SMT锡膏过炉后产生锡珠原因分析
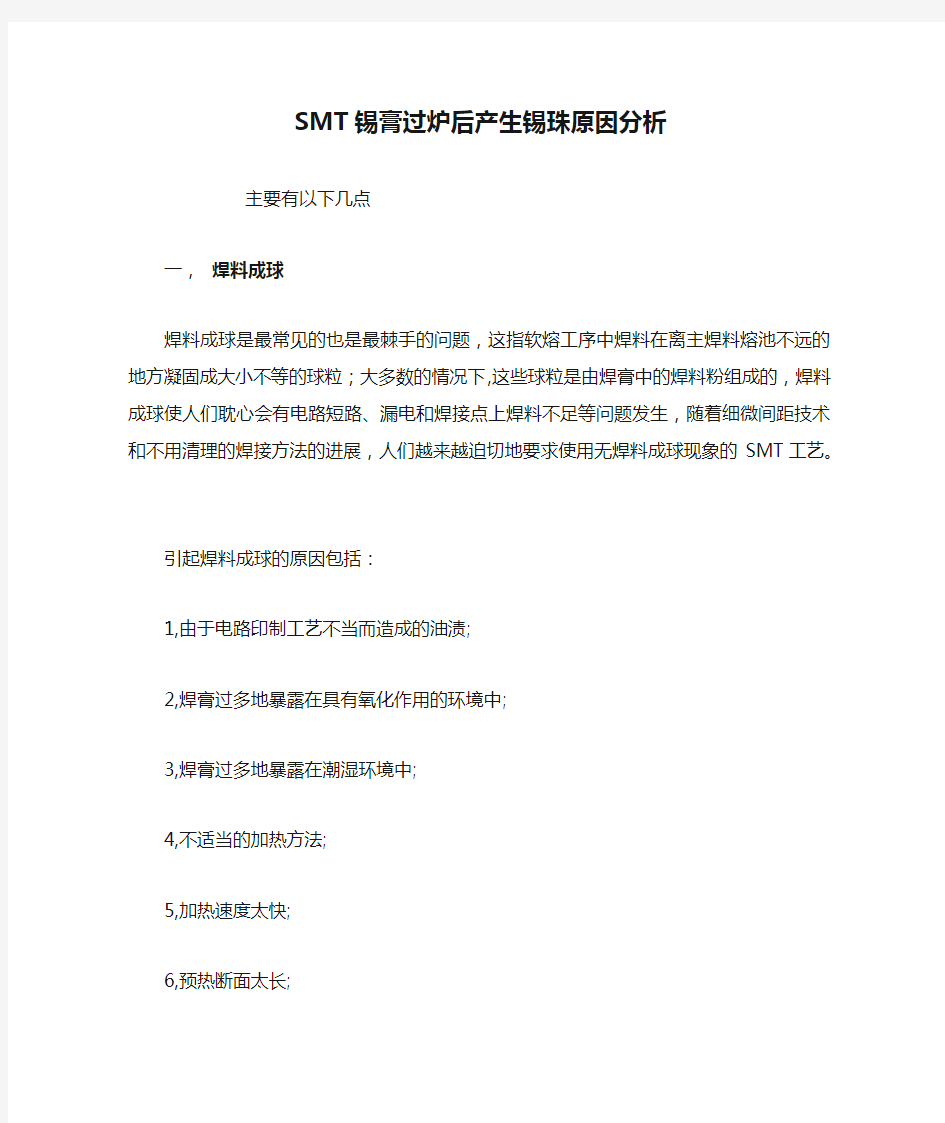
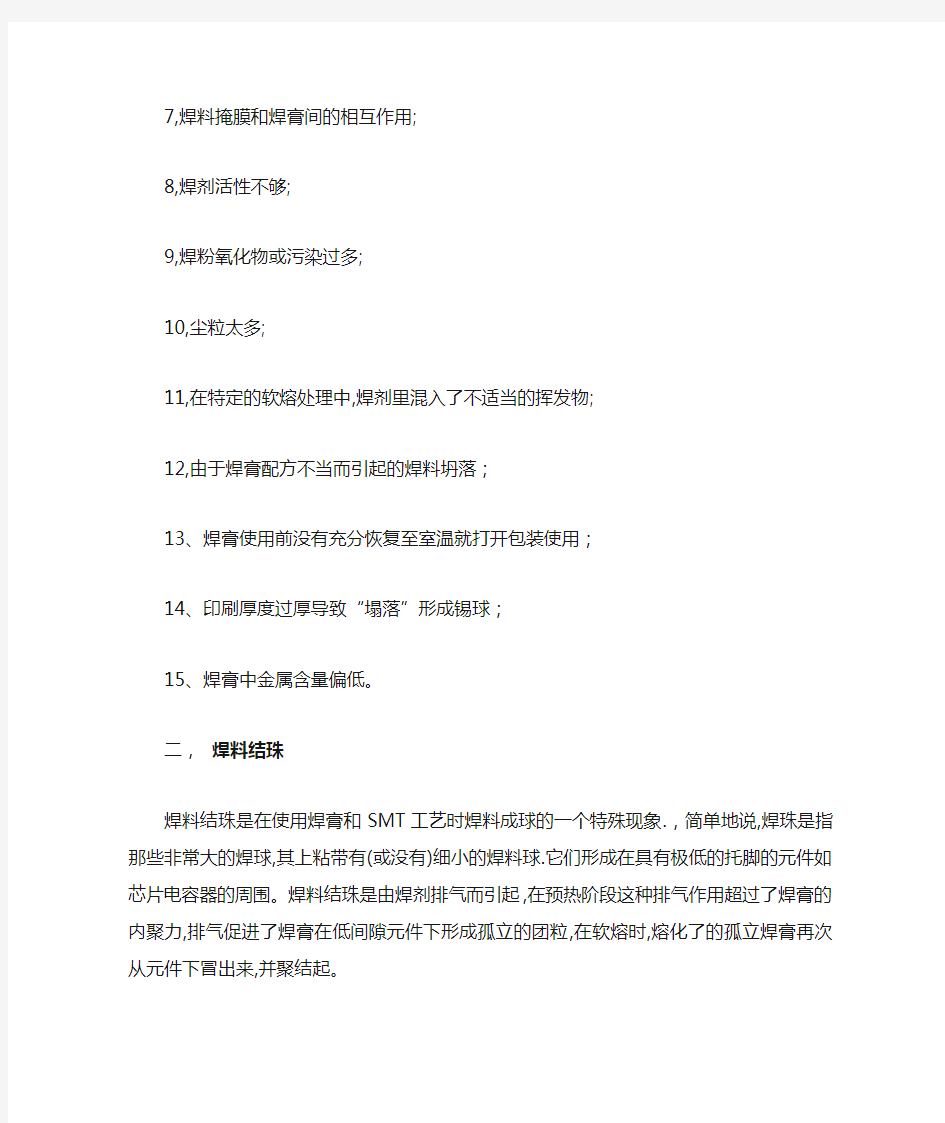
SMT锡膏过炉后产生锡珠原因分析
主要有以下几点
一,焊料成球
焊料成球是最常见的也是最棘手的问题,这指软熔工序中焊料在离主焊料熔池不远的地方凝固成大小不等的球粒;大多数的情况下,这些球粒是由焊膏中的焊料粉组成的,焊料成球使人们耽心会有电路短路、漏电和焊接点上焊料不足等问题发生,随着细微间距技术和不用清理的焊接方法的进展,人们越来越迫切地要求使用无焊料成球现象的SMT工艺。
引起焊料成球的原因包括:
1,由于电路印制工艺不当而造成的油渍;
2,焊膏过多地暴露在具有氧化作用的环境中;
3,焊膏过多地暴露在潮湿环境中;
4,不适当的加热方法;
5,加热速度太快;
6,预热断面太长;
7,焊料掩膜和焊膏间的相互作用;
8,焊剂活性不够;
9,焊粉氧化物或污染过多;
10,尘粒太多;
11,在特定的软熔处理中,焊剂里混入了不适当的挥发物;
12,由于焊膏配方不当而引起的焊料坍落;
13、焊膏使用前没有充分恢复至室温就打开包装使用;
14、印刷厚度过厚导致“塌落”形成锡球;
15、焊膏中金属含量偏低。
二,焊料结珠
焊料结珠是在使用焊膏和SMT工艺时焊料成球的一个特殊现象.,简单地说,焊珠是指那些非常大的焊球,其上粘带有(或没有)细小的焊料球.它们形成在具有极低的托脚的元件如芯片电容器的周围。焊料结珠是由焊剂排气而引起,在预热阶段这种排气作用超过了焊膏的内聚力,排气促进了焊膏在低间隙元件下形成孤立的团粒,在软熔时,熔化了的孤立焊膏再次从元件下冒出来,并聚结起。 焊接结珠的原因包括:
1,印刷电路的厚度太高;
2,焊点和元件重叠太多;
3,在元件下涂了过多的锡膏;
4,安置元件的压力太大;
5,预热时温度上升速度太快;
6,预热温度太高
7,在湿气从元件和阻焊料中释放出来;
8,焊剂的活性太高;
9,所用的粉料太细;
10,金属负荷太低;
11,焊膏坍落太多;
12,焊粉氧化物太多;
13,溶剂蒸气压不足。
消除焊料结珠的最简易的方法也许是改变模版孔隙形状,以使在低托脚元件和焊点之间夹有较少的焊膏。 回流焊接中出的锡球,常常藏于矩形片式元件两端之间的侧面或细距引脚之间。在元件贴装过程中,焊膏被置于片式元件的引脚与焊盘之间,随着印制板穿过回流焊炉,焊膏熔化变成液体,如果与焊盘和器件引脚等润湿不良,液态焊锡会因收缩而使焊缝填充不充分,所有焊料颗粒不能聚合成一个焊点。部分液态焊锡会从焊缝流出,形成锡球。因此,焊锡与焊盘和器件引脚润湿性差是导致锡球形成的根本原因。
三,原因分析与控制方法
造成焊锡润湿性差的原因很多,以下主要分析与相关工艺有关的原因及解决措施:
1,回流温度曲线设置不当。焊膏的回流是温度与时间的函数,如果未到达足够的温度或时间,焊膏就不会回流。预热区温度上升速度过快,达到平顶温度的时间过短,使焊膏内部的水分、溶剂未完全挥发出来,到达回流焊温区时,引起水分、溶剂沸腾,溅出焊锡球。实践证明,将预热区温度的上升速度控制在1~4°C/s是较理想的。
2,如果总在同一位置上出现焊球,就有必要检查金属板设计结构。模板开口尺寸腐蚀精度达不到要求,对于焊盘大小偏大,以及表面材质较软(如铜模板),造成漏印焊膏的外形轮廓不清晰,互相桥连,这种情况多出现在对细间距器件的焊盘漏印时,回流焊后必然造成引脚间大量锡珠的产生。因此,应针对焊盘图形的不同形状和中心距,选择适宜的模板材料及模板制作工艺来保证焊膏印刷质量。
3,如果在贴片至回流焊的时间过长,则因焊膏中焊料粒子的氧化,焊剂变质、活性降低,会导致焊膏不回流,焊球则会产生。选用工作寿命长一些的焊膏(我们认为至少4小时),则会减轻这种影响。
4,另外,焊膏印错的印制板清洗不充分,使焊膏残留于印制板表面及通孔中。
回流焊之前,被贴放的元器件重新对准、贴放,使漏印焊膏变形。这些也是造成焊球的原因。因此应加强操作者和工艺人员在生产过程的责任心,严格遵照工艺要求和操作规程行生产,加强工艺过程的质量控制
SMT产生锡珠的原因及对策
在表面着装技术精密发达的时代中,常常发生扰人的问题,其中以在零件部品旁,所发生小锡珠为最常见。
本篇就探讨其发生原因与解决对策,提供使用人在制程上参考。
1.如图a.锡膏在印刷后,零件部品在植装时,置件压力过强,锡膏因此产生挤压。当进入回焊炉加热时,部品零件温度上升通常比基板来得快,而零件部品下方温
度上升较慢。接着,零件部品的导体(极体)与锡膏接触地方,Flux因温度上升黏
度降低,又因部品零件导体上方温度较高而爬升靠近。所以锡膏是由温度最高
Pad外侧开始溶融。
2.如图b.溶融焊锡开始向零件部品的导体处往上爬,溶融焊锡形成像墙壁一般,
接着未溶融焊锡中Flux动向,因溶融焊锡而阻断停止流动,所以Flux无法向外流。当然所产生挥发溶剂(GAS)也因溶融焊锡而阻断包覆。
3.如图c.锡膏的溶融方向是向Pad的内部进行,Flux也向内部挤压,(GAS)也向内侧移动。零件部品a.点的下方因力量而使溶融焊锡到达b.点,又因吃锡不良a.点停止下降,产生c.力量逆流,a.b.c.d.的力量,使得焊锡移动。
?零件部品氧化,在导体侧面吃锡是有界线的如图c.所示,结果反而焊锡受压析出形成锡珠。
?另一方面Pad温度较快上升,在Pad上的溶融焊锡先产生回塑效果,无法拉引零件部品,此时的力量使得未溶融焊锡受压析出溶融而形成小锡珠。
?锡膏内Flux易析出气泡,Flux流动力量加上挥发型溶剂的挥发,再加上零件部品在Pad上拉引的力量同时使得未溶融焊锡受挤压析出溶融而形成
锡珠。
?锡膏量过多或Pad面积太小,溶融焊锡所保有空间过小也易形成锡珠。
对策
零件部品旁发生锡珠的原因很多,需检讨与修正。
1.在设计上Pad的温度,能均匀上升,考虑受热平衡,来决定Pad大小及导体
长宽。
2.在设计上考虑锡高的量,零件部品的高度与Pad面积,使得溶融焊锡保有
舒展空间。
3.温度曲线不可急遽上升。
4.印刷精度及印刷量的控制,与印刷时的管理。
锡珠的解决方案和分析
锡珠的解决方案和分析 焊锡珠现象是表面贴装过程中的主要缺陷之一,它的产生是一个复杂的过程,也是最烦人的问题,要完全消除它,是非常困难的。 焊锡珠的直径大致在0.2mm~0.4mm之间,也有超过此范围的,主要集中在片式阻容元件的周围。焊锡珠的存在,不仅影响了电子产品的外观,也对产品的质量埋下了隐患。原因是现代化印制板元件密度高,间距小,焊锡珠在使用时可能脱落,从而造成元件短路,影响电子产品的质量。因此,很有必要弄清它产生的原因,并对它进行有效的控制,显得尤为重要了。一般来说,焊锡珠的产生原因是多方面,综合的。焊膏的印刷厚度、焊膏的组成及氧化度、模板的制作及开口、焊膏是否吸收了水分、元件贴装压力、元器件及焊盘的可焊性、再流焊温度的设置、外界环境的影响都可能是焊锡珠产生的原因。 下面我就从各方面来分焊锡珠产生的原因及解决方法。 焊膏的选用直接影响到焊接质量。焊膏中金属的含量、焊膏的氧化度,焊膏中合金焊料粉的粒度及焊膏印刷到印制板上的厚度都能影响焊珠的产生。 A、焊膏的金属含量。焊膏中金属含量其质量比约为88%~92%,体积比约为50%。当金属含量增加时,焊膏的黏度增加,就能有效地抵抗预热过程中汽化产生的力。另外,金属含量的增加,使金属粉末排列紧密,使其在熔化时更容结合而不被吹散。此外,金属含量的增加也可能减小焊膏印刷后的″塌落″,因此,不易产生焊锡珠。 B、焊膏的金属氧化度。在焊膏中,金属氧化度越高在焊接时金属粉末结合阻力越大,焊膏与焊盘及元件之间就越不浸润,从而导致可焊性降低。实验表明:焊锡珠的发生率与金属粉末的氧化度成正比。一般的,焊膏中的焊料氧化度应控制在0.05%以下,最大极限为0.15%。 C、焊膏中金属粉末的粒度。焊膏中粉末的粒度越小,焊膏的总体表面积就越大,从而导致较细粉末的氧化度较高,因而焊锡珠现象加剧。我们的实验表明:选用较细颗粒度的焊膏时,更容易产生焊锡粉。 D、焊膏在印制板上的印刷厚度。焊膏印刷后的厚度是漏板印刷的一个重要参数,通常在0.12mm-2.0mm之间。焊膏过厚会造成焊膏的″塌落″,促进焊锡珠的产生。 E、焊膏中助焊剂的量及焊剂的活性。焊剂量太多,会造成焊膏的局部塌落,从而使焊锡珠容易产生。另外,焊剂的活性小时,焊剂的去氧化能力弱,从而也容易产生锡珠。免清洗焊膏的活性较松香型和水溶型焊膏要低,因此就更有可能产生焊锡珠。 F、此外,焊膏在使用前,一般冷藏在冰箱中,取出来以后应该使其恢复到室温后打开使用,否则,焊膏容易吸收水分,在再流焊锡飞溅而产生焊锡珠。 2、模板的制作及开口。我们一般根据印制板上的焊盘来制作模板,所以模板的开口就是焊盘的大小。在印刷焊膏时,容易把焊膏印刷到阻焊层上,从而在再流焊时产生焊锡珠。因此,我们可以这样来制作模板,把模板的开口比焊盘的实际尺寸减小10%,另外,可以更改开口的外形来达到理想的效果。上图是几种推荐的焊盘设计: 模板的厚度决了焊膏的印刷厚度,所以适当地减小模板的厚度也可以明显改善焊锡珠现象。我们曾经进行过这样的实验:起先使用0.18mm厚的模板,再流焊后发现阻容元件旁边的焊锡珠比较严重,后来,重新制作了一张模板,厚度改为0.15mm,开口形式为上面图中的前一种设计,再流焊基本上消除了焊锡珠。 件贴装压力及元器件的可焊性。如果在贴装时压力太高,焊膏就容易被挤压到元件下面的阻焊层上,在再流焊时焊锡熔化跑到元件的周围形成焊锡珠。解决方法可以减小贴装时的压力,并采用上面推荐使用的模板开口形式,避免焊膏被挤压到焊盘外边去。另外,元件和焊盘焊性也有直接影响,如果元件和焊盘的氧化度严重,也会造成焊锡珠的产生。经过热风整平的焊盘在焊膏印刷后,改变了焊锡与焊剂的比例,使焊剂的比例降低,焊盘越小,比例失调越严重,这也是产生焊锡珠的一个原因。 再流焊温度的设置。焊锡珠是在印制板通过再流焊时产生的,再流焊可分为四个阶段:预热、保温、再流、冷却。在预热阶段使焊膏和元件及焊盘的温度上升到120C-150C之间,减小元器件在再流时的热冲击,在这个阶段,焊膏中的焊剂开始汽化,从而可能使小颗粒金属分开跑到元件的底下,在再流
怎样消除pcb中的锡珠
消除PCB中的錫珠 本文介紹,一種U形模板開孔確定的錫膏沈澱可以防止錫珠的形成。 焊錫由各種金屬合金組成。由印刷電路板(PCB)裝配商使用的錫/鉛合金(Sn63/Pb37)是錫膏和用於波峰焊接的錫條或錫線的典型粉末。在PCB上不是設計所需的位置所找到的焊錫包括錫塵(solder fine)、錫球(solder ball)和錫珠(solder bead)。錫塵是細小的,尺寸接近原始錫膏粉末。對於-325~+500的網目尺寸,粉末直徑是25-45微米,或者大約0.0010-0.0018"。錫塵是由顆粒的聚結而形成的,所以大於原始的粉末尺寸。 錫珠(solder beading)是述語,用來區分一種對片狀元件獨特的錫球(solder balling)(圖一)。錫珠是在錫膏塌落(slump)或在處理期間壓出焊盤時發生的。在回流期間,錫膏從主要的沈澱孤立出來,與來自其他焊盤的多餘錫膏集結,或者從元件身體的側面冒出形成大的錫珠,或者留在元件的下面。 圖一、錫珠 IPC-A-610 C將0.13mm(0.00512")直徑的錫球或每600mm2(0.9in2)面積上少於五顆分爲第一類可接受的,並作爲第二與第三類的工藝標記2。IPC-A-610 C允許“夾陷的”不干擾最小電氣間隙的錫球。可是,即使是“夾陷的”錫球都可能在運輸、處理或在一個振動應用的最終使用中變成移動的。 錫球已經困擾表面貼裝工業許多年。對於只表面貼裝和混合技術的PCB,錫珠在許多技術應用中都遇到。查明相互影響和除掉錫珠的原因可以改善合格率、提供品質、提高長期的可靠性、和降低返工與修理成本。 錫珠的原因 人們已經將錫珠歸咎於各種原因,包括模板(stencil)開孔的設計、錫膏的成分、阻焊層的選擇、模板清潔度、定位、錫膏的重印、焊盤的過分腐蝕、貼片壓力、回流溫度曲線、波峰焊錫的飛濺、和波峰焊錫的二次回流。3-5
“波峰焊”过程中出现“锡珠”的原因及预防控制办法
“波峰焊”过程中出现“锡珠”的原因及预防控制办法 在“波峰焊”工艺过程中,“锡珠”的产生有两种状况:一种是在板子刚接触到锡液时,因为助焊剂或板材本身的水份过多或高沸点溶剂没有充分挥发,遇到温度较高的锡液时骤然挥发,较大的温差致使液态焊锡飞溅出去,形成细小锡珠;另一种情况是在线路板离开液态焊锡的时候,当线路板与锡波分离时,线路板顺着管脚延伸的方向会拉出锡柱,在助焊剂的润湿作用及锡液自身流动性的作用下,多余的焊锡会落回锡缸中,因此而溅起的焊锡有时会落在线路板上,从而形成“锡珠”。 因此,我们可以看到,在“波峰焊”防控“锡珠”方面,我们应该从两个大的方面着手,一方面是助焊剂等原材料的选择,另一方面是波峰焊的工艺控制。 (一)助焊剂方面的原因分析及预防控制办法 1、助焊剂中的水份含量较大或超标,在经过预热时未能充分挥发; 2、助焊剂中有高沸点物质或不易挥发物,经预热时不能充分挥发; 这两种原因是助焊剂本身“质量”问题所引起的,在实际焊接工艺中,可以通过“提高预热温度或放慢走板速度等来解决”。除此之外,在选用助焊剂前应针对供商所提供样品进行实际工艺的确认,并记录试用时的标准工艺,在没有“锡珠”出现的情况下,审核供应商所提供的其他说明资料,在以后的收货及验收过程中,应核对供应商最初的说明资料。 (二)工艺方面的原因分析及预防控制办法 1,预热温度偏低,助焊剂中溶剂部分未完全挥发; 2,走板速度太快未达到预热效果; 3,链条(或PCB板面)倾角过小,锡液与焊接面接触时中间有气泡,气泡爆裂后产生锡珠; 4,助焊剂涂布的量太大,多余助焊剂未能完全流走或风刀没有将多余焊剂吹下; 这四种不良原因的出现,都和标准化工艺的确定有关,在实际生产过程中,应该严格按照已经订好的作业指导文件进行各项参数的校正,对已经设定好的参数,不能随意改动,相关参数及所涉及技术层面主要有以下几点: (1),关于预热:一般设定在90-110摄氏度,这里所讲“温度”是指预热后PCB板焊接面的实际受热温度,而不是“表显”温度;如果预热温度达不到要求,则焊后易产生锡珠。 (2),关于走板速度:一般情况下,建议客户把走板速度定在1.1-1.4米/分钟,但这不是绝对值;如果要改变走板速度,通常都应以改变预热温度作配合;比如:要将走板速度加快,那么为了保证PCB焊接面的预热温度能够达到预定值,就应当把预热温度适当提高;如果预热温度不变,走板速度过快时,焊剂有可能挥发不完全,从而在焊接时产生“锡珠”。 (3),关于链条(或PCB板面)的倾角:这一倾角指的是链条(或PCB
产生“锡珠”的原因分析及措施
产生“锡珠”的原因分析及措施 从“缩减制程、节约成本、减少污染”等角度出发,越来越多的电子焊接采用焊后“免清洗”工艺。但是如果焊后板面有“锡珠”出现,则不可能达到“免清洗”的要求,因此“锡珠”的预防与控制在实施“免清洗”过程中就显得格外重要。“锡珠”的出现不仅影响板级产品外观,更为严重的是由于印制板上元件密集,在使用过程中它有可能造成短路等状况,从而影响产品的可靠性。 综合整个电子焊接情况,可能出现“锡珠”的工艺制程包括:“SMT表面贴装”焊接制程、“波峰焊”制程及“手工焊”制程,我们从这三个方面来一一探讨“锡珠”出现的原因及预防控制的办法。因为“波峰焊”及“手工焊”已推行多年,很多方面都已经比较成熟,因此,本文用了较多的篇幅介绍“SMT表面贴装”焊接制程中产生“锡珠”原因及防控措施。 一,关于的“锡珠”形态及标准 一些行业标准对“锡珠”问题进行了阐释。主要有MIL-STD-2000标准中的“不允许有锡珠”,而IPC-A-610C标准中的“每平方英寸少于5个”。在IPC-A-610C 标准中,规定最小绝缘间隙0.13毫米,直径在此之内的锡珠被认为是合格的;而直径大于或等于0.13毫米的锡珠是不合格的,制造商必须采取纠正措施,避免这种现象的发生。为无铅焊接制订的最新版IPCA- 610D标准没有对锡珠现象做更清楚的规定,有关每平方英寸少于5个锡珠的规定已经被删除。有关汽车和军用产品的标准则不允许出现任何“锡珠”,所用线路板在焊接后必须被清洗,或将锡珠手工去除。 常见的锡珠形态及其尺寸照片见下图: 二,“SMT表面贴装”制程“锡珠”出现的原因及预防控制办法 在“SMT表面贴装”焊接制程中,回流焊的“温度、时间、焊膏的质量、印刷厚度、钢网(模板)的制作、装贴压力”等因素都有可能造成“锡珠”的产生。因此,找到“锡珠”可能出现的原因,并加以预防与控制就是达成板面无“锡珠”的关键之所在。
无铅焊接产生锡珠原因
原因:1.烙铁温度过高,焊料升温过快,造成助焊剂的溶剂“沸腾”而炸锡; 2.焊锡丝本身的质量原因。 其实焊锡丝都存在锡珠飞溅的现象,尤其是现在的无铅锡丝。只是不同牌子或型号的锡丝的飞溅现象程度不一样。目前飞溅现象最小的锡丝应该是日本的ALMIT ,但是价格很贵,都是客户指定要用的,如CASIO ,MATSUSHITA ,IBM ,SHARP。不过现在很多日系的企业用一种机器在焊锡丝上开一个V型槽,这样助焊剂就可以和空气接触,而不会膨胀而不会产生爆锡的现象,但开槽后的锡丝要在很短的时间里用掉,否则助焊剂会失效。目前用SONY ,MATSUSHITA ,RICOH 都在用这种机器。是日本的叫BONKOTE 維修無鉛SMD元件 1)修理普通元件如0603,0805,3216的元件,電烙鉄溫度的範圍:350℃±50℃。 2)修理IC,電烙鉄溫度的範圍:350℃±50℃ 3)修理含有金屬材料的元件或元件接觸面積較大散熱較快的物料,電烙鉄溫度範圍: 380℃±50℃。 4.4維修無鉛THD元件 1)修理普通元件如1/4W.1/2W的電阻,小三極管,小容量內壓低的電容,IC,二極管等小元件電烙鉄溫度的範圍:340℃±50℃。 2)修理含有金屬材料的元件如散熱器,內壓高容量大的電解電容,高壓二極管,火牛等較大的物料,電烙鉄溫度的範圍:380℃±50℃。 3)修理含有塑膠皮的連接線,烙鉄溫度的範圍:350℃±50℃。 使用手工焊接时,烙铁的温度及焊接时间是多少?怎么控制?有无相关的标准? ?D#D蔲?n 睠3市 Z1c;??? 貼 這要看所焊的零件種類及面積, 同時要考慮焊接方法 !H g炒媖葏 如果是一般小電阻電容類, 就我過去的經驗如果用的 ?0腳f籗? 是30w左右的烙鐵, 溫度可設在約370度c應該足夠, 焊接時間約2-3秒且用較細的錫絲(0.8mm以下), 但是如果 @雵E?輛a 焊接面積大就應該用較大瓦特數(功率)如40w或更高, z%磕申 U? 有些超大焊接面積甚致用到60w, 而錫絲尺寸也隨著 ?檊靎?x? 焊接面積加大而加粗溫度可設在約400度c, 烙鐵焊接 9鑹?xUm? 除了溫度高低外還要考慮熱傳導量, 另外焊接方式方面癆n嚌?敿 傳統上很多人習慣先對錫絲加溫再加熱焊點的方法, "KM?叭繤 最好改為先對焊點加熱1-2秒後再加錫絲以避免錫絲內 ? ?FM诎 助焊劑加溫過久而焦化
锡珠产生的原因分析
焊锡珠产生的原因及解决方法 摘要:焊锡珠(SOLDER BALL)现象是表面贴装(SMT)过程中的主要缺陷,主要发生在片式阻容元件(CHIP)的周围,由诸多因素引起。本文通过对可能产生焊锡珠的各种原因的分析,提出相应的解决法。 焊锡珠现象是表面贴装过程中的主要缺陷之一,它的产生是一个复杂的过程,也是最烦人的问题,要完全消除它,是非常困难的。 焊锡珠的直径大致在0.2mm~0.4mm之间,也有超过此范围的,主要集中在片式阻容元件的周围。焊锡珠的存在,不仅影响了电子产品的外观,也对产品的质量埋下了隐患。原因是现代化印制板元件密度高,间距小,焊锡珠在使用时可能脱落,从而造成元件短路,影响电子产品的质量。因此,很有必要弄清它产生的原因,并对它进行有效的控制,显得尤为重要了。 一般来说,焊锡珠的产生原因是多方面,综合的。焊膏的印刷厚度、焊膏的组成及氧化度、模板的制作及开口、焊膏是否吸收了水分、元件贴装压力、元器件及焊盘的可焊性、再流焊温度的设置、外界环境的影响都可能是焊锡珠产生的原因。 下面我就从各方面来分焊锡珠产生的原因及解决方法。 1、焊膏的选用直接影响到焊接质量。焊膏中金属的含量、焊膏的氧化度,焊膏中合金焊料粉的粒度及焊膏印刷到印制板上的厚度都能影响焊珠的产生。 A、焊膏的金属含量。焊膏中金属含量其质量比约为88%~92%,体积比约为50%。当金属含量增加时,焊膏的黏度增加,就能有效地抵抗预热过程中汽化产生的力。另外,金属含量的增加,使金属粉末排列紧密,使其在熔化时更容结合而不被吹散。此外,金属含量的增加也可能减小焊膏印刷后的“塌落”,因此,不易产生焊锡珠。 B、焊膏的金属氧化度。在焊膏中,金属氧化度越高在焊接时金属粉末结合阻力越大,焊膏与焊盘及元件之间就越不浸润,从而导致可焊性降低。实验表明:焊锡珠的发生率与金属粉末的氧化度成正比。一般的,焊膏中的焊料氧化度应控制在0.05%以下,最大极限为0.15%。 C、焊膏中金属粉末的粒度。焊膏中粉末的粒度越小,焊膏的总体表面积就越大,从而导致较细粉末的氧化度较高,因而焊锡珠现象加剧。我们的实验表明:选用较细颗粒度的焊膏时,更容易产生焊锡粉。 D、焊膏在印制板上的印刷厚度。焊膏印刷后的厚度是漏板印刷的一个重要参数,通常在0.12mm-20mm之间。焊膏过厚会造成焊膏的“塌落”,促进焊锡珠的产生。 E、焊膏中助焊剂的量及焊剂的活性。焊剂量太多,会造成焊膏的局部塌落,从而使焊锡珠容易产生。另外,焊剂的活性小时,焊剂的去氧化能力弱,从而也容易产生锡珠。免清洗焊膏的活性较松香型和水溶型焊膏要低,因此就更有可能产生焊锡珠。
锡珠解决方法
几种SMT焊接缺陷及其解决措施 2002-5-30 13:48:54 阅读427次 双击鼠标自动滚屏,单击停止 1 引言 表面组装技术在减小电子产品体积重量和提高可靠性方面的突出优点,迎合了未来战略武器洲际射程、机动发射、安全可靠、技术先进的特点对制造技术的要求。但是,要制定和选择适合于具体产品的表面组装工艺不是简单的事情,因为SMT 技术是涉及了多项技术的复杂的系统工程,其中任何一项因素的改变均会影响电子产品的焊接质量。 元器件焊点的焊接质量是直接影响印制电路组件(PWA)乃至整机质量的关键因素。它受许多参数的影响,如焊膏、基板、元器件可焊性、丝印、贴装精度以及焊接工艺等。我们在进行SMT工艺研究和生产中,深知合理的表面组装工艺技术在控制和提高SMT生产质量中起到至关重要的作作。本文就针对所遇到的几种典型焊接缺陷产生机理进行分析,并提出相应的工艺方法来解决。 2 几种典型焊接缺陷及解决措施 2.1 波峰焊和回流焊中的锡球 锡球的存在表明工艺不完全正确,而且电子产品存在短路的危险,因此需要排除。国际上对锡球存在认可标准是:印制电路组件在600范围内不能出现超过5个锡球。产生锡球的原因有多种,需要找到问题根源。 2.1.1 波峰焊中的锡球 波峰焊中常常出现锡球,主要原因有两方面:第一,由于焊接印制板时,印制板上的通孔附近的水分受热而变成蒸汽。如果孔壁金属镀层较薄或有空隙,水汽就会通过孔壁排除,如果孔内有焊料,当焊料凝固时水汽就会在焊料内产生空隙(针眼),或挤出焊料在印制板正面产生锡球。第二,在印制板反面(即接触波峰的一面)产生的锡球是由于波峰焊接中一些工艺参数设置不当而造成的。如果助焊剂涂覆量增加或预热温度设置过低,就可能影响焊剂内组成成分的蒸发,在印制板进入波峰时,多余的焊剂受高温蒸发,将焊料从锡槽中溅出来,在印制板面上产生不规则的焊料球。 针对上述两面原因,我们采取以下相应的解决措施:第一,通孔内适当厚度的金属镀层是很关键的,孔壁上的铜镀层最小应为25um,而且无空隙。第二,使用喷雾或发泡式涂覆助焊剂。发泡方式中,在调节助焊剂的空气含量时,应保持尽可能产生最小的气泡,泡沫与PCB接触面相对减小。第三,波峰焊机预热区温度的设置应使线路板顶面的温度达到至少100°C。适当的预热温度不仅可消除焊料球,而且避免线路板受到热冲击而变形。 2.1.2 回流焊中的锡球 2.1.2.1 回流焊中锡球形成的机理
锡珠产生的原因及处理
因素一:锡膏的选用直接影响到焊接的质量 锡膏中的金属含量、金属粉末的氧化度、金属粉末的大小都能影响锡珠的产生。 a. 锡膏的金属含量 锡膏中的金属含量其质量比约为88%~92%,体积比约为50%。当金属含量增加时,锡膏的粘度增加,能有效的抵抗预热过程中汽化产生的力。金属含量的增加,使金属粉末排列紧密,使其在熔化时更容易结合而不被吹散。此外金属含量的增加也可能减小锡膏印刷后的“坍塌”,因此,不易产生焊锡珠。 b. 锡膏的金属粉末的氧化度 锡膏中的金属粉末氧化度越高,在焊接时金属粉末结合阻力越大,锡膏与焊盘及元件之间就不容易浸润,从而导致可焊性降低。实验证明:锡珠的发生率与金属粉末的氧化度成正比。一般,锡膏中的焊料氧化度控制在0.05%以下,最大极限为0.15% c. 锡膏中金属粉末的大小 锡膏中金属粉末的粒度越小,锡膏的总体表面积就越大,从而导致较细粉末的氧化度较高,因而焊锡珠的现象加剧。实验证明:选用较细颗粒的锡膏时,更容易产生锡珠。 d. 锡膏中助焊剂的量及焊剂的活性 焊剂量太多,会造成锡膏的局部坍塌,从而使锡珠容易产生。另外焊剂的活性太弱时,去除氧化的能力就弱,也更容易产生锡珠。 e. 其它注意事项 锡膏从冰箱中取出后没有经过回温就打开使用,致锡膏吸收水分,在预热时锡膏飞溅而产生锡珠;PCB受潮、室内湿度太重、有风对着锡膏吹、锡膏添加了过量的稀释剂、机器搅拌时间过长等等都会促进锡珠的产生。 因素二、钢网的制作及开口 a. 钢网的开口 我们一般依照焊盘的大小来开钢网,在印刷锡膏时,容易把锡膏印刷到阻焊层上,从而在回流焊时产生锡珠。因此,我们这样来开钢网,把钢网的开口比焊盘的实际尺寸小10%,另外可以更改开口的形状来达到理想效果。 b. 钢网的厚度 钢网百度一般在0.12~0.17mm之间,过厚会造成锡膏的“坍塌”,从而产生锡珠。 因素三、贴片机的贴装压力 如果贴装时压力太高,锡膏就容易被挤压到元件下面的阻焊层上,在回流焊接时锡膏熔化跑到元件的周围形成锡珠。解决方法:减小贴装压力;采用合适的钢网开孔形式,避免锡膏被挤压到焊盘外边去。 因素四、炉温曲线的设置 锡珠是在过回流焊时产生的。在预热阶段,使锡膏、PCB及元器件的温度上升到120~150℃之间,必须减少元器件在回流时的热冲击,这个阶段,锡膏中的焊剂开始汽化,从而使小颗粒的金属粉末分开跑到元件的底下,在加流时跑到元件周围形成锡珠。在这一阶段,温度上升不能太快,一般应小于 2.5℃/S,过快容易造成焊锡飞溅,形成锡珠。所以应该调整回流焊的预热温度和预热速度来控制锡珠的产生
焊锡珠产生的原因及解决方法
焊錫珠産生的原因及解決方法焊錫珠産生的原因及解決方法 摘要: 焊錫珠(SOLDER BALL)現象是表面貼裝(SMT)過程㆗的主要缺陷,主要發生 在片式阻容元件(CHIP)的周圍,由諸多因素引起。本文通過對可能産生焊錫珠的各種原因的分析,提出相應的解決方法。 焊錫珠現象是表面貼裝過程㆗的主要缺陷之㆒,它的産生是㆒個複雜的過程,也是最煩㆟的問題,要完全消除它,是非常困難的。 焊錫珠的直徑大致在0.2mm〜0.4mm 之間,也有超過此範圍的,主要集㆗在片式阻容元件的周圍。焊錫珠的存在,不僅影響了電子産品的外觀,也對産品的質量埋㆘了隱患。原因是現代化印製板元件密度高,間距小,焊錫珠在使用時可能脫落,從而造成元件短路,影響電子産品的質量。因此,很有必要弄清它産生的原因,並對它進行有效的控制,顯得尤爲重要了。 ㆒般來說,焊錫珠的産生原因是多方面,綜合的。焊膏的印刷厚度、焊膏的組成及氧化度、模板的製作及開口、焊膏是否吸收了水分、元件貼裝壓力、元器件及焊盤的可焊性、再流焊溫度的設置、外界環境的影響都可能是焊錫珠産生的原因。 ㆘面我就從各方面來分焊錫珠産生的原因及解決方法。 1、焊膏的選用直接影響到焊接質量。焊膏㆗金屬的含量、焊膏的氧化度,焊膏㆗合金焊料粉的粒度及焊膏印刷到印製板㆖的厚度都能影響焊珠的産生。 A、焊膏的金屬含量。焊膏㆗金屬含量其質量比約爲88%〜92%,體積比約爲50%。當金屬含量增加時,焊膏的黏度增加,就能有效㆞抵抗預熱過程㆗汽化産生的力另外,金屬含量的增加,使金屬粉末排列緊密,使其在熔化時更容結合而不被吹散。此外,金屬含量的增加也可能減小焊膏印刷後的“塌落”,因此,不易産生焊錫珠。 B、焊膏的金屬氧化度。在焊膏㆗,金屬氧化度越高在焊接時金屬粉末結合阻力越大,焊膏與焊盤及元件之間就越不浸潤,從而導致可焊性降低。實驗表明:焊錫珠的發生率與金屬粉末的氧化度成正比。㆒般的,焊膏㆗的焊料氧化度應控制在0.05%以㆘,最大極限爲 0.15%。 C、焊膏㆗金屬粉末的粒度。焊膏㆗粉末的粒度越小,焊膏的總體表面積就越大,從而導致較細粉末的氧化度較高,因而焊錫珠現象加劇。我們的實驗表明:選用較細顆粒度的焊膏時,
产生锡珠的原因分析及措施
产生“锡珠”的原因分析及措施 从缩减制程、节约成本、减少污染”等角度出发,越来越多的电子焊接采用焊后免清洗”工艺。但是如果焊后板面有锡珠”出现,则不可能达到免清洗” 的要求,因此锡珠”的预防与控制在实施免清洗”过程中就显得格外重要。锡珠” 的出现不仅影响板级产品外观,更为严重的是由于印制板上元件密集,在使用过程中它有可能造成短路等状况,从而影响产品的可靠性。 综合整个电子焊接情况,可能出现锡珠”的工艺制程包括:“ SMT表面贴装” 焊接制程、波峰焊”制程及手工焊”制程,我们从这三个方面来一一探讨锡珠” 出现的原因及预防控制的办法。因为波峰焊”及手工焊”已推行多年,很多方面都已经比较成熟,因此,本文用了较多的篇幅介绍“SMT S面贴装”焊接制程中 产生锡珠”原因及防控措施。 一,关于的锡珠”形态及标准 一些行业标准对锡珠”问题进行了阐释。主要有MIL-STD-2000标准中的不允许有锡珠”,而IPC-A-610C标准中的每平方英寸少于5个”。在IPC-A-610C 标准中,规定最小绝缘间隙0.13毫米,直径在此之内的锡珠被认为是合格的;而直径大于或等于0.13毫米的锡珠是不合格的,制造商必须采取纠正措施,避免这种现象的发生。为无铅焊接制订的最新版IPCA- 610D标准没有对锡珠现象做更清楚的规定,有关每平方英寸少于5个锡珠的规定已经被删除。有关汽车和军用产品的标准则不允许出现任何锡珠”,所用线路板在焊接后必须被清洗,或 将锡珠手工去除。 常见的锡珠形态及其尺寸照片见下图: 二, “SMT S面贴装制程锡珠”出现的原因及预防控制办法 在“SM S面贴装”焊接制程中,回流焊的温度、时间、焊膏的质量、印刷厚度、钢网(模板)的制作、装贴压力”等因素都有可能造成锡珠”的产生。因此,找到锡珠”可能出现的原因,并加以预防与控制就是达成板面无锡珠”的关键之所在。
浅谈SMT锡珠产生原因和预防
SMT锡珠产生原因与预防 在SMT技术高速发展的今天,产品的制造日趋朝着小型化、集成化发展。但直到今日,SMT 制造中常常会发生一些扰人的问题。其在贴装元件旁边,发生小锡珠问题较为常见。 本篇就锡珠的产生和解决对策,提出探讨建议。 一、元件旁边产生锡珠的原因 1、如图描述: 锡膏在印刷, 元件贴装时, 贴装压力过强, 锡膏因此产生挤压。当进入回焊炉加热时, 元件温度上升通常比PCB板快, 而元件下方温度上升较慢。接着, 元件的焊接端与锡膏接触,Flux 因温度上升黏度降低, 又因元件导体上方温度较高而爬升靠近。所以锡膏是由温度最高焊盘外侧开始溶融。 1、如图描述:
溶融焊锡开始从元件焊接端向上延伸, 形成焊点, 接着未溶融焊锡中Flux 动向, 因溶融 焊锡而阻断停止流动, 所以Flux 无法向外流。所产生挥发溶剂(GAS) 也因溶融焊锡而阻 断包覆。 3、如图描述: 锡膏的溶融方向朝焊盘的内部进行,Flux 也向内部挤压,(GAS) 也向内侧移动。元件a.点的下方因Flux的移动力量而使溶融焊锡到达b. 点,又因吃锡不良a. 点停止下降, 产生c.点力量逆流。而产生焊锡被挤出,产生锡珠。 二改善对策 1、焊盘设计需考虑焊接过程中温度的均匀上升,确保温度平衡。在此基础上决定焊盘的大小和尺寸。 同时需要考虑元件的高度与焊盘的面积匹配, 使得溶融焊锡保有舒展空间。 2、焊接回流温度曲线不可急剧上升。 3、印刷精度及印刷量的控制, 与印刷时的管理。防止锡膏印刷偏移或下锡不良。(多锡、形状塌陷) 4、贴装元件压力调整。避免元件将锡膏挤压变形。 5、元件本身质量,避免氧化回潮。 (摘自SMT之家论坛)
波峰焊时如何防止锡珠的产生
波峰焊时如何防止锡珠的产生 线路板在进行波峰焊接后,焊接面上会出现锡珠。而下述的线路板组装技术的发展趋势将使这种焊接缺陷越来越成为一个严重的问题: 线路板上元器件和IC引脚之间的间距越来越小,使得线路板更容易因为锡珠产生短路 焊接面上越来越多的贴片元件致使更多地使用托盘在波峰焊上进行选择性焊接 由于无铅焊料的使用,焊接温度更高 波峰焊更多地使用氮气氛以减少锡渣并改善工艺窗口 过去,大部分锡珠会在焊接后清洗线路板时被洗掉,而随着免清洗焊膏的使用,不再需要清洗过程,锡珠问题就不可避免了。 对于许多电子控制系统,如汽车上的安全气囊和其他汽车电子系统,锡珠的出现(可能会造成短路)会影响驾驶安全。 锡珠的形成原因 锡珠是在线路板离开液态焊锡的时候形成的。当线路板与锡波分离时,线路板会拉出锡柱,锡柱断裂落回锡缸时,溅起的焊锡会在落在线路板上形成锡珠。因此,在设计锡波发生器和锡缸时,应注意减少锡的降落高度。小的降落高度有助于减少锡渣和溅锡现象。 氮气的使用会加剧锡珠的形成。氮气氛能防止焊锡表面形成氧化层,增加了锡珠形成的概率,同时,氮气也会影响焊锡的表面张力。 锡珠形成的第二个原因是线路板材和阻焊层内挥发物质的释气。如果线路板通孔的金属层上有裂缝的话,这些物质加热后挥发的气体就会从裂缝中逸出,在线路板的元件面形成锡珠。 锡珠形成的第三个原因与助焊剂有关。助焊剂会残留在元器件的下面或是线路板和搬运器(选择性焊接使用的托盘)之间。如果助焊剂没能被充分预热并在线路板接触到锡波之前烧尽,就会产生溅锡并形成锡珠。因此,应该严格遵循助焊剂供应商推荐的预热参数。
阻焊层 锡珠是否会粘附在线路板上取决于基板材料。如果锡珠和线路板的粘附力小于锡珠的重力,锡珠就会从就会从线路板上弹开落回锡缸中。 在这种情况下,线路板上的阻焊层是个非常重要的因素。比较粗燥(rough)的阻焊层会和锡珠有更小的接触面,锡珠不易粘在线路板上。在无铅焊接过程中,高温会使阻焊层更柔滑(softer),更易造成锡珠粘在线路板上。 行业标准及规定 一些行业标准对锡珠进行了阐释。分类从MIL-STD-2000标准中的不允许有锡珠,到IPC-A-610C标准中的每平方英寸少于5个。 在IPC-A-610C标准中,规定最小绝缘间隙0.13毫米,直径在此之内的锡珠被认为是合格的;而直径大于或等于0.13毫米的锡珠是不合格的,制造商必须采取纠正措施,避免这种现象的发生。为无铅焊接制订的最新版IPCA-610D标准没有对锡珠现象做清楚的规定。有关每平方英寸少于5个锡珠的规定已经被删除。但有关汽车和军用产品的标准则不允许出现任何锡珠,所以线路板在焊接后必须被清洗,或将锡珠手工去除。 防止锡珠的产生
SMT各种缺陷产生的原因和对策
SMT各种缺陷产生的原因和对策 一、锡珠 摘要:锡珠(SOLDER BALL)现象是表面贴装过程中的主要缺陷,主要发生在片式阻容元件(CHIP)的周围,由诸多因素引起,本文通fg过对可能产生锡珠的各种原因的分析,提出相应的解决方法。 锡珠现象是表面贴装过程中的主要缺陷之一,它的产生是一个复杂的过程,也是最烦人的问题,要完全消除它,是非常困难的。 锡珠的直径大致在0.2mm~0.4mm之间,也有超出范围的,主要集中在片式阻容的周围,锡珠的存在不仅影响了电子产品的外观,也对产品的质量埋下了隐患。原因是现代化印刷板元件密度高,间距小,锡珠在使用时可能脱落从而造成元件短路,影响电子产品的质量,因而,很有必要弄清楚它产生的原因,并对它进行有效有控制,显得尤为重要了。 一般来说,锡珠的产生是多方面的,综合的,焊锡的印刷厚度,焊锡的组成及氧化度,模板的制作及开口,焊锡是否吸收了水份,元件贴装压力,元件器及焊盘的可焊性,再流焊温度的设置,外界环境的影响都有可能是锡珠产生的原因。 下面我就从各方面来分析锡珠产生的原因及解决办法。 焊锡的选用直接影响到焊接质量。焊锡中金属的含量、焊锡的氧化度。焊锡中合金焊料粉的粘度及焊锡印刷到印制板上的厚度都能影响锡珠的产生。 焊锡中的金属含量。焊锡中的金属含量其质量比约为88%~92%,体积比约为50%,当金属含量增加时,焊锡的粘度增加,就能有效地抵制预热过程中汽化产生的力,另外,金属含量的增加,使金属粉未排列紧密,使其在熔化时更容结合而不被吹散.此外,金属含量的增加也可能减小焊锡印刷后的”塌落”,因此,不易产生锡珠. B:焊锡的金属氧化度.在焊锡中,金属氧化度越高在焊接时金属结合的阻力越大,焊锡与焊盘及元件之间就越不浸润.从而导致可焊性降低,实验表明:锡珠的发生率与金属粉未的氧化度成正比.一般的,焊锡中的焊料氧化度应控制在0.05%以下,最大极限为0.15% C:焊锡中金属粉未的粒度,焊锡中粉未的粒度越小,焊锡的总表面积就越大,从而导致较细的粉未氧化度较高,因而焊钢珠现象加剧。我们的实验表明:选用较细颗粒的焊锡时,更容易产生锡珠
表面贴装过程锡珠产生原因和消除方法
表面贴装过程锡珠产生的原因和消除的方法 江门市新会区允中电子有限公司 黄华均 【内容摘要】锡珠现象是表面贴装(SMT )过程中常见的缺陷,主要是由哪些原因引起,又有哪些相应的解决方法?本文试图结合笔者在生产过程中的实践谈谈自己的看法。 【关 键 词】锡珠 锡膏 再流焊 钢网 贴片压力 操作 可焊性 锡珠是指散布在元件电极的连接部周围的不规则的焊料小球。在表面贴装过程中,我们常会遇见锡珠现象,锡珠的直径一般在0.1mm ~0.4mm 之间,主要集中在片式阻容器件的周围,有时也会散落在板面的其它部位。它是表面贴装过程中的主要缺陷之一,不仅影响产品的外观,还会给产品的性能带来隐患。因为在使用过程中,锡珠会随时滚落到间距小的元件脚上面而造成短路,影响产品的质量。因此,必须弄清产生锡珠的原因,并切实加以控制和消除。 一般来说,锡珠产生的原因是多种多样的。如锡膏的质量、再流焊炉的参数设置、钢网的制作、贴片的压力、元件和焊盘的可焊性以及员工的操作等因素影响都有可能引起锡珠的产生。下面,就笔者个人的实践经验,针对各种可能的影响因素,浅谈一些体会: 一、锡膏 若锡珠无飞溅,且呈蜂窝状(如图1), 甚至锡珠细小到需要在显微镜下才能观察到, 则有可能是锡膏不良引起。锡膏的金属含量、 氧化度、颗粒大小、助焊剂含量等都是影响锡 珠产生的因素。 1、锡膏的金属含量足够高时,粘度和粉 末排列的紧密程度会足以抵抗预热过程中汽 化产生的力,熔化时也不易被吹至塌落,能有效防止锡珠的产生。 2、锡膏的合金粉末被严重氧化,再流焊过程中会通过表面张力的作用形成锡珠。氧化程度越高,合金粉末的结合阻力会越大,焊盘及元件之间的可焊性会越差,有研究表明:锡膏中的合金粉末氧化度应控制在0.05%以下,最大极限为0.15%。 3、锡膏中直径在10μm 以下的小颗粒锡粉过多,会使锡珠在再流焊升温时随助焊剂流淌到焊盘之外。同时,由于锡膏的总的表面积增大,也会增大氧化度,从而加剧锡珠的产生。 图1
SMT不良产生原因及解决办法
Surface mount technology(SMT)不良产生原因及对策 零件反向 产生的原因:1:人工手贴贴反 2:来料有个别反向 3;机器FEEDER坏或FEEDER振动过大(导致物料反向)振动飞达 4:PCB板上标示不清楚(导致作业员难以判断) 5:机器程式角度错 6:作业员上料反向(IC之类) 7:核对首件人员粗心,不能及时发现问题 8:炉后QC也未能及时发现问题 对策:1:对作业员进行培训,使其可以正确的辨别元器件方向 2:对来料加强检测 3:维修FEEDER及调整振动FEEDER的振动力度(并要求作业员对此物料进行方向检查) 4:在生产当中要是遇到难以判断元器件方向的。一定要等工程部确定之后才可以批量生产,也可以SKIP 5:工程人员要认真核对生产程式,并要求对首件进行全检(特别要注意有极性的元件) 6:作业员每次换料之后要求IPQC核对物料(包括元件的方向)并要求作业员每2小时必须核对一次物料 7:核对首件人员一定要细心,最好是2个或以上的人员进行核对。(如果有专门的IPQC的话也可以要求每2小时再做一次首件) 8:QC检查时一定要用放大镜认真检查(对元件数量多的板尽量使用套版) 少件(缺件) 产生的原因:1:印刷机印刷偏位 2:钢网孔被杂物或其它东西给堵塞(焊盘没锡而导致飞件) 3:锡膏放置时间太久(元器件不上锡而导致元件飞件) 4:机器Z轴高度异常 5:机器NOZZLE上有残留的锡膏或胶水(此时机器每次都可以识别但物料放不下来导致少件) 6:机器气压过低(机器在识别元件之后气压低导致物料掉下) 7:置件后零件被NOZZLE吹气吹开 8:机器NOZZLE型号用错 9:PCB板的弯曲度已超标(贴片后元件弹掉) 10:元件厚度差异过大 11:机器零件参数设置错误 12:FEEDER中心位置偏移 13:机器贴装时未顶顶针 14:炉前总检碰撞掉落
锡珠---解析---最新
錫珠解析 所涉及的相關詞彙: 1、SMT:表面贴装技术(贴片) 2、锡珠(solder beads):焊料球形成在阻容元件腰部的不良现象 3、钢版(Stencil):用来印刷(涂布)焊料的模版 4、回流焊(Reflow):热量以对流形式来加热零部件的炉子 5、锡膏(Solder Paste):一种金属粉末悬浮于焊接溶剂中的膏状体 6、温度曲线(Profile):用来监测零部件受热过程的走势图 7、焊盘(PA D):电路板线路与零件引脚焊接的金属盘片 8、PCB :印刷电路版 9、粘度(Viscosity):锡膏的流变性质,单位是CP 或Pa. S(稀,干) 一般都有10%-20%的误差(黏度:反應和揮發) 锡膏黏度是根据不同的厂商不同的产品而有不同的黏度值.锡膏的黏度一般取决于锡膏所采取的flux 的成分和含量, 锡膏的黏度单位可以采用pa.s (帕斯卡.秒)或者是poise (实际常用为centipoise,cp或者是kcp),它们的换算关系为1pa.s等于1 kcp,测试工具常见的有japan的malcom和美国的brookfield。IPC的标准为IPC-TM-650 ,一般的锡膏黏度值为600~1400 kcp,200~300pa.s 10、粘性(Tackiness):粘着零件能力的大小(象胶水), 单位是gm(克) IPC-A-610C标准中的“每平方英寸少于5个”。在IPC-A-610C标准中,规定最小绝缘间隙0.13毫米,直径在此之内的锡珠被认为是合格的;而直径大于或等于0.13毫米的锡珠是不合格的,制造商必须采取纠正措施,避免这种现象的发生。为无铅焊接制订的最新版IPCA- 610D标准没有对锡珠现象做更清楚的规定,有关每平方英寸少于5个锡珠的规定已经被删除。有关汽车和军用产品的标准则不允许出现任何“锡珠”,所用线路板在焊接后必须被清洗,或将锡珠手工去除。 焊锡珠现象是表面贴装生产中主要缺陷之一,主要集中出现在片状阻容元件的某一侧面,不仅影响板级产品的外观,更为严重的是由于印刷板上元件密集,在使用过程中它会造成短路现象,从而影响电子产品的质量。因此弄清它产生的原因,并力求对其进行最有效的控制就显得犹为重要了。
锡珠的产生原因与解决措施
波峰焊接中溅锡珠的形成原因 ⑴ “小爆炸”理论 波峰焊接中在 PCB 的焊接面及元件面上均可能产生锡珠飞溅现象。普遍认为在 PCB 进入波峰之前有水汽滞留在PCB上的话,一旦与波峰钎料接触,在剧烈升温的过程中,就会在极短的时间内迅速汽化变成蒸汽,发生爆发性的排气过程。正是这种剧烈的排气可能引发正处在熔融状态中的焊接点内部的小爆炸,从而促使钎料颗粒在脱离波峰时飞溅在PCB上形成锡珠。 在波峰焊接前PCB水汽的来源,杭州东方通信公司对此进行过专题研究和试验,归纳的结论如下: ① 制造环境和PCB存放时间 制造环境对电子装联的焊接质量有着很大的影响。制造环境的湿度较重,或PCB包装开封较长时间后再进行贴片和波峰焊生产,或者PCB贴片、插装后放置一段时间后再进行波峰焊,这些因素都很有可能使PCB在波峰焊接过程中产生锡珠。 如果制造环境的湿度太大,在产品制造过程中空气浮动着水汽很容易会在PCB表面凝结,使PCB通孔中凝结有水珠,在过波峰焊时,通孔中的水珠经过预热温区后可能还没有完全挥发完,这些没有挥发完的水珠接触到波峰的焊锡时,经受了高温,就会在短时间内汽化变成蒸汽,而此时正是形成焊点的时候,水汽就会在焊料内产生空
隙,或挤出焊料产生锡球。严重的话就会形成一个爆点,并在它的周围分布有被吹开的细小的锡珠。 假如PCB在包装开封较长时间后再进行贴片和波峰焊,通孔中也会凝结有水珠;PCB完成贴片后或插装完成后放置了一段时间,也会凝结水珠。同样的原因,这些水珠都有可能在波峰焊过程中导致锡珠产生。 因而,作为从事电子装联的企业,对制造环境的要求和对产品制造过程中的时间安排显得特别地重要。贴片完成后的PCB应在24小时内完成插装并进行波峰焊,假如天气晴朗干燥,可以在48小时内完成。 ② PCB阻焊材料和制作质量 在PCB制造过程中所使用的阻焊膜也是波峰焊产生锡球的 原因之一。因为阻焊膜与助焊剂有一定的亲合性,阻焊膜加工不良常常会引起锡珠粘附,产生焊锡球。 PCB的制造质量不好也会在波峰焊时产生锡球。如果PCB通孔的孔壁镀层较薄或者镀层中有空隙,PCB通孔附着的水分受热变成蒸汽,水汽就会通过孔壁排出,遇到焊料就会产生锡球。因而在通孔内有造当的镀层厚度是很关键的,孔壁上的镀层厚度最小应为25μm。 PCB通孔中有污垢或不干净物质时,在过波峰焊的时候,喷入通孔中的助焊剂不能得到充分的挥发,液体助焊剂和水汽一样,在遇到波峰时也产生锡珠。
SMT锡膏过炉后产生锡珠原因分析
SMT锡膏过炉后产生锡珠原因分析 主要有以下几点 一,焊料成球 焊料成球是最常见的也是最棘手的问题,这指软熔工序中焊料在离主焊料熔池不远的地方凝固成大小不等的球粒;大多数的情况下,这些球粒是由焊膏中的焊料粉组成的,焊料成球使人们耽心会有电路短路、漏电和焊接点上焊料不足等问题发生,随着细微间距技术和不用清理的焊接方法的进展,人们越来越迫切地要求使用无焊料成球现象的SMT工艺。 引起焊料成球的原因包括: 1,由于电路印制工艺不当而造成的油渍; 2,焊膏过多地暴露在具有氧化作用的环境中; 3,焊膏过多地暴露在潮湿环境中; 4,不适当的加热方法; 5,加热速度太快; 6,预热断面太长; 7,焊料掩膜和焊膏间的相互作用; 8,焊剂活性不够; 9,焊粉氧化物或污染过多; 10,尘粒太多; 11,在特定的软熔处理中,焊剂里混入了不适当的挥发物; 12,由于焊膏配方不当而引起的焊料坍落; 13、焊膏使用前没有充分恢复至室温就打开包装使用; 14、印刷厚度过厚导致“塌落”形成锡球; 15、焊膏中金属含量偏低。 二,焊料结珠 焊料结珠是在使用焊膏和SMT工艺时焊料成球的一个特殊现象.,简单地说,焊珠是指那些非常大的焊球,其上粘带有(或没有)细小的焊料球.它们形成在具有极低的托脚的元件如芯片电容器的周围。焊料结珠是由焊剂排气而引起,在预热阶段这种排气作用超过了焊膏的内聚力,排气促进了焊膏在低间隙元件下形成孤立的团粒,在软熔时,熔化了的孤立焊膏再次从元件下冒出来,并聚结起。 焊接结珠的原因包括: 1,印刷电路的厚度太高; 2,焊点和元件重叠太多; 3,在元件下涂了过多的锡膏; 4,安置元件的压力太大; 5,预热时温度上升速度太快; 6,预热温度太高 7,在湿气从元件和阻焊料中释放出来; 8,焊剂的活性太高; 9,所用的粉料太细; 10,金属负荷太低;
回流焊产生锡珠的原因及解决方案
回流焊产生锡珠的原因及解决方案 在SMT生产工艺里面,经常会碰到经过回流焊过出来的板有锡珠,锡珠的产生,让产品的质量没有保证,让外观看起来不光滑。那产生锡珠的主要原因是什么,我们又如何去解决它,这就是我今天写这篇文章的目的。产生锡珠的主要原因是锡膏的问题。详细分析请看下面分析。 焊锡珠现象是表面贴装生产中主要缺陷之一,它的直径约为0.2-0.4mm,主要集中出现在片状阻容元件的某一侧面,不仅影响板级产品的外观,更为严重的是由于印刷板上元件密集,在使用过程中它会造成短路现象,从而影响电子产品的质量。因此弄清它产生的原因,并力求对其进行最有效的控制就显得犹为重要了。 焊锡珠产生的原因是多种因素造成的,在回流焊中的温度时间,焊膏的印刷厚度,焊膏的组成成分,模板的制作,贴片机贴装压力,外界环境都会在生产过程中各个环节对焊锡珠形成产生影响。 焊锡珠是在负责制板通过回流焊炉时产生的。回流焊曲线可以分为四个阶段,分别为:预热、保温、回流和冷却。预热阶段的主要目的是为了使印制板和上面的表贴元件升温到120-150度之间,这样可以除去焊膏中易挥发的溶剂,减少对元件的热振动。因此,在这一过程中焊膏内部会发生气化现象,这时如果焊膏中金属粉末之间的粘结力小于气化产生的力,就会有少量焊膏从焊盘上流离开,有的则躲到片状阻容元件下面,再流焊阶段,温度接近曲线的峰值时,这部分焊膏也会熔化,而后从片状阻容元件下面挤出,形成焊锡珠,由它的形成过程可见,预热温度越高,预热速度越快,就会加大气化现象中飞溅,也就越容易形成锡珠。因此,我们可以采取较适中的预热温度和预热速度来控制焊锡珠的形成。 焊膏的选用也影响着焊接质量,焊膏中金属的含量,回流焊焊膏的氧化物含量,焊膏中金属粉末的粒度,及焊膏在印制板上的印刷厚度都不同程度影响着焊锡珠的形成。 1:焊膏中的金属含量:焊膏中金属含量的质量比约为90-91%,体积比约为50%左右。当金属含量增加时,焊膏的粘度增加,就能更有效地抵抗预热过程中气化产生的力。另外,金属含量的增加,使金属粉末排列紧密,使其有更多机会结合而不易在气化时被吹散。金属含量的增加也可以减小焊膏印刷后的塌落趋势,因此不易形成焊锡珠。 .2:焊膏中氧化物的含量:焊膏中氧化物含量也影响着焊接效果,氧化物含量越高,金属粉末熔化后结合过程中所受阻力就越大,回流焊再流焊阶段,金属粉末表面氧化物的含量还会增高,这就不利?quot;润湿"而导致锡珠产生。 3:焊膏中金属粉末的粒度,焊膏中的金属粉末是极细小的球状,直径约为20-75um,在贴装细间距和超细间距的元件时,宜用金属粉末粒度较小的焊膏,约在20-45um之间,焊