生物质在制动摩擦材料中的应用

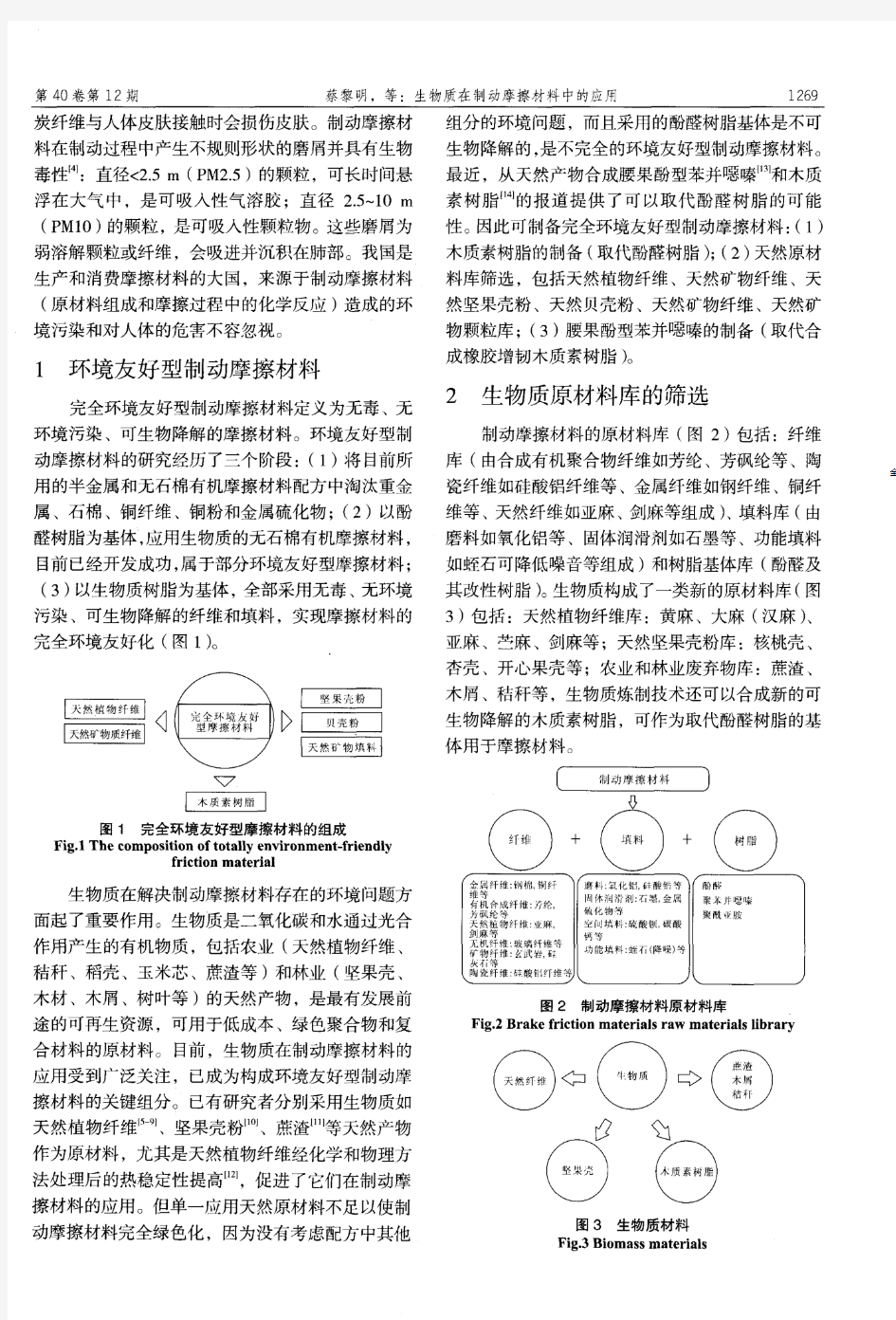
摩擦材料
摩擦材料(盘式片、鼓式片、制动蹄) ——指点行业运作迷津 (一)摩擦材料的应用领域及重要性 摩擦材料是用于运动中起传动、制动、减速、驻车等作用的功能配件,主要用于汽车、火车、飞机、摩托车、工程机械、船舶机械等的制动器、离合器中的刹车片、离合器面片、闸瓦(片)等,其中60%以上用于汽车工业。 汽车用制动器衬片俗称“刹车片”,按用途可分为两类:行车制动和驻车制动刹车片。行车制动又分为盘式制动和鼓式制动刹车片。 汽车用制动刹车片在汽车工业中属于关键的安全件,汽车的制动和驻车都离不开它,刹车片质量的优劣直接关系到使用者的生命财产安全,摩擦材料质量性能的好坏,直接影响这整车、整机的使用效果,虽然在主机中所占成本较小,但功能和地位十分显赫。 (二)摩擦材料行业现状 A—国外摩擦材料行业现状 1897年,在英国,一个名叫Aerber Frood的人创造行的发明了摩擦材料,并成立了FERODO公司,从此奠定了摩擦材料的发展基石。 100多年的发展,现状国外发达国家的刹车片行业已经发展到了一个全新的高度,无论是在制动刹车片的生产设备、技术及工艺上,还是在产品的质量个管理等方面均处于世界绝对领先地位,刹车片的生产已经精细化、完美化,甚至于艺术品化。 最重要的,同时也是中国摩擦材料行业基本上很难做到的一点:发达国家的刹车片生产企业和整车汽车生产商对刹车片的开发是同步的,从刹车片的选定到出样品,要经过噪声检测、台架试验、匹配试验以及冬、夏季路试等反复测试,直到其性能均达到要求并稳定后,才批量生产。 目前,从世界范围来看,摩擦材料行业早已经品牌化、规模化、标准化。对于先进的生产刹车片的技术工艺而言,国外大致分为三块:北美(半金属配方);欧洲(少金属配方)日本(NA——无石棉有机物配方)。国外行业规范,想进入其市场,刹车片生产企业的设备、技术、工艺、产品的质量都应匹配,同时通过其市场的质量认证标准。 B—中国摩擦材料行业现状 据不完全统计,我国国内现有摩擦材料生产企业超过600多家(若包括无生产许可证或小作坊式的,估计有800多家以上),销售产值约180亿人民币,其中70%产品为汽车用摩擦材料占30%,国外需求的摩擦材料占70%,产值前50各生产企业中,国外、合资、独资占30家。
鼓式制动器 设计说明书
车辆工程专业课程设计题目:鼓式制动器设计 学院机械与能源工程学院专业车辆工程 年级车辆10级班级车辆1012 姓名李开航学号 2010715040 成绩指导老师赖祥生
精品文档 目录 第1章绪论....................................................... 1.1制动系统设计的目的 (1) 1.2制动系统设计的要求 (1) 第2章鼓式制动器的设计计算及相关说明 (2) 2.1鼓式制动器有关计算 (2) 2.1.1基本参数 (2) 2.1.2确定前后轴制动力矩分配系数β (2) 2.1.3鼓式制动器制动力矩的确定 (3) 2.2鼓式制动器的结构参数与摩擦系数的选取 (4) 2.2.1制动鼓半径 (4) 2.2.2制动鼓摩擦衬片的包角、宽度、和起始角 (4) 2.2.3张开力作用线至制动器中心的距离 (4) 2.2.4制动蹄支销中心的坐标位置 (5) 2.2.5摩擦片的摩擦系数 (5) 2.3后轮制动轮缸直径与工作容积的设计计算 (5) 2.4摩擦衬片的磨损特性计算 (6) 2.5驻车计算 (8) 第3章鼓式制动器主要零件的结构设计 (10) 3.1制动鼓 (10) 3.2制动蹄 (11) 3.3制动底板 (12) 3.4支承 (12) 3.5制动轮缸 (13) 3.6摩擦材料 (13) 3.7制动器间隙 (13) 第4章鼓式制动器的三维建模 (14) 第5章结论 (15) 参考文献 (16)
第1章绪论 1.1制动系统设计的目的 汽车是现代交通工具中用得最多,最普遍,也是最方便的交通运输工具。汽车制动系是汽车底盘上的一个重要系统,它是制约汽车运动的装置。而制动器又是制动系中直接制约汽车运动的一个关键装置,是汽车上最重要的安全件。汽车的制动性能直接影响汽车的行驶安全性。随着公路业的迅速发展和车流密度的日益增大,人们对安全性、可靠性要求越来越高,为保证人身和车辆的安全,必须为汽车配备十分可靠的制动系统。 1.2制动系统设计的要求 本次的课程设计选择了鼓式制动器,制定出制动系统的结构方案,确定计算制动系统的主要设计参数制动器主要参数设计和液压驱动系统的参数计算。利用CATIA绘制装配图,布置图和零件图。最终进行制动力分配编程,对设计出的制动系统的各项指标进行评价分析。 第2章鼓式制动器的设计计算及相关说明 2.1鼓式制动器有关计算
解析汽车制动系统基础结构
制动十问解析汽车制动系统基础结构 理解制动系统的基础结构有什么好处?很多人对此嗤之以鼻,觉得张口闭口蹦出的都是 ABS、ESP之类的名词才叫酷,你还别小看这些基础的理论知识,它可以用来提高自己在防忽悠方面的抵抗力,比如,文中会提到的制动片磨损问题,当有奸商对你狠下毒手的时候, 你便可以给他好好的上一课,另外,这在买车时也能派上用场,为了促成一单生意,销售顾 问有可能会适当的将某些功能进行夸大,例如,他家的车所装配的行车稳定系统(ESP、DSC……)可以依据制动片的磨损程度来额外施加制动力以提高驾驶员的驾驭感受,此时,你便可笑着对他说:“别逗了”。 接手这个选题是需要一定勇气的,因为,围绕汽车制动这个话题在此前已经制作过太多的内 容,等到我来做这方面内容时,无论从选题立意还是文章的切入点来看,都不太容易带动大家的阅读热情。在斟酌之后,我打算换个方式聊聊汽车制动,以让大家对这一部分能有更深 刻的认识,当然,在文章中同样会收纳一些较为实用的内容,话不多说,大家各取所需吧。 ?为什么你踩下制动踏板时,车速会慢下来? 和土.匚事iirjjiLre.
一张图可以很清楚的把这个问题交代清楚,为了减轻大家的阅读压力,我不打算用过多文字 来描述这部分,还是把精力放在后面的内容吧。 ?在制动结束后,制动片和制动盘是怎么被分开的? 这又牵扯出一个问题,在完成制动后,制动片和制动盘是如何被分开的?其实很简单,松开制动踏板后,制动系统内的制动压力随即下降,因此,制动卡钳的活塞处于松弛的状态 (在 橡胶密封圈的变形作用下回位),滚动的车轮带着制动盘一起旋转,依靠旋转时细微的摆动,制动盘便可顺利挣脱制动片的束缚,推动制动片跟着活塞回位。 ?制动踏板的背后是什么? 脚下的每一块踏板分别具备何种作用是个关键,这在学车时,教练会反复强调,因为它不仅 是起步的关键,最为主要的则是与安全息息相关,但你知道在这些踏板的背后是什么样的构 造吗?顺应本文主旨,今日所谈仅限制动。
汽车制动系统摩擦片材料基本知识
汽车制动系统摩擦片材料基本知识 摩擦材料 一、概论 摩擦材料就是一种应用在动力机械上,依靠摩擦作用来执行制动与传动功能的部件材料。它主要包括制动器衬片(刹车片)与离合器面片(离合器片)。刹车片用于制动,离合器片用于传动。 任何机械设备与运动的各种车辆都必须要有制动或传动装置。摩擦材料就是这种制动或传动装置上的关键性部件。它最主要的功能就是通过摩擦来吸收或传递动力。如离合器片传递动力,制动片吸收动能。它们使机械设备与各种机动车辆能够安全可靠地工作。所以说摩擦材料就是一种应用广泛又甚关键地材料。 摩擦材料就是一种高分子三元复合材料,就是物理与化学复合体。它就是由高分子粘结剂(树脂与橡胶)、增强纤维与摩擦性能调节剂三大类组成及其它配合剂构成,经一系列生产加工而制成的制品。摩擦材料的特点就是具有良好的摩擦系数与耐磨损性能,同时具有一定的耐热性与机械强度,能满足车辆或机械的传动与制动的性能要求。它们被广泛应用在汽车、火车、飞机、石油钻机等各类工程机械设备上。民用品如自行车、洗衣机等作为动力的传递或制动减速用不可缺少的材料。 二、摩擦材料发展简史 自世界上出现动力机械与机动车辆后,在其传动与制动机构中就使用摩擦片。初期的摩擦片系用棉花、棉布、皮革等作为基材,如:将棉花纤维或其织品浸渍橡胶浆液后,进行加工成型制成刹车片或刹车带。其缺点:耐热性较差,当摩擦面温度超过120℃后,棉花与棉布会逐渐焦化甚至燃烧。随着车辆速度与载重的增加,其制动温度也相应提高,这类摩擦材料已经不能满足使用要求。人们开始寻求耐热性好的、新的摩擦材料类型,石棉摩擦材料由此诞生。石棉就是一种天然的矿物纤维,它具有较高的耐热性与机械强度,还具有较长的纤维长度、很好的散热性,柔软性与浸渍性也很好,可以进行纺织加工制成石棉布或石棉带并浸渍粘结剂。石棉短纤维与其布、带织品都可以作为摩擦材料的基材。更由于其具有较低的价格(性价比),所以很快就取代了棉花与棉布而成为摩擦材料中的主要基材料。1905年石棉刹车带开始被应用,其制品的摩擦性能与使用寿命、耐热性与机械强度均有较大的提高。1918年开始,人们用石棉短纤维与沥青混合制成模压刹车片。20世纪20年代初酚醛树脂开始工业化应用,由于其耐热性明显高于橡胶,所以很快就取代了橡胶,而成为摩擦材料中主要的粘结剂材料。由于酚醛树脂与其她的各种耐热型的合成树脂相比价格较低,故从那时起,石棉-酚醛型摩擦材料被世界各国广泛使用至今。 20世纪60年代,人们逐渐认识到石棉对人体健康有一定的危险性。在开采或生产过程中,微细的石棉纤维易飞扬在空气中被人吸入肺部,长期间处于这种环境下的人们比较容易患上石棉肺一类的疾病。因此人们开始寻求能取代石棉的其它纤维材料来制造摩擦材料,即无石棉摩擦材料或非石棉摩擦材料。20世纪70年代,以钢纤维为主要代替材料的半金属材料在国外被首先采用。80年代-90年代初,半金属摩擦材料已占据了整个汽车用盘式片领域。20世纪90年代后期以来,NAO(少金属)摩擦材料在欧洲的出现就是一个发展的趋势。无石棉,
摩擦材料
摩擦材料 一、概论 摩擦材料是一种应用在动力机械上,依靠摩擦作用来执行制动和传动功能的部件材料。它主要包括制动器衬片(刹车片)和离合器面片(离合器片)。刹车片用于制动,离合器片用于传动。 任何机械设备与运动的各种车辆都必须要有制动或传动装置。摩擦材料是这种制动或传动装置上的关键性部件。它最主要的功能是通过摩擦来吸收或传递动力。如离合器片传递动力,制动片吸收动能。它们使机械设备与各种机动车辆能够安全可靠地工作。所以说摩擦材料是一种应用广泛又甚关键地材料。 摩擦材料是一种高分子三元复合材料,是物理与化学复合体。它是由高分子粘结剂(树脂与橡胶)、增强纤维和摩擦性能调节剂三大类组成及其它配合剂构成,经一系列生产加工而制成的制品。摩擦材料的特点是具有良好的摩擦系数和耐磨损性能,同时具有一定的耐热性和机械强度,能满足车辆或机械的传动与制动的性能要求。它们被广泛应用在汽车、火车、飞机、石油钻机等各类工程机械设备上。民用品如自行车、洗衣机等作为动力的传递或制动减速用不可缺少的材料。 二、摩擦材料发展简史 自世界上出现动力机械和机动车辆后,在其传动和制动机构中就使用摩擦片。初期的摩擦片系用棉花、棉布、皮革等作为基材,如:将棉花纤维或其织品浸渍橡胶浆液后,进行加工成型制成刹车片或刹车带。其缺点:耐热性较差,当摩擦面温度超过120℃后,棉花和棉布会逐渐焦化甚至燃烧。随着车辆速度和载重的增加,其制动温度也相应提高,这类摩擦材料已经不能满足使用要求。人们开始寻求耐热性好的、新的摩擦材料类型,石棉摩擦材料由此诞生。 石棉是一种天然的矿物纤维,它具有较高的耐热性和机械强度,还具有较长的纤维长度、很好的散热性,柔软性和浸渍性也很好,可以进行纺织加工制成石棉布或石棉带并浸渍粘结剂。石棉短纤维和其布、带织品都可以作为摩擦材料的基材。更由于其具有较低的价格(性价比),所以很快就取代了棉花与棉布而成为摩擦材料中的主要基材料。1905年石棉刹车带开始被应用,其制品的摩擦性能和使用寿命、耐热性和机械强度均有较大的提高。1918年开始,人们用石棉短纤维与沥青混合制成模压刹车片。20世纪20年代初酚醛树脂开始工业化应用,由于其耐热性明显高于橡胶,所以很快就取代了橡胶,而成为摩擦材料中主要的粘结剂材料。由于酚醛树脂与其他的各种耐热型的合成树脂相比价格较低,故从那时起,石棉-酚醛型摩擦材料被世界各国广泛使用至今。 20世纪60年代,人们逐渐认识到石棉对人体健康有一定的危险性。在开采或生产过程中,微细的石棉纤维易飞扬在空气中被人吸入肺部,长期间处于这种环境下的人们比较容易患上石棉肺一类的疾病。因此人们开始寻求能取代石棉的其它纤维材料来制造摩擦材料,即无石棉摩擦材料或非石棉摩擦材料。20世纪70年代,以钢纤维为主要代替材料的半金属材料在国外被首先采用。80年代-90年代初,半金属摩擦材料已占据了整个汽车用盘式片领域。20世纪90年代后期以来,NAO(少金属)摩擦材料在欧洲的出现是一个发展的趋势。无石棉,采用两种或两种以上纤维(以无机纤维为主,并有少量有机纤维)只含少量钢纤维、铁粉。NAO(少金属)型摩擦材料有助于克服半金属型摩擦材料固有的高比重、易生锈、易产生制动噪音、伤对偶(盘、鼓)及导热系数过大等缺陷。目前,NAO (少金属)型摩擦材料已得到广泛应用,取代半金属型摩擦材料。2004年开始,随汽车工业飞速发展,人们对制动性能要求越来越高,开始研发陶瓷型摩擦材料。陶瓷型摩擦材料主要以无机纤维和几种有机纤维混杂组成,无石棉,无金属。其特点为: 1. 无石棉符合环保要求; 2. 无金属和多孔性材料的使用可降低制品密度,有利于减少损伤制动盘(鼓)和产生制动噪音的粘度。 3. 摩擦材料不生锈,不腐蚀; 4. 磨耗低,粉尘少(轮毂)。 三、摩擦材料分类 在大多数情况下,摩擦材料都是同各种金属对偶起摩擦的。一般公认,在干摩擦条件下,同对偶摩擦系数大于0.2的材料,称为摩擦材料。 材料按其摩擦特性分为低摩擦系数材料和高摩擦系数材料。低摩擦系数材料又称减摩材料或润滑材料,其作用是减少机械运动中的动力损耗,降低机械部件磨损,延长使用寿命。高摩擦系数材料又称摩阻材料(称为摩擦材料)。
生物质材料复习资料
生物质材料 一、绪论 环境:指与人类密切相关、影响人类生活和生产活动的各种自然(包括人工干预下形成的)力量或作用的总和。分为自然环境和社会环境。 环境对人类的贡献: 1、它是人类生存与发展的终极物质来源; 2、它承受着人类活动产生的废弃物和各种作用结果。 资源:广义的资源:指人类生存发展和享受所需要的一切物质的和非物质的要素。 狭义的资源:仅指自然资源 材料:指具有一定结构、组分和性能,具有一定用途的物质。 环境材料:具有良好的使用性能和优良的环境协调性的材料。在加工、制造、使用和再生过程中具有最低环境负荷、最大使用功能的人类所需材料。既包括经改造后的现有传统材料也包括新开发的环境材料。 生物质材料:是指由动物、植物及微生物等生命体衍生得到的材料,主要上由有机高分子物质组成,在化学成分上生物质材料主要由碳、氢和氧三种元素组成。 生物质材料的分类: 1、按组分:均质生物质材料、复合生物质材料 2、按所含化学结构单元:多糖类、蛋白质类、核酸、脂类、酚类、聚氨基酸、 综合类 生物质材料的一般特征: 1)都含有碳、氢和氧三种元素,部分生物质材料还可能含有氮、硫或者钠等元素,因此生物质材料归属于有机高分子材料,具有有机物和高分子的一般特性特征 2)种类多、分布广、储量丰富。 3)与合成高分子材料相比,都具有较好的生物降解性. 4)可再生 5)生物质材料能够进行与功能基相关的聚合物化学反应。 6)水分对生物质材料的性能影响明显 7)通常是多组分伴生 8)结构和性能变异大 二、纤维素基材料 纤维素:纤维素是构成植物细胞的基本成分,它存在于所有植物当中,是植物界中一种最丰富的可再生的有机资源。 综纤维素:指植物纤维原料中的全部碳水化合物,即纤维素与半纤维素之和。 故又称全纤维素。 制备方法: 1、氯化法 无抽提物试料氯气 木素被氧化 化木素综纤维素(白色)抽提 +
蹄块摩擦材料配方
制动器摩擦片材料介绍 目前,国内外用于制动的摩擦材料主要有石棉树脂(国家法规已限制使用)型摩擦材料、无石棉树脂型摩擦材料、金属纤维增强摩擦材料、半金属纤维增强摩擦材料和混杂纤维增强摩擦材料等,国内以半金属纤维增强摩擦材料的应用最为普遍。上述这些摩擦材料的基本成分是增强纤维摩擦材料的生产过程一般为: 原料储存→称重→混合→预成型(常温模)→高温压模→样品修饰处理→检视→包装出厂。 1、石棉、钢纤维及克维拉(芳纶纤维)制动片的典型配方 a.石棉制动片配方一般为:50%石棉、15%树脂、20%耐磨粒、15%填充料。 b.钢纤维制动片配方一般为:30%钢纤维、15%树脂,10%氧化锌,10%金属粉,15%陶瓷,10%橡胶粒、10%石墨。 c.芳纶纤维制动片配方一般为:5%芳纶纤维、15%金属粉、15%耐磨粒、15%树脂、50%填充料。 2、摩擦材料中各组分的作用 2.1增强纤维 纤维在摩擦材料中作为增强剂,对制动片的强度、摩擦和磨损性能起着重要作用。 2.2粘结剂树脂和纤维材料、填充料等各组分能否良好粘结,取决于树脂对这些材料的浸润性能以及与它们形成化学键的可能性。目前,摩擦材料最常用的粘结剂是各种酚醛树脂及其改性树脂,常用酚醛树脂的性能如表3所示,它的作用是将增强纤维与其他组分粘合在一起。粘结剂是摩擦材料的基体,直接影响到材料的各种性能,因此粘结剂应满足以下性能要求。 a.在一般温度(100℃以下)下,保证摩擦材料有足够的机械强度(抗击强度、冲击强度、压缩强度、剪切强度以及一定的伸长率)。 b.当制动摩擦表面温度在200~300℃时,树脂不发生粘流、分解,应保持一定的强度,以支持摩擦表面层的工作要求,且与对偶件有良好的贴合性。
中国摩擦材料发展方向
中国摩擦材料发展方向 我国摩擦材料的未来发展方向,主要体现在三个大的领域方面,随着我国汽车产业的不断发展,做为汽车制动系统关键零部件之一的刹车片也得到了突飞猛进的发展。而今新能源时代到来之际,我国企业须认清国际摩擦材料行业的发展形势。以下是刹车片的三种重要材料:首先是纤维增强材料,纤维做为摩擦材料的骨架材料,不但对摩擦片的强度起着至关重要的作用,同时也对摩擦片的性能有着重要的影响。目前在欧美等发达国家和地区又开始对纤维的结构和理化性能提出了更为严格的要求,而木质纤维、无机晶须(硫酸钡晶须;碳酸钙晶须;钛酸钾晶须等)、矿物纤维、陶瓷纤维、碳纤维、各种有机合成纤维等给我们提供了大量的选择余地,但从成本等综合因素上来看晶体结构和水溶性纤维材料等将是我们未来摩擦材料中 的首选纤维。?刹车片的另一个重要材料是粘合剂。粘合剂是我们生产摩擦材料必不可少的材料,人们从最早利用纯酚醛树脂(固态和液态),到后来采用各种橡胶通过多种工艺对酚醛树脂进行改性,发展到今天使用多种无机物或有机物对树脂进行改性。目前已经不再是单纯的追求摩擦系数和磨损性能的稳定和提高,而是从摩擦片与刹车盘表面的相互作用去分析摩擦材料的工作原理。所以做为摩擦材料的粘合剂材料,不再仅限于树脂与橡胶,而是已经拓展到了利用金属粉末或金属硫化物在高温下所具有的特殊性能,来 减少树脂在摩擦材料中的使用比例,弥补树脂及橡胶在高温条件下的不足,改善高温时在刹车片与刹车盘之间形成的转移膜的结构与性能,进而提高摩擦片的摩擦性能以及其与刹车盘的磨损性能,从而达到提高制动的安全性能、舒适性能和环保性能。?因此,我们在采用高性能的树脂来提高摩擦材料性能的同时,应更多地关注和利用一些金属粉末或金属硫化物以改善摩擦过程中形成的转移膜的形状与结构,使静态摩擦系数与动态摩擦系数达到相对的平衡,确保刹车片与刹车盘具有良好的磨损性能的同时,达到提高摩擦材料的速度与压力敏感性、消除高温衰退、减少噪音、减少落灰的目的。最后就是摩擦性能调节剂:摩擦性能调节剂在改善摩擦材料综合性能过程中起着非常关键的作用,过去我们的摩擦材料技术工作者在材料品种 的选择上做了大量的研究,并且对其形状和结构也做了相应的探讨,但与世界先进的水平相比还有很大的差距,今后的研究工作不但要在选材上不断扩大应用范围,而且要对每种材料的粒度分布做出明确的规定, 并且对其理化性能提出详细的技术参数,同时在配方的研究过程中,对于同一种材料的应用,要根据其形状与粒度的进行多种型号的搭配使用,以确保其优点在摩擦材料中得到充分的发挥。 汽车刹车材料的发展趋势
汽车制动摩擦材料的性能要求及影响因素分析
汽车制动摩擦材料的性能要求及影响因素分析 发表时间:2018-09-12T14:20:56.057Z 来源:《科技新时代》2018年7期作者:张国华 [导读] 本文围绕汽车制动摩擦材料的相关议题进行了探讨,分别论述了汽车制动摩擦材料摩擦磨损性能的影响因素。 杭州优纳摩擦材料有限公司浙江省杭州市 311404 摘要:本文围绕汽车制动摩擦材料的相关议题进行了探讨,分别论述了汽车制动摩擦材料摩擦磨损性能的影响因素,汽车制动摩擦材料热衰退性能的影响因素,以及启辰制动摩擦材料噪音及振动的影响因素,供相关人士参考。 关键词:摩擦材料、汽车、摩擦性能、热性能、影响因素 1引言 对于汽车生产来说,制动摩擦材料在汽车制动器、汽车离合器以及摩擦传动装置中起着关键的作用,在制动摩擦材料性能要求方面,不仅需要摩擦材料具备良好的摩擦磨损性能,同时在热衰退性能、振动性能以及减噪性能上也应有较良好的表现。在某种程度上制动摩擦材料性能的优劣将直接影响到汽车系统运行的安全性和可靠性。为此对汽车制动摩擦材料的性能进行分析和研究是十分重要且十分必要的。 2汽车制动摩擦材料摩擦磨损性能的影响因素 汽车制动摩擦材料的摩擦磨损性能主要与摩擦系数,摩擦稳定性以及磨损率有关,通常来说,摩擦材料需要在稳定适中的摩擦系数下尽可能拥有较低的材料磨损率。 (一)摩擦材料自身组分的影响 汽车制动摩擦材料是由多种材料所制成的复合型材料,因此在制作过程中各物料组分的不同会对摩擦材料的摩擦性能造成不同的影响。 磨料的影响。比如在摩擦材料中添加氧化铝、硫酸钡、锆英石、铬铁矿粉、硫化锑等金属填料,添加石墨等减磨材料,均可以使摩擦材料本身的摩擦性能得到改善和提升。根据添加物质性能的不同,也会对摩擦材料的性能产生不同的影响。比如添加氧化铝、锆英石、铬铁矿粉、硫化锑可以提高摩擦材料的高温摩擦系数;添加硫酸钡可以提高摩擦材料的热稳定性;添加石墨可以有效改善摩擦材料的热衰退性能,增加抗摩擦性能。 添加纤维的影响。在摩擦材料的制作过程中通过添加增强纤维可以提高材料的摩擦性能。在实际生产中,添加纤维有多种类型,如铜纤维、钢纤维等金属型纤维;玻璃纤维、陶瓷纤维等无机型纤维;芳纶纤维、纤维素纤维等有机型纤维等。金属型纤维在摩擦材料中起着骨架支撑的作用,但是由于金属的密度较大且对环境有一定的负面影响,因此在摩擦材料的制作中往往含量较低。有机型纤维在性能上具有较好的亲水性,同时在混合的过程中分散均匀度较好,因此可以提高摩擦材料的抗裂性能。此外由于该类型纤维对环境无污染,与其他物质的适应性好,因此应用较为普遍。无机型纤维在隔热性和减噪性方面表现良好,对环境无污染,但是在传热性上表现稍差,一般在应用时适当加入一些良好导热性的材料作为平衡。另外,无机纤维加入量过多容易导致摩擦材料的开裂,降低其摩损性能。 固体润滑剂的影响。固体润滑剂主要包括石墨、炭黑、氟化物等炭材料;硫、硒等硫族化合物;氮化硼;二硫化钼、硫化铅、硫化锌等金属硫化物。这些固体润滑剂有较低的莫氏硬度,可以在摩擦材料使用过程中发生有效的转移,以此来稳定摩擦材料的摩擦系数,减少摩擦噪音,提高摩擦材料的耐磨损性能。 (二)摩擦材料制作工艺的影响 不同的烧蚀或成型制作工艺也会对摩擦材料的摩擦性能造成影响。目前在摩擦材料的制作过程中多采用热压成型工艺。在热压成型过程中主要由加压、排气和固化三个基本环节。对于热压温度的控制需要参考模压树脂的差示扫描热量曲线中固化温度的变化情况。良好的热压成型工艺可以使树脂材料和其他物料结合程度得到改善,有效排出材料中的气体,控制摩擦材料成品中的含胶量,使摩擦材料成品拥有较好的密实度,提高摩擦材料的耐磨损性能。 3汽车制动摩擦材料热衰退性能的影响因素 摩擦材料的热衰退性能是影响摩擦材料使用寿命以及汽车运行安全与否的重要性能。通常情况下,高温会提高材料的热衰退性,若材料的热衰退十分严重,极容易导致汽车制动失效等故障,尤其是上下坡行驶过程中,摩擦材料的抗热衰退性对于行驶的安全十分必要。 (一)摩擦材料生产原料的影响 目前在摩擦材料的生产制造中,通常采用对树脂进行性能的优化,通过性能改良和优化来提高树脂的热分解温度,使摩擦材料能够在较高的温度条件下摩擦系数更加稳定,提高摩擦材料的抗热衰退性能。比如利用纳米金属材料对树脂进行导热性能的改良,纳米金属材料本身导热性能优异,与树脂原料结合后可以将摩擦表面产生的热量迅速地传递到材料内部,减少摩擦材料自身的温度差,减少树脂的热分解反应,提高摩擦材料的稳定性。另外,基于硫化锑在高温条件下容易生产硬度更高的氧化物,因此在原料中加入硫化锑不仅能够提高材料的耐磨损性,同时也起到了抗热衰退性的作用。 (二)摩擦材料制作工艺的影响 烧蚀技术涉及到摩擦材料的炭化,因此可以通过对烧蚀工艺优化来改善摩擦材料的抗热衰退性。为避免摩擦材料在高温过程中剧烈炭化,可以在烧蚀工艺前线对摩擦材料进行高温预处理,使材料在经过高温烧蚀过程中能够降低炭化的速率,提高摩擦材料的抗热衰退性。 4汽车制动摩擦材料噪音及振动的影响因素 随着汽车行业的不断发展,汽车制造技术也越来越贴合消费者的需求,从过去的功能性,美观性逐渐走向功能性、美观性、舒适性、环保性。对于汽车制动摩擦材料而言,越来越注重材料的降噪性能和抗振动性能。在降噪性能方面,可从摩擦材料的生产配方入手,通过降低原料中金属的含量来提高降噪性能。另外,由于摩擦材料中的孔隙率对降噪性能有着十分重要的影响,因此,可采用较高的显气孔率来
刹车片摩擦材料成分
刹车片(摩擦材料)的成分 摩擦材料种类繁多。汽车制动器和离合器用的摩擦材料,几乎都是用树脂或橡 胶作为粘接剂的有机摩擦材料。到目前发现可以用于制造有机摩擦材料的天然和合成材料近百种,人们选择其中几种或十几种原料,按一定比例混合,生产出具有不同特性的摩擦材料。原料的选取与配合比例称为配方。配方是摩擦材料生产中最重要的技术要素。配方五花八门,千变万化,但万变不离其宗。归纳起来,任何一种实用配方都不外乎由下述四大类基本材料组成: 粘合剂:约占5%~25% 增强剂:约占20%~50% 摩擦调节剂:约占30%~60% 工艺调节剂:约占0.5%~1% (1)粘合剂: 如热固性树脂和橡胶等。粘合剂的作用是将配方中各组分粘合为一体,形成具有足够强度、适当硬度、尽可能高的耐温性和耐磨性的固体。 粘合剂的耐温性是影响摩擦材料性能的主要因素。因此,其种类和用量 是配方设计中重点考虑的。 (2)增强纤维: 如石棉纤维、天然矿物纤维、人造矿物纤维、有机纤维、植物纤维、素纤维、碳纤维。增强纤维必须能提供足够的强度,应有很好的耐热性 能和耐磨性能,而且不能刮伤对偶。 (3)摩擦性能调节剂:
摩擦性能调节剂的种类很多,用途各异,必须针对所选择的树脂和纤维 的种类,结合使用要求,进行不同的搭配,以形成满足不同用途的配方 体系。 a\ 能提高摩擦系数的: 常采用的是非金属矿物及其制品。例如:重晶石(硫酸钡)、硅灰石、 氧化铝、矾土(刚玉)、氧化铁红(黑)、焦炭粉等等。这些原料的 主要作用是使刹车片有足够的摩擦系数,不仅在100°C左右的常温区 段,而且在400~500°C的高温区段都能产生足够的制动力。 b\ 能稳定摩擦系数的: 主要原料有石墨、二硫化钼、云母、滑石、软金属等。这些原料的硬 度都很低,在摩擦表面起润滑作用,使摩擦系数趋于稳定,并用来保 护摩擦对偶。 c\ 有机摩擦性能调节剂: 常用的有橡胶份、轮胎粉等。加入这些材料有助于降低材料的硬度和 密度、稳定摩擦系数、降低磨损,但过量的使用会导致热衰退。 d\ 金属粉末(屑): 在一些重载荷的刹车片配方中,也有加入一定份额的金属粉或屑的情 况,常用的有铁粉、铜粉(屑)、铝粉等。加入金属组分主要是为了 改进材料的高温摩擦磨损性能。 (4)工艺调节剂:
图解汽车 汽车制动系统结构解析
原创图解汽车(12)汽车制动系统结构解析 2012-09-25 18:21:16 来源:pcauto作者:陈启贞向编辑提问x 评论[219] 分享 第1页:制动系统的组成及分 在本页浏览全文>>(共计2页) 【太平洋汽车网技术频道】大家都知道,汽车的制动系统对我们的行车安全非常重要,行车中如出现制动失灵等故障,后果都将不堪设想。那么汽车的制动系统是如何制动的?为什么会失灵?ABS、ESP系统又是什么?对我们驾驶安全有什么帮助?好吧,下面我们一起来了解一下。 阅读提示:
PCauto技术频道图解类文章都可以使用全新的高清图解形式进行阅读。大家可以通过点击上面图片链接跳转到图解模式。高清大图面积提升3倍,看着更清晰更爽,赶紧来体验吧! ●制动系统的组成 作为制动系统,作用当然就是让行驶中的汽车按我们的意愿进行减速甚至停车。工作原理就是将汽车的动能通过摩擦转换成热能。汽车制动系统主要由供能装置、控制装置、传动装置和制动器等部分组成,常见的制动器主要有鼓式制动器和盘式制动器。
●鼓式制动器 鼓式制动器主要包括制动轮缸、制动蹄、制动鼓、摩擦片、回位弹簧等部分。主要是通过液压装置是摩擦片与岁车轮转动的制动鼓内侧面发生摩擦,从而起到制动的效果。 在踩下刹车踏板时,推动刹车总泵的活塞运动,进而在油路中产生压力,制动液将压力传递到车轮的制动分泵推动活塞,活塞推动制动蹄向外运动,进而使得摩擦片与刹车鼓发生摩擦,从而产生制动力。
从结构中可以看出,鼓式制动器是工作在一个相对封闭的环境,制动过程中产生的热量不易散出,频繁制动影响制动效果。不过鼓式制动器可提供很高的制动力,广泛应用于重型车上。 ●盘式制动器
摩擦材料几大巨头的介绍及产品编码规律以及刹车片的组成部分
世界刹车片的知名公司介绍及号码规律。 菲罗多公司于1897年在英格兰成立,1897年,制造出世界第一个刹车片。1995年,世界原厂装车市场占有率近50%,产量世界第一。FERODO-菲罗多是世界摩擦材料标准协会FMSI的发起人和主席。菲罗多-FERODO现为美国辉门公司(FEDERAL-MOGUL)旗下品牌。菲罗多在全世界20多个国家设为20多间独立或或合资或以发放专利许可证方式合作生产的工厂。生产和销售的主要品牌有:FEROD… 天合汽车集团(TRW Automotive) 是全球领先的汽车安全系统供应商,集团总部设在美国密歇根州利沃尼亚市,在全球25多个国家和地区拥有63,000多名员工,2005年销售额达126亿美元。天合生产制动、转向、悬挂、乘员安全方面的高科技主、被动安全产品及系统并提供售后市场作业。… 做为日本顶级的刹车片制造厂家,阿基波罗的OEM客户包括:通用(General Motors),福特(Ford Motor Company),戴姆勒·克莱斯勒(DaimlerChrysler),本田H(Honda),丰田(Toyota),三菱(Mitsubishi),马自达(Mazda),日产(Nissan),斯巴鲁(Subaru),五十铃(Isuzu)。实力自然无需多言。号码规律… MK Kashiyama Corp.公司是日本著名的汽车制动系统配件生产厂商。MK品牌在日本国内维修市场上享有最高的市场占有率,其高度可靠的制动零件在日本及全球市场上供应并受到好评。产品编码规律:刹车片:D9024,D9051M,编码解读:第一位“D”表示DISC BRAKE,指盘式刹车片。第二位数字表示车型,例如第二位是数字“1”,表示… 1948年,汽车售后市场摩擦材料制造商成立了一个行业协会叫“世界摩擦材料标准协会”。为汽车售后市场建立一个标准化的编码系统。该系统涉及的产品包括汽车制动系统配件和离合器面片。在北美,所有在公路上使用的车辆,均使用FMSI编码标准。… WVA编号是一个适用于道路车辆以及工程机械的刹车片-离合器片-其他摩擦材料的一种编码标准。WVA编码系统由德国摩擦材料产业协会(VRI-Verband der Reibbelagindustrie)建立。该协会位于德国科隆,是欧洲摩擦材料制造商协会(FEMFM - Federation of European Manufacturers of Friction Materials)成员之一。… ATE公司创建于1906年,后合并于德国大陆集团。在其创建后近一个世纪的时间里,一直是汽车制动系统的领导者。ATE产品覆盖整个制动系统,包括:刹车总泵、刹车分泵、刹车盘、刹车片、刹车软管、增压器、制动钳、刹车油、轮速传感器、ABS和ESP系统等。… 西班牙耐磨士公司成立超过三十年,是当今汽车刹车零件的领先生产商。公司在欧美地区拥有超过10间工厂,并不断扩展着。1997年,该公司被LUCAS收购。1999年,因LUCAS公司被TRW集团整体收购,随后成为TRW集团底盘体系的一部分。在中国,2008年,耐磨士成为中国重汽盘式制动刹车片的独家供应商。… TEXTAR(泰克斯塔)为泰明顿旗下品牌之一。德国泰明顿(TMD)摩擦村料集团成立于1913年,是欧洲最大的OE供应商之一。生产的TEXTAR(泰克斯塔)制动片,完全按照汽车和制动片行业的规范和标准进行检测,与驾驶有关的20多种制动性能都在检测之列,仅测试项目超过50种。… PAGID公司于1948年建立于德国埃森市,它是欧洲最优秀最古老的摩擦材料制造商之一。1981年,PAGID 和Cosid, Frendo and Cobreq一起成为Rütgers Automotive团体的成员。如今,这个团体已经成为TMD (Textar, Mintex, Don)的一部分。… 优力(JURID)与奔德士(Bendix)一样,同属霍尼韦尔摩擦材料有限公司旗下品牌。优力刹车片在德国生产,主要配套奔驰,宝马,大众,奥迪。优力(JURID)刹车片号码规律:A,乘用车:571488 J,
鼓式制动器设计(设计说明书)
毕业设计设计说明书 题目 SC6408V 商用车 鼓式制动器总成设计专业车辆工程(汽车工程)班级 2006级汽车一班 学生 ___ 廖械兵 指导老师 ___ 文孝霞 重庆交通大学2010年
前言 1 本课题的目的和意义 近年来,国内、外对汽车制动系统的研究与改进的大部分工作集中在通过对汽车制动过程的有效控制来提高车辆的制动性能及其稳定性,如ABS 技术等,而对制动器本身的研究改进较少。然而,对汽车制动过程的控制效果最终都须通过制动器来实现,现代汽车普遍采用的摩擦式制动器的实际工作性能是整个制动系中最复杂、最不稳定的因素,因此改进制动器机构、解决制约其性能的突出问题具有非常重要的意义。 对于蹄-鼓式制动器,其突出优点是可利用制动蹄的增势效应而达到很高的制动效能因数,并具有多种不同性能的可选结构型式,以及其制动性能的可设计性强、制动效能因数的选择范围很宽、对各种汽车的制动性能要求的适应面广,至今仍然在除部分轿车以外的各种车辆的制动器中占主导地位。但是,传统的蹄-鼓式制动器存在本身无法克服的缺点,主要表现于:其制动效能的稳定性较差,其摩擦副的压力分布均匀性也较差,衬片磨损不均匀;另外,在摩擦副局部接触的情况下容易使制动器制动力矩发生较大的变化,因此容易使左右车轮的制动力产生较大差值,从而导致汽车制动跑偏。 对于钳-盘式制动器,其优点在于:制动效能稳定性和散热性好,对摩擦材料的热衰退较不敏感,摩擦副的压力分布较均匀,而且结构较简单、维修较简便。但是,钳-盘式制动器的缺点在于:其制动效能因数很低(只有0.7 左右),因此要求很大的促动力,导致制动管路内液体压力高,而且其摩擦副的工作压强和温度高;制动盘易被污染和锈蚀;当用作后轮制动器时不易加装驻车制动机构等。 因此,现代车辆上迫切需要一种可克服已有技术不足之处的先进制动器,它可充分发挥蹄-鼓式制动器制动效能因数高的优点,同时具有摩擦副压力分布均匀、制动效能稳定以及制动器间隙自动调节机构较理想等优点。 2 商用车制动系概述 汽车制动系是用以强制行驶中的汽车减速或停车、使下坡行驶的汽车车速保持稳定以及使已停驶的汽车在原地(包括在斜坡上)驻留不动的机构。从汽车诞生时起,车辆制动系统在车辆的安全方面就扮演着至关重要的角色。近年来,随着车辆技术的进步和汽车行驶速度的提高,这种重要性表现得越来越明显。也只有制动性能良好、制
探究刹车片摩擦材料的研究现状与发展趋势
探究刹车片摩擦材料的研究现状与发展趋势 发表时间:2019-09-18T10:02:32.580Z 来源:《防护工程》2019年11期作者:赵盟盟 [导读] 新型陶瓷基摩擦材料是当前全新的一种材料,其材料的引用可以提升安全性与稳定性,满足当前的需求。 山东金麒麟股份有限公司山东乐陵 253600 摘要:现阶段的工业制造逐渐向轻量化、高质量、高安全以及高寿命方向发展,进而对当前的制动系统提出更高的要求,以保证其整体性能。新型陶瓷基摩擦材料是当前全新的一种材料,其材料的引用可以提升安全性与稳定性,满足当前的需求。 关键词:刹车片摩擦材料;现状;发展 1 引言 作为车辆和机械离合器总成及制动器中的关键性安全部件,高性能刹车片摩擦材料的研究广泛受到各科研机构和主机厂的关注。刹车片摩擦材料作为制动装置中的核心要素,利用摩擦材料的摩擦性能将转动的动能转化为热能及其他形式的能量,从而实现运动装置制动,其性能的优良直接影响着整机装备运行的安全性、可靠性、舒适性等. 2 刹车片摩擦材料的主要性能 一般对刹车片的基本要求主要有耐磨损、摩擦系数大、优良的隔热性能。按无石棉有机物刹车材料主要是作为石棉的替代晶而研制的,用于制动鼓或制动蹄。摩擦材料是一种应用在动力机械上,依靠摩擦作用来执行制动和传动功能的部件材料。它主要包括制动器衬片(刹车片)和离合器面片(离合器片)。刹车片用于制动,离合器片用于传动。任何机械设备与运动的各种车辆都必须要有制动或传动装置。摩擦材料是这种制动或传动装置上的关键性部件。它最主要的功能是通过摩擦来吸收或传递动力。如离合器片传递动力,制动片吸收动能。它们使机械设备与各种机动车辆能够安全可靠地工作。 所以说摩擦材料是一种应用广泛又甚关键地材料。摩擦材料是一种高分子三元复合材料,是物理与化学复合体。它是由高分子粘结剂(树脂与橡胶)、增强纤维和摩擦性能调节剂三大类组成及其它配合剂构成,经一系列生产加工而制成的制品。摩擦材料的特点是具有良好的摩擦系数和耐磨损性能,同时具有一定的耐热性和机械强度,能满足车辆或机械的传动与制动的性能要求。它们被广泛应用在汽车、火车、飞机、石油钻机等各类工程机械设备上。民用品如自行车、洗衣机等作为动力的传递或制动减速用不可缺少的材料。 3 刹车片摩擦材料发展过程 通过上文的分析发现,阿基波罗工业株式会社和美国辉门公司在专利数量和时期上具有代表性,对其各个时期的代表性专利进行分析,发现刹车片摩擦材料的发展可分为去石棉时期、无石棉发展时期和新材料时期。 3.1 去石棉时期 早在19世纪30年代,菲罗多就有专利提到了含铅或铅合金的摩擦片,还有一篇专利提到了含石棉的刹车片,这就是早期的石棉刹车片。早期的刹车片往往含有石棉,因为石棉能为摩擦材料提供较高机械强度及良好的耐热性、耐磨性等关键性能,甚至至今石棉在摩擦材料中的影响还没有被单一增强纤维所取代。自19世纪50年代,石棉被发现可能具有致癌性。之后19世纪70年代,石棉的致癌形成了一种共识,1989年,美国出台了法案规定禁止石棉材料的使用。 随后,各公司开始寻求对石棉的替代,大体分为两个发展方向,一种为用金属纤维等进行替代,后来演变为用途十分广泛的半金属刹车片,如菲罗多专利中出现了含金属纤维的刹车片,金属开始替代石棉;1982年阿基波罗公司一种定义为半金属的刹车片出现了,中提到了铝和氧化铝同酚醛树脂、金属粉末、橡胶、石墨和钢纤和高含碳量的铁粉热压得到这种摩擦材料。其中钢纤维和金属粉末(如:还原铁粉、铸铁粉等)主要替代石棉用作增强材料。提出一种包含碎玻璃纤维的摩擦材料具有良好的抗磨损和抗衰退性能,具体包含树脂,碎玻璃纤维(浸渍有1%的酚醛树脂)、有机粉末、填料、金属粉末、润滑剂和一些其他的纤维,并且分散了噪音的集中产生。这种刹车片即为早期的NAO型刹车片。此阶段汽车工业对于汽车速度提出了更高的要求,因此摩擦材料不仅关注对石棉纤维的替代,对于粘结剂的改性以提高分解温度也被重视。 3.2 无石棉发展时期 从20世纪80年代至2000年,刹车片摩擦材料的专利开始大量涌现,主要还是针对无石棉配方的改进。半金属配方刹车片具有较高的摩擦系数,优异的热传导性和耐磨性,但也有易生锈、易损伤刹车盘等缺点,另外在噪音和舒适性方面都不尽如人意,这也不满足汽车工业对汽车舒适性的要求。世界发达国家更加注重对噪音、振动、顿挫感(简称NVH)等舒适性能方面的研究。减少刹车片中金属含量,由半金属向低金属转变成为当时的主要研究方向。最显著的特点是发表了大量无石棉有机(简称NAO)刹车片,NAO主要特点为具有适宜的摩擦系数、低噪音、少落灰和较好的舒适性。 3.3 新材料时期 3.3.1 新型陶瓷基摩擦材料 21世纪初,面对世界范围内对于汽车环保和舒适性更高的要求,刹车片摩擦材料的发展对环保要求也越来越苛刻,日本、欧美地区的刹车片向着绿色,环保,经济的方向发展。此时由于芳纶与钛酸钾纤维具有良好的协同作用,在NAO型刹车片中已得到了十分广泛的应用。粉末状钛酸钾的工艺,并且和纤维状钛酸钾具有相似的摩擦性能和力学强度,可以对钛酸钾纤维进行替代。 3.3.2 新型陶瓷基摩擦材料 汽车制动器在进行制作过程中,其主要是利用当前的衬片功能进行发挥,其由当前的填料、增强纤维以及粘结剂组成,利用粘接剂自身的功能与优势,将相关的材料进行合理的融合,经过粘接、加热、固化等工序,促使其形成质量良好的摩擦材料,提升整体性能,满足当前的需求。例如,作者通过合理的实验,对当前的汽车刹车片新型陶瓷基材料的性能进行分析,通过不同的粘结剂的不同体积分数明确其最优效果,进而选择出摩擦材料的最高强度与韧性,提升其整体性能。以实际的案例为例,在某实验中,将当前的钛酸钾晶须作为增强纤维,充分发挥出其自身的摩擦性能,并利用不同的钛酸钾含量进行分析,不同的含量对其整体性能产生的影响。 填料也是当前重要的组成部分,其自身的性能优势在于对摩擦材料的磨损性能进行合理的调节,进而提升其实际的制动与传动要求,例如,当前较为常见的填料主要有碳酸钙、氧化铁、氧化铝等相关的材料,不同的材料其对于当前的性能影响也不同。氧化铝可以提升材
摩擦材料的演变过程
摩擦材料的演变过程 摩擦材料的演变发展,经历了100多年的历史。早期马力车时代,简单的制动是用木头、皮革等施加反作用力于车轮来实现。1897年英国人发明了制动片,并建立了世界上第一个生产摩擦材料的公司。安徽中力车辆制动系统制造有限公司是国内专业生产陶瓷刹车片的品牌厂家。最初的摩擦材料是由毛发或者棉带为基本组成,然后用沥青溶液浸渍加工成型,用于马力车和早期的机动车辆。棉带是天然纤维,其耐温性十分有限,到150度以上时就会失去摩擦能力。英国人认识到了它的缺陷,于1908年发明了用石棉代替天然纤维,缠绕制造摩擦材料。这是摩擦材料发展的第一次跳跃,从此奠定了一个世纪的摩擦材料发展基础。 石棉纤维在摩擦材料上的应用具有里程碑的意义。石棉是天然生成的矿物纤维,在摩擦材料中石棉的主要作用是其具有良好的耐热性,短期可以经受住700度以上的温度,又具有增强和阻燃效果,与粘合剂及各种填料的相容性也十分理想,石棉的应用使摩擦材料具有了真正的安全保障。 英国人最初发明的石棉摩擦材料,是用沥青、油和树胶的混合物,将铜线增强的石棉线缠绕粘接在一起。20世纪20年代中期,一个人研究用模压成型来代替缠绕成型,获得了第一个无缠绕摩擦材料的专利。专利应用了温石棉短纤维和黄铜粒等材料,并用亚麻籽油和高挥发性的烟煤代替了沥青。英国人也开发出了自己的干法混合模压成型摩擦材料,用于伦敦地铁的制动块。 20世纪初,化学家们开发出的具有更好热稳定性的酚醛树脂粘合剂进入实际应用阶段。酚醛树脂与干法混合工艺一起为更复杂的配料混合和鼓式制动片的发展开辟了道路;20世纪30年代,一些人也开始用橡胶、纺织棉布和石棉布,模仿橡胶行业的辊轧方法加工程要求的尺寸厚度;之后人们又开发了能够模压的橡胶/石棉纤维混合物;油改性的酚醛树脂与缠绕成型结合的短切石棉线或短石棉纤维制造的摩擦材料被应用于军用坦克的离合器片。