机床导轨爬行现象的产生机理研究
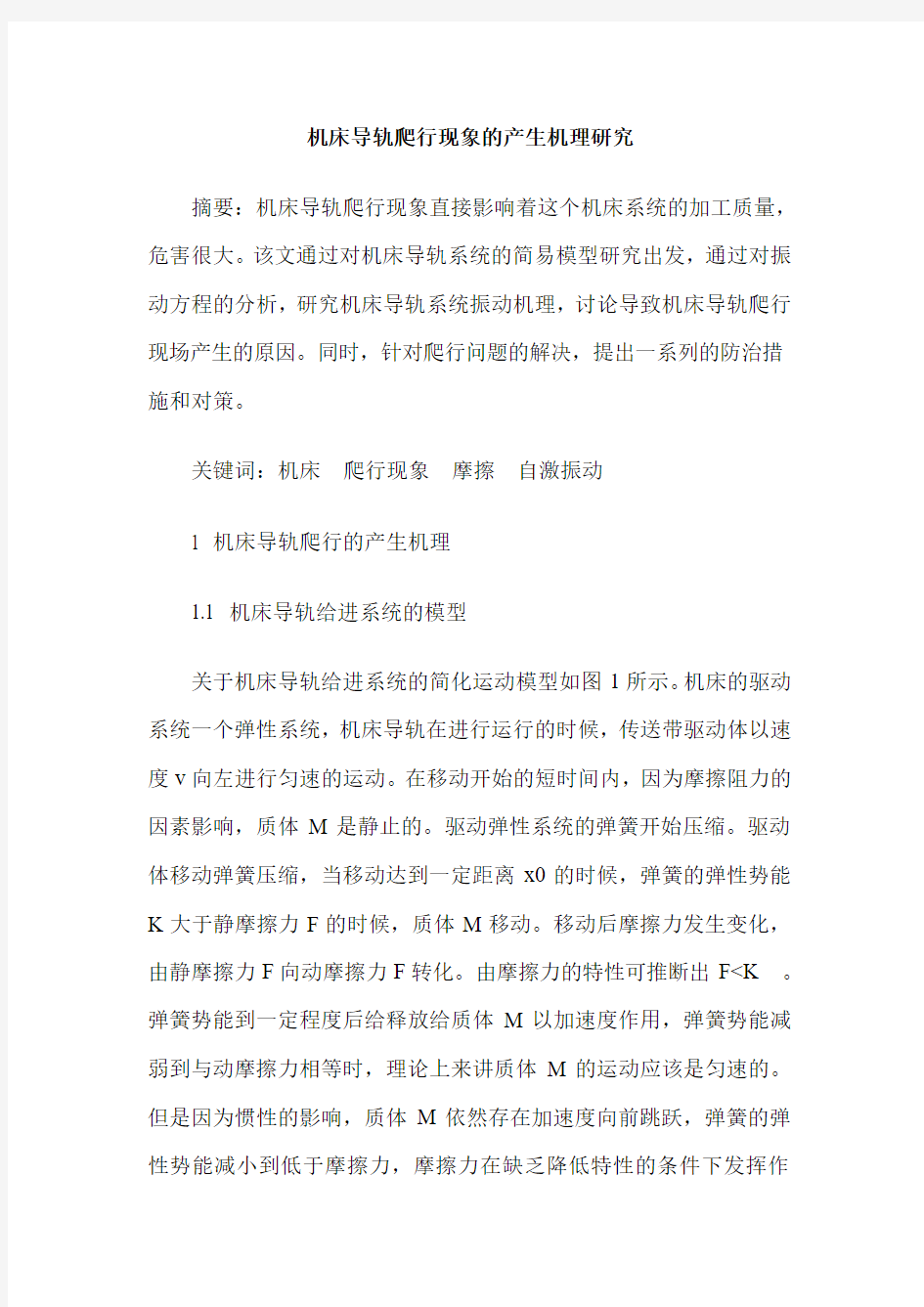

机床导轨爬行现象的产生机理研究
摘要:机床导轨爬行现象直接影响着这个机床系统的加工质量,危害很大。该文通过对机床导轨系统的简易模型研究出发,通过对振动方程的分析,研究机床导轨系统振动机理,讨论导致机床导轨爬行现场产生的原因。同时,针对爬行问题的解决,提出一系列的防治措施和对策。
关键词:机床爬行现象摩擦自激振动
1 机床导轨爬行的产生机理
1.1 机床导轨给进系统的模型
关于机床导轨给进系统的简化运动模型如图1所示。机床的驱动系统一个弹性系统,机床导轨在进行运行的时候,传送带驱动体以速度v向左进行匀速的运动。在移动开始的短时间内,因为摩擦阻力的因素影响,质体M是静止的。驱动弹性系统的弹簧开始压缩。驱动体移动弹簧压缩,当移动达到一定距离x0的时候,弹簧的弹性势能K大于静摩擦力F的时候,质体M移动。移动后摩擦力发生变化,由静摩擦力F向动摩擦力F转化。由摩擦力的特性可推断出F<K。弹簧势能到一定程度后给释放给质体M以加速度作用,弹簧势能减弱到与动摩擦力相等时,理论上来讲质体M的运动应该是匀速的。但是因为惯性的影响,质体M依然存在加速度向前跳跃,弹簧的弹性势能减小到低于摩擦力,摩擦力在缺乏降低特性的条件下发挥作
机床爬行的产生原因及消除
中国石油大学(华东)现代远程教育 毕业设计(论文) 题目:机床爬行的产生原因及消除 学习中心:威海学习中心 年级专业:网络07春机械设计及其自动化学生姓名:焉德强学号:0790784002 指导教师:林秀娟职称:讲师 导师单位:威海职业学院 中国石油大学(华东)远程与继续教育学院论文完成时间:2008 年11 月01 日
摘要:机床工作过程中产生爬行的原因有液压系统和机械系统两方面的,液压系统方面的原因是油液中侵入了空气或产生空穴,以及控制阀件磨损而出现太大的间隙;机械系统方面产生爬行的原因是摩擦力的变化。文章探讨了液压系统侵入空气产生爬行的机理及其消除方法和机械系统因摩擦力变化产生爬行的解决方法。 关键词:液压油, 摩擦, 润滑,爬行 爬行是机床上常见而不正常的运行状态,它主要出现在机床各传动系统的执行零部件上,比如刀架、与油缸连在一起的工作台等,且一般在低速运行时出现较多,因速度低时,润滑油被压缩、润滑油膜变薄、油楔作用降低、部分油膜破坏,使摩擦面的摩擦阻力发生变化。通常情况下,轻微程度的爬行是不易察觉的振动,显著的爬行则是大距离的跳动。当机床运动执行件出现爬行时,不仅会破坏液压系统工作的稳定性,产生冲击,同时也会影响机床的精度和被加工工件的精度。比如磨床出现爬行时,会使磨工件的表面粗糙度增大;坐标镗床出现爬行,会使精确定位难以实现。严重的爬行还能引起机床振动,损害机床及其工模具。因此,为了避免爬行的产生,必须分析清楚产生爬行的原因,一旦出现爬行现象,就要采取措施加以排除。 爬行是一种故障,它是在传动系统的刚性不足,驱动力与负载摩擦阻力波动变化的情况下形成的,体现在机床液压系统侵入空气、液压元件的间隙与机械装置本身都可能引起这种故障。 1液压系统侵入空气引起的爬行及消除方法 1.1空气侵入液压系统的方式及危害 空气侵入液压系统的方式是多种多样的,比如液压系统是由各液压元件组成,各种元件的零件之间,为达到连续的、断续和往复运动,需要有一定的配合间隙,而空气就从间隙中侵入,各元件之间的连接密封不严,且受到振动影响,接头螺帽松动,故而空气由此而入,元件中的零件由于同轴或直线度不好、线垫厚薄不均、螺钉没有均匀抓紧而造成泄漏,油泵吸油管和系统回油管在油池中没有隔开或靠在一起,回油飞溅,搅成泡沫,使油泵吸油管吸入空气,油泵吸油管处的滤油器被污物堵塞或滤油器孔太密、油液不足或吸油管侵入油池太少,导致吸油不畅,在吸油区形成局部真空而产生空穴,回油管的出油口在油面上,当机床停用时,空气就乘机而入,设计不合理,回油路中没有背压或背压很小,密封件损坏等,导致油缸左右油腔同时互通且通回油。此外,液压元
机床爬行与振动
数控机床中有很多明显的不正常现象,但在有一些经济数控系统中,却没有报警,即使有时出现报警,报警的信息表明也不是你所看到不正常现象的报警。 机床出现爬行与振动就是一个明显的例子。机床以低速运行时,机床工作台是蠕动着向前运动;机床要以高速运行时,就出现震动。 关于机床爬行有的书上写着:由于润滑不好,而使机床工作台移动时摩擦阻力增大。当电机驱动时,工作台不向前运动,使滚珠丝杠产生弹性变形,把电机的能量贮存在变形上。电动机继续驱动,贮存的能量所产的弹性力大于静摩擦力时,机床工作台向前蠕动,周而复始地这样运动,而产生了爬行的现象。 然而事实并非如此,仔细看一下导轨面润滑的情况,就可以断定不是这个问题。机床爬行和振动问题是属于速度的问题。既然是速度的问题就要去找速度环,我们知道机床的速度的整个调节过程是由速度调节器来完成的。特别应该着重指出,速度调节器的时间常数,也就是速度调节器积分时间常数是以毫秒计的,因此,整个机床的伺服运动是一个过渡过程,是一个调节过程。凡是与速度有关的问题,只能去查找速度调节器。因此,机床振动问题也要去查找速度调节器。可以从以下这些地方去查找速度调节器故障:一个是给定信号,一个是反馈信号,再一个就是速度调节器的本身。第一个是由位置偏差计数器出来经D/A转换给速度调节器送来的模拟是VCMD,这个信号是否有振动分量,可以通过伺服板上的插脚(FANUC6系统的伺服板是X18脚)来看一看它是否在那里振动。如果它就是有一个周期的振动信号,那毫无疑问机床振动是正确的,速度调节器这一部分没有问题,而是前级有问题,向D/A转换器或偏差计数器去查找问题。如果我们测量结果没有任何振动的周期性的波形。那么问题肯定出在其他两个部分。我们可以去观察测速发电机的波形,由于机床在振动,说明机床的速度在激烈的振荡中,当然测速发电机反馈回来的波形一定也是动荡不已的。但是我们可以看到,测速发电机反馈的波形中是否出现规律的大起大落,十分混乱现象。这时,我们最好能测一下机床的振动频率与电机旋转的速度是否存在一个准确的比率关系,譬如振动的频率是电机转速的四倍频率。这时我们就要考虑电机或测速发电机有故障的问题。因为振动频率与电机转速成一定比率,首先就要检查一下电动机是否有故障,检查它的碳刷,整流子表面状况,以及机械振动的情况,并要检查滚珠轴承的润滑的情况,整个这个检查,可不必全部拆卸下来,可通过视察官进行观察就可以了,轴承可以用耳去听声音来检查。如果没有什么问题,就要检查测速发电机。测速发电机一般是直流的。测速发电机就是一台小型的永磁式直流发电机,它的输出电压应正比于转速,也就是输出电压与转速是线性关系。只要转速一定,它的输出电压波形应当是一条直线,但由于齿槽的影响及整流子换向的影响,在这直线上附着一个微小的交变量。为此,测速反馈电路上都加了滤波电路,这个滤波电路就是削弱这个附在电压上的交流分量。 测速发电机中常常出现的一个毛病就是炭刷磨下来的炭粉积存在换向片之间的槽内,造成测速发电机片间短路,一旦出现这样的问题就避免不了这个振动的问题。这是因为这个被短路的元件一会在上面支路,一会在下面支路,一会正好处于换向状态,这3种情况就会出现3种不同的测速反馈的电压。在上面支路时,上面支路由于少了一个元件,电压必然要小,而当它这个元件又转到了下面支路时,下面的电压也小,这时不论在上面支路,还是在下面支路中,都必然使这两条支路的端电压下降,且有一个平衡电流流过这两条并联的支路,又造成一定的电压降。当这个元件处于换向,正好它也处于短路,这时上下两个支路没有短路元件,电压得以恢复,且也无环流。这样,与正常测速发电机状态一样。为此,
关于机械系统设计的综述报告
关于机械系统设计的综述报告 摘要:阐述了机械系统的组成部分和机械系统设计的各个组成部分; 并对机械系统设计的五大子系统进行了说明,介绍了每个子系统的概念以及设计重点。从总体总结了机械系统设计的一般步骤,每个环节所要完成的工作与注意部分。最后展望未来机械系统设计将与现代设计理论方法结合展现更大的优势。 关键词:机械系统;机械系统设计;子系统 1.引言 机械工业历来是发达国家的重要支柱产业,是一个国家的工业基础。但从70年代开始,世界传统工业因不适应科技水平和社会生产力的飞速发展而产生大幅度滑坡,一度曾被称之为“夕阳工业”。而现代机械系统以传统机械工业为基础,融合控制理论、计算科学和信息技术、体现系统论、优化论、对应论、智能论、寿命论、突变论、艺术论等现代设计思想,不但能代替人的体力劳动,更能解放人的一部分脑力劳动,已经成为现代人类改造客观世界的重要工具。同时,也使机械工业逐渐摆脱窘境,日益显示出其新的活力。 2.机械系统设计 2.1机械系统组成 机械系统是机电一体化系统的最基本要素,由若干机构,零件,部件组成,包括动力系统,执行机构,传动机构,支撑机构,控制机构等,用于完成指定的动作,传递功率,运动或者信息。 (1)动力系统 动力系统包括动力机及其配套装置,是机械系统工作的动力源。动力机输出的运动通常为转动,而且转速较高。选择动力机时,应全面考虑执行系统的运动和工作载荷、机械系统的使用环境和工况以及工作载荷的机械特性等要求,使系统既有良好的动态性能,又有较好的经济性。 (2)传动系统 传动系统是把动力机的动力和运动传递给执行系统的中问装置。如果动力机的工作性能完全符合执行系统工作的要求,传动系统也可
岩心分析报告技术(简版)
岩心分析技术及应用 一、X射线衍射 1.X射线衍射分析技术 全岩矿物组分和粘土矿物可用X射线衍射(XRD)迅速而准确地测定。XRD分析借助于X射线衍射仪来实现,它主要由光源、测角仪、X射线检测和记录仪构成。 由于粘土矿物的含量较低,砂岩中一般3%~15%。这时,X射线衍射全岩分析不能准确地反映粘土的组成与相对含量,需要把粘土矿物与其它组分分离,分别加以分析。首先将岩样抽提干净,然后碎样,用蒸馏水浸泡,最好湿式研磨,并用超声波振荡加速粘土从颗粒上脱落,提取粒径小于2μm(泥、页岩)或小于5μm(砂岩)的部分,沉降分离、烘干、计算其占岩样的重量百分比。 粘土矿物的XRD分析使用定向片,包括自然干燥的定向片(N片)、经乙二醇饱和的定向片(再加热至550℃),或盐酸处理之后的自然干燥定向片。粒径大于2μm或5μm的部分则研磨至粒径<40μm的粉末,用压片法制片,上机分析。此外还可以直接进行薄片的XRD分析,它对于鉴定疑难矿物十分方便,并可与薄片中矿物的光性特征对照,进行综合分析。 2.X射线衍射在保护油气层中的应用 1)地层微粒分析 地层微粒指粒径小于37μm(或44μm)即能通过美国400目(或325目)筛的细粒物质,它是砂岩中重要的损害因素,砂岩中与矿物有关的地层损害都与其有密切的联系。地层微粒的分析为矿物微粒稳定剂的筛选、解堵措施的优化提供依据。除粘土矿物外,常见的其它地层微粒有长石、石英、云母、菱铁矿、方解石、白云石、石膏等。 2)全岩分析 对粒径大于5μm的非粘土矿物部分进行XRD分析,可以知道诸如云母、碳酸盐矿物、黄铁矿、长石的相对含量,对酸敏(HF,HCl)性研究和酸化设计有帮助。长石含量高的砂岩,当酸液浓度和处理规模过大时,会削弱岩石结构的完整性,并且存在着酸化后的二次沉淀问题,可能导致土酸酸化失败。 3)粘土矿物类型鉴定和含量计算
铸造文献综述
概述 铸造是人类掌握比较早的一种金属热加工工艺,已有约6000年的历史。中国约在公元前1700~前1000年之间已进入青铜铸件的全盛期,工艺上已达到相当高的水平。 铸造是将金属熔炼成符合一定要求的液体并浇进铸型里,经冷却凝固、清整处理后得到有预定形状、尺寸和性能的铸件的工艺过程。铸造毛坯因近乎成形,而达到免机械加工或少量加工的目的降低了成本并在一定程度上减少了制作时间.铸造是现代装置制造工业的基础工艺之一。被铸金属有:铜、铁、铝、锡、铅等,普通铸型的材料是原砂、黏土、水玻璃、树脂及其他辅助材料。特种铸造的铸型包括:熔模铸造、消失模铸造、金属型铸造、陶瓷型铸造等。(原砂包括:石英砂、镁砂、锆砂、铬铁矿砂、镁橄榄石砂、兰晶石砂、石墨砂、铁砂等)。 铸造的发展 中国商朝的重875公斤的司母戊方鼎,战国时期的曾侯乙尊盘,西汉的透光镜,都是古代铸造的代表产品。早期的铸件大多是农业生产、宗教、生活等方面的工具或用具,艺术色彩浓厚。那时的铸造工艺是与制陶工艺并行发展的,受陶器的影响很大。 中国在公元前513年,铸出了世界上最早见于文字记载的铸铁件-晋国铸型鼎,重约270公斤。欧洲在公元八世纪前后也开始生产铸铁件。铸铁件的出现,扩大了铸件的应用范围。例如在15~17世纪,德、法等国先后敷设了不少向居民供饮用水的铸铁管道。18世纪的工业革命以后,蒸汽机、纺织机和铁路等工业兴起,铸件进入为大工业服务的新时期,铸造技术开始有了大的发展。 进入20世纪,铸造的发展速度很快,其重要因素之一是产品技术的进步,要求铸件各种机械物理性能更好,同时仍具有良好的机械加工性能;另一个原因是机械工业本身和其他工业如化工、仪表等的发展,给铸造业创造了有利的物质条件。如检测手段的发展,保证了铸件质量的提高和稳定,并给铸造理论的发展提供了条件;电子显微镜等的发明,帮助人们深入到金属的微观世界,探查金属结晶的奥秘,研究金属凝固的理论,指导铸造生产。 铸造产品发展的趋势是要求铸件有更好的综合性能,更高的精度,更少的加工余量和更光洁的表面。此外,节能的要求和社会对恢复自然环境的呼声也越来越高。为适应这些要求,新的铸造合金将得到开发,冶炼新工艺和新设备将相应出现。 铸造生产的机械化自动化程度在不断提高的同时,将更多地向柔性生产方面发展,以扩大对不同批量和多品种生产的适应性。节约能源和原材料的新技术将会得到优先发展,少产生或不产生污染的新工艺新设备将首先受到重视。质量控制技术在各道工序的检测和无损探伤、应力测定方面,将有新的发展。 铸造业的发展,铸造是现代机械制造工业的基础工艺之一,因此铸造业的发展标志着一个国家的生产实力。据2008年统计,我国年产铸件3350万吨,是世界铸造第一大国。 例如
导轨的设计与选择
一、导轨的设计与选择。 1、对导轨的要求 1)导轨精度高 导轨精度是指机床的运动部件沿导轨移动时的直线和它与有关基面之间的相互位置的准确性。无论在空载或切削工件时导轨都应有足够的导轨精度,这是对导轨的基本要求。 2)耐磨性能好 导轨的耐磨性是指导轨在长期使用过程中保持一定导向精度的能力。因导轨在工作过程中难免磨损,所以应力求减少磨损量,并在磨损后能自动补偿或便于调整。 3)足够的刚度 导轨受力变形会影响部件之间的导向精度和相对位置,因此要求轨道应有足够的刚度。 4)低速运动平稳性 要使导轨的摩擦阻力小,运动轻便,低速运动时无爬行现象。5)结构简单、工艺性好 导轨的制造和维修要方便,在使用时便于调整和维护。 2、对导轨的技术要求 1)导轨的精度要求 滑动导轨,不管是V-平型还是平-平型,导轨面的平面度通常取0.01~0.015mm,长度方面的直线度通常取0.005~0.01mm;侧导向面的直线度取0.01~0.015mm,侧导向面之间的平行度取
0.01~0.015mm,侧导向面对导轨地面的垂直度取0.005~0.01mm。2)导轨的热处理 数控机床的开动率普遍都很高,这就要求导轨具有较高的耐磨性,以提高其精度保持性。为此,导轨大多需要淬火处理。导轨淬火的方式有中频淬火、超音频淬火、火焰淬火等,其中用的较多的是前两种方式。 二、导轨的种类和特点 导轨按运动轨迹可分为直线运动导轨和圆运动导轨;按工作性质可分为主运动导轨、进给运动导轨和调整导轨;按接触面的摩擦性质可分为滑动导轨、滚动导轨和静压导轨等三大类。 1)滑动导轨:是一种做滑动摩擦的普通导轨。滑动导轨的优点是结构简单,使用维护方便,缺点是未形成完全液体摩擦时低速易爬行,磨损大,寿命短,运动精度不稳定。滑动导轨一般用于普通机床和冶金设备上。 2)滚动导轨的特点是:摩擦阻力小,运动轻便灵活;磨损小,能长期保持精度;动、静摩擦系数差别小,低速时不易出现"爬行"现象,故运动均匀平稳。缺点是:导轨面和滚动体是点接触或线接触,抗振性差,接触应力大,故对导轨的表面硬度要求高;对导轨的形状精度和滚动体的尺寸精度要求高。因此,滚动导轨在要求微量移动和精确定位的设备上,获得日益广泛的运用。 3)静压导轨是利用液压力让导轨和滑块之间形成油膜,使
机床导轨爬行的起因和解决措施
机床导轨爬行现象的起因和解决措施 机制09-**号 ***机床在低速或微量进给运动时,往往保持不了均匀的速度,进入时快时慢、时动时停的不稳定状态,这就是所谓爬行现象。爬行是一个复杂的摩擦自激振动现象,对其机理的认识,到目前为止依然争论颇多,尚未有统一的微分方程式对其精确描述。目前主要使用光栅爬行测量系统和激光干涉测量系统分析、测量导轨的爬行问题。 机床在运行过程中经常会遇到爬行问题。进给运动中的爬行现象破坏了系统运动的均匀性,不仅使被加工件精度和表面质量下降,也会严重影响机床的加工精度、表面粗糙度和定位精度,破坏液压系统工作的稳定性,使机床导轨加速磨损,甚至产生废品和事故。因此,爬行现象是精密机床及重型机床必须解决的问题,加工工件时应尽量避免它的产生。 我们知道爬行是指机床运动部件慢速动行时的不平稳性,表现为有规律的一停一跃。这种现象的出现,以磨床居多数,会严重影响工作的表面质量和尺寸精度。引起爬行的主要原因,是摩擦因数随运动速度的变化和传动系统刚性不足。机床在实际使用中,爬行现象主要是在传动系统刚性不足,驱动力与负载摩擦阻力波动变化的情况下形成。机床液压系统侵入空气,液压元件间隙增大及机械装置自身原因都可能引起爬行故障。 出现爬行现象可能由很多原因造成,概括起来包括机械和电气两方面因素。在解决此故障时要考虑诸多因素,逐一进行排除。例如,
数显机床在出现爬行问题时,要观察电机低速运转有无电流断续现象,电枢回路串接一块电流表,低速运行时观察指针有无摆动,若有摆动则故障多数发生在电气部分。对于直流调速系统控制的进给轴,又尤以测速机发生故障居多。在检查测速机时,可以先用万用表测量测速机反馈电压,监测电压是否平稳。如果反馈电压有波动,首先检查测速机线路有无故障,看看反馈线是否虚连。另外我们经常忽略的一个问题是检查测速机的屏蔽线是否联接良好,屏蔽线有损坏或者联接不好都有可能使外部信号干扰混入,从而发生爬行现象。在静态检查测速机时,可以测量测速机的电阻阻值及测速发电机有无匝间断路和短路现象。有时还要借助于示波器等检测手段观看电机运转时反馈的波形状态好坏。 分析完爬行现象产生的机理后,我们便要设法避免它的产生。目前较为常用的有改善导轨摩擦特性和降低驱动阻力这两种方法。改善导轨摩擦特性就是降低摩擦阻力和减小静、动摩擦系数之差。而驱动阻力的主要组成部分是导轨副的摩擦阻力,和正压力成正比,所以设计时应尽量减轻运动部件的重量。在维修上,主要应排除因零件质量或装配不善而引起的附加阻力。 在实际工作中,只要能够针对产生原因合理地采用有效地方法和措施,便可将机床运动中的爬行现象降低到最小的极限,从而保证机床的正常工作,我们也可更好的利用机床。
国内旋压设备及其相关技术的发展与现状
加工过程控制,实现自动批量生产的目的。随后,兵器55所也开展了录返旋压机床的研制。西安重型机械研究所研制了PLC控制的强力旋压机床,其主轴调速系统、旋轮纵向进给电液伺服系统、仿形系统等均由PLC控制,但主轴仍采用直流电机拖动、可控硅励磁;旋轮纵向移动采用伺服泵控制油马达的电液调速系统,并采用了电液仿形阀进行仿形控制。近年来,北京航空制造I程研究所、长春55所和北京航空航天大学现代技术研究所等单位在总结过去研制经验的基础上,瞄准困际水平,运用先进的设计方法与理念,采用了SIMENS840D和BOSCH比例伺服阀控制系统,伺服油缸驱动,光栅位置反馈,滚动导轨导向和交流变频调速等先进技术,推出新一代的国产CNC强力旋压机床,实现了困产旋压机的升级换代。机床最大吨位600kN,整机性能达到国际先进水平。图1和图2是北京航空制造工程研究所近年来研制的部分CNC数控旋压机床。 图1SY一11CNC数控三旋轮卧式旋压机 图2SY一12CNC数控三旋轮卧式旋压机 随着汽车、石油、化工行业的发展,园内的专用旋压设备也呈现出快速发展的趋势。如北京航空航天大学现代所、北京航空制造工程研究所等单位研制的皮带轮旋压机,兵器55所生产的轮辐旋压机和内旋压机,北京航空制造工程研究所研制的CNC收口旋压机,哈尔滨工业大学和辽阳重犁机械厂等单位生产的二步法封头旋压机,燕山大学和黑龙江省旋压技术研究所等单位研制的一步法封头旋压机, REVIEW 沈阳金属研究所和兵器55所等单位研制的滚珠旋压机等。这些旋压机的实用性较好,吸取‘T国外设备的先进设计思想,性能稳定,满足了国内汽车、石油化工行业的发展需求。 3发展与现状 3.1国内旋压设备研制水平与现状 3.1.1控制系统 近年来,国内研制的数控旋压机床大都实现了NC或CNC控制。一般说来,用于金属切削机床的数控系统都可以作为旋压机床的数控系统。这些系统主要有德国SIEMENS、法国NUM、日本FANUC以及国内的中国珠峰公司、北京航天机床数控系统公司、华中数控公司、沈阳高档数控国家工程研究中心研制的控制系统。系统可根据机床精度、驱动电机功率和用户要求进行选择。与金属切削机床相比。旋压机床一般为重载液压驱动,由于液压油的可压缩性导致系统刚性较差、电液控制非线性以及液压元件响应频率低等问题,为静态和动态特性调试带来一定困难。为此,一些公司专门开发了电液伺服驱动的液压模块,设有多项可调参数,如PID前馈控制、死区补偿、摩擦力、非线性补偿等。如SIEMENS公司的840D系统内嵌了专用于电液伺服的驱动模块,并可以通过友好的入机界面方便地进行修改与设置。与所选用的伺服阀和油缸相匹配,为系统的动/静态特性的调试带来了方便。目前,SIEMENS公司的840D已成为旋压机主流控制系统。 控制精度可以通过光栅尺与伺服阀/伺服油缸组成的闭环控制系统以及编码器与交流或直流变频电机组成的闭环控制系统来保证,可以在采用全闭环和半闭环位置控制和速度控制的前提下,采取提高监测的分辩率以及调节放大器PID参数的方法,提高系统的控制精度。 3.1.2驱动系统 旋压机床的驱动系统包括主轴驱动和进给驱动两个部分。主轴驱动可采用交流变频电机和直流变 频电机驱动;进给驱动主要采用伺服电机+滚珠丝杠
机床直线导轨的单元化及发展
2017年7月 第45卷第13期 机床与液压 MACHINE TOOL &HYDRAULICS Jul.2017 Vol.45No.13 DOI :10.3969/j.issn.1001-3881.2017.13.037 收稿日期:2016-04-14 基金项目:国家科技支撑计划(2015BAF32B03)作者简介:徐许林(1961 ),男,总工程师,从事曲轴磨床设计制造工作三E -mail:hbxgxxl@163.com三 机床直线导轨的单元化及发展 徐许林1,杨双双2,饶建华2,李昌平2 (1.湖北九洲数控机床有限责任公司,湖北孝感432000; 2.中国地质大学(武汉)机械与电子信息学院,湖北武汉430074) 摘要:导轨副是机床系统的重要组件,其质量是影响机床加工精度二运行效率和运动平稳性的直接因素三机床制造的专业化二机床结构的模块化都促进着机床导轨的独立化和单元化三介绍了机床直线导轨脱离机床床身形成独立单元体的过程,列出了3种典型的导轨单元,分别介绍了其结构特点及应用场合,总结了目前导轨单元的研究情况,并对机床直线导轨单元的未来发展进行了展望三 关键词:导轨单元;滚动导轨单元;磁悬浮;静压 中图分类号:TH117一一文献标志码:A一一文章编号:1001-3881(2017)13-159-6 Unitization of Linear Guide in Machine Tools and its Development XU Xulin 1,YANG Shuangshuang 2,RAO Jianhua 2,LI Changping 2 (1.Hubei Jiuzhou CNC Machine Tools Co.,Ltd.,Xiaogan Hubei 432000,China;2.Faculty of Mechanical &Electronic Information,China University of Geosciences, Wuhan Hubei 430074,China) Abstract :As one of the important components of machine tools,the quality of guide rail is a direct factor which has influence to machine tool s machining precision,movement efficiency and stability.Professionalization of machine tool manufacturing and modularity of machine tool structure constantly promote the development of machine tool guide rail s independence and unitization.The process of forming independent unites of linear guide in machine tool separating from machine tool itself is introduced.Three kinds of representa-tive linear guide units were listed,and the structural feature and application situation were introduced respectively.The research infor-mation about these various units is summarized,which provides an outlook about the future development of linear guide units in ma-chine tools. Keywords :Guide unit;Rolling guide unit;Magnetic suspension;Hydrostatic pressure 0一前言 现代机床向高速二高精度迅速发展,机床重要功能部件的独立模块化成为设计制造的发展趋势,如电主轴二刀架模块二进给模块等三机床导轨作为机床重要组件,直接影响机床运作效率二加工精度和使用寿命三随着机床标准化要求的不断提升及模块化程度的不断深化,导轨开始从机床床身及运动部件分离开来,形成独立的导轨单元模块三 直线导轨是机床导轨的一种,直线导轨单元化是指将直线导轨副从机床床身和移动单元中脱离出来,集成于一体,形成独立单元三该单元在具备基本功能的同时方便了导轨在机床上的安装二使用与维护,便于专业化制造,满足了现代机床对导轨的要求,不仅节省了设计时间和制造成本,更有效实现了导轨生产的标准化和系列化三 本文作者首先介绍了导轨单元的形成,从直线导 轨单元类型着手,重点阐述了3种典型直线导轨单元的工作原理与组合特点,分析了不同单元的应用优势与适用场合;此外,进一步综述了近年来机床直线导轨单元的研究情况,阐述了发展重点及难点,并对精密机床导轨单元未来发展进行了展望三 1一机床直线导轨单元1.1一机床导轨单元化 在传统机床中,通常选择在机床床身和移动部件 上加工出导轨作为导向和支承系统,如图1(a)中左上图所示三出于导轨对加工精度影响的重要性,机床床身导轨及运动件均需经过精磨级别的加工方可达到精度要求,并需反复调配达到要求的装配精度后才可使用三这样一来,就引发了以下几方面的问题:(1)加工难三重型机床床身具有较大的尺寸和质量,这使得在床身上加工导轨时有较大难度,需要大型高精度机床加工[1]三 万方数据
数控技术文献综述
国内并联机床的发展 并联机床作为一种新型的加工设备,已成为当前机床技术的一个重要研究方向,受到了国际机床行业的高度重视。并联机床克服了传统串联机床移动部件质量大、系统刚度低、刀具只能沿固定导轨进给、作业自由度偏低、设备加工灵活性和机动性不够等固有缺陷。并联机床可完成从毛坯至成品的多道加工工序,实现并联机床加工的复合化。 并联机床是近年来发展起来的一种新型结构机床。因没用实体坐标轴,固又称为虚拟轴机床。并联机床是空间机构学研究成果在数控机床领域中的创造性应用,它集机构学理论﹑机器人技术和数字控制技术于一体,是多学科交叉的新兴产物。它的发展可以分为3个阶段:模拟器阶段、并联机器人阶段和并联机床阶段。 并联机床的优点 并联机床是新一代的数控机床。它完全打破了传统机床结构的概念,采用了多杆并行驱动方式。从机床整体来说,传统的串联机构机床是属于位置求解简单而机构复杂的机床而相对于并联机构机床,则机构简单而位置求解复杂。在并联机构的位置分析中,位置反解比较简单,位置正解却非常复杂,与串联机构截然相反。与串联机构机床相比,并联机床主要有以下优点。 (1)刚度重量比大。因采用并联闭环静定或非静定杆系结构,且在准静态情况下,传动构件理论上为仅受拉压载荷的二力杆,故传动机构的单位重量具有很高的承载能力。 (2)动态性能好。运动部件惯性的大幅度降低有效地改善了伺服控制器的动态品质,允许动平台获得很高的进给速度和加速度,因而特别适合各种高速数控作业。 (3)机床结构简单,集成化、模块化程度高。这使得并联机床结构设计和加工等多方面得以简化。 (4)变换坐标系方便。由于没有实体坐标系,机床坐标系与工件坐标系的转换全部靠软件完成,非常方便。 (5)技术附加值高。并联机床结构看起来很简单,但设计、控制却很复杂,具有“硬件”简单、“软件”复杂的特点,是一种技术附加值很高的机电一体化产品。 (6)使用寿命长。并联机床由于没有传统机床导轨,避免了导轨磨损、锈蚀、划伤等现象。从以上分析可以看出,并联机床具有许多传统机床无法替代的优点,弥补了串联机床的不足。虽然不会成为传统机床的替代者,但我们完全可以预见在不远的将来并联机床将会在一些专业领域里成为传统机床强有力的补充者。 并联机床在国内的发展状况 我国并联机床的研究与开发几乎与世界同步。1994年并联机床在国际上首次展出之后,国内许多高校和科研单位也纷纷投入力量进行研究。由清华大学和天津大学合作开发的我国第一台并联机床,在1998年的北京机床展览会上展出。在1999年北京CIMT’99中国国际机床展览会上,展出了哈尔滨工业大学研制的BJ-30型并联机床,该机床还成功地进行了叶轮加工的演示。同时,在这次展
爬行现象
数控机床进给系统爬行与振动故障的检测与维修 作者:轴承供应商网发布时间:2009-6-6 9:39:29 文字选择:大中小浏览次数:27 轴承及轴承相关技术文章(轴承供应商网提供)关键字:轴承,数控机床 摘要:数控机床是机械、液压、电气和计算机技术高度集成的一体化产品,其故障的发生也多数是机械、液压、电气等方面的综合反映。分析数控机床进给系统的爬行与振动现象产生原因,阐述故障的诊断与维修,并通过实例说明诊断与维修技术方法。关键词:数控机床;爬行;振动;维修 1数控机床进给系统爬行与振动现象及其产生原因 在驱动移动部件低速运行过程中,数控机床进给系统会出现移动部件开始时不能启动,启动后又突然作加速运动,而后又停顿,继而又作加速运动,移动部件如此周而复始忽停忽跳、忽慢忽快的运动现象称为爬行。而当其以高速运行时,移动部件又会出现明显的振动。 对于数控机床进给系统产生爬行的原因,一般认为是由于机床运动部件之间润滑不好,导致机床工作台移动时静摩擦阻力增大;当电机驱动时,工作台不能向前运动,使滚珠丝杠产生弹性变形,把电机的能量贮存在变形上;电动机继续驱动,贮存的能量所产的弹性力大于静摩擦力时,机床工作台向前蠕动,周而复始地这样运动,产生了爬行的现象。 事实上这只是其中的一个原因,产生这类故障的原因还可能是机械进给传动链出现了故障,也可能是进给系统电气部分出现了问题,或者是系统参数设置不当的缘故,还可能是机械部分与电气部分的综合故障所造成。 2爬行与振动故障的诊断与排除 对于数控机床出现的爬行与振动故障,不能急于下结论,而应根据产生故障的可能性,罗列出可能造成数控机床爬行与振动的有关因素,然后逐项排队,逐个因素检查,分析、定位和排除故障。查到哪一处有问题,就将该处的问题加以分析,看看是否是造成故障的主要矛盾,直至将每一个可能产生故障的因素都查到。最后再统筹考虑,提出一个综合性的解决问题方案,将故障排除。 排除数控机床进给系统爬行与振动故障的具体方法如下: 2.1对故障发生的部位进行分析 爬行与振动故障通常需要在机械部件和进给伺服系统查找问题。因为数控机床进给系统低速时的爬行现象往往取决于机械传动部件的特性,高速时的振动现象又通常与进给传动链中运动副的预紧力有关。另外,爬行和振动问题是与进给速度密切相关的,因此也要分析进给伺服系统的速度环和系统参数。 2.2机械部件故障的检查和排除 造成爬行与振动的原因如果在机械部件,首先要检查导轨副。因为移动部件所受的摩擦阻力主要是来自导轨副,如果导轨副的动、静摩擦系数大,且其差值也大,将容易造成爬行。尽管数控机床的导轨副广泛采用了滚动导轨、静压导轨
机床爬行故障分析
中国高新技术企业 机床爬行故障分析 文/李洁裴晓光周立军 【摘要】数控机床的系统爬行问题是很普遍的现象,在机床中经常出现,甚至在有些数控机床中还没有报 警。 【关键词】爬行振动测速 机床以低速运行时,机床工作台是蠕动着向前运动;机床要以高速运行时,就出现震动。但有一些经济数控系统中,却没有报警,即使有时出现报警,报警的信息表明也不是你所看到不正常现象的报警。 一、概述 机床爬行和振动问题是属于速度的问题。我们知道机床的速度的整个调节过程是由速度调节器来完成的。速度调节器的时间常数,也就是速度调节器积分时间常数是以毫秒计的,因此,整个机床的伺服运动是一个过渡过程,是一个调节过程。 二、排除故障的方法 机床振动问题是速度调节器问题,只能从速度调节器入手。可以从下面这些方面查找爬行故障:一个是给定信号,一个是反馈信号,再一个就是速度调节器的本身。 1.给定信号问题 给定信号是由位置偏差计数器出来经数模转换器D/A转换给速度调节器送来的模拟给定VCMD,这个信号是否有振动分量,可以通过伺服板上的插脚(西门子8系统的伺服板是56号线)来看一看它是否在那里有振动。如果它就是有一个周期的振动信号,那毫无疑问机床振动是正确的,速度调节器本身没有问题,而是给定有问题,向D/A转换器或偏差计数器去查找问题或者是给定的外部元件问题。如果我们测量结果没有任何振动的周期性的波形。那么问题肯定出在其他两个部分。 2.反馈信号问题 首先就要检查一下电动机是否有故障,检查它的碳刷,整流子表面状况,以及机械振动的情况,并要检查滚珠轴承的润滑的情况,整个这个检查,可不必全部拆卸下来,可通过视觉进行观察就可以了,轴承可以用耳去听声音来检查。如果没有什么问题,就要检查测速发电机。 我们再用示波器去观察测速发电机的波形,可以看到,测速发电机反馈的波形中是否出现规律的大起大落,十分混乱现象。这时,我们最好能测一下机床的振动频率与电机旋转的速度是否存在一个准确的比率关系,譬如振动的频率是电机转速的四倍频率。这时我们就要考虑电机或测速发电机有故障的问题。 测速发电机就是一台小型的永磁式直流发电机,它的输出电压应正比于转速,也就是输出电压与转速是线性关系。只要转速一定,它的输出电压波形应当是一条直线,但由于齿槽的影响及整流子换向的影响,在这直线上附着一个微小的交变量。为此,测速反馈电路上都加了滤波电路,这个滤波电路就是削弱这个附在电压上的交流分量。 测速发电机中常常出现的一个毛病就是炭刷磨下来的炭粉积存在换向片之间的槽内,造成测速发电机片间短路,一旦出现这样的问题就避免不了这个振动的问题。这是因为这个被短路的元件一会在上面支路,一会在下面支路,一会正好处于换向状态,这3种情况就会出现3种不同的测速反馈的电压。在上面支路时,上面支路由于少了一个元件,电压必然要小,而当它这个元件又转到了下面支路时,下面的电压也小,这时不论在上面支路,还是在下面支路中,都必然使这两条支路的端电压下降,且有一个平衡电流流过这两条并联的支路,又造成一定的电压降。当这个元件处于换向,正好它也处于短路,这时上下两个支路没有短路元件,电压得以恢复,且也无环流。这样,与正常测速发电机状态一样。为此,三种不同情况下电压做了一个周期地变化,这个电压反馈到调节器上时,势必引起调节器的输出也做出相应地,周期地变化。这是仅仅说了一个元件被短路。特别严重时有一组换向片全部被碳粉给填平了,全部短路,这样就会更为严重的电压波动。 反馈信号与给定信号对于调节器来说是完全相同的。所以出现了反馈信号的波动,必然引起速度调节器的反方向调节,这样就引起机床的振动。 这种情况发生时,非常容易处理,只要把电机后盖拆下,就露出测速发电机的整流子。这时不必做任何拆卸,只要用尖锐的勾子,小心地把每个槽子勾一下,然后用细砂纸光一下勾起的毛刺,把整流片表面再用无水酒精擦一下,再放上炭刷就可以了。这里特别要注意的是用尖锐的勾子去勾换向片间槽口时,别碰到绕组,因为绕组线很细,一旦碰破就无法修复,只有重新更换绕组。再一个千万不要用含水酒精去擦,这样弄完了绝缘电阻下降无法进行烘干,这样就会拖延修理期限。 除了我们上面讨论过这些引起振动的原因外,还可能是系统本身的参数引起的振荡。我们知道一个闭环系统也可能由于参数设定不好,而引起系统振荡,但最佳的消除这个振荡方法就是减少它的放大倍数,在FANUC的系统中调节RV1,逆时钟方向转动,这时可以看出立即会明显变好,但由于RV1调节电位器的范围比较小,有时调不过来,只能改变短路棒,也就是切除反馈电阻值,降低整个调节器的放大倍数。 3.速度调节器问题 采用这些方法后,还做不到完全消除振动,甚至是无效的,就要考虑对速度调节器板更换或换下后彻底检查各处波形。故障也能消除。 在这个实例中,出现爬行时,电机是在低速,一旦提高速度就震起来,这时可能出现过流报警。产生这种报警的原因是机床工作台面为了迅速跟随反馈信号的变化而变化,必须有一个很大的加速度才行,这个加速度就是由电机的转矩给出的。电机转矩的变化来响应这个速度给定信号(实际上是反馈信号)的变化。转矩就是电流信号。大的转矩,就是大的电流信号造成的,在电流环中出现了一个电流的激烈变化,从而出现了过电流现象.在振动时不报警,而在振动加大时,出现了过电流报警。 三、结语 由于数控机床是机电一体化产品,这里边影响机床正常工作的因素很多,除了电气方面的问题之外,机械方面的问题也与电气的问题混在一起,这种情况就十分难以分辨出到底哪个因素在这个问题中的比重占有多少。这些相关的因素是制约我们迅速查出故障的重要因素。 (作者单位系第一重型机械集团公司有限责任公司设备维修分公司 阿城继电器股份有限公司 河北省质检站) 科技论坛68 --
机械设计文献综述最终版
1课题的背景和意义 扫描式三维形貌检测系统即为三坐标测量机,是经过40多年发展起来的一种高效率的新型精密测量仪器,有着非常广泛的用途。 20世纪60年代以来,工业生产有了很大的发展,特别是机床、机械、汽车、航空航天和电子工业兴起后,各种复杂零件的研制和生产需要先进的检测技术与仪器,因而体现三维测量技术的三坐标测量机应运而生,并迅速发展和日趋完善。作为近40年发展起来的一种高效率的新型精密测量仪器,三坐标测量机已广泛地用于机械制造、电子、汽车和航空航天等工业中。它可以进行零件和部件的尺寸、形状及相互位置的检测,例如箱体、导轨、涡轮和叶片、缸体、凸轮、齿轮、形体等空间型面的测量。此外,还可用于划线、定中心孔、光刻集成线路等,并可对连续曲面进行扫描及制备数控机床的加工程序等。由于它的通用性强、测量范围大、精度高、效率高、性能好、能与柔性制造系统相连接,已成为一类大型精密仪器,故有“测量中心”之称。 三坐标测量机主要由四大部分组成:主机机械系统(X、Y、Z三轴或其它)、测头系统、电气控制硬件系统、数据处理软件系统(测量软件)。 三坐标测量机的出现是标志计量仪器从古典的手动方式向现代化自动测试技术过渡的一个里程碑。三坐标测量机在下述方而对三维测量技术有重要作用: (1)解决了复杂形状表面轮廓尺寸的测量,例如箱体零件的孔径与孔位、叶片与齿轮、汽车与飞机等的外廓尺寸检测; (2)提高了三维测量的精度,目前高精度的坐标测量机的单轴精度,每米长度内可达1μm以内,三维空间精度可达1μm一2μm。对于车间检测用的三坐标测量机,每米测量精度单轴也可达3μm一4μm; (3)由于三坐标测量机可与数控机床和加工中心配套组成生产加工线或柔性制造系统,从而促进了自动化生产线的发展; (4)随着三坐标测量机的精度不断提高,自动化程度不断发展,促进了三维测量技术的进步,大大地提高了测量效率。尤其是电子计算机的引入,不但便于数据处理,而且可以完成CNC的控制功能,可缩短测量时间达95%以上。 2本课题相关技术的国内外发展概况 2.1三坐标测量机的发展历程 三坐标测量机是集机械、光学、控制技术、计算机技术为一体的大型的精密测量仪器,由于它的通用性强,测量范围大、精度高、效率高、性能好,因此自1959年
液压马达在低速时产生爬行现象的原因
液压马达在低速时产生爬行现象的原因 液压马达在低速时产生爬行现象的原因是: (1)摩擦力的大小不稳定。通常的摩擦力是随速度增大而增加的,而对静止和低速区域工作的马达内部的摩擦阻力,当工作速度增大时非但不增加,反而减少,形成了所谓“负特性”的阻力。 另一方面,液压马达和负载是由液压油被压缩后压力升高而被推动的,因此,可用图4-1(a)所示的物理模型表示低速区域液压马达的工作过程:以匀速v0推弹簧的一端(相当于高压下不可压缩的工作介质),使质量为m的物体(相当于马达和负载质量、转动惯量)克服“负特性”的摩擦阻力而运动。当物体静止或速度很低时阻力大,弹簧不断压缩,增加推力。 只有等到弹簧压缩到其推力大于静摩擦力时才开始运动。一旦物体开始运动,阻力突然减小,物体突然加速跃动,其结果又使弹簧的压缩量减少,推力减小,物体依靠惯性前移一段路程后停止下来,直到弹簧的移动又使弹簧压缩,推力增加,物体就再一次跃动为止,形成如图所示的时动时停的状态,对液压马达来说,这就是爬行现象。 液压马达爬行的物理模型 (2)泄漏量大小不稳定。 液压马达的泄漏量不是每个瞬间都相同,它也随转子转动的相位角度变化作周期性波动。由于低速时进入马达的流量小,泄漏所占的比重就增大,泄漏量的不稳定就会明显地影响到参与马达工作的流量数值,从而造成转速的波动。当马达在低速运转时,其转动部分及所带的负载表现出的惯性较小,上述影响比较明显,因而出现爬行现象。 实际工作中,一般都期望最低稳定转速越小越好。 7.最高使用转速液压马达的最高使用转速主要受使用寿命和机械效率的限制,转速提高后,各运动副的磨损加剧,使用寿命降低,转速高则液压马达需要输入的
机床爬行现象的分析及消除方法
机床爬行现象的分析及消除方法 摘要: 机床进给系统的运动件,当其运行速度低到一定值时,往往不是作续匀速运动,而是时走时停、忽快忽慢,这种现象称之为爬行。爬行是机床运动中常见的现象,以磨床居多,严重影响着工作的表面质量和尺寸精度,由于引起其原因复杂,往往不易排除,所以一直被认为是机床运动中最棘手的故障之一。本文简述了机床导轨爬行产生的机理以及消除方法。 关键词:爬行导轨摩擦因数刚性 爬行是机床常见而不正常的运动状态,主要出现在机床各传动系统的执行部件上(如刀架系统、工作台等),且一般在低速行时出现较多。运动速度低时,润滑油被压缩,油膜变薄,油楔作用降低,部分油膜破坏,摩擦面阻力发生变化。通常情况下,轻微程度的爬行有不易察觉的振动,显著的爬行则是大距离地跳动。进给运动中的爬行现象破坏了系统运动的均匀性,不仅使被加工件精度和表面质量下降,也会破坏液压系统工作的稳定性,使机床导轨加速磨损,甚至产生废品和事故。比如磨床出现爬行时,会使磨工件的表面粗糙度增大;坐标镗床出现爬行,会使精确定位难以实现。因此,为了避免爬行的产生,必须分析清楚产生爬行的原因,一旦出现爬行现象,就要采取措施加以排除。 一、机床产生爬行的原因 产生爬行的原因可归结为如下几点: (1)摩擦副存在着静动摩擦系数之差。当处于边界摩擦时,动摩擦系数又随滑动速度的增加而降低。这就可能使系统具有负阻尼或零阻尼; (2)运动件的质量较大,因而具有较大的惯性; (3)传动机构的刚度不足。 机床在实际使用中,爬行现象主要是在传动系统刚性不足,驱动力与负载摩擦阻力波动变化的情况下形成。机床液压系统侵入空气,液压元件间隙增大及机械装置自身原因都可能引起爬行故障。爬行只在低速运行时才会出现,高速时,从动件的速度来不及超过原动件,弹簧始终处于压缩状态,没有放能的阶段,另外,高速时润滑油的油楔作用增大,更接近于液体摩擦,于是静、动摩擦系数之差减小,所以,高速时不会产生爬行现象。事实上,存在明显的临界爬行速度低于此速度时,爬行立即出现;高于此速度时,爬行即消失。产生原因可用实例来说明:假设有一原动件通过弹簧推动另一从动件,当原动件以等速向前运动,通过弹簧推动从件在平面上滑行时,当原动件启动后,首先需压缩弹簧一段距离,直到足以克服从动件的静摩擦力时,从动件才会起动,此时弹簧蓄能。当从动件起动后,由于动摩擦系数小于静摩擦系数,于是使从动件获得一个加速度,此时弹簧放能。如果移动速度很慢,弹簧的压缩量又较大,那么从动件的速度很快就会超过原动件,产生一个跳跃,直到弹簧压力和动摩擦力平衡后,从动件开始减速,但因为惯性,但因为惯性,还会再向前冲一段距离。至此,从动件因为失去了原动力就会停下来,直到原动件重新压缩弹簧到能克服从动件的静摩擦力