汽车差速器壳加工工艺及夹具设计 (张武聪)1学士学位论文

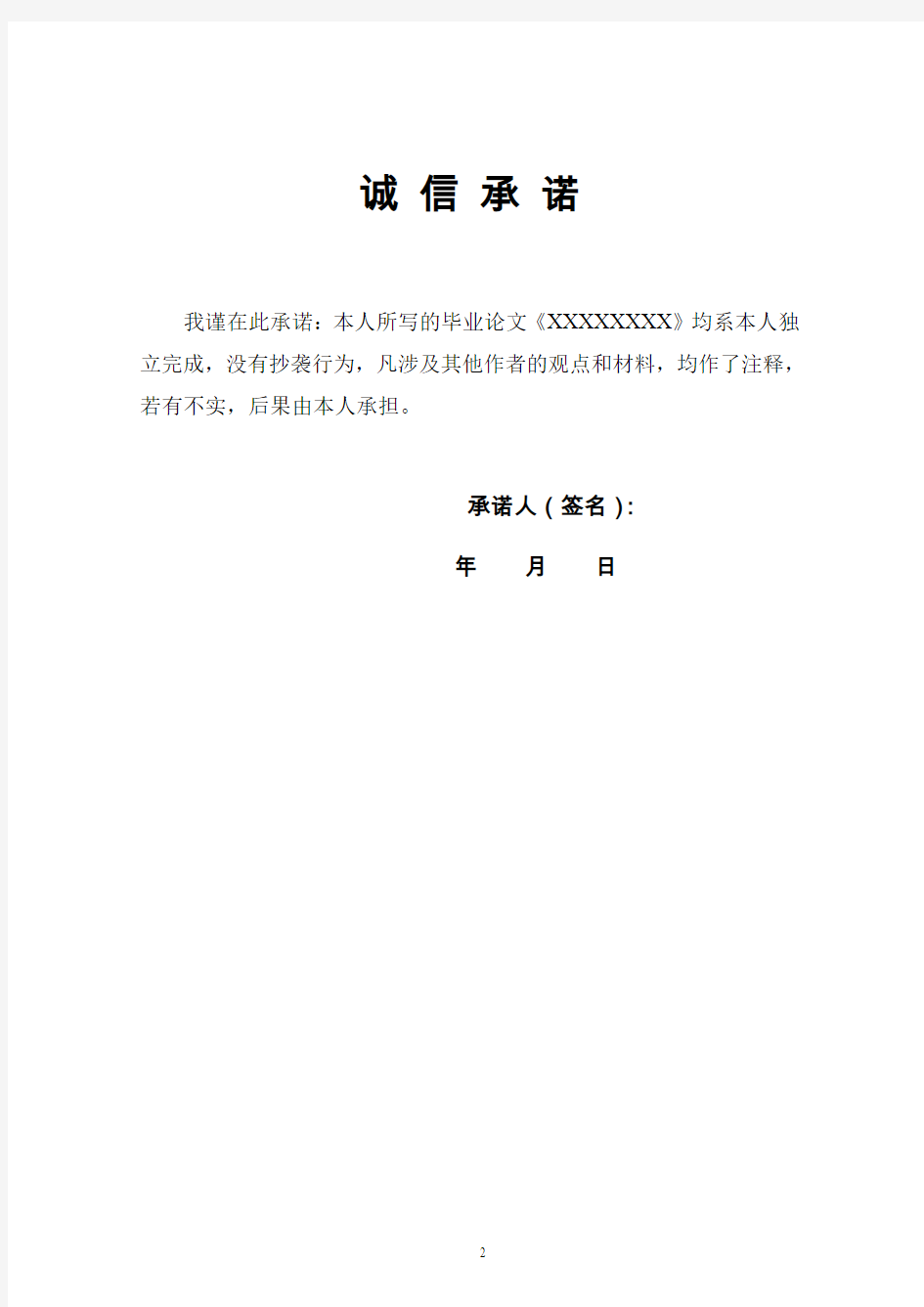
分 类 号
密 级
宁波大红鹰学院
毕业设计(论文)
毕业设计(论文)题目
所在学院
专 业 班 级 姓 名 学 号 指导老师
年 月 日
诚信承诺
我谨在此承诺:本人所写的毕业论文《XXXXXXXX》均系本人独立完成,没有抄袭行为,凡涉及其他作者的观点和材料,均作了注释,若有不实,后果由本人承担。
承诺人(签名):
年月日
摘要
在机床上加工工件时,定位和夹紧的全过程称为“安装”。在机床上用来完成工件安装任务的重要工艺装备,就是各类夹具中应用最为广泛的“机床夹具”。
机床夹具的种类很多,其中,使用范围最广的通用夹具,规格尺寸多已标准化,并且有专业的工厂进行生产。而广泛用于批量生产,专为某工件加工工序服务的专用夹具,则需要各制造厂根据工件加工工艺自行设计制造。本设计的主要内容是设计钻床夹具和铣床夹具,需要对零件上Φ22的孔进行铣削加工端面的铣削加工。
在机械加工中,孔的加工量所占比例较大,其中钻头、扩孔钻、铰刀、镗刀等定尺寸刀具加工占相当多数。这时,除了要保证孔的尺寸精度外,还要达到孔的位置精度要求。在单件小批量生产中,用划线后找正孔轴线位置方法加工。在批量生产中一般都采用钻床夹具与镗床夹具,钻床夹具又称钻模通过钻套引导刀具进行加工可准确地确定刀具与工件之间的相对位置。
摘要的内容构成要素:
目的、方法、对象和结论称为摘要的四要素。
(1)目的:毕业论文研究的范围,目的,重要性。
(2)方法:毕业论文的使用了哪些研究方法。
(3)成果:陈述毕业论文研究成果。
(4)结论:通过对问题的研究所得出的重要结论及主要观点。
关键词通用夹具专用夹具钻床夹具铣床夹具
Abstract
In machining the workpiece, positioning and clamping, the process is called " installation". On machine tool workpiece installation tasks to complete the important craft equipment, various types of fixture is the most widely used" machine tool fixture".
Machine tool fixture of many kinds, among them, the most widely used common fixture, size specifications have been standardized, and a professional production plant. While widely used in batch production, designed for a certain workpiece processing services for the fixture, it needs each factory according to workpiece machining technology to design and manufacture. The main contents of this design is the design of drilling jig and milling fixture, the need for parts than22hole milling face milling.
In the machining process, machining quantity larger proportion, wherein the drill bit, drill, reamer, boring cutter, sizing tool processing most. At this time, in addition to ensure hole size precision, but also to reach the hole position accuracy. In the single and small batch production, scribing for hole processing method of axis position. In the mass production are generally used in drilling jig and the jig boring machine, drilling jig is also called drilling die through the drill guide sleeve tool for processing can be accurately determined the relative position between the tool and the workpiece.
Key Words:Universal, jig , fixture for drilling, fixture for milling machine
目录
摘要 (1)
Abstract (2)
目录 (3)
第1章绪论 (5)
1.1 课题的背景及意义 (5)
1.2 差速器的主要分类 (5)
1.2.1 开式差速器 (5)
1.2.2 限滑差速器 (6)
1.3 差速器结构 (6)
1.3论文主要内容 (7)
2 零件的分析 (7)
2.1 零件的作用 (7)
2.2 零件的工艺分析 (8)
3 工艺规程设计 (9)
3.1 毛坯的制造形式 (10)
3.2 基准面的选择 (10)
3.2.1 粗基准的选择 (10)
3.2.2 精基准的选择 (10)
3.3 制订工艺路线 (10)
3.3.1. 工艺线路方案一 (11)
3.3.2 工艺路线方案二 (11)
3.3.3. 工艺方案的比较与分析 (11)
3.4 机械加工余量、工序尺寸及毛坯尺寸的确定 (12)
3.4.1 外圆表面 (12)
3.5 内圆表面 (14)
3.4.3 端面 (15)
3.4.4 凸台孔系 (15)
3.5 确定切削用量及基本工时 (16)
第4章钻孔夹具设计 (43)
4.1问题的提出 (43)
4.2定位基准的选择 (43)
4.3 定位元件与夹紧元件的选择 (43)
4.3切削力与夹紧力的计算 (44)
4.4钻套、衬套、钻模板及夹具体设计 (44)
4.5夹具精度分析 (47)
4.6本章小结 (48)
第5章铣小头端面夹具设计 (48)
5.1定位基准的选择 (48)
5.2 定位方案和元件设计 (48)
5.3 夹紧机构的设计 (48)
5.4 定位误差的计算 (49)
5.5本章小结 (49)
结论 (50)
参考文献 (51)
致谢 (52)
第1章绪论
1.1 课题的背景及意义
差速器的作用就是使两侧车轮转速不同。当汽车转弯时,例如左转弯,弯心在左侧,在相同的时间内右侧车轮要比左侧车轮走过的轨迹要长,所以右侧车轮转的要更快一些。要达到这个效果,就得通过差速器来调节。差速器由差速器壳、行星齿轮、行星齿轮轴和半轴齿轮等机械零件组成。
发动机的动力经变速器从动轴进入差速器后,直接驱动差速器壳,再传递到行星齿轮,带动左、右半轴齿轮,进而驱动车轮,左右半轴的转速之和等于差速器壳转速的两倍。当汽车直线行驶时,行星齿轮,左、右半轴齿轮和驱动车轮三者转速相同。当转弯时,由于汽车受力情况发生变化,反馈在左右半轴上,进而破坏差速器原有的平衡,这时转速重新分配,导致内侧车轮转速减小,外侧车轮转速增加,重新达到平衡状态,同时,汽车完成转弯动作。
差速器就是一种将发动机输出扭矩一分为二的装置,允许转向时输出两种不同的转速。
差速器有三大功用:把发动机发出的动力传输到车轮上;充当汽车主减速齿轮,在动力传到车轮之前将传动系的转速减下来;将动力传到车轮上,同时,允许两轮以不同的轮速转动。
当汽车转向时,车轮以不同的速度旋转。在转弯时,每个车轮驶过的距离不相等,即内侧车轮比外侧车轮驶过的距离要短。因为车速等于汽车行驶的距离除以通过这段距离所花费的时间,所以行驶距离短的车轮转动的速度就慢。
1.2 差速器的主要分类
1.2.1 开式差速器
开式差速器的结构,是典型的行星齿轮组结构,只不过太阳轮和外齿圈的齿数是一样的。在这套行星齿轮组里,主动轮是行星架,被动轮是两个太阳轮。通过行星齿轮组的传动特性我们知道,如果行星架作为主动轴,两个太阳轮的转速和转动方向是不确定的,甚至两个太阳轮的转动方向是相反的。
车辆直行状态下,这种差速器的特性就是,给两个半轴传递的扭矩相同。在一个驱动轮悬空情况下,如果传动轴是匀速转动,有附着力的驱动轮是没有驱动力的,如果传
动轴是加速转动,有附着力的驱动轮的驱动力等于悬空车轮的角加速度和转动惯量的乘积。
车辆转弯轮胎不打滑的状态下,差速器连接的两个半轴的扭矩方向是相反的,给车辆提供向前驱动力的,只有内侧的车轮,行星架和内侧的太阳轮之间由等速传动变成了减速传动,驾驶感觉就是弯道加速比直道加速更有力。
开式差速器的优点就是在铺装路面上转行行驶的效果最好。缺点就是在一个驱动轮丧失附着力的情况下,另外一个也没有驱动力。
开式差速器的适用范围是所有铺装路面行驶的车辆,前桥驱动和后桥驱动都可以安装。
1.2.2 限滑差速器
限滑差速器用于部分弥补开式差速器在越野路面的传动缺陷,它是在开式差速器的机构上加以改进,在差速器壳的边齿轮之间增加摩擦片,对应于行星齿轮组来讲,就是在行星架和太阳轮之间增加了摩擦片,增加太阳轮与行星架自由转动的阻力力矩。
限滑差速器提供的附加扭矩,与摩擦片传递的动力和两驱动轮的转速差有关。在开式差速器结构上改进产生的LSD,不能做到100%的限滑,因为限滑系数越高,车辆的转向特性越差。
LSD具备开式差速器的传动特性和机械结构。优点就是提供一定的限滑力矩,缺点是转向特性变差,摩擦片寿命有限。 LSD的适用范围是铺装路面和轻度越野路面。通常用于后驱车。前驱车一般不装,因为LSD会干涉转向,限滑系数越大,转向越困难。1.3 差速器结构
当汽车转弯行驶时,外侧车轮比内侧车轮所走过的路程长;汽车在不平路面上直线行驶时。两侧主轮走过的曲长短也不相等.即伸路面非平直,但由于轮胎制造尺寸误差,磨损程度不同,承受的载荷不同或充气压力不等,各个轮胎的滚动半径实际上不可能相等,若两侧车轮都固定在同一刚性转轴上,两轮角速度相等,则车轮必然出现边滚动边滑动的现象。车轮对路面的滑动不仅会加速轮胎磨损,增加汽车的动力消耗,而且可能导致转向和制动性能的恶化。若主减速器从动齿轮通过一根整轴同时带动两侧驱动轮,则两侧车轮只能同样的转速转动。为了保证两侧驱动轮处于纯滚动状态,就必须改用两根半轴分别连接两侧车轮,而由主减速器从动齿轮通过差速器分别驱动两侧半轴和车轮,使它们可用不同角速度旋转。这种装在同一驱动桥两侧驱动轮之间的差速器称为轮间差速器。
增加“国内外研究现状”一节内容,此节内容要写出差速器壳体加工工艺和夹具设计国内外研究现状,没有这方面内容,就不针对差带壳体写,那就写机械加工艺和夹具设计方面。
1.3论文主要内容
本论文的主要内容有:对差速器及常用差速器功能、作用及结构作一介绍。主要针对差速器壳体安排合理的加工工艺,在这方面要考虑如下几个问题:零件的精度、结构工艺性,零件的毛坯及生产纲领、粗精基准的选择,表面的加工方法,切削用量及工时,设计专用夹具,如确定定位方式、夹紧方式、夹紧元件、夹紧力,夹具的操作及维护等,贯穿起来,这是一篇集原理、生产、加工、使用合一的论文。
每章要有小结
2 零件的分析
2.1 零件的作用
题目所给定的零件是解放牌汽车的后桥差速器壳(见附录A)。汽车差速器是驱动轿的主件。差速器的作用就是在向两边半轴传递动力的同时,允许两边半轴以不同的转速旋转,满足两边车轮尽可能以纯滚动的形式作不等距行驶,减少轮胎与地面的摩擦。普通差速器由行星齿轮、差速器壳(行星轮架)、半轴齿轮等零件组成。发动机的动力经传动轴进入差速器,直接驱动差速器壳带动行星轮轴,再由行星轮带动左、右两条半轴,分别驱动左、右车轮。
上面图打印出来会看不清楚,放在附录A 中好了。
2.2 零件的工艺分析
差速器壳的零件可以分四组加工表面,图中规定了一系列技术要求:现分叙如下:
1.零件上各段外圆表面:
ф50
018
.0
002
.0
+
+公差等级 IT6,粗糙度Ra 1.6。
ф1540
04
.0
-公差等级 IT7,粗糙度Ra 1.6。
ф200 粗糙度Ra 12.5。ф150 粗糙度Ra 6.3。
2.内圆孔表面:
ф40
33
.0
17
.0
+
+公差等级IT11,粗糙度Ra 6.3。
ф50
039
.0
+
公差等级IT8,粗糙度Ra 1.6。
ф122
016
.0
+
公差等级IT10 ,粗糙度Ra 6.3。
ф130
04
.0
+
公差等级IT7。
3.端面:
ф50端面,粗糙度Ra 12.5
ф50
039
.0
+
台阶面,粗糙度Ra 3.2
ф200前端面,粗糙度Ra6.3 ф200后端面,粗糙度Ra3.2 4.凸台孔系
凸台上距中心线74.50
5.0
-的平面,粗糙度Ra 6.3
2×ф22H8 公差等级IT8,粗糙度Ra 3.2。
2×ф8H8 公差等级IT8,粗糙度Ra 3.2。
ф4H13 公差等级IT8
12×ф12.5
他们之间的要求:
1.基准A2为孔ф50H8,基准A3为孔ф130H7。
2.ф50外圆对A2-A3基准的跳动为0.03,位置度为ф0.03,精度等级:6级。
3.ф154、ф122内孔对A2-A3基准跳动为0.05,精度等级:8级。
4.两ф20孔之间的同轴度要求为0.025,精度等级: 6级。
5.ф200端面及后端面对基准A2-A3的跳动为0.05、0.06,精度等级:8级。
6.两ф20孔对A2-A3基准位置度为ф0.06,精度等级:8级。
7.ф8H孔对两ф20孔的位置度为0.1,精度等级:8级。
8.12个ф12.5的孔对A3的位置度为0.2,精度等级:8级。
由上分析可知,对于这几组加工表面,可以先加工好端面,内外圆表面可以用加工好的端面为基准先加工其中一组,然后借助专用夹具加工另一表面,并且保证它们之间的位置精度要求。
3 工艺规程设计
增加:确定零件的生产类型一节内容
按2000 台\年计算该零件生产纲领,再确定该零件生产类型
3.1 毛坯的制造形式
零件材料为QT420-10,球墨铸铁中的石墨呈球状,具有很高的强度,又有良好的塑性和韧性,起综合性能接近钢,其铸性能好,成本低廉,生产方便,工业中广泛应用。生产纲领:大批量生产,而且零件轮廓尺寸不大,故可以采用砂型机械造型,这从提高生产率、保证加工精度上考虑,也是应该的。
增加:毛坯形状,各主要加工面毛坯余量的确定一节内容
增加:绘制毛坯图一节
3.2 基准面的选择
基面的选择是工艺规程设计中的重要工作之一,基面选择的正确与合理,可以使加工质量得到保证,生产率得以提高。否则,加工工艺过程中会问题百出,更有甚者,还会造成零件大批报废,使生产无法正常进行。
3.2.1 粗基准的选择
按照有关的粗基准选择原则(保证某重要表面的加工余量均匀时,选该表面为粗基准。若工件每个表面都要求加工,为了保证各表面都有足够的余量,应选择加工余量最小的表面为粗基准,若工件必须保证不加工表面与加工表面之间的尺寸或位置要求,如壁厚均匀,先取不加工表面做粗基准)可以取铸件的大端作粗基准加工小端面,再以小端面为基准加工大端面,也可以取铸件的两个凸台作为粗基准,先加工好端面和要求不高的ф200外圆。
3.2.2 精基准的选择
按照有关的精基准选择原则(互为基准原则;基准统一原则;可靠方便原则),对于本零件,外圆和内圆两组加工表面相互之间有一定的精度要求,内圆粗加工时可以先选择加工好的端面作为加工基准,再以粗加工好的内圆表面为基准粗加工外圆表面,然后以粗加工好外圆表面为基准精加工内圆,最后再以基准精加工好的内圆精加工外圆。
后面加工零件肩上的行星轮轴孔可以用夹具以大端面为基准铣出两侧平面,再用专用夹具以端面和平面为基准加工孔。
3.3 制订工艺路线
制订工艺路线的出发点,应当是使零件的几何形状、尺寸精度以及位置精度等技术
要求能得到合理的保证。在生产纲领已经确定为中批生产的条件下,考虑采用普通机床配以专用夹具,多用通用刀具,万能量具。部分采用专用刀具和专一量具。并尽量使工序集中来提高生产率。除此以外,还应当考虑经济效果,以便使生产成本尽量下降。
3.3.1. 工艺线路方案一
工序Ⅰ铸造。
工序Ⅱ热处理:正火。
工序Ⅲ铣两端面。
工序Ⅳ粗、半精车ф50、ф150、ф154外圆,车ф200外圆,
工序Ⅴ粗镗ф40、ф50、ф122、ф130孔。
工序Ⅵ精镗ф50及端面、ф40、ф122、ф130孔,倒角。
工序Ⅶ精车ф50,ф154外圆及端面,倒角。
工序Ⅷ铣两凸台上平面。
工序Ⅸ钻ф4孔。
工序Ⅹ钻、绞两组ф22、ф8孔,ф8孔倒角。
工序Ⅺ钻大端法兰上12个ф12.5孔。
工序Ⅻ去毛刺,检查。
3.3.2 工艺路线方案二
工序Ⅰ铸造。
工序Ⅱ热处理:退火。
工序Ⅲ粗车、精车ф200及端面,倒角,钻ф40孔,粗镗ф40、ф50孔及端面、ф122、ф130孔。
工序Ⅳ粗、半精车ф50、ф154外圆及端面,车凸台上ф150外圆。
工序Ⅴ精镗ф50及端面、ф122、ф130孔,倒角。
工序Ⅵ精车ф50,ф154外圆及端面,倒角。
工序Ⅶ铣两凸台上平面。
工序Ⅷ钻ф4孔。
工序Ⅸ钻、绞两组ф22、ф8孔,ф8孔倒角。
工序Ⅹ钻大端法兰上12个ф12.5孔。
工序Ⅺ去毛刺,检查。
3.3.3. 工艺方案的比较与分析
上述两个方案的特点在于:方案一在铣床上先加工小端面,再以小端面定位加工大
端面,方案二是在车床上车出大端面,直接粗镗内孔,然后以孔和大端面定位,加工其它部分。两相比较起来可以看出,方案二的装夹次数要少于前者,精度更高,对工人的技术水平要求低一些。在大批生产中,综合考虑,我们选择工艺路线一。
工序Ⅰ铸造。
工序Ⅱ热处理:正火。
工序Ⅲ铣两端面。
工序Ⅳ粗、半精车ф50、ф150、ф154外圆,车ф200外圆,
工序Ⅴ粗镗ф40、ф50、ф122、ф130孔。
工序Ⅵ精镗ф50及端面、ф40、ф122、ф130孔,倒角。
工序Ⅶ精车ф50,ф154外圆及端面,倒角。
工序Ⅷ铣两凸台上平面。
工序Ⅸ钻ф4孔。
工序Ⅹ钻、绞两组ф22、ф8孔,ф8孔倒角。
工序Ⅺ钻大端法兰上12个ф12.5孔。
工序Ⅻ去毛刺,检查。
3.4 机械加工余量、工序尺寸及毛坯尺寸的确定
差速器壳零件材料为QT420-10,硬度为156~197HBS,毛坯质量约为2.4kg,生产类型为中批生产,采用砂型机械造型铸造。查《机械制造工艺设计简明手册》表2.2-5,毛坯铸造精度等级取9G。
根据上述材料及加工工艺,分别确定各加工表面的机械加工余量、工序尺寸及毛坯尺寸如下:
3.4.1 外圆表面
⑴.ф50mm
查《机械制造工艺设计简明手册》表2.2—1至2.2—4,加工余量2.5mm,尺寸公差为2,所以其外圆毛坯名义直径为ф55 1mm。参照《机械制造工艺设计简明手册》2.3—2至2.3—5,确定ф50外圆的加工余量
和工序间余量分布见下图:
图1-1毛坯余量分布图
由图可知:
毛坯名义直径:50+2.5×2=55 mm
毛坯最大直径:55+2/2=55 mm
毛坯最小直径:55-2/2=53 mm
粗车后最大直径:55-3.5=51.5 mm
粗车后最小直径:51.5-0.39=51.11 mm
半精车后最大直径:51.5-1.2=50.3 mm
半精车后最小直径:50.3-0.062=50.238 mm
精车后尺寸为零件尺寸,即ф50018.0002.0+
+ mm
将上刚上叙计算的工序间尺寸及公差整理成表1.1。
表1.1 加工余量计算表
⑵.ф200
查《机械制造工艺设计简明手册》表2.2—1至2.2—4,加工余量为4mm ,尺寸公差为2.8,所以其外圆毛坯名义直径为ф208±1.4mm 。
参照《机械制造工艺设计简明手册》2.3—2至2.3—5,确定各工序尺寸及余量为: 毛坯:ф208±
1.4mm
车:ф200mm 2Z=8mm
⑶.ф154
查《机械制造工艺设计简明手册》表2.2—1至2.2—4,加工余量为3mm ,尺寸公差为2.5,所以其外圆毛坯名义直径为ф160±1.25mm 。参照《机械制造工艺设计简明手册》2.3—2至2.3—5,确定各工序尺寸及余量为:
毛坯:ф160±1.25mm
粗车:ф155.60
63.0-mm 2Z=4.4mm
半精车:ф154.30
1.0-mm 2Z=1.3mm
精车:ф1540
04.0-mm 2Z=0.3mm
⑷.ф150
查《机械制造工艺设计简明手册》表2.2—1至2.2—4,加工余量为3mm ,尺寸公差为2.5,所以其外圆毛坯名义直径为ф156±1.25mm 。参照《机械制造工艺设计简明手册》2.3—2至2.3—5,确定各工序尺寸及余量为:
毛坯:ф156±1.25mm
车:ф150mm 2Z=6mm
3.5 内圆表面
⑴.ф130mm
查《机械制造工艺设计简明手册》表2.2—1至2.2—4,加工余量3mm ,尺寸公差为2.5,所以其孔毛坯名义直径为ф124±1.25mm 。参照《机械制造工艺设计简明手册》
2.3—8至2.3—12,确定各工序尺寸及余量为:
毛坯:ф124±1.2mm
粗镗:ф129.563.00+mm 2Z=5.5mm
半精镗:ф129.916.00+mm 2Z=0.4mm
精镗:ф13004.00+mm 2Z=0.1mm
⑵.ф50mm
查《机械制造工艺设计简明手册》表2.2—1至2.2—4,加工余量2.5mm ,尺寸公差为2mm ,所以其孔毛坯名义直径为ф45±1mm 。参照《机械制造工艺设计简明手册》2.3—8至2.3—12,确定各工序尺寸及余量为:
毛坯:ф45±1mm
粗镗:ф49.663.00+mm 2Z=4.5mm
半精镗:ф49.91.00+mm 2Z=0.4mm
精镗:ф50039.00+mm 2Z=0.1mm
⑶.ф122mm
查《机械制造工艺设计简明手册》表2.2—1至2.2—4,加工余量3mm ,尺寸公差为2.5mm ,所以其孔毛坯名义直径为ф116±1.25mm 。参照《机械制造工艺设计简明手册》
2.3—8至2.3—12,确定各工序尺寸及余量为:
毛坯:ф45±1mm
粗镗:ф121.663.00+mm 2Z=5.5mm
半精镗:ф12216.00+mm 2Z=0.4mm
⑷.ф40mm
查《机械制造工艺设计简明手册》表2.2—1至2.2—4,加工余量2.5mm ,尺寸公差为2mm ,所以其孔毛坯名义直径为ф35±1mm 。参照《机械制造工艺设计简明手册》2.3—8至2.3—12,确定各工序尺寸及余量为:
毛坯:ф35±1mm
钻孔:ф39.5mm 2Z=4.5mm
镗: ф4033.017.0+
+mm 2Z=0.5mm
3.4.3 端面
⑴.ф200前端面
毛坯: 160mm
粗车:157mm Z=3mm
⑵. ф50端面
车前:157mm
粗车:153mm Z=4mm
⑶.ф50039.00+台阶面
车前: 135.5mm
粗车:134.50
39.0-mm Z=1mm
半精车:133.50
2.0-mm Z=1mm
⑷.ф200后端面
车前:11mm
粗车:90
39.0-mm Z=2mm
半精车:81.00+ mm Z=1mm
3.4.4 凸台孔系
⑴.凸台上平面
铣前:距中心线75
铣后:距中心线74.50
5.0-, Z=0.5mm
⑵.2×ф22H8孔
钻:ф20 2Z=20mm
扩钻:ф21.8 2Z=1.8mm
绞:ф22033.00+ 2Z=0.2mm
⑶.2×ф8H8孔
钻:ф7.8孔 2Z=7.8mm
绞:ф8022.00+ 2Z=0.2mm
⑷.ф4H13、12×ф12.5 孔
一次钻好即可。
3.5 确定切削用量及基本工时
工序Ⅰ 铸造。
工序Ⅱ 热处理:退火。
工序Ⅲ 粗车、精车大头ф200,倒角。粗镗ф5、ф122、ф130孔。
1 加工条件
工件材料:QT420-10,铸造
加工要求:铣ф200端面, Ra 6.3。
2 计算切削用量
⑴铣ф200端面
机床:X6022型卧式铣床
刀具:两块镶齿套式面铣刀(间距为80),材料:15YT ,200D mm = ,齿数20Z =,为粗齿铣刀。
因其单边余量:Z=3mm
所以铣削深度p a :3p a mm =
每齿进给量f a :根据参考文献[3]表2.4-73,取0.15/f a m m Z =铣削速度V :参照参考文献[3]表2.4-81,取 2.54/V m s =
机床主轴转速n :
10001000 2.5460242.68/min 3.14200
V n r d π??==≈?, 按照参考文献[3]表3.1-74 245/min n r =
实际铣削速度v : 3.14200245 2.56/1000100060
dn v m s π??==≈? 进给量f V :0.1520245/6012.25/f f V a Zn mm s ==??≈
工作台每分进给量m f :12.25/735/min m f f V mm s mm ===
εa :根据参考文献[3]表2.4-81,mm a 60=ε
切削工时
被切削层长度l :由毛坯尺寸可知42l mm =,
刀具切入长度1l :
10.5((1~3)l D =
+0.5(200(1~3)7.6mm =+=
刀具切出长度2l :取mm l 22=
走刀次数为1
机动时间1j t :121427.620.07min 735
j m l l l t f ++++=
=≈ 查参考文献[1],表2.5-45工步辅助时间为:1.23min
2.车ф200外圆 1)切削深度:余量Z=4mm ,分两次切除。
2)进给量:查《机械制造工艺设计手册》表3—13
车刀 刀杆尺寸:25×25mm
f=0.9~1.3(mm/r),查机床说明书,现取f=1.02mm/r
3)计算切削速度
查《工艺师手册》表27-12: V=v v y x p m V
f a T C k v =
4.01
5.020.002.126054.0158???=33.4(m/min) 4)确定主轴转速:
n s =w
d v π1000=π2084.331000?=51.4r/min 按照机床说明书,取n s =50r/min
所以实际切削速度: V=
1000w d π n s =1000208π 50? =32.67m/min 5)检验机床功率:
主切削力 查《工艺师手册》 表2-14
F z =C Z F a z f x p f Z F y v z nF k z F ………………………………2.6
式中C Z F =900 ,x Z F =1.0 , y z F =0.85 , n z F =0,
k v T =0.89 k z mF =1.0, k F k r =0.89
代入公式得
F z =89.002.1290085.01???
=2729(N)
切削时消耗功率:
P C =4
106?C C V F =410667.322729??=1.48(KW ) CA6140机床电机功率为7.5KW, 所以机床功率足够。
6)检验机床进给系统强度:已知主切削力为径向切削力F p
参考《工艺师手册》
F Y =C y F a V F X p f FV Y v Fv n k V F ………………………………2.7
其中C y F =530, x Y F =0.90, y Y F =0.75, n Y F =0
查表27—16《机械工艺师手册》
k y F =0.89,
代入得:
F Y =530×3.359.0×1.026.0×1×0.89
=1416(N)
轴向切削力(走刀力):查表2-17《机械工艺师手册》
F x =C x F a X F x p f X F y v X nF k X F ………………………………2.8
其中 C x F =450, x X F =1.0, y X F =0.4 , n Fx =0 , k m =0.89
轴向切削力:
F x =450×3.35×1.024.0×1×0.89
=1351(N)
取机床导轨与床鞍摩擦系数u=0.1,则切削力在纵向进给方向对机床的作用力:
F= F x +u (F Y + F z )
=1765(N)
查机床说明书,机床最大纵向力为3530N,故机床进给系统可以正常工作。
7)切削工时:
刀具行程L=21l l l ++=14+2+2+2=45 (mm)
i nf
l l l fn Li T j 21++==