铝合金压铸件一般技术要求
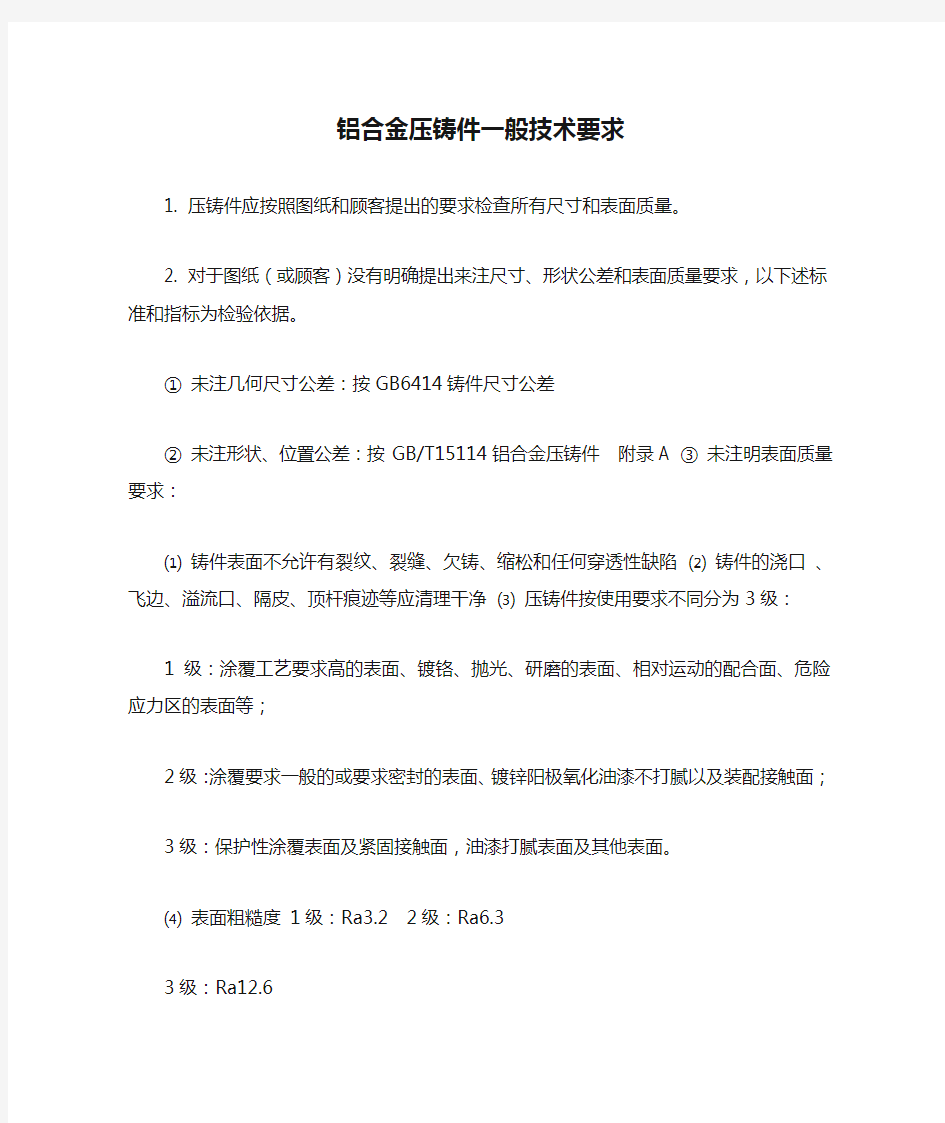

铝合金压铸件一般技术要求
1. 压铸件应按照图纸和顾客提出的要求检查所有尺寸和表面质量。
2. 对于图纸(或顾客)没有明确提出来注尺寸、形状公差和表面质量要求,以下述标准和指标为检验依据。
①未注几何尺寸公差:按GB6414铸件尺寸公差
②未注形状、位置公差:按GB/T15114铝合金压铸件附录A ③未注明表面质量要求:⑴铸件表面不允许有裂纹、裂缝、欠铸、缩松和任何穿透性缺陷⑵铸件的浇口、飞边、溢流口、隔皮、顶杆痕迹等应清理干净⑶压铸件按使用要求不同分为3级:
1级:涂覆工艺要求高的表面、镀铬、抛光、研磨的表面、相对运动的配合面、危险应力区的表面等;
2级:涂覆要求一般的或要求密封的表面、镀锌阳极氧化油漆不打腻以及装配接触面;
3级:保护性涂覆表面及紧固接触面,油漆打腻表面及其他表面。
⑷表面粗糙度1级:Ra3.2 2级:Ra6.3
3级:Ra12.6
⑸表面缺陷极限压铸件表面质量级别
1级2级3级缺陷面积不超过总面积的百分数(%)5 25 40
说明:①在不影响使用和装配的情况下,网状毛刺和痕迹:高度不超
过0.2mm;
②受压铸模镶块或受分型面影响而形成的表面高低不平的偏
铸件质量检查标准
一、目的: 为了确保外协标准铸件、成品铸件质量符合工艺、技术要求,为了满足产品特性,结合相关文件特制定本标准。 二、适用范围: 本办法适用于我公司产品外协、采购、装配过程中、全部铸件质量检查标准。 三、检查标准: 3.1、铸件结构要符合设计要求或加工工艺要求。无特殊要求时按铸件通用标准执行。通用标准等级分为: 交货验收技术条件标准;铸件质量分等通则(合格品、一等品、优等品)材质、检验方法;工艺和材料规格等一般性规则。 3.2、铸件成品检验。铸件成品检验包括:相关技术条件的检验、表面质量检验、几何尺寸检验等项内容。 ①相关技术条件的检验。包括铸件化学成分、机械性能等检验内容。机械性能检验和金相及化学成分检验等技术条件的检验,均必须按相关国家标准执行检验(此处略)。 ②表面质量检验。机械加工生产一线人员在工艺过程中对铸造毛坯的检查主要是对其外观铸造缺陷(如有无沙眼、沙孔、疏松、有无浇不足、铸造裂纹等)的检验;以及毛坯加工余量是否满足加工要求的检验。 表3-1铸件外观质量检验项目(GB6060.1—1985)
表3-2 铸件表面粗糙度(R a 值μm)(GB6414—1986) ③铸件成品几何尺寸检验。主要一种是采用划线法检查毛坯的加工余量是否足够。另一种方法是:用毛坯的参考基准面(也称工艺基准面)作为毛坯的检验基准面的相对测量法(需要测量相对基准面的尺寸及进行简单换算)。 表3-3 铸件尺寸公差数值(mm)(GB6414—1986) 注:铸件基本尺寸≤10mm 时,其公差等级提高3 级;大于10mm 至等于15mm 时,其公差等级提高2级;大于16mm 至25mm 时,其公差等级提高1 级。
铝合金压铸技术要求
1、围 本标准规定了铝合金压铸件的技术要求、试验方法、检验规则、交货条件等。 本标准适用于汽车发电机铝合金端盖压铸件。 2、引用标准 GB6414铸件尺寸公差 GB6987.1-GB6987.16铝及铝合金化学分析方法 GB288-87金属拉力试验法 GB/T13822-92 压铸有色合金试样 GB6060.5 表面粗造度比较样块抛(喷)丸、喷吵加工表面 3、技术要求 3.1 压铸铝合金的牌号 压铸铝合金采用UNS-A03800(美国A380.0,日本ADC10) 可选用材料UNS-A03830 (美国383.0,日本ADC12) 化学成份见表1 表1
供应商可选择上述四种牌号的任何一种,如在生产过程中更换其它牌号, 文档Word 需重新进行样件鉴定。回炉料使用规定 3.1.1回炉料分类 3.1.1.1 一级回炉料:浇道、化学成份合格的废铸件,后加工次品等不含水分和 油污。10二级回炉料:集渣包、坩埚底部剩料、退货废品、存放时间长(超过 天)的一级回炉料。三级回炉料:飞边、溅屑、细小的碎料、带有油污的渣料、因化学成份 报废的铸件、从铝渣中捡出的铝粒。 3.1.1.2回炉料使用比例 使用单一某级回炉料:,二级回炉料最大使用量40%。一级回炉料最大使用量50% 一级、二级回炉料混合使用:20%。,其中二级回炉料最
大使用量回炉料总量不超过40% 三级回炉料:必须经过重熔、精炼且化学成份分析合格后才能使用,其最不能直接使用,10%,仅与铝锭混合使用。大使用量 3.1.1.3加料循序 大块回炉料铝锭,如此循环。小颗粒回炉料 3.2 力学性能 采用单铸拉力试样检验,其力学性能应满足抗拉强度≥240Mpa,伸长率≥ 1%,HB85(5/250/30)。 试样尺寸及形状应符合GB/T 13822-92《压铸有色合金试样》的规定。 3.3 压铸件尺寸 压铸件的几何形状和尺寸应符合铸件图的规定。 3.4 待加工表面用符号“”标明,尖头指向被加工面。 例:0.5 表示该表面留有加工余量0.5mm 3.5 表面质量 3.5.1 铸件清理后的表面质量 铸件的浇口、飞边、溢流口、隔皮等应清理干净,但允许留有清理痕迹。在不影响使用的情况下,因去除浇口、溢流口时所形成的缺肉或高出均不得超过壁厚的四分之一,并且不得超过1.5 mm。 文档Word 3.5.2 铸件不加工表面的质量 3.5.2.1 不允许有裂纹,欠铸和任何穿透性缺陷。 3.5.2.2 由于模具组合镶拼或受分型面影响而形成铸件表面高低不平的
铝合金压铸技术要求
1、范围 本标准规定了铝合金压铸件的技术要求、试验方法、检验规则、交货条件等。本标准适用于汽车发电机铝合金端盖压铸件。 2、引用标准 GB6414铸件尺寸公差 GB6987.1-GB6987.16铝及铝合金化学分析方法 GB288-87金属拉力试验法 GB/T13822-92 压铸有色合金试样 GB6060.5 表面粗造度比较样块抛(喷)丸、喷吵加工表面 3、技术要求 3.1 压铸铝合金的牌号 压铸铝合金采用UNS-A03800(美国A380.0,日本ADC10) 可选用材料UNS-A03830 (美国383.0,日本ADC12) 化学成份见表1 表1
供应商可选择上述四种牌号的任何一种,如在生产过程中更换其它牌号,需重新进行样件鉴定。 3.1.1回炉料使用规定 3.1.1.1回炉料分类 一级回炉料:浇道、化学成份合格的废铸件,后加工次品等不含水分和油污。 二级回炉料:集渣包、坩埚底部剩料、退货废品、存放时间长(超过10天)的一级回炉料。 三级回炉料:飞边、溅屑、细小的碎料、带有油污的渣料、因化学成份报废的铸件、从铝渣中捡出的铝粒。 3.1.1.2回炉料使用比例 使用单一某级回炉料: 一级回炉料最大使用量50%,二级回炉料最大使用量40%。 一级、二级回炉料混合使用: 回炉料总量不超过40%,其中二级回炉料最大使用量20%。 三级回炉料: 不能直接使用,必须经过重熔、精炼且化学成份分析合格后才能使用,其最大使用量10%,仅与铝锭混合使用。 3.1.1.3加料循序 小颗粒回炉料大块回炉料铝锭,如此循环。 3.2 力学性能 采用单铸拉力试样检验,其力学性能应满足抗拉强度≥240Mpa,伸长率≥1%,
机械设计技术要求汇总(
机械设计技术要求大全 技术要求(冲压件)1.锐边去毛刺,冲压切口粗糙度 6.3.2.冲件表面氧化处理:H.Y.或(表面镀锌钝彩.Zn8.DC.).3.未注公差尺寸的极限偏差按GB/T 1804-92 m级. 技术要求(铸件)1.铸件不得有气孔、夹渣、裂纹等缺陷.2.未注明铸造斜度为1~2.5%%d.3.铸造公差按GB6414-86 CT6.4.未注明铸造圆角为R1~R2.5.5.未注公差尺寸的极限偏差按GB/T 1804-92 m级.6.未注形位公差按GB/T1184-96 H 级.7.去毛刺,未注倒角0.5x45%%D. 技术要求(锻件)1.未注锻造圆角半径为R1~R2.2.未注锻造斜度为1~1.5%%D,锻造公差为IT15级.3.锻件组织应致密,不得有折叠、裂纹等缺陷,并去飞边.4.去锐边毛刺,直角处倒钝.5.未注公差尺寸的极限偏差按GB/T 1804-92 m级.6.未注形位公差按GB/T1184-96 H级. 技术要求(活塞件)1.未注公差尺寸的极限偏差按GB/T 1804-92 m级.2.未注形位公差按GB/T1184-96 H级.3.去毛刺,未注倒角0.5x45%%D.4.表面磷化处理. 技术要求(橡胶件)1.零件表面应光洁.(模具表
面粗糙度应在Ra0.4以上)且不允许有气泡.杂技级凸凹等缺陷.2.合模缝不允许错位,合模飞边的凸起级厚度不得大于0.02mm.3.邵氏A 型硬度65%%P5.4.去净飞边. 技术要求(塑料件)1.成形前材料应预热干燥.2.成形后制件应光整不得有扭曲变形现象.3.未注圆角为R0.5.4.外表面应光滑,其粗糙度不大于Ra0.4.且不得有划伤,刻痕等缺陷.5.未注尺寸公差按GB/T 1804-92 m级. 技术要求(弹簧件)1.旋向:左旋.2.总圈数:no=123.工作圈数:no=104.钢丝硬度:HRC42~48.5.表面氧化处理:H.Y.(俗称发黑)6.单端并紧磨平.归纳一下,大约有以下方面的基本技术要求,以供参考(具体数值,具体条款由设计者根据实际情况定):1.一般技术要求:零件去除氧化皮。零件加工表面上,不应有划痕、擦伤等损伤零件表面的缺陷。去除毛刺飞边。.......归纳的很好,我在设计图纸时常用的还有这些,如在第5,如果是整机安装后的技术要求还应该增加:整机的的性能指标,最后的喷漆要求。第6,铸件方面的通常还要有:1、未注铸造圆角,未注拔模斜度,未注壁厚.2、时效处理。对于铸造机座还有有加工后涂防锈底漆技术要求一般包括几个方面1)图纸上的一些通用要求,如未注园角,未注公差等2)零部件制造过程中的一些要求,例如,实验检验要求,探伤要求,封口要求清洁度要求等等。3)部件装配的要求以及主要的装配数据4)图中无法用图形符号表达出来的其它信息。归纳一下,大约有以下方面的基本技术要求,以供参考(具体数值,具体条款由设计者根据实际情况定):1.一般技术要求:零件去除氧化皮。零件加工表面上,不应有划痕、擦伤等损伤零件表
铝合金压铸件的标准
铝合金压铸件的标准 2010-01-25 10:08 铝合金压铸件 GB/T 15114-94 1.主题内容与适用范围 本标准规定了铝合金压铸件的技术要求,质量保证,试验方法及检验规则和交货条件等. 本标准适用于铝合金压铸件. 2.引用标准 GB1182 形状和位置公差代号及其标准 GB2828 逐批检查计数抽样程序及抽样表(适用于连续的检查) GB2829 周期检查计数抽样程序及抽样表(适用于生产过程稳定性的检查) GB6060.1 表面粗糙度比较样块铸造表面 GB6060.4 表面粗糙度比较样块抛光加工表面 GB6060.5 表面粗糙度比较样块抛(喷)丸,喷砂加工表面 GB6414 铸件尺寸公差 GB/T11350 铸件机械加工余量 GB/T15115 压铸铝合金 3.技术要求 3.1化学成分 合金的化学成分应符合GB/T15115的规定. 3.2力学性能 3.2.1当采用压铸试样检验时,其力学性能应符合GB/T15115的规定 3.2.2当采用压铸件本体试验时,其指定部位切取度样的力学性能不得低于单铸试样的75%,若有特殊要求,可由供需双方商定. 3.3压铸件尺寸
3.3.1压铸件的几何形状和尺寸应符合铸件图样的规定 3.3.2压铸件尺寸公差应按GB6414的规定执行,有特殊规定和要求时,须在图样上注明. 3.3.3压铸件有形位公差要求时,其标注方法按GB1182的规定. 3.3.4压铸件的尺寸公差不包括铸造斜度,其不加工表面:包容面以小端为基准,有特殊规定和要求时,须在图样上注明. 3.4压铸件需要机械加工时,其加工余量按GB/T11350的规定执行.若有特殊规定和要求时,其加工作量须在图样上注明. 3.5表面质量 3.5.1铸件表面粗糙度应符合GB6060.1的规定 3.5.2铸件不允许有裂纹,欠铸,疏松,气泡和任何穿透性缺陷. 3.5.3铸件不允许有擦伤,凹陷,缺肉和网状毛刺等腰三角形缺陷,但其缺陷的程度和数量应该与供需双方同意的标准相一致. 3.5.4铸件的浇口,飞边,溢流口,隔皮,顶杆痕迹等腰三角形应清理干净,但允许留有痕迹. 3.5.5若图样无特别规定,有关压铸工艺部分的设置,如顶杆位置,分型线的位置,浇口和溢流口的位置等由生产厂自行规定;否则图样上应注明或由供需双方商定. 3.5.6压铸件需要特殊加工的表面,如抛光,喷丸,镀铬,涂覆,阳极氧化,化学氧化等须在图样上注明或由供需双方商定. 3.6内部质量 3.6.1压铸件若能满足其使用要求,则压铸件本质缺陷不作为报废的依据. 3.6.2对压铸件的气压密封性,液压密封性,热处理,高温涂覆,内部缺陷(气孔,疏孔,冷隔,夹杂)及本标准未列项目有要求时,可由供需双方商定. 3.6.3在不影响压铸件使用的条件下,当征得需方同意,供方可以对压铸件进行浸渗和修补(如焊补,变形校整等)处理. 4质量保证 4.1当供需双方合同或协议中有规定时,供方对合同中规定的所有试验或检验负责.合同或协议中无规定时,经需方同意,供方可以用自已适宜的手段执
铝合金压铸件资料
铝合金压铸件资料 ADC-12(相当国内的ZL104)是压铸铝合金牌号,为脆性材料,易崩裂。性质类似铸铁,但有质轻和导热性好的优点。主要用于做高档望远镜外壳,相机三脚架云台,发动机外壳等。具体性能指标,可由铝合金压铸厂提供,或等我查资料后再告知。在广东省南海市有大量生产厂家。 数码相机的铝合金外壳的壁厚多少合理?表面是如何处理的?有没有加工此类产品的厂家?壁厚:1.2~1.5mm,表面:铬酸皮膜后喷涂; 铝合金压铸件的内部裂痕怎样检测? 通过无损探伤来检测产品 1.超声波探伤 各类金属管材、板材、铸件、锻件和焊缝的超声波检测和超声波测厚. 当超声波在传播中遇到裂缝、空洞、离析等缺陷时,超声波的声速、振幅、频率等声学参数会因此改变。根据仪器测量这些改变,可以判断缺陷的存在,并能确定其具体位置. 超声波脉冲(通常为1.5MHz)从探头射人被检测物体,如果其内部有缺陷,缺陷与材料之间便存在界面,则一部分人射的超声波在缺陷处被反射或折射,则原来单方向传播的超声能量有一部分被反射,通过此界面的能量就相应减少。这时,在反射方向可以接到此缺陷处的反射波;在传播方向接收到的超声能量会小于正常值,这两种情况的出现都能证明缺陷的存在。在探伤中,利用探头接收脉冲信号的性能也可检查出缺陷的位置及大小。前者称为反射法,后者称为穿透法。 2.磁粉探伤 适宜于铁磁性材料如铸造、锻造和其它机加工部件的无损检测。 3.紫外线灯 价格低廉、可靠高和操作简单,各种管道的泄漏探查、涂镀层是否均匀的检验、杂质或污点的检测、半导体和生物领域、医疗、舞台特除艺术效果 4.射线探伤 射线探伤可以分为X射线、γ射线和高能射线探伤三种 X射线照相法探伤是利用射线在物质中的衰减规律和对某些物质产生的光化及荧光作用为基础进行探伤的。从射线强度的角度看,当照射在工件上射线强度为J0,由于工件材料对射线的衰减,穿过工件的射线被减弱至Jc。若工件存在缺陷时,因该点的射线透过的工件实际厚度减少,则穿过的射线强度Ja、Jb比没有缺陷的点的射线强度大一些。从射线对底片的光化作用角度看,射线强的部分对底片的光化作用强烈,即感光量大。感光量较大的底片经暗室处理后变得较黑。因此,工件中的缺陷通过射线在底片上产生黑色的影迹,这就是射线探伤照相法的探伤原理。 铝合金压铸件的结构设计经验 1。考虑壁厚的问题,厚度的差距过大会对填充带来影响 2。考虑脱模问题,这点在压铸实际中非常重要,现实中往往回出现这样的问题,这比注塑脱模讨厌多了,所以拔模斜度的设置和动定模脱模力的计算要注意些,一般拔模斜度为1到3度,通常考虑到脱模的顺利性,外拔模要比内拔模的斜度要小些,外拔模也就1度,而内拔模要2~3度左右 3。设计时考虑到模具设计的问题,如果有多个位置的抽心位,尽量的放两边,最好不要放在下位抽心,这样时间长了下抽心会容易出问题 4。有些压铸件外观可能会有特殊的要求,如喷油、喷粉等,这时就要时结构避开重要外观位置便于设置浇口溢流槽5。在结构上尽量的避免出现导致模具结构复杂的结构出现,如,不得不使用多个抽心或螺旋抽心等 6。对于需进行表面加工的零件,注意,需要在零件设计时给适合的加工留量,不能太多,否则加工人员会骂你的,而且会把里面的气孔都暴露出来的,不能太少,否则粗精定位一加工,得,黑皮还没干掉,你就等再在模具上打火花了,那给多少呢,留量最好不要大于0。8mm,这样加工出来的面基本看不到气孔的,因为有硬质层的保护。 7。再有就是注意选料了,是用ADC12还是A380等,要看具体的要求了 8。铝合金没有弹性,要做扣位只有和塑料配合。 9。一般不能做深孔!在开模具时只做点孔,然后在后加工! 10。如果是薄壁零件与不能太薄,而且一定要用加强肋,增加抗弯能力!由于铝铸件的温度要在800摄氏度左右!模具寿命一般比较短一般做如电机外壳的话只有80K左右就再见了!
铸件技术协议
外协铸件技术质量协议书 (合同编号:) 甲方(需方): 乙方(供方): 甲方委托乙方承担铸件铸造任务。根据甲乙双方的经济合同,经协商,制定本技术质量协议,作为经济合同的补充技术文件。 —、总则 1、乙方必须建立完善的质保体系,并保持有效的运行。 2、在合同履行期间,甲方有权对乙方的质量管理系统进行监督检查、对铸件制造过程进 行随机抽检,乙方应认真配合并满足要求。 二、铸造项目 需方委托供方加工制作JY-TC-S030 “连接座”、JY-TC-S026 “连接座”、JY-TC-S043 “支撑座”、JY-TC-S044 “支撑座”等4项铸件,以及铸件所要使用的模具。铸件生产所使用的模具(其中砂铸件用铝模2付,精铸件共用模具1 付)由供方自行投入,费用由需方一次性承担,所有权归需方。 三、铸造依据 1、依据甲方提供的图纸,数模及技术要求。铸件生产所采用的主见图纸由供方根据需方提供零件图纸绘制,经需方人员确认会签后方可进行模具加工和铸件生产; 2、铸件材料牌号按图纸要求进行制造(ZL101A(GB/T 1173-1995),进行T6处理),生产所需材料由乙方自备,铸件工艺由乙方自定,铸件生产时应保证铸件的化学成分及性能要求; 3、J Y-TC-S043 “支撑座”和JY-TC-S044 “支撑座” 2项铸件采用铝膜砂型铸造方式生产;JY-TC-S030 ”连接座”和JY-TC-S026 ”连接座” 2项铸件采用石膏型精密铸造方式生产。 4、甲方负责向乙方提供图纸一份,及相关数模,乙方按甲方提供的图纸,数模 及相关的技术要求制造; 5、甲方负责图纸及有关问题的解释与协调。 四、铸件质量要求 1、乙方应保证铸件满足使用要求,如果铸件加工后不能满足使用要求,乙方应无偿进行补制. 2、铸件生产所采用材料为ZL101A(GB/T 1173-1995),进行T6处理。
铝合金压铸件综合技术条件(拉力)资料
1 主题内容与适用范围 本标准根据GB 1173及GB 9438的相关内容,规定了铝合金铸件的分类和铸件的外观质量、内在质量以及铸件修补等内容的技术要求与检验规则等。 本标准适用于铝硅系合金铸件的砂型铸造、特种铸造(不含压力铸造)。 2 一般规定 2.1 合金牌号 2.1.1 铸造铝合金牌号由铝及主要合金元素的化学成分符号组成。主要合金元素后面跟有表示其名义百分含量的数字(名义百分含量为该元素的平均百分含量的修约化整值)。如果合金化元素的名义百分含量不小于1,该数字用整数表示;如果合金化元素的名义百分含量小于1,一般不标数字,必要时可用一位小数表示。 在合金牌号前面冠以字母“Z”(“铸”字汉语拼音第一个字母)表示属于铸造合金。 2.1.2 若合金化元素多于两个,除对表示合金的本质特性是必不可少的外,不必把所有的合金化元素都列在牌号中。 2.1.3 杂质含量较一般合金低、性能高的优质合金,在其牌号后面附加字母“A”。 2.1.4 在牌号中主要合金化元素按名义百分含量的递减次序排列,当名义百分含量相等时,按其化学符号字母顺序排列。 2.2 合金代号 本标准中合金代号由字母“Z”、“L”(它们分别是“铸”、“铝”的汉语拼音第一个字母)及其后面的三个阿拉伯数字组成。“ZL”后面第一个数字表示合金系列,其中“1”表示铝硅系列合金,第二、三两个数字表示顺序号。 优质合金,在其代号后面附加字母“A”。 引用顾客提供的材料标准时,其代号按原用代号不变。 2.3 合金铸造方法、变质处理代号 S——砂型铸造 J——金属型铸造 R——熔模铸造 K——壳型铸造 B——变质处理 2.4 合金状态代号 F——铸态 T1——人工时效 T2——退火 T4——固溶处理+自然时效 T5——固溶处理+不完全人工时效 T6——固溶处理+完全人工时效 T7——固溶处理+稳定化处理 T8——固溶处理+软化处理 2.5 数字修约规则 合金牌号中合金化元素的名义百分含量、合金化学成分、合金性能等数字修约按GB 1.1中附录C规定。 3 铸件分类 根据工作条件、用途以及在使用过程中如果损坏,所能造成的危害程度,来确定铸件的类别。 3.1 铸件分三类,其定义及检验项目见表1: 表1 铸件分类的定义及检验项目
铝合金铸件气孔标准修订稿
铝合金铸件气孔标准 WEIHUA system office room 【WEIHUA 16H-WEIHUA WEIHUA8Q8-
铝合金铸件气孔、针孔检验标准 一. 适用范围 本标准规定了铸件气孔、针孔允许存在的范围、大小、数量等技术要求。本标准规定了铸造铝合金低倍针孔度的分级原则和评级方法。本标准适用于铝合金的砂型铸造。适用于评定铸件外表面及需要加工面经加工后的表面气孔、针孔。 二. 引用标准 GB1173-86铸造铝合金技术条件 GB9438-88铝合金铸件技术条件 GB10851-89铸造铝合金针孔 三. 气孔、针孔等孔洞类特征 1. 位于铸件内部而不延伸到铸件外部的气眼。 (1)气孔、针孔内壁光滑,大小不等的圆形孔眼,单个或成组无规则的分布在铸件的各个部位。 (2)气渣孔其特征同气孔、针孔相似,但伴随有渣子。 2. 表面或近表面的孔眼,大部分暴露或与外表面相连。 (1)表面或皮下气孔大小不等的单个或成组的孔眼,位于铸件表面或近表面的部位,其内壁光滑。
(2)表面针孔铸件表面上细小的孔洞,呈现在较大的区域上。 四. 具体条件 1. 砂型、金属型铸件的非加工表面和加工表面,在清整干净后允许存在下列孔洞: (1) 单个孔洞的最大直径不大于3mm,深度不超过壁厚1/3,在安装边上不超过壁厚的1/4,且不大于1.5mm,在上述缺陷的同一截面的反面对称部位不得有类似的缺陷。 (2)成组孔洞最大直径不大于2mm,深度不超过壁厚的1/3,且不大于 1.5mm。 (3) 上述缺陷的数量及边距应符合表一规定 表一 非加工表面或加工表面总面积小于1000cm2 单个孔洞成组孔洞 在 10cm×10cm 单位面积上 孔洞数不多 于4个 孔洞边 距不小 于10mm 一个铸件的非加 工表面或加工面 上孔洞总数不多 于6个,孔洞边 缘距铸件或距内 孔边缘的距离不 小于孔洞最大直 径的2倍 以 3cm×3cm 单位面积 为一组, 其孔洞数 不多于3 个 在一个铸 件上组的 数量不多 于2组 孔洞边缘 距铸件边 缘或距内 孔边缘的 距离不小 于孔洞最 大直径的 2倍 2.液压、气压件的加工表面上,铸件以3级针孔作为验收基础,要求2级针孔占受检面积的25%以上,局部允许4级针孔,但一般不得超过受检面积的
灰球铸铁铸件检验标准-完成版
液压铸铁铸件检验标准 1.围 本标准规定了用灰铸铁和球墨铸铁铸造的液压铸铁件的技术要求和验收规。 本标准适用于液压泵、液压马达、液压缸和液压阀等液压元件的铸造承压壳体或结构件的铸件。 本标准使用于砂型或导热性与砂型相当的铸型中铸造的灰铸铁件,使用其他铸型铸造的灰铸铁件也可以参考使用。 2.术语和定义 GB/T 5611确立的术语以及下列术语和定义适用于本标准。 1)铸件的主要壁厚 relevant wall thickness 铸件的主要壁厚是指用以确定铸件材料力学性能的铸件断面厚度,由供需双方商定。 2)石墨球化处理 graphite spheroidizing treatment 在铁液中加入球化剂,使铁液凝固过程析出的碳形成以球状石墨形态为主的工艺过程。 3.灰球铸铁件 3.1 灰铸铁件 3.1.1 灰铸铁牌号 本标准的材料牌号表示方法,符合GB/T 5612的规定。 本标准中,单铸试棒是以直径Φ30mm的单铸试棒加工的标准试样所测得的最小抗拉强度。附铸试棒(块)是根据铸件的实际壁厚,选择相应的截面尺寸与铸件一同冷却的附铸试棒(块)加工的标准拉伸试样。本体试样为取自铸件本体材料制成的标准拉伸试样。标准拉伸试样的形状和尺寸应按GB/T 9439-2010的规定。本公司常用的HT200、HT250、HT300及HT350灰铸铁件的力学性能及金相组织见表1。 3.1.2 灰铸铁件的化学成分 若需方的技术条件中包含化学成分的验收要求时,按需方规定执行。 若需方对化学成分没有要求时,化学成分由供方自行确定,化学成分不作为铸件的验收依据。但化学成分的选取必须保证铸件材料满足本标准所规定的力学性能和金相组织的要求。 化学成分的检测频次和数量,供需双方商定或由供方自行确定。 3.1.3 灰铸铁的力学性能 在单铸试棒上还是在铸件本体或附铸试棒上测定力学性能,以抗拉强度还是以硬度作为性能验收指标,均必须在订货协议或需方技术要求中明确规定。铸件的力学性能验收指标应在订货协议中明确规定。 本标准规定的力学性能指标和金相组织是铸件验收的主要指标。 3.1.3.1 抗拉强度 1)单铸试棒的抗拉强度 本标准依据直径Φ30mm单铸试棒加工的标准拉伸试样所测得的最小抗拉强度值,本标准规定了本公司常用的HT200、HT250、HT300及HT350四个等级的铸铁件抗拉强度,各等级的最小抗拉强度值应符合表1的规定。 2)附铸试棒(块)的抗拉强度 附铸试棒的抗拉强度值应符合表1的规定。 3)铸件本体试样的抗拉强度
铝合金压铸件质量检验规范
铝合金压铸件质量检验规范 (ISO9001-2015) 1.范围 本标准规定了铝合金压铸件的技术要求、试验方法及检验规则等,主机厂和供应商双方确认的其他发动机及其附件支架可以参照执行此标准。 本标准仅适用于铝合金压铸件以及主机厂和供应商双方确认的其他发动机及其附件支架。2.引用标准 下列标准所包含的条文,通过在本标准中引用而构成本标准的条文。本标准出版时,所示版本均为有效。所有标准都会被修订,使用本标准的各方应探讨使用下列标准最新版本的可能性。 GB/T1182形状和位置公差.通则.定义.符号.和图样表示法 GB2828逐批检查计数抽样程序及抽样表(适用于连续批的检查) GB2829周期检查计数抽样程序及抽样表(适用于生产过程稳定性的检查) GB/T6060.1表面粗糙度比较样块铸造表面 GB/T6060.4表面粗糙度比较样块抛光加工表面 GB/T6060.5表面粗糙度比较样块抛(喷)丸,喷沙加工表面 GB6414铸件尺寸公差 GB/T11350铸件机械加工余量 GB/T15114铝合金压铸件 GB/T15115压铸铝合金 3.技术要求 3.1化学成分 铝合金的化学成分应符合GB/T15115的规定。 3.2力学性能 3.2.1当采用压铸试样检验时,其力学性能应符合GB/T15115的规定。 3.2.2当采用压铸件本体检验时,其指定部位切取试样的力学性能不得低于单铸试样的75%。 3.2.33.3压铸件尺寸 3.3.1压铸件的几何形状和尺寸应符合零件图样的规定。 3.3.2压铸件的尺寸公差应按GB6414的规定执行。 3.3.3压铸件有形位公差要求时,可参照GB/T15114;其标注方法按GB/T1182的规定。 3.3.4压铸件的尺寸公差不包括铸造斜度,其不加工表面:包容面以小端为基准,被包容面以大端为基准;待加工表面:包容面以大端为基准,被包容面以小端为基准。 3.3.5压铸件需要机械加工时,其加工余量按GB/T11350的规定执行。 3.4压铸件质量要求 3.4.1压铸件应符合零件图样的规定。 3.4.2表面质量
1压铸件质量要求
压铸件的分级 1.1铸件表面分级 压铸件表面使用围分为三级,见表1: 表1压铸件表面分级表 华为公司的产品一般为Y2、Y3级要求的表面。 1.2压铸件缺陷特征定义 压铸件常见缺陷特征定义如表2所示: 表2压铸件压铸件常见缺陷特征定义
1.3表面质量 1.压铸件表面粗糙度应符合GB 6060.1-1985的规定。 2.压铸件不允许有裂纹、欠铸等任何穿透性缺陷。 3.压铸件允许有拉伤、凹陷、网状毛刺等缺陷。但其缺陷的程度和数量应符合附录C的要求。 4.铸件的浇口、飞边、溢流口、隔皮、顶杆痕迹等应清理干净、平齐,但允许留有不刮手的痕迹。 5.若图样无特别规定,有关压铸工艺部分的设置,如顶杆位置、分型线的位置、浇口和溢流口的位置等可由生产厂自行规定。 6.压铸件需要特殊加工的表面,如抛光、喷丸、镀铬、涂覆、阳极氧化、化学氧化等以图样上的标注或供需双方商定的容、样件为准。 部质量 对压铸件的气密性、液压密封性、热处理、高温涂覆、部缺陷(气孔、疏松等)及本标准未列项目有要求时,以华为公司图样标注的技术要求为准。 后处理: 由于压铸件的残余应力分布不均匀会使有些零件产生变形,当华为公司有要求时,供应商必须进行相应的后处理(如:校形后时效处理等)以达到华为公司的要求。 1.4压铸件尺寸公差 表3压铸件尺寸公差数值
注:1、对铝合金压铸件选取围: CT5~CT7,一般情况取CT6级; 2、对锌合金压铸件选取围: CT4~CT6,一般情况取CT5级。 1.5平面度公差(形状公差) 压铸件的表面形状公差值(平面度和拔模斜度除外)应在有关尺寸公差值围: 表4平面度公差(mm) 1.6位置公差 表5位置公差平行度、垂直度、端面跳动公差(mm)
铝合金压铸件一般技术要求
铝合金压铸件一般技术要求 1.压铸件应按照图纸和顾客提出的要求检查所有尺寸和表面质量。 2.对于图纸(或顾客)没有明确提出来注尺寸、形状公差和表面质量要求,以 下述标准和指标为检验依据。 ①未注几何尺寸公差:按GB6414铸件尺寸公差 ②未注形状、位置公差:按GB/T15114铝合金压铸件 附录A ③未注明表面质量要求: ⑴铸件表面不允许有裂纹、裂缝、欠铸、缩松和任何穿透性缺陷 ⑵铸件的浇口 、飞边、溢流口、隔皮、顶杆痕迹等应清理干净 ⑶压铸件按使用要求不同分为3级: 1级:涂覆工艺要求高的表面、镀铬、抛光、研磨的表面、相对运动 的配合面、危险应力区的表面等; 2级:涂覆要求一般的或要求密封的表面、镀锌阳极氧化油漆不打腻 以及装配接触面; 3级:保护性涂覆表面及紧固接触面,油漆打腻表面及其他表面。 ⑷表面粗糙度 1级:Ra3.2 2级:Ra6.3 3级:Ra12.6 ⑸表面缺陷极限 压铸件表面质量级别 1级 2级 3级 缺陷面积不超过总面积的百分数(%) 5 25 40 说明:①在不影响使用和装配的情况下,网状毛刺和痕迹:高度不超过0.2mm; ②受压铸模镶块或受分型面影响而形成的表面高低不平的偏
差,不超过相关的公差尺寸; ③推杆痕迹表面凸出或凹入铸件表面的深度,一般为±0.2mm; ⑹表面质量要求(见附表) ⑺挫痕:目视挫痕应均匀、一致,不允许有明显的凹凸。经锉加工的表面 和未经锉加工的表面允许有角度,但角度应在10°以内; ⑻变形:压铸件成型后,如有变形应进行调整,经调整后的压铸件表面不 允许有明显的打击痕迹。调整部分的平面度:0.2mm; ⑼对于顾客的特殊要求,要形成相应的工艺文件,规定其相关的工艺过程 和检验方法。 总工办 2003年4月
铝合金压铸件外观质量标准(2012.5)
编号: 克拉克过滤器(中 国)有限公司 铝合金铸件 外观质量标准(暂行) 共2 页 第1 页 1.适用范围: 本标准适用于为克拉克过滤器(中国)有限公司配套的铝合金铸件(以下简称铸件)的外观检验,包括低压、高压铸造毛坯、成品滤座(完成铸造后机械加工的滤座)。 2.质量要求: 2.1总体要求 2.1.1整体外观:铸件外表面必须经过抛丸处理;颜色为白亮的银灰色,色泽均匀无色斑;各部位表面粗糙度的观感均衡。 2.1.2欠铸、气孔的封堵:铸件允许采用浸渗工艺封堵微孔,但不允许使用堵漏剂对大的孔穴进行人工封堵;特殊品种确需人工封堵时需要对堵漏剂的颜色、可靠性进行充分评价,并经我公司技术部、质量部书面批准。 2.1.3镶嵌件的锈蚀:铸件带有的任何嵌件不允许存在色斑、锈点等缺陷。 2.1.4隔皮、夹渣:铸件不允许存在隔皮、夹渣; 2.2非加工外表面 2.2.1表面修磨:对铸件外表面的任何修磨必须在抛丸前进行,修磨面与相邻表面应良好过渡; 2.2.2浇冒口:浇冒口应予以修磨,修磨后表面高出、凹陷不能超过0.5mm; 2.2.3顶杆痕迹:铸件顶杆痕迹高出、凹陷不能超过0.5mm,其表面形态(弧面或平面)应与所处位置一致; 2.2.4气孔或缩孔:气孔或缩孔的深度不能超过1mm,直径不能超过2mm,每50cm 2范围内存在的缺陷不能超过一处; 2.2.5飞边:铸件分型面飞边高度不能超过0.5mm; 2.2.6边角残缺:铸件因磕碰导致的边角残缺深度不超过0.5mm,宽度不超过2mm,任意100mm 长度范围内缺陷不得超过1处; 2.2.7线状凸起、凸瘤:铸件外表面因任何原因导致的线状凸起高度不允许超过0.3mm、长度不超过5mm;凸瘤高度、直径不能超过0.5mm,每个表面存在的缺陷数不得超过2处;
铝合金压铸技术要求(DOC)
页号:1/8 1、范围 本标准规定了铝合金压铸件的技术要求、试验方法、检验规则、交货条件等。 本标准适用于汽车发电机铝合金端盖压铸件。 2、引用标准 GB6414铸件尺寸公差 GB6987.1-GB6987.16铝及铝合金化学分析方法 GB288-87金属拉力试验法 GB/T13822-92 压铸有色合金试样 GB6060.5 表面粗造度比较样块抛(喷)丸、喷吵加工表面 3、技术要求 3.1 压铸铝合金的牌号 压铸铝合金采用UNS-A03800(美国A380.0,日本ADC10) 可选用材料UNS-A03830 (美国383.0,日本ADC12) 化学成份见表1 表1
页号:2/8 供应商可选择上述四种牌号的任何一种,如在生产过程中更换其它牌号,需重新进行样件鉴定。 3.1.1回炉料使用规定 3.1.1.1回炉料分类 一级回炉料:浇道、化学成份合格的废铸件,后加工次品等不含水分和油污。 二级回炉料:集渣包、坩埚底部剩料、退货废品、存放时间长(超过10天)的一级回炉料。 三级回炉料:飞边、溅屑、细小的碎料、带有油污的渣料、因化学成份报废的铸件、从铝渣中捡出的铝粒。 3.1.1.2回炉料使用比例 使用单一某级回炉料: 一级回炉料最大使用量50%,二级回炉料最大使用量40%。 一级、二级回炉料混合使用: 回炉料总量不超过40%,其中二级回炉料最大使用量20%。 三级回炉料: 不能直接使用,必须经过重熔、精炼且化学成份分析合格后才能使用,其最大使用量10%,仅与铝锭混合使用。
页号:3/8 3.1.1.3加料循序 小颗粒回炉料大块回炉料铝锭,如此循环。 3.2 力学性能 采用单铸拉力试样检验,其力学性能应满足抗拉强度≥240Mpa,伸长率≥1%,HB85(5/250/30)。 试样尺寸及形状应符合GB/T 13822-92《压铸有色合金试样》的规定。 3.3 压铸件尺寸 压铸件的几何形状和尺寸应符合铸件图的规定。 3.4 待加工表面用符号“”标明,尖头指向被加工面。 例:0.5 表示该表面留有加工余量0.5mm 3.5 表面质量 3.5.1 铸件清理后的表面质量 铸件的浇口、飞边、溢流口、隔皮等应清理干净,但允许留有清理痕迹。在不影响使用的情况下,因去除浇口、溢流口时所形成的缺肉或高出均不得超过壁厚的四分之一,并且不得超过1.5 mm。 3.5.2 铸件不加工表面的质量 3.5.2.1 不允许有裂纹,欠铸和任何穿透性缺陷。 3.5.2.2 由于模具组合镶拼或受分型面影响而形成铸件表面高低不平的偏差,不得超过有关尺寸公差。 3.5.2.3 推杆痕迹不得凸起,允许凹入铸件表面,深度不得超过该处壁厚的十分之一,并不超过0.4 mm。
铸件技术要求
1.铸件零件图号:MPE2A300125BD001F。/材料A217 WC6 2.铸件零件图号:MJP2A60025BF001N。/材料A217 WC9 此模具开金属蜡模/或石膏蜡模。 3.铸件需要新开铸造模具; 4.WC6铸造工艺:木模/砂型铸造/贴补浇道浇注工艺系统。 铸造工艺特点:按照JB/T 5263—2005标准规定铸件铸造过程中不得使用内冷铁和泥芯撑。 5. 铸件表面字牌、字体、摆放位置按照图纸技术要求执行。 6.按照设计要求阀体材料执行标准为ASTM A217-WC6.属压力容器部件,服役于高温高 压应用工况环境。适用于温度高达565℃,工作压力300P;法兰和焊接端口阀门应用环境,有一些耐腐蚀和抗石墨化特质。 7.A217-WC6是铸造铬钼钢(高温高压用合金钢铸钢)ASTM A217 等级 WC6 8. WC6铸件材料化学成分:执行标准ASTM A217/A217M-2010; 9. WC6铸造工艺过程中材料化学成分配比容许按照JB/T5263-2005表1规定:
10. 化学成分及机械性能见表2 11. WC6/WC9铸钢铸态正常金相组织为雾状铁素体(有钒的碳化物沉淀)+珠光体。 12. WC6/WC9铸钢经规范热处理(正火+回火)后正常金相显微组织为珠光体。 13. 由于WC6铸钢与我国铸钢牌号ZG15CrMoV基本相近似,容许按照中国牌号 ZG15CrMoV标准要求铸造。 14. 对WC6/ZG15CrMoV铸钢的铸造工艺性偏稍差,铸造时自由线收缩率约为2.2~2.5%。 由于钢的导热系数较低,因此在凝固过程中容易产生热裂倾向,在切除浇冒口过程中又容易产生冷裂,在铸造工艺过程中应引起高度重视。 15. WC6根据铸件形状结构设计要求,铸件壁厚不均匀,铸件最薄处壁厚尺寸应>13mm。 16. WC6铸件须附铸化学成分/力学性能试验试块试棒,试块容许从铸件浇道上采取。试棒 尺寸为Φ40×150;2件,无铸造缺陷。 17. WC6铸造过程中根据材料化学成分要求不容许与其他材料混淆,应单独开炉熔化浇注。 18. 铸件表面不容许有错箱、缺损、裂纹、气孔、疏松等铸造缺陷。 19. 铸件内外形尺寸公差及加工余量按照GB/T6414-CT13级执行。 20. 铸件机加工表面缺陷深度不得超过加工余量的2/3. 21. 铸件非加工表面上的浇口、冒口、补贴工艺拉筋切割后其残余高度应不得高于4mm. 22. 铸件经切割浇冒口、清砂处理、缺陷补焊、尺寸检验、检验无缺陷后再进行热处理。 23. 允许焊补的铸件,壁厚超过38mm的合金钢铸件,必须进行焊前预热,焊后热处理。合 金钢铸件挖补时,应采用机械加工方法,不得使用碳弧气刨。补焊焊口清理后,补焊前必须进行液体浸透检查,补焊后进行无损探伤检验。 24. 铸件补焊:补焊前应对铸件进行磁粉探伤检验或渗透探伤检验,确认对铸造缺陷切除后 25. 铸件缺陷补焊应须征得我方同意。 26. 铸件应以正火+回火状态供货。正火加回火温度应符合以下表-3的要求: WC6 铸件的回火温度应不低于595℃。 WC9铸件的回火温度应不低于675℃; 表-3 不锈钢热处理工艺技术规范。
铝合金壳体铸件检验标准
QJ B3100JQAQ(2010)005 QJ530410 上海汽车变速器有限公司 企业标准 QJ530410-2010 铝合金压铸件检验要求 2010-10-20 发布 2010-10-22 实施 上海汽车变速器有限公司 发 布
QJ530410—2010 前言 本标准是根据GB/T 1.1-2009《标准化工作导则第1部分:标准的结构和编写》的基本规定和格式要求进行编制的。 本标准编制时参考了ZF“铝合金铸件气孔等级检验规范”及F15压铸件质量原则等有关规定。 本标准由上海汽车变速器有限公司提出。 本标准由上海汽车变速器有限公司标准化室归口。 本标准起草单位:上海汽车变速器有限公司产品工程部。 本标准主要起草人:娄勇才、王建新。
铝合金压铸件检验要求 1.范围 本标准规定了铸件机加工后表面气缩孔及局部功能部位内部气缩孔的探测及评价的要求。 本标准适用于上海汽车变速器有限公司(简称本公司)及所有外协配套制造厂(供应商)生产的铝合金铸件。 2.铝合金压铸件气缩孔检验要求 下表中规定了铸件机加工后表面气缩孔及局部功能部位内部气缩孔的探测及评价的要求: 表气缩孔的探测及评价要求 3.铝合金铸件的外观及其他检验要求 3.1 铸件未注角度偏差为±1°; 3.2 铸件的最大错型值为0.5mm; 3.3 铸件未注起模斜度≤2°; 3.4 铸件须经时效处理; 3.5 铸件材料的化学成分及机械性能须符合技术要求; 3.6 铸件的表面硬度(或密度)须符合技术要求; 3.7 铸件表面粗糙度≤Ra12.5; 3.8 铸件非加工表面不允许存有欠铸、冷隔、裂纹等铸造缺陷,机械加工后的表面不允许存有影响使 用的铸造缺陷; 3.9 铸件的浇口、溢流口、飞边等必须清理干净,允许的残痕高度≤1mm; 3.10 铸件非加工表面上允许存在有轻度的网状毛刺,高度为≤0.2mm,由推杆造成的痕迹,其凸出高 度或凹入深度允许为≤0.5mm,毛孔毛刺及隔皮经清理后允许的痕迹≤0.4mm; 3.11 铸件的工艺基准,表面必须光滑平整,满足工装要求;
DAZCZGYQ铝合金压铸件技术条件A
DABG-GY-6 1 不合格,则铸件为不合格件。 4.3.5化学成分应符合表1要求。 表1 5 机械性能 5.1质量保证部负责测试铸件机械性能。 5.2试验仪器使用拉伸试验机。 5.3机械性能测试 5.3.1试验方法按按GB/T 1173《铸造铝合金》执行。 5.3.2每月取三根单铸试样测定合金机械性能,若有两根试样的机械性能符合表2规 定时,则认为合格。 5.3.3第一次试验的三根试样中,若有两根试样的机械性能低于表2规定时,则认为不 合格,但允许用加倍试样数量进行第二次试验。第二次试验若有两根试样的机械性能 不合格,但总平均值合格时,则认为合格;如不合格的试样多于两根,则机械性能不 合格。 5.3.4允许用金属型铸造的标准试样测定合金的机械性能。金属型试样的形状及尺寸 应按GB/T 1173《铸造铝合金》的规定。 5.3.5每次试验后均允许采用压铸件本体试验,其指定部位切取试样的力学性能,不得 低于单铸试样的75%。切取部位未做规定时,由检验部门确定。 5.3.6若单铸试样不合格,铸件上切取的机械性能试样合格时,则该熔批铸件为合格 件。 5.3.7由于试验本身的故障或试样上有目视可见的夹渣、气泡而造成试验结 果不合格时,应补试样重新进行试验。
5.3.8机械性能应符合表2的规定。 6 硬度 6.1检验员负责检测铸件硬度。 6.2试验仪器使用布氏硬度机。 6.3硬度试验方法按GB/T 1173《铸造铝合金》执行。 6.4硬度测试 6.4.1按图纸的规定,对铸件进行硬度检查。 6.4.2铸件上检查硬度的部位,按毛坯图或控制计划中要求执行。 6.4.3按熔批对铸件硬度进行抽查,每熔批抽检不得少于2件。 6.4.4硬度值应符合表2规定。 6.4.5硬度检查不合格时,抽查数量加倍。若再有不合格,铸件为不合格。 7压铸件尺寸 7.1 质量保证部检查压铸件毛坯的尺寸。 7.2使用游标卡尺或其它简单、有效的自制工具。 7.3 使用测量工具对铸件尺寸进行检验。 7.4 压铸件尺寸 7.4.1压铸件尺寸符合图样规定。其它未注尺寸公差按GB/T6414《铸件尺寸公 差与机械加工余量》的CT6级规定。 7.4.2压铸件按控制计划或作业指导书的要求进行定期划线,并填写DABG-GY-106 “铸件尺寸检查报告”。 7.4.3压铸的文字、符号、图案等一般为凸起状,其线条的宽度不小于0.5mm, 凸起高度不大于宽度,拔模斜度为10°~25°。 7.4.4铸件除模具镶拼结合处和分型面外,转角等均为铸造圆角,圆角半径一般为1mm~3mm。