SPC培训资料
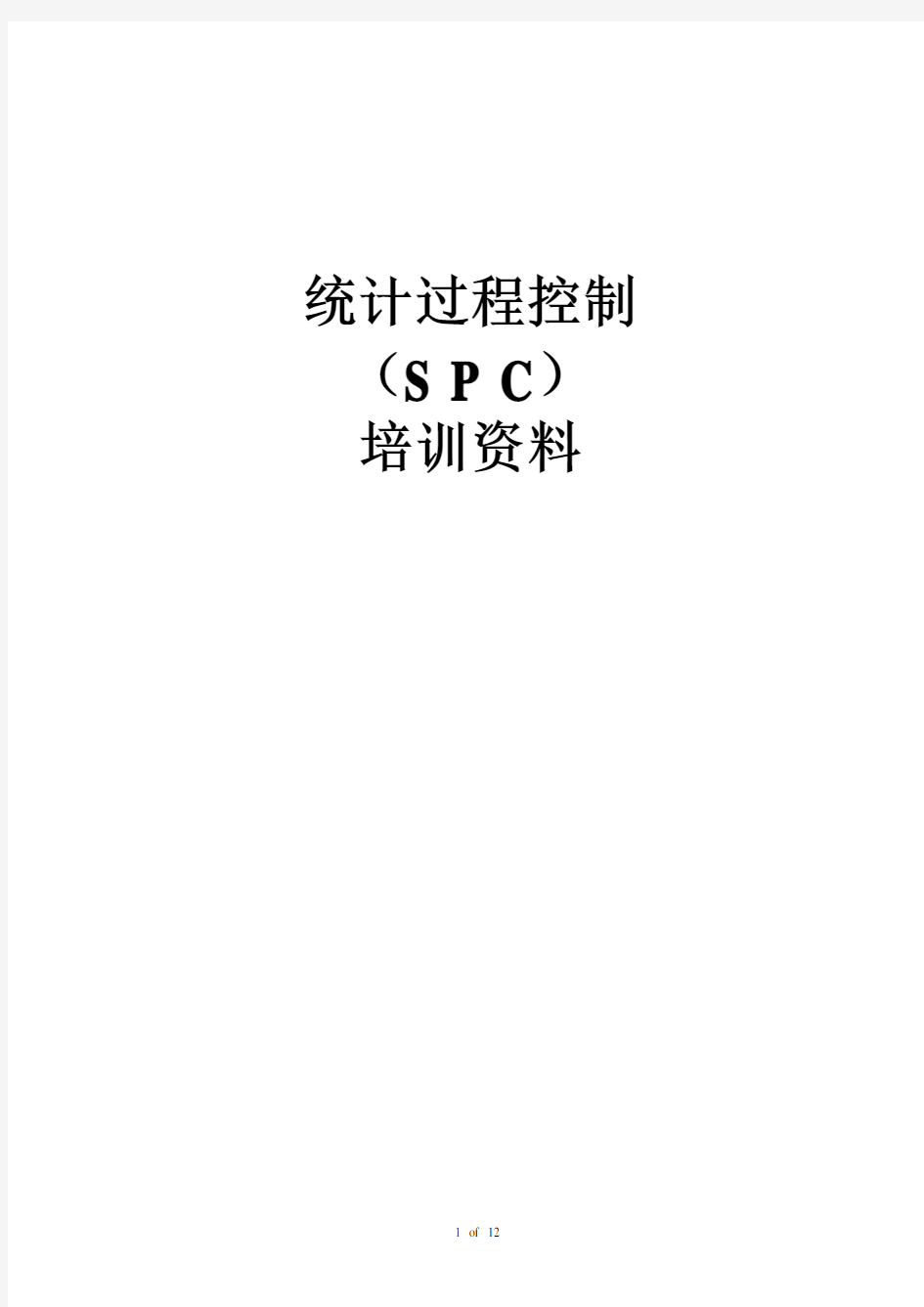

统计过程控制(S P C)
培训资料
一、什么叫SPC
SPC即统计过程控制(Statistical Process Control),是一种统计分析工具,主要通过对过程数据的分析来对生产过程进行实时监控,区分出生产过程中产品质量的随机波动与异常波动,从而对生产过程的异常趋势提出预警,以便管理人员及时采取措施,消除异常,恢复过程的稳定,从而达到提高和控制质量的目的。
二、什么情况下要做SPC
1.客户要求的关键特性
2.内部确定的关键特性
三、做SPC的前提
1.过程数据易于采集
2.过程处于受控状态
四、SPC的理论知识
变差
1.变差的概念
没有两件产品或特性是完全相同的,因为任何过程都存在许多引起变差的原因。产品间的差距也许很大,也许小得无法测量,但这些差距总是存在。例如一个冲压零件的尺寸易于受机器的稳定性、模具的磨损、材料的硬度、操作人员的操作方法、维修(润滑、零件的更换)及环境的影响. 产品间的差异即为变差。
2.变差的普通原因及特殊原因
普通原因变差是一直在过程中出现的变差(如模具的磨损、温度的变化等),过程只有此类变差时,就认为过程是稳定的和可预测的, 我们称之为:“处于受控状态”。
---此类变差通常与管理者有关,通常采取系统措施来解决。
---此类变差是必然存在的,只能改善或降低,不能完全被消除。
特殊原因变差是由异常或外部事件的影响产生的,在普通原因变差之外(如材料用错,操作方法错误等),当过程存在此类变差时,过程是不稳定的或不受控的。
---此类变差通常是与该过程操作人员有关,通常采取局部措施来解决。
---此类变差是可以被消除的
正态分布
一种用于计量型数据的、连续的、对称的频率分布,它是计量型数据用控制图的基础。正态分布的两个参数:平均值U和标准差 ,当一组测量数据服从正态分布时,有大约68.26%的测量值落在平均值处正负一个标准差的区间内,大约95.44%的测量值将落在平均值处于正负两个标准差的区间内;大约99.73%的值将落在平均值处正负三个标准偏差的区间内,超出三个标准差的只有0.27%(如图一:正态分布图)。
U-3σU-2σU-1σU U+σU+2σU+3σ
图一
U决定了图形的中心位置σ决定了图形中峰的陡峭程度
图二
过程只存在普通原因,样本均值落在正态曲线内,变差只为普通原因
当过程出现特殊原因时,样本均值可能就不落在正态曲线内.
控制图
SPC的核心工具是控制图,它可以客观地判断过程是否处于受控状态,可以区分变差的特殊原因和普通原因,为管理人员采取适当的局部改进措施还是要求采取系统管理措施提供依据。这样可以减少混淆、误导性解决问题而造成的高成本。控制图研究的对象是产品的品质特性之次数分配,正常的制程所产生的产品品质特性分配是呈正态分布,超出三个标准差的只有0.27%,落在范围内的可能性是99.73%,范围即为X±3σ.
1.控制图的类型
控制图可分为计量型数据控制图和计数型数据控制图。
A、计量型数据控制图
其数据均由仪器实际量测而得,如:长度、直径、重量等,常用的有以下几种:
平均值极差控制图( Xbar-R )
平均值标准差控制图( Xbar-s)
单值和移动极差控制图(X-MR)
B、计数型数据控制图
其数据均以单位计数,如:不良数、不良率、缺点数等,常用的有以下几种:
不合格品率控制图(P Chart)
不合格品数控制图(nP Chart)
缺陷数控制图(C Chart)
单位缺陷数控制图(U Chart)
2.控制图的选择
图三
冲压零件的尺寸主要为计量型数据,样本量在2-10之间,所以选择Xbar-R图,以下重点讲述Xbar-R图。
3. 平均值极差控制图( Xbar-R 图)
A.初始控制图的建立
①收集数据
应收集单一刀具、冲头、模具等生产出的零件数据(即一个单一的过程)。这样做的目的是每个零件都是在非常相似的生产条件下生产出来的。
一般情况下,初始控制图包含25或更多个样本子组、100或更多个单值数据。
例如: 收集100个数据,为25组,每组4个数据。
子组: 一般由4到5件连续生产的组合. 以上例子中的25组即为25个子组。
子组容量: 也叫样本量,即子组中的数据个数。以上例子中的4即为子组容量。子组容量确定后,所有子组样本的容量应保持不变.
子组容量的确定是计量型控制图的第一关键步骤,其意义就是:当过程有变
异时,抽取的样本能够使组间的变差最大化,同时组内的变差最小化。子组
容量的确定通常取决于采集数据的条件、工厂的测量能力、测量风险等.所以
子组容量的确定是根据测量能力、测量风险等综合评估的结果.
子组频率: 即抽样频次, 依据客户要求、测量能力、测量风险等确定,可以是每班两次、每小时一次或其他可行的频率。
②数据整理
③计算控制线
X1+X2+……+X 25 0.6973
总平均值X= = = 0.0279
k 25
R1+R2+……+R25 0.0160
极差平均值R= = = 0.00064
k 25
式中, X 是每个子组中的四个数的平均值。
R是每个子组中四个数的最大值减最小值,即极差。
K是子组数,即多少个子组。
Xbar图控制线
中心线=0.2790
上控制线UCLx = X+A2*R = 0.0279+0.73×0.00064 = 0.0284 (≈X+3σ)下控制线LCLx = X- A2* R = 0.0279-0.73×0.00064 = 0.0274 (≈X-3σ)R图控制线
CLr = R= 0.0007
上控制线UCLr= D4 * R= 2.28×0.00064 = 0.0015
下控制线LCLx = D3 * R = 0×0.00064 = 0
式中:D4、D3、A2为苏哈常数,它们随样本容量的不同而不同,以下是从苏哈常数表中摘录的子组容量n从2到10的一个表:
表二
*对于样本容量小于7的情况,LCL R在这种情况下没有下控制限,这意味着对于一个样本容量小于7的子组,“同样的”测量结果是可能成立的,所以n<7情况下,R图的下控制线为0。
④绘图
分别将控制线、各组X平均值及R值绘入图中,将各点用直线连接起来便得到趋势图形, 上方为Xbar图,下方为R图,见图四。
(注:一般将R图的刻度值设置为均值图的刻度值的2倍(例如:平均值图上1个刻度代表0.001英寸,则在极端差图上1刻度代表0.002英寸,在一般的子组大小情况下,均值和极差的控制限将具有大约相同的宽度,给分析以直观的帮助。)
X-R图
图四
检查所有画上去的点,看它们是否合理,如果有的点比别的点高得很多或低得很多,需确认计算及绘图是否正确,应确保所画的X和R点在纵向是对应的。
⑤读图
如果过程的零件间的变异性和过程均值保持在现有的水平,单个的子组极差(R)和均值(X)会单独地随机变化,它们会很少超过控制限。而且,数据中不会出现与由于随机变化产生的图形有明显不同的图形与趋势。分析控制图的目的在于识别过程变化性的任何证据或过程均值没有处于恒定的水平的证据——即其中之一或两者均不受统计控制,进而采取适当的措施。R图和X图应分别作分析:
先看R图,R图表示各组内的极差值(很短时间内的零件间的变差), 即组内变化。a.一个或多个点超出上控制限
说明存在下列情况中的一种或几种:
·零件间的变化性或尺寸分布的宽度已经增大(即变坏)
·测量系统变化(例如,不同的检验员或量具)
因为在只存在普通原因引起变差的情况下超出控制限的点会很少,我们便假设该超出的是由于特殊原因造成的。因此,任何超出控制限的点须立即进行分析,找出存在特殊原因的信号。给任何超出控制限的点作标记,以便根据特殊原因实际开始的时间进行调查,采取纠正措施
b.连续9点位于平均值的一侧或连续6点上升、下降
连续9点高于平均极差或连续6点上升说明存在下列情况中的一种或几种:
·零件间的变化性或尺寸分布的宽度开始增大,需要纠正.
·测量系统改变(例如,新的检验员或量具).
连续9点低于平均极差或连续6点下降说明存在下列情况中的一种或几种:
·零件间的变化性或尺寸分布的宽度变小,这常是一个好状态,应研究以便推广.
·测量系统改变,这样会遮掩过程真实性能的变化.
再看Xbar图,Xbar图表示各组平均值距中心线的位置及整体的变化趋势,即组间变化。
当极差受统计控制时,则认为过程的分布宽度——子组内的变差——是稳定的。然后应对均值进行分析看看在此期间过程的位置是否改变。由于X的控制限取决于极差图中变差大小,因此如果均值处于统计控制状态,其变差便与极差图中的变差——系统的普通原因变差有关。如果均值没有受控,则存在造成过程位置不稳定的特殊原因变差。出现特殊原因应及时分析,同样要记住并不是所有的特殊原因都是不利的,有些特殊原因可以通过减小极差而对过程改进起到积极作用,应对这些特殊原因进行评定,以便在过程的适当地方使之固定下来。
a.一个或多个点超出上下控制限
说明在这点出现特殊原因,存在下列情况中的一种或几种:
·过程已改变,或是在当时的那一点(可能是一件独立的事件)或是一种趋势的一部分.
·测量系统变化(例如,不同的检验员或量具)
任何超出控制限的点须立即进行分析,找出存在特殊原因的信号。给任何超出控制限的点作标记,以便根据特殊原因实际开始的时间进行调查,采取纠正措施。
b.连续9点位于平均值的一侧或连续6点上升、下降
说明存在下列情况中的一种或几种:
·过程均值已改变——也许还在变化.
·测量系统改变(飘移、偏倚等).
从该点做一条参考线延伸到链的开始点,分析时应考虑开始出现变化趋势或变化的时间。
c. 明显的非随机图形
其他一些特别的图形中也能表明存在变差的特殊原因。这些图形模式中有趋势、周期性,位于控制限点的异常分布宽度以及子组内数值之间的相关性等。
下图为检验异常的常见的八种规则:
SPC Chart 8 rules / SPC 控制图8种判异规则
图五
B. 重新计算控制线
在进行初次过程研究或重新评定过程能力时,失控的原因已被识别和消除或制度化,然后应重新计算控制限,以排除失控时期的影响。排除所有受已被识别并解决或固定下来的特殊原因影响的子组,然后重新计算新的均值、极差和控制线。确保当所有的均值、极差与新的控制限比较时,表现为受控,如有必要重复识别/纠正/重新计算的过程。由于出现特殊原因而从其中一图中去掉的子组,也应从另一图中去掉。
(注:排除代表不稳定条件的子组并不仅是“丢弃坏数据”,而是排除受已知的特殊原因影
响的点,我们有普通原因引起的变差的基本水平的更好估计值。这为用来检验将来出现变差的特殊原因的控制限提供了最适当的依据。但是要记住:一定要改变过程,以使特殊原因不会作为过程的一部分重现。)
初始控制线设定后,需要试用于以后的时期,然后根据实际情况进行修订。
C.修订控制线
一般固定周期(每月、每季度、每年)对控制线进行审核,必要时修订.
若有以下情况需要考虑修订控制线:
·有长期的过程变化
·主要原材料供应商变更
·机器、模具的变更
·工艺流程顺序变更
·客户特殊要求
过程能力
在解决了 X 和R两个图的控制问题,并且现行的控制图反映过程处于统计控制状态,之后开始过程能力的评定.一般情况下,将过程输出的分布与工程规范相比,看是否始终满足这些规范.有许多技术可用来评定处于统计控制状态过程的能力,最常见的过程能力指数有CPK 、PPK 、CPM.
1. CPK
过程能力指数,值越大表示过程能力越佳,应用于批量生产,过程稳定且受控,计算时用组内标准差σ (以下计算所用的数据为表一中收集的数据)
0.00064
σ= R/d2 = =0.00031
2.06
USL-X X-LSL
CPK = MIN( , )
3σ3σ
式中,d2为苏哈常数,可在苏哈常数表中查得,USL和LSL为规格的上下限,即图纸尺寸的上下限.
当X大于规格中心值SL时:
USL-X
CPK =
3σ
当X小于规格中心值SL时:
X-LSL
CPK =
3σ
因平均值0.0279小于规格中心值0.0280,所以
X-LSL X-LSL 0.0279-0.0260
CPK = = = = 1.86
3σ 3 X 0.00031 3 X 0.00031
有的公司要求的能力指数用Z表示,Z值为CPK值的3倍.
USL-X X-LSL
Z = MIN( , )
σσ
2.PPK
过程性能指数,一般是在初期时确认过程是否稳定,如果大于1.67即可转入长期过程能力管理CPK,计算时用的是总体标准差S .
在EXCEL中总标准差S可以用STDEV函数方便地计算出来.
除了变差不同,其它计算公式都同CPK.
USL-X X-LSL
PPK = MIN( , )
3 S3 S
3. CPM
过程能力指数,将均值与目标值的偏差也考虑进来,它对平均值的变化最敏感,有实际的改进意义(用表一中的数据计算如下),计算时用的是总体标准差.
USL-LSL 0.030-0.026
CPM = = = 2.24
^2 6 0.00028^2+(0.0279-0.0280)^2
从CPM公式中可以看出,X与目标值T越接近,CPM就越大.
(注:目标值不一定都是规格中心值,它是客供双方确定的一个最佳的数值.)
4.评价过程能力
①一般情况下,CPK的评价标准如下:
Cpk >2.0,过程能力十分充足,可以考虑成本的降低(如:放宽检验等);
2. 0 >Cpk >1. 67,过程能力充足,应当保持;
1. 67 >Cpk >1. 33,过程能力满足,但应尽力改善;
1. 33 >Cpk >1. 0,过程能力不足,制程因素稍有变异即有产生不良的危险,需改善;
1. 0 >Cpk >0. 67,过程能力差,必须改善;
0.67 >Cpk,过程能力严重不足,必须改善。
②一般情况下,PPK的评价标准如下:
PPK>1.67过程能力满足.
过程能力示意图
图六
spc基础培训资料
第一章节重新认识SPC 在QS-9000附属参考手册中,有一本“SPC手册”是专门规定SPC统计方法的:内容主要有:过程的概念;过程变差; 过程能力分析; 计量型控制图(X—R图,X—S图等); 计数型控制图(p图,np图,c图,u图等);
第二章节SPC应用的基础 .百分率:单项数据与所有数据总和的商的百分值。 累计百分率:顺序排列中,第1项的累计百分率,等于前 数据的分层 1.概念:将数据依照使用目的,按其性质,来源,影响等进行分类,把性质相同,在同一 生产条件下收集到的质量特性数据归并在一起的方法; 2.作用:分层的目的是为有利于查找生产质量问题的原因。
2.2频数分布表 作频数分布表时要确定组距、组数和组的边界值。 例:某零件的一个长度尺寸的测量值(mm )共100个,测量单位为0.01mm ①从数据中选出最大值和最小值,这时应去掉相差悬殊的异常数据. 最大值为42.44,最小值为42.27 ②用测量单位的1、2、5倍除以最大值与最小值之差(极差),并将所有得值取整数. 极差 =42.44-42.27=0.17mm 已知测量单位为0.01mm,为了求出组距,可用0.01mm 的1、2、5的倍数除以极差0.17mm. 0.17÷0.01=17 0.17÷0.02=8.5(取整数为9) 0.17÷0.05=3.4(取整数为3) 数据为④确定分组组界时,可把数据中的最小值分在第一组的中部,并把分组组界定在最小测量单位的1/2处,以避免测量值恰好落在边界上。这样就确定了第一组的下界,然后依次加上组距,直至确定它包括最大值的未一组的上界为止。
SPC培训心得
SPC培训心得 SPC好多年前就开始说这个名词了,但说使用除了外审的时候向审核老师提供检查外,目前公司还没有真的运用起来。外审提供给审核老师的资料就是一两个人做的,大家平时接触SPC的机会确实不多。但并不是说SPC就真的没用,作为TS16949的五大工具之一,世界上各国家的各种企业都在使用。只能说目前公司可能还没达到这样的管理水平。公司组织SPC的学习为我们将来工作中使用SPC做了前期的铺垫。 SPC统计过程控制,利用统计的方法来监控制程的状态,确定生产过程在管制的状态下,以降低产品品质的变异,是对过程进行控制和持续改进的工具。通过对统计数据的分析、维护、改进,按PDCA的过程计划、实施、研究、措施的方式不断改善产品质量达到产品质量受控的目的。通过对SPC的运用可以降低品质变异,及时发现问题,在问题发生前提前预知的目的。SPC需要大量的统计数据,数据可分为计量型数据“可以连续取值,也称连续型数据。如:零件的尺寸、强度、重量、时间、温度等;和计数型数据:不可以连续取值,也称离散型数据(计数型)。如:废品的件数、缺陷数。SPC统计后主要以控制图的形式体现,按数据类型的不同,如果是计量型数据就采用了-R图,如果收集的数据为计数型数据侧采用P图来表示。不管采用-R图或是P图,其中的计算过程较复杂,在设计给出的上规格界限:USL;下规格界限:LSL后作为生产控制还需要计算出上控制界限(UCL) 、下控制界限(LCL) ,最终计算出CPK值。如CPK>1.33我们认为过程稳定,可转入控制用图。除了看数据外图型的直观性也充分体现,如果数据是连续7点上升或下降,也需要及时找出发生的原因及时纠正。 分析用控制图是根据样本数据计算出控制图的中心线和上、下控制界限,画出控制图,以便分析和判断过程是否处于稳定状态。如果分析结果显示过程有异常波动时,首先找出原因,采取措施,然后重新抽取样本、测定数据、重新计算控制图界限进行分析。控制用控制图是经过分析用控制图分析证实过程稳定并能满足质量要求,此时的控制图可以用于现场对日常的过程质量进行控制。 SPC中最重要的就是合理使用控制图,能供操作者使用以对过程进行持续的控制,有助于过程表现一致并可预测,使过程达到更高的质量、更低的单位成本、更高的有效能力。生产实践证明,无论用多么精密的设备和工具,多么高超的操作技术,甚至由同一操作工,在同一设备上,用相同的工具,生产相同材料的同种产品,其加工后的尺寸总是有差异,这种
SPC培训试题(答案)
SPC培训考试 部门:姓名:分数: 一﹑填空题﹕(每空0.5分﹐共25分) 1.SPC是英文Statistical Process Control的前缀简称,即统计过程控制,也称为统计制程管制。 2.CL表示_管制中心限_; UCL表示_上控制界限__ ; LCL表示下控制界限。 3.Ca表示__准确度__ ;Cp表示__精密度_ ;CPK表示制程能力。 4.PPM是指制程中所产生之百万分之不良数﹐DPM是指制程中所产生之百万分之缺点 数。Defect Per Million pcs 卖出的产品中发生故障的百万分比 5.品管七大手法分别是查检表﹑柏拉图﹑特性要因图﹑散布图﹑管制图﹑ ﹑直方图﹑层别法。 6.实施SPC能够帮助企业在质量控制上真正作到“事前”预防和控制。 7.控制图的基本类型按数据类型分为计量值控制图和计数值控制图。 8.直方图是以一组无间隔的直条图表现频数分布特征的统计图,能够直观地显示出数据的分布情况。 9.如过程历史数据计算的AVERAGE=5, σ =0.2, 过程目标值=5.1,则LCL是 4.4 ,CL是 5.0 ,UCL 是 5.6 。 10.使用控制图,对数据进行分组的基本原则是组内变异小、组间变异大。 11.一般企业的瑕疵率大约是3到4个西格玛,以4西格玛而言,相当于每一百万个机会里,有 6210 次 误差。如果企业不断追求品质改进,达到 6 西格玛的程度,绩效就几近于完美地达成顾客要求,在一百万个机会里,只找得出3.4个瑕疪。 12.计算CP,CPK时数据量不得少于 25组。 13.影响过程的主要因素有人、机、料、法、环、测。 14.对于普通原因的波动通常需要采取系统措施。 15.日常工作中,將 X-Bar 控制图与 R控制图联合使用,较为方便有效。 16.当过程处于受控状态时,过程只受普通因素的影响,过程特性的波动具有统计规律性。当过程处 于失控状态时,过程受到特殊因素的影响;波动偏离原来的规律。 17.日常生产和服务中常见的波动分布有正态分布、二项分布、泊松分布。 18.若直方图符合正态分布,说明过程处于稳定受控状态。 19.若直方图出现孤岛型、偏向型等非正态分布,说明过程中有异常因素作用,应查明原因。 20.当X-MR图中有连续9个点落在中心线同一侧时,说明过程处于失控状态。 21.当控制图中有连续14点交替升降时,说明过程处于失控状态。 22.当控制图中有连续6点上升或下降时,说明过程处于失控状态。 23.“σ”指标准差,是用来衡量一个总数里标准误差的统计单位。 24.在“3σ”原则下,控制点落在μ-3σ到μ+3σ之间的概率是 99.73% 。 25.SPC执行成功的最重要条件是 Action ,即针对变差的特殊原因和普通原因分别采取措施。二﹑选择题﹕(每题1分﹐共15分)
SPC培训资料
统计过程控制(S P C) 培训资料
一、什么叫SPC SPC即统计过程控制(Statistical Process Control),是一种统计分析工具,主要通过对过程数据的分析来对生产过程进行实时监控,区分出生产过程中产品质量的随机波动与异常波动,从而对生产过程的异常趋势提出预警,以便管理人员及时采取措施,消除异常,恢复过程的稳定,从而达到提高和控制质量的目的。 二、什么情况下要做SPC 1.客户要求的关键特性 2.内部确定的关键特性 三、做SPC的前提 1.过程数据易于采集 2.过程处于受控状态 四、SPC的理论知识 变差 1.变差的概念 没有两件产品或特性是完全相同的,因为任何过程都存在许多引起变差的原因。产品间的差距也许很大,也许小得无法测量,但这些差距总是存在。例如一个冲压零件的尺寸易于受机器的稳定性、模具的磨损、材料的硬度、操作人员的操作方法、维修(润滑、零件的更换)及环境的影响. 产品间的差异即为变差。 2.变差的普通原因及特殊原因 普通原因变差是一直在过程中出现的变差(如模具的磨损、温度的变化等),过程只有此类变差时,就认为过程是稳定的和可预测的, 我们称之为:“处于受控状态”。 ---此类变差通常与管理者有关,通常采取系统措施来解决。 ---此类变差是必然存在的,只能改善或降低,不能完全被消除。 特殊原因变差是由异常或外部事件的影响产生的,在普通原因变差之外(如材料用错,操作方法错误等),当过程存在此类变差时,过程是不稳定的或不受控的。 ---此类变差通常是与该过程操作人员有关,通常采取局部措施来解决。 ---此类变差是可以被消除的 正态分布 一种用于计量型数据的、连续的、对称的频率分布,它是计量型数据用控制图的基础。正态分布的两个参数:平均值U和标准差 ,当一组测量数据服从正态分布时,有大约68.26%的测量值落在平均值处正负一个标准差的区间内,大约95.44%的测量值将落在平均值处于正负两个标准差的区间内;大约99.73%的值将落在平均值处正负三个标准偏差的区间内,超出三个标准差的只有0.27%(如图一:正态分布图)。
spc基础培训资料全
第一章节重新认识SPC 内容主要有:过程的概念;过程变差; 过程能力分析;
计量型控制图(X—R图,X—S图等); 计数型控制图(p图,np图,c图,u图等); 第二章节SPC应用的基础 ●质量数据 1.数据的特点:①波动性; ②规律性; 2.质量特性:反映产品特定性质之内容; (如:尺寸、重量、硬度、力度、电阻值、丝印寿命、外观等) 3.质量特性数据:测量质量特性所得的数据; (如:“力度150g”、“力度偏重20g”、“力度偏重5pcs”) 4.数据分类: ①计量值数据:(如单位为“mm、g、℃、Ω”的数据) ②计数值数据:(如单位为“PCS、箱、桶、罐”的数据) ●数据参数 1.数据表达式:公式中一般用X1 X2……Xn表示一组数据中n个数据。 2.频数:同一记录中同一数据出现的数据。 公式中一般用n1 n2 n3…ni表示个数。 3.平均数:所有数据的和与总数和商。 4.百分率:单项数据与所有数据总和的商的百分值。 5.累计百分率:顺序排列中,第1项的累计百分率,等于前N-1项百分率的和。 标准方差: 6. ●数据的分层 1.概念:将数据依照使用目的,按其性质,来源,影响等进行分类,把性质相同,在同一 生产条件下收集到的质量特性数据归并在一起的方法; 2.作用:分层的目的是为有利于查找生产质量问题的原因。 3.分层方法: ①操作人员:按个人分,按现场分,按班次分,按经验分; ②机床设备:按机器分,按工夹刀具分; ③材料:按供应单位分,按品种分,按进厂批分 ④加工方法:按不同的加工、装配、测量、检验等方法分,按工作条件分; ⑤时间:按上、下午分,按年、月、日分,按季节分; ⑥环境:按气象情况分,按室内环境分,按电场、磁场影响分; ⑦其他:按发生情况分,按发生位置分等。 4.两点原则:
SPC培训资料
品質管理教育訓練系列教材 統計制程管制(SPC) xx 企業管理有限公司 TEL: 地址: 東莞市長安鎮長盛西路蓮花苑5幢602室 G X 統計製程管制(SPC) GX
目錄 1.統計製程管制概論……………………………………………P1-P3 2.機遇性及可歸屬之品質變異…………………………………P3-P4 3.管制圖之基本原理……………………………………………P4-P13 4.計數值管制圖…………………………………………………P14-P28 5.計量值管制圖…………………………………………………P29-P39
一、統計制程管制概論 統計制程管制( statistical process control , 簡稱spc) 是利用抽樣樣本資料(樣本統計量),來監視制程之狀態,在必要時採取調整制程參數之行動,以降低產品品質特性之變異性。統計制程管制為預防性之品質管制手段,強調第一次就做對(do it right the first time )。品管界有一句名言: [品質是製造(build in ) 出來的,而非檢驗出來的( inspected out )。這句話說明制程之管制比事後之檢驗,更能提升產品品質。統計制程管制可以用圖4-1之回饋系統來說明。一個制程之輸入包含原料、機器、方法、工具、操作員和周圍環境因素,其輸出為產品。產品之好與壞是由其品質特性來決定。統計制程管制之第一項工作為收集產品品質特性資料。統計制程管制之第二項工作為評估、分析品質特性資料。在統計制程管制中,我們通常是以一個統計模式來做為判斷制程是否為正常的決策基準。目前最常用的工具為依據統計原理發展出來的管制圖(control charts)。當決策系統判斷制程不穩定時,接下來的工作是探討造成制程異常的原因,此階段之工作稱為診斷(diagnosis)。當找出造成制程不穩定之原因後,我們必須規劃一些改善的措施,以使得相同之問題不再發生。回饋管制系統之最後一個步驟是依據規則之改善措施,調整制程之可控制因素。上述步驟需重復進行,以持續改善制程。 操 原作方 料員法 設環工 備境具 因 素 圖1統計制程管制 xxxxxxxxxxxxxxx有限公司 制程 觀測值 評估實施 決策診斷