常压炉和鲁奇炉对比稿
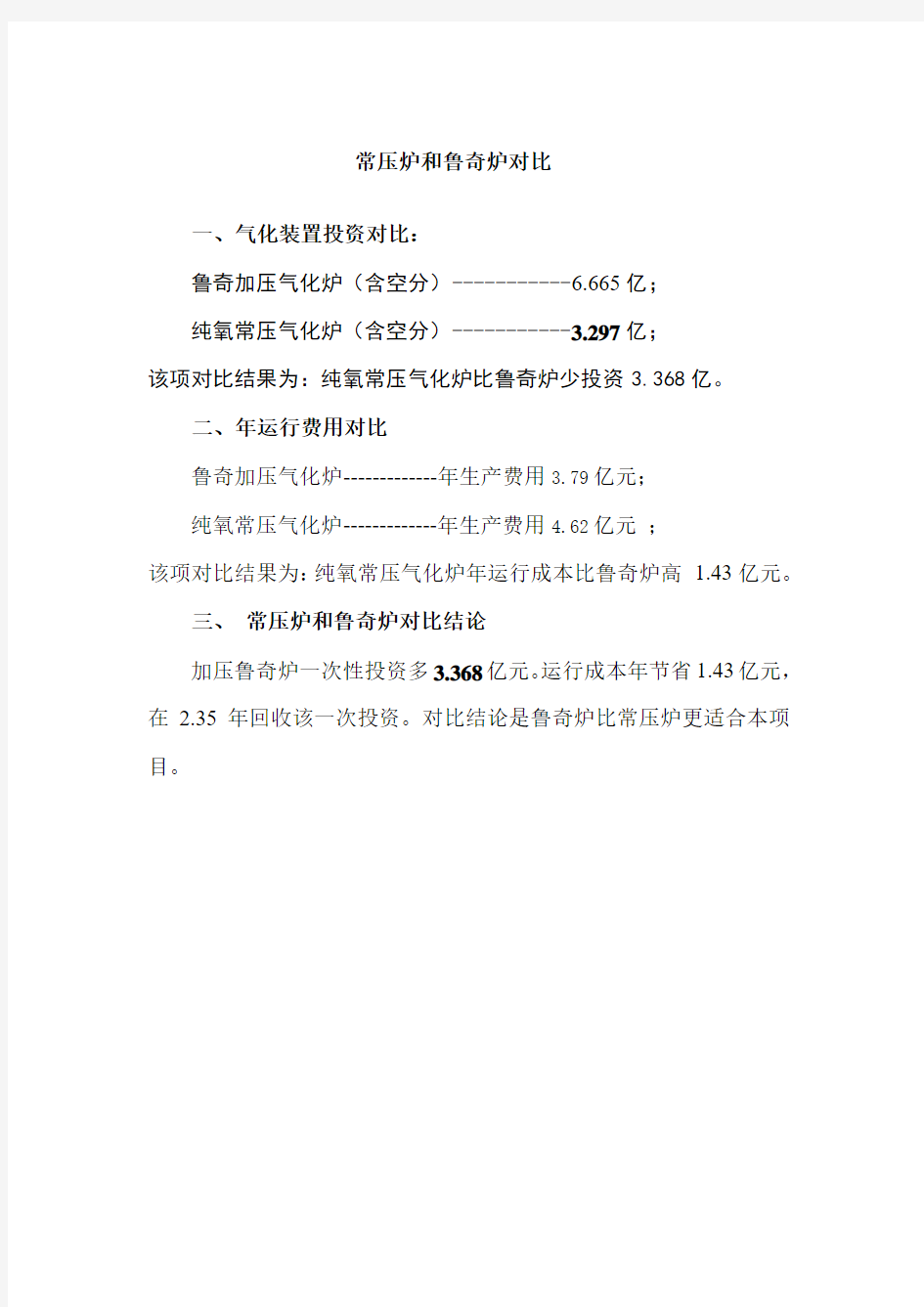

常压炉和鲁奇炉对比
一、气化装置投资对比:
鲁奇加压气化炉(含空分)-----------6.665亿;
纯氧常压气化炉(含空分)-----------3.297亿;
该项对比结果为:纯氧常压气化炉比鲁奇炉少投资3.368亿。
二、年运行费用对比
鲁奇加压气化炉-------------年生产费用3.79亿元;
纯氧常压气化炉-------------年生产费用4.62亿元;
该项对比结果为:纯氧常压气化炉年运行成本比鲁奇炉高 1.43亿元。
三、常压炉和鲁奇炉对比结论
加压鲁奇炉一次性投资多3.368亿元。运行成本年节省1.43亿元,在2.35年回收该一次投资。对比结论是鲁奇炉比常压炉更适合本项目。
四、常压炉和鲁奇炉分析明细
1、投资对比
序
号项目
纯氧常压气化炉
万元
鲁奇加压气化
万元
1 焦块筛分+焦粉制块
+输送
650 650
2 入炉前煤锁100 800
3 煤气炉系统11700(8开备2)38000(三开一备)
5 循环水处理站(回收)1220 12000
6 气柜+电除尘1000
7
一级压缩机
二级压缩机
10000
8 空分8000 15000(汽轮机拖动)
投资合计 3.297亿 6.665亿差值+3.368亿
该项对比结果为:纯氧常压气化炉比鲁奇炉少投资3.368亿2、年运行费用对比
一年(8000小时)生产费用表
序号项目纯氧常压气化炉鲁奇加压气化
1 焦炭t/h53 56
8000小时万元
13568 14336
(焦炭320元/t)
2 氧气耗Nm3/h 2592019948
8000小时万元
6220.8 4787.52
(氧气0,3元/Nm3)
3 蒸汽耗t/h 82126
30(回收用)
8000小时万元
7872 12096
(蒸汽120元/t)
4 电耗kw h 408001600
8000小时万元
18604.8 729.6
(电价0,57元/kwh)
8000小时生产费用
46265.631949.12
5合计
万元
差值+14316.68
对比结果:纯氧常压气化炉年运行成本比鲁奇炉高1.43亿元。
3、气化煤气成分对比 气化方法
煤 气 成 分 (V %)
CO 2
O 2 CO H 2 N 2 CH 4 煤气热值 纯氧常压气
化炉
16.8 0.3 44.4 36.5 0.2 0.4 10.43 MJ/Nm 3 鲁奇加压气
化 20.4 0.3 35.2 31.3 0.8 12 13.22 MJ/Nm 3
对比结果:有效成分都适用本项目,鲁奇加压气化CH 4偏高,可上LNG 装置提升产品的附加值。
4、气化原料需求对比
对比结果:焦块和焦粉成型都能在两种炉型上使用。
项 目
纯氧常压气化炉 鲁奇加压气化 床层形式
固定床 固定床 排渣形式
固态 固态 进料形式
块煤、型煤 块煤、型煤 适合的煤种
无烟煤、焦炭 褐煤、烟煤、焦炭 气化剂
氧气+蒸汽 氧气+蒸汽 气化压力Mpa
0.03 3.5~4.2 气化温度 ℃
1200 1100 煤的粒度要求mm
15~50 6~50 煤的灰份要求%
<25 <33 煤的灰熔点要求℃
>1200 >1200 单炉最大投煤量t/d 180 1000
5、噪声污染、泄漏率、操作人员数量
常压气化炉工艺压缩机的噪音是现在环保要求消除的一项要求,如果使用鲁奇炉工艺,不需要压缩机,噪声污染小。
常压气化占地面积较大、煤气流程长,泄漏率要高于煤气流程短的鲁奇炉,装置环境较差,粉尘产生量大,生产环境没有保障。。同时常压系统在事故状态下停车,例如停电时由于系统压力低,反应物无法送入火炬系统,只能排入大气中,安全和环保问题无法解决,随着环保要求的日益严格,常压不符合时代进步的要求。
鲁奇炉工艺不需要压缩机和电除尘操作工,减少定员28人(每班电除尘2人,压缩机3人,检修人员8)
6、运行周期和计划检修对比
常压气化炉工艺的主要故障在煤气炉10台炉每个月有1台炉大修,一台炉备用。7台压缩机,每台压缩机要2个月维修一次。这样对制氢系统的负荷波动频次17次。不利于生产的安—稳—长—满—优运行。鲁奇炉3开一备,运行周期10个月,没有压缩机。一年只影响3次。对比来讲鲁奇炉对制氢负荷影响次数,少于纯氧常压气化炉。
纯氧常压气化炉鲁奇加压气化
运行周期8个月10个月
计划检修因计划检修,年影响制氢负荷17次因计划检修,年影响制氢负荷3次
7、该项目选择鲁奇炉的七个优势
鲁奇碎煤固定床气化介绍:
鲁奇碎煤固定床气化,是德国鲁奇煤和石油技术公司在1926年开发的一种加压移动床煤气化设备。目前共有近200多台工业装置,鲁奇炉现已发展到炉径为5. 0m,每台产气量可达100000m /h,分别应用于美国、中国和南非。
碎煤加压气化采用自热式,逆流移动床生产工艺,气化炉为立式圆筒形结构,炉体由耐热钢板制成,有水夹套副产蒸汽,鲁奇碎煤固定床是干法排灰气化。鲁奇炉是在高温高压下进行的复杂多相的物理化学反应过程,在本质上是将煤由高分子故态物质转变为低分子气态物质的过程,气化过程的基本反应就是碳与蒸汽的反应,即C+H2O=CO+H2。
在气化炉内煤由上部加入,气化剂逆流流动,煤在向下运动的过程中,在气化炉内煤由上至下大致分为四个区,即干燥区、干馏区、气化区、灰渣区。气化区又分为氧化层、还原层和甲烷层。各区、层间并没有明确的界面,只能视其主要反应特性进行分区、分层。
通过对国内外煤制气工艺技术分析,结合本项目原料、产品、规模特点,从生产的环保性、经济性、安全可靠性、投资省、技术适用性等方面考虑,本项目采用鲁奇加压气化技术,是最为适宜的。具体分析如下:
1、鲁奇碎煤加压气化技术是目前世界上建厂数量最多的煤气化技术,运行中的气化炉达数百台。鲁奇气化炉生产能力大、煤种适应
性广,技术成熟,这是本项目选择该炉型的优势之一。
2、针对运行中的鲁奇气化炉气化成分中甲烷含量高(8~10%),不适合合成气使用的弱点。
该项目所需的只是全变换后的氢气,甲烷气选择上LNG装置来解决,发挥对能源的优化利用,这是本项目选择该炉型的优势之二。
3、针对运行的鲁奇气化炉气化成分中且含焦油、酚等物质,气化炉后需设置废水处理及回收等装置,用于造气生产流程长、投资大,生产的煤气比较适合城市煤气弱点。
该项目的气化装置全部采用焦碳为原料,所以鲁奇炉产生的焦油、酚类远低于同行业的鲁奇炉,也要比其他炉型低,所以产生的废水总量和污水含量也远远低于其他炉型,这是本项目选择该炉型的优势之三。
4、鲁奇加压气化采用碎煤加压技术,本项目的气化装置全部采用焦碳为原料,焦炭作为已经加工过的原料,焦炭的含N元素要低于气化煤,所以本项目气化炉作为源头第一步已经比同行业的气化炉在氨氮产生的环节有了一定降低氨氮的优势,这是本项目选择该炉型的优势之四。
5、本项目需要粗煤气为13.3万Nm3/h,规模上选用鲁奇炉是合适的,稳定供气是整个项目的基础。如果选用其它大型化的炉型,在本项目生产上需要备炉率高,造成投资的大幅度增加;选用小型炉带的占地很大,造成土地资源的浪费。这是本项目选择该炉型的优势之五。
6、鲁奇炉新工艺中,将气化污水用于气化,大大降低了污水的产生量,这是本项目选择该炉型的优势之六。
8、GSP、Shell、鲁奇三种气化工艺比较
GSP、Shell、Lurgi三种气化工艺比较表
名称GSP Shell Lurgi
原料要求(1)褐煤→无烟煤全部煤
种,石油焦、油渣、生物
质;(2)粒径250μm~
500μm含水2%干粉煤(褐
煤8%);(3)灰熔融性
温度<1400℃;(4)灰分
1%~15%(灰熔点低时可
放宽到20%)
(1)褐煤→无烟煤全部煤
种;(2)90%<100目含水
2%干粉煤(褐煤8%);(3)
灰熔融性温度<1400℃;(4)
灰分8%~15%(灰熔点低时
可放宽到20%)
除主焦煤外全部煤种,
5-50mm碎煤,含水35%
以下,灰25%以下,
灰熔点≥1200℃
气化温度/℃1450~1550 1450~1550 取决煤灰熔点,在DT-ST间操作
气化压力/Mpa 4.0 4.0 3-4.0
气化工艺特点干粉煤供料,顶部单喷嘴,
承压外壳内有水冷壁,激
冷流程,由水冷壁回收少
量蒸汽,除喷嘴外材质全
为碳钢
干粉煤供料,下部多喷嘴对
喷,承压外壳内有水冷壁,
废锅流程,充分回收废热产
蒸汽,材质碳钢、合金钢、
不锈钢;干法过滤+洗涤除
尘,透平循环,煤气冷激炉
出口粗煤气
粒状煤供料,固体物料
和气化剂逆流接触,煤
通过锁斗加入到气化
炉,通过灰锁斗将灰排
出炉外,气化炉由承压
外壳、水夹套、转动炉
篦组成,炉内物料明显
分为干燥、干馏、煤气
化洗涤除焦油/尘后进入
废锅。材质为碳钢
单台气化炉尺寸/mm 投煤2000t/d
φ内=3500
H-17000
投煤2300t/d
φ内=4600
H=31640
投煤量800-1000t/d
φ内=4000 H=11000
耐火砖或水冷壁寿
命/年
20年20年
喷嘴寿命10年,前端部分1年1年~1.5年
气化炉台数(1200
×106m3/d)
16 16 46
冷激室或废锅尺寸
/mm
冷激室φ内=3500 约为2500 洗涤+废锅除尘冷却方式分离+洗涤干式过滤+洗涤洗涤
去变换温度/℃220 40 180~185
标煤消耗t/106kJ (包括干燥)34.2 (包括干燥)34.2 33 氧耗Nm3/106kJ
(99.6%)
29 29 10 电耗kW/106kJ 3.6 5.8 0.3 碳转化率% 99 99 99 冷气效率% 80 80 80 气化热效率% 90 96 90
投资万元(1200×106Nm3/d) 967000(其中空分522000)1272000(其中空分522000)
480000(其中空分
184000)
由上表可知:
成熟的气流床气化工艺与Lurgi相比在消耗指标上差别最大的是氧气消耗,Shell、GSP气化是Lurgi气化2.9倍;电:Shell是Lurgi 气化19倍,GSP是Lurgi12倍;投资相差也很大:Shell投资是Lurgi 的2.6倍,GSP是Lurgi的2倍,造成投资大的主要原因除气化装置外,空分装置规模影响更大。
链条炉排结构型式有哪几种它们的结构型式和技术性能如何
链条炉排结构型式有哪几种?它们的结构型式和技术性能如何为了实现加煤和除灰的机械化,链条炉排结构作为燃煤工业锅炉的一种燃烧方式,已应用相当广泛。锅炉中采用的链条炉排型式有链带式,横梁式和鳞片式三种。一、链带式炉排它们的炉排片的形状好象链节,用圆钢串连成一个宽阔的链带。炉排的传动有变速箱传动、间歇液压传动和晶闸管无级调速传动等。间歇液压传动机构简单,但间歇运动对燃料稳定燃烧不利,且液压设备容易漏油,现在已很少采用。一般采用晶闸管和其他机械无级变速传动机构,其效果较好。链带式炉排具有如下几点特性:1、链带式炉排结构简单,金属耗量较少,制造成本低,安装制造和运行管理都比较方便。 2、由于自身结构原因,链带式炉排的通风截面是一般的16%左右,甚至更高。这使得漏煤量比较大,且运行一段时间后炉排片之间磨损严重,加大了通风间隙与漏煤量,一般漏量可达3%~7%。 3、轻型链带式炉排长时期运行后,圆钢拉杆极易变形,同时炉排片较薄、强度较低,许多炉排片串在一根圆钢拉杆上,有时互相配合不良;主动轴上的链轮直接和主动炉排片楔合,使主动炉排片在热应力和拉应力的作用下,容易折断,折断后更换比较困难。 4、容量较小的锅炉,大多数采用轻型链带式炉排。它只适用于10t/h以下的锅炉应用。 5、为了解决轻型链带式炉排片断裂问题,我国很多地区研制了大块炉排片,其结构就是把原来分为多片的炉排片合起来铸
成一块。在这基础上经过改进,研制了带活络芯片型链带式炉排片,在使用上取得较好的效果。二、横梁式炉排横梁式炉排的炉排片是安装在横梁上,炉排片不受力。横梁固定在两根或三根的链条上,链条的传动,一般用前轴做主动轴,与电动机变速机械相连,前后轴上链轮啮合,完成炉排的运行。链条上固定的许多横梁,横梁槽内装有几种型号的炉排片,有普通的炉排片,调整炉排片以及封闭炉排片等。横梁式炉排的特点有: 1、横梁式炉排的结构钢性大,炉排片装在钢性较强的横梁上,主动轴上链轮通过链条带动横梁运动,而炉排片不受力,故工作条件较好,不容易发生受热变形。 2、炉排面比较平整,而且耐用。有的炉排片有一个长长的犟三,筐前亏护排片互相交叠,可以大大减少漏煤损失。炉排通风截面比约 4.5%~9.4%。3、维修方便,即使有炉排片损坏,亦可在运行中方便地更换炉排片:它可在20t/h以下锅炉中应用,并能燃用无烟煤。 4、其缺点是结构笨重,金属耗量太大。另外,这种炉对链条的强度要求较高。由于链条所承受的载荷大,使得链条与链轮的啮合力量也较大。提高了对链条,链轮的加工精度要求。如果几根平行的链条由于加工质量、安装质量不好,个别链节与链轮脱离啮合,爬到链轮的齿顶上去,即产生爬牙现象,严重时会损坏链条或磨掉链轮齿牙。横梁式炉排除一些旧式锅炉外,目前国内已很少使用。三、鳞片式炉排鳞片式炉排整个炉排根据宽度不同有4到12根互相平
链条炉排常见故障的原因
链条炉排常见故障的原因 在小型锅炉的日常应用中,炉排的故障较多,维修量大,影响着锅炉的正常使用。锅炉炉排出现故障的原因是多方面的。 (1)材质要求不高。为降低造价,炉排侧密封铁多采用HT200,其耐热温度较低易造成高温烧损、变形卡链条。由于炉膛内温度较高,故宜采用耐热铸铁制造。如RQTA122,在空气炉气中耐热温到1100℃。炉排主链条也宜采用耐热铸铁,以保证长久良好的机械性能。 (2)炉排制造精度要求不高,误差大。作为快装锅炉,炉排前后轴的平整度影响着炉排行进阻力大小及应力平均程度,易造成炉排跑偏、断片。炉排跑偏时两侧螺栓调整没有参考标尽,单凭经验,给用户造成不便。 (3)炉排主动链齿工装误差大,造成链齿磨损,炉排因受力不均撕裂、起拱、炉排轴弯曲。链齿插铣键槽时没有统一校准或装配时秩序有误,造成链齿不同步。例如一台10t/h 锅炉链齿误差达12mm,锅炉运行中炉排经常大面积撕裂,炉排轴弯曲,不得已全面检修,耗时费力。 (4)风室落灰装置亟待改进。风室内积灰及时排除有利于正常供风,炉梁得以冷却。落煤灰得不到及时排除会因炉内高温而燃烧,烧坏炉梁道轨。除去运行操作人员要正确及时操作外,摇灰把手或拉杆要省力可靠,落灰板最好整板制作,摩擦面经打磨加工,充分考虑热变形带来的影响。另外,第一风室是煤的预热干燥阶段,所需风量小,运行时一般关闭,而漏灰多为细煤,极易燃烧。曾发现有几台锅炉多次出现炉梁过烧变形,大都集中在第一、二风室,后来维修时将第一风室封闭,使之不漏煤,使用效果良好。 (5)风门风量控制粗糙。由于炉排烘烤,风门处温度一般在100℃左右,受胀缩影响,部件易变形,造成关不严、开度与实际不符等故障。 (6)前后大轴润滑方式亟待改进。前后大轴多采用轴瓦滑运摩擦,用润滑脂润滑,一般由4~8个加油孔径组成。由于前后大轴工作温度在100℃附近,普通钙基脂易固化,宜采用耐温润滑脂。但油路过细过长,加油仍很困难。有的锅炉房尝试用30#机油杯代替,目前使用效果良好。 (7)运行过程中维护不当。很多单位的司炉人员工作素质偏低,缺乏锅炉的相关知识,有的则是责任心不强,如清灰不及时,导致通风不畅,油杯缺油,使得润滑不佳。很多细小的毛病得不到及时的发现,最终酿成在事故。 (8)领导管理出现问题。如不燃用规定煤种,以至于锅炉和燃煤不相适应,不做定期的检查保养。不恰当地减少司炉操作人员。 作为锅炉制造厂家,在制造过程中,应重视炉排燃烧部件的质量。作为使用者,在日常运行中也应重视对设备的精心维护。
链条炉燃烧操作原则配风方法有三种
链条炉燃烧操作原则配风方法有三种,即尽早配风法,推迟配风法和强风后吹法。 1、尽早配风法 这种方法是根据燃料层对空气的消耗能力尽早配风。在燃烧前期燃料放出大量的挥发物,此时就开始送人大量空气,并且随着燃料温度的提高和燃烧的加强,尽可能加大送风,直至燃尽。以五个风室为例:第一风室按燃煤挥发分的高低适量送风,一般到第二风室就送人大风(全开),第三风室也如此,直至第四风室,送风稍有减少。其后燃料层的燃烧转入燃尽阶段,空气消耗量进一步减少,送风量也随之大幅度减少,因此第五风室只需稍开或全关(供漏风供风)。这种配风方式有如下特点: (1)尽早配风法适用于高挥发分的燃煤,前期燃煤吸收热量释放大量的挥发物,为使可燃气体(挥发物)得到充分的燃烧,需要送入大量空气,形成炉排前部燃烧强烈。 (2)由于前部燃烧强烈,前拱区容易结渣,甚至烧坏煤闸门,因此要注意控制前部送风量;同时由于前部燃烧强烈,烟气体积急剧膨胀,致使后拱内的烟气流出不畅,形成烟气在后拱出口处的闷塞。 (3)燃烧高温区在靠前部,炉排后部弱燃烧区面积较大,温度降低,难以维持焦炭燃尽,导致炉渣含碳量增加,降低了锅炉的燃烧效率。 2、推迟配风法 推迟配风法仍以五个风室为例:第一风室为引燃期,不专门送风(只靠风室漏风供风);第二风室已进入燃烧旺期,但仍送小风或中风;在燃烧中期(第三、四风室)送强风;第五风室已处于炉排末段,只需很小风量,一般以保证炉排的可靠冷却为宜,因此风门全关,靠邻近风室漏风供风。 推迟配风法的特点是: (1)推迟配风法与尽早配风法的主要差别在于第二风室的配风量:推迟配风法是故意压减其送风量,而尽早配风法则是按可燃气体需要量送入大量空气。由于故意压减其风量,前部大量释放出的可燃气体形成一个缺氧的“饥饿”空间,极需炉排后部的过量空气及炉膛漏风供氧燃烧,有效地降低总的过量空气系数。 (2)由于燃煤层进入后拱后才送以强风,必然在后拱出口处或炉排中部形成一个高温区。这个高温区向前冲的高温风流容易深入前拱起着引燃的作用,对于向后通过辐射加热保持了燃烬区的高温,促进焦碳的燃尽,形成了“烧中间、促两头”的燃烧方式。 (3)推迟配风法的使用是有条件的,那就是要求炉拱的混合性能好,以保证后部富氧的烟气和前部较多燃气的烟气充分混合,达到可燃气体燃尽的目的。 3、强风后吹法 这是一种极端推迟的特殊配风法。从新煤进炉起的一段很长的炉排下不送风,直至最后一、二个风室才送以强风。此时因燃煤温度已较高,见风立即着火并强燃烧。后吹的强风将后部燃烧区大量灼热细粒煤从炉排煤层中吹起,随烟气向前飞去,撒落在前部的新煤上,形成一灼热煤粒覆盖层。这一覆盖层对新煤持续地加热,直至一、二风室处完成引燃。 这种配风法主要特点: (1)送风的极端推迟和后吹强风,创建了一个灼热煤粒覆盖层,目的是促进燃料的引燃,即所谓“烧后部、促前头”。 (2)强风后吹法的主要优点可以燃烧低挥发分无烟煤,是福建地区为燃烧当地无烟煤而提出来的。它的主要缺点是由于送风过于集中,燃烧强度大幅度增高,容易导致火床严重结渣,破坏后部燃烧区煤层,导致过量进风,影响正常燃烧。另外由于新煤上的覆盖层过厚,影响新燃料吸收辐射热,反而使着火恶化。 新安装的锅炉或经大修和改造的锅炉,锅炉的炉墙、炉顶以及前、后拱等,都是新砌筑的或是经过改造重新砌筑的。在炉墙内,耐火混凝土及抹面层内部都含有大量水分。
链条炉排对煤种的基本要求
链条炉排对煤种的要求 链条炉排燃用挥发分15%以上、热值大于4500kcal/kg、灰熔点高于1260摄氏度、粘结性弱的烟煤最为适宜。 一般水分、灰分增加、挥发分减少对燃料的引燃和燃烧都是不利的。 1、水分:煤中适当的水分可使碎屑和块煤粘在一起,使漏煤和飞灰减少。另外,水分蒸发可使煤层松动,加大煤粒间的间隙,通风阻力随之减小,有利于通风,起到强化燃烧的作用。不利的一面是不利于煤的着火,还会使烟气体积增加,使排烟热损失增加。对于在细粉较多且易粘结的高发热值的煤中掺入适量的水分,不但有利于燃烧,提高锅炉效率,还可减轻煤层的结焦。 2、灰分:灰分增加可使燃烧成分减少,发热量降低,不利于煤的着火和燃烧。过多的灰渣会阻碍焦炭与空气的接触,也就是阻碍了焦炭的燃烧,增加了燃烧时间,最后导致不完全燃烧损失增加。燃烧过程中,由于还原作用而产生大量的还原气体,主要是CO,它能将灰渣中的氧化铁还原为氧化亚铁,使原有的灰熔点降低,这就容易在炉排上结焦,影响炉排的正常工作,严重时会使炉排片过热变形和烧坏。反之,灰分太少,灰渣层太薄,也可能使炉排片过热。 3、挥发分:一般来讲,挥发分含量越高,越容易着火和燃烧。挥发分含量低,着火困难,在炉排长度有限情况下,燃烧和燃尽的时间就相对减少,机械未完全燃烧损失就增加。挥发分含量高时,对于炉膛容积热负荷较高的锅炉,由于炉膛容积相对较小,易增加化学
未完全燃烧损失。 4、热值:热值较低时,锅炉的出力和效率都会降低。当燃用热值较低的煤的时候,燃煤量就要加大,炉排速度和煤层厚度就要相应提高,这将不利于燃料的着火和燃尽。 5、粘结性强的煤:粘结性强的煤在炉内受到高温辐射,表面软化熔融,形成板状结焦,使通风不利,严重时会导致燃烧无法连续进行。 6、煤的颗粒度:粒度不一的煤粒,容易堆得结实,水蒸气不易散发出来,热量也不容易传到煤层深处,着火就困难。并且火床层的阻力增加易产生火口。
链条炉排相关知识
链条炉排相关知识 如何处理炉排起烘现象? 炉排烧坏的原因及处理方法 炉排装置介绍 小鳞片式链条炉排的运行管理 小鳞片式链条炉排使用范围和要求 链条炉排燃烧调整的介绍链条炉怎样调整负荷?如何处理炉排起烘现象?炉排烧坏的原因及处理方法炉排装置介绍小鳞片式链条炉排的运行管理小鳞片式链条炉排使用范围和要求链条炉排燃烧调整的介绍链条炉怎样调整负荷? 如何处理炉排起烘现象? 炉排起烘原因:1、链条太松,局部卡住;2、对炉排下的漏煤、漏灰太多,致使炉排片间或炉排与链轮间夹灰过多而拱起;3、炉排片间隙过小,而穿条螺栓紧得太紧,受热后,炉排片膨胀挤紧而拱起。 处理方法:1、调整链条,如是链条本身不合格,则需更换链条;2、订出制度,及时清除漏煤和漏灰;3、安装炉排片不得过紧,以能自由活动为宜。 炉排烧坏的原因及处理方法 炉排烧坏原因:1、炉排上煤层不均,温度过高、且未经烧完的煤层堆在老鹰铁处继续燃烧;2、炉排下部区的挡板没有定期排灰,以致由火室漏下的煤末及细小煤块,在细灰斗内继续燃烧,使炉排骨架烧弯变形,甚至使炉排链子烧断;3、埋火时,炉排下部失掉冷却以致把炉条及链子烧坏。 处理方法:1、改造操作,推平堆煤;2、定期清渣清灰;3、改进压火操作技术。
炉排装置介绍 一、炉排的可调张紧装置炉排的可调张紧装置,一般是炉排前轴的轴承做成可移动的,用丝杆调节前后移动。调整螺钉的结构。它的主要作用是调整炉排的松紧程度和炉排前、后轴的平行度。为了不使炉排在运行时拱起,炉排必须有一定的张紧度;炉排因安装或运行时受各种因素的影响,炉排跑偏时,进行炉排前、后轴的调整,保证炉排安全稳定运行。横梁式、鳞片式炉排还需要依靠自重张紧。 二、挡渣装置挡渣装置的主要作用有两个:一是为了不使炉渣落入后轴处翻开着的炉排片之间和延长炉渣在炉排上的逗留时间,便于炉渣燃尽,即“挡渣”作用;二是为历史老照片不能说的秘密慈禧军阀明末清初文革晚清了防止锅炉尾部渣井处的漏风,提高锅炉的热效率。 链条炉排上常用挡渣装置有两种:1、老鹰铁。它位于链条炉排末端即将转弯处,形如鹰嘴,铸铁制成,因而得名。它具有上述的第一个作用,但不能阻止尾部漏风,因此其热效率较差。由于它结构简单,制造方便,又不易出故障,故得到了广泛的应用。2、挡渣摆。挡渣摆安装于链条炉排尾部上方,它具有上述挡渣装置两个作用。因此能提高锅炉效率。但其缺点是结构比较复杂,使用不当时,炉排后部容易结渣并常常被烧坏,平时维修工作量大。因此,它的应用不如老鹰铁广泛。 三、侧密封装置为保证链条炉排灵活移动,炉排与两侧静止框架(墙板)之间必须留有一定的间隙,以免相互摩擦,阻碍炉排运行。但间隙不可太大、尽量避免空气漏入炉膛.恶化炉内燃烧、降低锅炉热效率。因此,必须采用可靠的侧密封装置,尽量减少漏风。 炉排的侧密封装置,其具体结构可能稍有不同,其型式各样,如灰封式侧
链条炉排锅炉燃烧问题分析
链条炉排锅炉燃烧问题分析 【摘要】本文主要分析了轻型链条炉排运行过程中煤料燃烧的对轻型链条炉排产生的影响。 【关键词】链条、炉排、燃烧 一、我国现有锅炉基本燃烧情况 我国锅炉大多数采用链条炉排,链条炉排突出的优点是冷却好、投资少、操作简单,运行比较可靠。但是也存在不少缺点:除结构复杂外,在燃烧方面存在的问题比较多如:煤燃烧不完全导致锅炉出力不足,炉渣含碳量高,冒黑烟、煤种适应性差,不能烧次煤,炉排漏煤量大等。分层燃烧技术是系列技术较好的解决了链条炉排层燃存在的问题。分层燃烧技术是系列技术,有分层半沸腾燃烧技术、分层半悬浮燃烧技术、分层半沸腾半悬浮燃烧技术、均匀分层半沸腾燃烧技术、均匀分层半悬浮燃烧技术、均匀分层半沸腾半悬浮燃烧技术。从结构上分两类即内分层和外分层。以上分层燃烧技术各有特点,效果都不错,但有所区别。应用以上技术要因炉制宜,视其炉型、额定出力多少,媒质及要求等因素选用恰当的技术。此种技术的共同特点:技术装备比较简单,实施起来比较容易,改造工程量很小,投资少,效果好见效快(3至6个月收回投资)。 运动炉排层燃问题剖析:运动炉排指链条炉排、振动炉排、往复炉排。由于我国现在应用大量的链条炉排锅炉。凡接触过工业锅炉的大都有同感:锅炉出力不足,增负荷慢、炉渣含碳量高。排烟热损失大,热效率低。锅炉不同程度的冒黑烟,上缴污染治理费。锅炉吃细不吃粗,不能烧次煤,煤闸板、老鹰铁易烧毁和炉排故障多等等。为什么会出现这些问题,采取什么方法解决这些问题。 1、煤种的制约:设计锅炉都要首先选定燃用煤种。严格讲什么炉子烧什么煤是一定的。当烧设计用煤而且达到燃烧要求时,锅炉才能达到额定参数。然而,在我们国家不仅达不到这么高要求,而且供应锅炉烧的煤相当混乱,基本上是来什么煤烧什么煤。非正规开采的小煤窑媒质变化更大,煤的灰分高达0.3-0.4,这势必带来诸如出力不足,增负荷慢等一系列问题。 2、给煤方式问题:常规锅炉给煤方式:煤从煤仓经落煤管、加煤斗落在炉排上,再随炉排的运动经煤闸进入炉内燃烧,这种给煤方式有许多缺点。 1)煤层密实:煤从煤仓落到炉排上落差较大,在加上煤仓和落煤管内煤的重量,炉排上的煤被压得很密实,煤在炉排的带动下煤层经过煤闸又一次被挤压,所以进入燃烧室的煤层相当密实,造成煤层通风阻力大,透气性差,致使煤层在供氧不足的情况下燃烧。势必燃烧不完全,达不到应发出的热量。将造成一系列的问题。 2)煤层颗粒大小不一,分布不合理:我们国家的工业锅炉大都烧原煤,原
大鳞片式链条炉排
特点:1、运行稳定可靠。 2、不漏煤,提高燃烧效率。 3、重量较大。 4、锅炉房土建投资较大。 5、散件出厂,现场组装。大鳞片式链条炉排技术参数: 炉排有 效面积(m2)炉排面高 度(mm) 前后轴距 (mm) 炉排有效 宽度(mm) 炉排内侧 宽度(mm) 出轴长度 (至炉排中 心线)(mm) 出轴高 度 (mm) 出轴端 直径 (mm) 进风口中 心高度 (mm) 风室 数量 10t/h12.549976600230024501630655Φ1005005 10t/h10.899976325196420801445655Φ1005005 15t/h19.129987000307431902469655Φ1304505 15t/h16.829977000270428201815655Φ1205005 15t/h16.619977000267028201820655Φ1204505 15t/h(水平)16.8211987000270428201748855Φ1205805 20t/h23.149977500344435602205655Φ130506 20t/h21.429977000344435602205655Φ1305005 20t/h21.439987000347435502318655Φ1305005 20t/h(水平)20.6612067500307431902185865Φ1307106 20t/h(水平)23.539977500341035602205655Φ1305006 30t/h27.549978000381439302400655Φ1305006 30t/h32.5111978500418443002587855Φ1305007
工业锅炉链条炉排分类结构及工作过程
工业锅炉链条炉排分类结构及工作过程 链条炉排是工业锅炉中历史悠久、结构可靠、运行稳定的一种机械化燃煤设备,获得了广泛的应用。 一、链条炉排的结构 链条炉排的外形好像皮带输送机,其结构如图3—7 所示。其运行过程是煤从煤斗内依靠自重落到炉排前端,随炉排自前向后缓慢移动,经煤闸板进入炉膛。煤闸板的高度可以自由调节,以控制煤层的厚度。空气从炉排下面分区送风室引入,与煤层运动方向相交。煤在炉膛内受到辐射加热,依次完成预热、干燥、着火、燃烧,直到燃尽。灰渣则随炉排移动到后部,经过挡渣板( 俗称老鹰铁) 落入后部水冷灰渣斗,由除渣机排出。链条炉排的结构形式一般可分链带式、横梁式和鳞片式 三种。 1 .链带式炉排 链带式炉排属于轻型炉排,适用于蒸发量10t /h 以下的锅炉,其炉排片连接结构如图3_8 所示。炉排片分为主动炉排片和从动炉排片两种,用圆钢拉杆串联在一起,形成一条宽幅的链带,围绕在前链轮和后滚筒上。主动炉排片担负传递整个炉排运动的拉力,因此其厚度比从动炉排片厚,由可锻铸铁制成。一台蒸发量4 t /h 的锅炉,由主动炉排片组成的主动链条共有三条( 两侧和中间) 直接与前轴( 主动轴)上的三个链轮相啮合。从动炉排片,由于不承受拉力,可由强度低的普通灰口铸铁制成。链带式炉排的优点是:比其他链条炉排金属耗量低,结构简单,制造、安装和运行都比较方便。缺点是:炉排片用圆钢串联,必须保证加工和装配质量,否则容易折断,而且不便于检修和更换;长时间运行后,由于炉排片互相磨损严重,使炉排间隙增大,漏煤损失增多。 2 .横梁式炉排 横梁式炉排适用于蒸发量20 ~40 t /h 甚至更大的锅炉。|其结构与链带式炉排的主要区别在于采用。了许多刚性较大的横梁。炉排片装在横梁的相应槽内,横梁固定在传动链条上。传动链条一般是两条( 当炉排很宽时,可装置多条) 。横梁式炉排的优点是:结构刚性大,炉排片受热不受力,而横梁和链条受力不受热,比较安全耐用;炉排面积可以较大,阻力小而风量分布均匀;运行中漏煤、漏风量少。缺点是:结构笨重,金属耗量多,约是链带式炉排的 2 .7 倍;制造和安装要求高;受热不均时,横梁易出现扭曲、跑偏等故障。 3 .鳞片式炉排 鳞片式炉排适用于蒸发量10 ~60 t /h 的锅炉。其炉排面通常由4 ~12 根互相平行的链条( 类似自行车上的链条结构) 组成。每根链条用铆栓将若干个由大环、小环、垫圈、衬管等元件组成的链条串在一起,如图3—10 所示。炉排片通过夹板组装在链条上,前后交叠,相互紧贴,呈鱼鳞状,其工作过程如图3—11 所示。当炉排片行至尾部向下转入空程以后,便依靠自重依次翻转过来,倒挂在夹板上,能自动清除灰渣,并获得冷却。各相邻链条之间,用拉杆与套管相连,使链条之间的距离保持不变。鳞片式炉排的优点是:煤层与整个炉排面接触,而链条不直接受热,运行安全可靠;炉排间隙甚小,漏煤很少;炉排片较薄,冷却条件好,能够不停炉更换;由于链条为柔性结构,当主动轴上链轮的齿形略有参差时,能自行调整其松 紧度,保持啮合良好。缺点是:结构复杂、金属耗量多,该炉排比链带式炉排约高30 %;当炉排较宽时,炉排片容易脱落或卡住。 在目前的引进技术中,采用层状燃烧的燃烧设备,基本上为以上几种形式的链条炉排。由于引进国外先进的炉排生产线,炉排片的铸造精度和整体装配水平都有很大提高,不但减少漏煤,而且减少运行故障率。 二、链条炉排的燃烧特点 链条炉排的着火条件较差。煤的着火主要依靠炉膛火焰和拱的辐射热,因而上面的煤先着火,
链条炉排故障的原因及处理方法
链条炉排故障的原因及处理方法 摘要:在企业生产单位中,工业锅炉作为重要的动力设备,在生产中有非常重要的作用。工业锅炉中,炉排作为燃烧部件,在1200℃以上的高温条件下进行运转工作,形成的灰渣等对机械的磨损是非常严重的,这对机组的正常运行有很大的影响。本文就锅炉链条炉排的故障进行了分析,对其原因进行了解决,提出了接触故障的具体办法和防范措施。 关键词:链条炉排;炉排故障;故障原因;处理方法 在经济高速发展的今天,关于锅炉的研究成果越来越多,越来越先进。锅炉在实际的运行当中,受到诸多实际因素的制约。链条锅炉是机械化程度较高的一种层燃炉,是工业锅炉中使用较广泛的一种炉型,容量大部分为10-130t/h,一少部分在1—2t的小容量锅炉中都有应用。链条炉的干燥、着火燃烧及燃尽的各个阶段是沿炉排长度相继进行的,但又是同时发生的,因此它属于单面着火方式,运行时燃料无自身扰动,沿炉排长度方向燃料层有明显的分区。采用二次风能使燃料中的可燃物和飞灰可燃物燃尽,由于着火条件不好,因此它不适于烧水分很大、灰分又多、结焦性强的煤;它的另一个缺点是金属耗量大。在链条锅炉设计、运行、改造过程中,合理地进行配风和调节,对链条炉的燃烧、经济运行和提高锅炉效率具有重大作用。 一、链条炉炉排故障树分析 1.炉排故障树建模 图1是链条炉炉排的故障树,炉排是指链条炉中堆置固体燃料并使之有效燃烧的部件,空气从炉排下面分区送风,燃料随着运动着的炉排逐渐被带到炉中,逐渐着火,最后被排入后面的灰渣斗中。其组成部件(以链带式炉排为例)主要有从动轴、主动轴、炉排片、原钢拉杆等,因此,炉排是链条炉中的关键部分。 图1炉排故障树 2.解决办法 炉排脱落需要根据具体的产生原因进行调整与维修,炉排面不平需要重新找准炉排面的水平度;炉排长销两端螺母松动,采取措施是拧紧螺母,同时采用定位销进行限位;整组炉排片脱落则需要重新安装炉排夹板,检查轴销,调整炉排片等步骤,变速箱有异常声音则需要注意润滑系统及轴承系统。 二、链条炉排故障分析 1.链条炉排出现的故障现象
垃圾焚烧炉排炉分类及特点
垃圾焚烧炉排炉分类及特点 【摘要】本文简单介绍了城市生活垃圾焚烧炉的发展概况,详细介绍了生活垃圾焚烧炉的分类及各种炉排的技术特点。通过了解机械炉排的分类有助于选择合适的炉膛形状及炉排形式,保证高质量的垃圾焚烧。 【关键词】焚烧炉焚烧炉分类炉排机械炉排炉 从18世纪开始,生活垃圾已经开始集中收集和堆放,但是集中堆放造成严重的环境污染问题,到19世纪开始出现焚烧处理垃圾的方式,但是方法比较简单。进入19世纪末机械焚烧炉开始出现,并应用于垃圾焚烧处理。经过100多年的发展,垃圾焚烧技术有了显著进步。目前应用于垃圾焚烧的各种型号的垃圾焚烧炉有数百种,根据不同的分类方法可以分为以下几类。 一、按处理方式分类 最具代表性的城市生活垃圾焚烧炉有:层燃焚烧炉、流化床焚烧炉、回转窑焚烧炉。 其中层燃焚烧炉按炉排形势,又分为滚动炉排、链条炉排、水平往复炉排、顺推倾斜往复炉排、逆推倾斜往复炉排等。其中层燃机械炉排炉技术可靠,处理量大,维护方便,较适合我国生活垃圾处理的现状。流化床焚烧炉可分为循环流化床及沸腾炉,最大优点是可以达到完全的燃烧效果并对有害物质进行最彻底的破坏,一般排出炉外的未燃物均在1%左右,是几种方式中燃烧最充分的[1]。回转窑锅炉在城市生活垃圾处理中应用较少,主要应用于焚烧特种垃 圾及污泥。 二、按炉膛形状分类 炉排炉能否将垃圾进行充分燃烧,主要是保证3t+e原则(temperature——炉膛燃烧温度,time——烟气在炉膛内的停留时间,turbulence——燃烧烟气湍流程
度,ex-cessoxygen——过热空气量)。炉膛燃烧烟气紊流程度主要和炉膛结构和尺寸,二次风布置有关。炉膛形状主要分为3种类型,顺流式、逆流式、混流式(见下图1)。 顺流式焚烧炉炉膛进口设在焚烧炉尾部,烟气流向与垃圾运动方向相同,适用于低水分,高热值垃圾。顺流式主要应用在欧美等发达国家,在国内应用较少。逆流式焚烧炉炉膛进口设置在焚烧炉前端,烟气流向与垃圾运动方向相反,具有较强的垃圾干燥能力,特别适用于高水分,低热值的垃圾。混流式焚烧炉炉膛进口位于炉排中部,根据垃圾热值的高低可调节炉膛位置,热值高时向焚烧炉尾部移动,热值低水分高的时候需要干燥新投入的垃圾,炉膛可向焚烧炉前部移动。根据我国城市生活垃圾的特性,目前国内应用较多的为混流式垃圾焚烧炉,依据城市的垃圾特性做结构的适当调整。 三、按炉排结构分类 层燃型垃圾焚烧炉主要由进料斗、进料管、推料器、炉排、炉排片、液压系统、液压站出渣口、除渣机、炉墙钢架及炉墙、一次风二次风系统等组成。其中炉排作为垃圾焚烧炉排炉最核心的的组件是用来区分机械炉排炉结构形式的主要方法。 层燃炉炉排主要分为往复炉排、滚筒炉排、链条炉排、摆动炉排、移动式炉排等。而目前应用较多的层燃型炉排主要有逆推倾斜炉排,顺推倾斜炉排,水平双向往复炉排组合式炉排,两段式炉排等等[2]。 (一)逆推式炉排 逆推式炉排指垃圾燃烧过程中垃圾的运动方向与炉排运动方向相反,每级炉排横向布置做往复运动。逆推式炉排一般倾斜布置,便于垃圾自然滚落,例如matin 型垃圾焚烧炉炉排倾角26?,alstom型垃圾焚烧炉炉排倾角24?。逆推炉排一般不分级,整体呈一个燃烧面,由于炉排倾角较大,垃圾有靠自重向前移动的倾向。
链条炉排的燃烧特点
链条炉排的燃烧特点链条炉排的着火条件较差。煤的着火主要依靠炉膛火焰和拱的辐射 热 , 因而上面的煤先着火 , 然后逐步向下燃烧。这样的燃烧过程 , 在炉排上就出现了明显的区域分层 , 如图 3- 11 所示。煤进入炉膛后 , 随炉排逐渐由前向后缓慢移动。在炉排的前部 , 是新煤燃烧准备区 , 主要进行煤的预热和干燥。紧接着是挥发分析出着火并开始进入燃烧区。在炉排的中部 , 是焦炭燃烧区 , 该区温度很高 , 同时进行着氧化和还原反应过程 , 放出大量热量。在炉排的后部 , 是灰渣燃尽区 , 对灰渣中剩余的焦炭继续燃烧。 - 在燃烧准备区和燃尽区都不需要很多空气 , 而在焦炭燃烧区则必须保证有足够的空 气 , 如果不采取分段送风 , 会出现空气在炉膛前后两端过剩 , 在中部不足的弊病。 为了改善上述燃烧状况 , 通常采取以下三种措施 : 1. 炉拱布置炉墙向炉膛内突出的部分称为炉拱。炉拱的主要作用是储蓄热量 , 调整燃烧中心 , 提高炉膛温度 , 加速新煤着火。其次是延长烟气流程 , 促进燃料充分燃烧。 炉拱有前拱、中拱和后拱三种。其中经常使用的是前拱和后拱。中拱多用于锅炉改造中 , 当供应的煤质较差时 , 作为改善燃烧条件的补充措施。 (1) 前拱 : 前拱位于炉排上方的前炉墙下部 , 一般由引燃拱 ( 又称点火拱 ) 和混合 拱 ( 又称大拱 ) 两部分组成。引燃拱的位置较低 , 靠近煤闸板 , 一般距炉排面 约 300~ 400mm, 主要作用是吸收高温烟气中的热量 , 再反射到炉排 J 前部 , 加速新煤的着火燃烧。混合拱的位置较高 , 主要作用是促进烟气和空气良好混合 , 延长烟气流程 , 使其充分燃烧。 图 3-12所示是常见的几种前拱结构形状。 图 3-12(a )所示的前拱 , 由小斜型引燃拱和低而长的混合拱组成 , 起遮盖作用 , 可减少炉排前部两侧的水冷壁管吸热 , 保持炉膛前部有较高的温度 , 以利于新煤烘干和着火。 图 3-12(b) 所示的前拱 , 由倾斜型引燃拱和较高的水平混合拱组成 , 能有效地将热量反射到新煤上 , 改善燃烧条件。 图 3-12(c) 所示的前拱 , 由抛物线型引燃拱和较高的水平混合拱组成 , 可将热量集中反射到新煤上 , 即起到“聚集“的作用 , 使燃烧条件更好。但这种拱的曲线复杂 , 砌筑和悬挂困难,表面不可能光洁 , 不容易收到理想的反射效果 , 所以实际应用不多。
振动炉排蒸汽锅炉的构造及燃烧特点
振动炉排蒸汽锅炉的构造及燃烧特点 一、振动炉排蒸汽锅炉的构造及工作原理: 振动炉排蒸汽锅炉是小容量锅炉采用的一种结构简单、钢耗量和投资费用较低的机械化燃烧设备。它的整个炉排面在交变惯性力的作用下产生振动,促使煤层在其上跳跃前进,实现了燃烧的机械化。 风冷固支点的振动炉排,由炉排片,上框架、弹簧板、固定支点,下框架和激振器等几个主要构部件组成。 上框架是组成炉排面的长方形焊接框架,其前端向焊有安置激振器的大梁,在整个长度上又横向焊接了一系列平行布置的“7”型梁。铸铁炉排片就搁置在“7”型梁上,并用拉杆钩住炉排片下的小孔,保证震动时炉排片不会脱落。 下框架是由左右两条钢板和用以固定炉排墙板的型钢拼焊而成,并用地脚螺栓固定在炉排基础上。弹簧板分左右两联结于上、下框架之间,它与水平的倾角为55°~70°,下端采用固定支点连接于 下框架,上端与“7”型梁相接支撑着上框架。 在蒸汽锅炉炉排前端装有激振器,它是振动炉排的振源,有轴承座、转轴、偏心块和皮带轮等组成。激振器由电动机通过皮带轮驱动旋转,产生一个周期变化而垂直于弹簧板的力,此作用力可分解为水平和垂直两个分力,水平分力使煤想炉后移动,垂直分力使煤从炉排上微跃。这样周期性地,间断微跃向后运动,实现了加煤、除渣的机械化。 改变偏心快的转速,可以调节振幅。转速增加,振幅也越大,煤的移动速度也越大。当转速达到某值时,炉排振幅达到最大值时,工程上称为共振,即偏心块转动产生的工作频率与蒸汽锅炉炉排本身的固有频率相同。此时,煤的移动速度最大,所耗的功率最小。通常,蒸汽锅炉震动炉排都选在共振状况下工作。蒸汽锅炉炉排的固有频率与蒸汽锅炉炉排的刚性成正比,与其质量成反比。而蒸汽锅炉炉排钢性可用弹簧板的厚度来调整。根据运行经验,蒸汽锅炉炉排工作的震动频率一 般宜在800~1400r/min左右;最佳振幅一般为3~5㎜,此时煤的运动速度约100㎜/s。蒸汽锅炉 炉排振动的间隔和每次振动的时间与锅炉负荷、蒸汽锅炉炉排结构和煤层厚度等因素有关,可采用时间继电器控制和调节,一般每隔1min左右震动一次,每次震动1~3s。 二、震动炉排蒸汽锅炉的燃烧特点: 振动炉排蒸汽锅炉排燃烧过程三阶段的划分也是沿蒸汽锅炉炉排长度来划分区段,其燃烧情况与链条蒸汽锅炉也相似。因此分段送风、设炉拱、采用二次风等措施也都适用。与链条蒸汽锅炉不 同点也是煤与蒸汽锅炉炉排有相对运动,其运动方式与往复推饲炉排蒸汽锅炉不同,煤不是在蒸汽锅炉炉排上向下滚动,而是微跃向后运动。 由于蒸汽锅炉炉排振动,煤层上下翻动,有较好的鳄拨火作用,不易结块。同时使燃料和空气有良好的接触,燃烧比链条蒸汽锅炉剧烈。蒸汽锅炉炉膛温度较高,一般高达1400℃左右。对煤种