可逆式冷轧机AGC系统

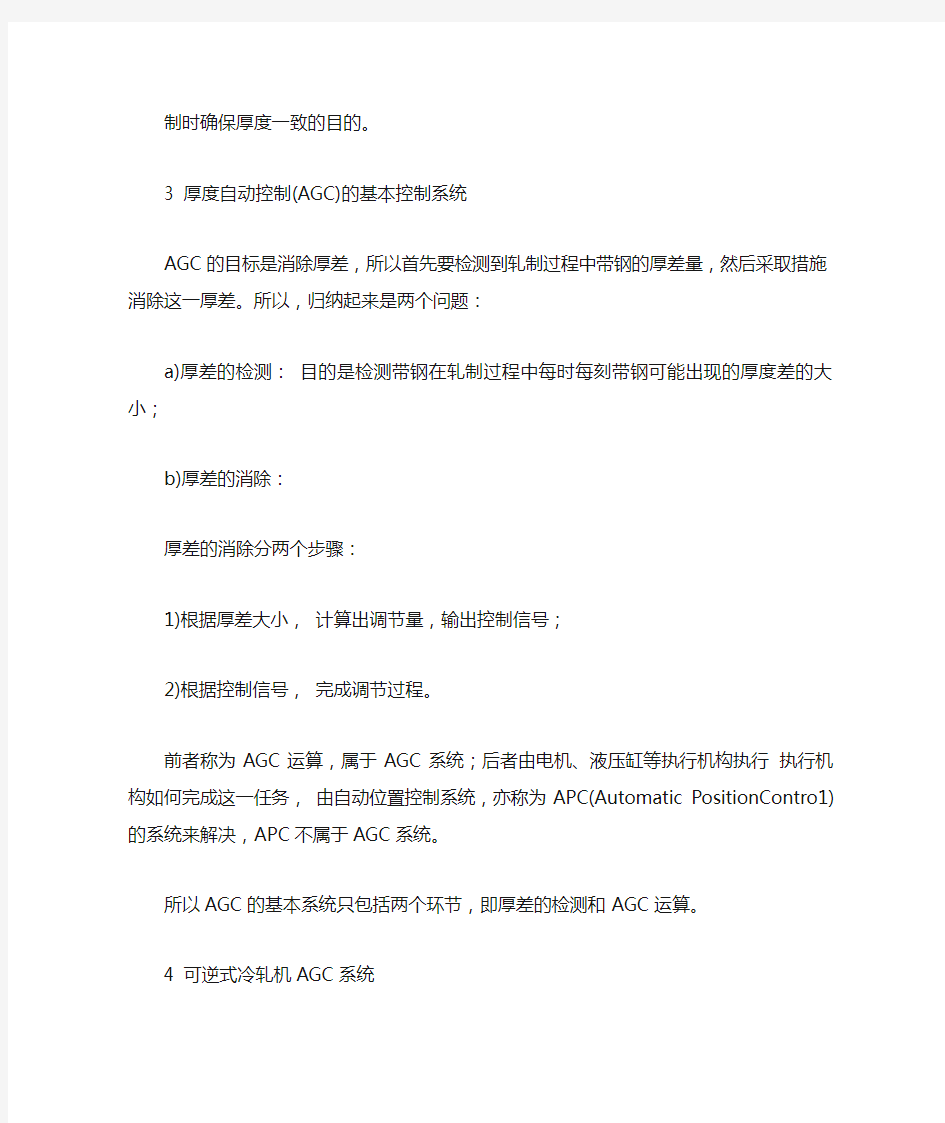
可逆式冷轧机AGC系统
1 概述
厚度自动控制(Automatic GaugeControl简称^AGC)在钢板轧机,特别是带钢轧机上得到普遍应用,从50年代初步应用到现在,已发展到十分成熟的地步。板带材厚度控制应包括板带横向厚度和纵向厚度控制,前者通常由板形控制来解决,后者一般由厚度控制系统来解决。
AGC系统的作用是消除轧制过程中所产生的带钢纵向长度上的厚度差,使带钢后部保持与前端厚度一致。它不管原始的辊缝设定值,而只能在预设定的基础上,使板带前后端厚度都控制在公差范围之内。
2 可逆式冷轧机厚控系统的特点
可逆式冷轧机不同于连续式冷轧机,其工艺特点是:
(1)轧件在可逆式轧机中往返轧制,轧制过程中要加速和减速;
(2)在一台轧机上采用多道次轧制,每道次的带钢厚度及硬化程度不同;
(3)带钢的性能随道次变化。
所以,可逆式冷轧机的厚控系统要考虑其往复可逆轧制的需要,在轧机前后各设一台测厚仪,而且当轧机逆轧时,要求反馈AGC系统能自动从一台测厚仪转到另一台。同时,主电动机速度要与卷取机速度联调,使张力调节充分有效,达到在加速或减速和稳态轧
制时确保厚度一致的目的。
3 厚度自动控制(AGC)的基本控制系统
AGC的目标是消除厚差,所以首先要检测到轧制过程中带钢的厚差量,然后采取措施消除这一厚差。所以,归纳起来是两个问题:
a)厚差的检测:目的是检测带钢在轧制过程中每时每刻带钢可能出现的厚度差的大小;
b)厚差的消除:
厚差的消除分两个步骤:
1)根据厚差大小,计算出调节量,输出控制信号;
2)根据控制信号,完成调节过程。
前者称为AGC运算,属于AGC系统;后者由电机、液压缸等执行机构执行执行机构如何完成这一任务,由自动位置控制系统,亦称为APC(Automatic PositionContro1)的系统来解决,APC不属于AGC系统。
所以AGC的基本系统只包括两个环节,即厚差的检测和AGC运算。
4 可逆式冷轧机AGC系统
典型的可逆式冷轧机AC,C自动厚度控制系统如图1所示,其具体构成包括轧制压力、前馈加减速补偿、压下监视器、张力监视器、弯辊力补偿、轧辊偏心率控制AGC等几个部分。
可逆式冷轧机各种AGC的功能为:
a)轧制压力AGC
把轧制压力变动视为板厚变动,按照下式进行控制;
这种AGC,因为直接检出和控制轧机轧制状态,与别的AGC相比,具有更强的抗高周波外部干扰能力。通常在加减速轧制时,因轧制速度的变化会使工作辊与
轧材的润滑状态改变,等价地造成了材料塑性系数变化,进而引起轧机出口厚度的变动,此时.AGC将上述改变认作轧制压力的变动而进行控制。
因此,在对由于板厚变动而产生的压力波动的大小及轧制压力杂波等进行考虑时,可在带锕形状等轧制时不产生故障的限度内尽量扩大增益。
b)加减速补偿AGC
加减速部分引起的板厚波动,仅用轧制压力AGC不能完全消除。作为补救手段,要消除由于润滑状态改变带来的板厚变动,用
加减速补偿AGC可对应轧制速度的变化操作轧辊辊缝,按照下式进行控制:
钢卷的头尾部的厚度,由于板形等因素,通常都比目标值要大,这是因为在道次切换时轧辊辊缝设定误差,或者有操作者的手动压下介入造成的。加速开始时的厚度偏差,因为钢卷本身或辊缝偏差等,所以也较大。
此种控制的功率输出要适时,过早输出会增加超厚部分的长度,但滞后又会使负偏差长度缺陷增加。为此,采用了监视器监测轧机出口厚度偏差,控制在一定数值以内时自动地开始工作。
c)前馈AGC
用x射线测厚仪检测出轧机进口处带钢厚度的变化,与带钢移动时同步操作轧辊辊缝并按下式进行实时控制:
d)、压下监测器AGC
上述AGC都可以对出口带厚进行预控制。压下监测器AGC用于使压下后的板厚与目标值一致。为此,由轧机出口处x射线测
厚仪所测板厚偏差信号依据下式控制辊缝:
在AGC 稳定界限以内尽量提高其应答性,根据速度改变其增益,此AGC在所有轧制状况下都能适用。预估器监控AGC的滞后时间随着轧制速度的变化而变化,传统的监控AGC都是采用比例一积分控制方式,这种控制方式的主要缺点是调节速度慢,易产生振荡和极限环振荡,为防止极限环振荡,一般在系统内设置—死区,靠牺牲控制精度来保证系统的稳定。
因此,传统的控制方式对提高精度有局限性。根据控制理论.可采用史密斯补偿方案。在监控AGC系统中增加了一个预估模型反馈环节.通过预估模型来预测输出的变化并进行超前反馈以抵消实测滞后的影响。
e)张力监测器AGC
与压下监测器AGC的用途相同,但只改变轧机入口处张力开卷机的张力,并按下式控制辊缝:
对于软钢撮薄带材,压力和张力的影响大,用张力AGC的作用显著。但是张力的极端变动和轧材滑动等要产生问题,故张力的变动量要限定在20%以内,并设置控制功率的上下限才能有效工作。
另一方面,影响系数对于各种钢、各种板厚由实验求得,其值非常大,而对软钢极薄带材需要修正者仅为数微米,故必须把轧机入口处的张力控制在1O%的范围内。因而,可以限制过早开始定时控制,也可以控制功率饱和,待出口侧板
厚偏差达到一定值时自动启动AGC,与此同时,比例增益起动从0到设定值是以一定的比例提高增益。
f)轧辊弯辊力补偿
在AGC操作轧辊间隙中带材形状会发生变化。作为修正手段,相应于轧制力的变化依照下式修正轧辊弯辊度:
影响系数用分割模型由数值计算得出。为了能对各种各样的轧材进行高精度轧制,可以根据从生产过程计算机得到的指令,变更各道次采用的AGC模型和增益。可逆式轧机与串列式轧机不同,同一个钢卷道次内部存在着头尾部的加减速问题.故为了减少头尾部的超差,要特别注意该部分的精度。另外,各种AGC 同时使用时不能产生干扰和误动作,以使其接近要求标准。
5 可逆式冷轧机AGC技术的新发展
随着计算机技术的发展和广泛应用,国外可逆式冷轧机A6C技术得到了迅速的发展,功能不断完善,流量AGC(MassflowAGC)也开始在可逆式冷轧机上使用.使厚度控制精度达到了相当高的水平。流量AGC国外早在70年代就开始成功地应用在冷连轧机上,80年代开始在可逆式冷轧机上使用.如美国2S公司和Waterbury公司的流量AGC在可逆式冷轧机上应用已相当成熟。国内90年代引进的轧机上有的装备了流量AGC,南京钢铁公司冷轧薄板厂1200WS四辊可逆式冷轧机组也采用了国内自行开发的这种新的AGC技术。
由于压力AGc受压力测量精度以及轧机刚度非线性等的限制,不能进一步提高控制精度,而且压力AGC亦不能消除由轧机本身原因引起的厚度变化。预控AGC虽能很好地消除入口侧带材厚度差引起的厚度变化,但也不能消除由轧机原因引起的厚度变化。监控AGC和张力AGC由于受刹厚仪安装位置的限制,是反馈滞后的纯滞后控制系统。使监控AGC和张力AGc的控制精度受到了限制。为了进一步提高整个厚控系统的控制精度,在系统中采用了新的控制技术一流量AGC。可逆式冷轧机上用的流量AGc是根据轧制带材质量不变原理(即流入轧机的带材体积与流出轧机的带材体积恒定原理)来测量并控制出口带材厚度的。
控制模型为:
因为认为在冷轧中的宽度是不变的,即B1 = B2。
所以有:
流量AGC就是根据入口厚度、入口速度和出口速度计算出出口厚度Ah 并进行控制的,由于速度信号和厚度信号的测量精度都能达到很高的要求,而且入口侧厚度偏差可精确测量和准确地估算出达到轧机的时间,故按上式可以达到很高的精度对于采用脉冲发生器测量速度的方式,速度信号只能按单位时间的平均速度计量.并且流量AGc只能按每段的平均厚度进行计算和控制。每段的长度取决于脉冲发生器的分辨率,脉冲发生器的分辨率越高,分段就愈短,滞后时间就愈小,控制精度也就愈高。
另外.还有动态设定型压力b,GC,其控制模型为:
由于动态设定型压力AGC具有响应速度快的特点,因此当轧机入口测厚仪不工
作时,即预控AGC与流量AGC不能工作,K取0.7~0.9,使轧机的等效刚度大于其自然刚度.为硬特性,能很好地消除来料所引起的出口厚度偏差。当两台测厚仪同时工作时,预控AGC与流量AGC投入工作.厚度偏差主要依靠预控AGC与流量AGC来消除.K:-M/Q,使轧机的等效刚度为零,为恒压力轧制(平整机特性),以消除轧辊偏心对出口厚度的影响当轧机用于平整时.除了由液压压上控制系统直接完成恒压力控制外,还可在轧制状态下用动态设定型压力AGc的恒压力特性来完成控制,控制效果是相同的
6 结柬语
可逆式冷轧机的AGC技术的发展到目前已比较成熟,如何应用以及如何确定模型中的参数,需要我们深入而细致的分析研究。
1200六辊可逆冷轧机电气自动化系统控制方案
1概述 根据《1200六辊可逆冷轧机技术规格电气招标书》所提供的工艺设备和技术要求,并参考了同类型的单机架六辊可逆冷轧机的工艺技术,编写了本电气传动及基础自动化控制的技术方案。 2 供电 2.1 电气设备运行条件 1)电气设备运行环境要求 环境温度 现场:0~40?C 电气室:10~35?C 操作室:25±5?C 空气湿度:相对湿度≤95%且无凝露; 污染等级:III级,无火灾爆炸危险、无导电性尘埃、不腐蚀金属物及不破坏绝缘介质的环境。 2)电气设备运输及储存环境要求 环境温度-20~65?C ; 空气湿度及污染等级要求与运行时相同。 3)电气设备使用的电压等级及技术条件 本机组所使用电气设备电压等级符合我国国家标准,主要用电设备的电压等级为: ◆供电电压及频率:10±5%kV,50±1Hz ◆低压供电电压:AC380/220V ◆交流电动机电压:AC380V ◆直流电动机电压:DC440~660V ◆电磁阀:DC24V
◆电磁抱闸:AC220V ◆控制电压:AC220V,DC24V ◆保护地:接地电阻<4Ω ◆系统地:接地电阻<4Ω 2.2低压供配电 辅传动供电系统 (1)辅传动供电系统单线图见MCC单线图。 (2)MCC设备(见附表) 由于本机组负荷较小,因此不设负荷中心。本机组负荷MCC(即马达控制中心)将采用GGD3柜,包含MCC的受电、馈出回路、UPS 系统、比例、伺服阀控制回路和照明开关柜,开关柜额定短路短时承受能>80kA/s。 额定短路分断能力与电网短路电流相适应,Icu >50kA 根据需要配置必要的电流、电压表计,端子板采用Phoenix端子。 单机架可逆冷轧机组设一套MCC,不同容量不同控制类型的回路至少有一个备用回路。 注①:主传动电动机均配置有空间加热器,这些加热器是在长期停机时防止电机绕组受潮而设置的。由本MCC供电。 注②:为了保证乳化液站的检修供电,需要检修电源或者备用一路供电回路。 (3) UPS电源 为保证控制系统运行的可靠性,机组设置一套容量为10kV A的UPS 电源为机组控制系统(PLC、AGC控制器、HMI设备等)提供可靠稳定电源。电池和逆变器选用进口产品。 容量:10kV A,30min;进线:220V AC
四辊可逆冷轧机传动电控系统设计设计
摘要 轧制是各种变形手段中效率高、产量大、成本低、成型精确的加工方式。而轧机是实现金属轧制过程的设备,泛指完成轧材生产全过程的装备,包括有主要设备﹑辅助设备﹑起重运输设备和附属设备等。从炼钢厂出来的钢坯还仅仅是半成品,必须到轧钢厂去进行热轧与冷轧后,才能成为合格的产品。 论文通过吸收和借鉴校内实训中心的四辊可逆冷轧机的先进设计理念,提出了四辊可逆冷轧机的电控系统设计方案,并总结出了电气调试方案。完成了整个轧机电控系统的硬件方案设计以及相关器件的选型工作。在硬件设计中,提出了PLC+变频器+电机等的闭环控制系统,从而达到变频器控制电机转速的目的。 关键词:轧机电控系统四辊闭环
ABSTRACT Means all kinds of deformation in rolling, high efficiency, large output, low cost, precision molding processing methods. The mill is the equipment of metal rolling process, rolled the whole production process refers to the completion of equipment, including major Equipment, Auxiliary Equipment, lifting and other transport equipment and ancillary equipment. Out from the steel mill is just the semi-finished billets to be to go for hot and cold rolling mills, the products can become qualified. Articles by absorb and learn the four-campus training center roller cold rolling mill of the advanced design concept, put forward a four-high reversing cold rolling mill electrical control system design. Completion of the entire rolling mill electrical control system hardware design and selection of work-related devices. In the hardware design is proposed such as PLC + inverter + motor closed-loop control system, so as to achieve the purpose inverter control motor speed. Keywords:Rolling mill;Electronic Control System;Four roller;Closed loop
650全液压四辊可逆轧机技术协议1 设备主要工艺参数 1.1 原料:经酸洗后的热轧卷板、热轧中宽带钢 材质:优质碳素钢、低合金钢 厚度:δ≤4.5 mm 最大强度极限:бb=610 N/mm2 最大屈服极限:бs=360 N/ mm2 宽度:≤650 mm 卷径:Φ508/Φ900~Φ1650 mm 最大卷重:8 T 1.2 成品 成品厚度:≥0.2 mm 带钢宽度:≤520 mm 卷径:Φ508/Φ900~Φ1650 mm 最大卷重:8T 成品厚度公差:0.01~0.02 mm(去掉头尾各8米) 1.3 主要技术参数: 最大轧制力:5000 KN 最大轧制力矩:35 KN . M 最大轧制速度:8 m/s 穿带速度:0.3 m/s 开卷最高速度:3.3 m/s 卷取最高速度:8.2 m/s 卷取张力:0~60 KN 工作辊规格:Φ220/Φ190×650 mm 支撑辊规格:Φ650/Φ680×600 mm 开卷机卷筒直径:Φ480~Φ520 mm 卷取机卷筒直径:Φ488~Φ508 mm
轧制线标高:+1000 mm 最大弯辊力:400 KN 冷却液类型:乳化液 工艺润滑系统流量:1000 L/min 稀油润滑系统流量:250 L/min 稀油润滑系统压力:0.4 Mpa 稀油润滑系统介质:中负荷No20 机组进料方向: 液压系统压力:压下、弯辊液压系统:3~25Mpa 一般液压系统:0~10Mpa 设备总重量:约140 T 传动方式:工作辊传动 年产量: 传动电机: 主机电机Z560-2A 440V 600KW n=600~1400rpm 1台 卷取电机Z4-355-11 440V 180KW n=500~1500rpm 2台 开卷电机Z4-250-41 440V 75 KW n=500~1500rpm 1台 2 设备组成 2.1 机械设备 2.1.1 开卷机1台 悬臂机构,由传动装置和卷筒组成,传动装置为二级减速箱,卷筒为四棱锥结构,主要参数为: 卷筒工作直径:Φ500 mm 卷筒涨缩范围:Φ452~Φ544 mm 开卷速度:≤3.3 m/s 开卷张力:4~30 KN 对中移动范围:±50 mm 对中横移缸:缸径Φ125 mm,
附录2 文献综述 一、课题的国内外现状 HC 轧机全名为HITACHI HIGH CROWNCONT ROLMILL,即日立中心高性能轧辊凸度控制轧机。该机型是日立公司于1972 年研究开发的轧机,两年后正式投入工业化应用。它具有普通四辊冷轧机不能达到的性能和优点,首先在日本得到推广使用,继而受到全世界的瞩目,广泛用于热轧和冷轧生产中的单机可逆轧机、连轧机和平整机。其主要结构特点是:在支撑辊和工作辊之间加入一对能够沿着轧辊轴向相对移动的中间辊,通过中间辊的相对移动来改变轧制压力在带钢方向上的分布,加上工作辊的正负弯辊作用,对改善带钢板形起到了明显的效果。 在国外,除日本各大钢铁公司普遍采用HC轧机机型外,美国、德国、加拿大、瑞典、巴西、墨西哥、韩国等国家均从日本引进了该轧机。 在国内,武汉钢铁公司为生产镀锡板基板,1987年首先引进1250HC六辊轧机,之后上海宝钢、辽宁鞍钢等国内各大钢铁公司先后引进了这种轧机机型。在引进设备的同时,国内相关单位也开始跟踪并开发国产的HC六辊轧机。国产大型六辊轧机已成功地用于工业生产,而且主要的技术水平和功能已达到国外同类设备水平。但是,六辊轧机种工作辊弯辊、中间辊横移、中间辊弯辊三种方式与带材板型的检测、控制相结合,实施有效的闭环控制,目前国内虽然在这方面也取得了不少成绩,但在精确度和稳定性方面仍然需要花大力气研究。 二、现有的主要研究成果 随着科学技术的不断进步,日本最近几年又在HC轧机的结构上进行了改进,推出了一些新型的HC轧机。例如,HCMW 轧机是综合HC轧机和HCM轧机的优点,其特点是中间辊和工作辊都能轴向移动。 在国内,HC轧机方面的研究也取得了很多可喜的成绩:降低轧辊表面缺陷的措施,预防轧辊剥落的措施,预防轧辊断裂的措施。近几年来,随着控制理论的发展,人们不断把一些新型控制方法引入板形自动控制系统中,以弥补PID控制中很难满足高精度控制要求的不足,比如基于动态负荷分配的板形控制方法。在日本,成品机架或成品道次采用软刚度的方法
第一章总的设计概述 1.1 设计目的 运动控制系统是自动化专业的主干专业课,具有很强的系统性、实践性和工程背景,运动控制系统课程设计的目的在于培养学生综合运用运动控制系统的知识和理论分析个解决运动控制系统设计问题,使学生建立正确的设计思想,掌握工程设计的一般程序、规范和方法,提高学生调查研究、查阅文献及正确使用技术资料、标准、手册等工具书的能力,理解分析、制定设计方案的能力,设计计算和绘图能力,实验研究及系统调试能力,编写设计说明书的能力。 1.2 设计内容 (1)根据工艺要求,论证、分析、设计主电路和控制电路方案,绘出该系统的原理图。 (2)设计组成该系统的各单元,分析说明。 (3)选择主电路的主要设备,计算其参数(含整流变压器的容量S,电抗器的电感量L,晶闸管的电流、电压定额,快熔的容量等),并说明保护元件的作用(必须有电流和电压保护)。 (4)设计电流环和转速环(或张力环),确定ASR和ACR(或张力调节器ZL)的结构,并计算其参数。 (5)结合实验,论述该系统设计的正确性。 1.3 课题设计要求 四辊可逆冷轧机的卷宗取机直流调速系统设计 (1)生产工艺和机械性能 四辊可逆冷轧机是供冷轧紫铜及其合金成卷带材之用,为提高其生产效率,冷轧机要往、返轧制其金属材料。直到达到要求的厚度时才停止。因为要求冷轧机左右两边的两台卷取机在从左往右的正向轧制过程中,左边一台卷取机用,其
工作在发电机状态,右边一台卷取机作卷取机用,工作在电动状态。若逆向轧制(从左往右轧制),右边卷取机作开卷机,工作在发电机状态,左边卷取机则作卷取机用,工作在电动状态。 两台卷取机的电动机参数完全一样,机械参数如下: 带卷内径(卷筒直径):500mm 带卷外径:680~1100mm 带卷最大重量:2000kg 带卷最大张力:2000kg 卷取机传动比:i=1.87 图一 设备结构简图 (2)设计要求 1、两台卷取机控制原理完全一样,仅设计其中一台; 2、技术指标:稳态无静差,电流超调量% 5≤σi ,空载启动至额定转速 时的转速超调量% 10≤σ n 能实现快速制动。 (3)直流电动机参数: 150n P k w =、 230n U V =、 165n I A =、 1400m in n n r =、 0.08a R =Ω 电枢回路电阻0.18R =Ω 、电流过载倍数 2.5λ=、2 2 121.5.G D N M =。
前言 直流电机在现代工业中是一种很重要的电机.它可以作电动机使用,也可以作发电机使用,此外还有其它特殊的用途。 直流电动机具有良好的起、制动性能,宜于在大范围内平滑调速,在许多需要调速或快速正反向的电力拖动领域中得到了广泛的应用。近年来,在电力电子变换器中以晶闸管为主的可控器件已经基本被功率开关器件所取代,因而变换技术也由相位控制转变成脉宽调制(PWM);交流可调拖动系统正逐步取代直流拖动系统。然而,直流拖动控制毕竟在理论上和实践上都比较成熟,而且我国早期的许多工业生产机械都是采用直流拖动控制系统,所以它在工业生产中还占有相当大的比重,短时间内不可能完全被交流拖动系统所取代。 从生产机械要求控制的物理量来看,电力拖动自动控制系统有调速系统、位置随动系统(伺服系统)、张力控制系统、多电机同步控制系统等多种类型,各种系统往往都是通过控制转速来实现的,因此调速系统是最基本的电力拖动控制系统。 调速系统按照不同的标准又可分为不同的控制系统。但是,从一定角度上来说,可以把调速系统笼统的分为开环调速系统和闭环调速系统。开环调速系统结构简单、容易实现、维护方便,但是它的静态和动态性能往往不能满足生产和控制要求。而闭环控制系统可以很好的解决这些问题,因此在实际生产中得到了广泛的应用。其中,转速、电流双闭环控制直流系统是性能最好、应用最广的直流调速系统。 本文为直流调速系统的设计,包括系统设计方案选择,各单元的组成,元件的参数与选择等内容!通过本系统的设计,了解运动控制在工业上的应用!
目录 前言 0 第一章设计的介绍 (3) 1.1 设计目的 (3) 1.2 设计内容 (3) 1.3 设计题目 (3) 1.3.1 生产工艺和机械性能 (3) 1.3.2 设计要求 (4) 1.3.3 直流电动机参数 (4) 第二章四辊可逆冷轧机的介绍 (5) 第三章系统各模块及其电路设计 (6) 3.1 主回路设计 (6) 3.2 控制回路设计 (6) 3.2.1 给定单元 (8) 3.2.2 转速调节器 (8) 3.2.4 反号器 (12) 3.2.5 触发电路 (12) 3.2.6 逻辑控制单元 (13) 3.2.7 零转矩检测单元和零电流检测单元 (14) 3.2.8 零封锁环节 (15) 3.2.9 电流反馈与过流保护 (16) 第四章系统参数设计与计算 (18) 4.1 整流变压器的选择 (18) 4.2 晶闸管的选择 (18) 4.3 晶闸管保护措施 (19) 4.4 电流互感器的选择 (19) 4.5 平波电抗器的计算 (20) 第五章双闭环的动态设计和校验 (22) 5.1 静特性分析和计算 (22) 5.2 系统动态结构参数设计 (22) 5.2.1 电流调节器的设计和校验 (23) 5.2.2 转速调节器的设计和校验 (25) 第六章系统调试和校正 (27) 6.1 系统各功能模块性能的调试与测试 (27) 6.1.1 系统的相位整定 (27) 6.1.2 触发器的整定 (27) 6.1.3 系统的开环运行及特性测试 (28) 6.1.4 速度反馈特性的测试 (29) 6.1.5 调节器的调试 (30) 6.1.6 电流调节器ACR的调试 (30) 6.1.7 反相器AR的调试 (30) 6.2 系统整体功能测试 (30)
负荷平衡控制在1200mm四辊可逆式冷轧机中的应用 文章介紹了负荷平衡控制在1200mm四辊可逆式冷轧机中的应用,避免了上辊和下辊之间由于负荷不平衡出现的电机过载、以至于功率组件损坏的情况,使得上辊和下辊的运行速度得到最佳匹配,对消除钛及钛合金板材在轧制过程中出现的上翘及下扣等不良板形问题取得良好效果。 标签:四辊可逆冷轧机;负荷平衡;直流调速系统;钛及钛合金板材;板形前言 我厂于上世纪六十年代中期引进的日本设备1200mm四辊可逆式冷轧机,已运行了近半个世纪,在生产过程中,经常出现上辊和下辊之间负荷分配不均、造成电机负荷剧烈波动及过载的情况,并且在钛及钛合金板材轧制过程中频频出现上翘和下扣之类的板形问题,制约了产品质量的提高,大大降低了生产效率以及成品率,也影响了该机组潜力的发挥,不能满足产品质量和精度日益提高的市场需求,直接影响了该机组的经济效益。 分析影响钛板上翘和下扣的原因,主要有两点:上下辊的传动系统动态特性和上下辊的辊径。所以,要改善和消除不良板型,大步提高生产效率及成品率,关键要从电气传动系统入手。该轧机传动系统采用的是旋转变流机组,不仅能耗大效率低,而且电气控制系统操作条件比较多,设备维护工作量比较大,系统可靠性也相对较低。运行了近半个世纪,元器件的老化造成系统故障频繁,调速性能变差,精度降低。因此对其电气控制系统进行了技术改造升级。 1 系统构成 该轧机是由两台1500kW直流电动机分别驱动上辊和下辊。在改造方案中,采用了SIEMENS数字式直流调速装置代替旋转变流机组,分别用两套独立的直流调速装置作为其原有的直流电动机的传动控制。为了改善和消除上翘和下扣之类的不良钛板板形,需保证上下辊电机出力平衡,使上下辊的速度得到最佳匹配,因此在两台驱动装置间引入了负荷平衡控制。 2 负荷平衡控制 2.1 负荷平衡的分类 两台电机组成的传动系统中的负荷平衡控制,一般有两种方法实现:一类由一套转速调节器为两套电机控制系统公用,该转速调节器的输出作为两套转矩控制环转矩的共同给定。此类负荷平衡控制系统响应快,动态平衡效果比较好,但是有可能会产生扭振,即两台电机负荷有可能会来回波动,可能会出现电流激磁震荡,甚至严重时引起系统过流跳闸。此种方法适用于两台电机之间通过“刚性”联系的情况,比如两台电机的串轴控制系统。第二类负荷平衡控制是两套电机传
附件1 机组工艺流程、技术参数及装机水平 1.1工艺流程描述 1.1.1 经酸洗处理后的热轧带卷由天车吊放到开卷机操作侧的受卷台上(此受卷台可以同时存放两个带卷)。上卷小车鞍座在受卷台下上升使带卷内孔对准开卷机卷筒中心后,小车继续向前运动将带卷套在开卷机卷筒上并使带卷在宽度方向上与机组中心线对中。开卷机卷筒涨径撑起带卷。上卷小车鞍座下降至下极限后小车退回到受卷台第二个带卷下面等候上第二卷。压辊压住带卷,人工将捆带剪断、拉走。开头机刮板抬起对准带卷头部,同时开卷机活动支承闭合,开卷机以穿带速度转动,使带头沿着刮板进入开头机,上夹送辊、上矫直辊压下夹送、矫直,进入切头剪,切下不合格的带头。如此反复数次,直到将不合格的带材头部全部剪下为止。机组继续以穿带速度将带材向前推进,先后经过导板、机前转向辊、机前张力装置、激光测速仪、测厚仪台架(此时测厚仪处于机组轧线以外)、机前辊式吹扫除油装置、可开合的对中导卫装置,六辊冷轧机、机后辊式吹扫除油装置、测厚仪台架、圆盘剪(此时测厚仪、圆盘剪均处于机组轧线以外)、激光测速仪、机后张力装置、机后转向辊、最后进入机后卷取机(此时卷取机卷筒处于缩径状态)。 1.1.2当带材进入机后卷取机钳口后,机前导卫装置合上,对中带材。机后卷取机卷筒涨径同时钳口动作夹住带头,卷取机压辊压上卷筒,卷取机活动支承闭合,卷筒启动开始卷取带材。卷取带材2~3圈后,AGC液压缸压上,建张,同时卷取机压辊、开头机上夹送辊、上矫直辊抬起,机前、机后激光测速仪、测张装置、测厚仪投入,机前导卫装置打开,工艺润滑乳化液自动从带材入口喷向轧辊,机组升速轧制。轧制到带尾时,机组减速轧制,开卷机压辊压住带卷,当带尾过机前转向辊进入轧辊前机组停止轧制,乳化液自动停喷,打开辊缝,卸张,
太原科技大学 毕业设计(论文)设计(论文)题目:四辊可逆式冷轧机的辊系设计 姓名 学院(系) 专业 _ 年级 _08级 指导教师 2011年 6月10日
太原科技大学毕业设计(论文)任务书 学院(直属系):时间:2011 年 6 月10 日 说明:一式两份,一份装订入学生毕业设计(论文)内,一份交学院(直属系)。
目录 摘要................................................................... II A BSTRACT................................................................... III 第1章绪论. (1) 1.1冷轧机的发展概况 (1) 1.2四辊可逆式冷轧机的发展 (1) 1.3冷轧带钢生产发展与新技术 (2) 1.3.1冷轧带钢生产技术设备的发展 (2) 1.3.2冷轧窄带钢轧机的技术特点 (3) 第2章轧辊 (5) 2.1冷轧轧辊的组成 (5) 2.2轧辊材质的选择 (5) 2.3辊系尺寸的确定 (6) 2.4轧辊力能参数计算 (7) 2.4.1基本参数 (7) 2.4.2艾克隆德方法计算轧制时的平均单位压力 (8) 2.4.3轧辊传动力矩 (11) 2.5轧辊的强度校核 (12) 第3章轧辊轴承 (16) 3.1轴承的选择 (16) 3.2轴承寿命计算 (16) 3.3轧辊轴承润滑 (17) 参考文献 (18) 致谢 (19) 附录1英文原稿 (20) 附录2英文翻译 (24)
四辊可逆式冷轧机的辊系设计 摘要 这篇文章主要讲述了冷轧机生产与发展概述,通过运用已知参数,如钢板的厚度、宽度、轧制速度和压下速度等,对工作辊、支撑辊及相关尺寸进行了计算和校核,然后选择合适的轧辊材质和轴承,并对轴承寿命进行计算和校核。 四辊可逆式冷轧机,衔接连铸后的技术工艺,减少工艺,可实现往返可逆轧制。四辊轧机还能提供较大的轧制压力,提高软件的可轧硬度范围,实现产品规格多样化。 关键词:四辊可逆式;冷连轧;工作辊
前言直流电机在现代工业中是一种很重要的电机.它可以作电动机使用,也可以作发电机使用,此外还有其它特殊的用途。直流电动机具有良好的起、制动性能,宜于在大范围内平滑调速,在许多需要调速或快速正反向的电力拖动领域中得到了广泛的应用。近年来,在电力电子变换器中以晶闸管为主的可控器件已经基本被功率开关器件所取代,因而变换技术也由相位控制转变成脉宽调制(PWM);交流可调拖动系统正逐步取代直流拖动系统。然而,直流拖动控制毕竟在理论上和实践上都比较成熟,而且我国早期的许多工业生产机械都是采用直流拖动控制系统,所以它在工业生产中还占有相当大的比重,短时间内不可能完全被交流拖动系统所取代。从生产机械要求控制的物理量来看,电力拖动自动控制系统有调速系统、位置随动系统(伺服系统)、张力控制系统、多电机同步控制系统等多种类型,各种系统往往都是通过控制转速来实现的,因此调速系统是最基本的电力拖动控制系统。调速系统按照不同的标准又可分为不同的控制系统。但是,从一定角度上来说,可以把调速系统笼统的分为开环调速系统和闭环调速系统。开环调速系统结构简单、容易实现、维护方便,但是它的静态和动态性能往往不能满足生产和控制要求。而闭环控制系统可以很好的解决这些问题,因此在实际生产中得到了广泛的应用。其中,转速、电流双闭环控制直流系统是性能最好、应用最广的直流调速系统。本文为直流调速系统的设计,包括系统设计方案选择,各单元的组成,元件的参数与选择等内容!通过本系统的设计,了解运动控制在工业上的应用!1
目录前言................................................................ 1 第一章设计的介绍.................................................. 4 1.1 设计目的................................................... 4 1.2 设计内容................................................... 4 1.3 设计题目................................................... 4 1.3.1 生产工艺和机械性能................................... 4 1.3.2 设计要求............................................. 5 1.3.3 直流电动机参数....................................... 5 第二章四辊可逆冷轧机的介绍........................................ 6 第三章系统各模块及其电路设计...................................... 7 3.1 主回路设计................................................. 7 3.2 控制回路设计............................................... 7 3.2.1 给定单元 (9) 3.2.2 转速调节器........................................... 9 3.2.4 反号器.............................................. 13 3.2.5 触发电路............................................ 13 3.2.6 逻辑控制单元........................................ 14 3.2.7 零转矩检测单元和零电流检测单元. (15) 3.2.8 零封锁环节.......................................... 16 3.2.9 电流反馈与过流保护.................................. 17 第四章系统参数设计与计算......................................... 19 4.1 整流变压器的选择.......................................... 19 4.2 晶闸管的选择.............................................. 19 4.3 晶闸管保护措施............................................ 20 4.4 电流互感器的选择.......................................... 20 4.5 平波电抗器的计算.......................................... 21 第五章双闭环的动态设计和校验...................................... 23 5.1 静特性分析和计算.......................................... 23 5.2 系统动态结构参数设计...................................... 23 5.2.1 电流调节器的设计和校验.............................. 24 5.2.2 转速调节器的设计和校验.............................. 26 第六章系统调试和校正............................................. 28 6.1 系统各功能模块性能的调试与测试............................. 28 6.1.1 系统的相位整定...................................... 28 6.1.2 触发器的整定........................................ 28 6.1.3 系统的开环运行及特性测试. (29) 6.1.4 速度反馈特性的测试.................................. 30 6.1.5 调节器的调试........................................ 31 6.1.6 电流调节器ACR 的调试.. (31) 6.1.7 反相器AR 的调试..................................... 31 6.2 系统整体功能测试........................................... 31 2
四辊可逆轧机机架辊故障分析及改造参考文本 In The Actual Work Production Management, In Order To Ensure The Smooth Progress Of The Process, And Consider The Relationship Between Each Link, The Specific Requirements Of Each Link To Achieve Risk Control And Planning 某某管理中心 XX年XX月
四辊可逆轧机机架辊故障分析及改造参 考文本 使用指引:此安全管理资料应用在实际工作生产管理中为了保障过程顺利推进,同时考虑各个环节之间的关系,每个环节实现的具体要求而进行的风险控制与规划,并将危害降低到最小,文档经过下载可进行自定义修改,请根据实际需求进行调整与使用。 针对3000mm中板四辊可逆轧机机架辊生产过程中易 出现的各类设备故障:轴承寿命短、传动易失效等具体问 题,结合现场生产条件,经过多次摸索、试制对机架辊结 构进行了改造优化,收到了实际成效,实现了三钢中板轧 机机架辊的使用寿命由4~6个月延长至10~12个月。 轧机机架辊简介 三钢中板四辊轧机机架辊位于轧辊两侧,是将板坯顺 利送入轧机辊缝并接受轧出的轧件的设备,通过斜垫、导 板、楔块卡紧在牌坊予设的凸台及卡槽内。每个辊子的传 动端辊颈内嵌入鼓形齿内齿套,与带鼓形齿的传动轴、电 机相接而传动。
机架辊故障分析 机架辊在轧制过程中,由于处于轧制坯料热幅射、轧辊冷却水及除鳞高压水的冷热工况下,且频繁受到轧件下扣的巨大撞击,导致了轧机机架辊使用寿命普遍较短。现通过结合现场轧制条件及原机架辊设计结构,分析出三钢中板轧机机架辊寿命较短的主要原因,并通过改造优化各零部件结构,以提高机架辊使用寿命。机架辊故障主要因素总结如下: 2.1.机架辊轴承易损坏 原设计机架辊传动侧轴承座是通过轴承座与牌坊之间的O圈挤压变形,通过变形量以防止冷却水及氧化铁皮进入机架辊轴承座。机架辊在生产过程中,O圈易受板坯温度、氧化铁皮及机架辊与牌坊相互振动挤压而变形失效,致轧辊冷却水及氧化铁皮沿轴承座与牌坊配合面,并透过透盖内侧与定距环、内齿套之间的间隙渗入到轴承座内
六辊可逆冷轧机组轧辊常见缺陷分析及改善2
六辊可逆冷轧机组轧辊表面剥落原因分析及改善 摘要:以六辊可逆冷轧机组为研究对象,介绍常见轧辊的缺陷,主要是轧辊的表面剥落缺陷。从轧辊的使用、磨削、检测等方面,提出了相应的预防措施和消除措施. 关键词:轧辊、剥落、措施 THE ANALYSIS AND IMPROVEMENT FOR THE CAUSATION OF ROLLER SURFACE PEELING OFF OF THE SIX-ROLL REVERSING COLD ROLLING MILL Abstract :This thesis takes the Six-roll Reversing cold rolling Mill group as its object of study, it introduces the common defect of the roller, mainly for the defect of peeling off from the suface of the roller. On the other hand, it proposes the provention and elimination methods accordingly from several aspects such as the roller usage, grinding inspection and etc.
key words: roller, peel off, method 前言:轧辊是轧机的重要部件,轧辊的质量好坏直接影响轧机的运行,影响产品的产量质量和成本,冷轧过程中,轧辊表面承受着很大的挤压应力和强烈的磨损,高速轧制时,卡钢、过烧等会出现一些质量问题和质量缺陷,会造成辊面裂纹,因此,冷轧工作辊应具有极高而均匀的硬度,一定深度的硬化层,以及良好的耐磨性与抗裂性。以保证轧辊的使用要求和质量要求。所以分析轧辊缺陷产生的原因以及如何控制轧辊质量显得非常重要,本文将从轧辊的合理使用,合理磨削,改善轧制条件加强检测等方面研究控制轧辊质量,并对轧辊的常见缺陷提出相应的预防和纠正措施。 1、使用情况 广东华美集团有一台1450六辊可逆冷轧机组,2006年5月份安装并试运行,在试生产过程中,由于轧辊使用不当及轧制工艺条件不成熟,造成了轧辊事故率多,消耗高,另一方面因换辊的频繁,降低了轧机有效作业率,影响了小时产量和产品质量。
四辊轧机设计计算书 3.1 冷轧轧辊的组成 冷轧辊是冷轧机的主要部件。轧辊由辊身、辊颈和轴头三部分组成。辊颈安装在轴承中,并通过轴承座和压下装置把轧制力传给机架。轴头和连接轴相连,传递轧制力矩。工作辊和支撑辊的结构如图所示。 工作辊结构 支撑辊结构
3.2、 冷轧辊系尺寸的选择 冷轧过程中,轧辊表面承受很大的挤压应力和强烈的磨损,因此,冷轧工作辊应具有极高而均匀的硬度,一定深度的硬化层,以及良好的耐磨性与抗烈性。降低轧辊硬度,虽然改善抗烈性,但耐磨性降低,因此,必须正确选择轧辊表面硬度。 冷轧辊用钢均多为高碳合金钢,如29r C 、o r M C 29等,我们这里选工作辊的材质为o r M C 29。 轧件对冷轧工作辊巨大的轧制压力,大部分传递给支撑辊上。支撑辊既要能承受很大的弯曲应力,还要具有很大的刚性来限制工作辊的弹性变形,以保证钢板厚度均匀。 轧机支撑辊的表面肖氏硬度一般为HS45左右。目前为提高板厚精度与延长轧辊的寿命,支撑辊硬度有提高的趋势。 支撑辊常用钢号为o r M C 29、V C r 9、及o n r M M C 60,我们这里选支撑辊材质为 o r M C 29。 3.3、 辊系尺寸的确定 1) 辊身长度L 及直径D 的确定。 辊身长度L 应大于所轧钢板的最大宽度m ax b ,即 []2max a b L += (3.1) 当m ax b =400—1200 mm 时,a=50—100 mm ,现m ax b =500mm ,取a=50mm 所以 mm a b L 55050500max =+=+= 四辊轧机的辊身L 确定以后,根据经验数据: 8.18.02 -=D L 来确定支撑辊直径2D ,取 7.12 =D L 所以 mm L D 3207 .12== 对于支撑辊传动的四辊轧机,一般选 4312-=D D ,现取2.31 2=D D
摘要 此次课程设计题目《850mm六辊可逆冷轧机开卷机直流调速系统》,核心落在转速、电流双闭环逻辑无环流调速系统的设计,是基于本学期所学课程《电力拖动自动控制系统—运动控制系统》的一次学以致用的深入拓展。 本文针对直流调速系统进行调速设计。尽管近年来,电力电子变换器中以晶闸管为主的可控器件已经逐步被功率开关器件所替代;伴随着变换技术由相位控制转向脉宽调制(PWM);交流可调拖动系统正逐步取代直流拖动系统,但是直流拖动本身具有理论和实践都很成熟的优势,我国早期的许多生产设备均采用直流拖动系统短时间内不会淘汰,而且直流电机原理相对简单易懂,因而对于初学者而言,直流调速还是很有实际意义的。 从生产机械要求的控制物理量来看,电力拖动自动控制系统分为调速系统、位随系统、张力控制系统、多电机同步控制系统等多种类型;按照调速方式大致可分为开环调速和闭环调速两大类,开环系统结构简单、易于实现、维护简单,但是其静特性与动态特性往往不满足生产和控制要求,而闭环系统尤其是双闭环调速系统具有良好的静特性和动态特性,采用PI调节器时可实现转速无静差以及电流无静差。 本次设计包括各元器件的参数配合与选择、调速方案的设计、整体电路图的绘制等,同时考虑到调速系统实际运用于六卷可逆冷轧机开卷机,各参数与方案都按照实际工程需要设计。 关键字:转速环、电流环、双闭环调速、逻辑无环流、DLC、开卷机、六辊、晶闸管
绪论 薄板、带钢的生产技术是钢铁工业发展水平的一个重要标志。冷轧钢板的生产主要是采用3~6机架的多辊冷轧机,特点是生产率高,机械化、自动化程度高,产品质量好。连轧机仅适用于产量大,品种规格单一的钢种冷轧生产,而对于生产量较小、质量要求较高、品种规格复杂的高合金钢和合金冷轧带材,采用连轧机并不恰当,而大多采用多辊可逆轧机。 带钢冷轧机生产线上除了五机架连轧机主体设备外,还包括头部的上料设备、开卷机以及尾部卷取机,有的在轧制头部还有矫直机、焊接机以及活套等设备。这些设备要要步调一致,密切配合,以保证连轧机位置控制、厚度控制、张力控制、速度控制以及板形控制的顺利进行。五机架冷连轧机的出现必须有自动控制和以计算机技术为基础。 冷轧机最初是在二辊、四辊基础建立起来的,科学技术和工业的发展需要极薄带材,原有低辊数轧机已经不能满足要求,因为轧辊本身的弹性压扁值往往比所需轧制带材厚度还要大,而轧辊的弹性压扁是与辊径成正比的。当轧辊材质一定时,要降低轧辊弹性压扁就必须减小辊径,而辊径的减小又会出现刚性不够的矛盾。为此,多辊轧机出现以提供良好刚性的塔形支撑辊系。多辊轧机发展很快,根据加工工艺要求,有八辊、十二辊、二十辊等。 开卷机作为连轧设备的首端,需要可逆工作,既需要转速控制又需要张力控制。当开卷机工作于换卷引带或断带时,系统外环即速度环调机器投入工作,这是一个速度调节系统;当带材咬入后,产生张力,使ASR的反馈小于给定值,处于饱和状态,其限幅值就是张力给定值,系统作为一个恒功率调剂系统而工作,维持张力恒定。本设计采用转速、电流双闭环逻辑无环流调速。
1200四辊可逆冷轧机压下规程设计及机架设计与分析 学院:机械工程学院 班级:09级轧钢2班 组员:岳猛超付振冲 张刚廉慧 祁福亮 指导教师:许秀梅王健
燕山大学专业综合训练(论文)任务书 院(系):机械工程学院基层教学单位:冶金系
一、 原料及设计技术参数 1.1、原料: 08F 来料尺寸4.2mm ×1050mm 成品尺寸0.6mm ×1050mm Q235 来料尺寸4.2mm ×1050mm 成品尺寸0.6mm ×1050mm Q195 来料尺寸3.5mm ×1050mm 成品尺寸0.65mm ×1050mm 1.2、成品出口速度v=8m/s 。 1.3、开卷机最大张力6吨,卷取机最大张力35吨。 二、 轧辊尺寸的预设定 设计课题为“1200四辊可逆冷轧机压下规程设计及机架设计与分析”,则工作辊的辊身长度 L=1200mm ,辊身长度确定后即可根据经验比例值法确定轧辊直径,冷轧板带轧机 1L / 2.3~3.0D = 常用比值为2.5 ~ 2.9; 2L /0.8~1.8,D = 常用比值为0.9~ 1.4; 21/ 2.3~3.5,D D = 常用比值为2.5 ~ 2.9; 对于支撑辊传动的四辊轧机,一般取 21/3~4,D D = 其中L 为辊身长度,1D 为工作辊直径,2D 为支承辊直径。 取 L/1D =2.5,12/3,D D = L=1200mm , 1D =480mm , 2D =1440mm 三、 压下规程制定
3.1、压下规程制定的原则及要求 压下规程设计的主要任务是确定由一定来料厚度的板坯经过几个道次后轧制成为用户所需求的,满足用户要求的板带产品。在此过程中确定所需采用的轧制方法,轧制道次及每个道次压下量的大小,在操作上就是要确定各道次辊缝的位置和转速。因此,还要涉及到各道次的轧制速度,轧制温度,前后张力及道次压下量的合理分配。在此过程中,主要考虑设备能力和产品质量,设备能力主要包括咬入条件,轧辊强度和电机功率三个要素,而产品质量主要包括几何精度和力学性能。 压下规程制定的原则:在考虑轧件塑性条件并保证产品质量的前提下,充分发挥轧机的设备生产能力,达到优质高产。 对于单机架可逆式冷轧机,第一道次应考虑到来料尺寸误差,预留一定的轧制能力,末道次考虑板型和表面质量,应给与较小的压下量,其余道次可采用等功率原则分配压下量。 3.2、压下规程预设定 ε= 010h h h -=0 h h ? '1 1h H =- ε ?? ? ?? ?- =R h 21arccos α ε:压下率 'ε:累计压下率 H :原料原始厚度 mm 0h :轧前厚度 mm 1h :轧后厚度 mm h ?: 绝对压下量 mm α :咬入角,rad R :轧辊半径,mm
摘要 随着经济社会的飞速发展,建设祖国的大业正处在飞速发展中,东部经济的飞跃发展携带西部建设的不断开发,因此我国要大力加快西部建设,建设离不开钢铁,钢铁是建设的脊梁,所以我们要大力开发钢铁资源,轧钢机广泛用于各个钢铁工厂中。 轧钢机即可逆冷轧机,可逆冷轧机的主传动系统采用直流电动机的晶闸管逻辑无环流可逆调速系统,以满足轧制工艺对轧机传动系统能实现无机调速,有较高的稳态控制精度,较高的抗扰能力,在起制动过程中加减速恒定等要求。 系统的主回路采用两组晶闸管变流器反并联的接线方式,既节省电源,又经济实惠,只需一个交流电源供电,由于无环流,不需要设置环流电抗器。 系统的控制回路采用典型的双闭环,保证生产工艺的要求,保证起制动过程中加减速恒定,通过给定积分器得到转速给定信号。利用调节器锁零电路,在系统处于停车状态,即速度给定电压为零,同时转速也的确为零时,将系统中所有调节器的输出都锁到零位上,避免了停车时各放大器零漂引起的晶闸管变流器有输出电压使电动机爬行。 关键词:直流调速逻辑控制无环流晶闸管稳态控制
Abstract Fly socially to develop soon along with the now economy, the big industry of the developments motherland is being placed in to fly to develop soon, the eastern region leaps economicly the development takes western region our country want to be strongly. Developments quickly and western region, development can not get away from the steel, the is back of developments, so we want to develop strongly steel resources, the extensive application in the machine of rolled steel is in each steel iron works. The machine of rolled steel then the machine of anti cold roll, can the main transmission system of the machine of anti cold roll adopt the thyristor logic non-circulation of the direct current motor can the specd control system to can realize to the stranding machine transmission system the limitless adjusting is soon, having the higher steady state control accuracy, higher anti-roa ability, add and subtract in rose braking process soon the heng settles the ect. Request. The major loop of the system adopts two the method of wiring of set thyristor inverter anti parallels, since save the power supply, again economic real benefit, needs an ACR power supply, because of non-circulation, do not need to place the circulation the battery the anti-machine. The control return adoption of the system typical a closed loops, guarantee the request of the production craft, guarantee to rise to add and subtract in the braking process soon the heng settles, passing to get the definite integral machine the revolving speed give to settle the sign. Make use of the modulator lock zero electric circuit, have the delivery of the modulator to all loke the electric potential of zero in system was placed in park the car condition, as soon as possible degree gave settle tension as zero, at the same time revolving speed too really for zero, system last, avoid the each amplifier in hour in engine room zeropiao cause thyristor inverter contain delivery tension make motor crawled along. Key Words:The direct current adjust soon;Logic control for have no circulation; Silicon transcstor;Stabilize control.