弯曲件回弹问题分析

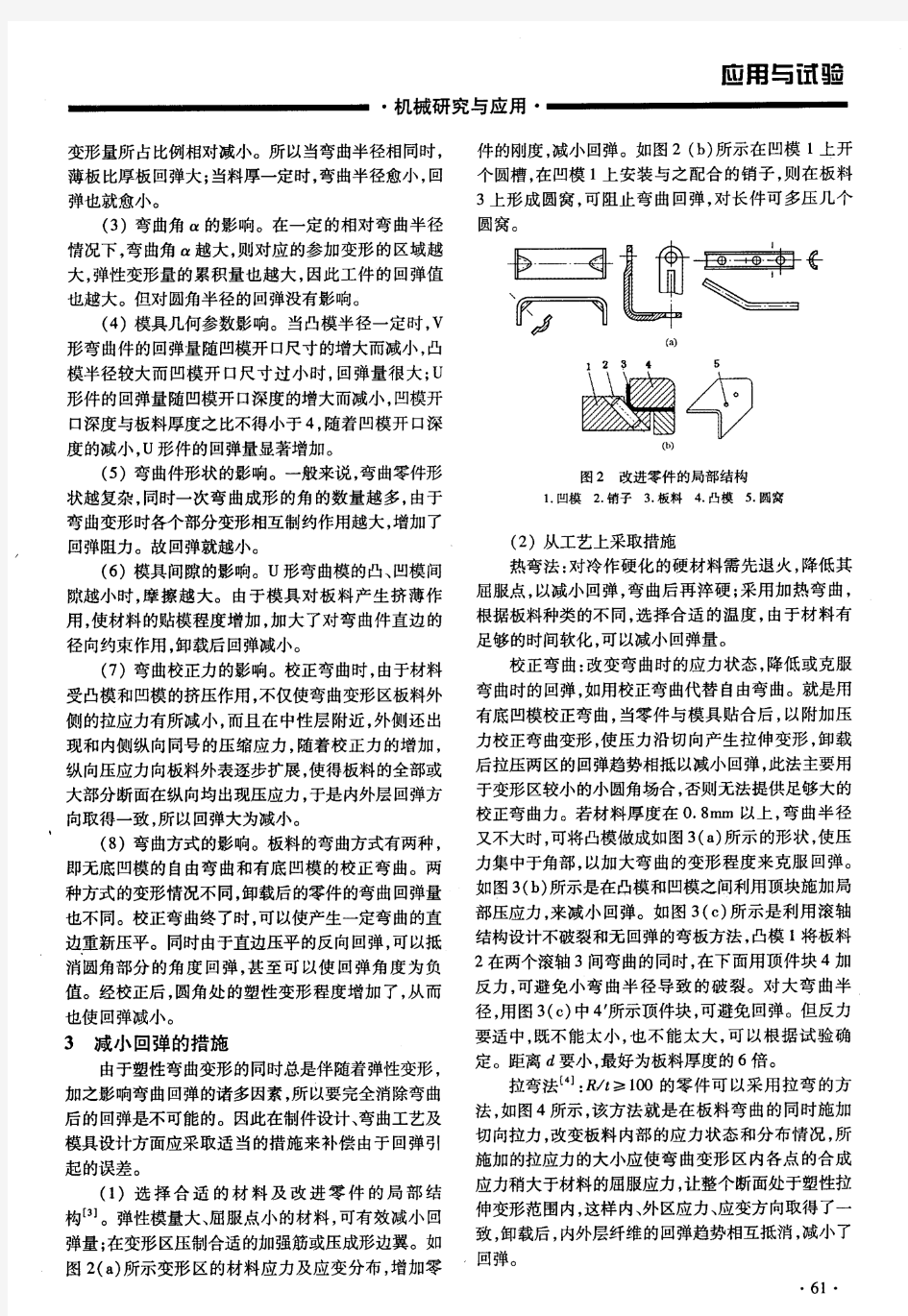
钣金弯曲回弹及控制
[摘要] 本文分析了弯曲回弹的影响因素,且着重介绍了控制弯曲回弹的具体措施。 正如起皱影响拉深件质量一样,回弹则主要影响弯曲件质量,故弯曲回弹及其控制是模具工作者一直所关心的问题。可以说任何板科塑性变形,卸载后都不可避免地要产生回弹,只不过弯曲表现得更为突出一些。究其原因是还可以有这么几点:其一是弯曲变形时内、外层应力性质相反,卸载后弹复方向一致,故而弯曲件形状、尺寸变化大;其二是弯曲加工不像拉深、翻边等工序那样为封闭形冲压,而呈非封闭状态,故而相互牵拉少,易于造成大的弹复;其三是弯曲加工中变形区小,不变形区大,大面积的不变形区对小面积变形区的牵连影响,使得小面积的变形区很难达到纯塑性弯曲状态。 现有理论认为即使材料在加工中内外纤维全部进入塑性状态,弹性变形消失了,也会出现回弹现象。 a 弹性弯曲 b弹塑性弯曲 c纯塑性弯曲 弯曲过程中毛坏变形区内切向应力分布情况。图la为弯曲初始阶段相对弯曲半径r/t较大,板料内部仅发生弹性弯曲;随着弯曲力加大、r/t值小、弯曲变形程度逐步增大,表层的切向应力达到屈服点,进而向板料中心扩展,则板料内部处于弹塑性变形状态;当r/t值继续减少到一定程度时,板料内、外层和中心的切向应力全部超过屈服点进入全塑性状态。塑性弯曲时总是伴有弹性变形的现象。2a 所示为纯塑性弯曲应力状态,2b为其卸载应力,2c为卸载后弯曲件在自由状态下的断面内残余应力;3为弹一塑性弯曲卸载过程中毛坏断面内切向应力变化情况。3a为卸载时应力,3c为卸载后弯曲件在自由状态下的断面内残余应力。由此可见,塑性弯曲卸载后弹复是不可避免的。 毛坯断面切向应力变化 由上所述可见干坯料回弹是客观存在的,无法改变的,只有因势利导,掌握好材料的回弹规律,尽可能准确地计称好回弹值的大小,才能有效地减少和控制好坯料的弯曲回弹。此乃是研究回弹、制订弯曲工艺、设计模具所要考虑的主要问题。 1 弯曲回弹的影响因素 回弹包括角度回弹及曲率回弹两个方面,此是弯曲变形区与不变形区两部分回弹综合效应的结果。影响回弹的因素很多,主要有:①坏料的机械性能σs、Eoσs愈高、E值愈小,弯曲回弹愈大;②变形程度r/t。在其相同的条件下,角度回弹量随r/t值增大而增大;曲率回弹量则随r/t值增大而减少; ③弯曲中心角αo弯曲中心角α大,回弹角大;④模具间隙Z。凸、凹模间隙大,回弹量大;⑤弯曲方式。自由弯曲回弹量大,较正弯曲回弹量小,全形镦校弯曲回弹量最小;⑥工件形状及材料组织状态。形状复杂,相互牵扯多回弹量小,冷作硬化后回弹量大;⑦模具结构及压边力大小。压边力大,工件弯后回弹量小。 -------------------------------------------------------------------------------- 2 回弹值的确定 确定工件的回弹值是为了采取应的措施来克服回弹以使弯曲工件达到图纸要求的精度。确定回弹值的方法有查图法、查表法和计算法一般来说都是近似的。目前不论国内还是国外对回弹的研究仍在继续。由于回弹涉及的因素多较为复杂目前还没有一个精确的计算公式。故对于回弹值的控制一般均是用不同结构的模具来修正主要是在试模中予以修正的。 3 控制回弹的措施 3.1 选择弯曲性能好的材料 用屈服极小、弹性模量大的材料作为弯曲件可获得较高的弯曲质量。此外坯料的厚度公差大小表面质量的优劣和平面度的好坏都对弯曲回弹有较大的影。对弯曲精度要求高的工件也要对坯料此方面的质量加以筛选。 3.2 选择较小的对弯曲半径 r/t值小表明变形程度大。一般在r/t≤3-5时认为板料的弯曲区已全部进入塑料状态。较小的弯曲半径对减烛回弹有利但过小的弯曲半径会使弯曲区破裂。目前资料上给出的材料最小弯曲半径主要是绝对经验数据可作为板金设计者设计工件弯曲半径的参考依据。 3.3 选择需要的模具间隙 V型弯曲其间隙值是靠高速机床来实的与模具本身无关。而对U型弯曲来说其回弹随凹模开口深
板料弯曲回弹及工艺控制
板料弯曲回弹及工艺控制 板料在弯曲过程中,产生塑性变形的同时会产生弹性变形。当工件弯曲后去除外力时,会立即发生弹性变形的恢复,结果使弯曲件的角度和弯曲半径发生变化,与模具相应形状不一致,即产生回弹。回弹是弯曲成形过程的主要缺陷,它的存在造成零件的成形精度差,显著地增加了试、修模工作量和成形后的校正工作量,故在冲压生产中,掌握回弹规律非常重要。如果在设计模具前,能准确掌握材料的回弹规律及回弹值大小,设计模具时可预先在模具结构及工作部分尺寸上采取措施,试冲后即使尺寸精度有所差异,其修正工作量也不会太大,这不仅可以缩短模具制造周期,而且有利于模具成本的降低及弯曲件精度的提高。 1 弯曲回弹的表现形式 弯曲回弹的表现形式有下列二个方面(如图1所示): (a) 弯曲半径增加:卸载前板料的内半径r (与凸模的半径吻合),在卸载后增加至r0,半径的增量为△r二r0一r (b) 弯曲件角度增大:卸荷前板料的弯曲角为α(与凸模的顶角吻合),在卸荷后增大到α0,角度增量为△α=α0一α 图1 回弹导致弯曲角和弯曲半径变化 2 弯曲回弹产生的原因 弯曲回弹的主要原因是由于材料弹性变形所引起的。板料弯曲时,内层受压应力,外层受拉应力。弹塑性弯曲时,这两种应力尽管超过屈服应力,但实际上从拉应力过渡到压应力时,中间
总会有一段应力小于屈服应力的弹性变形区。由于弹性变形区的存在,弯曲卸载后工件必然产生回弹。在相对弯曲半径较大时,弹性变形区占的比重大,回弹尤其显著。 回弹是由于在板厚方向应力或应变分布不均匀而引起的。这种应力和应变的不均匀分布是弯曲的特点,对于只施加弯矩的弯曲方式,要有效减少回弹是困难的。为了使回弹减小,应尽量使板厚断面内的应力和应变分布均匀,为此可采取在纵向纤维方向对板料进行拉伸或压缩的方法,也可采用在板厚方向施加强压的方法。在沿板的长度方向单纯拉伸变形的场合,除去外力后,由于在整个板厚断面内变形的恢复是均匀的,所以不会发生形状的变化。 3 影响弯曲回弹的因素 (1)材料的机械性能材料的屈服点σs越高,弹性模量E越小,回弹越大。 (2)相对弯曲半径R/t 弯曲半径R越大,材料厚度t越小,即相对弯曲半径R/t值越大,回弹越大。 (3)弯曲处校正力的大小校正力越大,回弹越小。 (4)凸凹模间隙间隙越大,回弹越大。间隙小于材料厚度时,有可能出现负回弹。 (5)弯曲件的形状弯曲件直边过短时,回弹较大。V型弯曲件的回弹比U型弯曲件的回弹大。 (6)凹模形状及尺寸凹模深度过小时,回弹很大。 4 控制弯曲回弹的方法与措施 减小回弹常用方法有补偿法、校正法、改变应力状态、改进工件设计等。影响弯曲回弹的因素很多,对于不同的影响因素,应采用不同的措施,也可综合运用几种方法,来减少回弹。 4.1 补偿法减少弯曲回弹 补偿法是按预先估算或试验所得的回弹量,在模具工作部分相应的形状和尺寸中予以“扣除”,从而使出模后的弯曲件获得要求的形状和尺寸。 (l) V型弯曲,如图2a所示。可在凸模和凹模上同时减小一个回弹角,使工件回弹后恰好等于所要求的角度,这种方法适用于相对弯曲半径较大,回弹较大的工件。 (2) L型弯曲,如图2b所示。凹模向内倾斜一角度△α,并同时缩小凸、凹模的间隙,单面间隙取小于材料厚度,促使工件贴住凹模。出模后工件回弹,直边恢复垂直。图2c所示,采用硬橡胶促使工件贴住凹模,补偿工件回弹。
浅谈解决弯曲件回弹现象的措施
浅谈解决弯曲件回弹现象的措施 摘要 弯曲件在机械零件中占有相当大的比例,它的质量将直接影响整机质量,而回弹是影 响弯曲件质量的重要因素,因此探讨弯曲件回弹的原因和防止措施是非常必要的。寻求防 止回弹的有效途径和方法,对保证产品质量和提高弯曲件生产的经济性是有积极现实意义的。 关键词:弯曲;回弹;措施 abstract Bending occupies a large proportion in mechanical parts, its quality will directly affect the overall quality, and the resilience is an important factor affecting the bending quality, thus to explore the causes of the springback and the prevention measures are very necessary. It is of positive and practical significance to ensure the quality of products and improve the economy of bending parts. Key words: bending; springback; measures 一、板料回弹的产生 在板料弯曲成形过程中,板料内外缘表层纤维进入塑性状态,而板料中心仍处于弹性状态,这时当凸模上升去除外载后,板料就会产生弹性回复。金属塑性成形总是伴有弹性变形,所以板料弯曲时,即使内外层纤维全部进入塑性状态,在去除外力时,弹性变形消失,也会出现回弹。弯曲时,弯曲变形只发生在弯曲件的圆角附近,直线部分不产生塑性变形。 影响板料弯曲回弹的因素很多,大体可分为以下几种:(1)材料的力学性能。(2)相对 弯曲半径 R/t的影响。(3)弯曲角的影响。(4)弯曲零件形状的影响。(5)模具几何参数 影响。(6)张力的影响。(7)工况参数。(8)模具间隙的影响。(9)弯曲校正力的影响。(10)弯曲方式的影响。 二、回弹现象的分析 由于金属板料在塑性弯曲时总伴随着弹性变形产生,当弯曲件从模具中取出之后,弯曲 件不受外力的作用,弹性变形消失,使工件的弯曲角度和弯曲半径发生变化,皆与模具的设
弯曲件的回弹及回弹值的确定实验
弯曲件的回弹及回弹值的确定实验 一、实验目的1、通过试件在V形弯曲模中的弯曲实验,观察回弹现象和学习测定弯曲回弹角的方法。2、培养分析材质和弯曲变形程度等对回弹值影响的能力和懂得针对实际情况采取减少回弹的措施。 二、实验原理弯曲工艺中的回弹,直接影响了弯曲件的精度。故研究影响弯曲回弹的因素和减少回弹的办法对保证弯曲件质量有重要意义。 弯曲的回弹值(弯曲角度和圆角半径的变化量)与下列因素有关: 1、材料的力学性能:材料的屈服强度和硬化模数D 愈大,回弹值愈大;材料的弹性模量E愈大,回弹值愈小。 2、相对弯曲半径r/t : r/t愈小,弯曲变形程度愈大,回弹值愈小,反之回弹值愈大。 3、弯曲中心角α:α的大小表达了弯曲变形区的大小,弯曲中心角愈大,所代表的弯形区愈大,回弹值愈大。 采用一副快换凸模的弯曲模进行弯曲实验,就可以测出以下几组数据: 1、相同材料、不同r/t的弯曲回弹角(包括相同厚度、
不同凸模圆角半径和相同圆角半径、不同厚度两种情况)。 2、不同材料、相同r/t的弯曲回弹角。 3、减少承压面积的凸模弯曲时的回弹角。 通过对实验数据的分析,可以看出材料的σs /E和r/t 对弯曲回弹的影响情况;以及使用减少承压面积的凸模达到减小回弹的良好效果; 利用较厚材料的弯曲,使其弯曲变形程度超过材料的极限变形程度,即r/t小于r min /t,可以观察到变形区外层材料破裂的情况。 三、实验设备、材料、模具和工具 1、J23-250型曲柄压力机一台。 2、长50mm ,宽15mm的Q195钢板31件,其中厚度分别为0.5, 1.5, 2.5mm的各10件,厚度为4mm 的一件;长宽尺寸同上,厚度为0.5mm的08钢板10件;长宽尺寸同上的H62黄铜板11件,其中厚度为0.5mm的10件,4mm的一件。 3、实验用弯曲模一副(图1),快换凸模10个,其中如图2所示的R分别为0.1,0.4,0.8,1.2,1. 5,2. 0,2. 5,3,4mm的九个,如图3所示的减少承压面积的一个。 4、一字旋具、万能角度尺、镊子各一件。
浅谈解决回弹现象的措施
目录 摘要 (Ⅱ) 关键词 (Ⅱ) 正文 (Ⅱ) 1 板料回弹的产生 (2) 2 回弹现象的分析 (2) 3 影响回弹的主要因素 (2) 参考文献 (Ⅴ) 结束语 (Ⅵ)
摘要 弯曲件在机械零件中占有相当大的比例,它的质量将直接影响整机质量,而回弹是影响弯曲件质量的重要因素,因此探讨弯曲件回弹的原因和防止措施是非常必要的。寻求防止回弹的有效途径和方法,对保证产品质量和提高弯曲件生产的经济性是有积极现实意义的。 关键词:弯曲;回弹;措施 正文: 一、板料回弹的产生 在板料弯曲成形过程中,板料内外缘表层纤维进入塑性状态,而板料中心仍处于弹性状态,这时当凸模上升去除外载后,板料就会产生弹性回复。金属塑性成形总是伴有弹性变形,所以板料弯曲时,即使内外层纤维全部进入塑性状态,在去除外力时,弹性变形消失,也会出现回弹。弯曲时,弯曲变形只发生在弯曲件的圆角附近,直线部分不产生塑性变形。 影响板料弯曲回弹的因素很多,大体可分为以下几种:(1)材料的力学性能。(2)相对弯曲半径 R/t的影响。(3)弯曲角的影响。(4)弯曲零件形状的影响。(5)模具几何参数影响。(6)张力的影响。(7)工况参数。(8)模具间隙的影响。(9)弯曲校正力的影响。(10)弯曲方式的影响。 二、回弹现象的分析 由于金属板料在塑性弯曲时总伴随着弹性变形产生,当弯曲件从模具中取出之后,弯曲件不受外力的作用,弹性变形消失,使工件的弯曲角度和弯曲半径发生变化,皆与模具的设计尺寸存在一个差值,这种现象称为弯曲件的回弹。 三、影响回弹的主要因素 3. 1 材料的机械性能 回弹的大小与材料的屈服极限成正比,与弹性模数成反比,即 Qs/E值愈小,回弹也愈小。 Qs——材料的屈服极限 E——材料的弹性模数 3. 2 相对弯曲半径 r/t
弯曲件回弹主要影响因素研究_王洪芬
第25卷第3期 吉林工程技术师范学院学报 V o l 125N o 13 2009年3月 Journa l of J ilin T eache rs Instit ute o f Eng i nee ri ng and T echno l ogy M ar 12009 收稿日期:2008-02-27 作者简介:王洪芬(1980- ),女,吉林德惠人,吉林工程技术师范学院机电工程学院助教,主要从事机械制造及冲压模具设计教学研究。 弯曲件回弹主要影响因素研究 王洪芬1 ,陶忠祥 2 (1.吉林工程技术师范学院机电工程学院,吉林长春130052; 2.空军航空大学航空机械工程系,吉林长春130022) [摘 要]板料成形过程中普遍存在着回弹问题,特别在弯曲和浅拉深过程中回弹现象更严重,在板料 成形领域,回弹已成为模具设计中的关键问题。本文旨在浅析板料成形过程中弯曲件的回弹现象,研究影响回弹的主要因素。 [关键词]弯曲件;回弹;影响因素 [中图分类号]TH 16 [文献标识码]A [文章编号]1009-9042(2009)03-0064-03 Study on theM ain I nfluence Factors of Spring Back in Bending Parts WANG H ong -fen 1 ,TAO Zhong-x iang 2 (1.Co llege of E lectro m echanical Engineer in g,J ilin T eachers Institute of Eng i neering and T echnology,Changchun J ili n 130052,China ;2.D e p art m ent of A vi a tionM echanical Eng i neering ,A viation Un i vers it y of A ir Force ,Changchun J ilin 130022,Ch i na) Abstract :Spring back ex ists w ide l y i n sheet m eta l for m ing processes ,and particularly in ben -ding and sha llo w dra w ing process .It has been the key prob le m of mould desi g n i n the fie l d o f sheetm etal for m i n g .Through the research on the pheno m enon o f spri n g back i n sheet m etal for m ing processes ,t h is paper d iscussed the m a i n infl u ence factors o f spri n g back i n bending parts . Key w ords :bend i n g parts ;spring back;i n fl u ence factors 板料成形过程中普遍存在着回弹问题,特别在 弯曲和浅拉深过程中回弹现象更严重,在板料成形领域,回弹已成为模具设计中要考虑的关键问题,由于回弹的存在,卸载后零件的形状尺寸与模具表面的形状尺寸不能完全符合,零件的尺寸精度达不到设计要求,对生产效率造成极大的影响,所以有必要对其进行深入的研究和有效的控制。回弹是不可避免的,在实际生产中,准确掌握回弹规律和回弹值大小,剖析影响回弹的因素,实用的工艺技术方法,有助于改善和消除弯曲回弹倾向,提高生产效率和工艺质量。因此,对回弹机理以及影响回弹因素的研究至关重要。本文旨在浅析板料成形回弹现象,研究影响回弹的主要因素。 1 弯曲件的回弹 1.1 回弹现象 与所有的塑性变形一样,塑性变形时伴随有弹性变形,塑性变形保留下来,而弹性变形会完全消失。由于弯曲时内、外区切向应力方向相反,因而弹性回复方向也相反,即外区弹性缩短而内区弹性伸长,这种反向的弹性回复加剧了工件形状和尺寸的改变,使弯曲件的形状和尺寸与模具尺寸不一致,这种现象叫弯曲回弹(简称回弹)。 另外,对整个坯料而言,不变形区占的比例比变形区大得多,大面积不变形区的惯性影响会加大变形区的会弹,这是弯曲回弹比其他成形工艺回弹严重的另一个原因。他们对弯曲件的形状和尺寸变化影响十分显著,加之回弹是不可避免的,因此,与其他变形工序相比,弯曲过程的回弹现象是一个影响弯曲件精度的重要问题。
1弯曲回弹的表现形式是什么
1弯曲回弹的表现形式是什么?产生回弹的主要原因是什么? 弯曲回弹的表现形式为:弯曲半径的变化和弯曲角的变化。 产生回弹的主要原因是:材料的力学性能、相对弯曲半径、弯曲中心角、弯曲方式、模具间隙等。 2拉深变形区的应力应变的特点是什么? 拉深变形区为凸缘部分,切向为压应力,径向为拉应力,切向压应力的绝对值最大,所以在切向是压应变,径向为拉应变。 3拉深时容易出现什么样的质量问题?为什么? 凸缘的起皱和底部圆角R处的开裂,前者是因为切向压应力太大,后者是R处的塑性变形小,加工硬化现象弱。 4、请简述拉深变形的变形区的应力和应变的特点。 在拉深过程中,毛坯受凸模拉深力的作用,在凸缘毛坯的径向产生拉伸应力σ1,切向产生压缩应力σ3。在它们的共同作用下,凸缘变形区材料发生了塑性变形,并不断被拉入凹模内形成筒形拉深件。 5、拉深时的危险端面在哪里?为什么? 危险端面为筒壁和圆筒底部的过渡区,材料承受筒壁较大的拉应力σ1、凸模圆角的压力和弯曲作用产生的压应力σ2和切向拉应力σ3。在这个区域的筒壁与筒底转角处稍上的位置,拉深开始时材料处于凸模与凹模间,需要转移的材料较少,受变形的程度小,冷作硬化程度低,加之该处材料变薄,使传力的截面积变小,所以此处往往成为整个拉深件强度最薄弱的地方,是拉深过程中的“危险断面”。 6什么是最小相对弯曲半径? 板料在弯曲时,弯曲半径越小,板料外表面的变形程度越大。如果板料的弯曲半径过小,则板料的外表面将超过材料的变形极限而出现裂纹。所以,板料的最小弯曲半径是在保证变形区材料外表面不发生破坏的前提下,弯曲件的内表面所能弯成的最小圆角半径,用r min表示。 最小弯曲半径与板料厚度的比值r min/t称为最小相对弯曲半径,它是衡量弯曲变形程度大小的重要指标。 7 拉深件的变形有以下特点: (1)变形区为毛坯的凸缘部分,与凸模端面接触的部分基本上不变形; (2)毛坯变形区在切向压应力和径向拉应力的作用下,产生切向压缩和径向拉伸的“一拉一压”的变形。 (3)极限变形参数主要受到毛坯传力区的承载能力的限制; (4)拉深件的口部有增厚、底部圆角处有减薄的现象称为“危险断面”(底部的厚度基本保持不变); (5)拉深工件的硬度也有所不同,愈靠近口部,硬度愈高(这是因为口部的塑性变形量最大,加工硬化现象最严重) 8.什么是弯曲回弹?影响弯曲回弹的主要力学性能是什么,他们是怎样影响的?? 答:当弯曲结束,外力去除后,塑性变形留存下来,而弹性变形则完全消失。产生了弯曲件的弯曲角度和弯曲半径与模具相应尺寸不一致的现象称为弯曲件的弹性回跳