订单安排记录表模板
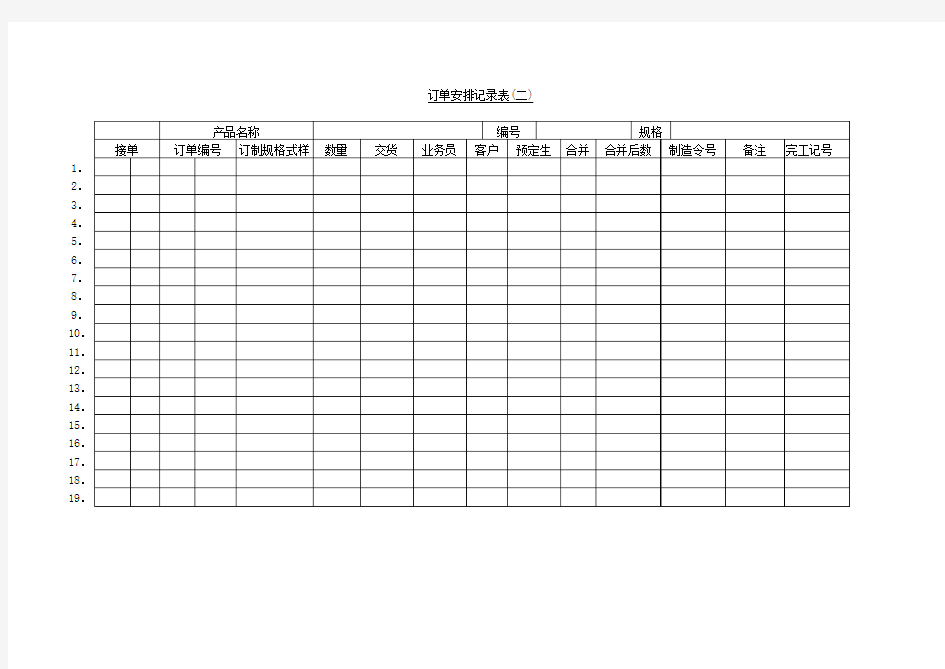
订单安排记录表(二)
1.
2.
3.
4.
5.
6.
7.
8.
9.
10
11
12
13
14
15
16
17
18
19
生产计划员主要是根据客户订单安排生产计划
生产计划员主要是根据客户订单安排生产计划。在生产计划排单过程中,要综合考虑到客户的交货日期、本公司的生产能力,供应商物料供应能力、订单相关沟通处理等。要及时跟踪生产物料情况、车间的实际生产情况、客户订单变更情况,并在计划实行过程中准确、及时发现解决问题。 一、生产计划员的主要工作流程 1、做好生产计划的综合平衡工作,合理安排,节约各项资源,降低制造成本,提高生 产效率; 2、负责根据生产任务或订单的要求,依据计划情况编排制定工程单号,及要求完工日 期,并下达到各职能部门及生产单位; 3、负责下达月、周指导性生产计划,采用项目管理的方法,逐项落实,实施过程监控; 4、及时调整生产计划,保证重大项目的供货,对于可能出现的问题及时反馈; 5、做好订单的评审、生产前的打样安排、确认、生产各环节的进度物料供应、工艺组 织布置、品质状况跟踪落实,依据生产计划的完成情况、采购物资供应情况,合理调整生产计划达成出货要求。 二、生产计划员的工作职责 1、产量:产量是工厂的关键任务,尤其是作为班长来讲。可以根据品种或型号,统计 汇总全年各月份产值或产量,可以通过饼图表现品种分布,通过折线图表现各月增长或总产量变化。当然除了数据还应有文字分析,可以结合数据从产能增加和紧急任务组织两个方面来说明。 2、效率:效率是老板比较关心的指标,一般可以通过小时数量和单位产品工时来表现, 当然不同行业有不同的表现方式。应该通过折线图表现全年每个月份效率的变化,同时要说明通过哪些事情或措施的实施,实现了这一目标。 3、品质:品质是非常关键的目标,可以通过结果品质和过程品质两个方面来说明,结 果品质的指标有客户满意度、成品检验合格率、废品率等等;过程品质指标有过程不良率、过程废品率、返工率等等。同样,仍是依据数据和图表采用柱状图表现不同品质问题的频度、饼图表现问题的分布,折线图表现全年每月的数据状况等等,也要有分析,什么样的问题如
订单的计划书
订单的计划书 篇一:订单计划规则 本公司采用订单式生产管理方式与半成品库存式生产管理方式相结合,特殊类型订单按照客服部门下达订单后计划员按照产品工艺安排生产车间进行生产,常规订单由计划员进行半成品备料式生产。 一、订单交期确定规则 1.1 客服部订单后识别订单类型为普通订单还是特殊订单,普通订单直接输入ERP,特殊订单交由计划科评审后由客服部输入ERP,客服部将订单输入到ERP时必须输入明确的订单编号、产品名称、技术要求、要求交货时间等内容。 1.2 计划科每天(上午下班前或下午下班前)集中从ERP 系统中对客服所下达订单要求交货时间进行排程后立即集中回复(如遇加急订单客服可以通过电话通知等方式通知计划人员及时回复要求交货时间)。 1.3 客服部对计划科回复的时间进行确认,当计划科回复时间与客户要求交货时间一致时计划回复时间即为该订单确定的交货时间,当计划科回复时间晚于客户要求交货时间时客服部门应与营销人员一同与客户进行交流。 1.4 客服部与营销人员同客户进行交流后,顾客同意按计划科回复时间作为交货时间的则回复时间作为该订单确定的交货时间,如顾客不同意按计划科回复的时间作为交货时间的(可能坚持原交货时间、可能适当延期几天的)该订单确定的交货时间为顾客要求时间,客服部应及时将信息书
面通知计划科,计划科接到通知后按插单或订单提前进行处理。 二、车间生产计划排程规则 2.1 生产车间按某个产品在本车间总体生产状况进行产能平衡后列出《xxx车间产能表》 例:锁芯机加车间818锁 818锁包涵零部件:818锁管、818锁芯 零部件生产产能:818锁管 9000pcs/8h 818锁芯8000pcs/8h 产能平衡:对生产车间人、机、料、法、环进行调整,如锁管每八小时能生产9000只减少一点,多余出来的资源用于提高锁芯产量,使锁芯八小时产量高于8000只,最终达到锁管八小时产量和锁芯八小时产量一致。 锁芯车间产能: 818锁——8700pcs/8h 2.2 生产车间产能在计划排程中的表示方法应按照车间生产特性制定,锁芯组装车间、拉手组装车间、抛光车间不受设备等其他硬性因素影响不同产品可以并行生产,因此上述车间当日总产能为《xxx车间产能表》中全部产能累加;冲压车间、压铸车间、锁芯机加车间受设备等其他硬性因素影响因 此,上述车间当日总产能为为多个(将如果生产这个产品是多少个的和可以同时生产那种产品多少个的进行累加)。 2.3计划员编制《XX订单排程计划表》,表格中应当包
订单计划表
订单计划表 篇一:订单计划书 篇一:订单计划规则 订单计划规则 本公司采用订单式生产管理方式与半成品库存式生产管理方式相结合,特殊类型订单按照客服部门下达订单后计划员按照产品工艺安排生产车间进行生产,常规订单由计划员进行半成品备料式生产。 一、订单交期确定规则 1.1客服部订单后识别订单类型为普通订单还是特殊订单,普通订单直接输入erp,特殊订单交由计划科评审后由客服部输入erp,客服部将订单输入到erp时必须输入明确的订单编号、产品名称、技术要求、要求交货时间等内容。 1.2计划科每天(上午下班前或下午下班前)集中从erp系统中对客服所下达订单要求交货时间进行排程后立即集中回复(如遇加急订单客服可以通过电话通知等方式通知计划人员及时回复要求交货时间)。 1.3客服部对计划科回复的时间进行确认,当计划科回复时间与客户要求交货时间一致时计划回复时间即为该订单确定的交货时间,当计划科回复时间晚于客户要求交货时间时客服部门应与营销人员一同与客户进行交流。
1.4客服部与营销人员同客户进行交流后,顾客同意按计划科回复时间作为交货时间的则回复时间作为该订单确定的交货时间,如顾客不同意按计划科回复的时间作为交货时间的(可能坚持原交货时间、可能适当延期几天的)该订单确定的交货时间为顾客要求时间,客服部应及时将信息书面通知计划科,计划科接到通知后按插单或订单提前进行处理。 二、车间生产计划排程规则 2.1生产车间按某个产品在本车间总体生产状况进行产能平衡后列出《xxx车间产能表》例:锁芯机加车间818锁 818锁包涵零部件:818锁管、818锁芯 零部件生产产能:818锁管9000pcs/8h818锁芯8000pcs/8h 产能平衡:对生产车间人、机、料、法、环进行调整,如锁管每八小时能生产9000只减少一点,多余出来的资源用于提高锁芯产量,使锁芯八小时产量高于8000只,最终达到锁管八小时产量和锁芯八小时产量一致。 锁芯车间产能:818锁——8700pcs/8h 2.2生产车间产能在计划排程中的表示方法应按照车间生产特性制定,锁芯组装车间、拉手组装车间、抛光车间不受设备等其他硬性因素影响不同产品可以并行生产,因此上述车间当日总产能为《xxx车间产能表》中全部产能累加;冲压车间、压铸车间、锁芯机加车间受设备等其他硬性因素影响因此,上述车间当日总产能为为多个(将如果生产这个产品是多少个的和可以同时生产那种产品多少个的进行
客户订单生产流程
客户订单生产发货流程
面向订单生产 在面向订单生产的方式中,产品的设计工作已经完成,而生产用的物料尚未订购。在此环境中销售量通常较小,而客户则必须等待进货和生产所需的时间。全部交货提前期包括物料采购时间和生产时间。 最终产品在收到客户订单后才能确定。接到订单后,才开始组织采购和生产。 特点 1. 产品种类比较多。由于是按单生产,且客户订单的细节要求往 面向订单生产业务过程回顾 往各不相同,就导致了面向订单生产的企业的产品种类比较多。 2. 需求波动比较大。这种波动包括需求时间和数量上的波动。有的产品,客户可能只下一次订单,后面就再也没有订单了;而有的产品生命周期远远大于设计的生命周期。另外,需求的数量受市场的影响也很不稳定,波动很大。 3. 单个订单对产品的需求数量相对比较小,即“需求少量多样”。 4. 需求变更频繁。产品的生产提前期(Lead Time)相对比较长。因此正所谓的“夜长梦多”,在这个期间内客户变更需求的机会就比较大。这种变更包括:增加或取消订单,交期的提前或延后,数量的增加或减少,产品结构或包装方式的变更,甚至原来要A产品,现在改要B产品等。 5. 紧急订单(Rush order)多,插单多;较长的生产提前期往往超出客户的期望。客户通过各种方式(如联系公司高层)提升订单的优先级,以获得期望交期。 6. 产品的生产过程比较复杂,生产中多会用到长采购提前期的关键物料和复杂的生产工艺。 管理难点
正是由于生产模式以上的特点,决定了在面向订单生产的企业管理中会有许多的管理难点。以下简要列出一些计划、采购、工程和财务成本部门的管理难点。 生产及计划管理 ◇物料/能力计划 面向订单生产的计划是非常重要的。计划做得好,既可以提升客户的满意度,又可以提高生产的效率,同时保持库存在一个合理的水平。计划做得不好则会造成库存很高,但生产线还是断线,客户交货达不成。由于MTO企业的产品一般比较复杂,加工工艺繁琐,因此手工进行物料和能力计划的难度会非常大。特别是对于共用物料的数量计算和共用设备或产线产能的分配往往是计划人员最头痛的事情。另外,由于计划不完备导致的频繁的缺料断线,大大吞噬了企业的生产效能和利润。还有就是各加工部门步调不一,使得最后的装配部门经常是“前松后紧”:前半周或前半月没有活干,后半周或后半月加班加点还是干不完。 ◇任务单变更/改制 由于客户需求的不断变化,经常会导致生产任务单要做变更或改制的处理,影响生产的正常进行。经常见到的情况是:仓库的料已经发到产线了,需求取消了;或者是A已经加工到半成品了,客户又不要A而要B了等等。另外这种变更和改制的处理同样增加了生产计划和执行的难度。 ◇车间管理 MTO企业的产品加工工艺一般比较复杂,因此车间的管理难度也较大。在进行派工的时候要兼顾考虑订单的紧急程度,物料是否齐备,设备负荷是否合理,模具状况是否良好,技能人员是否到位等等。同时,要做大量的手工的工序汇报,甚至要计算工人的计时计件工资。 ◇物料替代 在安排生产时,对共用料需要考虑物料的替代关系,以合理利用现有库存。有的物料替代是临时性的;而有的物料替代关系是一直有效的。对于隶属于单个客户订单的专用物料,
订单生产计划控制流程图
订单生产计划控制流程图
5.工作流程描述 生产计划部主计划员在接到客户下达的产品订单后,交给合同管理员进行汇总录入合同清单。录入完毕后,合同管理员将订单交还给主计划员。 主计划员先对产品进行判断,如果是科研产品,则交给生产计划员进入到‘科研产品订单评估分析流程’,再进入到‘5.3 物料信息的评估’。 5.1 主生产计划表的编制 5.1.1 如果是常规产品,主计划员根据需求制定相关备品计划,将其与产品订单一 起交给生产计划员。 5.1.2 生产计划员对产品订单的交货期进行初步判定,如果交货期不能够满足正常 生产周期,则由生产计划员依据关键物料对交货期进行初步调整。 5.1.3 生产计划员将客户下达的产品订单中的最终产品与主计划员制定的备品计划 中的最终产品录入到《主生产计划表》中,客户下达的生产订单的计划类别 为“确认”、计划部制定的备品计划的计划类别为“常备”。同时将客户下达 的生产订单中的非最终产品与计划部制定的备品计划中的非最终产品录入到 ‘MRPII物料需求计划模块’的‘独立需求’中。 5.2 常规产品的工艺信息评估 5.2.1 生产计划员确定常规产品是否有完整的图纸及调试文件,如果没有,则由生 产计划员制定《常规产品订单评估表》,并将其以邮件的方式发给工程技术部。 5.2.2 工程技术部对订单的图纸和相关调试文件进行确认,在收到评估表后的一个 工作日内以邮件的方式回复《常规产品订单评估表》。 5.3 物料信息的评估 5.3.1 生产计划员确定是否有明确的物料信息,如果物料信息不明确,则根据产品 订单的项目数量和加急程度确定订单类型,订单类型分为下述两种情况: A 项目数量较少的加急订单 B 除第一种情况之外的所有订单 5.3.2 如果生产计划员确认订单属于上述情况A,按如下方式进行评估: ⑴由生产计划员制定《常规产品订单评估表》,并将其以邮件的方式发给采 购部。
订单生产管理流程
3.1.6工作节点和部门分工 订单评审管理流程执行说明
3.2订单协调管理流程 3.2.1该流程由公司销售部部门组织研发部、生产部、品质部、综合部、销售部,根据客户提出的特殊技术要求,进行产品结构和工艺参数的确定。(针对特殊订单) 3.2.2确定后的产品结构和工艺参数。报研发部总监签批。 3.2.2.1研发部需提供新的:图纸、工艺资料、物料清单(BOM)(BOM)的编制,产品试制的,技术测试试、终试到样品。 3.2.2.2订单评审确认上述资料完全,由资材部下达《订单执行通知书》,进入《工单作业计划管理流程》。
3.2.4工作节点及部门分工 订单协调管理流程说明
3.3.订单计划生产综合管理流程 3.3.1本流程主要节点是对前两个流程的跟进。 3.3.2相关部门根据《订单执行通知书》 3.3.2.1一般订单 3.3.2.1.1启动生产正常流程,纳入生产体系管理 3.3.2.1.2编制生产综合计划并上报管理层 3.3.2.2特殊订单 3.3.2.2.1编制生产综合计划并上报管理层 3.3.2.2.2制定生产工艺,编制技术规程。 3.3.2.2.3制定产品原材料、半成品、产成品检验标准、检验方法。 3.3.2.2.4安排生产,检查生产设备状况。 3.3.2.2.5查看材料库存,编写材料购进表,交管理层。 3.3.2.2.6协调劳动组织进行产品加工。 3.3.2.2.7编写加工纠偏措施。 3.3.2.2.7填报日生产计划报表上报,并安排值班人员按时汇报日产量。 3.3.3研发部、销售部跟踪生产进度,协助解决生产技术、装备事宜。 3.3.4质管部跟踪质量检验。 3.3.5流程图:
项目订单管理流程
项目、订单管理流程 一、目的: 对订单产品前期评审、设计、采购、生产、试验与检验过程和产品交货过程进行有效控制,使得订单执行有效运作,最终生产出合格的产品以满足客户的要求。 二、范围: 适用于成套事业部订单项目控制,产品生产全过程的控制,产品生产全过程中状态标识的控制和标识可追溯性的控制及产品交付。 三、职责: 1.市场部负责签订项目合同、产品技术协议,接到用户订单需求在ERP系统中做合 同及销售订单;成品出货通知、运输安排等。 2.项目计划负责根据客户订单要求,按照交期、产能、人力、设备状况制订项目主 计划、对各部门的计划达成状况进行追踪并统计分析、问题协调等,负责按计划排定需求日期,将原材、须加工物料按时、按质、按量追踪到位;负责生产、检验过程中缺件、缺陷情况反馈跟踪; 3.技术部:负责按计划期发放项目物料清单、项目图纸(电气图纸、结构图纸);负 责项目技术的完备性,为生产、检验提供技术支持;负责生产、检验过程中设计问题的及时处理解决。 4.采购部:根据项目主计划制定物料计划,负责按预计到料期限跟催到料;对生产、 检验过程中不合格品的及时处理。 5.生产部:负责生产设施的维护保养;负责员工操作技能的培训;负责根据项目计 划,安排各班组、各工序的局部计划,并按交期确实达成计划;对生产过程及产生的重大环境因素进行控制,负责对产品进行防护和标识;负责对工作环境控制; 各工序装配技术员负责各个工序的装配操作及自检,各班长负责各工序的工艺质量监督。 6.质检部:负责物料进货检验、产品过程、最终验证、标识及可追溯性的归口管理, 负责对各环节出现的不合格进行判定,并辅助采购部对生产、检验过程中不合格品的及时处理;负责组织对特殊过程进行确认,负责对关键工序进行检验。 7.仓储负责物料的验收、送检、入库、发料及成品入库等。 8.售后服务:负责产品交付后的处理,包括安装调试指导前的工作、安装指导、用
订单的计划书范文
订单的计划书范文 篇一:订单计划规则 本公司采用订单式生产管理方式与半成品库存式生产管理方式相结合,特殊类型订单按照客服部门下达订单后计划员按照产品工艺安排生产车间进行生产,常规订单由计划员进行半成品备料式生产。 一、订单交期确定规则 1.1客服部订单后识别订单类型为普通订单还是特殊订单,普通订单直接输入ERP,特殊订单交由计划科评审后由客服部输入ERP,客服部将订单输入到ERP时必须输入明确的订单编号、产品名称、技术要求、要求交货时间等内容。 1.2计划科每天(上午下班前或下午下班前)集中从ERP系统中对客服所下达订单要求交货时间进行排程后立即集中回复(如遇加急订单客服可以通过电话通知等方式通知计划人员及时回复要求交 货时间)。 1.3客服部对计划科回复的时间进行确认,当计划科回复时间与客户要求交货时间一致时计划回复时间即为该订单确定的交货时间,当计划科回复时间晚于客户要求交货时间时客服部门应与营销人员一同与客户进行交流。 1.4客服部与营销人员同客户进行交流后,顾客同意按计划科回复时间作为交货时间的则回复时间作为该订单确定的交货时间,如顾客不同意按计划科回复的时间作为交货时间的(可能坚持原交货时间、可能适当延期几天的)该订单确定的交货时间为顾客要求时间,
客服部应及时将信息书面通知计划科,计划科接到通知后按插单或订单提前进行处理。 二、车间生产计划排程规则 2.1生产车间按某个产品在本车间总体生产状况进行产能平衡后列出《xxx车间产能表》 例:锁芯机加车间818锁 818锁包涵零部件:818锁管、818锁芯 零部件生产产能:818锁管9000pcs/8h818锁芯8000pcs/8h 产能平衡:对生产车间人、机、料、法、环进行调整,如锁管每八小时能生产9000只减少一点,多余出来的资源用于提高锁芯产量,使锁芯八小时产量高于8000只,最终达到锁管八小时产量和锁芯八小时产量一致。 锁芯车间产能:818锁——8700pcs/8h 2.2生产车间产能在计划排程中的表示方法应按照车间生产特性制定,锁芯组装车间、拉手组装车间、抛光车间不受设备等其他硬性因素影响不同产品可以并行生产,因此上述车间当日总产能为《xxx 车间产能表》中全部产能累加;冲压车间、压铸车间、锁芯机加车间受设备等其他硬性因素影响因 此,上述车间当日总产能为为多个(将如果生产这个产品是多少个的和可以同时生产那种产品多少个的进行累加)。 2.3计划员编制《XX订单排程计划表》,表格中应当包含订单信息栏目(订单编号、产品名称、技术要求、要求交货时间)及各车
生产订单管理流程
订单管理流程 1.目的 加强公司生产订单流程管理,体现从销售到生产环节的无缝衔接,实现产品加工过程安全、高效、低耗、按期交货。 2、适应范围:深圳市鹏桑普太阳能股份有限公司产品事业部 3、流程管理层 3.1订单评审管理流程 3.1.1该流程由订单主管部门(内、外销部)组织产品事业部的研发部、生产部、品质部、综合部、销售部、合同签订人等对订单进行技术评审,提出处理意见。 3.1.2对能满足客户(合同)要求的一般订单准备技术、原材料预案,对技术偏离较大的特殊订单由销售部和客户进行沟通,达成处理意见,由销售部报请产品事业部领导签批。 3.1.3根据领导签批 3.1.3.1由订单主管部门(销售部)下达《订单通知书》,转入《订单作业计划管理流程》。 3.1.3.2客户同意方案的,由订单主管部门(销售部)进入《订单生产准备流程》。 3.1.3.3客户协商不成的,由销售部进行退单并做好退单记录。 3.1.4按公司规定合同额小于10万元、无特殊技术要求或库存直接提货的只报事业部领导签批,不再进行技术评审。
3.1.5流程图(图1) 销售部 PMC部综合部开发部所属相关部门 3.1.6工作节点和部门分工 订单评审管理流程执行说明
3.2订单协调管理流程 3.2.1该流程由公司销售部部门组织研发部、生产部、品质部、综合部、销售部,根据客户提出的特殊技术要求,进行产品结构和工艺参数的确定。(针对特殊订单) 3.2.2确定后的产品结构和工艺参数。报事业部技术开发总监签批。 3.2.3签批方案执行 3.2.3.1图纸、工艺资料、物料清单(BOM)(BOM)的编制,产品试制的,技术测试试、终试到样品。 3.2.3.2只做结构调整变化的,由订单主管部门下达《订单通知书》,进入《订单计划管理流程》。 3.2.4流程图 销售部门研发部生产部 PMC部采购部品管部
订货计划表
订单计划规则 本公司采用订单式生产管理方式与半成品库存式生产管理方式相结合,特殊类型订单按 照客服部门下达订单后计划员按照产品工艺安排生产车间进行生产,常规订单由计划员进行 半成品备料式生产。 一、订单交期确定规则 1.1 客服部订单后识别订单类型为普通订单还是特殊订单,普通订单直接输入erp,特 殊订单交由计划科评审后由客服部输入erp,客服部将订单输入到erp时必须输入明确的订 单编号、产品名称、技术要求、要求交货时间等内容。 1.2 计划科每天(上午下班前或下午下班前)集中从erp系统中对客服所下达订单要求 交货时间进行排程后立即集中回复(如遇加急订单客服可以通过电话通知等方式通知计划人 员及时回复要求交货时间)。 1.3 客服部对计划科回复的时间进行确认,当计划科回复时间与客户要求交货时间一致 时计划回复时间即为该订单确定的交货时间,当计划科回复时间晚于客户要求交货时间时客 服部门应与营销人员一同与客户进行交流。 1.4 客服部与营销人员同客户进行交流后,顾客同意按计划科回复时间作为交货时间的 则回复时间作为该订单确定的交货时间,如顾客不同意按计划科回复的时间作为交货时间的 (可能坚持原交货时间、可能适当延期几天的)该订单确定的交货时间为顾客要求时间,客 服部应及时将信息书面通知计划科,计划科接到通知后按插单或订单提前进行处理。 二、车间生产计划排程规则 2.1 生产车间按某个产品在本车间总体生产状况进行产能平衡后列出《xxx车间产能表》 例:锁芯机加车间818锁 818锁包涵零部件:818锁管、818锁芯 零部件生产产能:818锁管 9000pcs/8h 818锁芯 8000pcs/8h 产能平衡:对生产车间人、机、料、法、环进行调整,如锁管每八小时能生产9000只减 少一点,多余出来的资源用于提高锁芯产量,使锁芯八小时产量高于8000只,最终达到锁管 八小时产量和锁芯八小时产量一致。 锁芯车间产能: 818锁——8700pcs/8h 2.2 生产车间产能在计划排程中的表示方法应按照车间生产特性制定,锁芯组装车间、 拉手组装车间、抛光车间不受设备等其他硬性因素影响不同产品可以并行生产,因此上述车 间当日总产能为《xxx车间产能表》中全部产能累加;冲压车间、压铸车间、锁芯机加车间 受设备等其他硬性因素影响因 此,上述车间当日总产能为为多个(将如果生产这个产品是多少个的和可以同时生产那 种产品多少个的进行累加)。 2.3计划员编制《xx订单排程计划表》,表格中应当包含订单信息栏目(订单编号、产品 名称、技术要求、要求交货时间)及各车间生产排程信息(零部件名称、零部件编号、技术 要求、计划生产数量、正常生产时间、计划开始生产时间、计划完成生产时间)。 2.4 计划员从erp中收到订单后直接从系统中导出相应信息,如明确的订单编号、产品 名称、技术要求、要求交货时间、生产零部件构成(到车间生产的零部件即可),填写到《xx 订单排程计划表》中,《xx订单排程计划表》应当在公司局域网内建立对应的映像文件便于 相关部门和人员进行订单进度查询。 2.5 计划员根据仓库库存情况确定各零部件在各车间的计划生产数量,根据各车间提供 的产能表计算该零部件在对应的车间生产需要的时间,并根据该产品的生产工艺过程、对应 零部件生产车间原排程计划计算该零部件在对应车间的计划开始生产时间、计划完成生产时 间。