轮胎硫化时间的优化
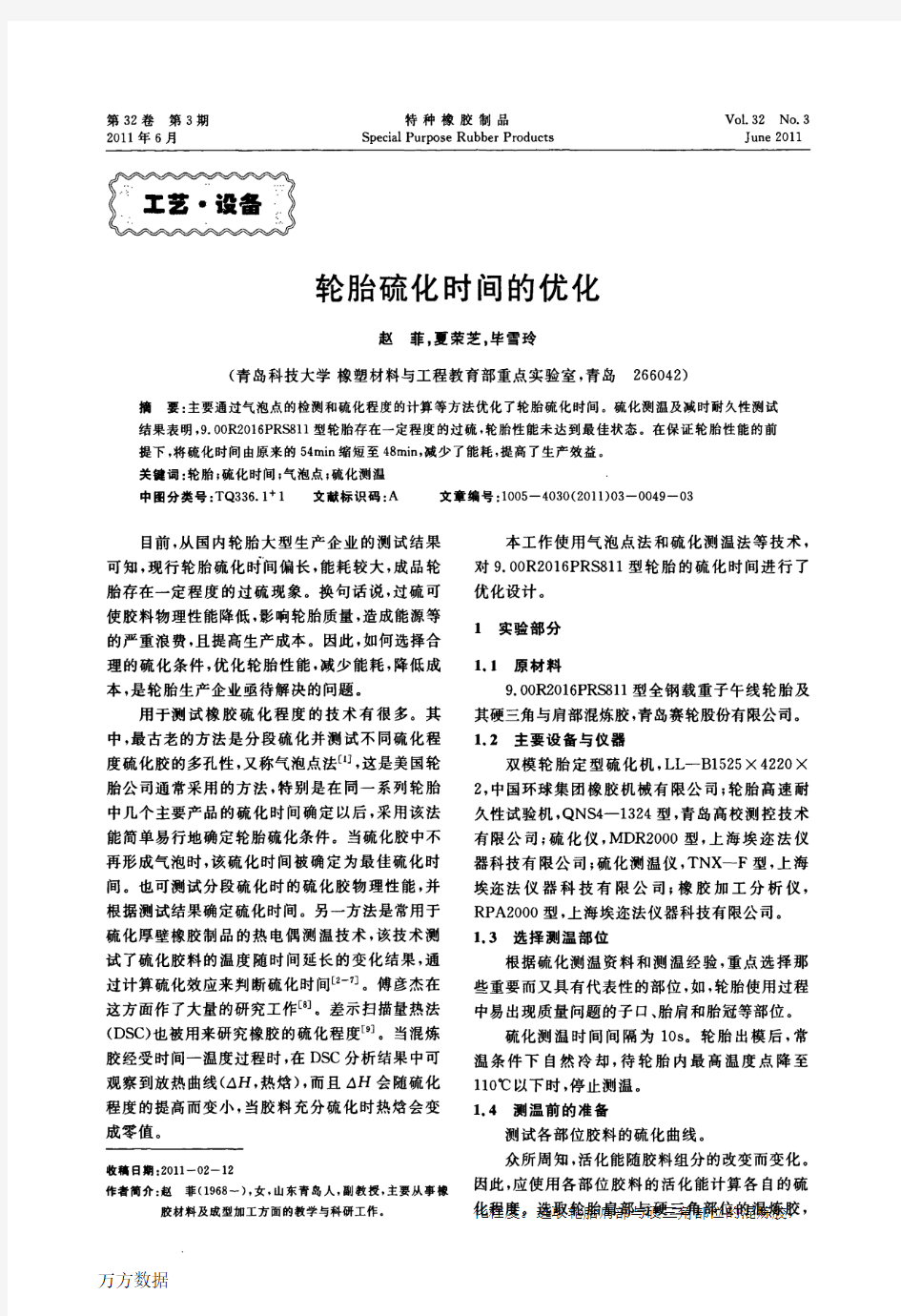

万方数据
万方数据
万方数据
万方数据
全钢载重子午胎质量缺陷产生原因及解决措施
全钢载重子午胎质量缺陷产生原因及解决措施 1胎里露线 胎里露线是指轮胎里面钢丝骨架材料内表面覆胶不足,钢丝露出胎里表面。胎里露线多在肩部或侧部出现。经过里程实验,出现露线的外胎在耐久实验15小时左右即出现肩部鼓包或爆破,基本没有使用价值,由于影响因素较多,因此,胎里露线是废品率很高的一种缺陷,也是全钢胎制造过程中最容易出现、最难解决的问题。 1.1原因分析 1.1.1胎里露线主要原因是机头平宽设计偏小或在成型过程中胎圈定位撑块出现漂移造成。成型机头宽度窄,两胎圈之间的帘线长度短,当硫化给内压时,由于胎胚外直径小于设计尺寸,伸张变形大,这样帘线会抽出内衬层导致胎里露线。 1.1.2材料分布不足也会产生胎里露线,如果胎面或垫胶的厚度或长度不够标准,在成型时强行拉伸,导致局部材料缺失,肩部内轮廓帘线伸展过渡,易出现胎里露线现象。 1.1.3内衬层的厚度及各部位的尺寸低于设计尺寸,或成型时贴合偏移,造成局部材料分布不均,或密封层的塑性过大均会造成肩部漏钢丝的现象。 1.1.4硫化定型失控也是造成成品肩部漏钢丝的不可忽视的原因。在硫化定型时,如果定型压力不能稳定在规定值,那么在合模过程中,胎胚外直径一直处于逐渐增大的状态,这样会有肩部部分胶料随着花纹块下移,造成上模花纹块处缺胶,成品胎里肩部露线。 1.1.5硫化机机械手定位高度过低,胎胚的中心线与胶囊中心线不吻合,定型时胎胚上部过度伸张,钢丝帘线析出内衬层表面,出现露线现象。 1.2 解决措施: 1.2.1 结构设计是内在因素,工艺和操作是外部因素。若存在着普遍的胎里露线现象,并且通过X光检测,发现胎体帘线成直线排列,则应重新考虑平宽的选取,一般增大2~4mm可解决。严格控制挤出、压型半成品部件的的尺寸,不合格的半成品部件严禁使用。 1.2.2 严格控制成型操作,每班开产前必须对成型鼓的平宽、送料架的定位尺寸进行测量,不符合要求的应通知维修人员解决后方可生产。同时要检查各种半成品部件是否符合施工条件,不合格的半成品严禁使用。 1.2.3 对于胎里露线的机台,在不装胎胚时进行胶囊定型,检查胶囊在一次压力下是否有继续增大的现象,如果有,则必须更换定型平衡阀膜片或平衡阀密封圈。严格控制硫化的一、二次定型压力,并在生产过程中周期性的检查,以防止发生波动。 1.2.4调整硫化机机械手下降高度和胶囊的拉伸高度,使二者中心线基本吻合,高度以胎胚下胎圈离模具钢圈表面20mm为宜。 2 胎圈漏钢丝(子口硬边) 胎圈漏钢丝是指胎圈着合面能看到钢丝包布印痕,甚至析出钢丝包布,有内胎轮胎常常伴有子口硬边出现。出现此问题的轮胎在使用过程中容易磨断包布钢丝,损坏胎体,造成子口爆破。 2.1原因分析 2.1.1胎侧压型过程中,耐磨胶尺寸超上公差,造成胎胚胎圈直径变小,在硫化定型时,上下钢圈压住子口将耐磨胶刮下,导致胎圈部位局部缺胶漏钢丝。 2.1.2成型时,胎侧定位光标间距偏小或操作失误,造成胎侧整体下移,胎圈部位胶料增厚、胎圈直径变小,硫化时造成局部缺胶。 2.1.3硫化定型过程中,由于机械手定中偏歪、定型不正,模具钢菱圈将一侧子口胶料甚至包布刮下,导致此处漏钢丝。 2.1.4钢丝圈直径在设计或卷曲过程中本身偏小。
外胎硫化工序工艺培训(修改)
外胎硫化工序工艺培训 把轮胎胎胚装入模型内,经过温度、压力和时间三个相互有关的硫化要素,使各部件密实地成为一体达到设计技术预期要求的物理机械性能和轮廓尺寸,成为有使有价值的产品的加工工艺过程,称为外胎硫化工序。 硫化设备 子午线轮胎硫化采用的是定型硫化机。定型硫化机有硫化大规格轮胎的单模定型硫化机和硫化中小规格轮胎的双模定型硫化机,定型硫化机使用胶囊而不使用水胎,胶囊呈筒状装在硫化机的中心机构上,外胎胎胚不必预先定型,硫化过程中对装胎、定型、硫化、卸胎等过程可全部实现自动控制。 国内广泛使用的是机械连杆式双模定型硫化机,现新上的工厂都在上液压式定型硫化机。机械连杆式定型硫化机机型按使用的胶囊形式不同有A型(或称AFV型)、B型(或称BOM型)和R型(或称RIB型)三类机型。 A型、B型、R型三种硫化机除中心机构外,其设备主要装置和工作原理基本相同。由于中心机构不同,三种硫化机所使用的胶囊形式也不同。 二.设备主要装置 1.传动装置:用来开启模型和对模型产生足够的合模力。 2.中心机构:主要有动力缸、定型套、调整套、胶囊上下卡盘、进出水管口等,主要用来控制胶囊伸缩膨胀,配合卸胎机构,使轮胎脱离下模,控制一次定型高度,向胶囊提供硫化介质。 3.蒸汽室(现多使用热板):蒸汽室分上、下蒸汽室。下蒸汽室固定在机座上,上蒸汽室可上下移动。 4.装胎机构(机械手):将胎胚从存胎盘上抓取后送到下模定位,充气定型。 5.卸胎机构:在上下卡盘下降动作的配合下,将硫化好的外胎取出送入卸胎辊道。 6.活络模操纵控制机构:控制活络模的收缩和张开。 7.安全装置:安全杆。 8.润滑系统:保证硫化机正常生产延长使用寿命,对主机各润滑点进行润滑加油。 9.管道系统:包括蒸汽热水,动力水和各种阀门。(作用:通过管路给硫化机提供各种硫化介质或进行控制) 10.电气控制系统:包括控制管理,主令控制器、程控器、控制柜及电磁阀、触摸屏等。 三.全钢子午线轮胎的硫化工艺流程 1.硫化工艺流程简述 1.1检查胎胚规格花纹、层级与模具是否相符,同时检查胎胚外观质量; 1.2硫化胶囊微量充压,检查胶囊,并均匀喷刷隔离剂; 1.3启动抓胎器垂直下落,机械手抓起胎胚; 1.4中心机构的卡盘上升达到一定的高度,胶囊抽真空收缩; 1.5抓胎器转入中心机构的上方垂直下落,将胎胚放入模型上; 1.6胎胚下落到设定的高度、胶囊充入设定的一次定型内压; 1.7抓胎器的页片收缩卸下胎胚垂直上升并回转; 1.8启动硫化机的上蒸汽室自动下落到设定的二次定型高度暂停,活络块张开,胶囊内蒸汽压达到二次定型压力; 1.9暂停时间到自动进行合模直至合模完毕; 1.10自动进入胶囊蒸汽达到规定的时间和压力;
全钢子午线轮胎新新用橡胶常用胶种跟性能
全钢子午线轮胎用橡胶常用胶种及性能 1、天然橡胶 全钢子午胎厂使用的天然橡胶一般有两种牌号,即SMR10和SMR20。对于这两种标准胶的质量标准原执行马来西亚天然橡胶研究院1979年颁布的No.9标准。 主要成分:高顺式聚1,4-异戊二烯和蛋白质等。 性能指标:国际上多采用马来西亚橡胶协会的标准作为参考,结合本国和本企业的内部标准对胶料性能予以控制,以下为橡胶制品中常用的天然橡胶品种的性能指标: SMR 10CV SMR 10 SMR 20CV SMR 20 Parameter SMR CV60 SMR CV50 LATEX SMR L SMR 5 SHEET MATERIAL a SMR CP BLEND FIELD GRADE MATERIAL Dirt retained on 44u aperture (max,% wt) 0.02 0.02 0.02 0.05 0.08 0.08 0.08 0.16 0.16 Ash content (max, %wt) 0.50 0.50 0.50 0.60 0.75 0.75 0.75 1.00 1.00 Nitrogen (max, %wt) 0.60 0.60 0.60 0.60 0.60 0.60 0.60 0.60 0.60 V olatile matter(max, %wt) 0.80 0.80 0.80 0.80 0.80 0.80 0.80 0.80 0.80 Wallace rapid plasticity (P0) (min) -35 30 --30 -30 Plasticity retention index (PRI) (min, %)b 60 60 60 60 50 50 50 40 40 Lovibond Colour: individual value (max) -- 6.0 ------ rang (max) -- 2.0 ------
硫化车间的设计
硫化车间 一、生产规模计算 g=Q/d(k-f) G=gd g-设计日产量,kg/d,m2/d,m/d,条/d,根/d… … Q-计划年产量,kg/a,m2/a,m/a,条/a,根/a… … k-不合格率,%;d-全年生产天数,K-合格率,%;f-产品检验率,% G -设计年产量,kg/a,m2/a,m/a,条/a,根/a 相关资料:Q=5000000条d=245天k=99.6% f=1/6000 代入得g≈20494条G=5021030条 综上,设计日产量为20494 条,年产量为5021030条 二、半成品和消耗定额计算 硫化所用半成品胎坯,一个轮胎需要一个胎坯,故胎坯的日消耗量为20494个,设计年消耗量为5021030个。 三、工艺方案的选择和论证 轮胎硫化而言,它是制造轮胎的最后过程,轮胎最终的均匀性和外观质量到此过程结束后才能显现或才有结论,而它本身又是重要制造过程;这样说,无非是强调轮胎硫化的重要性,不但要保持前面工序的质量,还要做好本身的工作,从而得到均匀性和质量好的轮胎成品 设备:三明化工机械厂XLL-B1320X2型双模外胎定型硫化机硫化9.00R20钢丝子午胎。 工艺条件:最大硫化蒸汽压力0.7MP A 过热水内压2.8MP A温度在165℃以上 动力水压力2.1MP A 动力空气压力0.7MP A 轮胎充气压力(后充气动力)1.0MP A 胶囊真空度0.53MP A 工艺要求: 1.胎坯入模前,胎圈与模型瓦环均匀上脱模剂,如硅油或皂液。涂模要求务必均匀呈薄膜状;
2.两半模装模时,胎坯直径不得大于990MM(周长3110MM),一般控制在982MM(烟斗花纹)~985MM(曲折花纹); 3.一次定型压力0.04MP A~0.06MP A,一次定型高度240MM(套筒); 4.二次定型压力0.06MP A~0.08MP A,根据胶囊新旧程度微调; 5.外温硫化温度,波动范围不得大于1℃; 6.硫化内压2.5MP A,过热水温度在165℃以上 7.硫化外蒸汽压力0.31MP A; 8.胶囊每隔24H涂硅油一次,两肩部位多涂一些; 9.外胎胎坯必须修剪,不得划伤; 不用的模型表面不允许潮湿存放,停用两月以上的,内表面必须涂上防锈油 四、生产设备类型的确定和台数计算 1.设备确定 三明化工机械厂XLL-B1320X2型双模外胎定型硫化机硫化9.00R20钢丝子午胎 2.设备生产能力计算 Q=60n/t 式中 Q - 硫化机生产能力,件/h; n - 一次硫化件数,件; t - 硫化操作周期,min,
全钢子午线轮胎10.00R20测温报告
1硫化测温准备工作 1.1测温轮胎规格: 测试轮胎为10.00R20规格XXX花纹16PR的全钢子午线轮胎。 1.2主要试验设备: 高铁硫化仪、硫化测温仪、笔记本电脑、63.5”双模定型硫化机等。 1.3测温模具准备: 根据测温导线总数,将测温用硫化模下侧模板开1个直径20mm的圆孔,留出导线口。 1.4测温导线的准备: 此次测温选取WL-Ⅳ型热电偶,将埋入轮胎的一端进行绞接,并将每对热电偶标识。根据测温点数量,准备24对热电偶线。 1.5埋线位置的确定: 根据硫化测温资料和测温经验,我们重点选那些重要而又具有代表性的位置,如:在轮胎使用中易出现质量问题的子口、胎肩、胎冠等位置。详见附图。 1.6埋线: 此次测温选择胎胚成型时埋线,依据预先确定并绘制的埋线图,及半成品设计尺寸与施工标准,对成型好的胎胚依次准确定位埋线,并进行固定。 2测温 我们于10月30日对10.00R20的XXX花纹16PR规格进行了测温,选择A2硫化机,按照现硫化工艺条件进行硫化。硫化工艺附后。
硫化计时开始后,测温间隔时间取10秒。在轮胎硫化结束出模后,正常条件下自然冷却至130℃左右为止。 3各部位胶料活化能计算 取轮胎各部件共12种胶料分别做141℃、151℃、161℃三个温度下的不同硫化程度 条件,根据阿累尼乌斯方程求算出各部件胶料活化能。 阿累尼乌斯方程:log(τ1/τ2)=E/(2.303R)*((t2-t1)/t2*t1) τ1、τ2: 正硫化时间t90 (min); t1、t2: 硫化温度(K) E: 活化能(KJ/mol) R: 气体常数(8.3143J/mol*K) 4测温数据的处理 根据试验室做出的151℃各胶料T90值以及求算出的胶料活化能,运用阿累尼乌斯方程对测温记录数据进行处理,求算出151℃等效硫化时间,并得出当前工艺条件下轮胎硫化程度。上述过程采用硫化测温仪自动计算。 等效硫化时间计算公式:Tg= exp{E/R(1/T0–1/T)}dt tm: 硫化终止时间(min) ts: 硫化起始时间(min) E: 活化能(KJ/mol) R: 气体常数(8.3143 J/mol*K)
轮胎硫化操作实习报告
毕业实习报告 所在系:机械工程系 专业班级:08级机制3班 姓名:李航 实习单位:汽轮有限公司 实习课题:轮胎硫化操作 实习时间:10年7月1日到10年12月31日 指导教师:王志航 实习成绩: 山西学院
轮胎硫化操作实习报告 摘要:找了一个实习的机会,在化工单位虽然不是我学的专业,但我也很高兴。又可以多学一些知识。为我以后的就业增加了一些资本。在这个单位主要是做轮胎的硫化,对中间控制项目的分析及学习。最后是一点心得体会。 一企业概况 山东德瑞宝轮胎有限公司位于东营市广饶经济及开发区,注册资本21000元,是一家集全钢子午胎半钢子午胎和销售于一体的大型现代化轮胎企业。 2010年,公司投资23亿元,新征地666700平方米,开工建设年产600万套全钢载重子午胎项目和年产2400万套半钢子午线轮胎项目,打造大型现代化轮胎研发生产基地。2010年12月,工程一期300万套全钢子午胎生产线全部竣工投产,达到年产全钢载重子午胎300万套的生产规模,可实现销售收入50亿元,利税6亿元,十二五期间,实现年产600万套全钢和2400万套的全部达产,届时可实现销售收入260亿元,利税18亿元。在技术领域的不断创新和进步,让德瑞宝不断在汽车世界实现自己的价值。 公司现拥有“德瑞宝、昊龙、DERUIBO”三大品牌,产品设计涵盖全钢子午线轮胎、半钢子午线轮胎全规格系列,并开发了全轮位、驱动专用、无内胎、短途、矿山、特种胎等具有针对性的七大系列150余种产品。公司销售网络覆盖欧洲、美洲、非洲、东南亚等多个国家和地区,并在国内各大省市和地区建立起了完善的销售服务网点。产品完全达到国家CCC产品认证要求,同时达到了美国交通部DOT产
机械式和液压式轮胎定型硫化机的性能特点和选用解读
机械式和液压式轮胎定型硫化机的性能特点和选用 作者:日期:2009-6-8 15:38:35 人气:标签: 机械式和液压式轮胎定型硫化机是当今轮胎定型硫化机的两大系列.由于两种硫化机的主要动力不同,结构形式各异运动方式也有别,其性能和适用的范围也有一定的差异,。 一结构和性能比较, 1两种硫化机的传动方式不同, 机械硫化机的传动路径为:电机+ 减速机+ 减速齿轮一曲柄+ 连杆+ 横梁( 上模) 。液压硫化机的传动路径为:液压缸+ 横梁( 上模) 。显见,机械式硫化机的传动路径冗长而复杂,因而其运动精度较差,液压硫化机的传动路径简单单一,因而其运动精度较高。仔细分析会发现,机械式硫化机虽然传动精度低,运动平稳性较差,但并不影响轮胎硫化的精度。因为我们知道,通常机械式硫化机横梁( 上模) 的运动轨迹由两部分构成,一段为竖直方向的升降,另一段为平行移动或者边移动边绕横梁轴转动。这其中只有在竖直方向的运动才对轮胎硫化的质量有某种程度的影响。但现在的机械式硫化机在横梁和底座间都设计有对中装置,横梁在升降段的运动直接由对中装置控制。因此,其上下模型的对中度、平行度等与液压硫化机并无大的区别。 2上横的运动轨迹不同, 上面已经介绍,机械式硫化机的上模运动轨迹分为两部分即升降和平移(或翻转),.开模时,模型先竖直上升后按照预定的轨迹向后平行移动或者边移动边翻转.开模到终点,上模与下模之间根据需要保持一定的距离.液压硫化机的上模只在竖直方向作升降运动.开模后上模位于下模正上方一定距离的地方.这样,机械式硫化机在开模后,下模的上方是完全敞开的,为后续的操作腾出了广阔的空间.而液压硫化机由于上模始终在下模的正上方,并且由于硫化机体度的限制,开模的高度也有一定的限制,上下模型间的距离自然不可能太大,使后续的操作受到一定的影响,。 3合模力的产生方式不同, 机械式硫化机的合模力来自主传动系统.合模后依靠传动件的自锁承受硫化时的张模力.合模力的调整是靠调整上下模的间隙实现的,调整十分繁琐.液压硫化机的合模力由专门的被称之为加力油缸的液压缸产生.由液压缸的压力承受张模力.通过调整加力油缸的压力可以方便的改变合模力的大小.加力油缸的作用点均布在下硫化室的某一圆周上模型受力比较均匀.张模力是通过加力油缸的柱塞传递给压力油的,由于液压油具有可压缩性,如果在硫化时由于某种原因使张模力产生波动,则液压油可以部分吸收这种波动,减少受力系统的变形,。 4横梁和底座的受力变形条件不同, 机械式硫化机除大规格(通常为75英寸以上)机型为单模,一般均为双模.即在同一横梁和底座上安装两套模型其横梁和底座的跨度都较大.液压硫化机虽然也有单模和双模之分,但其传动系统和合模力的产生对每个模型来说都是独立的.即一个横梁和一个底座上只安装一套模型,其横梁和底座的跨度较小.同时,对规格相同的机械式和液压式硫化机而言,硫化时前者的力是后者的两倍.因此,硫化时机械式硫化机横粱和底座的变形远远大于液压式硫化机.而且,液压式硫机一个模型两侧的变形是对称的,而机械式硫化机一个模型两侧的变形是非对称的.从而使硫化出的轮胎均匀性较差,。 二硫化机的选用, 机械式硫化机适用范围广,它不仅能硫化斜交胎也能硫化普通等级的子午胎.斜交胎的生胎高度一般都较大,机械式硫化机正好适应了这一需要.同时,由于机械式硫化机硫化时系统的受力变形较大,因此,不适于
轮胎氮气硫化的方法
目前,采用如图1所示的带胶囊的硫化设备,用气体作为加热和加压介质硫化汽车轮胎等橡胶制品的方法得到了应用。将生胎(图中所示制品为汽车轮胎b)放到模具a中,胶囊c采用充气定型,轮胎b的形状同模具a内部形状一致后,关闭模具a。接着,蒸气作为加热介质从供汽口e吹入,从蒸汽室中心较低位置水平方向进入f,轮胎被加热、加压。供汽口e 位于硫化设备中心,与供汽通道d互通。当轮胎b温度达到预定温度时或经过预定时间后,停止供应蒸汽,通入氮气或类似惰性气体作为加压媒介,直到加热工序结束,气体压力不得低于所供蒸汽压力。可从同一个供汽口e水平方向供气,也可从另一个供气口水平方向供气,后者专门用于加压媒介,与供蒸汽口e在同一高度,与通道d互通,或与另一供应通道互通,使气体进入胶囊内腔f,因而轮胎b的温度可以保持在预定温度。 在上面的工艺设备中,蒸气从蒸汽室中心下部位置沿水平方向吹入,蒸汽冷凝水积聚在轮胎b底部表面较低段排不出去,阻碍了底部胎侧加热。内部压力增高减少了蒸汽流入量,因而削弱了内部蒸汽流。内部蒸汽流速降到几乎为零时,湿蒸汽形成水滴向下滴,同时保持过热状态的其他蒸汽由于相对较小的比重向上升高,在轮胎b的垂直方向就形成了温差。此外,由于温度比蒸汽低一些的加压气体(惰性气体),同蒸汽一样,从位于轮胎内下部的喷嘴水平吹向轮胎较低区段,气体对着吹的部位(如下部胎圈部分等)被冷却到较低温度。在停止通入加压气体而造成内部压力升高的情况下,由于加压气体比蒸汽比重大,容易沉积于轮胎内部空间f底部,而象底部胎侧和胎圈部位与低温加压气体相接触的底部区段,其温度必然会降低。 另一方面,剩余蒸汽积聚在内部空间f上部,并经绝热压缩,虽然只是很短的时间,但因加压气体是在高压下通入的,因此尽管加压气体温度较低,蒸汽温度仍然升高,上部胎侧被加热到很高温度。 因此,在轮胎内部空间f形成了主要由蒸汽组成的上层g,主要由加压气体组成的中层h,
轮胎硫化实习报告
10月份实习报告 全钢载重子午线轮胎胎圈部位构造复杂,部件较多,且成型、硫化时受力变形较大,故生产过程中易产生质量缺陷。在实习的最后一个月,根据生产情况,主要对全钢载重子午线轮胎胎圈部位常见质量缺陷的产生原因进行了分析与研究。 1胎圈裂口 胎圈裂口分为胎圈外部裂口(主要集中在无内胎子午线轮胎装配线上方10~20 mm处,裂口深度达2~3 mm)和内部裂口。 1.1原因分析 (1)三角胶或胎侧设计不合理,导致胶料流动不合理或模具排气孔堵塞,造成胎圈外部裂口。 (2)胎坯胎侧耐磨胶反包后未压实、翘起;硫化时硫化胶囊卡盘泄漏或硫化胶囊处有隔离剂,导致胎圈内部裂口。 1.2解决措施 (1)合理设计半成品尺寸,定期清洗模具,保持排气孔畅通。 (2)加强工艺管理,严格按规范进行操作并及时检查。 2胎圈露线 胎圈露线是指在胎圈附近露出胎圈包布或胎体帘布,分为胎圈底部露线、胎圈外侧露线(多集中于无内胎轮胎)和胎圈内侧露线。2.1原因分析 (1)硫化定型过程中胎坯严重装偏,不能正确装入模具,造成胎圈部位胶料流失,局部出胶边,导致胎圈底部胶料严重不足,露出胎
圈包布或者胎体钢丝。 (2)半成品尺寸不符合工艺要求,胶料不足,造成胎圈底部露钢丝。 (3)胎侧耐磨胶粘度低,硫化时胎圈部位胶料流动过度,胎圈外侧胶料不足,露出胎圈包布。 (4)成型机平宽不符合工艺要求,造成胎坯轮廓过小,硫化时胎圈区域膨胀过度,致使胶料不足,造成露线。 (5)无内胎轮胎胎圈倾斜角度比有内胎轮胎大,若胎圈部位胶料不足,则导致硫化时胎踵到装配线间的胶料不足。 (6)硫化操作时硫化胶囊抽真空不充分,上环下降到定型高度时,硫化胶囊在胎圈处打褶将胶料挤走,造成胎圈内侧露线。 2.2解决措施 (1)定期检查硫化机机械手的对中性,调整胎坯一次定型的停放高度,保证下胎圈距离下钢棱圈底部2 cm。 (2)保证胶料的粘度及成型机的平宽符合工艺要求,同时增大无内胎轮胎胎侧耐磨胶厚度。 (3)保证硫化胶囊的真空度,及时更换老化的硫化胶囊。 (4)胎圈受损的胎坯应修补好再装模硫化。 (5)保证硫化装模时一次定型速度与中心机构上环下降速度相匹配。 3胎圈缺胶 胎圈缺胶表现为胎趾部位缺胶或胎踵部位重皮缺胶。
全钢子午胎成型基本缺陷及处理措施
4、胎里气泡和脱层 胎里气泡和脱层是指内衬层与胎体之间存有空气、水、汽油或隔离剂,硫化后胎里产生气泡或脱层的现象。 4.1 原因分析 (1)成型贴合时部件间因间隙超标存在空气或组合压辊各段压力和轨迹设置不当,以及超定型压力不足,造成胎肩垫胶、气密层等部件未压实,存有空气。 (2)部件层间夹有塑料垫布和胶带断头及纸片等杂质。 (3)硫化前、中期掉压时间超过6min,部件层间形成气孔。 (4)成型贴合时涂刷的汽油未挥发干即进行下一步操作,胎体气泡未刺破。 (5)胎肩垫胶定位偏歪,带束层与胎体帘布层间产生空隙。 (6)炼胶或半成品加工过程中温度偏高致使半成品焦烧时间短,胶料或半成品部件未按顺序使用,半成品过期后粘性差,喷霜后未经处理;汽油胶浆未干,成型过程中压辊不实,均会造成胎里脱层。(7)内衬层复合时未压实,层间存有气体。 (8)胶囊排气线不通畅,内压作用下胶料中的气体进入气密层与胎体帘布层间。 4.2 解决措施 (1)如有必要,重新设定成型机压力、各个压合辊轨迹参数以及各种定位参数,保证成型时各部件的贴合质量,使胎肩垫胶和气密层等部件接牢、压实。
(2)检查各半成品部件的灯光定位,防止定位灯光偏移。 (3)半成品部件按顺序使用,汽油挥发完后方可贴合下一个部件。(4)成型时除净塑料及纸片等杂质。 (5)适当延长硫化定型时间、提高定型压力,使胶囊充分伸展,保证胶囊排气线畅通。 (6)确保硫化温度、压力曲线正常。 (7)气泡刺破。 5、胎里窝气 胎里窝气是指轮胎硫化时由于硫化胶囊和胎体之间的空气未排干净而导致硫化后胎里周向呈现的胶囊棱筋不全或棱筋不清晰,严重者呈海绵状的现象。 5.1 原因分析 (1)胶囊及其夹环排气线不畅通或胶囊隔离剂喷涂过多且未挥发干就装胎胚,造成胎里和胶囊之间有水分存在,或合模后未及时充内压。(2)冬春季节节假日后,新换的胶囊没有充分预热,装胎时胶囊没有充分伸展;硫化机管路内的凉水未排干净,胎胚硫化前未预热,胶囊与胎胚轮廓吻合不好。 (3)硫化机停机时间过长,胶囊在硫化模具内自然下坠变形。(4)定型压力过小,囊壁与胎胚之间存在空气。 5.2 解决措施 (1)疏通胶囊排气线,待喷涂的胶囊隔离剂干后再装胎。 (2)温模时提前4h把胎胚放在硫化机前预热。
B型轮胎定型硫化机常见故障分析与处理
B 型轮胎定型硫化机常见故障分析与处理 王 亮 (银川佳通轮胎有限公司,宁夏银川 750011) 摘要:通过对B 型轮胎定型硫化机日常的开合模、装胎机构、中心机构、卸胎机构的各类故障原因进行分析,并从硫化机各部分的结构及生产操作方面给出故障处理方法,供轮胎工厂的设备管理、维修部分在分析、处理硫化机常见故障时参考。 关键词:B 型硫化机;合模;开模;机械手;中心机构;卸胎支臂 轮胎定型硫化机是目前轮胎制造中的主要设备,但随着全钢子午线轮胎的不断普及,轮胎定型硫化机在通过最初的安装调试后,将处于长时间的日常生产运行阶段。硫化机的日常维修是轮胎工厂设备管理、维修部门日常投入精力最多的工作,硫化机各类运行故障的及时、正确排除,是保证轮胎产能、轮胎质量的基本条件。同时,由于硫化十分重要,在处理故障时若时间掌握不当,方法选用不当,会直接造成轮胎质量缺陷。因此,在处理故障时,应由易到难,由浅到深,即先检查直观的、维护用时短的部位,若故障没有得到解决,再逐步的检查不易找出问题的部位。综合我公司全钢子午线轮胎定型硫化机日常生产运行所发生的各类故障,介绍其中的常见故障及其分析、处理方法,供各轮胎工厂的设备管理、维修部门在分析、处理硫化机常见故障时参考。1 开合模故障 1.合模接近到位时不合模,手动合模电流大。 原因分析:合模不到位或合模过位;活络模具上模偏转。处理方法:查看触摸屏“限位显示”界面、横梁左右连杆,确认合模角度,调整旋转编码器,使连杆与曲柄齿轮垂直;调整活络模位置,校正锅罩定位条。 2.合模到位后,运行硫化步序,步序时间不 运行。原因分析:控制柜程控器没有打通;控制柜转换开关档位不正确。处理方法:控制柜程控器打“通”;控制柜面板转换开关的档位“主机手/自 动”转换开关打在“自动”档位上;“机械手手/自动”打在“自动”档位。 3.合模到位后,运行步序时间,硫化步序不运 行。原因分析:控制柜程控器没有打通;控制柜转换开关档位不正确。处理方法:控制柜程控器打“通”;控制柜面板转换开关的档位“主机手/自动”转换开关打在“自动”档位上;“机械手手/自动”打在“自动”档位;若一时没有找到原因,为保证轮胎质量,可人工计时,到时间手动切换步序。 4.合模到位后,运行硫化步序,无内压内温。 原因分析:“阀组定义”不正确;仪表柜控制气源没有打通;机械阀没压到位,旋转编码器跑位合模不到位,仪表柜程控气源气压不够;熔断器熔丝烧断,程控电磁阀线圈烧或内部阀杆卡住。处理方法:查看触摸屏参数设置中的“阀组定义”,按施工标准正确设置;仪表柜面板控制气源旋塞阀打在“通”上;调整机械阀位置或阀杆高度,调整编码器角度使合模到位,仪表柜程控气源压力应在0.35~0.4MPa 之间;先手动拨上电磁阀,保证 轮胎质量,然后进行:(a )更换熔断器;(b )更换电磁阀。 5.合模到位后,运行硫化步序,掉内压内温。 原因分析:“阀组定义”不正确;仪表柜控制气源没有打通;机械阀没压到位,旋转编码器跑位合模不到位,仪表柜程控气源气压不够;机械阀压合不到位,开合模气源切换不到位,抽真空跑水;程控气源压力不够,风管漏风、切断阀膜片破损。处理方法:查看触摸屏参数设置中的“阀组定义”,按施工 ?22? 橡 胶 科 技 市 场 2009年第14期
全钢子午线轮胎制造工艺
全钢子午线轮胎制造工艺 全钢子午线轮胎制造工艺特点及工艺流程第一节全钢子午线轮胎制造工艺特点全钢子午线轮胎的制造工艺特点 1、各种胶料按照塑炼和混炼的质量要求做到均匀的充分的符合技术要求的物理机械性能的工艺技术操作性能。 2、各种部件的尺寸符合技术规定的尺寸标准。 3、骨架材料与胶料覆合要达到帘线密度均匀且帘线的两面胶料厚度均一。 4、各种复合材料半成品的成型覆贴组合定位准且要均匀对称。 5、各种半成品要做到在技术规定的时间内使用。 6、各种半成品要做到无污染、无变形。 7、胎胚在硫化过程中装胎胚要定位准严格执行硫化三要素。 8、成品的搬运、包装、仓储要满足全钢子午胎的要求。第二节全钢子午线轮胎制造工艺流程一、全钢子午线轮胎主要制造工艺 1、密炼——混炼胶 2、压出——胎面、胎侧、垫胶、胎圈胶芯 3、型胶压延——薄胶片、内衬层气密层 4、钢丝压延———胎体、带束层帘布、子口包布帘布 5、0?压出——0?带束层 6、纵裁——窄纤维胶帘布条和窄薄胶片条。 7、胎圈缠绕成型——胎圈和缠绕胎圈包布 8、胶芯敷贴——将胶芯敷贴在胎圈上 9、半硫化——将胎圈进行半硫化 10、15?裁断——带束层、子口 、90?裁断——胎体帘布 12、成型——胎胚 13、硫化——轮胎外胎成品 14、包布 11 质量检查——100地进行外观和X光透视检查二、制造工艺流程二、生产工艺条件 1、对温度、湿度要求 1成型、裁断区温度20?2?湿度50?5所有半成品要及时进入该区。 2锭子房的温度高于环境温度2-3?相对湿度?60。 30?带束层锭子房条件同上。 2、对紫外线和臭氧的要求。避免阳光的照射 3、无污染、无灰尘。第五章全
全钢载重子午线轮胎质量缺陷问题分析
全钢载重子午线轮胎质量缺陷问题分析 子午线轮胎制造工艺复杂,要求精度高。根据全钢载重子午线轮胎常见质量缺陷,进行了原因分析,并提出了相应的解决措施。 1、胎里露钢丝与肩部帘线弯曲 胎里露线是指轮胎里面钢丝骨架材料内表面覆胶不足,钢丝露出胎里表面。胎里露线多在肩部或侧部出现帘线露出或“露肋骨”现象。在使用中胎里露出的钢丝容易损坏内胎,使轮胎胎体鼓包甚至爆破。肩部帘线弯曲是指轮胎肩部胎体帘线出现周向弯曲。帘线弯曲在轮胎行驶当中受力不均,使钢丝与胶的生热增加,导致轮胎脱层或爆破,引起轮胎的早期损坏。 全钢丝载重子午线轮胎胎里露线和肩部帘线弯曲是生产和使用中困扰轮胎技术人员的一大难题。由于胎里露线和肩部帘线弯曲是相辅相成的,是一对矛盾的统一体,所以将两个问题一起讨论。 1.1 原因分析 (1)胎里露钢丝与肩部帘线弯曲主要原因是机头宽度与帘线假定伸张值选取不合理。胎体由一层钢丝帘布组成,帘线断裂伸张率为1.8~2.3之间,胎体的钢丝帘线伸张值一般在 1.0%~1.8%之间。帘线伸张值大,成型机头宽度窄,帘线长度短。当伸张值达到极限值;帘线会抽出内衬层导致胎里露线。 帘线伸张值小,成型机头宽度宽,帘线长度长,容易导致肩部胎体帘线弯曲。半成品的尺寸和重量是根据材料分布图计算出来的,当半成品尺寸和质量过大,会导致胎体帘线的材料过剩从而使胎体帘线弯曲。材料分布不足就会产生胎里露线,胎面或垫胶的厚度或长度超公差,使得肩部材料过剩,厚度增加,内轮廓帘线舒展不开,导致肩部帘线弯曲。反之,内轮廓帘线伸展过渡,易出现胎里露线现象。 (2)胎坯外周长的大小也是影响胎里露线和肩部帘线弯曲的一个因素。胎坯外周长达不到标准,则轮胎在硫化过程中伸张变形大,出现胎里露线;反之,胎坯外周长大,轮胎在硫化过程中伸张变形小,将易出现帘线肩部弯曲。 (3)一次法成型机传递环故障或鼓的撑块出现故障,成型过程中胎圈定位、撑块定位发生漂移或者平宽设定有误,造成内轮廓帘线较标准帘线长度增大,胎体帘线伸张不足,硫化后产生肩部帘线弯曲。反之,内轮廓帘线较
轮胎生产工艺流程
轮胎生产工艺流程The tyres Production Process Process One工序一:密炼工序Mixing Process 密炼工序就是把碳黑、天然/合成橡胶、油、添加剂、促进剂等原材料混合到一起,在密炼机里进行加工,生产出“胶料”的过程。 Mixing Process is to mix materials,such as Carbon Black, Natural/Synthetic Rubber, Oil, Additive, Accelerator etc. together, and processing in the Internal Mixer,then get rubber film. 所有的原材料在进入密炼机以前,必须进行测试,被放行以后方可使用。密炼机每锅料的重量大约为250公斤。 All the materials should be test before send into Internal Mixer,after be permited then can be used. Every pot weight is about 250 kilograms in Internal Mixer, 轮胎里每一种胶部件所使用的胶料都是特定性能的。 The glue stock used in every kind of Rubber part have specific performance . 胶料的成分取决于轮胎使用性能的要求。 The rubber film composition depends on the tyre performance requirement. 同时,胶料成分的变化还取决于配套厂家以及市场的需求,这些需求主要来自于牵引力、驾驶性能、路面情况以及轮胎自身的要求。 At the same time, the rubber film composition change also depends on the related producer and marke t’s demand. This demand mainly comes from the traction, driving performance, road surface condition and tire own requirements 所有的胶料在进入下一工序—胶部件准备工序之前,都要进行测试,被放行以后方可进入下一工序。 All the rubber film should be test before going into next process, after be permited then can be used in next process. Process Two工序二:胶部件准备工序Preparing Rubber parts process 胶部件准备工序包括6个主要工段section。在这个工序里,将准备好组成轮胎的所有半成品胶部件,其中有的胶部件是经过初步组装的。 This process include six sections,in this process,will prepare well all the semi-finished rubber parts of tyre. Some rubber parts is being initial assembled. 这6个工段分别为: The six sections is as following:
轮胎定型硫化机液压系统常见故障与解决措施 (2)
液压式轮胎硫化机液压系统常见故障分析 一、液压硫化机概述 液压式轮胎定型硫化机区别于机械式轮胎硫化机的地方就在于硫化机的多个主要部套都采用了液压驱动,比如活络模装置、升降驱动装置、中心机构和加力装置。正因为如此,液压式硫化机克服了机械式硫化机固有的缺陷,具有结构紧凑、效率高、自动化程度高、轮胎定型精度高、更换轮胎规格容易、维护使用方便等优点。从产品质量、能源消耗和生产率(直接产出率和设备利用率)诸方面看,液压式硫化机比机械式硫化机具有更佳的性价比,是轮胎硫化机的发展方向。 近几年,液压式硫化机已经大范围取代机械式硫化机,并且这种替代速度也呈加速态势。当然,在液压硫化机得到轮胎厂商认可和广泛使用的同时,我们也不能忽视现有液压硫化机存在的问题。液压式硫化机的优势在于其采用了液压的传动方式,所以要想最大化发挥其优势,提高生产率和设备使用寿命,那么做好硫化机的液压系统维护和保养工作就显得至关重要。本文将就液压硫化机液压系统在日常工作中的常见故障进行分析和解决。 二、液压硫化机液压系统工作原理 2.1 概述 液压硫化机在升降驱动装置、活络模装置、加力装置、中心机构上皆采用液压驱动。整机的液压系统主要由油箱装置、泵机组、冷却装置、过滤装置、阀台以及管路组成。 液压硫化机工作时,升降油缸带动上模沿导向柱上升到位后,装胎机械手抓胎后转进装胎,中心机构的上下环上升,胎胚定位,装胎机械手卸胎后退出,升降油缸带动上模沿导向柱下降合模,胎胚定型后合模到位,在模座下面的加力油缸作用下,产生要求的合模力。合模后,轮胎在硫化室内在加热、加压状态下保持一段时间后,硫化完毕。轮胎硫化结束后,加力油缸卸压,升降油缸带动上模上升,轮胎脱出上模,上模上升到位后,卸胎机构转进卸胎,中心机构上环上升,卸胎手提胎上升到位后转出,将硫化好的轮胎送至后充气冷却。之后如此反复。 2.2 主要元件及功能 液压式轮胎定型硫化机的液压系统图如图1所示。 三、液压硫化机液压系统常见故障与排除 总结国内外各厂家的现场经验,可以发现,液压硫化机液压系统在使用一段时间后经常会出现的问题不外乎这样几种:油液污染,油温过高,漏油,卡阀,爆管,冲击振动等。下面就这几种常见主要故障进行分析,并给出通常的解决办法。 3.1 油液污染 引发原因:(1)残留物污染。液压元件制造、储存、运输、安装和维修过程中带入的沙粒、铁屑、磨料、焊渣、锈片、油垢、棉纱和灰尘等。虽清洗过但可能未清洗干净。(2)侵入物污染。周围环境中的污染物(空气、尘埃水滴等)通过一切可能的侵入点,如外露的往复运动的活塞杆、油箱的进气孔和注油孔等侵入系统。(3)生成物污染。液压系统工作过程中产生的金属微粒,密封材料磨损颗粒、
轮胎硫化方式及步骤
轮胎硫化方式及步骤 工艺技市上Z杖JIL 1硫化方式 1.1过热水硫化 过热水硫化是比较传统的硫化方式,内温由过 热水提供,外温由热板式或蒸鼓式设备提供.采用 蒸鼓式供热,能耗较高,升温也较慢,但受热相对 较均匀.采用热板式供热,外温较稳定且波动小, 但热板不同部位可能受热不同,故热板中的蒸汽走 向设计要科学合理,以使整个热板不同点的温差尽 量小,同时模具和热板的接触面不能有杂质,模具 背面的排气槽要尽量窄,以增大热板和模具的接触 面积,即增大传热面积.此硫化工艺一般用于载重 斜交轮胎和全钢载重子午线轮胎. 1.2高温蒸汽和过热水硫化 高温蒸汽和过热水硫化是目前较多采用的硫 化方式,大部分轿车子午线轮胎采用此硫化工艺. 胶囊在通过热水之前内部温度相对较低,为使胶囊 快速升温,需先在胶囊中充入高温饱和蒸汽(压力 一 般为1.5MPa),一定时问后再充入压力较高的过 热水.此工艺相对较简单,技术也易于得到保障. 1.3全蒸汽硫化 全蒸汽硫化是目前国际上一些大公司普遍采 用的方法,主要用于硫化乘用子午线轮胎和轻载子 午线轮胎.全蒸汽硫化可节省能源且生产效率高, 但技术要求相对较高,须保证高温饱和蒸汽压力稳
定,同时还须解决胶囊上下部分的温差硫化机动力水泄漏,内压偏低造成的轮胎外观瑕疵增多及胶料和部分骨架材料的耐高温性能等问题. 1.4充氮气硫化 充氮气硫化内压可控且稳定,因此可节省能源 和提高轮胎质量,并能延长胶囊的使用寿命.充氮气硫化对设备的要求较高: (1)需购置制氮设备且设备维护成本高; (2)需使用氮气回收装置以降低成本; (3)为防止氮气泄漏,需采用专用阀门和氮 气输送管路; (4)硫化机管路需重新设计和改造,特别是 各阀门的泄漏问题必须解决,以免造成氮气的大量泄漏而对硫化内温造成影响. 2硫化步骤的设定 各轮胎公司采用的硫化步骤不尽相同,但主要 由以下步骤组成: (1)通高温饱和蒸汽; (2)充填水(视情况而定); (3)通过热水; (4)热水回收; 200%年第11期第1]页 MoDERNRUBBER&PLASTICS (5)通冷却水(视情况而定); (6)主排; (7)抽真空; (8)开模. 其中,第3步可采用3种方式:循环,半循环
轮胎定型硫化机复习题及答案
轮胎定型硫化机复习题及答案 1、轮胎定型硫化机按采用的胶囊类型不同可分为哪几种类型? A型(或称AFV型)定型硫化机 B型(或称BOM型)定型硫化机 AB型(或称AUBO型)定型硫化机 RIB型(rolling in bladdet type)定型硫化机 2、轮胎定型硫化机的规格表示方法是? □□——□□/ □×□ LL—B1050/1.37×2, 表示B型定型硫化机,护罩内径为 1050mm,双模,一个模具上的合模力为1.37MN. 3、轮胎定型硫化机的升降机构有几种类型? 曲柄连杆式升降机构 液压式升降机构 螺杆式升降机构 4、轮胎定型硫化机的蒸汽室有几种类型? 1)罐式蒸汽室(普通罐式蒸汽室、带锁环蒸汽室、带调模装置蒸汽室); 2)夹套式蒸汽室(带锁环夹套式蒸汽室、带调模装置夹套式蒸汽室); 3)热板式蒸汽室(普通热板式蒸汽室、带调模装置热板式蒸汽室) 5、B型定型硫化机中心机构主要有哪三部分组成? ①控制胶囊伸直与收缩部分; ②控制胶囊定型高度部分; ③控制轮胎脱离下模部分。 6、B型定型硫化机中心机构按中心机构整体升降的动力不同可分为哪三种? 液压杠杆式、液压式与液压机械式等类型 7、A型定型硫化机中心机构包括哪几部分? ①. 推顶器及夹具板 ②储囊筒及囊筒升降机构 8、使用后充气装置的目的是什么? 保证外胎的质量,而且还可节约2%的尼龙帘布。 9、子午线轮胎定型硫化时,为什么要采用活络模?活络模的优势在哪里? 1)子午线轮胎胎坯成型后的外径大于硫化模花纹的根部直径 2)○1在合模时,活络模块能自动的径向合拢,包住胎坯; ○2卸胎时,活络模块可以径向分离,脱离硫化的轮胎,这样保证胎体和胎冠的完整和硫化质量,有利于装卸轮胎
轮胎硫化胶囊寿命提升措施
轮胎硫化胶囊寿命提升措施 摘要:轮胎硫化所要用到的胶囊,其寿命一直为各轮胎厂家所关注,其不仅与轮胎成品质量、生产成本息息相关,与生产效率关联也较大。从开始更换胶囊算起,到更换后的首灶生产,其所消耗的时间至少在30分钟左右。本文将从胶囊的使用管理(存放条件、作业规范、使用前预处理、硫化介质除氧)及从胶囊规格选型、胶囊花纹等方面采取些措施来简述如何提升胶囊寿命。 关键词:胶囊;胶囊寿命;注射式胶囊;除氧处理; 胶囊为硫化轮胎必用的物料之一,硫化介质通过胶囊提供胎胚硫化时所需的能量及花纹成型的力量,胶囊内的硫化介质为高温高压的过热水或蒸汽,胶囊不停的受到硫化介质的冲击及定型时的拉升,其使用寿命是硫化工程技术人员关注的重点。 我公司硫化所用胶囊全为外厂采购。因胶囊厂家的生产工艺不同造成所生产出来的胶囊缘尺寸也不一样(外缘尺寸、安装尺寸),而这些尺寸的差异性在一定程度上影响胶囊的使用次数及成品轮胎的质量。目前公司胶囊的平均使用次数在为280次左右。 公司硫化工程技术人员经过多次反复试验、实践、研究,通过加强胶囊的使用管理(存放条件、操作工作业规范、预处理、硫化介质除氧)及从规格选型、胶囊花纹等方面采取些措施,有效的提高胶囊使用次数,现硫化胶囊平均使用次数达430次左右。下文对这些措施作以简述。 一、选用加工工艺为注射式的胶囊 当前胶囊生产的加工工艺有两种,一种为模压式,另一种为注射式。模压式胶囊的特点:
选定一台双模硫化机其一边安装注射式胶囊、另一边安装模压式胶囊,硫化胶囊为同一厂家生产,其胶囊配方相同,经过工程技术人员硫化测温试验、胶囊使用次数记录对比,可得出: 1、注射式胶囊较模压式胶囊传热要快,可缩短轮胎生产的硫化时间,从而提高产能、降低能耗,相关数据见表1。 表1 A13#硫化机注射式胶囊与模压式胶囊测温试验数据 2、同时胶囊耐老化性能更优越,使用寿命长,比模压式硫化胶囊使用次数增加160次左右,相关数据见表2。 表2 A13#硫化机注射式硫化胶囊与模压式硫化胶囊使用次数数据 二、选用合适规格的硫化胶囊 胶囊厂家的不同,其胶囊规格尺寸(胶囊断面周长、外直径、夹缘高度等)存在一定差异,如何让胶囊外缘尺寸与成品轮胎规格尺寸、设备工装尺寸的吻合性最优,在胶囊选型时需考虑相关伸张值及胶囊尺寸。其中断面周长伸张值(L)、