烧结余热利用现状和趋势
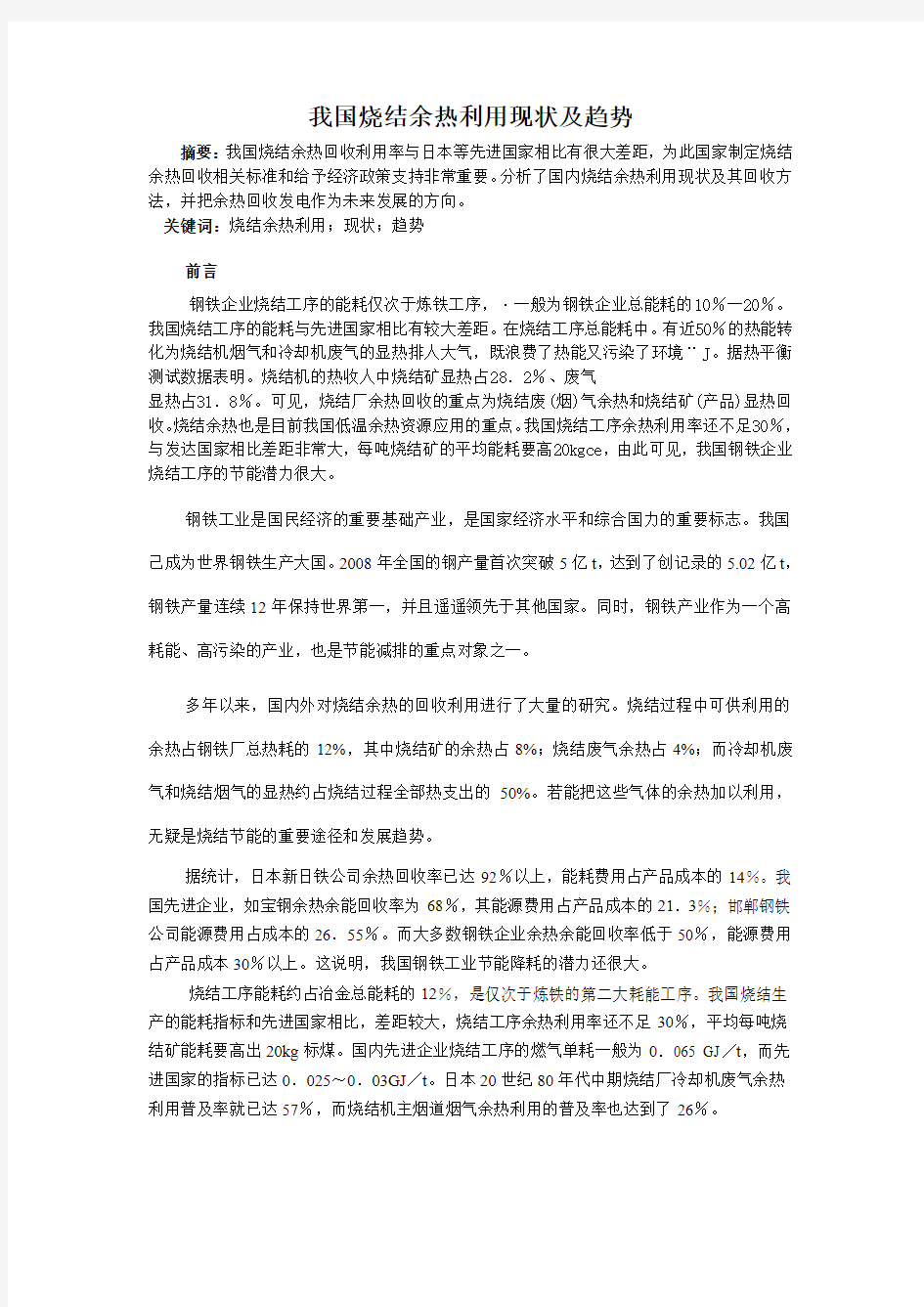
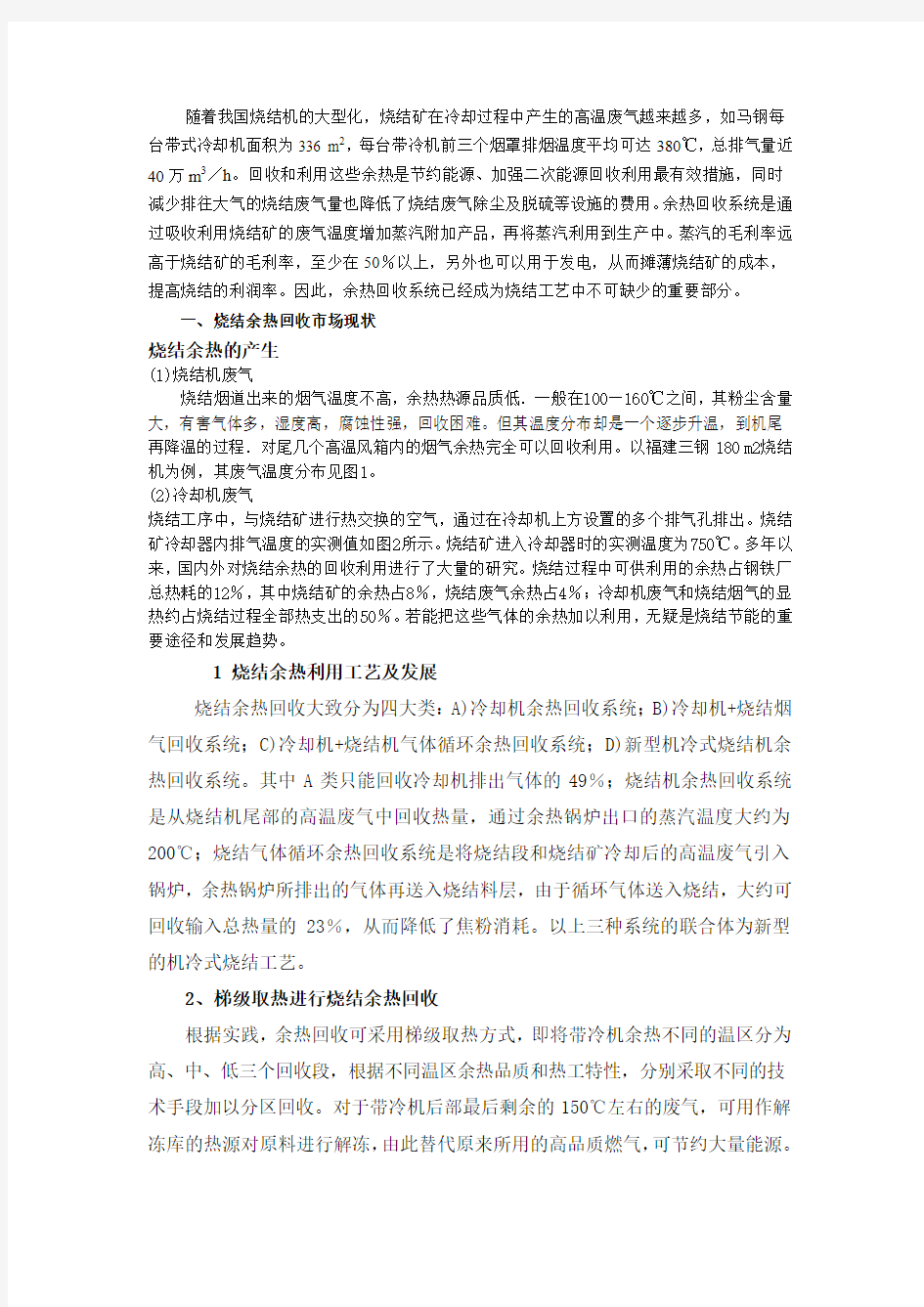
我国烧结余热利用现状及趋势
摘要:我国烧结余热回收利用率与日本等先进国家相比有很大差距,为此国家制定烧结余热回收相关标准和给予经济政策支持非常重要。分析了国内烧结余热利用现状及其回收方法,并把余热回收发电作为未来发展的方向。
关键词:烧结余热利用;现状;趋势
前言
钢铁企业烧结工序的能耗仅次于炼铁工序,·一般为钢铁企业总能耗的10%一20%。我国烧结工序的能耗与先进国家相比有较大差距。在烧结工序总能耗中。有近50%的热能转化为烧结机烟气和冷却机废气的显热排人大气,既浪费了热能又污染了环境¨J。据热平衡测试数据表明。烧结机的热收人中烧结矿显热占28.2%、废气
显热占31.8%。可见,烧结厂余热回收的重点为烧结废(烟)气余热和烧结矿(产品)显热回收。烧结余热也是目前我国低温余热资源应用的重点。我国烧结工序余热利用率还不足30%,与发达国家相比差距非常大,每吨烧结矿的平均能耗要高20kgce,由此可见,我国钢铁企业烧结工序的节能潜力很大。
钢铁工业是国民经济的重要基础产业,是国家经济水平和综合国力的重要标志。我国己成为世界钢铁生产大国。2008年全国的钢产量首次突破5亿t,达到了创记录的5.02亿t,钢铁产量连续12年保持世界第一,并且遥遥领先于其他国家。同时,钢铁产业作为一个高耗能、高污染的产业,也是节能减排的重点对象之一。
多年以来,国内外对烧结余热的回收利用进行了大量的研究。烧结过程中可供利用的余热占钢铁厂总热耗的12%,其中烧结矿的余热占8%;烧结废气余热占4%;而冷却机废气和烧结烟气的显热约占烧结过程全部热支出的50%。若能把这些气体的余热加以利用,无疑是烧结节能的重要途径和发展趋势。
据统计,日本新日铁公司余热回收率已达92%以上,能耗费用占产品成本的14%。我国先进企业,如宝钢余热余能回收率为68%,其能源费用占产品成本的21.3%;邯郸钢铁公司能源费用占成本的26.55%。而大多数钢铁企业余热余能回收率低于50%,能源费用占产品成本30%以上。这说明,我国钢铁工业节能降耗的潜力还很大。
烧结工序能耗约占冶金总能耗的12%,是仅次于炼铁的第二大耗能工序。我国烧结生产的能耗指标和先进国家相比,差距较大,烧结工序余热利用率还不足30%,平均每吨烧结矿能耗要高出20kg标煤。国内先进企业烧结工序的燃气单耗一般为0.065 GJ/t,而先进国家的指标已达0.025~0.03GJ/t。日本20世纪80年代中期烧结厂冷却机废气余热利用普及率就已达57%,而烧结机主烟道烟气余热利用的普及率也达到了26%。
随着我国烧结机的大型化,烧结矿在冷却过程中产生的高温废气越来越多,如马钢每台带式冷却机面积为336 m2,每台带冷机前三个烟罩排烟温度平均可达380℃,总排气量近40万m3/h。回收和利用这些余热是节约能源、加强二次能源回收利用最有效措施,同时减少排往大气的烧结废气量也降低了烧结废气除尘及脱硫等设施的费用。余热回收系统是通过吸收利用烧结矿的废气温度增加蒸汽附加产品,再将蒸汽利用到生产中。蒸汽的毛利率远高于烧结矿的毛利率,至少在50%以上,另外也可以用于发电,从而摊薄烧结矿的成本,提高烧结的利润率。因此,余热回收系统已经成为烧结工艺中不可缺少的重要部分。
一、烧结余热回收市场现状
烧结余热的产生
(1)烧结机废气
烧结烟道出来的烟气温度不高,余热热源品质低.一般在100—160℃之间,其粉尘含量大,有害气体多,湿度高,腐蚀性强,回收困难。但其温度分布却是一个逐步升温,到机尾再降温的过程.对尾几个高温风箱内的烟气余热完全可以回收利用。以福建三钢180 m2烧结机为例,其废气温度分布见图l。
(2)冷却机废气
烧结工序中,与烧结矿进行热交换的空气,通过在冷却机上方设置的多个排气孔排出。烧结矿冷却器内排气温度的实测值如图2所示。烧结矿进入冷却器时的实测温度为750℃。多年以来,国内外对烧结余热的回收利用进行了大量的研究。烧结过程中可供利用的余热占钢铁厂总热耗的12%,其中烧结矿的余热占8%,烧结废气余热占4%;冷却机废气和烧结烟气的显热约占烧结过程全部热支出的50%。若能把这些气体的余热加以利用,无疑是烧结节能的重要途径和发展趋势。
1 烧结余热利用工艺及发展
烧结余热回收大致分为四大类:A)冷却机余热回收系统;B)冷却机+烧结烟气回收系统;C)冷却机+烧结机气体循环余热回收系统;D)新型机冷式烧结机余热回收系统。其中A类只能回收冷却机排出气体的49%;烧结机余热回收系统是从烧结机尾部的高温废气中回收热量,通过余热锅炉出口的蒸汽温度大约为200℃;烧结气体循环余热回收系统是将烧结段和烧结矿冷却后的高温废气引入锅炉,余热锅炉所排出的气体再送入烧结料层,由于循环气体送入烧结,大约可回收输入总热量的23%,从而降低了焦粉消耗。以上三种系统的联合体为新型的机冷式烧结工艺。
2、梯级取热进行烧结余热回收
根据实践,余热回收可采用梯级取热方式,即将带冷机余热不同的温区分为高、中、低三个回收段,根据不同温区余热品质和热工特性,分别采取不同的技术手段加以分区回收。对于带冷机后部最后剩余的150℃左右的废气,可用作解冻库的热源对原料进行解冻,由此替代原来所用的高品质燃气,可节约大量能源。
采用梯级取热方法能将70%以上的余热废气量和近80%的可用余能加以有效地回收利用,可大量节约能源消耗,提高产品质量和降低生产成本。
3、热管式余热回收技术
热管作为一种高效的传热元件与传统换热器相比,有传热效率高、阻力损失小、结构简单等优点。烧结生产中余热属中、低品位余热,利用热管式余热回收装置可以使回收效率大大提高,它是中温(300℃左右)气-气热交换最理想的换热装置。例如,在环冷烧结机上热管换热器大多用于回收300℃左右的中温余热;在机冷烧结机上因烟气流量较大,温度低,含尘高,使余热回收利用困难。首钢采用气-汽热管换热器回收机冷烧结机上烟气余热用以产生蒸汽,供给二次混料机预热烧结混合料,(要求过热蒸汽温度达到180℃左右)实现了烧结系统生产用汽自给有余。
4、烧结余热发电
我国与先进国家相比,利用烧结低温余热发电技术起步较晚,但是发展速度很快。成功的有马钢2台300 m2带式烧结机低温余热利用发电、唐钢低温余热蒸汽发电项目、武钢435 m2烧结环冷机低温烟气余热发电项目、济钢320 m2烧结机余热发电、安钢360 m2和400 m2烧结机和承钢360 m2烧结机余热利用技术改造等。通过余热回收系统,在得到蒸汽的同时,还可以获得电能,一举两得。最重要的是电能要比蒸汽创造的价值更大,对降低烧结矿成本的贡献率更高。甚至可能成为主导产品,利润高于烧结矿本身。其次电能比蒸汽的利用率更高,商品化的程度更强。电能可以储存,蒸汽却无法实现。
纯低温余热发电技术以充分利用工业余热,近几年得到了迅速发展。统计数据表明,一个年产钢铁500万t的企业仅烧结及饱和蒸汽两项余热发电,即可全年发电约2.8亿度,可为企业增收1亿多元。
二、烧结余热回收市场前景
根据目前烧结余热回收的现状,我国烧结余热发电与梯级取热进行烧结余热回收装置将有良好的发展前景。截止2011年年底,我国现有烧结机约1200余台,其中在建和投产的180~660m2烧结机有120余台,其烧结面积达38590m2。目前已经建成和在建烧结余热发电项目共涉及33个钢铁企业77台烧结机(包括《钢铁企业烧结余热发电技术推广实施方案》中计划2012年以前建成的均视为在建
项目),占烧结机总量的61.6%(只计算大于180m2的烧结机在建项目的占量),而且以后配套建设的大型烧结机(180m2以上烧结机)大部分将会同步配套余热发电装置,每年约20台180m2新建的烧结机项目。根据这一现状推算(加上《钢铁企业烧结余热发电技术推广实施方案》中计划2012年的项目),未来三年后续还将建设的烧结余热(部分综合利用转炉余热及煤气)发电装置至少会达到55套(按每两座大于180m2烧结机配一套发电装置计算,平均每年约18套),涉及108套烧结机;另外,考虑到后两年新建大型烧结机同步配套余热发电项目约35套,“十二五”期间烧结和转炉余热发电年均需求约30套,呈现增长态势。
三总结
虽然我国是世界最大的钢铁大国,但与钢铁强国相比还存在不小的差距。从余热利用角度讲,随着技术的进步可回收的余热资源还很多。技术人员要跨过眼前的一道道技术难关,使烧结余热发电技术更加成熟、可靠、高效,烧结余热发电技术在深人节能中将起到更加重要作用。
参考文献
1)李宝东(1974一).高工;1140“辽宁省鞍山市。
2)李桂田.钢铁工业余热资源及几项指标[J].冶金能源,1997,16(1):3—9,
3)胡深亚,潘卫国,姜未汀等.烧结工艺余热利用多技术方案的比较研究[J].节能技术和产品,
4)闰为群,栾颖.烧结余热回收利用途径探讨[J】.河南冶金,2007,15(3);23—24.
5)范从振.锅炉原理[M].北京:中国电力出版社。
6)匡吾.我国烧结能耗现状和节能对策[J].烧结球团,1997(5):1I—12.
7)杜华云译.烧结生产二次能源利用的研究及研究成果
8)卢红军.戚云峰.烧结余热的基本特点及对烧结余热发电的影响[J].烧结球团,2008(1):35—38.
9)杨兴聪.李建军,郭奠球.国外烧结余热回收利用现状[J].烧结球团,1996(5):39—40.
10)唐先觉.我国第一鹰现代化烧结余热回收装置建成[J].烧结球团,1992(2):10—12.
11)谢泽民.宝钢l、3号烧结机设置余热回收装置[J].钢铁,
东海特钢烧结余热发电施工组织设计
唐山东海钢铁集团特钢有限公司 23198㎡烧结余热发电项目 施 工 组 织 设 计 编制单位:河南大成建设工程有限公司编制时间: 2014 年 06月 04日
第一章编制依据及工程概况 1.1 编制依据 1.1.1 唐山东海钢铁集团特钢有限公司1313.5MW烧结余热回收发电项目招标 文件; 1.1.2 唐山东海钢铁集团特钢有限公司施工现场实际状况及施工环境; 1.1.3 唐山东海钢铁集团特钢有限公司烧结生产工艺及状况; 1.1.3 国家电力公司国电电源[2002]849号《火力发电工程施工组织设计导则》; 1.1.4 国家现行的有关规程、规范; 1.1.5 河南大成建设有限公司多年的施工经验。 1.2 现场条件 1.2.1 概述 本项目为唐山东海钢铁集团特钢有限公司烧结余热发电工程,采用两段取风,闭路循环系统。5#及6#环冷机每台配设一台余热锅炉,一台热管锅炉,共用一台13.5MW补汽凝汽式汽轮机及一台15MW无刷励磁发电机。 1.2.2 地理位置 拟建厂址位于唐山市滦县茨榆坨工业园区内,距唐山市约31公里。拟建电站位于东海特钢烧结厂区内。唐山市滦县茨榆坨镇工业区,东临迁唐路,交通便利。 1.2.3 厂址自然条件 1.2.3.1地形地貌 本厂区属平原地貌,地势略有起伏,自然地面总体呈现为西高东低的趋势,最大高差约0.5米。项目场地标准冻深小于0.9m,故不考虑冻胀影响。 1.2.3.2气候特征 年平均气温 11℃ 极端最高气温 39.9℃
极端最低气温 -21 ℃ 海拔高度 25.9米 冻土深度: 0.9m 夏季室外计算干球温度: 32.7℃ 夏季室外计算湿球温度: 26.2℃ 最热月月平均相对湿度: 79% 1.2.3.3地质条件 拟建场地土属中硬场地土,建筑场地类别为Ⅱ类,位于相对稳定地块,不存在新构造活动运动,无不良地质作用,适宜作为建筑场地。 1.2.4电厂水源 该工程锅炉补充水、生活用水和其他用水采用厂区原有的水源,接入点由建设单位就近指定。 1.2.5 施工用电 从6#烧结厂西侧配电室引一条施工电源到主厂房西北角,能够满足施工区域电力供应。 施工用电应注意以下事项: 1.2.5.1实行TN-S配电系统,三级控制两级保护的配电方式,其中第一级保护的漏电保护器漏电动作电流根据用电设备数量确定,但漏电动作时间要小于 0.1s。 1.2.5.2变压器中性点直接接地的供电系统,一切用电设备、工具照明都实行保护接零;保护零线单独敷设,不通过任何开关和熔断器,在分支、终点、设备集中点或每长50m处都要重复接地,接地电阻小于10欧姆;保护零线的干线截面不小于相线的1/2,相线截面小于16平方时,保护零线与相线截面相同;移动式用电工具和设备和设备的保护零线用铜芯软线,其截面不小于相线的1/3,任何情况下小于 1.5mm2;用电设备的保护零线不得串联,用电设备的保护零线与保护零干线采用焊接、螺栓联结等,严禁缠绕和钩挂。 1.2.5.3一切用电设备在一般场所的第二级保护用漏电动作电流小于30mA,动作时间小于0.1s的漏电保护器,手持电动工具选择漏电动作电流小于15MA、动作
工业余热利用现状
工业余热利用现状集团档案编码:[YTTR-YTPT28-YTNTL98-UYTYNN08]
我国工业余热利用现状 摘要:工业发展带来了巨大的污染,工业余热的利用是节能减排的重要环节。本文主要介绍了工业余热的资源特点,概述了工业余热的利用方式,中国目前低温工业余热技术,以及分析了工业余热利用中存在的问题。总结出目前应该大力发展利用低温余热技术。 关键词:工业余热;低温余热利用技术;节能减排 0引言 工业部门余热资源总量极为丰富,“十二五”期间可以开发利用的潜力超过1亿吨标准煤。“十二五”是我国节能减排承前启后的关键时期,国务院和有关部委已就节能减排工作作出全面的决策部署,明确提出单位GDP能耗降低16%左右、单位GDP二氧化碳排放降低17%左右、规模以上工业增加值能耗降低21%左右等多项节能减排目标。工业部门能源消费约占全国能源消费的70%。 目前余热利用最多的国家是美国,它的利用率达到60%,欧洲的达到50%,我国30%。就余热利用来看,我国还有很大的利用空间。中、高温余热发电已经形成了比较完备的产业,而低温余热发电则刚刚开始。 1.工业余热资源特点 工业消耗的能源部门品种包括原煤、洗煤、焦炭、油品、天然气、热力、电力等。工业余热资源特点主要有:多形态、分散性、行业分布不均、资源品质较大差异等特点。 对钢铁、水泥、玻璃、合成氨、烧碱、电石、硫酸行业余热资源的调查分析结果显示,上述工业行业余热资源量丰富,约占这7个工业行业能源消费总量的1/3。“十二五”时期,综合考虑行业现状与发展趋势,这7个工业行业余热资源总量高达亿吨标准煤。 2010年末,余热资源开发利用总量折合为8791万吨标准煤。其中,余热资源开发利用量超过1000万吨标准煤的有钢铁、合成氨、硫酸、水泥4个行业,分别为3560万吨标准煤、2450万吨标准煤、1244万吨标准煤、1124万吨标准煤。 从余热资源的行业分布来看,上述7个工业行业中,钢铁、水泥、合成氨行业的余热资源量位居前三,分别为亿吨标准煤、9300万吨标准煤、3454万吨标准煤,占这7个工业行业余热资源总量的比重分别为%、%、%;硫酸、电石、烧碱、玻璃余热资源总量则较少,分别为1940万吨标准煤、1408万吨标准煤、495万吨标准煤、311万吨标准煤,合计占7个工业行业余热资源总量的122%。 从工业余热资源的地区分布来看,“十二五”时期,上述7个工业行业余热资源可开发利用潜力居前六位的地区是河北、江苏、山东、辽宁、山西、河
烧结余热回收
烧结余热回收 ■我国烧结工序能耗约占企业总能耗15%,仅次于炼铁工序,比国外先进指标高出20%以上。主要原因之一是余热资源回收与利用水平低。 ■烧结余热回收做得好的国家是日本,住友和歌山钢厂的4号烧结机生产每吨烧结矿可回收蒸汽量110~120 kg,其中低压蒸气为175℃(0.78MPa),中压蒸汽375℃(2.55MPa),吨矿回收电力20kWh,工序能耗40kgce/t。 ■我国马钢引进日本川崎余热发电技术,2台328m2 烧结机余热发电,2005年9月投产,装机容量17.5MW,吨矿发电10kWh,年发电0.7亿kWh,经济效益4000万元以上,年节约3万tce;济钢1台320m2烧结机国产化余热发电系统,2007年1月投产,装机容量10MW,吨矿发电17kWh,年发电0.7亿kWh。 废气温度低,且变化频繁 废气流量大,漏风率高 梯级回收,区分余热质量 煤调湿 “煤调湿”(CMC)是“装炉煤水分控制工艺”(coal moisture control process)的简称,是将炼焦煤料在装炉前去除一部分水分,保持装炉煤水分稳定在6%左右,然后装炉炼焦的一种煤预处理工艺。煤调湿有严格的水分控制措施,能确保入炉煤水分恒定。煤调湿以其显著的节能、环保和经济效益受到普遍重视。美国、前苏联、德国、法国、日本和英国等都进行过不同形式的煤调湿试验和生产,尤其是日本发展最为迅速。截至2009年底,日本现有的16个焦化厂51组(座)焦炉中,其中有36组(座)焦炉配置了煤调湿装置,占焦炉总数的70.5%。 煤调湿技术的效果是: 1)降低炼焦耗热量、节约能源。采用煤调湿技术后,煤料含水量每降低1%,炼焦耗热量相应降低62.0MJ/t(干煤)。当煤料水分从11%下降至6%时,炼焦耗热量相当于节省了62.0×(11-6)=310MJ/t(干煤)=10.6kgce/ t(干煤)。 2)提高焦炉生产能力。由于装炉煤水分的降低,使装炉煤堆密度增加,干馏时间缩短,因此,焦炉生产能力可提高4%~11%。 3)改善焦炭质量。焦炭的冷态强度DI 可提高1%~1.5%,反应后强度CSR提高1%~3%。4)扩大炼焦用煤资源。在保证焦炭质量不变的情况下,可多配弱黏结煤8%~10%。 5)减少氨水处理量。装炉煤水分若降低约5%,则可减少1/3的剩余氨水量,相应减少1/3的蒸氨用蒸汽量,同时也减轻了废水处理装置的生产负荷。 6)延长焦炉炉体寿命。因煤料水分稳定在6%水平上,使得煤料的堆密度和干馏速度稳定,焦炉操作趋于稳定,从而起到保护炉体、延长焦炉寿命的作用。 7)节能的社会效益。减少温室效应,平均每t入炉煤可减少约35.8kg的CO2排放量。 我国焦化厂炼焦煤含水量普遍偏高,年平均含水在11%左右。每万吨水进入焦炉,在焦炉中汽化要耗费大约3.9×1010kJ的热能,相当于约1300吨标准煤。如果采用煤调湿装置,不仅降低炼焦耗热量、减少温室气体排放,而且能提高焦炭产量和质量,并降低成本。由于装炉煤水分的降低,大大减少所需处理的酚氰废水量。 建议和发展方向 1)在用高炉煤气加热焦炉的钢铁企业焦化厂应大力推广以焦炉烟道废气为热源的煤调湿技术; 2)在用焦炉煤气加热焦炉的独立焦化厂应推广以低压蒸汽为热源的煤调湿技术。
烧结机废气余热利用
烧结机废气余热利用 冀留庆 林学良 (中钢集团工程设计研究院有限公司 北京100080) 摘 要 烧结机及烧结矿冷却机的废气温度在400℃以下,为了回收低温废气的余热,开发了纯低温余热锅炉。概述了锅炉及汽轮发电机组的设计和运行情况,并展望了应用前景。讨论的余热锅炉为发电用锅炉,用于回收烧结机和烧结矿冷却机排放的低温余热,机组安装于360m 2烧结机。 关键词 烧结机 烧结冷却机 余热锅炉 汽轮发电机组 W aste G as R ecovery of Sintering Machine J I Liu -qing LIN Xue -liang (Sinosteel Engineering Design &Research Institute Co.,Ltd. Beijing 100080) Abstract The tem perature of waste gas of sintering machine and sintering cooling machine is below 400℃.S ingle low -tem perature waste heat boiler is designed to recover the heat of low -tem perature waste gas.This paper describes the design and running situation of the boiler and turbogenerator set and prospects its application.The boiler mentioned is a power generation boiler.It is used to recover low -tem perature waste heat em itted by sintering machine and sintering cooling machine and installed in a 360m 2sintering machine.K eyw ords sintering machine sintering cooling machine waste heat boiler turbogenerator set 0 前言在钢铁生产过程中,烧结工序的能耗约占总能耗的 10%,仅次于炼铁工序。在烧结工序总能耗中,有近50%的 热能以烧结机烟气和冷却机废气的显热形式排入大气,既浪费了热能又污染了环境。烧结废气不仅数量大,而且可供回收的热量也大,但由于废气温度均低于400℃,所以如何回收其中的低温余热,进一步降低烧结生产能耗是我国烧结矿生产企业面临的节能技术课题。 在日本低温余热回收已应用得相当广泛,这种技术是利用烧结环冷机余热锅炉来产生低压过热蒸汽供汽轮机组发电。2005年9月,由日本川崎重工提供的一套先进而成熟可靠的低温余热发电成套设备在马钢炼铁厂投产发电。该套设备配2台容量为37.4t/h 废气锅炉(每台300m 2烧结机配备1台废气锅炉),装机容量为17.5MW 凝汽式汽轮发电机组。设计年发电量为1.4×108 kW ?h 。经4年运行实绩证明,该系统安全可靠,能为烧结生产带来显著的经济效益和环境效益。该技术近几年已经在我国烧结行业开始普及推广。对于关键设备余热锅炉的制造难点是如何应对烟气的低品位和高灰分问题,经过国内技术人员共同努力已经解决。方法是采用低成本的扩展受热面,即采用螺旋鳍片管来提高换热效率,采用机械振打清灰技术解决高灰分问题。 1 工艺简介 烧结环冷机余热锅炉是抽出环冷机第1段(300-400 ℃ )和第2段(250-300℃)的冷却热废气,废气进入余热锅炉经热交换后,余热锅炉出口排烟温度降至165℃。为了充分回收利用热能,将余热锅炉排出的165℃废气通过循环风机再送回烧结环冷机鼓风口,从而实现余热锅炉到烧结机之 间的烟气再循环方式。 烧结机余热锅炉是抽出烧结机高温段烟气,该段排出的 300-330℃的烟气进入余热锅炉经热交换后余热锅炉出口 排烟温度降至165℃。通过循环风机再送回烧结机低温段经烧结除尘器和主风机排向大气。产生的蒸汽与烧结环冷机余热锅炉产生的蒸汽混合进入汽轮发电机做功发电。 对于烧结余热利用可采用烧结环冷机余热锅炉和烧结机余热锅炉形式,也可以将环冷机高温段废气和烧结机高温段烟气混合后进入一个共同的余热锅炉进行热交换,但是带来的问题是余热锅炉出口排烟分配平衡调整不易。所以笔者认为2个余热锅炉较适宜。 2 锅炉规范及结构简述 对于360m 2烧结机配套的锅炉规范如下: 环冷机锅炉设计参数:型号QC720/350-45-1.25/300;第1段:废气流量360000m 3/h ,进口温度300-400℃,第2段:废气流量360000m 3/h ,进口温度250-300℃,出口温度 165-180℃,废气含尘量1g/m 3,漏风率≤2%,锅炉总废气 阻力≤500Pa ,蒸汽出口压力1.25MPa ,蒸汽出口温度300℃,蒸发量45t/h 。 烧结机锅炉设计参数:型号QC350/300-25-1.25/250;废气流量350000m 3/h ;进口温度300-330℃;出口温度165 -180℃;废气含尘量2g/m 3;漏风率≤2%;锅炉总废气阻力 ≤500Pa ;蒸汽出口压力1.25MPa ;蒸汽出口温度250℃;蒸发量25t/h 。 锅炉的总体方案是经充分调研并进行多方案比较而确定的。余热锅炉采用自然循环的立式结构,立式结构布置节约了占地面积,也方便了废气管道的布置;自然循环省掉 ? 61? 工业安全与环保 Industrial Safety and Environmental Protection 2009年第35卷第12期 December 2009
我国工业余热利用现状分析
我国工业余热利用现状分析 工业发展带来了巨大的污染,工业余热的利用是节能减排的重要环节。本文主要介绍了工业余热的资源特点,概述了工业余热的利用方式,中国目前低温工业余热技术,以及分析了工业余热利用中存在的问题。总结出目前应该大力发展利用低温余热技术。 1.工业余热资源特点 工业消耗的能源部门品种包括原煤、洗煤、焦炭、油品、天然气、热力、电力等。工业余热资源特点主要有:多形态、分散性、行业分布不均、资源品质较大差异等特点。 对钢铁、水泥、玻璃、合成氨、烧碱、电石、硫酸行业余热资源的调查分析结果显示,上述工业行业余热资源量丰富,约占这7个工业行业能源消费总量的1/3。综合考虑行业现状与发展趋势,这7个工业行业余热资源总量高达3.4亿吨标准煤。 余热资源开发利用量超过1000万吨标准煤的有钢铁、合成氨、硫酸、水泥4个行业,分别为3560万吨标准煤、2450万吨标准煤、1244万吨标准煤、1124万吨标准煤。 从余热资源的行业分布来看,上述7个工业行业中,钢铁、水泥、合成氨行业的余热资源量位居前三,分别为1.71亿吨标准煤、9300万吨标准煤、3454 万吨标准煤,占这7个工业行业余热资源总量的比重分别为50.3%、27.3%、10.2%;硫酸、电石、烧碱、玻璃余热资源总量则较少,分别为1940万吨标准煤、1408万吨标准煤、495万吨标准煤、311万吨标准煤,合计占7个工业行业余热资源总量的122%。 从工业余热资源的地区分布来看,上述7个工业行业余热资源可开发利用潜力居前六位的地区是河北、江苏、山东、辽宁、山西、河南,分别为1507万吨标准煤、680万吨标准煤、664万吨标准煤、530万吨标准煤、419万吨标准煤、361万吨标准煤。 从余热资源的来源来看,可分为高温烟气和冷却介质等六类,其中高温烟气余热和冷却介质余热占比最高,分别占50%和20%,而其他来源分别是废水、废
工业余热的现状与利用
工业余热现状与利用 姚** 北京科技大学机械学院,100083 摘要:工业余热指工业生产中各种热能装置所排出的气体、液体和固体物质所载有的热量。余热属于二次能源,是燃料燃烧过程所发出的热量在完成某一工艺过程后所剩余的热量。我国能源利用率相比发达国家较低,至少50%的工业耗能以各种形式的余热被直接废弃。工业余热节能潜力巨大,近年来已经成为我国节能减排工作的重要组成部分。 关键字:工业余热节能减排热管 0引言 当前,我国能源利用仍然存在着利用效率低、经济效益差,生态环境压力大的主要问题。节能减排、降低能耗、提高能源综合利用率作为能源发展战略规划的重要内容,是解决我国能源问题的根本途径,处于优先发展的地位。 实现节能减排、提高能源利用率的目标主要依靠工业领域。处在工业化中后期阶段的中国,工业是主要的耗能领域,也是污染物的主要排放源。我国工业领域能源消耗量约占全国能源消耗总量的70%,主要工业产品单位能耗平均比国际先进水平高出30%左右。除了生产工艺相对落后、产业结构不合理的因素外,工业余热利用率低,能源没有得到充分综合利用是造成能耗高的重要原因。 我国能源利用率仅为33%左右,比发达国家低约10%。至少50%的工业耗能以各种形式的余热被直接废弃。因此从另一角度看,我国工业余热资源丰富,广泛存在于工业各行业生产过程中,余热资源约占其燃料消耗总量的17%~67%,其中可回收率达60%,余热利用率提升空间大,节能潜力巨大。工业余热回收利用又被认为是一种“新能源”,近年来成为推进我国节能减排工作的重要内容。[1] 1工业余热资源 工业余热来源于各种工业炉窑热能动力装置、热能利用设备、余热利用装置和各种有反应热产生的化工过程等。目前,各行业的余热总资源约占其燃料消耗总量的17%~67%,可回收利用的余热资源约为余热总资源的60%。合理充分利用工业余热可以降低单位产品能耗,取得可观的经济效益。 工业余热按其能量形态可以分为三大类,即可燃性余热、载热性余热和有压性余热。 1)可燃性余热 可燃性余热是指能用工艺装置排放出来的、具有化学热值和物理显热,还可作燃料利用的可燃物,即排放的可燃废气、废液、废料等,如放散的高炉气、焦炉气、转炉气、油田伴生气、炼油气、矿井瓦斯、炭黑尾气、纸浆黑液、甘蔗渣、木屑、可燃垃圾等。 2)载热性余热 常见的大多数余热是载热性余热,它包括排出的废气和产品、物料、废物、工质等所带走的高温热以及化学反应热等,如锅炉与窑炉的烟道气,燃气轮机、内燃机等动力机械的排气,焦炭、钢铁铸件、水泥、炉渣的高温显热,凝结水、冷却水、放散热风等带走的显热,以及排放的废气潜热等。 3)有压性余热 有压性余热通常又叫余压(能),它是指排气排水等有压液体的能量。另外,因为工业余热的温度是衡量其质量(品位)的重要标尺,而其温度的高低亦影响了余热回收利用的方式,所以余热也通常按温度高低分为:高温余热,T≥650℃;中温余热,230 ℃≤T<650℃;低温余热,T<230℃。 余热资源来源广泛、温度范围广、存在形式多样.从利用角度看,余热资源一般具有以下共同点:由于工艺生产过程中存在周期性、间断性或生产波动,导致余热量不稳定;余热介质性质恶劣,如烟气中含尘量大或含有腐蚀性物质;余热利用装置受场地等固有条件限制。 2工业余热利用现状 2.1工业余热利用总体现状 我国能源利用率仅为33%左右,比发达国家低
工业余热回收、工业余热利用
工业余热回收、余热利用 余热概念:所谓工业余热(又称废热)是指工业生产中各种热能装置所排出的气体、液体和固体物质所载有的热量。余热属于二次能源,是燃料燃烧过程所发出的热量在完成某一工艺过程后所剩余的热量。这种热量若不加以回收利用,立即排放到大气和江河中,不仅所谓工业余热(又称废热)是指工业生浪费能源,而且还会污染环境。
以钢铁工业为例: 钢铁工业是环境污染、能源消耗大户,烟气除尘、余热回收利用是钢铁工业保护环境、节约能源的对策之一。电炉在生产过程中产生大量含尘、CO的高温烟气,平均每吨钢产生的烟尘量为18-20kg,随烟气带走的热量约150M .严重浪费能源、污染环境。随着电炉技术迅速、全面的发展,其烟气余热回收利用及除尘技术也得到了发展。
热管是余热回收装置的主要热传导元件,与普通的热交换器有着本质的不同。热管余热回收装置的换热效率可达98%以上,这是普通热交换器无法比拟的。 热管余热回收装置体积小,只是普通热交换器的1/3。 其工作原理如右图所示:左边为烟气通道,右边为清洁空气(水或其它介质)通道,中间有隔板分开互不干扰。高温烟气由左边通道排放,排放时高温烟气冲刷热管,当烟气温度>30℃时,热管被激活便自动将热量传导至右边,这时热管左边吸热,高温烟气流经热管后温度下降,热量被热管吸收并传导至右边。常温清洁空气(水或其它介质)在鼓风机作用下,沿右边通道反方向流动冲刷热管,这时热管右边放热,将清洁空气(水或其它介质)加热,空气流经热管后温度升高。
?1、安全可靠性高 常规的换热设备一般都是间壁换热,冷热流体分别在器壁的两侧流过,如管壁或器壁有泄露,则将造成停产损失。热管余热回收器则是二次间壁换热,即热流要通过热管的蒸发段管壁和冷凝段管壁才能传到泠流体。 ?2、热管余热回收器传热效率高,节能效果显著。 ?3、热管余热回收器具有良好的防腐蚀能力 热管管壁的温度可以调节,可以通过适当的热流变换把热管管壁温度调整在低温流体的露点之上,从而可防止露点腐蚀,保证设备的长期运行。由于避开烟气露点,使灰尘不易粘结于肋片和管壁上。同时热管在导热时会产生自振动,使灰不易粘附在管壁和翅片上,因而不会堵灰。
烧结余热利用技术开发及应用
烧结余热利用技术开发及应用 发表时间:2019-01-03T16:15:42.580Z 来源:《基层建设》2018年第32期作者:宋进栋 [导读] 摘要:近年来,能源短缺和环境污染严重的问题受到社会各界的高度重视,节能、减排、降耗已成为一个全球性的焦点话题。 河钢集团唐钢能源科技分公司河北唐山 063000 摘要:近年来,能源短缺和环境污染严重的问题受到社会各界的高度重视,节能、减排、降耗已成为一个全球性的焦点话题。我国的钢铁工业是能耗大户,约占全国总能耗的15%,而烧结工序生产过程中能耗约占钢铁企业总能耗的10%~20%,比炼铁工序略低。在烧结生产过程中会产生大量的余热,由于受工艺和技术等因素的限制,目前余热利用率不足30%,浪费严重,与这方面做得比较好的发达国家相比,还有一定的差距,节能潜力很大。从节省能源、降低能耗、保护环境、提高企业经济效益和社会效益出发,尽可能多的回收和利用烧结余热。 关键词:烧结余热;利用;技术开发;应用 1 烧结余热的特点 烧结工序中有两种能量可以被回收再次使用,分别是烧结烟气所蕴藏的热能和烧结环冷废气所释放的热能。烧结烟气的最高温度约为150℃,它所蕴含的热量是总热能的24%,机尾烟气最高温度可达450℃(正常温度范围一般在260℃到450℃之间),在总热量中占了更大的比重,这些总热量具有以下几种特征: 1.1温度随生产波动大 烧结工序中,由于烧结矿在烧结机上的燃烧状况各有差异,烧结废气和冷却中释放的废气温度不一致;烧结矿燃烧不充分时,释放的废气温度过高,燃烧激烈时,冷却环节释放的废气温度较低,根据唐钢北区烧结的数据可知,剩余热量回收环节所产生的废气温度可达450℃,但最低温度却只有150℃。由于温度波动幅度较大,不利于烧结剩余热量的回收再利用,同时这也是烧结余热回收环节所要重点关注和解决的难题。 1.2热源的连续性难以保证 烧结余热能的主要来源途径是物理显热,在烟气回收时有持续跟进的烧结矿,烧结余热量才会持续不断的供给。由于影响因素较多,烧结设备偶尔会出现短暂的停歇,热源的持续供给也难以100%得到保障,特别是近年来北方京津冀地区受环保限产影响很大,烧结机启停频繁,热源的连续性更是受到更多程度的限制。 2 烧结余热回收利用 2.1烧结余热发电 烧结余热发电是指烧结工艺生产过程中,烧结机尾落矿风箱及烧结环冷机密闭段产生大量的高温废气,由余热回收设备收集后,用引风机引入锅炉并加热锅炉内的水产生饱和蒸汽,推动汽轮机转动,带动发电机发电的技术。从能源利用和经济学角度看,采用烧结余热发电,符合能级匹配的原则。目前国内烧结余热发电技术比较成熟的有4种形式,分为单压、双压、复合闪蒸和补燃余热发电技术。在相同的条件下,双压余热发电技术实现了烟气热能的梯级利用,其发电能力是最高的。其中,马鞍山钢铁股份有限公司是我国最先应用烧结余热发电的,2004年把从日本引进的烧结机余热发电装机进行了大量技术革新,2005年9月正式投产使用,填补了我国利用烧结余热发电的空白。此后,许多大型钢铁公司也相继开始利用烧结余热技术发电,唐钢北区烧结余热发电系统曾在2011年烧结不限产时创下吨矿发电量22度的佳绩。 2.2补燃余热发电 补燃余热发电技术是在烧结余热发电运行过程中,针对烧结余热发电技术存在的问题,提出烧结余热发电系统与高温空气燃烧技术相结合的发电技术,是在原有烧结余热发电技术的基础上,将回收烟气余热、高效燃烧和降低有害气体排放等技术有机结合。利用蓄热式燃烧器在蒸汽过热炉中燃烧来提高汽轮机进口蒸汽的压力和温度,通过补燃少量煤气来提高蒸汽品质,从而提高发电效率和减少对设备的损耗。这样即使在冬春季节也能使余热发电系统正常运行,在满足自用的基础上可并入电网。 2.2其他方面的应用 2.2.1余热锅炉 对于小型烧结机采取余热锅炉方法对高温段余热进行回收。回收的废烟气首先用于烧结工艺本身,以降低工序能耗,其次作为外部供应。烧结余热锅炉的排烟温度,应避开烧结烟气的酸露点,防止对设备腐蚀,保证设备长期稳定,这种余热利于方式普遍存在于北方很多小型钢铁企业中,但余热利用效率较低。 2.2.2热风点火和热风烧结 环冷机中段废气余热采用非换热方式直接利用,将300℃左右的废气直接回收用于热风助燃,不仅能提高100℃烧结点火温度,还能强化和稳定点火过程,改善点火质量。热风烧结的适宜温度是250℃左右,故该段余热可采用直接利用的方式加以回收,将高含氧量的热废气作为热风烧结和烧结点火助燃空气。具体工艺是将环冷机中温段的热废气抽出,经高温除尘和保温后,利用高温风机将其输送到点火炉,直接用于点火助燃,或者是将废气抽出,经保温后直接用于热风烧结。同时,由于助燃空气温度的提高,使烧嘴喷出的混合燃气速度更快,火焰穿透力更强,加快了垂直点火过程。热风点火和热风烧结两热工过程相互促进,提高了上层料面的保温蓄热能力,节能效果十分明显。 2.2.3混合料预热技术 烧结过程中,将混合料含水分调配成7%~8%,利用余热锅炉回收的蒸汽来提高烧结混合料温度至65℃以上,避免由于混合料温度过低,产生的水蒸汽容易冷凝为液态,造成烧结台车断面下层混合料水分不断增加,超过混合料含水标准,导致料层透气性下降,影响烧结过程。有资料显示,混合料每提升10℃,烧结机利用系数可提高约5%,燃料消耗减少2 kg/t。 3 国外烧结余热回收利用 世界先进发达国家在对烧结余热回收再利用方面已走在我国前面。上世纪70年代末,日本住友公司将烧结机冷却器用废热锅炉回收蒸汽,80年代,余热回收利用技术在日本各个烧结厂被广泛利用,其中以冷却机排气利用的利用率最高,达到26%左右。 3.1引入余热预热烧结点火助燃空气
余热回收技术
余热回收技术 1、热管余热回收器 热管余热回收器即是利用热管的高效传热特性及其环境适应性制造的换热装置,主要应用于工业节能领域,可广泛回收存在于气态、液态、固态介质中的废弃热源。按照热流体和冷流体的状态,热管余热回收器可分为:气—气式、气-汽式、气—液式、液—液式、液—气式。按照回收器的结构形式可分为:整体式、分离式和组合式。 2、间壁式换热器 换热器是化工,石油,动力,食品及其它许多工业部门的通用设备,在生产中占有重要地位.在化工生产中换热器可作为加热器、冷却器、冷凝器、蒸发器和再沸器等,应用更加广泛。换热器种类很多,但根据冷、热流体热量交换的原理和方式基本上可分三大类即:间壁式、混合式和蓄热式。在三类换热器中,间壁式换热器应用最多。常见间壁式换热器如:冷却塔(或称冷水塔) 、气体洗涤塔(或称洗涤塔) 、喷射式热交换器、混合式冷凝器。 3、蓄热式换热器 蓄热式换热器用于进行蓄热式换热的设备,一般用于对介质混合要求比较低的场合。换热器内装固体填充物,用以贮蓄热量。一般用耐火砖等砌成火格子(有时用金属波形带等)。
蓄热式换热分两个阶段进行。第一阶段,热气体通过火格子,将热量传给火格子而贮蓄起来。第二阶段,冷气体通过火格子,接受火格子所储蓄的热量而被加热。这两个阶段交替进行。通常用两个蓄热器交替使用,即当热气体进入一器时,冷气体进入另一器。常用于冶金工业,如炼钢平炉的蓄热室。也用于化学工业,如煤气炉中的空气预热器或燃烧室,人造石油厂中的蓄热式裂化炉。 4、节能陶瓷换热器 陶瓷换热器是一种新型的换热设备,在高温或腐蚀环境下取代了传统的金属换热设备。用它的特殊材质——SIC质,把窑炉原来用的冷空气变成了热空气来达到余热回收的目的。由于其可长期在浓硫酸、盐酸和碱性气、液体中长期使用。抗氧化,耐热震,高温强度高,抗氧化性能好,使用寿命长。热攻工业窑炉。把换取的热风作为助燃风送进窑炉与燃气形成混合气进行燃烧,可节能25%-45%,甚至更多的能源。 5、喷射式混合加热器 喷射式混合加热器是射流技术在传热领域的应用,喷射式混合加热器是通过汽、水两相流体的直接混合来生产热水的设备。喷射式混合加热器具有传换效率高,噪音低(可达到65dB以下),体积小,安装简单,运行可靠,投资少。利用喷射式混合加热器回收发电厂、造纸厂、化工厂的余热,加热采暖循环水
15MW烧结余热发电工程项目可行性研究报告
XXXXXX有限公司 15MW烧结余热发电工程项目 可行性研究报告 编制单位:北京中投信德国际信息咨询有限公司 高级工程师:高建
XXXXXX有限公司 15MW烧结余热发电工程项目 可行性研究报告 报告目录 第一章总论 (1) 第一节项目名称及建设单位 (1) 一、项目名称 (1) 二、建设单位 (1) 三、场地及气象条件 (2) 四、建设性质 (2) 五、建设规模 (3) 第二节报告编制依据和研究范围 (3) 一、研究范围与误差控制 (3) 二、项目指导思想 (4) 三、编制依据 (5) 第三节主要技术结论 (5) 一、主要技术特点 (5) 二、装机方案 (6) 三、厂区总图布置 (6) 四、余热回收装置布置 (6) 五、发电主厂房布置 (7) 六、循环系统冷却塔 (7) 七、软水系统 (7) 八、热力系统 (7)
十、电气 (8) 十一、热工自动化 (9) 十二、计算机控制 (9) 十三、通风及空气调节 (9) 十四、土建设计 (9) 十五、节约能源措施 (10) 十六、环境保护 (10) 十七、劳动安全及工业卫生 (11) 十八、运行组织及定员 (12) 第四节主要技术经济指标分析 (13) 一、主要技术经济指标见表 (13) 二、项目总投资构成分析 (14) 三、资金来源与使用计划 (15) 四、综合经济技术指标分析 (16) 第五节主要研究结论 (17) 第二章项目建设背景及必要性 (19) 第一节项目提出背景 (19) 一、项目符合《产业结构调整指导目录(2011年本)(2013修正)》 (19) 二、项目符合《节能减排“十二五”发展规划》 (19) 三、项目符合《钢铁工业“十二五”发展规划》 (19) 四、项目属于申报资源节约和环境保护2014年中央预算内投资备选项目 (20) 第二节项目建设的必要性 (20) 一、市场发展的需要 (20) 二、企业发展的需要 (21) 第三章总图运输 (23) 第一节概述 (23) 一、厂址位置及交通概况 (23) 二、设计依据 (23) 三、生产设施组成 (23) 第二节总平面布置 (23) 一、厂区总平面布置 (23) 二、竖向布置 (24) 三、厂内运输及道路 (24)
关于我国冶金行业中余热利用现状的探讨
选课课号:(2012-2013-1)-BG11191-320401-1课程类别:公选课 《冶金工程概论》课程考核 (课程论文) 题目:关于我国冶金行业中余热利用现状的 探讨 学生姓名: 学号: 授课教师: 班级: 教师评语: 成绩: 重庆科技学院冶金与材料工程学院 2012年11月中国重庆
关于我国冶金行业中余热利用现状的探讨 陈宏林热动11-03 2011441386 摘要:钢铁冶金行业是我国工业企业节能减排的重点行业,同时增强节能减排和资源的综合利用对钢铁冶金行业提高经济效益和保持可持续发展同样起着至关重要的作用。本文介绍了我国在工业生产中余热资源利用的基本现状,探讨了余热利用技术的进展,并结合我国钢铁冶金行业余热利用方面存在的问题,为科学合理地进行余热利用提出了相关建议。 关键词:冶金;余热利用;现状 Discussion On The Status quo of Waste Heat Utilization in China's Metallurgical Industry Chen Honglin Energy and Power Engineering 11-03 2011441386 Abstract: Iron and steel metallurgy industry is energy saving and emission reduction of China's industrial enterprises in key industries, while enhancing energy conservation and comprehensive utilization of resources to enhance economic efficiency and maintain the sustainable development of the iron and steel metallurgy industry also plays a vital role. Introduced the status of waste heat utilization in China, discussed the advances of waste heat utilization technologies, Combined with the existing problems in China's iron and steel metallurgy industry, waste heat utilization, and put forward relevant proposals for scientific and rational utilization of waste heat. Key words: Metallurgy; waste heat utilization; current situation 1 前言 钢铁冶金行业是我国基础工业中最为重要的行业之一,同时也是一个高能耗的行业,是我国六大行业中的能耗“大户”,据国家统计数据显示,冶金行业总的能耗量占到我国总能耗的10%左右。国家早在“十一五”规划的时候就规定要将单位GDP能耗在“十五”的基础上下降20%,而钢铁冶金行业的节能减排工作就直接关系到了这一目标是否能够实现,钢铁冶金行业成为我国工业企业节能减排的重点行业,同时增强节能减排和资源的综合利用对钢铁冶金行业提高经济效益和保持可持续发展同样起着至关重要的作用。文章从我国钢铁冶金行业的余热利用现状人手,结合我国钢铁冶金行业余热利用方面存在的问题,为科学合理地进行余热利用提出了相关建议。自上世纪六七十年代以来,世界各国余热利用技术发展很快。目前,我国的余热利用技术也得到了长足进步,但是与世界先进水平还有
汽车发动机余热利用技术可行性分析
汽车发动机余热利用技术可行性分析 一、背景 自20世纪70年代世界性的能源危机发生以来,能源问题受到世界各国普遍重视,各经济大国都致力抢占能源市场同时,对节能技术的重视程度也大大加强。随着人们生活水平的提高,汽车保有量越来越大,汽车能源消耗在总能源消耗中所占的比例越来越高,汽车节能问题越来越受到各国关注。节能已经成为当今世界汽车工业发展的主题之一。汽车消耗的能源主要是石油燃料,而我国是一个石油存储量相对欠缺的国家,目前己成为世界第二大石油进口国。随着我国汽车工业的迅速发展,提高汽车燃料有效利用率和减少环境污染在我国具有更重要的战略意义。调查研究表明,汽车燃料燃烧所释放的能量只有三分之一左右被有效利用,其余能量都被散失或排放到大气中,造成了能源极大浪费,也带来了不良环境影响。因此将这些汽车废热有效利用是实现汽车节能,降低汽车能源消耗的一个有效途径。 二、汽车余热利用技术 从目前汽车所用发动机的热平衡来看,用于动力输出的功率一般只占燃油燃烧总热量的30%-45%(柴油机)或20%-30%(汽油机)。以余热形式排出车外的能量占燃烧总能量的55%-70%(柴油机)或80%-70%(汽油机),主要包括循环冷却水带走的热量和尾气带走的热量。表为内燃机的热平衡表 从表中可以看出汽车发动机冷却介质带走的热量有较大利用空间,如何将其有效利用自然受到人们越来越多的关注,不少人致力于此方面研究。 由于车用发动机特殊的使用场合,汽车余热利用具有鲜明的特点和特殊的要求,可将这些特点简单归结如下:一是汽车余热的品位较低,能量回收较困难;二是余热利用装置要结构简单,体积小,重量轻,效率高;三是废热利用装置要抗震动、抗冲击,适应汽车运行环境;四是要保证汽车使用中的安全;五是要不影响发动机工作特性,避免降低发动机动力性和经济性。由于汽车余热利用具有上述特点,使得研究的成果虽多,但投入商业化生产的不多,有待进一步的研究开发。 国内外汽车余热利用的技术,从热源来看,有利用发动机冷却水余热和利用排气余热两
烧结机工序的余热回收利用
烧结机工序的余热回收利用 烧结工序是高炉矿料入炉以前的准备工序。有块状烧结和球团状烧结两种工艺。块状烧结是将不能直接加入炉的炼铁原料,如精矿粉、高炉炉尘、硫酸渣等配加一定的燃料和溶剂,加热到1300~1500℃,使粉料烧结成块状。球团烧结则是将细磨物料,如精矿粉配加一定的黏结剂,在造球设备上滚成球,然后在烧结设备上高温烧结。两种烧结过程都要消耗大量的能源。据统计,烧结工序的能耗约占冶金总能耗的12%。而其排放的余热约占总能耗热能的49%。回收和利用这些余热,显然极为重要。烧结工序内废气温度分布示意图如右图。由图可知,回收余热主要在成品显热及冷却机的排气显热两个方面。 烧结生产时,在烧结机尾部及溜槽部分,烧结矿热料温度可达700~800℃,除热废气外,料品还以辐射形式向外界散发热量。这部分高品位热量主要通过余热锅炉回收。热管技术目前主要应用在冷却机废气的余热回收。 热烧结矿从烧结机尾部落下经过单辊破碎振动筛筛分后,落到冷却机传送带上,在冷却机上布置有数个冷却风罩,风罩内装有轴流风机(吸风式),使冷却风通过矿料层,能过矿料层后的风温在第一风罩内一般可达250~400℃,第二风罩内风温一般为200℃左右。冷却矿料的另一种形式是鼓风冷却,即风机在矿料层底部鼓风,通过矿层后进入风罩排空。 烧结余热回收的应用流程如右图所示。 在第一风罩内布置热管蒸汽发生器,冷却通过热的矿料,被加热到250~350℃,通过热管蒸汽发生器热管的蒸发段,温度降为150℃左右排空。第二风罩的热风温度较低,一般为200℃左右。在此风罩内布置软水加热器,加热汽包的给水。在溜槽或冷却机前端的密封罩内布有蒸汽过热器,过热从汽包产出的饱和蒸汽。
北台450m2烧结余热发电技术方案
辽宁本溪北营钢铁(集团)股份有限公司2×450m2烧结环冷机纯低温余热发电项目 技术方案 中冶北方工程技术有限公司 2010年8月
本溪北营钢铁(集团)股份有限公司2×450m2烧结环冷机纯低温余热发电项目 目录 1 装机方案 (1) 1.1 余热锅炉系统 (1) 1.2 装机方案 (3) 2 建厂条件 (6) 2.1 厂址概况 (6) 2.2 交通运输 (7) 2.3 水源 (7) 2.4 总体布置 (7) 2.5 电气部分 (8) 3 投资估算 (9)
1 装机方案 1.1 余热锅炉系统 1.1.1余热条件 北营公司烧结厂建设2台450m2烧结机,本余热锅炉可利用的烧结环冷机热风条件如下: (a)采用环冷机一段和二段高温端热风,风温为250-400℃。 (b)烧结环冷机各段风机参数如下: 450m2烧结机风机(单台) 风量:435000Nm3/h 风压:4300Pa (c)余热锅炉排气温度为140℃,采用再循环方式,再循环后风温可达280-420℃。 (d)余热风量含尘浓度为1.0g/Nm3。粉尘成分如下: TFe----55.71% FeO----7.5% SiO2----6.24% Al2O3—3.42% CaO----11.23% MgO----2.69% S-----0.0067% 1.1.2所利用的环冷机热风资源参数 将每台环冷机一段和二段高温端风箱排出的气体作为余热锅炉的热源。一段风量取风机额定流量的70%,二段高温端风量取风机额定流量的70%,因此余热发电所利用的环冷机热风资源原始设计参数如下表。
环冷机一段所利用的热风资源参数 环冷机二段高温端所利用的热风资源参数 1.1.3余热发电工艺流程 在环冷机一段和二段高温端风箱对应的上部风罩顶部分别设置集气烟筒。在烟筒顶部设置电动蝶阀。在风罩合适位置设置烟气连通管。将环冷机一段和二段高温端风箱的温度较高的热废气分别送进余热锅炉。 余热锅炉生产时,烟筒顶部电动蝶阀关闭,使环冷机一段和二段高温端风箱的全部废气都进入余热锅炉。余热锅炉系统发生故障时,烟筒顶部电动蝶阀开启排气,使环冷机能照常生产。 余热锅炉排出的140℃气体,通过烟道送至循环风机。使之经循环风机增压后,重新回到环冷机一段和二段。余热锅炉正常运行时, 环冷机一段和二段鼓风机停运。经过烟气热平衡计算,从环冷机一段、二段抽出的热烟气量总计为609800Nm3/h,从一、二段抽出的热烟气分别引入余热锅炉;余热锅炉排烟温度为140℃,烟气量为609800Nm3/h,
推荐:余热利用的现状
余热利用的现状 【学员问题】余热利用的现状? 【解答】节能降耗是冶金企业长期的战略任务。冶金企业从原料、焦化、烧结到炼铁、炼钢、连铸以及轧钢的生产过程中产生大量含有可利用热量的废气、废水、废渣,同时在各工序之间存在着含有可利用能量的中间产品和半成品。充分回收和利用这些能量,是企业现代化程度的标志之一。 在各种工业炉窑的能量支出中,废气余热约占15%~35%,这些废气净化处理后是一种输送和使用方便、燃烧后又无需排渣和除尘、不易造成环境污染的优质能源。若能按工艺要求提供合适热值的煤气作能源,还有利于改善产品质量。但是由于企业生产结构和工业炉窑配置等原因,目前我国许多冶金企业仍排放大量废气。这是造成企业能源消耗高的一个重要原因。本文将介绍国内各冶金企业废气余热回收利用的现状及存在的主要问题。 余热回收种类及原则 冶金企业常用的废气余热利用方式有:①安装换热器;②在换热器后安装余热锅炉;③炉底管汽化冷却;④发电(热电联产);⑤制冷。回收后的热量主要用于预热助燃空气、预热煤气和生产蒸汽。对电炉而言,预热废钢或进料可减少电炉的电能消耗,缩短熔炼时间;对加热炉而言,预热空气、燃料或工件,烟气余热返回炉内,可使火焰稳定、提
高燃料温度和燃烧效率以及炉子的热效率。 工业炉窑余热回收差的原因,除了排烟温度高和换热器能力小之外,鲜为人注意的是烟气和热风的显热未能有效保存,烟气由炉膛冒出、吸入冷风,地下烟道漏水、漏气,旁通烟道短路和管道绝热不良,使多数炉子在回收装置前的烟气热损失高达30%~50%,回炉热风的显热损失为20%~33%.针对这种情况,提出了一系列降低出炉烟温的措施和能充分保存与回收余热的排烟-供风系统,使上述两项热损失分别降到5%和3%左右,同时开发了各种高效、经济的换热器和能使用全热风的燃烧装置,回收后烟温可下降到180~250℃,不再需要安装价格昂贵而利用率不高的余热锅炉,使炉气余热从炉外回收转到炉内回收的方向来,正是在这种形势下提出了余热全自回收的新概念:首先设法降低炉子排出的烟温和烟量,并使余热回收过程中的各项热损失减少,然后通过高效换热器将余热最大限度地回收并全部送入炉内。 利用方式 (1)烧结废气 在钢铁生产过程中,烧结工序的能耗约占总能耗的10%,仅次于炼铁工序而位居第二。在烧结工序总能耗中,有近50%的热能以烧结机烟气和冷却机废气的显热形式排入大气,既浪费了热能又污染了环境。由于烧结废气的温度不高,以往人们对这部分热能的回收利用重视不够。但实际上大有文章可做,因为烧结废气不仅数量大,而且可供回收的热量也大。不过,烧结余热回收装置的投资费用较大,是否对烧结机或冷却机实施余热回收