耐蚀性[5]。
3.6.2材料表面改性
渗铝技术作为材料的表面改性处理方法,可以显著提高金属材料表面的防腐蚀性能。尤其是在炼油防腐蚀中,渗铝材料在多种介质中具有良好的耐蚀性,如耐高温硫、环烷酸、二氧化碳、低温硫化氢、高温氧化等腐蚀。由于渗铝后的金属材料表面显微硬度增高,同时还具有良好的耐磨性能。实验及应用结果表明:渗铝
技术作为一种金属表面改性手段,可有效地降低设备的投资,延长使用寿命。目前,碳钢渗铝材料的成本只有18-8钢的40%~60%,应用前景很好。对碳钢和低合金钢表面进行铬、铝、钼复合共渗可以满足加工高酸值原油的耐蚀性选材要求,且处理后的材料成本仅增加20%~50%[6]。
4、国内炼油厂炼制高酸值原油情况及防护措施
从目前我国各油田产出原油和各炼厂的原油来源分析,我国西北地区各炼厂,如兰炼、乌炼、独炼、克拉玛依炼厂等和辽宁地区的锦州、锦西炼厂等及华北、山东地区的炼厂,在原油加工过程中都遇到了高酸值原油引起的严重腐蚀;而沿海、沿江及南方各炼厂主要是加工高含硫原油引起的腐蚀,也有一部分炼厂加工高酸值原油引起的腐蚀。我国几种主要含酸原油的酸值、硫含量见表1[7]。
表1、我国各油田含酸原油产品性质
原油名称酸值/mgKOH?g-1 硫含量,%
北疆 4.51 0.13
渤海 3.61 0.34
绥中 3.33 0.39
辽河 2.55 0.75
锦州 2.12 0.23
孤岛 1.45~1.83 2.0~2.3
胜利 1.27 1.03
文昌0.68 0.103
大港0.64 0.21
冀东0.56 0.08
从表1中可看出,除胜利、孤岛和辽河原油含硫量较高外,其余油田的含硫量并不高,造成设备严重腐蚀的因素主要是原油中的有机酸即环烷酸。这些炼厂由环烷酸引起的严重腐蚀主要是在常减压装置和转油线上,而二次加工中由环烷酸引起的腐蚀较少。目前这些炼厂在腐蚀突出的部位都已经更换了不同牌号的不锈钢,甚至更换上316L、317L等优质不锈钢。在材料“升级”以后,还未发生重大的腐蚀问题,使炼厂基本达到2年一修的基本要求。
4.1炼制高酸值原油情况及防护措施
炼油厂蒸馏装置1984年5月前主要炼大庆、任丘及胜利原油,腐蚀问题不严重,1984年下半
年开始大量炼辽河原油和混合原油,见表2,其中所炼胜利原油的酸值亦有所提高,随之蒸馏装置的一些碳钢构件发生了严重的腐蚀。腐蚀主要在高温部位的设备和管线,例如常压炉、减压炉的炉出口管弯头,炉出口阀门,转油线高速段和低速段、常压塔和减压塔的进料蒸发段、塔壁、塔盘、主梁、支梁等部位。
表2、炼油厂主要含酸原油酸值、硫含量
原油名称酸值/mgKOH?g-1 硫含量,%
辽河 2.55 0.75
胜利 1.27 1.03
炼油厂炼制高酸值原油主要防护措施如下:
1)混炼
对原油酸值进行有目的的调整,做到合理、均衡地安排进入装置的原油酸值,从而有效地控制环烷酸腐蚀。
2)中和环烷酸
在原油进入装置之前加入氢氧化钠中和原油中的环烷酸,使原油酸值降至0.5 mgKOH/g以下。注碱虽然能够中和原油中的酸性物质,从而降低原油的酸值,达到降低腐蚀的目的,但会使生产成本增加,渣油的钠含量严重超标,致使渣油不能作为催化裂化、加氢裂化和焦化的原料。而且,注碱并不能完全控制高温部位腐蚀。
3)提高设备材料耐蚀等级
减压蒸馏装置在1988年5月进行了设备改造,在高温腐蚀突出部位引入了1Cr18Ni9Ti、316L等耐蚀材料,并于1990年5月完全停止注碱。经运行一年半时间,在大检修时检查,蒸馏装置高温部位未发现突出的腐蚀问题,有力地保障了加工高酸值原油的安全生产。
4)改造设备不合理结构以减缓冲刷腐蚀
设备结构要合理,应尽量减少部件结合部的缝隙和流体流向的死角、盲肠。减少管线震动,对已腐蚀减薄部位采取补贴加厚或外套补焊。热电偶插套外壁需加加强板。尽量取直管线走向,减少急弯走向。
4.2
镇海炼化公司炼制高酸值原油情况
近年来,炼化公司常减压装置加工过的高酸值原油品种已达10余种,主要为胜利、流花、辽河、葵土、罗凯利亚、杜里、特洛尔,其酸值及硫含量数据见表3。其中酸值最高的罗凯利亚原油,酸值达到3.40 mgKOH/g。高酸值原油的酸值、加工量及所占比例均逐年迅速递增[8]。
表3、镇海炼化公司主要含酸原油酸值、硫含量
原油名称酸值/mgKOH?g-1 硫含量,%
罗凯利亚 3.40 0.47
辽河 2.55 0.75
葵土 1.90 0.69
胜利 1.27 1.03
杜里 1.26 0.47
流花 1.12 0.24
特洛尔0.88 0.28
加工高酸值原油对生产操作的影响:
1)该公司所加工的高酸值劣质原油几乎都是重质原油,轻组分少,重组分多,热量后移,导致生产时因低温部位热量少,造成电脱盐温度低,从
而降低了电脱盐装置的脱盐效果。
2)蜡油量大,装置冷却设备超负荷,蜡油冷后温度超标。
3)渣油量大、粘度高,造成外放困难。
4)高酸值劣质原油“头轻脚重”,产品分布不均,常压拔出量少,渣油量大,加大了加热炉负荷,产品质量控制困难,难以提高装置处理能力。
镇海炼化公司加工高酸值原油对策如下:
1)加强系统配套改造
为了解决大量加工高酸值原油后续装置处理能力不配套、碱洗能力低及加氢能力有限的问题,镇海炼化公司大力加强系统配套改造,已新建了3.0 Mt/a柴油加氢装置和1.8 Mt/a蜡油加氢装置,解决加氢能力不足的矛盾,提高高酸值原油加工能力。
2)全面提高装置设备材质等级
在没有理想的工艺防腐蚀手段的情况下,提高设备材质的耐蚀等级是减轻环烷酸腐蚀最有效的方法。提高材质耐蚀等级的实质就是采用加入一定量的合金元素如Cr、Ni、Ti的合金钢,以便形成有一定效果的氧化物保护膜,该氧化物保护膜对金属离子扩散有着强烈的阻滞作用,从而保护金属不受进一步腐蚀。
3)采取混炼加工技术
为保证装置的长周期运行,加工高酸值劣质原油时应以带炼和掺炼为主,并控制好混合原油的酸值低于0.5 mgKOH/g。
4)重视脱盐操作
5)采用新型有机胺和高温缓蚀剂。
5、分公司炼制高酸值原油情况及对策
分公司共有4套蒸馏装置,原油加工能力13.5Mt/a。一蒸馏装置于1963年3月建成投产,几经改造,现炼油能力已达到3.0 Mt/a。由于加工原油性质多变,装置情况复杂,特别是自1987年以来,进厂的原油酸值持续上升,使该装置的高温重油部位的设备、管线腐蚀加剧。鉴于在原油酸值增高的情况下,原有高温易蚀部位的碳钢和Cr5Mo钢己不能适应生产上的需要,因此,从1988年底开始,已经实施了材质的升级。目前该装置高温重油部位的内构件及管线基本上采用了奥氏体不锈钢材料,基本满足高酸值原油加工的要求。
二蒸馏装置于1974年9月建成投产,原设计是以加工大庆原油为主的润滑油型装置,处理能力2.5 Mt/a。经1978年和1980年两次改造,处理能力已达3.0 Mt/a。加工原油品种也从原来的单一大庆油发展到炼国内外10余种高酸值及高含硫原油。
三、四蒸馏装置以加工进口高含硫原油为主,装置设备材质以耐硫腐蚀为主。
5.1分公司炼制的高酸值原油种类
分公司炼制的10多种主要含酸原油的酸值、硫含量见表4。
表4、分公司炼制的主要含酸原油酸值、硫含量
原油名称酸值/mgKOH?g-1 硫含量,%评价年份
巴西马林 1.34 0.788 2004
胜利 1.27 0.77 1997
印尼杜里 1.26 0.47
2006
挪威特劳尔0.85 0.30 2005
海南文昌0.68 0.103 2002
赤道几内亚扎非洛0.67 0.27 1997
尼日利亚班嘎0.59 0.25 2006
安哥拉罕戈0.56 0.62 2005
刚果杰诺0.50 0.233 1997
阿曼0.47 1.18 2004
涠洲0.45 0.10 2003
尼罗0.42 0.05 2003
注:表中数据采自原油评价报告数据。
从表4可知,分公司炼制的酸值最高的高酸值原油的是巴西马林原油,酸值达到1.34 mgKOH/g;炼制的高酸原油除巴西马林、胜利、安哥拉罕戈为高酸含硫原油外,其余一般都是高酸低硫原油。阿曼、涠洲和尼罗等原油虽然酸值小于0.5 mgKOH/g,不属于高酸原油,但它们的酸值也比较大,且减压蜡油的酸值也较高;用这些减压蜡油生产润滑油时,基础油酸值比较难降低,从而影响产品的质量。
5.3高酸值原油各馏分酸分布情况
分公司炼制过的3种高酸值原油各馏分酸分布情况见表5。
表5、3种高酸值原油各馏分酸分布情况
原油馏分
杜里、阿曼混合罕戈班嘎
酸值/
mgKOH?g-1
酸度/mgKOH?(100mL)-1
酸值/mgKOH?g-1
酸度/mgKOH?(100mL)-1
酸值/mgKOH?g-1
酸度/mgKOH?(100mL)-1
原油 1.00-0.56-0.59-
初顶-0.073-0-0.228
常顶- 0.212-0.203-0.559
常二油-10.43-15.8-14.3
常三油-72.3-28.11)-28.11)
常四油0.903--48.5-45.6
减一油1.26-0.756-0.699-
减二油1.44-1.031-0.808-
减三油1.46-1.063-1.05-
减四油0.993-0.949-0.860-
渣油0.312-0.209-0.381-
注:常三油已注碱。
从表5可知:高酸值原油的酸性物质主要分布在常三油、常四油、减一油、减二油、减三油和减四油,即馏程在250~500℃之间,也就是柴油组分和减压蜡油组分中,并以减三油酸值最高。因此,用高酸值原油生产的柴油组分和减压蜡油组分的酸值都较高,从而影响产品的质量。
5.3高酸值原油加工存在问题
茂名分公司高酸值原油加工主要存在以下问题:
1)容易引起常减压蒸馏装置严重腐蚀。
2)柴油组分酸值偏高。
3)减压蜡油酸值偏高,从而引起润滑油中和值偏高。
5.4炼制高酸值原油对策
茂名分公司炼制高酸值原油可以采用以下对策:
1)重视脱盐操作
原油脱盐不仅是原油蒸馏装置塔顶系统工艺防腐蚀的关键环节,而且是对重油催化裂化和加氢等后续加工有重要作用的原油预处理工艺。提高脱盐脱水效果,一方面可以减轻装置腐蚀和结垢,另一方面通过电脱盐装置脱水脱盐后,有效地减少原油中的金属离子、氯离子,去除杂质成分,优化常减压蒸馏装置产品质量。开发筛选普遍适用于高酸值劣质原油的高效破乳剂,优化高酸值劣质原油脱盐条件(
如脱盐温度、注水量、混合强度等),采用合理的电场梯度等是提高电脱盐效果的有力手段。
2)采用新型有机碱和高温缓蚀剂
鉴于传统的注碱方式,钠离子对二次加工装置影响较大,可以考虑用有机碱代替苛性钠作为高酸原油的中和剂,如单乙醇胺,二乙醇胺等,不过成本相对较高。对于减压蜡油的酸,也可以用有机碱中和。
针对环烷酸腐蚀特点,加入新型高温缓蚀剂可以达到不注碱的情况下减缓蒸馏装置高温部位环烷酸腐蚀的目的。新型高温缓蚀剂可以在金属材质表面形成吸附性保护膜,同时部分高温缓蚀剂直接与环烷酸作用,生成环烷酸脂,大分子量环烷酸脂可在金属表面建立吸附平衡,将环烷酸等有机酸与金属表面隔离,达到保护材质的目的。
3)混炼加工技术
混炼是防止环烷酸腐蚀的有效而且是低成本的方法,它不需要额外的支出或投资,只需要对计划和运行进行合理安排。对混合原油酸值进行有目的的调整,做到合理、均衡地安排进入装置的混合原油酸值小于0.5 mgKOH/g时,就可以有效地控制环烷酸腐蚀,并且还可以降低柴油组分和减压蜡油的酸值。
4)中和环烷酸
用注碱方法可中和柴油组分酸值。但柴油组分环烷酸较高时,碱中和容易产生乳化现象,因此,碱中和柴油组分环烷酸时要加入合适的破乳剂。
5)加强防腐蚀监测
在腐蚀突出的部位设置固定的监测点,定期进行壁厚监测。当腐蚀速度变化较大或腐蚀环境变化大(如原油腐蚀性很强、油种变化时)则增加监测频次。
6)监测物料的酸值
各种原油的酸值不相同,甚至同一品种不同批次其酸值也会不同,掌握蒸馏装置高温部位各部位酸值对于监控高温部位设备管线的腐蚀是十分必要的。监测物料的酸值,可以监测装置高温部位的腐蚀动态;可以通过监测物料的酸值及含硫量摸索确定酸值、含硫量之间关系与设备腐蚀的关联性,研究高酸、高硫原油的腐
蚀机理,指导设备防腐蚀工作。
5结论
1)在原油的酸性物质中,以环烷酸最为重要,含量也高,它约占原油酸性物质的90%。
2)环烷酸在原油中的分布规律十分特殊,中间馏分(250~500℃)环烷酸含量最高,而在低沸馏分和高沸馏分中环烷酸含量都比较低。
3)响环烷酸腐蚀的主要因素是温度、流速和原油硫含量。
4)加工高酸值原油的炼厂,其蒸馏装置的高温部位腐蚀严重。腐蚀主要发生在高温部位的设备和管线,例如常压炉、减压炉的炉出口管弯头,炉出口阀门,转油线高速段和低速段、常压塔和减压塔的进料蒸发段、塔璧、塔盘、主梁、支梁等部位。
5)加工高酸值原油易引起柴油组分和减压蜡
油酸值偏高,从而造成柴油酸值和润滑油中和值偏高。6)防止环烷酸腐蚀的有效措施较多,其中混炼是防止高温环烷酸腐蚀的最有效而且是低成本的方法,它不需要额外的支出或投资,只需要对计划和运行进行合理安排,把混合原油酸值降低到小于0.5 mgKOH/g时,就可以有效地控制环烷酸腐蚀。
参考文献
1 祝馨怡. 田松柏. 高酸原油的加工方法研究进展. 石油化工腐蚀与防护,2005,22(1):7
2 吕效平. 韩萍芳. 重质高酸原油及其油品脱环烷酸工艺研究进展. 化工进展,1999,(4):54~58
3 王会东. 贾春耀. 直馏柴油中石油酸的分离与回收工艺的研究. 石油炼制与化工,1995,26(2):25~28
4 周培荣等. 加工高硫原油与高酸原油的防腐蚀技术. 全面腐蚀控制,2003,17(3):4~5
5 张勇. 加工高硫高酸原油设备的腐蚀分析与防腐措施. 清洗世界,2005,21(7):25~26
6 娄世松. 加工低硫高酸值原油防腐蚀成套技术. 石油化工腐蚀与防护,2002,19(2):8~9
7 武文广. 试论我厂加工高酸值原油的技术措施. 化工设备与管道,2003,40(3):53~54
8 徐英. 高酸值原油加工过程中存在的问题与对策. 石油化工腐蚀与防护,2003,20(2):1~5
9 刘小辉. 抓好防腐蚀技术工作延长装置开工周期. 石油化工腐蚀与防护,2000,17(4):1~3
加工高酸值原油的方法及防腐措施
加工高酸值原油的方法及防腐措施 随着高酸、高硫原油加工量的不断增加,炼油厂设备腐蚀日趋严重,已影响到炼油装置的安全、稳定、长周期、满负荷、优质生产。重油装置高温部位通常采用耐腐蚀材料,而蒸馏塔顶低温轻油部位受HCl-H2S-H2O体系的腐蚀,若采用奥氏体不锈钢,则存在Cl-应力腐蚀开裂的问题,因此一般采用化学注剂防腐工艺,即用中和剂降低冷凝系统的酸性物,用缓蚀剂使它在金属表面形成一层保护膜。传统的做法是采用注氨水的方法中和冷凝液中的酸性物,但露点部位的腐蚀仍会发生。 早在八十年代初我国许多炼油厂即开始了“一脱四注”并取得了较好的效果。随着时间的推移,在美国到九十年代初已约有80%的炼油厂把注氨改为注有机胺,我国在九十年代已陆续有些炼油厂改注有机胺,有的还同时加入缓蚀剂和分散剂等助剂。近几年来,随着工艺防腐理论的发展和技术的进步,国内外炼厂开始逐渐采用一剂多用的中和缓蚀剂技术来控制塔顶冷凝系统的腐蚀。性能良好的中和缓蚀剂既具有中和塔顶冷凝区酸性物的作用,又具有在金属表面成膜的功效,能解决露点腐蚀及铵盐沉积造成的结垢和二次腐蚀问题。 二、防止腐蚀措施 1. 脱盐。目前大多数炼油厂采用二级脱盐工艺,个别厂已采用三级脱盐工艺,使脱后原油含盐达到石化企业规定标准——小于3mgNaCl/L。但是在这里需说明一点,即目前的脱盐工艺仅仅是脱除原油中可溶于水的无机盐类,由于其中以碱金属及碱土金属的氯化物为主,故将氯化钙、氯化镁和氯化钠均换算为氯化钠含量并以mgNaCl/L表示,但其中的盐并不一定都是氯化物,也可能是硫酸盐,碳酸盐和石油酸盐,如已发现在新疆及华北一些原油中含有较高的石油酸钙,而氯化物也不一定都是无机氯化物,如上所述原油中还含有氯代烃,这些有机金属化合物和氯代烃,目前的脱盐工艺是不能将其脱除的,它们将带入常压塔,金属盐类将浓缩于渣油中,而氯代烃及硫化物则部份分解进入塔顶馏分而造成腐蚀。 2. 注入中和剂控制塔顶pH值。目前一些炼油厂曾采用注氨中和塔顶酸性物质,控制塔顶pH值在6-7.5之间,由于氨不能进入塔回流线以下,NH4Cl会堵塞塔盘、降液管,引起垢下腐蚀,而且由于氨的易挥发性,也不易控制中和pH值在理想范围内,随后有人采用单一的中和剂(醇胺、吗啉等),或将其与氨混合使用都未能得到令人满意的结查。 3. 多组份胺类复合中和剂较用单一的胺或氨为好。我们认为若将多组份复合胺类中和剂与缓蚀剂复配混合使用更好,首先这种直链和环状胺类作为中和剂在塔顶中和时能提供理想的,较窄的pH值控制范围,其次中和形成的盐在油中有足够的溶解性,减少了形成沉淀的倾向。对于露点以上的腐蚀速率,则应要据塔顶总的蒸汽量的多少,适当增加剂的注入量。 4. 控制塔顶温度,减少塔顶蒸汽凝水量,亦可达到减缓腐蚀的目的。通过上述分析可知当塔顶温度在100℃或更低时,水蒸汽较易冷凝成水,HCl、H2S溶于其中形成酸性腐蚀介质而引起腐蚀。因此,适当提高塔顶温度使其达到110℃左右,减少塔顶冷凝水量,则有利于缓解腐蚀速度。 5. 常压塔顶注水不仅可以促使中和剂和缓蚀剂同塔顶的酸性气体较好的混合并将酸性组份稀释,而且可将塔板上沉积的盐垢冲洗除去而减少垢下腐蚀。新鲜水注入塔内,盐即溶于水,含盐的水可经馏出口抽出。 6. 加强工艺控制分析,做到心中有数。 ⑴加强电脱盐装置脱后盐含量分析,尤其有机氯含量的变化。 ⑵定期监测,控制常压塔顶物流pH值,建议安装pH在线测定系统。 ⑶在常压塔馏出线出口使用电阻探针或挂片进行在线监测,并定期对塔进行壁厚测量。 ⑷定期对常压塔顶冷凝水进行Fe2+、Fe3+、Cl-、S2-进行分析,判断腐蚀情况,并根据检测结果随时调整缓蚀剂、中和剂的加入量。
石油炼化常用的七种工艺流程
石油炼化七种工艺流程 从原油到石油要经过多种工艺流程,不同的工艺流程会将同样的原料生产出不同的产品。 从原油到石油的基本途径一般为: ①将原油先按不同产品的沸点要求,分割成不同的直馏馏分油,然后按照产品的质量标准要求,除去这些馏分油中的非理想组分; ②通过化学反应转化,生成所需要的组分,进而得到一系列合格的石油产品。 石油炼化常用的工艺流程为常减压蒸馏、催化裂化、延迟焦化、加氢裂化、溶剂脱沥青、加氢精制、催化重整。 (一)常减压蒸馏 1.原料: 原油等。 2.产品: 2.石脑油、粗柴油(瓦斯油)、渣油、沥青、减一线。 3.基本概念: 常减压蒸馏是常压蒸馏和减压蒸馏的合称,基本属物理过程:原料油在蒸馏塔里按蒸发能力分成沸点范围不同的油品(称为馏分),这些油有的经调合、加添加剂后以产品形式出厂,相当大的部分是后续加工装置的原料。 常减压蒸馏是炼油厂石油加工的第一道工序,称为原油的一次加工,包括三个工序:a.原油的脱 盐、脱水;b.常压蒸馏;c.减压蒸馏。 4.生产工艺: 原油一般是带有盐份和水,能导致设备的腐蚀,因此原油在进入常减压之前首先进行脱盐脱水预处理,通常是加入破乳剂和水。 原油经过流量计、换热部分、沏馏塔形成两部分,一部分形成塔顶油,经过冷却器、流量计,最后进入罐区,这一部分是化工轻油(即所谓的石脑油);一部分形成塔底油,再经过换热部分,进入常压炉、常压塔,形成三部分,一部分柴油,一部分蜡油,一部分塔底油;剩余的塔底油在经过减压炉,减压塔,进一步加工,生成减一线、蜡油、渣油和沥青。 各自的收率:石脑油(轻汽油或化工轻油)占1%左右,柴油占20%左右,蜡油占30%左右, 渣油和沥青约占42%左右,减一线约占5%左右。 常减压工序是不生产汽油产品的,其中蜡油和渣油进入催化裂化环节,生产汽油、柴油、煤油等成品油;石脑油直接出售由其他小企业生产溶剂油或者进入下一步的深加工,一般是催化重整生产溶剂油或提取萃类化合物;减一线可以直接进行调剂润滑油。 5.生产设备: 常减压装置是对原油进行一次加工的蒸馏装置,即将原油分馏成汽油、煤油、柴油、蜡油、渣油等组分的加工装置。原油蒸馏一般包括常压蒸馏和减压蒸馏两个部分。 a.常压蒸馏塔 所谓原油的常压蒸馏,即为原油在常压(或稍高于常压)下进行的蒸馏,所用的蒸馏设备叫做原油 常压精馏塔(或称常压塔)。 常压蒸馏剩下的重油组分分子量大、沸点高,且在高温下易分解,使馏出的产品变质并生产焦炭,破坏正常生产。因此,为了提取更多的轻质组分,往往通过降低蒸馏压力,使被蒸馏的原料油沸点范围降低。这一在减压下进行的蒸馏过程叫做减压蒸馏。
高酸原油
本世纪以来,随着国际原油价格的一路攀升,国内许多炼油厂在成本压力下开始炼制价格较低的高酸值原油,设备防环烷腐蚀问题也同时提到议事日程。 腐蚀监测技术是掌握设备腐蚀状态的有效手段,炼制高酸值原油设备的腐蚀程度可以通过不同的腐蚀监测方法进行跟踪,从而指导生产的安全运行。 l 环烷酸腐蚀彰晌因素 影响环烷酸高温腐蚀的主要因素有原油的总酸值(TAN)、温度、硫含量、流速和设备材质等。物料的物性、流动状态、气液相状态、压力及物料中环烷酸盐等也会间接影响环烷酸腐蚀速率的大小。 1。1 酸值 酸值是影响环烷酸高温腐蚀最主要的因素。一般认为当原油的TAN大子0。5 mgKOH/g时,就存在环烷酸腐蚀,且TAN值越高,腐蚀越严重。由于TAN 值只代表整体酸性(包括环烷酸以外的酸性),而油品中环烷酸是混合酸,沸点也不同,因此,对设备的某一具体位置来说,工艺物料中的真实酸值才真正反映其腐蚀性。这一事实对腐蚀监测有一定的指导意义,实施腐蚀监测之前要了解环烷酸在各种馏分中的分布情况。 1。2 温度(l~3] 温度也是影响环烷酸高温腐蚀的主要因素,在177℃就能发现环烷酸的腐蚀现象。在生产实践中,当温度达到232℃以上时,碳钢的腐蚀速率比较明显,随着温度升高,腐蚀速率加快。在一定的酸值下,温度每上升55.5℃,环烷酸对碳钢和低合金钢的腐蚀速率增加3倍。当温度在370℃左右时环烷酸腐蚀最严重,超过400℃时,由于环烷酸开始热分解,腐蚀速率下降。 生产实践中,腐蚀速率随温度的变化还受到高温硫腐蚀的影响。环烷酸腐蚀有两个显著的温度区,第一是274℃左右的碱三线蜡油,第二是345~385℃的常压塔进料段、常底、减四线、减压塔进料和减压塔底。 l。3 流速阳[4~5] 流速和流态是影响环烷酸腐蚀非常重要的因素。在高温及高流速下,酸值在很低水平(0.3KOHmg/g)的油液,比高酸值(1.5~1。8 KOHmg/g)的油液更有腐蚀性。实践表明在炼油设备的弯头、三通和泵中产生的湍流会加速设备的腐蚀。如当气量大于60%,蒸汽流速大于60 m/s的射流处,腐蚀最严重。在高流速条件下,某些设备(如炉管、弯头及管线)的腐蚀速率可增大两个数量级。1.4 硫含量【1~5】 原油中不同类别的硫化物和环烷酸之间的相互作用十分复杂,可增强也可减弱原油的腐蚀性。原油中的硫化物在高温下会释放出H2S,H2S与铁反应生成硫化亚铁覆盖在钢铁表面形成保护膜。H2S还能与环烷酸铁反应生成环烷酸。 在高温下,环烷酸腐蚀和硫腐蚀相互影响,高硫含量能抑制环烷酸腐蚀,Craig 就提出了用环烷酸腐蚀指数(NACI)的概念来判断腐蚀类型,用试样在腐蚀介
石油加工工程1
《石油炼制工程1》综合复习资料 第一章绪论 略 第二章石油的化学组成 一.判断对错。 1.天然石油主要是由烷烃、烯烃、环烷烃和芳香烃组成。 2.我国石油馏分中的环烷烃几乎都是六员环。 3.石油中的胶质能溶于正庚烷,而沥青质则不能。 4.石油中的含硫、氮、氧化合物,对所有石油产品均有不利影响,应在加工过程中除去。 5. 石油馏分就是石油产品。 6.对同一种原油,随其馏分沸程升高,烃类、非烃类及微量金属的含量将逐渐升高。 7.各种烃类碳氢原子比大小顺序是:烷烃≈环烷烃<芳香烃 8.原油中含有各种烃类化合物。 9.从分子结构上来看,石蜡和微晶蜡没有本质区别。 二.填空题 1.石油中的元素以、元素为主。根据的差别可将原油切割成若干馏分,200~350℃馏分油称为,>500℃馏分油称为。原油的直馏馏分是指,其中主要含有、、烃类和、、非烃类,原油及其直馏馏分中一般不含有烃。 2.石油中的含硫化合物根据其化学活性可划分为硫化物和硫化物。 3.常温下为固态的烃类在石油中通常处于状态,随温度降低会并从石油中分离出来,工业上将分离得到的固态烃称为。 4.石油馏分的结构族组成概念中,三个基本的结构单元是、和。5.石油中的非烃化合物主要有、、和。6.石油中的环烷酸在℃馏分中的含量最高。
7.石油中的元素以和元素为主,原油以及直馏馏分油中一般不含。8.原油的相对密度一般介于 g/cm3。 9.做族组成分析时,一般将渣油分成、、和。10.胶质在原油中形成溶液,沥青质在原油中形成溶液。 三.简答题 1.与国外原油相比较,我国的原油有哪些主要特点? 2.描述石油馏分烃类组成的方法有哪些?各有什么特点? 3.什么叫石油馏分?什么叫分馏?什么叫直馏馏分? 4.含硫化合物对石油加工及产品应用有哪些影响? 5.简述各种非烃化合物在石油中的分布规律。 第三章石油及油品的物理性质 一.判断对错。 1.石油馏分的沸程就是平均沸点。 2.石油馏分的比重指数(API0)大,表示其密度小。 3.石油馏分的特性因数大,表示其烷烃含量高。 4.石油馏分的粘度指数大,表示其粘度大。 5.馏分油及油蒸汽的粘度均随温度的升高而减小。 6.轻质油品的蒸汽压大,故其闪点、燃点低,自燃点也低。 7.石油馏分的蒸汽压不仅与温度有关,还与汽化率有关。 8.石油馏分的分子质量是指其中各组分的分子质量之和。 9.对同一轻质油品,其浊点、结晶点和冰点的关系为浊点>结晶点>冰点。 10.分子量大小相近的烷烃、环烷烃和芳香烃,粘度最高的是烷烃。 11.粘度大的油品其粘温性能好。 12.同一油品的雷德蒸汽压一般比真实蒸汽压要大。 13.特性因数、粘重常数、相关指数、特征参数都可以表征油品的化学组成。
石油炼化常用工艺流程
石油炼化常用工艺流程 (一)常减压: 1、原料:原油等; 2、产出品:石脑油、粗柴油(瓦斯油)、渣油、沥青、减一线; 3、生产工艺: 第一阶段:原油预处理 原油预处理:原油一般是带有盐份和水,能导致设备的腐蚀,因此原油在进入常减压之前首先进行脱盐脱水预处理,通常是加入破乳剂和水。 原油经过流量计、换热部分、沏馏塔形成两部分,一部分形成塔顶油,经过冷却器、流量计,最后进入罐区,这一部分是化工轻油(即所谓的石脑油);一部分形成塔底油,再经过换热部分,进入常压炉、常压塔,形成三部分,一部分柴油,一部分蜡油,一部分塔底油; 剩余的塔底油在经过减压炉,减压塔,进一步加工,生成减一线、蜡油、渣油和沥青。 各自的收率:石脑油(轻汽油或化工轻油)占1%左右,柴油占20%左右,蜡油占30%左右,渣油和沥青约占42%左右,减一线约占5%左右。 常减压工序是不生产汽油产品的,其中蜡油和渣油进入催化裂化环节,生产汽油、柴油、煤油等成品油;石脑油直接出售由其他小企业生产溶剂油或者进入下一步的深加工,一般是催化重整生产溶剂油或提取萃类化合物;减一线可以直接进行调剂润滑油; 4、常减压设备: 常压塔、减压塔为常减压工序的核心设备尤其是常压塔,其也合称蒸馏塔,两塔相连而矗,高瘦者为常压塔,矮胖的为减压塔 120吨万常减压设备评估价值4600万元。 (二)催化裂化: 催化裂化是最常用的生产汽油、柴油生产工序,汽油柴油主要是通过该工艺生产出来。这也是一般石油炼化企业最重要的生产的环节。 1、原料:渣油和蜡油 70%左右-------,催化裂化一般是以减压馏分油和焦化蜡油为原料,但是随着原油日益加重以及对轻质油越来越高的需求,大部分石
几种重质高酸原油的性质
几种重质高酸原油的性质 1、前言 随着原油的不断勘探和开发,高酸值原油被不断的发现和开采,该类原油的主要特点是密度大、酸值高、粘度大、胶质及沥青质含量高、重金属含量高。其加工难度主要体现在①酸值高,对设备及管线腐蚀严重;②常压石脑油、煤油、柴油的收率偏低;③蜡油酸值高、难裂化、做催化原料时轻油收率偏低;④密度大、钙含量较高,对电脱盐带来困难。根据其特点,针对常减压拔出率较高的高酸值原油,应先采用常减压装置进行分馏,减压渣油通过延迟焦化工艺处理。针对常压拔出率较高,减压拔出率较低的高酸值原油。可以只进行常压分馏、常压渣油直接进延迟焦化装置处理。针对常压拔出率较低的重质高酸值原油,如辽河超稠油、苏丹稠油,建议直接采用延迟焦化技术进行加工。采用延迟焦化工艺直接加工原油,可充分利用焦化加热炉出口温度高的特点,使环烷酸分解,降低产品的酸值;可利用分馏塔底高温油气的热量使原油中的轻组分闪蒸,节省了常压炉;可利用焦化装置的低温热量加热原油,节省能耗。本文就利用延迟焦化技术直接加工重质高酸值原油进行探讨。 2、几种重质高酸原油的性质
3、原油的预处理 重质高酸原油直接作为焦化原料时必须进行预处理。应对原油进行脱水、脱金属、脱酸和轻组份预闪蒸处理。原油的脱水、脱盐相对脱酸、脱钙而言是相对容易的。采用常规的电脱盐技术均可使脱后原油的NaCl含量小于3mg/l,水含量小于0.3%,而原油中的钙多为油溶性的环烷酸钙或其它油溶性钙化合物,有机钙能作为乳化剂使油水混合形成稳定的乳化液,造成油水分离困难和电脱盐处理过程不稳定,增加电耗和运行成本,采用一般的电脱盐方法也难以脱除。 目前国内外的脱钙技术主要有:络合萃取脱钙、加氢催化脱钙、膜分离脱钙、树脂脱钙、生物脱钙等。络合萃取脱钙应用较多,该技术的关键是选择合适的脱钙剂,一般采用实验手段进行筛选,脱钙剂能和有机钙化合物反应,生成络合钙化合物和有机酸,络合钙化合物能溶解于水和脱盐污水一起排出,达到脱除原油中钙的目的。目前国内常用的脱钙剂很多,主要有JA-024、JP-08、SXT301、SXT302、KR-1等。原油的性质不同,采用的脱钙剂也不同。脱钙剂的注入量和原油中的钙含量及脱钙率有关。原油中钙含量多,脱钙率高,由要求注入的脱钙量就大。电脱盐的每级脱钙率一般为60~80%。采用几级电脱盐和原油中的钙含量及对脱后原油钙含量的要求有关,根据焦化加热炉的设计,其进料中的盐含量应低于10ppm,钙含量应低于50ppm。盐及钙含量太高会导致炉管结焦速度加快,另外焦炭中灰分含量一般要求小于0.3%,为满足焦炭产品对灰分的要求,原料中的金属含量不应大于500ppm。超稠重质原油的电脱盐,应考虑电脱盐的操作温度和油水的分离,原油和水的密度均随温度的升高而降低,但油和水的体积膨胀系数不同,降低的幅度也不同,经过加热二者的密度差会发生变化。电脱盐的温度应选择水和油的密度差较大时的温度点,以有利于水的沉降。当在100~150℃之间油的密度大于水的密度或水油密度差较小时,应考虑在原油中掺混一定比例的轻油才可进行电脱盐处理。掺混的轻油可以是汽油和柴油,掺入的轻油比例以达到在特点的温度下,原油的密度低于水的密度并保证电脱盐的油水分离为准。对于焦化装置可直接掺入焦化汽油、焦化分馏塔顶循环油或焦化柴油。 原油中的轻组份及脱后原油中的水,在进焦化分馏塔前应尽可能的脱除,当轻组份含量较少时,可以通过调整换热流程,提高原油进原料缓冲罐的温度,使原油
原油蒸馏的工艺流程精编WORD版
原油蒸馏的工艺流程精 编W O R D版 IBM system office room 【A0816H-A0912AAAHH-GX8Q8-GNTHHJ8】
原油蒸馏的工艺流程 第一节石油及其产品的组成和性质 一、石油的一般性状、元素组成、馏分组成 (一)石油的一般性状 石油是一种主要由碳氢化合物组成的复杂混合物。世界各国所产石油的性质、外观都有不同程度的差异。大部分石油是暗色的,通常呈黑色、褐色或浅黄色。石油在常温下多为流动或半流动的粘稠液体。相对密度在0.8~0.98g/cm3之间,个别的如伊朗某石油密度达到1.016,美国加利福尼亚州的石油密度低到0.707。 (二)石油的元素组成 石油的组成虽然及其复杂,不同地区甚至不同油层不同油井所产石油,在组成和性质上也可能有很大的差别。但分析其元素,基本上是由碳、氢、硫、氧、氮五种元素所组成。其中碳、氢两中元素占96%~99%,碳占到83%~87%,氢占11%~14%。其余的硫、氧、氮和微量元素含量不超过1%~4%。石油中的微量元素包括氯、碘、磷、砷、硅等非金属元素和铁、钒、镍、铜、铅、钠、镁、钛、钴、锌等微量金属元素。 (三)石油的馏分组成 石油的沸点范围一般从常温一直到500℃以上,蒸馏也就是根据各组分的沸点差别,将石油切割成不同的馏分。一般把原油从常压蒸馏开始镏出的温度(初馏点)到180℃的轻馏分成为称为汽油馏分,180℃~350℃的中间馏分称为煤柴油馏分,大于350℃的馏分称为常压渣油馏分。 二、石油及石油馏分的烃类组成
石油中的烃类包括烷烃、环烷烃、芳烃。石油中一般不含烯烃和炔烃,二次加工产物中常含有一定数量的烯烃。各种烃类根据不同的沸点范围存在与对应的馏分中。 三、石油中的非烃化合物 石油的主要组成使烃类,但石油中还含有相当数量的非烃化合物,尤其在重质馏分油中含量更高。石油中的硫、氧、氮等杂元素总量一般占1%~4%,但石油中的硫、氧、氮不是以元素形态存在而是以化合物的形态存在,这些化合物称为非烃化合物,他们在石油中的含量非常可观,高达10%~20%。 (一)含硫化合物(石油中的含硫量一般低于0.5%) 含硫化合物在石油馏分中的分布一般是随着石油馏分的沸点升高而增加,其种类和复杂性也随着馏分沸点升高而增加。石油中的含硫化合物给石油加工过程和石油产品质量带来许多危害。 1、腐蚀设备 在石油炼制过程中,含硫化合物受热分解产生H 2 S、硫醇、元素硫等活性硫化物,对 金属设备造成严重的腐蚀。石油中通常还含有MgCl 2、CaCl 2 等盐类,含硫含盐化合物相互 作用,对金属设备造成的腐蚀将更为严重。石油产品中含有硫化物,在储存和使用过程中 同样腐蚀设备。含硫燃料燃烧产生的SO 2、SO 3 遇水后生成H 2 SO 3 、H 2 SO 4 会强烈的腐蚀金属 机件。 2、影响产品质量 硫化物的存在严重的影响油品的储存安定性,是储存和使用中的油品容易氧化变质,生成胶质,影响发动机的正常工作。
油脂精炼
油脂精炼 主讲人张传生 一、油脂精炼意义 增强油脂储藏稳定性 改善油脂风味 改善油脂色泽 为油脂深加工制品提供原料 二、毛油组成成分毛油中绝大部分为混酸甘油脂的混合物,即油脂,只含有极少量的杂质。这些杂质虽然量小,但在影响油脂品质和稳定性上却“功不可没”。悬浮杂质:泥沙、料胚粉末、饼渣水分胶溶性杂质:磷脂、蛋白质、糖以及它们的低级分解物脂溶性杂质:游离脂肪酸(FFA)、甾醇、生育酚、色素,脂肪醇,蜡其它杂质:毒素、农药 三、脱胶 油脂胶溶性杂质不仅影响油脂的稳定性,而且影响油脂精炼和深度加工的工艺效果。油脂在碱炼过程中,会促使乳化,增加操作困难,增大炼耗和辅助剂的耗用量,并使皂脚质量降低;在脱色过程中,增大吸附剂耗用量,降低脱色效果。脱除毛油中胶溶性杂质的过程称为脱胶。 我们在实际生产中使用的方法是特殊湿法脱胶,是水化脱胶方法的一种。 油脂水化脱胶的基本原理是利用磷脂等胶溶性杂质的亲水性,将一定量电解质溶液加入油中,使胶体杂质吸水、凝聚后与油脂分离。其中胶质中以磷脂为主。在水分很少的情况下,油中的磷脂以内盐结构形式溶解并分散于油中,当水分增多时,它便吸收水分,体积增大,胶体粒子相互吸引,形成较大的胶团,由于比重的差异,从油中可分离出来。 影响水化脱胶的因素: 水量/操作温度/混合强度与作用时间/电解质/电解质在脱胶过程中的主要作用中和胶体分散相质点的表面电荷,促使胶体质点凝聚。磷酸和柠檬酸可促使非水化磷脂转化为水化磷脂。 磷酸、柠檬酸螯合、钝化并脱除与胶体分散相结合在一起的微量金属离子,有利于精炼油气、滋味和氧化稳定性的提高。 使胶粒絮凝紧密,降低絮团含油,加速沉降。 四、脱酸 植物油脂中总是有一定数量的游离脂肪酸,其量取决于油料的质量。种籽的不成熟性,种籽的高破损性等,乃是造成高酸值油脂的原因,尤其在高水分条件下,对油脂保存十分不利,这样会使得游离酸含量升高,并降低了油脂的质量,使油脂的食用品质恶化。脱酸的主要方法为碱炼和蒸馏法。蒸馏法又称物理精炼法,应用于高酸值、低胶质的油脂精炼。这里主要介绍碱炼法。 碱炼脱酸的作用 烧碱能中和粗油中的绝大部分游离脂肪酸,生成的钠盐在油中不易溶解,成为絮状物而沉降。生成的钠盐为表面活性剂,可将相当数量的其他杂质也带入沉降物,如蛋白质、粘液质、色素、磷脂及带有羟基和酚基的物质。甚至悬浮固体杂质也可被絮状皂团携带下来。因此,碱炼具有脱酸、脱胶、脱固体杂质和脱色素等综合作用。 烧碱和少量甘三酯的皂化反应引起炼耗的增加。因此,必须选择最佳的工艺操作条件,以获得碱炼油的最高得率。 影响碱炼的因素 1、碱及其用量,理论碱量算法:NaOH(Kg)= 7.13 ×10-4×油重×酸值 2、碱液浓度 (1)碱液浓度的确定原则。
石油炼化公司的各个装置工艺的流程图大全及其简介
炼化公司的各个装置工艺的流程图大全及其简介 从油田送往炼油厂的原油往往含盐(主要是氧化物)带水(溶于油或呈乳化状态),
可导致设备的腐蚀,在设备内壁结垢和影响成品油的组成,需在加工前脱除。电脱盐基本原理: 为了脱掉原油中的盐份,要注入一定数量的新鲜水,使原油中的盐充分溶解于水中,形成石油与水的乳化液。 在强弱电场与破乳剂的作用下,破坏了乳化液的保护膜,使水滴由小变大,不断聚合形成较大的水滴,借助于重力与电场的作用沉降下来与油分离,因为盐溶于水,所以脱水的过程也就是脱盐的过程。 CDU装置即常压蒸馏部分 常压蒸馏原理:
精馏又称分馏,它是在精馏塔内同时进行的液体多次部分汽化和汽体多次部分冷凝的过程。 原油之所以能够利用分馏的方法进行分离,其根本原因在于原油内部的各组分的沸点不同。 在原油加工过程中,把原油加热到360~370℃左右进入常压分馏塔,在汽化段进行部分汽化,其中汽油、煤油、轻柴油、重柴油这些较低沸点的馏分优先汽化成为气体,而蜡油、渣油仍为液体。 VDU装置即减压蒸馏部分
减压蒸馏原理: 液体沸腾必要条件是蒸汽压必须等于外界压力。 降低外界压力就等效于降低液体的沸点。压力愈小,沸点降的愈低。如果蒸馏过程的压力低于大气压以下进行,这种过程称为减压蒸馏。 轻烃回收装置是轻烃的回收设备,采用成熟、可靠的工艺技术,将天然气中比甲烷或乙烷更重的组分以液态形式回收。
RDS即渣油加氢装置,渣油加氢技术包含固定床渣油加氢处理、切换床渣油加氢处理、移动床渣油加氢处理、沸腾床渣油加氢处理、沸腾床渣油加氢裂化、悬浮床渣油加氢裂化、渣油加氢一体化技术及相应的组合工艺技术。
油脂酸值的测定
油脂酸值的测定 酸值(A.V.)是评定油脂中所含游离脂肪酸多少的量度。其定义为:中和1g油脂中游离脂肪酸所需氢氧化钾的质量(mg),酸值的单位是mg KOH/g。 油脂酸值得大小瘦很多条件的影响,如原料的质量好坏(成熟的或未霉变的,其酸值较小);原料的组成特性(米糠及棕榈果等中含义解酯酶,其分解油脂产生的游离脂肪酸);油脂在储存、加工、运输期间的含水分、杂质的多少;与温度、空气、光照等因素也有关系。 酸值不能直接表示油脂中游离脂肪酸的百分率(F.F.A%),但能表示油脂中游离脂肪酸含量的高低,所以酸值是评定油脂品质好次、油脂精炼程度的重要指标。同时,也是油脂工厂碱炼脱酸时计算加碱量的理论依据。 目前,对于不同级别的食用油脂,其酸值都有不同的标准规定(见附录I)。 油脂酸值的表示,国外大多以游离脂肪酸的质量分数表示,我国一直延用1g油脂消耗氢氧化钾的质量(mg)表示。 酸值的测定常用酸、碱中和滴定法。对于酸值高、颜色深、不易中和滴定的油脂,也可应用pH计法测定。 (1)测定原理用中性乙醚—乙醇的混合溶剂溶解油脂试样后,再用氢氧化钾标准溶液滴定油脂中的游离脂肪酸,根据消耗氢氧化钾标准溶液的物质的量和油脂的质量,计算出算酸值的大小。
反应过程为 RCOOH+KOH→RCOOK+H2O (2)仪器分析天平(精度0.0001g)、250mL锥形瓶、碱式滴定管(10mL,最小刻度0.05mL)。 (3)试剂本方法所列试剂均为分析纯,水位蒸馏水。 ①中性乙醚—95%乙醇溶剂:乙醚—95%乙醇(2+1)混合;临用前每10mL混合溶剂中加入0.3mL酚酞指示剂,用氢氧化钾标准溶液准确中和。 ②0.05mol/L氢氧化钾标准溶液。 ③10g/L酚酞指示剂溶液:用95%(体积)乙醇配制。 (4)操作方法 ①试样的准备:对于液态样品,充分混匀备用;对于固态样品,缓慢升温使其熔化成液态,充分混匀备用。 ②称取试样:准确称取试样3.00-5.00g于250mL锥形瓶中。 ③测定:加入50mL预先中和过的中性乙醚-95%乙醇混合溶剂溶解试样,再加入2-3滴酚酞指示剂,然后用氢氧化钾标准溶液边摇动边滴定,至出现微红色且在0.5min内不褪色即为终点。 (5)结果计算 A.V.= 式中V——滴定试样所消耗的氢氧化钾标准溶液的体积,mL; C——氢氧化钾标准溶液的浓度,mol/L; m——试样的质量,g
高酸值原油加工综述学习资料
高酸值原油加工综述
高酸值原油加工综述[] 高酸值原油加工综述: 介绍了原油中石油酸的分布规律、环烷酸腐蚀机理及影响环烷酸腐蚀的因素。综述了近年来高酸原油的加工方法及国内一些炼油厂炼制高酸值原油情况及防护措施。重点介绍了茂名分公司炼制高酸值原油的情况,分析了高酸值原油各馏分的酸分布规律,提出了炼制高酸值原油的对策。 随着原油的不断开发利用,重质原油的产量越来越大,其密度、粘度及酸值也随之上升。近几年来,全球高酸原油的产量每年约增加0.3%。2001年,酸值(TAN)大于1 mgKOH/g的高酸原油的产量占全球原油总产量的5.0%,到2006年将达到5.5%。国内含酸原油的品种和数量也呈上升趋势。由于含酸原油在加工过程中会对生产设备造成较大的腐蚀,因此造成国际和国内市场上高酸原油供过于求,价格偏低。在原油采购成本占总成本90%的情况下,适当采购低酸值原油对经济效益具有较大的贡献。因此,如何进行高酸值原油的加工就显得十分重要。 1、原油中石油酸及其分布规律 原油酸值的大小反映了原油中环烷酸、脂肪酸以及酚类等酸性氧化物(总称石油酸)的多少。原油的酸值是1g原油中各种酸性组分所消耗的KOH的总量,以mgKOH/g表示。原油酸性物质除了环烷酸外,还有脂肪酸、芳香酸、无机酸、硫醇、硫化氢和苯酚等。当原油酸值大于0.5 mgKOH/g即能引起设备腐蚀,故通常将酸值大于0.5 mgKOH/g的原油称之为高酸值原油。在原油的酸性物质中,以环烷酸最为重要,含量也高,它约占原油酸性物质的90%。
环烷酸是一种带有五元或六元环的十分复杂的羧酸混合物,相对分子量变化范围很大,但以300~400居多。低分子量的环烷酸在水中有一定溶解度,而高分子量环烷酸几乎不溶于水。环烷酸在原油中的分布规律十分特殊,中间馏分(250~500℃)环烷酸含量最高,而在低沸馏分和高沸馏分中环烷酸含量都比较低。也就是说环烷酸含量一般从煤油馏分开始逐渐增加,至柴油馏分其含量几乎达到最高峰,然后有所下降。 2、加工高酸值原油引起的腐蚀 加工高酸值原油的炼厂,设备的腐蚀主要是由环烷酸引起的。其蒸馏装置的高温部位腐蚀严重,腐蚀主要发生在高温部位的设备和管线,例如常压炉、减压炉的炉出口管弯头,炉出口阀门,转油线高速段和低速段、常压塔和减压塔的进料蒸发段、塔壁、塔盘、主梁、支梁等部位。环烷酸的腐蚀与硫腐蚀不同,它不是均匀腐蚀,而是局部腐蚀或点蚀,而且环烷酸腐蚀受酸值、温度、流速、介质、物态变化等多方面因素的影响,因此不容易检测。 2.1 环烷酸腐蚀机理 环烷酸在石油炼制过程中,随 原油一起被加热、蒸馏,并与其沸点相同的油品一起冷凝,而且溶于其中,从而造成该馏分对设备材料的腐蚀。目前,一般认为环烷酸腐蚀的反应机理如下: 2RCOOH+Fe→Fe(RCOO)2 +H2
固体酸预处理高酸值油脂降低酸值
固体酸预处理高酸值油脂降低酸值 曹崇江3 刘晓庚 周国信 (南京财经大学应用化学系 南京210003) 摘 要 通过沉淀、回流和浸渍分别制备了A l 、Ga 掺杂的S O 2-4/Zr O 2固体酸催化剂,利用该促进型固体酸催化剂酯化预处理高酸值油脂,考察了固体酸焙烧温度、醇油摩尔比等因素对酯化反应的影响。结果表明,该类 型固体酸对高酸值油脂具有良好的酯化反应活性,其中600℃焙烧的Ga 2O 3/S O 2-4 /Zr O 2在67℃下,醇与油摩尔比为30∶1,催化剂用量为4%,对初始酸值为32的油脂进行酯化反应,经8h 反应,油脂酸值降为411,有利于后续用碱性催化剂对处理后的油脂进行酯交换反应生成生物柴油。 关键词 固体酸,预处理酯化,酸值 中图分类号:O643 文献标识码:A 文章编号:100020518(2008)0520613204 2007205220收稿,2007208210修回 江苏省高校自然科学基金(07KJD530075),南京财经大学科研基金(B0613)资助项目 通讯联系人:曹崇江,男,博士,讲师;E 2mail:chongjiangcao@g mail .com;研究方向:催化,应用化学 生物柴油是利用动植物油催化合成的一种性质近似于柴油的新能源。由于其可再生,环境友好等 优点使得它成为一种矿物柴油的很好替代品,具有极大的应用前景[1,2]。目前,生物柴油最常用的生产 方法是采用碱性催化剂进行酯交换反应,但其对原料纯度比较敏感,只能以动植物油脂为原料,因此生 产成本很高,不利于推广应用。若将废油脂回收利用作为原料生产生物柴油将大大降低成本[3,4]。但废 油脂中含有大量游离脂肪酸,用碱性催化剂易发生皂化反应阻碍生物柴油的制取,Lepper 等[5]采用一个预处理步骤来减少游离脂肪酸的含量,即在H 2S O 4催化剂的存在下油脂中的脂肪酸与甲醇进行酯化反应,使油相酸值降低,再用碱性催化剂进行酯交换反应,但该过程在碱性催化剂进行酯交换反应之前,必须脱出油相中的H 2S O 4,遗留在油相中的H 2S O 4还需要加入过量的碱中和。 由于液体酸的缺陷,工业上迫切需要新型绿色环保催化剂来替代。固体酸由于其无腐蚀、无污染、 易分离的优点被认为是最有前途的催化剂,本实验室曾报道[6]过A l 、Ga 的掺杂能够显著提高S O 2-4/ Zr O 2固体酸的催化性能,在烷烃异构化反应中显示出较高的催化活性与稳定性。本文利用A l 、Ga 掺杂的S O 2- 4/Zr O 2固体酸作为催化剂,酯化预处理高酸值的油脂,考察了固体酸焙烧温度、醇油摩尔比对酯化反应的影响。1 实验部分 1.1 试剂和仪器 硝酸锆、氨水、硫酸铝、硫酸镓、无水甲醇、油酸、Na OH 均为分析纯试剂。市售大豆油和饭店收集的废油作为原料油。ST A 2409PC 型同步热分析仪(德国Netzsch 公司);AS AP 2010型比表面分析仪(美国M icr omeritics 公司)。 1.2 固体酸的制备 在剧烈搅拌下,将015mol/L 的Zr (NO 3)4溶液缓慢滴加到5mol/L 的氨水溶液中,用氨水将此悬浮液的pH 值调至9~10,然后在100℃油浴中回流24h,沉淀用去离子水反复过滤洗涤至pH =710。将(NH 4)2(S O 4)3、Ga 2(S O 4)3或A l 2(S O 4)3的水溶液按一定比例加入Zr (OH )4沉淀中,搅拌10h 后,于120℃下烘干,最后在不同的温度下焙烧3h,得到S O 2-4/Zr O 2、S O 2-4/Ga 2O 3/Zr O 2、S O 2- 4/A l 2O 3/Zr O 2,分别记为SZ 2X 、GSZ 2X 、ASZ 2X (X 表示样品的焙烧温度℃)。 第25卷第5期 应用化学Vol .25No .52008年5月 CH I N ESE JOURNAL OF APP L I E D CHE M I ST RY M ay 2008
石油炼制过程
分类 习惯上将石油炼制过程不很严格地分为三类过程:(1)一次加工(2)二次加工(3)三次加工。 炼厂总体工艺图如下
原油一次加工 把原油蒸馏分为几个不同的沸点范围(即馏分)叫一次加工;一次加工装置;常压蒸馏或常减压蒸馏。是将原油用蒸馏的方法分离成轻重不同馏分的过程,常称为原油蒸馏,它包括原油预处理、常压蒸馏和减压蒸馏。一次加工产品可以粗略地分为:①轻质馏分油(见轻质油),指沸点在约370℃以下的馏出油,如粗汽油、粗煤油、粗柴油等。②重质馏分油(见重质油),指沸点在370~540℃左右的重质馏出油,如重柴油、各种润滑油馏分、裂化原料等。③渣油(又称残油)。习惯上将原油经常压蒸馏所得的塔底油称为重油(也称常压渣油、半残油、拔头油等)。
原油二次加工(裂化、重整、精制和裂解) 二次加工过程:将一次加工得到的馏分再加工成商品油叫二次加工;二次加工装置:催化、加氢裂化、延迟焦化、催化重整、烃基化、加氢精制等。一次加工过程产物的再加工。主要是指将重质馏分油和渣油经过各种裂化生产轻质油的过程,包括催化裂化、热裂化、石油焦化、加氢裂化等。其中石油焦化本质上也是热裂化,但它是一种完全转化的热裂化,产品除轻质油外还有石油焦。二次加工过程有时还包括催化重整和石油产品精制。前者是使汽油分子结构发生改变,用于提高汽油辛烷值或制取轻质芳烃(苯、甲苯、二甲苯);后者是对各种汽油、柴油等轻质油品进行精制,或从重质馏分油制取馏分润滑油,或从渣油制取残渣润滑油等。 裂化 一是热裂化 就是完全依靠加热进行裂化。主要原料是减压塔生产中得到的含蜡油。通过热裂化,又可取得汽油、煤油、柴油等轻质油。但是,热裂化所得到的产品,其质量不够好 二是催化裂化 就是在裂化时不仅加热而且加入催化剂。由于催化剂就像人们蒸制馒头时加入酵母一样,能大大加快反应速度,所以,催化裂化比热裂化获得的轻质油多(汽油产率可达60%左右),而且产品的质量也比较好 三是加氢催化 就是在加入氢气的情况下进行催化裂化。这种方法的优点是使所得到的轻质油收率更高,质量更好,而且原料没有严格的要求,原油以至渣油都可以用;缺点是
原油管道输送方式及工艺流程
原油管道输送方式及工艺流程 一、组成 长距离输油管道由输油站和线路组成; 输油站就是给油流一定的能量(压力能和热力能),按所处位置分首站、中间站、末站; 中间站按任务不同分加热站、加压站、热泵站(加压、加热); 首站:输油管道起点的输油站,任务是接受(计量、储存)原油,经加压、加热向下一站输送; 输油管道终点的输油站称末站,接受来油和把油品输给用油单位,配有储罐、计量、化验及运转设施。 二、输送工艺 1、“旁接油罐”式输送工艺: 上站来油可进入泵站的输油泵也可同时进入油罐的输送工艺,油罐通过旁路连接到干线上,当本站与上下站的输量不平衡时,油罐起缓冲作用 特点; a 各管段输量可不等,油罐起缓冲作用; b 各管段单独成一水力系统,有利于运行调节和减少站间的相互影响; c 与“从泵到泵”相比,不需较高的自动调节系统,操作简单。 2、“从泵到泵” 输送工艺: 为密闭输送工艺,中间站不设缓冲罐,上站来油全部直接进泵
特点: a 可基本消除中间站的蒸发损耗; b整个管道成一个统一的水力系统,充分利用上站余压,减少节流,但各站要有可靠的自动调节和保护装置; c工艺流程简单。 三、输油站的基本组成 1、主生产区 (1)油泵房(输油泵机组、润滑、冷却、污油回收等系统);(2)加热系统(加热炉和换热器); (3)总阀室(控制和切换流程); (4)清管器收发室; (5)计量间(流量计及标定装置); (6)油罐区; (7)站控室; (8)油品预处理设施(热处理、添加剂、脱水等)。 2、辅助生产区 (1)供电系统(变、配、发电); (2)供热系统(锅炉房、燃料油系统、热力管网等); (3)给排水系统(水源、循环水、软化水、消防水等); (4)供风系统(仪表风、扫线用风); (5)阴极保护设施; (6)消防及警卫、机修化验、库房、办公后勤设施等。
高酸值原油加工综述
高酸值原油加工综述[] 高酸值原油加工综述: 介绍了原油中石油酸的分布规律、环烷酸腐蚀机理及影响环烷酸腐蚀的因素。综述了近年来高酸原油的加工方法及国内一些炼油厂炼制高酸值原油情况及防护措施。重点介绍了茂名分公司炼制高酸值原油的情况,分析了高酸值原油各馏分的酸分布规律,提出了炼制高酸值原油的对策。 随着原油的不断开发利用,重质原油的产量越来越大,其密度、粘度及酸值也随之上升。近几年来,全球高酸原油的产量每年约增加0.3%。2001年,酸值(TAN)大于1 mgKOH/g的高酸原油的产量占全球原油总产量的5.0%,到2006年将达到5.5%。国内含酸原油的品种和数量也呈上升趋势。由于含酸原油在加工过程中会对生产设备造成较大的腐蚀,因此造成国际和国内市场上高酸原油供过于求,价格偏低。在原油采购成本占总成本90%的情况下,适当采购低酸值原油对经济效益具有较大的贡献。因此,如何进行高酸值原油的加工就显得十分重要。 1、原油中石油酸及其分布规律 原油酸值的大小反映了原油中环烷酸、脂肪酸以及酚类等酸性氧化物(总称石油酸)的多少。原油的酸值是1g原油中各种酸性组分所消耗的KOH的总量,以mgKOH/g表示。原油酸性物质除了环烷酸外,还有脂肪酸、芳香酸、无机酸、硫醇、硫化氢和苯酚等。当原油酸值大于0.5 mgKOH/g即能引起设备腐蚀,故通常将酸值大于0.5 mgKOH/g的原油称之为高酸值原油。在原油的酸性物质中,以环烷酸最为重要,含量也高,它约占原油酸性物质的90%。 环烷酸是一种带有五元或六元环的十分复杂的羧酸混合物,相对分子量变化范围很大,但以300~400居多。低分子量的环烷酸在水中有一定溶解度,而高分子量环烷酸几乎不溶于水。环烷酸在原油中的分布规律十分特殊,中间馏分(250~500℃)环烷酸含量最高,而在低沸馏分和高沸馏分中环烷酸含量都比较低。也就是说环烷酸含量一般从煤油馏分开始逐渐增加,至柴油馏分其含量几乎达到最高峰,然后有所下降。 2、加工高酸值原油引起的腐蚀 加工高酸值原油的炼厂,设备的腐蚀主要是由环烷酸引起的。其蒸馏装置的高温部位腐蚀严重,腐蚀主要发生在高温部位的设备和管线,例如常压炉、减压炉的炉出口管弯头,炉出口阀门,转油线高速段和低速段、常压塔和减压塔的进料蒸发段、塔壁、塔盘、主梁、支梁等部位。环烷酸的腐蚀与硫腐蚀不同,它不是均匀腐蚀,而是局部腐蚀或点蚀,而且环烷酸腐蚀受酸值、温度、流速、介质、物态变化等多方面因素的影响,因此不容易检测。 2.1 环烷酸腐蚀机理 环烷酸在石油炼制过程中,随 原油一起被加热、蒸馏,并与其沸点相同的油品一起冷
8种炼化工艺流程动图及装置图文大详解
8种炼化工艺流程动图及装置图文大详解从原油到燃料油及各种化工原料要经过多种复杂的工艺流程,不同的工艺流程生产出的产品也一样。 今天带大家了解一下石油炼制的工艺流程和装置。 一、炼油工艺流程分类 1、燃料型炼油工艺流程图
燃料型炼油厂以燃料油为主,主要产品为汽油、柴油、煤油等燃料油。 2、燃料—润滑油型炼油工艺流程图 燃料—润滑油型炼油厂除生产燃料油外,还生产润滑油,一般润滑油与石蜡联合生产。 3、燃料—化工型炼油工艺流程
燃料—化工型炼油厂以生产燃料油及化工原料为主,除燃料油外,乙烯裂解原料、芳烃、丙烯等化工原料占总产品量的比例较大。 二、炼油装置及工艺详解 1、炼油工艺及装置分类 (1)一次加工 常压蒸馏或常减压蒸馏,把原油蒸馏分为几个不同的沸点范围(即馏分); (2)二次加工 催化、加氢裂化、延迟焦化、催化重整、烃基化、加氢精制等。 将一次加工得到的馏分再加工成商品油。 (3)三次加工 裂解工艺制取乙烯、芳烃等化工原料。 2、炼油工艺及装置详解
2.1原油预处理 预处理原因:原油中的盐和水的存在,给炼油装置的稳定操作、设备防腐带来了危害,因此在原油蒸馏前必须进行脱水脱盐。 因此原油进入炼油厂后,必须先进行脱盐脱水,使含水量达到0.1%~0.2%。含盐量<5mg/l,对于有渣油加氢或重油催化裂化过程的炼油厂,要求原油含盐量<3mg/l。 电脱盐原理:原油中的盐大部分溶于水中,脱水的同时,盐也被脱除。 常用的脱盐脱水过程是向原油中注入部分含氯低的新鲜水,以溶解原油中的结晶盐类,并稀释原有盐水,形成新的乳状液,然后在一定温度、压力和破乳剂及高压电场作用下,使微小的水滴,聚集成较大水滴,因密度差别,借助重力水滴从油中沉降、分离,达到脱盐脱水的目的。 2.2常减压装置
原油蒸馏的工艺流程
原油蒸馏的工艺流程 第一节石油及其产品的组成和性质 一、石油的一般性状、元素组成、馏分组成 (一)石油的一般性状 石油是一种主要由碳氢化合物组成的复杂混合物。世界各国所产石油的性质、外观都有不同程度的差异。大部分石油是暗色的,通常呈黑色、褐色或浅黄色。石油在常温下多为流动或半流动的粘稠液体。相对密度在?0.98g/cm 3之间,个别的如伊朗某石油密度达到,美国加利福尼亚州的石油密度低到。 (二)石油的元素组成石油的组成虽然及其复杂,不同地区甚至不同油层不同油井所产石油, 在组成和性质上也可能有很大的差别。但分析其元素,基本上是由碳、氢、硫、氧、氮五种元素所组成。其中碳、氢两中元素占96%?99%,碳占到83%?87%,氢占11%?14%。其余的硫、氧、氮和微量元素含量不超过1%?4%。石油中的微量元素包括氯、碘、磷、砷、硅等非金属元素和铁、钒、镍、铜、铅、钠、镁、钛、钴、锌等微量金属元素。 (三)石油的馏分组成 石油的沸点范围一般从常温一直到500C以上,蒸馏也就是根据各组分的沸点差别,将石油切割成不同的馏分。一般把原油从常压蒸馏开始镏出的温度(初馏点)到180C的轻馏分成为称为汽油馏分,180C?350C的中间馏分称为煤柴油馏分,大于350C的馏分称为常压渣油馏分。 二、石油及石油馏分的烃类组成 石油中的烃类包括烷烃、环烷烃、芳烃。石油中一般不含烯烃和炔烃,二次加
工产物中常含有一定数量的烯烃。各种烃类根据不同的沸点范围存在与对应的馏分中。 三、石油中的非烃化合物石油的主要组成使烃类,但石油中还含有相当数量的非烃化合物,尤其在重质馏分油中含量更高。石油中的硫、氧、氮等杂元素总量一般占1%- 4% 但石油中的硫、氧、氮不是以元素形态存在而是以化合物的形态存在,这些化合物称为非烃化合物,他们在石油中的含量非常可观,高达10%-20%。 (一)含硫化合物(石油中的含硫量一般低于%)含硫化合物在石油馏分中的分布一般是随着石油馏分的沸点升高而增 加,其种类和复杂性也随着馏分沸点升高而增加。石油中的含硫化合物给石油加工过程和石油产品质量带来许多危害。 1 、腐蚀设备 在石油炼制过程中,含硫化合物受热分解产生HS、硫醇、元素硫等活 性硫化物,对金属设备造成严重的腐蚀。石油中通常还含有MgC2、CaCb等 盐类,含硫含盐化合物相互作用,对金属设备造成的腐蚀将更为严重。石油产品中含有硫化物,在储存和使用过程中同样腐蚀设备。含硫燃料燃烧产生的SO、SO遇水后生成H2SO、H2SQ会强烈的腐蚀金属机件。 2、影响产品质量 硫化物的存在严重的影响油品的储存安定性,是储存和使用中的油品容易氧化变质,生成胶质,影响发动机的正常工作。 3、污染环境 含硫石油在加工过程中产生的H2S 及低分子硫醇等有恶臭的毒性气体, 会污染环境影响人体健康,甚至造成中毒,含硫燃料油燃烧后生成的SO2、