手机结构设计高手多年经验小结

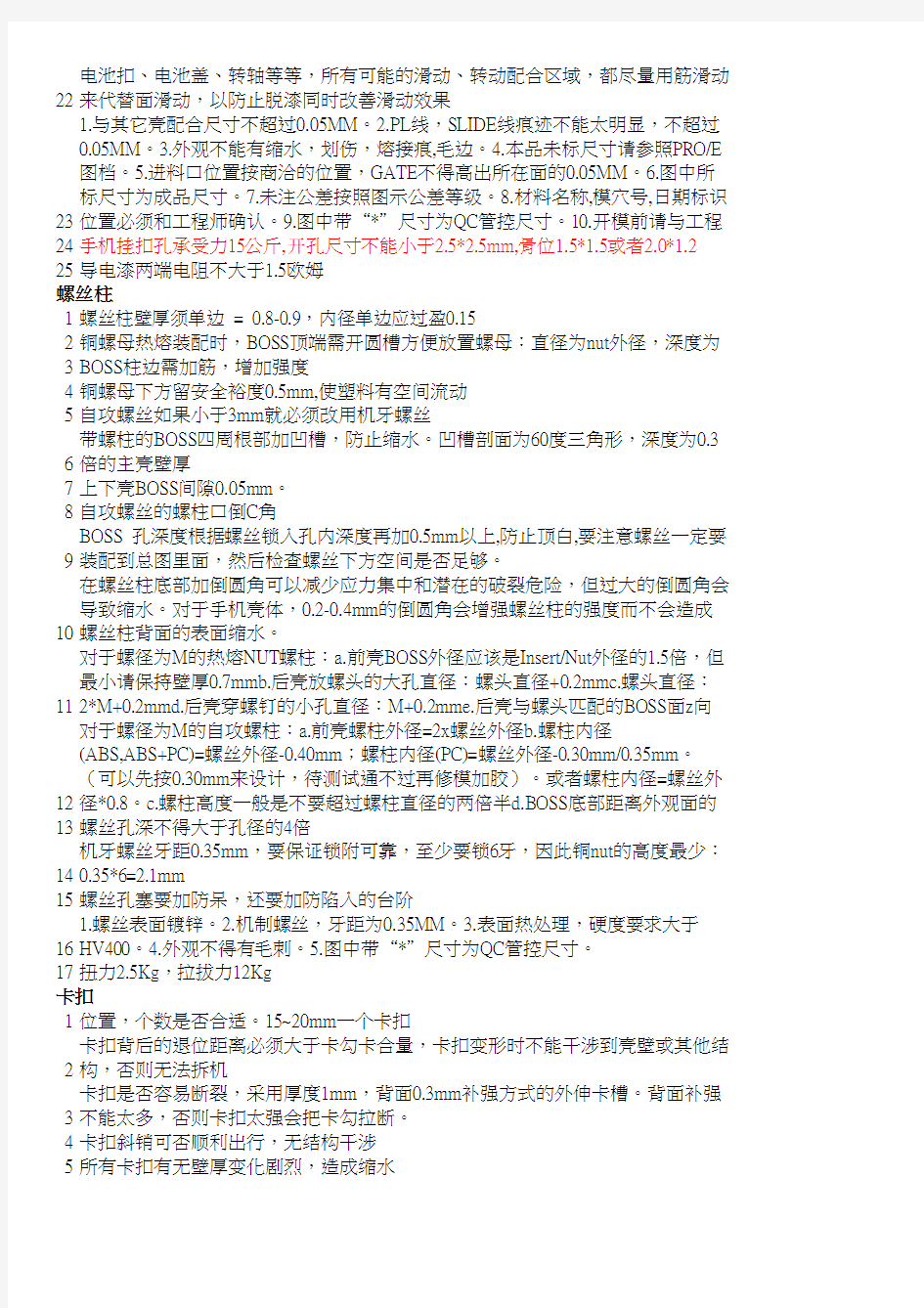
1开始结构设计前,请确认曲面是否已作拔模角或后续能够拔模。尤其要检查是否存在倒拔模。本色件拔模角5度,喷漆件拔模角3度,因为漆可以遮挡可能的外观
2壳体四周每隔15~25mm需要有一个卡扣或者螺丝柱来做固定。如果壳体框架很强,可以放宽标准
3机器四角尽量考虑加螺丝防跌落以及四角缝隙问题。4美工沟防段差,尺寸0.3x0.2或者0.3x0.3。
5尽量加反骨(RIB)防跌落开裂和段差,与壳子间隙0.05~0.1,且远离卡钩,否则机器很难拆。如果因为空间问题加不上反骨,可以把另一个壳子的唇边破开,然后换反骨筋为叉片。
6塑胶材质直板机框架厚度1.5~1.8,尽量不要超过2.0;平面厚度1.2mm。外观面最薄不要小于0.7mm,否则会有明显缩水。非外观的大的平面肉厚0.8,最薄不要小于0.4,并且连续面积不得大于100平方毫米。0.3也能做出来,但要与模厂确认面积
7塑胶材质翻盖机抽壳厚度1.2~1.5。转轴处壁厚:1.2~1.5mm。B、C壳材料选用PC 8B、C壳在转轴处的间隙0.1。注意转轴配合出不能喷漆。
9内部结构台阶处是否都有R角/C角过渡。R角尺寸参考:R角/壁厚=0.25会同时兼顾到比较好的受力性能和注塑结果。R最大不要超过0.5壁厚。
10RIB厚度与壳体壁厚百分比:ABS-60%~70%;ABS&PC-50%~60%。对壳体壁厚低于1mm的RIB,允许80%的肉厚。
11RIB中心距大于2倍壁厚。(壳体开孔的话,孔壁与客体外壁或者孔壁与孔壁之间的间距也是要大于2倍壁厚。)。RIB高度大概为均壁厚3倍。
12滑块退位空间>=8mm。(具体与模具厂check)
13内置电池的电池盖定位、卡合间隙0.07~0.1mm。电池盖厚度>=1.0mm。内置电池的电池盖外观曲面要比后壳外观曲面下沉0.05~0.1mm,防止电池盖段差。
14热融母体上的热融孔要倒C角或者做沉台,当铆钉的作用;同时保证热熔面是平面(参考下面的热熔柱)
15注意按键与壳体的按键框要配合拔模,拔模后z向配合面要是平行的,不能做成v 型的,否则外观看间隙大,而内部却已经干涉。
16均一的壁厚是非常的重要的。厚胶的地方比旁边薄胶的地方冷却得比较慢,并且在相接的地方表面在浇口凝固後出现收缩痕。甚至产生缩水印、热内应力、挠曲部份歪曲、颜色不同或不同透明度。若厚胶的地方渐变成薄胶的是无可避免的话,应尽量设计成渐次的改变,并且在不超过壁厚3:1的比例下。
17对于存在碰穿的位置,碰穿面斜度3~5度,最小3度,否则磨具会碰伤降低寿命
18材料选择方面,如果壳体较薄弱,建议采用PC1414,如果壳体较厚且筋位足够,建议用PC+ABS C1200HF.开模前跟模厂沟通,告诉对方先用PC+ABS的材料,如果强度不够会换成纯PC料,让他们提前考虑磨具尺寸(基本上都不会有问题)。对于翻盖和滑盖机,BC壳都必须用PC料或者更强的玻纤料。
19侧键、耳机孔、USB孔尽量拉开距离,否则卡勾、螺丝等无法放置,且壳体刚性20对于盲孔﹐在挤塑或注射成型时﹐其孔深不得大于孔径的4倍
21手机表面deco用双面胶固定时,必须要增加热熔柱或卡扣,防止做温度冲击和环境试验时,deco局部翘起,尤其是IML件
housing
1. 按化學結構分類a.聚烯烴類--聚乙烯(PE)、聚丙烯(PP)、超高分子量聚乙烯(UHMPE)、聚苯乙烯類 聚苯乙烯(PS)、丙烯晴-苯乙烯(AS)、丙烯晴-丁二烯-苯乙烯共聚體(ABS)b.聚銑胺類--不同的各種尼龍c.聚醚類--聚碳酸酯(PC)、聚甲醛(POM)、聚楓(PSU)
2. 按結晶形態分類結晶性材料 在適當的條件下能產生某几種几何形態晶體結構的塑料(如PE,PP,PA,POM,PBT) . 無定型塑料 分子形狀和分子排列不呈晶體結構而呈無序狀的塑料(如ABS,PC,PSU,PMMA,P S)
3. 按受熱呈現基本行為分類熱塑性塑料 在特定溫度范圍內能反復加熱軟化和冷卻硬化。熱固性塑料 受熱后成為不熔的物質,再次受熱不再具有可塑性。如蜜胺-甲醛樹脂(MF) 尿-甲醛樹脂(UF)及
22电池扣、电池盖、转轴等等,所有可能的滑动、转动配合区域,都尽量用筋滑动来代替面滑动,以防止脱漆同时改善滑动效果
231.与其它壳配合尺寸不超过0.05MM。2.PL线,SLIDE线痕迹不能太明显,不超过0.05MM。3.外观不能有缩水,划伤,熔接痕,毛边。4.本品未标尺寸请参照PRO/E 图档。5.进料口位置按商洽的位置,GATE不得高出所在面的0.05MM。6.图中所标尺寸为成品尺寸。7.未注公差按照图示公差等级。8.材料名称,模穴号,日期标识位置必须和工程师确认。9.图中带“*”尺寸为QC管控尺寸。10.开模前请与工程24手机挂扣孔承受力15公斤,开孔尺寸不能小于2.5*2.5mm,骨位1.5*1.5或者2.0*1.225导电漆两端电阻不大于1.5欧姆
1螺丝柱壁厚须单边 = 0.8-0.9,内径单边应过盈0.15
2铜螺母热熔装配时,BOSS顶端需开圆槽方便放置螺母:直径为nut外径,深度为3BOSS柱边需加筋,增加强度
4铜螺母下方留安全裕度0.5mm,使塑料有空间流动
5自攻螺丝如果小于3mm就必须改用机牙螺丝
6带螺柱的BOSS四周根部加凹槽,防止缩水。凹槽剖面为60度三角形,深度为0.3倍的主壳壁厚
7上下壳BOSS间隙0.05mm。
8自攻螺丝的螺柱口倒C角
9BOSS 孔深度根据螺丝锁入孔内深度再加0.5mm以上,防止顶白,要注意螺丝一定要装配到总图里面,然后检查螺丝下方空间是否足够。
10在螺丝柱底部加倒圆角可以减少应力集中和潜在的破裂危险,但过大的倒圆角会导致缩水。对于手机壳体,0.2-0.4mm的倒圆角会增强螺丝柱的强度而不会造成螺丝柱背面的表面缩水。
11对于螺径为M的热熔NUT螺柱:a.前壳BOSS外径应该是Insert/Nut外径的1.5倍,但最小请保持壁厚0.7mmb.后壳放螺头的大孔直径:螺头直径+0.2mmc.螺头直径:2*M+0.2mmd.后壳穿螺钉的小孔直径:M+0.2mme.后壳与螺头匹配的BOSS面z向12对于螺径为M的自攻螺柱:a.前壳螺柱外径=2x螺丝外径b.螺柱内径
(ABS,ABS+PC)=螺丝外径-0.40mm;螺柱内径(PC)=螺丝外径-0.30mm/0.35mm。(可以先按0.30mm来设计,待测试通不过再修模加胶)。或者螺柱内径=螺丝外径*0.8。c.螺柱高度一般是不要超过螺柱直径的两倍半d.BOSS底部距离外观面的13螺丝孔深不得大于孔径的4倍
14机牙螺丝牙距0.35mm,要保证锁附可靠,至少要锁6牙,因此铜nut的高度最少:0.35*6=2.1mm
15螺丝孔塞要加防呆,还要加防陷入的台阶
161.螺丝表面镀锌。2.机制螺丝,牙距为0.35MM。3.表面热处理,硬度要求大于HV400。4.外观不得有毛刺。5.图中带“*”尺寸为QC管控尺寸。
17扭力2.5Kg,拉拔力12Kg
1位置,个数是否合适。15~20mm一个卡扣
2卡扣背后的退位距离必须大于卡勾卡合量,卡扣变形时不能干涉到壳壁或其他结构,否则无法拆机
3卡扣是否容易断裂,采用厚度1mm,背面0.3mm补强方式的外伸卡槽。背面补强不能太多,否则卡扣太强会把卡勾拉断。
4卡扣斜销可否顺利出行,无结构干涉
5所有卡扣有无壁厚变化剧烈,造成缩水
螺丝柱
卡扣
6卡钩/卡槽有效搭接长度0.4~0.8。太大根本无法拆卸。如果是后壳与其装饰件之间的死扣的话,扣合量可以设计成0.7mm对于活扣视壳体侧壁厚度来定,侧壁厚度大于1.5mm时卡合量取0.4mm;小于1.2mm时取0.55mm,如果卡合不够后续可+以修模加大。卡主板的卡勾,卡合量0.3~0.4mm即可。机器顶部或者底部卡合量可适当加大,在0.5~0.7之间。没有把握时先按小设计,待验证后再加胶。7卡钩/卡槽配合面z向间隙0.05~0.1mm
8卡钩钩子端面距离卡槽匹配面的x向间隙为0.2mm
9卡槽端面距离卡钩匹配面的x向间隙为0.2mm
10如果是卡槽伸出的方式,卡钩处的壁厚要保持0.7以上,防止拆卸的时候外边露11对于卡槽伸出的方式,卡槽尽量做成封闭式,即槽(扣子)靠PCB的内侧加上0.3mm的肉厚将其封住,这对于强度有相当大的帮助。
12如是减胶卡勾(卡槽伸出,卡勾在壳体内壁上),卡勾顶面离分模面距离>0.1,方便火花加工,同时防止漏光
13有卡扣的部件不能电镀,否则卡扣变脆失效
1上下壳静电墙间隙单边 0.05-0.07
2静电墙减胶最薄处留2/3侧壁厚,防止应力痕。需加胶的壳的静电墙壁厚>=0.53嵌合面应有0.5~1°的拔模斜度,端部设倒角或圆角以利装入。
4整机外观应尽量避免孔或者缝隙的存在。有缝隙的地方要确保静电墙连续,防止静电直接爬入。在按键等开孔处也尽量加类似静单墙的档板(按键帽缘),延长静电进入的路程。
5高度〉=0.6mm,保证能挡住ESD,宽度大于等于0.05mm,外部间隙0.05mm,内部鼻孔让位0.8mm
1热熔柱的直径一般是0.8mm以上,壳体上的孔的直径1mm,同时要留出槽以供热熔的时候容胶。热熔件定位需要专门两个孔/柱来配合,间隙0.1mm,其他尽量2热熔柱高出热熔孔0.50MM以上,厂家推荐0.7mm.
3热熔孔需做0.4mm以上深的溢胶沉孔,沉孔直径需比热熔孔单边大0.50MM,以保证能够热熔平整。一般做到直径2.2深0.4以上比较好,可以通过计算容积来设计的4对于小件固定,提倡采用实心柱子热熔固定,实心柱子和对应的孔要相应做1.5度到2度的拔模.对于大件固定或者胶壳肉厚比较薄(比如厚度0.8mm,就不能做0.8mm 的热熔柱了)时,提倡采用内径0.5mm和外径1.5mm的空心柱子或十字骨位或者宽0.5mm,长2.5~3mm的筋热熔固定
5要考虑热熔头的直径,一般直径为2mm,机壳要做出让位
6装饰件时要尽量采用热熔柱和卡勾固定,不能只用背胶固定,高低温测试很难通过,特别是IML件的固定。
7热熔柱热熔后会有0.5mm的突出量,设计时要做好干涉检查,否则实物干涉1雾气 Moisture Streaks
2玻纤分配不均 Glass Fiber Streaks
3困气 Gas Trap Effect
4银丝纹 Sliver Marks
5结合线 Weld Line
6水波痕 Water Wave Effect
7黑点 Dark Sport
8顶出印 Visible Ejector Marks
9变形 Deformation During Demolding
10填充不足 Short Filling
11冷料流痕 Cold Slug
12进胶口点不良 Dull Spots Near The Sprue
塑胶件常见缺陷及造成原因
唇边,止口
热熔柱
13喷射痕 Jetting
14表面起层 Flaking Of The Surface Layer
15浮泡 Entrapped Air
16过热变色 Burnt Streaks
17龟裂 Stress Crack
18缩水痕 Sink Marks
19真空气泡 Density Bubble
20披锋 Flash
21擦伤印 Scratch Marks
1整体设计规则同塑胶料,体强面弱
2由于镁合金模内压力很大,且无弹性变形,因此一般不能走斜顶,可以用后加工
3各部位尺寸比同位置塑胶料正常尺寸减0.2mm基本就可以。最薄只能做到0.5mm,再薄会碎掉。如壳体边框厚1.5mm,LENS贴附面厚0.65mm
4机牙BOSS壁厚可以做0.5mm 50.65mm的厚度最适宜镁件压铸
6相对于塑胶料,镁合金的拔模角要求大一些,最小不能小于0.75度,一般要求2度。一些较高的筋位拔模角最小要3度
7进料口尽可能的多
8补强肋的方向尽量与流动方向一致。如补强肋的方向与流动方向垂直时,可考虑增加一些帮助流动的肉厚(模内流道)以改变流动方向,事后再以后加工方式铣
9为增加补强肋的强度及充填性,根部倒R0.5之圆角,如有成品的配合干涉问题,最好仍有R0.2以上之圆角
1盲孔/槽的深度尽量不要超过孔径/槽宽的一半。否则无法保证外观。可与厂家
2尽量不要电镀有金属嵌件的部件。由于膨胀系数不同,电镀液会对衔接部位产生不良影响
3需要有外观要求的电镀面,不要存在尖角。要加上0.2~0.3的圆角来避免电镀堆积。造型上一定要要求方的地方,也要在一切角和棱的地方倒圆角R=0.2~0.3 mm。不要有过深的凹部,不能有过细的孔和盲孔直径不能太小,这些部位不仅电镀困难,而且容易残存溶液污染下道工序的溶液。像旋钮和按钮不可避免的盲孔,应
4电镀件肉厚,手机外观部件要求1.2mm以上的厚度。对于短的且剖面是T字或十字结构的小部件,最薄处厚度与部件总长度比例大概是1:25,同时要保证最薄处厚度宽度比1:1左右。如果比例适当且结构筋做得恰当,局部厚度做到0.4mm
5如果有电镀要求,则材料中PC的含量不能大于30%,因为加PC后对电镀的附着力有影响。
6要避免采用大面的平面,尽量采用表面弧面或表面装饰。
7厚度的突变容易造成应力集中,一般来说厚度差不应超过两倍。8文字击起的高度以0。3-0。5为宜,斜度65度。
9电镀会使部件的外观瑕疵表现的非常明显,因此需要电镀的部件务必考虑好外观质量,在开模的时候分模线不要设定在分型处,而是要沿着装配面往壳体内部方向跑0.4mm左右,或者整个跑进去,这样装配后分模线就被其他壳子压住看不到
镁合金压铸件电镀技术