甲醇测定方法
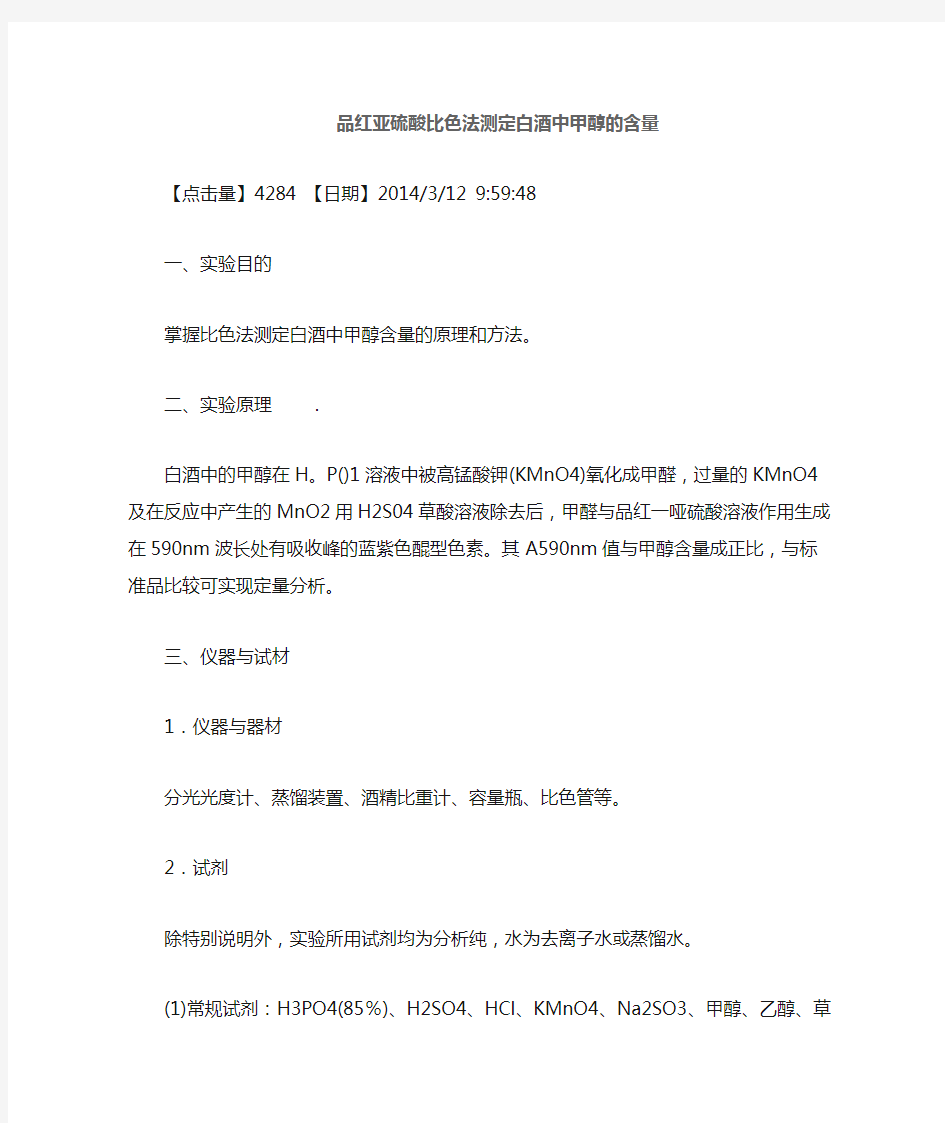

品红亚硫酸比色法测定白酒中甲醇的含量
【点击量】4284 【日期】2014/3/12 9:59:48
一、实验目的
掌握比色法测定白酒中甲醇含量的原理和方法。
二、实验原理.
白酒中的甲醇在H。P()1溶液中被高锰酸钾(KMn O4)氧化成甲醛,过量的KMnO4及在反应中产生的MnO2用H2S04草酸溶液除去后,甲醛与品红一哑硫酸溶液作用生成在590nm 波长处有吸收峰的蓝紫色醌型色素。其A590nm值与甲醇含量成正比,与标准品比较可实现定量分析。
三、仪器与试材
1.仪器与器材
分光光度计、蒸馏装置、酒精比重计、容量瓶、比色管等。
2.试剂
除特别说明外,实验所用试剂均为分析纯,水为去离子水或蒸馏水。
(1)常规试剂:H3PO4(85%)、H2SO4、HCl、KMn O4、Na2SO3、甲醇、乙醇、草酸、碱性品红(生化试剂)。
(2)常规溶液:H2SO4溶液(1+1,体积比)、Na2SO3溶液(1()(]童/L)、KMn O4一H3PO4溶液(将3g KMnO。加入15mL 85%H3PO4与70m L水的混合溶液中,溶解后,加水定容至100mL,储于棕色瓶)、H2SO4一草酸溶液(将5g无水草酸以H2SO4溶液溶解并定容至100mL)。
(3)品红一业硫酸(H2SO3)溶液:将0.1g碱性品红研细后,加入60mL 80℃的水,边加水边研磨使其溶解,过滤于100tnL容量瓶中,冷却后加10mI。Na2SO3溶液和1mL HCl,加水至刻度,混匀后,静置过夜。如果溶液有颜色,可加少量活性炭搅拌后过滤,储于棕色瓶中,避光保存。
(4)甲醇标准溶液(10mg/mL):取1.000g甲醇置于100mL容量瓶中,加水稀释至刻度,于4℃保存。
(5)甲醇标准使用液(0.50mg/mL):吸取10.0mL甲醇标准溶液,置于100mI。容量瓶中,加水稀释至刻度。再取25.0mL稀释液置于50mL容量瓶中,加水至刻度。’
(6)无甲醇的乙醇溶液:取0.5mI。乙醇溶液(95%),加水至5mL,加2m L KMnO4一H3PO4溶液,混匀,放置10min。加2mI。H2SO4一草酸溶液,混匀后,再加5mL品红一亚硫酸溶液,混匀,于25℃静置O.5h。检查,不应显色。如果显色,表明含有甲醇,应去除,具体方法见注意事项。
3.实验材料
酒精度分别为30度、40度、50度和60度的白酒,各250mI。。
四、实验步骤
1.标准曲线的绘制(1)吸取0、0.10mL、0.20mI.、0.40mL、0.60mL、0.80mL、1.00mL 甲醇标准使用液(相当于0、0.05mg、0.10mg、0.20mg、0.30nlg、0.40mg、0.50mg 甲醇),分别置于25m L具塞比色管中。
(2)以无甲醇的乙醇溶液稀释至1.0mL,加水至5mL,加2mL KMnO4-H3PO4溶液,混匀,放置10min。
(3)加2m L H2SO4一草酸溶液,混匀后,再加5mL品红一亚硫酸溶液,混匀,于25℃静置0.5h。
(4)用2cm比色皿,以甲醇含量为O的比色管中的溶液调零,于波长590nrn处测定
A590nm值。
(5)以A590nm为横坐标,甲醇浓度为纵坐标,绘制标准曲线。
2.样品测定
(1)分别取酒精度为30度、40度、50度和60度的白酒样品各1.0mL、0.8mL、0.6m L 和0.5m L,置于25mL具塞比色管中。
(2)按“标准曲线的绘制”中(2)~(4)进行操作,分别测定A590nm
(3)根据A590nm,从标准曲线上查找对应的甲醇量。
3.计算
按下式计算样品中甲醇的含量:
X=(m/V×1000)×100
式中,X为样品中甲醇的含量,g/100mL;m为从标准曲线上查得的甲醇质量,mg;V为样品的体积,mL。
五、注意事项
1.本实验方法甲醇的最低检出量为0.02g/100mL
2.品红亚硫酸溶液呈红色时应重新配制,新配制的品红亚硫酸溶液需在4℃冰箱中放置
24~48h后再用较好。
3.白酒中醛类物质,以及除乙醇以外的其他醇类物质经KMn O4氧化后产生的醛类物质(如丙醛等),也可以与品红一亚硫酸作用显色,但是在H2SO4酸性溶液中容易褪色,只有甲醛与品红一亚硫酸形成的有色物质可以持久不褪色,所以,加入品红一砸硫酸溶液后一定要放置0.5h以上,否则测定结果会偏高,或出现假阳性。
4.酒样和标准溶液中的乙醇浓度对比色有一定的影响,故样品与标准管中乙醇含量要大致相等。
5.对于有颜色或浑浊的蒸馏酒或配制酒,应先蒸馏后,再进行甲醇的测定。
6.乙醇中甲醇的去除方法:取300m L乙醇溶液(95%),加KMnO4少许,蒸馏,收集馏出液。在馏出液中加入1g AgNO3(以少量水先溶解)和1.5g Na OH(以少量水先溶解),摇匀,取上清液蒸馏,弃去最初的50mL馏出液,收集中间约200mL馏出液,陔馏出液不含甲醇。用酒精比重计测定酒精度,加水稀释成60%乙醇溶液。
甲醇合成与精制
甲醇生产---甲醇合成与精制 甲醇合成与精制 甲醇是极为重要的有机化工原料和清洁液体燃料,是碳一化工的基础产品。合成气的主要成分是CO和H2,它们在催化剂作用下可制得甲醇。在石油资源紧缺以及清洁能源、环保需求的情况下,以煤为原料生产甲醇,有望成为实现煤的清洁利用,弥补石油能源不足的途径。一、甲醇有哪些物理性质和化学性质?由性质进而掌握甲醇分析检测及安全环保的相关知识。 1、物理性质:甲醇是最简单的饱和一元醇,俗称“木精”、“木醇”,其分子式为CH3OH,分子量为32.04。 常温常压下,纯甲醇是无色透明、易燃、极易挥发且略带醇香味、刺激性气味的有毒液体。甲醇能和水以任意比互溶,但不形成共沸物,能和多数常用的有机溶剂(乙醇、乙醚、丙酮、苯等)混溶,并形成恒沸点混合物。甲醇能和一些盐如CaCl2、MgCl2等形成结晶化合物,称为结晶醇,如CaCl2、CH3OH、MgCl2、6CH3OH,和盐的结晶水合物类似。 2、化学性质:甲醇不具酸性,也不具碱性,对酚酞和石蕊均呈中性。 甲醇有很强的毒性,口服5~10ml可以引起严重中毒,10ml以上造成失明,30ml以上可致人死亡。甲醇属神经和血液毒物,它可以通过消化道、呼吸道和皮肤等途径进入人体,对中枢神经系统有麻醉作用;对视神经和视网膜有特殊选择作用,引起病变;可导致代谢性酸中毒,故空气中甲醇蒸汽的最高允许浓度为操作区5mg/m3,居民区0.5 mg/m3。甲醇在常温下无腐蚀性,但对于铅、铝例外。 3、甲醇定性检测法:检测试剂为浓硫酸和间苯二酚溶液(5克/升)。检测时将一小段表面被氧化的细铜丝投入约6毫升含甲醇的试样中,间隔一段时间,将此溶液缓缓倒入浓硫酸之中,会出现分层现象,再滴加间苯二酚溶液2滴,在和浓硫酸的分界面之间会出现玫瑰红色,这就证明有甲醇存在。 二、甲醇的主要用途: 甲醇是一种重要基本有机化工原料和溶剂,在世界上的消费量仅次于乙烯、丙稀和苯。甲醇可用于生产甲醛、甲酸甲酯、香精、染料、医药、火药、防冻剂、农药和合成树脂等;也可以替代石油化工原料,用来制取烯烃(MTP、MTO)和制氢(MTH);还广泛用于合成各种重要
_管壳外冷-绝热复合式甲醇合成反应器的应用
2009年第28卷增刊CHEMICAL INDUSTRY AND ENGINEERING PROGRESS ·419· 化工进展 管壳外冷-绝热复合式甲醇合成反应器的应用 应卫勇,张海涛,马宏方,房鼎业 (华东理工大学化工学院,上海 200237) 摘要:由煤制合成气经合成甲醇制燃料和化工产品的技术路线是煤洁净高效利用的方向之一。根据甲醇合成反应的特点,将管壳外冷-绝热复合式固定床催化反应器应用于甲醇生产中,单塔45万吨/年甲醇合成反应器已设计,单塔30~35万吨/年甲醇合成反应器已投入使用。双塔并联50万吨/年甲醇合成反应技术已经投入使用,工业生产情况表明:甲醇合成反应器结构合理,催化剂装卸方便,催化床温度调节简单,床层热点至出口温差小,回收高位热能、副产蒸汽。正在开展“十一五”国家科技支撑计划课题180万吨/年甲醇合成反应器的研究。 关键词:甲醇合成;反应器;工程应用 我国的能源特点是“少油、有气、多煤”,以煤为主。以煤为原料制合成气合成甲醇,甲醇可作为醇醚燃料,可用于生产系列化工产品,特别是用于生产甲醛、乙酸、乙烯、丙烯。因此,以煤为原料经甲醇制燃料、化工产品的技术路线是煤洁净利用、多联产的有效途径[1]。 甲醇合成反应器是甲醇生产的关键设备。华东理工大学30年来一直致力于甲醇反应器的研制开发,先后承担了国家科技攻关课题“低压甲醇合成反应器”和科技支撑计划课题“气冷-水冷串联式甲醇合成反应器”等,形成了用于甲醇合成的催化反应器的系列专利。 工业生产情况表明:华东理工大学开发的甲醇合成系列反应器结构合理,催化剂装卸方便;催化床温度调节简单,床层温度平稳;催化剂使用寿命长,可达3年;回收高位能热量,副产蒸汽1.1吨/吨甲醇;甲醇产品质量好。 2005~2007年间,根据已收到的效益证明,6家企业生产甲醇271.90万吨;新增产值860 552万元;新增利润117 117万元,新增税收960 33万元,取得了巨大的经济效益。甲醇合成反应器国产化,提高了我国甲醇生产技术水平。在上海研究开发的甲醇合成反应器技术用于全国,尤其是用于西部地区的开发,更具有显著的社会效益。 从2008年以来,华东理工大学继续将以管壳外冷-绝热复合式固定床催化反应器为核心的双塔并联式甲醇合成工艺应用于甲醇生产中。2008年4月河南永煤集团龙宇煤化工一期年产50万吨甲醇项目顺利投产。 1 2008年应用情况 2008年前,管壳外冷-绝热复合型甲醇合成反应器已经转让给二十多个企业实施:包括兖矿鲁化(100 kt/a)、华鲁恒升(200 kt/a)、浙江巨化(100 kt/a)、兖矿国泰(240 kt/a)、兖矿国宏(500 kt/a)、兖矿国际(200 kt/a)、山西丹峰(100 kt/a)、新疆克拉玛依(200 kt/a)、南京惠生(300 kt/a)、宁夏煤业(250 kt/a)、河南永城(500 kt/a)、河南平安(200 kt/a)、甘肃牛家峡(100 kt/a)、安徽临淮(200 kt/a)、陕西神木(400 kt/a)、山东凤凰(360 kt/a)、哈尔滨气化(300 kt/a)、新疆天富(200 kt/a)、江苏索普(540 kt/a)、宁波万华(200 kt/a)等。 2008年,管壳外冷-绝热复合型甲醇合成反应器在以下单位得到应用。 企业甲醇规模/kt·a-1工艺路线投产运行兰州蓝星化工有限公司200 水煤浆气化、低温甲醇洗净化、低压合成、三塔精馏设备制造综能协鑫煤化工有限公司300 U-Gas煤气化、低温甲醇洗净化、低压合成、三塔精馏详细设计久泰能源科技有限公司600 固定床制气、NHD净化、低压合成、三塔精馏设备安装山西省焦炭集团200 以焦炉气为原料气,转化、低压合成、三塔精馏详细设计延长石油集团兴化300 多元料浆煤气化、低温甲醇洗净化、低压合成、三塔精馏设备制造重庆万盛300 水煤浆气化、低温甲醇洗净化、低压合成、三塔精馏设备制造新能凤凰能源有限公司360 水煤浆气化、低温甲醇洗净化、低压合成、三塔精馏设备制造云天化股份有限公司260 水煤浆气化、低温甲醇洗净化、低压合成、三塔精馏详细设计
合成气制甲醇(精品)
合成气制甲醇(精品) 合成气制甲醇( 合成气可以由煤、焦炉煤气、天然气等生产) 一、甲醇合成工艺技术 合成甲醇工艺技术概况: 自从1923年德国BASF公司首次用一氧化碳在高温下用锌铬催化剂实现了甲醇 合成工业化之后,甲醇的工业化合成便得以迅速发展。当前,合成法甲醇生产几乎 成为目前世界上生产甲醇的唯一方法。半个多世纪以来,随着甲醇工业的迅速发 展,合成甲醇的技术也得以迅速改进。目前世界上合成甲醇的方法主要有以下几种: 1、高压法(19.6~29.4 MPa) 这是最初生产甲醇的方法,采用锌铬催化剂,反应温度为360~400?,压力 19.6~29.4Mpa。随着脱硫技术的发展,高压法也在逐步采用活性高的铜系催化剂, 以改善合成条件,达到提高效率和增产甲醇的效果。高压法虽然有70多年的历 史,但是,由于原料及动力消耗大,反应温度高,投资大,成本高等问题,其发展 长期以来处于停滞状态。 2、低压法(5.0~8.0 MPa) 这是20世纪60年代后期发展起来的甲醇合成技术。低压法基于高活性的铜 系催化剂。铜系催化剂活性明显高于锌铬催化剂,反应温度低(240~270?),在较低 的压力下获得较高的甲醇收率,而且选择性好,减少了副作用,改善了甲醇质量, 降低了原材料的消耗。此外,由于压力低,不仅动力消耗比高压法降低很多,而且 工艺设备的制造也比高压法容易,投资得以降低,总之低压法比高压法有显著的优 越性。 3、中压法(9.8~12.0 MPa)
随着甲醇单系列规模的大型化(目前已有日产2000吨的装置甚至更大单系列的装置),如采用低压法,势必导致工艺管道和设备非常庞大,因此在低压法的基础上,适当提高合成压力,即成为中压法。中压法仍采用与低压法相同的铜系催化剂,反应温度也与低压法相同,因此它具有与低压法相似的优点,但由于提高了合成压力,相应的动力消耗略有增加。目前,世界上新建或扩建的甲醇装置几乎都采用低压法或中压法,其中尤以低压法为最多。英国I.C.I公司和德国Lurgi公司是低压甲醇合成技术的代表,这两种低压法的差别主要在甲醇合成反应器及反应热回收的形式有所不同。目前世界上合成甲醇主要采用低压法工艺技术,它是大型甲醇装置的发展主流。甲醇合成系统包括合成气压缩(等压合成除外)、甲醇合成热量回收、甲醇精馏等工序,其核心设备是甲醇合成塔。有多种形式的合成塔在工业化装置中应用,经实际验证都是成熟可靠的。但在选择中要精心比较。二、甲醇精制 甲醇精制目前工业上采用的有两塔流程和三塔流程,两塔流程已能生产优质的工业品甲醇,但从节能降耗角度出发,选择三塔流程是较好的。三塔流程将以往的主精馏塔分为加压精馏塔和常压精馏塔,将加压精馏塔塔顶出来的甲醇蒸汽作为常压精馏塔的热源,降低了蒸汽消耗。通常情况下可降低能耗30%,但投资略有增加试析甲醇行业未来发展方向 甲醇是一种重要的有机化工原料,应用广泛,可以用来生产甲醛、合成橡胶、甲胺、对苯二甲酸二甲脂、甲基丙烯酸甲脂、氯甲烷、醋酸、甲基叔丁基醚等一系列有机化工产品,而且还可以加入汽油掺烧或代替汽油作为动力燃料以及用来合成甲醇蛋白。随着当今世界石油资源的日益减少和甲醇单位成本的降低,用甲醇作为新的石化原料来源已经成为一种趋势。尽管目前全球甲醇生产能力相对过剩,并且不排除由于某种原因而引起甲醇市场的波动,但是对于有着丰富的煤、石油、天然
合成气制备甲醇原理与工艺
合成气制备甲醇原理与工艺 简要概述 班级:xxxxxxxxxxxxxxxxxxxxx 专业:化学工程与工艺 姓名:xxxxx 学号:201473020108 指导教师:xxxxx
一、甲醇的认识 1.物理性质 无色透明液体,易挥发,略带醇香气味;易吸收水分、CO2和H2S,与水无限互溶;溶解性能优于乙醇;不能与脂肪烃互溶,能溶解多种无机盐磺化钠、氯化钙、最简单的饱和脂肪醇。 2.化学性质 3.甲醇的用途 (1)有机化工原料 甲醇是仅次于三烯和三苯的重要基础有机化工原料 (2)有机燃料 (1)、甲醇汽油混合燃料;(2)、合成醇燃料;(3)、与异丁烯合成甲基叔丁基醚(MTBE)、高辛烷值无铅汽油添加剂;(4)、与甲基叔戊基醚(TAME)合成汽油含氧添加剂
4.甲醇的生产原料 甲醇合成的原料气成分主要是CO 、 CO2、 H2 及少量的N2 和CH4。主要有煤炭、焦炭、天然气、重油、石脑油、焦炉煤气、乙炔尾气等。 天然气是生产甲醇、合成氨的清洁原料,具有投资少、能耗低、污染小等优势,世界甲醇生产有90%以上是以天然气为原料,煤仅占 2%。 二、合成气制甲醇的原理 1.合成气的制备 a.煤与空气中的氧气在煤气化炉内制得高 CO 含量的粗煤气; b.经高温变换将 CO 变换为 H2 来实现甲醇合成时所需的氢碳比; c.经净化工序将多余的 CO2 和硫化物脱除后即是甲醇合成气。 说明: 由于煤制甲醇碳多氢少,必需从合成池的放气中回收氢来降低煤耗和能耗,回收的氢气与净化后的合成气配得生产甲醇所需的合成气, 即( H2-CO2) /( CO+CO2)=2.00~2.05。 2.反应机理 主反应 OH CH H CO 322→+ △H 298=-90.8kJ/mol CO 2 存在时 O H OH CH H CO 23222+→+ △H 298=-49.5kJ/mol 副反应 O H OCH CH H CO 233242+→+ O H CH H CO 2423+→+ O H OH H C H CO 2942384+→+ O H CO H CO 222+→+ 增大压力、低温有利于反应进行,但同时也有利于副反应进行,故通过加入催化剂,提高反应的选择性,抑制副反应的发生。 3. 影响合成气制甲醇的主要因素 (1)合成甲醇的工业催化剂
甲醇合成反应器概述
甲醇合成反应器概述 现有的工业化甲醇合成工艺基本上是气相合成法。从上世纪60年代至今,除了在反应器的放大催化剂的研究方面有些进展外。其合成工艺基本上没有大的突破。鉴于气相合成存在的一系列问题,从上世纪70年代人们把甲醇合成工艺研究开发重点转移到液相合成法,相初步实现了工业化的生产。进入上世纪90年代后,我国也将开发高效节能的合成甲醇工艺和装置列为技术开发的重点。 甲醇合成反应器是甲醇合成生产的心脏设备。设计合理的甲醇合成塔应做到催化剂床的温度易于控制,调节灵活,合成反应的转化率高,催化剂生产强度大,能从较高位能回收反应热,床层中气体分布均匀,低压降。在结构上要求简单紧凑,高压空间利用率高,高压容器及内件无泄露,催化剂装卸方便。在材料上要求具有抗羰基化物的生成及抗氢脆的能力。在制造、维修、运输、安装上要求方便。 1.现有的有工业化的甲醇合成反应器 (1)ICI冷激型甲醇合成塔 ICI冷激型甲醇合成塔是英国ICI公司在1966年研制成功的。它首次采用了低压法合成甲醇,合成压力为5 MPa,这是甲醇生产工艺上的一次重大变革。采用固定床4段冷激式绝热轴流动反应器,通过特殊设计的菱形分布系统将冷激气喷人床层中间带走热量,床层多段连续,压降为0.5-0.6 MPa。反应热预热锅炉水。该反应器适于大型化,易于安装维修。上世纪80年代ICI公司又开发出一种新型轴.径向流动的固定床反应器,其直径、壁厚明显减少.操作简单。已有31个生产能力约1 400 t/d的这种装置运行。 ICI冷激型合成反应器的主要结构为:①塔体。为单层全焊结构,不分内件、外件,故简体为热壁容器,要求材料抗氧蚀能力强,抗张强度高,焊接性好。②气体喷头。为4层不锈钢的圆锥体组焊而成,固定于塔顶气体入口处,使气体均匀分布于塔内。这种喷头可以防止气流冲击催化床而损坏催化剂。③菱形分布器。菱形分布器埋于催化床中,并在催化床的不同高度平面上各安装1组,全塔共装3组,它使冷激气和反应气体均匀混合,以调节催化床层的温度,是塔内最关键的部件。这样结构的合成塔,装卸催化剂很方便,3 h可卸完30 t的催化剂,装催化剂需10 h可以完成。 (2)Lurgi管壳型甲醇合成塔 Lurgi型甲醇合成塔是德国Lurgi公司研制的一种管束型副产蒸汽合成塔。操作压力为5MPR,温度为250℃。Lurgi合成塔既是反应器又是废热锅炉。合成塔内部类似一般的列管式换热器,列管内装催化剂,管外为沸腾水。甲醇合成反应放出的热很快被沸水移走。合成塔壳程的锅炉水是自然循环的,这样通过控制沸腾水的蒸汽压力,可以保持恒定的反应温度,变化0.l MPa相当于l 5"C。这种合成塔温度几乎是恒定的,有效地抑制了副反应,延长了催化剂的使用寿命。但该合成塔结构复杂,装卸催化剂不方便。 (3)TEC新型反应器 多年来甲醇合成反应器的设计基本上是ICI冷激式和Lurgi列管式,直到进入上世纪90年代以后,日本TEC公司才在此方面向前迈进一步。 该公司开发的MRF—Z新型反应器的基本结构是反应器为圆筒状,有上下两
甲醇生产工艺原理
一氧化碳加氢为多方向反应,随反应条件及所用催化剂的不同,可生成醇、烃、醚等产物,因而在甲醇合成过程中可能发生以下反应: ●主反应:CO+H2≒CH3OH+Q CO2+3 H2≒CH3OH+H2O+Q ●副反应:CO+3H2≒CH4+H2O+Q 2CO+4H2≒C2H5OH(乙醇)+H2O+Q 2CO+4H2≒CH3OCH3(甲醚)+H2O+Q 一、甲醇合成反应影响因素有哪些? 1、温度 2、压力 3、空速 4、惰性气 5、CO2含量:CO2也能参加合成甲醇的反应,但对锌铬系催化剂,对于铜系催化剂,CO2的作用比较复杂,即有动力学方面的作用,还可能具有化学助剂的作用,归纳起来,其有利的方面为: 1)含有一定量的CO2可促进甲醇的提高 2)提高催化剂的选择性,可降低醚类等副反应的发生 3)可更有利于调节温度,防止超温,延长催化剂使用寿命 4)防止催化剂结炭 其不利方面:
1)与CO合成甲醇相比,每生成1kg甲醇多消耗0.7m3的H2 2)使粗醇中水含量增加,甲醇浓度降低 总之,在选择操作条件时,应权衡CO2作用的利弊。通常,在使用初期,催化剂活性较好时,应适当提高原料气中CO2的浓度使合成甲醇反应不致于过分剧烈,以得于床层温度的控制;在使用后期,可适当降低原料气中的CO2浓度,促进合成甲醇反应的进行,控制与稳定床层温度。 二、铜基甲醇催化剂还原方法有几种,优缺点? 铜基甲醇催化剂掺入使用前,必须用氢小心还原使其活化。其还原过程是一个强放热反应,每消耗1%的H2,引起绝热漫长约28℃,反应式如下: CuO+H2=Cu+86.7kj/mol 在工作业上,可采用低氢和高氢还原两种方法。 低氢还原特点:床层温度便于控制,有利于提高催化剂的活性,缺点:时间较长(80-100小时)。 高氢还原特点:还原时间较短40小时,缺点:操作必须十分细心严格,稍有不慎,将引起催化剂床层剧烈超温,导致催化剂失活报废。另外操作不当,催化剂强度易受到损害,造成催化剂部分粉化而引起床层压差大。有文献认为,在高浓度氢气下,容易发生深度还原,使CuO全部还原成金属铜而引起活性与选择性的下降。 三、何为醇净值?怎样进行估算?
甲醇合成工艺
甲醇合成工艺 当今甲醇的生产主要采用低压法和中压法这两种,很少采用高压法,目前高压法的发展已处于停滞的状态,主要以低压法为主。用中压法和低压法这两种工艺生产出来的甲醇约占世界甲醇总产量的一半以上。 1. 低压合成工艺(5.0- 8. 0MP a) 是20世纪50年代后期发展起来的一种甲醇合成技术。低压法主要采用CuO- ZnO- Al2 O3- V2O5 催化剂,其活性较高,能耗低,反应温度最佳,一般反应温度在(240- 265)℃,在压力较低的的条件下即可获得较高的甲醇产率。并且其选择性好,减少了很多副反应的发生,降低了原料的损耗,并且提高了甲醇的质量。除此之外,由于压力要求较高,可以有效的减少动力的消耗,使工艺设备的制造更加容易。这一方法被英国ICI公司在1966 年研究使用成功,从而打断了甲醇合成高压法的垄断制度。这一制度的应用,在很大程度上提高了甲醇的产量,为日后甲醇的高产带来了合适的方法。 2. 中压合成工艺(9.8- 12. 0MP a) 随着社会的不断发展,甲醇的需求越来越大,如果继续采用低压法就要改造工艺管道,使工艺管道变得更大,设备也就变得更大,这样就浪费了空间和成本,因此在低压的基础上适当的加大压力,即发展为中压法。中压法采用的催化剂和低压法的相 同,都为C uO- ZnO- Al2O3 - V2O5催化剂,因此反应温度与低压法大致相同,由于压力的提高使动能的消耗也增加了。齐鲁石化公司第二化肥厂引进了联邦德国公司的中压甲醇合成装置。使得该公司的日产量有了很大程度的提高。 3. 高压合成工艺(30- 32 MP a) 是比较原始的一种方法,采用ZnO- C r 2O3 催化剂,其活性远不如铜系催化剂,反应温度在(350- 400)℃。随着科学技术的发展,高压法也开始逐步采用活性相对较高的铜系催化剂,以改善合成的条件。高压法虽然存在了70 多年,但由于材质苛刻,投资高,能耗物高,反应温度高,且生成的粗甲醇中杂志含量较多不易提纯,所以其发展前景不可观,目前处于停滞状态。
甲醇合成原理方法与工艺
甲醇合成原理方法与工艺 图1煤制甲醇流程示意图 煤气经过脱硫、变换,酸性气体脱除等工序后,原料气中的硫化物含量小于0.1mg/m3。进入合成气压缩机,经压缩后的工艺气体进入合成塔,在催化剂作用下合成粗甲醇,并利用其反应热副产3.9MPa中压蒸汽,降温减压后饱和蒸汽送入低压蒸汽管网,同时将粗甲醇送至精馏系统。 一、甲醇合成反应机理 自CO加氢合成甲醇工业化以来,有关合成反应机理一直在不断探索和研究之中。早期认为合成甲醇是通过CO在催化剂表面吸附生成中间产物而合成的,即CO是合成甲醇的原料。但20世纪70年代以后,通过同位素示踪研究,证实合成甲醇中的原子来源于CO2,所以认为CO2是合成甲醇的起始原料。为此,分别提出了CO和CO2合成甲醇的机理反应。但时至今日,有关合成机理尚无定论,有待进一步研究。 为了阐明甲醇合成反应的模式,1987年朱炳辰等对我国C301型铜基催化剂,分别对仅含有CO或CO2或同时含有CO和CO2三种原料气进行了甲醇合成动力学实验测定,三种情况下均可生成甲
醇,试验说明:在一定条件下,CO和CO2均可在铜基催化剂表面加氢生成甲醇。因此基于化学吸附的CO连续加氢而生成甲醇的反应机理被人们普遍接受。 对甲醇合成而言,无论是锌铬催化剂还是铜基催化剂,其多相(非匀相)催化过程均按下列过程进行: ①扩散——气体自气相扩散到气体一催化剂界面; ②吸附——各种气体组分在催化剂活性表面上进行化学吸附; ③表面吸附——化学吸附的气体,按照不同的动力学假说进行反应形成产物; ④解析——反应产物的脱附; ⑤扩散——反应产物自气体一催化剂界面扩散到气相中去。 甲醇合成反应的速率,是上述五个过程中的每一个过程进行速率的总和,但全过程的速率取决于最慢步骤的完成速率。研究证实,过程①与⑤进行得非常迅速,过程②与④的进行速率较快,而过程③分子在催化剂活性界面的反应速率最慢,因此,整个反应过程的速率取决于表面反应的进行速率。 提高压力、升高温度均可使甲醇合成反应速率加快,但从热力学角度分析,由于CO、C02和H2合成甲醇的反应是强放热的体积 缩小反应,提高压力、降低温度有利于化学平衡向生成甲醇的方向移动,同时也有利于抑制副反应的进行。 二、甲醇合成的主要反应 (1)甲醇合成主要反应 CH3OH CO+2H CO2CH3OH+H2O 同时CO2和H2发生逆变换反应 CO 2CO+H2O
溶胶凝胶法的技术进展和展望
溶胶-凝胶法的技术进展和展 大连理工大学化工学院 摘要:溶胶-凝胶法是一种条件温和的材料制备方法, 文章简述了Sol-Gel 法的基本原理和主要步骤。研究了工艺过程的影响因素,总结溶胶-凝胶法的优缺点。结果表明,水的加入量、温度、醇盐的滴加速度、反应液的pH 都会影响溶胶-凝胶法的产品质量。溶胶-凝胶法可制得的材料主要有以下几大类型:单晶、纤维材料、涂层和薄膜材料、超细粉末材料及复合材料等,有很大的发展前景。 关键词:溶胶-凝胶法;原理;影响因素;应用; Abstract:Sol-gel method is a method for material preparation under mild condition .In this paper , basicprinciples of sol-gel method and the main step are briefly described .The paper studiedinfluence factor of process of sol-gel method and generalized its advantages anddisadvantages.Results showed the addition amount of water, the dropping-speed of alkoxide, the pH of reaction solution all affected on the product quality of sol-gel method. Sol-gel method could prepare some materials: single crystal, fiber material, coating, film material,superfine powder material. Sol-gel method had good development prospects. Key word:Sol-gel method;principles;influence factor;application; 1.引言 溶胶-凝胶法(Sol-Gel法, 简称S-G 法)就是以无机物或金属醇盐作前驱体, 在液相将这些原料均匀混合, 并进行水解、缩合化学反应, 在溶液中形成稳定的透明溶胶体系, 溶胶经陈化, 胶粒间缓慢聚合,形成三维空间网络结构的凝胶, 凝胶网络间充满了失去流动性的溶剂, 形成凝胶。凝胶经过干燥、烧结固化制备
甲醇合成的基础知识2
甲醇合成的基础知识 一、合成甲醇的化学反应: (1)主反应: CO+2H2=CH3OH+102.5kJ/mol CO2+3H2=CH3OH+H2O+Q kJ/mol (2)副反应: 2 CO+4H2=CH3OCH3+H2O+200.2 kJ/mol CO+3H2=CH4+H2O+115.6 kJ/mol 4CO+8H2=C4H9OH +3H2O+49.62 kJ/mol CO+H2=CO+H2O-42.9 kJ/mol nCO+2nH2=(CH2)n+nH2O+Q kJ/mol 二、一氧化碳与氢气合成甲醇反应热的计算: 一氧化碳与氢气合成甲醇是一个放热反应,在25℃时,反应热为90.8 kJ/mol。 一氧化碳和氢气合成甲醇是一个气相可逆反应,压力对反应起着重要作用,用气体分压表示的平衡常数可用下面公式表示: k p=p CH3OH /p CO·p H22 式中k p——甲醇的平衡常数 p CH3OH、p CO、p H2——分别表示甲醇、一氧化碳、氢气的平衡分压。 反应温度也是影响平衡的一个重要因素,下面公式用温度来表示合成甲醇的平衡常数: lgKa=3921/T-7.9711lg T+0.002499 T-2.953×10-7T2+10.20 式中Ka——用温度表示的平衡常数; T——反应温度,K。 四、温度对甲醇合成反应的影响: 甲醇的合成反应是一个可逆放热反应。从化学平衡考虑,随着温度的提高,甲醇平衡常数数值将为降低。但从反应速度的观点来看,提高反应温度,反应速度加快。因而,存在一个最佳温度范围。对不同的催化剂,使用温度范围是不同的。C307型合成甲醇
催化剂的操作温度:190~300 ℃,而最佳温度:210~260 ℃。 实际生产中,为保证催化剂有较长的使用寿命和尽量减少副反应,应在确保甲醇产量的前提下,根据催化剂的性能,尽可能在较低温度下操作,(在催化剂使用初期,反应温度宜维持较低的数值,随着使用时间增长,逐步提高反应温度)。另外,甲醇合成反应温度越高,则副反应增多,生成的粗甲醇中有机杂质等组分的含量也增多,给后期粗甲醇的精馏加工带来困难。 五、压力对甲醇合成反应的影响: 甲醇的合成反应是一个体积收缩的反应,增加压力,反应向生成甲醇的方向移动;从动力学考虑,增加压力,提高了反应物分压,加快了反应的进行;另外,提高压力也对抑制副反应,提高甲醇质量有利。所以,提高压力对反应是有利的。但是,压力也不宜过高,否则,不仅增加动力消耗,而且对设备和材料的要求也相应提高,投资费用增大. C307型合成甲醇催化剂的操作压力:3~15 MPa。 六、空速对甲醇合成反应的影响: 气体与催化剂接触时间的长短,通常以空速来表示,即单位时间内,每单位体积催化剂所通过的气体量。其单位是m3(标)/( m3催化剂·h),简写为h-1。 空速是调节甲醇合成塔温度及产醇量的重要手段。在甲醇生产中,气体一次通过合成塔仅能得到3%~6%的甲醇,新鲜气的甲醇合成率不高,因此,新鲜气必须循环使用。在一定条件下,空速增加,气体与催化剂接触时间减少,出塔气体中甲醇含量降低。但由于空速的增加,单位时间内通过催化剂的气体量增加,所以甲醇实际产量是增加的。当空速增大到一定范围时,甲醇产量的增加就不明显了。同时由于空速的增加,消耗的能量也随之加大,气体带走的热量也增加。当气体带走的热量大于反应热时,床层温度会难于维持。 甲醇合成的空速受到系统压力、气量、气体组成和催化剂性能等诸多因素影响。C307型合成甲醇催化剂的操作空速:4000~20000 h-1。 七、碳氢比的控制对甲醇合成反应的影响: 甲醇由一氧化碳、二氧化碳与氢反应生成,反应式如下: CO+2H2≒CH3OH CO2+3H2≒CH3OH+H2O 从反应式可以看出,氢与一氧化碳合成甲醇的物质的量比为2,与二氧化碳合成甲醇的物质的量比为3,当一氧化碳与二氧化碳都有时,对原料气中碳氢比(f或M值)有以下两种表达方式:
甲醇合成的工艺方法介绍
甲醇合成的工艺方法介绍 自1923年开始工业化生产以来,甲醇合成的原料路线经历了很大变化。20世纪50年代以前多以煤和焦碳为原料;50年代以后,以天然气为原料的甲醇生产流程被广泛应用;进入60 年代以来,以重油为原料的甲醇装置有所发展。对于我国,从资源背景来看,煤炭储量远大于石油、天然气储量,随着世界石油资源的紧缺、油价的上涨和我国大力发展煤炭洁净利用技术的背景下,在很长一段时间内煤是我国甲醇生产最重要的原料。下面简要介绍一下甲醇生产的各种方法。按生产原料不同可将甲醇合成方法分为合成气(CO+H2方法和其他原料方法。 一、合成气(CO+H2生产甲醇的方法 以一氧化碳和氢气为原料合成甲醇工艺过程有多种。其发展的历程与新催化剂的应用,以及净化技术的进展是分不开的。甲醇合成是可逆的强放热反应,受热力学和动力学控制,通常在单程反应器中,CO和CO2的单程转化率达不到100%,反应器出口气体中,甲醇含量仅为6~12%,未反应的CO、CO2和H2需与甲醇分离,然后被压缩到反应器中进入一步合成。为了保证反应器出口气体中有较高的甲醇含量,一般采用较高的反应压力。根据采用的压力不同可分为高压法、中压法和低压法三种方法。 1、高压法 即用一氧化碳和氢在高温(340~420℃高压(30.0~50.0MPa下使用锌-铬氧化物作催化剂合成甲醇。用此法生产甲醇已有八十多年的历史,这是八十年代以前世界各国生产甲醇的主要方法。但高压法生产压力过高、动力消耗大,设备复杂、产品质量较差。其工艺流程如图所示。 经压缩后的合成气在活性炭吸附器1中脱除五羰基碳后,同循环气一起送入管式反应器2中,在温度为350℃和压力为30.4MPa下,一氧化碳和氢气通过催化剂层反应生成粗甲醇。含粗甲醇的气体经冷却器冷却后,迅速送入粗甲醇分离器3中分离,未反应的一氧化碳与氢经压缩机压缩循环回管式反应器2。冷凝后的粗甲醇经粗
甲醇合成塔介绍
甲醇合成塔介绍 2011-09-01 16:17 【打印】【收藏】百川资讯更新时间:来源:甲醇合成塔关键字: 甲醇合成塔设计的关键技术之一就是要高效移走和利用甲醇合成反应所放出的巨大热量。摘要:甲醇合成塔设计的关键技术之一就是要高效移走和利用甲醇合成反应所放出的巨大热量。甲醇合成反应器根据反应热回收方式不同有许多不同的类型,下面将应用较广的几种合成器分别予以简单介绍。一、I.C.I反应器 英国ICI公司低压法甲醇合成塔采用多层冷激式绝热反应器,内设3-6层催化剂,催化剂用量较大,合成气大部分作为冷激气体由置于催化剂床层不同高度平行设立的菱形分布器喷入合成塔,另一部分合成气由顶部进入合成塔,反应后的热气体与冷激气体均匀混合以调节催化床层反应温度,并保证气体在催化床层横截面上均匀分布。反应最终气体的热量由废热锅炉产生低压蒸汽或用于加热锅炉给水回收。该法循环气量比较大,反应器内温度分布不均匀,呈锯齿形。 ICI冷激塔结构简单、用材省且要求不高、并易于大型化。单塔生产能力大。但由于催化剂床层各段为绝热反应,使催化剂床层温差较大,在压力为8.4MPa和12000h-1空速下,当出塔气甲醇浓度为4%时,一、二两段升温约50℃,反应副产物多,催化剂使用寿命较短,循环气压缩功耗大,用冷原料气喷入各段触媒之间以降低反应气温度。因此在降温的同时稀释了反应气中的甲醇含量,影响了触媒利用率,而且反应热只能在反应器出口设低压废锅回收低压蒸汽。为了防止触媒过热,采用较大的空速,出塔气中甲醇含量不到4%。最大规模3000t/d,全世界现有40多套。 二、德国林德Lurgi管壳式反应器 水冷型。图2Lurgi甲醇合成反应器是管壳式的结构。管内装催化剂,管外充满中压沸腾水进行换热。合成反应几乎是在等温条件下进行,反应器能除去有效的热量,可允许较高CO含量气体,采用低循环气流并限制最高反应温度,使反应等温进行,单程转化率高,杂质生成少,循环压缩功消耗低,而且合成反应热副产中压蒸汽,便于废热综合利用。可以看出Lurgi公司正是根据甲醇合成反应热大和现有铜基触媒耐热性差的特点而采用列管式反应器。管内装触媒,管间用循环沸水,用很大的换热面积来移去反应热,达到接近等温反应的目的,故其出塔气中甲醇含量和空时产率均比冷激塔高,触媒使用寿命也较长。其主要性能特点是:该塔反应时触媒层温差小,副产物低,需传热面大。但该反应器比I.C.I反应器结构复杂,上下管板处联结点和焊点多,制作困难,为防壳体和管板、反应管之间焊接热应力,对材料及制造方面的要求较高,投资高。反应器催化剂装填系数也不如I.C.I反应器大,只有30%,且装卸触媒不方便。塔径大,运输困难 Lurgi管壳式反应器已在国内不少甲醇厂使用,但在大型化甲醇装置中因结构复杂、反应管数较多、体积大,国内目前。单塔最大生产能力为1250吨/天。产量增大时,反应器直径过大,而且由于管数太多,反应管长度只能做到10米,因此在设计与制造时就有困难了。1 / 5 近年来又提出与冷管型串联的流程以适应大型化生产的需鲁奇公司曾提出两塔并联的流程,座套甲醇装置(约40两个塔),全世界现有29求,但是都还未工业化。最大规模3000t/d( /年。,总产能810万吨合成塔) MRF型反应器三、东洋公司(TEC)的反应器为多段间接冷却径向流动反应器,采用套管锅炉水强制循环冷却副产蒸气,MRF字分温度分布呈多段Z反应气体呈径向流过沿径向分布的多级冷却套管管外分布的触媒层,径向流动使气体通过床层的阻力降低;温度分布有所改善,从而有利于提高催化剂寿命;布,有催化剂在管外装填,反应器催化剂装填系数得到适当增大,多孔板可保证气体分布均匀;利于实现大型化,但其结构复杂,制造难度大。 米,反应器吨的产能,甲醇塔直径5MRF-Z型反应器达到日产5000据了解,TEC可用单台催化米,米,床高12按14万吨/年的反应器直径2.5管长22.4m,催化剂装填量为350m3。。工业业绩:
生产甲醇的工艺流程
生产甲醇的工艺流程 (一)生产工序 合成气合成甲醇的生产过程,不论采用怎样的原料和技术路线,大致可以分为以下几个工序 1.原料气的制备 合成甲醇,首先是制备原料氢和碳的氧化物。一般以含碳氢或含碳的资源如天然气、石油气、石脑油、重质油、煤和乙炔尾气等,用蒸汽转化或部分氧化加以转化,使其生成主要由氢、一氧化碳、二氧化碳组成的混合气体,甲醇合成气要求(H2-CO2)/(CO+CO2)=2.1左右。合成气中还含有未经转化的甲烷和少量氮,显然,甲烷和氮不参加甲醇合成反应,其含量越低越好,但这与制备原料气的方法有关;另外,根据原料不同,原料气中还可能含有少量有机和无机硫的化合物。 为了满足氢碳比例,如果原料气中氢碳不平衡,当氢多碳少时(如以甲烷为原料),则在制造原料气时,还要补碳,一般采用二氧化碳,与原料同时进入设备;反之,如果碳多,则在以后工序要脱去多余的碳(以CO2形式)。 2.净化 一是脱除对甲醇合成催化剂有毒害作用的杂质,如含硫的化合物。原料气中硫的含量即使降至1ppm,对铜系催化剂也有明显的毒害作用,因而缩短其使用寿命,对锌系催化剂也有一定的毒害。经过脱硫,要求进入合成塔气体中的硫含量降至小于0.2ppm。脱硫的方法一般有湿法和干法两种。脱硫工序在整个制甲醇工艺流程中的位置,要根据原料气的制备方法而定。如以管式炉蒸汽转化的方法,因硫对转化用镍催化剂也有严重的毒害作用,脱硫工序需设置在原料气设备之前;其它制原料气方法,则脱硫工序设置在后面。 二是调节原料气的组成,使氢碳比例达到前述甲醇合成的比例要求,其方法有两种。 (1)变换。如果原料气中一氧化碳含量过高(如水煤气、重质油部分氧化气),则采取蒸汽部分转换的方法,使其形成如下变化反应:CO+H2O==H2+CO2。这样增加了有效组分氢气,提高了系统中能的利用效率。若造成CO2多余,也比较容易脱除。 (2)脱碳。如果原料气中二氧化碳含量过多,使氢碳比例过小,可以采用脱碳方法除去部分二氧化碳。脱碳方法一般采用溶液吸收,有物理吸收和化学吸收两种方法。(如:低温甲醇洗)
合成气生产甲醇工艺流程
编号:No.20 课题:合成气生产甲醇工艺流程 授课内容:合成气制甲醇工艺流程 知识目标: ? 了解合成气制甲醇过程对原料的要求 ?掌握合成气制甲醇原则工艺流程 能力目标: ?分析和判断合成气组成对反应过程及产品的影响 ?对比高压法与低压法制甲醇的优缺点 思考与练习: ?合成气制甲醇工艺流程有哪些部分构成? ?对比高压法与低压法制甲醇的优缺点 ?合成气生产甲醇对原料有哪些要求?如何满足?
授课班级: 授课时间: 四、生产甲醇的工艺流程 (一)生产工序 合成气合成甲醇的生产过程,不论采用怎样的原料和技术路线,大致可以分为以下几个 工序,见图5-1。 图5-1 甲醇生产流程图 1.原料气的制备 合成甲醇,首先是制备原料氢和碳的氧化物。一般以含碳氢或含碳的资源如天然气、石 油气、石脑油、重质油、煤和乙炔尾气等,用蒸汽转化或部分氧化加以转化,使其生成主要由氢、一氧化碳、二氧化碳组成的混合气体,甲醇合成气要求(出—CO2)/(CO+CO2)=2.1 左右。合成气中还含有未经转化的甲烷和少量氮,显然,甲烷和氮不参加甲醇合成反应,其 含量越低越好,但这与制备原料气的方法有关;另外,根据原料不同,原料气中还可能含有 少量有机和无机硫的化合物。 为了满足氢碳比例,如果原料气中氢碳不平衡,当氢多碳少时(如以甲烷为原料),则 在制造原料气时,还要补碳,一般采用二氧化碳,与原料同时进入设备;反之,如果碳多,则在以后工序要脱去多余的碳(以CO2形式)。 2.净化 净化有两个方面: 一是脱除对甲醇合成催化剂有毒害作用的杂质,如含硫的化合物。原料气中硫的含量即 使降至1ppm,对铜系催化剂也有明显的毒害作用,因而缩短其使用寿命,对锌系催化剂也有一定的毒害。经过脱硫,要求进入合成塔气体中的硫含量降至小于0.2ppm。脱硫的方法 一般有湿法和干法两种。脱硫工序在整个制甲醇工艺流程中的位置,要根据原料气的制备方 法而定。如以管式炉蒸汽转化的方法,因硫对转化用镍催化剂也有严重的毒害作用,脱硫工
甲醇合成工段
甲醇合成工段 目前工业上几乎都是采用一氧化碳、二氧化碳加压催化氢化法合成甲醇。1. 工艺路线:典型的流程包括原料气制造、原料气净化、甲醇合成、粗甲醇精馏等工序。 煤与焦炭是制造甲醇粗原料气的主要固体燃料。用煤和焦炭制甲醇的工艺路线包括燃料的气化、气体的脱硫、变换、脱碳及甲醇合成与精制。用蒸汽与氧气(或空气、富氧空气)对煤、焦炭进行热加工称为固体燃料气化,气化所得可燃性气体通称煤气是制造甲醇的初始原料气,气化的主要设备是煤气发生炉,按煤在炉中的运动方式,气化方法可分为固定床气化法、流化床气化法和气流床气化法。国内用煤与焦炭制甲醇的煤气化——般都沿用固定床间歇气化法,煤气炉沿用UCJ炉。在国外对于煤的气化,目前已工业化的煤气化炉有柯柏斯-托切克(Koppers-Totzek)、鲁奇(Lurge)及温克勒(Winkler)三种。还有第二、第三代煤气化炉的炉型主要有德士古(Texaco)及谢尔-柯柏斯(Shell-Koppers)等。用煤和焦炭制得的粗原料气组分中氢碳比太低,故在气体脱硫后要经过变换工序。使过量的一氧化碳变换为氢气和二氧化碳,再经脱碳工序将过量的二氧化碳除去。原料气经过压缩、甲醇合成与精馏精制后制得甲醇。 甲醇生产中所使用的多种催化剂,如天然气与石脑油蒸气转化催化剂、甲醇合成催化剂都易受硫化物毒害而失去活性,必须将硫化物除净。气体脱硫方法可分为两类,一类是干法脱硫,一类是湿法脱硫。干法脱硫设备简单,但由于反应速率较慢,设备比较庞大。湿法脱硫可分为物理吸收法、化学吸收法与直接氧化法三类。 粗甲醇中存在水分、高级醇、醚、酮等杂质,需要精制。精制过程包括精馏与化学处理。化学处理主要用碱破坏在精馏过程中难以分离的杂质,并调节pH。精馏主要是除去易挥发组分,如二甲醚、以及难以挥发的组分,如乙醇高级醇、水等。
甲醇合成反应器维护检修规程
甲醇合成反应器维护检修规程 总则 1.1 适用范围 本规程适用于甲醇合成反应器R2001的检修和维护。 1.2 设备概述 甲醇合成反应器R2001属于固定床气-固相列管式催化反应器,它类似于一个副产蒸汽的立式管壳式固定管板列管式换热器,管板与管箱壳体之间直接焊接,无法兰连接。上下封头采用半球型封头,上封头合成气入口设置气体分布器,换热管内及上管板的上部装填铜基催化剂,在催化剂上部铺丝网后装填耐火球;下管板下面装填耐火球,耐火球与封头上反应气出口之间装有制成件。合成反应器壳侧筒体上部接有蒸汽出口管和沸水出口管,下部接有进水管。 1.2 技术参数 容器类别三 参数名称壳程管程 工作压力 MPa 4.0 5.4 设计压力 MPa 5.0 6.0 工作温度进/出℃250/250 200/265 设计温度℃270 275 壁温℃249 255.9 介质水,水蒸汽H2,CO,CO2,CH4,N2 介质特性-易燃易爆,中度危害 主要受压元件材料20MnMoNi55 筒体:20MnMoNi55 封头:15CrMoR 换热管:SAF2205 腐蚀裕量 mm 3 3 焊接接头系数 1 1 保温材料与保温厚度 mm 复合硅酸盐厚60 换热管规格与数量φ44×2×7500 4004根 管子与管板联接方式强度焊+贴胀 热处理消除应力热处理 设备最大质量 kg 437000 最大吊装质量 kg 180000 1.3 设备完好标准 1.3.1 零部件 零部件完整齐全,质量符合要求。 壳体、换热管无明显冲刷、腐蚀缺陷。 设备筒体垂直度偏差为0.5/1000。 基础完好,地脚螺栓紧固、齐全。 管道上各阀门开关灵活、有效;管道、管件支架等安装合理,牢固完整,标志分明。 热电偶灵敏、准确、可靠。 防腐、防冻设施完整、有效。
柠檬酸溶胶凝胶法制备复合氧化物的研究
柠檬酸溶胶凝胶法制备复合氧化物的研究 摘要:柠檬酸溶胶凝胶法具有操作简单,成本低,产物纯度高,粒度细等优点,广泛应用在氧化物制备领域。本文就制备条件进行了讨论,包括柠檬酸用量、溶液pH值,凝胶化及陈化,并就柠檬酸溶胶凝胶法的反应机理进行了阐述。当前研究认为这些制备条件对最张取得的氧化物粉体的物性参数有着较大的影响。 关键词:柠檬酸溶胶凝胶法复合氧化物制备条件成胶机理 在催化研究领域,单一氧化物通常具有一些较好的物化性能,可以作为载体或是直接应用作催化剂。但是随着人们对催化性能要求的提高及绿色化学低碳经济的兴起,这些单一氧化物逐渐无法满足工业生产对其性能的要求。研究人员将不同的氧化物复合,从而获得兼具两种材料优点的复合或掺杂材料。[1]这种氧化物的复合在催化、电化学中都有着重要作用。然而复合方式的不同对复合的效果影响较大。 溶胶凝胶法是现在常用的氧化物复合掺杂方法。整个制备过程经历溶液、溶胶、凝胶、干凝胶、焙烧。由溶胶凝胶法制备的粒子纯度高粒度细、可精确调控组成,方便对材料的复合或掺杂,反应条件温和易于操作控制,一般制得的氧化物都具有较大的比表面积[2]。该方法经历了传统胶体、无机聚合物胶体、络合法制胶这三个过程。传统方法需要找到合适的沉淀剂。当制备的离子各类较多时,很难寻到合适的沉淀剂。无机络合法常使用金属醇盐为原料。但金属醇盐有易燃、有毒、不易长入保存、成本较高等特点。近些年来发展的柠檬酸-溶胶凝胶法属于无机聚合物法。不仅可以在较低的温度下,取得尺寸均匀,粒度在微米甚至纳米级别的氧化物,而且保留了制备温度温和、操作方法简易的优势。然而柠檬酸凝胶溶胶法作为一种新兴方法,在制备条件和操作方法上仍有许多地方值得探讨。 一、制备条件及机理分析 1.柠檬酸用量 柠檬酸作为络合剂,对胶体的稳定性具有决定性的作用。用量过少,将会导致形成的胶体不稳定,极可能在放置陈化过程中出现沉淀现在,导致实验失败[3-5]。不同的文献中均采用放置检验的方法,将溶胶放置足够长的时间,并观察,以刚好不出现金属盐析出为柠檬酸的最少使用量。而不同的金属盐,其对应的最小使用量,从1:0.5到1:3不等。在氧化物焙烧条件相同的情况下,增加柠檬酸的用量可以得到更粒度更细分散度更好的氧化物。但李意峰认为过量的催化剂会残留在干凝胶中,致使焙烧过程中柠檬酸燃烧不充分,产物结晶下降[4]。 2.溶液pH