磨削加工的特点是什么
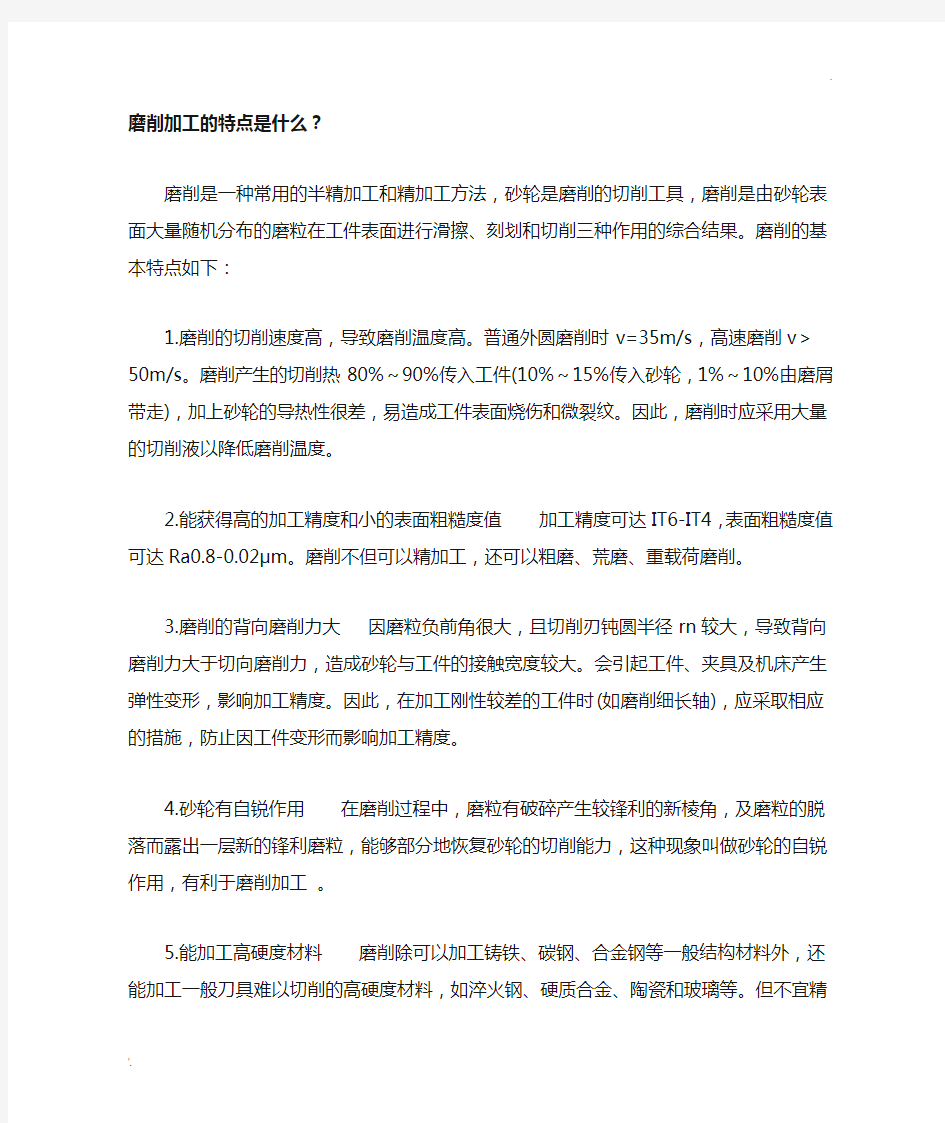
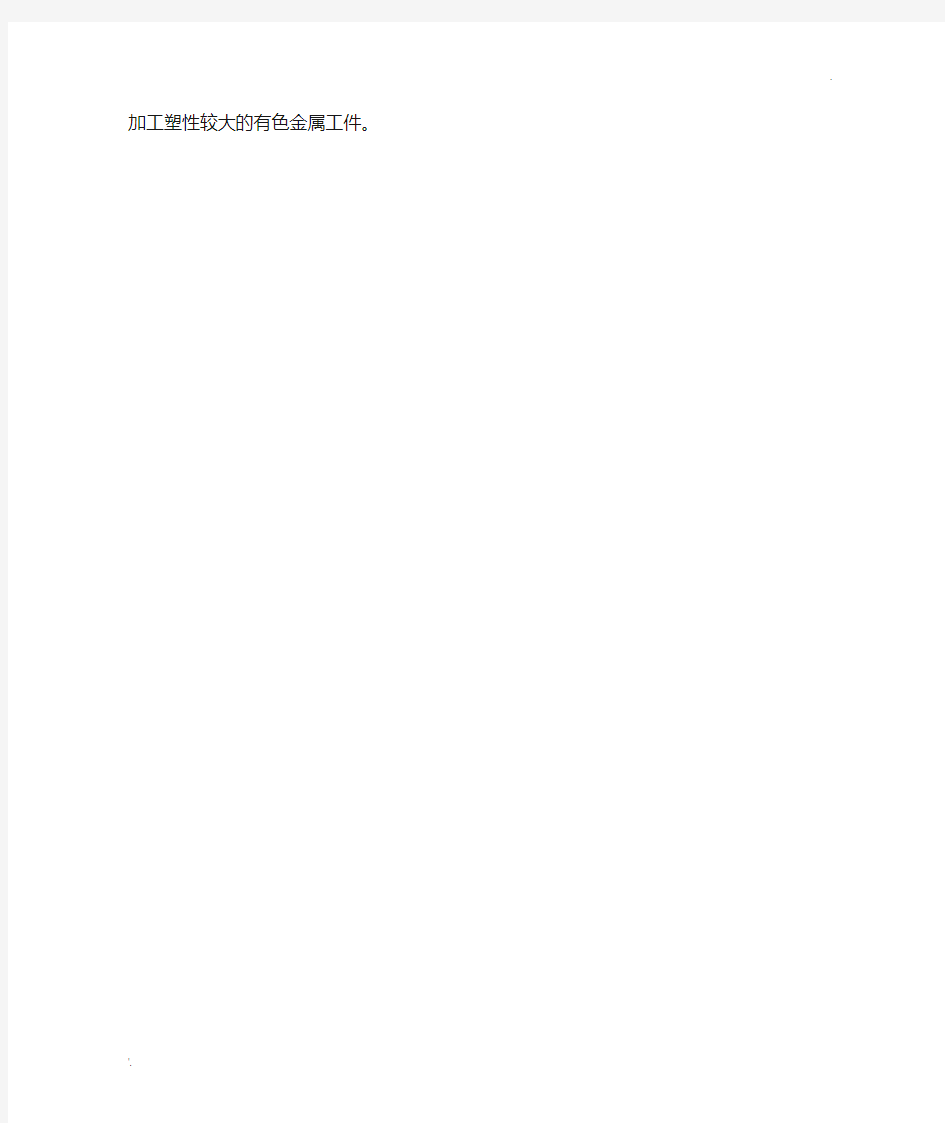
. 磨削加工的特点是什么?
磨削是一种常用的半精加工和精加工方法,砂轮是磨削的切削工具,磨削是由砂轮表面大量随机分布的磨粒在工件表面进行滑擦、刻划和切削三种作用的综合结果。磨削的基本特点如下:
1.磨削的切削速度高,导致磨削温度高。普通外圆磨削时v=35m/s,高速磨削v >50m/s。磨削产生的切削热80%~90%传入工件(10%~15%传入砂轮,1%~10%由磨屑带走),加上砂轮的导热性很差,易造成工件表面烧伤和微裂纹。因此,磨削时应采用大量的切削液以降低磨削温度。
2.能获得高的加工精度和小的表面粗糙度值加工精度可达IT6-IT4,表面粗糙度值可达Ra0.8-0.02μm。磨削不但可以精加工,还可以粗磨、荒磨、重载荷磨削。
3.磨削的背向磨削力大因磨粒负前角很大,且切削刃钝圆半径rn较大,导致背向磨削力大于切向磨削力,造成砂轮与工件的接触宽度较大。会引起工件、夹具及机床产生弹性变形,影响加工精度。因此,在加工刚性较差的工件时(如磨削细长轴),应采取相应的措施,防止因工件变形而影响加工精度。
4.砂轮有自锐作用在磨削过程中,磨粒有破碎产生较锋利的新棱角,及磨粒的脱落而露出一层新的锋利磨粒,能够部分地恢复砂轮的切削能力,这种现象叫做砂轮的自锐作用,有利于磨削加工。
5.能加工高硬度材料磨削除可以加工铸铁、碳钢、合金钢等一般结构材料外,还能加工一般刀具难以切削的高硬度材料,如淬火钢、硬质合金、陶瓷和玻璃等。但不宜精加工塑性较大的有色金属工件。
'.
第一节 磨削的应用及工艺特点
教师姓名 授课形式讲授授课时数1授课日期年月日授课班级 授课项目及任务名称 第九章磨削 第一节磨削的应用及工艺特点 教学目标知识目 标 掌握磨削的应用及其工艺特点等基础知识。 技能目 标 学会应用磨削的基础知识加工工件。 教学重点磨削的工艺特点及应用教学难点磨削的工艺特点 教学方法教学手段 借助于多媒体课件和相关动画及视频,详细教授磨削的工艺特点及应用等基础知识。教师先通过PPT课件进行理论知识讲解,再利用相关动画和视频进行演示,让学生能够将理论知识转化成实践经验。同时学生根据所学内容,完成知识的积累,为以后的实践实训打下基础。 学时安排1.磨削的应用约10分钟; 2.磨削的工艺特点约35分钟; 教学条件多媒体设备、多媒体课件。 课外作业查阅、收集磨削的相关资料。检查方法随堂提问,按效果计平时成绩。 教学后记
授课主要内容 第一节磨削的应用及工艺特点 近年来,磨削正朝着两个方向发展:一是高精度、低粗糙度磨削;另一个是高效磨削。 高精度、低粗糙度磨削包括精密磨削、超精密磨削和镜面磨削,可以代替研麿加工,以便节省工时和减轻劳动强度。 高效磨削包括高速磨削、强力磨削和砂带磨削,主要目标是提高生产效率。 一、磨削的应用 磨削可以加工的零件材料范围很广,既可以加工铸铁、碳钢、合金钢等一般结构材料,也能够加工高硬度的淬硬钢、硬质合金、陶瓷和玻璃等难切的材料,但是,磨削不宜精加工塑性较大的有色金属零件。 磨削可以加工外圆、内圆、平面、螺纹和齿轮等各种的表面,还常用于各种刀具的刃麿。 二、磨削的工艺特点 磨削是机器零件精密加工的主要方法之一,去除的加工余量很小。磨削的工艺特点有: 1.精度高 比一般切削加工机床精度高,刚度及稳定性较好,并有微量进给机构。 2.表面粗糙度小 一般磨削表面粗糙度值为0.8μm~0.2μm,当采用小粗糙度磨削时,表面粗糙度值可达0.1μm~0.08μm。 3.背向磨削力较大 麿外圆时总麿削力F也可以分解为三个互相垂直的力,其中:FX称为进给磨削力,很小,一般可忽略不计。 F称为背向磨削力,不消耗功率,一般作用在工艺系统刚度较差的方向上,因此容易使工艺系统变形,影响零件加工精度。 F称为磨削力,决定磨削时消耗功率的大小。 .残余应力和表面变形强化严重 与普通刀具切削相比,磨削的残余应力层比表面变形强化层要浅得多,但对零件的加工精度、加工工艺和使用性能均有一定的影响。 5.砂轮有自锐作用 在磨削过程中,砂轮存在着自锐作用,正由于砂轮本身的自锐性,使得磨粒能够以较锋利的刃口对零件进行切削。 6.磨削温度高 磨削时切削速度为一般切削加工的10~20倍,在高的切削速度下,磨削时所消耗的能量绝大部分转化为热量。
精密和超精密加工的应用和发展趋势
精密和超精密加工的应用和发展趋势 [摘要]本文以精密和超精密加工为研究对象,对世界上精密和超精密加工的应用和发展趋,势进行了分析和阐释,结合我国目前发展状况,提出今后努力方向和发展目标。 【关键词】精密和超精密加工;精度;发展趋势 精密和超精密制造技术是当前各个工业国家发展的核心技术之一,各技术先进国家在高技术领域(如国防工业、集成电路、信息技术产业等)之所以一直领先,与这些国家高度重视和发展精密、超精密制造技术有极其重要的关系。超精密加工当前是指被加工零件的尺寸精度高于0.1μm,表面粗糙度Ra小于0.025μm,以及所用机床定位精度的分辨率和重复性高于0.01μm的加工技术,亦称之为亚微米级加工技术,且正在向纳米级加工技术发展。超精密加工技术在国际上处于领先地位的国家有美国、英国和日本。这些国家的超精密加工技术不仅总体成套水平高,而且商品化的程度也非常高。 美国是开展超精密加工技术研究最早的国家,也是迄今处于世界领先地位的国家。早在20世纪50年代末,由于航天等尖端技术发展的需要,美国首先发展了金刚石刀具的超精密切削技术,称为“SPDT技术”(Single Point Diamond Turning)或“微英寸技术”(1微英寸=0.025μm),并发展了相应的空气轴承主轴的超精密机床。用于加工激光核聚变反射镜、战术导弹及载人飞船用球面非球面大型零件等等。如美国LLL实验室和Y-12工厂在美国能源部支持下,于1983年7月研制成功大型超精密金刚石车床DTM-3型,该机床可加工最大零件¢2100mm、重量4500kg的激光核聚变用的各种金属反射镜、红外装置用零件、大型天体望远镜(包括X光天体望远镜)等。该机床的加工精度可达到形状误差为28nm(半径),圆度和平面度为12.5nm,加工表面粗糙度为Ra4.2nm。 在超精密加工技术领域,英国克兰菲尔德技术学院所属的克兰菲尔德精密工程研究所(简称CUPE)享有较高声誉,它是当今世界上精密工程的研究中心之一,是英国超精密加工技术水平的独特代表。如CUPE生产的Nanocentre(纳米加工中心)既可进行超精密车削,又带有磨头,也可进行超精密磨削,加工工件的形状精度可达0.1μm,表面粗糙度Ra<10nm。 日本对超精密加工技术的研究相对于美、英来说起步较晚,但是当今世界上超精密加工技术发展最快的国家。日本的研究重点不同于美国,是以民品应用为主要对象。所以日本在用于声、光、图象、办公设备中的小型、超小型电子和光学零件的超精密加工技术方面,是更加先进和具有优势的,甚至超过了美国。 我国的精密、超精密加工技术在20世纪70年代末期有了长足进步,80年代中期出现了具有世界水平的超精密机床和部件。北京机床研究所是国内进行超
高速磨削技术的现状及发展前景
高速磨削技术的现状及发展前景 The Situ ation and Developing Vistas of High-Speed G rinding T echnology 荣烈润 摘 要:本文综述了高速磨削的概念、优势、关键技术、应用近况和发展前景。 关键词:高速磨削 动平衡 砂轮修整 精密高速磨削 高效深磨 Abstract:This paper introduced concept,advantages,key technical points,application and developing vistas of high2speed grinding technology. K ey w ords:high2speed grinding dynamic balancing grinding wheel trim precision high2speed grind2 ing high2efficiency deep grinding 0 引言 人们一直对于提高磨削的砂轮速度所带来的技术优势和经济效益给予了充分的注意和重视。但是在高速磨削过程中,工件受热变形和表面烧伤等均限制了砂轮速度的进一步提高,砂轮强度和机床制造等关键技术也使得高速磨削技术在一段时间内进展缓慢。当20世纪90年代以德国高速磨床FS-126为主导的高速磨削(High-speed Grinding)技术取得了突破性进展后,人们意识到一个全新的磨削时代已经到来。 高速磨削技术是磨削工艺本身的革命性跃变,是适应现代高科技需要而发展起来的一项新兴综合技术,它集现代机械、电子、光学、计算机、液压、计量及材料等先进技术成就于一体。随着砂轮速度的提高,目前磨削去除率已猛增到了3000mm3/ mm?s甚至更多,可与车、铣、刨等切削加工相媲美,尤其近年来各种新兴硬脆材料(如陶瓷、光学玻璃、光学晶体、单晶硅等)的广泛应用更推动了高速磨削技术的迅猛发展。日本先端技术研究会把高速加工列为五大现代制造技术之一。国际生产工程学会(CIRA)将高速磨削技术确定为面向21世纪的中心研究方向之一。 1 高速磨削的概念及优势 高速加工(High-speed Machining)概念首先由德国切削物理学家Card.J.Salomon于1931年提出,他发表了著名的Salomon曲线,创造性地预言了超越Taloy切削方程式的非切削工作区域的存在,提出如能大幅度提高切削速度,就可以越过切削过程产生的高温死谷而使刀具在超高速区进行高速切削,从而大幅度减少切削工时,成倍地提高机床生产率。这对今后高速磨削的发展有着非常重要的启示,对于高速磨削技术的实用化起到了直接的推动作用。 高速磨削与普通磨削相比具有以下突出的技术优势: (1) 可大幅度提高磨削效率,减少设备使用台数。以往磨削仅适用于加工余量很小的精加工,磨削前须有粗加工工序和半精加工工序,需配有不同类型的机床。而高速磨削既可精加工又可粗加工,这样就可以大大减少机床种类,简化了工艺流程。 (2) 可以明显降低磨削力,提高零件的加工精度。高速磨削在材料切除率不变的条件下,可以降低单一磨粒的切削深度,从而减少磨削力,获得高质量的工件表面,尤其在加工刚度较低(如薄壁零件)的工件时,易于保证较高的加工精度。 (3) 成功地越过了磨削热沟的影响,工件表面层可获得残余压应力(这对工件受力有利)。 (4) 砂轮的磨削比显著提高,有利于实现自动化磨削。 (5) 能实现对硬脆材料(如工程陶瓷及光学玻璃等)的高质量加工。
第五节 磨削的工艺特点及其应用
第五节磨削的工艺特点及其应用 用砂轮或其他磨具加工工件,称为磨削。本节主要讨论用砂轮在磨床上加工工件的特点及其应用,磨床的种类很多,较常见的有外圆磨床、内圆磨床和平面磨床等。 作为切削工具的砂轮,是由磨料加结合剂用烧结的方法而制成的多孔物体。由于磨料、结合剂及制造工艺等的不同,砂轮特性可能差别很大,对磨削的加工质量、生产效率和经济性有着重要影响。砂轮的特性包括磨料、粒度、硬度、结合剂、组织以及形状和尺寸等。 一.磨削过程 磨削可以加工外圆面、内孔、平面、成形面、螺纹、齿轮等 1.外圆磨削 1、在外圆磨床上进行 磨法:纵磨法横磨法综合磨深磨法 2、无心外圆磨 圆面必须连续,不能有较长键槽等孔的磨削 2.平面磨削 周磨质量较高,但较慢 端磨较快,但质量不高 特点:主运动是砂轮的旋转运动; 磨削过程:实际上是磨粒对工件表面的切削、刻削和滑擦三种作用的综合效应; 砂轮的“自锐性” :磨削中,磨粒本身也会由尖锐逐渐磨钝,使切削能力变差,切削力变大,当切削力超过粘结剂强度时,磨钝的磨粒会脱落,露出一层新的磨粒,这就是砂轮的“自锐性”。
磨削往往作为最终加工工序。 砂轮的修整 由于砂轮的“自锐性”以及切屑和碎磨粒会阻塞砂轮,在磨削一定时间后,需用金刚石车刀等对砂轮进行修整。 二.磨削的工艺特点 磨床的特点: a.使用磨料、磨具(如砂轮、砂带、油石、研磨料等)为工具,进行切削加工。 b.用来加工硬度较高的材料。 c.加工精度高、光洁度高。 d.一般加工余量较小。 工业发达国家,磨床比例高(约30%左右),磨床用于粗、精加工,发展了新型强力磨和高速磨。
三.磨削的应用和发展 (一)外圆磨床 磨床中所占比例较大的一种,包括万能外圆磨床、外圆磨床、无心外圆磨床。 1.万能外圆磨床 万能性好,常用于加工以下几种典型表面。 <1>磨外圆 加工所需的运动 砂轮主运动 n 工件的圆周进给运动 f1 工件的纵向进给运动 f2 砂轮的横向切入运动 c <2>磨长圆锥面 外圆磨床工作台分两层,上工作台相对下工作台调整至一定的角度位置(不超过±7°)机床运动与(1)相同,但工件回转中心线与工作台纵向进给方向不平行,故磨削出来的是圆锥面。 <3>磨短圆锥面 圆锥面的宽度小于砂轮宽度。砂轮架在水平面内转角度,工件不作往复运动。 <4>磨内锥孔(包括圆柱孔) 工件卡盘装在头架主轴上,头架可在水平面内转角度,此时大砂轮不转,内圆磨具支架翻下,小砂轮磨削。 由上可知:万能外圆磨床万能性高,但是机床的层次多,刚性差,加工精度低。 2.普通外圆磨床 与万能外圆磨床的区别~头架、砂轮架、头架主轴都固定不可转动,并且没有内圆磨具。主要加工外圆柱表面和锥度不大的圆锥表面。 特点:结构简单,刚性好,加工精度高,但万能性较差。 3.无心外圆磨 工件很短(如销钉)无法用顶针顶起,是以工件的外圆面作定位面的外圆磨床。 无心磨的两种方法: 1.贯穿磨法~工件中心高出e=(15~25%)D工件,导轮用橡胶和树脂作磨粒粘结剂,摩擦系数大,工件随导轮转,速度相同,且磨粒粒度细不产生磨削。 砂轮转速快,与工件有相对运动,产生磨削。导轮中心线倾斜α角,导轮与工件接触处的线速
磨削加工的危险因素
编号:SM-ZD-33863 磨削加工的危险因素Organize enterprise safety management planning, guidance, inspection and decision-making, ensure the safety status, and unify the overall plan objectives 编制:____________________ 审核:____________________ 时间:____________________ 本文档下载后可任意修改
磨削加工的危险因素 简介:该安全管理资料适用于安全管理工作中组织实施企业安全管理规划、指导、检查和决策等事项,保证生产中的人、物、环境因素处于最佳安全状态,从而使整体计划目标统一,行动协调,过程有条不紊。文档可直接下载或修改,使用时请详细阅读内容。 1.机械伤害 机械伤害是指磨削机械本身、磨具或被磨削工件与操作者身体接触、碰撞所造成的伤害。例如,磨削机械的运动零部件木加防护或防护不当,夹持不牢的加工件甩出,操作者与高速旋转的磨具触碰造成擦伤,或由于磨具破裂,高速运动的碎块飞出伤人等。 2.噪声危害 磨削机械是高噪声机械,磨削噪声来自多因素的综合作用,除了磨削机械自身的传动系统噪声、干式磨削的排风系统噪声和湿式磨削的冷却系统噪声外,磨削加工的切削比能大、速度高是产生磨削噪声的主要原因。在进行粗磨、切割、抛光和薄板磨削作业,以及使用风动砂轮机时,噪声更大,有时高达115dB(A)以上,对操作者听力会造成损伤。 3.粉尘危害 磨削加工是微量切削,切屑细小,尤其是磨具的自砺
磨削加工的发展趋势论文
磨削加工的发展趋势 王哲 (北京石油化工学院机械工程学院,机G111班) 摘要多年以来随着我国制造业技术水平的不断发展进步,机械制造业有了长足的发展,磨削加工作为机械制造业金属切削加工方法中的一种,有着不可替代的位置及十分重要的作用,相对于早期的磨削加工技术,今天的金属磨削加工技术有了很大的变化,无论是从材料性质,刀具材料以及磨削加工技术等都有了很大的发展变化,本文主要就磨床磨削加工及发展趋势做简单的介绍。 关键词超高速磨削相关技术;数控磨床;精密磨削;刀具材料 1引言 对于目前机械加工领域磨削加工技术发生的变化,磨削加工技术的发展变化,本文作了简要的论述,磨削加工技术的主要发展方向是自动化、集成化、高速化、精密化等方向发展,分别对应的数控磨床、超高速磨削技术、精密磨削技术,此外刀具材料也发生了很大的变化,向能够耐高温、可用于高速加工等。本文主要引用近几年发表的文献,对于研究磨削加工技术发展有一定的帮助,本文就几个磨削加工的主要发展方向作简要的论述。 在机械制造中,有许多金属加工方法,例如切削加工、电加工、冷冲压、铸造、锻造、焊接、粉末冶金、化学加工和特种加工等。金属切削加工时利用切削刀具在工件上切除多余的金属层,从而获得具有一定的尺寸、形状、位置和表面质量的机器零件的一种加工方法。他已被广泛应用于生产实践中。金属切削机床是用切削方法将金属毛坯加工成机器零件的机床。在各类机械制造部门所拥有的装备中,机床占百分之五十以上,所负担的工作量占总加工量的一半以上,机床的技术水平高低直接影响机械产品的质量和零件制造的经济性。 我们对于磨削技术发展应该有一个简单的了解,一般来讲,按砂轮线速度的高低将磨削分为普通磨削和高速磨削以及超高速磨削。按磨削精度将磨削分为普通磨削、精密磨削、超精密磨削。按磨削效率将磨削分为普通磨削、高效磨削。高效磨削包括高速磨削、超高速磨削、缓进给磨削、高效深切磨削、砂带磨削、快速短行程磨削、高速重负荷磨削。[2]高速高效磨、超高速磨削在欧洲、美国和日本等一些工业发达国家发展很快,如德国的Aachen大学、美国Connecticut大学等,有的在实验室完成了V为250m/s、350m/s、400m/s 的实验。据报道,德国Aachen大学正在进行目标为500m/s的磨削实验研究。在实用磨削方面,日本已有200m/s的磨床在工业中应用。在我国对高速磨削及磨具的研究已有多年的历史,如湖南大学在70年代末期便进行了80m/s、120m/s的磨削工艺实验,前几年某大学也计划开展250m/s的磨削研究。在实际应用中,砂轮线速度,一般还是45m/s-60m/s。[2]对于磨削加工是一种常用的半精加工和精加工方法,砂轮是磨削的切削工具,磨削是由砂轮表面大量随机分布的磨粒在工件表面进行滑擦、刻划和切削三种作用的综合结果。磨削的基本特点如下:
先进磨削技术的发展
先进磨削技术的新发展 摘要:磨削是指用磨料或磨具去除材料的加工工艺方法,磨削与车、铣削在常规加工材料上竞争可能难分高下。尽管硬车削已经替代了很多磨削加工,但由于粘结技术的进步、高级磨料的应用,磨削依然保持强势。作为先进制造技术中的重要领域,磨削加工技术已在机械、国防、航空航天、微加工、芯片制造等众多领域得到广泛应用。磨削加工的发展趋势正朝着采用超硬磨料、磨具,高速、高效、高精度磨削工艺及柔性复合磨削、绿色生态磨削方向发展。如今磨削加工的发展趋势,主要包括高速磨削、超高速磨削、精密和超精密磨削、缓进给磨削、高效深切磨削、砂带磨削及绿色磨削技术。我们也需要了解超高速磨削加工的机理及超高速磨削的优越性,把握高速超高速磨削加工技术的发展前景。 关键词:磨削精密磨削高效磨削超高速磨削 正文:磨削加工技术是利用磨料去除材料的加工方法,也是人类最早使用的生产技艺方法。18世纪中期世界上第一台外圆磨床问世,由石英石、石榴石等天然磨料构成,随后又研制出平面磨床。20世纪40年代末,人造金刚石出现;1957年立方氮化硼研制成功;随着磨削技术的发展,特别是超硬磨料人造金刚石砂轮与立方氮化硼党的应用,磨削加工范围日益增大,磨削加工精度和加工效率也不短提高。 磨削技术发展趋势 如今磨削加工技术正朝着高速化,精细化方向发展。因此,我们了解超高速磨削加工的机理及超高速磨削的优越性,把握高速超高速磨削加工技术的发展前景是很有必要的。主要包括高速磨削、超高速磨削、精密和超精密磨削、缓进给磨削、高效深切磨削、砂带磨削及绿色磨削技术 首先了解一下精密及超精密磨削机理,精密磨削一般使用金刚石和立方氮化硼等高硬度磨料砂轮,主要用金刚石修整刀具以极小而又均匀的微进给(10~15mm/min)对砂轮进行精细修整,以获得众多的等高微刃,加工表面的磨痕较细,加工过程中,由于微切削、滑移、摩擦等综合作用,加工工件达到了小的表面粗糙度值和高的精度要求。超精密磨削则采用较小的修整导程和较小的背吃刀量修整砂轮,靠超细微磨粒等高微刃的磨削作用进行磨削加工。现在我们就对以上提到的磨削技术详细了解一下。 高效磨削技术 高效磨削是一种先进的制造技术,在其不断的发展中达到了一个崭新的水平。所谓高效磨削,是指加大磨削负荷或提高砂轮线速度,增加单位时间金属比切除率和单位时间的金属去除量,以达到和车削、铣削那样高的金属切除率,或者甚至更高。高效磨削主要包括高速磨削、缓进给磨削、高效深磨和砂带磨削,现已成为磨削加工技术发展的总体趋势。高效磨削技术的大力推广可有效地提高磨削效率、加工质量、砂轮耐用度,并降低生产成本。 缓进给磨削 缓进给磨削是继高速磨削之后发展起来的一种高效加工方法,对成型表面的加工有显著的成效。缓进给磨削是强力磨削的一种,又称深切缓进给磨削或蠕动磨削。缓进给磨削与普通磨削的不同在于采用增大磨削深度、降低磨削速度、砂轮与工件有较大的接触面积和高的速度比,达到很高的金属切除率。磨削工件时,只需经过一次或数次行程即可磨到所需的形状和尺寸精度。由于砂轮的磨削深度大,致使砂轮与工件的接触面积加大,有效抑制了磨削时振动的产生,磨
磨削加工
磨削加工 一、磨削特点 磨削是在磨床上用砂轮作为切削刀具对工件进行切削加工的方法。该方法的特点是: 1.由于砂轮磨粒本身具有很高的硬度和耐热性,因此磨削能加工硬度很高的材料,如淬硬的钢、硬质合金等。 2.砂轮和磨床特性决定了磨削工艺系统能作均匀的微量切削,一般 ap=0.001~0.005mm;磨削速度很高,一般可达v=30~50m/s;磨床刚度好;采用液压传动,因此磨削能经济地获得高的加工精度(IT6~IT5)和小的表面粗糙度(Ra=0.8~0.2μm)。磨削是零件精加工的主要方法之一。 3.由于剧烈的磨擦,而使磨削区温度很高。这会造成工件产生应力和变形,甚至造成工件表面烧伤。因此磨削时必须注入大量冷却液,以降低磨削温度。冷却液还可起排屑和润滑作用。 4.磨削时的径向力很大。这会造成机床—砂轮—工件系统的弹性退让,使实际切深小于名义切深。因此磨削将要完成时,应不进刀进行光磨,以消除误差。 5.磨粒磨钝后,磨削力也随之增大、致使磨粒破碎或脱落,重新露出锋利的刃口,此特性称为“自锐性”。自锐性使磨削在一定时间内能正常进行,但超过一定工作时间后,应进行人工修整,以免磨削力增大引起振动、噪声及损伤工件表面质量。二、砂轮 砂轮是磨削的切削工具,它由许多细小而坚硬的磨粒和结合剂粘而成的多孔物体。磨粒直接担负着切削工作,必须锋利并具有高的硬度,耐热性和一定的韧性。常用的磨料有氧化铝(又称刚玉)和碳化硅两种。氧化铝类磨料硬度高、韧性好,适合磨削钢料。碳化硅类磨料硬度更高、更锋利、导热性好,但较脆,适合磨削铸铁和硬质合金。
同样磨料的砂轮,由于其粗细不同,工件加工后的表面粗糙度和加工效率就不相同,磨粒粗大的用于粗磨,磨粒细小的适合精磨、磨料愈粗,粒度号愈小。 结合剂起粘结磨料的作用。常用的是陶瓷结合剂,其次是树脂结合剂。结合剂选料不同,影响砂轮的耐蚀性、强度、耐热性和韧性等。 磨粒粘结愈牢,就愈不容易从砂轮上掉下来,就称砂轮的硬度,即砂轮的硬度是指砂轮表面的磨粒在外力作用下脱落的难易程度。容易脱落称为软,反之称为硬。砂轮的硬度与磨料的硬度是两个不同的概念。被磨削工件的表面较软,磨粒的刃口(棱角)就不易磨损,这样磨粒使用的时间可以长些,也就是说可选粘接牢固些的砂轮(硬度较高的砂轮)。反之,硬度低的砂轮适合磨削硬度高的工件。 砂轮在高速条件下工作,为了保证安全,在安装前应进行检查,不应有裂纹等缺陷;为了使砂轮工作平稳,使用前应进行动平衡试验。 砂轮工作一定时间后,其表面空隙会被磨屑堵塞,磨料的锐角会磨钝,原有的几何形状会失真。因此必须修整以恢复切削能力和正确的几何形状。砂轮需用金刚石笔进行修整。 三、平面磨床的结构与磨削运动 磨床的种类很多,主要有平面磨床、外圆磨床、内圆磨床、万能外圆磨床(也可磨内孔)、齿轮磨床、螺纹磨床,导轨磨床、无心磨床(磨外圆)和工具磨床(磨刀具)等。这里介绍平面磨床及其运动。 1.平面磨床的结构(以M7120A为例,其中:M——磨床类机床;71——卧轴矩台式平面磨床;20——工作台面宽度为200mm;A——第一次重大改进。) 1)砂轮架——安装砂轮并带动砂轮作高速旋转,砂轮架可沿滑座的燕尾导轨作手动或液动的横向间隙运动。 2)滑座——安装砂轮架并带动砂轮架沿立柱导轨作上下运动。 3)立柱——支承滑座及砂轮架。
精密机械加工的发展趋势
精密机械加工发展趋势 摘要:本文主要从精密机械加工技术的角度讨论了精密机械加工的现状和发展趋势,阐述了精密机械加工的概念以及未来的发展。 关键词:精密加工加工精度发展趋势 1 引言 机械制造技术从提高精度与生产率两个方面同时迅速发展起来。在提高生产率方面,提高自动化程度是各国致力发展的方向,近年来,从C N C到C I M S发展迅速,并且在一定范围内得到了应用。从提高精度方面,从精密加工发展到超精密加工,这也是世界各主要发达国家致力发展的方向。其精度从微米到亚微米,乃至纳米,其应用范围日趋广泛,在高技术领域和军用工业以及民用工业中都有广泛应用。如激光核聚变系统、超大规模集成电路、高密度磁盘、精密雷达、导弹火控系统、惯导级陀螺、精密机床、精密仪器、录象机磁头、复印机磁鼓、煤气灶转阀等都要采用精密加工技术。 随着精密机械和电子技术的发展,现代产品越来越精密。例如:超大规模集成电路中要求在1mm2平面上集成几十万个以上的元件,线条宽度只有1μm,形状和位置误差小于0.05μm。于是对相应的机床精度提出更高的要求,加工工艺等也必须相应采取有效措施来保证加工要求。 根据相关资料的技术研究,精密加工目前所能达到的水平为:尺寸公差不大干0.5~1μm,形状公差不大于0.01μm,表面粗糙度Ra不大于0.01μm。所用的机床有:精密铣床、精密研磨机、光学透镜精密研磨机、精密宝石研磨加工机、超精密磨加工机等。机床的零部件是动、静压轴承和导轨、弹性导轨、滚珠或滚柱预压含油轴承和导轨,使用的刀具与材料是磨科与金刚石等,控制系统一般为直流伺服电机(DC)——半闭式,带编码器最佳控制、逻辑控制或精密直流伺服电机——闭环,用微机实现自适应控制。 目前,先进制造技术已经是一个国家经济发展的重要手段之一,许多发达国家都十分重视先进制造技术的水平和发展,利用它进行产品革新、扩大生产和提高国际经济竞争能力。发展先进制造技术是当前世界各国发展国民经济的主攻方向和战略决策,同时又是一个国家独立自主、繁荣富强、经济持续稳定发展、科技保持先进领先的长远大计。目前,精密与特种加工技术水平是一个国家制造工业水平的重要标志之一。精密加工所能达到的精度、表面粗糙度、加工尺寸范围和几何形状是一个国家制造技术水平的重要标志之-。精密与特种加工技术已经成为国际竞争中取得成功的关键技术。发展尖端技术,发展国防工业,发展微电子工业等,都需要精密与特种加工技术来制造相关的仪器、设备。 2 精密机械加工方法 根据加工方法的机理和特点,精密加工可分为刀具切削加工、磨料加工、特种加工和复合加工四大类。 随着加工技术的发展,出现了许多新的加工机理,因此在精密加工,特别是在微细加工中.根据零件成形机理和特点。分为去除加工、结合加工和变形加工三大类。去除加工又称为分离加工,是利用力、热、电、光等加工方法从工件去除一部分材料,如切削、磨削、电加工等。结合加工是利用理化方法在工件表面上附着(沉积)、注入(渗入)、焊接一层不同材料,如电镀、气相沉积、氧化、渗碳、粘接、焊接等。变形加工是利用力、热、分子运动等手段使工件产生变形,改变其尺寸、形状和性能,如铸造、锻压等。可见加工的概念已突破传统的去除加工手段,具有堆积、生长、变形等特色,同时强调了表面处理,形成了表面加工技术。 3 精密机械(切削)加工的技术和工艺优势
精密机械加工的发展趋势
精密机械加工的发展趋势
精密机械加工发展趋势 摘要:本文主要从精密机械加工技术的角度讨论了精密机械加工的现状和发展趋势,阐述了精密机械加工的概念以及未来的发展。 关键词:精密加工加工精度发展趋势 1 引言 机械制造技术从提高精度与生产率两个方面同 时迅速发展起来。在提高生产率方面,提高自动化程度是各国致力发展的方向,近年来,从C N C到C I M S发展迅速,并且在一定范围内得到了应用。从提高精度方面,从精密加工发展到超精密加工,这也是世界各主要发达国家致力发展的方向。其精度从微米到亚微米,乃至纳米,其应用范围日趋广泛,在高技术领域和军用工业以及民用工业中都有广 泛应用。如激光核聚变系统、超大规模集成电路、高密度磁盘、精密雷达、导弹火控系统、惯导级陀螺、精密机床、精密仪器、录象机磁头、复印机磁鼓、煤气灶转阀等都要采用精密加工技术。 随着精密机械和电子技术的发展,现代产品越来越精密。例如:超大规模集成电路中要求在1mm2平面上集成几十万个以上的元件,线条宽度只有1μm,形状和位置误差小于0.05μm。于是对相应的机床精度提出更高的要求,加工工艺等也必须相应采取有效措施来保证加工要求。
根据相关资料的技术研究,精密加工目前所能达到的水平为:尺寸公差不大干0.5~1μm,形状公差不大于0.01μm,表面粗糙度Ra不大于0.01μm。所用的机床有:精密铣床、精密研磨机、光学透镜精密研磨机、精密宝石研磨加工机、超精密磨加工机等。机床的零部件是动、静压轴承和导轨、弹性导轨、滚珠或滚柱预压含油轴承和导轨,使用的刀具与材料是磨科与金刚石等,控制系统一般为直流伺服电机(DC)——半闭式,带编码器最佳控制、逻辑控制或精密直流伺服电机——闭环,用微机实现自适应控制。 目前,先进制造技术已经是一个国家经济发展的重要手段之一,许多发达国家都十分重视先进制造技术的水平和发展,利用它进行产品革新、扩大生产和提高国际经济竞争能力。发展先进制造技术是当前世界各国发展国民经济的主攻方向和战略决策,同时又是一个国家独立自主、繁荣富强、经济持续稳定发展、科技保持先进领先的长远大计。目前,精密与特种加工技术水平是一个国家制造工业水平的重要标志之一。精密加工所能达到的精度、表面粗糙度、加工尺寸范围和几何形状是一个国家制造技术水平的重要标志之-。精密与特种加工技
精密磨削加工技术的应用与发展
精密磨削加工技术的应用与发展 作者:王永康 摘要:精密磨削加工技术是现代机械制造业的一项关键技术之一,对人们的生产生活、国家国防与航空航天建设、社会的经济发展有着相当重要的作用。本文主要阐述了精密加工技术的原理、现行状况、发展趋势等。 关键词:精密磨削加工、磨削机理、磨削技术的发展、磨削技术的未来 引言 随着科学技术水平不断的提高,磨削加工已广泛应用于金属及其他材料的粗、精加工,是非常重要的切削加工方式。目前,磨削加工已经成为现代机械制造领域中实现精密与超精密加工最有效、应用最广泛的基本工艺技术,为人们提供高精度、高质量、高度自动化的技术装备的开发和研制。 磨削是指用磨料或磨具去除材料的加工工艺方法,一般来讲,按照砂轮线速度的高低可将其进行分类,把砂轮速度低于45 m/s的磨削称为普通磨削,把砂轮速度高于45 m/s的磨削称为高速磨削,把砂轮速度高于150m/s的磨削称为超高速磨削。按磨削效率将磨削分为普通磨削、高效磨削(高速磨削、超高速磨削、缓进给磨削、高效深切磨削、砂带磨削、快速短行程磨削和高速重负荷磨削)。磨削加工能达到的磨削精度在生产发展的不同时期有不同的精度范围,当前,按磨削精度将磨削分为普通磨削(加工精度>1μm、表面粗糙度R a0.16~1.25μm)、精密磨削(加工精度1~0.5μm、表面粗糙度R a0.04~1.25μm)、超精密磨削(加工精度≤0.01μm、表面粗糙度R a≤0.01μm)。 一、精密磨削的内涵: 精密加工是指在一定发展时期中,加工精度和表面质量达到较高程度的加工工艺,当前是指被加工零件的加工精度为l~0.1μm,表面粗糙度值Ra0.2~0.01μm的加工技术。精密磨削是目前对钢铁等黑色金属和半导体等脆硬材料进行精密加工的主要方法之一,在现代化的机械和电子设备制造技术中占有十分重要的地位。 精密磨削主要靠对砂轮的精细修整,使用金刚石修整工具以极小而又均匀的微进给(10~15mm /min)。获得众多的等高微刃,加工表面磨削痕迹微细,最后采 用无火花光磨。由于微切削、滑移和摩擦等综合作用,达到低表面粗糙度值和高精度要求。高精密磨削的切屑很薄,砂轮磨粒承受很高的应力,磨粒表面受高温、高压作用,一般使用金刚石和立方氮化硼等高硬度磨料砂轮磨削。 二、磨削机理 精密磨削一般使用金刚石和立方氮化硼等高硬度磨料砂轮,主要靠对砂轮的精细修整,使用金刚石修整刀具以极小而又均匀的微进给(10~15mm/min),获得众多的等高微刃,加工表面磨削痕迹微细,最后采用无火花光磨,由于微切削、滑移和摩擦等综合作用,达到低表面粗糙度值和高精度要求.超精密磨削采用较小修整导程和吃刀量修整砂轮,靠超微细磨粒等高微刃磨削作用进行磨削。精密与超精密磨削的机理与普通磨削有一些不同之处: 1)超微量切除.应用较小的修整导程和修整深度精细修整砂轮,使磨粒细微破碎而产生微刃。一颗磨粒变成多颗磨粒,相当于砂轮粒度变细,微刃的微切削作用就形成了低粗糙度。 2)微刃的等高切削作用.微刃是砂轮精细修整而成的,分布在砂轮表层同一深度上的微刃数量多,等高性好,从而加工表面的残留高度极小。 3)单颗粒磨削加工过程.磨粒是一颗具有弹性支承和大负前角切削刃的弹性体,单颗磨粒磨削时在与工件接触过程中,开始是弹性区,继而是塑性区、切削区、塑性区,最后是弹性区,这与切屑形成形状相符合。
各种加工方法的特点及比较
各种加工方法的特点分析及比较 学号:XXX 姓名:XXX 【摘要】随着机械加工工艺不断发展,企业间竞争的扩大,要求产品既节省成本又有可靠的性能。如何选择加工方法关系到竞争的胜败。本文从经济方面、质量方面、生产周期方面各种加工方法的特点总结,力求对“如何选择加工方法”有所用处。 【关键字】性能;生产周期;精度;加工;铸造;锻造;焊接;切削;钳工;数控加工 1.前言 希望本文通过对各种加工方法的分析能对制定工艺流程、降低机械加工的产品成本、提高产品质量等方面有帮助。灵活运用各种加工方法,才能在竞争中立于不败之地。 2.正文 2.1铸造、锻造、焊接、切削、钳工和数控加工的主要特点分别分析: 2.1.1铸造工艺 由于铸造采用液态下一次成形,所以对材料种类及零件形状、尺寸大小和生产批量的适应性非常广,特别适合复杂形状铸件的生产,且生产成本较低,在机械制造中具有重要的地位。铸造可直接利用成本低廉的废机件和切屑,设备费用较低。同时铸件加工余量小,节省金属,减少机械加工余量,从而降低制造成本。但液态成形的特点也使铸造工序多、铸件质量控制难度大、铸件力学性能差。 铸造车间一般工作环境差,容易对工人的健康有危害,而且对环境污染较严重。 铸造的应用范围:生产毛坯。如机床床身、内燃机等 2.1.2锻造工艺 由于金属材料经过锻造后,其内部组织更加致密、均匀,使同一种金属的锻件比铸件有更好的力学性能。
因此,各种承受重载荷及冲击载荷的重要零件,多以锻件作为毛坯,但由于锻造固态塑性成形的特点,无法获得形状(特别是内腔)复杂的锻件。 2.1.3焊接工艺 焊接是通过加热加压或加压或两者并用的方法,使金属达到原子结合的一种加工方法。与其它方法相比,焊接具有节省材料、接头密封性好、经济性好、生产周期短等优。但对工人的技术要求比较高。 焊接的应用范围在造船、电力设备生产、航天工业中广泛应用。 2.1.4车削工艺 车削加工是指在车床上应用刀具与工件作相对切削运动,用以改变毛坯的尺寸和形状等,使之成为零件的加工过程。车工在切削加工中是最常用的一种加工方法。车床占机床总数的一半左右,故在机械加工中具有重要的地位和作用。 车床应用范围:用来加工各种回转表面,如:内、外圆柱面;内、外圆锥面;端面;内、外沟槽;内、外螺纹;内、外成形表面;丝杆、钻孔、扩孔、铰孔、镗孔、攻丝、套丝、滚花等。 2.1.5铣削工艺 由于铣削的主运动是铣刀的旋转,铣刀又是多齿刀具,故铣削的生产效率高,刀具的耐用度高 铣床及其附件的通用性广,铣刀的种类很多,铣削的工艺灵活。 铣削的加工范围较广,铣削两样适用小批与大批量的生产。 2.1.6刨削工艺 在刨车上用刨刀加工工件的方法叫刨削。 常见的刨床有牛头刨、龙门刨。 刨削的适用范围主要有:加工平面、加工沟槽(如直槽、T形槽、燕尾槽)、母线为直线的成形面。 2.1.7磨削工艺 加工精度高,常用的磨削经济精度为IT6到IT5,表面粗糙度为0.8到0.2μm。同时适合于粗加工与精加工。磨削温度高,必须使用切削液。 适应范围广,不仅适用于一般的金属材料,而且适用于碳钢、铸铁、合金钢、淬火钢、合金。 2.1.8钳工工艺 钳工工作劳动强度大,生产效率低、对工人技术要求高,但所用工具简单,操作灵活简便。 因此,适应范围较为广泛。主要的操作包括:划线、锯削、锉削、錾削、钻孔、铰孔、攻丝、套扣、刮削、研磨、装配及修理。 2.1.9数控
高速磨削难加工材料的研究进展
@@[ 1 ] Choy K L. Chemical vapour deposition of coatings [ J ]. Prog Mater Sci,2003,48:57- 170. @@[2]陈利,吴恩熙,尹飞,等.(Ti,A1)N涂层的微观组织和性 能[J].中国有色金属学报,2006,16(2):279 - 283. @@[3]张武装,刘咏,贺跃辉,等.具有梯度结构的涂层硬质合金 刀片[J].中国有色金属学报,2005,15(5):757-762. @@[4]羊建高,王海兵,刘咏,等.碳含量对矿用硬质合金梯度结 构形成的影响[J].中国有色金属学报,2004,14(3):424- 428. @@[5]Lengauer W, Dreyer K.Tailoring hardness and toughness gradi ents in functional gradient hardmetals (FGHMs) [ J ]. Interna tional Journal of REfractory Metals& Hard Materials, 2006, 24 (1/2) : 155 - 161. @@[6]Suzuki H, Koji H, Yasuro T.The β- free layer formed near the surface of vacuum - sintered WC - β- Co alloys containing ni trogen[J] .Trans Japan hint Met, 1981, 22(11) :758-764.@@[7]Schwaczkopf M, Exner H E,Fischmeister H F. Kinetics of com positional modification of(W, Ti) C - Co alloy surface[ J]. Mater Sci Eng A, 1988, 105/106:225 - 231. @@[8]Yohe W C. The development of cubic- carbide - free surface layers in cemented carbides without[ J]. 1nt J Refract Met Hard Mater, 1993 - 1994,12:137 - 144. @@[9]Ekroth M, Frykholm R, Lindholm M, et al. Gradient zones in WC- Ti ( C, N) - Co based cemented carbides-experimental study and computer simulations[J]. Acta Mater,2000,48:2177 - 2185. @@[10]Ettmayer P, Kolaska H, Dreyer K. Effect of sintering atmo sphere on the properties of cermets[ J] .Power Metal Int, 1991, 23(4) :224 - 229. 第一作者:张凤洁,重庆科技学院冶金与材料工程学院,401331重庆市 高速磨削难加工材料的研究进展 陈建毅1郑祝堂1徐西鹏2 厦门城市职业学院华侨大学脆性材料加工技术教育部工程研究中心 摘要:高速磨削是实现对难加工材料的高效、优质加工的一种先进加工技术。本文总结了难加工材料高速磨 削的相关研究,从磨削力、磨削温度、磨削比能、表面形貌等磨削特性进行探讨。 高速磨削;难加工材料;磨削特性 TG580.61+4A Review of Present Research on High Speed Grinding of Difficult-to-cut Materials Chen JianyiZheng Zhutang 2011-04-01 万方数据
磨削加工的特点(新版)
( 安全技术 ) 单位:_________________________ 姓名:_________________________ 日期:_________________________ 精品文档 / Word文档 / 文字可改 磨削加工的特点(新版) Technical safety means that the pursuit of technology should also include ensuring that people make mistakes
磨削加工的特点(新版) 磨削加工是借助磨具的切削作用,除去工作表面的多余层,使工件表面质量达到预定要求的加工方法。进行磨削加工的机床称为磨床。磨削加工应用范围很广,通常作为零件(特别是淬硬零件)精加工工序,可以获得很高的加工精度和表面质量,可以用于粗加工、切割加工等。 从安全角度来看,磨削加工有以下特点: 1、磨具的运转速度高。普通磨削可达30-50m /s,高速磨削可达45-60m /s甚至更高,其速度还有日益提高的趋势。 2、磨具的非均质结构。磨具是由磨料,结合剂和气孔三要素组成的复合结构,其结构强度大大低于由单一均匀才智组成的一半金属切削刀具。
3、磨削的高热现象。磨具的高速运动、磨削加工的多刃性和微量切削,都会产生大量的磨削热,不仅可能烧伤工件表面,而且高温时磨具本身发生物理、化学变化、产生热反应力、降低磨具的强度。 4、磨具的自砺现象。在磨削力度作用下,磨钝的磨粒自身脆裂或脱落的现象,称为磨具的自砺性。磨削过程中的磨具自砺作用以及修正磨具的作业,都会产生大量磨削粉尘。 云博创意设计 MzYunBo Creative Design Co., Ltd.
第七章 磨削加工
第七章磨削加工 基本要求及重点: 1、了解磨削特点和各种磨削方法与磨削运动。 2、明确砂轮的特性及其选择原则。 3、理解砂轮磨损及耐用度、磨削力及功率、磨削温度及烧伤等概念。 4、了解磨削过程,知道磨削表面缺陷产生的原因及解决办法。 5、了解高效率和高精度及小粗糙度磨削的方法。 §7-1 磨削概述及其原理 一、概述 磨削加工是用硬质磨粒作为切削工具对工件进行微细切削加工过程的统称。它是一种精密加工方法。 1、磨削加工的优点及其应用 与其他切削加工方法相比,磨削加工是一种多刀多刃的高速切削方法。它是为适应传统金属材料的精加工及其淬硬表面加工的需要而发展起来的。随着磨料磨具和高效磨削工艺(如高速磨削、强力磨削、重负荷磨削、砂带磨削等)的发展,以及磨床结构性能的不断改进,磨削加工效率和经济性在显著提高,磨削的应用已从精加工逐步扩大到粗加工领域。同时,在当今的钛合金、高温合金、超高强度钢、不锈钢及高温结构陶瓷等难加工材料以及硬脆材料的加工中,磨削是一种非常有效的加工方法。 3、磨削加工机床分类 磨床是用磨料或磨具(砂轮、砂带、油石或研磨料)作为工具对工件表面进行加工的机床。 为了适应磨削加工表面、结构形状和尺寸大小不同的各种工件的需要,满足不同生产批量的要求,需要的磨床种类很多。 按加工工件表面不同,分为如下几类: (1) 外圆磨床包括万能外圆磨床、外圆磨床及无心外圆磨床等。 (2) 内圆磨床包括内圆磨床,无心内圆磨床及行星式内圆磨床等。 (3) 平面磨床包括卧轴矩台平面磨床、立轴矩台平面磨床、卧轴圆台平面磨床
及立轴圆台平面磨床等。 (4) 工具磨床 包括万能工具磨床(能刃磨各种常用刀具)、拉刀刃磨床、滚刀刃磨床等。 (5) 曲线磨床 (6) 专用磨床 包括曲轴磨床、凸轮轴磨床,花键轴磨床、轧辊磨床、轴承套圈滚道磨床等。 (7) 坐标磨床 (8) 锯磨机 (9) 精磨机床 包括研磨机、珩磨机、抛光机、超精加工机床及砂轮机等。 二、磨削原理 1、砂轮构造 磨削时所用的砂轮是由磨粒、结合剂 和气孔组成的,见图7-1。 2、磨削过程 磨削是由磨床、砂轮、工件,夹具 等形成的一种切削加工工艺系统。而磨 削过程是由处于砂轮和工件接触区域的 许多磨粒在挤压作用下不断同时地切入 工件,使金属层产生变形的过程。因此,磨削过程的本质是磨粒的切削过程。 磨粒的切削过程如图 7-2所示。磨粒 切削材料的过程经历了弹性变形、塑性变 形及切屑形成三个阶段。在EP 段中,由 于切削深度极小,磨粒刃尖圆弧形成的实 际负前角很大,磨粒仅在工件表面上滑擦 而过,所引起的变形完全弹性恢复,在工 件表面不残留任何沟痕,称为弹性滑擦阶 段。在PC 段中,随着磨粒挤入工件深度的增大,磨粒与工件表面间的压力逐步增加,工件表面由弹性变形逐步过渡到塑性变形。这时挤压摩擦剧烈,热应力急剧增加,磨粒在工件表面上挤压刻划出沟痕,沟痕 图7-2 磨粒的切削过程