风力发电叶片制作工艺介绍

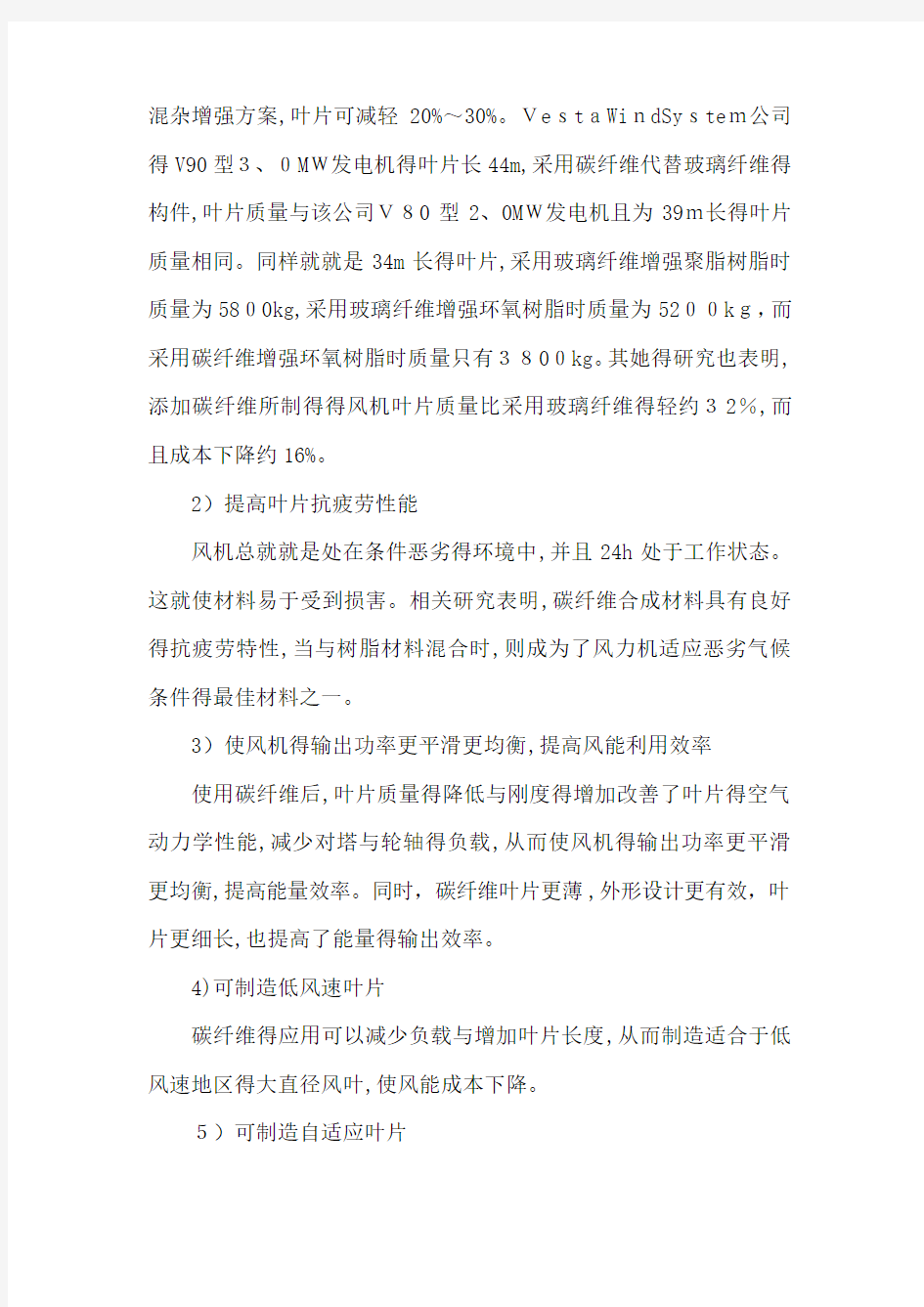
风力发电叶片制作工艺介绍
风力发电机叶片就就是接受风能得最主要部件,其良好得设计、可靠得质量与优越得性能就就是保证发电机组正常稳定运行得决定因素,其成本约为整个机组成本得15%-20%。根据“风机功价比法则”,风力发电机得功率与叶片长度得平方成正比,增加长度可以提高单机容量,但同时会造成发电机得体积与质量得增加,使其造价大幅度增加。
1碳纤维在风力发电机叶片中得应用
叶片材料得发展经历了木制、铝合金得应用,进入了纤维复合材料时代。纤维材料比重轻,疲劳强度与机械性能好,能够承载恶劣环境条件与随机负荷,目前最普遍采用得就就是玻璃纤维增强聚酯(环氧)树脂。但随着大功率发电机组得发展,叶片长度不断增加,为了防止叶尖在极端风载下碰到塔架,就要求叶片具有更高得刚度。国外专家认为,玻璃纤维复合材料得性能已经趋于极限,不能满足大型叶片得要求,因此有效得办法就就是采用性能更佳得碳纤维复合材料。
1)提高叶片刚度,减轻叶片质量
碳纤维得密度比玻璃纤维小约30%,强度大40%,尤其就就是模量高3~8倍。大型叶片采用碳纤维增强可充分发挥其高弹轻质得优点。荷兰戴尔弗理工大学研究表明,一个旋转直径为120m得风机得叶片,由于梁得质量超过叶片总质量得一半,梁结构采用碳纤维,与采用全玻璃纤维得相比,质量可减轻40%左右;碳纤维复合材料叶片刚度就就是玻璃纤维复合材料叶片得2倍。据分析,采用碳纤维/玻璃纤维
混杂增强方案,叶片可减轻20%~30%。VestaWindSystem公司得V90型3、0MW发电机得叶片长44m,采用碳纤维代替玻璃纤维得构件,叶片质量与该公司V80型2、0MW发电机且为39m长得叶片质量相同。同样就就是34m长得叶片,采用玻璃纤维增强聚脂树脂时质量为5800kg,采用玻璃纤维增强环氧树脂时质量为5200kg,而采用碳纤维增强环氧树脂时质量只有3800kg。其她得研究也表明,添加碳纤维所制得得风机叶片质量比采用玻璃纤维得轻约32%,而且成本下降约16%。
2)提高叶片抗疲劳性能
风机总就就是处在条件恶劣得环境中,并且24h处于工作状态。这就使材料易于受到损害。相关研究表明,碳纤维合成材料具有良好得抗疲劳特性,当与树脂材料混合时,则成为了风力机适应恶劣气候条件得最佳材料之一。
3)使风机得输出功率更平滑更均衡,提高风能利用效率
使用碳纤维后,叶片质量得降低与刚度得增加改善了叶片得空气动力学性能,减少对塔与轮轴得负载,从而使风机得输出功率更平滑更均衡,提高能量效率。同时,碳纤维叶片更薄,外形设计更有效,叶片更细长,也提高了能量得输出效率。
4)可制造低风速叶片
碳纤维得应用可以减少负载与增加叶片长度,从而制造适合于低风速地区得大直径风叶,使风能成本下降。
5)可制造自适应叶片
叶片装在发电机得轮轴上,叶片得角度可调。目前主动型调节风机得设计风速为13~15m/s(29~33英里/h),当风速超过时,则调节风叶斜度来分散超过得风力,防止对风机得损害。斜度控制系统对逐步改变得风速就就是有效得。但对狂风得反应太慢了,自适应得各向异性叶片可帮助斜度控制系统,在突然得、瞬间得与局部得风速改变时保持电流得稳定。自适应叶片充分利用了纤维增强材料得特性,能产生非对称性与各向异性得材料,采用弯曲/扭曲叶片设计,使叶片在强风中旋转时可减少瞬时负载。美国Sandia National Lab oratories致力于自适应叶片研究,使1、5MW风机得发电成本降到4、9美分/(kWh),价格可与燃料发电相比。
6)利用导电性能避免雷击
利用碳纤维得导电性能,通过特殊得结构设计,可有效地避免雷击对叶片造成得损伤。
7)降低风力机叶片得制造与运输成本
由于减少了材料得应用,所以纤维与树脂得应用都减少了,叶片变得轻巧,制造与运输成本都会下降,可缩小工厂得规模与运输设备。
8)具有振动阻尼特性
碳纤维得振动阻尼特性可避免叶片自然频率与塔架短频率间发生任何共振得可能性。
2叶片制造工艺及流程
2、1三维编织体/VARTM技术
2、1、1材料选择
目前得风力发电机叶片基本上就就是由聚酯树脂、乙烯基树脂与环氧树脂等热固性基体树脂与玻璃纤维、碳纤维等增强材料,通过手工铺放、树脂注入成型工艺复合而成。对同一种基体树脂,采用玻璃纤维增强得复合材料制造得叶片得强度与刚度得性能要差于采用碳纤维增强得复合材料制造得叶片得性能。随着叶片长度不断增加,叶片对增强材料得强度与刚性等性能也提出了新得要求,从而对玻璃纤维得拉伸强度与模量也提出了更高得要求。为了保证叶片能够安全得承担风温度等外界载荷,大型风机叶片可以采用玻璃纤维/碳纤维混杂复合材料结构,尤其就就是在翼缘等对材料强度与刚度要求较高得部位,则使用碳纤维作为增强材料。这样,不仅可以提高叶片得承载能力,由于碳纤维具有导电性,也可以有效地避免雷击对叶片造成得损伤。
2、1、2三维编织
增强材料预成型加工方法有:手工铺层、编织法、针织法、热成型连续原丝毡法、预成型定向纤维毡法、p Form法与三维编织技术等。
编织法过去大多采用经纬交织得机织物来制作玻/碳纤维基布材料,从承载状态上来考虑采用经编织物作为增强复合材料得基布比经纬交织得机织物具有更明显得优势。如图1所示:
图1、经编织物结构图
这类轴向织物由于承受载荷得纱线系统按要求排列并绑缚在一起,因此能够处于最佳得承载状态。另一方面,由于机织物中得纱线呈波浪形弯曲,再加上纱线自身得捻度,使其模量、拉伸强度与抗冲击强度都有一定得损失。而轴向技术使得织物得纱线层能按照特定得方向伸直取向,故每根纤维力学理论值得利用率几乎能达到100%。此外,轴向织物得纱线层层铺叠,按照不同得强度与刚度要求,可以在织物得同一层或不同层采用不同种类得纤维材料,如玻璃纤维、碳纤维或碳/玻混杂纤维,再按照编织点由编织纱线将其绑缚在一起。
除了经编轴向织物外,还可以利用纬编绑缚系统开发纬编轴向织物,如图2所示:
图2、纬编织物结构图
根据经纬编结构得特性,纬编轴向织物较经编绑缚结构具有更好得可成型性,因此在风电叶片结构设计中具有极好得应用前景。
三维编织技术得发展就就是因为单向或二向增强材料所制得得复合材料层间剪切强度低,抗冲击性差,不能用作主受力件。采用三维编织技术不仅能直接编织复杂结构形状得不分层整体编织物,从根本上消除铺层。三维编织复合材料采用了三维编织技术,其纤维增强结构在空间上呈网状分布,可以定制增强体得形状,制成得材料浑然一体,不存在二次加工造成得损伤,因此这种材料不仅具备传统复合材料所具有得高比强度、高比模量等优点,还具有高损伤容限与断裂韧性以及耐冲击、不分层、抗开裂与耐疲劳等特点。
按编织工艺分,常见得编织材料可分为四步编织法、二步编织法与多层联锁编织法等3类。其中四步编织法发明最早,应用最广。按编织预制件得横截面形状,三维编织方法可分为矩形编织、圆形编织与异形编织3大类,其中矩形编织工艺适合编织矩形与板状材料得增强体,而圆形编织适合编织圆形与管型材料得增强体,异形编织则用于编织各种特殊形状得增强体。只要织物得结构形状就就是由矩形组合或就就是圆或圆得某一部分组合而成,就可以用编织方法一次成型。
四步编织法发明之初,所有得纱线都参加编织运动,且全部编织纱都在空间3个方向内发生相对运动,因此这种编织方法就就是一种真正得三维编织工艺。具体编织过程如图3(a)所示,在一个编织周期中,编织纱沿着正交得2个方向依次进行往复运动,一个完整得编织周期中携纱器需要完成4个动作,因此被称为四步法。如图3(b)所示,由于结构中所有纱线在空间中得分布只有4个不同得方向,因此制成得复合材料被称为三维四向编织复合材料。
针对三维编织物得特点,RTM工艺就就是三维编织复合材料成型得最有效方法。根据三维编织物得形状制成模具,将预成型坯装入模腔,此时同时控制了纤维体积含量与制品形状;预成型坯中纤维束间得空隙为树脂传递提供了通道,而且三维编织体很好得整体性提高了预成型坯耐树脂冲刷得能力。
2、1、3 RTM工艺
树脂传递模塑法简称RTM法,就就是首先在模具型腔中铺放好按性能与结构要求设计得增强材料预成型体,采用注射设备通过较低得成型压力将专用低粘度树脂体系注入闭合式型腔,由排气系统保证树脂流动顺畅,排出型腔内得全部气体与彻底浸润纤维,由模具得加热系统使树脂等加热固化而成型为FRP构件。RTM工艺属于半机械化得FRP成型工艺,特别适宜于一次整体成型得风力发电机叶片,无需二次粘接。与手糊工艺相比,这种工艺具有节约各种工装设备、生产效率高、生产成本低等优点。同时由于采用低粘度树脂浸润纤维以及加温固化工艺,复合材料质量高,且RTM工艺生产较少依赖工人得技术水平,工艺质量仅仅依赖于预先确定好得工艺参数,产品质量易于保证,废品率低,工艺流程如图4所示。
注胶压力得选择一直就就是RTM成型工艺中一个有争议得问题。
低压注胶可促进树脂对纤维表面得浸润;高压注胶可排出残余空气,缩短成型周期,降低成本。加大注胶压力可提高充模速度与纤维渗透率。所以有人赞成在树脂传递初期使用低压以使树脂较好地浸润纤维,而当模具型腔中已基本充满树脂时使用较大压力以逐出残余空气。但压力不能太大,否则会引起预成型坯发生移动或变形。
注胶温度取决于树脂体系得活性期与达到最低粘度得温度。在不至于过大缩短树脂凝胶时间得前提下,为了使树脂能够对纤维进行充分得浸润,注胶温度应尽量接近树脂达到最低粘度得温度。温度过高会缩短树脂得活性期,影响树脂得化学性质,进而可能影响到制品得力学性能;温度过低会使树脂粘度增大,压力升高,也阻碍了树脂正常渗入纤维得能力。注射温度与模具预热温度得选择要结合增强体得特性及模具中得纤维量等综合考虑。
RTM工艺得技术含量高,无论就就是模具设计与制造、增强材料得设计与铺放、树脂类型得选择与改性、工艺参数(如注塑压力、温度、树脂粘度等)得确定与实施,都需要在产品生产之前通过计算机模拟分析与实验验证来确定。
2、1、4 VARTM工艺
随着技术得发展,现已开发出多种较先进得工艺,如预浸料工艺、机械浸渍工艺及真空辅助灌注工艺。真空辅助灌注成型工艺就就是近几年发展起来得一种改进得RTM工艺。它多用于成型形状复杂得大型厚壁制品。真空辅助就就是在注射树脂得同时,在排气口接真空泵,一边注射一边抽真空,借助于铺放在结构层表面得高渗透率得介质引
导将树脂注入到结构层中。这样不仅增加了树脂传递压力,排除了模具及树脂中得气泡与水分,更重要得就就是为树脂在模具型腔中打开了通道,形成了完整通路。另外,无论增强材料就就是编织得还就就是非编织得,无论树脂类型及粘度如何,真空辅助都能大大改善模塑过程中纤维得浸润效果。所以,真空辅助RTM(VARTM)工艺能显著减少最终制品中夹杂物与气泡得含量,就算增大注入速度也不会导致孔隙含量增加,从而提高制品得成品率与力学性能。
用真空灌注工艺生产碳纤维复合材料存在困难。碳纤维比玻纤更细,表面更大,更难有效浸渍,适用得树脂粘度更低。SP公司得SPRINT工艺技术就采用树脂膜交替夹在碳纤维中,经加热与真空使树脂向外渗透。树脂沿铺层得厚度方向浸渍,浸渍快且充分,同时采用真空加速树脂得流动。
2、2叶片复合材料结构设计流程
2、2、1常规制备流程
1)制造外壳与主梁外壳由玻璃钢在模具内进行制造,主梁在真空袋中高温浇注而成;
2)安置模具,在模具内喷涂胶衣树脂,形成叶片得保护表面;
3)把外壳放入模具中,并铺覆玻璃纤维;
4)安装主梁,起到支撑作用;
5)安装泡沫材料;
6)在泡沫材料上铺覆玻璃纤维;
7)在玻璃纤维与泡沫材料上铺放真空膜;
8)灌注树脂,并进行高温真空浇注;
9)取下真空膜;
10)用相同方法制成另外一半壳体;
12)安装腹板(腹板为夹层结构);
13)安装避雷装置等;
14)安置主模具,在壳体边缘与腹板上涂胶粘剂,粘合两壳体;
15)加热,使玻璃纤维更硬;
16)叶片脱模,进行最终加工(切割与打磨)。
模具由符合材料制作而成,这样模具更轻,刚度更高。另外,用同种材料制造得叶片与其模具在灌注树脂时对温升得反应相同。
2、2、2加入碳纤维改进
随着叶片长度得增加,对材料刚度提出了更高得要求。玻璃纤维复合材料得性能已经达到应用极限,不能有效满足材料要求,因此碳纤维在风机叶片中得应用逐年增加。但就就是由于碳纤维比玻璃纤维昂贵,采用100%得碳纤维制造叶片从成本上来说就就是不合算得。目前国外碳纤维主要就就是与玻璃纤维混合使用,碳纤维只就就是用到一些关键得部分。碳纤维在叶片中应用得主要部位有,如图5所示:
1)横梁,尤其就就是横梁盖。
2)前后边缘,除了提高刚度与降低重量外,还起到避免雷击对叶片造成得损伤。
3)叶片得表面,采用具有高强度特性得碳纤维片材。
采用三维四步编织术,主体使用GFR,在图5所示得5、6、7、8区域轴向加入CFR,织出与模具形状一致得预制件。将预制件固定在模具中,采用VARTM得方式注入树脂。
风力发电叶片制作工艺介绍
风力发电叶片制作工艺 介绍 Company Document number:WTUT-WT88Y-W8BBGB-BWYTT-19998
风力发电叶片制作工艺介绍风力发电机叶片是接受风能的最主要部件,其良好的设计、可靠的质量和优越的性能是保证发电机组正常稳定运行的决定因素,其成本约为整个机组成本的15%-20%。根据“风机功价比法则”,风力发电机的功率与叶片长度的平方成正比,增加长度可以提高单机容量,但同时会造成发电机的体积和质量的增加,使其造价大幅度增加。 1碳纤维在风力发电机叶片中的应用 叶片材料的发展经历了木制、铝合金的应用,进入了纤维复合材料时代。纤维材料比重轻,疲劳强度和机械性能好,能够承载恶劣环境条件和随机负荷,目前最普遍采用的是玻璃纤维增强聚酯(环氧)树脂。但随着大功率发电机组的发展,叶片长度不断增加,为了防止叶尖在极端风载下碰到塔架,就要求叶片具有更高的刚度。国外专家认为,玻璃纤维复合材料的性能已经趋于极限,不能满足大型叶片的要求,因此有效的办法是采用性能更佳的碳纤维复合材料。 1)提高叶片刚度,减轻叶片质量 碳纤维的密度比玻璃纤维小约30%,强度大40%,尤其是模量高3~8倍。大型叶片采用碳纤维增强可充分发挥其高弹轻质的优点。荷兰戴尔弗理工大学研究表明,一个旋转直径为120m的风机的叶片,由于梁的质量超过叶片总质量的一半,梁结构采用碳纤维,和采用全玻璃纤维的相比,质量可减轻40%左右;碳纤维复合材料叶片刚度是玻璃纤维复合材料叶片的2倍。据分析,采用碳纤维/玻璃纤维混杂增强方案,叶片可减轻20%~30%。VestaWindSystem公司的V90型发电机的叶片长44m,采用碳纤维代
风电叶片制造工艺现状及我国目前市场格局
风电叶片制造工艺现状及我国目前市场格局 目前国外风机叶片大量采用复合材料制造,并向大型化、低成本、高性能、轻量化、多翼型和柔性化方向发展。而国内的风机叶片起步晚,离高性能叶片的要求有一定的距离。目前国外大的风力机叶片厂家已积极抢滩中国,如LM、Vestas、Gamesa以及Suzlon等均已入驻天津,就地生产叶片,占据了很大的市场份额。国内的主要厂家如中复连众、保定惠腾等均有引进技术。国家对可再生清洁能源的支持,加快了风力发电的发展速度,也为我国的大型复合材料叶片开发提供了一个不可多得的发展机遇。面临着巨大的市场需求和强劲的国际竞争,我国大型复合材料叶片有着巨大的发展机遇与挑战。 风电叶片制造工艺发展现状 传统复合材料风力发电机叶片多采用手糊工艺制造。手糊工艺的主要特点在于以手工劳动为主,简便易行、成本低,但效率亦低、质量不稳定且工作环境差,多用于中小型叶片的成形。因此手糊工艺生产风机叶片的主要缺点是产品质量对工人的操作熟练程度及环境条件依赖性较大,生产效率低,而且产品质量均匀性波动较大,产品的动静平衡保证性差,废品较高。特别是对高性能的复杂气动外型和夹芯结构叶片,还往往需要黏接第二次加工,黏接工艺需要黏接平台或型架以确保黏接面的贴合,生产工艺更加复杂和困难。 叶片最新发展的成型方法是RTM,即树脂转移模塑成型法。将纤维预成型体置于模腔中,然后注入树脂,加温加压成形。RTM是目前世界上公认的低成本制造方法,发展迅速,应用广泛。应该指出的是RTM是该法的一个总称,其中可有多种分支。生产大型叶片多用的是VARTM和SCRIMP法。VARTM即真空辅助RTM一边抽真空一边注入树脂,此时只用单面模具,另一面用真空袋。SCRIMP即西曼复合材料熔塑成形法,为美国人西曼所发明,仅需单面模具且要求简单,另一面亦为真空袋,适用于制造大型复杂制件。TPI Composites公司已用该法制造了30m长的叶片。Vestas公司和Gamesa公司都采用了预充填的方法,该方法将预充填层切裁成合适的尺寸并放进上、下模段中,一个空心的翼梁也被分层覆盖在一个芯轴柄上。塑料薄膜被铺在三个模型之上,并利用真空法将多层纤维压缩在一起并挤走任何隐蔽的气泡。在真空状态时将模型加热到120 ℃,环氧树脂聚合物将变成黏度非常低的材料,空气释放有助于预充填层固紧在一块,几分钟后,升温使环氧树脂聚合物固化,固化之后,将塑料薄膜移走,将叶片部件黏合成一体。 随着叶片技术的发展,热塑材料得到了应用。LM Glasfibre公司用玻璃钢、碳纤维和热
风力发电叶片制作工艺介绍
风力发电叶片制作工艺介绍 风力发电机叶片是接受风能的最主要部件,其良好的设计、可靠的质量和优越的性能是保证发电机组正常稳定运行的决定因素,其成本约为整个机组成本的15%-20%。根据“风机功价比法则”,风力发电机的功率与叶片长度的平方成正比,增加长度可以提高单机容量,但同时会造成发电机的体积和质量的增加,使其造价大幅度增加。 1碳纤维在风力发电机叶片中的应用 叶片材料的发展经历了木制、铝合金的应用,进入了纤维复合材料时代。纤维材料比重轻,疲劳强度和机械性能好,能够承载恶劣环境条件和随机负荷,目前最普遍采用的是玻璃纤维增强聚酯(环氧)树脂。但随着大功率发电机组的发展,叶片长度不断增加,为了防止叶尖在极端风载下碰到塔架,就要求叶片具有更高的刚度。国外专家认为,玻璃纤维复合材料的性能已经趋于极限,不能满足大型叶片的要求,因此有效的办法是采用性能更佳的碳纤维复合材料。 1)提高叶片刚度,减轻叶片质量 碳纤维的密度比玻璃纤维小约30%,强度大40%,尤其是模量高3~8倍。大型叶片采用碳纤维增强可充分发挥其高弹轻质的优点。荷兰戴尔弗理工大学研究表明,一个旋转直径为120m的风机的叶片,由于梁的质量超过叶片总质量的一半,梁结构采用碳纤维,和采用全玻璃纤维的相比,质量可减轻40%左右;碳纤维复合材料叶片刚度是玻璃纤维复合材料叶片的2倍。据分析,采用碳纤维/玻璃纤维混杂增强方案,叶片可减轻20%~30%。VestaWindSystem公司的V90型
3.0MW发电机的叶片长44m,采用碳纤维代替玻璃纤维的构件,叶片质量与该公司V80型2.0MW发电机且为39m长的叶片质量相同。同样是34m长的叶片,采用玻璃纤维增强聚脂树脂时质量为5800kg,采用玻璃纤维增强环氧树脂时质量为5200kg,而采用碳纤维增强环氧树脂时质量只有3800kg。其他的研究也表明,添加碳纤维所制得的风机叶片质量比采用玻璃纤维的轻约32%,而且成本下降约16%。 2)提高叶片抗疲劳性能 风机总是处在条件恶劣的环境中,并且24h处于工作状态。这就使材料易于受到损害。相关研究表明,碳纤维合成材料具有良好的抗疲劳特性,当与树脂材料混合时,则成为了风力机适应恶劣气候条件的最佳材料之一。 3)使风机的输出功率更平滑更均衡,提高风能利用效率 使用碳纤维后,叶片质量的降低和刚度的增加改善了叶片的空气动力学性能,减少对塔和轮轴的负载,从而使风机的输出功率更平滑更均衡,提高能量效率。同时,碳纤维叶片更薄,外形设计更有效,叶片更细长,也提高了能量的输出效率。 4)可制造低风速叶片 碳纤维的应用可以减少负载和增加叶片长度,从而制造适合于低风速地区的大直径风叶,使风能成本下降。 5)可制造自适应叶片 叶片装在发电机的轮轴上,叶片的角度可调。目前主动型调节风机的设计风速为13~15m/s(29~33英里/h),当风速超过时,则调节
风力发电机叶片工艺流程
风力发电机叶片制作工艺流程 传统能源资源的大量使用带来了许多的环境问题和社会问题,并且其存储量大大降低,因而风能作为一种清洁的可循环再生的能源,越来越受到世界各国的广泛关注。风力发电机叶片是接受风能的最主要部件,其良好的设计、可靠的质量和优越的性能是保证发电机组正常稳定运行的决定因素,其成本约为整个机组成本的15%-20%。根据“风机功价比法则”,风力发电机的功率与叶片长度的平方成正比,增加长度可以提高单机容量,但同时会造成发电机的体积和质量的增加,使其造价大幅度增加。并且,随着叶片的增大,刚度也成为主要问题。为了实现风力的大功率发电,既要减轻叶片的重量,又要满足强度与刚度要求,这就对叶片材料提出了很高的要求。 1 碳纤维在风力发电机叶片中的应用 叶片材料的发展经历了木制、铝合金的应用,进入了纤维复合材料时代。纤维材料比重轻,疲劳强度和机械性能好,能够承载恶劣环境条件和随机负荷,目前最普遍采用的是玻璃纤维增强聚酯(环氧)树脂。但随着大功率发电机组的发展,叶片长度不断增加,为了防止叶尖在极端风载下碰到塔架,就要求叶片具有更高的刚度。国外专家认为,玻璃纤维复合材料的性能已经趋于极限,不能满足大型叶片的要求,因此有效的办法是采用性能更佳的碳纤维复合材料。 1)提高叶片刚度,减轻叶片质量 碳纤维的密度比玻璃纤维小约30%,强度大40%,尤其是模量高3~8倍。大型叶片采用碳纤维增强可充分发挥其高弹轻质的优点。荷兰戴尔弗理工大学研究表明,一个旋转直径为120m的风机的叶片,由于梁的质量超过叶片总质量的一半,梁结构采用碳纤维,和采用全玻璃纤维的相比,质量可减轻40%左右;碳纤维复合材料叶片刚度是玻璃纤维复合材料叶片的2倍。据分析,采用碳纤维/玻璃纤维混杂增强方案,叶片可减轻20%~30%。Vesta Wind System 公司的V90型3.0 MW发电机的叶片长44m,采用碳纤维代替玻璃纤维的构件,叶片质量与该公司V80 型2.0MW发电机且为39m长的叶片质量相同。同样是34 m长的叶片,采用玻璃纤维增强聚脂树脂时质量为5800kg,采用玻璃纤维增强环氧树脂时质量为5200kg,而采用碳纤维增强环氧树脂时质量只有3800kg。其他的研究也表明,添加碳纤维所制得的风机叶片质量比采用玻璃纤维的轻约32%,而且成本下降约16%。 2)提高叶片抗疲劳性能 风机总是处在条件恶劣的环境中,并且24h处于工作状态。这就使材料易于受到损害。相关研究表明,碳纤维合成材料具有良好的抗疲劳特性,当与树脂材料混合时,则成为了风力机适应恶劣气候条件的最佳材料之一。 3)使风机的输出功率更平滑更均衡,提高风能利用效率 使用碳纤维后,叶片质量的降低和刚度的增加改善了叶片的空气动力学性能,减少对塔和轮轴的负载,从而使风机的输出功率更平滑更均衡,提高能量效率。同时,碳纤维叶片更薄,外形设计更有效,叶片更细长,也提高了能量的输出效率。 4)可制造低风速叶片 碳纤维的应用可以减少负载和增加叶片长度,从而制造适合于低风速地区的大直径风叶,使风能成本下降。 5)可制造自适应叶片 叶片装在发电机的轮轴上,叶片的角度可调。目前主动型调节风机的设计风速为13~15m/s(29~33英里/h),当风速超过时,则调节风叶斜度来分散超过的风力,防止对风机的损害。斜度控制系统对逐步改变的风速是有效的。但对狂风的反应太慢了,自适应的各向异性叶片可帮助斜度控制系统,在突然的、瞬间的和局部的风速改变时保持电流的稳定。自适应叶片充分利用了纤维增强材料的特性,能产生非对称性和各向异性的材料,采用弯曲/扭曲叶片设计,使叶片在强风中旋转时可减少瞬时负载。美国Sandia National Laboratories致力于自适应叶片研究,使1.5MW风机的发电成本降到4.9美分/(kW?h),价格可和燃料发电相比。 6)利用导电性能避免雷击
风电叶片质检工序步骤
风电叶片质检工序步骤 质检员:做好工序检验,及时纠正工序差错,保证过程质量,减少返工、返修浪费;负责调查质量检验技术现状;参与质量分析、编制质量控制计划,设计质量控制卡,确定质量控制点;负责确认质量事故现象,参与调查质量事故,分析质量事故原因,编制质量事故报告;负责产品质量状态标识工作,严格控制不良品,确定质量问题、跟踪验证质量问题的解决情况 1、模具清理 叶片脱模后,用刀具清理模具上沾的真空膜以及残留的胶,或用吸胶毡擦拭模具上的粉层,擦拭干净后会用洁膜剂清理模具(通常只是边缘)。 2、脱模剂 模具清理好后,涂一层脱模剂,其固化需要等待一段时间方可铺层。脱模剂的作用在于在模具表面形成一个致密层,使得模具更加容易和叶片分离,达到脱模的效果。 3、部件 整只叶片一般可分为蒙皮、主梁、翻边角、叶跟、粘接角等各个部件,其中主梁、翻边角、叶跟、粘接角等用专用模具进行制作。等将各个部件制好后,在主模具上进行胶接组装在一起,合模后加压固化后制成一整只叶片。 4、主梁 主梁是在单独的模具上成型的,铺放主梁时需要工装对其进行精确定位,并保证经过打磨处理及表面清洁。主梁在切割车间转运到蒙皮车间后需要人工脱模,然后要剥离脱模后残余的一些附着物。最后用布擦拭表面。 5、腹板 PVC泡沫有较高的剪切模量,组成的结构有良好的刚度特性,主要增加截面刚度。上下两层纤维布,中间是泡沫板形成夹芯结构,铺放时需要保证各块PVC板材之间连接紧密。 6、玻璃纤维铺层制作 首先铺脱模布,然后是覆盖整个模具的大布,叶根区域铺设错层,主梁的错层与叶根错层镶嵌。主梁下面需要铺设连续毡,以便导流。主梁通过工装定位后,两旁的轻木和泡沫的位置就有了基准,芯材的位置正确之后,才能保证前缘的单向布铺设正确。此过程需要注意铺放位置正确,搭接尺寸足够。另外还需注意(抽真空时也要留意),叶根增强铺层有几十层,是最容易产生对结构强度影响比较大的褶皱的地方。 7、真空材料 纤维布铺设完成后,需要依次铺设脱模布、带孔隔离膜、导流网、导流管和螺旋管、溢流管、一层真空、吸胶毡、二层真空。脱模布和隔离膜主要起真空灌注工艺结束后更好地去除真空辅料的作用。导流网能更好地排除真空体系中残留的空气,并且能够使树脂均匀地渗透到所生产产品各部位,对灌注的效果和速度都有较大影响。在导流网上方布置有导流管,导流管通过进胶盘连通进胶管;在远离且低于导流管的位置有流管,流管连接抽气管,抽气管连接真空泵和压力表。在以上材料的上方盖至少一层真空袋。打两层真空袋是为了确保抽真空的效果。一层真空上方可放吸胶毡以加快抽真空。真空袋把整个产品密封起来,使得整个系统处于负压状态,以便达到真空灌注的工艺要求。 8、粘接角工装
风电叶片的改进
风电叶片的改进 传统能源资源的大量使用带来了许多的环境问题和社会问题,并且其存储量大大降低,因而风能作为一种清洁的可循环再生的能源,越来越受到世界各国的广泛关注。风力发电机叶片是接受风能的最主要部件,其良好的设计、可靠的质量和优越的性能是保证发电机组正常稳定运行的决定因素,其成本约为整个机组成本的15%-20%。根据“风机功价比法则”,风力发电机的功率与叶片长度的平方成正比,增加长度可以提高单机容量,但同时会造成发电机的体积和质量的增加,使其造价大幅度增加。并且,随着叶片的增大,刚度也成为主要问题。为了实现风力的大功率发电,既要减轻叶片的重量,又要满足强度与刚度要求,这就对叶片材料提出了很高的要求。 1 碳纤维在风力发电机叶片中的应用 叶片材料的发展经历了木制、铝合金的应用,进入了纤维复合材料时代。纤维材料比重轻,疲劳强度和机械性能好,能够承载恶劣环境条件和随机负荷,目前最普遍采用的是玻璃纤维增强聚酯(环氧)树脂。但随着大功率发电机组的发展,叶片长度不断增加,为了防止叶尖在极端风载下碰到塔架,就要求叶片具有更高的刚度。国外专家认为,玻璃纤维复合材料的性能已经趋于极限,不能满足大型叶片的要求,因此有效的办法是采用性能更佳的碳纤维复合材料。 1)提高叶片刚度,减轻叶片质量 碳纤维的密度比玻璃纤维小约30%,强度大40%,尤其是模量高3~8倍。大型叶片采用碳纤维增强可充分发挥其高弹轻质的优点。荷兰戴尔弗理工大学研究表明,一个旋转直径为120m的风机的叶片,由于梁的质量超过叶片总质量的一半,梁结构采用碳纤维,和采用全玻璃纤维的相比,质量可减轻40%左右;碳纤维复合材料叶片刚度是玻璃纤维复合材料叶片的2倍。据分析,采用碳纤维/玻璃纤维混杂增强方案,叶片可减轻20%~30%。Vesta Wind System 公司的V90型3.0 MW发电机的叶片长44m,采用碳纤维代替玻璃纤维的构件,叶片质量与该公司V80 型2.0MW发电机且为39m长的叶片质量相同。同样是34 m长的叶片,采用玻璃纤维增强聚脂树脂时质量为5800kg,采用玻璃纤维增强环氧树脂时质量为5200kg,而采用碳纤维增强环氧树脂时质量只有3800kg。其他的研究也表明,添加碳纤维所制得的风机叶片质量比采用玻璃纤维的轻约32%,而且成本下降约16%。 2)提高叶片抗疲劳性能 风机总是处在条件恶劣的环境中,并且24h处于工作状态。这就使材料易于受到损害。相关研究表明,碳纤维合成材料具有良好的抗疲劳特性,当与树脂材料混合时,则成为了风力机适应恶劣气候条件的最佳材料之一。 3)使风机的输出功率更平滑更均衡,提高风能利用效率 使用碳纤维后,叶片质量的降低和刚度的增加改善了叶片的空气动力学性能,减少对塔和轮轴的负载,从而使风机的输出功率更平滑更均衡,提高能量效率。同时,碳纤维叶片更薄,外形设计更有效,叶片更细长,也提高了能量的输出效率。 4)可制造低风速叶片 碳纤维的应用可以减少负载和增加叶片长度,从而制造适合于低风速地区的大直径风叶,使风能成本下降。 5)可制造自适应叶片 叶片装在发电机的轮轴上,叶片的角度可调。目前主动型调节风机的设计风速为13~15m/s(29~33英里/h),当风速超过时,则调节风叶斜度来分散超过的风力,防止对风机的损害。斜度控制系统对逐步改变的风速是有效的。但对狂风的反应太慢了,自适应的各向异性叶片可帮助斜度控制系统,在突然的、瞬间的和局部的风速改变时保持电流的稳定。自适
宁夏关于成立风电叶片生产制造公司可行性分析报告
宁夏关于成立风电叶片生产制造公司 可行性分析报告 规划设计/投资分析/实施方案
报告摘要说明 风力发电行业主要由上游原材料生产、中游零部件制造和风力机组制造、以及下游风电场运营和电网运营等环节构成。风力发电机主要由叶轮、机舱、塔筒三部分构成。由于风电场招标时塔筒一般单独招标,风力机组 此时即指叶轮和机舱两部分。 xxx实业发展公司由xxx有限责任公司(以下简称“A公司”)与xxx集团(以下简称“B公司”)共同出资成立,其中:A公司出资410.0万元,占公司股份76%;B公司出资130.0万元,占公司股份24%。 xxx实业发展公司以风电叶片产业为核心,依托A公司的渠道资源 和B公司的行业经验,xxx实业发展公司将快速形成行业竞争力,通过 3-5年的发展,成为区域内行业龙头,带动并促进全行业的发展。 xxx实业发展公司计划总投资12239.85万元,其中:固定资产投 资10808.63万元,占总投资的88.31%;流动资金1431.22万元,占总投资的11.69%。 根据规划,xxx实业发展公司正常经营年份可实现营业收入13527.00万元,总成本费用10387.39万元,税金及附加206.07万元,利润总额3139.61万元,利税总额3778.73万元,税后净利润2354.71万元,纳税总额1424.02万元,投资利润率25.65%,投资利税率
30.87%,投资回报率19.24%,全部投资回收期6.70年,提供就业职位187个。 风电作为可再生资源,节能环保,是未来能源的重要发展方向。风电的应用推广,经济性和市场化是重要影响因素。
第一章总论 一、拟筹建公司基本信息 (一)公司名称 xxx实业发展公司(待定,以工商登记信息为准) (二)注册资金 公司注册资金:540.0万元人民币。 (三)股权结构 xxx实业发展公司由xxx有限责任公司(以下简称“A公司”)与xxx集团(以下简称“B公司”)共同出资成立,其中:A公司出资410.0万元,占公司股份76%;B公司出资130.0万元,占公司股份24%。 (四)法人代表 段xx (五)注册地址 xx产业示范基地(以工商登记信息为准) 宁夏回族自治区,简称宁,是中国5个自治区之一,首府银川。位于中国西北内陆地区,界于北纬35°14'-39°14',东经104°17'-109°39'之间,东邻陕西,西、北接内蒙古,南连甘肃,宁夏回族自治区总面积
风电叶片设计流程
叶片设计流程 一. 空气动力设计 1.确定风轮的几何和空气动力设计参数 2.选择翼型 3.确定叶片的最佳形状 4.计算风轮叶片的功率特性 5.如果需要可以对设计进行修改并重复步骤4,以找到制造 工艺约束下的最佳风轮设计。 6.计算在所有可遇尖速比下的风轮特性 对于每个尖速比可采用上面步骤4所述的方法,确定每个叶素的空气动力状态,由此确定整个风轮的性能。 7.风力机叶片三维效应分析 8.非定常空气动力现象 9.风力机叶片的动态失速 10.叶片动态入流 .风机载荷计算 作为风力机设计和认证的重要依据,用于风力机的静强度和疲劳强度分析。国际电工协会制定的IEC61400-1标准、德国船级社制定的GL 规范和丹麦制定的DS 472标准等对风力机的载荷进行了详细的规定。
2.1 IEC61400-1标准规定的载荷情况 2.2 风机载荷计算 1计算模型 1)风模型 (1)正常风模型 (2)极端风模型 (3)三维湍流模型 2)风机模型 风机模型包括几何模型、空气动力学模型、传动系统动力学模型、控制系统闭环模型和运行状态监控模型等。 2风力机载荷特性 1)叶片上的载荷 (1)空气动力载荷 包括摆振方向的剪力Q yb和弯矩M Xb、挥舞方向的剪力Q b和弯矩M Jb以及与变浆距力矩平衡的叶片俯仰力矩M b。可根据叶片空气动力设计步骤4中求得的叶素上法向力系数Cn和切向力系数Ct,通过积分求出作用在叶片上的空气动力载荷。 (2)重力载荷 作用在叶片上的重力载荷对叶片产生的摆振方向弯矩,随叶片方位角的变化呈周期变化,是叶片的主要疲劳载荷。 (3)惯性载荷 (4)操纵载荷
2 )轮毂上的载荷 3)主轴上的载荷 4)机舱上的载荷 5)偏航系统上的载荷 6)塔架上的载荷 三.风力机气动弹性 当风力机在自然风条件下运行时,作用在风力机上的空气动力、惯性力和弹性力等交变载荷会使结构产生变形和振动,影响风力机的正常运行甚至导致风力机损坏。因此,在风力机的设计中必须考虑系统的稳定性和在外载作用下的动力响应,主要有①风力机气动弹性稳定性和动力响应②风力机机械传动系统的振动③风力机控制系统(包括偏航系统和变浆距系统等) 的稳定性和动力响应④风力机系统的振动。 3.1风力机气动弹性现象 1.风力机叶片气动弹性稳定性问题 2.风力机系统振动和稳定性问题 3.2 风力机气动弹性分析 目的是保证风力机在运行过程中不出现气动弹性不稳定。主要的方法 是特征值法和能量法。特征值法是在求解弹性力学的基本方 程中,考虑作用在风力机叶片上的非定常空气动力,建立离散的描述风力机叶片气动弹性运动的微分方程。采用Floquet理论求解,最后稳定性判别归结为状态转移矩阵的特征值 计算。 1.风力机气动弹性模型 1)结构模型
风电厂生产工艺流程
风力发电机生产工艺流程 风轮机 风力发电厂 一、定义 风力发电机主要包括水平轴式风力发电机和垂直轴式风力发电机等。其中,水平轴式风力发电机是目前技术最成熟、生产量最多的一种形式。 二、结构 1、风力发电机组构成:风力发电机组由风轮、传动系统、偏航系统、液 压系统、制动系统、发电机、控制与安全系统、机舱、塔架、变频器和
基础等组成。 2、输变电设备构成:箱式变压器、集电(架空)线路、高压配电装置、主 变构成。 三、生产流程及主要系统 生产流程 风轮将风能转换为机械能,机组通过风力推动叶轮旋转,再通过传动系 统增速来达到发电机的转速后来驱动发电机发电,有效的将风能转化成 电能;整个机舱由高大的塔架举起,由于风向经常变化,为了有效地利 用风能,还安装有迎风装置,它根据风向传感器测得的风向信号,由控 制器控制偏航电机,驱动与塔架上大齿轮啮合的小齿轮转动,使机舱始 终对风;并且通过变频器与箱式变压器相连,及并网发电。发电后电能 通过集电线路、高压配电装置汇集到主变低压侧,经过主变升压后并入 电网。 主要系统 控制系统 监控系统(SCADA):监控系统实现对全风场风机状况的监视与启、 停操作,它包括大型监控 软件及完善的通讯网络。 主控系统:主控系统是风机控制系统的主体,它实现自动启动、自动 调向、自动调速、自动并 网、自动解列、故障自动停机、自动电缆解绕及自动记录与监控等重 要控制、保护功能。它对 外的三个主要接口系统就是监控系统、变桨控制系统以及变频系统 (变频器),它与监控系统 接口完成风机实时数据及统计数据的交换,与变桨控制系统接口完成 对叶片的控制,实现最大 风能捕获以及恒速运行,与变频系统(变频器)接口实现对有功功率 以及无功功率的自动调节。 变桨控制系统:与主控系统配合,通过对叶片节距角的控制,实现最 大风能捕获以及恒速运行, 提高了风力发电机组的运行灵活性。目前来看,变桨控制系统的叶片 驱动有液压和电气两种方 式,电气驱动方式中又有采用交流电机和直流电机两种不同方案。究 竟采用何种方式主要取决 于制造厂家,多年来形成的技术路线及传统。 变频系统(变频)器:与主控制系统接口,和发电机、电网连接,直 接承担着保证供电品质、 提高功率因素,满足电网兼容性标准等重要作用。 发电系统 风力发电系统的主要部件是塔架、发电机、齿轮增速器(一般为传动效率 高的行星齿轮传动)、变桨偏航系统 (按风力大小调整桨叶迎风面)、桨
风电叶片实习总结中材(工艺制造质量)工作总结DOC
实习总结 漫长的实习期已经过去了,这些天来我感受颇多。从一进厂的陌生,到后来对公司上下组织机构和生产制造流程的逐步熟悉,适应这个新环境也经历了并不长的一段时间。作为新进员工,对企业也有了总体认识。从大的方面来看,锡林郭勒风电叶片有限公司处于中材集团的第五层的组织架构,即从上到下依次为中材集团有限公司、中材股份有限公司、中材科技股份有限公司、中材科技风电叶片股份有限公司、和我们所处的中材科技(锡林郭勒)风电叶片股份有限公司。从小的方面来说,我们公司是中材科技风电叶片股份有限公司七个产业基地之一,即北京康庄、北京八达岭、甘肃酒泉、吉林白城、云南大理、江苏阜宁和内蒙锡林。而我公司在其中的生产规模相对较小,生产型号为1.5MW长度为37.5m 和40.3m的两种叶片,在叶片长度区间中属中等,其主要采用行业内传统的复合材料手糊工艺制造。 此次被安排在蒙皮工段合模班进行实习(班组成员共11人,包括我和XXX 在内),班长XXX。从未做过重体力劳动的我,感触最深的是24小时满身的疲惫与伤痛,每一天周而复始,令我的身心都受到了煎熬。每个工作日要合两个模,为了赶进度工作中几乎没有休息的空挡,只有在吃午饭的时候才得到些许放松。时间是紧迫的,吃完饭又马上赶回来继续工作。虽说体能已经处于透支状态,但操作的同时内心明白,只有不断坚持打起精神认认真真做好每一道工序,才能够理解工艺理论和熟悉操作规程。每每遇到不懂的地方,我就“偷个懒”向班里的同事请教,再不清楚就问一旁的质检员,实践中与操作规程文件相比对,不断进行摸索依照这些天的工作重心,我做出了下面的归纳和小结。
一、工艺流程及实际操作中注意事项 一、清理蒙皮 1.撕真空膜 分别在上模和下模用壁纸刀从叶尖处将真空膜割破,沿着模具边缘向叶根方向剥开,将真空膜剥离模具,拉至叶根模具下。 注意事项:割膜时,千万注意勿将真空管和U型管割破,叶根处的膜尾部不急于割掉,平铺于地下裁剪好大小适当的一块,以备后续清理蒙皮其他材料时当做垃圾包装袋使用。 2.清理Z形导流网 将其由叶尖至叶根逐步取下,小心收好,以备上模导胶管接口时使用。 3.摘除下模主胶板护板 用脚蹬踏板边使其脱离模具,如粘结牢固,必要时可用钢管以适当力量击打,至分离后搬开。 注意事项:(1)若击打主胶板,需小心钢管反弹伤及自身,也不要用力过猛以防将主胶板击坏(2)将主胶板小心放置在模具下的板架上,切勿随意扔在地上。 4.撕掉下层导流网织物及多孔膜 首先,将叶尖处导流网用壁纸刀割开,用力将其向上拉,使织物布面与脱模布分离,直至撕到叶根方可。之后,将导流网织物折断叠放由叶根拖至事先铺放
风力发电叶片制作工艺介绍
风力发电叶片制作工艺介绍 风力发电机叶片就就是接受风能得最主要部件,其良好得设计、可靠得质量与优越得性能就就是保证发电机组正常稳定运行得决定因素,其成本约为整个机组成本得15%-20%。根据“风机功价比法则”,风力发电机得功率与叶片长度得平方成正比,增加长度可以提高单机容量,但同时会造成发电机得体积与质量得增加,使其造价大幅度增加。 1碳纤维在风力发电机叶片中得应用 叶片材料得发展经历了木制、铝合金得应用,进入了纤维复合材料时代。纤维材料比重轻,疲劳强度与机械性能好,能够承载恶劣环境条件与随机负荷,目前最普遍采用得就就是玻璃纤维增强聚酯(环氧)树脂。但随着大功率发电机组得发展,叶片长度不断增加,为了防止叶尖在极端风载下碰到塔架,就要求叶片具有更高得刚度。国外专家认为,玻璃纤维复合材料得性能已经趋于极限,不能满足大型叶片得要求,因此有效得办法就就是采用性能更佳得碳纤维复合材料。 1)提高叶片刚度,减轻叶片质量 碳纤维得密度比玻璃纤维小约30%,强度大40%,尤其就就是模量高3~8倍。大型叶片采用碳纤维增强可充分发挥其高弹轻质得优点。荷兰戴尔弗理工大学研究表明,一个旋转直径为120m得风机得叶片,由于梁得质量超过叶片总质量得一半,梁结构采用碳纤维,与采用全玻璃纤维得相比,质量可减轻40%左右;碳纤维复合材料叶片刚度就就是玻璃纤维复合材料叶片得2倍。据分析,采用碳纤维/玻璃纤维
混杂增强方案,叶片可减轻20%~30%。VestaWindSystem公司得V90型3、0MW发电机得叶片长44m,采用碳纤维代替玻璃纤维得构件,叶片质量与该公司V80型2、0MW发电机且为39m长得叶片质量相同。同样就就是34m长得叶片,采用玻璃纤维增强聚脂树脂时质量为5800kg,采用玻璃纤维增强环氧树脂时质量为5200kg,而采用碳纤维增强环氧树脂时质量只有3800kg。其她得研究也表明,添加碳纤维所制得得风机叶片质量比采用玻璃纤维得轻约32%,而且成本下降约16%。 2)提高叶片抗疲劳性能 风机总就就是处在条件恶劣得环境中,并且24h处于工作状态。这就使材料易于受到损害。相关研究表明,碳纤维合成材料具有良好得抗疲劳特性,当与树脂材料混合时,则成为了风力机适应恶劣气候条件得最佳材料之一。 3)使风机得输出功率更平滑更均衡,提高风能利用效率 使用碳纤维后,叶片质量得降低与刚度得增加改善了叶片得空气动力学性能,减少对塔与轮轴得负载,从而使风机得输出功率更平滑更均衡,提高能量效率。同时,碳纤维叶片更薄,外形设计更有效,叶片更细长,也提高了能量得输出效率。 4)可制造低风速叶片 碳纤维得应用可以减少负载与增加叶片长度,从而制造适合于低风速地区得大直径风叶,使风能成本下降。 5)可制造自适应叶片
风力发电机设计与制造课程设计
风力发电机设计与制造 课程设计 Document serial number【UU89WT-UU98YT-UU8CB-UUUT-UUT108】
一.总体参数设计总体参数是设计风力发电机组总体结构和功能的基本参数,主要包括额定功率、发电机额定转速、风轮转速、设计寿命等。 1.额定功率、设计寿命 =;一般风力机组设计寿命至少为20根据《设计任务书》选定额定功率P r 年,这里选20年设计寿命。 2.切出风速、切入风速、额定风速 = 3m/s 切入风速取 V in 切出风速取 V = 25m/s out = 12m/s(对于一般变桨距风力发电机组(选)的额定风速与平额定风速 V r ==×≈12m/s) 均风速之比为左右,V r 3.重要几何尺寸 (1) 风轮直径和扫掠面积 由风力发电机组输出功率得叶片直径: 其中: ——风力发电机组额定输出功率,取; P r ——空气密度(一般取标准大气状态),取m3; ——额定风速,取12m/s; V r D——风轮直径; η——传动系统效率,取; 1 η——发电机效率,取; 2 η——变流器效率,取; 3
C p ——额定功率下风能利用系数,取。 由直径计算可得扫掠面积: 综上可得风轮直径D=104m ,扫掠面积A=84822 m 4. 功率曲线 自然界风速的变化是随机的, 符合马尔可夫过程的特征, 下一时刻的风速和上一时刻的结果没什么可预测的规律。由于风速的这种特性, 可以把风力发电机组的功率随风速的变化用如下的模型来表示: )(t P ——在真实湍流风作用下每一时刻产生的功率, 它由t 时刻的V(t)决定; )(t P stat ——在给定时间段内V(t)的平均值所对应的功率; )(△t P ——表示t 时刻由于风湍流引起的功率波动。 对功率曲线的绘制, 主要在于对风速模型的处理。若假定上式表示的风模型中P stat (t)的始终为零, 即视风速为不随时间变化的稳定值, 在切入风速到切出风速的范围内按照设定的风速步长, 得到对应风速下的最佳叶尖速比和功率系数,带入式: 1η——传动系统效率,取; 2η——发电机效率,取; 3η——变流器效率,取; ——空气密度(一般取标准大气状态),取m 3; V r ——额定风速,取12m/s ; D ——风轮直径; C p ——额定功率下风能利用系数,取。 由以上公式,使用excel 计算出不同风速对应的功率值,见表1
风电叶片质检工序步骤
风电叶片质检工序步骤公司标准化编码 [QQX96QT-XQQB89Q8-NQQJ6Q8-MQM9N]
风电叶片质检工序步骤 质检员:做好工序检验,及时纠正工序差错,保证过程质量,减少返工、返修浪费;负责调查质量检验技术现状;参与质量分析、编制质量控制计划,设计质量控制卡,确定质量控制点;负责确认质量事故现象,参与调查质量事故,分析质量事故原因,编制质量事故报告;负责产品质量状态标识工作,严格控制不良品,确定质量问题、跟踪验证质量问题的解决情况 1、模具清理 叶片脱模后,用刀具清理模具上沾的真空膜以及残留的胶,或用吸胶毡擦拭模具上的粉层,擦拭干净后会用洁膜剂清理模具(通常只是边缘)。 2、脱模剂 模具清理好后,涂一层脱模剂,其固化需要等待一段时间方可铺层。脱模剂的作用在于在模具表面形成一个致密层,使得模具更加容易和叶片分离,达到脱模的效果。 3、部件 整只叶片一般可分为蒙皮、主梁、翻边角、叶跟、粘接角等各个部件,其中主梁、翻边角、叶跟、粘接角等用专用模具进行制作。等将各个部件制好后,在主模具上进行胶接组装在一起,合模后加压固化后制成一整只叶片。 4、主梁 主梁是在单独的模具上成型的,铺放主梁时需要工装对其进行精确定位,并保证经过打磨处理及表面清洁。主梁在切割车间转运到蒙皮车间后需要人工脱模,然后要剥离脱模后残余的一些附着物。最后用布擦拭表面。 5、腹板 PVC泡沫有较高的剪切模量,组成的结构有良好的刚度特性,主要增加截面刚度。上下两层纤维布,中间是泡沫板形成夹芯结构,铺放时需要保证各块PVC 板材之间连接紧密。 6、玻璃纤维铺层制作 首先铺脱模布,然后是覆盖整个模具的大布,叶根区域铺设错层,主梁的错层与叶根错层镶嵌。主梁下面需要铺设连续毡,以便导流。主梁通过工装定位后,两旁的轻木和泡沫的位置就有了基准,芯材的位置正确之后,才能保证前缘的单向布铺设正确。此过程需要注意铺放位置正确,搭接尺寸足够。另外还需注意(抽真空时也要留意),叶根增强铺层有几十层,是最容易产生对结构强度影响比较大的褶皱的地方。 7、真空材料 纤维布铺设完成后,需要依次铺设脱模布、带孔隔离膜、导流网、导流管和螺旋管、溢流管、一层真空、吸胶毡、二层真空。脱模布和隔离膜主要起真空灌注工艺结束后更好地去除真空辅料的作用。导流网能更好地排除真空体系中残留的空气,并且能够使树脂均匀地渗透到所生产产品各部位,对灌注的效果和速度都有较大影响。在导流网上方布置有导流管,导流管通过进胶盘连通进胶管;在远离且低于导流管的位置有流管,流管连接抽气管,抽气管连接真空泵和压力表。在以上材料的上方盖至少一层真空袋。打两层真空袋是为了确保抽真空的效果。一层真空上方可放吸胶毡以加快抽真空。真空袋把整个产品密封起来,使得整个系统处于负压状态,以便达到真空灌注的工艺要求。
风力发电原理及风力发电的工艺流程
风力发原理及风力发电的工艺流程 发电风力发电机最初出现在十九世纪末。自二十世纪八十年代起,这项技术不断发展并日渐成熟,适合工业应用。近二三十年,典型的风力发电机的风轮直径不断增大,而额定功率也不断提升。 在二十一世纪 00 年代初,风力发电机最具经济效益的额定输出功率范围在 600 千瓦至 750 千瓦之间,而风轮直径则在 40 米至 47 米之间。当时所有制造商都有生产这类风力发电机。新一代的兆瓦级风力发电机是以这类机种作为基础发展出来的。
二零零七年初,有一些制造商开始生产额 定功率为几兆瓦而风轮直径达到约 90 米的风力发电机(例如 Vestas V90 3.0 兆瓦风电机, Nordex N90 2.5 兆瓦风电机等等),甚至有些直径达 100 米 ( 如 GE 3.6 兆瓦风电机 ) 。这些大型风力发电 机主要市场是欧洲。在欧洲,适合风电的地段日渐减少,因此有逼切性安装发电能力尽量高的风力发电机。 另一类更大型的为海上应用而设计的风力 发电机,已经完成设计并制成原型机。例如 RE Power 公司设计的风力发电机风轮直径达 126 米,功率达 5 兆瓦。 1) 风的功率 风的能量指的是风的动能。特定质量的空 气的动能可以用下列公式计算。 能量 = 1/2 X 质量 X ( 速度 )^2 吹过特定面积的风的的功率可以用下列公 式计算。 功率 = 1/2 X 空气密度 X 面积 X ( 速度 )^3 其中, 功率单位为瓦特; 空气密度单位为千克 / 立方米;
面积指气流横截面积,单位为平方米; 速度单位为米 / 秒。 在海平面高度和摄氏 15 度的条件下,乾空 气密度为 1.225 千克 / 立方米。空气密度随气压 和温度而变。随著高度的升高,空气密度也会 下降。 於上述公式中可以看出,风的功率与速度 的三次方〔立方〕成正比,并与风轮扫掠面积 成正比。不过实际上,风轮只能提取风的能量 中的一部分,而非全部。 2) 风力发电机的工作原理 现代风力发电机采用空气动力学原理,就 像飞机的机翼一样。风并非 " 推 " 动风轮叶片,而是吹过叶片形成叶片正反面的压差,这种 压差会产生升力,令风轮旋转并不断横切风流。 风力发电机的风轮并不能提取风的所有功 率。根据 Betz 定律,理论上风电机能够提取的 最大功率,是风的功率的 59.6% 。大多数风电机 只能提取风的功率的 40% 或者更少。 风力发电机主要包含三部分∶风轮、机舱 和塔杆。大型与电网接驳的风力发电机的最常
浅谈风电叶片的特点及制造工艺
浅谈风电叶片的特点及制造工艺 摘要:对于风力发电机组来说,复合型风电叶片是不可缺少的组成设备,也是现今风力发电厂不可缺少的设备,所以本文就风电叶片的特点和制造工艺进行了分析。 关键词:复合型风电叶片特点制造工艺 由于现今不可再生能源的匮乏,因此全世界各国能源科研者都在不断的研发新形势的能源,而早已被开发和使用的风能便成为现今主要利用发电的能源,由于它有着无污染、绿色环保、取之不尽用之不完的功效,所以到目前为止仍然倍受人们的关注,因此风力发电便成为了国内外最为看好的发电能源。 1、复合材料风电叶片的制造工艺 由于在风力发电机组起着关键作用的是风力发电机的叶片,由于在叶片中使用了新型的复合材料对叶片进行加工,因此制造叶片的工艺就有非常的高的难度,再者因为叶片是风力发电机组的主要设备,因此对其进行的设计、加工的材料、制造的工艺也是决定风力发电机组是否能够正常的工作并且是否能够保证工作的效率。 从风力发电机开始的研制和使用延续到现今,对于叶片制造使用的材料也在随着时代的变化、科技的进步和风力发电机组工作效率的提高,因此风力发电机组的叶片也在不段进行这更新换代由最开始的木质到现今的复合型材料。 现今社会科学技术的发展的速度已经达到了让人叹为观止的地步,网络化、联网的形式已经出现在各大企业中,电力事业同样步入了联网型风力发电的时代,由此,风力发电事业迈入了一个全新的高峰期,因此对于风力发电机组的关键设备的叶片制造使用的材料也必须跟上现代化、高效率化的发电事业中,由此叶片制造使用的材料就一定要保证叶片在大负荷、高效率的运转状态下依然能正常的进行工作,发挥其重要的特性。在此情况下,现今的很多叶片的制造的厂家都使用复合型的材料作为主要的材料对叶片进行加工制造,这使得风电叶片进入了一个全新的领域中。 1.1 复合型材料作用于叶片中的优点 首先,复合型材料在具有高强度和刚度的情况下,还兼备着轻质量的特点。 而后,复合型材料制成的叶片具有高强度的抗疲劳性、优良的抗震性,同时其所承受的内阻大、敏感性低。由于其具备这些特点,因此它可以在正常的工作环境下延长叶片的使用寿命。 第三,由于现今很多大型的风力发电机都设置在海上,因此对于叶片承受的抗酸、抗水、等等的腐蚀性来说就要具有高强度的抗性,这正符合复合型材料的特点。 最后,复合型叶片比较人性化的方面就是其维护和清理的过程非常的方便和简单,通常情况下,只需要在叶片上间隔一定的时间段涂抹上涂料即可。 1.2 复合叶片的形成工艺 目前,对于复合型叶片的制造过程中,首先是要在制造的,模子上形成叶片蒙皮、主梁等一系列的零件,而后在经胶组装在一起,最后合模固化形成风电机组所使用的叶片。加工制造的整个过程如下: (1)手糊;(2)真空导入树脂模塑(VIP);(3)树脂传递模塑(RTM);(4)西门子树脂浸渍工艺(SCRIMP);(5)纤维缠绕工艺(FW);(6)木纤维环氧饱和工艺(WEST);
风电叶片
对风电叶片服役之后表面状态的调查以及对原厂涂装的反思 朱平 3M中国有限公司, 北京,100176 摘要:截止2011年底,我国累计安装风电机组45894台。“十二五”期间,我国规划风电新增装机70000 MW以上,以单机功率1.5MW估算,装机量不低于4.6万台。五年之后我国风机总量将会达到10万台左右,运转的叶片数目将达到30万支左右。如何确保这些风机安全经济运行是我国风电行业面临的巨大挑战。风叶是风机的吸能部件,风叶的健康高效运转是风机安全经济运行的前提,而风叶服役之后问题最先会出现在表面涂层。本文介绍了风电叶片在我国典型风场服役之后,表面涂层出现的若干问题,并由此反思叶片在制造阶段的涂料选择以及涂装工艺。最后提出若干建议,在叶片制造阶段选用合适的高性能涂料以并提高涂装工作质量,从源头做起为叶片的安全经济运行夯实基础。 关键词:风电叶片;服役之后;表面状态;涂装 Field investigation into surface conditions of wind blades in several typical wind farms and reconsideration about the coating specification In China, the total installation of wind turbine generator (WTG) reached 45894 sets with the whole capacity of 62364.2 Mw till the end of 2011. The schemed installation would be no less than 70000 MW according to China’s 12th five year plan. Given the capacity of 1.5 MW for each new WTG, the number would be more than 46000 sets. That means the total WTG installation will exceed 100 thousand after 5 years. There will be 300 thousand plus wind blades operating across China and offering clean energy to China society. It is a big challenge to maintain those WTGs operating smoothly and economically. Wind blades absorb energy for the WTG, its effective and efficient running is the prerequisite for the economy and safety of WTG. Deterioration always occurs on the blade surface first. This paper introduces certain problems about the surface of wind blades in several typical wind farms. Those problems enable us to rethink and reconsider about the wind blade coating products and coating specification during the blade OEM stage. We should select suitable high-quality coating products and optimize coating process, so as to build a solid basic for the safe and economical operation of wind blades. The wind farm owner, wind equipment