Q345钢板焊接性能分析解读
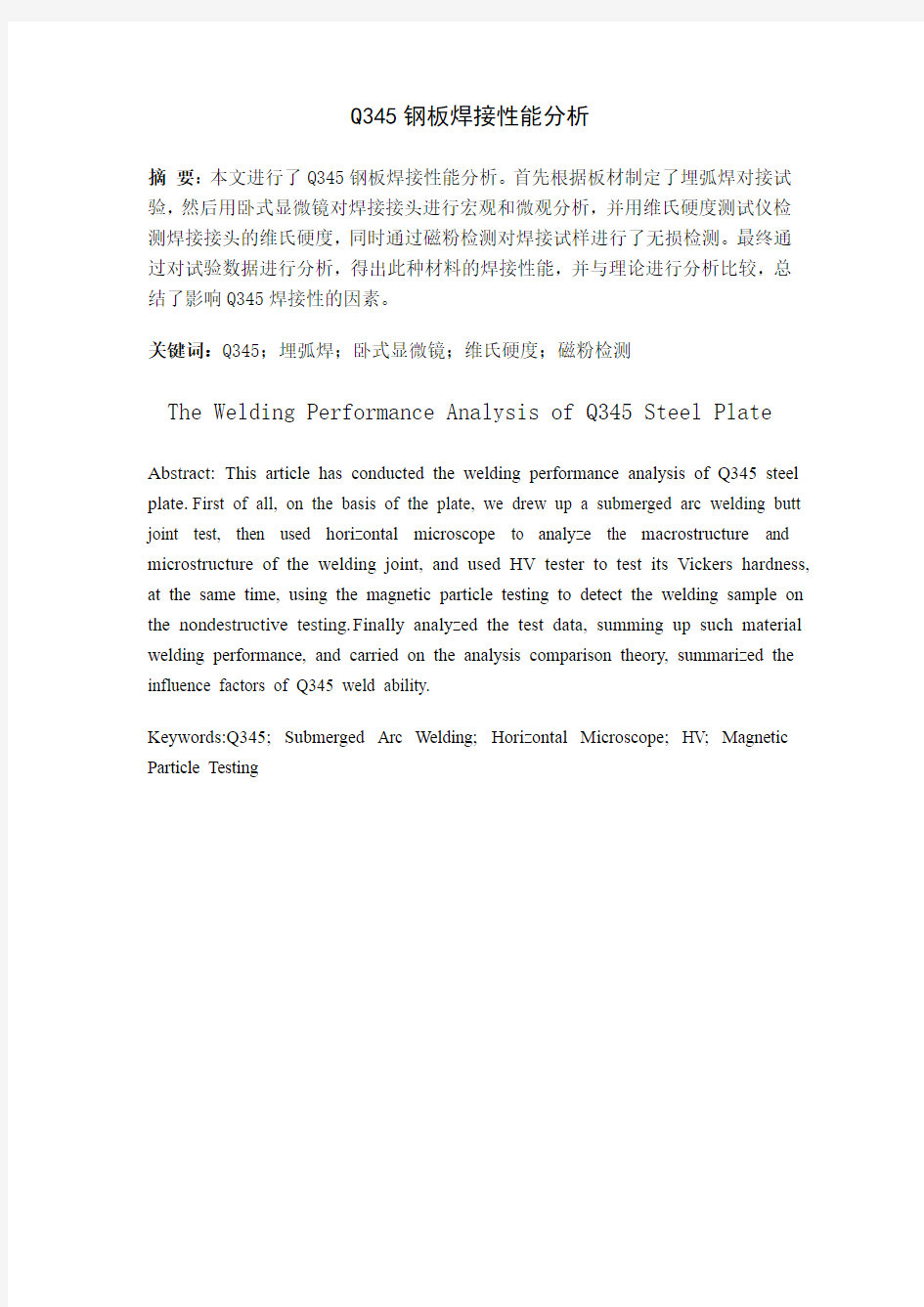

Q345钢板焊接性能分析
摘要:本文进行了Q345钢板焊接性能分析。首先根据板材制定了埋弧焊对接试验,然后用卧式显微镜对焊接接头进行宏观和微观分析,并用维氏硬度测试仪检测焊接接头的维氏硬度,同时通过磁粉检测对焊接试样进行了无损检测。最终通过对试验数据进行分析,得出此种材料的焊接性能,并与理论进行分析比较,总结了影响Q345焊接性的因素。
关键词:Q345;埋弧焊;卧式显微镜;维氏硬度;磁粉检测
The Welding Performance Analysis of Q345 Steel Plate
Abstract:This article has conducted the welding performance analysis of Q345 steel plate.First of all, on the basis of the plate, we drew up a submerged arc welding butt joint test, then used horizontal microscope to analyze the macrostructure and microstructure of the welding joint, and used HV tester to test its Vickers hardness, at the same time, using the magnetic particle testing to detect the welding sample on the nondestructive testing.Finally analyzed the test data, summing up such material welding performance, and carried on the analysis comparison theory, summarized the influence factors of Q345 weld ability.
Keywords:Q345; Submerged Arc Welding; Horizontal Microscope; HV; Magnetic Particle Testing
Q345(16Mn)是应用最广用量最大的低合金高强度结构钢,综合性能好,低温冲击韧性,冷冲压性及切削性能均好,屈服强度≥345MPa,抗拉强度≥490Mpa,适用于多种焊接方法,本次实验选择焊接性能良好的埋弧焊。
本实验所用试样为Q345(250×40×10)
1、埋弧焊工艺
1.1 埋弧焊方法简介
埋弧焊是指电弧在焊剂层下燃烧进行焊接的方法,为电弧焊的一种。埋弧焊的特点是在电弧热的作用下,焊丝、焊剂和焊件被熔化形成的一层由熔渣和气体组成的保护膜,对焊接区起到隔离空气、绝热和屏蔽光辐射的作用。这种焊接方法,生产率高,焊缝质量好,无弧光辐射和火花飞溅,在室内和室外都可焊接各种钢结构。适用于焊接低碳钢、低合金钢及不锈钢等金属。
1.1.1焊接设备
图1—1 埋弧焊设备
如图1—1所示,埋弧焊设备包括埋弧焊机和各种辅助设备。其中,埋弧焊机是核心部分,由机械系统、焊接电源和控制系统三部分组成。辅助设备是为了使焊缝处于最佳施焊位置,或为了达到某些工艺目的所配置的工艺装置,包括使焊件准确定位和夹紧的焊接夹具,使焊件旋转、倾斜、翻转的焊件变位机,使焊接机头准确送到待焊位置的焊机变位机,以及能自动回收焊剂的焊剂回收器等。
1.2 焊接过程
1.2.1 焊前准备
(1)坡口的选择
由于埋弧焊使用的电流比较大,熔透深度比较大,因此当焊件厚度小于14mm时可以不开坡口,这样仍能保证良好的焊缝成形。试验所用焊件厚度为10mm,因此,不开坡口。
(2)焊件的清理
焊接前,用砂纸打磨焊件待焊部位及其周边部位,以清除其表面的锈蚀、油污、水分、氧化皮等。
(3)焊丝的清理和焊剂的烘干
焊接前,将焊丝表面清理干净。同时,将试验所用焊剂HJ431按250℃、2h烘干。
(4)焊件的装配
焊件装配时,必须保证间隙均匀,高低平整。定位焊的位置应在第一道焊缝的背面,长度一般应大于30mm。此次定位焊选用CO2气体保护焊,在焊件的对接部位两端焊接1cm左右长的焊缝,防止埋弧焊过程中焊件的开裂。
1.2.2焊接工艺参数的选择
本实验所用试样为Q345(250×40×10),不开坡口,对接接头双面焊,选用焊丝H10Mn2(Φ1.2)、焊剂HJ431。根据试样厚度及焊丝直径查《熔焊方法与设备》一书中表5-13选择埋弧焊工艺参数如下表1—1所示:
表1—1 不开坡口对接接头双面焊的焊接参数
1.2.3焊接操作过程
本实验所用的埋弧焊机型号为MZ-1000(A310-1000)。具体操作步骤如下:
1、在焊料斗内装上HJ431焊剂;
2、在焊机上安装H10Mn2焊丝;
3、将表面清理过并进行定位焊(CO2气保焊)后的焊件在工作台上放置好;
4、合上电源,打开焊机开关,让焊接小车预行走,对正焊缝;
5、按表5设置10mm的Q345对接接头正面焊接参数;
6、将焊料斗上的闸门打开;
7、按下启动按钮,埋弧焊机自动进行引弧和焊接;
8、正面焊接完成后,待焊件稍微冷却后清除焊缝上渣皮,翻转焊件;
9、设定反面焊接参数,继续进行另一面的焊接;
10、反面焊接完成后,按下停止按钮。
2.金相试样的制备
2.1金相显微镜
金相显微分析是研究金属和合金组织的主要方法之一,为了探索金属材料的
性能,经常需要进行金相组织的检查和分析。金相显微分析是利用显微镜的光学理论借助于试样表面对光线的放射特点来进行的。为了对金相显微组织进行鉴别和研究,需要将所分析的金属材料制备成一定尺寸的试样,并经研磨、抛光与腐蚀等工序,最后通过金相显微镜来观察和分析金相的显微组织状态及分布情况。显微组织包括相的组成、数量、形态、大小、分布。显微缺陷则包括各种非金属夹杂物、裂纹(性质、大小、形态、走向及其与显微组织的关系等)、显微孔洞(大小、分布)、珠光体球化程度和石墨化程度、脱碳、过烧、过热……。光学金相显微分析广泛用于火电厂,已成为电厂金属监督中不可缺少的一种重要分析方法。
2.1.1金相显微镜放大原理
放大镜是最简单的一种光学仪器,它实际上是一块会聚透镜(凸透镜),利用它就可以将物体放大。但金相显微镜不象放大镜那样由单个透镜组成,而是由两组透镜组成。
金相显微镜是依靠光学系统实现放大作用的,其基本原理如图2—1所示。光学系统主要包括物镜、目镜及一些辅助光学零件。对着被观察物体A B的一组透镜叫物镜O1;对着眼睛的一组透镜叫目镜O2。现代显微镜的物镜和目镜都是由复杂的透镜系统所组成。
图2—1 金相显微镜光路图
光学显微镜的放大倍数可达到1600~2000倍。当被观察物体AB置于物镜前焦点略远处时,物体的反射光线穿过物镜经折射后,得到一个放大的倒立实像A1B1(称为中间象)。若A1B1处于目镜焦距之内,则通过目镜观察到的物象是经
目镜再次放大了的虚象A1’B1’。由于正常人眼观察物体时最适宜的距离是250mm(称为明视距离),因此在显微镜设计上,应让虚象A1’B1’正好落在距人眼250mm处,以使观察到的物体影像最清晰。
金相显微镜总的放大倍数应为物镜与目镜放大倍数的乘积,即M总=M物ХM目。在使用显微镜观察试样时,应根据其组织的粗细情况,选择适当的放大倍数。以细节部分观察得清晰为准。显微镜的鉴别能力(鉴别率)是显微镜也是物镜最重要的特性,它是指显微镜对于试样上最细微部分所能获得清晰映象的能力。物镜的数值孔径,表示物镜的聚光能力。物镜的数值孔径越大,表明物镜的鉴别能力也就是显微镜的鉴别能力越高。
2.1.2 金相显微镜的操作步骤
金相显微镜是一种精密光学仪器,在使用时要求细心和谨慎,严格按照使用规程进行操作。
①将显微镜的光源插头接在低压(6V~8V)变压器上,接通电源。
②根据放大倍数,选用所需的物镜和目镜,分别安装在物镜座上和目镜筒内,旋动物镜转换器,使物镜进入光路并定位(可感觉到定位器定位)。
③将试样放在样品台上中心,使观察面朝下并用弹簧片压住。
④转动粗调手轮先使镜筒上升,同时用眼观察,使物镜尽可能接近试样表面(但不得与之相碰),然后反向转动粗调手轮,使镜筒渐渐下降以调节焦距,当视场亮度增强时,再改用微调手轮调节,直到物象最清晰为止。
⑤适当调节孔径光栏和视场光栏,以获得最佳质量的物象。
⑥如果使用油浸系物镜,可在物镜的前透镜上滴一些松柏油,也可以将松柏油直接滴在试样上,油镜头用后,应立即用棉花沾取二甲苯溶液擦净,再用擦镜纸擦干。
2.1.3卧式显微镜
本实验所用设备为卧式金相显微镜。大型卧式显微镜主要由电源箱、照明光源、显微镜主体、垂直照明器、投影与摄影装置等部分组成,如图2—2所示。这种显微镜采用双筒目镜,使观察更为方便。光源方面增加了氙灯,这是一种较
新颖的光源,提高了光源强度,有利于高倍、偏光、暗场的观察并提高显微镜摄影的质量。
图2—2 卧式显微镜
该设备直接与计算机相连接,可以直观的在计算机上显示金属试样的微观组织,并且可以拍摄所需组织的金相照片,操作方便简洁。
2.2金相试样的制备
金相试样制备的质量好坏,直接影响到组织观察的结果。如果样品制备不符合特定要求,就有可能由于出现假象而产生错误的判断,致使整个分析得不到正确的结论。因此,为了得到合乎要求的理想金相显微组织试样,需要经过一系列的制备过程。
2.2.1 试样制备过程:
(1)截取所需试样的表面
选择合适的、有代表性的试样是进行金相显微分析及其重要的一步。金相试样的选择要考虑取样部位、取样方法和试样尺寸三部分。
a.取样部位
●取样部位及检测面的选择取决于被分析材料或零件的特点、加工工艺过
程及热处理过程,应选择有代表性的部位;
●生产中常规检验所用试样的取样部位、形状、尺寸都有明确的规定;
●检验和分析失效的原因时,应根据失效的原因,除了在材料失效的部位
取样外,还需要在距离破坏处较远的部位取样,以便于对比分析;
●对于一般经热处理后的零件,由于金相组织比较均匀,试样截取可在任
一截面进行。
b.试样的截取方法
●取样时,应该保证不使被观察的截面由于截取而产生组织变化,因此对
不同的材料要采用不同的截取方法;
●对于软材料,可以用锯、车、刨等加工方法;
●对于硬材料,可以用砂轮切片机切割或电火花切割、线切割等方法;
●对于硬而脆的材料,如白口铸铁,可以用锤击方法;
●在大工件上取样,可用氧气切割等方法;
●在用砂轮机切割或电火花切割时,应采取冷却措施,以减少由于受热而
引起的试样组织变化。试样上由于截取而引起的变形层或烧损层必须在后续工序中去掉。
c.试样尺寸
●金相试样的大小以便于握持、易于磨制为准。通常显微试样为直径16~
25mm、高16~20mm的圆柱体或边长为25mm的立方体;
●对于形状特殊或尺寸细小不易握持的试样,要进行镶嵌或机械夹持。
注意事项:
●试样取下后一般先用砂轮磨平,对于很软的材料(如铝、铜等有色金属)
可用锉刀搓平;
●在一般情况下,试样的周界要用砂纸或锉刀磨成圆角,以免在磨光及抛
光时将砂纸或抛光织物划破;
●对于需要观察表层组织(如渗碳层、脱碳曾)的试样,则不能将边缘磨
圆,这种试样最好进行镶嵌。
(2)试样表面的磨光与抛光
金相试样截取好之后,就要对要观察表面进行磨光与抛光:
基本步骤:
①将要观察试样的截面在砂轮机进行粗磨,直到表面比较平整光滑为止。在
打磨过程中,要经常用冷水将试样冷却,防止过热使金相试样组织发生变化;
②选用金相砂纸进行精磨。金相砂纸是磨光金相试样的重要材料,一般采用
的磨料为碳化硅和氧化铝。手工磨光试样时,砂纸应放在玻璃板上,依次用280号、500号、水砂纸、01、03、05、06号金相砂纸磨光,在磨制过程中,每换一号砂纸,试样磨制方向旋转90
后才能换下一号砂纸;
③在抛光机上对试样表面进行抛光,抛光的目的是在于去除金相磨面由细磨
所留下的细微磨痕及表面变形层,使磨面成为无划痕的光滑镜面。
注意事项:
●横截面:试样从中心到边缘组织分布的渐变情况,像表面渗层、硬化层、
镀层等表面处理的深度及其组织,表面缺陷以及非金属夹杂物在横截面
上的分布情况;
●纵截面:非金属夹杂物在纵截面上的分布情况、大小、数量及形状,金
属的变形程度,如有无带状组织的存在;
●选择互相垂直的磨面,研究立体形貌;
●严禁在磨片机旋转时更换砂纸、砂布;
●试片打磨,抛光时应拿紧,并力求与磨面接触平稳;
●抛光操作时,对试样所施加的压力要均衡,且应先重后轻。在抛光初期,
试样上的磨痕方向应与抛光盘转动的方向垂直,以利较快的抛除磨痕。
在抛光后期,需将试样缓缓转动,这样有利于获得光亮平整的磨面,同
时能防止夹杂物及硬性的相产生曳尾现象。
(3)试样表面侵蚀
本实验选用化学侵蚀法,此法是利用化学试剂的溶液,借助于化学或电化学作用显示金属的组织。
将试样磨面朝上平放在工作台上,以蘸有酒精的棉花在磨面上轻轻揩擦,用吹风机吹干。然后用蘸有硝酸酒精的棉花在磨面上轻轻擦拭,持续时间2~3s后,立即用酒精将表面擦拭干净,再用吹风机吹干。
2.2.2金相试样显微组织的观察与拍摄步骤
①仪器的开机:接通总电源,然后向上扳动仪器上的总电源开关,指示灯亮,向上扳动白炽灯开关,指示灯亮,开启相连的电脑。
②装上目镜、物镜等(根据要求选择合适倍数的物镜、目镜)。
③打开电脑桌面快捷方式进入软件,显示图像。
④把试样放在载物台上(试样要经过预磨、抛光、腐蚀)。
⑤调整粗、微调旋钮进行调焦,观察电脑屏幕显示的图像,直至观察到清晰的图像为止。
⑥调整载物台位置,找到关心的视场,调整图像的亮度、对比度,进行金相分析。
⑦对图像进行采集和保存(叠加标尺)。
⑧全部完成后,取下物镜、目镜并收藏好。
⑨仪器的关机:向下扳动白炽灯开关,指示灯灭。向下扳动仪器上的总电源开关,指示灯灭。电脑关机,切断总电源。
3.焊接接头宏观及微观组织分析
3.1焊接接头的宏观组织
宏观分析主要内容为:观察与分析焊缝成形、焊缝金属结晶方向和宏观缺陷等。图3—1所示为焊接接头的宏观组织,可分为三部分:①中心区为焊缝:②靠近焊缝的是热影响区;③两边未受影响的是母材区。
图3—1 焊接接头宏观组织
3.2显微组织的观察
显微分析的主要内容为:借助于放大100倍以上的光学金相显微镜进行观察,分析焊缝的结晶形态、焊接热影响区金属的组织变化和焊接接头的微观缺陷等。
钢材焊接后,焊接接头主要由焊缝和热影响区组成。其中,焊缝由经过熔化的金属部分组成,热影响区是焊缝两侧发生组织和性能变化的区域。焊缝的组织取决于焊接时达到的最高温度和随后的冷却速度。由于从熔化区到母材区的变化是连续发生的,所以热影响区也没有非常明显的分界线。
下列各图为试验中所拍摄的显微金相组织:
图a)为焊缝与母材的过渡区显微组织。中间
有一条很明显的分界线(熔合线),在熔合线的左
上半部分为等轴晶区,该区为焊缝组织;熔合线右
下部分成带状的组织为母材组织。
图a)
图b )为焊缝金属的显微组织,柱状晶分布,
晶界处为铁素体,晶内为索氏体和铁素体。
冷却时,由于向外散热,故使焊缝的熔融金
属沿热扩散方向结晶而获得柱状晶,此时,
先共析的铁素体沿柱状晶界析出,由于温度
较高,且冷速又稍快,因此组织呈过热特征,
但随后的冷却过程中,奥氏体因过冷度较大,
而转变为索氏体组织。焊缝晶粒较细,从金
像照片看,存在大量树枝晶,焊缝结晶形态
由合金浓度、结晶速度、温度梯度、过冷度 决定,焊缝结晶为非自发形核,即开始结晶是以熔合线处半熔化状态的母材晶粒为晶核,在焊缝边缘,合金浓度较小,温度梯度大,结晶速度较快,形核后的晶粒以枝晶形式向焊缝中心生长,越到焊缝中心,温度梯度逐渐变小,合金浓度逐渐升高,过冷度逐渐下降,结晶速度逐渐减慢,到焊缝中心时可能出现平面晶,因此,从熔合线至焊缝中心,结晶形态为柱状晶→柱状晶、平面晶共存→平面晶,大多数情况下,焊缝中心不存在平面晶,即焊缝结晶形态为柱状晶→柱状晶、平面晶共存。
图c )为母材的显微结构组织,铁素体
和珠光体呈带状如图c )。从金相组织可看出,
过热区形成了魏氏组织,容易产生脆化,构
成了接头的薄弱环节,这时宜以小线能量焊
接,在过热区获取板条马氏体,韧性会大大
改善。
图c )
3.3维氏硬度的测量
3.3.1 维氏硬度测量原理
采用正四棱锥体金刚石压头,在试验力作用下压入试样表面,保持规定时间后,卸除试验力,测量试样表面压痕对角线长度。
试验力除以压痕表面积的商就是维氏硬度值。维氏硬度值按下式计算:HV = 常数×试验力/压痕表面积≈0.1891 F/d2
式中:HV—维氏硬度符号;
F―试验力,N;
d—压痕两对角线d1、d2的算术平均值,mm
实用中是根据对角线长度d通过查表得到维氏硬度值。
国家标准规定维氏硬度压痕对角线长度范围为0.020~1.400mm
3.3.2 维氏硬度计测量的具体过程
①开启电脑和维氏硬度计,打开维氏硬度测量软件。
②转动变荷手轮,选择合适的试验力(本实验中设置为4.903N)。在硬度计下方按键上选择合适的加载时间(本实验中设置为10s)。
③在菜单里设置好相关数据及试样材料。
④转动转盘,使40X物镜处于前方位置(此时光路系统总放大倍率为400х)。
⑤将试样放在十字试台上,转动升降手轮使试台上升,观察电脑屏幕,当试件离物镜下端1mm左右时,屏幕视场内出现明亮光斑,此时应缓慢上升试台,直至屏幕中观察到试样表面清晰成像。
⑥将压头转至前方位置,转动时应小心缓慢地进行,防止过快产生冲击。
⑦按“启动”键,此时加试验力,键盘上显示“10、9、8、……0秒倒计时,当加载时间重新跳回设定值时,表示加卸试验力结束。
⑧将40х物镜转到前方,在屏幕中可看到压痕,稍微转动升降手轮将其调到最清楚。
⑨点击电脑屏幕右侧的“图像态”,此时图像中会出现两条红色的竖线,点击鼠
标左键将其中一根竖线拖至与菱形横向压痕角相切的位置后,再点击右键将另一根竖线拖至与相对角相切的位置,此时出现确定第一条对角线测量的对话框。确定后出现出现两条红色的横线,点击鼠标左键将其中一条横线拖至与菱形竖向压痕角相切的位置,再点击鼠标右键将另一根横线拖至与对角相切的位置。此时出现维氏硬度测量结果。确认测量结果。并按照以上步骤进行其他点的测量。
⑩所有硬度点测量结束后,生成测试报告。
3.3.3 实验结果与分析
采用正四棱锥体金刚石压头,在试验力作用下压入试样表面,保持规定时间后,卸除试验力,测量试样表面压痕对角线长度。如下图所示。
图3—2 维氏硬度测量图示
实验找到六个不同点,每点之间距离约为1mm左右,测得其硬度值,其中三个点的分布如图3—2右图所示,得到不同硬度数据,经过绘图如下图3—3所示:
图3—3 实验测得维氏硬度分布图
分析:从硬度值的测量结果可以看到热影响区的硬度值是比较大的,并且硬度值不均匀,而焊缝硬度平均值要低于母材。这在一定程度上可以说明焊缝的韧性要比母材好。
过热粗晶区的韧性要比焊缝和母材都低,这就是由于该区存在粗大的魏氏组织导致。之后的相变重结晶区,因为相当于正火,获得的组织是细致均匀的,拥有较好的力学性能,韧性和强度都较高。不完全重结晶区由于存在粗大的F,组织不均匀,所以韧性较低,并且硬度值也有起伏。
4.焊件的无损检测
无损检测技术是第二次世界大战后迅速发展起来的一门新的综合性工程科学,它已经广泛地应用于众多的科技领域特别是工业领域。无损检测技术主要是根据物质的各种物理特性变化,在不损伤被检物使用性能与形状的条件下可以实现百分之百检查,从而判断被检物的质量状况。为了保障在役设备的安全运行,无损检测技术可以充分发挥其非破坏性及可靠性并且在许多情况下更可以实施原位检测(即不需拆卸解体)的特长。因此,无损检测技术的应用已经在工业生产、
物理研究和生物工程等广大科技领域获得极大的重视和迅猛发展,已经成为控制
产品质量、保证设备安全运行等方面的极为重要的技术手段。
尽管无损检测技术本身并非是一种生产技术,但其技术水平却能反映该部门、该行业、该地区甚至该国的工业技术水平。然而,在一般设备或者普通民用设备的诊断维护工程中目视检测等常规无损检测都尚未受到足够的重视和广泛应用。
4.1 目视检测(Visual Testing)
4.1.1 目视检测基本方法
目视检查在无损检测中占有重要地位,许多重要故障都是在目视发现问题后再用仪器检查的,随着CCD技术的发展,用以辅助目视检测的仪器也发展很快,可以列入此类的有视频显微镜系统、视频内窥镜、视频孔探仪等。目视检测,是国内实施的比较少,但在国际上非常重视的无损检测第一阶段首要方法。按照国际惯例,目视检测要先做,以确认不会影响后面的检验。按照国际惯例,目视检测要先做,以确认不会影响后面的检验,再接着做四大常规检验。经过国际级的培训,其VT检测技术会比较专业,而且很受国际机构的重视。
VT常常用于目视检查焊缝,焊缝本身有工艺评定标准,都是可以通过目测和直接测量尺寸来做初步检验,发现咬边等不合格的外观缺陷,就要先打磨或者修整,之后才做其他深入的仪器检测。例如焊接件表面和铸件表面较多VT做的比较多,而锻件就很少,并且其检查标准是基本相符的。
4.1.2 表面目视检验的条件
●直接目视检验时,眼睛与被检表面的距离不得大于610mm,视线与被检表面
所成的视角不小于30°。
●被检表面应有足够的照明,一般检验时光照度不得低于1601x;对细小缺陷
进行鉴别时,光照度不得低于5401x。
●可以使用2~5倍的放大镜,对细小缺陷进行鉴别。
4.1.3 检验工具
①检验用的焊接检验尺、量具和仪器必须经计量检定部门的检验合格。
②几何外形尺寸测量用的样板应符合有关工程技术标准的规定。
4.1.4 目视结果与分析
焊后焊材的一部分如图4—1所示,可以明显地看到母材表面有飞溅和凹坑。
图4—1 目视检测照片
分析:上述的凹坑可能是在取样过程中,被其他工件碰坏的,不是焊接造成的。飞溅造成的原因是,焊接过程中焊接电流过大,造成熔滴飞溅。
4.2 磁粉检测(Magnetic Particle Testing )
4.2.1 磁粉检测基本原理
铁磁性材料工件被磁化后,由于不连续性的存在,使工件表面和近表面的磁力线发生局部畸变 而产生漏磁场,吸附施加在工件表面的磁粉,在合适的光照下形成目视可见的磁痕,从而显示出不连续性的位置、大小、形状和严重程度。
4.2.2 磁粉检测适用范围
1. 适用于检测铁磁性材料表面和近表面缺陷,例如:表面和近表面间隙极窄
的裂纹和目视难以看出的其他缺陷。 不适合检测埋藏较深的内部缺陷。
2. 适用于检测铁镍基铁磁性材料,例如:马氏体不锈钢和沉淀硬化不锈钢材
料,不适用于检测非磁性材料,例如:奥氏体不锈钢材料。
3. 适用于检测未加工的原材料(如钢坯)和加工的半成品、成品件及在役与
使用过的工件。
4.适用于检测管材棒材板材形材和锻钢件铸钢件及焊接件。
5.适用于检测工件表面和近表面的延伸方向与磁力线方向尽量垂直的缺陷,
但不适用于检测延伸方向与磁力线方向夹角小于20度的缺陷。
6.适用于检测工件表面和近表面较小的缺陷,不适合检测浅而宽的缺陷。
4.2.3 磁粉检测步骤
第一步:预清洗
所有材料和试件的表面应无油脂及其他可能影响磁粉正常分布、影响磁粉堆积物的密集度、特性以及清晰度的杂质。
第二步:缺陷的探伤
磁粉探伤应以确保满意的测出任何方面的有害缺陷为准。使磁力线在切实可行的范围内横穿过可能存在于试件内的任何缺陷。
第三步:探伤方法的选择
检测近表面缺陷时,应采用湿粉连续法,因为非金属夹杂物引起的漏磁通值最小,检测大型铸件或焊接件中近表面缺陷时,可采用干粉连续法。
为了检测工件近表面的缺陷,实验采用湿粉检测法。其具体步骤为:采用软管浇淋或浸渍法将磁悬液施加于试件,使整个被检表面完全被覆盖,使用磁粉探伤机将工件磁化,磁化电流应保持1/5~1/2秒,此后切断磁化电流,使试样倾斜去掉表面多余的磁悬液,然后观察磁粉聚集情况,从而判断工件缺陷。
第四步:退磁
将零件放于直流电磁场中,不断改变电流方向并逐渐将电流降至零值。大型零件可使用移动式电磁铁或电磁线圈分区退磁。
第五步:后清洗
在检验并退磁后,应把试件上所有的磁粉清洗干净;应该注意彻底清除孔和空腔内的所有堵塞物。
4.2.3磁粉检测实验结果分析
下图为磁化后的试样表面:
图4—2 磁粉探伤照片
5、总结
在这次为期两个星期的材料性能分析综合训练中,通过老师辛苦的指导和帮助,我成功地完成了该次实践,并对埋弧焊和金相显微组织的分析及Q345钢的性能及其焊接性等有了更深一步的了解和认识。在书本上学到的知识理论知识,比较抽象,不容易理解。这次的综合分析训练,给我们提供了一个很好的将理论用于实践的机会,使我受益匪浅。实践使我对理论有了更深刻的认识,同时理论也在指导着我们的实践,两者的结合,激发了我对这门课程的热情和兴趣。在以
后的学习中,我将更加努力,使自己掌握的知识更多。
参考文献:
[1] 杨顺贞.工程材料实践教程[M].北京:机械工业出版社
[2] 李亚江. 焊接冶金学:材料焊接性[M]. 北京:机械工业出版社,2011.
[3] 王宗杰. 熔焊方法及设备[M] . 北京:机械工业出版社,2006.
[4] 张文钺. 焊接冶金学:基本原理[M]. 北京:机械工业出版社,2008.
[5]李亚江. 焊接组织性能与质量控制[M].北京:化学工业出版社,2005.
[6] https://www.360docs.net/doc/8810001846.html,/view/13b30d23a5e9856a56126095.html
[7] https://www.360docs.net/doc/8810001846.html,/question/79212081.html
[8] 孙亚英. 光学显微分析[M].北京:清华大学出版社,2003.
[9] 赵熹华.焊接检验[M].北京:机械工业出版社,2011.
[10] 陈裕川.焊接工艺设计与实例分析[M].北京:机械工业出版社,2009. 7.
金属材料的焊接性能汇总
金属材料的焊接性能 (2014.2.27) 摘要:对各种常用金属材料的焊接性能进行研究,通过参考各类焊接丛书及焊接前辈多年的经验总结,对常用金属材料的焊接工艺可行性起指导作用。 关键词:碳当量;焊接性;焊接工艺参数;焊接接头 1 前言 随着中国特种设备制造业的不断发展,我们在制造产品时所用到的金属材料种类也在不断增加,相应地所必须掌握的各种金属材料的焊接性能也在不断研究和更新中,为了实际产品制造的焊接质量,熟悉金属材料的焊接性能,以制定正确的焊接工艺参数,从而获得优良的焊接接头起到至关重要的指导作用。 2 金属材料的焊接性能 2.1 金属材料焊接性的定义及其影响因素 2.1.1 金属材料焊接性的定义 金属材料的焊接性是指金属材料在采用一定的焊接工艺包括焊接方法、焊接材料、焊接规范及焊接结构形式等条件下,获得优良焊接接头的能力。一种金属,如果能用较多普通又简便的焊接工艺获得优良的焊接接头,则认为这种金属具有良好的焊接性能金属材料焊接性一般分为工艺焊接性和使用焊接性两个方面。 工艺焊接性是指在一定焊接工艺条件下,获得优良,无缺陷焊接接头的能力。它不是金属固有的性质,而是根据某种焊接方法和所采用的具体工艺措施来进行的评定。所以金属材料的工艺焊接性与焊接过程密切相关。 使用焊接性是指焊接接头或整个结构满足产品技术条件规定的使用性能的程度。使用性能取决于焊接结构的工作条件和设计上提出的技术要求。通常包括力学性能、抗低温韧性、抗脆断性能、高温蠕变、疲劳性能、持久强度、耐蚀性能和耐磨性能等。例如我们常用的S30403,S31603不锈钢就具有优良的耐蚀性能,16MnDR,09MnNiDR低温钢也有具备良好的抗低温韧性性能。
Q345钢板焊接性能分析解析
Q345钢板焊接性能分析 摘要:本文进行了Q345钢板焊接性能分析。首先根据板材制定了埋弧焊对接试验,然后用卧式显微镜对焊接接头进行宏观和微观分析,并用维氏硬度测试仪检测焊接接头的维氏硬度,同时通过磁粉检测对焊接试样进行了无损检测。最终通过对试验数据进行分析,得出此种材料的焊接性能,并与理论进行分析比较,总结了影响Q345焊接性的因素。 关键词:Q345;埋弧焊;卧式显微镜;维氏硬度;磁粉检测 The Welding Performance Analysis of Q345 Steel Plate Abstract:This article has conducted the welding performance analysis of Q345 steel plate.First of all, on the basis of the plate, we drew up a submerged arc welding butt joint test, then used horizontal microscope to analyze the macrostructure and microstructure of the welding joint, and used HV tester to test its Vickers hardness, at the same time, using the magnetic particle testing to detect the welding sample on the nondestructive testing.Finally analyzed the test data, summing up such material welding performance, and carried on the analysis comparison theory, summarized the influence factors of Q345 weld ability. Keywords:Q345; Submerged Arc Welding; Horizontal Microscope; HV; Magnetic Particle Testing
第二章焊接材料的组成及作用
第二章 焊接材料的组成及作用 1、焊条的工艺性能包括哪些方面?焊条的工艺性能对焊条及焊接质量有什么意义? 1)焊条的工艺性能包括: ①焊接电弧的稳定性 ②焊缝成形 ③各种位置焊接的适应性 ④飞溅⑤脱渣性 ⑥焊条溶化速度 ⑦焊条药皮发红 ⑧焊接烟尘 2) 焊条的工艺性能: 是指在焊接操作中的性能,是衡量焊接质量的重要指标之一,可以降低电弧气氛的电离电位,因而能提高电弧的稳定性;焊缝表面成形不仅影响美观,更重要的是影响焊接接头的力学性能如果熔渣的凝固温度过高,就会产生压铁水的现象,严重影响焊缝成形,甚至产生气孔,良好的焊条能适应全位置焊接脱渣性差的不仅造成清渣的困难,降低焊接生产率,而且在多层焊施工时,还往往产生夹渣的缺陷。 2、综合分析碱性焊条药皮中2CaF 的作用及对焊缝性能的影响。 它的主要作用是脱氧,在焊条药皮中加入2CaF 发生的焊接冶金反应生成HF 气体,HF 是比较稳定的气体,高温时不易发生分解,也不溶于液体金属中,而是与焊接烟尘一起挥发了,所以减低熔池金属中的H 含量,提高了焊缝金属的冲击韧性和抗裂性能。 3、配置22CaF TiO SiO CaO ---渣系焊条,经初步试验发现药皮套筒过长,电弧不稳,此时应该如何调整该焊条的药皮配方? 药皮套筒过长,是因为药皮熔点过高,溶化速度过慢,则可以通过减少药皮中CaO ,而适当加入些3232N CO a CO K 或,电弧不稳是因为焊条药皮中含2CaF 生成HF 气体的缘故,可适当降低2CaF 含量。 4、试分析低氢型碱性焊条降低发尘量及毒性的主要途径。 低氢型碳钢焊条的焊接烟尘量高于钛钙型焊条,烟尘中危害最大的是KF ,NaF ,而钠钾主要存在于水玻璃中,故可用树脂来降低水玻璃的粘性作用。
材料焊接性考试重点试题及答案
3.5.分析低碳调质钢焊接时可能出现的问题?简述低碳调质钢的焊接工艺要点,典型的低碳调质钢如(14MnMoNiB、HQ70、HQ80)的焊接热输入应控制在什么范围?在什么情况下采用预热措施,为什么有最低预热温度要求,如何确定最高预热温度。 答:焊接时易发生脆化,焊接时由于热循环作用使热影响区强度和韧性下降。焊接工艺特点:焊后一般不需热处理,采用多道多层工艺,采用窄焊道而不用横向摆动的运条技术。。典型的低碳调质钢的焊接热输入应控制在Wc>0.18%时不应提高冷速,Wc<0.18%时可提高冷速(减小热输入)焊接热输入应控制在小于481KJ/cm当焊接热输入提高到最大允许值裂纹还不能避免时,就必须采用预热措施,当预热温度过高时不仅对防止冷裂纹没有必要,反而会使800~500℃的冷却速度低于出现脆性混合组织的临界冷却速度,使热影响区韧性下降,所以需要避免不必要的提高预热温度,包括屋间温度,因此有最低预热温度。通过实验后确定钢材的焊接热输入的最大允许值,然后根据最大热输入时冷裂纹倾向再来考虑,是否需要采取预热和预热温度大小,包括最高预热温度。 4.3. 18-8型不锈钢焊接接头区域在那些部位可能产生晶间腐蚀,是由于什么原因造成?如何防止?答:18-8型焊接接头有三个部位能出现
腐蚀现象:{1}焊缝区晶间腐蚀。产生原因根据贫铬理论,碳与晶界附近的Cr形成Cr23C6,并在在晶界析出,导致γ晶粒外层的含Cr量降低,形成贫Cr层,使得电极电位下降,当在腐蚀介质作用下,贫Cr层成为阴极,遭受电化学腐蚀;{2}热影响区敏化区晶间腐蚀。是由于敏化区在高温时易析出铬的碳化物,形成贫Cr层,造成晶间腐蚀;{3}融合区晶间腐蚀{刀状腐蚀}。只发生在焊Nb或Ti的18-8型钢的溶合区,其实质也是与M23C6沉淀而形成贫Cr有关,高温过热和中温敏化相继作用是其产生的的必要条件。防止方法:{1}控制焊缝金属化学成分,降低含碳量,加入稳定化元素Ti、Nb;{2} 控制焊缝的组织形态,形成双向组织{γ+15%δ};{3}控制敏化温度范围的停留时间;{4}焊后热处理:固溶处理,稳定化处理,消除应力处理。 4.7何为“脆化现象”?铁素体不锈钢焊接时有哪些脆化现象,各发生在 什么温度区域?如何避免?答:“脆化现象”就是材料硬度高,但塑性 和韧性差。现象与避免措施:{1}高温脆性:在900~1000℃急冷至 室温,焊接接头HAZ的塑性和韧性下降。可重新加热到750~850℃, 便可恢复其塑性。{2}σ相脆化:在570~820℃之间加热,可析出σ相 。σ相析出与焊缝金属中的化学成分、组织、加热温度、保温时间以 及预先冷变形有关。加入Mn、Nb使σ相所需Cr的含量降低,Ni能使形成σ相所需温度提高。{3}475℃脆化:在400~500℃长期加热后可出 现475℃脆化。适当降低含Cr量,有利于减轻脆化,若出现475℃脆
Q420高强度钢板焊接工艺性能研究
龙源期刊网 https://www.360docs.net/doc/8810001846.html, Q420高强度钢板焊接工艺性能研究 作者:裴广州 来源:《中小企业管理与科技·下旬刊》2013年第08期 摘要:在对凤凰山矿井下所使用的电机护罩用高强度钢板Q420的电阻点焊工艺性能进行深入研究中,对不同工艺条件下点焊接头宏观金相、焊接接头力学性能进行了分析,研究结果表明:该实验条件下,最佳点焊工艺参数为:焊接电流7.5~8.0KA,焊接时间20cyc,电极压力450kgf。为了防止发生焊接缺陷,避免焊接电流过小或者焊接时间过长,导致锻压力不足等现象,在焊接过程中需要保持电极和工件表面的清洁。 关键词:Q420钢电阻点焊焊接工艺缺陷防止 0 引言 Q420钢具有较高的碳当量,焊后硬化可能性更高。因此,许多先进煤机制造企业密切关注着其焊接性能。鉴于此,为了探讨不同点焊工艺参数下Q420的焊接性能,本文通过点焊工艺和力学性能试验等对凤凰山矿井下电机护罩所用的Q420钢进行研究分析,进而对Q420钢合理的点焊规范参数范围进行确定。 1 实验方法 1.1 设定焊接参数本文通过采用单脉冲规范对Q420进行点焊工艺试验。电极压力为 350kgf、400kgf、450kgf,焊接时间为7cyc、10cyc、15cyc、20cyc和24cyc。在进行每组试验的过程中,固定电极压力和焊接时间,通过改变型控DIN100制器的焊接热量(功率输m百分比)进而改变焊接电流的大小,对Q420进行焊接。最小焊接热量通过拉伸试验进行确定,在焊接过程中以5%数量级进行取样焊接,发生飞溅时停止对Q420焊接。同一焊接热量,通常 情况下要进行2-3次的取样。由于焊件和电极表面状态存在差异,在一定程度上造成电流值大小的不同,由于这些微小的变化对试验不构成影响,所以在较小范围内可以忽略不计。 1.2 力学性能实验通常情况下,借助接头强度来反映点焊接头质量的好坏,然而一般采用拉伸剪切强度对接头强度进行评定。因此,本文通过利用拉剪试验对点焊工艺试验后的试样进行试验。在试验过程中,根据GB2651-81《焊接接头拉伸试验法》中的相关规定,确定拉剪试样的形状与尺寸。 2 试验结果与分析 2.1 工艺参数对焊点性能的影响 2.1.1 焊接电流。按照焊接规范,电极压力选450kgf,焊接时间为7cyc、10cyc、15cyc、20cyc、24cyc。通过点焊工艺和接头拉剪试验对不同焊接电流下的点焊接头的拉剪断裂载荷进
各种材料的焊接性能
金属材料的焊接性能 (1)焊接性能良好的钢材主要有: 低碳钢(含碳量<0.25);低合金钢(合金元素含量1~3、含碳量<0.20);不锈钢(合金元素含量>3、含碳量<0.18)。 (2)焊接性能一般的钢材主要有: 中碳钢(合金元素含量<1、含碳量0.25~0.35);低合金钢(合金元素含量<3、含碳量<0.30);不锈钢(合金元素含量13~25、含碳量£0.18) (3)焊接性能较差的钢材主要有: 中碳钢(合金元素含量<1、含碳量0.35~0.45);低合金钢(合金元素含量1~3、含碳量0.30~0.40);不锈钢(合金元素含量13、含碳量0.20)。 (4)焊接性能不好的钢材主要有: 中、高碳钢(合金元素含量<1、含碳量>0.45);低合金钢(合金元素含量1~3、含碳量>0.40);不锈钢(合金元素含量13、含碳量0.30~0.40)。 焊条和焊丝选择的基本要点如下: 同类钢材焊接时选择焊条主要考虑以下几类因素: 考虑工件的物理、机械性能和化学成分;考虑工件的工作条件和使用性能; 考虑工件几何形状的复杂程度、刚度大小、焊接坡口的制备情况和焊接部位所处的位置等;考虑焊接设备情况;考虑改善焊接工艺和环保;考虑成本。 异种钢材和复合钢板选择焊条主要考虑以下几类焊接情况: 一般碳钢和低合金钢间的焊接;低合金钢和奥氏体不锈钢之间的焊接;不锈钢复合钢板的焊接。 焊条和焊丝的选择参数查阅机械设计手册中焊条和焊丝等章节和焊条分类及型号(GB 980-76)、焊条的性能和用途(GB 980~984-76)等有关国家标准。 ###15CrMoR的换热器的热处理工艺 ***当板厚超过筒体内径的3%时,卷板后壳体须整体热处理。 *** 15CrMoR焊接性能良好。手工焊用E5515-B2(热307)焊条,焊前预热至200-250℃(小口径薄壁管可不预热),焊后650-700℃回火处理。自动焊丝用H13CrMoA和焊剂250等。 ###压力容器用钢的基本要求 压力容器用钢的基本要求:较高的强度,良好的塑性、韧性、制造性能和与相容性。 改善钢材性能的途径:化学成分的设计,组织结构的改变,零件表面改性。 本节对压力容器用钢的基本要求作进一步分析。 一、化学成分 钢材化学成分对其性能和热处理有较大的影响。 1、碳:碳含量增加时,钢的强度增大,可焊性下降,焊接时易在热影响区出现裂纹。 因此压力容器用钢的含碳量一般不应大于0.25%。2、钒、钛、铌等:在钢中加入钒、钛、铌等元素,可提高钢的强度和韧性。
材料焊接性
《材料焊接性》(专科)学案 第一章绪论 二、本章习题 1. 根据本章所述内容,举例说明低合金钢焊接在工程结构中的重要作用。 2.先进材料的发展和应用在工程中越来越受到人们的重视,简述先进材料(如陶瓷、金属间化合物和复合材料等)和金属材料相比,在工程结构中的应用有什么不同? 第2章材料焊接性及其试验方法 1. 了解焊接性的基本概念。什么是工艺焊接性?影响工艺焊接性的主要因素有哪些? 焊接性,是指金属材料在采用一定的焊接工艺包括焊接方法、焊接材料、焊接规范及焊接结构形式等条件下,获得优良焊接接头的难易程度。 工艺焊接性是指在一定焊接工艺条件下,获得优质、无缺陷的焊接接头的能力。 影响因素:材料因素、工艺因素、结构因素、使用条件。 2. 什么是热焊接性和冶金焊接性,各涉及到焊接中的什么问题? 冶金焊接性指在熔焊高温下的熔池金属与气象熔渣等相互之间繁盛化学冶金反映所引起的焊接变化
3. 举例说明有时工艺焊接性好的金属材料使用焊接性不一定好。 工艺焊接性是指影响焊接操作的焊接性能,如电弧的稳定性、焊缝的成形性、脱渣性、飞溅大小及发尘量等。而使用焊接性则是指焊件需满足的使用要求,如接头的力学性能、物理性能及化学性能要求。 有时,工艺焊接性好的材料如果焊接材料选择不当,其使用性能就不一定好:例如不锈钢焊接,若使用普通结构钢焊条焊接,其工艺焊接性很好,即焊接过程很顺利,但是,焊缝不耐腐蚀,就不能满足不锈钢焊件的使用要求,因此焊接接头是不合格的。 金属材料使用性能主要指力学性能,即金属材料在外力作用下表现出来的各种特性,如弹性、塑性、韧性、强度、硬度等。 比如低碳钢焊接性好,但其强度、硬度却没有高碳钢好| 第3章低合金结构钢的焊接 1. 分析热轧钢和正火钢的强化方式及主强化元素有什么不同。二者的焊接性有何差异,在制定焊接工艺时应注意什么问题。 热轧钢的强化方式有:(1)固溶强化,主要强化元素:Mn,Si。(2)细晶强化,主要强化元素:Nb,V。(3)沉淀强化,主要强化元素:Nb,V.;正火钢的强化方式:(1)固溶强化,主要强化元素:强的合金元素(2)细晶强化,主要强化元素:V,Nb,Ti,Mo(3)沉淀强化,主要强化元素:Nb,V,Ti,Mo.;焊接性:热轧钢含有少量的合金元素,碳当量较低冷裂纹倾向不大,正火钢含有合金元素较多,淬硬性有所增加,碳当量低冷裂纹倾向不大。热轧钢被加热到1200℃以上的热影响区可能产生粗晶脆化,韧性明显降低,而是、正火钢在该条件粗晶区的析出相基本固溶,抑制A长大及组织细化作用被削弱,粗晶区易出现粗大晶粒及上贝、M-A等导致韧性下降和时敏感性增大。制定焊接工艺时根据材料的结构、板厚、使用性能要求及生产条件选择焊接 2. 分析16Mn的焊接性特点,给出相应的焊接材料及焊接工艺要求。
高强度钢板的性能及焊接
BS系列高强钢简介 Brief introduction 开发历史 工程机械用系列高强、超高强结构钢是宝钢于2000年在国内率先开发成功的一类热轧新产品,牌号大多采用“BS”开头, 如第一代高强钢BS600MC和BS700MC已大量应用于工程机械、集装箱制造等行业。2005年宝钢开发成功具有优良低温韧性的第二代高强钢,牌号为BS700MCK2、BS600MCJ4、BS550MCK4等等。BS系列高强钢为低碳低合金结构钢,具有良好的可焊接性和冷成形性,可广泛应用于工程机械、车辆结构、集装箱等制造行业。 高强钢 BS系列高强结构钢采用宝钢股份公司先进的冶炼技术、铌钛微合金化处理以及精确的控制轧制和控制冷却技术获得金相显微组织为少量铁素体加针状体组织。制造工艺和金相组织保证了合格稳定的力学性能、加工性能和可靠的质量。自从2000年开发成功以后,深受用户青睐,产销量逐年增加。超高强钢选用高强钢代替传统产品可显著减小钢板的设计厚度,进而减轻结构的自重。除此之外,BS系列高强钢还具有如下特点: ? 优良的成形性,不同强度级别钢板均能够冷加工成形; ? 良好的焊接性,钢板具有低焊接裂纹敏感性,焊接接头的性能优良; ? 良好的低温冲击韧性。 制造工艺及交货状态 生产工艺流程: BS系列高强钢采用氧气转炉冶炼镇静钢,经过二次精炼后进行连续铸造,连铸坯送热轧厂再加热并采用控轧控冷工艺轧制成卷,精整检验后可以钢卷状态交货,也可以矫直切板后以钢板状态交货。交货状态: BS系列高强钢基本采用轧态(TMCP)交货。 所示,超出规格范围可与宝钢热轧高强钢产销研小组联系(附后)。 牌号Steel grade 可供厚度Thickness,mm 可供宽度Width,mm 可供长度Length,mm BS550- 2.5-16 850-1750 2000-12000 BS600- 2.5-16 850-1750 2000-12000 BS700- 2.5-14 850-1600 2000-12000 BS960- 4-10 950-1200 2000-12000 牌号及可供规格范围 Product range of dimensions 宽度 (width), mm 18 10 14 6 17 9 13 5 16 8 12 4
ND钢焊接性能及检验
ND钢的焊接 耐硫酸露点腐蚀用09CrCuSb钢板的可焊接性及焊接技术要求,通过焊接工艺试验制定了合理的焊接工艺参数,在酸性气燃烧炉的焊接施工中应用,获得了满意的焊接质量,保证了设备的制造要求。 1、概况 露点腐蚀对加热炉设备的使用寿命有很大的影响,为了提高燃料的热效率,稍降低排烟温度就会使设备严重腐蚀,这就给生产带来了很大的困难,由此也可以看出解决露点腐蚀的难度。1987-1990年间由中石化北京设计院、江苏江阴兴澄钢铁有限公司与机械部伤害材料研究所共同研究开发了新型耐硫酸露点腐蚀用钢---ND钢,其主要特点是在中温中浓度的硫酸(如70℃、50%H2SO4溶液)中表面发生钝化,形成一层富含Cu、Cr、Sb等合金元素的保护层,因而具有高的耐硫酸腐蚀能力。 在兰炼酸性水汽提及硫酸回收装置的技术改造过程中,酸性气燃烧炉壳体材质就选用了ND钢——09CrCuSb,炉内介质为H2S、SO2、H2O,用ND钢可防止硫酸露点腐蚀,保证设备的正常运行。 2 09CrCuSb钢的可焊性 09CrCuSb钢的显微组织为铁素体+珠光体组织,珠光体含量为15%,夹杂物为硫化物及少量氧化物,晶粒度为8-9级。其化学成分及力学性能见表1、表2 表1 09CrCuSb钢板(厚12mm)的力学性能 须控制在C<0.10%、Sb<0.10%范围以内,除此以外要保证主要合金元素含量越高越耐蚀,耐蚀性能主要取决于合金元素的配比,任何合金成分中元素的偏析都将使ND钢的耐蚀性受到影响,甚至出现局部腐蚀。可通过严格控制合金元素的成分,使合金元素达到均匀化的目的。 一般来说,钢的可焊性是用它的碳当量C eq、焊后最高硬度值HV max及焊接裂纹敏感系数P cm 来衡量的。 (1)按实际元素含量计算碳当量C eq: C eq=C+Mn/6+Si/24+Ni/40+Cr/5+Mo/4+V/14=0.355% C eq<0.4% 由此可知09CrCuSb钢板焊接时基本无淬硬倾向。 (2)按碳当量用下式近似估算09CrCuSb钢焊接后的硬度HV max HV max=1200×C eq-200: HV226.5<HV350 由此可知该钢板焊前无须预热,而且焊接时冷裂倾向很小。 (3)焊接裂纹敏感系数P cm: P cm=C+Si/30+Mn/20+Cu/20+Cr/20+Ni/60+Mo/15+V/10+5B=0.179% 由P cm值可以看出09CrCuSb钢属于地焊接裂纹敏感性钢材。 综上所述,09CrCuSb钢含碳量较低,又添加了少量Cr、Cu、Sb等合金元素,补偿了由于碳含量较低可能引起的强度损失,同时根据碳当量C eq及焊后硬度HV max值可知这种钢的淬硬倾向较小,焊前无须预热,而且由焊接裂纹敏感系数P cm可知这种钢是一种低焊接裂纹敏感性的钢材,因此可以看出09CrCuSb钢具有良好的焊接性能。
各种常用材料焊接的焊接材料选择原则
各种常用材料焊接的焊接材料选择原则 为得到高质量的焊接接头,首先要合理选择焊接材料。由于焊接部件在运行中的工况有很大差异,母材的材质性能、成分千差万别,部件的制造工艺错综复杂,因此需要从各方面综合考虑确定对应的焊接材料。选择焊接材料应遵循以下原则: 满足焊接接头使用性能的要求。包括常温、高温短时强度、弯曲性能、 冲击韧性、硬度、化学成分等,以及一些技术标准和设计图纸中对街头性能的特殊要求,诸如持久强度,入编极限、高温抗氧化强度、抗腐蚀性能等。 满足焊接接头制造工艺性能和焊接工艺性能的要求。焊接接头组成的构 件,在制造过程中不可避免要进行各种成型和切削加工,例如冲压、车、刨等,要求焊接接头具有一定的塑性变形能力和切削性能、高温综合性能等。 合理的经济性。在满足上述性能外,应选择价格便宜的焊接材料,降低 制造成本。例如重要部件的低碳钢手工电弧焊时,应优先选择碱性药皮焊条,因为碱性焊条脱硫、脱氧充分,且氢含量低,焊缝金属抗裂性能及冲击韧性性能好。而对于一些非重要不见,可选用酸性焊条,因为酸性焊条仍能满足费重要部件的性能要求,而且工艺性良好,价格便宜,可降低制造成本。 第二节碳素钢、低合金钢焊接材料的选择 碳素钢、低合金钢(包括低合金耐热钢、低合金高强钢)焊接材料的选择,应考虑下列因素:等强性和等韧性原则 承压承载的部件,通常根据材料的拉伸应力进行强度计算,拉伸需用应力与 材料的标准抗拉强度下限值有关,即许用应力 (σ)=σb/nb(各种标准nb的取值同) (σ)为材料的拉伸许用应力 σb为材料的标准抗拉强度下限值 nb 为安全系数(各种标准nb的取值不同) 所以焊接接头作为部件的一部分,其焊缝抗拉强度应不小于母材标准抗拉强度规定的下限。同时应注意焊接材料熔敷金属的抗拉强度不能大大高于母材的抗拉强度,而导致焊缝塑性性能降低,硬度增大,不利于随后的制造成型。尽管强度计算仅考虑材料的抗拉强度,各种工艺评定标准对焊缝的屈服强度均无要求,但选择焊接材料时也应考虑焊接材料熔敷金属的屈服强度不应低于母材的屈服强度,并注意保证一定的屈强比。当接头在高温运行通常用工作温度(或设计温度)下材料的高温短时抗拉强度规定下限进行需用应力计算即 [σt]= σbt/nb 其中[σt]为材料t温度下,短时抗拉强度规定值下计算的高温许用应力 σbt为材料t温度下,短时抗拉强度规定值下限 或工作温度下材料的持久强度蠕变极限进行许用应力计算 [σDt]= σDt/nD 其中,[σDt]为材料t温度下持久强度计算的许用应力 σDt为材料t温度下的持久强度 nD为安全系数(各种标准的取值不同) 因此,选择高温运行焊接接头的焊接材料时,应考虑其高温短时抗拉强度或持久强度不得低于母材的对应值。一般碳素钢和普通低合金钢选择焊接材料只要考虑焊接材料的考拉强度,可不考虑熔敷金属的化学成分与母材匹配,但对于Cr-Mo耐热钢材料的焊接,选择焊接材料不仅考虑其等强性,还应考虑合金元素的匹配以保证焊接接头的综合性能与母材一致。 在特殊情况下,部件按材料的屈服强度计算许用应力进行设计时,就必须以屈服强度的等强
冷轧钢焊接性能研究
冷轧钢焊接性能研究 一、冷轧钢与热轧性能比较 1、冷轧与热轧区别及各自优缺点 热轧和冷轧都是型钢或钢板成型的工序,它们对钢材的组织和性能有很大的影响,钢的轧制主要以热轧为主,冷轧只用于生产小号型钢和薄板。 热轧: 优点:可以破坏钢锭的铸造组织,细化钢材的晶粒,并消除显微组织的缺陷,从而使钢材组织密实,力学性能得到改善。这种改善主要体现在沿轧制方向上,从而使钢材在一定程度上不再是各向同性体;浇注时形成的气泡、裂纹和疏松,也可在高温和压力作用下被焊合。 缺点:1.经过热轧之后,钢材内部的非金属夹杂物(主要是硫化物和氧化物,还有硅酸盐)被压成薄片,出现分层(夹层)现象。分层使钢材沿厚度方向受拉的性能大大恶化,并且有可能在焊缝收缩时出现层间撕裂。焊缝收缩诱发的局部应变时常达到屈服点应变的数倍,比荷载引起的应变大得多;2.不均匀冷却造成的残余应力。残余应力是在没有外力作用下内部自相平衡的应力,各种截面的热轧型钢都有这类残余应力,一般型钢截面尺寸越大,残余应力也越大。残余应力虽然是自相平衡的,但对钢构件在外力作用下的性能还是有一定影响。如对变形、稳定性、抗疲劳等方面都可能产生不利的作用。 冷轧: 优点:成型速度快、产量高,且不损伤涂层,可以做成多种多样的截面形式,以适应使用条件的需要;冷轧可以使钢材产生很大的塑性变形,从而提高了钢材的屈服点。 缺点: :1.虽然成型过程中没有经过热态塑性压缩,但截面内仍然存在残余应力,对钢材整体和局部屈曲的特性必然产生影响;2.冷轧型钢样式一般为开口截面,使得截面的自由扭转刚度较低。在受弯时容易出现扭转,受压时容易出现弯扭屈曲,抗扭性能较差;3.冷轧成型钢壁厚较小,在板件衔接的转角处又没有加厚,承受局部性的集中荷载的能力弱。 2、焊接性能比较 同等材质的钢材,热轧时经高温加热,相当于一个退火过程钢材自身基本没有应力。而冷轧板在轧制时不加热,在冷态时轧制,有一个“冷作硬化”的作用,强度有所升高,硬度也增加,同时也产生了应力。 在焊接时有一个“焊接应力”,由于冷轧板(含其他型材)的自有应力,加上
各种材料的焊接性能
###焊接性能良好的钢材主要有: 低碳钢(含碳量<0.25); 低合金钢(合金元素含量1~3、含碳量<0.20); 不锈钢(合金元素含量>3、含碳量<0.18)。 焊接性能一般的钢材主要有: 中碳钢(合金元素含量<1、含碳量0.25~0.35); 低合金钢(合金元素含量<3、含碳量<0.30); 不锈钢(合金元素含量13~25、含碳量£0.18)。 焊接性能较差的钢材主要有: 中碳钢(合金元素含量<1、含碳量0.35~0.45); 低合金钢(合金元素含量1~3、含碳量0.30~0.40); 不锈钢(合金元素含量13、含碳量0.20)。 焊接性能不好的钢材主要有: 中、高碳钢(合金元素含量<1、含碳量>0.45); 低合金钢(合金元素含量1~3、含碳量>0.40); 不锈钢(合金元素含量13、含碳量0.30~0.40)。 焊条和焊丝选择的基本要点如下: 同类钢材焊接时选择焊条主要考虑以下几类因素: 考虑工件的物理、机械性能和化学成分;考虑工件的工作条件和使用性能; 考虑工件几何形状的复杂程度、刚度大小、焊接坡口的制备情况和焊接部位所处的位置等;考虑焊接设备情况;考虑改善焊接工艺和环保;考虑成本。 异种钢材和复合钢板选择焊条主要考虑以下几类焊接情况: 一般碳钢和低合金钢间的焊接;低合金钢和奥氏体不锈钢之间的焊接;不锈钢复合钢板的焊接。 焊条和焊丝的选择参数查阅机械设计手册中焊条和焊丝等章节和焊条分类及型号(GB 980-76)、焊条的性能和用途(GB 980~984-76)等有关国家标准。 ###15CrMoR的换热器的热处理工艺 ***当板厚超过筒体内径的3%时,卷板后壳体须整体热处理。 *** 15CrMoR焊接性能良好。手工焊用E5515-B2(热307)焊条,焊前预热至200-250℃(小口径薄壁管可不预热),焊后650-700℃回火处理。自动焊丝用H13CrMoA和焊剂250等。 ###压力容器用钢的基本要求 压力容器用钢的基本要求:较高的强度,良好的塑性、韧性、制造性能和与相容性。 改善钢材性能的途径:化学成分的设计,组织结构的改变,零件表面改性。 本节对压力容器用钢的基本要求作进一步分析。 一、化学成分 钢材化学成分对其性能和热处理有较大的影响。 1、碳:碳含量增加时,钢的强度增大,可焊性下降,焊接时易在热影响区出现裂纹。 因此压力容器用钢的含碳量一般不应大于0.25%。2、钒、钛、铌等:在钢中加入钒、钛、
厚钢板焊缝强度匹配对韧度影响的试验方法
厚钢板焊缝强度匹配对韧度影响的试验方法 苗张木陶德馨吴卫国李永信 武汉理工大学,武汉,430063 摘要:提出了研究厚钢板焊缝强度匹配对韧度影响的试验方法:用“直接测量法”确定焊缝强度匹配系数;用裂纹尖端张开位移(C TOD )断裂韧度作为焊缝材料韧度的指标。用“直接测量法”确定了低合金高强钢S355ML 钢板(厚65mm )自动埋弧焊和手工电弧焊的焊缝强度匹配系数,同时将这两项焊接工艺的对接焊缝制成全厚度断裂韧度试样,运用裂纹尖端张开位移试验方法测定其焊缝中心的断裂韧度。结果表明,厚钢板焊态对接焊缝,低匹配焊缝具有较高的韧度,高匹配焊缝的韧度比较低。 关键词:焊缝强度匹配系数;断裂韧度;裂纹尖端张开位移(C TOD );厚钢板中图分类号:T G404;T G115.5 文章编号:1004-132X (2006)09—0958—05 Experimental Method of the Influence of Strength Mismatch on Toughness in Thick Sheet Steel Miao Zhangmu Tao Dexin Wu Weiguo Li Y ongxin Wuhan University of Technology ,Wuhan ,430063 Abstract :A testing met hod of exploring t he influence of st rengt h mismatch on toughness in t hick sheet steel welds was developed.By means of t his met hod ,t he mismatching factors can be determined wit h “direct measurement met hod ”,and t he crack tip opening displacement (C TOD )should be selected to be as index characterized t he toughness of welds.First ,t he mismatching factors of submerged arc welding (SAW )and shielded metal arc welding (SMAW )of S355ML steel (65mm t hickness )were de 2termined wit h “direct measurement met hod ”.Then ,t he butt welds of SAW and SMAW were made to f ull t hickness f ract ure toughness specimens and t he fract ure toughness in welds cent re were measured by C TOD test.The result s indicate t hat t he welds po ssess higher toughness for lower mismatch ,whereas t he welds possess lower toughness for higher mismatch for butt welds of t hick sheet steel. K ey w ords :mismatching factor of toughness ;f ract ure toughness ;crack tip opening displacement (C TOD );t hick sheet steel 收稿日期:2005—11—30 0 引言 焊接结构设计必须确定焊缝金属的强度和韧度。强度和韧度是焊接结构安全中密切联系的两个问题。韧度是材料在断裂前所经历的弹塑性变形过程中吸收能量的能力[1],是强度和塑性的综合指标,它比强度这个单一指标更应受到关注,特别是对于焊接接头。焊缝强度对其韧度的影响,已经有许多文献进行了讨论,但存在一些分歧[2,3],如文献[3]指出了两种不同观点:一是在保证焊缝常规延性、韧性(如使焊缝金属与母材具有相同延伸率)的条件下,适当选用屈服点较高的焊缝金属,即高匹配是有利的;二是着眼于焊缝的韧性或延性,而其强度与母材相比可适当降低,即低匹配。已有的研究多限于较薄钢板的焊接,厚钢板焊缝强度对韧度的影响研究的文献较少。随着经济发展和科学技术不断进步,海洋结构、桥梁结构、现代建筑及水电核电等工程项目的规模越 来越大,焊接结构呈厚壁化、大型化趋势,所用厚钢板焊接接头破坏的主要原因是由于韧度不足。 因此,研究厚钢板焊缝强度匹配对韧度的影响具有重要的意义。 研究厚钢板焊缝强度匹配对韧度的影响,一是要能够准确测量并计算焊缝强度匹配系数,二是要选择恰当的指标来评价焊缝韧度。本文针对厚钢板特点,结合低合金高强钢S355ML (相当于国产Q345钢)厚钢板(厚65mm )自动埋弧焊和手工电弧焊焊缝强度对韧度的影响研究,提出了研究厚钢板焊缝强度匹配对韧度影响的试验方法:用“直接测量法”确定焊缝强度匹配系数;用裂纹尖端张开位移(C TOD )断裂韧度作为综合度量焊缝韧度的指标。 1 焊接工艺 1.1 母材 本研究采用厚65mm 的S355ML 热轧钢板,系从日本进口。其化学成分见表1,最大碳当量为 8 59
材料焊接性答案--第三章
第三章:合金结构钢 1.分析热轧钢和正火钢的强化方式和主强化元素又什么不同,二者的焊接性有何差别?在制定焊接工艺时要注意什么问题? 答:热轧钢的强化方式有:(1)固溶强化,主要强化元素:Mn,Si。(2)细晶强化,主要强化元素:Nb,V。(3)沉淀强化,主要强化元素:Nb,V.;正火钢的强化方式:(1)固溶强化,主要强化元素:强的合金元素(2)细晶强化,主要强化元素:V,Nb,Ti,Mo(3)沉淀强化,主要强化元素:Nb,V,Ti,Mo.;焊接性:热轧钢含有少量的合金元素,碳当量较低冷裂纹倾向不大,正火钢含有合金元素较多,淬硬性有所增加,碳当量低冷裂纹倾向不大。热轧钢被加热到1200℃以上的热影响区可能产生粗晶脆化,韧性明显降低,而是、正火钢在该条件下粗晶区的V析出相基本固溶,抑制A长大及组织细化作用被削弱,粗晶区易出现粗大晶粒及上贝、M-A等导致韧性下降和时效敏感性增大。制定焊接工艺时根据材料的结构、板厚、使用性能要求及生产条件选择焊接。 2.分析Q345的焊接性特点,给出相应的焊接材料及焊接工艺要求。答:Q345钢属于热轧钢,其碳当量小于0.4%,焊接性良好,一般不
需要预热和严格控制焊接热输入,从脆硬倾向上,Q345钢连续冷却时,珠光体转变右移,使快冷下的铁素体析出,剩下富碳奥氏体来不及转变为珠光体,而转变为含碳量高的贝氏体与马氏体具有淬硬倾向,Q345刚含碳量低含锰高,具有良好的抗热裂性能,在Q345刚中加入V、Nb达到沉淀强化作用可以消除焊接接头中的应力裂纹。被加热到1200℃以上的热影响区过热区可能产生粗晶脆化,韧性明显降低,Q345钢经过600℃×1h退火处理,韧性大幅提高,热应变脆化倾向明显减小。;焊接材料:对焊条电弧焊焊条的选择:E5系列。埋弧焊:焊剂SJ501,焊丝H08A/H08MnA.电渣焊:焊剂HJ431、HJ360焊丝H08MnMoA。CO2气体保护焊:H08系列和YJ5系列。预热温度:100~150℃。焊后热处理:电弧焊一般不进行或600~650℃回火。电渣焊900~930℃正火,600~650℃回火 3 .Q345与Q390焊接性有何差异?Q345焊接工艺是否适用于Q390焊接,为什么? 答:Q345与Q390都属于热轧钢,化学成分基本相同,只是Q390的Mn含量高于Q345,从而使Q390的碳当量大于Q345,所以Q390的淬硬性和冷裂纹倾向大于Q345,其余的焊接性基本相同。Q345的焊接工艺不一定适用于Q390的焊接,因为Q390的碳当量较大,一级Q345的热输入叫宽,有可能使Q390的热输入过大会引起接头区过热的加
各种材料的钎焊
中国焊接服务平台: 中国焊接服务平台博客: 各种材料的钎焊 一、碳钢和低合金钢的钎焊 1、钎焊材料 (1)钎料碳钢和低合金钢的钎焊包括软钎焊和硬钎焊。软钎焊中应用量广的钎料是锡铅儿料,这种钎料对钢的润湿性随含锡量的增加而提高,因而对密封接头宜采用含锡量高的钎料。锡铅钎料中的锡与钢在界面上可能形成FeSn2金属间化合物层,为避免该层化合物的形成,应适当控制钎焊温度和保温时间。几种典型的锡铅钎料钎焊的碳钢接头的抗剪强度如表1所示,其中以w(Sn)为50%的钎料钎焊的接头强度最高,不含锑的钎料所焊的接头强度比含锑的高。 表1 锡铅钎料钎焊的碳钢接头的抗剪强度 碳钢和低合金钢硬钎焊时,主要采用纯铜、铜锌和银铜锌钎料。纯铜熔点高,钎焊时易使母材氧化,主要用于气体保护钎焊和真空钎焊。但应注意的是钎焊接头间隙宜小于0.05mm,以免产生因铜的流动性好而使接头间隙不能填潢的问题。用纯铜钎焊的碳钢和低合金钢接头具有较高的强度,一般抗剪强度在150~215MPa,而抗拉强度分布在170~340MPa之间。 与纯铜相比,铜锌钎料因Zn的加入而使钎料熔点降低。为防止钎焊时Zn的蒸发,一方面可在铜锌钎料中加入少量的Si;另一方面必须采用快速加热
的方法,如火焰钎焊、感应钎焊和浸沾钎焊等。采用铜锌钎料钎焊的碳钢和低合金钢接头都具有较好的强度和塑性。例如用B-Cu62Zn钎料钎焊的碳钢接头抗拉强度达420MPa,抗剪强度达290MPa,银铜站钎料的熔点比铜锌钎料的熔点还低,便于针焊的操作。这种钎料适用于碳钢和低合金钢的火焰钎焊、感应钎焊和炉中钎焊,但在炉中钎焊时应尽量降低Zn的含量,同时应提高加热速度。采用银铜锌钎料钎焊碳钢和低合金钢,可获得强度和塑性均较好的接头,具体数据列于表2中。 表2 银铜锌钎料钎焊的低碳钢接头的强度 (2)钎剂钎焊碳钢和低合金钢时均需使用钎剂或保护气体。钎剂常按所选的钎料和钎焊方法而定。当采用锡铅钎料时,可选用氯化锌与氯化铵的混合液作钎剂或其他专用钎剂。这种钎剂的残渣一般都具有很强的腐蚀性,钎焊后应对接头进行严格清洗。 采用铜锌钎料进行硬钎焊时,应选用FB301或FB302钎剂,即硼砂或硼砂与硼酸的混合物;在火焰钎焊中,还可采用硼酸甲酯与甲酸的混合液作钎剂,其中起去膜作用的是B2O3蒸气。 当采用银铜锌钎料时,可选择FB102、FB103和FB104钎剂,即硼砂、硼酸和某些氟化物的混合物。这种钎剂的残渣具有一定的腐蚀性,钎焊后应清除干净。 2、钎焊技术 采用机械或化学方法清理待焊表面、确保氧化膜和有机物彻底清除。清理后的表面不宜过于粗糙,不得粘附金属屑粒或其他污物。
材料焊接性---实验
第三部分高级电焊工知识要求 第二十六章焊接接头试验方法 第一节焊接性试验方法 一、焊接冷裂纹试验方法 1、间接评定方法根据焊件材料的化学成分或焊接接头热影响区的最高硬度,进行材料冷裂纹的评定方法,叫间接评定法。 1)碳当量法将钢中合金元素(包括碳)的含量按其作用换算成碳的相当含量,叫该种材料的碳当量,常以符号C E表示。 国际焊接学会推荐的碳当量计算公式为:C E=C+Mn/6+(Ni+Cu)/15+(Cr+Mo+V)/5 (%) 碳当量C E值愈高,钢材淬硬倾向愈大,冷裂敏感性也愈大。经验指出,当C E>0.45%~0.55%时,就容易产生冷裂纹。 利用碳当量只能在一定范围内,对钢材概括地、相对地评价其冷裂敏感性,因为: ①碳当量公式是在某种试验情况下得到的,所以对钢材的适用范围有限。 ②碳当量计算值只表达了化学成分对冷裂倾向的影响。实际上,除了化学成分以外,冷却速度对冷裂的影响相当大,不同的冷却速度,可以得到不同的组织,因而抗裂性也不一样。确切地说,在刚性和扩散氢含量相同的情况下,应当主要是钢材的组织而不是碳当量确定冷裂敏感性。 ③影响金属组织从而影响冷裂敏感性的因素,除了化学成分和冷却速度外,还有焊接热循环中的最高加热温度和高温停留时间等参数。此外,钢材规定成分中没有表明微量合金元素和杂质元素的影响,也没有在碳当量计算公式中表示出来。 因此说,碳当量公式不能作为准确的评定指标。 (2)根部裂纹敏感性评定法这是专门评定根部裂纹的碳当量法,根据裂纹敏感指数P cM进行评定,计算公式为 P Cm=C+Si/30+Mn/20+Cu/20+Cr/20+Ni/60+Mo/15+V/10+5B (%) 钢的P cM值越低,热影响区的冷裂纹敏感性越低。 为了克服单纯用碳当量评定冷裂倾向的缺点,可以进一步把氢和板厚(代表应力)作为延迟裂纹的三因素综合一起考虑,得到冷裂纹敏感性指数P w,其计算公式为P w= P Cm+δ/600+H/60 (%)式中δ——板厚,mm;H一焊缝金属中扩散氢含量,mL/100g。 (3)热影响区最高硬度法(GB4675.5-84)试件的形状和尺寸,分别见图26—1和表26—1。(P266)试件的标准厚度为20mm。1号试件在室温下,2号试件在预热温度下进行焊接。焊后经12h,加工成如图26—2(P266)试样,在切点O及其两侧各7个以上的点作为硬度的测定点。把点中维氏硬度最大值与该钢材规定的热影响区最大允许值作比较,若超过允许值,则材料冷裂敏感倾向大。 这种方法比较简便,对于判断热影响区冷裂倾向有一定价值。但它只考虑了组织因素,没有涉及氢和
焊接性能
标准中的焊接性能 标准中将焊接性能分为:工艺焊接性能和使用焊接性能。 焊接性能:金属材料对焊接加工的适应性。主要指在一定的焊接工艺条件下,获得优质焊接接头的难易程度;或材料在限定施工条件下焊接成按设计要求的构件,并满足预先服役要求的能力。焊接性受材料(母材和填充金属)、焊接方法、构件类型及使用要求四个因素的影响。 工艺焊接性能:在某一焊接工艺条件下,得到优质焊接接头的能力。它不是金属本身固有的性能,而是根据采用的焊接方法和具体工艺措施进行的评定。它取决于:1)热源对被焊金属的热作用(与焊接方法和焊接参数有关);2)熔池金属的治金作用(与焊材有关);3)预热和后热等工艺措施 也就是说标准中所指的母材或填充金属的工艺焊接性能是指在所限定的母材或填充金属条件下,所采用焊接工艺(焊接方法、焊接参数、焊接材料和工艺措施等)是否能
得到优质焊接接头。 如果按照所拟定的焊接工艺施焊,能得到优质、无缺陷焊接接头,则该母材或填充金属的工艺焊接性能良好。承压设备要求评定工艺缺陷的内容主要是抗裂性能试验,对有色金属还有抗气孔试验。 工艺焊接性能试验分为直接法和间接法两种。 直接法主要有焊接冷裂纹试验、焊接热裂纹试验、再热裂纹试验、层状撕裂试验和焊接气孔敏感性试验等。 对于碳钢和低合金钢主要通过焊接冷裂纹试验评价其工艺焊接性能。试验方法有最高硬度法(HV10max)、斜Y型坡口法和插销法。 直接法,对于碳钢和低合金钢主要有碳当量法(Ceg)、裂纹敏感性指数(Pcm)等方法。使用焊接性能:整个焊接接头或整体结构满足技术条件规定使用性能要求。其中包括力学性能、缺口敏感性和耐蚀性能等。 也就是说标准中所指的母材或填充金属的使用焊接性能是指在所限定的母材或填